GB/T32994-2016
水泥工业用回转窑
Rotarykilnforcementindusty
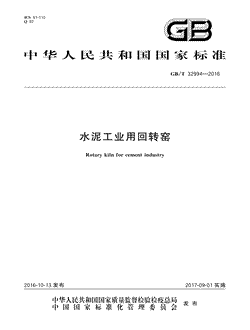
- 中国标准分类号(CCS)Q92
- 国际标准分类号(ICS)91.110
- 实施日期2017-09-01
- 文件格式PDF
- 文本页数16页
- 文件大小471.33KB
以图片形式预览水泥工业用回转窑
水泥工业用回转窑
国家标准 GB/T32994一2016 水泥工业用回转窑 Rotarykinforeementindustry 2016-10-13发布 2017-09-01实施 国家质量监督检验检疫总局 发布 国家标准化管理委员会国家标准
GB/T32994一2016 前 言 本标准按照GB/T1.1一2009给出的规则起草 本标准由建筑材料联合会提出 本标准由全国建材装备标准化技术委员会(SAC/TC465)归口
本标准起草单位:中材装备集团有限公司、江苏鹏飞集团股份有限公司、江苏海建股份有限公司、上 海新建重型机械有限公司中信重工机械股份有限公司、唐山冀东装备工程股份有限公司、朝阳重型机 器有限公司安徽省风形耐磨材料股份有限公司南京凯盛国际工程有限公司、建材机械工业协会
本标准主要起草人:邓荣娟、白文生、卢华武,责道春、于旺江、史韶光、赫连旭阳、李雨森、王守玲、 许友娼,杨平,高杰,朱国民,张瑞,刘波
m
GB/T32994一2016 水泥工业用回转窑 范围 本标谁规定了水泥工业用回转窑(以下简称回转密)的型号,基本参数,要求,试验方法、检验规则 标志、包装、运输和贮存
本标准适用于水泥工业用回转窑
规范性引用文件 下列文件对于本文件的应用是必不可少的
凡是注日期的引用文件,仅注日期的版本适用于本文 件
凡是不注日期的引用文件,其最新版本(包括所有的修改单)适用于本文件 GB/T7002006碳素结构钢 GB/T1175一1997铸造锌合金 铸造铜及铜合金 GB/T1l762013 GB/T1184一1996形状和位置公差未注公差值 GB/T1800.2一2009产品几何技术规范(GPs极限与配合第2部分;标淮公差等级和孔、轴 极限偏差表 GB/T1804一2000 一般公差未注公差的线性和角度尺寸的公差 GB/T2970一2004厚钢板超声波检验方法 GB/T3274碳素结构钢和低合金结构钢热轧厚钢板和钢带 B/T3323一2005金属熔化媒焊接接头射线照相 GB/T5117非合金钢及细晶粒钢焊条 GB/T5118热强钢焊条 GB5226.1 机械电气安全机械电气设备第1部分;通用技术条件 铸钢件超声检测第1部分一般用途铸锅件 GB/T7233.1 2009 GB/T8110气体保护电弧焊用碳钢低合金钢焊丝 G;B/T9439一2010灰铸铁件 GB/T9444一2007铸钢件磁粉检测 GB/T10095.1一2008圆柱齿轮精度制第1部分;轮齿同侧齿面偏差的定义和允许值 GB/T10095.2一2008圆柱齿轮精度制第2部分;径向综合偏差与径向跳动的定义和允许值 GB/Tl1345一2013焊缝无损检测超声检测技术、检测等级和评定 GB/T13306 标牌 GB/T16746锌合金铸件 GB/29712一2013焊缝无损检测超声检测验收等级 GB/T50561建材工业设备安装工程施工及验收规范 JB/T5000.15一2007重型机械通用技术条件第15部分;锻钢件无损检测 JB/T63962006大型合金结构钢锻件技术条件 JB/T6397一2006 大型碳素结构钢锻件技术条件 JB/T6402一2006 大型低合金钢铸件
GB/T32994一2016 JC/T401.3建材机械用铸钢件第3部分;缺陷处理规定 JC/T402水泥机械涂漆防锈技术条件 JC/T406水泥机械包装技术条件 JC/T532建材机械钢焊接件通用技术条件 型号与基本参数 3.1型号 -回转窑简体公称长度(m) -回转窑简体变径公称内径(m),无变径可省略 -回转窑简体公称内径(m) -回转窑代号 示例1筒体内径为4m,窑体长度60m的回转窑标记为 水泥工业用回转窑 GB/T32994一2016 Y4×60 示例2:筒体内径为6m,简体扩大内径为6.4m,窑体长度90m的回转窑标记为 GB/T329942o16 Y6/6.4×90 水泥工业用回转窑 3.2基本参数 回转窑的基本参数应包含表1中的内容 表1回转窑基本参数 项目 基本参数 规格/m 公称内径(3一6.4)×公称长度(40110 产量/(t/d 50012000 功率/kw 37~1200 二5.5 主传动转速/(n r/min) s15 辅助传动转速/r/h 窑体斜度 3.5%、4.0% 挡轮型式 液压或机械 注:窑体斜度指简体倾斜角度的正弦值 要求 基本要求 4.1 4.1.1回转窑产品应符合本标准的规定,并按规定程序批准的设计图样,技术文件和技术规范制造、安 装和使用
本标准和设计图样,技术文件和技术规范未规定的技术要求,应符合相关国家标准及行业标 准中的有关规定
4.1.2图样上机械加工面的未注公差值的极限偏差应符合GB/T1804一2000中m级的规定,非机械
GB/T32994一2016 加工面的未注尺寸公差值的极限偏差应符合GB/T1804一2000中v级的规定,机械加工的未注形位公 差值应不低于GB/T1184一1996中K级的规定 4.1.3焊接件应符合JC/T532的规定
碳钢焊条,低合金钢焊条和焊丝应分别符合GB/T5117.,GB/T5118和GB/T8110的规定 4.1.4 4.1.5外购件、外协件应符合有关标准的规定,并应有合格证和相关检验结果
4.2整机要求 4.2.1回转窑的基本参数应符合表1或设计图纸和相关技术文件规定 4.2.2回转窑各轴承温升应符合4.5.3的规定
4.2.3回转窑的安全防护装置应符合4.6的规定 4.2.4回转窑的油漆不应有腐蚀、剥落,机加工件不应有磕碰等现象
4.2.5电气安全应符合GB5226.1的规定 4.3主要零部件要求 4.3.1筒体 4.3.1.1筒体所选材料使用性能应符合以下要求: a)对于筒体内径不大于4m的窑,应不低于GB/T700一2006中的Q235B b 对于简体内径大于4m的窑,应不低于GB/T700一2006中的Q235C e)对于特殊环境使用的回转窑,筒体所选材料使用性能应与对应的使用环境相匹配 4.3.1.2筒体钢板表面质量应符合GB/T3274的规定
4.3.1.3 对于厚度不小于38mmm 或轧制宽度超过1900mm 的钢板,下料前应对成材边缘宽度为 60mm的区域内进行超声检测,其质量等级应达到GB/T2970一2004表4中的】级
除轮带下和轮带两侧的过渡钢板外,筒体图样中的钢板宽度(即筒体小段节的长度)制造时可 4.3.1.4 按以下要求进行调整 a调整后齿圈下段节环向焊缝与弹簧板连接焊缝的距离应不小于100mm b)调整后环向焊缝与人孔门孔边距离应不小于100mm 4.3.1.5除进料端锥形筒体外,其他筒体小段节的最短长度应不小于1m,同一跨内长度小于1.5m的 小段节不应多于1节
4.3.1.6筒体小段节钢板作环向拼接时,每个小段节的纵焊缝不应多于2条
4.3.1.7筒体各相邻段节的纵向焊缝应相互错开45"以上,最短拼板弧长不应小于1/4周长
4.3.1.8筒体段节纵向焊缝对口错边量b应不大于1.5mm,环向焊缝对口错边量b
应不大于 2.0mm,如图1所示 纵向焊缝 环向焊缝 说明 纵向媒缝对口错边量 b1 -环向媒缝对口错边量 b S 简体钢板厚度
图1筒体焊缝对口错边量示意 ,如 4.3.1.9简体段节纵向焊缝区域的形状应与简体圆形理论值一致,其偏差值E
应不大于2.0mm, 图2所示
GB/T32994一2016 说明 弧形样板; A E 筒体实际形状偏差值; 9 -样板弦长; S 简体钢板厚度; D 筒体公称内径
图2筒体段节纵向焊缝区域表面形状示意 4.3.1.10筒体段节环向焊缝区域相邻筒体的母线应在同一直线上,偏差E应不大于2.0mm,如图3 所示
说明 C 条形样板; B -样板长度; -筒体段节母线偏差值 E S 筒体钢板厚度 图3筒体段节环向焊缝区域表面形状示意 4.3.1.11筒体小段节内径公差应符合表2的要求
表2筒体小段节内径公差 筒体内径/m1 3.00 4.00 5.00 6.00 公差/mm 士l.0 士1.5 士2.0 士3.0 注:对于其他筒体内径的公差,可按表中参数等差计算选取
4.3.1.12筒体小段节同一横截面上的最大直径与最小直径之差应符合如下要求 安装轮带或大齿圈处同一筒体小段节不应大于筒体公称内径的0.15%; a b其余同一小段节不应大于筒体公称内径的0.20%
4.3.1.13 不等厚钢板对接时,当两板厚度差大于薄板厚度的30%或超过5mm时,应将厚板段节外壁 加工成过渡圆锥面,如图4所示
过渡圆锥面的表面粗糙度Ra的最大允许值为l2.5m,宽度L应不
GB/T32994一2016 小于两板厚度差值的5倍 说明 厚板厚度 S S -薄板厚度; 过渡圆锥面宽度 图4厚板过渡圆锥面示意 4.3.1.14出厂两相邻大段节在接缝处的周长差应不大于0.15%的筒体内径,且不超过6.0mm.
4.3.1.15筒体出厂段节两端的端面偏差f应不大于1.0mm,见图5
说明 端面偏差 图5筒体出厂段节端面偏差示意 4.3.1.16出厂大段节中心线的直线度应符合如下要求 安装轮带与大齿圈处的段节为声10 a mm; 其余段节为声5.0 b mm
4.3.1.17出厂大段节的长度偏差为该段节长度的士0.025%
4.3.1.18出厂段节两端的焊接坡口在制造厂内应采用切削加工
4.3.1.19轮带下筒体的垫板应符合如下要求 a)垫板固定用焊缝和垫板本身不应与筒体的纵焊缝重叠,两种焊缝边缘的距离应不小于 50mm; b 垫板与筒体焊前应紧密贴合; 垫板与简体焊接后应对垫板外表面进行加工 c 与焊接于筒体的定位挡块相遇的纵焊缝应磨平
d 4.3.1.20筒体的人孔门等开孔应符合如下要求 a)加工表面粗糙度Ra的最大允许值为25am孔口四周上下棱角应倒圆 b)简体焊缝处不应开孔,且孔边缘与焊缝边缘的距离应不小于100mm e)孔边缘60mm内进行超声检测,其质量等级应达到GB/T2970-2004表4中的级
4.3.1.21焊缝应饱满,最低点不应低于基体金属表面,且超出基体金属表面的高度应符合如下要求 简体内部烧成带及相邻区域应不大于0.5 a mm; b)简体内部除烧成带及相邻区域外的区域应不大于1.5 mm; 筒体外部应不大于3.0 c mm
GB/T32994一2016 4.3.1.22焊缝咬边深度不应大于0.5mm,连续长度不应大于100mm
每条焊缝的咬边总长度不应超 过该焊缝长度的10%
4.3.1.23简体每一条焊缝均应超声检测,对用超声检测发现的可疑处,可用射线检测进一步评定,媒缝 同一部位返修次数不应超过两次,检测要求如下 当采用超声检测时,检测等级按GB/T113452013表A.1中的B级,验收等级达到 a GB/T297122013表A.l中的2级; b 当采用射线检测时,质量等级应达到GB/T33232005中的皿级 4.3.2大齿圈 4.3.2.1大齿圈所用材料使用性能应不低于JB/T6402一2006中的ZG35Mn. 4.3.2.2大齿圈应进行热处理,精加工后齿顶圆表面硬度应不低于185IHB
4.3.2.3大齿圈的制造精度应符合GB/T10095.1一2008,GB/T10095.2一2008中的9级
大齿圈加工后轮缘厚度应均匀,其偏差为轮缘设计厚度的 4.3.2.4 一5%十10%
4.3.2.5大齿圈粗加工后,齿面至向内60mm范围内和重点受力区域应进行超声检测,质量等级达到 GB/T7233.l2009表1中的3级
4.3.3小齿轮 4.3.3.1小齿轮所用材料使用性能应不低于JB/T63962006中的35CrMo 4.3.3.2小齿轮应进行调质处理,精加工后齿顶圆表面硬度不低于230HB,小齿轮齿顶圆硬度应比大 齿圈齿顶圆硬度高20HB以上
4.3.3.3小齿轮的制造精度应符合GB/T10095.1一2008,GB/T10095.2一2008中的9级
4.3.3.4小齿轮粗加工后应进行超声检测,质量等级应达到JB/T5000.15-2007表1中的川级
4.3.4小齿轮轴 4.3.4.1小齿轮轴所用材料使用性能不应低于JB/T63972006中的45锻钢的规定
4.3.4.2小齿轮轴应进行调质处理,精加工后外圆表面硬度应不低于230HB 4.3.4.3小齿轮轴粗加工后机加工面应进行超声检测,质量等级应达到JB/T5000.15一2007表1中的 级
4.3.5托轮 4.3.5.1托轮所用材料使用性能不应低于JB/T6402一2006中ZG35CrlMo的规定
4.3.5.2托轮进行热处理,精加工后外圆表面硬度应不低于190HB
4.3.5.3托轮外圆硬度应比轮带外圆硬度高20HB以上
4.3.5.4托轮粗加工后的轮缘、轮毂的厚度偏差不应超过设计尺寸的5%
4.3.5.5托轮外圆直径公差等级按GB/T1800.2一2009表1中的ITl1
4.3.5.6外圆表面中心线对轴孔中心线(基准)的同轴度公差等级应不低于GB/T1184一1996表B4中 的8级,公差值根据外圆直径选取 4.3.5.7托轮外圆柱面圆柱度公差为0.2mm
4.3.5.8托轮粗加工后机加工面应进行超声检测,质量等级应达到GB/T7233.1一2009表1中的3级
4.3.6托轮轴 4.3.6.1托轮轴所用材料使用性能应不低于JB/T6397一2006中的45锻钢的规定
4.3.6.2托轮轴应进行调质处理,调质后硬度应不低于210HB.
GB/T32994一2016 4.3.6.3轴表面粗糙度Ra的最大允许值应符合如下要求 a)与衬瓦和密封件配合处为1.6Am b)与托轮配合处为3.2Mm. 4.3.6.4轴与托轮配合处的轴径对两端轴瓦处轴颈的同轴度公差等级应不低于GB/T1184一1996表 B4中的7级,公差值根据托轮处轴径选取
轴与托轮和衬瓦配合处的圆柱度公差等级应不低于GB/Tl18! 4.3.6.5 1996表B2中的7级,公差 值根据托轮和衬瓦配合处的轴径选取
若轴径大于或等于600mm,圆柱度公差值应符合表3的要求
表3轴与托轮和衬瓦配合处的圆柱度公差 轴径/mm 600 700 800 900 公差/mm 0.023 0.026 0.029 0.032 注:对于大于600mm的其他规格的轴径,按本表中参数等差计算选取
4.3.6.6托轮轴粗加工后机加工面应进行超声检测,质量等级应达到JB/T5000.15一2007表1中的 级
4.3.7轮带 4.3.7.1轮带所用材料使用性能应不低于JB/T6402一2006中的ZG35Mn的规定
4.3.7.2轮带应进行热处理,精加工后外圆表面硬度应不低于170HB
4.3.7.3轮带内径与筒体垫板外径应配做,保证设计的间隙要求
4.3.7.4轮带粗加工后机加工面应进行超声检测,质量等级达到GB/T7233.1一2009表1中的3级
4.3.7.5轮带外圆直径公差为GB/T1800.2一2009表1中IT0. 4.3.7.6轮带内外圆柱面中心线的同轴度公差等级应不低于GB/T1184一1996表B4中的8级,公差 值根据轮带外径选取
4.3.7.7轮带外圆柱面圆柱度公差为0.3mm
4.3.7.8轮带与挡轮接触角度偏差均为士3'
4.3.8挡轮 4.3.8.1挡轮所用材料使用性能应不低于JB/T6402一2006中的ZG35CrlMo的规定
4.3.8.2挡轮应进行热处理,加工后工作面硬度应不低于210HB 4.3.8.3挡轮粗加工后机加工面应进行超声检测,质量等级应达到GB/T7233.1一2009表1中的3级
4.3.9挡轮轴 4.3.9.1挡轮轴所用材料使用性能应不低于JB/T6397一2006中的45锻钢
4.3.9.2挡轮轴应进行调质处理,调质后硬度应不低于210HB
4.3.9.3挡轮轴粗加工后机加工面应进行超声检测,质量等级应达到JB/T5000.15一2007表1中的 皿级 4.3.10托轮轴承衬瓦 4.3.10.1托轮轴承衬瓦所用材料使用性能应符合如下要求 采用铸造铝青铜时,应不低于GB/T1176- 2013中的ZCuAl10Fe3 a b采用铸造锌合金时,应不低于GBy/T1175一1997中的ZA27.
注锌合金可采用尚未录人该标准由ZA27衍生的新品种ZA303
GB/T32994一2016 4.3.10.2锌合金衬瓦的铸件质量应符合GB/T16746的规定,铜合金衬瓦参照GB/T16746执行
4.3.10.3衬瓦径向许用比压应不低于4.5MPa,轴向止推面比压应不低于4MPa,硬度不小于 100HB 4.3.10.4不刮瓦衬瓦内圆柱面直径应大于托轮轴轴颈公称直径,其差值为托轮轴轴颈的公称直径 0.2%0.3%
4.3.10.5衬瓦内外圆柱面中心线的同轴度公差等级不应低于GB/T1184一1996表B4中的7级,公差 值根据衬瓦内径选取
4.3.10.6衬瓦肩端面对内圆柱面的垂直度公差等级应不低于GB/T1184一1996表B3中的6级,公差 值根据瓦肩外径选取
4.3.11托轮轴承球面瓦 4.3.11.1托轮轴承球面瓦所用材料使用性能应不低于GB/T9439一2010中的HT200. 4.3.11.2托轮轴承球面瓦铸件不应有裂纹和影响使用的砂眼、,缩孔等缺陷
4.3.11.3托轮轴承球面瓦应进行水压无渗漏试验
4.3.11.4球面瓦的球心对内圆柱面轴线及其沿轴向的对称中心线的位置度公差为S40.10 mm
4.3.12托轮轴承座 4.3.12.1托轮轴承座所用材料使用性能应不低于GB/T94392010中的HT200. 4.3.12.2托轮轴承座铸件不应有裂纹和影响使用的砂眼、缩孔等缺陷
4.3.12.3同一托轮轴承组两端的轴承座中心高度差应符合GB/T1800.2一2009表1中的IT10.
4.3.13
铸钢件缺陷处理 4.3.13.1托轮、轮带、挡轮、,大齿圈的允许补焊条件按照4.3.13.2执行,允许不补焊的条件按4.3.13.3 执行,铸钢件缺陷处理的其他要求应符合Jc/T401.3的规定 4.3.13.2粗加工后的托轮、轮带、挡轮、大齿圈的允许补焊条件为 切凿宽度不超过工作宽度的10%; a b 切凿深度不超过壁厚的25%; e)切凿面积总和不超过该面总面积的2% d 连同毛坯件的切凿面积在内总和小于该面总面积的4%
4.3.13.3精加工后轮带、托轮、挡轮及大齿圈的表面允许存在的缺陷周边应进行修整,无毛刺和尖角, 允许不补焊条件为 缺陷的长度和宽度均小于25 n,深度小于5 a m mm; b)两个缺陷的最小距离应大于200" mm; 单个零件上缺陷的数量不超过10处 c 4.3.13.4焊补前应预热,焊补后应进行热处理
焊补区域精加工后应进行磁粉探伤,质量等级应达到 GB/T9444一2007表1中的2级
4.3.14监测装置" 4.3.14.1回转窑需配置筒体扫描仪来监测全长筒体的运行温度,对非正常工况应预警,必要时跳停
4.3.14.2回转窑支承装置和挡轮装置的主要轴承需配置检测温度的装置,对超出正常运行的温度应预 警,必要时跳停
4.3.14.3对液压挡轮的回转窑,需要配置窑位移监测装置,超出设计允许范围时应报警,必要时跳停
GB/T32994一2016 装配和安装要求 回转窑的装配和安装应符合GB/T50561的相关要求
4.5试运转要求 4.5.1运转时,先开启设备配备的润滑和液压系统运行30min后再开启电机运转
4.5.2空载运转应在窑砌内衬之前进行,空运转试验时间应符合如下要求 a)电动机不应少于2h; b)主电动机带动主减速器不应少于2h; 辅助电动机带动辅减速器不应少于2h; 辅助电动机带动回转窑不应少于2h; d 主电动机带动回转窑不应少于4h; e f 液压系统,冷却系统、润滑系统及泵、阀不应少于4h
4.5.3空运转时的轴承温升应符合如下要求 托轮滑动轴承温升不应超过30K; a b)电动机、减速器和小齿轮装置等轴承温升不应超过25K
4.5.4运转时应无异常振动和噪声,润滑和密封正常,各处螺栓不应有松动现象
主电机试运转时,从低迷逐步提高到最高迷,运行时间不应少手1h,额定转速下运行时间不应 4.5.5 少于1h
4.5.6回转窑砌衬后点火前转速不应超过0.6r/nmin,以防衬体松动
4.6安全要求 4.6.1在回转窑传动装置中,应设置当辅助传动装置启动时能切断主电动机电源的连锁装置
4.6.2回转窑辅助传动装置应另设应急独立动力源
4.6.3回转窑传动装置中的高转速联轴器、,开式齿轮等传动部件应设置防护罩
4.6.4回转窑辅助传动装置应安装制动装置
4.6.5在运行回转窑前,对所有安全元件及检测仪表进行测试,确认仪表正常运转后,方可启动转窑
4.7防锈涂漆要求 4.7.1回转窑零部件出厂前应防锈处理
4.7.2回转窑零部件涂漆应符合JC/T402的规定
试验方法 整机试验方法 5.1 5.1.1轴承温升按5.4.1的方法检测
5.1.2安全防护装置按5.,5的方法检测
5.1.3回转窑外观通过目视检测
5.1.4电气安全按GB5226.1给出的方法检测
5.2主要零部件的试验方法 5.2.1回转窑主要零部件的所用材料使用性能按相关标准进行检测并提供检测报告
5.2.2回转窑主要零部件表面粗糙度采用粗糙度检测仪或粗糙度比较样块进行检测
GB/T32994一2016 5.2.3主要零部件的硬度采用便携式硬度检测仪检测,直径2m以下检测点数不应少于4个,直径 2m4m检测点数不应少于6个,4m~6m检测点数不应少于8个,6m以上检测点数不应少于 10个,检测点不应在一个截面上,且分布均匀
5.2.4对于4.3.1.2筒体钢板表面质量的检测按GB/T3274给出的方法进行
5.2.5对于4.3.1.3中钢板成材边缘检测按GB/T29702004给出的方法进行
5.2.6表4中要求采用目视检测
表4 采用目视检测要求 序号 检测项目 要求条款 4.3.1.6 筒体每个小段节纵焊缝条数 垫板固定用焊缝和垫板本身不应与筒体的纵焊缝重叠 4.3.1.19a 垫板与简体接后应加工垫板外表面 4.3.l.19e) 与焊接于筒体的定位挡块相遇的纵媒缝应磨平 4.3.1.19d 筒体人孔门四周上下棱角均应倒圆 4.3.1.20a 筒体焊缝处不应开孔 4.3.1.20b 4.3.11.2 托轮轴承球面铸件不应有裂纹和影响使用的砂眼,缩孔等的缺陷 5.2.7对于4.3.1.5筒体同一跨内长度小于1.5m的小段节节数用钢卷尺配合目视检测
5.2.8对于4.3.1.7相邻段节的纵向焊缝相互错开角度用角度测量仪配合目视检测
5.2.9对于4.3.1.8简节焊缝对口错边量、4.3.1.21焊缝超出基体金属表面、4.3.1.22焊缝咬边深度用焊 缝检验尺检测
5.2.10对于4.3.l.9筒体纵向焊继区域形状用弦长不小于筒简体内径五分之一且不小于】m的孤形样 板检测
对于4.a.1.10环向焊缝区域相邻筒体直线偏差用长座不小于500mm的条形样板检谢
5.2.11 5.2.12对于4.3.1.11简体段节内径用钢卷尺检测
5.2.13对于4.3.1.12通过在同一简体小段节的两端面,用钠卷尺检测每个端面至少四处简体内径,最 大与最小差值应符合4.3.1.12的要求
5.2.14对于4.3.1.13通过焊缝检验尺或者钢板尺及角度尺检测
5.2.15对于4.3.1.14出厂两相邻大段节在接缝处的周长用钢卷尺检测,其差值应符合4.3.1.14的 要求
5.2.16对于4.3.1.15简体出厂段节两端的端面偏差应在机床上找平后,两端面吊两根垂线,测量垂线 下端与筒体下端的距离
每一端面测量不少于2处
5.2.17对于4.3.1.16通过将出厂大段节内径沿圆周方向至少分为四等分,将等高块放置于大段节两端 相同等分处,铁丝或粉线放置在等高块上用钢板尺检测筒体表面与铁丝或粉线的距离,最大与最小差值 应与4.3.1.16出厂大段节中心线的直线度的要求相同
5.2.18对于4.3.1.17出厂大段节长度使用钢卷尺检测 5.2.19对于4.3.1.19b)轮带下筒体与垫板焊前紧密贴合程度用0.5mm塞尺检测,最大塞人深度不应 大于100mm,且每块垫板塞人深度小于100mm的数量不应多于2处
5.2.20对于4.3.1.20e)孔边缘超声检测按GB/T29702004给出的方法进行
5.2.21对于4.3.1.23筒体焊缝检测按GB/T11345一2013给出的方法进行
5.2.22对于4.3.2.3大齿圈及4.3.3.3小齿轮的制造精度检测,按GB/10095.1一2008和GB/T10095.2 2008给出的方法进行
10o
GB/T32994一2016 5.2.23对于4.3.2.4大齿圈的轮缘和4.3.5.4托轮的轮缘,轮毂厚度,采用卷尺、钢板尺检测,检测点数 不应少于4个且分布均匀
5.2.24对于大齿圈、托轮、轮带、挡轮的超声检测,按GB/T7233.1一2009给出的方法进行
5.2.25对于小齿轮、小齿轮轴、托轮轴、挡轮轴的超声检测,按JB/T5000.152007给出的方法进行
5.2.26对于4.3.5.5托轮外圆直径和4.3.7.5轮带外圆直径在机床上用千分尺、卡尺或x尺进行检测
5.2.27对于4.3.5.6中托轮外圆表面中心线对轴孔中心线的同轴度、4.3.6.4托轮轴与托轮配合处的轴 径对两端轴瓦处轴颈的同轴度、4.3.7.6轮带内外圆柱面中心线的同轴度、4.3.10.5衬瓦内外圆柱面中心 线的同轴度,用百分表在机床上进行检测,检测点不应少于3处
5.2.28对于4.3.5.7托轮外圆、4.3.6.5托轮轴与托轮和衬瓦配合处、4.3.7.7轮带外圆的圆柱度检测,用 百分表在车床上或平台上进行检测,检测截面不应少于3处 5.2.29对于4.3.7.8中轮带与挡轮接触角度采用 万能角度尺进行检测
5.2.30对于4.3.10.2锌合金衬瓦的铸件质量按GB/T167 746给出的方法进行检测
5.2.31对于4.3.10.4不刮瓦衬瓦内圆柱面直径 ,在衬瓦整体加工后、剖分前用内径千分尺进行检测
5.2.32对于4.3.10.6衬瓦肩端面对内圆柱面的垂直度,用百分表在机床上进行检测
5.2.33对于4.3.11.3通过对托轮轴承球面瓦进行水压试验进行检测,压力为0.6MPa,保压30nmin. 5.2.34对于4.3.12.3轴承座中心高度差采用水平仪、直尺、高度尺配合检测 5.2.35对于4.3.13.3允许不补焊的缺陷采用钢卷尺检测,缺陷数量采用目视检测
5.2.36对于4.3.13.4粗加工焊补区域磁粉检测按GB/T9444一2007给出的方法进行
5.2.37设备监测装置采用目视检测
5.3装配和安装试验方法 回转窑装配和安装检测按GB/T50561给出的方法进行
5.4试运转试验方法 5.4.1对于4.5.3托轮滑动轴承、电动机、减速器和小齿轮温升通过采集测温仪数据获得
5.4.2对于4.5.4轴承振动用便捷式测振仪检测,润滑和密封渗漏情况、螺栓是否松动均用目视检测
5.5安全试验方法 5.5.1对于4.6.1,启动辅助传动电源,通过目视观察切断主电动机电源的连锁装置是否正常
5.5.2对于4.6.2,关闭主电源,启动应急独立动力源,通过目视观察辅助传动装置是否启动
5.5.3对于4.6.3,通过目视检测
对于4.6.A,关闭辅助传动装置电源,通过目视观察制动装置是否正常 5.5.4 5.6防锈涂漆试验方法 对于4.7.1、4.7.2涂漆防锈采用Jc/T402给出的方法进行
检验规则 6.1检验分类 检验分为出厂检验和型式检验
6.2 出厂检验 6.2.1产品零部件应经制造厂质量检验部门逐件检验,部分部件可在用户处进行出厂检验
11
GB/T32994一2016 6.2.2产品零部件按表5完成出厂检验,检验合格后签发合格证书
6.2.3出厂检验质量分类按照表5的规定
表5出厂检验质量分类表 分类 对应标准条文 检测方法 项目 筒体材料的选取 4.3.1. 5.2.l 5.2.5 筒体钢板的超声检测 4.3.l.3 筒体焊缝的超声检测 4.3.1.23 5.2.21 关键项 大齿圈,托轮,轮带、挡轮的超声检测 4.3.2.5、4.3.5.8、4.3.7.4、4.3.8.3 5.2.24 小齿轮,小齿轮轴、托轮轴、 4.3.3.4、4.3.4.3、4.3.6.6、4.3.9.3 5.2.25 挡轮轴的超声检测 筒体纵向焊缝的错开角度 4.3.1.7 5.2.8 筒体焊缝错边量 4.3,1.8 5.2.9 筒体纵向焊缝区域表面形状 4.3.l.9 5.2.10 简体环向烬缝区城表面形状 4.3.1.10 5.2.ll 大段节端面周长差 4.3.1.14 5.2.15 段节端面偏差 .15 5.2.16 4.3.1. 重要项 4.3.1.16 5.2.17 出厂大段节中心线直线度 垫板的要求 4.3.1.19 5.2.6、5.2.19 筒体炽缝的咬边 4.3.1.22 5.2.9 大齿圈、小齿轮的制造精度 4.3,2.3、4.3.3.3 5.2.22 托轮轴的表面粗糙度 4.3.6.3 5.2.2 球面瓦的水压试验 4.3.11.3 5.2.33 铸钢件的缺陷规定 4.3.13 5.2.35、5.2.36 4.3.1.12 5.2.13 筒体段节直径差值 筒体不等厚钢板对接 .3.1.13 5.2.14 大段节长度公差 4.3.1.17 5.2.18 -般项 筒体焊缝的要求 4.3.1.21 5.2.9 大齿圈,小齿轮,小齿轮轴,托轮、 4.3.2.2、4.3.3.2、4.3.4.2、4.3.5.2、 5.2.3 托轮轴、轮带挡轮、挡轮轴的硬度 4.3.6.2、4.3.7.2、4.3.8.2、4.3.9.2 轮带及挡轮的接触角度 4.3.7.8 5.2.29 6.3型式检验 型式检验项目为第4章全部条款
有下列情况之一时应进行型式检验 新产品试制定型鉴定时; a b老产品在结构、材料、工艺有较大改变可能影响产品性能时; 产品长期停产后恢复生产时; d)交收检验结果与上次型式检验有较大差异时 12
GB/T32994一2016 6.4判定规则 6.4.1出厂检验时,表4中关键项重要项中任何一项或一般项中两项不符合要求时,产品判定为不合 格
有不合格项的产品应由制造厂返修处理,直至经检验部门复检合格后,方可出厂
6.4.2型式检验时,从交收检验合格的产品中随机抽取进行检验
若有项目不合格,允许修复、调整一 次
如复查合格,则判该批产品为合格
否则判为不合格品,并应立即停产,检查产品制造加工、装配的 全过程 标志包装、运输和贮存 7.1 标志 回转窑应在适当而明显的位置固定产品标牌,其型式和尺寸应符合GB/T13306的规定,标牌上的 内容应包括; a)产品型号和名称; 主要技术参数 b e)供应商名称和地址 d出厂编号和出厂日期; 产品执行标准
e) 7.2包装和运输 7.2.1出厂筒体大段节两端以及轮带处筒体段节处应加支撑装置防止变形
7.2.2拆成两半运输的大齿圈,应采取防止变形的加固措施
7.2.3回转窑包装未规定事项还应符合Jc/T406的规定
7.2.4包装箱外和裸装件应有文字标记和符号,内容应包括 a)收货单位及厂址; b 主要产品名称、型号和规格 出厂编号和箱号 d 外形尺寸、毛重和净重; e)制造厂名称
7.2.5随机技术文件应包括 a)产品使用说明书; b 产品合格证 c)装箱单; d) 产品安装图
7.3贮存 长期堆放的轮带,大齿圈等重要零件,应水平存放,其上放置重物时支承点应上下对齐,超过3点支 撑时应使用等高块,同时应采取防潮、防雨措施
水泥工业用回转窑GB/T32994-2016
水泥工业是我国重要的基础性工业之一,而回转窑则是水泥生产过程中经常使用的设备。回转窑是通过旋转筒体来完成物料的热处理和化学反应的设备,在水泥生产过程中扮演着至关重要的角色。
回转窑的分类比较多,主要有干法水泥回转窑、湿法水泥回转窑、冶金行业的回转窑等。干法水泥生产线上的回转窑,是通过将石灰石、粘土等原材料混合后破碎并配以相应的生料搅拌均匀,然后进入回转窑进行烧成,制成水泥熟料。湿法水泥生产线上的回转窑,则是先把生料加水调整至适宜的含水率,再进入回转窑进行烧成,最后制成水泥熟料。
GB/T32994-2016是我国针对水泥工业用回转窑制定的标准。该标准规定了回转窑的要求、分类、名称、基本参数和规格、技术要求、试验方法、检验规则和标志、包装、运输和贮存等方面的内容。具体来说,标准中规定了回转窑的长度、直径、旋转速度、倾角、筒体内衬等技术要求,以及对回转窑进行检验的方法和标准。
总之,在水泥生产过程中,回转窑是至关重要的设备,其稳定性和高效性对水泥生产的质量和效率都有着很大的影响。因此,严格按照标准进行回转窑的设计、制造和检测,确保其符合要求,才能保证水泥生产的顺利进行。