GB/T37400.11-2019
重型机械通用技术条件第11部分:配管
Heavymechanicalgeneraltechnicalspecification—Part11:Piping
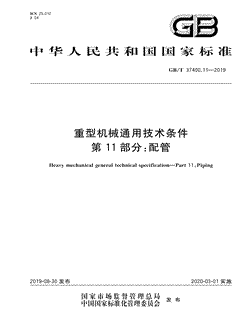
- 中国标准分类号(CCS)J04
- 国际标准分类号(ICS)25.010
- 实施日期2020-03-01
- 文件格式PDF
- 文本页数17页
- 文件大小1.37M
以图片形式预览重型机械通用技术条件第11部分:配管
重型机械通用技术条件第11部分:配管
国家标准 GB/T37400.11一2019 重型机械通用技术条件 第 11部分:配管 Heavy mechaniteallgeneraltehmiealspecifieation一Part11iping 2019-08-30发布 2020-03-01实施 国家市场监督管理总局 发布 国家标准化管理委员会国家标准
GB:/T37400.11一2019 前 言 GB/T37400《重型机械通用技术条件》分为16个部分 第1部分:产品检验; 第2部分:火焰切割件 第3部分;焊接件; 第4部分;铸铁件 第5部分:有色金属铸件 第6部分;铸钢件 第7部分;铸钢件补焊 第8部分;锻件 第9部分;切削加工件 第10部分 :装配; 第11部分配管 第12部分涂装 第13部分包装 第14部分铸钢件无损探伤 第15部分;锻钢件无损探伤; 第16部分液压系统
本部分为GB/T37400的第11部分
本部分按照GB/T1.12009给出的规则起草
本部分由全国冶金设备标准化技术委员会(sAc/Tc409)提出并归口
本部分起草单位;一重集团大连工程技术有限公司、中冶陕压重工设备有限公司、常州宝菱重工机 械有限公司、中冶华天南京工程技术有限公司、太原重型机械集团工程技术研发有限公司、上海电气上 重碾磨特装设备有限公司、重型机械研究院股份公司、二重(德阳)重型装备有限公司
本部分主要起草人;王霞、温长山,刘震,李雪民、杨晓鸥苍、张辉、孔念荣、朱国敏、卫卫、何家宝、 黄苹、张英蝉、常远、朱志荣、唐保国、夏娟、毕鹏、邵鞠民
GB:/T37400.11一2019 重型机械通用技术条件 第11部分:配管 范围 GB/T37400的本部分规定了重型机械配管的技术和安全要求
本部分适用于重型机械产品本体上的油润滑、脂润滑、液压、气动和工业用水配管 本部分不适用于压力容器配管
规范性引用文件 下列文件对于本文件的应用是必不可少的
凡是注日期的引用文件,仅注日期的版本适用于本文 件
凡是不注日期的引用文件,其最新版本(包括所有的修改单)适用于本文件
GB/T324焊缝符号表示法 GB/T3765卡套式管接头技术条件 GB/T7306.155'密封管螺纹第1部分;圆柱内螺纹与圆锥外螺纹 GB/T7306.25"密封管螺纹第2部分;圆雏内螺纹与圆维外螺纹 GB 7307 55"非密封管螺纹 "封管螺纹 GB 12716 GB/T14383钢制承插焊和螺纹管件 GB/T37400.1重型机械通用技术条件第1部分产品检验 重型机械通用技术条件第3部分;焊接件 GB/T37400.32019 重型机械通用技术条件第12部分涂装 GB/T37400.122019 GB/T37400.16重型机械通用技术条件第16部分液压系统 管路制作技术要求 3.1管材、零部件配管前的检查 3.1.1制造厂自制的零部件,应经质量检验部门检验合格后方可装配
3.1.2外购的材料和零部件,应符合GB/T37400.1的有关规定
3.1.3确认管子的管径、材质及壁厚符合要求
3.2管子切割 管子应优先采用锯切割或机械加工方法,不准许采用砂轮切割和火焰切割
切割管子断面的垂直 度应符合表1的规定
GB/T37400.11一2019 表1管子断面垂直度 项目 图示 要求 断面与管子轴线垂直度 Aa<30 3.3管子的弯曲加工 3.3.1管子的弯曲一般采用冷弯,即在专用的弯管机上常温下进行
冷弯管的弯曲半径R应按图1、 表2规定
管子热弯时,应符合GB/T37400. -2019的有关规定
图 表2钢管的弯曲半径 单位为毫米 管子外径 弯曲半径R 6<<12 壁厚>1.0时,最小2×管子外径 12<内<48 所有壁厚,最小2×管子外径 48<114 所有壁厚,最小2.5×管子外径 3.3.2管子外径D小于30mm时,圆度公差E不大于10%,应符合图2和式(1)的规定,并不准许出 现波纹、皱褶和扭曲;管子外径D不小于30mm时,圆度公差及波纹深度应符合GB/37400.3-2019 附录A中表A.3的规定
图2 E= ×100% D
GB:/T37400.11一2019 式中 E 圆度公差,% 长轴直径,单位为毫米(mm) 短轴直径,单位为毫米(mm); D 管子外径,单位为毫米(mm) 3.3.3管子冷弯曲壁厚减薄率C不大于15%,按式(2)计算: 工一工xim 式中: 辟厚减薄率,%; 弯曲前管子壁厚,单位为毫米(mm) T -弯曲后管子壁厚,单位为毫米(mm). 注:用钢管做试件弯曲后解剖检查,也可用超声波测厚仪检查 管子弯曲对于未完全确定尺寸,但应确保其功能,长度未注公差应符合表3中的C级;对于完全 3.3.4 确定了尺寸的长度未注公差应符合表3中的B级
角度未注公差全部按表4中的B级
表3长度尺寸公差 单位为毫米 长度尺寸范围 >120 >400 >1000 >2000 >8000>12000>16000 公差 30 4000 30 等级 120 400 l000 2000 4000 8000~12000160002000020000 极限偏差 土1 士2 士2 土3 土4 士6 士8 士10 士12 士14 士16 士3 士4 士6 士8 士11 士14 士18 士21 士24 士27 士l 注:长度尺寸指的是外部尺寸、内部尺寸、台肩尺寸、弯曲直径和弯曲半径
表4角度尺寸公差 公称尺寸范围/mm 公差等级 二400 4001000 1000 400 >4001000 >1000 允许偏差 允许偏差的正切值/" /mm 士45'" 士30 士20' 0.013 0.009 0.006 士1 士45 士30'" 0.018 0.013 0.009 注:角度尺寸公差的公称尺寸范围是指的短边长度
3.3.5弯制焊接钢管时,应使焊缝位于弯曲方向的侧面
3.4管路装配前要求 3.4.1装配前所有管子应去除管端飞边、毛刺并倒角
用压缩空气或其他方法清除管子内壁附着的杂 物及浮锈
不锈钢管路的制作与碳钢管路的制作应有效隔离,使用专用的制作工具,防止不锈钢管路受 到污染
管子下料时,应考虑留有足够的余量,便于弯曲夹持,调整补偿
3.4.2安装接头时应注意螺纹的清洁、润滑
安装不锈钢接头时,螺纹及接头锁紧螺母的接触面应涂
GB/T37400.11一2019 上足够的润滑剂,以防止接头锁死
安装所有管路元件时均应参考制造厂家的说明书或样本,确保安装 后的管路元件工作有效可靠
3.4.3使用由两种不同材料制成的法兰或接头,留在管子上的部分(无法拆卸的法兰和焊接接头)出于 酸洗的原因应与管子的材料相同
酸洗之前可以拆卸下来的所有管路元件(分体法兰等)均可用表面处 理过的(镀锌、镀铬、镀镍等)钢制成
3.4.4管螺纹加工应分别符合GB/T7306.1,GB/T7306.2,GB/T7307和GB/T12716的规定
3.4.5用于固定的管夹、支座等部件的机体表面应平直,不应影响管路整齐排列否则应修整
预制完 成的管路在储运过程中应防止磕碰,踩压和弯曲变形
3.4.6装配前,所有碳钢管(精密钢管除外)及碳钢管预制成型的管路都要进行酸洗、中和、清洗吹干及 防锈处理;镀锌管、铜管及不焊接的不锈钢管不酸洗,不防锈;焊后的不锈钢管只酸洗,不防锈
酸洗除 锈等级要达到GB/T37400.122019中规定的Be级
为了不使防锈漆产生化学分解,在酸洗磷化处 理48h后,外表面才可涂防锈漆,同时应尽快在酸洗后的碳钢管内壁涂上挥发性防锈油进行防锈,也可 在管子内部喷灌混合防锈油(按管子内部体积估算,喷灌量>100mL/m=),并及时封口,磷化膜的质量 应保证包装,涂装前不生锈
涂装应符合GB/T37400.12一2019有关规定
3.5管路装配要求 对于管路未完全确定尺寸、自由敷设的管路,但应确保其功能,长度和角度尺寸未注公差应符合 3.5.1 表3,表4中的C级;对于完全确定了尺寸的管路《例如;配管详图、预制品图等),长度和角度尺寸未注 公差应符合表3、表4中的B级
管路的直线度、平面度、平行度公差应符合表5中的F级
表5直线度、平面度,平行度 单位为毫米 公称尺寸范围 >30 >120 >400 >l000 >2000 >4000>8000 >12000 l6000 公差等级 120 一400 一1000 20004000 一8000~12000~16000~2000o20000 极限偏差 4.5 10 12 14 16 1.5 注:公称尺寸范围是指的平面的长边长度
3.5.2装配时,对管夹、支座、法兰及接头等用螺纹连接固定的部位要拧紧,防止松动
3.5.3若使用端面带有弹性密封件的旋人式接头,则不准许另外使用密封剂密封
对于端面不带弹性 密封件的接头和螺纹配件应根据工作压力选择相应的密封剂进行密封
3.5.4所有阀门仪表、液压缸或气缸接口的连接孔以及阀块接口在最终安装之前,都应使用合适的工 具(例如垫圈、盖子、胶带),以避免对控制部件造成污染
因检验和安装打开的连接孔,应在操作结束 后立即重新封闭
3.5.5用胶带密封的螺纹接头不得留有胶带毛边
密封带缠绕时,应保持密封带清洁,不许黏附灰尘 及其他杂物
3.5.6管螺纹部位缠绕密封带时,应顺螺纹旋向从根部向前右缠绕,管端剩1牙~2牙,见图3
对小于 3/8的管螺纹在缠绕密封胶带时,用1/2胶带宽度进行缠绕
GB:/T37400.11一2019 胶带走向 密封胶费e 缠绕方向 收拉电一送 图3 3.5.7已密封的零件需修复时,要将内、外螺纹上附着的密封带完全除去
3.5.8采用卡套式管接头连接用碳钢无缝管应是精密冷拔正火状态,不锈钢无缝钢管是退火状态
卡 套式管接头的安装应按GB/T3765的要求
装配时各接触部位涂少量润滑油,且保证卡套在管端上沿 轴向不窜动,径向能稍转动
3.5.9完全按图样预装完成的管路,应结合总装要求,留出调整管,最后确定尺寸
3.5.10固定管件用的支架,管夹等,若图纸中未规定布置方式,管子外径>25mm时两个固定点的间 距不得超过表6中给出的数值
管子外径<25mm的管夹装配位置及装配方法见附录A
在会松开 的连接件和弯管旁亦应加装固定件
具体位置可按实际需要调整
焊接的管夹采用角焊缝a=0.31(t 为垫板厚度). 表6管路固定点间距 管子外径/mm" 38<<89 >89 25<币38 2.5 3.0 最大间距/m 1.5 3.5.11机体上排列的各种管路应互不干涉,又便于拆装
同平面交叉的管路不得接触
自重回油管 道,在配管时应有最小1:100的斜度
3.6管路密封及耐压试验 3.6.1预制完成的管子焊接部位均应进行耐压试验
液压管路试验压力为工作压力的1.5倍,气动管 路试验压力为工作压力的l.15倍,其他管路试验压力为工作压力的1.25倍,保压15min,应无泄漏及 其他异常现象发生
试验完成的管子应做标记 3.6.2应对装配完成的管路按不同的系统做密封及耐压试验,并应符合以下要求 对脂涧滑管路,在工作压力下进行通油试验,确保各分配器指针灵活无卡阻,各连接处无泄漏 a b 油润滑系统管路以工作压力的1.25倍进行压力试验,保压15min,再降至工作压力进行全面 检查,应无泄漏及其他异常现象发生; 对气压系统管路,以工作压力的1.15倍进行压力试验,保压15min,再降至工作压力进行全面 检查应无泄漏和变形; 除合同、设计技术文件有特定要求注明外液压及工业用水系统管路试验压力应符合表7要 d 求
保压15min,应无泄漏
表7液压及工业用水系统管路试验压力 16.0 16.031.5 >31.5 系统工作压力p./MPa 试验压力 l.50 1.25 1.15
GB/T37400.11一2019 3.7管路清洗 3.7.1应按以下要求执行清洗前的准备工作: 确认管子的材质和耐压试验后的打印标记 a 拆卸安装在管子上的零件(阀门、计量仪、压力表、流量计和螺栓等) b 拆下各类密封环、密封圈,各螺纹部位的密封面应作好防腐处理(如涂聚乙烯或包上绝缘带)
c 3.7.2管路清洗检验应符合以下要求: 工业用水管路经酸洗、预装完成后,要进行通水冲洗检验(阀类件除外),保证达到管路清洁度 a 要求,见表8
表8管路清洁度要求 管路名称 人口压力,流量 出口处液体状态 出口液体过滤要求 备注 选择适当的压力和液柱离开管口水平用180目~240目的过滤在冲洗过程中,用木棒 等通径的工业 于 网接2min目测,无残留或塑料棒逐段敲击,使 流量,使管内液体达喷射长度不小 用水管路 到奈流状态 物为合格 杂质冲洗下去 100mm b 脂润滑系统,在配管完成后,拆下各给脂装置(分配阀等人口的连接,进行油脂清洗
直至流 出的油脂清洁无异色后再进行连接
油润滑系统应通油清洗清洗一段时间后用清洗液清洗过的烧杯或玻璃杯采100ml的清洗 液放在明亮场所30min后,目测确认无杂质后为合格
d 液压系统及伺服系统的清洗检验及清洁度应符合GB/T37400.16要求
3.8管路拆卸及包装发运 3.8.1拆卸工作量应减少到最低程度
应确保用于输送氧气的管道上绝对没有油、脂
碳钢管应在管 子内壁涂上挥发性防锈油或采用其他防锈措施,然后对管道和输送流体元件进行快速封闭(例如:在法 兰处使用钢板和软密封件),确保其内部不会再受到污染
没有法兰的末端可以使用塑料盖
精密型钢 管应使用带有24"内锥的封闭件或塞子封堵
并拴标签
标签上记人装配位置号
3.8.2对分解包装发运的管路,应将设计图样给出的标记打印在标签上,并拴在管路上
标签推荐采 用外形尺寸在50nmm×30mm铜板或铝板制造,也可以采用其他材质和尺寸的标签
3.8.3对于需在海上长途运输的应在管道内注人气雾防锈剂,防止管道受潮生锈
3.9配管资料 应注意在配管制作过程中的资料收集,包括配管酸洗报告、耐压试验报告、管路冲洗清洁度报告等 留档备查
配管焊接技术要求 焊工应经过专业培训,具有职业资格等级证,方可持证上岗,担任配管的焊接工作
4. 4.2焊接前应确保焊缝区域表面上没有氧化皮、炉渣、铁锈、油漆、油脂及水等杂物
进行整焊之前,应 清除定位点焊中的裂纹、熔合缺陷和气孔巢
预制管需打磨焊接区域(管路内外表面),焊缝两边各大于 20mm, n,且不锈钢管需用专用砂轮片打磨
4.3根据焊接工艺,进行合理的焊前预处理(例如;坡口角度、钝边大小等)
管路对接及角接焊的坡口
GB:/T37400.11一2019 形状、尺寸见表9.
表9对接及角接焊缝预处理措施 管壁厚; 焊缝符号 根部间隙”b 焊缝名称 破口形式、角焊缝示意图 (GB/T324) mm mmm 2.0 I形焊缝 03 ~60 2.0<1<25 Y形焊缝 U形焊缝 25 六60 15 23 带V形根部 单边V 02 所有 形焊缝 所有 角焊缝 2.5MPa 该数值适用于已完成定位点焊的状态
4.4焊缝施工的基本原则对接焊缝中力作用线上的应力应均匀分布
如果没有为对接焊缝标注横截 面尺寸,则应全焊透
封闭管道内部的所有焊缝都应是连续焊缝,中间不得断开
如果壁厚允许,所有 焊缝都应多层焊接
在对高压管道进行手工电弧焊时,在中间层和覆盖层区域只能使用碱性焊条
应 彻底清除加固件、运输吊环等的辅助焊接
应对相关部位的表面进行无凹槽打磨,且应采用合适的方法 检验是否存在裂纹
不得因打磨而低于所需的壁厚
4.5对于碳钢管路,压力不大于2.5MPa时,应采用角焊缝焊接,压力大于2.5MPa时,应采用单V形 坡口焊缝 4.6管道内部不准许出现焊渣
所以焊接钢管时包括定位点焊),一般应采用钨极氧弧焊或钨极氯弧 焊打底,同时应在管内部通约5L/min氯气
焊缝单面焊双面成型
焊缝不得有未熔合、未焊透,夹渣 等缺陷
有缺陷的焊缝应清除缺陷后再补焊
补焊焊缝应整齐一致并应去除表面飞溅物
因焊缝根部 余高造成的管道断面收缩率,管道外径不大于25mm时,不超过20%;若管道外径大于25mm,则不超 过15%
这种情况可通过目视方法进行检查,必要时应通过磨削加工处理
GB/T37400.11一2019 4.7管与管(或接头)对接焊的错位公差e不大于0.101,最大不超过1.0mm,见图4
对于错位公差 超过此要求的对接焊部位,建议采用机械加工方式将接头内孔加工成锥度不大于10"的过渡锥面,再进 行焊接
图4 4.8管子与法兰插人焊焊接要求见图5(适用于t<16mm)、式(3)、式(4)与式(5)
单位为毫米 (02 钢管 图5 K1=(1.01.4)t 式中 K 外侧焊脚高,单位为毫米(mm); 管壁厚,单位为毫米(mm)
K=(0.751.0)1 式中 K 内侧焊脚高,单位为毫米(mm); 管壁厚,单位为毫米(mm)
L =K
十(02) 式中 -管插人后的余量,单位为毫米(n mm K 内侧焊脚高,单位为毫米(G mm; -管壁厚,单位为毫米(mm)
4.9焊接法兰时,如图样无特殊要求,其螺栓孔中心线不得与管子的铅垂,水平中心线相重合,而应如 图6所示对称配置,且每个法兰上的螺孔数都能被4整除
焊接后,螺栓孔的位置偏差Aa不应大于 30'或应符合表10规定的公差a值
GB:/T37400.11一2019 图6 表10螺栓孔的位置偏差 单位为毫米 螺孔直径 公差 图示 <1.5 26 4.10法兰等管件的焊接角度公差应符合表4中的B级,见图7中的角度公差示例
上工 图7 4.11支管焊接在主管上,除设计注明外,其支管中心线对主管中心线左或右的偏差AA不大于1nmm 见图8
图8 角度及垂直度偏差Aa按表4中的B级,见图9
GB/T37400.11一2019 支管角尺 图9 4.12支架焊接后的尺寸公差和几何公差应符合GB/T37400.3一2019中8.3未注公差的规定
4.13管子对接焊时,焊缝外凸高a和内凸高b应符合表11规定值;当焊缝外凸高a和内凸高超差 时,应用砂轮修磨达到要求
表11焊缝外凸高和内凸高 单位为毫米 外凸高 管壁厚 内凸高 图示 0.51.5 0~l.0 1225 0.52.5 4.14 管路焊缝的评定按照GB/T37400.32019中的表9中规定的评定等级,即:压力不大于 2.5MPa,则按照评定等级D施工(仅GB/T37400.3一2019中表B.1的序号9按照评定等级C);压力 大于2.5MPa,则按照评定等级C施工;如有特殊要求,则无论压力等级如何,都应按照评定等级B进行 焊缝施工,此时应在图样上注明
管路煤缝的检验.所有等级焊缝需执行100%目视检验;B级焊缝x光检验不小于25%,C级焊 4.15 缝X光检验不小于10%,也可以使用等效的内部特性检验方法代替X光检验;压力及密封检验按3.6 规定执行
4.16焊接时的注意事项应符合以下要求 当钢管温度低于0C时,不应焊接;碳钢管路(壁厚不小于30mm)焊前应进行预热处理,预热 a 温度100C左右; b 焊接位置宜采用平焊; c 不应在管子上打火引弧; d 不同焊层的起点和终点不得集中在一处;应错开10mm一20mm; 在下次焊层开始焊接前,应彻底清除焊渣和各种缺陷 e 清除咬边、凹坑等缺陷时,应在缺陷前后10mm一20mm范围内用砂轮打磨扩展,然后进行 f) 补焊
5 安全要求 5.1配管安全要求 5.1.1高处配管,应准备好脚手架,防护网及防护人员的双扣安全带等安全物品
10
GB:/T37400.11一2019 5.1.2不应用配管的管路、系、阀及管路附件做脚手架和攀登物
5.1.3应避免上、下两层同时作业,若必须进行时,应提前联系好、戴安全帽、两层中间放置可靠的隔离 物
以防工具等物坠落伤人
5.1.4使用弯管机、切割机等机床工具时,应按设备操作规程进行,不准许违章作业
5.2悍接安全要求 5.2.1应严格按焊接安全操作规程的有关规定进行施工 5.2.2不应用管路(特别是装有易燃介质的管路)作为地线
5.2.3为防止弧光伤害,除焊工戴好防护用具外,对周围的人应设遮光装置
5.2.4与焊工配合的其他操作者,在施工时应戴好防护眼镜
5.2.5焊接镀锌钢管或钢板时,可能引起氧化锌中毒
除戴防毒口罩外,焊接区域(热影响区域)注意 先要去锌,作业场所还应注意通风排气
因火花可能造成火灾或爆炸危险时,应采取防止火花落下措施或请专人看守,准备好消防器材
5.2.6 5.3试压安全要求 试压前应仔细检查预制件螺纹紧固及支架的牢固性,防止试压时由于支架不稳造成不良后果
5.3.1 试压现场应有明显的标志,不准许非工作人员进人试压区域内,试压件四周应设置防护板
5.3.2 泵 和操作人员应距防护板5m~10m. 5.3.3试压应有专人指挥,专人操作
5.3.4试压时应逐级增压(5MPa为一级),每级持续2min一3min,不应超压,仔细检查焊缝及管路连 接处的泄漏情况,确认无异常后方可进行升压工作
达到试验压力后,保压时间按3.6的规定
5.3.5管路应设放气阀,充液体的管路内气体应排尽,泵和管路末端各装一块压力表(刻度极限值应大 于试验压力的1.5倍). 5.3.6试压时,若发现有异常现象应立即停止试验,查明原因并及时处理
5.3.7试压过程中,不应敲击振动及焊补焊缝
5.3.8试压过程中,若发现有泄漏处应先卸压,确认无压力后再进行处理,对处理完成情况进行确认后 再重新开始试压
11
GB/T37400.11一2019 附 录 A 规范性附录) 管夹装配位置及装配方法 范围 A.1 本附录适用于管子外径不大于25mm配管用管夹的装配
连续直线配管没有管接头的场合 A.2.1水平配管时,间隔应小于1500mm,见图A.1
单位为毫米 1500 图A.1 A.2.2垂直配管时,间隔应小于2000mm,见图A.2. 单位为毫米 2000 图A.2 A.3连续直线配管有管接头的场合 A.3.1水平配管时 接头间隔为600mm1500mm时,按图A.3装配; a b) 接头间隔为300mm一600mm时,按图A.4装配; 接头间隔不大于300mm时,按图A.5装配
c 12
GB:/T37400.11一2019 单位为毫米 100150 100150 甲 600~1500 图A.3 单位为毫米 100~150 10015O 中 中由 300600 图A.4 单位为毫米 串 300 图A.5 A.3.2垂直配管时: a 接头间隔为600" mm~2000mm时,按图A.6装配; b)接头间隔为300" mm600mm时,按图A.4装配; 接头间隔不大于300mm时,按图A.5装配 c 单位为毫米 00150 1150 母舟 母中 602000 图A.6 A.4非直线配管的场合 A41当L,不大于300mm,且L不大于350mm时,按图A.7装配;当L,大于300mm,且L
大于 350mm时,按图A.8装配 13
GB/T37400.11一2019 单位为毫米 300 -中 10015Q 3wos0 图A.7 单位为毫米 L>300 -中一[ 1015O800-35O 副 图A.8 A.4.2其他情况的配管按图A.9和图A.10装配管夹
单位为毫米 岛" 00~15O m一1团2o 350 0015O 图A.9 单位为毫米 200-350 虎 鼻 - 200-350 1000 图A.10 14
GB:/T37400.11一2019 A.5运转时管夹位置确定 运转时包括试运转),管子的振动振幅大于1mm时,应在其发生最大振幅附近装配管夹 A.6管夹垫板的焊接方式 管夹垫板根据实际情况可按图A.11所示进行断续焊
单位为毫米 20 D<48 图A.11
重型机械通用技术条件第11部分:配管GB/T37400.11-2019
重型机械在使用过程中需要进行各种液压、气动等系统的控制,而这些系统涉及到的管路布置和连接方式等方面的要求,由国家制定了《重型机械通用技术条件》标准,其中第11部分为配管标准,即GB/T37400.11-2019标准。
GB/T37400.11-2019标准概述
GB/T37400.11-2019标准规定了重型机械在配管过程中所需遵循的基本要求、技术要求及检验方法等方面的内容。
1.基本要求
GB/T37400.11-2019标准明确了配管过程中应遵循的基本要求,包括:
- 应根据工作流体积、流速等要求选择合适的管路规格和材料;
- 应根据各个系统的连接要求进行管路的布置和连接;
- 应遵循相关安全标准,保证管路的安全性和可靠性;
- 应对管路进行清洗、压力试验等必要的检查和测试。
2.技术要求
GB/T37400.11-2019标准还规定了重型机械配管过程中的技术要求,主要包括:
- 管路的材料应符合相关标准的要求,并且应有相应的防腐蚀措施;
- 管路的布置应符合相关的工作要求,并且应设置支架和吊具等支撑设施;
- 管路的连接方式应符合相关标准,并且应进行严密的密封处理;
- 管路的清洗和试验应符合相关标准,并且应记录相关数据和结果。
3.检验方法
为确保配管质量和可靠性,GB/T37400.11-2019标准还制定了相应的检验方法,包括外观检查、尺寸检查、连接检查、压力试验等环节。
结语
配管是重型机械液压、气动系统中不可或缺的一部分,其质量和可靠性直接影响到整机的工作效率和安全性。GB/T37400.11-2019标准对于重型机械配管过程中的基本要求、技术要求及检验方法等做出了明确规定,为重型机械制造企业提供了重要的参考依据。