GB/T8601-2021
铁路用辗钢整体车轮
Forgedandrolledsolidwheelsforrailway
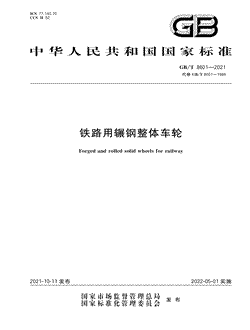
- 中国标准分类号(CCS)H52
- 国际标准分类号(ICS)77.140.70
- 实施日期2022-05-01
- 文件格式PDF
- 文本页数29页
- 文件大小2.58M
以图片形式预览铁路用辗钢整体车轮
铁路用辗钢整体车轮
国家标准 GB/T8601一2021 代替GB/T8601一1988 铁路用辗钢整体车轮 Forgelandrolledsolidwheelsforrailway 2021-10-11发布 2022-05-01实施 国家市场监督管理总局 发布 国家标涯花管理委员会国家标准
GB/T8601一2021 前 言 本文件按照GB/T1.1一2020<标准化工作导则第1部分:标准化文件的结构和起草规则》的规定 起草
本文件代替GB/T8601一1988《铁路用辗钢整体车轮》
本文件与GB/T8601一1988相比,除结构 性调整和编辑性改动外,主要技术变化如下 增加了按轴重和速度划分的1级.2级、3级车轮级别,取消了A,B级车轮的分级规定(见第4 章,1988年版的第3章); b 删除了车轮尺寸规格的规定(见1988年版的4.l); 增加了CL50,CL55,CIL65、CL70四个车轮钢牌号,删除了CL45MnSiV车轮钢牌号(见6.1, 1988年版的5.1); C轮绸冲击韧性、轮孵表面硬度、热处理均匀性要求,删除 d 增加了车轮的辐板拉伸性能、-20 -60C辐板韧性、落锤试验等(见6.3,1988年版的5.4.2); 更改了非金属夹杂物级别要求(见6.5,1988年版的5.7); e f 更改了低倍组织要求(见6.6,1988年版的5.6); 更改了超声波探伤要求(见6.7,1988年版的5.8) g 更改了喷丸要求(见6.10,1988年版的5.1l1); h 增加了车轮型式试验要求(见7.4) 增加了车轮钢钢液氢含量检测内容(见附录A) 增加了疲劳性能要求与试验内容(见附录B)3 k 增加了应变片法确定踏面下深处周向残余应力的变化破坏性试验法)内容(见附录C) m增加了不平衡的清除方法内容(见附录D). 请注意本文件的某些内容可能涉及专利
本文件的发布机构不承担识别专利的责任
本文件由钢铁工业协会提出 本文件由全国钢标准化技术委员会(SAc/Tc183)归口
本文件起草单位;马鞍山钢铁股份有限公司宝武集团马钢轨交材料科技有限公司、冶金工业信息 标准研究院
本文件主要起草人;刘学华,陈刚、钟斌、刘宝石、崔银会、鲁松、王玉姨、龚志翔、江波、王志刚、赵海、 邓荣杰、王翔
本文件1988年首次发布为GB/T8601一1988;本次为第一次修订
GB/T8601一2021 铁路用辗钢整体车轮 范围 本文件规定了铁路机车车辆用辗钢整体车轮的分级,型式尺寸极限偏差及形位公差、技术要求、试 验方法、检验要求、标志,交货及质量证明书等
本文件适用于最高运行速度不大于250km/h、轴重不大于33t的铁路机车车辆用辗钢整体车轮
规范性引用文件 下列文件中的内容通过文中的规范性引用而构成本文件必不可少的条款
其中,注日期的引用文 件,仅该日期对应的版本适用于本文件;不注日期的引用文件,其最新版本(包括所有的修改单)适用于 本文件
GB/T222钢的成品化学成分允许偏差 钢铁及合金化学分析方法二安替比林甲婉磷钼酸重量法测定磷量 GB/T223.3 GB/T223.4钢铁及合金含量的测定电位滴定或可视滴定法 223.5钢铁酸溶硅和全硅含量的测定还原型硅钼酸盐分光光度法 2223.11钢铁及合金铬含量的测定可视滴定或电位滴定法 GB 223.12钢铁及合金化学分析方法碳酸钠分离-二苯碳酰二阱光度法测定铬量 GB 223.13钢铁及合金化学分析方法硫酸亚铁铵滴定法测定饥含量 GB GB/T223.14钢铁及合金化学分析方法钮试剂萃取光度法测定钥含量 GB 223.18钢铁及合金化学分析方法硫代硫酸钠分离-碘量法测定铜量 GB 223.19钢铁及合金化学分析方法新亚饷灵三氯甲炕萃取光度法测定铜量 223.23钢铁及合金镍含量的测定 二酮肪分光光度法 GB 丁 223.26钢铁及合金钼含量的测定硫氢酸盐分光光度法 GB 《-安息香厉重量法测定钼量 GB 223.28钢铁及合金化学分析方法 GB 223.53钢铁及合金化学分析方法火焰原子吸收分光光度法测定铜量 GB 223.54钢铁及合金化学分析方法火焰原子吸收分光光度法测定镍量 223.58 钢铁及合金化学分析方法 亚呻酸钠-亚硝酸钠滴定法测定钮量 223.59钢铁及合金磷含量的测定 钞磷钼蓝分光光度法和饼磷钼蓝分光光度法 GB 223.6o钢铁及合金化学分析方法高氯酸脱水重量法测定硅含量 GB GB 223.61钢铁及合金化学分析方法磷钼酸铵容量法测定磷量 GB/T223.62钢铁及合金化学分析方法乙酸丁酯萃取光度法测定磷量 GB 223.63钢铁及合金化学分析方法高碘酸钠(钾)光度法测定量 GB/T 223.64钢铁及合金锰含量的测定火焰原子吸收光谱法 GB/T223.67钢铁及合金硫含量的测定次甲基蓝分光光度法 GB/T223.68钢铁及合金化学分析方法管式炉内燃烧后碘酸钾滴定法测定硫含量 GB/T223.69钢铁及合金碳含量的测定管式炉内燃烧后气体容量法 GB/T223.71钢铁及合金化学分析方法管式炉内燃烧后重量法测定碳含量
GB/T8601一2021 GB/T223.72钢铁及合金硫含量的测定重量法 GB/T223.76钢铁及合金化学分析方法火焰原子吸收光谱法测定饥量 GB/T223.79钢铁多元素含量的测定xX-射线荧光光谱法(常规法 钢铁及合金碗含量的测定感应炉燃烧后红外吸收法 GB/T223.85 GB/T223.86钢铁及合金总碳含量的测定感应炉燃烧后红外吸收法 228.1 金属材料拉伸试验第1部分;室温试验方法 GB/T229 金属材料夏比摆锤冲击试验方法 GB/T231.1 金属材料布氏硬度试验第1部分:试验方法 2007金属材料平面应变断裂韧度Kc试验方法 GB/T4161 GB/T4336碳素钢和中低合金钢多元素含量的测定火花放电原子发射光谱法(常规法 GB/T6394一2017金属平均晶粒度测定方法 GB/T10561一2005钢中非金属夹杂物含量的测定标准评级图显微检验法 GB/T11261钢铁氧含量的测定脉冲加热惰气熔融-红外线吸收法 GB/T13298 金属显微组织检验方法 GB/T18838.3涂覆涂料前钢材表面处理喷射清理用金属磨料的技术要求第3部分;高碳铸 钢丸和砂 GB/T18838.4涂覆涂料前钢材表面处理喷射清理用金属磨料的技术要求第4部分;低碳铸 钢丸 GB/T20066钢和铁化学成分测定用试样的取样和制样方法 GB/T20123钢铁总碳硫含量的测定高频感应炉燃烧后红外吸收法(常规方法 GB/T20125低合金钢多元素含量的测定电感耦合等离子体发射光谱法 JB/T10174钢铁零件强化喷丸的质量检验方法 TB/T3031一2002铁路用辗钢整体车轮径向全截面低倍组织缺陷的评定 YB/T081 冶金技术标准的数值修约与检测数值的判定 YB/T4375轨道交通车轮及轮箍超声波检测方法 YB/T4376轨道交通车轮磁粉探伤方法 3 术语和定义 本文件没有需要界定的术语和定义
车轮分级 车轮宜按轴重和/或最高运行速度分为3级(见表1
表1车轮分级 车轮级别 机车车辆类型 1级 2级 3级 轴重25t一33t或最高运行速 轴重小于25t且最高运行速 货车 度大于120km/h 度不大于120km/h 其他机车车辆 运行速度200km/h~250km/h最高运行速度小于200km/h
GB/T8601一2021 车轮型式尺寸极限偏差及形位公差 5.1车轮制造厂应按经规定程序批准的图样制造和检验
5.2车轮尺寸极限偏差及形位公差检测项目和偏差/公差要求由供需双方协商确定 技术要求和试验方法 6. 牌号和化学成分 6.1.1要求 6.1.1.1 车轮钢牌号和化学成分熔炼分析应符合表2规定
1级车轮的全氧含量应不大 于15×10-4%
6.1.1.2车轮成品化学成分允许偏差应符合GB/T222的规定
表2车轮钢牌号和化学成分(熔炼分析 化学成分(质量分数)/% Mn Mo Ni Cr十Mo+Ni 钢牌号 Cr Cu 不大于 CL50 0.55 0,40o 0.80 0.02o 0,020 0.30 0.30 0.08 0.30 0.06 0,5o CL55 0.60 0,40 0,80 0.020 0,020 0.30 0.30 0.08 0.30 0.06 0,.50 CL60 0.65 0,40 0,80 0.025 0,025 0.30 0.30 0,08 0.30 0.06 0.50 CL65 0.67 1.00 1.20 0.025 0,025 0.30 0.30 0.08 0.30 0.08 0,50 CL.70 0.77 0.025 0.025 0.5o0 1.00 1.20 0.30 0.30 0.08 0.30 0.08 6.1.2试验方法 6.1.2.1车轮钢的熔炼化学分析每炉取一个试样,其取样和分析试验应按GB/T20066,GB/T20123 或GB/T4336规定的方法进行
6.1.2.2成品车轮的化学成分和全氧含量分析应在轮剌公称直径处的踏面下30 处取不少于50g mm 的钢屑试样和/或棒状样,其分析方法应按GB/T20123,GB/T20125和GB/T11261的规定进行
当 采用光谱分析时,可使用拉伸试样端部,试验应按GB/T4336,GB/T11261规定的方法进行
当出现 异议时,应按GB/T223.3,GB/T223.4,GB/T223.5、GB/T223.11,GB/T223.12,G;B/T223.13、 GB/T223.14、GB/T223.18,GB/T223.19,GB/T223.23,GB/T223.26,GB/223.28、GB/T223.53 GB/T223.54,GB/T223.58,GB/T223.59,GB/T223.60,GB/T223.61,GB/T223.62,GB/T223.63、 GB/T223.64,GB/T223.67,GB/T223.68,GB/T223.69,GB/T223.71GB/T223.72、GB/T223.76、 GB/T223.79,GB/T223.85,GB/T223.86或GB/T20123以及GB/T11261规定的化学分析方法进行 仲裁
6.2车轮制造 6.2.1车轮应采用经炉外精炼和真空脱气处理的连铸坯或模铸锭制造
模铸锭钢锭应从底部浇铸
钢液氢含量应不大于2.0×10-%,钢液氢含量的分析试验应按附录A规定的方法进行
GB/T8601一2021 6.2.2如采用模铸钢锭制造车轮,应用切过头的钢锭,切头量应足以消除钢锭两端影响车轮质量的有 害部分
钢锭所有表面不应有影响轧制质量的缺陷
车轮应经整体锻造和/或轧制成型,并经热处理 6.2.3 6.3力学性能 6.3.1拉伸性能 6.3.1.1要求 车轮的拉伸性能见表3
表3车轮的拉伸性能 轮锻 辐板 钢牌号 上屈服强度(R.n R减小值" 抗拉强度(Rm 断后伸长率(Amm 断后伸长率(A MPa MPa % MPa % CL.50 520 >l1o >14 820 >l6 CL55 >58o >12 >120 >900 >14 Cl.60 >58o >910 >10 >120 >14 CL65 620 >1010 >10 >130 >12 习 CL70 >650 >1050 >10 130 s10 如果屈服现象不明显,可用规定塑性延伸强度Rn代替
同一车轮上相对于轮抗拉强度的减小值
6.3.1.2试样取样位置 试样应取自车轮的轮绸和辐板处,其位置如图1所示
GB/T8601一2021 单位为毫米 标引序号说明 -轮惘拉伸试样取样位置; -辐板拉伸试样取样位置
注所示尺寸为精加工尺寸
图1拉伸试样取样位置 6.3.1.3试验方法 试验应按GBT228.1规定的方法进行
轮铜拉伸试样平行长度内直径为15mm,原始标距为其 直径4倍;辐板拉伸试样平行长度内直径为10mm,原始标距为其直径的5倍
6.3.2冲击性能 6.3.2.1要求 冲击吸收能量值应符合表4规定 表4冲击性能及试样要求 -20 KV, KU .(一20) 冲击吸收能量 冲击吸收能量 试样要求 试样要求 钢牌号 取样 单个试样 取样 单个试样 槽口 槽口 平均值 平均值 部位 深度 最小值 部位 深度 最小值 CL5o 轮制 轮锻 5mmm 17 12 2mm 10 5 CL55 >13 >9 5 轮辅 轮锻 5mm 2mm 8
GB/T8601一2021 表4冲击性能及试样要求续) KU.(+20C KV.(一20) 冲击吸收能量 冲击吸收能量 试样要求 试样要求 钢牌号 单个试样 单个试样 取样 槽口 取样 槽口 平均值 平均值 部位 深度 最小值 深度 最小值 部位 CL60 辐板 2mm >16 >11 辐板 2mm >16 >l CL65 2mm 20 > 轮绸 214 >12 辐板 >8 2mm CL.70 >18 >13 轮剿 2mmm 当需方有需求时,可对一40C冲击吸收能量进行检验,具体要求由供需双方协商
6.3.2.2 试验取样位置 冲击试验取样位置见图2和图3
试验温度为十20C时,对CL.50和CL.55钢车轮应采用槽深 5mm的U型缺口试样,在轮绸上取样;对CL.60,CL65和CL70钢车轮应采用槽深2mm的U型缺口 试样,在辐板/轮制上取样
一20C时,应采用槽深2mm的V型缺口试样,在轮绸上取样
试验温度为 单位为毫米 试样 开槽面 标引序号说明 轮轭冲击试样; -缺口
注:所示尺寸为精加工尺寸
图2轮绸冲击试验取样位置
GB/8601一2021 单位为毫米 125土5 标引序号说明: -辐板冲击试样,底部缺口朝向外侧面
注所示尺寸为精加工待组装尺寸
图3辐板冲击试验取样位置 6.3.2.3试验方法 试验应按GB/T229规定的方法进行
6.3.3轮轭断面硬度 6.3.3.1 要求 对CL.50和CL55钢车轮,在轮轭踏面下35mm处布氏硬度最小值应不小于表5中规定的值
对 CL60,cL.65和cL70钢车轮,在轮绸踏面下30mm处布氏硬度最小值应不小于表5中规定的值
轮 锻一辐板过渡处(图4中A点)的硬度应至少比踏面下35mm(对CL.50,CL.55钢车轮)或30mm(对 CL60,CL65和CL70钢车轮)处硬度值低10HBw
表5轮绸处硬度值 钢牌号 测试位置距踏面距离 布氏硬度最小值(HBW10/3000) CL50 35mm 245 CL55 35mm 255 CL60 30mm 265 28o0 CL65 30mm cCL.70 30mm 300
GB/T8601一2021 单位为毫米 30 70 125 标引序号说明: 踏面下深度为35mm(对CL.50和CL.55钢车轮)或30mm(对CL.60,CI65和CL70钢车轮)处 -加工后的车轮内侧面 -公称滚动圆; -测试点
注所示尺寸为精加工尺寸 图4轮绸径向截面硬度读数测点位置 6.3.3.2测试点位置" 如图4所示,在轮绸径向截面上测4点硬度
6.3.3.3试验方法 试验应按GB/T231.1规定的方法进行
6.3.4疲劳性能 附录B规定了车轮疲劳性能要求与试验方法
6.3.5轮搁韧性 6.3.5.1 要求 对于CL50钢,6个试样所得K
平均值应大于或等于80MPam',任一试样的K
最小值应不低 于70MPam'
此项为型式试验要求,只对1级CL.50钢车轮进行试验
6.3.5.2试验取样位置 应从轮绸上图5所示位置切取6个试样
试样应绕轮绸均匀分布
GB/T8601一2021 单位为毫米 3.5'.s 注:所示尺寸为精加工尺寸
图5轮辗韧性试样取样位置 6.3.5.3试验方法 试验应按GB/T41612007的规定进行
具体试验条件如下: 紧凑拉伸试样CT;厚度30mm(CT30试样)具有90'张角的山形缺口,见GB/T4161一2007 a 图c.1 b)试验温度为十15C十25C; 试样裂纹位移的测量按GB/T4161一2007图3进行; c 应力强度因子速率AK/S应在0.55MPam'/s1MPam'/s范围内
d 韧性值应认为是根据载荷-位移数据中的最大载荷值(F
)计算得出的K
值
6.3.6轮辗表面硬度 6.3.6.1 要求 热处理后轮辖表面硬度值应符合表6的规定
试验时的布氏硬度压痕可以留在轮圜表面
表6轮搁表面硬度值 钢牌号 布氏硬度最小值(HBw10/3000 CL.50 245 CL55 255 CL60 277 CL65 302 cL70 321 6.3.6.2测试点位置 测量轮绸表面硬度测试的压痕应在图6所规定区域内取得
GB/T8601一2021 单位为毫米 标引序号说明 -布氏硬度测试区域 注:所示尺寸为精加工尺寸
图6轮绸表面硬度测试区域 6.3.6.3试验方法 试验应按GB/T231.l的规定进行
应对每一车轮进行轮绸表面硬度检测,试验可以在机械加工 前进行
6.4热处理均匀性 6.4.1硬度值 同一车轮的轮搁上测量的硬度值变动应在30HB范围内
6.4.2测试点位置 应在轮捎外侧面上均匀分布的3个点上测试硬度
压痕应在图6所规定区域内的相同直径上 取得
6.4.3试验方法 试验应按GB/T231.l的规定进行
6.5显微组织、晶粒度及非金属夹杂物 6.5.1要求 6.5.1.1车轮轮绸经淖火和回火处理后,其显微组织应为细珠光体,允许存在铁素体,不应存在影响车 轮使用性能的其他有害组织 6.5.1.2车轮轮轭经淬火和回火处理后晶粒度应为6级或更细
对于CL70钢车轮,晶粒度检验评定 为型式试验要求 6.5.1.3车轮非金属夹杂物级别应符合表7规定
10
GB/T8601一2021 表7非金属夹杂物级别 最大非金属夹杂物级别 夹杂物类型 1级(车轮级别 2级车轮级别 3级车轮级别 粗系 细系 粗系 细系 粗系 细系 1.5 1.5 A(硫化物类 B氧化铝类) c(硅酸盐类 1.5 1.5 D(球状氧化物类 1.5 B+C十D DS(单颗粒球状类 .5 2.5 D不参与评级 客车车轮应进行DS类夹杂物检验,其他机车车辆车轮是否进行检验由供需双方商定 6.5.2试验取样位置 显微组织晶粒度评定试验取样位置见图7,检验面应平行于轮圜横断面
非金属夹杂物检验评定 试验取样位置见图8,检验面应平行于轮穰外侧面
单位为毫米 标引序号说明 公称滚动圆 检验面
注所示尺寸为精加工尺寸
图7显微组织,晶粒度试验取样位置示意图 11
GB/T8601一2021 单位为毫米 标引序号说明 -公称滚动圆; -检验面
注:所示尺寸为精加工尺寸
图8非金属夹杂物试验取样位置示意图 6.5.3试验方法 6.5.3.1应按GB/T13298规定的方法进行显微组织检验
6.5.3.2应按GB/T6394一2017中规定的比较法进行晶粒度的评定,晶粒度的显示按供需双方商定的 方法进行
6.5.3.3应按GB/T10561一2005规定的A方法进行非金属夹杂物检验
6.6低倍组织 6.6.1要求 车轮低倍试片上不应有白点、缩孔残余、分层,裂纹、翻皮、异型偏析、异金属夹杂等
一般疏松.中 心疏松和偏析分别不应严重于TB/T3031一2002中图1、图2和图3的限定
各型非金属夹杂,对23级车轮,应小于或等于2级;对1级车轮,应小于或等于1级
6.6.2试验取样位置 车轮低倍检验试样为车轮半径方向整个横截面
6.6.3试验方法 应按TB/T3031一2002规定的方法进行检验和评定
6.7内部完好性 6.7.1一般要求 内部完好性应通过超声波检测确定
从事车轮超声波检测的人员应具有相应资质
标准缺陷为具有不同直径的平底孔,见表8. 12
GB/8601一2021 表8标准缺陷直径 单位为毫米 车轮级别 1级 2级 3级 轮桐标准缺陷直径 2.0 3.0和5.0 辐板标准缺陷直径 3.0和5.0 轮毂标准缺陷直径 6.7.2验收要求 6.7.2.1轮绸 不应有大于或等于表8规定的平底孔当量大小的缺陷 在轴向检验时,回波衰减不应高于4dB. 6.7.2.2辐板 型式试验要求如下: 不应有10个以上大于或等于克3mm平底孔当量缺陷; aa 不应有大于或等于声5mm平底孔当量缺陷; b c 两个允许存在的缺陷(大于或等于内3mm平底孔当量但小于负5m平底孔当量)之间的距 离至少应为50 mm 6.7.2.3轮毂 型式试验要求如下 a 不应有3个以上大于或等于卢3mm平底孔当量缺陷; b 不应有大于或等于夕5mm当量平底孔缺陷; 两个允许存在的缺陷(大于或等于内3mm平底孔当量但小于5mm平底孔当量)之间的距 c 离应不小于50mm; d 在轴向检验时,回波衰减应不高于6dB 6.7.3试验方法 超声波检测方法应按YB/T4375规定执行
根据需方要求,也可以采用其他标准进行检测
6.8残余应力 6.8.1要求 6.8.1.1车轮热处理应在轮绸内产生周向残余压应力区,并应同时保证使用性能
6.8.1.2采用切割法检验时,内部应力释放后,两个标记之间距离的缩小值应不小于1mm 6.8.1.3仅对CL.50,CL55钢车轮采用应变片法测量残余应力分布,为型式试验要求
在车轮踏面表面 附近测得的周向压应力值应不大于一80MPa
如果测得的周向压应力值小于一200MPa,应证明车轮 辐板的径向残余应力水平是可以接受的
13
GB/T8601一2021 6.8.2试样 试样应为热处理后的整个车轮
6.8.3试验方法 6.8.3.1用切割法进行残余应力检验时,应在轮轭外侧面上位于轮辆厚度的中心处做两个相距100mm 的标记,然后从轮缘顶部开始直达轮毂孔进行径向切割,切缝应在两个标记中间;通过测量两个标记之 间距离的减缩检验压应力的存在
6.8.3.2应变片法测量残余应力分布,可以估算出车轮踏面下一定深度处周向应力的变化,详见附 录C
6.9表面完好性 6.9.1一般要求 6.9.1.1表面完好性应通过磁粉探伤进行确定
6.9.1.2磁粉探伤范围为除轮毂孔和踏面以外的整个车轮表面(轮毂孔和踏面由供需双方协商)
6.9.1.3磁粉探伤应在最终机加工后、抛丸和防腐处理前进行,表面无油污
6.9.1.4从事车轮磁粉探伤的人员应具有相应资质
6.9.2验收要求 除非另有规定,表面磁痕显示最大允许长度应符合以下要求 a 机加工表面为2mm; b)非机加工表面为6 mm 6.9.3缺陷去除 对磁粉探伤发现的超过6.9.2规定的不连续性磁痕,可用机械加工或磨削方法去除
6.9.3.1 6.9.3.2修整后的车轮尺寸应能满足图纸规定的最小尺寸要求
6.9.3.3表面返修后,应重新进行磁粉探伤
6.9.4试验方法 磁粉探伤方法应按YB/T4376规定的方法执行
根据需方要求,也可以采用其他标准进行检测
6.9.5剩磁 应对磁粉探伤后的车轮退磁并进行剩磁检查,其剩磁应不大于0.7mT
6.10喷丸强化 6.10.1一般要求 6.10.1.1根据需方要求,可进行喷丸强化
喷丸应在热处理之后进行,如需方要求喷漆(油),则应在热 处理之后、喷漆(油)之前进行
喷丸区域为车轮辐板的内外侧面,并延伸至轮铜内外侧面圆弧中点和轮 毂内外圆弧处的中点 6.10.1.2喷丸不应损害车轮装配部位和标记,必要时应采取相应的防护措施
14
GB/T8601一2021 6.10.1.3在正常设计车轮的辐板外侧面靠近轮毂圆弧处和辐板内侧面靠近轮饷圆弧处,以及反向辐板 设计车轮的辐板外侧面靠近轮圆弧处和辐板内侧面靠近轮毂圆弧处的C型标准弧高试片应产生不 小于0.20mm的平均弧高
6.10.1.4最短喷丸时间应足以保证喷丸表面达到C型标准弧高度试片100%表面覆盖率
注:表面覆盖率的定义见JB/T10174
6.10.1.5钢丸应为GB/T18838.3或GB/T18838.生的铸钢丸
喷丸机应有分离装置,用以不断去除 破碎的钢丸,且应添加足够的新钢丸以保证喷丸机内任何时候都至少有85%的170号或更大尺寸的 钢丸
6.10.2试验方法 6.10.2.1喷丸强度应按JB/T10174进行检验
6.10.2.2应用附在一个检验车轮上的c型标准弧高度试片测定弧高,且每班或8h至少测一次弧高
检验结果应予以保存
6.10.2.3如果某次检验达不到0.20mm的C型标准弧高度试片弧高的要求,则可以进行两次复验,复 验数据应不小于0.20mm
算出两次复验数据与该次检验数据的平均值,应不小于0.20mm. 6.10.2.4如果测定值不能满足6.10.2.3规定,则应采取纠正措施,并在进行生产性喷丸前获得合格的 测定值
如果不合格检验的平均弧高是0.16mm~0.19nmm n,则应对上次合格检验和这次不合格检验 之间的时间内喷丸的后二分之一车轮重新喷丸,喷丸时间应至少为正常喷丸时间的二分之一
如果平 均弧高小于0.16mm,则上次检验合格之后喷丸的所有车轮均应重新喷丸,喷丸时间为正常喷丸时间
6.11残余静不平衡 在交货或待组装状态下,精加工车轮的最大残余静不平衡见表9规定
6.11.1 表9精加工车轮的最大残余静不平衡 运行速度(G 静不平衡 符号 km/h 120 125 E3 120之w200 <75 E2 200
GB/8601一2021 表10检验要求续 每批提交检验的车轮数 检验 每个车轮 检验 检验 试验 或每批检验次数 序号 试验和检验项目 类型 方式 状态 单元 的试验数 <250 >25o0 16 100% 轮绸 a,b x,y 超声波 17 辐板 20% 检测 18 轮毂 20% 19 磁粉探伤 a,b 100% Xy a,b 20 表面质量和尺寸 100% Xy 残余静不平彻 00% 21 x,y 2 剩磁 00% x,y 残余应力分布 1个 23 24 1个 轮绸断裂韧性 疲劳性能 25 2个 -由制造厂质量检验部门进行;b需方可进行到货检验c同一炉号的车舵d试验应在规定 注:a 的热处理之后进行;e-由供需双方认可部门进行f试验在最终交货状态下进行;h同一热处理批 的车轮i -3000个车轮为一个试验单元;w -以一个车轮为一个试验单元;x -出厂检验项目;y 型式检验项目; 制造厂首次生产本文件规定的材料的车轮(不包括货车轮).或制造工艺发生重大变化 时进行
不包括CL60钢车轮
仅对cL5和cL.60钢车轮 仅对CL60,CL65和CL70钢车轮 CL.70钢为型式检验项目
CL.50,CL.55钢车轮每批检验10%,cL60.CL.65,CL70钢车轮每批检验1 个 车轮尺寸偏差和形位公差检验项目和检验频次按供需双方商定和7.2.2的规定
7.3尺寸及偏差检验规则 7.3.1滚动圆直径、轮圜宽度、轮毂孔径、轮毂长度、轮缘和踏面外形应逐个测量
7.3.2轮辖外侧内径、轮辖内侧内径、同侧轮酮厚度差、轮毂内侧外径、轮毂外侧外径、同侧轮毂壁厚 差,内侧绸毂距、,辐板厚度、辐板轮廓应每班开班或每工作8h至少测量一次
7.3.3滚动圆圆度、轮绸内侧面端面跳动、轮毂孔径跳动为型式检验项目
7.4复验与判定规则 7.4.1对成品化学成分,当成品化学成分不合格时,可在同批其他车轮上取双倍试样进行复验,复验结 果只要其中有一项不合格,则判定该批车轮不合格
7.4.2对低倍组织,若低倍组织发现有白点、缩孔残余,分层、裂纹、翻皮、异型偏析和金属异物,则该批 车轮不合格,低倍组织因其他项目不合格时可在同批车轮中另取两个车轮进行复验
复验结果只要有 -项不合格,则判定该批车轮不合格
17
GB/T8601一2021 7.4.3对非金属夹杂物,当非金属夹杂物检查不合格时,可在同批其他车轮上取双倍试样进行非金属 夹杂物复验
复验结果只要有一项不合格,则判定该批车轮不合格
当拉伸、硬度、冲击、显微组织或晶粒度检验不合格时,可在同批其他车轮上取双倍试样进行复 7.4.4 验,复验结果只要其中有一项不合格,则判定该批车轮不合格
供方可对该批车轮重新进行热处理,但 重复热处理次数不得多于两次,回火次数不计
重新热处理的车轮应进行除低倍组织,化学成分和非金 属夹杂物外的全部检查与验收
7.5型式试验条件 在下列情况下应进行型式试验 首次生产; a 制造工艺发生重大变化时 b) c 停产两年及以上,再重新投人批量生产时 d 生产场地发生变更时
7.6数值修约 数值修约应按YB/T081的规定进行
8 标志 8.1每个成品车轮均应在轮酮外侧面或轮毂内端面上打印制造标记,可采用热打印或冷打印方式,但 打印方式应经需方认可
标志应包含以下内容 制造年份末两位数; a) b 制造月份; 工厂标记; c 车轮钢牌号; d 车轮型号; e D 熔炼炉号; 车轮顺序号 日 8.2无标记或标记不清无法辨认者,不应交货
残余不平衡位置和标记按6.11.2的规定执行.
8.3 8.4非精加工状态交货的车轮其标记由供需双方商定,合同中注明 9 交货 9.1交货状态 车轮可以下列状态交货 未加工(锻制或轧制)状态:除为满足订单中规定的技术要求而进行的机械加工外未进行任何 a 机械加工; 粗加工状态(按需方要求);车轮已进行了机械加工,但尚需进行后续加工; b c 半精加工状态;除轮毅孔外,车轮某些部位已经进行了精加工,而其他部位还需进行精加工(包 括轮毂孔); 18
GB/T8601一2021 d)精加工状态;除轮毂孔外,车轮所有部位均进行了精加工; 精加工待装配状态;车轮所有部位,包括轮毂孔均进行了最后加工,处于最终待装配状态
e 9.2包装防护 9.2.1在每个车轮的内侧辐板上用油漆标明轮径尺寸,字迹应清晰可辨,轮径精确到小数点后一位
如有其他要求,可由供需双方协商确定,在合同中注明
9.2.2车轮表面应按需方要求在指定部位涂刷用户指定或者认可的防护层,防护层应均匀覆盖需涂刷 部位
9.2.3车轮应4个或5个一组,成串运输
防止车轮运输过程中受到机械损伤,特别是轮毂孔两端及轮 缘应采取有效防护
如有其他要求,可由供需双方协商确定,在合同中注明
10质量证明书 0.1制造厂应对每批车轮开具质量证明书
10.2质量证明书应包括以下试验内容 a 化学分析(实测值); 轮剌拉伸、辐板拉伸(实测值); b 轮绸冲击、辐板冲击(实测值) o 轮剌断面硬度及A点硬度(实测值); d 表面硬度; f 残余应力值(实测值); 低倍组织 g h)显微组织; 非金属夹杂物(各类夹杂物级别 晶粒度(实测值); j k 超声波探伤; 磁粉探伤 表面质量" m n)尺寸; 残余静不平衡
o 0.3证明书同时应包括以下内容: 制造厂名称; aa b 车轮型号; 车轮钢牌号; c 车轮数量; d 熔炼炉号 ee 车轮顺序号(单个); f 出厂日期 g 19
GB/T8601一2021 附 录 A 规范性 车轮钢钢液氢含量检测 在线检测 A.1 A.1.1测试方式 应在真空脱气操作结束后对钢包中的钢水氢含量采用定氢系统进行在线测定
A.1.2定氢系统组成 定氢系统由处理器装置、气动装置,氮气瓶,测枪定氢探头等组成
A.1.3检测原理 测试时,将定氢探头浸人钢水中,载体气体(N.)通过与氢气结合吸收溶解在钢水中的氢气
在气 动装置内,通过TCD(热传导率检测或热导计)连续监控载体气体的导热性并将其转换成氢气分压力, 然后转换成氢含量,这样处理器装置产生实时氢含量对时间的曲线,待测量曲线平直后处理器装置显示 正确的氢含量
A.2化学分析法 A.2.1当采用化学分析法时,应在浇铸钢锭或倒人中间包过程中取样
为符合技术条件的要求,应按 下述四种方法之一进行取样 铜模 a b)二氧化硅吸管; c 石英起泡管(透明石英因其吸湿性而被禁用); 埋人式探头法(采用热导探测器的载体气法)
d) A.2.2可采用下列两种方法之一进行分析 在温度为650C一1050C范围内“真空提取” a b)在650士20C时,将载体气注人钢液中
所得到的含有氢的扩散气体被回收用于再循环和 分析
A.3其他要求 从事氢含量分析的操作者应经过专门培训
20
GB/T8601一2021 附录 B 规范性 疲劳性能要求与试验 B.1疲劳性能要求 在规定的试验应力下,经过10次循环后车轮不应产生裂纹.CL50.CL55和CL60车轮的辐板径 向试验应力见表B1,其他钢牌号的车轮试验应力由供需双方商定
表B.1车轮的辐板径向应力 对称加载 非机加工辐板 机加工辐板 检验的径向应力值 士168MPa 土240MPa B.2疲劳试验试样 试样为成品尺寸未涂装的车轮
车轮表面质量应符合6.12的规定
B.3试验方法 试验装置应能使车轮辐板产生对称弯曲应力
表B.1中应力值指通过测量得到的可能萌生裂纹区 域的径向应力;试验载荷通过测量可能萌生裂纹区域的径向应力确定
B.4试验装置 B.4.1可采用试验装置A或试验装置B进行车轮疲劳试验
B.4.2试验装置A如图B.1所示,其中 车轮过盈安装到一根模拟车轴上,轮轴组件固定在试验台法兰上; a b)试验轮轴组件绕轴中心线转动,在轴的自由端通过伺服液压系统施加恒定的载荷,使车轮辐板 发生弯曲
B.4.3试验装置B如图B.2所示,其中 车轮过盈安装到一根模拟车轴上,轮轴组件固定在试验台地基上; aa b)加载装置在轴颈部位施加旋转载荷,进而在试验部位产生循环交变应力
B.5检验规则 每次检验车轮数量为2个
21
GB/T8601一2021 标引序号说明: 施加载荷, 工装垫板 -旋转; 试验台法兰; 装配轴; 紧固螺栓
-车轮试样; 图B.1试验装置A 标引序号说明 -试验台地基 夹紧工装; 5 -试验车轮; -连接车轴; -连接螺栓; 加载装置 图B.2试验装置B 22
GB/T8601一2021 附录 C 资料性 应变片法确定踏面下深处周向残余应力的变化破坏性试验法 C.1方法原理 该方法的要点是导致轮捎中存在的残余应力的逐渐释放的切割操作 通过在表面用应变片测量局部变形测得每次切割操作所导致的残余应力状态的变化
通过在表面测得的状态,用线性插值法得到轮绸内部应力状态的变化
热处理可有效地使周向残余应力分布均匀,试验仅对一个径向横截面进行测量
C.2程序 c.2.1安装应变片 在切割车轮前,在轮酮横截面上安装应变片(见图C.1),应变片粘贴位置如下: 沿圆周方向和轴向; a 位于辐板与轮搁联结处的对称面上的踏面点1处
b 沿圆周方向和径向; -轮惘外侧面上的点2E处和轮绸内侧面上的点21处 辐板圆角的点3E处(外侧)和点3I处(内侧).
2E 3E 标引序号说明: 1、2E、21,3E、31 测试点; -测试点1和21的轴向距离; -测试点1和2E的轴向距离 -测试点1和3I的轴向距离; d -测试点1和3E的轴向距离 图c.1安装应变片 C.2.2实施切割 切割操作按一定程序进行(见图C.2),这样将不会产生残余应力除非切割区域厚度很薄. 按下述顺序进行三步切割操作 沿两个径向和距应变片3和3E下深度至少为'的平行于轴向的面,切取长度s至少为轮绸 a 宽度两倍的一段轮绸截面[第1步操作见图c.2a)] 在辐板与轮绸联结起始处沿平行于轴向的面切割[第2步操作见图c.2b)] b 穿过轮绸沿平行于轴向的面切割[第3步操作见图C.2c],该步操作将仅在轮绸厚度大于 30mm时进行
23
GB/T8601一2021 C.2.3切割操作 切割操作如下 第1步切割操作后,测量应变; a 记录轮绸横截面一端上径向横截面的精确轮廓; b c 粘贴应变片4[见图C.,2b)] 第2步切割操作后,测量应变片1和4的应变 d 测量厚度h,和ha[见图c.2b)] e fD 粘贴应变片5[见图C.2c)]; 第3步切割操作后,测量应变片1和5的应变" g h)测量厚度h,和h;[见图c.2e)]
S>2n 1 3E 第1步操作 第2步操作 b 第3步操作 标引序号说明 1、21,2E,3I,3E、4,5--测试点 -轮辆切取长度; 轮轭宽度; 测试点3I和3E的轴向距离; 第2步操作后切取的两部分试块标记: S1,S h1、h 第2步和第3步操作后切取的两部分试块沿径向的高度 A、B -第2步和第3步操作切割面与测试点1径向延长线交点
图c.2切割操作 24
GB/T8601一2021 C3踏面下深处周向残余应力变化的计算 C.3.1 总则 按式(C.1)计算在测量点“j”处进行切割操作“”而产生的周向应力变化()) E (C.1 ,[e十we门 式中: E=210000MPa; 7=0.28; -周向测得的应变; e 轴向(或径向)测得的应变
C.3.2由第1步切割操作产生的周向应力变化的计算 计算应力i,ole,l,iE、和i,然后按式(C.2)和式(C.3)计算点2和点3[图C.3a)]的应力值: oE十 C,3 d ir十 大 沿径向的应力变化用应力图上通过图C.1中点1和点3的直线表示,该两点纵坐标与点到踏面的 距离有关
在点2处计算出的应力[图C.3a)]落在这条直线上,误差为士20MPa
C3.3由第2步切割操作产生的周向应力变化的计算 计算应力i和,然后按式(C.4)计算点A处[图C.2b)]的应力 -2h十h2)Sd十hSgo a= C.4 Srh十h2 沿径向的应力变化用应力图上通过图C.1中点1和点A的直线表示,该两点的纵坐标与点到踏面 的距离有关[图C.3b]
C3.4由第3步切割操作产生的周向应力变化的计算 计算应力oi和a,然后按式(C.5)计算点B处[图C.2c)]的应力 h2? 2h十ha oi= o C.5 一叫十 -h h十h " 沿径向的应力变化用应力图上通过图C.1中点1和点B的直线表示,该两点的纵坐标与点到踏面 的距离有关[图C.3c]
C3.5踏面深处周向应力变化的最终结果表示 通过图C.3a)和图C.3b)确定应力值;和i
图C.1中点1处周向残余应力(G)值等于每一切割操作后测得应力值的代数和,即=十i十 di
同样,图C.3中点B处残余应力值(a)为;=十i十oi
踏面深处周向应力变化最终示图用应力图上通过相当于图C.1中点1和图C.3中点B纵坐标a 和的直线表示,该两点的纵坐标与点到踏面的距离有关[图C.3d] 25
GB/T8601一2021 MPa MPan MP MPa 标引序号说明 -图c.1中测试点1的位置,坐标原点 -测试点21和2E连线与图C.1中测试点1径向延长线的交点 测试点3I和3E连线与图c.I中测试点1径向延长线的交点 A,B -第2步和第3步操作切割面与图C.1中测试点1径向延长线交点
图c3确定踏面深处周向应力变化的方法示意图 26
GB/T8601一2021 附 录 D 资料性) 不平衡的清除方法 D.1不平衡的清除是在车轮内侧面的辐板与轮绸之间的过渡部位进行偏心加工(见图D1),去除的轮 绸厚度小于4mm,加工面和非加工面圆滑过渡,该处不作为轮绸厚度的测量点
不采取附加平衡块或 钻孔的方式达到平衡
D.2如果有特殊情况,则消除残余不平衡部位可由供需双方特别协商进行调整
单位为毫米 清除不平衡 偏心 图D.1不平衡的校正示例
铁路用辗钢整体车轮GB/T8601-2021介绍
铁路交通是我国重要的交通运输方式之一,而车轮作为列车的核心部件之一,对列车的安全和稳定性具有重要意义。为了规范铁路用辗钢整体车轮的生产和使用,国家标准化管理委员会最近发布了最新的标准GB/T8601-2021。
一、产品分类
根据车轴的类型和轮胎的结构,将铁路用辗钢整体车轮分为非直板式车轮和直板式车轮两类。
二、质量指标
铁路用辗钢整体车轮的质量指标包括轮辋、轮缘和轮毂等方面的要求,并且规定了各项指标的测试方法。
三、加工要求
标准还规定了铁路用辗钢整体车轮的加工要求,包括材料的选择、热处理、车削、轨侧修整等方面。
四、检验方法
标准还制定了铁路用辗钢整体车轮的检验方法,包括尺寸、表面质量、硬度和力学性能等方面的测试方法。
五、标志、包装、运输和储存
对于铁路用辗钢整体车轮的标志、包装、运输和储存也作了详细规定,以确保产品在运输和储存过程中不受到损坏。
六、技术要求
标准还规定了铁路用辗钢整体车轮的技术要求,包括非直板式车轮和直板式车轮的轴向与径向动态强度、横向稳定性、旋转平衡、轮距策略等方面。
通过GB/T8601-2021这个标准的制定和实施,可以规范铁路用辗钢整体车轮的生产和使用,提升车轮产品的质量和安全性,保障铁路交通运输的顺利进行,同时促进我国铁路运输产业的健康发展。