GB/T17744-2020
石油天然气工业钻井和修井设备
Petroleumandnaturalgasindustries—Drillingandwellservicingequipment
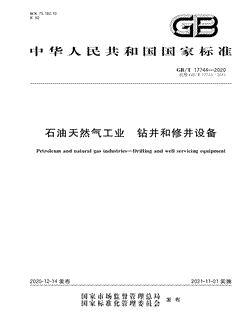
- 中国标准分类号(CCS)E92
- 国际标准分类号(ICS)75.180.10
- 实施日期2021-11-01
- 文件格式PDF
- 文本页数81页
- 文件大小6.72M
以图片形式预览石油天然气工业钻井和修井设备
石油天然气工业钻井和修井设备
国家标准 GB/r17744一2020 代替GB/T177442015 石油天然气工业钻井和修井设备 Petroleuandnaturalgasindustries一Driinmgandwellsermieingequipment 2020-12-14发布 2021-11-01实施 国家市场监督管理总局 发布 国家标涯花管理委员会国家标准
GB/17744一2020 目 次 前言 范围 2 规范性引用文件 术语和定义、缩略语 3.1术语和定义 3.2缩略语 设计 4.1设计条件 4,2强度分析 4.3尺寸级别代号 4.4额定值 4.5额定载荷值依据 4.6设计安全系数 .7剪切强度 4.8特定设备 4.9设计文件 设计验证 10 5.1总则 10 5.2设计验证功能试验 5.3设计验证压力试验 5.4设计验证载荷试验 12 5.5额定载荷的确定 12 5.6另一种设计验证试验程序和额定值计算 13 5.7载荷试验装置 13 5.8设计更改 5.9记录 材料要求 6.1总则 6.2书面规范 6.3金属材料 6.4非金属和复合材料 19 焊接要求 19 7.1总则
GB/T17744一2020 20 7.2焊接评定 7.3书面文件 20 20 7.4焊材控制 20 7.5焊缝性能 20 7.6焊后热处理(PwHT 7.7质量控制要求 DS 组焊 20 7.8特定要求 20 补焊 7.9特定要求 8 质量控制 2 8.1总则 2 8.2质量控制人员资格 21 8.3测试设备 8.4特定设备和零部件的质量控制 21 8.5尺寸验证 25 8.6验证载荷试验 25 26 8.7静水压试验 8.8功能试验 26 8.9要求确认的过程 26 设备 2 9.1总则 2 9.2转盘 27 9.3转盘补心 34 卡瓦座 9.4 34 9.5转盘卡瓦 35 9.6卡盘 36 9.7高压钻井液软管和高压水泥软管 37 9.8活塞钻井泵零部件 45 9.9绞车零部件 51 9.10手动大钳 52 9.11不用作提升设备的安全卡瓦 53 53 9.12防喷器(BOP)移运系统和设备 9.13高压钻井液循环系统泄压装置 60 9.14大钳尾绳 62 63 9.15滚动轴承 63 10标志 63 10.1产品标志 64 0.2标志要求
GB/T17744一2020 64 1文件 64 11.1记录保存 64 11.2制造商保存的文件 64 1.3设备携带的随机文件 66 附录A规范性附录附加要求 68 附录B(资料性附录热处理/热操作设备鉴定指南 70 附录C资料性附录手动大钳载荷极限设计 73 附录D(资料性附录产品订单信息 参考文献
GB/17744一2020 前 言 本标准按照GB/T1.1一2009给出的规则起草
本标准代替GB/T17744一2015《石油天然气工业钻井和修井设备》,与GB/T17744一2015相 比,主要技术变化如下 在“范围”中,删除了7种设备、增加了3种设备(见第1章,2015年版的第1章); 设计中删除动力大钳等设备的要求,增加转盘卡瓦、卡瓦座等的要求(见4.1、4.4、4.6,2015年 版的4.1、4.4、4.6); -将设计验证载荷试验中的公式(3)修改为表3(见5.4.3,2015年版的5.4.3) -增加了非金属材料的要求(见6.4); -增加了非金属件的验收准则要求(见8.4.7.5); 增加了要求确认的过程(见8.9); 修改了转盘补心中的部分要求(见9,3,2015年版的9.3); 删除了标准转盘卡瓦和非标准转盘卡瓦的内容(见2015年版的9.4和9.5); -设备中增加了卡瓦座.,转盘卡瓦.卡盘的内容(见豆4 9.6); 工作压力小于或等于51.7MPa钻井水龙带和软管的试验压力由2倍改为1.5倍(见表10 2015年版的表9); 将水龙带和减震软管的静水压试验压力修改为1.5倍工作压力(见9.7.7.1,2015年版的 9.6.7.1); 删除了设备标志内容中的制造商名称或商标及标准号(见2015年版的9.7,9.8,9,10,9,12 9.13、9.14); 设备中删除手动卡盘、气动或液压卡盘,动力大钳的要求(见2015年版的9.9~9.12及9.15); 附录A中sR2A改为仅金属件,增加了sR2B非金属件要求(见附录A); 删除了原附录C推荐的活塞钻井泵术语(见2015年版的附录C); 增加了附录c手动大钳载荷极限设计(见附录C); 增加了附录D产品订单信息(见附录D) 本标准由全国石油钻采设备和工具标准化技术委员会(SAc/Tc96)提出并归口
本标准起草单位;宝鸡石油机械有限责任公司,国家油气钻井装备工程技术研究中心、南阳二机石 油装备集团股份有限公司兰州兰石石油装备工程股份有限公司、石油工业井控装置质量监督检验中 心,四川宏华石油设备有限公司、中石化四机石油机械有限公司
本标准主要起草人;何根良、贾秉彦、郝建旭、王春春、余利军、魏孔财、刘炯、严小妮、廖江、唐浩、 王小通、徐军
本标准所代替标准的历次版本发布情况为 GB/T17744一1999,GB/T17744一2008,GB/T17744一2015
GB/17744一2020 石油天然气工业钻井和修井设备 范围 本标准规定了钻井和修井设备及主承载替换件的设计、制造和质量控制要求
本标准适用于以下设备 转盘; a 转盘补心 b 卡瓦座; c 手动和动力转盘卡瓦: d 手动和动力卡盘; e f 高压钻井液和水泥软管" 活塞钻井泵零部件; 8 绞车零部件; h 手动大钳 不用作提升设备的安全卡瓦 k)防喷器(BOP)移运系统; D 高压钻井液循环系统泄压装置; m大钳尾绳
规范性引用文件 下列文件对于本文件的应用是必不可少的
凡是注日期的引用文件,仅注日期的版本适用于本文 件
凡是不注日期的引用文件,其最新版本(包括所有的修改单)适用于本文件 GB/T228.1金属材料拉伸试验第1部分:室温试验方法 GB/T229金属材料夏比摆锤冲击试验方法 GB/T8423(所有部分)石油天然气工业术语 GB/T8834纤维绳索有关物理和机械性能的测定 GB/T9253.,2石油天然气工业套管,油管和管线管螺纹的加工、测量和检验 GB/T9445无损检测人员资格鉴定与认证 GB/T15169钢熔化焊焊工技能评定 GB/T16825.1静力单轴试验机的检验第1部分;拉力和(或)压力试验机测力系统的检验与 校准 GB/T20174石油天然气钻采设备钻通设备 GB/T22513石油天然气工业钻井和采油设备井口装置和采油树 JB/T8727液压软管总成 sY/T5170石油天然气工业用钢丝绳 SY/T6666石油天然气工业用钢丝绳的选用和维护的推荐作法 SY/T6727石油钻机液压盘式刹车
GB/T17744一2020 2ationforStructural lsteelBuildimgs) AISC360-05结构钢建筑物规范(Speeifiee ASMEB1.2统一英制螺纹用量规和测量(GagesandGagingforUnifedInchScrewThreads) AMEB16.34法兰、螺纹和焊连接的阀门(Valves一Flanged,Threaded,andweldingEnd ASMEB30.9吊索(Slings) ASMEB31.3工艺管道(ProcessPiping) AsMEBPvCc.V2019无损检测(NondestruetiveExamination AsMEBPvc..12019高压容器建造规则(RulesforConstructionofHighPressureVessels) AsMEBPvVC..2高压容器建造另一规则(RulesforConstruetionofHighPressureVessels AlternativeRules) AsMEBPvc.媒接和钉媒评定(wedingandBrazingQualifications) ASNTSNT-TC1A无损检测人员资格鉴定推荐作法(RecommendedPractieeforPersonnel QualificationandCertificationinNondestructiveTes sting ASTMA370钢制品力学性能试验的标准试验方法和定义(StandardTestMethodsandDefini tionsforMechanicalTestingofSteelProducts ASTMA388锻钢件超声波检验的标准方法(StandardPracticeforUltrasonieExaminationof Steel lForgings) AsTMA488 铸钢件焊接工艺和人员资格鉴定的标准方法(StandardPracticeforSteel Castings, welding,QualificeationsofProceduresandPersonnel ASTMA751 钢制品化学分析的标准试验方法、作法和术语(StandardTestMethods,Praetices andTerminologyforChermicealAnalysisofteelProducts) AsTMA770特殊用途钢板的全厚度拉伸试验标准规范(StandardSpecificationforThrough ThieknessTensionTestimgfsteelPlatesforspecialApplieations) tandardPracticesforForceVerifeationofTesing ASTME4测试仪器力验证的标准作法(Sta Machines AsTME125黑色金属铸件磁粉指示的标准参考照片(StandardReferencePhotographsfot MagnetieParticleIndicationsonFerrousCastin ings ASTME165液体渗透检验的标准试验方法(StandardTestM thodforLiquidPenetrantExam- Ne ination AsTME186壁厚为51mm~114mm(2in一4场in)的厚壁铸钢件用标准参考射线照片 [StandardRedferteneeRadiographeforHearywaAled(2o4另-in.(s1o114mm)stedlcaeting时 ASTME28o壁厚为114mm~305mm(4项in12in)的厚壁铸钢件用标准参考射线照片 [StandardReferenceRadiographsforHeavy-Walled(4to12-in.114to305-mm)SteelCastings AsTME428超声波检验用钢试块的制造和控制标准作法(StandardPraeticeforFabrieation andControlofSteelReferenceBlocksUsedin ltrasonicExamination ASTME446壁厚不超过51mm(2in) )的铸钢件用标准参考射线照片[StandardReferenceRa" diographsforSteelCastingsUpto2in.51mminThickness] AsTME709磁粉探伤标准指南(StandardGuideforMagnetieParticleExamination) AwSD1.1/D1.lM钢结构焊接规范(St Structural weldngCodeStee AwsQc1煤接检验员资格鉴定标准(StandardforAwscerifieationfweldinglnspectors) DNV起重设备认证规则(RulesfortheCertifieationofLiftingAppliances) ationtestofweldersFusion weding- EN287(所有部分钢件熔焊焊工鉴定试验(Qualifieat
GB/17744一2020 Steels) MSSSP-53阀、法兰、管件和其他管件铸钢件和锻钢件质量标准磁粉探伤方法Quality StandardforSteelCastingsandForgingsforValves,FlangesandFitingsandOtherPipingCompo- nentsMagneticParticleExaminationMethod MSsSP55阀、法兰、管件和其他管件铸钢件质量标准表面缺陷评价的目视方法(Quality StandardforSteelCastingsforValves,FlangesandFittingsandOtherPipingComponentsVisual MethodforEvaluationofSurfacelrregularities) NFPAT2.12.10R1液压传动系统和产品试验的一般测量原理和技术的推荐作法(Recommen dedPracticeHydraulicFluidPowerSystemmsandProducts -Testin《 GeneralMeasurementPrinci plesandTechniques) 术语和定义、缩略语 3.1术语和定义 GB/T8423界定的以及下列术语和定义适用于本文件
3.1.1 各向异性材料anistropicmaterial 性能随着相对于初始基准面的测试方向变化而变化的材料
3.1.2 elimitload 平均极限载荷average 在载荷极限设计中,导致限载件释放主载荷的主载荷平均值
3.1.3 防喷器移运系统和设备 bowoutpreventerhandlingsystemsandeguipmment 设计用来贮存、提升、下放和运输钻井和(或)生产设备上所用防喷器组的设备
3.1.4 缓冲件bufleredcoponents 在载荷极限设计中,除限载件外的所有主承载件
3.1.5 ufferedload 缓冲载荷 在载荷极限设计中,除限载件外的所有主承载件的最低载荷
3.1.6 蠕变 creep 零件保持应力不变的条件下,应变随时间延长而增加的现象
3.1.7 关键区域 criticalarea 主承载件上的高应力区域
3.1.8 设计载荷 designload 设备产生最大许用应力的静载荷与动载荷之和
GB/T17744一2020 3.1.9 设计安全系数designsafetyfaector;Dsr 在材料最大许用应力与规定的最小屈服强度之间考虑一定安全余量的系数
3.1.10 设计验证试验 designverificationtest 用来确认所采用的设计计算的正确性而进行的试验 3.1.11 动载荷 dynamicloadl 由于加速效应而施加给设备的载荷
3.1.12 端部连接装置 endconnector 位于软管总成端部,带有管线管螺纹或法兰或毂或与软管接头材料整体制造的锤击式由壬的附件, 用来把软管总成连接到管路系统上
3.1.13 等效圆 equivalentrond;ER 确定热处理低合金钢和马氏体不锈钢硬化特性时,把各种形状的截面用等效的圆形截面表示
3.1.14 glasstrasitiontemperature 玻璃化转变温度 低于该温度时,弹性体具有脆性、玻璃状性能的温度
3.1.15 危险区域 haZardoISareaorzOne 因易燃性气体或蒸气、易燃液体、可燃粉尘,或可燃纤维或漂浮物而可能存在火灾或爆炸危险的 场所
3.1.16 highpressure 高压 工作压力值,范围从10.3MPa103.4MPa1500psi15000psi)
注:见表10
3.1.17 高压水泥软管 high-pressurecementhose 用于在高压下输送水泥浆的软管
3.1.18 高压钻井液软管hehpreswredrlingnual h0Sse 钻井水龙带、减振软管或跨接软管
3.1.19 软管总成 hoseassembly 包括软管体和软管接头 注:结构型式见图11
3.1.20 软管体 h0sebody 不带软管接头或端部连接附件的平端软管
GB/17744一2020 3.1.21 软管接头hosecopling 连接在软管体两端的装配附件
3.1.22 软管设计系列hosedesignfamily 各种内径和工作压力的软管总成,但加强层数量相同,软管接头连接采用的方法相同,并按相同设 计方法和最大许用应力准则设计
3.1.23 相同设计原理 identicaldesignconcept -类设备的所有设备在主承载区域均具有相似的几何结构与功能特性
3.1.24 跨接软管 jumperh0se 用于输送高压钻井液的柔性软管总成
位于钻井系排出口和钻台上地面高压钻井液管汇之间的高 压钻井液管路系统中的任何位置,以适应其之间的相对运动
3.1.25 方钻杆补心 kellybIshing 与主补心配合的适配器,通过方瓦、销或其他方法,将转盘扭矩传递给方钻杆;同时,方钻杆补心工 作时,允许方钻杆垂直运动
3.1.26 限载件load-limitingcompoment 在载荷极限设计中,如果过载,将释放或限制主载荷的零部件、材料或机构
3.1.27 线性指示 linearindication 在无损检测中,长度大于3倍宽度的一种指示
3.1.28 载荷方差 loadVariance 在载荷极限设计中,度量均值的离散程度
3.1.29 单件装置 lo0segear 总成内所用的悬挂,固定或提升载荷的成品设备
注:包括但并不局限于钩环,链、吊钩、连接杆,螺旋扣、结合件、滑轮和旋转接头
3.1.30 maximuallowalestress 最大许用应力 规定的最小屈服强度除以设计安全系数
3.1.31 最高工作温度 maximumworkingtemperature 规定的工作温度范围上限
3.1.32 inimumbendradis;MBR 最小弯曲半径 从软管中心线测量的软管最小弯曲半径尺寸
GB/T17744一2020 注:见图11
3.1.33 monp0ol ludamee 月池导向系统 System 在配置和收回防喷器组过程中,防止防喷器组和浮移式海洋钻井装置结构物之间接触所设置的 结构
3.1.34 多载荷路径 multipleloadpaths 防喷器移运系统内安装的同时共同地承受静载荷和动载荷的两个或两个以上独立的主承载机械或 结构零部件
3.1.35 主载荷 primaryload 设备执行其主要的设计功能时设备所承受的载荷
3.1.36 主承载件 primaryloadearryingcomponents 设备中承受主要载荷的零部件
3.1.37 验证载荷试验 proofloadtest 为确认设备结构完好性所进行的产品载荷试验
3.1.38 额定载荷 ratedload 施加于设备的最大工作载荷
注:额定载荷包括静载荷和动载荷,在数值上等于设计载荷
3.1.39 额定速度 ratedspeed 设备在额定运行状态下的旋转、移动速度或速率
3.1.40 额定工作压力 ratedworkingpressre 设备设计承受和(或)控制的最大内部压力
3.1.41 修补 repair 制造过程中,通过焊接或其他的方法清除构件或部件的缺陷并进行整修
注:本标准表述的术语“修补”,仅适用于新设备制造期间的材料缺陷的修补 3.1.42 转盘卡瓦系统 rotaryslipsystemm 转盘卡瓦及其附带的卡瓦座的组合
3.1.43 转盘卡瓦rotaryslps -种安装在转盘上,能悬挂各种类型管柱且不能作为提升设备的装置,其内部有牙板以夹紧各种管 柱管体的外表面,卡瓦外表面锥度与卡瓦座内表面配合,通过手动、弹簧、气动、液动操作
3.1.44 roundedindication 圆形显示 在无损检测中,长度小于3倍宽度的接近圆形或椭圆形的任何显示
GB/17744一2020 3.1.45 安全工作载荷 safeworkingload 安全工作载荷等于设计载荷减去动载荷
3.1.46 卡瓦座slpbowls 支承卡瓦的带有锥形内表面的整体或分体式圆柱体
3.1.47 大钳尾绳snwb-line 大钳工作时,钢丝绳的一端固定在大钳手柄连接点的端部,另一端固定以保持大钳平稳
注:大钳尾绳不通过滑轮或弯曲
3.1.48 特殊过程spetial process 可以改变或影响设备所用材料力学性能(包括韧性)的工艺方法
3.1.49 卡盘spiders 钻井结构上悬挂各种管具而不能用作吊卡的装置,其内径上的一些零件用来夹紧各种管具的外表 面,通过手动、弹簧、气动、液动或其他辅助装置与方式操作
3.1.50 stressrelaxation 应力松弛 零件保持应变不变的条件下,应力随时间延长而减小的现象
3.1.51 减振软管vibratorhose 在两个管路系统之间或在钻井泵排出口和高压钻井液管路系统之间用来输送高压钻井液的柔性软 管总成,目的是吸收噪声和(或)减振,或补偿不对准和(或)热膨胀
3.1.52 factor 钢丝绳设计系数 wireropedesign 形成文件的最低破断强度与钢丝绳和吊索施加的工作载荷极限之间的比率
3.1.53 工作载荷极限wkimg" loadlimit 制造商分配给单件装置的载荷值,是断裂载荷值的若干分之一,在使用防喷器移运系统和设备期 间,不宜超过
3.2缩略语 下列缩略语适用于本文件
FSL;挠性规范级别(lexiblespeeificationlevel HAZ;热影响区(heataffectedzone dniling unit MODU:移动式海洋钻井装置mobileofshore NDE;无损检测nondestruciveexaminationm PQR:工艺评定记录(procedurequalifieationrecord PwHT;焊后热处理(post-weldheattreatment) SMYS,规定的最小屈服应力(speeifiedminimum yield streSs
GB/T17744一2020 TIR:总跳动(totalindicated runout wPs;焊接工艺规程(weldingprocedurespeeifcation 设计 4.1设计条件 钻井和修井设备的设计、制造和试验应在各方面满足其预定的用途
设备应能安全地传递规定的 载荷
设备的设计应能保证安全运行
应采用下面的设计条件: 确定设计载荷和安全工作载荷
设备操作者应负责确定特定作业下的安全工作载荷
a b)除非有附加要求(见附录A中sR2和sR2A),否则,转盘和绞车的设计最低工作温度为0 32下)
除非有附加要求,否则,安全卡瓦、卡盘、转盘卡瓦、卡瓦座、转盘补心、转盘适配器、 转盘卡瓦系统和手动大钳的设计及最低工作温度为一20C一4F);规定时才采用的附加要 求见附录A
除非在设备的制造中使用了在更低设计温度下具有要求韧性的合适材料(见附录A中sR2和 SR2A),否则,不推荐在低于上述设计温度时的额定载荷下使用本标准涵盖的设备 4.2强度分析 4.2.1 总则 设备的设计分析应着重考虑屈服、疲劳或屈曲等可能的失效模式
强度分析应以弹性理论为基础
另一方面,在设计文件认为合理的地方,也可采用极限强度(塑性 分析
与设计有关的力都应纳人计算
针对所要考虑的每个横截面,均应采用最不利的力的组合、位置和 方向
4.2.2简化假设 可以采用有关应力分布和应力集中的简化假设,但假设应符合公认的作法或基于丰富的经验或综 合性试验
4.2.3经验公式 只要验证零件内应力的应变仪测试文件记录结果能证明经验关系,那么,就可用经验关系替代分 析
当设备或零部件不准许使用应变仪验证其设计时,应按5.6的试验方法来鉴定
4.2.4等效应力 根据冯米塞斯-享克(VvonMises-Heneky)理论,设计载荷引起的名义等效应力,不应超过按公式 l)计算的最大许用应力口m R. o 式中 -最大许用应力 口max R
-最小屈服强度;
GB/17744一2020 设计安全系数
n 4.2.5极限强度(塑性)分析 极限强度(塑性)可在下列任一种条件下分析 接触区域 a b)零件的几何形状所引起的局部高应力集中区域及断面平均应力小于或等于4.2.4中规定的最 大许用应力的其他高应力梯度区域 在这些区域,平均应力以下的所有应力值应采用弹性分析法
塑性分析时,按照冯米塞斯-享克(VonMises-Henchy)理论,等效应力不应超过最大许用应力 ,按公式(2)进行计算
omax, R omnx 1
式中: 最大许用应力 口md -最小极限抗拉强度 Rm 设计安全系数
7, 4.2.6稳定性分析 稳定性分析应按照公认的弯曲理论进行
4.2.7疲劳分析 除非另有协议,否则,疲劳分析寿命应不少于20年
应按照公认的理论进行疲劳分析
可以采用的疲劳分析方法参见参考文献[14]
4.3尺寸级别代号 设备尺寸级别代号表示的尺寸互换性,应符合第9章的要求 4.4额定值 4.4.1转盘、卡盘、转盘卡瓦、卡瓦座、转盘卡瓦系统、转盘补心(方钻杆补心除外),转盘适配器、主补心 和手动大钳的额定值,应符合本标准规定的要求
4.4.2主载荷路径内所有轴承的额定静载值,应满足或超过设备的额定载荷
4.4.3制造商应规定各种结构使用的手动大钳的额定扭矩值 4.5额定载荷值依据 额定载荷值计算应基于: 4.6中规定的设计安全系数(DsF),除非第9章中另有规定; aa b 主承载件所用材料规定的最小屈服强度; 设计计算确定的应力分布值和(或)5.6中规定的设计验证试验得出的结果数据
4.6设计安全系数 4.6.1设计安全系数作为设计准则,任何情况下工作载荷不应超过额定载荷值
4.6.2卡盘、转盘卡瓦和转盘卡瓦系统的设计安全系数应按表1确定
GB/T17744一2020 1 表 卡盘和转盘卡瓦的设计安全系数 额定载荷P” 设计安全系数n kN(USton) <1334(150 3.00 3.00-0.75×(P-1334/3114 1334(150)4448(500 3.00-0,75×(P一150)/350" >4448(500 2.25 式中P单位为千牛(kN
式中尸单位为短吨(Uston) 4.6.3转盘和转盘补心主载荷路径内结构件的最小设计安全系数应为1.67
手动大钳和颗板最小设计安全系数应按表2确定 4.6.4 4.7剪切强度 当设计计算包含剪切时,则剪切屈服强度与拉伸屈服强度的比值应为0.58
4.8特定设备 特定设备设计要求见第9章
表2手动大钳和颗板的最小设计安全系数 额定扭矩值M 设计安全系数n kNm(ftlIb 三4130×10 3,00 3.00-0,75(M一41/95 >4130×10')136(100×10' 3.00一0.75M一30X×10/(70×10'" >136(100×10' 2.25 式中,M值单位为千牛米(kN m
式中,M值单位为英尺磅ftIb)
4.9设计文件 设计文件应包括方法、假设、计算和设计要求
设计要求至少应包括尺寸、试验和工作压力、材料、 环境和规范的要求以及其他有关的设计要求
这些要求也适用于设计更改文件
5 设计验证 5.1总则 为了确保设计的完整性和计算的准确性,应对第9章中有要求的设备进行设计验证试验 设计验证试验应按照形成文件的程序进行
10
GB/17744一2020 设计验证试验应由对产品的设计和制造没有直接责任,且具有进行该工作资格的人员执行或验证
设计验证试验可由本标准特定设备章条要求的一个或多个所列试验组成 功能试验 a b压力试验; c 载荷试验
5.2设计验证功能试验 5.2.1试验抽样 当设备通过其部件的连续运转传递力、,运动或能量时,每一种型号的设备应抽取一台(套)样机进行 功能试验
5.2.2试验程序 制造商应制定试验时间、试验施加的载荷和试验速度的形成文件的程序
连续运转的设备,试验样 机应在额定速度下至少试运转2h;间断运转或周期运转的设备,除第9章另有规定外,试验样机应在额 定速度下最少试运转2h或10个工作周期(取时间长者). 合格评定 5.2.3 样机工作应无明显的动力损失
轴承和润滑油的温度,应在设计和试验程序文件规定的可接受的 范围内
5.3设计验证压力试验 5.3.1试验抽样 所有设计的承压项目或第9章规定的主承压件,应进行设计验证静水压试验
本试验不包括传递 液压动力的零部件
5.3.2试验程序 试验压力应为最大额定工作压力的1.5倍
冷水、加人添加剂的水或实际作业中常用的液体应作 为试验液体
试验应在已完工油漆前的零件或总成上进行
静水压试验应进行两次
每次均应由以下四步组成 初始保压期 a b试验压力降至零; 试验件所有外表面完全干燥; c 二次保压期
d 二 保压期应从达到试验压力,且设备和压力测试仪表同压力源切断时开始计时.保压期不应少于 3min
5.3.3 合格评定 在每次试验循环后,应仔细地检查,确保试验不出现渗漏或永久性变形
不满足这个要求或过早失 效,应重新进行试验,重新进行设计评价 1
GB/T17744一2020 5.3.4单个零件 若试验装置的加载情况适用于组件中的单个零部件,这些零部件可单独进行试验
5.4设计验证载荷试验 5.4.1总则 当第9章所列特定设备有要求时,设备应进行设计验证载荷试验
5.4.2试验抽样 具有相同设计原理、不同规格和额定值的同系列设备的设计应力计算的验证,应采用下列任一种 方法 最少选该设计的3台样机进行设计验证载荷试验,试验样机应选自额定载荷值范围的低端、中 a 端和高端; D)另一种方法是,试验样机的数量以每台样机可验证高于和低于它的一个额定载荷值为原则来 确定(产品额定值范围不大时,通常采用这种方法). 5.4.3试验程序 试验程序如下 试验样机总成应加载到最大额定载荷
在卸载后,应检查样机预期的设计功能,设备的所有零 a 部件的功能不应因本次加载而削弱
b 试验样机上应力较高且可采用应变仪测量的部位应使用应变仪
应变仪适合使用的位置也推 荐采用有限元分析、模拟、涂脆性漆膜等方法予以确认
在关键区域,推荐采用三维应变仪,应 变仪不需精确定向,便能确定剪切应力
试验样机施加的设计验证试验载荷,应按表3确定
d 试验样机应加载设计验证试验载荷
试验载荷宜逐渐增加,同时读取应变仪数值并观察是否 有屈服迹象
必要时,试验样机可以多次加载,以获得足够的数据
应变仪读数计算出的应力值不应超过设计计算(基于设计验证试验载荷)得出的应力值,不应 大于5.7中规定的试验装置的误差
不满足本要求或任何试验样机过早失效,应按原要求以 相同数量的试验样机(包括与失效样机额定载荷值相同的试验样机)再次试验,完全重新评价 设计
设计验证载荷试验完成后,应拆开试验样机,并应检查每个主承载件的尺寸是否有永久变形的 迹象
若试验装置的加载情况适用于组件中的单个零部件,这些零部件可单独进行载荷试验
5.5额定载荷的确定 额定载荷应按第4章要求的设计验证载荷试验结果和(或)应力分布计算值来确定
在额定载荷值 下的应力不应超过最大许用应力
应允许接触区域有局部屈服
样机设计验证载荷试验后,除接触区 域外,应变仪或其他合适方法测得的关键永久变形不应超过0,2%
如果应力超过许用值,则受影响的 零部件应重新设计.直到达到所需的额定值
只有当分析确定的应力值不小于设计验证载荷试验期间 观测到的应力值时,应力分布计算才可用于设备额定载荷值的计算
12
GB/17744一2020 5.6另一种设计验证试验程序和额定值计算 如果设备所用材料的屈服强度和拉伸强度被确定后,则试验样机可进行破坏性试验
这可通过采 用与所代表零部件同炉及热处理批的拉伸试样来进行,并满足GB/T228.1或ASTMA370的要求
总成的每一个零部件应在承载最不利的情况下进行鉴定
可采用下列任一种方法进行零部件的 鉴定 应计算总成的每一个零部件的比值TR
公式中应采用这些比值的最小值
a b 若试验装置的载荷条件适用于每个零部件,则每个零部件可按公式(3)分别进行载荷试验
在 这种情况下,每次试验按公式(4)计算所用的比值T应为试验的特定零部件的计算值
T" P=P× 1, TR- 式中 TR 构件的比值 设计安全系数(见4.6); n R. 最小屈服强度; R 实际极限抗拉强度; 破断载荷 ” -额定载荷
由于这种设计验证方法不依据应力计算,因此仅限于试验的特定型号、尺寸、尺寸范围和额定值
表3试验载荷的确定 额定载荷值P 设计验证试验载荷 kNUSton l11201250),以及所有额定扭矩值 0,8×P×n,,但不小于2P >11120(1250)~14678(1650) >14678(1650y 1.5XP sI单位,P单位为kN 一11120 C=2一0.5× 3558 USC单位:P单位为USton 1250 -0.5 400 式中: 额定载荷值,单位为kN(USton)或kNm(ftlb)(如适用); -3.1.9和4.6中规定的设计安全系数
注为了研发和评定额定载荷值实际超过11120kN(1250USton)的设备,调整试验载荷系数,主要是因为试验 装置的儿何结构和材料的限制 5.7载荷试验装置 模拟试验样机上工作载荷所用的加载装置,应按GB/T16825.1或ASTME4的规定校准,以确保 13
GB/T17744一2020 试验载荷的准确度
载荷超过3560kN400USton)的载荷试验装置,误差应小于2.5%
试验装置应以与实际作业相同的方式在相同的承载接触面上给样机(零件)加载
样机(零件)的所 有加载设备的试验能力应予以验证
5.8设计更改 当因设计或制造的任何更改而更改计算的额定载荷值时,则应根据本章要求进行支持性的设计验 证试验
制造商应评价设计或制造方面的所有更改,以确定是否影响计算的额定载荷值
这种评价应 形成文件
5.9记录 所有设计验证记录和支持性数据,应按第11章中设计文件的规定进行控制
6 材料要求 6.1总则 本章规定了主承载件和承压件材料的各种鉴定、性能和加工要求(除非另有规定). 6.2书面规范 本标准适用的设备的主承载件制造所用的材料,应满足或超过设计要求
6.3金属材料 6.3.1力学性能 6.3.1.1 冲击韧性 冲击试验应按照GB/T229或ASTMA370(夏比V型缺口)进行
当必须使用小尺寸冲击试样时,则验收准则应乘以表4所列的相应的调整系数
不应采用宽度小 于5mm(%in)的小尺寸试样
设计温度低于4.1中规定的温度时,可采用附加冲击韧性要求,见附录A的附加要求SR2 和SR2A
表4小尺寸冲击试样的调整系数 试样尺寸 调整系数 mmXmm 10.0×7.5 0.833 10,0×5,0 0.667 6.3.1.2厚度方向的性能 若设计要求厚度方向上的性能时,则材料应按照ASTMA770沿厚度方向取样进行拉伸试验,获 取断面收缩率指标
最小断面收缩率应为25%
14
GB/17744一2020 6.3.2材料鉴定 6.3.2.1总则 本标准所要求的力学性能试验,应在质量鉴定试棒上进行,该试棒代表零件制造中所用的热处理炉 次及热处理批次
试验应按GB/T228.1、GB/T229或AsTMA370或等效的国家标准的要求,在材 料最终热处理状态下进行
如果PwHT温度低于母材热处理状态改变的温度,则为了材料鉴定试验 的焊后消除应力不看作是热处理
如果消除应力温度低于热处理状态改变的温度,则材料鉴定试验可 在消除应力过程之前进行
6.3.2.2等效圆(ER) 采用ER方法,确定零件质量鉴定试棒的尺寸
确定简单实体件和空心件ER的基本模型如图1 和图2所示
所示任何形状均可用于质量鉴定试棒
图3规定了更为复杂截面ER确定的步骤
采用 “热处理状态”下零件的实际尺寸,确定零件的ER
质量鉴定试棒的ER应等于或大于其鉴定的零件的 ER尺寸,但并不要求该ER超过125mm(5in)
图4和图5为AsTMA370基尔试块要求尺寸确定 的程序
6.3.2.3材料试样 在所有憎 质量鉴定试棒应与其代表的零件是一体或分体,也可是解剖产品零件的一部分 6.3.2.3.1 况下,试样应与其鉴定的零件出自同一炉,应经过相同的工序,并且应与零件一起进行热处理
6.3.2.3.2试样应取自连体或分体质量鉴定试棒,对于实心(质量鉴定)试棒,试样纵向中心轴线完全在 实心(质量鉴定)试棒4!包封的芯部以内,或对于空心(质量鉴定)试棒,试样纵向中心轴线完全在空心 质量鉴定)试棒最厚截面的壁厚中心的3mm(1/8in)以内
拉伸试样的标距长度或冲击试样的缺口 应距质量鉴定)试棒端部至少t
6.3.2.3.3解剖产品零件切取的试样,应取自零件最厚截面的4包封的芯部位置
6.3.2.3.4对于完全由锻造材料加工的完全按实心棒材或管材热处理的零件,标准x!包封完全或部 分地在成品零件关键和(或)非关键区域之外,这些棒材或管材切取的试样,也可以按照如下方法取自更 具代表性的区域 取样区域外径,通过最终成品零件的最大外径和最小内径确定的包封规定; a b)取样区域内径,应等于或大于成品零件的最小内径
示例:外径150mm6.0in)的4340MOD棒材,正火、淬火加回火(NQT);零件最终尺寸为最大外径139.7nmm (5.5in).最小内径63.5mm(2.5in)
=(139.7一63.5)/2= =38.lmm %!=12.7mm 成品零件!/包封内的外径为l4.
mm(4.5im),因此,试样可以取自外径4.3mm(45im)x 内径63.51 mm 2.5in)规定的区域的任一处(成品零件%!包封和内径). 15
GB/T17744一2020 ER= ER=1.1n ER=1.25/r ER=1.5 圆形 正六边形 正方形 长方形或平板 注1:当L<时,按厚度为L的平板考虑
注2:图中阴影为取样尺寸
图1等效圆模型 -长度为L的实体 ER=2! 当D63.5mm2.5in),ER=2.5 当D>63.5mm2.5in),ER=3.5! 注1;当L
GB/T17744一2020 6.3.3制造 6.3.3.1制造过程应确保零部件重复生产时满足本标准的所有要求
6.3.3.2所有锻造材料的制造过程,应保证零件内部组织结构的同一性
6.3.3.3 所有热处理操作应呆用拨制造商或加工商规定要求整定合格的设备
热处理炉内任何一个零 件的装载,应不影响同批次中任何其他零件的热处理特性
热处理周期的温度和时间要求,应按照制造 商或加工商的书面规范确定
应记录实际热处理温度和时间,热处理记录应能溯源到相应的零部件
注:热处理设备鉴定的推荐作法参见附录B
6.3.4化学成分 每炉材料成分均应按照ASTMA751(详细信息见IS/TR9769)或等效的国家标准的要求,对制 造商书面材料规范中规定的所有元素进行分析
6.4非金属和复合材料 总则 6.4.1 应允许采用非金属和复合材料制造主承载件,但材料应满足设计要求的性能
6.4.2力学性能 6.4.2.1总则 所有非金属材料的机械性能要求,应以对设备功能至关重要特性的最佳限制进行制定
6.4.2.2试验温度 材料性能应在最低温度一20(一4“F)(除非第9章另有规定)和规定的最高温度(推荐的最高工 作温度)进行鉴定
如果规定sR2B(见附录A),要求最低温试验温度
6.4.2.3试样取向 试验各向异性材料所取的试样时,应沿所考虑力学性能最不利情况下的极限值方向
6.4.2.4蠕变,应力松弛和速率效应 蠕变和(或)应力松弛敏感材料.应试验作业中遇到的最苛刻条件下,对时间、温度、,应力和应变等的 抵抗能力
零部件出现蠕变和(或)应力松弛时,不应在工作条件下引起其功能的损失
加载速率影响力学性能的材料,应以作业中遇到的最剧烈的加载速率进行试验
6.4.2.5等效屈服强度 对于屈服强度不明显的材料,应取极限强度值乘以0.80或弹性模量的5%取其小者)作为等效屈 服强度
6.4.3环境因素 非金属材料应对作业中可能遇到的任何化学品的化学浸蚀进行试验
试验至少应指出什么化学品 影响设备的使用性能或设备在额定载荷下的使用能力
非金属材料应评估紫外线辐射和其他环境因素的影响
评估应包括在零部件预期寿命内作业中可 18
GB/17744一2020 能遇到的暴露
6.4.4材料鉴定 总则 6.4.4.1 本标准所要求的力学性能试验,应在质量鉴定试样上进行,该试样代表零件制造中所用的同一批成 品材料
所有相同化学过程的同批材料制造的非金属件应被视为同一批
可以对非金属材料的温度、 取向、蠕变,应力松弛、加载速率效应和化学性能进行预评定
预评定材料的性能应满足或超过设计所 需的值
力学性能不应进行预评定
每批应进行力学性能的试验
6.4.,4.2材料试样 质量鉴定试样应与其鉴定的零件出自相同批次,应经过相同的制造过程,并且应与其鉴定零件的暴 露环境条件相同
6.4.4.3制造 制造过程应确保零部件重复生产时满足本标准的所有要求
所有热操作应采用按制造商或加工商的规定鉴定合格的设备
炉子和烘箱内任何一个零件的装 载,应不影响同一装载中任何其他零件的热特性
温度和时间要求应按照制造商的书面规范确定
注:热操作设备鉴定的推荐作法参见附录B. 6.4.5文件 制造商按照采购协议交付设备时,应在检验和维护手册中,向用户和(或)业主提供所有非金属材料 检验的特定程序(包括频次、方法,设备、验收和拒收准则)
因为备件的老化和储存期,这些程序也应包 括推荐的最长更换周期
制造商也应提供关于材料化学侵蚀抵抗力说明和信息,影响设备使用性能或 设备在额定载荷下使用能力的各种类型化学品清单
制造商应提供设备在额定载荷下可以使用的最低 温度和最高温度,以及不利的会影响设备在额定载荷下工作能力的任何其他环境条件
6.4.6附加要求 6.4.6.1玻璃化转变温度为工程塑料使用温度的上限,为橡胶或弹性体的使用下限 6.4.6.2陶瓷和陶瓷基复合材料仅用作主承载件的受压部件
6.4.6.3单向拉伸加载的无粘结弹性涂层芳纶纤维绳索 -材料的鉴定和控制应符合制造商的书面规 范
材料规范应包括(至少有适当的范围)未加涂层的绳索直径、绳纤丝,加涂层的绳索直径、加捻密度 和拉伸强度
拉伸强度应按GB/T8834进行试验
所有力学性能试验需在至少一个完全封装的单股 绳上进行
材料应进行循环加载预评定
上述材料试样应按额定载荷加载拉力,并完全卸载,至少循环 1500次或零部件设计寿命相应的循环数,取其大者
然后,同一试样加载拉力直到断裂
循环试验后 试样断裂的载荷不应小于规定的拉伸强度 焊接要求 7.1总则 本章规定了主承载件和承压件组焊和补焊的要求,包括连接焊缝
19
GB/T17744一2020 7.2焊接评定 所有零部件的焊接,应采用ASMEBPVC.X、AwsD1.1和(或)ASTMA488评定合格的焊接工 艺进行
只有按照上述标准或GB/T15169或EN287鉴定合格的焊工或焊机操作工,才允许进行 焊接
未列人上述标准的母材的焊接工艺,应单独地或按可焊性、拉伸性能或成分分组进行评定
若母材 金属延展性不能满足ASMEBPVC.的弯曲试验要求,弯曲试验应按下列方式进行;母材金属按相应 规范的延展性和强度要求热处理后切取的弯曲试棒,应进行弯曲直至破坏
由焊缝试样切取的侧面弯 曲试样,弯曲的角度误差应能在由此确定的角度的5"范围之内
7.3书面文件 焊接应按书面焊接工艺规范(wPs)进行,并按相应标准进行评定
wPS应规定相应标准所列的 所有重要参数、非重要变素和附加的重要变素(当需要时)
也可采用符合相应标准的预先评定的书面 焊接工艺
S 工艺评定记录(PQR)应记录评定试验用焊接工艺的所有重要参数和附加的重要参数(当需要时)
wPs和PQR均应按第11章的要求作为记录保存
7.4焊材控制 焊材应符合焊材制造商或美国焊接协会(AwS)的规范
制造商应具有贮存和控制焊材的书面程序
低氧型材料应按焊材制造商的推荐作法贮存和使用, 以保持其原有的低氢性能
7.5焊缝性能 工艺评定试验确定的焊缝力学性能,至少应满足设计要求规定的最低力学性能
当要求母材做冲 击试验时,工艺评定应进行冲击试验
焊缝和母材热影响区(HAZ)的试验结果,应满足母材的最低要 求
连接焊缝,仅要求冲击试验的材料热影响区(HAZ)满足上述要求 所有焊缝试验应在试验焊件相应的焊后热处理状态下进行
7.6焊后热处理(PwHr 零部件的焊后热处理应符合相应的评定合格的wPs 7.7质量控制要求 焊缝质量控制应符合第8章的相关要求
7.8特定要求 -组焊 焊缝接头形式和尺寸应满足制造商的设计要求,并反映在制造商的wPs文件中
-补焊 7.9特定要求一 7.9.1方法 应有适当的方法来评价、移除和检验需要补焊的缺陷
20
GB/17744一2020 7.9.2熔合 选定的wPS和适用的补焊方法,应确保与母材完全熔合
7.9.3锻件和铸件 所有补焊应按制造商的书面焊接规范进行
wPs应予以形成文件,并应在采购方要求时予以 提供
制造商应将下列允许补焊的准则形成文件 缺陷类型 缺陷尺寸极限; 大修补和(或)小修补的定义
补焊前的所有开挖(缺陷清除)和随后的补焊,应满足第8章规定的质量控制要求
7.9.4热处理 补焊所用的wPS,应能反映出实际补焊操作和热处理的顺序
8 质量控制 8.1总则 本察规定了设备和材料的质量控制要求
所有质量控制工作应通过制造商形成文件的指导书加以 控制,该指导书应包括相应的方法、定量和定性的验收准则
NDE活动的指导书,应充分地详述本标准和所有适用的引用规范的要求
所有NDE指导书应由 GB/T9445或ASNTSNT-TC-1A级注册检验师批准
所有设备,零部件和材料的验收状态应在设备、零部件和材料上或在其可追溯性记录中予以指明
8.2质量控制人员资格 NDE人员应按GB/T9445或ASNTSNT-TC-1A,取得资格和(或)证书
对焊接操作和完工焊缝进行目检的人员,应按照下列方式之一进行资格鉴定: -AwsQC1或等效标准; -制造商形成文件的培训计划(如可等效上述标准). 所有进行直接影响材料和产品质量的其他质量控制活动的人员,均应按照制造商形成文件的程序 进行资格鉴定
8.3测试设备 检查、试验或检验材料的设备或其他设备,应按照制造商形成文件的指导书和公认的标准规范(例 如;ISo10012-1,MIL.STD120),定期进行识别、控制、校准和调整,以保证其所需准确度
8.4特定设备和零部件的质量控制 8.4.1 总则 除非另有规定,质量控制要求应适用于所有主承载和(或)承压设备和零部件
制造商应建立并保存关键区域图,识别高应力区域,与本章一起使用
21
GB/T17744一2020 本章中,关键区域应定义为零部件中应力不小于公式(5)的所有区域: 0.75R. 式中: -高应力临界应力: a 设计安全系数 1 Rd -最小屈服强度
如果在关键区域图上没有识别关键区域.则应认为零部件的所有表面均为关键区域
零部件中存在压应力和(或)应力级别不大于下列数值的区域,不应在8.4.7.4规定的验收准则范围 内
这样规定的低应力区域,按公式(6)计算,可以在关键区域图上予以识别 0.1R 6) 1 式中 低应力临界应力 o 规定的最小屈服强度; R 设计安全系数
n 8.4.2化学分析 金属材料应按6.3.4的方法和准则验收
8.4.3拉伸试验 应按6.3和6.4的方法和准则验收
8.4.4冲击试验 应按6.3和6.4的方法和准则验收
8.4.5追溯性 零部件应能通过炉(号)和热处理批、标志进行追溯
在完工的零部件或总成上以及在制造各阶段的材料和零部件上,应保持标志
制造商形成文件的 追溯性要求,应包括维护和更换标志及标志控制记录的条款
紧固件和管接头不要求追溯性,但应按公 认的标准规范标记
8.4.6目检 零部件应进行目检
铸件的目检应满足MSssP55的要求
锻轧材料的目检应符合制造商形成 文件的要求
8.4.7表面NDE 8.4.7.1总则 每一完工零部件的所有可接近表面,均应在最终热处理和最终机加工后按照8.4.7进行检验
若设备需进行载荷试验,则应在载荷试验之后进行NDE
对于制造商识别的延迟裂纹敏感材料. 应在载荷试验至少24h后进行NDE
设备应拆卸进行该项检验
检测前应除去表面导电涂层
除非 22
GB/17744一2020 已经证明,在涂层的最厚处可检测到8.4.7.3中规定的最小相关指示,否则,在检测之前,应除去表面非 导电涂层
8.4.7.2方法 铁磁性材料应按AsMEBPvC.V一2019A分卷第7章和B分卷第25章或ASTME709进行磁粉 检测
机加工表面应采用湿荧光磁粉法进行检测,其他表面应采用湿磁粉法或干磁粉法进行检测
非铁磁性材料应按AsMEB;Pvc.V2019A分卷第6章和B分卷第24章或AsTME165进行液 体渗透法检测
如果不得不采用磁化电极时,所有磁化电极的烧痕应磨除,影响区域应采用液体渗透法重新检测
8.4.7.3指示的评价 只有主要尺寸大于2mm%in)且与表面破裂有关的那些指示才应认为是相关指示
与表面破裂 无关的固有指示(例如磁导率变化、非金属条带等)应认为是非相关指示
如果大于2mm(%in的磁 痕指示被认为是非相关指示,则这些指示应采用液体渗透法进行检测.以证实其非相关性,或应予以清 除并重新检验,以证实其非相关性
相关指示应按照8.4.7.4中规定的验收准则进行评价
8.4.7.4验收准则 8.4.7.4.1铸件 AsTME15宜作为评价铸件相关指示的参考标准
验收准则应按表5的规定
8.4.7.4.2锻件 锻造材料的表面NDE,应采用下列验收准则 -无任何主要尺寸等于或大于5mm%in)的相关指示; 在任何一个连续的40cm=(6in)的面积上,相关指示不超过10个; 在任一条直线上,边距小于2mm(%in)的相关指示不超过3个; 在压力密封区域、旋转螺纹根部区域或螺纹式接头的应力释放结构中,无任何相关指示
表5铸件指示验收准则 最大允许等级 缺陷类型 类型 关键区域 非关键区城 热裂、裂纹 无 1级 缩孔 2级 2级 川 夹杂物 2级 2级 内冷铁、型芯撑 1级 1级 2级 气孔 1级 8.4.7.5非金属件 制造商应有书面规范,规定每种类型的预期不连续的最大尺寸,方向、分组等
考虑的不连续类型 23
GB/T17744一2020 至少为空隙、切口、裂纹、分层和(或)撕裂
预期不连续探测的方法应予规定,并证明可以有效地探测到小至最大许用尺寸或严重程度75%的 不连续
所有主承载件需在关键和非关键区域进行检测
8.4.8铸件体积NDE 8.4.8.1方法 铸件的射线检测应按照AsMEBPvc.V2019A分卷第2章和B分卷第22章,但不应采用荧光 增感屏
超声波检测应按照ASMEBPvc.V-2019A分卷第5章和B分卷第23章
零部件应按照第23 章sA-609采用垂直法进行检测,若零部件的部位在垂直法检测期间不能保持背反射或两个表面之间 的夹角大于1时,应按照第万章的丁5342进行斜探法检测 8.4.8.2取样 主承载铸件至少应按以下取样原则进行体积NDE 一首批铸件或试生产铸件的所有区域都应采用超声波或射线法检测,直到检测结果表明生产技 术已符合要求; 在批量生产中,每一个生产批的铸件每10件抽取一件,当生产批的铸件数量少于10件时,也 应抽取一件,应在关键区域图上识别的所有关键区域进行体积检测
若任何铸件显示的任何 指示超出8.4.8.3规定的验收准则,则应从该生产批中再取两个铸件,以相同的方式进行检测 如果这两个铸件都合格,则该批剩余的铸件可通过验收,最初的不合格铸件应返修或报废
8.4.8.3验收准则 8.4.8.3.1总则 零部件应力级别小于低应力值的区域[按公式6)计算],不应进行体积检测
8.4.8.3.2射线检测 射线检测的验收准则,按被检测的壁厚,分别基于ASTME446,ASTME186或ASTME280的 标准参考射线照片
在所有情况下,不应有裂纹、热裂和夹渣缺陷类型分别为D,E和F)
参考射线照片上显示的其他指示类型,在所有关键区域内应满足质量2级,在非关键区域内应满足 质量3级
关键区域应按照8,4.1的规定
如果在关键区域图上没有识别关键区域,则零部件的所有区 域均应视为关键区域
8.4.8.3.3超声波检测 铸件的直射束法和斜射束法超声被检渊的验收准则,按AsMEPvc.v-209B分卷第23章中 的sA-609质量3级,但在距铸件表面50mm(2in)内应符合质量1级
不应有深度变化为25mm 1in)或壁厚一半(取较小者)的指示缺陷
8.4.9焊缝NDB 8.4.9.1 总则 若要求检测,则在焊接期间,应对基本焊接参数和设备进行监测
整个可接近焊缝以及至少13mm 24
GB/17744一2020 in)的周围母材金属,应按8.4.9的方法和验收准则进行检测
8.4.9要求的NDE应在最终热处理之后进行
8.4.9.2组燥 目检 8.4.9.2.1 所有组焊焊缝应按ASMEBPVC.V一2019A分卷第9章进行目检
咬边不应使影响区的厚度小 于设计厚度,并应打磨至与周围材料光滑地过渡
密封表面或距密封表面3 (%im)内,不应有表面气孔或裸露的夹渣
mm 8.4.9.2.2表面NDE 所有主承载及承压焊缝和主承载及承压件的连接焊缝,应按8.4.7.2进行检测
应采用以下验收准则 无任何相关线性指示; 焊缝厚度不大于17mm(%in),无任何主要尺寸大于4 (%in的圆形显示 mm -焊缝厚度大于17mm(%in),无任何主要尺寸大于5mm(%im)的圆形显示; 在任一条直线上,边距小于2mm(%in)的相关指示不超过3个
8.4.9.2.3体积NDE 主承载焊缝和承压媒缝应采用超声波或射线方法进行检测
超声波检测应按AsMEBPvc.V 2019A分卷第4章,射线检测应按AsMEBPvc.V一2019A分卷第2章
本条仅适用于全焊透焊缝 如适用,验收准则应按照ASMEBPVC..1一2019中Uw-51和附录12的要求
8.4.9.3补焊焊缝 8.4.9.3.1焊缝开挖(缺陷清除》) 焊缝补焊的所有开挖(缺陷清除),应采用8.4.7规定的方法和验收准则进行磁粉检测
8.4.9.3.2铸件的补焊焊缝 铸件的所有补焊焊缝均应按照8.4.7.2进行检测
验收准则应与组焊焊缝的验收准则相同 见8.4.9.2
8.4.9.3.3焊缝的修补 焊缝缺陷修补的NDE,应与原焊缝的NDE相同(见8.4.9.2)
8.5尺寸验证 尺寸检验应在制造商规定和形成文件的抽样的基础上进行
所有主承载和压力密封螺纹,应按相应螺纹规范的要求进行测量
8.6验证载荷试验 当第9章有关设备标题下指出要求验证载荷试验时,应符合下列要求 每台生产设备或主承载件,应按本章要求进行载荷试验
b 设备应安装在试验装置上,能以与实际作业相同的方式在相同的承载接触面上加载
试验可 25
GB/T17744-2020石油天然气工业钻井和修井设备
随着现代化科技的发展以及石油天然气资源的不断开采,钻井和修井设备在石油天然气工业中扮演着越来越重要的角色。为了保障设备的质量、安全以及环保性能,相应的标准逐渐得到了完善,其中GB/T17744-2020就是一项十分重要的标准。