GB/T34510-2017
汽车用液化天然气气瓶
Liquefiednaturalgascylindersforvehicles
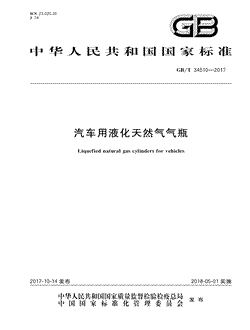
- 中国标准分类号(CCS)J74
- 国际标准分类号(ICS)23.020.30
- 实施日期2018-05-01
- 文件格式PDF
- 文本页数38页
- 文件大小2.65M
以图片形式预览汽车用液化天然气气瓶
汽车用液化天然气气瓶
国家标准 GB/T34510一2017 汽车用液化天然气气瓶 Liquefielnaturalgaseylindersforvehicles 2017-10-14发布 2018-05-01实施 国家质量监督检验检疫总局 发布 国家标准化管理委员会国家标准
GB/34510一2017 前 言 本标准按照GB/T1.1一2009给出的规则起草
请注意本文件的某些内容可能涉及专利
本文件的发布机构不承担识别这些专利的责任
本标准由全国气瓶标准化技术委员会(S.AC/TC31)提出并归口
本标准起草单位:查特深冷工程系统(常州)有限公司、北京天海工业有限公司、张家港富瑞特种装 备股份有限公司、张家港中集圣达因低温装备有限公司、大连市锅炉压力容器检验研究院、特种设 备检测研究院、四川空分设备(集团)有限责任公司
本标准起草人;徐惠新、李兆亭、张保国古海波易希朗,潘华军、股劲松、蔡浩,黄强华、韩冰 王艳辉、陈祖志、王炼、姚欣、郑任重,刘守正
GB/34510一2017 汽车用液化天然气气瓶 范围 本标准规定了汽车用液化天然气(LiquefiedNaturalGas,缩写LNG)气瓶(以下简称气瓶)的术语 和定义、符号、型式,基本参数、材料、设计、制造、试验方法、检验规则、标志、包装、运输、存放、产品合格 证、产品使用说明书、批量检验质量证明书和使用规定
本标准适用于在正常环境温度(一40C60C)下使用、贮存介质为LNG设计温度不高于一196C、 公称容积为150L500L、公称工作压力为0.8MPa3.5MPa的用作汽车燃料箱的可重复充装焊接 绝热气瓶
规范性引用文件 下列文件对于本文件的应用是必不可少的
凡是注日期的引用文件,仅注日期的版本适用于本文 件
凡是不注日期的引用文件,其最新版本(包括所有的修改单)适用于本文件
GB/T228.1金属材料拉伸试验第1部分;室温试验方法 GB/T229金属材料夏比摆锤冲击试验方法 -般公差未注公差的线性和角度尺寸的公差 GB T 1804 2653接接头弯曲试验方法 GB/T7144气瓶颜色标志 GB/T9251气瓶水压试验方法 112137气瓶气密性试验方法 GB 气瓶术语 GB 13005 GB/T135505A分子筛及其测定方法 GB 15384气瓶型号命名方法 GBy/T17925气瓶对接炽缝X射线数字成像检测 18443.2真空绝热深冷设备性能试验方法第2部分:真空度测量 GB 第3部分漏率测量 T GB 18443.3真空绝热深冷设备性能试验方法 GB/T18443.4真空绝热深冷设备性能试验方法第4部分;漏放气速率测耿 GB/T18443.5真空绝热深冷设备性能试验方法第5部分:静态蒸发率测量 GB 真空绝热深冷设备性能试验方法第7部分维持时间测量 18443.7 真空绝热深冷设备性能试验方法第8部分;容积测量 GB 18443.8 承压设备用不锈解解板及钢带 GB/T24511 GB/T25986汽车用液化天然气加注装置 GB/T31480深冷容器用高真空多层绝热材料 GB/T31481一2015深冷容器用材料与气体的相容性判定导则 GB/T33209焊接气瓶焊接工艺评定 HG/T269013X分子筛 JB/T6896空气分离设备表面清洁度
GB/T34510一2017 JB4732钢制压力容器 分析设计标准 NB/T47013.2承压设备无损检测第2部分:射线检测 NB/T47013.3承压设备无损检测第3部分;超声检测 YS/T599超细氧化钯粉 TsGR0006一2014气瓶安全技术监察规程 术语和定义、符号 3.1术语和定义 GB/T13005界定的以及下列术语和定义适用于本文件 3.1.1 批量batceh 包含内胆批量和产品批量
3.1.1.1 内胆批量batchofinnereomtainmentvessels 采用同一设计、同一材料牌号、,同一焊接工艺,连续生产的气瓶内胆所限定的数量
3.1.1.2 产品批量batehofeylinders 采用同一设计,同一材料牌号、同一焊接工艺、同一绝热工艺,连续生产的气瓶产品所限定的数量 3.1.2 内胆innercontainmentvessel 用于充装LNG介质的内层承压元件
3.1.3 外壳outershel 形成和保护气瓶绝热空间的外壳体
3.1.4 静态蒸发率statieevaporationrate 气瓶在充装至最大允许量的低温液体静置48h后,24h内自然蒸发损失的低温液体质量和气瓶有 效容积下低温液体质量的百分比,换算为标准环境下(20C,latm)的蒸发率值
注单位为%/d
3.1.5 净重 net weight 气瓶及其不可拆连接件的实际重量(包括管道系统)
3.1.6 有效容积efteetieolume 内胆允许的最大盛液容积
3.1.7 真空夹层漏率vaeuuminterspaceleakrate 单位时间内漏人真空夹层的气体量
注单位为Pam'/s
GB/34510一2017 3.1.8 漏放气速率leakandoutgassingrate 气瓶夹层放气速率与漏率之和
放气速率为常温状态下气瓶真空夹层中各种材料在单位时间内解 吸的气体量 注:单位为Pam/s.
3.1.9 wakinpe 公称工作压力nominal eSSure 气瓶正常工作状态下,内胆顶部气相空间可能达到的最高压力
3.1.10 壁应力wallstress 气瓶内胆在水压试验下简壁所承受的应力
3.1.11 设计压力designpressure 气瓶强度设计时作为计算载荷的压力参数
气瓶的设计压力 -般取试验压力
3.1.12 有效厚度efteetiethicknes 名义厚度减去腐蚀裕量和钢材厚度负偏差
3.1.13 安全空间safeyspace 内胆中设置的与内胆连通的一部分空间,充装液体结束时,安全空间内仍为气相,用于容纳气瓶内 低温液体由于温度上升造成的体积膨胀,达到避免满液的目的
3.1.14 自动限充功能automaticsafc-spaceinsurancefunetionm 充液时,能够确保在气瓶内胆留有一定安全空间的功能
3.1.15 限流装置excess-flowunit 安装在出液管道上,当在规定方向的流量超过预定的值时,能够自动截止,防止超流状态发生的 装置
3.1.16 维持时间holdtime 气瓶充滥至规定的初始充滥量,从规定的起始条件开始,关闭气瓶各条管线,并开始记时,直至压力 升高达到一级安全阀起跳压力为止所经历的时间
注单位为“天” 3.2符号 下列符号适用于本文件
-封头曲面与样板的间隙.,mm -断后伸长率,%; 焊接接头对口错边量,mm; 封头表面凹凸量,mm, -厚度附加量(C=C+C) mm;
GB/T34510一2017 钢材厚度负偏差, mm; 腐蚀裕量,mm; 内胆公称直径,mm; D 弯曲试验的弯轴直径,mm; 内胆封头或简体的内直径, ,nmm; 外壳封头或筒体的外直径 ,mm 对接焊接接头棱角高度,mm 外壳材料弹性模量,MPa; E 内胆或外壳筒体同一截面最大最小直径差,mm; H 气瓶的外形总长度(含保护圈保护罩). mm; H 封头内凸面高度,mm 封头直边高度,mms K 由椭圆形长短轴比值决定的系数,见表5 外壳体上两相邻支撑线之间的距离,当筒体部分没有加强圈,则取筒体的总长度加上每个" 形封头曲面深度的1/3," mm; 样板长度,mm; 弯轴直径与试样厚度的比值 公称工作压力,MPa 许用外压力,MPa; 设计压力,MPa; 外壳封头的当量半径,mm;对于椭圆封头,R=KD 内胆的设计壁厚,mms 内胆简体实测最小壁厚,mm; 外壳筒体的有效厚度,mm: 外壳封头成形后的最小厚度 mm; 内胆名义壁厚,, ,mm 拉力试样焊接接头宽度,mm; 温度,C; 总热传导系数,kJ/(hm'C) 内胆公称容积,L; 静态蒸发率,%/d; 壁应力,MPa; 抗拉强度,MPa; Rm 规定非比例延伸强度,MPat R. 封头内高度(H,十h)公差 mm; 开D 内圆周长公差, ,mm
型式及基本参数 4.1型式与产品型号 4.1.1气瓶的结构型式为卧式,见图1
GB/34510一2017 说明 -阀门等组合部件 -外壳; -绝热层; -内胆; 保护圈
图1气瓶结构示意图 4.1.2气瓶的产品型号按照GB/T15384进行命名,表示方法如下 改型序号,用罗马字母I、l、l等表示 公称工作压力,MPa 内胆公称容积,L 内胆公称直径,mmm 气瓶型式,用w表示卧式 汽车用液化天然气气瓶名称,用CDP表示 示例 DPw0-4501.9" 表示公称容积为450l,公称工作压力为1.59MPa,内胆公称直径为600mm,第二次改型的气瓶
4.2基本参数 4.2.1气瓶公称容积V和推荐的公称直径D按表1的规定
表1公称容积及推荐采用的公称直径 150~200 200~350 350~500 公称容积V/儿 推荐的内胆公称直径D/mm 300450 450~550 550~750 气瓶的静态蒸发率按表2的规定,其他公称工作压力的气瓶 4.2.2公称工作压力1.0MPa1.6MPa" 静态蒸发率按设计图样规定
4.2.3气瓶真空夹层漏率和漏放气速率按表2规定
GB/T34510一2017 表2静态蒸发率、真空夹层漏率及漏放气速率一览表 公称容积V/L 150 175 200 300 450 500 静态蒸发率n/%/d), 3,48 2.88 2.76 2.64 2.52 2.4 真空夹层漏率/Pam'/s) <6×10" 漏放气速率/(Pam'/s <6×10 注1;公称容积为推荐参考值
注2静态燕发率指液氮的静态燕发率
4.2.4气瓶内胆壁厚的设计压力P为公称工作压力的2倍,压力试验压力不低于公称工作压力的 2倍
材料 5 5.1材料的一般规定 5.1.1气瓶的内胆材料应采用奥氏体型不锈钢,且应符合GB/T24511等材料标准的规定,化学成分和 力学性能不应低于表3和表4的规定
若采用境外牌号材料时,应符合TsGR00062014中2.2的 规定
5.1.2焊在内胆上所有的零部件,应采用与内胆材料性质相适应的奥氏体型不锈钢材料,并应符合相 应技术标准的规定
所采用的不锈钢焊接材料焊成的焊接接头,其熔敷金属化学成分应与母材相同或相近,且抗拉 5.1.3 强度不应低于母材抗拉强度规定值的下限且不低于设计图纸的规定
5.1.4材料(包括焊接材料)应具有材料生产单位提供的质量证明书原件
从非材料生产单位获得材 料时,应同时取得材料质量证明书原件或加盖供材单位检验公章和经办人章的有效复印件
5.1.5内胆简体和封头材料应按炉罐号进行化学成分复验和按批号进行力学性能复验,经复验合格的 材料,应用无氧无硫的记号笔做材料标记 5.1.6外壳材料应采用奥氏体不锈钢
5.1.7真空夹层中的绝热材料及吸附材料应满足以下规定 真空夹层中应采用多层绝热的阻燃材料,其性能应符合GB/T31480的规定,并应通过 a GB/T31481一2015中4.4.4的点燃试验 b) 作为吸附材料的5A分子筛和13X分子筛,应分别符合GB/T13550和HG/T2690的规定
真空夹层中添加的氧化钯,应符合Ys/T599的规定
c 5.2化学成分 内胆主体材料的化学成分及允许偏差按表3的规定
表3内胆主体材料化学成分和允许偏差质量分数 N C 化学成分 Mn C0.035 17.0020.00 百分含量/% 0,08 2.00 0.03 l.00 8.00ll.0 士0.01 士0.04 十0.005 十0,005 士0,05 士0.10 士0.20 允许偏差/%
GB/34510一2017 5.3力学性能 内胆主体材料的力学性能按表4规定
表4内胆主体材料力学性能 抗拉强度Rm 规定非比例延伸强度(R.a 断后伸长率(A >520MPa >40% >205MPa 设计 6.1 -般规定 6.1.1气瓶由内胆,外壳以及夹层中绝热层和阀门管路系统组成
内胆与外壳之间的连接应有足够的 强度,能够承受使用过程中的振动载荷、惯性载荷和冲击载荷,并按照本标准附录A的要求通过安全性 能试验 6.1.2内胆的组成最多不超过三部分,即纵向焊接接头不应多于一条,环向焊接接头不应多于两条
6.1.3气瓶应采用真空多层绝热方式,并进行传热计算,总的热传递不超过2.09J/(hCL)
6.2内胆 6.2.1内胆封头设计 气瓶内胆的封头应是凹面承压,形状为半球形或长短轴比为2:1的标准椭圆形
6.2.2内胆壁厚 内胆设计壁厚不小于按式(1)计算的结果 /0.4P十o -号<.5 o一1.3P. 式中壁应力取下列各项中的最小值: 310MPa; a b) 按8.2测定的焊接接头的最小抗拉强度的50% 按8.1测定的母材的最小抗拉强度的50% c d 按8.1测定的母材的屈服强度; 带纵缝内胆的壁应力不超过上述数值最低值的85%
6.2.3 内胆开孔 只准在封头上开孔,开孔应是圆形
开孔直径不应大于内径的1/3,开孔位于以封头中心为中 6.2.3.1 心的80%封头内直径的范围内
当开孔直径超过76nmm时,应采用有限元分析计算方法对开孔进行 强度校核,可按照JB4732执行
6.2.3.2内胆上的每一个开孔应焊装管接头等其他附件,附件与封头的连接应采用全焊透的焊接形式
6.3外壳 6.3.1 一般要求 外壳筒体和封头壁厚的设计应满足许用外压力不小于0.21MPa的要求
GB/T34510一2017 6.3.2外壳筒体壁厚 外壳筒体壁厚按式(2)进行校核 2s 2.6E(S./D." 2 P1= 05 L/D.一0,45S./D." 6.3.3外壳封头壁厚 外壳封头壁厚按式3)进行校核 P=0.25E(S/R)9 3 如果封头为椭圆形,则R一K,D.,K按照表5选取 表5椭圆封头系数对照表 D/2h 2.6 1.8 .6 1.4 1.2 1.0 2.4 2.2 2.0 K 1.18 0.73 0.57 1.08 0.99 0.90 0.81 0.65 0.50 注1,中间值由内插法求得
注2:K=0.9为标准椭圆形封头
注3:h
=H十S 6.3.4外壳泄放装置 外壳应设置泄放装置,且泄放装置应当满足以下要求 泄放装置的开启压力不应大于0.1MPa; a b) 总的泄放面积不应小于内胆公称容积与0.34mm'/L的乘积
6.4焊接接头 纵、环焊接接头应采用全焊透对接型式
6.4.1 6.4.2纵向焊接接头不应有永久性垫板
6.4.3环向焊接接头允许采用永久性垫板或缩口锁底焊结构
6.4.4连接到内胆封头或筒体上的所有附件,应采用熔化焊焊接,对于受压元件的焊接接头应保证全 焊透
6.5管路系统 6.5.1 -般要求 管路系统的设置应具备充液、出液、自动和手动泄压、超速排放限流、压力显示液位显示等基本功 能
管路系统阀门宜标明介质流向,并且截止阀应标明开启和关闭方向
6.5.2相容性要求 管路系统及其部件所用的密封件不得与液化天然气发生化学反应,并且能够承受盛装介质的低温 6.5.3防护要求 管路系统应设置不可拆卸的防护装置,可采用整体式护罩或支撑结构防护圈
防护装置的设置不
GB/34510一2017 应影响阀门,管路以及抽真空接口的维修或更换
6.5.4充液管路 充液管路上宜设有专用的充液接头
充液接头应具有气瓶内介质流向外部的止回功能,且应带有 防尘盖
如果不设置专用充液接头,则应当设置截止阀、螺纹堵头或者采用法兰等密封结构保证充液 完毕后及使用过程中介质不外泄
6.5.5出液管路 出液管路及管路上的接头、阀门的通径大小,安装位置、安装方式等应能够满足排出能力的要求
出液管路应设有截止阀、限流装置
限流装置安装在出液管路液体侧末端、汽化器前端之间,并且能在其后部的燃料供给管路发生大量 泄漏、破裂,断裂等情况下能够自动切断管路
对于装有外置汽化增压器的结构气瓶,气瓶回气管接头部位应装设单向阀或止回阀),防止瓶内气 体外泄
6.5.6泄压管 泄压管路应与气瓶内胆气相空间直接相通,且管路通径应满足安全泄放的要求
泄压管路分为自动泄压(安全阀开启泄压)和手动泄压
气瓶安装在汽车上时应将泄压管路的出口接引至安全位置排放
车辆停放时泄压管还应符合 10.8e)要求
充装时如果需要泄压,严禁直接对大气排放,可以排放至加气站的LNG储存容器内
6.5.7安全阀 内胆应设置至少两只安全阀,安全阀人口接管应各自与内胆气相空间直接连通
每只安全阀的排 放能力应能单独满足安全泄放的要求
安全阀可按任意方位装设,但安全阀前不应装设截止阀
气瓶主安全阀的出口应满足6.5.5的规定
气瓶不应装设爆破片
安全泄放量和安全阀排放能力的计算见附录B
主安全阀的开启压力不大于公称工作压力的1.2 倍,副安全阀的开启压力不大于公称工作压力的1.8倍
6.5.8压力表 压力表量程为公称工作压力的1.5倍3.0倍,精度不低于2.5级
压力表进口管路应与内胆气相 空间直接连通
6.5.9液位计 每只气瓶应设置能将液位信号传输至汽车驾驶室内的液位计,且当瓶内燃料剩余量为最大充装量 的5%时具有警示功能
6.6安全空间 气瓶内应具有足够的安全空间,充装饱和蒸气压为0.8MPa(表压,下同)的LNG,且安全阀的开启 压力为1.6MPa时,安全空间至少应为内胆总容积的10%
充装饱和蒸气为其他压力,或安全阀采用 其他开启压力的LNG气瓶,则应根据LNG在充装压力和安全阀开启压力下的密度差计算安全空间的
GB/T34510一2017 容积
安全空间的计算方法参见附录C
气瓶的安全空间及设计对应的饱和燕气压力和安全阀开启压 力均应在设计图样和提供给用户的技术文件中注明
6.7自动限充功能 气瓶应具备自动限充功能
在瓶内LNG任意残留量的状态下再次充装时,均应保证瓶内实际安 全空间与设计值相符
自动限充功能试验方法见附录D. 6.8维持时间 气瓶的维持时间不应少于5天
制造 7.1组批 气瓶按内胆组批进行制造,即一个气瓶产品批中一般只包含同一批的内胆,但一个内胆批允许分成 几个气瓶产品批
7.2焊接工艺评定 7.2.1焊接工艺评定应针对纵向或环向焊接接头分别进行
材料壁厚为6mm以下时,每种壁厚均需 进行评定,同等壁厚时,小直径气瓶的评定结果可代替大直径的气瓶
气瓶制造单位在改变内胆材料、 焊接材料、焊接工艺、焊接设备时,投产前均应进行焊接工艺评定,焊接工艺评定除按本标准规定外,其 余要求应符合GB/T33209的规定 7.2.2纵向焊接接头焊接工艺评定可以在焊接试板上进行;环向接接头的焊接工艺评定应在模拟的 圆筒试件上进行,也可以直接在内胆简体上进行
进行工艺评定的焊接接头,应能代表内胆的主要焊接 接头(纵,环,角焊接接头)
焊接工艺评定试件经外观检查应无咬边、裂纹、表面气孔,煤渣,凹坑、焊瘤等缺陷,试板焊接接 7.2.3 头经100%射线透照检测,检测结果应符合NB/T47013.2级要求 7.2.4煤接工艺评定用的煤接接头试样数量规定如下;拉力试样2件,横向弯曲试样4件(面弯,背弯各 2件),内胆材料最低使用温度下低温冲击试样6件(焊接接头、热影响区各3件)
7.2.5当进行焊接工艺评定的内胆材料实测厚度不足以制备厚度2.5mm的低温冲击试样时,应从符 的焊接试板上制备厚度为2.5mm的试样,其试板 合本标准5.1、5.2和5.3规定的厚度不超过3.2mm 材料的含碳量不得低于0.05%
该试板炉号可与该批内胆炉号不同,但应采用相同的焊接工艺
7.2.6焊接工艺评定试验结果要求如下 焊接接头试样无论断裂发生在任何位置,其实测抗拉强度均不得小于内胆材料标准规定值的 a 下限,且不低于设计图纸规定 焊接接头低温冲击试样的冲击吸收功应不小于表6的要求
b 焊接接头试样弯曲至180°时应无裂纹,试样边缘的先期开裂可以不计,但由夹渣或其他焊接缺 c 陷引起的试样开裂应判为不合格
10
GB/34510一2017 表6焊接接头低温冲击试样冲击功参数表 媒接接头或热影响区每组三个 试样尺寸 单个试样的最小值 试样的平均值 mmm 10×1o 20.4 13.6 10×7.5 17 1.6 0×5 13.6 9.5 10×2.5 6.8 4.8 注1:当焊接接头或热影响区每组三个试样的平均值不小于上述单个试样的最小值时,且其中一个以上试样的 冲击值低于要求的平均值,或一个试样的冲击值低于单个试样准许的最小值时,可再取焊接接头或热影响 区三个附加试样进行试验;每一个试样的冲击值均不小于平均值的要求为合格
注2;若由于试样本身的缺陷原因,允许重复取样进行试验
7.2.7煤接工艺评定报告需由煤接责任工程师审核,制造单位技术总负责人批准
7.3筒体 7.3.1筒体由钢板卷焊时,钢板的轧制方向应与筒体的环向一致
7.3.2筒体同一横截面最大最小直径差e不大于0.01D
7.3.3筒体纵焊接接头对口错边量b不大于0.1s,,见图2
7.3.4简体纵向焊接接头棱角高度E不大于0.1S,十2mm,见图3,用长度1为0.5D,但不大于300nmm" 的样板进行测量
样板 图2纵向焊接接头对口错边量示意图 图3纵向焊接接头棱角高度示意图 7.4封头 7.4.1封头钢板不准许拼接
7.4.2内胆封头最小厚度应不小于其简体设计壁厚的90%,外壳封头最小壁厚按照6.3.3规定
封头 的外形不得有突变,且形状与尺寸公差不得超过表7的规定,表中符号见图4
1
GB/T34510一2017 表7封头尺寸公差参数表 单位为毫米 公称直径 圆周长公差 最大最小直径差 表面凹凸量 曲面与样板间歇 内高公差 开AD. h 400 十4.0 十5 -3 400800 士6.0 样板 样板 0.3D 0.8D 图4封头形状尺寸公差示意图 7.4.3封头不得有裂纹,起皮、折皱等缺陷
7.5未注公差尺寸的极限偏差 未注公差尺寸的极限偏差按GBT1804的规定,具体要求如下 机械加工件为中等m级; a b)非机械加工件为粗糙c级
7.6组装 7.6.1气瓶的各零件组装前均应检查合格,且不准进行强力组装
7.6.2封头与筒体的对接环焊接接头对口错边量6不大于0.25S,棱角高度E不大于0.1S,2 mm, 见图5,检验尺的长度应不小于150t mm
图5环向焊接接头对口错边量及棱角高度示意图 7.6.3附件的组装应符合图样的规定
7.7内胆焊接的一般规定 7.7.1气瓶的焊接,应由按照有关安全技术规范的规定考核合格,取得相应项目的《特种设备作业人员 证》的人员,在有效期内担任合格项目内的焊接工作
施焊后,焊接接头应有可跟踪的标识和记录
7.7.2气瓶的纵向、环向焊接接头焊接应采用自动保护焊,施焊工艺应严格按照评定合格的焊接工艺 进行
12
GB/34510一2017 7.7.3焊接坡口的形状和尺寸,应符合图样规定
坡口表面应清洁,光洁,不得有裂纹、分层、夹杂等 缺陷
7.7.4焊接(包括焊接接头返修)应在室内的专用场地上进行,焊接场地应保持清洁、干燥,地面应铺橡 胶或木质垫板,零部件应放置在木质架子上 7.7.5气瓶的焊接工作,应在相对湿度不大于90%,温度不低于0的室内进行
7.7.6施焊时,不得在瓶体上非焊接处引弧,纵向焊接接头应有引弧板和熄弧板
去除引,熄弧板时 应采用切除的方法,严禁使用敲击的方法,切除处应磨平
7.8焊接接头外观 7.8.1内胆对接焊接接头的余高为0mm2.5mm,同一焊接接头最宽最窄处之差不大于3m nm
7.8.2角焊接接头的几何形状应圆滑过渡到母材
7.8.3气瓶上的焊接接头和热影响区表面,不准许有咬边、未焊透、裂纹、气孔、凹陷和不规则突变等缺 陷,焊接接头两侧的飞溅物应清除干净
7.9无损检测 7.9.1 内胆纵.环焊接接头经外观检测合格后应逐只进行无损检刹
从事气瓶无损检测的人员,应持 有有效的特种设备无损检剖人员资格证书 7.9.2内胆纵、环焊接接头进行100%射线透照检测,焊接接头缺陷等级评定按NB/T47013.2进行,缺 陷等级不低于I级,射线检测技术等级不低于AB级
不能进行射线检测的部分,可以采用超声检测 替代 无损检测可采用数字成像方法,采用时应当满足GB/T17925要求
7.9.3 7.10焊接接头返修 7.10.1焊接接头返修应按返修工艺进行,应由具有7.7.1规定资格的人员担任,返修部位应重新按7.8、 7.9进行外观和无损检测
7.10.2内胆焊接接头同一部位的返修次数不宜超过两次,如超过时,返修前应经制造单位技术总负责 人批准
7.10.3返修次数和返修部位应记入产品生产检验记录
7.11表面质量及清洁度 7.11.1内胆及外壳的内外表面均应光滑,不得有裂纹,重皮、,划痕等缺陷,否则应进行修磨,修磨处应 圆滑光沽,且内胆壁厚需满足6.2,外壳壁厚需满足6.3的要求
7.11.2内胆内外表面及所有接触介质的零部件应进行脱脂处理,符合JB/T6896有关规定,并有良好 的保护措施
7.11.3凡处于真空状况的表面和零部件应清洁干燥,不得有油污、灰尘
7.12容积与重量 7.12.1气瓶内胆的实测水容积不应小于其公称容积,实测容积可以用理论计算代替,但不得有负 偏差
7.12.2气瓶制造完毕后应逐只进行净重测定
7.13压力试验 7.13.1气瓶的内胆经射线透照检测合格后应逐只进行压力试验,压力试验采用水压或气压试验,试验 13
GB/T34510一2017 压力按4.2.4的规定
水压试验介质为清洁的水且氯离子含量应不超过25mg/L;气压试验应采用干 燥无油的空气或氮气
7.13.2气压试验应有安全防护措施
7.13.3在试验压力下保压应不少于30s,内胆不得有宏观变形、泄漏和异常响声等现象,压力表量程 为试验压力的2.0倍~3.0倍,精度不低于1.6级
7.13.4水压试验后应及时排净内胆与接管中的水,并使其干燥 7.13.5如果在压力试验中发现焊接接头有泄漏,应按7.10的规定进行返修,返修合格后,重新按要求 进行压力试验
7.14内胆焊接接头力学性能试验 7.14.1 每批内胆应进行焊接接头力学性能试验,可在内胆或产晶焊接试板上取样
在焊接试板上戴 取试样时,只进行纵向焊接接头的力学性能试验
产品焊接试板应和受试内胆在同一块钢板(或同炉批钢板)上下料,作为受试内胆纵焊接接头 7.14.2 的延长部分与纵缝一起焊成,试板应标上受试内胆和焊工的代号,试板上的焊接接头应进行外表检查和 100%射线透照检测,并符合7.8和7.9的规定,焊接试板尺寸和力学性能试样取样的位置按图6. 单位为毫米 CCC 500 说明: -拉力试件; -弯曲试件 冲击试件; 舍弃部分 图6焊接试板上力学性能试样取样的位置示意图 7.14.3在气瓶内胆上取样的位置按图7
m 件横向背弯试样 3件冲击试样 件拉力试 1件械向面弯试样 I件横向背弯试样 3件冲击试样 图7内胆上力学性能试样取样的位置示意图 7.14.4试样的焊接接头截面应良好,不得有裂纹、未熔合、未焊透,夹渣和气孔等缺陷
14
GB/34510一2017 7.14.5力学性能试验结果应符合7.2.6的要求
7.15绝热材料与吸附材料 7.15.1绝热材料及吸附材料的选用应符合5.1.7和图样的规定
7.15.2绝热层包扎应牢固,不应出现溃散现象
7.16真空检漏 7.16.1 气瓶应逐只进行真空检漏,漏率应符合4.2.3的要求
7.16.2如果在真空检漏试验中发现焊接接头有泄漏,可按7.10的规定进行返修,返修合格后,重新按 7.13的要求进行压力试验,合格后再按照要求进行真空检漏试验
7.17真空 气瓶充装液氮后,夹层真空度不低于2×10-Pa
7.18管路气密性试验 气瓶的阀门及安全附件组装后应用干燥无油的洁净空气或氮气进行管路气密性试验,试验压力为 公称工作压力,保压时间不少于1 阀门、接头及安全附件等不得有泄漏现象
min
试验方法 8.1材料复验 气瓶不锈钢材料化学成分和力学性能的复验,按其材料标准规定的方法取样分析和试验
8.2焊接工艺评定试板力学性能试验 8.2.1按7.2.2的要求,从焊接工艺评定试板(尺寸参照图6)上截取样坯时,试板两端舍去部分不少于 50mm,样坯一般用机械加工方法截取
采用热切割时,应去除热影响区
从内胆上用热切割截取样坯 时(截取部位参照图7),试样上不得留有热影响区 8.2.2炽接工艺评定用的炽接接头试样数量按7.2.4的规定
8.2.3试样的焊接接头正面和背面,均应进行机械加工,使其与母材齐平,对于不平整的试样,可以用 冷压法矫平
8.2.4试样制作和试验方法应满足以下规定: 拉伸试样按图8加工,夹持部分长度根据试验机夹具确定,拉伸试验方法按GB/T228.1进行
a 单位为毫米 0+S 图8拉伸试样加工尺寸 b)弯曲试样宽度为38mm,弯曲试验按GB/T2653进行
试验时应使弯轴轴线位于焊接接头中 15
GB/T34510一2017 心,两支辗面间的距离应做到试样恰好不接触辐子两侧面(如图9),弯轴直径d应为试样厚度 的4倍,试验角度应符合7.2.6的规定
3.OS. 图g弯曲试验示意图 冲击试样的尺寸采用10mm×10mm×55mm标准试样,或采用厚度为7.5mm、5mm或 2.5mm的小试样,取样方法和要求按照GB/T33209
焊接接头冲击试样纵轴应垂直于焊接 接头轴线,缺口轴线垂直于母材表面
焊接接头试样的缺口轴线应位于焊接接头中心线上,热 影响区试样的缺口轴线与熔合线交点的距离大于零,且应尽可能多地通过热影响区
低温冲击 试验方法按GB/T229进行
试件冷却温度为-196C,从试件取出到完成冲击试验的时间不 得大于5s
8.3焊接接头无损检测 内胆纵、环焊接接头射线透照检测按照NB/T47013.2进行,X射线检测可采用数字成像方法,采 用时应当满足GB/T17925要求
超声检测按照NB/T47013.3进行
8.4焊接接头力学性能试验 8.4.1从内胆上截取焊接接头试样;分别从纵向和环向焊接接头上截取拉力、横向面弯和背弯试样各 1件、低温冲击试样缺口位于焊接接头中心)3件
试板和样坯的截取部位见图7
从产品焊接试板上截取焊接接头试样;拉力试样1件,横向面弯和背弯试样各1件,冲击试样(缺 8.4.2 口位置位于焊接接头中心)3件,样坯的截取部位见图6
8.4.3从气瓶内胆上或产品焊接试板上截取样坯方法应符合8.2.1的规定
8.4.4焊接接头拉力、弯曲和冲击试样的制作及其试验按8.2.3,8.2.4的规定进行
8.4.5当内胆材料的实测厚度小于2 时可免做冲击试验
.5mm 8.5内胆的压力试验 采用水压试验时,按照GBT9251的规定进行
8.5.1 8.5.2采用气压试验时.先缓慢升压至规定试验压力的10%.保压足够时间.并且对所有焊接接头和连 接部位进行初次检查;如无泄漏后,再继续升压到规定试验压力的50%;如无异常现象,其后按规定试 验压力的10%逐级升压,直到试验压力;保压至少保持30s;然后降至公称工作压力,对焊接接头进行 气密性检查
8.6管路的气密性试验 管路的气密性试验按GB/T12137规定进行,试验介质为干燥、清洁无油的空气或氮气
8.7重量与容积的测定 8.7.1采用称量法测定气瓶的净重,重量单位为千克(kg).
16
GB/34510一2017 8.7.2称量应使用最大称量为实际称量的1.5倍3.0倍的衡器,其精度应满足最小称量误差的要求
8.7.3内胆应进行容积测量,测定方法按GB/T18443.8的规定进行
由于结构等原因可用几何尺寸 测量法测量并计算容积
8.7.4重量和容积的测定应保留三位有效数字,其余数字对于重量应进1,对于容积应舍去 8.8壁厚的测定 壁厚测定应使用超声波测厚仪测量 8.9外观检查 8.9.1目测检查内胆和外壳的表面,焊接接头外观及安全附件
8.9.2用白色、清洁、干燥的滤纸擦抹脱脂表面,纸上应无油脂痕迹和污物,与介质接触的表面应按 JB/T6896要求进行检查
8.10真空度的试验 真空度的试验方法按GB/T18443.2规定进行
8.11真空检漏试验 真空检漏可采用氮质谱检漏的方法进行
8.12真空夹层漏率试验 真空夹层漏率的试验方法按GB/T18443.3规定进行
8.13漏放气速率试验 漏放气速率的试验方法按GB/T18443.4规定进行
8.14静态蒸发率试验 静态燕发率的试验按GB/T18443.5规定进行
8.15维持时间试验 维持时间按GB/T18443.7规定进行
检验规则 g.1材料检验 g.1.1气瓶制造单位应按8.1的规定方法对内胆的材料,按炉罐号进行化学成分验证分析,按批号进行 力学性能验证试验
g.1.2内胆材料的化学成分和力学性能试验复验结果应符合5.2,5.3和设计图样的要求,检验项目按 照5.1.5的要求;若采用国外材料时,则应符合5.1.1的规定
g.2出厂检验 9.2.1逐只检验 气瓶逐只检验应按表8规定项目进行
17
GB/T34510一2017 9.2.2批量检验 9.2.2.1 分批和抽样规则 以不多于200只内胆为一批,从每批抽取1只内胆或做一块产品试板取样进行焊接接头力学性能 试验
9.2.2.2批量检验项目 气瓶以内胆批为基础进行组批
其批量检验项目按表8的规定,其中静态蒸发率检测,每批产品抽 检数量不少于3只
9.2.3复验规则 g.2.3.1在批量检验中,如有不合格项目,应进行加倍复验
加倍抽样方式按照9.2.3.2和9.2.3.3的规 定进行
9.2.3.2在焊接接头力学性能试验中,如果试验不合格可在同一内胆或原产品焊接试板上按照原要求 取相同数量的试件,也可在同批内胆中重新取样试验
如有证据证明是操作失误或试验设备失灵造成 试验失败,则可在同一内胆上或原产品焊接试板上做第二次试验;第二次试验合格,则第一次试验可以 不计
焊接接头力学性能试验经加倍复验仍不合格时,则该批气瓶内胆为不合格
9.2.3.3进行静态蒸发率测试时,如有1只不合格应从该批产品中再抽取数量不少于6只进行加倍复 验
在进行加倍复验时,如果仍有1只不合格,则该批气瓶也应进行逐只检验
如有证据证明是操作失 误或试验设备失灵造成试验失败,可以用同一只气瓶进行第二次试验;第二次试验合格,则第一次试验 结果可以不计
g.3型式试验 9.3.1新设计气瓶首次批量投产前或停产逾六个月而重新投产的首批气瓶应按照9.3.2的要求进行型 式试验
9.3.2提交满足数量的同规格气瓶和内胆,按表8规定的项目进行型式试验
表8型式试验检验项目表 序号 检验项目 逐只检验 批量试验 型式试验 检验方法 判断依据 9.1 材料复验 8.l 绝热材料点燃试验 5.1.7 5.1.7 最大最小直径差e" 7.3.2 简体纵向焊接接头对口错边量b 7.3.3 7.3.3 纵向焊接接头棱角高度E 7.3,4 7.3.4 内圆周周长公差开\D 7.4.2 最大最小直径差
" 人 7.4.2 7.4.2 表面凹凸量 封头曲面与样板间隙a 7.4.2 7.4.2 人 10 内高公差h 7.4.2 外观 7.4.3 12 壁厚 8.8 7.4.2 18
GB/34510一2017 表8(续》 序号 检验项目 逐只检验 批量试验 型式试验 检验方法 判断依据 13环向焊接接头对口错边量 7.6,2 7.6,2 7
14 6.2 7.6.2 环向焊接接头棱角高度E 7.11 15 8.9 内胆、外壳表面质量 16 焊接接头外观 8.9.1 7.8 气瓶壁厚 8.8 图样 7.9,2 18 8.3 纵向、环向焊接接头无损检测 或7.9.3 媒接接头力学性能 8.4 19 7.14.5 8," 7.12 20 重量与容积 21 8.5 7.13 内胆压力试验 22 管路气密性试验 8.6 7.18 23 清洁度 8.9.2 7.l1 24 真空度的试验 8.10 7.17 真空检漏 25 8.lm 7.l6 26 真空爽层漏率试验 8.12 4.2.3 27 漏放气速率试验 8.13 4,2.3 28 8.14 4.2.2 静态燕发率试验 维持时间测定 6.8 29 8.14 30 安全性能试验 附录A 附录A 31 自动限充功能试验 附录D 附录D 注:表示检验该项目
9.3.3当改变设计而影响气瓶的绝热性能时,应按照表9或表A.1要求进行相关型式试验
表9设计变更需重新进行型式试验的试验项目 变更内容 内胆 内胆 安全 绝热系统 夹层 型式试验项目 内胆 内胆 内胆 材料或 支撑 管道 材料 空间 设计壁 直径 容积 设计 结构 走向 类型 设计 粼接接头力学性能 绝热材料点燃试验 真空度试验 真空夹层漏率试验 漏放气速率试验 静态蒸发率试验 19
GB/T34510一2017 表9(续 变更内容 绝热系统 内胆 夹层 内胆 安全 型式试验项目 内胆 内胆 内胆 材料或 支撑 管道 材料 空间 设计壁厚 直径 容积" 设计 设计 结构 走向 类型 维持时间测定 自动限充功能试验 注1:关表示需要进行的型式试验项目
注2设计变更的安全性能试验项目见表A.1
绝热系统材料或设计的变更是指绝热材料类型、吸附材料类型或包扎方式等影响绝热性能的变更
仅容积变化且变化率不超过已通过型式试验的受试瓶内胆容积的100%时可免做
安全空间设计内容包括占内胆总容积的比例(%)和进排液方式
10标志、包装、运输、存放 10.1气瓶应在明显部位焊接固定铭牌,铭牌应包括以下内容 制造单位名称和制造许可证号码; a b 制造单位代号; c 气瓶型号; d 气瓶编号; 产品标准号; 实际容积,L; 公称工作压力,MPa; g 水压试验压力,MPa; h 充装介质; 最大充装量,kg; 气瓶净重,kg; k 监检标记 m制造日期 安全空间,L; n 注意事项:本气瓶的气相安全空间仅适用于充装蒸气压不小于×.×MPa的饱和LNG
o 10.2气瓶应在明显部位牢固设置“安全使用告知"警示牌
内容至少包括;“远离火源、集中排放" 10.3气瓶的字样、字色和色环等可按照GB/T71挂的有关规定
10.4气瓶出厂时应对内胆充装0.o1MPa一0.05MPa干燥氮气,并关闭所有阀门
10.5气瓶的包装应根据图样规定或用户要求
10.6气瓶在运输和装卸过程中,要防止碰撞、受潮和损坏附件
10.7在外壳前封头便于观察的部位,应当压制明显凸起的LNG介质符号,其字体高度不应低于 60m
10.8气瓶的存放应满足以下规定: 20
GB/34510一2017 气瓶应存放在阴凉干燥处
a b 气瓶在未安装到汽车上之前,禁止带液(LNG;)存放
对于已安装有气瓶的汽车在存放期内应将带液气瓶的安全泄放装置排气口与按规定要求制作 的泄压排放管相连,将超压排放的天然气接引至安全位置泄放
产品合格证、产品使用说明书和批量检验质量证明书 11.1产品合格证及使用说明书 11.1.1出厂的每只气瓶均应附有产品合格证,且应向用户提供产品使用说明书
在使用说明书中应 注明充装介质的最低饱和蒸气压、安全阀动作压力,操作安全要求等内容
11.1.2出厂产品合格证格式参见附录E,且应至少包含以下内容 a 制造单位的名称; b 气瓶型号; c 气瓶编号; d)公称容积,L 公称工作压力,MPat e 产品批号; 内胆批号; g 充装介质的最低饱和蒸气压,MPa h 出厂检验标记; 制造年月 j k 产品标准号; 制造单位制造许可证编号
11.2批量检验质量证明书 1.2.1批量检验质量证明书的内容,应包括本标准规定的批量检验项目,格式参见附录F 11.2.2出厂的每批气瓶,均应附有批量检验质量证明书
该批气瓶有一个以上用户时,所有用户均应 有批量检验证明书的复印件
11.3资料保存年限 气瓶制造单位应妥善保存气瓶的检验记录和批量检验质量证明书的复印件(或正本),保存时间不 应少于15年
使用规定 12 2.1真空丧失的气瓶严禁继续使用
2.2遭遇车祸的气瓶应当在检测机构经过检测判定合格方可继续使用
2.3严禁私自维修气瓶,气瓶的维修应由有制造资格的厂家或在其指导下委托有关单位进行维修
2.4气瓶使用单位应建立产品使用管理制度、安全操作制度、维护制度和定期检查制度,每年对气瓶 进行定期检查后出具定期检查报告
21
GB/T34510一2017 附 录 A 规范性附录) 安全性能试验 A.1安全性能试验项目及要求 A.1.1安全性能试验项目包括 a 振动试验; b)火烧试验; c 跌落试验
A.1.2符合以下情况的,应进行安全性能试验 a 新设计的产品,应进行安全性能试验
b 因设计、制造有重大变更时,应按照表A.1的规定进行安全性能试验
表A.1设计变更时安全性能试验项目 安全性能试验项目 变更内容 振动试验 火烧试验 跌落试验 支撑结构改变 内胆名义壁厚改变 公称直径变大 绝热材料类型或包扎方式改变 公称容积变大" 公称容积变小 管路系统保护圈或保护罩改变" 注;“A"表示要做的项目 表示相同的内胆直径、内胆壁厚,仅仅是公称容积的变化
当仅管路系统保护圈或保护罩改变时,仅需进行对管路系统淄的3m跌落试验 A.1.3安全性能试验用的产品,应按照表8经过检验合格后进行,试验结果应详细记录,资料存人技术 档案,至该类型产品不再生产以后15年
A.1.4安全性能试验应在首批生产的气瓶中任意选取,数量应满足下列项目试验要求 振动试验; aa 火烧试验; b) 3m高度跌落试验 d)10m高度跌落试验 A.1.5若气瓶加装外置增压器,则该增压器,连接管路及气瓶的固定支座,还应与气瓶一同进行安全性 能试验
固定支座应具有足够的强度和刚度,以便对连接在气瓶外部的装置、管路和附件起到保护 作用
进行3m跌落试验时,应采用措施使气瓶着地时固定支座承受地面撞击力,必要时可加装试验工 22
GB/34510一2017 装,试验工装沿长度方向应超出保护圈或保护罩至少250mm
试验工装应与固定支座刚性连接,使气 瓶着地时通过试验工装将地面撞击力传导至固定支座
试验工装应具有足够的强度和刚度,以避免试 验时试验工装发生明显的变形影响试验结果
A.1.6经安全性能试验合格的,增压器,连接管路以及气瓶和增压器与固定支座的栓固方式不应改变, 如更改则应重新进行安全性能试验
对于加装外置增压器的气瓶已通过安全性能试验的,可不再进行同规格气瓶的振动试验、火烧 试验
A.2安全性能试验方法及评定要求 A.2.1振动试验 A.2.1.1试验目的 实施振动试验的目的是模拟检验气瓶在汽车运行条件下,内胆与外壳的支撑结构管路系统等的耐 久性
A.2.1.2试验条件 振动试验前气瓶中充装与装满LNG等重的液氨,气瓶处于完全冷却状态,压力为0MPa(表压》. A.2.1.3试验规程 试验规程要求如下 对于客车用气瓶;振动加速度为3g(3倍重力加速度),对于重型货车用气瓶(不包括半挂牵引 a 车)振动加速度为5g(5倍重力加速度); 振动方向为上下垂直方向(见图A.1); b 说明 -气瓶; 振动台
图A.1振动试验示意图 振动试验在8Hz一40Hz范围内扫频,扫频时发现有共振的,应更改气瓶设计,然后重新进行 型式试验; 振动频率的变动方法及加振时间,按照表A.2规定的振动频率和时间加振
d 对于运行路况特别恶劣的重型货车用气瓶,试验参数可由供需双方协商确定 e 23
GB/T34510一2017 表A.2振动频率与加振时间对照表 30 振动频率/Hz 15 20 25 35 40 l70 122 89 67 54 45 38 34 加振时间/min A.2.1.4试验评定 试验结果应同时满足以下要求为合格 振动完毕后,任何部位不得出现泄漏 a b) 振动完毕后,静置30min以上气瓶外壳不应有结露或结霜现象(内胆与外壳连接支撑部位除 外)
A.2.2火烧试验 A.2.2.1试验目的 实施火烧试验的目的是检验气瓶在外部高温环境下气瓶绝热系统性能的安全可靠性
A.2.2.2试验条件 火烧试验前,装满与LNG等高度的液氮,气瓶处于放空或瓶内维持0.8MPa的饱和蒸气压,且完 全冷却状态,试验前关闭放空阀
加装外置增压器的气瓶进行火烧前,应开启增压阀,火烧时增压阀应 保持开启状态
气瓶应水平架起或吊装固定好,不准许火焰直接烧到安全阀、截止阀、压力表、调压阀等 附件
允许采用金属板作为管路系统的保护罩
瓶体底部沿轴向布置不少于3只热电偶用以监测气瓶 外表面温度,热电偶距离气瓶底部不应大于10mm,热电偶间距不大于0.75m
应采用适当的方式监 测气瓶内压力
温度或压力应至少30s记录一次
仪表及表线等应引到隐蔽体或防护屏障内,保证万 -气瓶爆炸不会给试验人员带来危险并保证试验过程中能正常测定温度和压力的变化
A.2.2.3试验规程 试验采用天然气(或液化石油气)为燃料
在倒置的气瓶正下部放置燃气管路、燃烧装置等,保证气 瓶的最低点距燃烧装置120mm130mm, 燃烧装置大小应足以使气瓶的主体边缘完全置于火焰之 中,因此燃烧装置长度与宽度应至少超出气瓶在水平面投影长度与宽度的100mm;保证足够燃烧 时间
试验场所的风速不应超过2.2m/s 试验时间要求在气点火10min内,任意一只热电偶测得的温度应不低于590C,此时开始计时;并 控制热电偶温度在590C附近,火烧时间应满足表A.3的规定
表A.3气瓶火烧时间对照表 瓶内初始压力/MPa 0.8 安全阀起跳时间/min 30 el5 当满足时间要求后,继续进行试验,直至安全阀开启,然后切断火源
记录安全阀开启的压力
A.2.2.4试验评定 气瓶内压力达到安全阀开启压力后,安全阀应能正常动作,且开启时的火烧时间应满足表A.3 24
GB/34510一2017 规定
A.2.3跌落试验 A.2.3.1试验目的 实施跌落试验目的是检验气瓶在冲击条件下的完整性
跌落试验包括:对气瓶的最关键部位(自行 指定,管路系统端除外)进行10m高的跌落试验和对管路系统端3m高的跌落试验
A.2.3.2试验条件 跌落试验前,气瓶应装满与LNG等重量的液氮,气瓶处于放空且完全冷却状态,试验前关闭放空 阀
跌落平面应为坚固、平整的水平水泥地面
A.2.3.3试验规程 将气瓶升高前测定气瓶的重量、环境温度、风速,填人相应的表内
用防冻液体清除待冲击部位的霜和水
将气瓶升高到规定的高度,然后释放气瓶,让气瓶做自由落体运动
在释放气瓶时,爱求所有固定 点应同时释放 待气瓶落地后,用照相机将气瓶的落点、在水泥地面上的方向,位置等情况记录下来
A.2.3.4试验评定 跌落试验完毕后的1h内任何部位不得出现泄漏,气瓶外壳不得有大面积结露或结霜现象(内胆 与外壳连接支撑部位除外). 25
GB/T34510一2017 录 附 B 规范性附录) 气瓶安全泄放量和安全阀排放能力的计算 B.1符号 下列符号适用于本文件; 在额定泄放压力(取1.2倍的安全阀整定压力)下,将以瓶内介质计算的气瓶最小安全 Q,Q心 泄放量折合成自由流空气(101.325kPa绝对压力,15,6C)的流量,nm/h(体积流 量); 泄放压力下瓶内介质的温度,C; 气体系数,由表B.1查得或表B1上方的计算式计算得到; U 气瓶绝热材料的总热传导系数,可以通过绝热层的热传导率除以绝热层厚度得到热 传导率可由试验测定,kJ/(hm'C) 气瓶瓶体外表面积,m' A
w,w
在额定泄放压力(取1.2倍的安全阀整定压力)下,将以瓶内介质计算的气瓶最小安全 泄放量折合成自由流空气101.325kPa绝对压力,15,6C)的流量,kg/h质量流 量); -气体压缩系数,对空气和天然气,Z取1.0 泄放压力下瓶内所装介质的汽化潜热,kJ/kg; 气体特性系数,对空气C取356,对天然气C取348 气体的摩尔质量,对空气M取29,对天然气M取16 安全阀的额定排量,kg/h(质量流量); 安全阀的泄放系数,与安全阀的类型、结构有关,一般选用0.6,或由安全阀制造单位 实测确定; 安全阀的额定泄放压力(绝对压力),MPa; -泄压装置的泄放面积,mm' -泄放装置泄放温度,K,对自由流空气,取288.8K
B.2气瓶安全泄放量的计算 B.2.1当气瓶绝热层完整但绝热层真空被破坏,绝热层空间被所装介质或大气所充满,气瓶的最小安 全泄放量可以由式(B.1)确定: 0.382(54.4一')G,UA Q. B.1 649 式中,U值是在绝热层真空被破坏,绝热层空间被所装介质或大气所充满条件下取得,取两者中较 大值
U值应在绝热层平均温度(也可采用37.8)下确定
B.2.2当绝热层真空被破坏,绝热层空间被所装介质或大气所充满,同时处于外部高温条件(试验环境 或火灾)下,气瓶的最小安全泄放量可以由计算式(B.2)确定 B.2 Qa=GUA"s 式中,U值是在绝热层真空被破坏,绝热层空间被所装介质或大气所充满条件下取得,取两者中较 26
GB/34510一2017 大值
U值应在649C外部高温条件(试验环境或火灾)下确定
B.2.3气瓶最小安全泄放量需按式(B.3)和式(B.4)将由式(B.1)和式(B.2)计算所得体积流量转换到质 量流量 B.3 w.=1.224Q. (B.4 w
=1.224Q. B.3安全阀的额定排量计算 安全阀的额定排量按下式计算: B.5) w,-7.6义I0'cKPA一 由于W.、W为折合成自由流空气的安全泄放量,在计算w时,相应的气体参数应按自由流空气 取值,以便进行比较评定
B.4判定 -级安全同的额定排量应不小于气瓶的最小安全泄散量w. 二级安全阀的额定排量应不小于气瓶的最小安全泄放量We 当安全阀的额定排放压力低于0.69MPa或介于表B.1中所列两档之间时,G按表中较大值取值 当额定的安全阀排放压力高于2.76MPa时,G,按式(B6)进行计算
241649-Z27 G= B.6 gC M 表B.1安全阀额定泄放压力对应的气体系数G 系数G 介质 额定泄放压力/MPa 0.69 3,42 1.38 4.06 液化天然气 2.07 4.93 2.76 5.95 0.69 5,95 1.38 6.88 液氮 2.07 8.05 2.76 10.44 27
汽车用液化天然气气瓶GB/T34510-2017解析
一、概述
随着全球能源危机的日益严峻,新能源汽车作为一种新型的交通工具受到越来越多消费者的关注。而液化天然气作为新能源之一,由于其低碳环保、价格优势等特点,正在逐渐成为新能源汽车领域的重要发展方向。
GB/T34510-2017标准则是针对液化天然气(LNG)在汽车上应用所需的气瓶质量和安全问题制定的。该标准规定了适用于汽车用液化天然气的气瓶技术要求及相关性能指标,以确保汽车用液化天然气气瓶的质量和安全性。
二、液化天然气气瓶的技术要求
根据GB/T34510-2017标准,适用于汽车用液化天然气的气瓶需要满足以下技术要求:
- 1. 气瓶应该具有一定的热稳定性和耐腐蚀性;
- 2. 气瓶应该在服役期内保持良好的机械性能和安全性能;
- 3. 气瓶的设计和制造应符合国家相关法律法规的要求;
- 4. 气瓶应该通过各种测试和检验,包括试压、爆破、冲击、燃烧等测试以及超声波探伤、X-ray射线检测等检验;
- 5. 气瓶应配备恰当的保护装置以保证安全性。
三、液化天然气气瓶的性能指标
根据GB/T34510-2017标准,适用于汽车用液化天然气的气瓶需要进行以下性能指标测试:
- 1. 爆破压力
- 2. 承载容量
- 3. 冲击试验
- 4. 燃烧测试
- 5. 超声波探伤
测试结果应符合标准中的要求。
四、结论
在新能源汽车发展的背景下,液化天然气作为一种重要的新能源之一,其应用领域不断扩大。GB/T34510-2017标准则是针对液化天然气在汽车上应用所需的气瓶质量和安全问题制定的,其规定了适用于汽车用液化天然气的气瓶技术要求及相关性能指标。该标准的实施将有助于确保汽车用液化天然气气瓶的质量和安全性,为新能源汽车的发展提供有力保障。