GB/T32270-2015
压力管道规范动力管道
Pressurepipingcode—Powerpiping
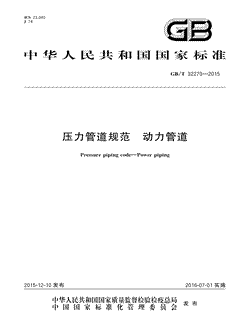
- 中国标准分类号(CCS)J74
- 国际标准分类号(ICS)23.040
- 实施日期2016-07-01
- 文件格式PDF
- 文本页数85页
- 文件大小3.19M
以图片形式预览压力管道规范动力管道
压力管道规范动力管道
国家标准 GB/T32270一2015 压力管道规范动力管道 Presurepipingeode一Powerpiping 2015-12-10发布 2016-07-01实施 国家质量监督检验检疫总局 发布 国家标准化管理委员会国家标准
GB/T32270一2015 目 次 前言 范围 规范性引用文件 术语和定义 管道分级 材料 设计与计算 30 制作与安装 检验与试验 安全防护 保温及防腐 l0 52 附录A(规范性附录)材料的许用应力 55 附录B(资料性附录)常用材料物理性能 62 附录c规范性附录柔性系数和应力增加系数 67 附录D(资料性附录)制作和安装常用资料 74 附录E规范性附录管道预制组对偏差 78 附录F(规范性附录安全泄放装置的计算 8G
GB/T32270一2015 前 言 本标准按照GB/T1.1一2009给出的规则起草
本标准由全国锅炉压力容器标准化技术委员会(SAC/TC262)提出并归口
本标准起草单位;电力规划设计协会、电力工程顾问集团东北电力设计院、西安热工研究 院、电力工程顾问集团中南电力设计院、电力工程顾问集团华东电力设计院、广东省电力设计 研究院、河南省电力勘测设计院、江苏省电力设计院、华电重工股份有限公司、江苏电力装备有限公司、 河北省电力建设第一工程公司电力工业管道产品质量检验测试中心,浙江省电力设计院、国核电力规 划设计研究院、浙江格洛斯无缝钢管有限公司
本标准主要起草人;郭晓克、马洪,裴育蜂、郭亚莉、叶菲、刘启军,黄涛、周柴灿、康豫军、许玉新、 薛家春,林磊、陈娟、邓成刚,潘诚,程祖田,王志斌、孙国模,翁燕殊、李诗玉,浦万生、毛敏、何朋臣,间平 郭延军、钱海平、徐红波、王成立、陈宝、陈卓,石平
GB/T32270一2015 压力管道规范动力管道 范围 本标准规定了火力发电厂界区内以蒸汽,水和易燃易爆,有毒及腐蚀性液体或气体为介质的管道的 材料,设计,制作、安装、检验、试验、安全防护、保温及防腐的基本要求等
其中易燃易爆、有毒及腐蚀性 液体或气体为介质的管道参照GB/T20801 本标准不适用于下列管道 a)锅炉本体管道; b 核电厂管道; 采暖通风与空气调节的管道及非圆形截面的管道; c d)各种塔、建筑构架、贮罐、机械设备和仪表用的管道
本标准不包括非金属管道的材料要求
本标准规定的管道与锅炉本体范围内的管道分界见图1和图2
过热器 汽轮机阀或规范规定的切断阀 汽轮机 至设备 汽水分离器 再热器 对流和帮H 集水器 启动系统可按锅炉 制选厂要求改变 省煤器 如果使用 再循环泉 M (如果使 如果使用)(如果使用 锅炉给水裂 说明 -锅炉本体管道; 一锅炉外部管道和接头(第1章中规范的蒸汽,水管道和接头)1 O非锅炉外部管道和接头
图1与直流锅炉连接的管道界限管理
GB/T32270一2015 排气和连接测量仪表 单台设备- 多台设各备 公用 水位计 表面排污 连续排污 加药 进水连箱 采用时 【锅水取样 热 -吹灰器 单台汽轮机设备 主然 再热器出口 热 器 -吹灰器 多台轮机设备 再热器进口 公用集箱 -单台锅炉 单台锅炉 该错飘炉给水 下锅筒 调节阀门 -通过同一水源 商合或锅炉给水 单台和多台设备 疏水 说明 一锅炉本体管道" -锅炉外部管道和接头(第1章中规范的蒸汽、,水管道和接头); D非锅炉外部管道和接头
图2与汽包锅炉连接的管道界限管理 规范性引用文件 下列文件对于本文件的应用是必不可少的
凡是注日期的引用文件,仅注日期的版本适用于本文 件
凡是不注日期的引用文件,其最新版本(包括所有的修改单)适用于本文件 GB1502011(所有部分)压力容器 GB/T229金属材料夏比摆锤冲击试验方法 GB/231.1金属材料布氏硬度试验第1部分;试验方法 GB/T7002006碳素结构钢 GB713一2014锅炉和压力容器用钢板 GB/T1048管道元件P(公称压力)的定义和选用 低中压锅炉用无缝钢管 GB3087 低压流体输送用焊接钢管 GB/T3091 GB/T3274碳索素结构钢和低合金结构钢热轧厚钢板和钢带 GB/T4622.2一2008缠绕式垫片管法兰用垫片尺寸 GB5310 高压锅炉用无缝钢管 GB/T7233(所有部分铸钢件超声检测 GB/T8163输送流体用无缝钢管
GB/T32270一2015 GB8624建筑材料及制品燃烧性能分级 GB/T8923(所有部分涂覆涂料前钢材表面处理表面清洁度的目视评定 GB/T9115对焊钢制管法兰 GB/T9116带颈平焊钢制管法兰 GB/T9119板式平焊钢制管法兰 GB/T9123钢制管法兰盖 GB/T9124钢制管法兰技术条件 GB/T9125 管法兰连接用紧固件 GB/T12228通用阀门碳素钢锻件技术条件 GB/T12229 通用阀门碳素钢铸件技术条件 GB/T12230 通用阀门不锈钢铸件技术条件 122412005安全阀一般要求 GB 22422005压力释放装置性能试验规范 12243一2005弹簧直接载荷式安全阀 金属波纹管膨胀节通用技术条件 GB 12777 132981991金属显微组织检验方法 GB 13927一2008工业阀门压力试验 GB 1995大气环境腐蚀性分类 GB 15957 承压钢铸件 16253 17116(所有部分)管道支吊架 GB 17186钢制管法兰连接强度计算方法 GB 金属里氏硬度试验方法 GB/T17394 GB/T208012006(所有部分压力管道规范工业管道 GB50016建筑设计防火规范 GB50021岩土工程勘察规范 GB50126工业设备及管道绝热工程施工规范 GB50185工业设备及管道绝热工程施工质量验收规范 GB50229火力发电厂与变电站设计防火规范 GB50264工业设备及管道绝热工程设计规范 GB50764一2012电厂动力管道设计规范 DL/T438一2009火力发电厂金属技术监督规程 DL./T515一2004电站弯管 DL/T868一2014焊接工艺评定规程 DL/T869一2012火力发电厂焊接技术规程 DL/T991一2006电力设备金属光谱分析技术导则 DL/T5072一2007 火力发电厂保温油漆设计规程 JB/T3223焊接材料质量管理规程 JB/T4730(所有部分承压设备无损检测 JB/T5263电站阀门铸钢件技术条件 JB/T6439阀门受压件磁粉探伤检验 JB/T6440阀门受压铸钢件射线照相检验 JB/T6902阀门液体渗透检测 JB/T7927阀门铸钢件外观质量要求
GB/T32270一2015 JB/T9625锅炉管道附件承压铸钢件技术条件 JB/T9626锅炉锻件技术条件 JB/T10087汽轮机承压铸钢件技术条件 NB/T47008 承压设备用碳素钢和合金钢锻件 NB/T47009低温承压设备用低合金钢锻件 NB/T47010承压设备用不锈钢和耐热钢锻件 NB/T47014承压设备焊接工艺评定 SY/T5037 普通流体输送管道用理弧悍钢管 SY/T5038普通流体输送管道用直缝高频焊钢管 TSGD0001压力管道安全技术监察规程 -工业管道 术语和定义 下列术语和定义适用于本文件
3.1 管道pipine 由管道组成件和管道支吊装置等组成,用以输送、分配、混合、分离、排放、计量或控制流体流动
3.2 管道系统pipingsystem" 按流体与设计条件划分的单根或多根管道连接成的一组管道,简称管系
3.3 管道组成件 pipingcomponent 用于连接或装配成管道的元件,包括管子、管件,法兰、垫片、紧固件、阀门、滤网及补偿器等
3.4 管子 pipeortube 用于输送流体的横截面为圆形的管道组成件
3.5 管件 pipefitting 管道组成件的一个类别,包括弯管或弯头、三通、接管座、异径管和封头等 3.6 管段 pipingassembly 按配管设计单独编号的管子、管件,弯管和法兰等组成的组合件
3.7 制造 manufacture 管道组成件或管道支吊架等产品的生产过程
3.8' 制作 tabrieationm 管道安装前在工厂或在现场进行的切割,坡口制备、弯曲成形、焊接、热处理等工序,将管件和管子 连接成管段的过程
3.9 安装 erection 按照管道设计的规定,将一个管道系统完整就位的过程
GB/T32270一2015 3.10 试验 test 按照标准或规程,由业主和制造、制作和安装单位共同规定的确认产品质量特性的一种方法
包括 水压试验和气密性试验等
3.11 验证 verification 动力管道制作或安装单位对接收的管道组成件和支吊架进行文件确认的过程
3.12 验收 receivingacceptance 动力管道制作或安装单位通过验证和(或)检验对接收的管道组成件和支吊架进行确认的过程
3.13 支管连接 branchconnection 从主管引出支管的结构,包括整体加强的三通管件及不带加强的焊接结构的支管连接
3.14 ipkedrainlee) 疏水收集器liquideolleetin 在气体或蒸汽管道的低位点设置收集冷凝水的装置 3.15 减振装置swaylrace 用以控制管道低频高幅晃动或高频低幅振动的装置
3.16 阻尼装置 Snubber 用以承受管道地震荷载或冲击荷载,控制管系高速振动位移,同时允许管系自由地热胀冷缩装置
3.17 应力增加系数stressintensifieationfaetor 弯管、弯头、异经管和三通管件在弯矩的作用下,产生的最大弯曲应力与承受相同弯矩的直管产生 的最大弯曲应力的比值
或直管的疲劳强度与在相同交变弯矩作用下弯管、弯头、异径管和三通管件的 疲劳强度的比值
3.18 冷紧cldsprina 在安装管道时预先施加于管道的弹性变形,以产生预期的初始位移和应力,达到降低初始热态应力 和初始热态管端的作用力和力矩
3.19 柔性 lexiblity 管道通过自身变形吸收热胀、冷缩和其他位移变形的能力
3.20 热位移 hotdisplacement 管道系统支吊点处冷、热状态间的位置变化量
3.21 冷位移 colddisplacement 由管道冷紧产生的位移,当采用热态吊零时,还包括弹簧附加力产生的位移
GB/T32270一2015 3.22 selfs 自拉 spring 由于应变自均衡或高温应力松弛,热态应力下降,管道再由热态到冷态时产生反向应力的现象 3.23 electricresistance 电阻焊焊管 一weldedpipe 以管坯本身作为电流回路,利用电阻加热管坯、在压力作用下连续对接焊接的管子
3.24 电熔焊焊管 eleetrie-fusion-wededsteelpipe 采用自动电弧焊或手工电弧煤,在预成形的坯料上纵向对接焊成的管子
3.25 焊接接头系数weldjointefriecieneyfactors 焊缝许用应力修正系数的简称,应根据对接接头的焊缝形式及无损检测的长度比例确定
用以反 映由于焊接材料、焊接缺陷和焊接残余应力等因素使焊接接头强度被削弱的程度,是焊接接头力学性能 的综合反映
3.26 iinspeetioncertifieate 质量证明书 材料质量证明(检验文件)的一种形式
由制造厂生产部门以外的独立授权部门或人员,按照标准 及合同的规定,按批在交货产品上(或取样)进行检验和试验,并注明结果的检验文件
制造厂质量证明书由独立于生产部门的制造厂检验部门或第三方检验机构签署并批准生效
法律 法规有规定的,由法定检验检测机构出具监督检验证明
3.27 安全泄放装置safetyreliefdeviee 在非正常运行工况下,为防止系统内压力超过预定的安全值,利用进口静压力作用开启,泄放流体 的装置
3.28 安全阀整定压力 setpressureofthesafetyvalve 在运行条件下安全阀阀瓣开始开起的预定压力,又称为开启压力,设定压力或起座压力
3.29 maximum 最大泄放压力 relietimgpe reSSure 在泄放状态下,安全阀的阀瓣达到规定开启高度时的最大进口压力
管道分级 动力管道(GD类)划分为GD1级和GD2级 GD1级;设计压力>6.3MPa,或者设计温度>400C GD2级;设计压力<6.3MPa,且设计温度一之400C
材料 5.1 -般规定 5.1.1材料选用 管道材料应根据使用条件选用,并满足本标准规定的材料使用要求和限制
GB/T32270一2015 5.1.2材料牌号和性能 5.1.2.1常用管道材料的牌号、许用应力和使用范围等应符合附录A的规定
5.1.2.2对符合本标准规定而未列于附录A的材料,如符合GB/T208o1.2一2006可直接取用,许用应 力按照GB/T20801.2一2006中的附录A选取
5.1.2.3对符合本标准规定但未列于附录A的国外成熟应用材料,应满足所引用材料标准的要求,其 许用应力数值可直接取用
5.1.2.4常用钢管材料的弹性模量和线膨胀系数可按附录B选取,未列出的材料的弹性模量和线膨胀 系数可按GB/T20801.22006的附录B选取
5.1.2.5对符合本标准规定但未列于附录B的国外成熟应用材料,应满足所引用材料标准的要求,其物 理性能参数可直接取用
5.2材料选用的基本原则 5.2.1管道材料应按照材料的使用性能、工艺性能和经济性选用
材料的使用性能应满足管道组成件的设计温度、受力状况、介质特性及工作的长期性和安全性 5.2.2 的要求 5.2.3材料的工艺性能应满足管道组成件的几何形状尺寸,制造工艺以及修复方法的要求
不同的材料组合时不应对材料产生不利的影响
5.2.4 5.2.5在管子上直接焊接的零部件宜采用与管子相同的材料
5.3材料的使用 5.3.1管道组成件 5.3.1.1无缝管子和管件 符合GB/T8163的无缝钢管,可用于设计压力不大于1.6MPa的管道;符合GB.3087的无缝 a 钢管,可用于设计压力不大于5.3MPa的管道;符合GB5310的无缝钢管,可用于设计压力大 于5.3MPa的管道; b)采用无缝钢管制作的管件,其压力使用范围应与管子的规定相同
5.3.1.2焊接管子和管件 a)符合ASMESA672和ASMESA691的直缝电熔焊钢管和对应的管件可用于设计压力不大于 10MPa且设计温度不在蠕变范围之内的管道; b GB/T3091,SY/T5037,SY/T5038电熔焊钢管可用于设计压力不大于1.6MPa且设计温度 不大于300C的管道; 电熔焊钢管的纵向焊接接头系数根据表1中的焊接接头型式和检测比例确定; 电阻焊碳钢钢管,纵向焊接接头系数按0.85选取,不应采用附加检测的方法增大纵向焊接接 头系数;电阻焊碳钢钢管不应用于设计压力大于1.6MPa或设计温度大于200C管道;不应采 用电阻焊碳钢钢管制造对焊管件
GB/T32270一2015 表1纵向焊接接头系数 号 检测比例 系 数 接头型式 按产品标准检测 0,85 单面焊(无填充金属 00%射线或超声检测 1.00 按产品标准检测 0.80 单面媒(有填充金属) 100%射线或超声检测 1.00 按产品标准检测 0.90 双面(无填充金属) 100%射线或超声检测" 1.00 按产品标准检测 0,90 双面焊(有填充金属 00%射线或超声检测 1.00 射线检测,超声检测应符合8.3或相应的材料标准要求
5.3.1.3铸钢件: 符合JB/T5263、JB/T10087、JB/T9625、GB/T16253,GB/T12229,GB/T12230等国内标准的 铸钢件可应用于阀体等管道附件,铸钢件质量系数取0.8. 在满足附加无损检测要求时,铸钢件可取表2中的质量系数 表2铸钢件质量系数及附加无损检测要求 序号 附加无损检测要求 铸件质量系数e 铸作表面加工至RA3,挺高目楼检在的清嘴度,开清是BT797中B拨的要求 0.85 铸件表面按JB/T6902(PT)中的4级或JB/T6439(MT)进行着色渗透检测或磁粉 0,85 检测 铸件按GB/T7233(UT)或JB/T6440(RT)进行超声或射线照相检测,按GB/T7233 0.95 UT)检测的缺陷的底波反射波高不应大于V5型对比试块所得的底波反射波高 铸件表面加工至R.6.3,提高目视检查的清晰度,并满足JB/T7927中B级的要求 铸件表面按JB/T6902(PT)中的4级或JB/T6439(MT)进行着色渗透检测或磁粉 0,90 检测 铸件表面加工至R.6.3,提高目视检查的清晰度,并满足JB/T7927中B级的要求 铸件按GB/T7233(UT)或JB/T6440RT)进行超声或射线照相检测,按GB/T7233 1.00 UT)检测的缺陷的底波反射波高不应大于V5型对比试块所得的底波反射波高 铸件表面按JB/T6902(PT)中的4级或JB/T6439(MT)进行着色渗透检测或磁粉 检测 1.00 铸件按GB/T7233(UT)或JB/T6440RT)进行超声或射线照相检测,按GB/T7233 UT)检测的缺陷的底波反射波高不应大于V5型对比试块所得的底波反射波高 5.3.1.4锻钢件 管道组成件的锻钢件应符合NB/T47008,NB/T47009,NB/T47010,GB/T12228,JB/T9626的 要求
GB/T32270一2015 5.3.2管道支吊架 管道支吊架所采用的材料应符合6.5.4和GB/T17116的要求
5.3.3材料的使用限制 5.3.3.1碳素结构钢或低合金结构钢 碳素结构钢或低合金结构钢的使用应符合下列规定: a)管道受压元件以及直接焊接于受压元件上的承载构件应采用镇静钢
承压件选用B级和C级 镇静钢时,设计温度不应高于300C,厚度不应大于30mm b)除a)外的其他构件可选用沸腾钢和半镇静钢.但厚度不应大于12mm; 含碳量大于0.35%的碳素结构钢或低合金结构钢不宜在媒接结构上使用 c) d)碳素结构钢或低合金结构钢不应用于毒性程度为极度危害介质、高度危害气体介质和工作温 度高于标准沸点的高度危害液体介质的管道
5.3.3.2优质碳素钢与低合金耐热钢 优质碳素钢与低合金耐热钢的使用应符合下列规定 用于焊接结构的优质碳素钢、低合金耐热钢,含碳量不应大于0.35% a 对低合金耐热钢,当使用温度大于455C时,焊缝金属的含碳鼠应大于0.05%; b 低碳(C<0.08%)非稳定化不锈钢(如06Crl9Nil0,06Crl7Ni12Mo2)在非固溶状态下包括固 溶后经热加工或焊接)不应用于可能发生晶间腐蚀的环境
奥氏体钢使用温度高于525C时 含碳量不应小于0.04%
5.3.4材料的使用温度限制 5.3.4.1材料使用温度上限: a)材料的使用温度不应超过附录A中给出许用应力值的最高温度; b)确定材料的实际使用温度上限应考虑腐蚀介质的影响,高温条件下长期使用的材料,应考虑 因组织或性能变化对材料使用可靠性的影响,蠕变温度以上长期使用的材料,应考虑因蠕变引 起的过度变形、过大位移、材料组织和性能的劣化以及螺栓的应力松弛; 碳钢、碳锰钢不宜在425C以上的温度下长期使用,碳钼钢不宜在470C以上的温度下长期使 用,但在自限式卸压安全装置的直接对空排放管道中,碳钢可以用于425C以上; 铬钼合金钢长期在400C550C温度下使用时,应根据使用经验和具体工况采取适当的防 护措施 在高于454C温度下使用低合金铬钢含铬量2.25%)时,母材和焊缝填充金属的含碳量应等 于或大于0.05% 铁素体不锈钢及马氏体不锈钢不宜在370以上的温度使用 fD 铬镍奥氏体不锈钢在540C900温度下长期使用时应控制奥氏体钢中的铁素体含量及过 g 度冷变形 双相不锈钢不得在300以上的温度使用 h i 奥民体钢的使用温度高于325C时,钢中的碳含量应不低于Q.04% GC类管道中的材料高温下使用的限制应符合GB/T20801.2一2006中第7章的规定
材料的使用温度下限 5.3.4.2 设计者应考虑材料在低温下试验、使用出现脆性断裂的可能性;
GB/T32270一2015 bGC类管道的材料使用温度下限应符合GB/T20801.2一2006中第8章的规定
5.3.5材料标记和质量证明文件 5.3.5.1材料标记 5.3.5.1.1材料标记应符合相应标准的规定和合同约定
5.3.5.1.2标记内容至少应包括:制造厂标识、材料牌号代号,压力管道组成件还应包括规格和材料 炉(罐)批号或代号
5.3.5.1.3材料应逐件标记,标记应清晰、牢固,公称直径小于或等于DN40的材料可采用标签或其他 替代方法进行标记
5.3.5.2质量证明文件 5.3.5.2.1材料应具有相应的质量证明文件 5.3.5.2.2质量证明文件应包括标准以及合同规定的检验和试验结果,且具有可追溯性
5.3.5.2.3进口材料还应提供原产地证明文件和人境货物检验检疫证明 设计与计算 6.1设计条件和设计准则 6.1.1设计条件 6.1.1.1 一般要求 管道设计应根据压力、温度及管内介质特性等工艺条件,并结合环境,荷载等综合条件进行
6.1.1.2设计压力 6.1.1.2.1管道组成件的设计压力,不应低于运行中可能出现的最高持续压力; 6.1.1.2.2GD类管道的设计压力应符合下列规定: 超临界及以下参数机组,主蒸汽管道设计压力应取用锅炉最大连续蒸发量时过热器出口的额 定工作压力 b)超超临界参数机组,主蒸汽管道设计压力应取用下列两项的较大值 l汽轮机主汽门进口处设计压力的105%; 2 汽轮机主汽门进口处设计压力加主蒸汽管道压降
再热蒸汽管道设计压力应取用汽轮机最大计算出力工况(调节汽门全开,即VwO工况)热平 衡中高压缸排汽压力的1.15倍
对于再热器出口联箱到汽轮机的部分,可减至再热器出口安 全阀动作的最低整定压力
d 汽轮机抽汽管道设计压力应符合下列规定 1 非调整抽汽管道,应取用汽轮机最大计算出力工况下该抽汽压力的1.1信,且不小于0.1MPa 2调整抽汽管道,应取其最高工作压力; 3 背压式汽轮机排汽管道应取其最高工作压力,但不应小于0.1MPa
与直流锅炉启动分离器连接的汽水管道设计压力应取用分离器各种运行工况中可能出现的最 高工作压力
高压给水管道设计压力应符合下列规定: 非调速给水泵出口管道从前置泵到主给水泵或从主给水泵至锅炉省煤器进口区段,应分 10o
GB/T32270一2015 别取用前置泵或主给水泵特性曲线最高点对应的压力与该泵进水侧压力之和; 调速给水泵出口管道,从给水泵出口至第一个关断阀的管道,设计压力应取用系在额定转 速特性曲线最高点对应的压力与进水侧压力之和;从泵出口关断阀至锅炉省煤器进口区 段,应取用泵在额定转速及设计流量下系提升压力的1.1倍与泵进水侧压力之和; 高压给水管道设计压力,应计及水系进水温度对压力的修正
低压给水管道设计压力应符合下列规定: 对于定压除氧系统,应取用除氧器额定压力与最高水位时水柱静压之和; 对于滑压除氧系统,应取用汽轮机最大计算出力工况(调节汽门全开,即VwO工况下除 2 氧器加热抽汽压力的1.1倍与除氧器最高水位时水柱静压之和
凝结水管道设计压力应符合下列规定 h 凝结水泵进口侧管道,应取用泵吸人口中心线至汽轮机排汽缸接口平面处的水柱静压 1 此时凝汽器内按大气压力),且不小于0.35MPa 2 凝结水系出口侧管道,应取用泵出口阀关断情况下泵的提升压力与进水侧压力(凝汽器 热井最高水位与泵吸人口中心线的水柱静压)之和
加热器疏水管道设计压力应取用汽轮机最大计算出力工况(调节汽门全开,即VwO工况)下 抽汽压力的1.1倍,且不应小于0.1MPa
当管道中疏水静压引起压力升高值大于抽汽压力的 3%时,应计及静压的影响
锅炉排污管道设计压力应符合下列规定: 锅炉排污阀前管道,对于定期排污管道,设计压力不应小于汽包上所有安全阀中的最低整 定压力与汽包最高水位至管道最低点水柱静压之和;对于连续排污管道,设计压力不应小 于汽包上所有安全阀的最低整定压力 锅炉排污阀后管道,当排污阀后的管道装有阀门或堵板等可能引起管内介质压力升高时 其设计压力应按排污阀前管道设计压力的选取原则确定;当锅炉排污阀后的管道上未装 有阀门或堵板等不会引起管内介质压力升高时,排污管道(定期排污或连续排污)的设计 压力应按表3选取
表3锅炉排污阀后管道设计压力 单位为兆帕 锅炉压力 项目 1.7504.150 4.151一6,200 6.201~10.300 >10,301 管道设计压力 1.750 2.750 4.150 6.200 k)给水再循环管道设计压力应符合下列规定 当采用单元制系统时,进除氧器的最后一道关断阀及其以前的管道,应取用相应的高压 给水管道的设计压力,其后的管道,对于定压除氧系统,应取用除氧器额定压力;对于滑 压除氧系统,应取用汽轮机最大计算出力工况(调节汽门全开,即VwO工况)下除氧器加 热抽汽压力的1.1倍 当采用母管制系统时,节流孔板及其以前的管道,应取用相应的高压给水管道的设计压 力;节流孔板后的管道,当未装设阀门或介质出路上的阀门不可能关断时,应取用除氧器 的额定压力
安全阀后排汽管道设计压力应根据排汽管道的水力计算结果确定
! 其他管道的设计压力应符合下列规定: m 1对于输送气化温度低的流体(液化气体)管道组成件,其设计压力不应小于阀被关闭或流 1l
GB/T32270一2015 体不流动时在最高环境温度下气化所能达到的最高压力 离心泵出口至第一道关断阀之间的管道组成件,对于定速泵,其设计压力不应小于泵额 定工作特性曲线最高点对应的压力与泵吸人口压力之和;对于调速泵,其设计压力不应 小于泵额定转速特性曲线最高点对应的压力与泵吸人口压力之和; 3 装有安全阀的管道,管道组成件的设计压力不应小于安全阀的最低整定压力 减压装置后没有安全阀且流体可能被关断或堵塞的管道,管道组成件的设计压力不应低 4 于减压装置前流体可能达到的最高压力
6.1.1.3设计温度 6.1.1.3.1管道的设计温度不应低于管内介质持续运行的最高工作温度
6.1.1.3.2GD类管道的设计温度应符合下列规定: a 主燕汽管道设计温度应取用锅炉过热器出口蒸汽额定工作温度加上锅炉正常运行时允许的温 度偏差值,当锅炉制造厂未提供温度偏差时,温度偏差值可取用5C
再热蒸汽管道设计温度应符合下列规定 高温再热燕汽管道,应取用锅炉再热器出口蒸汽额定工作温度加上锅炉正常运行时允许 的温度偏差,当锅炉制造厂未提供温度偏差时,温度偏差值可取用5C; 低温再热蒸汽管道,应取用汽轮机最大计算出力工况(调节汽门全开,即Vwo工况)下高 2 压缸排汽参数,等嫡求取在管道设计压力下的相应温度 汽轮机抽汽管道设计温度应符合下列规定 非调整抽汽管道,应取用汽轮机最大计算出力工况(调节汽门全开,即Vwo工况)下抽汽 1 参数,等嫡求取管道设计压力下的相应温度; 调整抽汽管道,应取用抽汽的最高工作温度; 2) 3)背压式汽轮机排汽管道应取用排汽的最高工作温度
减温装置后的蒸汽管道设计温度应取用减温装置出口蒸汽的最高工作温度
D 与直流锅炉启动分离器连接的汽水管道设计温度应取用分离器各种运行工况中管内介质可能 出现的最高工作温度 高压给水管道设计温度应取用高压加热器后高压给水的最高工作温度
f 低压给水管道设计温度应符合下列规定 g 定压除氧器系统,应取用除氧器额定压力对应的饱和温度 1 2) 滑压除氧器系统,应取用汽轮机最大计算出力工况(调节汽门全开,即VwO工况下 1.1倍除氧器加热抽汽压力对应的饱和温度
h 凝结水管道设计温度应取用低压加热器后凝结水的最高工作温度
加热器疏水管道设计温度应取用该加 加热器抽汽管道设计压力对应的饱和温度
iD 锅炉排污管道设计温度应符合下列规定 锅炉排污阀前管道(定期排污或连续排污)的设计温度,应取用汽包上所有安全阀中的最 低整定压力对应的饱和温度 锅炉排污阀后管道,当排污阀后管道装有阀门或堵板等可能引起管内介质压力升高时,排 污管道(定期排污或连续排污)的设计温度应按锅炉排污阀前管道的选取原则确定;当排 污阀后未装设阀门或堵板等不会引起管内介质压力升高时,排污管道(定期排污或连续排 污)的设计温度应按表4选取 12
GB/T32270一2015 锅炉排污阀后管道设计温度 锅炉压力/MPa 项目 1.7504.l5o A.151" 6.200 6.20110.300 10.301 管道设计温度/ 230 255 210 280 k给水再循环管道设计温度应符合下列规定 1对于定压除氧系统,应取用除氧器额定压力对应的饱和温度; 2 对于滑压除氧系统,应取用汽轮机最大计算出力工况下1.1倍除氧器加热抽汽压力对应 的饱和温度
安全阀后排汽管道排汽管道的设计温度,应根据排汽管道水力计算中相应数据选取
6.1.1.3.3对于非金属材料衬里的管道,基体管道的设计温度宜按流体的最高温度确定 6.1.2设计准则 6.1.2.1管道组成件的压力-温度等级除用设计压力和设计温度表示外,还可用公称压力表示
6.1.2.2管道组成件公称压力的选用应符合GB/T1048的有关规定
6.1.2.3对于只标明公称压力的管件,除另有规定外,在设计温度下的允许工作压力应按式(1)进行 计算 [a] P尸,=K叭×PN [] 式中: P 在设计温度下的允许工作压力,单位为兆帕(MPa); K 系数,K=0.1MPa; PN 公称压力; [] 在设计温度下材料的许用应力,单位为兆帕(MPa); [a] 公称压力对应的基准应力,是指材料在指定某一温度下的许用应力,单位为兆帕(MPa)
6.1.3许用应力 管子及管件用钢材的许用应力,应根据钢材的有关强度特性取下列三项中的最小值 6.1.3.1 RR康Ra.i 2 3 式中: R部" 俐材在20C时的抗拉强度最小值,单位为兆帕(MPa); -钢材在设计温度下的下屈服强度最小值,单位为兆帕(MPa); R 钢材在设计温度下0.2%规定非比例延伸强度最小值,单位为兆帕(MPa); Ra -钢材在设计温度下10h持久强度平均值,单位为兆帕(MPa)
o 6.1.3.2许用应力的应用应符合下列规定: a)附录A中材料的许用应力系指许用拉应力,使用时应符合下列规定: 1媒接管子和焊接管件采用附录A的许用应力时,应另外按表1计人媒接接头系数; 2)对于铸造和锻造管道组成件用材料,应计及铸件和锻件质量系数并符合5.3.1.3的 规定 b)许用剪切应力为附录A许用应力的0.8倍
13
GB/T32270一2015 压缩许用应力应符合结构稳定性的要求,且不大于拉伸许用应力
6.2管道组成件的选用 6.2.1一般规定 6.2.1.1管道组成件应根据管道系统内介质的性质、各种可能出现的运行工况、外部环境、材料的使用 性能和工艺性能以及经济性等综合因素选用
6.2.1.2按照本标准中所列的有关标准制造或制作的采用接连接、法兰连接的管道组成件均可用于 管道系统
但其材料、压力和温度都应符合本规范的规定,弯头、弯管、支管连接、封头和异径管等材料 的选用宜与所连接的管子材料一致
6.2.1.3对于本标准中所列标准中未包括的管道组成件应同时符合6.3及TsGD0001的有关规定,方 可采用 6.2.1.4在管道系统中,管道组成件的连接形式宜采用对接焊接
6.2.1.5弯头,弯管,支管连接,异径管、封头,法兰盖的强度计算应符合6.3的规定
6.2.1.6管道及管件的最小壁厚或厚度应符合6.3的规定
6.2.2管子 管子材料的选用应符合3的规定
6.2.2.1 6.2.2.2高温再热蒸汽管道应采用无缝钢管,300Mw及以上容量机组低温再热蒸汽管道宜采用电熔 焊钢管或无缝钢管
6.2.2.3低压给水管道应采用无缝钢管
6.2.2.4管道系统中汽水两相流的管道宜采用CrMo合金钢材料 6.2.3弯头 6.2.3.1弯头宜采用长半径弯头
6.2.3.2公称压力大于PN25的管道上均应采用无缝热压弯头,且宜带直管段
低温再热燕汽管道可 采用同质量电熔焊钢管热成型弯头
6.2.3.3按本标准规定进行承受内压计算、制造(制作)的斜接弯头,可与制造(制作)斜接弯头的直管一 样用于相同的工作条件
工作压力不应超过1.0MPa,工作温度不应超过300
6.2.4弯管 对于主蒸汽、再热燕汽和高压给水等主要管道,宜采用较大弯曲半径的弯管,弯管弯曲半径宜为管 子外径的3倍5倍
6.2.5支管连接 6.2.5.1公称压力为PN25及以下,在满足补强要求的前提下可采用直管开孔连接;公称压力大于或等 于N,设计温度大于2:0.笔的支管迷搓应采用成型管件 6.2.5.2三通不宜采用带加强元件的辅助加强型式 6.2.5.3下列管道的三通型式宜按表5选用
14
GB/T32270一2015 表5三通型式 机组参数 管道类别 超超临界参数 超临界参数 亚临界参数 亚临界以下参数 主燕汽管道 缎制挤压 锻制挤压 锻制挤压 挤压 高温再热燕汽管道 锻制挤压 锻制挤压 锻制挤压 挤压 媒接 焊按 媒接挤压 低温再热蒸汽管道 焊接 高压给水管道 挤压焊接 挤压焊接 挤压焊接 挤压 6.2.5.4亚临界及以上参数机组的主蒸汽、再热蒸汽管道的合流或分流三通宜采用斜三通或“Y”型 三通
6.2.6异径管 6.2.6.1异径管可采用同心或偏心型式 6.2.6.2异径管宜采用钢管模压型式,钢板焊制异径管不应用于PN25以上的管道 6.2.7 封头法兰盖 6.2.7.1公称压力不小于PN40的管道宜采用椭球形封头等对焊封头,公称压力不大于P25的管道 可采用平焊封头
6.2.7.2法兰盖的型式选用应符合GB/T9123的规定,突面法兰盖只能用在不大于PN25的管道上, PN40和PN63的管道上宜采用凸凹面法兰盖,法兰盖附件的选用应符合6.2.!的规定 6.2.7.3法兰盖的材料选用应符合附录A中规定的温度范围,并应符合6.2.9的规定
6.2.8阀门 阀门应根据管道的设计温度、设计压力、介质性质和管道系统对阀门的功能要求选择,并计及 6.2.8.1 外部荷载对阀门操作性能和密封性能的影响
阀门应按相应标准规定的压力温度等级选用
6.2.8.2 6.2.8.3连接不同压力等级管道的阀门、法兰等管道组成件,应按压力等级高的选用
6.2.8.4阀门的泄漏等级应符合合同约定及GB/T13927的规定 6.2.8.5除设计另有规定外,对于PN40及以上阀门的选用应符合下列规定 阀盖密封不应采用螺纹连接的密封结构,宜采用压力自密封结构 a b)阀门端部宜采用对焊连接
6.2.8.6下列阀门应采用钢制阀门: PN16及以上的阀门; a b与高压除氧器或给水箱相连接的阀门; c)给水泵进口阀门; D 油系统阀门; 仪用压缩空气系统阀门; fD 其他有特殊要求的阀门
6.2.8.7 易燃或可燃气体的阀门应采用严密性较好的可燃气体专用阀门,不应采用输送普通流体的阀 门代替 6.2.8.8有毒介质管道的阀门应采用严密型的钢制阀门,阀门本体的密封应有可靠的防泄漏措施
15
GB/T32270一2015 6.2.8.9对于双向密封阀门应采取适当的安全措施防止因温度升高导致内部超压 6.2.8.10流体为饱和蒸汽和汽水两相流时,阀门的阀座及阀芯应采用耐冲蚀材料
6.2.8.11管道系统中至少下列阀门应满足启动时间要求 a)汽轮机抽汽管道的关断阀; 加热器事故疏水阀; b 高压加热器给水管道进出口阀门和旁路阀 c d 有安全功能要求的汽轮机旁路阀
6.2.8.12高压加热器三通阀应以阀门打开或关闭时阀座两侧的最大不平衡压差作为设计压力的基准 值,阀座直径不应小于连接管道内径的90%
6.2.8.13当开启阀门前需预热主管线或用于平衡阀门两侧压力以便于阀门操作时需设置旁通阀
6.2.9法兰及垫片和紧固件 6.2.9.1法兰的选择应符合下列规定: 达兰型式的选用应符合本标谁中所列标准 法兰应符合GBy/T9124中关于压力温度等级的规定 2)连接不同压力等级管道的法兰,应按高等级选用 b管道法兰型式的选择除应符合GB/T91l5,GB/T9116和GB/T9119等相关标准的规定外 并应满足下列要求 设计温度大于300C或公称压力大于等于PN40的管道,应选用对焊法兰
设计温度在 1 300C及以下且公称压力小于等于PN25的管道,宜选用带颈平媒法兰 管道系统中不宜采用承插炽法兰、松套法兰和螺纹法兰 3 对焊法兰宜采用凸凹面(MF)和突面(RF)型式 4)带颈平焊法兰应采用突面(RF)型式
法兰的材料选用应采用符合附录A中规定的温度范围
d)当需要选配特殊法兰时,除应核对接口法兰的尺寸外,还应按6.3.6及相关标准进行计算,保 证所选用的法兰厚度不小于连接管道公称压力下国家标准法兰的厚度
6.2.9.2垫片的选择应符合下列规定 垫片应根据流体性质,使用温度、压力以及法兰密封面等因素选用,垫片的密封荷载应与法兰 的压力等级、密封面型式,表面粗糙度和紧固件相适应
b 垫片的选用应符合下列要求 管道法兰垫片宜采用柔性石墨金属缠绕式,并应符合GB/T4622等相关标准的规定
对 公称压力小于等于PN10,且设计温度小于150C情况也可采用非金属垫片
缠绕式垫 片内环材料应满足流体介质和管道设计温度的要求,外环材料应满足管道设计温度的 要求; 2 对于突面法兰(RF),宜采用带定位环或带内环和定位环型,不应采用基本型或仅带内 环型; 33 对凹凸面法兰MF),应采用带内环型缠绕式垫片;用在突面RF)型法兰上时宜带外定 位环; 非金属垫片的外径可超过突面(RF)型法兰密封面的外径,制成“自对中"式的垫片
6.2.9.3紧固件的选择应符合下列规定 六角头螺栓、等长双头螺柱、螺母和垫圈等紧固件的选用应符合GB150和GB/T9125等相关 a 标准的规定 b)法兰紧固件选用应符合下列规定 16
GB/T32270一2015 紧固件应符合预紧及设计参数下垫片的密封要求 1 2 高温条件下使用的紧固件应与法兰材料具有相近的热膨胀系数
6.2.10补偿器 6.2.10.1补偿器应按照介质种类、运行工况、位移值选用,并符合GB/T12777的规定
6.2.10.2波型补偿器不宜用于受扭转的场合
6.3管道组成件的强度设计 6.3.1一般规定 6.3中所列的管道组成件强度计算方法是内压下的强度计算
6.3.2直管的壁厚计算 6.3.2.1承受内压的直管最小壁厚计算: <1.了的管子,在设计乐力和设计温度下所需的最小壁原s,
" )式(4)计算 对于 ,按式(3 按管子外径确定壁厚时: PD 十C s 7平YT 按管子内径确定壁厚时 PD十2[a]'C十2YPC Sm 2[]7-2P(-Y 式中: S -管子最小壁厚,单位为毫米(mm m; P -设计压力,单位为兆帕(MPa); 管子外径,单位为毫米(n mm; D. D -管子最大内径,单位为毫米(mm);(包括内径正偏差和加工过盈偏差 Y 修正系数,按表6取用; [] -在设计温度下材料的许用应力,单位为兆帕(MPa); 许用应力的修正系数,对于无缝钢管刀=1.0;对于焊接钢管,其值按5.3.1.2取用; C -腐蚀、磨损和机械强度要求的附加厚度,单位为毫米(mm);对于存在汽水两相流介质管 道及超超临界参数机组的主蒸汽管道和高温再热燕汽管道,可取1.6mm2mm;对于 腐蚀性介质管道,根据介质的腐蚀特性确定
表6系数Y值 温度/ 材料 482 510 538 566 593 621 铁素体钢 0.4 0.5 0.7 奥氏民体钢 0,4 0.5 0.7 注1;介于表列中间温度的Y值可用内插法计算
注2:当管子的D./s.<6时,对于设计温度小于等于480笔的铁素体和奥氏体钢,其Y值应按下式进行计算 D+D
GB/T32270一2015 6.3.2.2管子的计算壁厚 管子的计算壁厚应按式(5)计算: S
=Sm十e c 式中: 管子计算壁厚,单位为毫米(mm) S
管子壁厚负偏差的附加值,单位为毫米(mm)
6.3.2.3管子壁厚负偏差附加值 管子壁厚负偏差附加值应按下列规定选取 a)对于管子规格以外径×壁厚标示的无缝钢管,可按式(6)确定: mS C 100一mn 式中: -管子产品技术条件中规定的壁厚允许负偏差,%
m 对于管子规格以最小内径×最小壁厚标示的无缝钢管,壁厚负偏差值等于零
b 对于焊接钢管,采用钢板厚度的负偏差值且不应小于0.5mm
c 6.3.2.4管子的取用壁厚: 对于以外径标示的管子,应根据管子的计算壁厚,并计及管子直径偏差引起的对口焊接要求
a 按管子产品规格中公称壁厚系列选取; 对于以内径标示的管子,应根据管子的计算壁厚,并计及管子直径偏差引起的对口焊接要求 b 遵照制造厂产品技术条件中有关规定,按管子壁厚系列选取
6.3.3弯管弯头的壁厚计算 6.3.3.1弯管的弯曲半径宜为外径的3倍5倍
6.3.3.2弯管弯制前直管的最小壁厚可按表11、表12选用,也可根据制造厂的具体加工工艺条件适当 调整
6.3.3.3弯管和弯头加工完成后的最小壁厚s按式(7)或式(8)确定 按外径确定壁厚时: PD S 十C 7TYP 按内径确定壁厚时: PD十2[a]'C/I十2YPC S 7+YP 一P) 弯管和弯头内弧处: 4(R/D.)一1 I= 9 4(RD.-2 弯管和弯头外弧处: 4(R/D.)十1 (10 4(RD.千2 弯管和弯头中性线处: 11 =1.0 式中: R -弯管或弯头弯曲半径,单位为毫米(mm. 18
GB/T32270一2015 6.3.3.46.3.3.3中所有公式计算得出的壁厚为弯管或弯头成型件外侧和内侧允许的最小壁厚,不应包 括弯制过程中的工艺减薄量和弯制选用管子负偏差的附加值
6.3.3.5弯管或弯头任何一点的壁厚,不应小于弯管(弯头)相应点的计算壁厚,且外弧侧壁厚不应小于 相连管子的最小壁厚S
6.3.4支管连接的补强 6.3.4.1支管连接的强度计算方法有面积补偿法和压力面积法
6.3.4.2采用面积补偿法应符合下列规定: 焊接或锻造的直三通支管连接可采用面积补偿法计算
a 当支管或补强元件材料与主管材料不同时,应符合以下规定 b 支管或补强元件材料采用与主管焊接性能、热处理要求和热膨胀系数相近的材料; 1 当支管或补强元件的许用应力低于主管材料许用应力时,由支管或补强材料提供的补强 2 面积按材料许用应力之比相应折减 当支管或补强元件的许用应力高于主管材料许用应力时,不计及其增强作用
3 面积补偿法(见图3),即主管上开孔挖去的纵断面上的金属面积,应由主、支管在有效补强范 围内补强的金属面积和焊缝面积之和来补偿,其条件按式(12)计算
A十A2十A3>A 式中: 需要补强的面积,单位为平方毫米(mm=)
A=Smhdl 13) 补强范围内主管的补强面积,单位为平方毫米(mm')y A1=(2L一d)(S一S) 补强范围内支管的补强面积,单位为平方毫米(mm' A?=2L(S一S, (15 mb 补强范围内角焊缝面积,单位为平方毫米(mmr'); A -主管上经加工的支管开孔沿纵向中心线的尺寸,单位为毫米(mm) d=D.一2S% (16) 主管有效补强范围宽度之半 那位为笔米fmm服山或s.+s,+“ -两者 L 中的较大者,但任何情况下不大于D山
支管有效补强高度,单位为毫米(mm);" L取2.5(S一C或2.5(S一C两者 中的较小值; 主、支管外径,单位为毫米(mm) D.h、D. 主,支管的公称壁厚,单位为毫米(mm)7 S 主、支管的最小壁厚,单位为毫米(mm)
S 主管上多开孔的补强应符合以下要求,如图4所示 D 多个支管的开孔不宜使其有效补强范围相互重叠; 1 当必须紧密布置时,其强度应等于单个开孔所要求的补强的总和
在计算补强面积时, 2 任何部分截面不得重复计人; 3)任意两开孔中心最小距离不应小于1.5倍的开孔平均直径,且在两孔间的补强面积不应 小于两个开孔所需补强总面积的50%
19
GB/T32270一2015 支竹多全壁 主管中心线 说明 A -所需补强面积 nA 主管提供的补强积 支管提供的补强面积; 焊缝提供的补强面积
园A 图3面积补强法计算示意图 科强范围 补强范围 开 开孔 图4多个开孔的补强 6.3.4.3压力面积法应符合下列规定; 压力面积法的计算示意图见图5,三通纵向断面上主、支管交叉区域内的有效承载断面积和平 a 均应力的乘积,与其相应的有效受压面积和内压的乘积相平衡,并控制此承载面积内的一次膜 态应力不超过钢材的许用应力
压力面积法的强度条件: (17 P1'>"(+ 有效补强长度 主管 Li=、/DSSm 18 支管 2o0
GB/T32270一2015 .(19 L,=1.25(DSsm 在计算承载面积A
时,应计及成型方式造成的面积计算误差
坡口加工段不宜在有效补强 d 范围内,否则有效承载面积应扣除坡口加工减少的面积
D/2 实 三通主管中心线 图5压力面积法计算示意图 6.3.5异径管壁厚计算 6.3.5.1异形管壁厚计算简图见图6
异径管(大端)最小壁厚s按以式(20)和式(21)计算,取二者中 的较大值
PD.十2[a]'C十2YPC 20 ([]'?一2p一Y)cos pD 2[a]p十2Y 2 ! 中心线 d.s 图6异径管壁厚计算简图 式中 异径管平均直径,单位为毫米(mm); Dm D
=D
一s 22 半锥角,宜小于15; 壁厚的附加值,单位为毫米(mm);可按6.3.2.1选取
6.3.5.2异径管小端与管道连接处的强度根据图7按式(17)校核
图7中La、L八按式(23),式(24) 计算 21
GB/T32270一2015 23 L,=/Ds L八=a丽s 24 异径管中心线 图7异径管小端计算示意图 6.3.5.3异径管外侧弯曲半径不宜小于0.1D
6.3.6法兰及法兰附件计算 6.3.6.1螺栓连接的法兰强度应分别按运行工况及螺栓预紧力进行计算,并计及流体静压力及垫片的 压紧力
6.3.6.2法兰连接计算应包括下列内容: a)确定垫片材料,型式及尺寸; b)确定螺栓材料,规格及数量; e)确定法兰材料,密封面型式及结构尺寸; 进行应力校核,计算中所有尺寸均不包括腐蚀裕量
d 对于未按标准规定制造的法兰,法兰及法兰连接应按GB/T17186或GB150.3一2011中 6.3.6.3 第7章的规定计算
盲板的厚度(见图8)应按式(25)计算 6.3.6.4 S=Sm十C 25 式中S为压力作用下的设计厚度,按式(26)计算; 3P S=d 26 6]'7 式中: 对于凸型法兰或平法兰为垫圈内径,或对带垫圈法兰为垫圈节径; de 设计压力,单位为兆帕(MPa) P 厚度裕量,单位为毫米(mm)
图8夹在法兰间的盲板 22
GB/I32270一2015 6.3.7封头及节流孔板的厚度计算 6.3.7.1椭球型封头最小壁厚计算: 最小壁厚S应按式(27),式(28)进行计算,取两者中的较大值
a KPD 27 [-0.5P K(PD十2[a]'C十2YPC 28 Sm= 2[]7-2P-Y 式中: D 封头内径
,mm; 比值有关的修正系数,当椭球形封头的椭圆形状系数D./2h;=2(h;为椭圆短半 K 与 厅 径)时,K值可按图9查取; 修正系数,可按6.3.2.1选取; 许用应力修正系数,封头无拼接时,刀=l.0;有拼接时,7值按表1取值;当设计温度在所 n 用钢材的蠕变温度以上时,)=0.7 [] 设计温度下材料许用应力,单位为兆帕(MPa); -设计压力,单位为兆帕(MPa); C -腐蚀附加厚度,单位为毫米(mm) 出 a.06 0.04 0.02 0.010 0s 0.006 0.004 火 0.002 0.0010 0.0008 0.0006 0.0001 2.0 2.5 图9椭球形封头的椭圆形状系数为2时修正系数K 对焊封头和平封头壁厚按式(29)计算 6.3.7.2 .(29 S=K'D []'9 式中 D 封头内径,单位为毫米(mm)(取相连管道的最大内径); K" 与封头结构有关的系数,按表7选取; 9 设计温度下材料许用应力,单位为兆帕(MPa) [] -设计压力,单位为兆帕(MPa)
23
GB/T32270一2015 表7封头结构型式系数 堵头型式 备注 结构要求 >2s2s1>/>s 0.4 1.05 1.00 推荐优先采用的结构型式 用于不大于PN25和不大于DN400 0,6 0.85 的管道 只用于水压试验 0.4 1,05 用于小于PN25和小于DN40的 0.6 0.85 管道 用于回转堵板,中间堵板和法兰式 0.45 0.85 节流孔板 6.3.7.3孔板厚度计算 a)夹在法兰之间的节流孔板,中间堵板和回转堵板的厚度计算,可按平封头的厚度计算公式 K'值取0.45; b)焊接式节流孔板厚度可按平封头厚度计算公式,其K'值取0.6
管道应力计算 6.4 6.4.1一般规定 6.4.1.1本规范应力计算方法适用于利用管子自身的柔性进行补偿的管道
6.4.1.2管道应力计算宜按管道系统进行计算,对各种可能工况进行应力校核
6.4.2管道应力验算 6.4.2.1管子在内压作用下的应力验算 管子在工作状态下,由内压产生的折算应力,不应大于钢材在设计温度下的许用应力 a 2
GB/I32270一2015 P0.5D.-YS.- 30 1.0[] 口 n(S, 式中: -内压折算应力,单位为兆帕(MPa); o 设计压力.单位为兆帕(MPa); D. -管子外径,单位为毫米(mm); -管子实测最小壁厚,单位为毫米(mm); s 修正系数,见6.3.2.l 许用应力的修正系数.见ha2ln 腐蚀、磨损和机械强度的附加厚度,单位为毫米(mm); 钢材在设计温度下的许用应力,单位为兆帕(MPa)
[] 管道在运行工况下,允许温度和(或)压力超过设计值,但应符合下列规定 b 所计算的环向应力不超过相应温度下许用应力的1.15倍,允许每次不超过8h,且每年不 超过800h; 所计算的环向应力不超过相应温度下许用应力的1.2倍,允许每次不超过1h,且每年不 2 超过80h
持续荷载的应力验算 6.4.2.2 管道在工作状态下,由内压、自重和其他持续荷载作用下,产生的轴向应力之和,应满足式(31)的要求 PD M 31 十0.75 S1.0[o] w D:一D 式中: -管道在工作状态下,由持续荷载产生的轴向应力之和,单位为兆帕(MPa); o1 设计压力,单位为兆帕(MPa); D. 管子外径,单位为毫米(mm) 管子内径,单位为毫米(mm); D 自重和其他持续荷载作用在管子截面上的合成力矩,单位为牛[顿]毫米(N M mm; W 管子截面抗弯矩,单位为立方毫米(mm'); W 32 -(D:一D 32D. -应力增加系数(见附录C),且0.75不得小于1; [] 钢材在设计温度下的许用应力,单位为兆帕(MPa) 6.4.2.3持续荷载与偶然荷载组合工况的应力验算 管道在工作状态下,由内压、自重等持续荷载和偶然荷载作用下,产生的轴向应力应满足式33)的 要求: PD +认万十认万
GB/T32270一2015 2 计算主管的合成力矩 M.(M或Me)一/十M干M 39y M.(M
或Me)=/M干MM 40) 式中: ,Ma.M.aM M.,M,,M 作用在三通交叉点处的当量力矩
主管的截面抗弯矩按式(32)和连接管子尺寸计算
各合成力矩仍按三通的交叉点取值, 见图10
M M2 M 交叉点 图10合成力矩示意图 3)计算支管接管座(见附录cC中的图c.3)的合成力矩 M,(M或M.)=/NMMM 41 接管座的截面抗弯矩按式(42)计算 w=r(rml)'S 如果附录C中图C.3中的a,b,e中L>0.5(r,Si),那么在计算接管座的截面抗弯矩和应力增加 系数时,尸'应计算到s值的一半,验算点应取接管座中心线与主管外表面的交点
6.4.3管道支承反力的计算 6.4.3.1管道对设备或支承点的推力应按6.4.2中荷载组合工况计算,推力应在设备所能安全承受的范 围内
当数根管道与设备相连时,管道在工作状态和冷状态下推力和力矩的最大值,应按设备和各连 6.4.3.2 接管道可能出现的运行工况分别计算和进行组合 6.5管道支吊架 -般规定 6.5.1 6.5.1.1管道支吊架的设置和选型应根据管道布置和对支吊架的功能要求确定
6.5.1.2 支吊架间距应根据管道荷载的合理分布,并满足管道强度,刚度和防止振动等要求 支吊架应支承在可靠的构筑物上,便于施工.,且不影响设备检修及其他管道的安装和扩建
6.5.1.3 6.5.1.4支吊架零部件应有足够的强度和刚度,结构简单,宜采用标准产品
27
压力管道规范动力管道GB/T32270-2015详解
作为一种重要的输送能源和化工产品的设施,压力管道在工业生产和民用领域发挥着至关重要的作用。为了规范压力管道的设计、制造、安装和使用,国家标准化管理委员会于2015年发布了《压力管道规范动力管道GB/T32270-2015》(以下简称GB/T32270)。
首先,GB/T32270适用于输送石油、天然气、水蒸气、饱和蒸汽、超he蒸汽等介质的各种压力管道,主要包括动力管道和工艺管道两类。其中,动力管道是指输送蒸汽、压缩空气、燃料气体等介质的管道;工艺管道是指输送水、油、气、液体等介质的管道。
从技术要求来看,GB/T32270主要包含以下内容:
- 基本规定
- 材料和制造要求
- 设计要求
- 安装、验收和使用要求
- 检验和试验要求
- 标记、包装、运输和贮存要求
其中,设计要求的规定较为详细,包括管道的内径、壁厚、公称直径和长度等方面。此外,还对于弯头、三通、四通、法兰等附件的设计也进行了具体规定。
此外,GB/T32270还对压力管道的质量检验进行了全面规定。检验项目包括尺寸偏差、外观质量、化学成分、机械性能、硬度、冲击功、压力试验等多个方面,确保了产品的整体质量和安全性能。
总之,GB/T32270作为压力管道的通用技术条件,为保障相关领域的生产质量和安全提供了有力的支撑。对于从事石油、天然气、水蒸气等介质输送领域的企业和从业人员来说,熟悉和掌握该标准的具体规定,才能更好地生产、安装和使用压力管道。