GB/T26610.4-2014
承压设备系统基于风险的检验实施导则第4部分:失效可能性定量分析方法
Guidelineforimplementationofrisk-basedinspectionofpressureequipmentsystem―Part4:Quantitativeanalysisapproachoffailurelikelihood
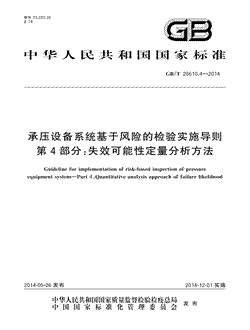
- 中国标准分类号(CCS)J74
- 国际标准分类号(ICS)23.020.30
- 实施日期2014-12-01
- 文件格式PDF
- 文本页数132页
- 文件大小2.03M
以图片形式预览承压设备系统基于风险的检验实施导则第4部分:失效可能性定量分析方法
承压设备系统基于风险的检验实施导则第4部分:失效可能性定量分析方法
国家标准 GB/T26610.4一2014 承压设备系统基于风险的检验实施导则 第4部分失效可能性定量分析方法 Guidelineforimplementationofrisk-basedinspectionofpressure qipmemtsystem一Part4:Quanttateanalysisappraehftalurelikelihodl 2014-05-06发布 2014-12-01实施 国家质量监督检监检疫总局 发布 国家标准花管理委员会国家标准
GB/T26610.4一2014 目 次 前言 范围 规范性引用文件 术语和定义、符号 缩略语 失效可能性定量分析程序 同类设备平均失效概率 设备修正系数 管理系统评价系数 2 超标缺陷影响系数 2 附录A(资料性附录)失效概率计算表 附录B(规范性附录)管理系统评价工作手册 附录c规范性附录减薄次因子确定 26 附录D规范性附录应力腐蚀开裂次因子确定 63 附录E规范性附录)高温氢蚀(HTHA)次因子确定 81 附录F(规范性附录炉管损伤次因子确定 84 附录G(规范性附录)机械疲劳损伤次因子确定 93 附录H规范性附录)设备衬里破坏次因子确定 98 附录1(规范性附录)外部损伤次因子确定 103 附录J规范性附录)脆性断裂次因子确定 114 附录K(规范性附录安全阀失效可能性计算 123 附录L(规范性附录)热交换器管束失效可能性计算 29
GB/T26610.4一2014 前 言 GB/T26610(《承压设备系统基于风险的检验实施导则》分为5个部分 -第1部分:基本要求和实施程序; 第2部分基于风险的检验策略; 第3部分;风险的定性分析方法 第4部分;失效可能性定量分析方法 第5部分;失效后果定量评价方法 本部分为GB/T26610的第4部分
本部分按照GBT1.1 -2009给出的规则起草
本部分参考了APRP581《基于风险的检验》,并结合我国的实际情况制定
本部分由全国锅炉压力容器标准化技术委员会(SAc/Tc262)提出并归口
本部分起草单位;合肥通用机械研究院、特种设备检测研究院、石油化工股份有限公司、 石油天然气股份有限公司、石油化工股份有限公司广州分公司,石油化工股份有限公司齐 鲁分公司、广州市特种设备检测研究院、浙江省特种设备检测研究院
本部分主要起草人:陈学东、艾志斌、贾国栋、刘汇源、,胡久韶、吕运容、王辉,史进、陈照和、王建军、 陈轩,李群友、王笑梅、高亮,叶伟文,刘富君
本部分为首次制定
GB/T26610.4一2014 承压设备系统基于风险的检验实施导则 第4部分:失效可能性定量分析方法 范围 GB/T26610的本部分规定了承压设备系统基于风险的检验(以下简称RBD)过程中失效可能性的 定量分析方法
本部分适用于GB/T26610.1中所指的承压设备系统
规范性引用文件 下列文件对于本文件的应用是必不可少的
凡是注日期的引用文件,仅注日期的版本适用于本文 件
凡是不注日期的引用文件,其最新版本(包括所有的修改单)适用于本文件 GB18306地震动参数区划图 GB/T19624一2004在用含缺陷压力容器安全评定 GB/T26610.1承压设备系统基于风险的检验实施导则第1部分:基本要求和实施程序 GB/T26610.5一2014承压设备系统基于风险的检验实施导则第5部分:失效后果定量评价 方法 术语和定义、符号 3.1术语和定义 GB/T26610.1界定的术语和定义适用于本文件
3.2符号 下列符号适用于本文件
-设备或管道拟服役时间占剩余寿命的百分数 B 失效概率; F F 设备修正系数; F 同类设备平均失效概率; F 超标缺陷影响系数; F, 管理系统评价系数; 实际厚度,mm T 设备或管道拟连续服役时间,年 T! Ts 剩余寿命,年
缩略语 下列缩略语适用于本文件
GB/T26610.4一2014 TMF:技术模块因子(TechnicalModuleFactor) HB氢鼓泡(HydrogenBlistering Induced Cracking) HIC;氢致开裂(Hydrogen sOHIC;应力导向氢致开裂(Str ressOrientedHydrogenlnducedCre aekin) Cracking SCC;应力腐蚀开裂(StressCorosion Cracking) SSCC;硫化物应力腐蚀开裂(SulfideStressCorrosion Cracking) CISCC;氧化物应力腐蚀开裂(ChlorideStressCorrosion PASCC;连多硫酸应力腐蚀开裂(PolythionicAcidStressCorrosion Creacking) rrosionUnderInsulation) CUI:保温层下腐蚀(Corr ngPresure) MAWP:最高允许工作压力(MaximumAIlowableworkinm OP;操作压力(OprationPressure CA:腐蚀裕量(CorrosionAllowance MEA:乙醇胺(MonoEtobaccoolAmine) DIPA:;二异丙醇胺(Diisopropanolamine DEA:二乙醇胺(Diethylamine) MDEA;甲基二乙醇胺(MethylDethanolAminey DGA:二甘醇胺(DiethyleneGlycolAmine PwHT;焊后热处理(PostweldHeatTreatment) HTHA;高温氢蚀(HighTemperatureHydrogenAttack FMR;现场金相复型(FieldMetallographicRepiceation) AUBT;高级超声反向散射技术(AdvancedUltrasonicBackscatterTechnique) 失效可能性定量分析程序 设备失效可能性的定量分析程序如下 a)确定同类设备平均失效概率,设备修正系数、管理系统评价系数和超标缺陷影响系数,按式(1 计算失效概率F F =F×F;×F×F 具体计算步骤参见附录A
其中,计算管理系统评价系数时,应先按照附录B对企业的管理系统 进行评价
b 根据失效概率计算结果,按照表1确定失效可能性等级
表1失效可能性等级划分 失效可能性等级 失效概率F 0,00000
GB/T26610.4一2014 d 工艺因子
各因子的主要构成如图1所示
7.2计算步骤 设备修正系数的计算步骤如下: a)分别按照7.3一7.6确定技术模块因子,通用条件因子、机械因子和工艺因子; b)将技术模块因子、,通用条件因子、机械因子、工艺因子数值相加,按照表3确定设备修正系数
表3设备修正系数 各因子数值总和 设备修正系数F 1,0 各因子数值总和绝对值的倒数 -1.0~1.0 .0 各因子数值总和 >1,0 设备修正系数 通用条件因子 机械因子 工艺因子 木候块子 减薄次因子 工厂条件次因子 结构复杂性次因子 工艺连续性次因子 计划停车子因子 设备复杂性子因子 应力腐蚀开裂次因子 寒冷气候运行次因子 高温氢蚀次因子 地震活动次因子 管道复杂性子因子 非计划停车子因子 工艺稳定性次因子 炉管损伤次因子 建造规范次因子 机械疲劳损伤次因子 寿命周期次因子 安全阀状态次因子 设备衬里破坏次因子 安全系数次因 维护程序子因子 污垢状态子因子 外部损伤次因子 操作压力子因子 操作温度子因子 腐蚀状态子因子 脆性断裂次因子 清洁状态子因子 振动监测次因子 图1设备修正系数的构成 7.3技术模块因子 7.3.1技术模块因子由减薄次因子,应力腐蚀开裂次因子、高温氢蚀次因子、炉管损伤次因子、机械疲 劳次因子、设备衬里破坏次因子、外壁损伤次因子和脆性断裂次因子构成,用于评价潜在的损伤机理对 失效可能性的影响,主要考虑以下2个因素 运行环境导致的材料损伤程度 a b检验程序对识别或检测损伤程度的有效性
GB/T26610.4一2014 7.3.2技术模块因子的分析包括以下5个步骤 确定潜在的损伤机理 a b 预测每种损伤机理的损伤程度并确定严重程度指数; 评价检验程序对识别或检测损伤程度的有效性 c d)根据严重程度指数和检验程序的有效性(包括检验次数)分别按照附录C附录」确定每种损 伤机理对应的次因子; 将所有损伤机理的次因子相加得到最终的技术模块因子
各种损伤机理对损伤因子的确定方法见附录c一附录了
7.3.3对确定存在某种损伤机理的设备,根据以下几方面的信息或资料来评估设备的损伤程度 a)公开发表的数据; 试验室数据 b c)现场测试数据, d 同类设备的使用经验 e)以往的检验数据
7.3.4如未发现损伤机理,则该设备的技术模块因子为一2
7.3.5对于确定可能存在内部均匀腐蚀损伤的设备,腐蚀速率的取值至少为0.0254mm/年
7.4通用条件因子 7.4.1通用条件因子的组成 通用条件因子的组成如下: a工厂条件次因子; b 寒冷气候运行次因子; 地震活动次因子
将上述3个次因子的数值相加,即为通用条件因子
7.4.2工厂条件次因子 工厂条件次因子的评价主要考虑以下因素 企业管理的总体状况; a b)对装置进行日常维护管理的措施和效果; e)是否存在油漆脱落、保温破损和蒸汽泄漏情况及严重程度
按照表4对工厂条件次因子进行评级和赋值
表4工厂条件次因子赋值 装置条件 级别 赋值 高于现行工业标准要求 -l.0 满足现行工业标准大致要求 略低于现行工业标准大致要求 1.5 明显低于现行工业标准大致要求 4.,0 7.4.3寒冷气候运行次因子 寒冷气候运行次因子可以根据装置现场的最低平均日温度确定
按照表5对寒冷气候运行次因子
GB/T26610.4一2014 进行赋值
对于室内装置,则应考虑最低室内温度 表5寒冷气候运行次因子的赋值 冬季温度 赋值 4以上 -7C4 1.0 -29C一7C以下 2.0 29以下 3.0 7.4.4地震活动次因子 地震活动次因子可以根据GB18306中装置所在的地震动反应谱特征周期分区确定
按照表6对 地震活动次因子进行赋值
表6地震活动次因子赋值 地震动反应谐特征周期区 赋值 1区 2区 1.0 3区 2.0 7.5机械因子 7.5.1机械因子的组成 机械因子的组成如下 a)结构复杂性次因子 b) 建造规范次因子; e)寿命周期次因子 安全系数次因子 d 振动监测次因子
将上述5个次因子的数值相加,即为机械因子
7.5.2结构复杂性次因子 7.5.2.1结构复杂性次因子的分类 结构复杂性次因子分为以下2个子因子 a)设备复杂性子因子; 管道复杂性子因子
b 上述2个子因子分别适用于设备和管道
7.5.2.2设备复杂性子因子 设备复杂性子因子根据设备上的接管数量来确定
所有在用和停用的外径大于或等于50 mm 的 接管和人孔都应计算在内
根据设备的接管数量,按照表7对设备复杂性子因子进行赋值
GB/T26610.4一2014 表7设备复杂性子因子 接管数量 设备类型 塔 全部 20 20~35 36一46 >46 当 10 1017 1823 23 710 >10 压缩机 热交换器 -壳程 <7 316 712 >16 热交换器 管程 9~11 >11 泵 712 1316 >16 赋值 -1,0 1.0 2.0 7.5.2.3管道复杂性子因子 管道复杂性子因子的计算主要考虑下列因素 a)法兰连接面数量(n)管段上的每组法兰连接面复杂性系数为10.0; b注人点数量(n)每个注人点增加的复杂性系数为20.0: 支管数量(n;);以三通而不是注人点的形式接人被评价管段的任何管线(包括排液管、混合三 通、安全阀支管等)都被认为是一条支管,每条支管的复杂性系数为3.0; d)阀门数量(包括除安全阀外的所有阀门,n):每个阀门复杂性系数为5.0
管线总复杂性系数"按式(2)计算 n=(n1×10.0)十(n,×20.0)十(n,×3.0)十(n×5.0) 每米管长的复杂性系数等于总复杂性系数"除以管段的长度L,按照表8对每一管段的复杂性子 因子进行赋值
表8管道复杂性子因子 复杂性系数/m" 赋值 复杂性系数/m" 赋值 n/L<0.1 -3.0 2.0
GB/T26610.4一2014 表9(续 类 赋 所依据规范的状况 值 制造这个设备时还没有正式规范,或未按当时规范制造这类设备 注;“C”类设备的赋值可以根据可靠的行业实践经验在2.010.0范围内进行调整
7.5.4寿命周期次因子 根据设备的已服役年限与设计寿命的比值,按照表10对寿命周期次因子进行赋值
设计时未给出 设计寿命的设备,设计寿命一般设为20年
表10寿命周期次因子 已服役年限与设计寿命的比值7" % 值 赋 07 2.0 875 76~100 1.0 >100 4.0 7.5.5安全系数次因子 7.5.5.1安全系数次因子的组成 安全系数次因子的组成如下 a)操作压力子因子; 操作温度子因子
b 将上述2个子因子的数值相加,即为安全系数次因子, 7.5.5.2操作压力子因子 根据操作压力与设计压力的比值m,按照表11对操作压力子因子进行赋值 表11操作压力子因子 数 = =操作压力/设计压力 值 5.0 n1.0 0,9
GB/T26610.4一2014 表14计划停车子因子 每年计划内停车次数 赋 值 -1.0 1.1一3 3.1一6 l.0 1.5 7.6.2.3非计划停车子因子 根据过去3年里每年非计划停车次数的平均值,按照表15对非计划停车子因子进行赋值
表15非计划停车子因子 每年非计划停车的次数 赋值 -1.5 1.l一3 3,16 2.0 3,0 7.6.3工艺稳定性次因子 根据以下6方面因素来评价装置工艺稳定性,并按照表16对工艺稳定性次因子进行赋值 化学工艺是否特别复杂 a) b 该工艺是否包括任何放热反应或异常苛刻的操作温度或压力; 该工艺是否在本厂或其他企业引发过重大事故 c) d该工艺是否涉及任何未经验证的工艺技术或设计概念,或者该工艺的管道或设备是否要求采 用特殊的材料来建造 控制系统是否满足现行标准;是否包括具有适当安全特性的计算机控制;是否需要和/或配备 了紧急停车系统和控制系统备用电源, 相关工艺操作人员是否经过了工艺培训 表16工艺稳定性次因子 稳定性评价 赋 比平均工艺更稳定 一l.0 与平均工艺稳定性相当 比平均工艺稳定性低 1.0 明显低于平均工艺稳定性 2.0 7.6.4安全阀状态次因子 7.6.4.1安全阀状态次因子的组成 安全阀状态次因子的组成如下 10
GB/T26610.4一2014 a)维护程序子因子 b)污垢状态子因子; c 腐蚀状态子因子 d)清洁状态子因子
将上述4个子因子数值相加,即为安全阀状态次因子
7.6.4.2维护程序子因子 根据安全阀实际的维护状态,按照表17对维护程序子因子进行赋值
表17维护程序子因子 别 赋 值 安全阀维护状态 类 延期维护的安全阀小于5% 一1.0 延期维护的安全阀占大于或等于5%且小于15% 延期维护的安全阀占大于或等于15%且小于25% 1.0 延期维护的安全阀大于或等于25% 2.0 7.6.4.3污垢状态子因子 根据工艺流体的结垢趋势,按照表18对安全阀的污垢状态子因子进行赋值
表18污垢状态子因子 S 结垢趋势 别 赋 值 类 没有大量结垢 具有聚合物或其他结垢物质,在系统的一些部分有过偶然堆积的现象 B 2.0 易结垢,在安全阀和/或系统的其他部件上有过沉积物频繁堆积的现象 4.0 7.6.4.4腐蚀状态子因子 根据工艺流体是否具有腐蚀性和防腐蚀设计,按照表19对腐蚀状态子因子进行赋值
表19腐蚀状态子因子 腐蚀状态 无防腐蚀设计 有防腐设计 是 否 7.6.4.5清洁状态子因子 对于无结垢趋势、无腐蚀物质或其他污染物的工艺流体,按照表20对清洁状态子因子进行赋值
11
GB/T26610.4一2014 表20清洁状态子因子 清洁状态 值 赋 是 一1.0 否 管理系统评价系数 8.1按照如下步骤确定管理系统评价系数 按照附录B对企业的管理系统进行评价 a b根据图2给出的半对数曲线,将管理系统评价分值转换为管理系统评价系数
8.2一般情况下,同一个企业不同装置的管理系统评价系数应该是相同的
该系数对被评估的所有设 备作用相同,不改变各设备间的相对风险排序
100 管理系统评价系数 1002003004005006007008009001000 分值 说明 F,=10l-益
图2管理系统评价分值与管理系统评价系数的关系 超标缺陷影响系数 9.1超标缺陷影响系数的确定 当设备中存在超标缺陷时,应根据设备的原始制造质量及服役过程中是否存在与时间相关的退化 机理,确定超标缺陷影响系数 9.2设备在服役过程中不存在与时间相关的退化机理时超标缺陷影响系数的确定 9.2.1设备中不存在超标缺陷时,取F=1.0
9.2.2设备中存在超标缺陷时,根据下述条件对超标缺陷影响系数进行赋值 超标缺陷在设备定期检验规程允许的范围内,或对其进行合于使用评价合格且安全系数大于 a 2时,取F,=1.0; 对超标缺陷进行合于使用评价合格且安全系数小于2时,取FL b =1.5; e)对超标缺陷进行合于使用评价不合格时,取F=500
12
GB/T26610.4一2014 9.3设备在服役过程中存在与时间相关的退化机理时超标缺陷影响系数的确定 根据服役条件、可能存在的损伤机理、拟服役时间T,和剩余寿命T的比值,按照表21对超标缺 陷影响系数进行赋值
设备的剩余寿命可以根据合于使用评价或成熟的工程经验进行估算
表21设备在服役过程中存在与时间相关的退化机理时的超标缺陷影响系数 服役条件 损伤机理 F 0.5 常温疲劳 0.5B0.8 常温疲劳十腐蚀 0.8GB/T26610.4一2014 附 录A 资料性附录 失效概率计算表 失效概率的计算参照表A.1进行
表A.1失效概率计算表 同类设备平均失效概率 设备类型 破裂口尺寸 6mm 25mm 100mm 破裂 从表2中选择同类设备不同破裂口的平均失效概率 设备修正系数 第1步技术模块因子 识别的损伤机理 减薄/腐蚀(是/否)局部(是/否 高温氢蚀(HTHA)是/否 应力腐蚀开裂(sScc)(是/否) 注:4一7项用于记录应用于技术模块的某些基本信息
并非每个模块都需要所有项,并且提供的以下数据并非 是每个技术模块要求的所有数据 设备在当前工况条件下的服役年限 估算/实测损伤速率 Nelson曲线 b SCC裂纹尺寸或敏感性 确定检验有效性(A,B.C,D,E) 最高有效性检验次数 按照附录C~附录J确定每种潜在的损伤机理对应的次 因子 冗余设计的修正 高度可靠腐蚀速率数据的校正 修正的技术模块因子 确定技术模块因子(如果未识别出明确的损伤机理,则 10 D 第2步通用条件因子 根据表4对工厂条件次因子进行赋值 12 根据表5对寒冷气候运行次因子进行赋值 13 根据表6对地震活动次因子进行赋值 14
GB/T26610.4一2014 表A.1(续 同类设备平均失效概率 确定通用条件因子 第3步机械因子 结构复杂性次因子 根据设备上的接管数量按表7对设备复杂性子因子进 15 行赋值 16 法兰连接面数量×10 1 注人点数量×20 支管数量×3 18 19 阀门数量X5 管道长度(m) 20 根据16、17、18、19项右栏之和/管道长度(m)的计算结 21 果按表8对管道复杂性子因子进行赋值 22 确定结构复杂性次因子(15与21项右栏之和 23 根据表9对建造规范次因子进行赋值 21 根据表10对寿命周期次因子进行赋值 安全系数次因子 根据表11对操作压力子因子进行赋值 25 根据表12对操作温度子因子进行赋值 26 27 确定安全系数次因子(25 和 6项右栏之和) 2 28 根据表13对动设备的振动监测次因子进行赋值 29 确定机械因子(22、23、24、27和28项右栏之和 第4步工艺因子 30 根据表14对计划停车子因子进行赋值 31 根据表15对非计划停车子因子进行赋值 确定工艺连续性次因子(30和31项右栏之和) 32 33 根据表16对工艺稳定性次因子进行赋值 34 根据表17对安全阀维护程序子因子进行赋值 35 根据表18对安全阀结垢状态子因子进行赋值 36 根据表19对安全阀腐蚀状态子因子进行赋值 37 根据表20对安全阀清洁状态子因子进行赋值 确定安全阀状态次因子(34,.35、36,.37项右栏之和 38 39 确定工艺因子(32,33,38项右栏之和 确定设备修正系数(10,14.29,39项右栏之和) 40 管理系统评价系数 15
GB/T26610.4一2014 表A.1(续 同类设备平均失效概率 按附录B进行的管理系统评估结果和图2确定管理系 统评价系数 超标缺陷影响系数 根据第9章确定超标缺陷影响系数 42 调整的失效概率 破裂口尺寸 25mm 00mm 破裂 6mm 13 同类设备平均失效概率×设备修正系数×管理系统评 价系数×超标缺陷影响系数 16
GB/T26610.4一2014 B 附 录 规范性附录 管理系统评价工作手册 B.1概述 从安全生产责任制、工艺安全信息、工艺危害性分析,安全检查,变更管理、操作规程、安全作业、人 员培训、检验和维护,投用前的安全检查应急措施、事故调查、分包管理、安全生产管理系统评估等 14个方面对企业的管理系统进行评价,各方面需要回答的问题数及分值见表B1
根据表B.2表B.15 计算上述14个方面的得分并求和,即可得到管理系统评价分值
B.2 -般要求 B.2.1管理系统评价一般采用面谈和问卷调查等形式进行,被评估企业参与调查的人员应来自于管理 决策层、运行(操作),维护,安全管理、检验检测、教育培训和设计等单位或部门
B.2.2对被指定的面谈人员,应从总管理系统评价系统中选取一组或多组与其专业知识相符的问题进 行调查
对于每一个评分项,若完全做到,则获得100%的分数,若基本做到,则获得50%的分数;若基 本未做到或未做到,则得0分 B.2.3完成管理系统评价,一般情况下至少需要进行4次面谈
调查人员应比较不同面谈人员的各种 回答,并通过对相关书面程序,文件及记录进行实物审查来证实这些回答,针对每个问题获得唯一最符 合实际的答案
表B.1问题数及分值分配 总分值 项目 主题 问题数 实际得分值 安全生产责任制 80 工艺安全信息 80 工艺危害性分析 95 40 安全检查 变更管理 70 操作规程 120 安全作业 80 10 人员培训 60 95 检验和维护 投用前的安全检查 90 10 75 应急措施 事故调查 40 40 13 分包管理 14 35 安全生产管理系统评估 总计 86 1000 17
GB/T26610.4一2014 表B.2安全生产责任制 安全生产责任制 满分 实评分 企业的安全生产责任制度符合国家法律法规的规定,并适时修订 18 安全生产管理机构的设计符合国家法律法规的规定,并适合企业的具体情况 1.2 10 1.3 安全生产管理人员的配备适合企业的具体情况 20 1.4 安全生产管理人员的责任和权限的规定清晰明确 1.5 定期对安全生产管理人员进行考核,考核结果与经济效益挂钩 10 1.6 具有完善的针对安全生产责任制的监督、检查制度,并切实执行 10 安全生产责任制的宣贯方式 a 纳人质量手册(1分): 1.7 张贴于各作业区(1分) 作为操作规范和章程的一部分(1分), 在所有主要培训课程中涉及(1分) 总分数 80 表B.3工艺安全信息 满分 实评分 工艺安全信息 使用或加工的化学品均有数据记录,包含以下内容 化学品的数据记录标明有关物理、化学性质(6分); 12 2.1 化学品的数据记录标明化学品的最大存储量(4分): b 化学品的数据记录提供给操作,维护人员和分包方的有关人员(2分 具有保证材料的接收和使用符合有关规定的质量控制程序 能在现场获取以下资料的书面最新版本 操作过程的化学原理概要(4分). a 12 2. 工艺参数的安全上下限范围(4分); 艺参数偏离安全范围所导致安全事故后果(4分 工艺流程框图或工艺流程简图齐全,并能在现场获取 2." 2.5 现场配备所有装置的工艺和仪表框图(P&.ID) 具有设备的设计制造符合相关的规范、标准的书面见证 2.6 13 设备具有完善的书面记录,包含下述内容 材料2分); a 设计规范和标准(2分); b 电性能类别1分) 2.7 10 d) 安全泄放系统的设计及其依据(2分); 通风系统的设计1分); 安全保护装置包括联锁、监测和紧急控制系统)(2分 具有保证工艺管理人员拥有与其责任相关的工艺安全方面的知识的规定,并切 2.8 10 实执行 上述资料、信息编撰成册,妥善保存 80 总分数 18
GB/T26610.4一2014 表B.4工艺危害性分析 工艺危害性分析 满分 实评分 3.1 涉及危险化学品的装置在过去5年中,进行了正式工艺危害性分析的比例 建立了进行工艺危害性分析的优先级排序方法,该方法考虑了以下因素 a)有毒、易燃、易爆化学品的数量(2分); 危险化学品的毒性和反应性等级(3分).; b 3.2 设备周围的人口密度(1分) c d 工艺的复杂性(1分); 恶劣的操作条件,或可能引起腐蚀/侵蚀的条件(1分) 已进行的工艺危害性分析针对以下要素: 工艺的危险性(3分); a 以往的意外事件/事故(确认其中潜在的灾难性事故)(4分); 对危险品的工程控制与管理控制,及两者的相互关系(3分); 3.3 18 工程与管理失控所致的后果(3分); dD 设备的位置(1分); e 人的因素(2分); 因失控对人员安全及健康影响的定性评估(2分 最近进行的工艺危险性分析的人员素质: 组长在相关技术领域经验丰富(5分); b组长受过工艺危险性分析的正规培训(4分); 3.4 18 个组员是所分析工艺方面的专家(3分). 至少 c d 评估组独立性强,至少一个组员未参与所评价装置的设计(3分); 评估组在工 良好的职业纪律(3分 作中体现了 具有正规的质量体系,可以保证工艺危险性分析中提出的问题建议被及时采纳 和执行,结果形成书面记录或报告
质量体系中 制定了纠正和预防措施的进度时间表(G分). 3.5 18 b 具有跟踪措施和手段(8分) 将处理工艺危害性分析所提出的建议的决议及其执行情况通报给所有的 操作,维修和其他有关人员(5分 已经完成和将要进行的工艺危害性分析所采用的方法适合所评价工艺的复 已 3.6 18 杂性 3.7 确定工艺危险性后,对失效可能性及后果进行定性或定量分析 总分数 95 表B.5安全检查 安全检查 满分 实评分 过去5年中,进行了正式安全检查的装置的比例 4. 10 安全检查的级别以下选项选择其一) 上级组织的安全检查(6分). a 4.2 同级相互间的安全检查(4分); 基层自发的安全检查(2分) 19
GB/T26610.4一2014 表B.5(续 安全检查 满分 实评分 安全检查的频率(以下选项选择其一): 至少每年1次(6分); bD 4.3 每2年1次(4分); 每3年1次(2分); 少于3年1次(0分 dD 具有正规的质量体系,可以保证安全检查中提出的问题建议被及时采纳和执 行,结果形成书面记录或报告
质量体系中 a)制定了纠正和预防措施的进度时间表(5分); 18 4,4 具有跟踪措施和手段(8分): 将处理安全检查所提出的建议的决议及其执行情况通报给所有的操作、维 修和其他有关人员(5分 总分数 40 表B.6变更管理 变更管理 满分 实评分 具有书面的变更管理程序 5.l 1l 变更管理程序包含以下内容 a)设备的“物理”变更,如扩产、设备维修、仪表或报警系统更新等(2分); 5.2 b 工艺中化学品(进料,催化剂.溶剂等)的变更及其参数调整(2分); 工艺条件(如操作温度、操作压力、产量等)的变动(2分); 操作程序(开停车程序、装置定员标准或分工等)的重大变动(2分 d 对设备的“临时”变更进行管理 5.3 a 对设备的“临时”变更有清晰的定义和解释(8分); 临时变更设备有明确清晰的标志(1分 变更管理程序明确规定了工艺系统发生变更后应采取的措施(以下各项均为 1.5分): 对操作单元进行危险性分析; 更新有关的操作规程; b 5,4 更新有关的维修程序及检测计划; dD 修改P&.ID,操作参数的范围、材料数据,有关的工艺安全信息; 通知工艺变更范围的所有操作和维护人员包括分包方),必要时进行 培训; 审核工艺变更对上下游相关设备的影响 15 5,5 审核变更对设备及材料的失效机理或速度所产生的影响 5.6 维修或更换采用的新材料经过正规审核,确认其满足工艺的要求 18 总分数 70 心
GB/T26610.4一2014 表B.7操作规程 操作规程 满分 实评分 操作规程明确规定每个操作人员的岗位职责 6.1 26 操作规程包含以下操作注意事项 a)首次开车(3分); 正常和紧急情况下的操作(4分); b 正常停车(2分); 紧急停车(4分); d 避免偏离安全操作范围的步骤,以及偏离安全操作范围的后果(3分) 30 6.2 e 维修后的开车(2分); 安全系统及其作用(3分)3 g h 工艺介质中的化学品的特性及其危害性(3分); 防止人身暴露于化学品的措施,包括控制措施及个人防护设备(3分) 接触化学品后应采取的揩施(3分) 6, 操作规程简明扼要 12 6.4 所有装置的操作及维护人员都能获得书面的操作程序将规程 22 6.5 具备健全的程序,确保各班次间交接相关信息 操作规程的审核频率(以下选项选择其一) 至少每年1次,或只要工艺发生更改即进行审核(12分): a 6.6 bD 每2年1次(6分); 12 仅在重大工艺变更时审核(3分); dD 尚未建立审核计划0分 操作规程的评价频率C以下选项选择其一). 至少每6个月1次(10分): a 6,7 每年1次(5分); b 10 每3年1次(2分); 尚未进行评价(0分) d 总分数 120 表B.8安全作业 安全作业 满分 实评分 对以下可能存在危险的作业,建立严格的安全作业措随 高温作业(3分); a 中断流程(3分); b 锁闭/开锁(3分); 进人受限制的区域(3分); d 打开工业设备或管道的作业(3分); 32 7.l 进人设备的作业(3分); 车辆进人作业区(3分); h 吊装(2分); 特殊危险品的处理(如有毒,放射性物质等)(6分) 在用设备的检修与维护(3分
GB/T26610.4一2014 表B.8(续 安全作业 满分 实评分 7.2 12 7.1中所列的安全作业实施前需要工作授权书或作业许可 在质量体系中,要求至少每3年对所有安全作业制度进行正式评审,在必要时 12 7.3 进行更新,具有按时对安全作业制度进行正式评审的见证件 安全作业制度执行情况的评审和通报频率(以下选项选择其一): 至少每3个月1次(12分); 每6个月1次(6分) b 12 7.4 每年1次3分); c 尚未进行评审(0分) 7.5 进行了作业环境是否符合人机工程标准的审查 12 总分数 80 表B.9人员培训 人员培训 满分 实评分 具有对新进人员进行一般性培训(如安全操作、作业手册等)的书面程序,并切 8.1 实执行 具有对新进操作,维护人员进行针对其岗位的岗前培训的书面程序,并切实 10 8,2 执行 岗前培训包含以下内容 工艺过程及其安全性的概述(1分) 操作规程(1.5分); b 应急措施(1.5分)3 c 8.3 d 安全作用审批(1分); 安全装置1分); 安全作业措施(1分); 基本技能(1分) 8.4 对安全生产管理人员进行培训 8.5 对安全作业措施审批人员进行培训 对培训效果的考核方式(以下选项选择其一): 进行理论考试和操作技能考核(6分). 8,6 b 仅进行操作技能考核(3分) 征求培训教师的意见(1分) 不进行考核(0分 (再)培训的频次(以下选项选择其一): 至少每3年1次(4分); 8.7 仅当主要操作工艺变更时进行再培训(1分)1 b 不进行培训(0分) 22
GB/T26610.4一2014 表B.9(续 人员培训 满分 实评分 人均培训时间以下选项选择其- 一 10天/年或更长(2分); a 8.8 3天/年一9天/年q1分) b 少于3天/年(0分 有系统的方法获取员工的培训需求; 建立了确认培训需求的程序(2分) 8.9 进行定期评审(1分 采取适宜的培训方式 颁发培训证书(0.5分); b 使用合适的培训教材和资料(1分) 8.10 采用合适的工具和一起进行“实践”训练(1分); 记录培训时间(0.5分) 60 总分数 表B.10检验和维护 检验和维护 满分 实评分 9. 书面检验计划内容全面 19 检验的频率和内容满足相关法规的要求 9.2 20 所有的检验,试验和维修都形成书面记录或报告,并及时存档 1l 9.3 预防性维护程序全面、合理, 强调所有和安全相关的关键的设备、零部件(3分); 采用检查表,检验清单(2分) b 9.4 11 及时完成维护工作(2分); 根据检测反馈信息,及时更改程序(2分) d 确认,追踪和完成维修(2分) 具有完善的缺陷返修程序,并切实执行 11 9.5 具有完善的设备改造,更换程序,并切实执行 9.6 设备档案完整,并妥善保存 12 9.7 总分数 95 表B.11投用前的安全检查 投用前的安全检在 满分 实评分 质量体系中有对新建或重大改造的装置应在设计阶段进行工艺危害性分析的 10.1 14 规定,并切实执行 具有对投用前进行审查以确认操作过程的制定、检验规程的制定,维护规程的 制定,安全和应急规程的制定,人员培训,采纳工艺危害性分析中提出的建议等 10.2 已经完成的规定,并切实执行 23
GB/T26610.4一2014 表B.11(续) 投用前的安全检在 10 满分 实评分 具有在投用前进行检验的相关规定,并切实执行
设备按照设计规范和制造商的建议进行安装(5.5分); 14 10.3 对检验中发现的问题采取纠正措施并有相应的跟踪措施(5.5分); b 出具正式的检验报告(3分 10.4 具有对涉及高危害化学品的设备进行泄漏检查的规定,并切实执行 14 具有对控制装置进行检查的规定,并切实执行 12 10,5 具有对安全保护装置如安全阀,连锁器、检漏设备等)进行检查的规定,并切实 14 10.6 执行 具有对上述检查结果及设备合格证书必须整理归档的规定,并切实执行 10.7 18 总分数 90 表B.12应急措施 1 应急措施 满分 实评分 1. 20 建立了适用于各种可能紧急情况的应急预案 应急预案完整、可靠,包括以下要素 制定协调人员及其相应职责(3分); b 紧急疏散程序和紧急疏散路线(3分); 紧急操作规程(3分); 紧急疏散后对人员的清点(0.5分) d 11.2 20 救援和医疗(3分); 对火灾和其他紧急情况的首选处理措施(3分)5 对危险品的控制3分); g h 调查和抢救计划1分) 清理和重建计划(0.5分 对应急预案定期进行检查和修订,考虑以下因素 变更管理程序包括变更对应急计划的可能影响(6分) 1l.3 b)根据最新工艺危害性分析结果,确认新发现的危险源是否导致应急计划的 改变(6分 设置应急中心 11.4 设有通告或解释应急预案的人员,并将其名单粘贴于控制室、安全办,应急中心 11.5 等处 定期进行应急预案的演习 1 11.6 总分数 75 2
GB/T26610.4一2014 表B.13事故调查 ]2 事故调查 满分 实评分 规定了协助进行事故调查的人员,包括受过事故调查技术培训的人员、工艺员 13 12.1 或熟悉工艺过程的人员,检验人员,其他技术人员等 在过去一年里,将所有事故报告或结论及其纠正预防措施都通报到公司(厂)内 27 12.2 其他车间 总分数 40 表B.14分包管理 13分包管理 满分 实评分 对分包方进行评价,包括以下内容 审查分包方的安全,健康程序文件(3分); a 13.1 b 审查分包方从事相关工作的经验(3分); 市蠢分包方具备安全高效完成其工作的经脸和技能的见证件(3分) 所有分包方包括维修、检修、重大技术改造或特种作业等)都受分包评价程序 13.2 的控制 对分包方进行安全教育包括以下内容 分包方的工作和工艺流程中的所有潜在危险源(2分); a 13.3 b5 安全作业措施(2分); 10 进/出作业场所的控制程序(3分)1 c d 应急预案中的相关部分(3分 召开工作会议,明确工作范围,安全要求、质量保证等 13.4 10 13.5 定期对分包方的人员培训和管理情况进行评估 总分数 40 表B.15安全生产管理系统评估 14安全生产管理系统评估 满分 实评分 对安全生产管理系统进行评估的频率(以下各项选择其一) 每年1次(5分); a 14.1 b 每2年1次(3分)7 未进行评估(0分 已经制定针对上次评估要求的改进计划 14.2 10 最近一次)评估组的人员素质: 经过评估的正式培训 14.3 a 10 深人了解所评估的体系 最近一次)评估的深度和广度符合工厂实际情况 14.4 10 总分数 35 25
GB/T26610.4一2014 c 附 录 规范性附录 减薄次因子确定 C.1范围 本附录用于存在腐蚀减薄机理设备的技术模块因子中减薄次因子的确定
所有设备都应确定其减薄次因子
c.2基本数据 C.2.1必需数据 表C.1给出了设备至少进行了一次有效检测后,确定其减薄次因子所需的基本数据 表C.1确定减薄次因子所需的基本数据 基本数据 明 说 厚度1/mm 投人使用时的实测最小厚度 设备的服役年限
如果工艺条件发生变化并可能导致腐蚀速率发生较大改变,则服役年 服役年限a/年 限应从工艺改变的时间算起,厚度则应为改变时的最小壁厚 腐蚀裕量" 设计时给出的腐蚀裕量或投人使用时的实际壁厚余量 /mm 根据可靠的厚度数据计算的当前腐蚀速率
如果根据目前相对较短的时间间隔的实测 厚度差计算出的“短期”腐蚀速率明显不同于根据更长时间间隔的实测厚度差计算出的 腐蚀速率r/mm/年) “长期”腐蚀速率,则应用“短期”腐蚀速率进行评估
如果设有实测腐蚀速率,则估计的 腐蚀速率可参考相关的资料或专家建议来确定 10%以上表面积受到腐蚀且壁厚变化小于1.27mm n的腐蚀现象定义为全面腐蚀 减薄类型 10%以下表面积受到腐蚀且壁厚变化大于或等于1.27mm的腐蚀现象定义为局部腐蚀 运行温度/ 运行期间(考虑正常和异常运行条件)预计的最高运行温度 OP/MPa 操作压力,预计的最高运行压力(一般为安全阀的整定压力 MAwP/MPa 用来确定最小允许壁厚的压力(可用设计压力代替 检验有效性 对设备进行的每次检验活动的有效性类别 检验次数 服役期间已进行的有效性不低于“中度有效”的检验活动的总次数 在线监测 采用的在线监测方法的类型,如腐蚀探针、挂片,定点测厚等 腐蚀减薄机理 确定设备潜在的减薄机理 材料类别 设备/管道的材料类别 是否存在注人 对管道来说,确定管路中是否存在注人点或混合点 混合点(是/否 /混合点检测等级 对有注人或混合点的管路,是否针对这些部位的局部腐蚀进行了高度有效检测 迷 人 盲管段腐蚀的检测类型对有盲管的管路,是否针对育管局部腐蚀进行了高度有效的检测 26
GB/T26610.4一2014 C.2.2附加数据 如果没有可靠的实测腐蚀速率,则按表C.2中的步骤来确定推荐的腐蚀速率
表c.2确定推荐的腐蚀速率步骤 步 骤 措施 为回答表C.3中所列的筛选问题收集数据 回答表C.3中的筛选问题 为2中识别出的适用的减薄机理补充收集基本数据表中规定的数据 c3基本假设 在基本数据表定义的时间期限内,腐蚀速率基本恒定
检测越彻底和检测越频繁,且持续进行在线 监测,则腐蚀速率大于预计值的可能性更小
减薄次因子的确定 图C.1中给出了确定减薄次因子的流程图
开始 是否测量或猫锁 识别腐理 算了腐蚀速率 评腐速率 是 厚度 计算ar/ 时间 腐蚀是否 为局部的 局部腐蚀的松 全面腐蚀的检 验有效性 验有效性 确定TMF 确定TMF 局部 全面 检骑数量 检验数量 M全面成部 实际厚度 确定 刺余腐裕量 设计 TM作乘以设计 安全 安全系数 MAWT 系数 OP 确定 在线监测类型 在线 TM陈以在线 监测 监测系数 喊薄机理 系数 修正的TMF 全面或局部 图C.1减薄次因子的确定 27
承压设备系统基于风险的检验实施导则第4部分:失效可能性定量分析方法GB/T26610.4-2014
承压设备是工业生产中不可或缺的一种设备,其安全性关系到生产过程中的人员安全和生产效率。为了确保承压设备的安全可靠,需要对其进行定期检验。而在检验过程中,需要评估承压设备的失效可能性。
GB/T26610.4-2014《承压设备系统基于风险的检验实施导则第4部分:失效可能性定量分析方法》就是一项非常重要的标准,它规定了承压设备检验实施过程中失效可能性的定量分析方法和管理要求。
该标准中的失效可能性定量分析方法主要包括以下内容:
1. 确定失效模式和机理
在进行失效可能性的定量分析前,需要首先确定承压设备的失效模式和机理。这一过程可以帮助检验人员更好地了解承压设备可能存在的问题,为后续的失效可能性评估提供依据。
2. 确定失效发生的条件和影响因素
在进行失效可能性的定量分析时,需要确定失效发生的条件和影响因素。这一过程可以帮助检验人员更全面地了解失效的可能性和影响程度,从而指导后续的检测工作。
3. 进行失效可能性评估
失效可能性评估是对失效概率进行定量分析和评价。通过采用相应的评估方法,可以得出具体的失效可能性值,并根据评估结果制定相应的措施。
4. 制定风险控制措施
根据失效可能性评估结果,需要制定相应的风险控制措施并加以实施。通过控制失效的发生和扩大,有效保障承压设备的安全运行。
总之,GB/T26610.4-2014所规定的失效可能性定量分析方法是承压设备检验过程中必不可少的一个环节。它可以帮助检验人员更好地了解和掌握失效可能性评估的方法和技巧,从而提高承压设备的安全性和可靠性。