GB/T28426-2012
大型超声波钢轨探伤车
Railflawdetectionvehicle
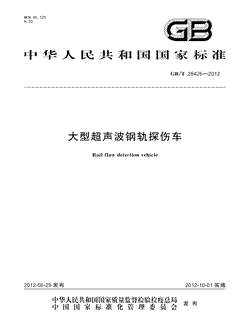
- 中国标准分类号(CCS)S22
- 国际标准分类号(ICS)45.120
- 实施日期2012-10-01
- 文件格式PDF
- 文本页数15页
- 文件大小441.23KB
以图片形式预览大型超声波钢轨探伤车
大型超声波钢轨探伤车
国家标准 GB/T28426一2012 大型超声波钢轨探伤车 Railflawdetectionvehicle 2012-06-29发布 2012-10-01实施 国家质量监督检监检疫总局 发布 国家标准花管理委员会国家标准
GB/T28426一2012 前 言 本标准按照GB/T1.1一2009给出的规则起草
本标准由铁道部提出 本标准由铁道部标准计量研究所归口
本标准主要起草单位:铁道科学研究院基础设施检测研究所、宝鸡南车时代工程机械有限公 司,铁道部标准计量研究所
本标准主要起草人:刘峰、张殿军,左荣森
GB/T28426一2012 大型超声波钢轨探伤车 范围 本标准规定了大型超声波钢轨探伤车的技术要求、检查与试验方法和检验规则等
本标准适用于大型超声波钢轨探伤车(以下简称钢轨探伤车)的设计、制造和检验
规范性引用文件 下列文件对于本文件的应用是必不可少的
凡是注日期的引用文件,仅注日期的版本适用于本文 件
凡是不注日期的引用文件,其最新版本(包括所有的修改单)适用于本文件 标准轨距铁路机车车辆限界 GB146.1 内燃机车制成后投人使用前的试验方法 GB/T3315 GB/T3766液压系统通用技术条件(GB/T3766-2001,eqvIso4413;1998 重型轨道车技术条件 GB/T10082 GB/T16904.1标准轨距铁路机车车辆限界检查第1部分;检查方法 铁路大型线路机械检查与试验方法 GB/T25336 JB/T10062超声探伤用探头性能测试方法 TB/T456机车车辆用车钩、钩尾框 铁道车辆车钩缓冲装置组装技术条件 TB/T493 机车轮对组装技术条件 TB/T1463 TB/T1491机车车辆油压减振器技术条件 TB/T1580新造机车车辆焊接技术条件 TB/T2340钢轨超声波探伤仪 重型轨道车试验方法 TB/T2769 铁道车辆用辗钢憋体车轮技术条件 TB/T2817 B/T2879.5铁路机车车辆涂料及涂装第5部分客车和牵引动力车的防护和涂装技术条件 车辆铆接通用技术条件 TB/T2911 B/T2945铁道车辆用LZ50钢车轴及钢坯技术条件 铁道机车年辆电子装置 TB/T3021 机车车辆阻燃材料技术条件 TB/T3138 TB/T3139机车车辆内装材料及室内空气有害物质限量 术语和定义 下列术语和定义适用于本标准
钢轨探伤车raillawdeteetiovehiele 采用超声波探测在役钢轨内部伤损,检测系统具有B型探伤图形显示、探伤数据存储和自动分析 功能,能够独立走行的铁路专用车辆
GB/T28426一2012 3.2 人工伤损检出deteetionm 对于试验线路中设置的人工伤损,探伤车检测产生正确的B型超声波显示图形和计算机辅助判别 伤损信息
3. 3 伤损误报talsenlarm 对于试验线路中确定的人工伤损以外的部分,探伤车检测生成错误的B型超声波显示图形并由计 算机辅助判别认定为伤损
3.4 人工伤损检出率deteetionrate 对试验线路的一次检测中,人工伤损检出数量与实际设置的人工伤损数量的比率
3.5 伤损误报率talsealarmrate 对试验线路的一次检测中,伤损误报数量与实际设置的人工伤损数量的比率
3.6 edetecetionrepeatabilit3 平均人工伤损检出率averageG 对试验线路进行多次检测,人工伤损检出率的平均值 3.7 平均伤损误报率averageftalsealarmrate 对试验线路进行多次检测伤损误报率的平均值
工作环境及性能要求 4.1工作环境要求 4.1.1环境温度 普通型一15一十40C a 低温型:一25C十40C b 4.1.2最高作业海拔高度;2500m
4.2线路条件 4.2.1标准轨距;1435 mm
4.2. 线路最大超高:180 mm
4.2. 线路最大坡度:33%
3 4.2.4最小通过曲线半径;140m. 4.2.5最小作业曲线半径;160 m 4.3性能要求 4.3.1最高自行速度:120km/h
4.3.2最高联挂速度;120km/h
最高检测速度:>60km/h
4.3.3 4 4.3. 轴重:<23t
GB/T28426一2012 技术要求 5.1 -般要求 55 1.1非作业状态时,外形尺寸应符合GB146.1的规定
. .1.2满足43kg/m一75kg/m在役钢轨的探伤作业需要
1.3零部件均应按经规定程序批准的产品图样及其他技术文件制造、采购和组装
5. 原材料及铸件、锻件应符合有关标准的规定
5. 1.4 55. 1.5焊接件焊缝的焊接、检查和验收应符合TB/T1580和产品图样的要求
重要焊缝应进行探伤 检查
1.6铆接结构质量应符合TB/2911的规定
5. 5. 1.7各安全保险及紧固零部件,如保险杆保护罩、,开口销、螺钉、保护链、保护用橡胶件等,均应齐全 有效
55 1.8油漆颜色、指示铭牌的位置应符合产品图样规定
涂装基本要求及检查验收应符合TB/T2879.5 的规定 55. 1.9动力学性能应符合GB/T10082的规定 5. .1.10运行操作位在驾驶室左侧
5.1.11 可双向行驶及检测
应配备保障运行安全的监控装置,如无线列调、机车信号、运行监控装置、轴温监测装置等 牵引性能、运行阻力,起动加速性能、冷却能力应符合GBy/T10082规定的要求 5.1.13 应按规定配备起复装置和灭火器,安全锤等安全用具
5.1.14 5.2动力传动系统 5.2.1采用柴油发动机提供牵引动力,功率应满足区间走行和作业的要求,平直线路上以最高自行速 度持续运行时发动机应无过热现象
55 2.2采用液力机械传动方式 5.2.3动力传动部件之间的联结应可靠,具有可靠的防松措施
传动轴应加装安全吊环等保险装置
5.2.4传动系统的各项要求应符合GB/T10082的相关规定
5 .2.5燃油箱的容量应满足连续运行1200km或24h的需要,并配备加油泵和易观察的油位显示 装置 5.3 车架 5.3.1车架强度性能应满足编挂在列车最后三辆运行的要求
采用带车钩缓冲装置的自动车钩,满足与标准车辆连挂的要求
5.3.2 车钩、钩尾框应符合TB/T456的规定
5.3.3 5.3. 车钩缓冲装置应符合TB/T493的规定
5.4车体和驾驶室 5. .4.1车体强度性能应符合设计要求,并满足探伤车运行和作业的要求
车体及外装设备应具有防雨、雪风、沙侵袭的能力
5 4 .2 55 .4.3钢轨探伤车两端均应设驾驶室,车顶两端安装旋转警示灯
车辆两端安装风喇叭,电喇叭,驾驶 位,副驾驶位均可操作
驾驶室设双向运行操作设备,操作方便、视野开阔
GB/T28426一2012 5.4.5驾驶室风挡玻璃采用安全玻璃,并设除霜、雨刮器和遮阳装置,雨刮器及喷水装置应动作灵活, 动作范围满足运行及作业要求
门窗应开启灵活,关闭严密,且牢固可靠
5.4.6内部装饰材料应符合TB/T3138及TB/T3139的规定
应设有温度调节装置
在41.1规定下,夏季高温时,室内温度应能保持在26C土2C;冬季 5.4.7 低温时,室内温度不应低于15c(发动机间除外)
空调器应具有除湿功能
厨房、卫生间应安装通风 设施
5. .4.8运行时驾驶室噪声应低于80dBA),探伤作业时探伤操作室噪声应低于78dB(A).
5 .4.9各指示仪表(指示灯)应齐全有效
5. .4.10日光直射或夜间关闭室内照明灯后,距仪表和指示灯500mm处,应能清楚的辨别仪表显示值 和灯光显示信号
5. .4.11夜间行车时,驾驶室照明灯关闭后,驾驶员应能进行正常的观察和操作
各指示灯和照明灯不 应使驾驶员对前方行车信号产生错觉 5.5走行系统 5.5.1 总体要求 总装后的走行系统应满足整车运行性能和作业性能要求
5.5.1.1 5.5.1.2采用两轴转向架,转向架上的悬挂装置和减震器应能有效地吸收振动和冲击 5.5.2部件要求 轮对应符合下列各项要求 5.5.2. a)车轴的材料及技术要求应符合TB/T2945及产品图样的相关规定 b)车轮的材料及技术要求应符合TB/T2817及产品图样的相关规定; 轮对组装应符合TB/T1463的有关规定,同轴左右轮径差不大于1 整机轮径差不大于 mm, 2mm, 3mm士3mm; ,轮对内侧距为1353 同一轮对上的减振器,其安装高度差不大于3 d mm 5.5.2.2轴承箱应符合下列各项要求 a)轴承箱的组装应符合有关标准及产品图样的相关规定; b 组装后的轴箱应转动灵活,无卡滞 e轴承箱的轴承部位温升不大于45C,最高温度不超过85C
5.5.2.3车轴齿轮箱应符合下列各项要求 a)车轴齿轮箱组装后,在台架试验时,各轴应转动灵活,无卡滞; b 车轴齿轮箱轴承部位温升不大于45C,最高温度不超过85C 5.5.3轮对轴箱、车轴齿轮箱台架试验 组装后的轮对轴箱,车轴齿轮箱都应进行台架试验,并符合下列各项要求 轮对台架试验转速相当于常用转速,试验时间为正反转各0.5h; a 磨合试验时无渗漏油及其他异常现象
b 5.5.4基础制动装置 基础制动装置应符合GB/T10082的相关规定
5.5.5油压减振器 应设有油压减振器,油压减振器性能应符合TB/T1491的规定
GB/T28426一2012 5.6制动系统 5.6. 1 制动系统应设置空气制动装置,还应设置驻车制动装置
制动系统性能应符合铁路有关规定 5.6.2空气压缩机的排量应符合探伤车运行制动的要求
在柴油机额定转速下,总风缸压力从0升到 800kPa士20kPa所需时间不大于5min
达到额定压力后,压缩机应有卸载装置
5.6.3空气制动系统应设置空气干燥,空气滤清、压力保护、压力控制、油水分离等辅助装置 5.6.4实施常规制动后,整机缓解时间应小于10s
5.6.5驻车制动装置,制动率不小于20%.
5.6.6单机在平直线路上以120km/h运行时,紧急制动距离不大于800m
制动时不擦伤车轮
5.6.7制动系统还应符合下列各项要求 a)制动系统的组装应在清洁干净的环境中进行,组装完后应进行泄漏试验; b 制动机或各阀体装车前应在试验台上逐台进行单件性能试验 系统的压力应能监控和显示,各仪表,制动系统的操作等操作手柄应设置于驾驶员便于观察和 操作的位置,并有明显的指示标牌
各仪表显示应清晰、准确; 组装后各种阀件应动作灵活、可靠,无卡滞
5.7电气系统 5.7.1一般要求 5.7.1.1系统应保证整车用电设备所需电源
有24V低压直流电源,220V,50Hz单相和380V 50Hz三相交流电源,供启动、照明、仪器仪表、信号、控制电路和生活用电
5.7.1.2应配备足以支持整车工作的备用电源,确保应急状态下的行车及检测工作安全
5.7.1. 系统应能对发动机的启动、调速、紧急停车进行控制及保护
3 5 .7.1.4系统的电子装置应满足TB/T3021的要求
5.7.1.5系统应具备一定的抗电磁干扰的能力 5.7.1.6各电路绝缘电阻值应符合GB/T10082的要求
5.7.1.7系统设有外接交流电源接口
5.7.2组装要求 5.7.2.1操作台的布置应保证驾驶员易于操作
5.7.2.2电气线路排列整齐,接线端子压接良好,接线端应有清晰的编号;各连接线无松动脱落,导线 绝缘层无破损
5 .7.2.3操作台、接线箱的安装和布线应满足防水,防尘和散热的要求
5.7.2.4车体上的电缆线应穿管或采用线槽牢固敷设,不应有油污,破损
5.7.2.5操作台配电箱,板应安装牢固,面板上电器元件标志清楚
5.7.2.6仪表、开关、按钮、指示灯、照明灯等应安装牢固,工作正常、指示准确
8 5 照明系统 5.8.1前后照灯的光照性能在距离前照灯400m处的照度值不小于0.1lx
5.8.2前照灯安装固定可靠,在驾驶室可对照射方向进行调整并更换,具有防雨,抗振性能
玻璃罩和 面罩在风、沙、雨、雪的侵袭下,不应出现破损
5.8.3警示灯、作业照明灯、标志灯、前后驾驶室内照明灯等应完好,安装牢固,工作正常
GB/T28426一2012 5 液压和气动系统 5.9.1液压系统应符合GB/T3766的规定
5.9.2液压和气动系统应具备以下作业控制功能 a)超声波换能器支持机构的上升、下降、横移 b 检测装置的对中; e喷洒合水(液 5.g.3应设置工作装置安全锁定
5.9.4系统具有应急功能,在紧急情况下,应能在5min内将超声换能器及其支持机构回收到位,恢复 到运行状态
5.9.5系统应设置油液滤清器、蓄能器、回路保护及故障报警等功能
5.9.6系统采用的液压油洁度、液压油的牌号和规格应符合设计要求
5.9.7系统中各回路中的压力应有监控和显示,各仪表、报警装置、手控阀等的设置应便于观察和操 作,并有明确的指示标牌
主要回路应设有对液压和气动系统主要技术参数检测的接口
5.9.8 5.9.9液压油箱应配备易观察的油位标记装置
5.9.10软,硬管路排列整齐,弯管处不应有过压现象,分布合理,固定可靠,作业时不产生摩擦或磕碰
各 气缸、油缸工作时运动平稳,活塞杆部位不应渗漏
其他各元件连接和安装应牢固,可靠,接 5.9.11 口处无渗漏
5.10供水系统 应分别设置工作水箱和生话水箱
工作水箱容量满足&h或300km检测需要
生活水箱容 5.10.1 量不小于1m
设有单向阀门,可将生活用水补充至工作水箱
5. 10.2水箱和管路应采用不锈钢或有色金属材料,防锈蚀,无渗漏,可清洗,满足车站上水要求,并设 有水位显示装置
供水系统应满足冬季作业和生活的需要
5.11作业装置 5.11.1超声波换能器 5.11.1.1换能器回波频率2MHz5MHz 5.11.1.2换能器应具有互换性
5.11.1.3纵波换能器灵敏度余量不小于46dB,横波换能器灵敏度余量不小于60dB 5.11.1.4纵波换能器分辨力不小于26dB.横波换能器分辨力不小于22dB
5.11.1.50"声束声轴偏斜角误差不大于1";45"及以下角度声束折射角误差不大于1.5";70"声束折射 角误差不大于2” 5.11.1.670"声束钢轨轨头声场宽度不小于50mm 5.11.2超声波换能器支持机构 5.11.2.1满足最高检测速度下安全运行的需要
应设置锁止装置确保收起时人位可靠
5.11.2.2 在收起位非检测状态时),满足最高自行速度和最高连挂速度下安全运行的需要 可由工作人员通过控制台控制升降及锁定,并设有视频监视设备
5.11.2.4 5.11.2.5检测时超声换能器及其支持机构能安全通过道岔
GB/T28426一2012 11.2.6应安装对中调节装置,以保证换能器的正常工作
5. 5.11.2.7超声换能器可进行手动或自动对中
5.11.2.8支持机构及其伺服控制系统应安装报警装置
换能器支持悬挂机构应安装辅助应急提升系统,在主提升系统失效的情况下可以收起换能 5.11.2.9 器及支持机构 5.11.2.10耦合水(液)喷洒系统应保证均匀润湿轨面为超声换能器提供良好耦合
应配备油污清扫洗)装置清除钢轨及超声换能器表面油污 5.11.2.11 5.11.2.12低温型设备应配置轨面清扫装置
5.11.3检测系统 5.11.3.1系统应具有多通道、同时处理不同信号的能力,通道数不少于24个
5.11.3.2各通道参数应能独立控制调节 a)通道参数由计算机程序控制调节; b通道可以单独打开或关闭; e)通道增益或衰减的调节范围不小于80dB d)信号增益或衰减的最小调节量不大于1/2dB; 通道时间参数最小调节量不大于1 e As
检测系统应有同时探测轨头、轨腰及其延伸部位裂纹(包括横向疲劳裂纹、纵裂、斜裂、平裂 5.11.3.3 和螺孔裂纹等)的能力(由轨面人射的超声束无法射及的部位除外)
超声发射重复频率满足扫查间隔不大于6mm的要求
5.11.3.4 5.11.3.5探伤灵敏度不低于 a)钢轨头部横向裂纹;直径8nmm平底孔当量 b 钢轨头部及腰部纵向水平裂纹;最小面积10mm×15mm e)螺栓孔裂纹;裂纹深度8nmm 5. 11.3.6系统检出率大于或等于80%,系统误报率小于或等于20%
5.11.3.7应具有超声波A型显示和实时多通道超声拟合及钢轨伤损B型彩色显示的功能
55 .11.3. 8 应能够进行实时的超声波信号采集、处理、显示和存储,检测数据存储能力不低于50000km. 1.3.9能够对钢轨伤损及其特征实时自动判别,相关参数可人工设定,并有声音报警和B型显示延时 提示功能 5. 11.3.10能够回放超声波B型显示并对数据进行重复分析
5.11.3.11具有自动和手动修正里程信息的功能
5.11.3.12探伤检测系统应有较强的抗干扰能力,能够在电气化线路正常工作
应为中文显示,界面友好;能够打印出伤损位置、伤损严重程度及辅助判别结果等信息,可编 5.11.3.13 辑和打印中文格式的探伤报告
检查与试验方法 6.1限界检查 限界检查方法按GB/T16904.1的规定进行
6.2车辆运行性能试验 动力学性能试验,紧急制动距离试验,牵引性能试验,运行阻力试验,起动加速性能试验、冷却能力试 验,车体内部噪声试验按TB/T2769的有关规定进行
GB/T28426一2012 6.3车体、传动、制动和照明装置检查与试验 走行系统、车架,车体和驾驶室、动力传动系统、制动系统、照明装置的检查与试验按照GB/T25336的 有关规定进行
车体淋雨试验 车体淋雨试验按照GB/T3315的有关规定进行
6.5液压和气动系统检查与试验 液压和气动系统检查与试验如下 在专用试验台上进行液压系、马达、同等零部件性能的检测, a 按作业功能试验内容,对液压系统控制功能的正确性进行检测 b 用压力表,流量计对回路系统压力流量进行检测 e 用测温仪检测作业2h的液压回路的油温; dD 用专用设备检查液压油的清洁度及理化指标
6.6制动系统检查与试验 制动系统检查与试验如下 a)制动系统阀类部件的校验需在专用试验台上进行; 在总风缸达到规定压力的条件下,进行制动系统和气动系统泄漏和性能静态试验
静态试验用 b 压力表和秒表、泄漏试验用涂泡沫剂的方法进行; 用露点计检测空气干燥器出口处的压缩空气露点; d)用专用仪器对油水分离器性能进行检测
6.7电气系统检查与试验 电气系统检查与试验按照GB/T3315的有关规定进行
6.8检测装置检查 a)应安装正确,动作灵活、可靠; b) 计算机及显示系统、打印装置应工作正常,显示准确
6.9检测系统性能试验 6.9.1超声换能器测试 超声换能器的灵敏度测试按照TB/T2340和JB/T10062的有关规定进行
6.9.2动态试验 6.9.2.1试验线路 试验线路要求如下 a 试验应在平直线路上进行,试验线路长度不小于2000m,线路中间无道岔 b)试验线路中部铺设含人工伤损的钢轨,两端应留有足够的加速和减速距离; 采用标准25m的50kg/m或60kg/m钢轨制作人工伤损轨,钢轨表面无锈蚀、轨头磨耗小于 3 mm;
GB/T28426一2012 d人工伤损钢轨左右股各10根,每根伤损钢轨含有不少于一个确定的人工模拟伤损,应连续铺设; 用直径5nm不同深度的轨头横孔模拟钢轨横向裂纹,螺栓孔处不同取向的锯口模拟螺孔裂纹 人工伤损的布局和尺寸要求参见附录A 6.9.2.2检出率 检测能力试验应在系统最高检测速度下对试验线路的人工伤损进行连续不间断10次探测,10次检测 平均人工伤损检出率为系统的检出率,10次检测的平均伤损误报率为系统的误报率 6.9.3换能器及支持机构通过道岔性能试验 换能器及支持机构在检测位按系统标称的通过道岔速度,以正常的操作方式正反向通过标准铁路道 岔直股各一次
6.9.4应急提升系统试验 关闭主提升系统,使用应急提升系统将超声换能器及其支持机构从检测位收起至收放位完整动作- 次,并测试动作时间
检验规则 7.1检验分为型式试验和出厂检验
7.2批量生产的探伤车每台均应进行出厂检验,检查与试验项目按表1中带“s"符号的项目进行
7.3探伤车属于下列情况之一时应进行型式试验,检查与试验项目按表1中带“T”符号的项目进行 a)新产品定型时 b)停产五年以上(包括五年)又重新生产时 产品的结构、工艺或材料的改变可能影响到系统的某些性能时,应对部分或全部进行型式检验; d转厂生产时; 连续生产八年后
表1探伤车的检查与试验项目表 序号 检查与试验内容 检验项目 型式试验(T' 出厂检验(S 限界检查 5.1. 动力传动系统检查 5.2 车架系统检t 5.3 车体和驾驶室检查 5,4 5.5 走行系统检t 5,6.6 单机紧急制动距离试验 制动系统检查 其他项目检查 5.6.15.6.5、,5.6.7 电气系统检查 5.7 照明系统检查 5.8 液压和气动系统检查 5.9
GB/T28426一2012 表1(续 序号 检查与试验内容 检验项目 型式试验(Ty 出厂检验(s) 供水装置检查 10 5.10 T 1 5.11 作业装置检查 T 12 动力学试验 5.1.9 5.1.13 13 牵引性能试验 14 运行阻力试验 5.1.13 15 起动加速性能试验 5.1.13 16 冷却能力试验 5.1.13 17 车体内部噪声试验 5.4.8 18 作业性能试验 6.9 7.4钢轨探伤车出厂应附有下列随车技术文件和备件 a)产品合格证 b)使用保养说明书;
易损件目录; d随车备件、附件和工具及其清单
整机的标志、包装和运输 标志 探伤车上的表示产品主要性能的铭牌及与运输相关的其他技术参数标志,如“禁止驼峰”“禁止烟火" 放"“禁止攀登"等应符合产品图样及技术文件的规定
“禁止溜放” 8.2包装 8.2.1应放尽燃油箱和耦合柴油箱中的燃油
8.2.2超声换能器应从其支持机构上拆除 8.2.3换能器支持机构应置于收起位,并用铁丝捆扎加固
8.2.4以下部件应进行保护处理 前后照灯、标志灯、工作灯应用塑料布包拥; a 车外部探伤系统的监控摄像头应进行包捆防护 b) 影响长途附挂回送的螺栓应紧固; d)车轴齿轮箱、轴承箱等应按要求的牌号及数量加装润滑油
8.3运输 8.3.1探伤车整机运输应按无火附挂回送办理,联挂不应超过最高允许联挂速度
8.3.2各运动部位应按规定加足润滑脂(油)
8.3.3无火回送应有专人押送
10
GB/T28426一2012 附 录 A 资料性附录 探伤车试验线路人工伤损布局和尺寸 图A.1为试验线人工伤损总体布局图
图A.2中人工伤损A,B,c,K和L为轨头横孔,用以模拟轨 头横向伤损
图A.1中标注于钢轨内侧的从轨头内侧钻孔,标注于钢轨外侧的从轨头外侧钻孔
人工伤 损A,B和C加工时垂直于断面中心线
人工伤损E、F,G,H和J为螺栓孔锯口,模拟螺栓孔裂纹 10 左轨 H 右轨 图A.1试验线人工伤损总体布局图 单位为毫米 孔平行于轨底 礼平行于轨底 人工伤损 b B 人工伤损A 图A.2人工伤损图 11
GB/T28426一2012 单位为毫米 d 人工伤损E 人工伤损e 45 45 O 人工伤损G 人工伤损! 45 h)人工伤损 人工伤损H g 图A.2(续 12
GB/T28426一2012 单位为毫米 5.37深,平行于轨底 120 17.5 17.5 人工伤损K和L 图A.2(续) 13
大型超声波钢轨探伤车GB/T28426-2012
大型超声波钢轨探伤车是一种利用超声波技术来检测钢轨缺陷的设备。它可以对铁路、地铁等基础设施上的钢轨进行无损检测,从而及时发现存在的缺陷并进行修复,保障交通运输的安全和顺畅。
该设备符合国家标准GB/T28426-2012《钢轨无损检测规范》,其中规定了大型超声波钢轨探伤车的性能和技术指标。根据该标准,大型超声波钢轨探伤车具有以下特点:
- 采用高频率、宽带宽的超声波探头,可以有效检测钢轨内部的细小缺陷;
- 采用多通道同步技术,可以同时检测出横向和纵向等不同方向上的缺陷;
- 采用数字信号处理技术,可以减少信号噪声,提高探伤精度;
- 配备专业的数据分析软件,可以对检测结果进行快速、准确的分析和评估。
大型超声波钢轨探伤车具有以下应用领域:
- 铁路、地铁、城市轨道交通的钢轨无损检测;
- 港口、码头、物流园区等货运场所的钢轨无损检测;
- 钢厂、冶金企业等生产领域的钢轨无损检测。
总之,大型超声波钢轨探伤车是一种在现代交通运输和工业生产中不可或缺的设备。它通过高精度的无损检测技术,为我们的生活和工作保驾护航。