GB/T12333-1990
金属覆盖层工程用铜电镀层
Metalliccoatings--Electroplatedcoatingsofcopperforengineeringpurposes
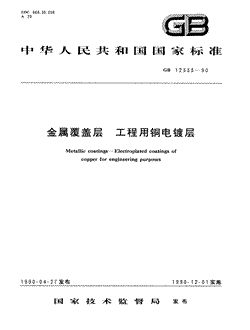
- 中国标准分类号(CCS)A29
- 国际标准分类号(ICS)25.220.40
- 实施日期1990-12-01
- 文件格式PDF
- 文本页数8页
- 文件大小621.02KB
以图片形式预览金属覆盖层工程用铜电镀层
金属覆盖层工程用铜电镀层
国家标准 GB1233了一90 金属覆盖层工程用铜电镀层 Metalliccoatings一Eleetroplatedcoatingsof copperforengineeringpurposes 1990-04-27发布 1990-12-01实施 国家技术监督局 发布国家标准
国家标准 金属覆盖层工程用铜电镀层 GB1233了-90 Metalliccoatings--Electroplatedcoatingsofcopper forengineeringpurp0ses 主题内容与适用范围 本标准规定了金属基体上工程用铜电镀层的有关技术要求
本标准适用于工程用途的铜电镀层,例如在热处理零件表面起阻挡层作用的铜电镀层;拉拔丝加工 过程中要求起碱磨作用的铜电镀层;作锡镀层的底层防止基体金属扩散的铜电镀层等 本标准不适用于装饰性用途的铜电镀层和铜底层及电铸用铜镀层
引用标准 金属镀层及化学处理表示方法 GB1238 电工电子产品基本环境试验规程试验T锡焊试验方法 GB2423.28 B495金属覆盖浸厚度测定阳被游解库仑力法 GB4956磁性金属基体上非磁性覆盖层厚度测量磁性方法 GB5270金属基体上金属覆盖层(电沉积层和化学沉积层)附着强度试验方法 GB5931轻工产品金属镀层和化学处理层的厚度测试方法B射线反向散射法 GB6462金属和氧化物覆盖层横断面厚度显微镜测量方法 GB6463金属和其他无机覆盖层厚度测量方法评述 GB12609电沉积金属覆盖层和有关精饰计数抽样检查程序 GB12334金属和其他无机覆盖层关于厚度测量的定义和一般规则 术语 了 了.1主要表面 制件上某些已电镀或待电镀的表面,在该表面上镀层对制件的外观和(或)使用性能是重要的
最小局部厚度 了.2 在一个制件的主要表面上所测得的局部厚度的最小值,也称最小厚度
镀层的表示方法 镀铜层及有关处理的表示方法见GB1238
基体金属 本标准未对基体金属电镀前的表面状态作规定,但供需双方应对其进行商定
需方应向供方提供的资料 6.1 必要资料 国家技术监督局1990-04-27批准 1990-12-01实施
GB123了了 90 本标准的标准号,即GB12333; 铜电镀层的最小厚度要求(见第7章); 主要表面,应在定货单或图纸上标明,也可用有适当标记的样品说明, 抽样方案(见第11章); 破坏性试验的试样数量 是否进行孔隙率试验,需进行时,应说明孔隙率的要求; 是否进行可焊性试验,需进行时,应说明有关细节(见13.2); 是否进行氢脆性试验,需进行时,应说明试验方法和要求; 规定的铜镀层的厚度是否有尺寸公差的要求,若有要求,应说明公差值
6.2附加资料 必要时,需方还应提供下述资料 基体材料牌号; 零件的最大抗张强度或硬度; 是否已经作过或需要作消除应力的热处理, 是否要求作消除氢脆的热处理; d
铜镀件的包装、贮存或运输要求
6.3必要时,需方应提供代替产品进行试验的试样,即“替代试样"见第12章). 厚度系列 铜电镀层的厚度系列,即最小厚度要求及应用实例列于表1
表!铜电镀层的厚度系列 要求的最小局部厚度 应用实例 Hm 25 热处理的阻挡层 渗碳、脱碳的阻挡层;印制电路板通孔镀铜;工程拉拔丝 20 镀铜 12 电子、电器零件镀铜;螺纹零件密合性要求镀铜 锡覆盖层的底层,阻止基体金属向锡层扩散 上述类似用途或其他用途 按需要规定 钢件电镀前消除应力的热处理 8. 若箭方规定电饿前粥制零件要作消除应力的热处理,一般按丧3的规定进行 表2钢件电镀前消除应力的热处理规定 热处理 钢的最大抗张强度值Rm MPa 温度,c 时间,h R1050 190220c 至少1h 1050
GB12333--90 8.了表面曾淖火的零件,消除应力应在130~150C至少处理5h
如果允许基体表面的硬度降低,也可 以在较高温度下作较短时间的处理
9 镀层要求 外观 在主要表面上,镀层应光滑平整,不应有明显的缺陷,如起泡、麻点、粗糙、裂纹、剥皮、烧焦及漏镀 处
局部电镀层(如防渗碳镀铜)的边界应无毛刺,结瘤或其他有害的不规则边缘
非主要表面上可允许 的镀层缺陷及其程度应由需方规定
主要表面上不可避免的挂具痕迹的状况及其位置也应由需方作出 规定
必要时,供方可提出修改意见,但应由需方认可, g.2厚度 主要表面上铜层的最小厚度应符合表】的规定或需的要求,若有尺寸公差的要求时,还应达到需 方规定的公差值(见6.1中b和). 注,螺纹零件镀铜时,应避免螺纹的牙顶上镀得太厚,为了使牙顶上的镀层厚度不超过允许的最大厚度值,可以允 许其他表面上镀层的厚度比规定值略小
g.了结合强度 镀层与基体应结合良好,结合强度试验按GB5270中规定的适合铜镀层使用的一种或几种方法进 行
试验后镀层与基体之间不应有任何形式的分离
g.4孔隙率 当需方规定镀层有孔隙率要求时,可按附录A(参考件)规定的方法或需方指定的其他标准方法进 行孔隙率试验,试验结果应达到需方规定的要求
g.5可焊性 当需方规定镀层有可焊性要求时,应按GB2423.28中规定的一种方法或需方指定的其他标准方法 进行可爆性试验
试验结果应达到GB2423.28中4.6.4(焊槽试验)或4.7.4(烙铁试验)或4.8.4焊球 试验)规定的要求或者需方指定的其他方法规定的要求
需方还应说明试验的部分细则,具体内容见 13.2
g.6氢脆性 当需方规定某些结构钢或高强度钢零件电镀后需进行氢脆性试验时,可按附录B(参考件)规定的 方法或箭方指定的其他标难方法进行氢脆性试验
试验结果应达到各方法规定的要求
钢件电镀后消除氢脆的热处理 10 若需方规定电镀后钢制零件要作消除复胞的热处理,应按表3的规定进行
10.1 表3锅件电镀后消除氢胞的热处理 处理 热 钢的最大抗张强度R. MPa 时间,h 温度,C R1050 190~220c 至少8h 0501800 190~220C 至少24h 10.2热处理应在电镀后4h内尽快实施
10.了热处理温度不能超过零件的回火温度
10.4表面曾悴火的零件,消除氢脆时,应在130~150C加热至少2h,如果允许基体表面的硬度降低
GB12333-90 也可在较高温度下处理
10.5电镀的弹性零件或其他需要承受弯曲的零件,在消除氢脆之前不应被弯曲
17 抽样 为了检查铜镀层是否符合本标准第9章中的要求,应按GB1260.9的有关规定抽样
12 替代试样 12-1当镀件的大小和形状不宜进行本标准中规定的某些试验,或破坏性试验会明显地减少小批量电 镀产品的数量时,需方应说明是否采用替代试样进行本标准中规定的某些破坏性试验
替代试样与它所代表的镀件应该完全相同或十分接近,包括它们的基体金属材料的成分、含量、状 态、电镀前表面粗糙度,以及电镀工艺过程,甚至在电镀槽中与阳极和其他镀件的相对位置,距离等均应 与镀件一致,并与所代表的镀件同时进行镀前准备电镀和镀后处理
12.2如果需方没有另外的说明,在生产现场进行非破坏性试验和目测检查时,不得使用替代试样
试验方法 13 13.1厚度 可以根据镀件的不同情况选择GB4955,GB4956,GB5931,GB6462中的方法测量镀铜层的厚度, 也可以选择GB6463中规定的适合铜镀层使用的其他方法,但要保证测量误差在10%以内
有关镀层厚度测量的规定见GB12334 13.2可焊性 当按GB2423.28的规定进行镀层的可焊性试验时,需方应说明下述试验细则 是否进行加速老化试验 a. b. 老化试验的方法(见GB2423.28); 可焊性试验方法的类型,即焊槽法、烙铁法或焊球法、一般镀铜零件常用焊槽法
c.
GB1233了-90 附 录 孔隙率的试验方法 参考件 本附录规定的方法能测量钢铁基体上铜电镀层中通达基体的孔隙
贴滤纸法 本方法适用于试验表面允许贴附一定面积滤纸的零件 A1.1 试验溶液 A1.2 用蒸憎水配制含有下列成分的溶液; 铁银化押(K,re(cN)3 10g/L 氯化钠(NaCI) 20g/L 试剂级别;化学纯 A1.了试验步骤 应保持试验环境的清洁,避免空气中弥漫铁粉尘 用乙醇或其他适当的除油剂彻底除去待测表面的油污,以蒸馏水洗净并晾干.刚出镀槽的零件不必 除油
将具有一定湿态强度的滤纸条浸入Al.2溶液.然后紧峦贴附在待测表面上,速纸和测试面之间不 允许有任何间隙,保持20mn,试验过程中应使滤纸保持润湿
取下滤纸并观察与镀层接触的表面
镀层中如有通达基体的孔隙就会有蓝色印痕出现
A1.4孔隙率的测算 将刻有方格(大小为lcm')的有机玻璃板,放在印有孔隙痕迹的检验谜纸上
记录测试面积和孔隙 数目,计算孔隙率(每平方厘米个数)
必要时,还应测量和记录最大孔隙的尺寸、数量和单位面积(如 cm')或指定面积内最多孔隙数,并在试验报告中说明
A2漫溃法 本方法适用于任何尺寸和形状的零件
A2.1 A2.2试验溶液 用蒸溜水配制含有下列成分的溶液 铁化钾(K.re(cN)1 10g/L 15g/L 氯化钠(Nac1) 白明胶 20g/L 试剂级别;化学纯 A2.了试验步骤 按AL.3的要求处理待测零件,然后浸入A2.2亲液,5min后取出观察,镀层中如有通达基体的孔 隙就会出现蓝色斑点 孔隙率的测算 A2.4 仔细测算浸入溶液中的表面积和蓝色斑点数,计算孔隙率(每平方厘米个数)
或按A1.4的方式处 理
GB12333--90 附录 B 氢脆性试验方法 (参考件) 本附录规定了用延迟破坏方法,鉴定高强度钢和抗张强度在1372MPa(140ke/mmi)以上的结构 俐和弹簧钢对某镀覆工艺的氢脆性是否合格
并可对镀覆工艺及产品的氢脆性作仲裁鉴定 B1 方法原理 高强度钢和结构钢由于吸收氢和施加应力的作用,在小于屈服强度的静载荷下持续一定时间,将发 生早期的脆性断裂 B2试样 B2.1试样的材料 B2.1.1鉴定镀覆工艺时,试样应与产品的材料相同,并热处理至抗张强度的上限
B2.1.2鉴定产品时,试样的材料和热处理工艺均与产品相同
B2.2试样的形状和尺寸 延迟破坏的试样,其形状和尺寸应符合图B1规定
" 60”土1" 0.02 R5 1×45 R0.120.0t 编号 13 6 图B1延迟破坏的试样(R0.12,K,=4) 2.了应力集中系数K 本方法规定试样缺口根部应力集中系数K,等于4,K,值是按Neuler公式作图求出的 试样的制备 B2.4 使试样的轴线平行于材料的轧制纤维方向,按图示要求加工
粗加工后热处理至材料要求的 B2.4.1 抗张强度,然后精加工到规定尺寸
缺口处用中软细粒氧化铝砂轮磨削,磨削量不宜过大,冷却液应充 分
试样加工进刀量开始为0.02~0.1mm,精加工时为0.005mm
磨削后应保证缺口根部半径圆滑 并投影检查,以保证缺口尺寸符合图示要求
逐根测量缺口根部直径尺寸(图中4.5士0.05mm),并记 录备查
股本?为了保证同心度,.试样两端的螺纹应热处理后再精加工到要求的尺寸 B2.5镀前消除应力
GB12333g0 试样应按本标准第8章的要求进行镀前热处理,以消除磨削应力
消除应力时的最高温度,应比试 样材料的回火温度低10一20c,同时要避开材料回火脆性区,以保证清除应力后的试样硬度不变 B2.6电镀 试样应按替代试样的要求进行镀前准备、电镀和镀后处理
V形缺口处镀层的厚度为12一18wm 镀层应符合本标准第9章中规定的质量要求,镀层应一次完成,不允许重复电镀
电镀后试样应按本斥 准第10章的规定于3h内尽快进行消除氢脆的热处理 B延迟破坏试验 延迟破坏试验用的持久试验机,其力值误差应小于1%,不同心度小于15% B3.1 B2试样进行延迟破坏试验时所承受的载荷等于未镀覆试祥缺口截面积乘以其缺口试样抗张强度 的75%,加载后记录断裂时间
未镀覆试样的缺口抗拉强度应是3一5个未镀覆试样的平均值
如果 5个试样的缺口抗拉强度值相差太大,应再取3~5个试样重新试验
B4试验结果评定 B4.1鉴定镀覆工艺的氢脆性时用六根平行试样进行延迟破坏试验;鉴定产品氢脆性时用二根,在规 定的(见B3.2)静载荷下200h不断裂,则认为该工艺或该产品的氢脆性合格.如果有一个试样断裂时间 少于200h则认为氢脆性不合格
B4.2在分析断裂原因时,应考虑基材含氢量以及各加工工艺,如热处理等,增氢因素的影响
附加说明: 本标准由机械电子工业部提出
本标准由金属与非金属覆盖层标准化技术委员会归口
本标准由机械电子工业部武汉材料保护研究所负责起草 本标准主要起草人陶维正、谢锐兵