GB/T36955-2018
柔性直流输电用启动电阻技术规范
Technicalspecificationforpre-insertionresistorofhigh-voltagedirectcurrenttransmissionusingvoltagesourcedconverters(VSC-HVDC)
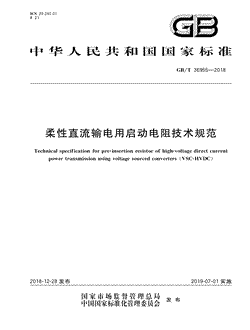
- 中国标准分类号(CCS)F21
- 国际标准分类号(ICS)29.240.01
- 实施日期2019-07-01
- 文件格式PDF
- 文本页数26页
- 文件大小5.23M
以图片形式预览柔性直流输电用启动电阻技术规范
柔性直流输电用启动电阻技术规范
国家标准 GB/T36955一2018 柔性直流输电用启动电阻技术规范 Teehniealspeeificatioforpre-insertionresistorofhigh-voltagedireeteurrent transmissionusingvoltagesoreedconverters(VsC-IHVDC' p0Wer” 2018-12-28发布 2019-07-01实施 国家市场监督管理总局 发布 国家标准化管理委员会国家标准
GB/T36955一2018 次 目 前言 范围 2 规范性引用文件 3 术语和定义 使用条件和安装条件 技术参数 设计和结构 6 型式试验 出厂试验例行试验 15 现场试验 包装、贮运,安装,运行及维修和技术资料 10 15 17 附录A资料性附录)启动电阻位置示意图 附录B(资料性附录电阻器典型设计参数 19 附录c(资料性附录)启动电阻典型充电电流波形 21
GB/36955一2018 前 言 本标准按照GB/T1.1一2009给出的规则起草
本标准由电力企业联合会提出
本标准由全国高压直流输电工程标准化技术委员会(SAC/TC324)归口
本标准起草单位:国网经济技术研究院有限公司、全球能源互联网研究院有限公司
本标准主要起草人:潘尔生、梅念、郭贤珊、杜晓磊、马为民、薛英林,乐波、陈东、李探、赵峥、魏争 李高望、厉、陈钊,许冬、苑宾,祝全乐、程炜、李达、季兰兰、周啸、王晓宇
GB/36955一2018 柔性直流输电用启动电阻技术规范 范围 本标准规定了柔性直流输电用启动电阻的使用条件和安装条件、技术参数,设计和结构,型式试验、 出厂试验、现场试验、包装、贮运、安装及维修和技术资料
本标准适用于柔性直流输电用启动电阻,包括交流侧启动电阻和直流侧启动电阻,统一潮流控制器 UPFC)工程交直流侧启动电阻可参照执行
规范性引用文件 下列文件对于本文件的应用是必不可少的
凡是注日期的引用文件,仅注日期的版本适用于本文 件
凡是不注日期的引用文件,其最新版本(包括所有的修改单)适用于本文件
GB/T311.1一2012绝缘配合第1部分;定义,原则和规则 GB/T4208一2017外壳防护等级(IP代码 GB/T11022一2011高压开关设备和控制设备标准的共用技术要求 GB/T13540高压开关设备和控制设备的抗震要求 GB/T16927.1一2011高电压试验技术第1部分一般定义及试验要求 GB/T30547一2014高压直流输电系统滤波器用电阻器 GB/T50064!交流电气装置的过电压保护和绝缘配合设计规范 术语和定义 下列术语和定义适用于本文件
3.1 启动电阻pre-insertionresistor 柔性直流换流站不控充电过程中为减少电压源换流器充电电流而投人的电阻
3.2 交流侧启动电阻pre-insertionresistoratACside 根据系统条件布置在联接/换流变压器的网侧或阀侧的启动电阻
注:交流侧启动电阻典型位置示意参见附录A
布置在联接/换流变压器的网侧的启动电阻称为交流网侧启动电 阻,布置在联接/换流变压器的阀侧的启动电阻称为交流阀侧启动电阻
3.3 直流侧启动电阻preinsertionresisto”atDcside 根据系统条件布置在电压源换流器的直流极母线或中性母线处的启动电阻
注直流侧启动电阻典型位置示意参见附录A 3.4 resistormodule 电阻器模块 由多个电阻元件、联结材料及支撑材料通过串联或者并联方式组装于单个外壳或外套中并有出线 端子的组装体
GB/T36955一2018 3.5 充电电流chargingcurrent 不控充电过程中,启动电阻中流过的电流
3.6 额定电阻值 norminalresistance 无电流条件下,启动电阻折算到25C的直流电阻值
电阻值温升偏差 resistancetemperaturetolerance 温度变化造成的电阻值偏差
注:温度变化范围指从最低环境温度下无电流时的温度到最高环境温度下承受冲击能量后的温度
最低环境温度 下无电流通过时电阻值与额定电阻值偏差的百分数,称为低温偏差;最高环境温度下承受冲击能量后的电阻值 与额定电阻值的偏差,称为高温偏差
3.8 冲击能量impulsion emrey 柔性直流换流器充电过程中流过启动电阻的功率积分,包括正常充电过程的冲击能量和充电过程 中发生短路时的冲击能量
3.9 冲击能量耐受能力impulsionemerswithstandablity 电阻器在通过充电电流时能承受的冲击能量值w,由式(1)给出
W=c×m×0 式中 电阻材料比热,单位为焦每千克开O(keK1. 电阻材料质量,单位为千克(kg); mm 允许增加的温升,单位为开(K)
0 注:9小于电阻器短时最大允许温度减去最高环境温度 使用条件和安装条件 4.1使用条件 可按照GB/T11022一2011中2.1,2.2和2.3执行
4.2安装条件 电阻器宜采用瓷绝缘子支撑式安装
5 技术参数 5.1电阻值 5.1.1额定电阻值(R、 额定电阻值在0Hz一3000Hz频率范围内应满足0%十10%的偏差
电阻值温升偏差应根据 具体工程条件满足附录B所列要求
测量额定电阻时,随着温度的变化电阻值在一定范围内变化,其额定电阻值R、按式(2)计算,测量 时应测试5次取平均值
GB/36955一2018 -盏 R aT一25 式中 R 额定电阻值(已折算到25C),单位为欧(Q); 测量电阻值,单位为欧(n R, -电阻材料温度系数,单位为每开(K-'); 测量时的温度值,单位为摄氏度(C). 下标,表示第i次测量
5.1.2热态额定值(Rn 电阻热态额定值计算参见7.3.3,热态额定值与额定电阻值的高温偏差不应超过0%+10%
5.2电阻器的材料 电阻器宜选用片状合金材料,陶瓷盘式电阻材料
5.3无感化设计 电阻器应采用无感化设计
5.4绝缘水平 应符合GB/T31l.12012、GB/T305472014和GB/T50064中的规定 5.5充电电流 典型的充电电流参见附录C,电流包络线通常按指数衰减,应根据具体工程条件满足附录B所列的 充电电流峰值和冲击后稳态电流要求
5.6重复充电时间间隔 启动电阻应满足连续5次间隔0.5h再次充电的要求,5次以后可间隔2h再次充电
冲击能量耐受能力要求 5.7 应能耐受正常充电能量和短路时冲击能量最大值的两倍,交流网侧启动电阻还应耐受变压器励磁 涌流造成的冲击能量
5.8温升限值 主要电阻器材料在冲击能量下的温升要求见表1
表1主要电阻器材料的温升限值 电阻器型式 电阻器材料 电阻器最热点温升/K Cr20Ni30 小于550 Crl5Ni60 小于600 片状 Cr23Ni60 小于550 Ni25Cr2oMo5 小于550 圆盘式 小于12o 陶瓷材质
GB/T36955一2018 5.9爬电距离() 爬电距离应根据爬距计算电压和爬电比距确定,如式(3)所示
,=×U 式中 爬电比距,单位为毫米每千伏(mm/kV). l 爬距计算电压,单位为千伏(kV
U 5.10使用寿命 应不小于10000次或不小于40年使用寿命
设计和结构 6 6.1一般要求 启动电阻应为单相或单极、空气自然冷却、户外或户内布置,设计时应考虑下列因素: 在运行、安装和维护期间的机械应力 a 在运行时的热应力; b 内部或外部故障对电阻器的电磁力; c d 风力,冰雪负荷; 抗震要求; e f 温度变化引起的机械应力影响
6.2结构设计 启动电阻一般为金属箱式或空心绝缘子型
完整的电阻器应包括电阻元件,连接件,支柱绝缘子和 固定件
固定件应便于与基础连接并有接地孔 设计时应考虑现场安装、更换、检查和维护方便
电阻器和/或电阻器模块应配备起吊孔,以便安装 及替换
外壳及内部的金属支架不应出现电位悬浮
所有接线应可靠,并且规范
电阻器设计应考虑 发热对设计裕度的影响,按GB/T311.12012中3.3进行校验,以满足热空气对绝缘的影响
金属箱式电阻器、金属构架应有良好的防腐蚀层,外罩应采用耐腐蚀性好的材料
电阻器钢框架最 低要求应为镀锌钢
侧面,顶蓬、防鸟保护的盖板以及电阻器排气网应采用不锈钢,最低要求应为AI SI316或等效的钢材
每个电阻器的两个相对的面板应装有活叶 空心绝缘子型电阻器,应采取必要措施以便查看内部情况 对于电阻元件采用陶瓷材料的电阻器,应采用可靠的陶瓷电阻,形状为圆饼状,侧面覆涂绝缘漆,两 平面喷铝做电极连接
电阻片串联安装在复合绝缘套管中 -端应有弹性机构提供必要的压接力
对于内部电阻元件与外罩相连的电阻器,应采取必要措施,以便测量套管与外罩之间的电阻值
对 于空心绝缘子型电阻器及串联的电阻器段,应采取必要措施,以便测量每一段的电阻值
6.3电阻器模块 每个模块的额定电阻值应从整相电阻器或整极电阻器额定电阻值计算得到,计算公式见式(4)
R、 RNn ***** (4 式中 R、 电阻器模块的额定电阻值,单位为欧(Q);
GB/36955一2018 R 整相电阻器或整极电阻器额定电阻值,单位为欧(Q); 电阻器模块串联数
电阻器模块阻值的公差水平和整相电阻器或整极电阻器阻值的公差水平相同
6.4电阻元件 电阻元件的要求如下: 应确保在各种工作电流下电气和机械性能稳定可靠; a b 电阻材料应采用抗氧化、耐腐蚀、耐高温、温度系数低加工性能好的合金材料 c 应采用无感制作工艺; d 电阻元件之间连接应可靠; 电阻元件的支撑和固定应采取措施,以消除高温对其产生的影响
6.5保护 应通过启动电阻回路电流测量装置对启动电阻充电电流、冲击能量等进行监测,保护定值整定应充 分考虑保护动作时间和交流断路器跳闹延时等因素的影响
6.6电阻材料 不应被潮气和含有酸碱性质成分的空气所腐蚀 6.7支撑绝缘子和箱体套管 电阻器支撑绝缘子和箱体套管应能承受所在位置的电压,并能满足机械强度和爬电距离要求
6.8屏蔽装置 金属箱式和空心绝缘子型电阻器应根据运行电压等级安装适当的屏蔽装置,满足防电晕设计要求
6.9端子 电阻器接线端子的载流量应满足要求,方便连接,并保证足够的机械强度
接线端子耐受机械荷载的能力应满足:静态安全系数不小于2.75,动态安全系数不小于1.67
6.10外壳防护等级 金属箱式电阻器外壳应符合GB/T4208一2017中第5章和第6章的规定,一般宜为IP23级
空心绝缘子型电阻器,应采取密封设计
6.11焊接 焊接应避免虚焊,裂缝及其他任何缺陷
由焊接相连的钢板应精确地按尺寸要求切割,并靠压力连续地将焊件的棱边滚轧成合适的曲率半 径
切割钢板和其他材料在进行焊接时不应产生任何弯曲
进行焊接的棱边的尺寸和形状应足以允许 完全融熔和全部熔焊,而且钢板的棱边应严格地成形,以使之能适应于各种焊接条件
应提供认可的焊接工艺,最好的材料,焊条和焊接的非破坏性试验
6.12铭牌 每台电阻器应提供不受气候影响的材料制成的铭牌,并安装在明显可见的位置
铭牌上应标出下 述各项,且应用耐久的方法制出(如用蚀制、雕刻和打印法)
GB/T36955一2018 制造厂商及商标; a b 产品型号及名称; e 额定电阻值,Q.R、/n; 制造偏差 d 热态电阻.Q; e f 冲击能量,J 质量,kg; 日 h 材质; 产品编号; N 制造日期 型式试验 7.1概述 型式试验是为了确定电阻器在设计和制造方面是否满足本标准中所规定的性能和要求
所有试验应在同一电阻器模块上进行
除非另有规定,拟用来做型式试验的电阻器应为出厂试验 合格的电阻器
同一试品全部试验合格后,才能判定通过试验
7.2型式试验项目 型式试验包括 电阻值测量; a b) 电感值测量; 温升试验 c a 绝缘试验; 抗震试验; e D 无线电干扰电压试验; 防护等级检查; g hh 冲击能量试验; 冲击电流试验; 特殊试验
7.3电阻值测量 7.3.1概述 用准确度0.5级的仪器测量电阻器阻值
7.3.2冷态额定值 受试电阻器在环境空气中放置一段时间,当其温度与环境空气温度之差不超过2K时,用准确度 0.5级仪器测量两出线端间电阻值RaM.a,,测量5次,将所测数据按式2)折算为25C时的电阻值,其 值均应在规定的公差范围之内
温升试验和冲击能量/电流试验前后电阻值的变化应不超过士2%,计算见式(5)
Ran应 5 1)×100%<2% R0
GB/36955一2018 式中: 温升试验前阻值折算值,单位为欧(n); Reld.n,b R
温升试验后阻值折算值,单位为欧(Q).
eod.n 7.3.3热态额定值 温升试验中每个通电周期结束时,及冲击能量/电流试验中一次冲击能量后,均应测量电阻器两端 电压U及流过的电流1按式(6)算出热态额定值,再按式(2)折算为25C时的电阻值
Ues 6 n" hol,n Ite6 式中 U -试验电压,单位为伏(V); est 试验电流,单位为安(A); Ite 改接线后并联组倍数 m 电阻器热态额定值应符合5.1的规定
7.4电感值测量 在工频频率下测量残余电感值
7.5温升试验 7.5.1概述 温升试验可在电阻器模块上进行,试验电阻器的安装条件与实际状态尽可能一致,并应在接近无风 的环境下进行,电阻器本身发热引起的气流除外
如果试验电源输出电压有限制,可改变受试设备内部接线方式,如将串联连接改成并联连接,应保 证通过电阻元件的电流不变,总功率不变,保证温升试验的等效性
改接线后的电阻值和试验电流值会 改变,计算受试设备的电阻器热态额定值时,应根据改线情况进行换算
试验时,将电阻元件与外罩连接线断开,外壳接地,试验结束后,受试设备恢复原状态
交流侧启动电阻宜采用交流电流试验,直流侧启动电阻宜采用直流电流试验
7.5.2试验程序 环境温度测量采用温度计,其余各处温度测量采用热电偶或红外线测温仪,应采取措施防止温度计 或热电偶受热气体的影响
每次通电后,冷却30min再次通电;共通电5个周期,记录每次的启动电阻温升
启动电阻需满足 连续5次间隔0.5h再次充电的要求,5次以后可以间隔2h再次充电
每个周期分为3个阶段如图1所示 第一阶段;试验电流按照模拟不小于2倍冲击能量w的等效电流I,试验时间T为冲击电流 a 时间(一般不大于10s),应根据式(7)确定等效试验电流
1"R、d>2×w 第二阶段;试验电流按照不小于技术参数的2倍的冲击后稳态电流执行,试验时间T为持续 b 充电电流时间(一般不小于60) 第三阶段:冷却301 min
GB/T36955一2018 电流 连续做5个 周期 不<10s T>60 =30min" 第2个周期 图1温升试验示意图 测量温升的时间包括但不限于以下时间点 第 -阶段结束前时刻; a 第二阶段开始前时刻 b 第二阶段结束前时刻
测温点应包含,但不限于下列各点 电阻元件,测温点位于中间元件上端位置; a b 内部绝缘子,电阻箱内上端绝缘子外表面; 套管,电阻箱内套管外表面; 电阻元件的金属支撑件,支撑件中部上端位置; 排出空气,百叶窗中部上端位置; 顶蓬,中间位置; 空心绝缘子型电阻的电阻材料表面(仅空心绝缘子型电阻器适用); g h)环境温度,距离受试设备约1m处
7.5.3温升试验的判定 温升试验前后电阻值变化应符合7.3.2的规定
电阻元件的温升,不超过设备所用材料允许工作温度,就认为试验合格
试验完毕,待冷却后,电阻元件没有龟裂和变形
电阻器放置足够长时间,待冷却到环温后,恢复到原接线,测量电阻值,并记录周围环境温度
电阻 值变化应符合7.3.2的规定
7.6绝缘试验 7.6.1概述 电阻器的绝缘试验分工频耐受电压试验、直流电压试验、雷电冲击电压耐受试验和操作冲击耐受电 压试验
试验时周围的大气条件和大气条件修正系数应该按GB/T16927.1一2011中4.2、4.3和4.4的 规定
端子间的绝缘耐受试验如试验设备有困难时,可使用现场情况一致充电试验替代
每次绝缘试 验前后,需测量电阻值5次,误差满足7.,3.2的要求
7.6.2 绝缘电阻值 试验采用2500V兆欧表,试验电压施加于电阻器引线端子与支架的接地端之间
GB/36955一2018 7.6.3工频耐压试验 7.6.3.1端子间 交流侧启动电阻端子间应进行工频耐压试验,试验在电阻器模块上,在容量允许的条件尽可能长时 间运行
试验电压按照式(8)确定
u U. -×k est 式中: U -电阻器两端间启动时承受的最大工频电压,单位为千伏(kV); -电阻器模块串联数; -电压不均匀分布系数,通常取1.051.1
也可采用等效原则,利用多个模块串联或模块内电阻元件进行试验,试验电压相应折算
试验期间试品应无闪络、无放电、泄漏电流无明显增大
7.6.3.2端子对外壳 交流侧启动电阻端子对外壳应进行工频耐压试验,试验在电阻器模块上进行,将电阻元件与外壳连 接线断开,试验电压加到高压出线端上,外壳接地
按GB/T16927.1一2011中第6章规定进行试验
试验电压升到规定的工频耐受电压值,持续时间1min
试验期间应无击穿也不发生闪络
试验电压(U)应按式(9)和式(10)确定
U 一×(电阻器中点与外壳连接 9 e= 艺 ×n 'k(电跟蒙中点不与外无逃接 10 Ue= 式中 U 电阻器工频耐压要求值(整相电阻器进出线端子间),单位为千伏(kV) 电阻器模块串联数; 电压不均匀分布系数,通常取1.05~1.1
试验期间试品应无闪络,无放电、泄漏电流无明显增大
对于空心绝缘子型电阻;在复合或瓷套管上进行试验
试验电压(U.)应按式(10)确定 7.6.3.3端子及外壳对地 交流侧启动电阻端子及外壳对地应进行工频耐压试验,试验在电阻器模块上进行,将电阻元件与外 壳等电位连接,试验电压加到任一出线端上
按GB/T16927.1一2011中第6章规定进行试验
试验 电压为电阻器对地工频耐压值
试验电压升到规定的工频耐受电压试验值,持续时间1min. 试验期间试品应无闪络、无放电、泄漏电流无明显增大
7.6.3.4模块间 采用多模块串联的交流侧启动电阻应进行模块间工频耐压试验,试验在多个电阻器模块上进行,试 验电压加到模块间绝缘子上
试验电压升到规定的工频耐受电压试验值,持续时间1min.
GB/T36955一2018 试验期间试品应无闪络、无放电、泄漏电流无明显增大
7.6.4直流耐压试验 7.6.4.1 端子间 直流侧启动电阻端子间应进行直流耐压试验,试验在电阻器模块上,在容量允许的条件尽可能长时 间运行
试验电压按照式(1l)确定
Uae Ue ×k 11 式中 U -电阻器两端间启动时承受的最大直流电压,单位为千伏(kV); 电阻器模块串联数; 电压不均匀分布系数,通常取1.051.1 也可采用等效原则,利用多个模块串联或模块内电阻元件进行试验,试验电压相应折算
试验期间试品应无闪络、无放电、泄漏电流无明显增大 端子对外壳 7.6.4.2 直流侧启动电阻应进行端子对外壳直流耐压试验,试验在电阻器模块上进行,将电阻元件与外壳连 接线断开,试验电压加到高压出线端上,外壳接地
按GB/T16927.1一2011中第5章规定进行试验
试验电压升到规定的直流耐受电压值,持续时间1" min
试验期间应无击穿也不发生闪络
试验电压(U)应按式(12)和式(13)确定
12 一×k(电阻器中点与外壳连接 Uet =2Xn "xA心阻谢中点不与外布连接" (13 Ua一 式中 电阻器直流耐压要求值(整极电阻器进出线端子间),单位为千伏(kV); 电阻器模块串联数; 7 电压不均匀分布系数,通常取1.051.1
试验期间试品应无闪络、无放电、泄漏电流无明显增大
对于空心绝缘子型电阻;在复合或瓷套管上进行试验
试验电压(U)应按式(13)确定
7.6.4.3端子及外壳对地 交流阀侧启动电阻和直流侧启动电阻应进行端子对外壳直流耐压试验试验在电阻器模块上进行
将电阻元件与外壳等电位连接,试验电压加到任一出线端上
按GB/T16927.1一2011中第5章规定 进行试验
试验电压为电阻器对地直流耐压值
试验电压升到规定的直流耐受电压试验值,持续时间1nmin. 试验期间试品应无闪络、无放电、泄漏电流无明显增大
7.6.4.4模块间 采用多模块串联的交流阀侧和直流侧启动电阻应进行模块间直流耐压试验,试验在多个电阻器模 块上进行,试验电压加到模块间绝缘子上
10
GB/36955一2018 试验电压升到规定的直流耐受电压试验值,持续时间1min. 试验期间试品应无闪络,无放电、泄漏电流无明显增大
7.6.5雷电冲击耐压试验 7.6.5.1端子间 试验在电阻器模块上进行,将试验电压加到高压出线端,低压出线端接地
试验方法按 GB/T16927.1一2011中第7章规定进行试验
电压波形采用标准雷电冲击波,即1.2/50!s,试验次数;半电压下正、负极性各1次;全电压下正、 负极性各15次
试验期间试品应无闪络、,无放电、泄漏电流无明显增大
试验电压(Ue)应按式(l4)确定
U ek U (14 ×k 式中: U -电阻器两端间雷电冲击电压,单位为千伏(kV); pak 电阻器模块串联数; 电压不均匀分布系数
7.6.5.2端子对外壳 试验在电阻器模块上进行,将试验电压加到高压出线端,外壳接地
试验方法按GB/T16927.1 2011中第7章规定进行试验 电压波形采用标准雷电冲击波,即1.2/504s,试验次数;半电压下正、负极性各1次;全电压下正、 负极性各15次
试验期间试品应无闪络,无放电、泄漏电流无明显增大
试验电压(U.)应按式(15)和式(16)确定
Upenk U ×(电阻器中点与外壳连接 et D 2×n U A 16 U一 ×k(电阻器中点不与外壳连接) 式中 U. 电阻器两端间雷电冲击电压,单位为千伏(kV). 电阻器模块串联数; 电压不均匀分布系数
7.6.5.3端子及外壳对地 试验在电阻器模块上进行,电阻器所有箱体与出线端子短接,将试验电压加到任一出线端
试验方 法按GB/T16927.1一2011中第7章规定进行试验
电压波形采用标准雷电冲击波,即1.2/50As,试验次数:半电压下正,负极性各1次;全电压下正、 负极性各15次
试验电压为电阻器对地雷电冲击耐压值
试验期间试品应无闪络,无放电、泄漏电流无明显增大
7.6.5.4模块间 采用多模块串联的启动电阻应进行模块间雷电冲击耐压试验,试验在多个电阻器模块上进行,试验 11
GB/T36955一2018 电压加到模块间绝缘子或空气间隙上
试验方法按GB/T16927.1一201l中第7章规定进行试验
电压波形采用标准雷电冲击波,即1.2/50s,试验次数:半电压下正、负极性各1次;全电压下正、 负极性各15次
试验电压应根据接线方式确定
试验期间试品应无闪络、无放电、泄漏电流无明显增大
7.6.6操作冲击耐压试验 7.6.6.1端子间 试验在电阻器模块上进行,将试验电压加到高压出线端,低压出线端接地
试验方法按 GB/T16927.1一2011中第8章规定进行试验
电压波形采用标准操作冲击波,即250/2500s,试验次数:半电压下正、负极性各1次;全电压下 正,负极性各15次
试验期间试品应无闪络、无放电、泄漏电流无明显增大
试验电压(U.)应按式(17)确定
Ue (17 U 式中: 电阻器两端间操作冲击电压,单位为千伏(kV). U Dcak 电阻器模块串联数; n 电压不均匀分布系数
7.6.6.2端子对外壳 试验在电阻器模块上进行,将试验电压加到高压出线端,外壳接地
试验方法按GB/T16927.1 2011中第8章规定进行试验
电压波形采用标准操作冲击波,即250/2500!s,试验次数:半电压下正,负极性各1次;全电压下 正负极性各15次
试验期间试品应无闪络、无放电、泄漏电流无明显增大
试验电压(U)应按式(18)和式(19)确定
U 18 ×k(电阻器中点与外壳连接 Ue U ×k(电阻器中点不与外壳连接 Jest= 式中 U 电阻器两端间操作冲击电压,单位为千伏(kV); peak 电阻器模块串联数; 电压不均匀分布系数
7.6.6.3端子及外壳对地 试验在电阻器模块上进行,电阻器所有箱体与出线端子短接,将试验电压加到任一出线端
试验方 法按GB/T16927.1一2011中第8章规定进行试验
电压波形采用标准操作冲击波,即250/25004s,试验次数:半电压下正,负极性各1次;全电压下 正,负极性各15次
12
GB/36955一2018 试验电压为电阻器对地操作冲击耐压值
试验期间试品应无闪络,无放电、泄漏电流无明显增大
7.6.6.4模块间 采用多模块串联的启动电阻应进行模块间操作冲击耐压试验,试验在多个电阻器模块上进行,试验 电压加到模块间绝缘子和空气间隙上
试验万法放G8/TI271一中第8章规定进行试怕
电压被形采用标准操作冲击波,即250/25004s,试验次数半电压下正、负极性各1次;全电压下 正,负极性各15次
试验电压应根据接线方式确定 试验期间试品应无闪络,无放电、,泄漏电流无明显增大
7.7抗震试验 试验宜按GB/T13540的规定进行
电阻器应能承受规定地震烈度的作用而不损坏
可模拟产品结构进行抗地震性能的计算分析,以验证电阻器的抗震性能
7.8无线电干扰电压试验 本项试验仅适用于高压端对地爬距计算用电压为126/及以上的电阻器
试验按GB/T11022一2011中6.3规定进行,无线电干扰电压不大于2500AV 7.9外壳防护等级检查 按GB/T4208一2017中第12章和第13章的规定进行,应满足6.10的规定
7.10冲击能量试验 按照技术协议的冲击能量要求,对电阻器施加瞬时能量(不小于冲击能量要求),通电时间不大于 3s
冲击能量试验可与标准中规定的热态电阻值计算一起进行 对电阻器用红外线测温设备测量,测点不少于5点,测量点需包括但不限于以下点
实际电阻元件; aa b) 内部绝缘子; 套管; c d)电阻网的金属支撑材料(如有) 顶棚 e 排出空气 f 环温
g 试验中测量箱体及帽子的温度(金属电阻),记录冲击时和冲击后30min内温度变化
观察电阻片 的表现
试验后检查电阻片的状况,应无龟裂和变形金属电阻),应无烧灼现象(陶瓷电阻),颜色应无 明显变化 非金属电阻可根据要求在电阻片或比例单元上进行型式试验
试验之前及之后均应对电阻值进行测量,前后测量电阻值改变应不超过土5%
电阻元件的温升,不超过设备所用材料允许工作温度
试验后按式(6)计算热态额定值R.a,并折算为25时的电阻值,其值应符合5.1的规定
13
GB/T36955一2018 7.11冲击电流试验 对电阻器施加不小于充电电流峰值的试验电流,试验时间不小于ls
通电时间内电阻吸收能量达 最大冲击能量要求,则该试验可与能量冲击试验合并进行
对电阻器用红外线测温设备测量,测点不少于5点,测量点需包括但不限于以下几点 实际电阻元件 a b 内部绝缘子; 套管; c d 电阻网的金属支撑材料(如有); 顶棚 e 排出空气 fD) 环温 g 试验中测量箱体及帽子的温度金属电阻),记录冲击时和冲击后30min内温度变化
观察电阻片 的表现
试验后检查电阻片的状况,应无龟裂和变形(金属电阻),应无烧灼现象陶瓷电阻),颜色应无 明显变化
试验之前及之后均应对电阻值进行测量,前后测量电阻值改变不应超过士5%
电阻元件的温升,不超过设备所用材料允许工作温度
8 出厂试验(例行试验 8.1概述 交货前对每一台电阻模块进行出厂试验
8.2出厂试验项目 包括 外观及一般检查; a 额定电阻值测量 b) 电感值测量; c d 工频耐压试验(交流侧启动电阻); 直流耐压试验(交流侧阀侧启动电阻和直流侧启动电阻)
e 8.3外观及一般检查 包括 a 电阻器外观不应有明显划痕和变形 b) 铭牌应牢固,参数正确; 观察门应关闭灵活,紧固件无漏装,无松动; c 套管、,绝缘子表面应无损伤,绝缘子的质量应符合产品标准的质量要求 d 8.4额定电阻值测量 根据电阻值的大小,选取合适的测试仪器进行测量,通常用准确度0.5级的仪器测量电阻值R, 用温度计记录试品所处地点的环境温度
将所测数据按式(2)折算为25C时的电阻值,其值应符合规定要求
14
GB/36955一2018 8.5电感值测量 按7.4进行
8.6工频耐压试验 按7.6.3进行
8.7 直流耐压试验 按7.6.4进行
现场试验 9.1概述 为确保投运前的可靠性,电阻器安装后,应进行现场交接试验
9.2现场试验项目 包括: 外观及一般检查; a b额定电阻值测量; c 工频耐压试验(可结合现场试验条件决定是青进行此试验) d)直流耐压试验(可结合现场试验条件决定是否进行此试验》 9.3外观及一般检查 包括 电阻器外观不应有明显变形; aa b 套管、绝缘子表面应无损伤,应符合各自产品标准的要求 按图纸检查总体安装应正确,接线应可靠 c d 电阻器内部应无杂物
9.4额定电阻值测量 应在工频频率下对电阻值进行测量,所得结果考虑温度校正值之后应在规定的误差范围之内
需 现场进行绝缘电阻测试
g.5工频耐压试验 按7.6.3进行
9.6直流耐压试验 按7.6.4进行
10 包装、贮运、安装,运行及维修和技术资料 10.1包装 电阻器的外包装应坚固,牢靠,适于长途运输,能多次搬运和装卸,并在包装箱的侧面以运输常用的 15
GB/T36955一2018 标记和图案标明起吊位置,以便于装卸搬运
标志应清晰整齐,并保证不因运输或贮存长久而模糊不 清,标志应有下列内容: 工程名称/合同号; a b 到货地址; c 收货人 d 货物及部件名称; 箱号/件号; e fD 毛重/净重(千克); 体积(长×宽×高,以毫米表示); 8 h)包装箱上应明显地标有“小心轻放”“向上”“防雨”等字样或标记
对需单独运输的电阻器用零部件应装人完好的包装箱内
10.2贮运 电阻器运输过程中不得受剧烈冲撞,不得倒置,应防止外力损伤
0.3安装 如果电阻器不是组装后发运的运输单元应当清晰地加以标记,并有总装图样和零部件明细 应有安全开箱和起吊所需资料 a) b)应按安装使用说明书规定程序就位 安装后检查应符合9.3和9.4的规定 c 10.4运行及维修 运行前应按第9章进行现场试验,应按制造厂提供的安装使用说明书要求,在停电检修期间对设备 清理检查,并做好记录
0.5技术资料 包括 装箱清单 a b) 产品合格证; 出厂检验报告; c 支柱绝缘子、套管的检验报告; d 安装使用说明书; e 图纸资料
f 16
GB/36955一2018 附 录 A 资料性附录 启动电阻位置示意图 -般应在交流侧配置启动电阻,位置可选为联接/换流变压器网侧或阀侧
根据系统研究可配置直 流侧启动电阻
双极接线和对称单极接线下启动电阻可选安装位置示意如图A.1和图A.2所示
直流侧极线启动电阻 极线 子模块阀级 桥臂电抗器 换流变压器 十- 网侧启动 阀倒启动 电阻 电阻 直流侧中性母线 启动电阻 金属回线或接 中性母线 换流器 地极线路 直流侧中性母线 启动电阻 子模块阀级 桥臂电抗器 换流变压器 闵侧启动 网侧启动 电阻 电阻 极线 直流侧极线启动电阻 图A.1 双极接线启动电阻的布置示意图 17
GB/T36955一2018 直流侧极线启动电阻 极线 子模块阀级 桥臂电抗器 联接变压器 阀侧启动 网侧启动 电阻 电阻 直流侧极线启动电阻 极线 换流器 图A.2对称单极启动电阻位置示意图 18
GB/36955一2018 附录 B 资料性附录 电阻器典型设计参数 电阻器典型设计参数如表B.1所示
表B.1电阻器典型设计参数 序号 名称 单位 招标人要求值 投标人保证值 结构型式或型号 冷却方式 额定阻值(25C" 电阻值允许偏差 % 电阻值温升偏差 mH 最大电感值 充电电流(峰值 冲击后稳态电流(持续60s)(有效值 冲击能量 M0 冲击能量持续时间 ms 最高运行电压(端子间和端对地》 k 操作冲击(端子间 k 操作冲击(端对地 k 雷电耐受(端子间 kV 10 雷电耐受(端对地 kV kv 工频耐压(端对地 11 工频耐压(端子间) k 12 具有较长持续时间的工频过电压(端对地 k kV 直流耐压(端对地) 1 直流耐压端子间 kV 14 具有较长持续时间的直流过电压端对地 kV 15 最小爬电比距 mm/kV 极线端子载荷 水平纵向分量 16 垂直分量 N 水平横向分量 弯矩 Nm 17 电阻器组件数 18 钢材型号AISI,成分表示 19
GB/T36955一2018 表B.1续 单位 招标人要求值 投标人保证值 序号 名称 温升试验下的热点温升/平均温升 19 冲击能量下温升 20 21 电阻元件材料有效质量 kkg 22 钢材型号AISI,成分表示 20
GB/36955一2018 录 附 C 资料性附录 启动电阻典型充电电流波形 交流侧启动电阻典型充电电流波形如图C.1和图C.2所示
肩动电阻电压R 400 00 200 00 0 一100- -200 -300 -400 启动电阻电流R 0.060 0.040 0.020 0.000 S -0.020 -0.040 -0.060 启动电阻平均功率PR 9.0 美 0. 肩动电阻平均能量ER 12.0 0.0 8.0 6.0 4.0 2.0 0.0 0.0 2.0 4.0 6.0 8.0 10.0 12.C 14.0 图c.1一侧换流站单独充电过程 21
GB/T36955一2018 启动电阻电压lR 400 0o 00 100 0 2 一100 --200 -300 -40o 启动电阻电流/R 0.060 0.040 0.020 0.000 黑 -0.020 一0.040 一0.060- 启动电阻平均功率R 9.0 0.0 启动电阻平均能量R 2.0 10.0 8.0 6.0 4.0 2.0 0.0 6.0 8.0 10.0 12.0 0.0 4.0 图C.2一侧换流站充电未完成时另一侧开始充电过程 直流侧启动电阻典型充电电流波形如图C.3所示 22
GB/36955一2018 启动电阻电压R 600 500 400 300 200 100 肩动电阻电流/R 0.60 0.50 0.40- 0.30 0.20 0.10- 0.00 启动电阻平均功率R. 300 250 200 150 100 50 启动电阻平均能量ER. 7.0 6.0 5.0 4.0 3.0 2.0 1.0 0.0 2.00 2.25 2.50 2.75 3.00 3.25 3.50 3.75 4.00 图C.3直流侧启动电阻典型充电电流波形
柔性直流输电用启动电阻技术规范GB/T36955-2018解读
随着能源消费结构的调整和环境保护意识的提高,清洁能源在全球范围内得到了广泛关注和推广。而柔性直流输电技术作为一种高效、可靠、安全的能源传输方式,正逐渐成为未来低碳经济发展的趋势和重要方向。
柔性直流输电系统的运行离不开启动电阻这一关键技术,其主要作用是限制直流电路的初始电流,在稳态时自动消除。同时,启动电阻还能起到保护电源、减小对地干扰、降低设备损坏风险等作用。
因此,为了规范柔性直流输电用启动电阻的设计、制造和应用,国家质量监督检验检疫总局和国家标准化管理委员会于2018年正式发布了《柔性直流输电用启动电阻技术规范GB/T36955-2018》。
该规范主要从启动电阻的基本原理、结构特点、选型及安装等方面进行了详细阐述,并提出了相应的技术要求和测试方法。其中涉及到的关键指标包括启动电阻的额定电流、耐压能力、温度特性、稳态电阻值等,以确保其在柔性直流输电系统中的稳定运行。
此外,该规范还强调了启动电阻在实际应用中需要注意的问题,例如对电路影响的分析和评估、与其他电器设备配合使用的技术要求等。同时,针对不同类型和功率的柔性直流输电系统,规范也给出了相应的适用范围和参数要求。
可以说,该规范的出台将有助于推动我国柔性直流输电技术的发展和应用,提高其在清洁能源领域中的竞争力和地位。未来,随着柔性直流输电系统的规模和应用范围的不断扩大,启动电阻技术也将得到持续的发展和完善。
总之,柔性直流输电用启动电阻技术规范GB/T36955-2018的发布标志着我国在该领域规范建设上取得了重要进展,为相关企业和机构提供了可靠的技术依据和参考标准,对于加速清洁能源产业的发展和推广都具有重要意义。