GB20006-2005采
木工机床安全镂铣机
Safetyofwoodworkingmachines--Singlespindlehandfed/integratedfedroutingmachines
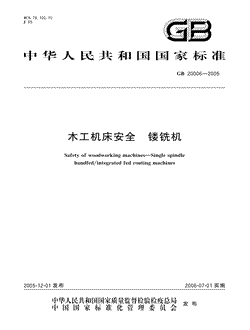
- 中国标准分类号(CCS)J65
- 国际标准分类号(ICS)79.120.10
- 实施日期2006-07-01
- 文件格式PDF
- 文本页数31页
- 文件大小1.01M
以图片形式预览木工机床安全镂铣机
木工机床安全镂铣机
国家标准 GB200062005 木工机床安全镂钒机 Safetyofwo0dworkingmachinesSinglespindle handfed/integratedfedroutingmachines 2006-07-01实施 2005-12-01发布 国家质量监督检验检疫总局 发布 中 国国家标准化管委员会国家标准
GB20006一2005 18 5.3.10危险材料 18 5 .3.11振动 18 5. .3.12辐射 18 5.3.13激光 19 5. .3.14静电 19 5.3.15装配误差 5.3.16能量输送的切断 5.3.17维修 使用信息 6.1警告装置 6.2标志 6.3使用说明书 附录A(规范性附录 噪声测量时机床的工作(运转)条件 A. -般要求 A.2噪声测量 吵 A.3机床噪声测量数据单 附录B(资料性附录)安全工作方法 26 -般要求 26 B1 B.?操作者的培训 26 B.3稳定性 26 B 机床的安装和调整 4 26 B5工件的导向 26 B.6旋转方向和速度选择 26 B.7机床的运转,防护装置的选择和调整 B.8在工件全长上铁削的直线加工 B.9间断直线加工 27 B.10成型加工 27 B.11顺削 27 B.12附件和自动化 27
GB20006一2005 前 言 本标准的第3章,6.3p)中第2和4分项及附录B是推荐性的,其余为强制性的
本标准修改采用欧洲标准EN848-2:1998《木工机床安全刀具旋转的单面铁床第2部分:手动 进给/机动进给的单轴镂饥机》,在标准的技术内容上与EN848-2:1998基本一致,增加了机床空运转噪 声声压级限值
本标准自实施之日起,JB5724一1991《木工镂酰机结构安全》作废
本标准的附录A是规范性附录
本标准的附录B是资料性附录
本标准由机械工业联合会提出
本标准由全国木工机床与刀具标准化技术委员会(SAC/TC84)归口
本标准由福州木工机床研究所负责起草
本标准主要起草人;郑宗鉴、郑莉、王喜宏
本标准首次发布
GB20006一2005 木工机床安全镂铁机 范围 本标准规定了木工镂钒机的安全技术要求
本标准适用于手动进给和机械进给的木工镂铁机(以下简称机床)
本标准不适用于手提式和台式木工镂钒机及CNC和Nc木工镂机
规范性引用文件 下列文件中的条款通过本标准的引用而成为本标准的条款
凡是注日期的引用文件,其随后所有 的修改单(不包括勘误的内容)或修订版均不适用于本标准,然而,鼓励根据本标准达成协议的各方研究 是否可使用这些文件的最新版本
凡是不注日期的引用文件,其最新版本适用于本标准
GB/T3770一1983木工机床噪声声功率级的测定 GB/T3767一1996声学声压法测定噪声源声功率级反射面上方近似自由场的工程法 GB/T3768一1996声学 声压法测定噪声源声功率级反射面上方采用包络测量表面的简易法 GB4208一1993外壳防护等级(IP代码 GB5013.1一1997额定电压450/750V及以下橡皮绝缘电缆第1部分:一般要求 额定电压450/750V及以下聚氯乙烯电缆第1部分 GB5023.11997 一般要求 GB5226.l1 2002 机械安全机械电气设备第1部分;通用技术条件(IEC60204-l:2000, IDT GB125572000木工机床安全通则 低压开关设备和控制设备 GB14048.42003 机电式接触器和电动机起动器 低压开关设备和控制设备第5-1部分;控制电路电器和开关元器件机电 GB14048.52001 式控制电路电器 GB/T15706.1一1995机械安全基本概念与设计通则第1部分;基本术语,方法学 GB/T15706.2一1995机械安全基本概念与设计通则第2部分;技术原则与规范 GB/T16755一1997机械安全安全标准的起草与表述规则 GB/T18831一2002机械安全带防护装置的联锁装置设计和选择原则 GB18955-2003木工刀具安全钒刀、圆锯片 JB6113一1992木工机用刀具安全技术条件 JB/T6359一1992木工镂机精度 sO3743-1l;1994声学噪声源的声功率级测定混响场中小的,可移动的声源工程法第1部 分;硬围墙的实验室的比较法
so3743-2:1994声学噪声源的声功率级测定混响场中小的、可移动的声源工程法第2部 分;专用混响室的方法 ISO3745;2003声学噪声源声功率级的测定消声室和半消声室的精密法 sO4871:1996声学机器与设备的噪声发射值的声明与检验 SO11202;1995声学机器与设备发射的噪声操作者位置和其他特定位置上声压级测定的简 易法工地简易法 SO11204:1995声学机器与设备发射的噪声操作者位置和其他特定位置上声压级测定的简 易法环境修正的方法
GB20006一2005 ISO/TR1l688-l:1995声学低噪声机械与设备的推荐设计方法第1部分;计划 EN982:1996机械安全流体动力系统和部件的安全要求液压装置 EN983;1996机械安全流动体力系统和部件的安全要求气动装置 术语和定义 以下术语和定义适用于本标准,推荐给于采用
-般术语和定义 3.1 镂铁机rotmngmaehine 是一种“C”型机身的机床,工件的眈削通过 -个装在工作台上方的刀具主轴,转速一般为8000r/min20000r/min
有的加工头可以 倾斜,但加工时是固定的 用于支承工件或仿形夹具的工作台,有的可倾斜和/或沿X.Y及乙方向移动和/或绕C轴 湖整; -有的刀具主轴通过手动或液压(气动)装置可作上、下移动
工件进给可以是手动或机械进给 3.1.2 直线加工straightwork 工件加工时,其一个面与工作台接触,另一面与导向板接触,加工从工件的一端开始,连续到另一端 见图1) 3.1.3 间断直线加工soppedstrulahtwk 工件长度上一部分的加工(见图2)
加工面 直线加工 加工面 图2间断直线加工 3.1.4 成型加工shapedwork 在一工件表面或边缘进行的曲线加工
注;这可通过将工件装在一夹具上来实现
夹具的底而是一模板
模板与刀具正下方的工作台中间的导向销紧贴
夹具与销接触并沿销移动
这样,照模板的形状,在工件上加工出相同的形状(见图3和图4)
GB20006一2005 在装有工件机械进给系统的机床上,模板置于夹具下方,夹具由驱动辗驱动作回转移动(见图5)
加工面 图3成型加工 工件 衬垫 刀具 夹具体 导向销 硬木支座 靠模或模板 图4成型加工(手动进给的机床
GB20006一2005 刀具 工件 挡块 底 模板 可移动外报轮 中心固定的轮 中心线 图5成型加工(机动进给机床 3.1.5 喉口尺寸throateapaeity 指主轴中心线与立柱之间的最小距离
3.1.6 手动进给handfeed 工件采用手动夹持和导向
手动进给包括使用手动操作的夹具,工件手动地置于或夹紧在该夹具 上或用手推动的移动工作台上 3.1.7 机械进给intergratedfeed 见GB12557一2000中3.5
3.1.8 上料loadingthemachine 见GB12557一2000中3.6
3.1.9 转速范围speedrange 刀具主轴或刀具额定最大运转速度与最小运转速度间的区间
3.1.10 抛射ejetin 见GB125572000中3.10
3.1.11 返弹kiekback 见GB12557一2000中3.11
3.1.12 止逆装置anti-kiekbackdeviee 用以降低工件、工件或机床的零部件返弹的可能性,或阻止其运动的装置
GB20006一2005 3.1.13 起动时间run-uptime 见GB125572000中3.13
3.1.14 惯性运动时间run-downtime 见GB125572000中3.14
3.1.15 可换主轴removablespindle 更换时不需拆卸主轴轴承的刀具主轴
3.1.16 机械致动机构machineactuator -种用以引起机械运动的动力机构见GB5226.12002中3.32)
3.1.17 保证书confirmationm 见GB125572000中3.15
3.1.18 转塔挡块revolvingstop 是一种调整装置,它固定在机头的可移动部件上
成批加工产品时,供以工作台作为基准调整饥削 深度用 3.1.19 可移动的机床transportablemachine 该机床是安置在地面上,使用时是静止的;它装有一个能使机床在场所之间移动的装置,例如轮子
3.2机床主要零部件术语 机床主要零部件的名称见表1和图6
表1单轴手动进给/机械进给镂铁机主要零部件名称 序号 称 英 文 名 称 中文名 刀具和/或工件的进给部分 feedofworkpieceandortools 自动进给装置 automaticfeedunite 工件的支承、夹紧和导向部分 workpiecesupport,elampandguide 2.1 工作台 table 2.2 导向板 fence 2.3 工作台套环 tablering 导向销 guidepin 2.4 夹具 2.5 jp 刀夹 tool-holders 加工头和刀具传动部分 workheadandtooldrives 主轴 spindle 4.l 操纵装置部分 controls 转速选择开关 speedselectswitch 工作台升降装置 5.2 tableriseandalladjustment
GB20006一2005 表1(续 文 名 称 英 文 名 称 序号 中 导向销提升杆 5.3 guidepinraiselever 加工头倾斜锁紧装置 5.4 lheadtiltlock 5.5 加工头升降操纵装置(气动 headcontrol(pneumatie 5.6 深度限位转塔 deptlhstopturret 安全装置(实例 safetydevices(example) 6.1 刀具防护装置 cutterguard spindlebrake 6.2 主轴制动器 吸尘管接头 exhaustoutlet 6.2 2.4 5.6 2.1 4.1 6.1 2.3 5.3 5.2 5.5 l,T 2.2 2.5 图6镂铁机实例
GB20006一2005 危险一览表 本一览表涉及了机床的所有危险 -对于重大危险,应规定安全要求和/或措施,或参照相关的B类标准; -对于非重大危险,例如一般的、次要的或从属的危险,应参照相关的A类标准,特别是 GB/T15706.1~15706.2. 表2中所列危险是根据GB/T16755一1997的附录A提出的
表2危险一览表 序号 符合本标准的条文 险 危 机械危险;如由机器或工件的下列要素引起的 形状 相对位置 质量和稳定性;(各零件的位能) 质量和速度各零件的动能); 机械强度不足; 由以下原因引起的位能积累;弹性零件(弹簧)或压力下的液体或 气体;真空 挤压危险 5.2.7 剪切危险 1.2 5.2.7 切割或切断危险 5 .2.7,5.2.4 1.3 . 缠绕危险 5.2.7 . 引人或卷人危险 5.2.7 冲击危险 不适合 刺伤或扎伤危险 .2.10 1.8 摩擦或磨损危险 不重要 . 高压流体喷射危险 不适合 1.10 机械或被加工的材料或工件)部件抛射危险 5.2.3,5.2.5,5.2.10 n 机械或机械零部件不稳定 5.2.l .12 与机械有关的滑倒,倾倒,跌倒危险 不适合 电气危险诸如下列因素引起的; 电接触(直接或间接 5.3,4 2 静电现象 不适合 热辐射或其他现象;如熔化粒子的喷射、短路,化学效应过载等 不适合 电气设备外部影响 5,3.12 热危险;由下列各因素引起的 人们可接触的火焰或爆炸及热鄙牺射的烧伤和烫伤 不适合 由于热或冷的工作环境对健康的影响 不适合 3.2 由噪声产生的危险导致, 听力损失等 5.3.2 干扰语言通讯,听觉信号等 不适合 由振动产生的危险 不适合 由辐射等产生的危险,尤其是由 不适合 6,l1 电弧 激光 不适合 6.2 6.3 电离辐射 不适合 用高频电磁场进行加工的机械 不适合 6
4
GB20006一2005 表2(续 序号 符合本标准的条文 临 由机械加工时,使用的或排出的材料和物质产生的危险,例如 由于接触或吸人有害的液体、气体、烟雾和灰尘导致的危险 5.3.3 7.2 火或爆炸危险 5.3.1 生物和微生物(病毒或细菌)危险 不适合 在设计中忽略人类工效学产生的危险(机械与人的特征和能否匹 配),例如 不利于健康的姿态或过分用力 5.1.2 不适当考虑人的手/手臂或脚/构造 不适合 8.2 8.3 忽略了使用个人防护装备 6.3 不适当的工作面照明 不适合 8.5 精神过分紧张或准备不足等 不适合 人的差错 6.3 各种危险的组合 不适合 0 由于能源故障,机械零件损坏或其他功能故障产生的危险;例如 10.1 能源故障(能源或控制电路 5.l.9 机械零件或流体意外抛射 10.2 5.2.5,5.2.10 控制系统的失效,失灵(意外起动,意外过流) 5.1.1,5.1.7 10.3 10,4 装配错误 6.3 10.5 机械翻倒意外失去稳定性 5.2. 由于防护措施中止(短时的)或防护措施设置不正确产生的危险, 例如: 11.1 5.2.7,5.2.8 各类防护装置 1.2 各类安全有关的(防护)装置 5.2.7.5.2.8 起动装置和停机装置 5.l.2 安全信号和信号装置 6.1,6.2 1.4 各类信息和报警装置 6.3 出 能源切断装置 5.3.16 n." 急停装置 5.1.5 工件的进给/取出装置 5.2.6 1.8 安全调整和/或维修的主要设备和附件 5,2.3.3 1.9 11.1o 气体等的排送设备 5.3.3.1 安全要求和/或措施 机床的安全除应符合本标准的规定,还应符合GB12557、GB/T15706.1和GB/T15706.2的 规定
5.1控制和指令装置 5.1.1控制系统的安全性和可靠性 对本标准而言,有关安全控制系统包括从最初的手动操纵器或位置传感器到最终的机械致动机构 或部件(例如电机)的输人点
机床的有关安全控制系统为 起动(见5.1.3); 正常停止(见5.1.4) 紧急停止(如果需要)(见5.2.3.1); 电动的主轴调整(见5.2.3.1,5.2.3.2);
GB20006一2005 主轴变速(如果速度选择是电动见5.1.7); 主轴的旋转方向(见5.2.3.4); -联锁(见5.2.10): 带防护锁定的联锁(见5.2.7.2); 夹紧压力指令(如果需要)(见5.2.10); 能源故障情况下的意外起动的防护(见GB/T15706.2和本标准5.1.9) -模式选择(如果需要)(见5.1.6); 制动(见5.2.4); 制动释放(见5.2.4). 这些控制系统应至少用经验证的元件和经验证的原则予以设计和制造
本标准中“经验证”的元件和原则是指 电气元器件应符合相应国家标准、行业标准的规定,包括下列元器件 a 强制切断的拉制开关(其用于联锁的防护装置中作为机械操作的位置传感器)相用于辅助 电路中的继电器应符合GB14048.5的规定 用于主电路上的电气机械式接触器和电动机起动器应符合GB14048.1的规定 -橡散绝缘电缆应符合GB5oa.1的熄定 通过定位(例如在接触床身内部)附加抵抗机械损坏防护的聚氯乙烯绝缘电缆应符合 GB5023.1的规定
b)在电的原则方面,它应符合GB5226.1-2002中9.4.2.1规定的前4种措施,电路应附加接 触
电子元件另行规定,不采用这原则
机械的零部件应符合GB/T15706.2一1995中3.5的规定
防护装置用的机械操作的位置开关应采用强制作用的模式,它的安排和连接以及凸轮设计和 安装应符合GB/T18831一2002中5.2和5.3的规定
带防护锁的联锁装置,至少应符合GB/T188312002表1中的三态联锁
e 气动和液压元器件及系统应分别符合EN983和EN982的规定
f 检验方法;检验相应图样和/或电路图;在机床上进行检验;电气元器件要求出具其制造者保证书证 明其符合相应标准
5.1.2操纵器的位置 用于机床起动,正常停止、紧急停止(如果需要、主轴调整、旋转方向选择和模式选择(如果需要)电 气控制的操作件一般应位于 工作台前端边缘50nmm以下,离地高度不低于600mnm(见图7); 或,图7中固定的悬挂式操作面板的前面
机械的操纵器不应安装在机床的背面
检验方法;检查有关图样,在机床上作检验
5.1.3起动 见GB5226.1一2002中9.2.5.2
对本标准而言,“安全防护装置就位并起作用"”是通过安装5.2.7.2中规定的联锁装置来实现
而 “运转”是指刀具主轴的旋转和/或机动调整
GB5226.1一2002中9.2.5.2叙述的例外情况与本标准无关
只有加工头处于停止位置时,有意操作一单独的操纵器,才能起动主轴
在装有真空夹紧装置的机床上,只有当控制点上真空已获得气压的情况下才能起动机械进给(见 5. 2.10和6.3) 检验方法;检查相应图样和/或电路图,在机床上作功能试验等检验
GB20006一2005 尺寸单位,mm 8 工作台中线 操作而板中线 图7操纵器的位置 5.1.4正常停止 一般要求 5.1.4.1 机床应装有一个停止操纵器,当它被操作时,应能切断所有的机械致动机构的动力
对装有制动器 的机床,还应能使制动器起作用
装有机械制动器的机床,机床的正常停止控制系统应符合GB5226.1-2002中9.2.2的0类停止 的规定
若机床采用电气制动器并带或不带机械进给装置和/或真空夹紧装置,则正常停止系统应按 GB5226.12002中9.2.2规定的1类停止
采用1类停止的机床,正常停止的顺序应是 使机床加工头停止运动 切断机械进给装置机械致动机构的动力源,(如果装有机械进给装置 -切断除工件夹紧装置如果有)以外的所有机械致动机构的动力源并使制动器起作用, 当完成制动后(例如借助于延时器),切断到制动装置和工件夹紧装置(如果有)的动力 正常停止顺序应通过控制电路的结构来实现
如果采用一延时器,则延时至少等于最小的制动时 间
延时器应是固定的,或它的调整装置应是密封的
5.1.4.2附加停止 通过1类停止(按GB5226.1一2002中9.2.2)的各操纵器应能分别停止主轴运转,真空夹紧装置 1o
GB20006一2005 的电机和机械进给装置(如果有. 操作机械进给停止操纵器时不应引起加工头的运动;停止主轴驱动电机也应停止机械进给的传动
检验方法;检查相应图样(包括电路图),在机床上作功能试验等检验
5.1.5急停 机械致动机构(电气的、气动的,液压的或它们的一个组合)多于1个的机床,应装有一个急停控制
但带1个电机和加工头机动的(气动或液压)定位只有一个的机床除外 当操作急停操纵器时应能停止所有的机械制动机构(见GB5226.1一2002中3.3.6),若机床装有 -个机械的制动器,则急停控制系统应按GB5226.1一2002中9.2.2的0类和10.7中除10.7.4以外 的所有规定
若机床装有一个电气的制动器,则急停系统应按GB5226.1一2002中9.2.2的1类和 9.2.5.4的规定
急停操纵器的位置见5.1.2 正常停止顺序见5.1.4 在所有电机停止运动前,急停作用不应导致工件松开
这些要求应通过控制电路的结构来实现
延时至少等于最小制动时间
延时器应是可调的或其调 整装置应是密封的
5.1.6模式选择 5.1.3和5.1.4中规定的起动和正常停止的要求应由一个模式选择开关在以下各项中选择来 完成 主轴旋转 主轴旋转加真空夹紧; 主轴旋转加机械进给 主轴旋转加机械进给加真空夹紧
有机械进给系统的机床,应装有一个模式选择开关,以便调整
在调整模式中应不能起动主轴传动电机,但能手动旋转主轴作调整
除主轴旋转外的所有运动只 能通过操作自复位的开关来实现
检验方法;检查相应图样(包括电路图),在机床上作功能试验等检验
5.1.7转速改变 在装有主轴无级变速自动控制装置(例如变频器)的机床上,该装置应保证主轴实际转速超过所选 择的转速不大于后者的10%(例如借助辅助电路) 5.1.8机械进给 在装有机械进给系统的机床上,刀具主轴运转的接通应不迟于进给系统的接通;进给系统切断时主 轴应保持在加工位置上
检验方法;检查相应图样(包括电路图),在机床上作相应功能试验等检验
5.1.9动力源故障 对于用电驱动的机床,在电源中断的情况下,电源电压复原后,自动再起动的防护按GB5226.! 2002中7.5的规定 装有工件机动夹紧装置(气动的,液压的,真空)的机床,在动力源故障情况下,仍能保持夹紧,例如 通过使用一单向阀来防护 加工头能作机动调整的机床,应装有一个装置,在动力源故障情况下它能使加工头保持在适当的位 置上
检验方法;检查相应图样(包括电路图),在机床上作相应功能试验等检验
控制电路故障 5.1. 0 见5.1.1 11
GB20006一2005 5.2机械危险的防护 5.2.1稳定性 机床的结构应具备将其安装在地面、台面或其他稳定结构上的措施,例如在机床底座上有安装孔
工件的稳定性见6.3
检验方法;检查相应图样或在机床上作检验
5.2.2运转中的断裂危险 见GB/T15706.2一1995中3.3,此外,安全防护装置见5.2.8
刀具的安全要求按5.2.3
5.2.3刀夹和刀具的结构 5.2.3.1刀具的要求 按6.3和GB18955和JB61l3的要求
5.2.3.2主轴 所有主轴应按JB/T6359一1992中(G5的规定制造
5.2.3.2.1高度调整 高度调整控制装置一起动主轴部件的升起运动,主轴部件就运动到安全位置并通过机械作用停止 在该位置上
只有通过-有意的操作才能下降主轴部件 加工头的工作位置应能调整
例如,向转塔挡块下移
转塔挡块应被保持在它的选择位置,例如通 过弹簧和滚珠机构
机床应装有一个指示器,指示加工头垂直移动的增量
检验方法;检查相应图样(包括电路图),在机床上进行功能试验等检验
5.2.3.2.2倾斜调整 若主轴是可倾斜的,则机床上应装有一个指示器,指示主轴相对工作台倾斜的角度
倾斜调整装置 应能自锁
刀具主轴置于一垂直位置上,在它的外露端沿水平方向施加一个300N的力,刀具主轴的倾斜变化 不应超过1"
检验方法;检查相应图样,在机床上作测量等检验
5.2.3.3主轴的锁定 若为了更换刀具等需要主轴保持固定,则应提供主轴锁定装置,例如双头扳手,或由操作者插人主 轴的锁定棒
锁定棒可以连接在机床上的,也可以不与机床连接,其直径应不小于8mm,用抗拉强度 不低于350N/mm的钢制造
当主轴电机意外接通时,锁定棒应能防止主轴旋转
检验方法;检查相应图样,测量、检验、检查锁定棒制造者的保证书,在机床上作功能试验
因此,应 验证由于主轴锁定装置的插人,主轴传动电机接通后,主轴仍保持静止
5.2.3.4旋转方向 单向旋转的机床刀具主轴,应是顺时针方向旋转(从上往下看)
双向旋转的机床刀具主轴,逆时针方向旋转应符合下列规定 a 机床的正常操作位置旁应装有一个主轴旋转方向选择装置,它的操纵器的运动方向应与作用 方向一致 当选择了逆时针的旋转方向时,一个可视警告装置应通知机床操作者;选择了逆时针的旋转 方向
警告装置的颜色应为黄色、允许用声响警告装置代替可视警告装置; 主轴一停止逆时针方向旋转,旋转方向选择装置应自动返回到 顺时针方向,然后: 通过一个闭合装置将选择装置保持在顺时针旋转方向位置; 而且若要选择逆时针旋转方向,只能通过手动超越闭合装置来实现
22 或一个中间位置(在该位置上闭锁装置是有效的),若要进一步选择任一旋转方向,还应手 12
GB20006一2005 动超越闭锁装置
d 操作旋转方向选择装置不应引起主轴起动
主轴的结构应确保无论在何种旋转方向下,起动、切削和制动中刀具或可换主轴不会松脱
检验方法:检查相应图样(包括电路图,在机床上进行相应功能试验等检验
5.2.4制动 5.2.4.1 一般要求 无机械进给装置和真空夹紧装置的机床可装有机械的制动器
电气的制动器只能采用直流电注人
主轴制动的惯性运转时间超过10s的机床,应装有一个自动的制动器 制动时间应: -小于10s; 或,起动时间超过10s的机床,应小于起动时间,但不应超过30s 检验方法:有关不制动的惯性运动时间,起动时间和制动时间的确定见下列相应检验
5.2.4.2检验条件 主轴装置应按制造者的使用说明书安装(例如皮带的张紧)
选择速度和刀具时,应选择能产生机 床设计允许的最大动能的状态
检验前,机床应空运转不少于15nmin,使主轴装置升温
验证主轴实 际速度偏差应在额定速度的10%范围内
当试验带有手动星三角起动的装置时,应阅读制造者的使用 说明书
速度测量仪器的精度不应低于全读数的士1%
时间测量仪器的精度不应低于士0.1s 5.2.4.3检验 5.2.4.3.1不制动的惯性运转时间 按以下方法测量不制动的惯性运动时间 a)切断主轴驱动电机的动力,测量其不制动的惯性运转时间 bb 重新起动主轴,使其达到预定的速度; 重复步骤a)和b)两次
c 上述3次测量的平均值为不制动的惯性运转时间
5.2.4.3.2起动时间 按以下方法测量起动时间 a)切断主轴驱动电机的动力,使主轴完全停止旋转 重新起动主轴测量起动时间 bb 重复步骤a)和b)两次
e 上述3次测量的平均值为主轴起动时间
5.2.4.3.3制动时间 按以下方法测量制动时间 切断主轴驱动电机的动力,对主轴进行制动
测量制动时间 a 主轴保持静止1min 重新起动主轴运转1min d重复步骤a)和b)至c)9次
上述十次测量的平均值为机床制动的时间
5.2.4.4制动释放 在装有一个控制器用以释放主轴制动器,以便转动调整刀具的场合,只有当主轴完全停止运转才能 释放制动器
例如通过在操作停止操纵器和制动释放之间的延时来实现
13
GB20006一2005 检验方法:检查相应图样,在机床上进行功能试验
5.2.5将抛射的可能性和影响降低到最小的装置 5.2.7.1中要求的防护装置应向工件上施加一个50N~150N的作用力F见图8). 50mm G=100N F力的测量点 用弹黄祥在垂直f工作台面方向刻盘力r 最高工作位置 最低工作位置 图8刀具的防护 在有导向板的机床上,应对止逆装置(例如导向板两端的可调挡块,见5.2.10)的固定(例如固定孔 或固定槽)进行防护
在返弹方向上,止逆装置承受300N静载荷,变形不应超过2m 丁形槽应平行于进给方向
固定孔的直径不应超过12mm
检验方法:检查相应图样,进行测量等检验
5.2.6工件的支承和导向 5.2.6.1 一般要求 在主轴中心线每一侧的工作台尺寸不应小于喉口尺寸的60%
工作台面从主轴中心线向前延续的尺寸为不应小于喉口尺寸的60%或不小于300mm(无论何种 情况,该数值均为最小值)
在工作台可倾斜的机床上,工作台面相对水平面倾斜角度不应大于45°"并应有可靠的倾斜锁紧措 施;5.2.6.2中要求的导向板应能安装在倾斜后工作台上处于低位置的那一边缘上,并应能平行于这 较低的边向主轴做向前、离开平行的调整 从工作位置上看,机床工作台在主轴中心线的每一侧应有固定延伸工作台措施(见6.3) 对于结构上能装有机械进给的机床,若工作台孔的直径大于等于20mm,应配备有一个工作台孔 的衬套,当不用机械进给装置时,可以此堵住工作台的孔
工作台的升降机构应有可靠的锁紧措施
秘 l4
GB20006一2005 动工作台应有防止脱落的措施
检验方法:检查相应图样;在机床上作测量、功能试验等检验;检查使用说明书
5.2.6.2直线加工的工件导向 机床上应有固定导向板的措施(例如槽)
装有一个导向板的机床应符合下列要求 不需借助于工具将导向板固定到工作台上; -导向板应能相对于工作台的前边缘作向前和离开调整 -导向板或其靠近刀具的导向面应用轻金属、塑料或木材制造,使得若刀具与其接触,不会产生 危险(例如刀具破裂),并应使环形防护装置能压紧工件厚度的最小值为8n mm; -导向板或导向板导向面的长度应与机床最大加工范围相适应,但不应小于500mm
其高度 工作台可倾斜的机床,导向板的高度不应小于110mm(中间部分除外),以 不应小于65r mm
便压靠溥的工件 机床上应装有将工件压向导向板的压紧装置
该装置应能安装不同尺寸的压紧器(见图9. 检验方法;检查相应图样,在机床上作目测,测量和功能试验等检验 侧面压紧器 导向板 工件 工作台 导向板 上命 图9小断面的工件 5.2.6.3成型加工工件的导向 所有机床均应能在工作台中安装导向销
15
GB20006一2005 导向销及其安装布局应符合图10的要求
尺寸单位;mnm 昌 导向销头部 工作台面 导向销体 12min 图10导向销 检验方法检查相应图样和材料制造者保证书
5.2.7移动零部件危险的防护 5.2.7.1刀具的防护 5.2.7.1.1 般要求 应提供一个自关闭可调防护装置,用以在该防护装置与工件接触前,防止从上部和在防护装置的各 位置上的任何水平方向的各侧进人刀具(见图8)
5.2.7.1 环形防护装置 环形防护装置应符合下列要求 环形防护装置的内径应能安装机床设计的最大直径的刀具
若刀具最大直径大于80mm,则 aa 机床应提供至少2种不同内径的环形防护装置; b)环形防护装置的下表面与工作台面的平行度允差在100mm长度上为0.5mm 环形防护装置应联结到一个吸尘管接头上
该管接头固定在机床的固定件上 c 检验方法;检查相应图样,使用信息,在机床上作测量、功能试验等检验
5.2.7.1.3环形防护装置的支承 环形防护装置的支承应: 设计成使环形防护装置能与刀架一起自动地移动; a b 设计成无论工作台处于何位置,环形防护装置的下表面均能调整到与工作台面平行; 设计成环形防护装置的位置调整能考虑到机床设计允许的最大长度的刀具; 无需借助工具进行调整 d 刚度应达到按图8所示,在100N的力G作用下位移不超过3nm mm 使刀具更换时无需拆卸除环形防护装置外的其他零部件 检验方法;检查相应图样,使用说明书
在机床上进行测量、刚度试验和功能试验 16
GB20006一2005 5.2.7.1.4直线加工的防护装置 应在导向板前面固定一个附加装置,以此确保加工中工件靠紧在导向板上,并防止进人刀具 见5.2.6和附录B) 检验方法:检查相应图样
在机床上作功能试验等检验
5.2.7.2传动的防护 刀具和机械进给等的传动机构应用固定式防护装置防护
在需进人传动机构进行维修或调整的场 合,应采用移动式防护装置来防护,其防护要求按GB12557一2000中5.3.7.3的规定 检验方法:检查相应图样(包括电路图),在机床上作功能试验等检验 5.2.8安全防护装置特性 防护装置应采用下列材料之一制造: 钢抗拉强度不小于350N/mm',壁厚不小于2 mm a bb 轻金属;抗拉强度不小于185N/mm',壁厚不小于5mm; 聚碳酸脂;壁厚不小于6mm;或冲击强度大于等于6m厚的聚碳酸脂的其他塑性材料; c 铸铁;抗拉强度不小于350N/mm d ,壁厚不小于2mm
检验方法;检查相应图样,测量结果、材料制造商的保证书;在机床上作检验 5.2.g自动化和机械化 不适用 5.2.10夹紧装置 在采用机动夹紧的机床上,应按下列要求对轧伤危险进行防护 采用两步夹紧;由最大夹紧力产生的夹紧效果在1、内不超过150N;夹紧表面应大于 a 60mm×60mm; 或采用手动调整装置将夹紧装置与工件的间隙减少到不大于6mm,以及行程的最大值为 b 10mm; 或夹紧速度限制到不大于10mm/s; 或通过固定在夹紧装置上的防护装置来防护,将工件与防护装置之间的间隙减小到不大于 d mm,夹紧装置延伸到防护装置外的最大值不应超过6mm
6 气动夹紧和液压夹紧还应分别按EN983及EN982的要求
真空夹紧装置应与主轴旋转及机械进给联锁(见5.1.3,5.1.4和5.1.6)
在装有真空夹紧装置的机床上,应在接近夹紧工作台处固定一个传感器,它能探测出0.75×机床 设计规定的额定压力
主轴运转期间,只有当刀架处于停止位置上及机械进给(如果有)停止时,真空夹紧装置才能释放
检验方法;检查相应图样(包括电路图),在机床上作测量和功能试验等检验
5.3非机械危险的检验 5.3.1火和爆炸 应满足5.3.3和5.3.4的要求
以避免和防护火和爆炸的危险
5.3.2噪声 5.3.2.1设计阶段的降噪 设计机床时,应考虑GB12557一2000的附录B和ISO/TR11688-1中在噪声源方面控制噪声的信 息和技术测量
5.3.2.2噪声测量 5. .3.2.2.1空载噪声声压级限值及测量 机床在空运转条件下,测定出的机床最大噪声声压级;主轴转速大于等于12500r/min的机床不应 超过85dBA);主轴转速小于12500r/min的机床不应超过83dBA. 17
GB20006一2005 测量噪声时机床的工作(运转)条件按附录A的规定
测量方法按GB12557一2000中5.4.2.2.2的规定
但环境或修正系数K或局部环境修正系数 K;应小于等于1dB 局部环境修正系数K;应按IsO11204:1995附录A中的A.2计算,并参照GB/T3768,而不是 1SO11202:1995附录A给出的方法
当使用ISO3743-1,ISO3743-2,GB/T3767测量时,也可按上述 相应测量标准计算
.3.2.2.2噪声声功率级的测定 5. 在本标准实施2年之内,应进行机床噪声声功率级的测定
测出的机床噪声声功率级连同工作(运 转)条件及遵照的测定方法应记人机床的使用说明书
测定方法按GB125572000中5.4.2.2.2和本标准附录A的规定
5.3.2.3声明 见6.3. 5.3.3木屑、粉尘和有害气体的排放 控制措施:应采取措施从机床中吸取出粉尘和木屑,或是采用整体的吸收和采集系统;或是在机床 上设置有吸尘口,以便与单独的吸尘系统相连接 主轴双方向旋转的机床,木屑和粉尘的吸收系统在主轴两个旋转方向下均应有相同的效率
当没有连接吸尘系统时,穿过任何吸尘管接头均不可能接触刀具
注;为了保证木屑和粉尘从其原始点被输送到收集系统,建议吸尘罩、导管、挡板的结构基于抽出的气体在导管中的 速度为20m/s(对于含水率小于等于18%的木屑)和28m/s(对于含水率大于18%的木屑)
检验方法;检查相应图样,在机床上作检验
5.3.4电气设备 GB5226.1的要求是适用的,除非本标准中另有规定
尤其是电击的防护要求应按GB5226.1 2002第6章,短路保护和过载保护应按GB5226.l一2002第7章的规定
保护接地应按GB5226.1 2002第8章的规定
控制装置的外壳和电动机等防护等级应符合GB4208中IP54
检验方法;检查相应图样(包括电路图、制造者的保证书、在机床上作检查以及按GB5226.1作相 应检验
5.3.5人类工效学和安全搬运的要求 机床人类工效学和安全搬运要求应符合GB12557一2000中5.4.5和本标准5.1.2和6.3的规定
5.3.6照明 不适合 5.3.7气动装置 按EN983的规定
5.3.8液压装置 按EN982的规定
5.3.9热危险 不适合
5.3.10危险材料 按5.3.3的规定 5.3.11振动 不适合 5.3.12辐射 不适合
5.3.13激光 不适合
18
GB20006一2005 5.3.14静电 不适合 5.3.15装配误差 按6.3的规定
5.3.16能量输送的切断 按GB12557一2000中5.2.1的规定
电源的切断开关应按GB5226.1一2002中5.3的规定
若机床装有直流电的制动器,则总开关应带有一个锁定装置,只有当锁定装置脱开后总开关才能切 断
否则总开关不应设置在机床上起动和停止操纵器的同一边,或操纵台上起动和停止操纵器的同 -边
气动系统的切断装置上应配备一个将切断装置锁定在断开状态用的装置,例如用一挂锁
若气动 的动力鄙只用于火紧,朋气动火紧装置的切断可通过切断一个快速作用的离合器来实现(见EN983) 无需锁定
若机床上装有液压装置或气动装置,则电气的切断装置应也能切断液压装置或气动装置的传动电 机,并从蓄液器(如果安装有)中卸去残余的液压压力
若卸去残余的液压或气动的压力会使机床的零部件运动,那么应将压力保持在系统中,以防止产生 上述运动,应通过有意操作一个单独的开关才能卸去压力
在需存储残余能量的场合,例如用一存储器或管道,则应提供卸下残余压力的措施,例如采用一个 阀门
不应采用断开管接头的方法,实现卸下残余压力
检验方法;检查相应图样(包括电路图),在机床上作功能试验等检验
5.3.17维修 机床维修方面的有关要求按GB125572000第6章的规定
应提供GB/T15706.2一1995中5.5.le)中要求的维修信息
检验方法;检查相应图样,使用说明书;在机床上作功能试验等检验
使用信息 警告装置 见GB/T15706.21995第5章、本标准的附录B和5.2.3.4b)以及GB18995
标志 若机床上装有气动装置,而气动的能量不是由电气的总开关切断,则应在该电源切断总开关的附近 设置一个永久性的警告标牌,在上面写着;气动能量未切断
机床上应制有对应于一具体直径和切削速度的最佳速度图表,当操作者改变主轴速度时,其应清晰 可见
机床的标志还应符合GB12557一2000中7.2的规定
检验方法;检查相应图样;在机床上的检查
6.3使用说明书 按GB12557一2000中7.3的规定,至少应包括下列内容: 遗留风险的警告; a b 推荐的安全工作方法(见附录B); 用于本机床的刀具的范围、型式和尺寸,包括必要的夹紧长度和必要的平衡要求等; c e 为了降低返弹风险,切削速度应大于35ms'
但不应超过80ms'以降低损坏的风险; 因增加真空夹紧装置而对机床所做的任何改变,均应符合5.1.1的规定; 19
GB20006一2005 装有静压的刀具夹紧装置的机床,只能使用带有附加的机械装置的刀具夹紧装置,该附加装 s 置能防护因静压系统泄漏导致的刀具松脱 hh 必要的夹紧压力的信息(例如装有真空夹紧装置的机床上,真空和工件最小夹紧表面); 使用指南,包括耳朵和眼睛的人体个人防护器的使用;水材的种类和最小工件尺寸的建议, 环形防护装置的使用和内径 k 压紧装置的调整方法和压紧器的固定方法 止逆装置例如端部挡块安装到工作台或导向板上的方法; 延伸工作台的固定方法; m 由待加工工件确定的夹具的设计保证安全加工应考虑的主要因素是;工件的精确定位,可靠 夹紧方法和可靠的手持方法(对于手动进给工件的夹具)
夹具的导销应有足够的强度并具 有预定目的的结构 按5.3.2.2规定的测量方法确定的机床气动力噪声功率级的声明(按GB12557一2000中7.3 第1,2),3)项的要求》雕声声明中应附有所采用的测放方法和检验时机床的工作(运转)茶 件及相应的不确定度K(用双数字声明的形式,定义在1so4871中)
不确定度K的数值(规 定)如下 4dB当使用GB/T3768和Iso11202时 2dB当使用GB/T3767、GB/T3770.,Iso3743-1或1s03743-2时 1dB当使用Iso3745时
举例如下 噪声声功率级Lw=93dB(测量值) 不确定度K=4dB 测量方法按GB/T3768, 如果要核查噪声声明中放射值精度,则应采用与声明中的测定相同的方法和工作(运转)条件
声明应附下列说明“所提供的数值只是放射值,不是必须的安全数值
尽管放射值和暴露值 之间有一定的关系,但它不能可靠地用以确定是否需进一步的防护措施
影响实际工作力暴 露值的因素包括;工作间的特性,其他噪声源等
例如机床的数量和其他的邻近加工
但是这 些信息能使机床使用者较好地进行伤害和风险的评价
” 安装到机床上的吸尘装置的有关信息 -风量,m'h; 各连接管的压降(建议); 吸尘管中建议的空气速度,ms 各吸尘管接头的断面尺寸和结构细节(建议)
安装和维修的要求,包括要检验的装置(尤其是机械制动器)的检验频次和检验方法的明细表
20
GB20006一2005 附录A 规范性附录 噪声测量时机床的工作(运转)条件 一般要求 A.1 本附录规定了噪声测量时机床的工作(运转)条件
为了在机床的操作者位置测量声压级以及测定机床的声功率级,规定了传声器的位置(见图A.1 本标准的条件应尽量严格遵守
如果存在特殊情况,需与标准条件有偏差,应将测量时的实际条件 记录在表A.1中的“在允许范围内选择的条件或与标准条件(偏差)”栏中
噪声测定中应安装和使用强制性和标准的安全附件
记录工作(运转)条件信息的数据单见表A.1
本附录也可用于与本机床结构和功能类似的专用机床的噪声测量
尺寸:mm 操作者传声器位置 基准体 满服表街 oy 传声器位置
图A.1测定机床噪声功率级的测量表面和传声器位置 21
GB20006一2005 噪声测量 A
2 机床应在下列条件下进行试验: 按本附录规定的工作(运转)安排及刀具和切削参数进行机床的空运转噪声检验; a b)按本附录规定进行机床负载噪声检验时,以至少3次测量的平均值作为测量结果
在机床工 作循环的起始阶段,由于试件进人刀具,可能会产生较高的噪声级,这与进给速度有关
在手 动进给的机床上进给速度难以控制,因此,在测量时运转循环中这一部分的测量不应计人 检验时操作者的传声器位置(见图A.l); 离地面高度为1.5m:; 22 在包含工作台的前边缘的平面上的工作台的中间位置
注:推荐采用积分式声级计测量
A.3机床噪声测量数据单 机床的噪声测量数据单见表A.1
22
GB20006一2005 表A.1机床噪声测量数据单 机床数据 机床制造者 机床型号 制造日期 系列号 机床外形尺寸" 长度 宽度 高度 mmm mm mm 额定转迷 电机max 主轴 r/min r/min min: r/min 口附装的变频器 口单独的变频器 口皮带传动 备注/说明 机床的安装 按机床制造者使用说明书安装机床 是 口 否 按制造者的技术条件安装机床和吸尘器 是 口 否 机床安装在隔振体上 是 否 机床装在单独的隔声罩中 是 否 机床装有整体的隔声罩 是 口 否 口 机床装有消音罩 是 否 其他的噪声控制措施 是 否
GB20006一2005 表A.1(续 试验运转条件 在允许范围内选择的条件 镂恍刨花板边缘 单位 标准条件 或与标准条件偏差 运转安排 锁铁刀 刨花板 刀具和切削数据 刀具型式;带柄镂钒刀 主轴速度 18000" r/min 切削圆直径 mm 25 切削速度 m/s 刀片数量 切削刀片长度 mm 4050 切削深度a mmm 进给速度 m/min 6士2 切削原理
逆削 凸出机床而不影响噪声传播的零件如手轮、手柄等)可忽略不计
主轴速度应尽量接近18000r/nmin
24
GB20006一2005 表A.1(续 试验材料 三层刨花板 材料: 含水率 6%一10% 板厚度 l6mm 板长度: 600mm800mm 板宽度 600mm一800mm,加工到最终最小宽度为150mm. 无 预加工 被检验机床的照片或安装图 检验实验室 公司/研究所 地址 25
GB20006一2005 附录B (资料性附录 安全工作方法 B.1 -般要求 下列建议的内容作为机床安全使用的实例
B.2操作者的培训 所有操作者均必须经过机床的使用、调整和操作方面足够的培训,包括下列内容 机床的安装和运转原则,包括工件的夹紧和导向装置的正确使用和调整以及每一操作刀具的 a 选择; 切削时工件的安全操纵 b 正确使用夹具,模板、延伸工作台和端部挡块等安全附件 c d 防护耳朵和眼睛的个人的人体防护器的使用
B.3稳定性 应将机床可靠地安装在地面或稳定的结构上
B.4机床的安装和调整 机床安装前应 确保所使用的刀具是锐利的,按刀具制造者的建议进行正确选择、维护和调整; a 切断机床的动力源 b 使用导向销的头部直径与刀具直径一致; c d 使用的刀具符合GB18955的规定; 注意刀具的维护; 使用切实可行的专门的装置例如调整样规
B.5工件的导向 工件的导向应; 直线加工时应使用导向板,以提供足够的工件导向; a b)使用辅助导向板,以便将刀具与导向板面之间的间隙减到最小; 采用机动进给装置(在任何可能的场合) d)对着导向板手动进给工件,使用一辅助进给用推棒和防护装置; 用辗子支架或延伸工作台支承长的工件
B.6旋转方向和速度选择 B.6.1旋转方向 最重要的是将刀具装在机床上按正确的方向旋转以及工件逆着主轴旋转方向进给
B.6.2速度选择 重要的是选择的转速与所采用的刀具相适应
26