GB/T25390-2010
风力发电机组球墨铸铁件
Spheroidalgraphitecastironforwindturbine
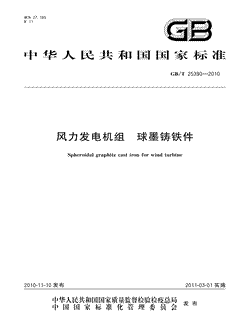
- 中国标准分类号(CCS)F11
- 国际标准分类号(ICS)27.180
- 实施日期2011-03-01
- 文件格式PDF
- 文本页数15页
- 文件大小451.68KB
以图片形式预览风力发电机组球墨铸铁件
风力发电机组球墨铸铁件
国家标准 GB/T25390一2010 风力发电机组球墨铸铁件 Spheroidalgraphitecastironforwindturbine 2010-11-10发布 2011-03-01实施 国家质量监督检验检疫总局 发布 国家标准化管理委员会国家标准
GB/T25390一2010 目 次 前言 范围 规范性引用文件 术语和定义 牌号和分类方法 订单信息 技术要求 试验方法 检验规则 标志.,防锈,包装.运输及贮存 l0出厂质量证明书 10 附录A(资料性附录)风力发电机组用球墨铸铁典型件超声波探伤质量等级要求 参考文献 12
GB/T25390一2010 前 言 本标准结合了风力发电机组中轮毂,机架、轴承座、行星架、主轴齿轮箱箱体等铸件技术要求和相 关铸造行业标准的要求,其中铸件材料要求,超声探伤和磁粉探伤要求的相应条款参考了欧洲EN1563 《铸造球墨铸铁》,EN12680-3;(E《铸造超声波检测第3部分;球墨铸铁铸件》和EN1369《铸 磁粉检验》的主要内容
造 本标准的附录A为资料性附录
本标准由机械工业联合会提出 本标准由全国风力机械标准化技术委员会(SAC/T50)归口
本标准起草单位;江苏一汽铸造股份有限公司、江苏吉鑫风能科技股份有限公司,金风科技股份有 限公司、华锐风电科技有限公司,河海大学
本标准主要起草人俞旭如,李小青、华永辈、刘河,宫靖远、王泽华
GB/I25390一2010 风力发电机组球墨铸铁件 范围 本标准规定了风力发电机组用球墨铸铁件的技术要求、试验方法、检验规则、标志、包装和贮存
本标准适用于风力发电机组中使用球墨铸铁铸造的零件(如用轮毂,机架、轴承座、行星架,主铀,齿 轮箱箱体等
规范性引用文件 下列文件中的条款通过本标准的引用而成为本标准的条款
凡是注日期的引用文件,其随后所有 的修改单(不包括勘误的内容)或修订版均不适用于本标准
然而,鼓励根据本标准达成协议的各方研 究是否可使用这些文件的最新版本,凡是不注明日期的引用文件,其最新版本适用于本标准
GB/T223.3~GB/T223.74钢铁及合金化学分析方法 GB/T228金属材料室温拉伸试验方法(GB/T228-2002,IsO6892;1998(E).eqw) 金属材料夏比摆锤冲击试验方法(GB/T2292007,Is(148-1;2006,MoD) GB/T229 GB/T231.1~GB/T231.3金属布氏硬度试验(GB/T231.1GB/T231.3一2002,IsO6506-l: 1999(E)~Is(6506-3:1999,eqv GB/T1348球墨铸铁件 GB/T5611 铸造术语 GB/T5612铸铁牌号表示方法(GB/T5612一2008,IsO15931:2004,MOD) GB/T6060.1表面粗糙度比较样块铸造表面(GB/T6060.1一1997,eqIS02632-3:1979) GB/T6414铸件尺寸公差与机械加工余量(GB/T64141999,eqvIs(8062;1994 铸钢件超声探伤及质量评级方法(GB/T723一1987,neqBs6208;1982) GB/T7233 GB/T9441球墨铸铁金相检验 GB/T9444铸钢件磁粉检测(GB/T9444一2007,IsO4986;1992,IDT) (GB/T9445无损检测人员资格鉴定与认证(GB/T9445-2008,IsO9712;2005,IDT) GB/T11351 铸件重量公差 GB/T11344无损检测接触式超声脉冲回波法测厚方法(GB/T11344一2008,ASTME0797 2005,MOD) GB/T15056铸造表面粗糙度评定方法 JB/T4009接触式超声纵波直射探伤方法 JB/T9219球墨铸铁超声声速测定方法 术语和定义 GB/T5611确立的以及下列术语和定义适用于本标准
球墨铸铁spheroidalgraphiteeastiron;duetileironm 球墨铸铁是铁液经球化处理,碳大部分或全部以球状石墨存在,有时也有少量团絮状石墨形态存在 的铸铁材料
GB/T25390一2010 3.2 石墨球化处理nodularizatonm 在铁液中加人球化剂,使铁水在凝固过程中形成以球状石墨为主的工艺过程
3.3 单铸试块separatelyeastsaples 与铸件同时但单独浇注的试块 附铸试块 cast-onsamples 附铸在铸件主要壁厚上的试块
牌号和分类方法 4.1球墨铸铁牌号按力学性能进行分类
4.2球墨铸铁的力学性能是通过测定试块上经加工试样的性能而确定的
4.3球墨铸铁的牌号表示方法符合GB/T5612的规定,并分为单铸和附铸试块两类
订单信息 5.1下列订货信息应由铸件采购方提供 . 1.1铸件材料牌号、图纸、技术要求 1.2需要进行无损探伤的铸件的部位以及需要检验的铸件数量或者百分比
55 S 55 .3 对于铸件各个部位进行无损探伤时所需要的合格等级
检验方法的要求
5 任何特殊要求应由采购方提出,并经生产厂确认
经供需双方商定后执行,主要包括下列内容 如为附铸试块验收,则应确认在铸件上附铸的位置,对应的铸件壁厚和试块厚度
5.2.2铸件壁厚如要求正公差则应在技术要求或图纸中注明
5 2. 3 在力学性能和金相组织达到要求而采购方要求铸件进行热处理时
高于“6技术要求”的要求 技术要求 6.1风力发电机组用球墨铸铁牌号和性能要求 6.1.1力学性能 风力发电机组常用球墨铸铁的力学性能见表1
需方也可根楣工作要求和设计要求按GB/T1348选用除表1所列以外的牌号
6.1.2低温冲击功 风力发电机组常用的球墨铸铁件试块上加工的试样的低温冲击功见表2. 6.1.3力学性能特殊要求 6.1.3.1本体力学性能要求 经供需双方协商,可以从铸件上切取本体试样,取样部位及要达到的力学性能指标,由供需双方 商定
因铸件的致密性和铸件壁厚的变化,铸件本体性能值无统一标准值
铸件本体力学性能一般低于 试块性能
高指标力学性能要求 6.1.3.2 经供需双方协商,可以提高力学性能指标作为验收要求,如对QT400-18AL
和QT400-18L要求按
GB/T25390一2010 -30C时或一40C时最小冲击功验收或对QT350-22AL和QT350-22L保证一40C最小冲击功时适 当提高机械强度
表1试块上加工的试样力学性能 抗拉强度 屈服强度 延伸率 铸件主 试块 Rm R, 硬度 牌号 要壁厚 适用件举例 N/mm % HBw 类型 N/mm" mmm 最小值 最小值 最小值 30 25mm附铸 350 22o 22 120~16o 轴承盖 齿轮箱 3060 40mm附铸 330 210 18 120~160 QT350-22AL 扭力臂 轮毂、底座 0mm附钩 60200 320 200 15 120~160 轴承座 QT350-22IL 6o 25mm单铸 350 22o 22 120~175 轴承盖 18 30 25mm附铸 400 240 120~175 轴承盖 齿轮箱 0mm附钩 >30~60 120~175 390 230 15 扭力臀 QT400-18AL 轮毂,底座 370 22o 12 120175 60200 70 mm附铸 轴承座 18 QT400-18L s60 25mm单铸 400 240 120175 轴承盖 QT700-2A >60~200 70mm附铸 660 380 225305 行星架 注1:牌号中“A"表示附铸试块上加工的试样测得的力学性能,以区别于单铸试棒上测得的性能
注2;牌号中“L"表示该牌号有低温冲击功要求
注3,对轴承盖等主要壁厚在30mm以下或单件重量在1o0kg以下的铸件一般用单铸试块
表2试块上加工的试样的低温冲击功 最小冲击功AkV 铸件主要 试块类型 -20士2) 40士2)c 牌号 壁厚 和厚度 mm 平均 单个 平均 单个 25或40nm附铸 60 12 QT350-22AL 70mm附铸 10 60200 QT350-22IL S60 25mm单铸 12 5或40mm附铸 12 60 QT400-18AL 70mm附铃 60200 10 12 QT400-18L S6o 25mm单铸 6 金相组织 风力发电机组中球墨铸铁件试块上的金相组织要求见表3
铸件本体球化率不低于85%
GB/T25390一2010 表3风力发电机组中球墨铸铁件试块上的金相组织 牌号 渗碳体/% 石墨大小 球化率/% 铁素体/% 珠光体/% 磷共品/% QT350-22AL QT350-221 >90 QT400-18Al 5级及以上 >90 QT400-18L 90 QT700-2A 6. 3 超声波无损探伤缺陷要求 铸件本体声速 铸件检测超声波声速铸态必须达到5550m/s以上,退火处理后必须达到5500m/s以上 6.3.2质量等级划分 按重要度不同铸件上质量等级划分为二个区域
A区高要求的区城 B区中等要求的区域 风力发电机组常用球墨铸铁典型件不同区域质量等级参考要求参见附录A
根锯设计要求最终由 需方决定并在图纸或其他技术文件中标明
允许的最大缺陷尺寸 6.3.3 允许的体积反射类最大缺陷的尺寸不得超过表4的要求
允许的夹渣类最大缺陷的尺寸不得超过表5的要求
经供需双方协商一致,可另行商定接受准则
表4允许的最大缺陷显示尺寸一体积反射类 质量等级 单位 特征 受检验区 5050200200 5050200200 5050200200 50 50 mmm 公称壁厚 缺陷最大厚度 20 25 30 35 占壁厚百分数 边缘区中 1000 2000 600 mm" 100010002000 最大缺陷" 中心区中的 mm" 1000o150001500l500o200003000020000 最大缺陷 缺陷的总面积占 10 15 15 15 20 20 15 20 30 30 40 受检表面的百分比 关于夹渣,参见表5
b边缘区,按图1. 任何缺陷指示均不得超过表9中给出的极限值
表5缺陷的最大允许指示尺寸-夹渣 质量等级 特 征 壁厚百分/% 0 15 20 25 任何缺陷显示均不得超过表9中给出的极限值
GB/T25390一2010 -边缘区边缘厚度;=/3(最大30mm); 中心区; 名义壁厚
图1铸件壁截面的边缘区和中心区划分机加工之后的尺寸 磁粉探伤缺陷要求 检测部位 按检测图或铸件浇注时易产生夹渣的铸件最上表面和堤芯形成的内腔下表面
如顾客有要求也可 在加工后加工面上进行检测 6.4.2接受准则 磁粉探伤的各质量等级不得超过表6的要求
铸件上要求高的区域(A区)质量等级要求达到2级,其他(B区)质量等级要求达到3级
表6磁粉探伤的各质量等级的要求 质量等级 显示观察手段 目视 目视 目视 目视 目视 放大倍数 应考虑的最小显示长度/mm 1.5 10 总面积/mm 10 35 500 70 200 非线状簇状 显示(SM)?" 2l 4 66" 10" 单个显示长度/mm 16 显示类型 单个 累加单个 累加单个 累加单个 累加单个累加 线状显示(LM)" 壁厚心<16mm 10 10 18 18 25 或点线状显示 27 壁厚16mm<<50mm 12 18 18 227 9 40 AM 10 70 壁厚>50mm 10 20 15 30 30 45 45 应用实例 根据表面粗糙度和其应用情况的其他铸件 注:本表规定了105mm×148rmm评定框内允许的最大面积(mm')和最大长度(mm "非线状显示(sM);儿<3h,式中L是显示的长度,h是显示的宽度 h允许有二个不超过表中规定的长度显示
线状显示(LM):L>36
点线状显示(AM),至少含有三个最大间隙为2tmm的线状显示或非线状显示
GB/T25390一2010 50~100" S 50~100 R50~100 打磨深度; -要求最小壁厚; t最小 实际壁厚
1家际 图2允许的可打磨形状 表7在最小壁厚时打磨区域允许面积和深度 名义壁厚1/mm 允许打磨的最大面积/mm 允许打磨的最大深度h '<30 1200 <5% 30<50 2000 5%t 50心t80 3200 5%t 80<1130 <5%t 4900 t>130 8100 <5%1,但最大不超过10mm 6.5外观质量要求 6.5.1铸件不得有裂纹、冷隔缺陷
不得有影响使用的缩孔、缩松,夹渣、夹砂等缺陷
6.5.2铸件表面应清除毛刺
6.5.3表面粗糙度按GB/T6060.1要求应不低于Ra25
6.5.4最大允许显示出的不连续点状缺陷的尺寸见表6
6.5.5铸件表面缺陷可以打磨修正
打磨应将缺陷清除,如果表7给出的在最小壁厚时的最大允许打 磨深度和最大允许打磨面积的要求均可满足时,应根据图2按半径(50~100) )mm圆弧进行打磨
6.6铸件尺寸公差和重量公差 6.6.1铸件尺寸公差 铸件尺寸公差按GB/T6414中CTl1-12执行,壁厚公差放宽1级
对于轮毂件,为保证强度,一般壁厚采用尺寸正公差,但应在相关技术要求或图纸中注明
如不注 明则采用正负公差
6.6.2铸件重量公差 铸件重量公差按GB/Tl1351中MT9-10级执行
对于轮毅件如采用尺寸正公差,则按公差带作 正公差上限但下限允许采用负公差
铸件修补 铸件不允许用焊补加以修复
试验方法 7.1材料试验方法 7.1.1化学成分分析按GB/T223.3GB/T223.74进行
7.1.2抗拉强度、屈服强度、延伸率检测按GB/T228进行
7.1.3硬度检测按GB/T231.1~GB/T231.3进行
7.1.4低温冲击值检测按GB/T229进行
7.1.5金相组织检测按GB/T9441进行
GB/T25390一2010 7.2无损检测 7.2.1检验人员 无损检测工作应由具备资格的人员来完成
检验人员的资质,应按照GB/T9445规定的2级或以 上的要求进行资质审查
7.2.2超声波无损探伤方法 按JB/T4009,GB/T7233.GB/T11344和JB/T9219规定的要求进行
7.2.2.1超声探伤设备 设备应满足 a)量程设定,设定范围须至少为10mm一2m; b 增益,须能够在一个至少为80dB的范围内进行调节,调节的最大级差为2dB,测量精度为 1dB e)水平和垂直线性度须小于显示屏面调节范围的5%; d)频率范围须至少为0.5MHz一5MHz(含5MHz)
7.2.2.2探头 为了涵盖需要检测的瑕疵类型范围,可以使用压缩波单晶或双晶探头
双晶探头用于靠近表面部 位的检验
双晶探头常用的为2MHz一2.25MHz,对于薄壁铸件通常使用高的频率进行检验
宜采用的探头是;SE2-0';DL.2R-0';MSEB2;B2s等 7.2.2.3偶合介质 采用符合要求的油、凝胶或类似物
对于标定和所有随后的检测操作须使用相同的偶合介质
7.2.2.4超声探伤设备的设定 按照DAC方法校准
设定时如使用球墨铸铁的参考块,双方须在询价和订货时达成一致意见
该参考块的厚度需和被检测的铸件的厚度范围具有可比性,同时须具有和被检测铸件相同的超声特性, 并且须具有相同的表面光洁度
该参考块具有符合表8要求的平底孔,或者具有替代平底孔那样的侧 横孔 超声波探伤设备也能用GS(Distance-Gain-Size距离-增益-大小)方法设定,在这种情况下可不必 使用参考块,而直接在铸件上进行设定,条件是铸件的厚度是已知的,并且铸件具有平行的表面
表8对超声波探伤适宜性的要求 单位为毫米 受检区域中的件壁厚 >1020 >20~100 >100250 >250500 能够检出的最小平底孔直径 10 7.2.2.5检测灵敏度 最小检测灵敏度设定的要求是:表9中给出的平底孔的高度须至少占到满屏的40%,且林状草波 高要比表9中给出的平底孔的高度至少低6dB 表9需要评价的超声探伤缺陷指示 回波高度高于噪声检出 按照7.2.2.5要求能够检出 受检区域中的铸件壁厚 -次回波的衰减最小值 的最小平底孔直径 级别的最小值" dB mm dB mmnm >10~20 12 >20100 20 >100~250 12 >250~500 10 仅仅适用于由于铸件几何形状的原因而没有一次回波的区域
GB/T25390一2010 7.2.2.6铸件表面检测顺序和检测表面的要求 如果规定要对铸件进行多种方法试验时,先进行目测,然后是磁粉试验,最后是超声波试验
但是 当磁粉试验是针对机加工表面时,超声波探伤应在机加工以前进行
要进行试验的表面必须清洁,无油无油脂、无砂子或其他污物,表面粗糙度不大于Ral2.5,无影响 试验或结果解释的异物存在
铸件表面的要求能够保证和探头之间的正确偶合
7.2.2.7缺陷的评价和记录 7.2.2.7.1缺陷长度按图3来确定;“不可测量”且超过记录要求的缺陷用“GdB”法,“可测量”且一次 回波衰减时,按照表9的规定用“12dB或20dB”法
不可测量 可测量 图3缺陷的可测量性 7.2.2.7.2缺陷厚度尺寸按图4来确定
7.2.2.7.3当量超过记录要求的缺陷用“6dB”法,对于一次回波衰减的缺陷用“12dB和20dB”法
7.2.2.7.4除非是另外达成协议,否则所有一次回波的衰减达到或者超过表8中给出的极限值的回波 高度均须进行评价,并且记录下来,如果其数值超过表4和表5中所给出的极限值的75%的话
每当 发现此类缺陷指示时,须注明其位置并且将其记录在检验报告中
需要记录的缺陷的位置可以用格栅、 示意图或者照片来记录
d=t一(si十: 图4缺陷的厚度方向尺寸计算 7.2.2.7.5对于那些已经发现的需要记录伤纹指示的部位,须对这些部位的类型,形状,尺寸和位置进 行进一步的更加细致的调在
此时可以改空传感器的频率,改空检验的方法,或者利用其他检验方法 例如射线探伤)来进行调查
7.2.2.8超声探伤检验报告 超声探伤检验报告须至少含有以下信息 引用的标准; a b)被检验的铸件的特征数据(零件号,炉料号或批号等);
GB/T25390一2010 检验的范围 d) 所使用的检验设备的类型; 使用的探头 检验区域上使用的检验技术; g)用于灵敏度的设定所必需的所有数据 h)超声探伤适宜性的详细说明 所记录的缺陷的所有特点信息(例如后壁回波的衰减、壁厚截面方向上缺陷的位置和尺寸、长 度、面积和平底孔的直径)以及缺陷位置的描述(示意图或者照片); 试验人员姓名和资格、检验日期以及批准人员的姓名和资格、批准日期
jD 7.2.3磁粉无损探伤方法 探伤方法 磁粉检验应根据GB/T9444规定的方法进行 7.2.3.2设备 最小为44N提升力的交流电磁轭,并且满足相关要求
7.2.3.3磁粉 7.2.3.3.1荧光磁粉 宜使用悬浮在水中或油中的荧光磁粉
使用荧光粉做试验时应配有 一盏黑光灯,在试验表面有最小1000Aw/enm的强度; a 最大的背景照度为20lx
b 7.2.3.3.2黑磁粉 如果使用黑磁粉做试验,应在以下情况下进行 a)在铸件表面涂有反差增强剂 b黑磁粉要悬浮在水或油中; 在试验表面上的最小照度为500lx c 7.2.3.4磁粉探伤检验报告 磁粉探伤检验报告须至少含有以下信息
a)引用的标准 b)被检验的铸件的特征数据(零件号、炉料号或批号等); 检验的范围, 所使用的检验设备的类型; 检验区域上使用的检验技术; 用于灵敏度设定所必需的所有数据; 磁粉探伤适宜性的详细说明; g 试验结果 所记录的缺陷的所有特点信息(例如缺陷的形状、长度)以及缺陷位置的描述(示意图或者 照片); 试验人员姓名和资格、检验日期以及批准人员的姓名和资格、批准日期
j 7.3外观检查 外观检查采用目测方法逐件进行检验
表面粗糙度按GB/T15056采用比较样块法
7.4尺寸检测 尺寸检测按GB/T1348中的要求进行
GB/T25390一2010 7.5铸件重量 铸件重量按称量法进行
检验规则 1 检验类别 8 产品检验为出厂检验
产品必须经生产厂检验合格后方可出厂 附铸试块在铸件上的位置,以不影响铸件的使用性能、铸件外观质量和试块的致密性,由供需双 方确认
铸件一般不热处理,但如铸态性能达不到要求,则允许热处理,但最多不超过二次
如铸件需 热处理,则附铸试块需与铸件一起热处理后从铸件上取下
8.2出厂检验 材质检验;出厂检验每件以附铸试块或单铸试块检测下列项目,抗拉强度,屈服强度,延伸率 8.2.1 低温冲击功.球化率.石墨大小,铁素体或珠光体),渗碳体,确共晶和硬度
化学成分由生产厂自行确 定,不作验收依据
超声波无损探伤A区按100%全检,B区按100%全检;声速按30%抽检
也可按需方要求 8.2.2 进行
8.2.3磁粉探伤;对要求检测处每件检查, 8.2.铸件尺寸;按双方商定检验
8.2.5外观质量;每件全检
8.2.6铸件重量;对轮毂按10%抽检称重,其他件不检查称重
如需方有特殊要求时按供需双方商定 的要求执行
8.2.7出厂检验项目中超声波无损探伤、铸件尺寸、铸件重量等抽检项目如不合格,则针对该不合格件 的前后各十件的该项目进行全检
标志、防锈、包装、运输及贮存 9.1铸件标志 每件铸件应铸有;材料牌号,铸造厂标识,系列号(可追溯号)、铸件图号和版本号
所有标记应按图 纸规定要求放置,且应在加工和表面处理后仍保持
9.2防锈 按供需双方商定的要求执行
9.3包装、贮存、运输 按供需双方商定的要求执行
l 出厂质量证明书 出厂质量证明书必须记录下列内容 a)材料类型 b 抗拉强度; 0. .2%屈服强度; c d 延伸率; 在 -20C或一40C条件下V型缺口的冲击功适用时); 附铸试块的类型; 金相组织中石墨的评级、铁素体量或珠光体量; h 无损检测报告; i 防锈处理报告必要时 10
GB/T25390一2010 附 录A 资料性附录 风力发电机组用球墨铸铁典型件超声波探伤质量等级要求 缩松和夹渣是球墨铸铁的常见缺陷,由于凝固特性、工艺特性和实际的经济性等原因,球墨铸铁内 部的缩松和夹渣一般不能完全消除,但必须控制在允许的范围内
风力发电机组用球墨铸铁的内部缩松和夹渣缺陷一般用超声波探伤检测,风力发电机组用球墨铸 铁典型件重要度分级和超声波探伤要求质量等级见表A.1,供设计参考,需方可根檐工作要求确定实际 质量等级和探伤要求
表A.1风力发电机组用球墨铸铁典型件重要度分级、超声波探伤和磁粉探伤质量等级要求 铸 件 区 域 质量要求划区 超声波探伤质量等级 浆叶法兰、主轴法兰 2级 轮毂 其余 B 3级 轴承支撑面,连接法兰面 A 2级 吊耳 底座 B 3级 其余 主轴 所有区 A 2级 输出轴部位 2级 行星架 圆盘部位 2级 腹板 B 3级 轴承座 全部 2级 B 悬挂部位(力矩臂两端孔部位、 A 2级 中心孔,过渡部位 扭力臂 B 其余 3级 箱体地脚、外壳、加强筋、轮缘 2级 箱体 B 其余 3级 11
GB/T25390一2010 参 考 文 献 [1门 s945-1一2008铸铁微观结构第1部分;通过目视分析进行石墨的分类 [2]EN1369一1996铸造磁粉检验 [幻 EN15631997铸造球墨铸铁 [句 EN12680-3一2003铸造超声波检测第3部分;球墨铸铁铸件 12