GB/T37431-2019
风力发电机组风轮叶片红外热像检测指南
Windturbines—Guideforinfrareddetectionofrotorblade
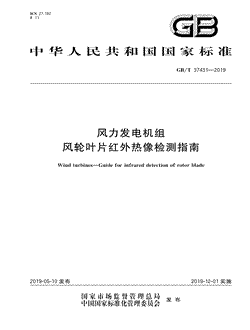
- 中国标准分类号(CCS)F11
- 国际标准分类号(ICS)27.180
- 实施日期2019-12-01
- 文件格式PDF
- 文本页数24页
- 文件大小6.93M
以图片形式预览风力发电机组风轮叶片红外热像检测指南
风力发电机组风轮叶片红外热像检测指南
国家标准 GB/T37431一2019 风力发电机组 风轮叶片红外热像检测指南 windturbines一Guideforinfrareddetectionofrotorlade 2019-05-10发布 2019-12-01实施 国家市场监督管理总局 发布 币国国家标准化管理委员会国家标准
GB/37431?2019 ? ? Χ 2 淶? ? -? ??? ?? ? ?????? ?A??) ?B??)?? ?c(???? ?D(??)±??? 12 ?E(??)?伤? 18 ?F(??)?ο? 19 ?G(??)?? 20 ο 2
GB/37431一2019 前 言 本标准按照GB/T1.1一2009给出的规则起草
本标准由机械工业联合会提出
本标准由全国风力机械标准化技术委员会(SAC/Tc50)归口
本标准起草单位:北京维泰凯信新技术有限公司、首都师范大学、北京金风科创风电设备有限公司、 中材科技风电叶片股份有限公司杭州派肯科技有限公司、农业机械工业协会、中科宇能科技发展 有限公司、南京诺威尔光电系统有限公司、重庆师范大学、华电电力科学研究院、龙源(北京)风电工程技 术有限公司
本标准主要起草人:李晓丽、陶宁、张浩军、高克强、王迅、金万平、庄岳兴、张淑丽、陈力、曾智、陈淳、 冯立春、徐宇何毅、雷阳、肖剑、柴海棣
GB/37431一2019 风力发电机组 风轮叶片红外热像检测指南 范围 本标准规定了风力发电机组风轮叶片红外热像检测的一般原则与方法 本标准适用于风轮叶片生产过程、交付、局部损伤修复、运行维护等阶段的检测
本标准不建立评价判据,缺陷的定义和具体判据由制造商用户和检测方协商确定
本标准没有完全给出进行检测时的安全要求,使用本标准的各方有义务在检测前建立适当的安全 和健康准则
规范性引用文件 下列文件对于本文件的应用是必不可少的
凡是注日期的引用文件,仅注日期的版本适用于本文 件
凡是不注日期的引用文件,其最新版本(包括所有的修改单)适用于本文件
GB/T2900.53电工术语风力发电机组 GB/T3961纤维增强塑料术语 GB/T5616无损检测应用导则 GB7247.1激光产品的安全第1部分;设备分类、要求 GB/T7247.14激光产品的安全第14部分:用户指南 GB/T9445无损检测人员资格鉴定与认证 GB/T12604.9无损检测术语红外检测 GB19517国家电气设备安全技术规范 GB/T20737无损检测通用术语和定义 GB/T266432011无损检测闪光灯激励红外热像法导则 GB/T28s43.3一2015无损检测闪光灯激励红外热像法第3部分试块 GB/T31768.2一2015无损检测闪光灯激励红外热像法第2部分;检测规范 GB/T31768.4无损检测闪光灯激励红外热像法第4部分;检测系统 G;JB5304军用复合材料术语 术语和定义 GB/T2900.53,GB/T3961,GB/T5616,GB/T12604.9,GB/T20737和G;JB5304界定的术语和 定义适用于本文件
技术概述 4.1红外热像检测 红外热像检测通过对被测物体进行加热,其内部的缺陷、损伤和结构的热特性差异会影响对应表面
GB/T37431一2019 区域的升温或冷却过程,热像仪探测并记录与之相应的表面温场变化,经过数据分析和处理可获得被测 物体内部的缺陷、损伤及其结构异常的信息
红外热像检测原理示意图见图1. 热激励源 加热形式 风轮叶片 红外热像仪 控制和 处理系统 图1红外热像检测原理示意图 4.2热激励方法 对热激励方法的选择应满足7.2的要求,例如,闪光灯,激光、卤素灯及太阳能辐射等
5 -般要求 5.1 人员 5.1.1应熟悉红外的基础知识及红外热像检测的相关知识,能够正确操作红外检测系统
5.1.2应了解检测对象,即所检测叶片的结构、相关制作工艺和检测要求
5.1.3检测人员应按GB/T9445的相关规定通过相应的资格鉴定与认证,或供需双方的规定
5.2检测系统 5.2.1基本要求 检测系统的功能、性能应满足第7章的相关要求
5.2.2非均匀性校正 热像仪在使用前,应按使用要求进行非均匀性校正,可根据需要进行平面视场校正;当使用替换镜 头、重新调焦时,应重新进行非均匀性校正;在改变温度范围或改变积分时间时,应根据设备制造商的要 求确定是否需要重新进行非均匀性校正
5.2.3校验 应定期或在需要时使用试块对检测系统进行检测能力和加热均匀性校验
5.3检测条件和环境 室内检测时,应尽量避免或减少检测区域周边环境对检测的影响,例如,其他热辐射源、环境温度 变化
外场检测时,根据实验要求,应增加必要的辅助设施或装置,还应尽量避免或减少温度、气流、日照、 降水及其他干扰的影响
GB/37431一2019 5.4安全性 5.4.1基本要求 检测人员应熟知现场作业的危险点及相关的控制措施,必要时,检测前应先建立适当的安全准则
应保证检测人员、设备、检测对象和环境的安全
5.4.2 人员安全 对应热激励装置应设置明显的安全警告标志;热激励装置宜配有隔离措施;在使用激光激励时,应 根据激光的安全等级制订相应的防护措施
5.4.3设备安全 设备安全主要包括 系统电气安全应符合GB19517及相关标准; -应确保检测系统在安全的条件和环境下使用; 应严格按照设备生产商的说明书操作使用设备 被检测叶片安全 5.4.4 应确保检测过程不对被检测叶片造成损伤 5.4.5环境 在易燃、易爆的环境中使用电力加热装置,应制订安全有效的防护措施 叶片缺陷类别 6.1常见缺陷 红外热像法适用于常见的叶片缺陷检测,例如分层,脱粘、,夹杂,缺胶、气泡、褶皱、裂纹、干纱等
叶 片结构示意图如图2所示,常见缺陷的类型,位置等信息示意如图3所示
一些缺陷的红外检测热图参 见附录A
前缘 腹板 后缘 图2叶片结构示意图
GB/T37431一2019 裂纹 气泡 褶皱 分层 缺胶 脱粘 注常见缺陷示意图对应位置见图2虚线所示区间
图3常见缺陷示意图 6.2缺陷的模拟和对比 6.2.1标准试块 应根据检测要求和GB/T26643.3一2015中5.1,5.2的要求,针对叶片关键部位或常见缺陷设计标 准试块,用于评价检测系统的设备状态或检测能力,也可用于检测参数调整和缺陷判定比对
6.2.2对比试块 6.2.2.1宜根据GB/T26643.3一2015中5.3的要求预先设计、制作实际检测用对比试块,材料、结构和 制作工艺宜与实际检测对象一致或相近,缺陷可以是人工设计模拟的,也可以是自然形成的
6.2.2.2应能确定对比试块缺陷的类型,大小,位置等信息,人工模拟缺陷还需描述模拟方法和工艺
6.2.2.3设计制作人工模拟缺陷时,应考虑检测对象真实缺陷的可能类型尺寸、位置和生成原因,能真 实模拟实际缺陷在热源加热后所产生的热响应特性
6.2.2.4设计多个人工缺陷时,两相邻缺陷边缘的间距应大于两者中较大缺陷的直径;缺陷边缘距试块 边缘的距离应大于缺陷的直径(边缘缺陷除外)
6.2.2.5在预制缺陷中应包括要求检出的特定深度下的最小缺陷
亦可对相同材料和制作工艺的平板背面加工平底孔的方法制造试块
平底孔可被认为是最容 6.2.2.6 易检测的缺陷,系统对实际缺陷的检测能力一般低于对平底孔缺陷的检测能力
检测系统 7.1概述 应具有热激励源、热像仪、控制和处理系统,热激励源可以是人工热源也可以是自然热源
闪光灯 激励红外热像检测系统应满足GB/T31768.4的相关规定
检测系统结构框架示意图见图4 7.2热激励源 7.2.1基本要求 应满足检测对于加热均匀性、加热能量、加热效率的要求,宜适用于外场检测
7.2.2闪光灯激励 闪光灯激励红外检测方法适用于检测近表面缺陷和定量测量
通常单次加热能量不小于5k,脉
GB/37431一2019 冲宽度不大于20ms
闪光灯激励红外热像检测实例参见附录B 热激励源 热像仪交互功能模块 检测系统 热像仪 触发加热功能模块 控制和处理系统 图像显示功能模块 数据处理功能模块 图4检测系统结构框架示意图 7.2.3激光激励 激光激励能获得较高的能量密度,对于检测深层缺陷较有优势
通常激光能量密度不宜小于 800w/m*,光强非均匀度不大于50%
使用激光加热应符合GB7247.1和GB/T7247.14的相关要 求,并制订安全管理措施
激光激励红外热像检测实例参见附录c
卤素灯激励 7.2.4 卤素灯成本较低,适用性强,波长在可见光到近红外波段,较适合于大面积检测
通过设计和控制 加热的时长来控制加热量
通常功率不小于1000w
卤素灯激励红外热像检测实例参见附录D. 7.2.5太阳辐射激励 利用太阳光的能量对叶片进行整体加热,其优势在于具有很强的加热能力,但受限于气象条件、周 边环境及时段、叶片朝向等因素
太阳辐射激励检测实例参见附录E
7.3热像仪 性能指标应能满足检测要求.例如工作波段、鹌频、嗓声等效温度差,空间分辨力、镜头视场等
通 常应满足如下要求 -工作波段在中红外到远红外区域; -图像分辨率满足检测要求,热像仪探测器像元数不宜小于320×240; -噪声等效温度差不大于100mK; 最大帧频宜不低于25Hz
7.4控制和处理系统 控制和处理系统的功能要求主要包括 应具备对人工热源控制功能,例如,开关、调制 应能控制加热与采集的时序关系; 应能显示热像仪采集到的图像序列,并能存取、回放 宜具有的功能;能观察任意像素点的温度-时间曲线,能够对原始的热图序列进行相关的数据 处理运算,例如,均值滤波、减背景、降噪、微分处理等 宜具有图像拼接功能"
GB/T37431一2019 8 红外检测的一般程序 8.1制定检测方案 8.1.1采用红外热像检测方法能否检出缺陷主要取决于缺陷的大小、所在深度及其热物理属性与周围 的本体材料的差异程度
缺陷越大,越接近于物体表面,缺陷与本体材料的热物理属性区别越明显,就 越容易检测到
一般来说,缺陷的宽深比小于1,不建议采用本方法
应根据检测对空间分辨力及视场的需求选择热像仪及镜头并确定工作距离
其组合应满足需 8.1.2 检测到的最小缺陷在探测器上成像至少覆盖3×3个相邻像素
应根据检测需要和现场条件,以及各种热激励方式的加热特点制订方案
浅层缺陷可尝试多种 8.1.3 加热方式,深层缺陷对加热能量要求大,宜使用卤素灯或激光进行长时间加热,而更深或大面积的检测 可利用太阳能辐射加热 8.1.4应根据被测物体表面红外发射率、可见光吸收率、表面光洁度、红外光谱特性等表面状况进行 必要的表面处理
例如,对被检物表面进行涂漆或覆膜等处理
8.1.5当待检测区域面积大于系统单次检测视场覆盖面积时,应进行分区检测,并作标识,用于对检测 结果的拼接处理及确定缺陷的相对位置
8.1.6应根据材料的热特性,缺陷的深度,处理系统的计算能力以及存储介质的大小设置采集频率和 采集时间
通常浅层缺陷宜采用较高帧频和较短的采集时间,反之则采用较低帧频和较长采集时间
应考虑数据量对处理速度和存储的影响
8.1.7应考虑热像仪动态范围并确保不对被检物造成损伤选择加热能量
如发现有图像饱和现象,可 采取降低热流密度、减少加热时间、减少热像仪积分时间等措施
但应注意,减少热像仪积分时间会降 低温度灵敏度;在不确定对被检物是否安全时,应采用试块进行检验 8.1.8在检测条件复杂的情况下,可准备备选方案,以确保现场检测顺利实施
在条件允许的情况下 应利用试块对检测方案充分细化
检测方案参考要素参见附录F 8.2检测准备 8.2.1根据6.2准备试块,用于系统调试和校验及确定检测参数等工作
8.2.2对检测系统正确连接,并做必要调试,确定其工作正常
如果需要外场测试,在系统运输前后均 需确定其可正常工作
8.2.3清洁被检物表面,必要时做表面处理或分区处理
对待检测区域作必要的记录,比如被检物名 称、编号、材料、结构、检测部位、表面状况、分区情况等
对于表面难清洁掉的痕迹应予记录,以避免在 后期分析结果时发生误判 8.2.4根据检测条件准备必要的辅助设施,如支架,延长线缆、移动电源等
采取措施减少环境热辐射干扰及对流影响
必要时记录温度、,风速等情况
8.2.5 8.2.6制订检测程序,草拟记录表格、作业文件等
8.3检测实施 8.3.1按照检测方案、检测程序、检测作业文件实施检测 8.3.2根据检测要求确定一次成像面积大小,设置检测参数
8.3.3热像仪视场对准被检测叶片的待检测表面,宜垂直
8.3.4在数据采集的过程中,被检叶片与热像仪应保持相对静止 8.3.5采集结束后存储数据并记录对应检测参数,文件名称和存储位置
8.3.6分区检测时,为了避免漏检和利于后续数据处理,相邻区域应有一定的重叠
为了减少热影响,
GB/37431一2019 建议隔区检测
8.4数据分析和处理 8.4.1常用方法 可根据检测目的和检测要求使用图像分析、曲线分析、比对等方法或多种方法的组合来处理数据 8.4.2图像分析 为了完整的判定检测结果,应利用原始热图、一阶或二阶微分热图序列做数据分析
通过逐播放 和连续播放热图序列和微分热图序列,查找热异常区域
通过对热异常区域对比度、大小、形状、位置及 出现时间的分析,判读可疑缺陷
原始热图和微分热图的处理宜采用GB/T26643一2011第8章和GB/T31768.,2一2015第6章的 方法
8.4.3 曲线分析 利用温度-时间温差-时间对数曲线、微分曲线可获取缺陷深度、缺陷类型等信息,闪光灯微励时宜 采用GB/T26643一201第8章和GBT317682一2015第6章的方法
8.4.4 比对 试块比对
根据不同厂家、不同叶片、不同位置,应提供典型缺陷或结构的对比试块,以此做参 8.4.4.1 照来分析检测结果 8.4.4.2档案比对
与此前同一叶片相同位置在类似检测条件下的结果进行比较,以获取缺陷的存在 及扩展信息
8.4.43同型比对
对同一批次、同一工艺、同一位置上的叶片做比较,分析检测结果
8.5检测报告 应包括检测地点、检测时间、检测人员、被检叶片描述、检测目的与要求、检测设备、检测参数,环境 条件、数据分析、检测结论
宜辅以照片、热图、曲线,对热异常区域做出标记,并标明尺寸、位置、深 度等
9 出厂检测 出厂检测要求示例参见附录G
GB/T37431?2019 ? A ??) ?????? ???????A.1?A.6 ?е ?е ?A.1??? ? ? ?2 ?A.2?? ?? b ?A.3??
GB/37431一2019 热异常 图A.4原位检测 发白 粘接宽度 粘接宽度测量 发白形状及大小 图A.5定量测量 粘按区 图A.6粘接区检测热图拼接
GB/T37431一2019 B 附 录 资料性附录 闪光灯激励红外热像检测实例 B.1脱粘缺陷检测示例 两个厚度为2mm的玻纤/环氧树脂复合材料板,中间由粘接胶粘接,其热图如图B.la)所示,粘接 区中间亮的区域为胶中的气泡
在粘接处局部破坏其粘接力,造成局部脱粘,再次用红外热像法检测
其热图结果如图B.1b)所示
测试前在检测面喷涂了水溶性黑漆
检测参数:采集频率60Hz,采集时 间15s,闪光灯激励能量9.6kJ,脉冲宽度2ms
气池 气池泡 脱粘前 脱粘后 a b 闪光灯激励红外热图 图B.1 B.2夹杂缺陷检测示例 ,包含有四种夹杂,分别是脱膜布、密封胶 火杂试块材料为玻纤/环氧树脂复合材料,总厚2.5 mm, 带、薄膜和纸
测试前在检测面喷涂了水溶性黑漆
用闪光灯激励红外热像法测试,得到结果如图B.2 所示
检测参数:采集频率60HHz,采集时间15s,闪光灯激励能量9.6kJ,脉冲宽度21 mS
脱膜布 薄胶 密封胶带 图B.2夹杂试块闪光灯激励红外热图 0
GB/37431一2019 录 附 C 资料性附录 激光激励红外热像检测实例 模拟缺陷试块描述见E.2
激光激励红外热像检测实例见图C.1
粘接区 试块可见光照片 b)粘接情况示意图 大功率激光激励检测热图 图C.117mm厚梁与腹板粘接试块检测示例 检测中选用制冷型热像仪室温下热像仪的温度分辨率优于20mK,采集时间180s,采集频率 10Hz
激光器功率为200w,发散角25",加热时间5s 11
GB/T37431?2019 ? D ??) ±??? D.1???? ?????/??,??,????? ??2mm3mm4nmm,???????D.1?汳??? ?D.2? ??? 2mm -o16 20 ??? 3mm 20 16 -12 63 -o6?5 ??? 4mm -12 16 -8 020 250. ?D.1????? ?D.2???鱳?? 12
GB/37431一2019 红外热像检测处理后的结果如图D.3所示
本结果采用卤素灯激励,功率2×1000w,加热时间 10s
选用非制冷型热像仪,室温下热像仪的温度分辨率优于50mK,采集频率20Hz,采集时间40s
b)21s 13.8,时 31.2,时 s时 图D.3分层模拟试块不同时刻红外热图 由于三排缺陷的深度不同,在热图序列中三排缺陷将顺次显现
红外热像检测中常用所能检测的 缺陷的宽深比代表系统的检测能力,图D.3的检测结果显示,本系统可检测到深度分别在2n mm 3mm、4mm处最小的平底孔,直径分别为2mm、3mm、4mm,即所能检测到的宽深比优于2
其他 叶片类似材料可以参考
D.2缺胶模拟试块检测示例 图D.4所示是玻纤/环氧树脂复合材料梁与腹板粘接缺胶模拟试块的可见光照片,为了消除材料红 外半透明的影响,测试前在检测面喷涂了水溶性黑漆
该试块是利用叶片中使用的梁与腹板材料,模拟 局部缺胶制作而成,粘接面距检测面厚度为17 mm
检测面 检测面背面 a b 图D.4缺胶模拟试块可见光照片 13
GB/T37431一2019 粘接区 图D.5缺胶模拟试块粘接区域示意图 梁与腹板粘接面的粘接情况示意图如图D.5所示
红外热像检测结果如图D,6所示
本结果采用卤素灯激励,功率2×1000w,加热时间30s 选 用非制冷型热像仪,室温下热像仪的温度分辨率优于50mK,采集频率5Hz,采集时间300s
缺胶 粘接区 图D.6缺胶模拟试块卤素灯激励红外热像检测热图 D.3干纱缺陷检测示例 玻纤/环氧树脂复合材料制作而成的干纱模拟件厚10mm,干纱主要分布于试块左右两侧局部,测 试前在检测面喷涂水溶性黑漆,可见光照片如图D.7a)所示
使用卤素灯激励红外热像法检洲,检渊参数为;加热功率2X100w,加热时间20s;呆用非制冷 热像仪,室温下热像仪的温度分辨率优于50mK,采集频率10Hz,采集时间100s
检测后得到的热图 如图D.7b)所示 14
GB/37431一2019 干纱 检测前可见光照片 闪光灯激励红外检测热图 图D.7干纱试块检测示例 D.4芯材间隙试块检测示例 通常芯材拼接处的间隙过大是不准许的,但不同的生产企业或用户对芯材间隙的管理不同
如 图D.8所示为试块可见光照片,芯材左右拼接处的宽度分别为6mm和5mm
在试块表面喷涂水溶 性黑漆后进行测试,得到红外测试热图,如图D.9所示
检测参数为;加热功率2×1000w,加热时间 5s,采用非制冷热像仪,室温下热像仪的温度分辨率优于50mK,采集频率50Hz,采集时间20s 图D.8芯材间隙试块可见光照片 15
GB/T37431一2019 5哪服 6mm间 图D.9芯材间隙试块卤素灯激励红外检测热图 D.5碳纤维分层模拟试块检测示例 利用叶片中所使用的碳纤维梁的一段材料,制作平底孔分层模拟缺陷,可见光照片如图D.10所示 试块材料中的纤维铺层为单向
孔的直径均为20mm,8个孔距离检测面的深度分别是1mm、.2mm、 3mm、4mm、5mm1、6mm、7mm、8mm
缺陷示意图如图E.1l所示
a 检测面的可见光照片 D 检测面背面的可见光照片 图D.10碳纤维分层模拟试块 16
GB/37431一2019 -8X20 7mm 5mm 3mm 1mm 8mm 6mm 4mm 2mm 340 图D.11碳纤维分层模拟试块设计示意图 利用卤素灯持续加热50s,在加热的同时用热像仪采集升温过程
加热功率2×1000W,采集频 率为5Hz,采集时间200s
对所采集的数据进行处理,得到图D.12所示热图结果
由于纤维单向铺 层导致的材料各向异性使圆孔沿纤维方向被拉长
图D.12碳纤维分层模拟试块卤素灯激励红外检测热图 17
GB/T37431一2019 附录 E 资料性附录 太阳辐射激励检测实例 利用太阳能辐射激励,连续采集太阳初升或落下的一段时间的温场变化,然后进行数据处理得到叶 片内部信息
图E.la)为检测叶片的可见光照片,检测区域如虚线矩形所示,位于叶片最大弦长处;图E,1b)是利 用太阳辐射加热后的降温阶段数据,经过处理后得到的热图
热图中可见梁与两腹板的粘接区,同时发 现一处热异常区域,由于未经解剖验证或比对分析,在此不对缺陷类型进行判定
检测中所用热像仪的 视场角为30×23",检测距离8.5m 热异常 桑与腹板 粘接区 叶片检测部位可见光照片 可见光照片对应部位检测热图 b 图E.1实际叶片局部检测热图 可以通过该视场一个像元所代表的尺寸计算得到梁与腹板粘接胶的宽度
18
GB/37431一2019 附录F 资料性附录) 检测方案参考要素 F.1背景描述 F.1.1被检叶片描述 基本信息应包括 -型号、编号; 状态,如出厂、待装、运行、停机维修等; 材料、大小、结构、工艺 表面状况
F.1.2检测现场描述 基本信息应包括 -测试地点; 周边环境和条件,例如,地形、气象条件、供电等 F:.2检测目的 检测目的是方案制订的出发点
应充分了解需求,包括缺陷类型,缺陷所处深度和位置,允许最小 缺陷的尺寸等
F.3制定方案 参照8.1执行
F.4实施计划 实施计划至少应包括下列信息 检测时间; 检测人员; 设备准备、参数设置; 数据处理方法 19
GB/T37431一2019 附录 G 资料性附录 出厂检测要求示例 出厂检测要求示例见表G.1 表G.1x××叶片厂出厂检测要求示例 序号 类型 检验项目 分级 检验标准 A 厚度低于2mm时,累计长度超过500mtm A 厚度超过10mm时,累计长度超过500mm 粘接胶的厚度 腹板,前缘、后缘 B 厚度低于2mm时,连续长度超过50mm 厚度超过10mm时,连续长度超过50mm 低于标准宽度20%,累计长度超过200mm A 粘 A 低于标准宽度10%,累计长度超过300mm 粘接胶的宽度 面 腹板、前缘、后缘) 低于标准宽度20%,连续长度超过50mnm 低于标准宽度10%,连续长度超过100mm A 粘接面脱粘 不准许 粘接胶欠固化 B 欠固化区域大于25mm×100mm 胶气泡直径大于5mm,且1m以内不准许有一个以上的气泡 胶气泡 不准许存在弦向褶皱 帮皱 褶皱高宽比大于0.1,轴向 A A 褶皱与展向夹角大于30" 丰 干纱 不准许有干纱 复 复合层分层 B 大于25mm×25mm 合 B 复合层气泡 直径大于15mm 层 芯材间隙 间隙大于3mm 所有的金属异物应清除 A 夹杂 B 非金属异物直径应小于25 5mm 20
GB/37431一2019 献 参 考文 GB/T19870一2015工业检测型红外热像仪 [[2]GB/T25383一2010风力发电机组风轮叶片 [3] GB/T25384一2010风力发电机组风轮叶片全尺寸结构试验 [4]GB/T28706一2012无损检测机械及电气设备红外热成像检测方法 [5]GB/T29183一2012红外热像法检测建设工程现场通用技术要求 [] DL/T664一2008带电设备红外诊断应用规范 [7]DL/T796一2012风力发电场安全规程 [[8]DL./T907一2004热力设备红外检测导则 [[9]JG/T2692010建筑红外热像检测要求 [[10]JGJ/T277一2012红外热像法检测建筑外墙饰面粘结质量技术规程 MH/T3022一2011航空器复合材料构件红外热像检测 12]IEC/TS61400-23WindturbinesPart23:Full-scalestructuralte ofrotorblades esting"