GB/T23570-2009
金属切削机床焊接件通用技术条件
Weldingpartsformetalcuttingmachines-Generalspecifications
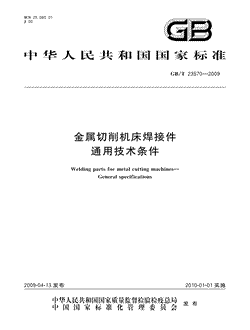
- 中国标准分类号(CCS)J50
- 国际标准分类号(ICS)25.080.01
- 实施日期2010-01-01
- 文件格式PDF
- 文本页数8页
- 文件大小533.46KB
以图片形式预览金属切削机床焊接件通用技术条件
金属切削机床焊接件通用技术条件
国家标准 GB/T23570一2009 金属切削机床焊接件 通用技术条件 weldingpartsfo”metaleuttingmachines Generalspeeificeations 2009-04-13发布 2010-01-01实施 国家质量监督检验检疫总局 发布 国家标准化管蹬委员会国家标准
GB/T23570一2009 前 言 本标准由机械工业联合会提出
本标准由全国金属切削机床标准化技术委员会(SAC/TC22)归口 本标准起草单位;沈阳机床(集团)有限责任公司.北京机床研究所
本标准主要起草人:王兴海、李祥文、张维
本标准为首次发布
GB/T23570一2009 金属切削机床焊接件 通用技术条件 范围 本标准规定了金属切削机床(以下简称机床)焊接零部件的制造和验收的基本要求
本标准适用于由碳素结构钢、低合金结构钢和不锈钢采用手工电弧焊或气体保护焊等方法制造的 金属切削机床焊接件
规范性引用文件 下列文件中的条款通过本标准的引用而成为本标准的条款
凡是注日期的引用文件,其随后所有 的修改单(不包括勘误的内容)或修订版均不适用于本标准,然而,鼓励根据本标准达成协议的各方研究 是否可使用这些文件的最新版本
凡是不注日期的引用文件,其最新版本适用于本标准
GB/T985.1气焊,焊条电弧焊、气体保护焊和高能束焊的推荐坡口GB/T985.1一2008 ISO9692-1:2003,MOD (GB/T2649焊接接头机械性能试验取样方法 GB/T2650焊接接头冲击试验方法(GB/T2650一2008,ISO9016;2001,IDT) GB/T2651焊接接头拉伸试验方法(GB/T2651一2008,IsO4136;2001,IDT) GB/T2653焊接接头弯曲试验方法(GB/T2653一2008,ISO5173;2000,IDT) GB/T2654焊接接头硬度试验方法(GB/T2654一2008,IsO9015-1:2001,IDT GB/T3323金属熔化焊焊接接头射线照相(GB/T33232005,EN1435;1997,MOD) 材料 3.1焊接母材的钢号、规格、机械性能等应符合有关标准的规定,并应满足图样或工艺文件的要求
焊接材料应符合工艺文件的规定,并应按相应标准检验合格后方可使用
零件的下料与成形 火焰切割下料的尺寸偏差应符合表1的规定
表 单位为毫米 用于不需切削加工 用于需切削加工 板材厚度 下料尺寸 二20 >2040 >4060 20 >20一4o >406o 极限偏差 500 士1.0 士1.5 士2.0 士2.0 士2.5 士3.0 士1.5 士2.0 >5001000 士2.5 土3.0 土3.5 士4.0 0001600 士1. .8 士2.3 士2.8 士3.7 士4.2 士4.8 6002500 士2.2 士2." 士3.2 士4.5 士5.0 士5.5 >2500~4000 士2.7 士3.2 士3.7 士5.4 士5.9 士6.4 >40006300 士3.3 士3.8 士4.3 士6.6 士7.1 士7.8 >6300 土4.0 士4!.5 士5.0 士8.0 士8.5 士9.0
GB/T23570一2009 4.2激光切割机下料尺寸偏差为士0.2 mm 4.3剪切下料的尺寸偏差应符合表2的规定
表2 单位为毫米 用于不需切削加工 用于需切削加工 板材厚度 下料尺寸 38 38 >814 >8l4 极限偏差 500 士0,7 士1.0 士1,4 士1.4 士1.7" 士2.1 5001000 士1.0 士1.3 士l.7 士2.0 士2.3 土2.7 >1000~1600 士1. 2 士1.5 士1.9 士2.4 士2.7 士3.1 600~2500 士1.4 土1.7 士2.1 士2.8 士3.1 士3.5 >2500~4000 士1.6 士l.9 士2.3 士3.3 士3.6 士4.0 数控等离子切割下料尺寸偏差为士0.2mm;手工等离子切割下料尺寸偏差应符合表3的规定
4 单位为毫米 板材厚度 下料尺寸 68 >23 3一4 >5一6 >810>l0~l" 极限偏差 <500 士0.2 士0.5 土1.0 土2.0 士2.5 士3.0 士3.5 士4.0 士4.5 5001000 士0,5 士1.0 士1.5 士2.5 士3.0 士3.5 士4.0 士4.5 士5.5 士2.5 士5.5 士7.o 10001600 士1.0 士2.0 士3.5 士4.0 士4.5 士5.0 600一2500 士1.5 士3.0 士3.5 士4.5 士5.0 士5.5 士6.0 士6.5 士8.0 >25004000 士2.0 士5,0 士5,5 士3.5 士4,0 士6.0 士6.5 士7.0 士8,5 零件的角度下料,其偏差由相应的尺寸偏差确定
,在全长范围内的公差应符合表4的 板材零件的平面度公差在任意1000mm长度内为2! mm, 规定
表4 单位为毫米 板材厚度 >314 >l4 板材长边尺寸 平面度公差 >10001600 2.5 2.0 30 >l6002500 4.0 3.0 2.5 >25004000 5.0 4.0 3.0 5.o 40006300 6.0 4.0 >6300 6.o 7.0 5.0 板材零件棱边在板材平面内相互间的平行度、垂直度和直线度公差应符合表5的规定
GB/T23570一2009 表5 单位为毫米 平行度 垂直度 直线度 下料尺寸 公差 <50o 1.5 1.0 2.0 >5001000 2.5 2.0 1.2 2.3 1000一1600 2.8 1.4 >1600~2500 3.2 2.7 1.6 >25004000 3.7 3.2 1.8 型材零件的纵向直线度公差、各垂直面相互间的垂直度公差应符合表6的规定
表6 单位为毫米 <500 >500~1000 >l000~1600 >2500~4000 下料尺寸 >1600一2500 直线度公差 1.0 1.5 2.o 3.0 4.0 垂直度公差 4.9型材零件的扭曲量,当长度小于或等于2000mm时不得超过1mm,长度大于2000mm时不得 超过31 mm 4.10火焰切割面对板材、型材平面的垂直度公差应符合表7的规定
表 单位为毫米 7 板材厚度 型材高度(边宽 垂直度公差 S50 1.0 8 -20 >50100 1.5 2040 >100200 2.0 4060 200 4.11对不需切削加工的零件,剪切下料的切割面上不应有超过0.5mm的凸刺,火焰下料的切割面上 的割痕深度(粗糙度)不应超过表8的规定 8 表 单位为毫米 手工火焰切割 机械火焰切割 板材厚度 割痕深度 20 1.0 0.5 >2040 1.5 1.0 4060 2.0 1.5 4.12冷作零件的成型应符合图样或技术文件的规定 焊接部件 5.1焊接部件的外观表面不应有锤痕、焊瘤、金属飞溅物及引弧痕迹,边棱、尖角处应光滑
所有焊缝 的熔渣均应清理干净,外观焊缝还应打磨平整
5.2焊接部件的尺寸偏差应符合表9的规定
当焊接部件需经切削加工时,其尺寸偏差不得超过加工 余量的2/3,并应保证不小于4mm的加工余量
GB/T23570一2009 表9 单位为毫米 用于需切削加工 用于不需切削加工 基本尺寸 极限偏差 500 士1.5 士2.5 >500~1000 士2.0 士3,0 >l000~1600 士2.5 士3.5 6002500 士3.0 士4.5 >25004000 士4.0 士6,0 士7.5 40006300 土5.0 >6300 士6.0 士9.0 注:当需要提高精度时,需在工艺文件中注明
焊接部件的角度偏差应符合表10的规定
表10适用于小于90° 单位为毫米 长边尺寸 1000 1000~2500 >25004000 4000~6300 >6300 基准边(短边)尺寸 极限偏差 500 士5 士6 士7 士8 士9 >500~1000 士8 士4 士5 士6 士7 士7 l000 士4 士5 士6 5.4煤接部件表面的平面度公差,以及有关部位的同轴度、垂直度、对称度和平行度的公差应符合 表11的规定 表11 单位为毫米 平面度 同轴度、垂直度、对称度 平行度 基本尺寸 公差 500 2.0 2.5 5.0 >5001000 3.0 3.o 6.0 >1000~1600 3.5 7.0 >16002500 5.0 4.5 9.0 >2500~4000 6.0 6.0 12.0 >4000~6300 7.0 7.5 15.o >6300 8.0 9.0o 18.o 焊接接头与焊接 焊接接头的基本尺寸形式和尺寸应符合GB/T985.1或图样的规定
2 5.5. 焊接坡口表面不应有裂纹、分层和夹杂等治金缺陷
采用火焰切割的坡口,应将熔渣、氧化皮等 清理干净
5.5.3非加工面的外观焊缝的余高一般应符合表12的规定
下塌量一般不大于0.5 mm
GB/T23570一2009 表12 单位为毫米 焊逢宽度 焊缝余高 >6~10 <1.5 >1018 <1.9 >18~30 2.5 >30 3.0 5.5.4外观焊缝沿长度方向的尺寸均匀性一般应符合表13的规定
表13 单位为毫米 媒缝宽度 宽度(单边)允差 3.0 >18~30 3.5 30 4.0 5.5.5外观焊缝应呈光滑的或均匀的鳞片状波纹表面
5.5.6对接焊缝的错边量不应大于板厚的4,且最大不得超过2mm 5.5.7重要的承载焊缝,在任意100mm长度上直径不大于2mmm的气孔不应多余一个
未焊深度不 应大于母材壁厚的15%
咬边深度不应超过较薄母材壁厚的5%,且最大不应超过1.5mm;咬边长度 不应超过焊缝全长的10% 5.5.8焊缝不允许出现裂纹,连续焊缝不允许出现间断
5.5.9油箱、油池等常压容器的焊缝不允许出现渗、漏现象 5.5.10油缸等承压焊缝的质量按有关规定
5.6重要的焊接部件应进行消除应力处理
检验方法 6.1焊接部件的外观质量一般用目测法检验
焊接零件、部件和焊缝的尺寸及形状.位置误差用通用或专用的量具、检具检验
焊缝的外部缺陷用目测或低倍放大镜观察
内部缺陷可根据不同要求用超声波法、磁力探伤法、 钻孔法或按GB:/T3323检验 容器的密封性用涂刷煤油、盛水或其他等效方法检验
用涂刷煤油检验的方法是在焊缝的一侧涂 6 刷白垩粉水溶液,待干燥后在焊缝另一侧涂刷煤油2一3次,经15min一20min后,如白垩粉上未出现 油斑和油带,则为合格
进行煤油试漏时,环境温度不应低于5C
6.5焊缝的耐压性一般用水压(或压缩空气)方法检验,水压检验的压力不应低于工作压力的1.5倍, 保持时间不应少于5nmin 6.6焊缝的机械性能检验,按GB/T2650,GB/T2651、GB/T2653,GB/T2654等标准规定的方法 进行
对需要进行机械性能试验的焊缝,按GB/T2649的规定
试件的钢号、厚度、坡口型式、焊接规 6 范,焊条及焊点热处理均应与焊接部件完全相同
验收规则 7.1焊接零件及部件应按图样,工艺文件和本标准进行检查验收 7.2焊接部件的外观质量应逐件检查
GB/T23570一2009 7.3重要焊接部件的主要尺寸应逐件检查
7.4重要的承载焊缝和外观焊缝的尺寸及表面质量应逐个检查,其他焊缝抽查
7.5焊缝内部质量和机械性能检查的项目、数量与技术指标应根据图样和工艺文件的规定进行
7.6储油,储水的常压及高压容器应逐件进行渗漏或耐压检查