GB/T37400.8-2019
重型机械通用技术条件第8部分:锻件
Heavymechanicalgeneraltechnicalspecification—Part8:Forgings
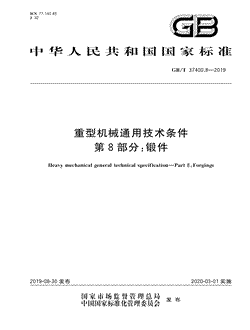
- 中国标准分类号(CCS)J32
- 国际标准分类号(ICS)77.140.85
- 实施日期2020-03-01
- 文件格式PDF
- 文本页数11页
- 文件大小791.24KB
以图片形式预览重型机械通用技术条件第8部分:锻件
重型机械通用技术条件第8部分:锻件
国家标准 GB/37400.8一2019 重型机械通用技术条件 第8部分锻件 lspeeifieatio一Part8.rForginS Heavy mechaniecalgeneraltechnical 2019-08-30发布 2020-03-01实施 国家市场监督管理总局 发布 币国国家标准化管理委员会国家标准
GB;/T37400.8一2019 目 次 前言 范围 2 规范性引用文件 订货要求 制造工艺 技术要求 6 检验规则和试验方法 复试和重新热处理 质量证明书 8 标识和包装 --+
GB;/T37400.8一2019 前 言 GB/T37400《重型机械通用技术条件》分为16个部分 第1部分:产品检验; 第2部分:火焰切割件 第3部分;焊接件; 第4部分:铸铁件; 第5部分:有色金属铸件 第6部分;铸钢件; 第7部分;铸钢件补焊 第8部分;锻件 第9部分;切削加工件 第10部分:装配 第11部分配管 第12部分;涂装; 第13部分;包装; 第14部分;铸钢件无损检测 第15部分;锻钢件无损检测 第16部分液压系统
本部分为GB/T37400的第8部分
本部分按照GB/T1.12009给出的规则起草
本部分由机械工业联合会提出
本部分由全国大型铸锻件标准化技术委员会(SAc/Tc506)归口、全国冶金设备标准化技术委员 会(sAc/TC409)副归口
本部分起草单位;一重集团大连工程技术有限公司,一重集团有限公司、二重德阳)重型装备 有限公司、中冶陕压重工设备有限公司,太原重型机械集团有限公司、重型机械研究院股份公司、上 海电气上重铸锻有限公司
本部分主要起草人;杨晓鸥、张苏星、李雪民、冯敬、刘亚军,宋国旺、苏静、王晓芳,刘震、王兴齐、 徐赛、,邵鞠民、陈杰、马建平、张辉、张江伟包杭、王霞
GB;/T37400.8一2019 重型机械通用技术条件 第8部分;锻件 范围 GB/T37400的本部分规定了一般用途大型锻件的订货要求、制造工艺,技术要求、检验规则和试 验方法,复试和重新热处理质量证明书及标识和包装
本部分适用于液压机和锻锤自由锻造的碳素结构钢和合金结构钢大型锻件的订货,制造与检验
其他材料的锻件也可参照使用 规范性引用文件 下列文件对于本文件的应用是必不可少的
凡是注日期的引用文件,仅注日期的版本适用于本文 件
凡是不注日期的引用文件,其最新版本(包括所有的修改单)适用于本文件
GB:/T223(所有部分钢铁及合金化学分析方法 GB/T228.1金属材料拉伸试验第1部分:室温试验方法 GB/T229金属材料夏比摆锤冲击试验方法 GB/T231.1金属材料布氏硬度试验第1部分;试验方法 4336碳素钢和中低合金钢多元素含量的测定火花放电原子发射光谱法(常规法 T GB 6394金属平均晶粒度测定方法 GB 俐中非金属夹杂物含量的测定标准评级图显微检验法 GB 10561 GB/T20066钢和铁化学成分测定用试样的取样和制样方法 21469锤上钢质自由锻件机械加工余量与公差一般要求 GB 21470锤上钢质自由锻件机械加工余量与公差盘、柱、环,筒类 GB 锤上钢质自由锻件机械加工余量与公差轴类 GB 21471 33083大型碳索结构钢锻件技术条件 GB GB/T33084大型合金结构钢锻件技术条件 GB/T37400.1 重型机械通用技术条件第15部分;锻钢件无损检测 JB/T9179.1液压机上钢质自由锻件机械加工余量与公差第1部分;一般要求 JB/T9179.2液压机上钢质自由锻件机械加工余量与公差第2部分;圆轴、方轴和矩形截面类 JB/T9179.3液压机上钢质自由锻件机械加工余量与公差第3部分;台阶轴类 JB/T9179.4液压机上钢质自由锻件机械加工余量与公差第4部分:圆盘和冲孔类 JB/T9179.5液压机上钢质自由锻件机械加工余量与公差第5部分;短圆柱类 JB/T9179.6液压机上钢质自由锻件机械加工余量与公差第6部分;模块类 JB/T9179.,7液压机上钢质自由锻件机械加工余量与公差第7部分;简体类 JB/T9179.8液压机上钢质自由锻件机械加工余量与公差第8部分;圆环,筒节和法兰类 订货要求 3.1需方应在订货合同中写明锻件名称,执行的标准编号、锻件组别、材料牌号、相应的技术要求和检
GB/T37400.8一2019 验项目,交货状态和供货数量以及其他附加说明
3.2需方应提供零件图或粗加工图
3.3当需方提出本部分以外的特殊要求和补充要求(如高温强度、低温韧性、晶粒度、夹杂物、金相组织 等)时,应在订货时向供方提出,并经供需双方商定
制造工艺 4.1冶炼 锻件用钢应采用电炉冶炼或电炉、转炉冶炼并经炉外精炼处理,经需方同意也可采用保证质量的其 他方法冶炼
有无损检测要求的锻件应进行真空处理,对于仅进行表面无损检测的小件,无需真空处理 也能满足要求的可不进行
钢锭可根据具体产品要求,经供需双方商定,使用单真空锭、双真空锭、电渣锭等
4.2锻造 4.2.1钢锭的水口和冒口应有足够的切除量,以确保成品锻件无缩孔和严重的偏析
4.2.2锻件应在有足够压力的锻压设备上锻造成形,对钢锭的原始缺陷进行改善(如凝固缺陷焊合、夹 杂打碎等),以保证锻件内部质量
4.2.3用钢锭锻造时,未经徵粗者,其锻造比一般不小于3;经徵粗者,锻造比不小于2.5
法兰部分的 锻造比不小于1.7
当采用先进锻造方法时,其锻造比可适当减小
用锻材或轧材锻造时,锻造比一般 不小于1.5,法兰的锻造比不小于1.3
对于性能要求高、长期承受严重交变载荷或表面高接触应力和弯 曲应力的产品,经供需双方商定,其材料的纯净度,锻造比及组织的要求应相应提高
4.2.4锻件锻后以一定的方式进行锻后热处理,锻后热处理应考虑去除气的不良影响和为最终热处理 做组织准备
对于以锻后热处理作为最终热处理的锻件,要求热处理后应满足订货技术要求
4.2.5锻件的形状和尺寸应符合锻件图纸和技术要求
4.2.6锻造工艺应考虑锻造的均匀性
锻后热处理应考虑去除气的不良影响和为最终热处理做组织 准备
4.3热处理 锻件的最终热处理应按订货合同或图纸上规定的交货状态进行
在热处理后、交货前,按照订货图 纸的要求进行尺寸检查,并记录主要尺寸;所得的尺寸应在订货图纸规定的公差范围内
4.4机械加工余量 4.4.1根据订货图纸规定的尺寸与表面粗糙度确定机械加工余量
4.4.2液压机锻件的机械加工余量、公差,按JB/T9179.1JB/T9179.8的规定
需方有特殊要求者 按合同规定
4.4.3锤上锻件的机械加工余量、公差,按GB/T21469,GB/T21470,GB/T21471的规定
需方有特 殊要求者按合同规定
5 技术要求 5.1化学成分和力学性能 5.1.1碳素结构钢的牌号、化学成分及力学性能应符合GB/T33083的规定
规定元素成品化学成分
GB;/T37400.8一2019 允许偏差见表1
5.1.2合金结构钢的牌号、化学成分及力学性能应符合GB/T33084的规定
规定元素成品化学成分 允许偏差见表2
5.1.3其他材料锻件的牌号、化学成分及力学性能按相应标准的规定
表1碳素结构钢成品化学成分允许偏差 截面面积/em" 规定化学 元素 成分上限 650 >6501300 >1300~2600>26005200>5200l0400>l0400 值/% 超过规定值上限或下限的允许偏差值/% 0.25 士0.02 士0.03 士0.03 士0.04 士0,05 士0.05 >0.250.5o 士0.03 士0.0s 士0.04 士0.04 士0,06 士0.06 >0.50 士0.04 士0.05 士0,05 士0.06 士0.07 士0,07 <0.37 士0.02 士0.03 士0,04 士0.04 士0.05 士0.08 Si >0.37 士0.05 土0.06 士0.06 土0.07 士0.07 士0.09 <0.90 士0.03 士0.04 士0.05 士0.06 士0.07 土0.08 Mn >0.90 士0.06 士0.06 士0.07 士0.08 士0.08 士0.09 十0.002 十0.003 十0.004 S0,025 十0,002 +0,003 +0.004 s0.025 十0.002 十0.002 十0.003 十0.003 十0.004 十0.004 表2合金结构钢成品化学成分允许偏差 横截面面积/em 规定化学 元素 成分上限 <650 >650~1300 >1300260o>26005200>5200~10400>10400 值/% 超过规定值上限或下限的允许偏差值/% 0.30 士0.01 士0,03 士0,03 士0.04 士0,05 士0.05 >0.300.55 士0.02 ),05 十0.06 士0.04 士0.04 士0. 士0.,06 s0.37 士0.02 士0.03 士0.04 士0.04 士0.05 士0.06 S >0.371.4o 士0.04 士0.06 士0.06 士0.07 士0.07 士0,09 <1.00 士0.03 士0.04 士0.05 士0.06 士0.07 士0.08 Mn >l.001.90 士0.04 士0.06 士0.07 士0.08 士0.08 士0.09 十0.007 十0,007 +0.010 十0,010 s0,025 十0,005 十0,005 +0.005 S0,025 十0,005 十0,005 十0.005 十0.006 十0.006 ).05 士0.05 二0.90 士0.03 士0,04 士0 士0.06 >0.90~2.1o 士0.05 士0.06 士0.06 士0.07 士0.07 士0,08 >2.102.70 士0,10 士0.10 士0,12 士0.l4 士0.15 土0.16 <1.00 士0.03 士0.03 士0.03 士0.03 士0.03 士0.03 Ni >1.002.00 士0.05 士0.05 士0.05 士0.05 士0.05 士0.05 >2.004.50 士0.07 士0.07 士0.07 士0.07 士0.07 士0.07
GB/T37400.8一2019 表2(续 横截面面积/em 规定化学 元素 成分上限 650 >650~1300 >1300~2600>26005200>520010400>10400 值/% 超过规定值上限或下限的允许偏差值" /% 士0.01 0.30 士0,02 士0.02 士0,02 士0.03 士0,03 Mo >0.30~0.6o 士0.02 土00s 士0.04 士0.,04 士003 士003 >0.60~0.8o 士0.03 士0.04 士0,05 士0.,06 士0.07 士0.08 Nb s0.045 士0.02 士0.02 士0,02 士0,02 士0.03 士0,03 Ti s0.10 十0.02 十0.02 十0.03 十0,03 十0.04 十0.04 1.00 士0.04 士0.05 士0.05 士0,06 士0.06 士0,07 >l.001.20 士0.08 士0.09 士0.12 士0.10 士0,12 士0,14 A >0.70~1.10 士0,05 士0,05 士0.05 士0.,07 士0,07 士0,09 十0,01 0.10 十0.01 十0.,01 十0.01 十0.,01 十0.01 >0,100.30 士0.,03 士0.03 士0.03 士0,03 士0.03 士0.03 5.2表面及内部质量 5.2.1锻件表面不应有裂纹、缩孔、折叠、夹层、锻伤等缺陷,若有缺陷应按以下规定处理: 不需机械加工的锻件表面,,经修整后其最大深度不得超过该处尺寸的下偏差
a b) 需要机械加工的锻件表面,经测定,若锻件上剩余的单边机械加工余量不小于公称单边余量的 50%,则此缺陷可不清除;小于50%时应清除
裂纹、缩孔、折叠,夹层、锻伤等缺陷都应清除 锻件表面缺陷深度超过单边机械加工余量时,在需方同意的前提下可进行补焊,将缺陷清除后 应按供方的工艺规范实施补焊,补焊的质量应符合需方对锻件质量的要求
采用非机械方法去除锻件表面缺陷时,该处去除的尺寸及组织影响的深度均不应超过该锻件 d 的机械加工余量.否则应得到需方的同意 5.2.2发现有白点的锻件应予报废,且与该锻件同一熔炉号、同炉热处理的锻件均应逐件进行检查
5.2.3对锻件有超声检测、磁粉检测或渗透检测要求时,应在图纸或技术协议中注明无损检测方法、部 位和质量等级要求
检验规则和试验方法 6.1化学成分分析 6.1.1熔炼分析 6.1.1.1供方应对每炉(包)钢液进行熔炼分析,分析结果应符合相应标准的化学成分要求
对于多炉 合浇的大钢锭,应报告权重平均分析结果
6.1.1.2取样或试验不符合要求时,可在钢锭或锻件近表面适当部位取替代试样
6.1.2成品分析 需要时可在锻件上取样进行成品分析
圆盘件或其他实心件取自二分之一半径至外径之间的任一
GB;/T37400.8一2019 点,空心件或环件取自内,外表面之间的二分之一处,也可以取自力学性能试样上
成品分析可以代替 熔炼分析 6.1.3化学分析方法 化学成分分析方法应按GB/T223的规定,也可按GB/T4336的规定
化学分析用试样的取样和 制样方法应按GB/T20066的规定
6.2力学性能试验 6.2.1检验项目和取样数量 锻件的力学性能检验项目和取样数量按需方选定的锻件组别确定,见表3
表3检验项目和取样数量 抽样规定 锻件组别 组批条件 检验项目 硬度 力学性能 不检验 每批检验5%,但不少于 5件,同一锻件硬度差不超 同材料牌号,同热处 过40HBw,同一批锻件硬 硬度 理炉次,外形尺寸相 度差不超过50HIBW,试验 同或相近的锻件 件至少测一处,锻件较长或 形状复杂,则在锻件的头、 尾,中间各测一处 每件均受检验,硬度差不超 过40HIBW,锻件较长或形 硬度 单件 状复杂,在头、尾和中间各 测一处 每件均受检验,硬度差不超 每批抽检数量2%,但不得少 拉伸、 同材料牌号、同热处 过40HBW,同一批锻件硬 2件,同一锻件取一组试 冲击、 理炉次、外形尺寸相 度差不超过50HBw,锻件 样
需方有特殊要求时,可增 硬度 同或相近的锻件 较长或形状复杂,在头、尾 加试样数量 和中间各测一处 每件均受检验,硬度差不超 拉伸 取一组试样,逐件检验
需方 过40HBw,锻件较长或形 冲击、 单件 有特殊要求时,可增加试样 状复杂,在头、尾和中间各 硬度 数量 测一处 对于N、V组锻件,当力学性能作为验收指标时,则硬度不作为验收指标,仅用于检验零件硬度的均匀性
当硬 度必须作为验收指标时,应在图纸或技术文件中注明
除I组锻件在图纸中不需注明外,其余各组均应注明锻件组别
GB/T37400.8一2019 6.2.2取样位置和方向 6.2.2.1锻件的拉伸,冲击试样应取自锻件的延长部位(加长或加大部分). 6.2.2.2轴类,方形或长方形锻件,其拉伸、冲击试样方向应取轴向(纵向),当取横向或切向时,其力学 性能指标降低百分数应按表4的规定
空心简体、圆盘、环形锻件,其拉伸、冲击试样方向应取切向(圆 周方向 6.2.2.3实心轴类锻件的试样应取自距表面三分之一半径处,方形和长方形的锻件,取自截面对角线顶 点到中心的三分之一处(见图1). 6.2.2.4空心锻件的试样应取自二分之一壁厚处(见图2). 6.2.2.5圆盘锻件,当在外径加大部位取样时,试样应取自加大部位的二分之一高度处;当在加长部位 取样时,试样应取自距外缘三分之一半径处或至少距边缘20mm处(见图3). 6.2.2.6环形锻件,当在外径加大部位取样时,试样应取自加大部位二分之一高度处;当在加长部位取 样时,试样应取自二分之一壁厚处(见图4. 6.2.3试验方法 6.2.3.1常温拉伸试验应按GB/T228.1的规定
6.2.3.2冲击试验应按(GB/T229的规定
布氏硬度试验应按GB/T231.1的规定
6.2.3.3 6.2.3.4锻件的平均晶粒度的测定应按GB/T6394的规定
非金属夹杂物的测定应按GB/T10561 的规定
6.2.3.5锻件的超声检测、磁粉检测及渗透检测应按GB/T37400.15的规定
6.2.3.6当需方有高温强度、低温韧性,低倍组织及缺陷、其他夹杂物(非金属夹杂物除外)、金相组织、 残余应力等其他要求时,检验方法和验收标准应由供需双方商定
A向 加长部分 切向试样 卡工长 纵向试样 加长部分 2 纵向试栏 B向 加长部分 切向试样 子 纵试样 图1实心轴类、方形和长方形锻件取样位置
GB;/T37400.8一2019 切向试样 加长部分 纵向试样 图2空心筒体锻件取样位置 加大部分 加长部分 切向试样 切向试样 图3圆盘锻件取样位置 加长部分 加大部分 切向试样 切向试样 图4环形锻件取样位置 表4切向、横向力学性能指标降低量 1t一25t钢锭锻造锻件 >25t钢锭锻造锻件 锻造比 锻造比 力学性能 试样方向 35 5 指标降低量/% 切向 R 横向 切向 Ra(Rp2) 横向 切向 25 30 35 40 25 35 A 25 25 35 30 35 横向 40 20 20 35 30 35 切向 40 40 横向 20 20 35 30 35 40 切向 25 25 35 30 35 KU或KV 40 横向 25 25 35 30 35
GB/T37400.8一2019 复试和重新热处理 7.1在力学性能试验时,如果由于试验机故障,试样的制备不正确或试验的试样有缺陷,只要不是因裂 纹和白点而导致力学性能不符合要求,就允许重新取样试验,作为初次试验结果
7.2若拉伸试验中某一试验结果不合格,则可在原试样相邻部位取两个试样进行复试,两个试样的复 试结果应全部满足规定要求
7.3冲击试验复试应符合以下规定 a 当进行V型缺口冲击试验时,若一组冲击试样的试验结果不合格,可在原试样相邻部位再取 一组三个试样进行复试,前后两组试样的算术平均值不应低于规定要求,且单个值低于规定值 的个数不应多于两个,只能有一个单个值低于规定值的70% b 当进行U型缺口冲击试验时,若某一试验结果不合格时,可在原试样相邻部位取一组两个试 样进行复试,两个试样的复试结果应全部满足规定要求
复试后任何一项结果仍不合格时,锻件可以进行重新热处理,并重新取样试验
重新热处理次数 7.4 不得超过两次,回火次数不限
8 质量证明书 供方应向需方提供质量证明书,质量证明书至少应包括以下内容 合同号和图号 a 锻件名称; b 执行的标准编号和材料牌号; c 熔炼炉号和锻件标识号; d 锻件的实际尺寸和重量; e 热处理报告 f) 合同和图纸中规定的各种检验结果
8 标识和包装 9 g.1供方应在锻件上相当于钢锭水口端打印合同号、图号,熔炼炉号、锻件标识号和厂名等标识,并用 白漆圈上
9.2供方应对锻件表面进行适当保护,经机械加工的锻件表面应进行防锈和保护,以避免运输中损伤 和腐蚀
重型机械通用技术条件第8部分:锻件GB/T37400.8-2019解读
1. 引言
重型机械作为国民经济的重要支柱产业之一,锻件作为其主要零部件之一,在机械制造行业中扮演着不可替代的角色。针对锻件制造领域中存在的质量问题和生产效率低下等问题,我国推出了一系列技术标准和规范,其中重型机械通用技术条件第8部分——锻件GB/T37400.8-2019就是其中之一。
2. 锻件的基本概念
锻件是指通过金属材料在高温、高压下受力变形而成的一种常见的零部件。锻件具有密度高、组织细致、力学性能高、抗疲劳性好等优点,广泛应用于汽车、航空、航天、军工等领域。
3. GB/T37400.8-2019标准的主要内容
GB/T37400.8-2019标准主要涉及锻件制造的各个方面,包括材料、加工、热处理、检验等。其中,对于每种类别的锻件都有相应的技术要求和试验方法。
3.1 材料
该标准规定了锻件常用的几种材料,如碳素钢、合金钢、不锈钢、铝合金等。除此之外,还规定了材料的化学成分、机械性能要求等。
3.2 加工
在锻造过程中,需要考虑到一系列因素,如温度、变形量、变形速率、升降速度等。该标准明确了锻造的工艺参数和控制要求,保证了锻件的质量和性能。
3.3 热处理
热处理是影响锻件组织和力学性能的重要因素之一。该标准规定锻件的热处理工艺和参数,以及相应的试验方法,保证了锻件的硬度、韧性等性能指标。
3.4 检验
该标准规定了锻件检验的内容和要求,包括外观质量、尺寸偏差、缺陷检测、力学性能测试等。通过严格的检验,可以保证锻件的质量符合标准要求。
4. 锻件制造中的常见问题及解决措施
在锻件制造过程中,常见的问题有材料成分不符合要求、温度控制不当、加工变形量不一致等。针对这些问题,可以采取以下措施进行改进
4.1 材料问题
针对材料成分不符合要求的问题,需要加强材料的采购和检验。选用有品质保证的材料,并严格按照标准要求进行检验。
4.2 温度控制问题
温度对于锻造过程中的变形量、组织结构等都有着重要影响。因此,在锻造过程中需要加强温度控制,确保工艺参数的稳定性,避免出现温度偏差导致的问题。
4.3 加工变形量不一致问题
在锻造过程中,变形量需要保持一致,否则会对锻件的性能产生影响。应加强工艺参数的控制,确保变形量的一致性,可以采取自动化生产线的方式提高生产效率和质量。
5. 结论
GB/T37400.8-2019标准为锻件制造提供了一系列技术规范和要求,有助于提高锻件的质量和生产效率。实践证明,遵循该标准可以有效地解决锻件制造中常见的问题,提高锻件的可靠性和使用寿命。因此,制造企业应该认真学习并贯彻执行该标准。