GB/T34476-2017
转炉热平衡测试与计算方法
Methodsofdeterminationandcalculationofheatbalanceinconverter
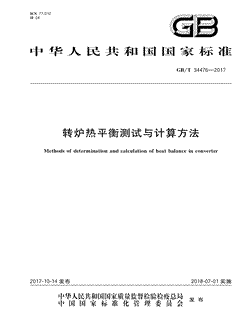
- 中国标准分类号(CCS)H04
- 国际标准分类号(ICS)77
- 实施日期2018-07-01
- 文件格式PDF
- 文本页数24页
- 文件大小1.25M
以图片形式预览转炉热平衡测试与计算方法
转炉热平衡测试与计算方法
国家标准 GB/T34476一2017 转炉热平衡测试与计算方法 Methodsofdeterminationandcaleulationofheatbalanceinconverter 2017-10-14发布 2018-07-01实施 国家质量监督检验检疫总局 发布 国家标准化管理委员会国家标准
GB/34476一2017 前 言 本标准按照GB/T1.1一2009给出的规则起草
本标准由钢铁工业协会提出
本标准由全国钢标准化技术委员会(SAC/Tc183)归口
本标准起草单位:中钢集团鞍山热能研究院有限公司、冶金工业信息标准研究院、鞍钢股份有限 公司
本标准主要起草人:丛伟、王姜维,谢国威、仇金辉,马彦珍、马光宇、赵春竹、李卫东、王一凌、徐阳 刘常鹏、范天骄
GB/34476一2017 转炉热平衡测试与计算方法 范围 本标准规定了转炉热平衡测试与计算基准、设备及转炉概况、转炉近期生产情况、测试准备、测试步 骤,测试内容,部位与方法,物料平衡计算,热平衡计算、热平衡测试报告
本标准适用于钢铁行业转炉热平衡测试与计算,其他行业可参照使用
热平衡测试与计算基准 2.1基准温度 采用环境平均温度,即转炉车间内的环境平均温度
2.2热平衡测试范围 根据测试要求,转炉热平衡测试体系的边界线规定在炉口处,根据需要和可能也可以将体系边界线 划到煤气回收系统后
2.3热平衡测试时间 在8h内完成,至少测试3次
每次测定一个冶炼周期,即从上炉出钢完成到本炉出钢完毕为止 2.4物料平衡和热平衡计算单位 以1t合格钢水为计算单位,即kg/t和J/t
设备及转炉概况、转炉近期生产情况 3.1设备及转炉概况 设备及转炉概况参考附录A填写
3.2转炉近期生产情况 被测转炉测定冶炼钢种与拟测定炉次相同的10炉平均生产数据参考附录B填写
测试准备 4.1熟悉设备状况 熟悉转炉及有关设备的结构、性能、操作与运行情况,并了解生产工艺流程等
4.2制定测试方案 根据测试要求制定测试方案,并选择能够代表转炉实际生产情况的测试部位和测试点,确保测试人 员及测试工作安全有序进行
GB/T34476一2017 4.3组织测试人员 根据测试方案组织测试人员
测试工作由专业技术人员指挥,按工作需要对测试人员进行分工,并 根据情况进行必要的技术培训与安全教育
参加测试人员应了解测定目的与要求,熟悉负责测试的内 容,熟练掌握测试技术
测试应在指定的专业人员统一指挥下进行
4.4检修设备与准备测试仪器和工具 准备好所需测量工具,对现场已有仪表及各种便携的测量仪器进行校正,满足测试要求
工厂无计 量装置时,在测试前应安装符合测试要求的计量装置
4.5选择测试时机 测试一般应选在炉役中期,根据特殊要求也可选在炉役前期或后期,但设备及操作条件应处于正常 的情况下
4.6预备性测试 正式测试之前对其中的几儿项或全部项目进行必要的预备性测试,验证测试手段的可靠性,检验测试 方案的安全性
在正式测试前应对炉口平面下炉气成分、,炉气温度、炉口、横烟道及垂直烟道等处的含 尘量,钢水、钢渣及铁水温度、铁渣量等做预备性测试
5 测试步骤 按测试内容进行测试与记录
采用以测量为主,控制中心记录数据为参考的方法,对所测数据进行 分析整理,并按本标准的计算方法进行计算
对测试结果进行分析并提供测试报告
创造必要的测试 条件,包括炉口测试平台、烟气取样口、电力接头的准备等
如现场无标准中规定的测试条件,亦可采用 现场能够满足测试要求的仪器装置进行测试
测试内容与方法 6.1主要测试内容 主要项目测试参见附录C
6.2测试方法 6.2.1环境状况 用温度计测量车间环境平均温度
用大气压计测量车间大气压
用干湿球温度计测量相对湿度 再换算成绝对湿度 6.2.2冶炼操作 仔细观察并记录上一炉和本炉出钢后炉内状况
准确记录吹炼各期枪位变化,倒渣、取样,测温及 测氧起止时间
记录本炉冶炼周期的炉况变化
6.2.3废钢 选用成批的已化检验完成分的返回废钢
对各类废钢应分别分类称量
对各类废钢取样并分析其
GB/34476一2017 成分,包括测定或估算其氧化量及杂质含量
6.2.4铁水 人炉铁水重量用称量空罐-重罐-空罐的方法测量
人炉铁渣重量,如无条件扒除铁渣时用碳酸铆 稀释法测定
6.2.5熔剂 对人炉前各类熔剂取样分析其成分、水分含量并称重
6.2.6脱氧剂及合金 对各类脱氧剂及铁合金在人炉前取样做成分分析并称重
6.2.7钢水 用快速微型热电偶测定开始出钢时及出钢过程中炉内钢水温度,取样做成分分析,并用定氧探头测 定钢水中含氧量
精确称量终点俐水重量,即称空罐重量,重罐重量、铸完锭坯后空罐重量,称量或估算出罐内和炉内 残钢重量等
6.2.8钢渣 每次放渣时应测定钠渣温度并取样做成分分析
倒炉出钢时用快速微型热电偶测定钢水温度,同时以定氧头测定钢水与钢渣的温度,以其差值与快 速微型热电偶测得值之和可作为钢渣温度
直接称量各喷出渣,炉口、氧枪及姻罩等的黏结渣,放出渣,钢包存渣和渣罐溢出的重量及其中残钢 重量,并扣除炉外加人合金的脱氧产物量
6.2.9炉尘 烟气含尘量用高温测尘仪于一文前测量,炉尘成分由含尘量测定处取样分析
对于有转炉煤气回 收的转炉也可以用转炉尘泥成分代替
出炉炉尘温度可取含尘量测定处炉气温度
6.2.10炉衬侵蚀 进人炉渣中的炉衬量可视为炉衬被蚀量
炉衬被蚀量可采用现场经验数据,也可由钙、镁平衡估算 此时应取散状料,钢渣及炉衬样分析钙、镁含量) 6.2.11吹氧情况 记录吹炼过程中氧气流量、温度和压力
记录氧气的纯度
记录熔炼过程中枪位变化
6.2.12炉气 2 开始吹氧后每隔1nmin一 min用抽气式热电偶于炉口测一次炉气温度,一直测到提枪停吹为止 在测炉气温度的同时,在同一位置用套有纸管的不锈钢管并且前面装有露出200mm以上的陶瓷管取 1个2个炉气样,应用气体分析仪或气相色谱仪进行气体成分分析
取炉口炉气时,为保证气样可靠性,应将取样系统内空气排除干净并注意安全,防止爆炸
取样过 程中,要将排放的高浓度一氧化碳气体返人烟道或做其他无害化处理,以防中毒
以露点仪或高温测尘仪测定炉口炉气的含水量
在一文前用陶瓷取样管,S型毕托管和热电偶等
GB/T34476一2017 测定炉气(烟气)的成分,流量,静压和温度
按图纸或实测结果确定炉口面积
根据炉口尺寸,准确确定取样位置
6.2.13炉体 将炉体分成若干个温度相近的测定区域,用红外测温仪或热流计测定各区域的表面温度或热流
6.2.14冷却水 用现场计量仪表或体积法测定炉口及氧枪冷却水的流量,用水银温度计测定进、出口温度
物料平衡计算 7.1收入物料重量的计算 7.1.1经过测定及计算得出每吨钢水的以下各项物料重量 铁水重量,单位为千克每吨(kg/t); G -铁水带渣重量,单位为千克每吨(kg/t); G G 废钢重量,单位为千克每吨(kg/t); 石灰重量,单位为千克每吨(kg/t); 镁砂重量,单位为千克每吨(kg/t): G -铁矿石重量,单位为千克每吨(kg/t) G 氧化铁皮重量,单位为千克每吨(kg/t); G 萤石重量,单位为千克每吨(k g/t A G 生白云石重量,单位为千克每吨(kg/t) G0 -铁合金重量,单位为千克每吨(kg/t); Gm 人炉氧重量,单位为千克每吨(kg/t). 7.1.2物料含水重量G1按式(1)计算 G=G"十G"十十G" 式中 物料含水重量,单位为千克每吨(kg/); G2 G",G"、,G"人炉废钢、石灰人炉氧的含水重量,单位为千克每吨(kg/t)
7.1.3吸人空气重量G按式(2)计算 (2 G=4.35[G+G十0.01429(goV'一fVn 式中 Gm -吸人空气的重量,单位为千克每吨(kg/t); Gm 元素氧化反应耗氧的重量,单位为千克每吨(kg/t); G -钢水中含氧的重量,单位为千克每吨(kg/t) -炉口炉气中氧含量的体积分数,用百分数(%)表示; Po 人炉氧气浓度的体积分数,用百分数(%)表示; Pog Vm -吨钢水氧耗量,单位为立方米每吨(m`'/t); V" -炉口干炉气体积,单位为立方米每吨(m/t),按式(3)计算 187(Ge十Ge c分 V', Pco十Pcog 式中 G 每吨钢水中碳的氧化重量,单位为千克每吨(kg/);
GB/34476一2017 石灰与白云石分解出气体中的含碳重量,单位为立方米每吨(m/t); Gc" 炉口干炉气CO,CO成分的体积分数,用百分数(%)表示
Peofco 元素氧化反应耗氧重量按式(4)计算 /0.55Ge 5Gp 0.05Gs GpFao 3GroFeo Gs =1.429 22.4(4 Go 2十0 12 124 32 112 224 式中 1.429 标准状况下氧气的密度,单位为千克每立方米(kg/m'): G、G、G、 ,G -每吨钢水C,Si、Mn、P、S的氧化重量,单位为千克每吨(kg/t); cGiw、 铁氧化成Fe0,Fe.,O的耗氧重量,单位为千克每吨(kg/t) GF一Fo,GRo-Feo 人炉物料中铁的氧化成氧化亚铁和氧化铁的重量分别按式(5)和式(7)计算: 56 GFcO GrFO 5 7 式中 人炉物料中氧化亚铁的生成量,单位为千克每吨(kg/t),按式(G)计算 GcO Gr0=G'wx十G'wx十G'wx十G'w Gw'x,( -G2w'x Gwx Gw'x
(6 式中 G'.,G'.,G',G 出炉钢渣、炉尘,兑铁水时撒失铁渣黏结物,吹炼中喷渣 等重量,单位为千克每吨(kg/t) 铁水带渣,废钢、铁矿石、氧化铁皮等重量,单位为千克 G2、,G、,G6、G 每吨(kg/t); 出炉钢渣、炉尘,兑铁水时撒失铁渣黏结物,吹炼中喷 w'x、7wx、w'x、wx、Twx:、7w'xi、7w'xi、7w'x 渣、铁水含渣、废钢、铁矿石、铁皮等氧化亚铁含量的质 量分数,用百分数(%)表示
112 GredFeo Greo 160 式中: 人炉物料中氧化铁的生成量,单位为千克每吨(kg/t),按式(8)计算 Greo G ,ux+G,w%+G',w;十G,ux;-G;w,-G,w;-G,wh一G;叫 Greo (8 式中: 出炉钢渣、炉尘、兑铁水时撒失铁渣黏结物、吹炼中喷 wY、 、uwx、 、w'y、wY、wY、wY、wYe、wY 渣,铁水含渣,废钢、铁矿石、铁皮等氧化铁含量的质 量分数,用百分数(%)表示 人炉物料中非铁元素的氧化重量按式(9)计算: 9 G"w G=(G1+G)1 7e 式中 人炉物料中某种非铁元素的氧化重量,单位为千克每吨(kg/t); G G ,G -铁水、废钢重量,单位为千克每吨(kg/t); 7 人炉物料中某种非铁元素成分的质量分数,用百分数(%)表示; -脱氧出钢前炉内某种非铁元素成分的质量分数,用百分数(%)表示 w G" 脱氧出钢前炉内钢水总重量,单位为千克每吨(kg/),按式(10)计算: Twc十w'Mn十wU's十wp十ws G+G. Grao 100 G" (10 we十wUMn十w'sr十wU十ws I00
GB/T34476一2017 式中 -终渣含钢珠重量(一般波动在终渣重量的2%10%之间),单位为千 克每吨(kg/t); -人炉物料中C,Mn,Si,P,S的质量分数,用百分数%)表示; wc,w'Mn、w's,wp、ws 脱氧出钢前钢水中C,Mn,Si、P,S的质量分数,用百分数(%)表示
we,wM、w's'、wy,ws 7.1.4炉衬侵蚀的重量可用钙镁平衡法计算,也可按铁水量的0.3%计
7.1.5收人物料重量总和按式(11)计算 习G=G+G十G+GG十G
+G+G十G,+G+G+Gg+G+G l1 式中 G 铁水带渣重量,单位为千克每吨(kg/t); G 石灰重量,单位为千克每吨(kg/t):; G 镁砂重量,单位为千克每吨(kg/t); 铁矿石重量,单位为千克每吨(kg/t); 氧化铁皮重量,单位为千克每吨(kg/t); 萤石重量,单位为千克每吨(k /t; A G 生白云石重量,单位为千克每吨(k /t; Ag o 铁合金重量,单位为千克每吨(kg/); G 人炉氧重量,单位为千克每吨(kg/ /t; G 吸人空气的重量,单位为千克每吨(kg/t); G 炉衬侵蚀的重量,单位为千克每吨(kg/t): 习G -收人物料重量总和,单位为千克每吨(kg/t). 7.2支出物料重量的计算 7.2.1经测定得到以下各项的物料重量: G -出炉钢水重,G-100kg/ G" 终渣含钢珠重量(一般波动在终渣重量的2%~10%之间),单位为千克每吨(kg/t); G -出炉钢渣重量,单位为千克每吨(kg/t); -出炉炉尘重量,单位为千克每吨(kg/t) -兑铁水撒失铁渣黏结物重量,单位为千克每吨(kg/t); G -吹炼中喷渣重量,单位为千克每吨(kg/t)
7.2.2出炉炉气重量按式(12)计算 G'- 12) 28pco十44gco十32po2十28N 100×22.4 式中 G -出炉炉气重量,单位为千克每吨(kg/t); 炉口干炉气N
成分体积分数,用百分数(%)表示 9N 7.2.3物料水分生成水蒸气的量按式(13)计算 (13 G'=G 式中 G -物料水分生成水蒸气的重量,单位为千克每吨(kg/t)
物料各项收人总和习G与已测各项支出总和之差即为差值2G按式(I4)计算 7.2.4 十G (14 AG=G-(G'+G'+G'十
GB/34476一2017 式中: AG 物料平衡差值,单位为千克每吨(kg/t) G 出炉钢水重,G=1000kg/t
差值包括未测出的支出及误差
物料平衡允许相对误差值为士5%以内,按式(15)计算: AG (15) ×1005 G 7.2.5支出总和计算按式(16)计算 十G'十G 16 G'=G'+G'十 式中: G 物料支出总和,单位为千克每吨(kg/t). 7.3物料平衡表 将物料平衡各收,支项的计算结果列人表1中
表1物料平衡表 收人 支出 热量 热量 符号 符号 项目 项目 % kg/t kg/t G 铁水重量 出炉钢水重量 F 铁水带渣重量 G 终渣含铁珠重量 G 废钢重量 出炉钢渣重量 G 石灰重量 出炉炉尘重量 G 镁砂重量 兑铁水撒失铁渣黏结物重量 铁矿石重量 G 吹炼中喷渣重量 氧化铁皮重量 出炉炉气重量 G 萤石重量 G 物料水分生成的水蒸气重量 白云石重量 铁合金重量 G0 人炉氧重量 Gmn 物料含水重量 Gg 吸人空气重量 G3 G 炉衬侵蚀重量 G 差值 合计 100 G 合计 100 注1百分率精确到小数点后一位
注2:热量值取4位有效数字
GB/T34476一2017 8 热平衡计算 8.1热量收入项目计算 8.1.1铁水带人的物理热量按式(17)计算: (17 Q=G(C-Cl
十217.44) 式中 Q -铁水带人的物理热量,单位为千焦每吨(k/t); C 铁水在0亿至4同的平均比热容,单位为千焦每千克摄民度[k/(kg)] 人炉铁水的温度,单位为摄氏度(C); 铁水在0C至
间的平均比热容,单位为千焦每千克摄氏度[kJ/(kgC] 环境温度,单位为摄氏度(C); 217.44 铁的熔化潜热,单位为千焦每千克(kJ/kg)
8.1.2铁渣带人的物理热量按式(18)计算: 18 Q=G.(C;t-Cal.十209.08) 式中 -铁渣带人的物理热量,单位为千焦每吨(kJ/t): Q G 铁渣在0至t间的平均比热容,单位为千焦每千克摄氏度[kJ/(kg
] 人炉铁渣的温度,单位为摄氏度(); c 铁渣在0C至t
间的平均比热容,单位为千焦每千克摄氏度[k/(kg
笔]; 209.08 人炉铁渣的熔化潜热,单位为千焦每千克(k/kg). 8.1.3元素氧化放出的热量按式(19)计算: Q=9199.,52×0.9Ge十32746.11×0.1Ge+32169.05Gs十7004.18GMn #* 19 +24069.29Gp十9270.61×0.3Gs十4775.39G-Ro十7367.98G F一Feo 式中 元粼氧化放出的热量.单位为千焦每吨(HJ97 Q 碳元素氧化成一氧化碳和二氧化碳的化学反应热,按 9199.52、32746.l1 90%生成一氧化碳,10%生成二氧化碳计算,单位为 千焦每千克(J/lkg)3 32169.05、7004.18、24069.29,9270.61 硅、、磷、硫元索氧化的化学反应热,其中硫元素按 30%生成二氧化硫计算,单位为千焦每千克(kJ/kg); 4775.39、7367.98 铁元素氧化成氧化亚铁及氧化铁的化学反应热,单位 为千焦每千克(kJ/kg)
8.1.4成渣反应放出的热量按式(20)计算: 142 60 十5093.19Gp (20 Q=2103.34G 62 式中 Q 成渣反应放出的热量,单位为千焦每吨(k/); 2103.34,5093.19-Si,P的氧化反应热,单位为千焦每千克(k/kg). 8.1.5炉衬烧损带人的物理热量按式(21)计算 (21 Q,=G(Cl-Cd. 式中 Q -炉衬烧损带人的物理热量,单位为千焦每吨(kJ/t);
GB/34476一2017 -被侵蚀的炉衬在0C至t间的平均比热容,单位为千焦每千克摄氏度[k/(kgC]; -被侵蚀的炉衬在兑铁水时的平均温度,单位为摄氏度(C) 1 C 被侵蚀的炉衬在0至
间的平均比热容,单位为千焦每千克摄氏度[/(kg
C)]
1e 8.1.6热量总收人按式(22)计算 Q=Q+Q+Q+QQ 式中 习Q -热量总收人,单位为千焦每吨(/t)
8.2热量支出计算 8.2.1钢水带出的物理热量按式(23)计算: Q=G'(c''-c,4十271.8) 式中: 出炉孵水带出的物理热量.单位为千焦每吨(D Q G 出炉钢水在0C至'间的平均比热容,单位为千焦每千克摄氏度[k/(kgC)]; 出炉钢水的温度,单位为摄氏度(C); ' C'" 出炉锅水在0C至.间的平均比热容,单位为千焦每千克摄民度[k/(kg C; 钢的熔化潜热,单位为千焦每千克(kl/kg)
271.8 钢珠带出的物理热量按式(24)计算 8.2.2 Q'=G'(C',t'-C,.
十271.8) 24 式中 钢珠带出的物理热量,单位为千焦每吨(kJ/t); Q C" 钢珠在0C至'间的平均比热容,单位为千焦每千克摄氏度[kJ/(kgC]; 出炉钢珠的温度,单位为摄氏度(C); t C 钢珠在0C至t
间的平均比热容,单位为千焦每千克摄氏度[kJ/(kgC]
8.2.3钢渣带出的物理热量按式(25)计算: 25 Q'=G'(C,t'-C'.t
十209.08) 式中 -钢渣带出的物理热量,单位为千焦每吨(kJ/t); Q c" 钢渣在0C至'间的平均比热容,单位为千焦每千克摄氏度[k/(kgC] t" 出炉钢渣的温度,单位为摄氏度(C) C' 钢渣在0C至1
间的平均比热容,单位为千焦每千克摄氏度[kJ/(kgC]
8.2.4物料分解反应吸收的热量按式(26)计算: 十4072.88G 26 Q'=5151.73GFeo 十2304.06Gco-Mco Gcog-caco; 式中: -物料分解反应吸收的热量,单位为千焦每吨(/t): Q 5151.73、4072.88、2304.06 物料分解成氧化铁及二氧化碳所需要的化学反应热,单位为千焦 每千克(k/kg):; 石灰和白云石中碳酸钙生成二氧化碳的量,单位为千克每吨(kg/); Gcoe -caco) G -白云石中碳酸镁生成二氧化碳的量,单位为千克每吨(kg/t rco-Meco 8.2.5炉气带出的物理热量按式(27)计算 27 Q'=G'(C''-C'.t. 式中: Q 炉气带出的物理热量,单位为千焦每吨(k/t);
GB/T34476一2017 C' -炉气在0C至'间的平均比热容,单位为千焦每千克摄氏度[kJ/kg)] tt" -炉口出炉气的温度,单位为摄氏度(C); C -炉气在0C至t
间的平均比热容,单位为千焦每千克摄氏度[kJ/(kgC]
8.2.6冷却水带走的物理热量按式(28)计算 Q,=G.(Cw'“-Cw/i 式中 Q -冷却水带走的物理热量,单位为千焦每吨(kJ/t) G 氧枪、水冷炉口、耳轴等处冷却水的总重量,单位为千克每吨(kg/t); 冷却水在0C至t间的平均比热容,单位为千焦每千克摄氏度[kJ/(kgC] C2 -冷却水出水的温度,单位为摄氏度(); '2 C 冷却水在0C至t间的平均比热容,单位为千焦每千克摄氏度[k/(kg
C)]; -冷却水进水的温度,单位为摄氏度(C)
1w 8.2.7炉尘带出的物理热量按式(29)计算: Q'=G'(C't'-c',.十209.08) 29 式中 Q 炉尘带出的物理热量,单位为千焦每吨(k/t); Ce -炉尘在0C至'间的平均比热容,单位为千焦每千克摄氏度[k/kgC)] 出炉炉尘的温度,单位为摄氏度(C) C 炉尘在0C至t
间的平均比热容,单位为千焦每千克摄氏度[kJ/(kg
]; 炉尘的熔化潜热,单位为千焦每千克(k/kg). 209.08 8.2.8物料中水分蒸发带出的热量按式(30)计算 Q,=G'[c.(I00一.)十2253.88十1.24(C,'-15.05)] (30 式中 -物料中水分蒸发带出的热量,单位为千焦每吨(kJ/t) 水在t
至100C平均比热容,单位为千焦每千克摄氏度CkJ/(kgC] 水蒸气在0C至t'间的平均比热容,单位为千焦每千克摄氏度[kJ/(kgC]
炉体表面散发的热量按式(31)计算 8.2.9 r习q.A Q= 31 60G 式中 Q -炉体表面散发的热量,单位为千焦每吨(kJ/t); 转炉冶炼周期,单位为分钟(min) A -第i部分炉体表面散热面积,单位为平方米(m=) -第i部分炉体表面平均面积热流量,单位为千焦每平方米小时[kJ/(mh)],如不能直接 g! 测量,可按式(32)计算 1273十t 273十t
(32 g,=20.4le 十aa(h一t
100 100 式中: 炉体表面黑度 -第i部分炉体表面平均温度,单位为摄氏度(C); t 对流给热系数,单位为千焦每平方米小时[kJ/(m'
h)],见式(33),式(34)和式(35)
a 无风时,按式(33)计算: 10
GB/34476一2017 a
=A(一t.) 33 式中 系数,散热面向上时A=11.7,向下时A=6.3,垂直时A=9.2 A一 当风速w<5m/s时,按式(34)计算 a
=22.2十15.1W 34 当风速W>5m/s时,按式(35)计算 a=27.1w" 35 8.2.10炉口辐射损失的热量计算按式(36)计算 273十te A三[/3土 Q=20.41 36 100 100 式中 Q -炉口辐射损失的热量,单位为千焦每吨(kJ/t); 炉口面积,单位为平方米(m'); A" 角度系数
8.2.11撒失铁渣损失的热量按式(37)计算 a=c'(c',一 37 一C't
十217.44 式中: Q 撒失铁渣损失的热量,单位为千焦每吨(k/); 撒失铁随在0七至一间的早均比热容.单位为千焦每千党挺民度1u/(gt刀. C C' 撒失铁渣在0C至
间的平均比热容,单位为千焦每千克摄氏度[kJ/(kgC)]: 217.44 -撒失铁渣的熔化潜热,单位为千焦每千克(k/kg) 8.2.12喷出炉渣损失的热量按式(38)计算 (e c'.
十209.08 Q= 38 式中 Q -喷出炉渣损失的热量,单位为千焦每吨(k/t); 喷w如法在w它毫团的平的比热容.单他为下焦每下克撇氏度ue它 C" 喷出炉渣在0C至t
间的平均比热容,单位为千焦每千克摄氏度[J/kgC] 喷出炉渣的熔化潜热,单位为千焦每千克(/lkg)
209.08 8.2.13当炉口不能布置测点时,可将热平衡测试体系界面移到烟道处,计算热损失时需增加以下3项 计算 炉口逸气损失的热量按式(39)计算 a Q1=V'(Ctt'-C'al. 39 式中: Q 炉口逸气损失的热量,单位为千焦每吨(k/t); c' 一炉口逸气在0至'间的平均比热容,单位为千焦每立方米摄氏度[/mC]; C 炉口逸气在0C至
间的平均比热容,单位为千焦每立方米摄氏度[kJ/m'C]; V -每吨钢的炉口逸气量,单位为立方米每吨(m'/t),按式(40)计算 P
十P 2814br 9.8 -[长+(C一,) V'一 (40 6o(r一r,),(273+')c 1
GB/T34476一2017 式中 -炉口处的炉气表压,单位为帕斯卡(Pa); -炉口至姻罩下沿的高度,单位为米(m); 流量系数,厚墙从=0.82,薄墙从=0.62(当心<3.5d时为薄墙,为炉墙的厚度,d为炉口的 当量直径); b 炉口周长,单位为米(m); -环境大气压,单位为帕斯卡(Pa); 环境温度下的空气密度,单位为千克每立方米(kg/m=).见式(41)
1.293 41 ( 1o1325 1十 27 -'下炉气密度,单位为千克每立方米(kg/m'),见式(42). 42 101325 ly 273 式中 44we'co十18wo十64Pso十28pN十32o (43 ro 22.4×100 b)汽化烟道燕汽获得的热量按式(44)计算 W Q=G(ht-ctt 一" (44 10o 式中 汽化姻道蒸汽获得的热量,单位为千焦每吨(kJ/t); Q 每吨钢水的产汽量,单位为千焦每吨(kg/t); c h 蒸汽的热熔,单位为千焦每千克(k/kg); C 水蒸气在0C至'间的平均比热容,单位为千焦每千克摄氏度[k/(kgC] -给水温度,单位为摄氏度(C); 汽化潜热,单位为千焦每千克(kJ/kg); 燕汽湿度,以百分数(%)表示
炉口至测点间烟道表面散热量Q计算,同8.2.9
c 8.2.14当热平衡体系界面由炉口移至烟道时,计算炉气带出的热量Q'见8.2.5)中的炉口干炉气量 V'用烟道测点处的干烟气量V'代替,按式(45)计算 V( pco十9co: V'一 45 Pco十9co 式中: V 姻道测点处干烟气量,单位为立方米每吨m/t). -烟道测点处烟气中一氧化碳含量的体积分数,用百分数(%)表示 co 烟道测点处烟气中二氧化碳含量的体积分数,用百分数(%)表示 9co 烟道表面散热量Q%计算同8.2.9. 8.2.15 8.2.16热平衡各项收人热量总和习Q与已测各项支出热量总和之差即为差值AQ,按式(46)计算: (46 AQ=习Q一(Q'+Q'+Q'十十Q) 式中 -热平衡差值,单位为千焦每吨(J/t); Q 12
GB/34476一2017 Q -冷却水带出的物理热量,单位为千焦每吨(/t); 烟道表面散热量,单位为千焦每吨(kJ/t)
Qs 差值包括未测出的支出热量及误差
热平衡允许相对误差值为士5%以内,见式(47). AQ ×10o 47 8.2.17支出热量总和计算按式(48)计算 习Q'=Q'十Q+Q'十十Q'十4Q 48) 式中 习Q 支出热量总和,单位为千焦每吨(k/t)
8.3热效率计算 热效率按式(49)或式(50)计算 Q十Q'-一 Q ×100% 习Q-Q 式中: 转炉热效率,用百分数(%)表示
当热平衡体系界面移至烟道时,有余热蒸汽产生时,应按式(50)计算 Q'+Q'-Q -×100% 50 7=可 8.4热平衡表 将热平衡各收、支项热量的计算结果列人表2中
表2热平衡表 收人 支出 热量 热量 符号 项目 符号 项目 M/e % M/t 铁水带人的物理热量 Q 钢水带出的物理热量 Q o Q 铁渣带人的物理热量 钢珠带出的物理热量 元素氧化放出的热量 Q 俐渣带出的物理热量 Q 成渣反应放出的热量 Q 物料分解反应吸收的热量 炉衬烧损带人的物理热量 Q" 炉气带出的物理热量 冷却水带走的物理热量 Q Q 炉尘带出的物理热量 物料中水分蒸发带出的 Q 物理热量 Q 炉体表面散发的热量 Q 炉口辐射损失的热量 Q 撒失铁渣损失的热量 Q1 喷出炉渣损失的热量 13
GB/T34476一2017 表2(续 收人 支出 热量 热量 符号 项目 符号 项目 % M/t M/ Q 炉口逸气损失的热量 Q 汽化烟道蒸汽获得的热量 Q 烟道表面散热量 4Q 差值 习Q 100 合计 100 合计 注1百分率精确到小数点后一位 注2;热量值取4位有效数字
8.5主要经济技术指标 转炉热平衡测试主要经济技术指标见表3.
表3主要技术经济指标 序 号 符号或算
式 值 数 标 单位 单位氧耗 单位铁水耗量 kg/t G 单位废钢铁耗量 kg/t 单位钢铁料耗量 G十G kg/t % 废钢比 热平衡测试报告 9 热平衡测试报告包括以下内容 前言 a 主要设备概况及生产状况 b) 主要测定数据; c d 物料平衡表; 热平衡表; e f 主要技术经济指标; 分析与改进建议; 8 h)测定单位、负责人、报告人、审核人(签字) 14
GB/34476一2017 附 录 A 资料性附录 设备及转炉概况 设备及转炉概况见表A.1
表A.1设备及转炉概况 项目 单位 内容或数值 厂名及车间名 转炉编号 建成或末次大修日期 公称吨位 实际吨位 平均日出炉数 平均日产量 日利用系数 t/(td) 主要冶炼钢种 炉容比 m'/t 熔池直径 m 熔池深度 m 熔池面积 m 炉口型式 平均炉龄 氧枪型式 平均枪龄 转炉 供铁水系统 设备完好情况 供废钢系统 渣车系统 铸锭系统 15
GB/T34476一2017 附 录 B 资料性附录) 测试前一个月生产状况 测试前一个月生产概况见表B.1
表B.1测试前生产概况 项 单 内容或数值 统计钢种 统计炉数 统计时间范围 供氧 min 辅助 mmin 平均时间 故障 min 全炉 min 钢铁料 kg/ 铁水 kg/t 平均单耗 废钢铁 kg/t 矿石 kg/t 氧' nm'/t 钢渣量 kg/t " 吹损率 16
GB/34476一2017 录 附 C 资料性附录 主要测试项目 主要测试项目见表C.1
表c.1主要测试项目 人炉石灰总重量 kg/炉 炉 净石灰重量 kg/炉 其 量 中 含水重量 kg/炉 净石灰重量 kg/t 每吨钢水耗量 含水重量 kg/t CaO % 灰 MgO % 净石灰的平均化学成分 Al.O % % SiO 人炉镁砂总重量 kg/炉 炉 净镁砂总重量 加 kg/ 其 量 中 含水重量 kg/炉 净镁砂重量 kg/t 每吨钢水耗量 含水重量 e/儿n MgO % % 砂 CaO 净镁砂平均化学成分 % SiO A.o % 人炉生白云石总重量 kg/炉 炉 /炉 净生白云石总量 kg/ 其 量 中 含水量 kg/炉 净生白云石总量 kg/t 每吨俐水耗量 含水量 kg/ CaO % 净生白云石平均化学成分 SiO. % 9% Al.(O 17
GB/T34476一2017 表c.1(续 人炉萤石总重量 kg/炉 净萤石重量 炉 kg/炉 其 量 中 /炉 含水重量 kg/ 净萤石重量 kg/" 每吨钢水耗量 含水重量 kg/ CaF % Al.O % 净萤石的平均化学成分 CaO MgG % 炉衬侵蚀总重量 kg/炉 每吨钢水侵蚀重量 kg/ CaO % MgO % 平均化学成分 SiO % Al.O 办 氧化铁皮重量 kg/ 敏 每吨钢水氧化铁皮量 kg/t % FeO 平均化学成分 皮 % Fe.O 人炉总量 kg/炉 每吨钢水耗量 kg/t % S 孟 % Mn 平均化学成分 铁 % % F % 人炉总量 kg/炉 每吨钢水耗量 kg/t % Si Mn P % 平均化学成分 铁 % C % F 18
GB/34476一2017 表c.1续 人炉总量 kg/炉 每吨钢水耗量 kg/t % Si Mn % % 平均化学成分 孟 % % % F 人炉总量 lkg/炉 每吨钢水耗量 kg/" A % 化学成分 人炉总量 kg/炉 每吨钢水耗量 kg/t 钢水温度 钢 % Mn % % 水 脱氧出钢前平均化学成分 % % % 出炉总量 kg/炉 净钢渣重量 kg/炉 其中 终渣含钢珠重量 kg/炉 净钢渣重量 kg/t 每吨钢水出量 终渣含钢珠重量 kg/t SiO. % Al.o % 钢 % MnO P, % 查 % MgO 净钢渣平均化学成分 Ca(O % % CaF FeO % % Fe.O TFe叫 % 平均出炉温度 19
GB/T34476一2017 表c.1(续 炉口处表压力 Pa 炉口至烟罩高度 m 炉口周长 mm 环境大气压 Pa o 炉口处平均温度 出炉总量 kg/炉 每吨钢水尘泥重量 kg/t % SiO A.O % Mn(o 炉 P,O % % Mg(O 污 平均化学成分 CaO % 泥 % CaF FeO % FegO TFe 平均出炉温度 喷溅黏结物重量 lkg/炉 每吨钢水喷溅黏结物重量 kg/ SiO % 总 % Al.O % 水 MnO 时 ? 喷 % Mgo 微 平均化学成分 CaO % 黏 结 CaF % 物 % FeO % Fe.O TFe % 平均出炉温度 20
GB/34476一2017 表c.1续 喷渣重量 kg/炉 每吨钢水喷渣重量 kg/t SiO. % Al.o % 吹 MnO % 炼 PO % 过 程 % MgO 平均化学成分 中 % CaO 喷 CaF % 渣 Fe(O % Fe.O % TFe % 平均出炉温度 全炉总氧重量 kg/炉 每吨钢水耗氧重量 kg/t 氧 g 平均温度 平均压力 Pa 炉气温度 CO. % % O CO % 平均化学成分 % N % 人炉总水重量 lg/炉 每吨俐水耗水重量 kg/t 冷 人水 却 平均水温度 出水 蒸发重量 kg/炉 汽 每吨钢水蒸发重量 kg/t 化 蒸发压力 Pa 烟 平均蒸汽温度 道 平均给水温度 21
GB/T34476一2017 表c.1(续 散热面积 m 炉帽 表面平均温度 kJ/ 表面平均面积热流量 m',h 散热面积 m 炉身 表面平均温度 炉 表面平均面积热流量 k/(m'h 体 散 散热面积 m 热 熔池 表面平均温度 表面平均面积热流量 kJ/m'
h 散热面积 m 表面平均温度 炉底 表面平均面积热流量 kJ/m'h 前一炉出钢完毕时 炉 本炉兑铁水时 本炉出钢时 22
转炉热平衡测试与计算方法GB/T34476-2017
转炉是一种冶金设备,广泛应用于钢铁生产中。为了保证炼钢过程的稳定和优质,对转炉内部温度、物质流动等参数进行监测和控制至关重要。其中,热平衡测试是一种常用的手段。
热平衡测试的目的是确定转炉内的热平衡状态,即满足各种化学反应所需的热力学条件。在测试过程中,需要测量转炉内各部分的温度、压力、氧含量等参数,并据此计算出热平衡状态下各个区域的温度和物质组成。
GB/T34476-2017是热平衡测试与计算方法的标准,该标准规定了热平衡测试的基本原理、操作方法、数据处理和结果报告等方面的内容。具体来说,标准要求测试人员应熟悉转炉的结构和工艺,掌握测试仪器的使用方法,严格按照测试步骤进行操作,并对测试数据进行有效处理。
在进行热平衡测试时,需要注意以下几点:
- 测试前应检查测试仪器是否正常运行,校准各种传感器;
- 测试时应保持转炉内的温度、压力等参数稳定,避免因外部干扰导致测试结果不准确;
- 测试结束后,应及时将测试数据进行处理,计算出转炉内各个区域的温度和物质组成;
- 最后,根据测试结果对转炉的操作进行调整,使之满足热平衡状态的要求。
总的来说,热平衡测试是一项非常重要的工作,能够帮助钢铁生产企业提高产品质量、降低生产成本。标准GB/T34476-2017为热平衡测试提供了详细的操作指南,值得相关工作者认真学习和遵循。