GB/T34019-2017
超高压容器
Ultra-highpressurevessels
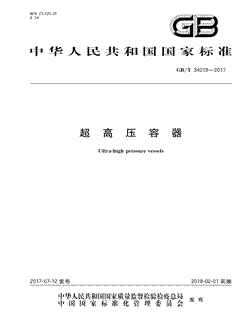
- 中国标准分类号(CCS)J74
- 国际标准分类号(ICS)23.020.30
- 实施日期2018-02-01
- 文件格式PDF
- 文本页数87页
- 文件大小7.75M
以图片形式预览超高压容器
超高压容器
国家标准 GB/T34019一2017 超 压 高 器 容 Utra-highpressurevesels 2017-07-12发布 2018-02-01实施 国家质量监督检验检疫总局 发布 国家标准化管理委员会国家标准
GB/34019一2017 前 言 本标准按照GB/T1.1一2009给出的规则起草
请注意本文件的某些内容可能涉及专利
本文件的发布机构不承担识别这些专利的责任
本标准由全国锅炉压力容器标准化技术委员会(SAC/TC262)提出并归口
本标准起草单位:特种设备检测研究院、浙江大学、锅容标(北京)技术服务中心有限公司、 石化工程建设有限公司,浙江省特种设备检验研究院、内蒙古北方重工业集团有限公司、江苏省特种设 备安全监督检验研究院、中原特钢股份有限公司、台州市特种设备监督检验中心 本标准主要起草人;寿比南、郑津洋、陈志伟、张勇、杨国义、李涛、丁利伟、郭伟灿、许锐冰、马歆、 范志霞、李隆骏、许林滔
GB/T34019一2017 引 言 本标准是全国锅炉压力容器标准化技术委员会(以下简称“委员会”)负责制定和归口的压力容器技 术标准之一,用以规范在境内建造或使用的超高压容器设计,制造、检验和验收的相关技术要求
本标准的技术条款包括了超高压容器建造过程(即指设计、制造、检验和验收工作)中应遵循的要 求
由于本标准没有必要、也不可能囊括适用范围内超高压容器建造中的所有技术细节,因此,在满足 法规所规定的基本安全要求的前提下,不应禁止本标准中没有特别提及的技术内容
本标准不能作为 具体超高压容器建造的技术手册,亦不能替代培训、工程经验和工程评价
对于未经委员会书面授权或认可的其他机构对标准的宣贯或解释所产生的理解歧义和由此产生的 任何后果,本委员会将不承担任何责任
对于标准技术条款的询问应以书面形式向委员会秘书处提交,并有义务提供可能需要的资料
与 标准条款没有直接关系或不能被理解的询问将视为技术咨询的范略,委员会有权拒绝回答
参见附 录A
GB/34019一2017 超 高 压 容 器 范围 1.1本标准规定了非焊接单层超高压容器(以下简称容器)材料,设计、制造、检验和验收等方面的 要求
1.2本标准适用于同时满足以下条件的容器 设计压力大于或等于100MPa; a b) 设计温度范围:一40C一400C 1.3下列容器不在本标准的适用范围内 直接火焰加热的容器; a b 核能装置中存在中子辐射损伤失效风险的容器; 旋转或往复运动机械设备中自成整体或作为部件的受压器室(如泵壳、压缩机外壳、涡轮机外 壳、液压缸等; 移动式容器; d 军事用途容器
1.4容器界定范围 1.4.1容器与外部管道连接 螺纹连接的第一个螺纹接头端面 aa 法兰连接的第一个法兰密封面 b 专用连接件或者管件连接的第一个密封面 c 1.4.2 容器开孔部分的承压盖及其紧固件 1.4.3 容器的超压泄放装置(见附录B)
规范性引用文件 下列文件对于本文件的应用是必不可少的
凡是注日期的引用文件,仅注日期的版本适用于本文 件
凡是不注日期的引用文件,其最新版本(包括所有的修改单)适用于本文件
GB/T150(所有部分压力容器 GB/T222钢的成品化学成分允许偏差 GB/T223适用部分钢铁及合金化学分析方法 GB/T226钢的低倍组织及缺陷酸蚀检验法 拉伸试验第1部分;室温试验方法 金属材料 GB/T228.1 GB 228.2金属材料拉伸试验第2部分;高温试验方法 GB/T229金属材料夏比摆锤冲击试验方法 GB/T231.1金属材料布民硬度试验第1部分;试验方法 GB/T1979结构钢低倍组织缺陷评级图 GB/T4336碳素钢和中低合金钢多元素含量的测定火花放电原子发射光谱法(常规法 GB/T6394金属平均晶粒度测定法
GB/T34019一2017 GB/T10561钢中非金属夹杂物含量的测定标准评级图显微检验法 GB/T20066钢和铁化学成分测定用试样的取样和制样方法 GB/T20123钢铁总碳硫含量的测定高频感应炉燃烧后红外吸收法(常规方法) 金属材料 GB/T21143 准静态断裂韧度的统一试验方法 GB/T26929压力容器术语 NB/T47013.32015承压设备无损检测第3部分;超声检测 NB/T47013.4承压设备无损检测第4部分;磁粉检测 NB/T47013.5 承压设备无损检测第5部分渗透检测 NB/T47013.6承压设备无损检测第6部分:涡流检测 JB/T4711压力容器涂敷与运输包装 JB4732(2005年确认钢制压力容器 分析设计标准 NB/T47008承压设备用碳素饷和合金钢锻件 TsG21固定式压力容器安全技术监察规程 3 术语和定义、符号 3.1术语和定义 GB/T150,GB/T26929和JB4732(2005年确认)界定的以及下列术语和定义适用于本文件
3.1.1 压力presure 垂直作用在容器单位表面积上的力
在本标准中,除注明者外,压力均指表压力
3.1.2 设计压力designpressure 设定的容器顶部的最高压力,与相应的设计温度一起作为容器的基本设计载荷条件,其值不低于工 作压力
3.1.3 工作压力operating pressure 在正常工作情况下,容器顶部可能达到的最高压力
3.1.4 试验压力testpressure 进行耐压试验或泄漏试验时,容器顶部的压力
3.1.5 设计温度designtemperature 容器在正常工作情况下,设定的元件的金属温度(沿元件金属截面的温度平均值)
设计温度和设 计压力一起作为设计载荷条件
3.1.6 试验温度 testtemperature 进行耐压试验或泄漏试验时,容器壳体的金属温度
3.1.7 爆破压力burst pressre 容器在内压作用下发生爆破前能够承受的最大压力
GB/34019一2017 3.1.8 自增强autofrettage 对容器施加内压,使其自内壁起一定厚度范围内产生塑性变形,内压卸除后产生对疲劳强度有利的 残余应力的方法
3.1.9 热应力 thermalstreSS 因温度变化引起的自由膨胀或者收缩受到约束,在容器内所引起的应力
3.1.10 失效模式failuremde 容器丧失其规定功能或者危及安全的事件及其本质原因
3.1.11 脆性断裂britlefracture 容器未经明显的塑性变形而发生的断裂
3.1.12 塑性垮塌plastieeollapse 在单调加载条件下容器因过量总体塑性变形而不能继续承载导致的破坏 3.1.13 局部过度应变excessiveloealstrains 容器结构不连续处因材料延性耗尽而产生的裂纹或者撕裂
3.1.14 疲劳fatigue 循环载荷作用下,容器在某点或者某些点产生局部的永久性损伤,并在一定载荷循环次数后形成裂 纹或者裂纹进一步扩展至完全断裂
3.1.15 棘轮rteheting 容器同时承受恒定载荷和循环载荷作用,容器产生逐次递增的塑性变形累积现象
3.1.16 泄漏leakage 容器本体或者连接件失去密封功能
3.2符号 下列符号适用于本文件
容器的设计压力,MPa; P -由容器内装介质重力引起的压力载荷,MPa; M 容器及相关附件的自重载荷,MPa; 耐压试验压力最低值,MPa P 试验温度下材料的屈服强度,MPa; R 0, R -设计温度下材料的屈服强度,MPa; K 容器外径内径之比
GB/T34019一2017 通用要求 4.1通则 本标准适用范围内容器的材料,设计,制造、检验和验收除应符合本标准规定外,还必须遵守国 4.1.1 家颁布的相关法律、法规和安全技术规范
容器的设计,制造单位应建立健全的质量管理体系并有效运行
4.1.2 4.1.3《固定式压力容器安全技术监察规程》管辖范围内的容器设计和制造应接受特种设备安全监察 机构的监察
4.2资质与职责 4.2.1资质 《固定式压力容器安全技术监察规程》管辖范围内的容器建造单位应具有相应的特种设备许可资质 证书 4.2.2职责 4.2.2.1用户或设计委托方的职责 容器的用户或设计委托方应当以正式书面形式向设计单位提出容器设计条件,其中应至少包含以 下内容 a 容器设计所依据的主要标准和规范 操作参数(包括工作压力、工作温度范围、接管载荷等) b 容器使用地及其自然条件(包括环境温度,抗震设防烈度等): c 介质组分和特性; d 预期使用年限和循环使用次数; 儿何参数; 设计需要的其他必要条件
g 4.2.2.2设计单位的职责 设计单位应对设计文件的正确性和完整性负责; a b 设计单位应根据风险评估报告确定设计的输人条件及制造要求,向用户出具的风险评估报告 应符合附录C的要求; 容器的设计文件至少应包括风险评估报告、强度计算书,设计图样,制造技术要求,必要时还应 当包括安装与使用维修说明; d 设计单位应在容器设计使用年限内保存全部容器设计文件
4.2.2.3制造单位的职责 制造单位应按照设计文件的要求进行制造,如需要对原设计进行修改,应当取得原设计单位同 意修改的书面文件,并且对改动部位做出详细记载
b 制造单位应根据用户和设计文件的要求,在容器制造前制定完善的质量计划,其内容至少应包
GB/34019一2017 括容器或元件的制造工艺控制点、检验项目和合格指标
制造单位的检查部门在容器制造过程中和完工后,应按本标准、,图样规定和质量计划的规定对 容器进行各项检验和试验,出具相应报告,并对报告的正确性和完整性负责
制造单位在检验合格后,出具产品质量合格证明
制造单位对其制造的容器产品应在容器设计使用年限内至少保存下列技术文件备查 质量计划 制造工艺图或制造工艺卡; 22 33 产品质量证明文件; 容器的热处理工艺文件及热处理记录(时间-温度关系曲线); 标准中允许制造单位选择的检验、试验项目记录; 5 容器制造过程中及完工后的检查、检验,试验记录; 6 容器的原设计图和竣工图
fD 制造单位对特殊制造工艺应进行工艺验证并保留工艺验证记录,如热处理、自增强处理、厚壁 圆筒无损检测等
4.2.2.4 检验机构的职责 对《固定式压力容器安全技术监察规程》管辖范围内的容器实施监督检验的机构及其监检员,在监 检工作中应当按照该规程的规定履行相应的工作职责;对出具的检验报告的完整性和正确性负责
4.3设计一般要求 4.3.1概述 容器设计单位(设计人员)应严格依据用户或设计委托方所提供的容器设计条件制定风险评估报告 并进行设计
4.3.2载荷 容器设计时,应考虑如下载荷: 在相应温度下的内压; a b 容器自重(包括内件等),以及正常工作条件下或耐压试验状态下内装介质的重力载荷 由温度梯度或热膨胀量不同引起的作用力; c 附属设备及隔热材料,衬里等的重力载荷 d 连接管道和其他部件的作用力; e 冲击载荷,包括由压力急剧波动引起的冲击载荷和超压泄放装置动作时引起的反力等 f 4.3.3失效模式 4.3.3.1标准涵盖的失效模式 本标准针对容器的下列失效模式提出了相关的设计要求, 脆性断裂失效-按第5章选材并按6.5.5中断裂力学法对脆性断裂失效进行评定; aa 按6.2的规定对塑性垮塌失效进行评定 b 塑性垮塌失效 局部过度应变失效 -按6.3的规定对局部过度应变失效进行评定;
GB/T34019一2017 d 棘轮失效 按6.4的规定对由循环载荷引起的棘轮效应进行评定; 疲劳失效 按6.5的规定对由循环载荷引起的疲劳失效进行评定; e fD 泄漏失效 参照附录D的规定对泄漏失效进行结构设计,防止泄漏失效
4.3.3.2工程上应考虑的失效模式 除本标准所涵盖的失效模式外,设计人员在设计时还应充分考虑容器在运行过程中可能出现的其 他失效模式,如介质腐蚀、碱脆等
4.3.4安全系数 4.3.4.1爆破压力法的安全系数 容器的爆破安全系数,当按照材料的拉伸试验数据计算爆破压力时,应当取大于或等于2.2,对于超 高压水晶釜应当取大于或等于2.4;当按照材料扭转试验数据计算爆破压力时,应当取大于或等于2.2
4.3.4.2疲劳分析的安全系数 疲劳分析时,交变应力幅和循环次数的安全系数分别取2和15. 4.3.4.3螺柱(螺栓)的安全系数 设计温度下屈服强度安全系数应大于或者等于1.8
4.3.5载荷放大系数 当采用弹塑性分析法时,载荷放大系数应按表1确定 表1载荷放大系数 条 载 荷组 合 塑性垮塌失效评定 2.0(P+尸十M 设计工况 局部过度应变失效评定 1.42(P十P十M) fR 耐压试验工况 塑性垮塌失效评定 .5 -(P尸s+M LRa2 4.4耐压试验 4.4.1 般要求 4.4.1.1容器加工完毕后应进行耐压试验,耐压试验的要求和试验压力值应在图样上标明
4.4.1.2耐压试验应当制定严密的试验程序和要求,应满足7.7中关于耐压试验的规定
4.4.2试验压力 容器的耐压试验一般采用液压试验,试验压力最低值尸按式(l计算 R风.2 P下=1.12P R! p.3
GB/34019一2017 式中: p -容器的设计压力(对于在用容器可取工作压力),单位为兆帕(MPa). R 试验温度下材料的屈服强度,单位为兆帕(MPa); pn. R 设计温度下材料的屈服强度,单位为兆帕(MPa)
自增强容器免除耐压试验的特殊要求 4.4.3 若满足下列所有条件,则自增强容器可免作液压试验 自增强后,容器处于最终装配状态 a b)容器的封头、堵头、密封件在自增强作业过程中装配齐全 自增强压力大于或者等于耐压试验压力; c d自增强时,已按7.7检查合格
4.5安全附件和仪表 4.5.1安全附件 容器的超压泄放装置应符合附录B的规定
4.5.2仪表 4.5.2.1容器温度测量误差不应大于1%,严禁超温运行
4.5.2.2选用的压力表应与容器内的介质相适应,容器使用的压力表的精度不得低于1.6级;压力表盘 刻度极限值应当为工作压力的1.5倍2.0倍
4.5.2.3仪表的接管材料应使用与容器内介质相适应的高强度合金或不锈钢钢管
4.5.2.4压力表、热电偶、自动记录装置的仪器等应定期进行检验;不经检验或超过检验周期的不得 使用
5 材料 5.1总则 5.1.1本标准对容器受压元件所使用的钢锻件做出了相关规定
5.1.2容器受压元件用材料的技术要求,试验方法和检验规则应符合相应的国家标准、行业标准或有 关技术条件的规定,同时应满足本标准的要求
5.1.3容器用材料应附有材料质量证明书原件,材料质量证明书应由材料生产单位提供,并在指定部 位或其他明显部位做出清晰,牢固的标志,容器制造单位应按质量证明书对材料进行验收
5.1.4容器选材时应考虑容器的使用条件(如设计压力、设计温度、介质特性和操作特点等)、材料性能 力学性能、工艺性能、化学性能和物理性能、容器的制造工艺以及经济合理性 5.1.5容器受压元件应采用锻造或挤压方法成型,锻件应当保留有足够的加工余量
锻件锻造比应不 小于3,对于经电渣重熔精炼的钢锭,其锻造比可不小于2 5.1.6首次使用本标准受压元件用钢材的制造单位应按照《固定式压力容器安全技术监察规程》的相 关规定通过技术评审后,其材料方可投人使用
5.1.7使用本标准以外钢材制造容器受压元件,应按照《固定式压力容器安全技术监察规程》的规定通 过技术评审
GB/T34019一2017 5.2冶炼方法和化学成分 5.2.1冶炼方法 容器受压元件用钢应是采用电炉或转炉冶炼的镇静钢,并应经炉外精炼(含真空处理)或电渣重熔
5.2.2化学成分 容器受压元件用钢的化学成分(熔炼分析)应符合表2的规定
成品钢材的化学成分允许偏差应符 合GB/T222的规定,其中P+0.003%.s+0.02%. 表2受压元件用钢的化学成分 化学成分(质量分数)/% 牌 Mnm si C N Mo Cu 0.30- 0,20 0.10 0.50 2.50 0.40~ 0.10~ 35CrNi3MoVR <0.005<0.012 S0,.20 0.40 0.80 0.35 1.20 3.30 0.70 0.25 0.32 0.20 1.20 3.00 0.35 0.10~ 36CrNi3MoVR 0.37 0,005 0,012 0,20 3.50 0.25 0.42 0.80 1.50 0,.45 5.3锻件 5.3.1粗加工 锻件经消除应力退火处理后进行粗加工,其形状和尺寸应符合毛坯图样的要求
5.3.1.1 5.3.1.2锻件表面缺陷允许打磨,其打磨深度不得超过精加工余量的1/3,打磨后,其表面不允许有肉 眼可见的夹杂和裂纹等缺陷
5.3.1.3锻件粗加工后(最终性能热处理前)应逐件按NB/T47013.4的规定对外表面进行100%磁粉 检测,合格级别为I级
5.3.2热处理 锻件性能热处理为正火加痒火加回火,其中回火温度应不低于540c
5.3.2.1 5.3.2.2受压元件性能热处理后应按7.5进行100%的超声检测,合格级别为级
5.3.3标志 锻件供应方应在每个锻件上打印元件代号、炉号,链号和锻件号
5.4硬度 5.4.1锻件性能热处理后应进行硬度检测
锻件性能热处理后,对于筒形锻件应在锻件外壁上均布划出5个与锻件轴线相垂直的环线,在 5.4.2 每个环线上均布取4点,做硬度检查
硬度值应符合产品图样或标准的规定,环线间各点硬度最高值与 最低值差不应大于40HBw;同一环线上各点硬度最高值与最低值差不应大于20HBw
GB/34019一2017 5.5低倍组织 容器用锻件不允许存在裂纹、白点、气孔、夹渣等缺陷
一般疏松、中心疏松应不超过2.0级;锭型 偏析、点状偏析应不超过2.0级
5.6金相检查 5.6.1锻件性能热处理后,应按GB/T6394进行晶粒度检查,晶粒度应大于或等于6.0级
5.6.2锻件性能热处理后,应按GB/T10561进行非金属夹杂物检验
其A,B,C,D各类夹杂物的粗 系级别和细系级别应分别不大于2.0级,DS类夹杂物应不大于2.0级;A,B,C,D各类夹杂物的粗系级 别之和应不大于3.5级,A,B,C,D各类夹杂物的细系级别之和不大于3.5级 5.7性能试验 5.7.1锻件经性能热处理后,力学性能应符合表3的规定,高温下材料的最低强度值见表4
表3钢材的力学性能 力学性能 牌 断后伸长率断面收缩率冲击吸收能量(一40y 屈服强度 抗拉强度 侧向膨胀量 R./MPa A/% Z/% KV,/J LE/mm Rma/MPa 35CrNi3MoVR >96o 10701230 >16 >45 >47 >0,53 36CrNi3MoVR >895 0001150 >16 >45 >47 >0.53 表4钢材的高温力学性能 号 牌 强度指标/MPa 100C 150C 200C 250 300 350 400 R >1060 >1060 >1060 >1007 954 >901 >845 35CrN3MoVR >870 857 843 >799 720 >777 >758 R2 R >990 >990 >990 >950 >931 891 >838 36CrNi3MoVR R2 >814 >796 >783 >774 >761 >742 >714 5.7.2容器受压元件的锻件,应由锻件生产单位提供力学性能报告
报告中力学性能试验项目、数量 和方法应符合5.13的规定
5.7.3 当改变冶炼、锻造或者热处理工艺时,应当提供锻件的断裂韧性Kc和韧脆转变温度 FATT50)试验报告
5.7.3.1断裂韧性试验按GB/T21l43进行,其Ke应不小于130MPaVm
5.7.3.2韧脆转变温度试验按GB/T229进行,测试其50%的剪切断面率所表示的韧脆转变温度 FATT50)
5.8设计疲劳曲线 图1给出了本标准所列钢锻件的设计疲劳曲线,表5给出了用于精确内插值的设计疲劳曲线的 Sa值
GB/T34019一2017 0 1o 注:弹性模量尼=1.95×10MPa 0 10' 1o 10 10 允许循环次数N 图1温度不超过400C的本标准所列钢锻件的设计疲劳曲线 表5设计疲劳曲线的取值 N" lE1 2El 5E1 1E2 2E2 5E2 5.2E2 1E3 2E3 5E3 1E4 2E4 5E4 1E5 Sa/MPa 2353182013401094917 758 753 614 507 410 360 325 293 276 所刚的允许循环次数应按如下方法读出iE=1X10,姐52=5X10或.500. S 两列表值间的数值可按双对数图用如下公式进行插值;对S>S二 besL/s SS -( 式中s,S,S为应力幅值Sa;N,N,N为设计疲劳数据得到的相应循环数
5.9弹性模量 表6给出了本标准所列锻件的弹性模量
表6钢材弹性模量 在下列温度(/C)下的弹性模量/10MPa 钢 种 25 150 100 200 250 300 350 400 203 98 194 190 186 本标准所列锻件 206 200 180 10
GB/34019一2017 5.10线膨胀系数 表7给出了本标准所列锻件的平均线膨胀系数
表7钢材平均线膨胀系数 在下列温度(/")与20C之间的平均线膨胀系数[10-"mm/mm" 钢 种 100 150 200 250 300 350 400 本标准所列锻件 12.90 10,76 ll,53 1l.88 12.25 12.56 13,24 13.58 5.11无损检测 材料的无损检测应符合7.5的相关规定
5.12材料检验取样 5.12.1 化学成分试样 熔炼分析试样应取自每炉钢水或每包钢水
采用电渣重熔工艺时,化学成分成品分析试样应从每 个电渣锭(或重熔钢锭对应的一个锻件)进行取样分析
其中,取样方法应按GB/T20066的相关规定 进行
5.12.2力学性能试样 质量小于500kg,长度小于2m的锻件,按同一冶炼炉号,同一热处理炉号选一件取样;对于 质量大于500kg的锻件,应在每个锻件的冒口端取样; 力学性能试样取样位置和方向应符合NB/T47008的相关规定
b 组批原则 5.12.3 质量小于500kg、长度小于2m的锻件,按同一炉号,同一热处理制度为一批;质量大于500kg的 一支锻件为一批
5.12.4 金相试样 金相试验取样应符合以下规定 非金属夹杂物;从每个冶炼炉的毛坯中选取一个毛坯在冒口端取样; a b)晶粒度:;从每热处理炉中选取一个毛坯在冒口端取样
5.13检验方法 材料的检验项目取样数量、取样方法及试验方法见表8
11
GB/T34019一2017 表8检验项目,取样数量、取样方法及试验方法 序号 检验项目 取样数量 取样方法 试验方法 GB/T223 GBT20066 化学成分 1个/炉 GB/T4336 GB/T20123 NB/T47008 拉伸 1个/批 GB/T228. NB/T47008 GB/T229 冲击(侧向膨涨量LE) 3个/批 硬度 逐件 NB/T47008 GB/T231.1 GB/T226 低僧 1个/批 GB/T1979 GB/T6394 金相(晶粒度,非金属夹杂) 1个/批 NB/T47008 GB/T10561 断裂韧性K" 1组/批 GB/T21143 GB/T21143 韧脆转变温度(FATT50 1组/批 NB/T47008 GB/T229 高温拉伸 2个/批 NB/T47008 GB/T228.2 NB/T47013.3 NB/T47013.4 无损检测 逐件 10 NB/T47013.5 NB/T47o13.6 当冶炼、锻造或者热处理工艺改变时,需重新进行检验
5.14螺柱(含螺栓)和螺母用钢棒 螺柱(含螺栓)和螺母用钢棒材料一般选35CrNi3MoV或36CrNi3MoV,其主要技术要求按本章容 器本体材料的相关规定
设计 6 6.1总则 本章规定了容器的设计要求,涵盖了对容器塑性垮塌、局部过度应变、棘轮,疲劳和脆性断裂失效的 评定方法;按本章设计的容器同时还应符合4.3的相关要求
6.2塑性垮塌失效评定 6.2.1评定方法 本节给出了容器塑性垮塌失效的评定方法,分别采用爆破压力法或弹塑性分析法
6.2.2符号 下列符号适用于本节
A,Bc -用于拟合材料切应力-应变曲线所得的常数; 容器外径与内径之比; P 爆破压力,MPa; 12
GB/34019一2017 R -材料在设计温度下的抗拉强度,MPa; Raa -材料在设计温度下的屈服强度,MPa; -切应力,MPa; -切应变; 容器内、外壁的切应变
Ui、U
6.2.3爆破压力法 容器圆筒的爆破压力应按材料拉伸试验数据或按材料扭转试验数据进行计算,安全系数应满足 4.3.4的相关要求 按材料拉伸试验数据计算,如式(1 a P=(R;十R)lnK 厅 b 按材料扭转试验数据计算(适用于常温) 根据容器圆筒材料的切应力切应变下曲线(此曲线由材料扭转试验数据获得),在塑性 1D 段取三组切应力和切应变,代人式(3),求得3个常数A,BC -Cu =A士h 根据式(4),式(5),通过试差法确定圆简容器直径比为K的容器的内外壁切应变u和, e" 1=K2(e" -- Au十BuCu" 5 e醉 A,十Bou.十C , 3)将u和
代人式(6),即可求得爆破压力尸: ,4.25 (o2 u U -(-) P= ]1十B[(-云)+ 320 30 3060 ,2.125 s +c(8 6 25. 2.25 2970 6.2.4弹塑性分析法 容器的塑性垮塌失效应采用如下步骤进行评定,见图2: 创建模型 确定载荷工况组合 调整结构 或载有 弹塑性数值计算 合格判定 (收敛? 评定通过 图2塑性垮塌失效评定步骤 13
GB/T34019一2017 创建模型 a 创建的数值分析模型应给出容器的几何特性、边界条件和作用载荷
b)确定载荷工况 载荷工况组合应按表1确定
c 弹塑性数值计算 每种载荷工况组合均应进行弹塑性数值计算
在计算中应采用材料真实应力应变模型(可参考附 录E,VonMises屈服准则和相关联的流动法则,同时应考虑几何非线性
d)合格判定 若数值计算均得到收敛解,则评定通过;若结果不收敛,则应对模型进行调整如改变厚度等),重新 评定
6.3局部过度应变失效评定 6.3.1评定方法 本节给出了采用弹塑性分析容器局部过度应变失效的评定方法
6.3.2符号 下列符号适用于本节 A 材料断后伸长率,%; 累积应变损伤系数; D 第友步载荷顺序下产生的应变损伤系数; 材料参数,由表9计算得到 m2、mn3、m 材料在设计温度下的屈服强度与抗拉强度之比,R/R; 材料在设计温度下的抗拉强度,MPa; R 材料在设计温度下的屈服强度,MPa R p,3 材料断面收缩率,%; 主应力,MPa; o1、o?、G
第人步加载后的主应力,MPa; C1,k、o2,k、G3, 当量应力,MPa; o 第人步载荷顺序下的VonMises当量应力,MPa; d 当量塑性应变; ew 三轴应力状态对应的应变极限; -第卜步加载时三轴应力状态对应的应变极限 eL, 单向拉伸应力状态对应的应变极限,应取m?、,m,m,中最大值; eLm 第人步加载后产生的当量塑性应变增量
Aepmmn, 6.3.3弹塑性分析法 6.3.3.1评定步骤 容器局部过度应变失效应采用如下步骤进行评定,见图3. 创建模型 a 数值分析模型应给出容器的几何特性、边界条件和作用载荷
确定载荷工况 b) 载荷工况组合应按表1确定
14
GB/34019一2017 弹塑性数值计算 c 每种载荷工况组合均应进行弹塑性数值计算
在计算中应采用材料真实应力应变模型(可参考附 录E),VonMises屈服准则和相关联的流动法则,同时应考虑几何非线性
d)确定应变极限 容器任意部位的三轴应变极限e按式(7)计算 2.2 (a十
十o .( e=ELexp m 3om 式中,当量应力a按式(8),其他参数取值见表9 [(a一a,)!十(a;一a))?十(a
一a))3] 8 G= 厅 对35CrNi3MoVR和36CrNi3MoVR锻件制造的容器,应采用式(9)代替式(7)对三轴应变限制进 行计算 1a十十o 2.28 9 e=0.6
exp 3d 合格判定 若容器任意部位的当量塑性应变=均满足式(10),则评定通过 10 epen 创建模型 确定载荷工况组合 调整结构 弹塑性数值计算 或载街 确定应变极限 8 合格判定 s G叫 评定通过 图3局部过度应变失效评定步骤 表9弹塑性分析中参数取值 料 mn 1 材 0.6(1一R) 2ln(1十A/100) n[100/(100- 高强度低合金俐 15
GB/T34019一2017 6.3.3.2累积损伤 若能够明确各种载荷工况的加载顺序,应采用如下步骤计算累积损伤效应,见图4
创建模型 确定载荷工况 明确共步加载 第k步加载 弹塑性数值计算 调整结构 或载荷 确定应变极限 k=k1 应变损伤系数 D k=n2 型 评定通过 图4局部过度应变失效累积损伤评定步骤 a 创建模型 数值分析模型应给出容器的儿何特性、边界条件和作用载背
b)确定载荷工况 按表1,确定在分析中应用到的载荷工况组合,明确加载顺序,分别设为第1步,第2步,第" 步加载
弹塑性数值计算 c 第人步加载后,进行弹塑性数值计算
计算中应采用材料真实应力应变模型(可参考附录E),Vom Mises屈服准则和相关联的流动法则,同时考虑儿何非线性
d)确定应变极限 计算完成后,容器中任意部位的三轴应变极限eL按式(11)计算 2.2 o1,上十G2,k十o G3" l eL.=e
exp 十71? 3a, 式中,当量应力d按式(12),其他相关参数取值见表9 d.)2] 12 [(a,4一oa;.t)'十(o;k一,)'十(a. 对35CrNi3MoVR和36CrNi3MoVR锻件制造的容器,应采用式(13代替式(11对三轴应变限制 进行计算 16
GB/34019一2017 /a1,k十o2,k十o8, 2.28 E=0.6exp 13 3m 应变损伤系数 e 第人步加载的应变损伤系数按式(14)计算 .(14 D, =Aepq/eL. 式中,公e,即在第更步加载下产生的塑性应变增量,EeL.即对应的三轴应变极限 fD 合格判定 根据加载顺序,依次按上述步骤计算,得到每步加载对应的应变损伤系数D.,最终按式(15)计算 累积应变损伤系数D. 15 D,= D. 若容器任意部位的D
均小于或等于1,则评定通过
6.4棘轮失效评定 容器的棘轮失效应采用如下步骤进行评定,见图5
创建模型 确定载荷工况 调整结构 弹塑性数值计算 或载街 k=k十1 卸-加载 合格判定 满足条件之 评定通过 图5棘轮失效评定步骤 创建模型 a 数值分析模型应给出容器的儿何特性、边界条件和作用载荷
b)确定载荷工况 明确容器在操作状态下的载荷工况
弹塑性计算 应采用理想弹塑性模型.VonMiss屈服准则和相关的流动法则,同时应考虑几何非线性
其中,理 17
GB/T34019一2017 想弹塑性模型的屈服强度取材料在设计温度下屈服强度的0.9倍
d)合格判定 进行n次加-卸载弹塑性计算后(取n>3),满足下列条件之一则评定通过 1模型中只有弹性变形,无塑性应变区; 模型中存在弹性核心区域; 2 3)模型无永久性塑性变形 6.5疲劳失效评定 6.5.1评定方法 本节给出了容器疲劳失效的评定方法
若容器能够按6.5.3判定为未爆先漏,按6.5.4的疲劳分析 法或6.5.5的断裂力学法进行评定;若不能够判定为未爆先漏,则应按6.5.5的断裂力学法进行评定
6.5.2符号 下列符号适用于本节
-断裂力学评定时假设的初始裂纹深度,m; a 临界裂纹深度,取K=Ke对应的裂纹深度和0.8倍壁厚中的较小 a 者, ,m; -裂纹扩展计算时假定的裂纹扩展深度, ,m; a C 裂纹扩展系数,见表11 da/dN 裂纹扩展速率,m/次 计算裂纹扩展门槛值的系数,见表11; 材料系数,见表ll; 材料系数,见表1l; 应力强度因子,MPa、/m; K 材料的断裂韧性,MPa/m; K 除残余应力之外的所有循环载荷作用下的应力强度因子最大值,MP Vm; Kd -除残余应力之外的所有循环载荷作用下的应力强度因子最小值,MPa m; 由自增强所引起的残余应力得到的应力强度因子,MPa/m; K AK的 裂纹扩展门槛值,MPam; 裂纹扩展指数,见表11 mn 预计循环次数; 编号为1、2、3等应力循环中每种循环在容器的寿命周期中的预计循环 11、712、71 次数; 允许循环次数; N、Ng、N -编号为1、2,3等应力循环中每种循环在容器的寿命周期中的允许循环 次数; 裂纹扩展至1/4a
所需的循环次数; N N 裂纹扩展至临界裂纹深度4.所需的循环次数; 18
GB/34019一2017 AN 裂纹扩展Aa所需的循环次数; R 在整个循环中最高工作温度和最低工作温度的平均值温度下材料的 抗拉强度; 材料在常温下的屈服强度; R, M," Ra
在整个循环中最高工作温度和最低工作温度的平均值温度下材料的 屈服强度; 整个循环中的交变应力幅,MPa Sl 主应力方向在循环中变化时的交变应力幅,MPa; sh的 当量交变应力强度幅,MPa; S S 当量交变应力幅,MPa; S 主应力方向在循环中变化时的交变应力幅,MPa; S, 整个循环中的主应力差值,MPa 主应力方向在循环中变化时的波动主应力差值,MPa S 在整个循环中主应力差的最大值和最小值,MPa; jmxSmn Sm 平均应力,MPa; S. 主应力方向在循环中变化时的平均应力,MPa; S. 主应力的和,MPa; 主应力和的均值,MPa s s 主应力方向在循环中变化时主应力的和,MPa; s 主应力方向在循环中变化时主应力和的均值,MPa 壁厚,mm:; 累计使用系数; U,U.、,U 编号为1、2、3等应力循环中每种循环在容器的寿命周期中的使用 系数 主应力,MPa; 主应力波动,MPa; 整个循环中的6个应力分量,MPa 应力分量波动,MPa; 整个循环中极端点(代数值最大或最小)所对应的时刻的各个应力分 、Oni、oi、Ttni、Tnri、Tt 量,MPa
6.5.3未爆先漏判定 若容器圆筒内表面的轴-径向裂纹(设初始深长比a//=1/3同时满足如下条件,则判定为未爆 先漏 裂纹扩展至0.8时,Ki
GB/T34019一2017 6.5.4.3.2当所考虑元件部位的主应力方向在循环中变化时,应按下列步骤确定交变应力强度幅: 波动主应力 a 1 确定所考虑点在6.5.4.2中所述的各种载荷下确定整个循环中的6个应力分量,分别以 a,d.,d,,r、T、表示; 选取循环条件的极端点(代数值最大或最小)所对应的时刻,将这一时刻的各个应力分量 分别表示为;dw,ow,d、,Tm、rm; 在循环中的每个时刻,从每个与该时刻对应的应力分量a,a,等中减去i时刻的相应 应力分量ow,d,等,所得的波动应力分量记为:',o,等; 在循环的每个时刻,计算由六个应力分量波动',o,,a'、T'、T',,所导出的主应力波动 ! d,'、'
这些波动主应力的方向虽然在循环中变化,但其编号应保持不变
b)波动主应力差 按式(26)计算在整个循环中,相对于时间的波动主应力差s; 26 ls'=a' 交变应力幅 c 在整个循环中确定各主应力差的代数最大值s,.和最小值S,交变应力幅';按式(27 计算 .(27 SM们=0.5(S'm-s" min d)波动主应力和 按式(28)计算在整个循环中的波动主应力的和S.行 ,g='+口' 28 n23" 波动主应力和的均值: S
=0.5(S,十s 29 miimin f 平均应力 按如下要求计算与交变应力幅S,相关的平均应力S: -R 1若s》m.
GB/34019一2017 按式(30)计算当量交变应力强度幅 S一maxS,e,seg,sa 35) 6.5.4.4 允许循环次数 a 由6.5.4.3计算求得的当量交变应力强度幅S乘以设计疲劳曲线图(见图1中所给定的弹性 模量与所用材料弹性模量之比 b 在设计疲劳曲线图上的纵坐标中读取该值,过此点做水平线与设计疲劳曲线相交,交点的横 坐标值即为所对应的允许循环次数N
6.5.4.5合格判定 若容器的预计循环次数"不大于允许循环次数N,评定通过;否则,应采用改变操作条件、容器结 构尺寸等措施,重复本节中之前的操作步骤,直到满足本条要求为止
6.5.4.6累积损伤 如果有两种或多种显著应力循环时,应对每种应力循环计算其交变应力强度和平均应力
应采用 以下规定计算疲劳累积损伤效应 编号为1、2、3等应力循环中每种循环在容器的寿命周期中的预计循环次数,分别为:n、n、n a 等
在确定其中任一循环的循环次数时,应计及不同循环叠加时,各应力循环的主应力差值叠 加的影响 按6.5.4.3中规定的方法确定每种应力循环中的当量交变应力强度s.,相应地记为s.a.Ss.a b S等; 按6.5.4.4求取S,Sg,S等单独作用时的允许循环次数Ni、N、,N等; c 对每种应力循环,按式(36)确定各自的使用系数U、,U.U,等 d U1= -" U一 " 36 u " 按式(37)计算累积使用系数U,累计使用系数U不得大于1.0: 37 U=U十U十U十 6.5.5断裂力学法 容器的疲劳失效应采用如下步骤进行断裂力学评定,见图7
23
GB/T34019一2017 初始裂纹尺寸 材料斯裂韧性K 明确找树工况 应力强度因子Ke,Kn,K K十K O A人一人m a,+I=a,+A 1,+A1 ,+1=" 裂纹扩展速率d山au/dN=0 人 结束 r(R)=1+3.53R (R)=[1.5/(1.5一R)]" 杏 调整结构 或载荷 裂纹扩展速率d/aN=G(R)AK” 裂纹扩展Aa循环次数AN,=Au/d/4w) 4,+Au<.8
GB/T34019一2017 用减少A的方法反复进行试算,直至N,和N无明显变化 6.5.5.6合格判定 若容器的预计循环次数满足式(44),评定通过;否则,应采用改变操作条件、容器结构尺寸等措 施,重复本节中之前的操作步骤,直到满足本条要求为止 n
超高压容器GB/T34019-2017
超高压容器是指在极高的压力下储存和输送气体的设备。随着科学技术的不断发展,超高压容器已经广泛应用于航空航天、能源、化工等领域。为了保证超高压容器的安全性和可靠性,国家制定了GB/T34019-2017标准。
一、超高压容器的定义
根据GB/T34019-2017标准的规定,超高压容器是指设计压力大于10MPa的容器。其中,常见的超高压容器有气瓶、气体储罐、管道等。
二、超高压容器的分类
按照GB/T34019-2017标准的要求,超高压容器可以分为以下几种类型:
- 钢制无缝气瓶
- 复合材料无缝气瓶
- 钢制焊接式气瓶
- 复合材料缠绕式气瓶
- 钢制无缝气体储罐
- 复合材料无缝气体储罐
- 钢制焊接式气体储罐
- 复合材料缠绕式气体储罐
- 钢制压力容器
- 复合材料压力容器
- 钢制管道
- 复合材料管道
三、超高压容器的使用要求
超高压容器在使用时需要遵守GB/T34019-2017标准中规定的要求。主要包括以下几个方面:
- 超高压容器必须经过定期检测和检验。
- 超高压容器应该按照规定的工艺进行充装和排放气体。
- 超高压容器的安全阀必须能够正常工作,并且设置在容器的最高点。
- 超高压容器在运输和使用过程中,需要遵守相关的安全规定和操作程序。
四、超高压容器的检测方法
为了保证超高压容器的安全性,GB/T34019-2017标准规定了超高压容器的检测方法。
其中,常见的检测方法有如下几种:
- 水压试验
- 气密性检测
- 超声波探伤检测
- 磁粉探伤检测
- 放射性检测
五、超高压容器的维护与保养
超高压容器在使用过程中需要定期进行维护和保养。主要包括以下几个方面:
-
<
- 超高压容器的外观、阀门、安全阀等部件应该定期清洁和检查。
- 超高压容器的润滑油应该定期更换。
- 超高压容器在存放和使用过程中要注意防潮、防晒、防腐蚀。
- 超高压容器不得与其他物品混放或受到重击、摩擦等影响。
总之,超高压容器作为一种重要的气体储存和输送设备,其安全性和可靠性对于生产和工业领域都有着至关重要的作用。因此,遵守GB/T34019-2017标准的相关要求,定期进行检测和维护,才能够确保超高压容器的正常运行和使用。