GB/T37400.12-2019
重型机械通用技术条件第12部分:涂装
Heavymechanicalgeneraltechnicalspecification—Part12:Painting
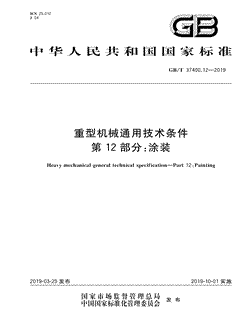
- 中国标准分类号(CCS)J04
- 国际标准分类号(ICS)25.010
- 实施日期2019-10-01
- 文件格式PDF
- 文本页数15页
- 文件大小1.10M
以图片形式预览重型机械通用技术条件第12部分:涂装
重型机械通用技术条件第12部分:涂装
国家标准 GB/T37400.12一2019 重型机械通用技术条件 第12部分:涂装 speeifieaton一Part12;Paintng Heavy mechanicalgeneraltechnical 2019-03-25发布 2019-10-01实施 国家市场监督管理总局 发布 国家标准化管理委员会国家标准
GB:/T37400.12一2019 前 言 GB/T37400《重型机械通用技术条件》分为16个部分 第1部分:产品检验; 第2部分:火焰切割件 第3部分;焊接件; 第4部分;铸铁件 第5部分:有色金属铸件 第6部分;铸钢件 第7部分;铸钢件补焊 第8部分;锻件 第9部分;切削加工件 第10部分 :装配; 第11部分配管 第12部分涂装 第13部分包装 第14部分铸钢件无损探伤 第15部分;锻钢件无损探伤; 第16部分液压系统
本部分为GB/T37400的第12部分
本部分按照GB/T1.12009给出的规则起草
本部分由全国冶金设备标准化技术委员会(sAc/Tc409)提出并归口
本部分起草单位;大连华锐重工集团股份有限公司,太原重工股份有限公司、上海电气上重碾磨特 装设备有限公司、中冶华天南京工程技术有限公司、一重集团有限公司、重型机械研究院股份 公司北方重工集团有限公司、二重(德阳)重型装备有限公司
本部分主要起草人;张光志、郭胜伟、王晓斌、韩成军、姜朋飞、陈志恢、赵敬芳、卫卫、孙保生、 石海军、,谭加、夏娟、王晓鹏、万木春、李多、白敏
GB:/T37400.12一2019 重型机械通用技术条件 第12部分:涂装 范围 GB/T37400的本部分规定了重型机械产品及其零部件的涂装技术要求及检测要求
本部分适用于应用在大气、水或土壤腐蚀环境下的厚度不低于3mm的碳钢和低合金钢产品表面 涂装
规范性引用文件 下列文件对于本文件的应用是必不可少的
凡是注日期的引用文件,仅注日期的版本适用于本文 件
凡是不注日期的引用文件,其最新版本(包括所有的修改单)适用于本文件
GB/T5206色漆和清漆术语和定义 GB/T5210色漆和清漆拉开法附着力试验 GB6514涂装作业安全规程涂漆工艺安全及其通风净化 工业管道的基本识别色、识别符号和安全标识 GB7231 涂装作业安全规程涂漆前处理工艺安全及其通风净化 GB7692 GB/T8264涂装技术术语 GB/T8923.1涂覆涂料前钢材表面处理表面清洁度的目视评定第1部分;未涂覆过的钢材 表面和全面清除原有涂层后的钢材表面的锈蚀等级和处理等级 GB/T8923.2涂覆涂料前钢材表面处理表面清洁度的目视评定第2部分;已涂覆过的钢材 表面局部清除原有涂层后的处理等级 GB/T8923.3涂覆涂料前钢材表面处理表面清洁度的目视评定第3部分;焊缝,边缘和其他 区域的表面缺陷的处理等级 GB/T9286色漆和清漆漆膜的划格试验 GB/T13288.5涂覆涂料前钢材表面处理喷射清理后的钢材表面粗糙度特性第5部分:表面 粗糙度的测定方法复制带法 GB/T17849涂覆涂料前钢材表面处理喷射清理用非金属磨料的试验方法 GB/T18570.3涂覆涂料前钢材表面处理表面清洁度的评定试验第3部分;涂覆涂料前钢材 表面的灰尘评定 GB/T18570.9涂覆涂料前钢材表面处理表面清洁度的评定试验第9部分:水溶性盐的现场 电导率测定法 GB/T30790.2色漆和清漆防护涂料体系对钢结构的防腐蚀保护第2部分;环境分类 GB/T30790.3色漆和清漆防护涂料体系对钢结构的防腐蚀保护第3部分;设计依据 GB/T30790.4色漆和清漆防护涂料体系对钢结构的防腐蚀保护第4部分;表面类型和表面 处理 GB/T30790.5色漆和清漆防护涂料体系对钢结构的防腐蚀保护第5部分:防护涂料体系 SY/T0407涂装前钢材表面预处理规范 GSB05-1426漆膜颜色标准样卡
GB/T37400.12一2019 术语和定义 GB/T5206,GB/T8264界定的术语和定义适用于本文件
技术要求 4.1环境分类 4.1.1为了确保所选防护涂料体系的有效性,应将不同的环境进行分级
与环境腐蚀性等级相关的腐 蚀应力是决定选择何种防护涂料体系的基本参数
4.1.2大气腐蚀性等级宜采用标准试样的暴露试验确定
表1根据低碳钢和/或锌制成的标准试样在 暴露第一年后的质量或厚度损失对腐蚀性等级进行了定义
以钢和锌试样的质量或厚度损失划分环境 腐蚀性等级,有时可能得出不同的结果
在这种情况下,应将其归为腐蚀性较高的等级
如果不能把标 准试样放在所考虑的实际环境中进行暴露,可简单地从表1列出的关于典型环境的示例来考虑评价腐 蚀性等级
列举的示例仅供参考,只有对质量或厚度损失进行实际测量才能确定正确的等级
对于浸 在水中或埋在土壤中的结构,其腐蚀性等级宜参考表2
表】和表2中的环境腐蚀性等拨和典狠环地 示例均应符合GB/T30790.2的相关规定
表1大气腐蚀性等级和典型环境示例 单位面积质量损失/厚度损失 温和气候下典型的环境示例" 低碳钢 锌 腐蚀性等级 外部 内部 质量损失 厚度损失 质量损失 厚度损失 g/m m g/m" m 清洁大气环境 下的保温建筑 C1 10 0.7 物,例如;办公 l.3 0.l 室、商店、学校、 旅馆 低污染水平的大可能发生凝露 气,大多数乡村的不保温建筑 >10且<200 >1.3且25 >0.7且<5 >0.1且s0,7 地区 物,例如;仓库 体育馆 城市和工业大气
高湿度和存在 中度二氧化硫污 -定空气污染 染,低盐度的沿海的生产场所,例 Cc3 且<40o>25且<50 >5且<15>0.7且<2.l 200" 如:食品加工 地区 ,洗衣房、酿 酒厂、牛奶场 工业区和中盐度化工厂、游泳 >400且<650 >50且<8o >15且<30 >2.1且<4.2的沿海地区 池,沿海船舶和 造船厂
GB:/T37400.12一2019 表1(续》 单位面积质量损失/厚度损失" 温和气候下典型的环境示例" 低碳钢 锌 腐蚀性等级 外部 内部 质量掀失 厚度掀失 质量损失 厚度损失 g/m g/m Am Am 高湿度和侵蚀性凝露和高污染 大气的工业区 持续存在的建 C5-I >60且<! >30且<60>4.2且<8.4 500>80且<200 筑物或地区 高盐度的沿海和凝露和高污染 海上区域 持续存在的建 C5-M >650且1500>80且<200 >30且60 >4.2且8.4 筑物或地区 经过第一年暴露后 环境示例仅供参考 表2水和土壤的等级 环境 环境和结构的示例 等级 Iml 淡水 河流设施,水力发电站 港口地区的构筑物(闸门、锁栓、防波堤;海上构筑物 lm2 咸水或微咸水 土壤 埋在地下的储罐、钢桩、钢管 Im3 4.2设计依据 结构的整体设计应有利于进行表面处理、涂装、检查和维护等
结构设计应符合GB/T30790.3的 相关规定
4.3涂装前的表面处理 4.3.1所有用于设备制造的钢铁原材料,涂漆前均应进行表面处理
制件表面缺陷处理应按照 GB/T8923.3的规定,缺陷处理等级不得低于P2级彻底处理:大部分缺陷已被清除)
4.3.2施工前,应检验喷砂、清洁和喷漆等用压缩空气中是否存在油和水,压缩空气中存在油和水不允 许进行施工
若无其他规定,检验方法为压缩空气向白布吹lmin,目测白布表面是否存在油和水
4.3.3除锈前,应先用有机溶剂,碱液、乳化剂、蒸汽等除去钢铁表面的油脂、污垢
若无其他规定,检 验方法为用白布揩拭清除油脂后的试样,白布上留有油脂污迹目测),表明油脂清洁不干净
4.3.4表面处理等级要求见表3和表4
表3和表4均应符合GB/T30790.4的相关规定
GB/T37400.12一2019 表3一次(全面)表面处理的标准处理等级 标准处理表面处GB/8923.1中的 处理后表面的主要特征 应用领域 等级 理方法代表性照片示例 BSa1 附着不牢的氧化皮、锈蚀、涂料涂层和杂物表面处理类型 Sa1 CSa1 等已去除 a)无涂层钢结构表面; DSa1 bb 有涂层钢结构表面(如果 涂层被清理到规定等级的 BSa2 氧化皮,锈蚀,涂料涂层和杂物等已基本去 程度 Sa2 CSa2 除,其残留物应是牢固附着的 DSa2 氧化皮、锈蚀,涂料涂层和杂物等已去除,任 AA Sa21/2 喷射 BSa21/2 何残留的痕迹应仅是点状或条纹状色斑 清理 Sa21/2 CSa21/2 DSa21/2 ASa3 氧化皮、锈蚀、涂料涂层和杂物等已去除,该 BSa3 表面应呈现均匀的金属光泽 Sa3 CSa3 DSa3 附着不牢的氧化皮,锈蚀、涂料涂层租杂物 BSt2 St2 CSt2 等已去除 手工和 DSt2 动力工 BSt3 附着不牢的氧化皮、锈蚀、涂料涂层和杂物 具清理 St3 cSt3 等已去除
除锈应比st2更彻底,金属基材 DSt3 显露出金属光泽 AFT 氧化皮、锈蚀、涂料涂层和杂物等已去除
BF 任何残留的痕迹应仅表现为表面变色(不同 火焰 F CF 颜色的色调 清理 DF 氧化皮、锈蚀和涂料涂层的残余物彻底被去举例:;热没镀锌前 酸洗 Be 除 酸洗前采用合适的方法去除涂料涂层 详细信息,包括表面处理前后的状况见GB/T8923.1
表4二次(局部)表面处理的标准处理等级 GB/T8923.1或 标准处理表面处 处理后表面的主要特征 应用领域 lGB/T8923.2中的 等级 理方法 代表性照片示例 BSa2 牢固附着的涂料涂层应完好无损,表面的其保留部分涂料涂层的钢材表 他部分应去除疏松涂层,大部分氧化皮、锈面的局部清理 CSa2 局部 DSa2 蚀和外来杂质,任何残留污物应牢固附着 PSa2 喷射 (适用于表面无 清理 涂层的部分)
GB:/T37400.12一2019 表4(续》 GB/T8923.1 或 标准处理表面处 (GB/T8923.2中的 应用领域 处理后表面的主要特征" 等级 理方法 代表性照片示例 BSa21/2 牢固附着的涂料涂层应完好无损,表面的其 CSa21/2 他部分应去除疏松涂料涂层、氧化皮、锈蚀 和外来杂质,任何污染物的残留痕迹应仅显 DSa21/2 IPSa21/2 适用于表面无现点状或条状的色斑 局部 涂层的部分) 喷射 清理 牢固附着的涂料涂层应完好无损,表面的其 Sa3 DSa3 他部分应去除疏松涂料涂层、氧化皮、锈蚀 PSa3 (适用于表面无和外来杂质,表面应呈现均匀的金属光泽 涂层的部分) PMa 牢固附着的涂料涂层应完好无损,表面的其 局部 他部分应去除疏松涂料涂层,氧化皮、锈蚀 PMa 机械 和外来杂质,任何污染物的残留痕迹应仅呈 打磨 现点状或条状的色斑 牢固附着的涂料涂层应完好无损,表面的其 CSt2 PSt2 DSt2 他部分应去除附着不牢的氧化皮、锈蚀、涂 局部手 料涂层和外来杂质 工和动 CSt3 牢固附着的涂料涂层应完好无损,表面的其 力工具 DSt3 他部分应去除附着不牢的氧化皮,锈蚀、 涂 Pst3 清理 料涂层和外来杂质
但表面要比PSt2处理 的更彻底,金属基底呈现金属光泽 详细的信息,包括表面处理前后的状况见GB/T8923.2
4.3.5若无其他规定,钢铁表面处理等级及应用领域应按表5执行
表5表面处理方法、表面处理等级及应用领域 表面处理方法 标准处理等级 应用领域 辅助部件或辅助设备及用于轻度腐蚀性环境中的钢铁制件表面; Sa2 与混凝土接触或埋人其中的钢铁制件表面 主要部件或主要设备及用于腐蚀性较强的环境中的钢铁制件表面 San21/2或 喷射清理 长期在潮湿、潮热、盐雾等环境下作业的钢铁制件表面, PSa21/2 与高温接触并且需要涂耐热漆的钢铁制件表面 与液体介质或腐蚀性介质接触的表面,如油箱、减速机箱,水箱等内表面压 Sa3或PSa3 力容器 与高温接触但不需要涂耐热漆的钢铁制件 St2或PS2 手工和动力工具清理 钢铁构件形状特殊无法进行喷丸除锈的部位 St3或PSt3 设备上的各类钢制管道;不能喷丸的薄板件(壁厚小于5mm); R 酸洗 结构复杂的中,小型零件
GB/T37400.12一2019 4.3.6焊接件在组装焊接后需要进行热处理的,应将除锈工序放在热处理之后进行
4.3.7若无其他规定,喷射处理后的表面粗糙度为404m~100m,测试方法按GB/T13288.5进行
4.3.8磨料水浸出液的电导率不大于250As/cm,测试方法按GB/T17849进行
若无其他规定,钢板 表面各种水溶性盐的总表面浓度不超过50mg/m=,测试方法按GB/T18570.9进行
4.3.9涂覆涂料前,应按照GB/T18570.3对钢材表面的灰尘进行检验
若无其他规定,表面残留灰尘 不超过2级
4.3.10经喷丸或手工除锈、动力工具除锈后的待涂表面,应立即涂底漆
一般情况下,间隔时间不超 过4h,保护环境下不超过8h,在海洋露天环境下应不超过2h
酸洗除锈后经过磷化处理的待涂表 面,涂底漆的间隔时间不得小于48h(在冬季寒冷的气候环境下,其间隔时间不得小于72h)
如果涂 渎前发现钢铁表面出现锈蚀,应重新进行表面处理
4.3.11用于制造机器构件的钢铁板材及型材,厚度大于5mm的,应预先进行喷(抛)丸除锈,除锈质量 等级应达到Sa21/2级;厚度小于5mm的,可进行化学处理酸洗、冲洗、中和、钝化或磷化等),其除锈 质量邻级应达到级,酸洗处理方法应拨照附录八的有关规定,并在规定的时间范围内涂保养底漆 车间底漆)
预处理时的漆膜厚度及涂料选择推荐如下 a Mm25 推荐漆膜(干膜)厚度:l5 Mm; b)推荐涂料品种;无机硅酸锌(车间)底漆等; c 所用的底漆是产品配套漆系中的品种或与配套漆系中的底漆相适应的漆种 4.4机器产品的防腐烛涂层设计 44.1机器产品的环境腐蚀性等级见表1和表2
涂层耐久性年限见表6
宜采用面漆颜色见表7
与不同环境腐蚀性等级、不同表面处理等级和涂层耐久性等级相对应的防护涂料体系选择参见 4.4.2 GB/T30790.5
若无其他规定,按低档耐久性年限(2年一5年)进行涂层设计
表6涂层耐久性年限 类别 耐久性年限 高耐久性 15年以上 中耐久性 5年15年 低耐久性 2年~5年 注耐久性年限不是“担保期限”
耐久性年限是为业主制定维护计划时提供技术上的参考
担保期限属于合同 条款,不属于本部分考虑的范
没有规则来闸述这两个期限之间的关联性
4.4.3产品设计工程师应根据表1和表2确定环境腐蚀性等级,根据表7选择产品的主体面漆颜色,并 将所确定的内容在产品图样或技术文件中予以注明[如;“产品使用环境类别为C3,面漆颜色为59橘黄 YR04)”]
4.4.4产品防腐蚀工程师应根据环境腐蚀性等级、耐久性年限、主体面漆颜色等有关参数,进行产品的 防腐蚀设计
该设计包括: 确定涂料配套漆系(涂料品种、涂层厚度); a b)确定产品主体及各部位、各系统颜色 c 编制“产品涂装工艺” 4.4.5选定的涂料配套漆系中的所有涂料,原则上应是同一厂家或同一品牌的产品
为了确保不同涂 层的可追溯性,不同涂层宜采用不同颜色
GB:/T37400.12一2019 4.5机器产品特殊部位的涂装要求 4.5.1不封闭的箱形梁、箱形结构的内表面等,无特殊要求的,一般应涂60m~ 80nm厚的底漆;封闭 的箱形梁、箱形结构的内表面不涂漆,但内表面应清洁不存在水,油脂,污垢等污染物. 4.5.2装配后不能靠近、无法涂装的部位,应在装配前完成涂漆
4.5.3有涂漆要求的有色金属表面,应根据不同情况,选用相适应的底漆,面漆
如锌表面应选用磷化 底漆或磷酸锌底漆等
面漆(或中间漆)要与底漆配套
4.5.4钢制容器内部的涂装无人孔的除外),应根据容器内工作介质的性质选择油漆或涂硬膜防锈 油
不锈钢容器不涂漆
4.5.5工矿车辆冶金车辆的碰头车钩以及转向架中的铸造侧架、铸造摇枕、车轮、轮轴等,如无特殊要 求,应涂清油或清漆,涂层厚度不得低于30m. 4.5.6高强度螺栓联接件结合面,应根据摩擦系数的不同或按图样要求,在喷砂后涂无机富锌底漆,厚 度为601 也可涂刷两层过氯乙烯可剥清漆(两层之间贴一层纱布)加以保护,联接前再将可剥清漆 m 剥除
必要时,表面还应使用薄铁皮加以覆盖
.5.7属下列情况之一的,不应进行涂装 a 产品或部件与混凝土接触或埋人混凝土中的部位、紧贴耐火材料的部位 b 机械加工的配合面、工作面、摩擦面 配管与阀、系的结合面 c 不锈钢制件表面; d 钢丝绳、地脚螺栓及其底板 e 电镀表面、无特殊要求的有色金属表面; 非金属制件表面; g h)外购成品机电配套件表面(电机等》. 4.6涂漆颜色要求 4.6.1机器产品的面漆颜色应符合合同要求
合同中无规定的,宜按表7的推荐选取颜色 表7机器产品宜采用的面漆颜色 产品类别 推荐面漆颜色 热轧设备 30淡绿(G02),24湖绿(BG02)、28苹果绿G01)、32中绿(G04),31艳绿(G03 冷轧设备 24湖绿(BG02),28苹果绿(G01)、40豆绿(GY01),10天)蓝(PB09 装卸机械 59橘黄(YRo4),.60橘红(R05),72中灰(EB02).57棕(YR05) 连铸设备 28苹果绿(G01),38纺绿(GY02),银白,30淡绿(G02) 治炼设备 28苹果绿(G01)73谈灰(B03)黑色 锻压机械 28苹果绿(G01),30淡绿(G0224湖绿(BG02),32中绿(G04、6海蓝(PB05) 矿山设备 28苹果绿(G01),40豆绿(GY01,48淡黄(Y06),60橘红(R05)、黑色 焦炉机械,煤气设备 72中灰(B02),28苹果绿(G01),38纺绿(GY02),淡海铁)蓝(BI1) 工矿车辆 59橘黄(YR04),60橘红(R05)、32中灰(B02)、黑色 冶金车辆 黑色 破碎机械 73淡灰(03
GB/T37400.12一2019 表7(续 产品类别 推荐面漆颜色 造矿烧结设备 38纺绿(GY02 人造板设备 湖绿(BG02) 24 橡胶制品设备 24湖绿(G02) 73淡灰(I03) 水泥制品设备 4.6.2除用户有特殊要求外,“产品涂装工艺说明”中提到的油漆颜色,宜采用GSB05-1426中标示的 颜色 4.6.3机器产品的特殊部位宜按表8的规定选择面漆颜色 表8机器产品特殊部位宜采用的面漆颜色 产品特殊部位名称 面漆颜色 油箱、减速机内壁及其内部零件的涂漆表面 奶油色(Y03 栏杆、扶手 黄色(Y06,07,08) 操纵室的顶棚及内壁 半光浅色漆 操纵室地板 铁红色(R01 盖板,走台板,铺板、楼梯板 与主机同色或绿色(GYo2 机械停止按钮、刹车及停车装置的操纵手柄;机器转动部件的裸露部分,如飞轮、齿 大红色(R03 轮皮带轮等的轮辐部分;指示器上各种表头的极限位置的刻度 4.6.4有危险的机械部位或装置,应涂以宽度约100 mm、 与水平面成45"斜角、颜色为黄、黑相间警示 条纹
同一条棱线两侧的条纹倾斜方向应相反
如果表面面积较小,条纹宽度可以适当缩小,但黄条纹 与黑条纹每种不得少于两条
前述有危险的机械部位或装置包括:各种机械在工作或移动时容易产生 碰撞的部位,如移动式起重机的外伸腿、,起重机的吊钩滑轮侧板、起重臂的顶端、四轮配重;平顶拖车的 排障器及侧面栏杆;门式起重机门架下端;剪板机的压紧装置;冲床的滑块等
4.6.5机器产品配管的面漆颜色应与机器的面漆颜色相同
距机器1m以外的配管颜色,应符合表9 关于基本识别色的规定
且表9应符合GB7231的相关规定 表9八种基本识别色及其色标 输送介质种类 基本识别色 色标(GSB05-1426 水 艳绿 G03 水燕气 大红 R03 B03 谈灰 空" 气 中黄 Y07 气体 酸或碱 P02 紫 可燃液体 棕 YR05 其他液体 黑 氧 淡蓝 PB06
GB:/T37400.12一2019 4.7涂装施工要求 4.7.1环境要求 4.7.1.1一般情况下,涂装施工环境温度不得低于5C,相对湿度应不大于85%,待涂装表面温度应高 于露点温度3C以上
冬季施工,应尽量选用适合低温下施工和固化的油漆
4.7.1.2雨、雪,雾天气及大风等恶劣天气时,不应在室外施工
待涂装表面有结霜、结露的,不应施工
4.7.1.3涂装及固化过程中,涂装件表面温度不应超过55C,漆膜不应在烈日下暴晒
4.7.1.4施工区域应保持空气流通
涂装及固化过程中应无粉尘及其他异物飞扬
4.7.2施工要求 4.7.2.1涂装时,应严格遵守各种涂料对温度、湿度等的要求,遵守重涂间隔时间及调配方法的有关 规定
4.7.2.2施工前,若发现涂料出现胶化、结块等异常现象,应停止调配和施工
4.7.2.3涂装施工过程中,应注意各种施工方法对漆膜的影响
应尽量保证漆膜的均匀,不得漏涂
对 于边、角、夹缝、螺钉头,铆接缝、焊缝等部位应先涂刷,然后再大面积涂装
4.7.2.4 对焊后或装配后无法涂漆的构件部位,应在焊前或组装前涂漆 两种不同颜色的涂层交界处,其界面应明显、整齐
4.7.2.5 4.7.2.6需经常拆装的零件,其相互连接处的油漆面应平整
缝线应明显,不应出现漆膜崩落、界线不 分或漆成一片等现象 4.7.2.7喷涂施工时,应对产品不需涂装的部位应进行遮盖,防止误涂
4.7.2.8机器产品表面是否需要刮腻子,应在图样或技术文件中注明
刮腻子时,应先涂底漆,底漆干 燥后再进行刮腻子操作
刮腻子一般进行1次2次,每次厚度约为0.5 -1mm,局部最大总厚度 mm 不得超过5mm
腻子干燥后应对表面进行打磨,打磨后的腻子表面应平整、光滑、牢固、无裂纹 4.7.2.9机器产品的最后一遍面漆一般应在总装试车完成后再进行涂装
4.7.2.10对安装过程中损坏的漆膜应进行修补
修补前应对表面进行清理
修补部分对周围涂层的 覆盖宽度应不少于50mm(损坏面积较小时,修补的面积应比损坏的面积大一倍以上)
修补应符合相 关工艺或标准的规定
补漆部位的颜色,涂层厚度应与周围的颜色、涂层厚度一致
4.7.2.11油漆施工应遵守相关国家法律法规要求
4.7.3涂装安全及通风要求 4.7.3.1涂装预处理的施工安全及通风要求应按GB7692的有关规定执行
4.7.3.2涂装施工中的安全及通风要求应按GB6514的有关规定执行
涂装质量控制与检测 涂料质量的检测按涂料说明书规定的方法进行,并应符合以下规定 5.1 涂料说明书中规定的检测方法,应符合相关国家标准的规定 a b)对于配套漆系中的涂料,若其说明书中无检测项目或指标,而使用厂防腐蚀工程师认为确有必 要了解的,则涂料供应商应无条件提供由国家质量技术监督部门出具的该项目或指标的检测 报告
5.2涂料供应商在向使用厂提供涂料时,应附带本批次涂料的产品合格证和检测报告,否则涂料使用 厂有权拒收
GB/T37400.12一2019 5.3使用涂料的企业的质量管理部门,对涂料供应商提供的涂料产品质量负有日常监督职责
5.4涂料的调配应严格按照说明书的规定和要求进行
5.5施工时,应经常用湿膜测厚仪测定湿膜厚度,以便更准确地控制干膜厚度
5.6漆膜的干膜厚度检测,应在涂料说明书规定的干燥时间以外进行
5.7漆膜外观应满足以下要求;底漆、中层漆、面漆漆膜不允许有针孔、气泡、裂纹、咬底、渗色、漏涂、流 挂、局部剥落、橘皮等缺陷;面漆表面应平整均匀、漆膜丰满,色泽一致
检查方法经协商可采用肉眼或 用五倍放大镜观察
5.8涂层干膜厚度的检测应在每一涂层干燥后进行
全部涂层涂装完毕后,再检测总干膜厚度
若无 其他规定,检测方法及验收准则按GB/T30790,5执行
检测区域的涂层厚度应满足以下要求 a 所有测量值的算数平均值应大于或等于额定干膜厚度值; 所有测量值应大于或等于额定干膜厚度值的80% c 所有测量点中,低于额定干膜厚度的测量点应不超过总测量点的20% d 所有测量值应低于或等于规定的最大干膜厚度值
如无其他规定,最大干膜厚度值应不超过 额定干膜厚度值的3倍
5.9涂层脱离底材的抗性评定应按以下方法进行:选六块规格为200mm×200mm的试板,经表面处 理后,涂上与产品相同的涂层漆系
抗性评定在漆膜实干后进行(根据用户要求,可分层逐次评定或最 终一次性评定,最终的评定经协商可采用画叉法,划格法或拉开法进行: 画叉法用锋利的刀片或保险刀片在试板表面划一个夹角为60的又,刀痕要划至钢板,然后贴 a 上宽度为25mm的专业压敏胶带,使胶带贴紧漆膜,然后用手迅速扯起,刀痕两边涂层被揭下 的总宽度若不超过2mm即为合格; 划格法;按GB/T9286的相关规定进行评定
其评定结果应不低于附录B中的2级要求 b 拉开法附着力试验;按GB/T5210的相关规定进行评定
无特殊规定时,附着力测量值应大 c 于2MPa
0
GB:/T37400.12一2019 录 附 A 规范性附录 酸洗 A.1适用范围 本附录适用于钢材表面的酸洗处理
A.2质量要求 A.2.1可用化学和电解两种方法做酸洗处理
酸洗后钢材表面应没有肉眼可见的氧化皮、锈和旧 涂层
A.2.2钢材表面的腐蚀程度应适合规定的涂装要求
A.2.3允许酸洗后的钢材表面在颜色的均匀性上受钢材的钢号,原始锈蚀程度、外形、轧制或加工痕迹 以及腐蚀方式的影响
A.3酸洗前的表面处理 A.3.1应按SY/T0407中规定的方法,除掉钢材表面上绝大部分油、油脂、润滑剂和其他污物(不包括 氧化皮、氧化物和锈)
A.3.2宜用工具除锈方法或喷(射)除锈方法,除掉表面上大部分氧化皮、锈和旧涂层,以缩短酸洗除锈 的时间
酸洗方法及要求 A.4.1将钢材表面浸人常温下的硫酸、盐酸或磷酸溶液中,酸洗液中应加人足量缓蚀剂,以减少对基层 金属的腐蚀,直到所有的氧化皮和锈全部除掉后,用淡水充分冲洗,再做钝化处理
A.4.2将钢材表面浸人60C以上、浓度为5%~10%(按重量计)的硫酸溶液中,酸洗液中应加人足量 缓蚀剂,直至所有的氧化皮和锈全部除掉后再用淡水充分冲洗,最后将钢材表面放在80C左右、含 0.3%~0.5%磷酸铁,浓度为1%~2%(按重量计)的磷酸溶液中浸泡1min一5min. A.4.3将钢材表面浸人75C 80C、体积分数为5%的硫酸溶液中,酸洗液中应加人足量缓蚀剂直 至所有的氧化皮和锈全部除掉后再用75C80C的热水冲洗2nmin,最后用85C以上的钝化液浸泡 nmin以上
钝化液中应含有0.75% 6的重铬酸钠或0.5%左右的正磷酸
22 A.4.4将钢材放置在酸或碱电解槽中电解
电解中若工件作为阴极,应做适当处理以防止或减少氨脆 现象的发生
若在碱溶液中进行电解,电解后需用热水充分冲洗,接着在稀磷酸或稀重铬酸盐的溶液中 浸泡,直至残留在表面上的碱迹全部清除为止
A.4.5酸洗处理应满足下列要求 硫酸槽中所溶铁的含量不应超过6%,盐酸槽中所溶铁的含量不应超过10%
a b 用纯净的淡水或燕僧水做溶液或冲洗液
在冲洗过程中,应连续不断地向冲洗槽中注人清水, 使每升水中携带的酸及可溶盐的总量不超过2g 从酸洗槽中取出的钢材应在该槽上方短时悬挂,沥净大部分酸洗液
1
GB/T37400.12一2019 d 酸洗后应除掉有害的酸洗残渣、未发生反应的酸或碱、金属沉积物和其他有害污物
e 酸洗后的钢材应在表面完全干燥后再垒起来
fD 应在可见锈出现之前进行涂装
A.5安全措施 A.5.1应设置足够的通风设施,以保证工作人员的身体健康并应限制氢气的浓度,使其在爆炸的极限 范围以下 A.5.2操作人员应戴护目镜
A.5.3工作人员应穿戴橡皮围裙、橡皮靴子、橡皮手套
A.5.4酸洗和电解过程中所产生的废液的排放,应按国家现行的相关标准执行
酸洗和电解过程所使用的化学药品的搬运和储存应符合国家现行的相关规定 A.5.5 A.5.6应将浓酸缓慢地倒人水或稀酸中,且应边倒边搅动
12
GB:/T37400.12一2019 录 附 B 规范性附录 漆膜划格试验结果分级 总体要求 B.1 漆膜的划格试验结果分级应符合GB/T9286的相关规定
B.2漆膜的划格试验结果分级 漆膜的划格试验结果分级见表B.1
表B.1试验结果分级 发生脱落的十字交叉 明 分级 切割区的表面外观 切割边缘完全平滑,无一格脱落 在切口交叉处有少许涂层脱落,但交叉切割面积受影响不能明显大 于5% 在切口交叉处和/或沿切口边缘有涂层脱落,受影响的交叉切割面 积明显大于5%,但不能明显大于15% 涂层沿切割边缘部分或全部以大碎片脱落,和/或在格子不同部位 上部分或全部剥落,受影响的交叉切割面积明显大于15%,但不能 明显大于35% 涂层沿切割边缘大碎片脱落,和/或一些方格部分或全部出现脱落 受影响的交叉切割面积明显大于35%,但不能明显大于65% 剥落的程度超过4级 13
重型机械通用技术条件第12部分:涂装GB/T37400.12-2019
涂装是重型机械制造过程中必不可少的一环。为保护机器表面,提高耐久性,防止腐蚀和氧化,涂装工艺显得十分重要。
事实上,关于重型机械涂装的相关规定已经被整合在了《重型机械通用技术条件》标准中,其中第12部分便是《重型机械通用技术条件第12部分:涂装》(GB/T37400.12-2019)。
涂装工艺与要求
标准中明确规定了重型机械的涂装工艺和要求,包括了底漆、中间漆和面漆的涂装顺序、前后涂装之间的时间间隔、干燥和固化等详细步骤。
此外,标准还规定了各种涂料的使用条件、膜厚、表面处理质量要求等,以确保涂层质量达到国际标准,并且具有足够的抗腐蚀性能和耐久性。
检测方法
标准明确规定了重型机械涂装的检测方法,包括对于涂层外观、厚度、硬度、附着力、耐热性、耐候性、耐盐雾腐蚀性等指标的检测方法和要求。
通过这些检测方法,可以有效地验证涂层是否符合标准的质量要求,并提供了一定的技术支持和保障。
应用与意义
GB/T37400.12-2019标准的出台,对于重型机械制造行业有着重要的意义。它不仅规范了涂装工艺和涂层质量的要求,还为相关企业提供了标准化的技术支持,提高了产品质量和企业信誉度。
此外,该标准的实施还有利于加强行业内的合作与交流,促进重型机械行业的发展和创新。
结语
总之,《重型机械通用技术条件第12部分:涂装》(GB/T37400.12-2019)是一项非常重要的行业标准,对于确保重型机械涂装质量、提高产品质量和促进行业发展都有着积极的意义。在今后的生产中,企业应该严格按照标准的要求进行涂装工艺和检测,不断提高产品质量和市场竞争力,为行业的发展做出更大的贡献。