GB/T34349-2017
输气管道内腐蚀外检测方法
Externalinspectionmethodologyforinternalcorrosionofnaturalgaspipelines
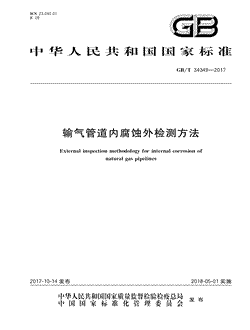
- 中国标准分类号(CCS)E29
- 国际标准分类号(ICS)23.040.01
- 实施日期2018-05-01
- 文件格式PDF
- 文本页数18页
- 文件大小1.41M
以图片形式预览输气管道内腐蚀外检测方法
输气管道内腐蚀外检测方法
GB/34349一2017 前 言 本标准按照GB/T1.1一2009给出的规则起草
本标准由全国锅炉压力容器标准化技术委员会(SAC/TC262)提出并归口
本标准起草单位:特种设备检测研究院、北京交通大学,北京科技大学、大庆油田特种设备检验 中心、广东大鹏液化天然气有限公司、深圳市燃气集团股份有限公司、石油天然气股份有限公司塔 里木油田分公司、石油天然气股份有限公司长庆油田分公司第一采气厂,大庆油田有限责任公司天 然气分公司、石油化工股份有限公司中原油田普光分公司、石油天然气管道科学研究院、重庆 市特种设备检测研究院、上海市质量技术监督局
本标准主要起草人:杨永、何仁洋、马红莲、兰惠清、李晓刚、吴亚滨、单洪翔、王良军、陈秋雄、 王笑梅、周卫军、党晓峰,田一华、郭强、徐昌学,王力,王善江
GB/34349一2017 输气管道内腐蚀外检测方法 范围 本标准规定了埋地钢质输气管道内腐蚀外检测的内容、方法及程序,包括总则、数据收集、腐蚀位置 预测、开挖检测、检测周期确定、记录和报告及附录等内容
本标准适用于因短期异常而存在少量液态水(或其他电解质)的干气输送管道
地面敷设输气钢质 管道内腐蚀外检测可参照本标准执行
规范性引用文件 下列文件对于本文件的应用是必不可少的
凡是注日期的引用文件,仅注日期的版本适用于本文 件
凡是不注日期的引用文件,其最新版本(包括所有的修改版)适用于本文件
GB/T17747(所有部分天然气压缩因子的计算 GB/T19285埋地钢质管道腐蚀防护工程检验 GB/T19624在用含缺陷压力容器安全评定 GB/T30582基于风险的理地钢质管道外损伤检验与评价 压力管道定期检验规则 长输(油气)管道 TSGD7003 术语、定义和符号 3.1术语和定义 下列术语和定义适用于本文件
3.1.1 干气drygas 高于露点温度且不含凝析液体的气体
3.1.2 管道内腐蚀外检测internalcorrosionexternalinspeetionforpipeline 从管道外部对管道内壁腐蚀情况进行检测的方法,包括数据收集、腐蚀位置预测、开挖检测及检测 周期确定等步骤
3.1.3 临界倾角criticalinelinationangle 流动模型计算出的层流条件下气体不发生携液的最小倾角
3.1.4 实际倾角inelinationangle 管道上两点间高程变化形成的角度
3.1.5 检测区段inspeetonregiom 开展内腐蚀外检测的管道上,有类似的物理特征和运行参数,流体特性没有显著变化的一段连续管 道(包括焊缝
GB/T34349一2017 3.2符号 下列符号适用于本文件
-管道内径,单位为毫米(mm); did 重力加速度,取9.81m/s; M 气体分子量,单位为克每摩尔(g/mol): P 操作压力,单位为兆帕(MPa); P -标准大气压力,取0.101325MPa; STp 流量,单位为千标立方米每小时(kNm'/h); Q 理想标准气体常数,取8.314Pa”m'/(Kmol); S -管道内截面积,单位为平方毫米(mm'); T 介质操作温度,单位为摄氏度(); T 气体标准状态温度,取0C; sTP 表观气速,单位为米每秒(m/s); 气体压缩因子,无量纲[不同条件下的天然气的Z值可依据GB/T17747(所有部分)计算或 查询相关专业文献] -实际倾角,单位为度(); -临界倾角,单位为度('); -气体密度,单位为千克每立方米(kg/m); P 液体密度,单位为千克每立方米(kg/m')5 9 H -测点间的高程差,单位为米( m; L -测点间的直线距离,单位为米( m 总则 4.1输气管道内腐蚀外检测工作应满足TSGD7003等国家相关法规标准的规定
4.2本标准提供一套流程化的管道内腐蚀检测方法,从管道外部对无法开展内检测的管道进行检测 应用举例参见附录A)
在检测过程中发现第三方破坏、外部腐蚀、机械损伤、应力腐蚀开裂等其他威 胁管道安全的因素时,检测人员应依据GB/T30582GB/T19285、GB/T19624等相应标准开展其他的 检测评价工作
4.3依据本标准开展检测工作前,应确定检测的管道满足以下条件: a 管道无内涂层
对于有清管作业史的管道,检测人员对本方达的适用性进行技术论证
b 内部没有积聚的固体、,泥浆、生物膜/生物质或污垢等
当存在这些物质且使用本标准时,对上 c 述物质的内腐蚀影响进行专门的评价
4.4实施检测前,检测单位应充分收集管道的内腐蚀数据,特别是与内腐蚀相关的事故情况,制定检测 技术方案
在实施检测过程中,负责解决检测过程的技术问题
管道使用单位应负责协调检测过程涉 及的相关单位或部门关系,并提供检测所需的相关数据
4.5检测单位及人员应在许可范围内从事检测工作,并对检测结论的真实性、,准确性和有效性负责
注:真实性表示报告、结论以客观事实为基础,不作假证;准确性表示报告、结论所涉及到的检测数据符合相关要 求;有效性表示检验机构的资质、检验人员的资格符合要求,所使用的仪器设备在检定校准有效期内,检验依据 合法,报告审批程序符合要求
4.6内腐蚀外检测方法的主要步骤及流程如图1所示
GB/34349一2017 确定管道范围 数据收集 香 判断透用性 停止本方法 制定方案 划分检测区段 临界倾角计算 管道实际倾角计算 开挖似置初步选择 开挖检测 下次检测周期确定 出具报告 图1内腐蚀外检测主要步骤及流程 5 数据收集 检测工作开始前应收集表1所列数据 5.1 收集数据的来源可包括设计文件、安装资料运行维护记录.计量台账和腐蚀检查记录、气质分析 5.2 报告及前期完整性评估或维护活动的检测报告 检测人员可根据相似管道系统的经验和掌握的信息,对个别无法获得的非计算过程直接使用的数 5.3 据,进行保守处理并应做好书面记录
GB/T34349一2017 表1内腐蚀外检测需要的基本数据 类别 数据名称 需收集的数据 管径,壁厚和材质 管道公称直径、壁厚以及材质 管道的起止位置 起止点 管道本体 支管 管道上当前和历史上的所有注人和分输支管处的位置及相对距离 高程 地形数据,包括管道埋深
选择测量设备时应确保设备精度满足要求 气体质量 不同管段位置的气质分析结果 介质条件 输送介质历史 是否曾输送过原油或其他液体产品等情况 水露点信息 水露点 压力 最小和最大运行压力 包括所有人口和出口在最大和最小运行压力下的最小,最大流量
特 操作工况 流量 别是低流量及停输的时间段 温度 介质温度 运行参数 管道安装及运行时间、气体流向变化 具有倾角的特征位置 道路、河流、沟渠、阀门将集液包等 上游处理设备发生异常的频率和特点(间歇式或长期的),发生异常时 上游设备异常 进人管道的流体体积(如果知道)和流体特性 水压试验信息 是否存在遗留水,水压试验用水的水质数据 管道内是否存在固体,异物;管段修复和更换;以前的检测情况;无损 检测数据;清管的管段、频率和日期
清管器、液体分离器、凝水器等 其他数据 修复/维护数据 清理出的固体杂质和液体的分析数据,以确定清出物的化学成分、腐 蚀性及是否存在细菌 泄漏/失效 泄漏及失效的位置和性质 包括监测类型[如检查片、电阻(ER)/线性极化(LPR)探针、场图法 腐蚀监测 (FsM],时间、位置,壁厚变化,记录腐蚀速率 内涂层 具有内涂层的位置 需要的其他数据 由检测人员确定 腐蚀位置预测 6 6.1概述 6.1.1腐蚀位置预测是依据流动模型计算结果识别管道潜在积液位置,并以此预测检测区段可能发生 内腐蚀的位置
6.1.2腐蚀位置预测工作包括检测区段划分、临界倾角计算、管道实际倾角计算及内腐蚀位置识别
6.2检测区段划分 6.2.1现场检测工作开始前,依据第5章收集的数据划分检测区段
GB/34349一2017 6.2.2可依据如下原则划分检测区段(检测区段定义举例参见附录B) 输送介质可能含水的注人支管应作为分界点: a b)流量、温度、压力等工艺参数变化较大处应作为分界点; 介质正反输送工况的每个输送方向上应分别划分检测区段
c 6.3临界倾角计算 6.3.1应对每个检测区段采用流动模型计算可能产生积液的临界倾角
6.3.2公称直径在DN100DN1200范围内、操作压力小于7.6MPa的层流气体状态管道宜采用式(1 计算临界倾角
其他管道应选用适用的多相流模型计算临界倾角 1.09 180 pg 一aresin[675× 一P g×d铺 式(1)中的气体密度风
由式(2)确定,表观气速V
由式(3)确定 P×M p Z×R×273十T Q×(273十T)×Z×尸smm 273+Ts)又P×S 一寸文 6.3.3应使用依据历史工艺参数值即压力、温度和表观气速)计算出的临界倾角最大值确定初步开挖 位置
6.3.4同一个检测区段内的临界倾角可能存在多个数值例如该区段内管径发生变化导致),通常可将 各数值逐一标注在倾角与高程图上
6.4管道实际倾角计算 6.4.1应对管道高程数据进行验证,管道埋深检测误差应不大于实际埋深的10%(埋深小于1m的以 m计算),高程测绘测量中误差不得大于士3cm(相对于邻近控制点);不满足精度要求时,应重新检 测
依据管道高程计算管道的实际倾角,绘制成管道实际倾角剖面图
6.4.2根据管道走向、位置与地形等因素,确定管道高程测量点的水平间距,该间距应能反应管道所有 实际倾角变化
6.4.3实际倾角可由式(4)计算 180 AH 0. arcSIn 6.5内腐蚀位置识别 6.5.1管道实际倾角大于临界倾角的顺气流开始上坡段易积液而产生内腐蚀
6.5.2应重点关注穿越公路、铁路,河流,沟渠等易出现较大实际倾角的管段
6.5.3应选择各检测区段内顺气流实际倾角大于最大临界倾角的第一个管段;当实际倾角均小于临界 倾角时,则选择各检测区段内最大实际倾角的管段作为可能发生内腐蚀的位置
6.5.4位于较短上升斜坡段(如穿公路等),可能发生内腐蚀的管段较短
当管道经过较长上坡段(如 穿山丘或山脉等),该段管道的积液位置难以判断,整段均可能存在积液
6.5.5宜将集液包或其他聚积液体的附件部位识别为内腐蚀位置
6.5.6当预测的内腐蚀可能发生位置与历史数据严重不符时,则应确认所收集数据的准确性及计算结 果的正确性 6.5.7管道曾长时间停输时,应考虑实际倾角大于最大临界倾角管段上游最低处的腐蚀可能性
GB/T34349一2017 开挖检测 7.1概述 7.1.1开挖检测的目的是通过对开挖段管道壁厚的检测判断开挖检测位置是否存在内腐蚀,并以检测 结果评估管道的整体内腐蚀情况
7.1.2开挖检测位置包括腐蚀位置预测阶段及开挖检测过程中识别到的潜在腐蚀位置
开挖检测的 -般流程如图2所示
图中的子区段是指存在腐蚀的两个倾角之间或检测区段起始点与第一个倾角之 间的管段
7.1.3通过开挖出管道进行壁厚检测判断内腐蚀情况,并以检测结果评估管道的整体内腐蚀状况
7.1.4管道开挖、检测及回填过程中,应满足规范、标准的健康安全环保相关要求
7.1.5可选择其他开挖检测流程(包括概率统计法)代替图2所示流程,但应书面记录该流程的技术合 理性及优点
GB/T34349一2017 置未发现内腐蚀,且下游第三个实际倾角大于临界倾角的检测位置验证检测未发现内腐蚀,则开始子区 段检测,如图2所示
检测位置选择还应遵守以下规定 实际倾角都小于临界倾角时,应检测最大实际倾角位置
检测发现内腐蚀,继续选择下游的最 大实际倾角部位检测
检测未发现内腐蚀,以剩余最大实际倾角位置进行验证性检测; b)子区段0段(检测区段起点与第一个检测点之间)一般应至少检测两个位置;如果该子区段内 只有一个上升段,则应检测一个位置;如果该子区段中没有任何上升段,则不需要检测 对曾返输操作的管道,应考虑流向改变对腐蚀分布的影响
7.2.2当管道实测壁厚小于管道的最小规定壁厚,可认为管道发生了严重的内腐蚀(考虑外腐蚀造成 的壁厚减薄)
也可用其他经技术论证的方法确认管道内腐蚀程度
7.2.3检测人员认为必要时,可增加开挖位置进行验证性检测
7.2.4当开挖检测过程中发现了大范围的严重内腐蚀时,检测人员确认本标准的适用性
7.2.5开挖检测时,可采用外壁漏磁、外壁远场涡流等无损检测手段,结合超声波测厚仪对内腐蚀情况 进行详细、准确的检测,应确定腐蚀减薄缺陷尺寸及相对位置
无损检测工作应依据相应标准或作业指 导书进行
7.2.6当管道内腐蚀缺陷的轴向长度超出开挖范围时,应进行扩挖
7.2.7 干气内腐蚀一般为局部腐蚀,随意安装的腐蚀试片一般难以反映管道实际腐蚀状况
管道开挖 后,可安装失重挂片、电子探针或电阻阵列等腐蚀监测设备来帮助确定检测周期,并通过对最可能发生 内腐蚀位置的监测获得内腐蚀有用信息
7.2.8上游管段的内检测结果用于评估无法进行内检测的下游管道内腐蚀状态时,应结合开挖检测结 果对内检测结果进行验证
7.2.9应书面记录管道的检测过程、详细的壁厚数据和强度计算结果
7.3其他设施部件检测 7.3.1集液包或其他设施部件可作为开挖检测点
7.3.2当集液包或其他设施部件的几何形状抑制了内部积液的蒸发时,应在管道实际倾角大于临界倾 角的可积液的下游段,至少检测一个类似装置
检测周期确定 8.1应根据内腐蚀程度、腐蚀速率、维修情况及输送工况等情况确定下次检测周期
8.2可用以下方法之一确定内腐蚀速率: 按一定周期连续监测同一位置的管道壁厚损失确定腐蚀速率(即监测管道的腐蚀量) a b 在基于流动模型预测出的积水管道位置或典型的管道位置,安装腐蚀监测装置 基于操作条件、气体质量、液体组分和其他关键因素,建立模型计算腐蚀速率; c d)基于操作条件、气体质量,液体组分和其他关键因素,通过实验室试验确定流体的腐蚀性
8.3可通过剩余寿命预测或剩余强度计算确定下次检测周期
未发现内腐蚀缺陷时不需计算内腐蚀 剩余寿命,即管道不存在内腐蚀危险;存在内腐蚀的管道可依据发现的最严重缺陷计算内腐蚀剩余寿 命
剩余强度可依据GB/T19624,GB/T30582等相关标准计算
8.4下次检测周期应不大于剩余寿命的一半
记录和报告 9 g.1记录 9.1.1检测过程应完整记录所需要的数据及相关附加信息
GB/34349一2017 g.1.2数据收集阶段应记录所有表1要求的数据及数据来源
g.1.3腐蚀位置预测阶段应记录检测区段的特征、边界(地理参考位置)及管道实际倾角剖面图的测绘 过程数据
9.1.4开挖检测阶段,应记录所有检测的活动和决策,包括但不只限于以下信息 开挖前、后收集的数据,包括金属腐蚀损失几何尺寸、用于识别其他可能腐蚀位置的数据,以及 用于估算腐蚀速率的数据; b 腐蚀缺陷处理的计划; 开挖检测点的增加及其排序的依据及相关描述
c 9.1.5检测周期确定阶段应记录评价方法、评价依据的内腐蚀缺陷尺寸、腐蚀速率的确定及下次检测 周期
9.2报告 9.2.1检测报告的内容应以记录为依据
g.2.2检测报告应包括不仅限于以下内容 管道基本情况; a b 数据收集;应简要说明数据来源,并特别注明有怀疑或矛盾的数据 检测区段划分情况:包括划分依据,边界的地理位置参考; c 管道实际倾角计算包括现场高程测量、管道埋深的检测数据及数据计算 d 临界倾角计算;包括计算使用的参数、计算过程及结果; 开挖检测位置确定;包括开挖检测位置的选择依据及结果, 开挖检测;包括检测过程、使用的仪器设备及检测数据; g 下次检测周期;包括剩余寿命或剩余强度的计算以及确定的下次检测周期 h 维护建议;需要时,对发现的严重腐蚀问题提出维护建议
GB/T34349一2017 附 录 A 资料性附录) 干气管道内腐蚀外检测应用举例 A.1 管道基本情况 所检测管道DN660mm×壁厚14.3mm,管道东西向敷设,气体只能单一方向输送
管道的工艺 条件见表A.1
表A.1管道工艺条件 工艺参数 最高 平均 最低 流量 417 347 231 kNm'/h 压力 6.4 5.2 4.0 MPa 温度 16 16 16 A.2临界倾角计算 压力和流量可变化,但最大,最小值已知
计算中采用了最低操作压力4.0MPa,最大流量 417kNm/h,选定这些值是因为它们代表了管道可能携液的极端条件,由此可推导出管道最大理论临 界倾角
温度相对恒定在16C
因为管道上没有汇人和汇出点或调压装置,划分为一个检测区段
例中计算临界倾角所需参数为管道内径(dw),操作压力(P)介质操作温度(T)最大标准流量 Q).液体密度()(默认1g/enm',可变化),及气体分子量(M)(或采用甲烧分子量16g/mol)
重力加 速度g取9.81m/s';理想标准气体常数R取8.314Pa
m=K
mol);查相关资料,气体压缩因子取 0.83
气体密度如式(A.1)所示 P×M A.1) 0g= 又R又T 代人相关参数得: 4.0十0.101325×10Pa×16×10-kg/mol =33 Pg= kg/mm" 0.83×8.314Pam/Kmol×289K 气体在管道中流动的表观速度如式(A.2)所示 Q×(273十T)×Z×尸 STp (A.2 V
= 3600X27+TT)又PXs 代人相关参数得 417×10'm'/h)×273十16)KX0.83×0.101325MPa 3600×4.0十0.1I01325MPa×273十0)K又.I4159×0.6314m7 =8.03m/s 10
GB/34349一2017 通过式(A.3)来得到临界倾角0 l.0o9 180 0
一 A.3 (675× -arcsin p一p, g×d 代人相关参数得: 1.09 180 8.03m/s)" 33kg/m arcsin(675x -10.08" 0
= = 000 9.81m/s0.6314m 33kg/m kg/m" A.3实际倾角检测计算 计算实际倾角,通过与临界倾角比较以确定开挖检测的初步位置
海拔高度剖面可由全球卫星定 位系统GPS和管道检测仪共同确定
Grs可确定具体位置和地面海拔,管道检测仪可确定管道埋深 管道实际倾角大小可由这些数据计算得来
对于每一段,实际倾角可由式(4)计算得到,结果见表A.2 A.4临界倾角与实际倾角比较 高程剖面和实际倾角剖面图见图A.1,图中起始点是0m,图中上侧实曲线为高程,下侧实曲线为 实际倾角,水平虚线为沿流动方向的临界倾角
图A.1标识出了检测区段中实际倾角值大于临界倾角 值的位置点,表A.2给出了具体数值
1600 30 500 1400 高程 20 1300 1200 临界倾角 高程/m 倾角/(”10 1100 1000 900 实际倾角 800 700 600 -10 1000 2000 3000400050006000 7000 8000 90001000011000 距离/m 图A.1管道实际倾角和高程剖面示例图 11
GB/T34349一2017 表A.2示例-检测结果 高程检测点 检测子区段 距离/m" 高程/m 倾角/("y 开挖检测结果 序号 313.7 1229 未开挖 560.14 1248 4.42 未发现内腐蚀 2105.9 277 1.075 未发现内腐蚀 2494.9 356 11.72 发现内腐蚀 2887.57 331 -3.65 未开挖 3308.6 284 6.41 未开挖 3895.31 0.39 未发现内腐蚀 288 4605.03 295 0.57 未发现内腐蚀 5315.29 454 12.94 发现内腐蚀 5943 410 4.02 未开挖 6 155.91 381 7.83 未开挖 6951.21 343 -2.74 未开挖 7391.99 374 4.033 未开挖 7635,32 417 10.18 未发现内腐蚀 8361.21 379 -3.00 未开挖 8723.22 未发现内腐蚀 448 10.90 9013.72 -0.99 443 未开挖 18 9407.58 468 3.64 未开挖 9710.87 1501 6.25 未发现内腐蚀 19 20 10064.86 151l 1.62 未开挖 A.5开挖详细检测 开挖检测位置示例见图A.2
本例中顺气流前两个超过临界倾角的部位(开挖点1井和2井)检测 中发现内腐蚀,下游之后的2个大于临界倾角的部位(开挖点3井和4井)未发现内腐蚀,再以下流最大 倾角(开挖点5#)验证,未发现内腐蚀
由此确定两个检测子区段;子区段0从0m2494.9m(从01 至开挖点1井)和子区段1从2494.9m一5315.29m(从开挖点1井至2#)
在子区段0内的两个上升 段都进行检测(开挖点6井和7井,未发现内腐蚀
子区段1内选择最大倾角位置(开挖点8井)检测 未发现内腐蚀,以剩下的最大倾角部位(开挖点9井)进行验证,未发现内腐蚀
因此完成检测区段的详 细检测过程
表A.2列出了具体的定性检测结果
12
GB/34349一2017 30 150o 1400 高程 20 1300 1200 高程/m 临界倾角 1100 倾角/(10 1000 6# 900 7 800 实际倾角 70o -10 600 60007000 90001000011000 1000 2000 3000 4000 5000 8000 距离/m 图A.2开挖检测位置示例图 A.6检测周期确定 在管道材输送压力、腐蚀速率确定情况下,按照GB/30582对检测得到的最严重腐蚀缺陷(同时 考虑腐蚀深度及面积)进行腐蚀剩余寿命预测,计算剩余寿命为10.6年,则依据检测周期不大于剩余寿 命一半原则,确定下次检测周期为5年
13
GB/T34349一2017 附 录 B 资料性附录) 检测区段定义举例 图B.1是给定管道的检测区段划分的举例
该管道1995年投人使用,除发送端和接收端外,中间 位置A和位置B有两处支管,其中位置A处支管为人口,位置B处支管为出口,各管段流量如图B.1所 示;在20012002年由于工艺调整,使位置A和B之间管段存在返输
由于位置A和B上下流量变化 较大,从发送端到接收端流向划为3个检测区段,位置B到A的反输段可划为1个检测区段,则该管道 共计4个检测区段
1995一2000年及2002一2015年期间介质流向 发送端 位置B 接收端 位置A 最大流量 最大流量 250Nm/h 气流方向 300kNm/h 气流方向 最大流量 最大流量 00kNm/h 150kNm/h 2001一2002年期间介质流向 发送端 接收端 位置A 位置B 最大流量 150kNm-/h 气流方向 气流方向 检测区段4 3 检测区段1 检测区段2、 图B.1检测区段定义示意图 14
GB/34349?2017 NACESP02062006 [1] nternalCorrosionDirectAssessmentMethodologyforPipelines CaryimgNormalyDryNaturalGass(DGIcDA
输气管道内腐蚀外检测方法GB/T34349-2017详解
输气管道是天然气等气体输送的重要设施,其安全性和可靠性对于社会经济的发展具有重要意义。然而,输气管道长期运行过程中由于内部介质等原因,容易出现腐蚀问题,给输气管道的安全运行带来威胁。为了确保管道运行安全,国家发布了输气管道内腐蚀外检测方法标准GB/T34349-2017,本文将对其进行详细解读。
1. 适用范围
GB/T34349-2017标准适用于在使用过程中的输气管道内腐蚀的外检测,包括钢制输气管道、阀门、法兰、弯头等。
2. 定义
为了便于理解,本章节对其中出现的一些专业术语进行解释:
- 腐蚀:指管道内表面材料与介质或环境中某些化学物质的作用下产生的损伤。
- 壁厚削弱率:表示管道壁厚相对初始壁厚的损失程度。
- 缺陷尺寸:指管道内表面上的线性、点状或面状缺陷的大小。
3. 技术要求
GB/T34349-2017标准对输气管道内腐蚀的外检测技术要求进行了详细规定。其中,包括以下几个方面:
- 检测方法:标准对于目前常见的几种检测方法进行了解析和比较,包括超声波检测、磁粉检测、涡流检测、X射线检测等。
- 检测原理:每种检测方法针对腐蚀形成的原理进行了详细阐述,为相关从业人员提供了参考。
- 检测设备及工具:标准对于每种检测方法所需的设备和工具进行了详细规定,包括传感器、探头、电缆等。
- 检测操作及数据处理:针对每种检测方法,标准都对其操作流程和数据处理方式进行了详细规定,以确保检测结果的准确性和可靠性。
4. 总结
输气管道内腐蚀外检测方法GB/T34349-2017是当前我国输气管道运行安全的重要标准之一,对于防范腐蚀问题和保障输气管道安全具有至关重要的意义。本文对其适用范围、定义、技术要求等方面进行了详细的解读,希望能够为相关从业人员提供一些参考。
5. 结论
输气管道内腐蚀外检测方法GB/T34349-2017是保障输气管道安全运行的重要手段之一。本文对其适用范围、定义、技术要求等方面进行了详细解读,相信可以为相关从业人员提供一些参考和帮助。