GB/T39332-2020
高精度齿轮抗疲劳制造通用技术要求
Generalrequirementsfortheanti-fatiguemanufacturingofprecisiongears
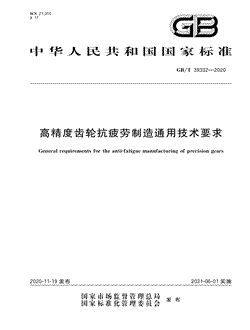
- 中国标准分类号(CCS)J17
- 国际标准分类号(ICS)21.200
- 实施日期2021-06-01
- 文件格式PDF
- 文本页数20页
- 文件大小1.68M
以图片形式预览高精度齿轮抗疲劳制造通用技术要求
高精度齿轮抗疲劳制造通用技术要求
国家标准 GB/T39332一2020 高精度齿轮抗疲劳制造通用技术要求 Generalrequirementsfortheanti-fatiguemanufaeturingofpreeisiongears 2020-11-19发布 2021-06-01实施 国家市场监督管理总局 发布 国家标涯花管理委员会国家标准
GB/39332一2020 目 次 前言 引言 范围 2 规范性引用文件 术语和定义 设计 4.l 几何设计 强度计算 4,2 4.3精度确定 4.4润滑设计 5 材料与热处理 5.1原材料 5.2锻件 5.3热处理 机加工 6.1磨齿 6.2磨削烧伤和磨削裂纹 6.3磨削烧伤和磨削裂纹的检查方法 6.!磨齿工艺的基本要求 6.5磨削裂纹的规避 表面处理 7.1喷丸强化 7.2齿面光整 检测与试验 14 8.1齿轮精度测量 14 8.2齿轮装置试验 l4 8.3齿轮探伤检测 15 参考文献 16
GB/39332一2020 前 言 本标准按照GB/T1.1一2009给出的规则起草
本标准由全国齿轮标准化技术委员会(SAC/TC52)提出并归口
本标准起草单位;郑州机械研究所有限公司、湖南大学、上海交通大学、河南中豫远大重工科技有限 公司、郑州中机轨道交通装备科技有限公司、郑州江宇机械有限公司、江苏中工高端装备研究院有限公 司、中机智能装备创新研究院(宁波)有限公司,郑州高端装备与信息产业技术研究院有限公司、北京工 业大学、中机生产力促进中心、昆山新浦瑞金属材料有限公司
本标准主要起草人:王伟、王志刚、周长江,张坤,李海霞、姜传海,李纪强,都长海,刘忠明、丁英晖 陈国民、陆军、王盈颖、张清朗、李优华,王长路、龙伟民、石照耀、张敬彩、张元国、王新波、吕泮功、郑明、 弓宇、管洪杰、范瑞丽、丁军、马聘天、张荣锋
GB/T39332一2020 引 言 齿轮的抗疲劳制造涉及齿轮生产的各个环节
其含义可做两方面解释;一是给定工况(如已知负 载)下尽可能延长齿轮的使用寿命,二是给定条件(如设定寿命)下尽可能提高齿轮完好性的可靠程度
如何最大限度地发挥参数(含精度)搭配、材料制备、热处理、机加工、表面强化、试验检测等生产环 节对于齿轮产品抗疲劳的贡献度,齿轮及其他相关专业人员已经做了大量工作
本标准是对这些工作 的 一般性总结,目的是帮助本标准的使用者在齿轮制造过程的某个或某几个环节上提高零件的抗疲劳 制造水平 对于一些已经建立了国家及行业标准(或规范)的齿轮制造环节,本标准将主要依据或参考的标准 和规范编列出来,供本标准的使用者参考;对于一些尚没有齿轮专业标准的制造环节,本标准有针对性 地给出了推荐的技术要求和操作说明
基本情况如下 关于齿轮的几何设计和强度计算;齿轮的几何与强度设计理论源于国外,目前我国以IsO标 准为主要参考规范,涉及齿轮(含圆柱齿轮、锥齿轮、蜗轮蜗杆)的名词术语、几何要素、符号代 号,齿形,强度计算等,已基本形成标准体系
关于齿轮的材料目前我国参考多国(或组织)的标准在化学成分、悴透性、纯度及冶炼、缎造 比晶粒度、表面硬度、心部硬度、硬化层深度,表面含碳量、显微组织表面裂纹.心部显微组织 等方面均有自建的规范,已基本形成标准体系
关于齿轮的精度设定与测量评价目前我国以Iso标准为参考规范,已基本形成标准体系
关于齿轮的热处理;目前我国除参考IsO标准以外,还执行自建的国家和行业标准,已基本形 成标准体系
特别是硬齿面齿轮的热处理工艺,如渗碳、,渗氮、感应淖火标准,在多年的应用中 起到了显著的作用
关于齿轮的试验;齿轮试验分为两大类;单齿轮试验(主要包括材料组织,机械性能、抗疲劳能 力等)和齿轮箱试验(主要包括啮合、效率、,噪声、振动、润滑、寿命等)
目前我国除参考Is 标准以外,部分项目还执行自建的国家和行业标准
关于齿轮的润滑;润滑作为齿轮设计的一个重要方面,本标准除引用了一些相关标准外,还对 润滑状态,润滑作用、润滑油品、,润滑系统等方面做出了必要的说明
关于磨齿和磨齿损伤;磨齿是齿轮机加工过程中最重要的工序,而磨齿损伤(烧伤和裂纹)可能 伴随而来,本标准从检测、规避和补救等方面做出了必要的说明
关于齿轮的表面处理;适宜的轮齿表面处理工艺有助于提高齿轮抗疲劳能力,本标准重点对喷 丸工艺做出了必要的说明
提醒本标准的使用者注意 齿轮的抗疲劳制造技术处于不断的发展中,例如,新的热处理工艺开始在齿轮制造方面得到应 用,包括高温真空渗碳、双频感应加热,激光表面强化、离子束表面强化等
这些新工艺今后完 全可能形成新的标准或规范 在齿轮的抗疲劳制造中人的因素必不可少
以齿轮设计为例;这是齿轮制造的基础,是齿轮产" 品验收的依据,其工作连接着客户需求和制造工艺,需要考虑的、兼顾的问题非常多,这就要求 设计者既了解规范,又应具有丰富的实践经验
IN
GB/39332一2020 高精度齿轮抗疲劳制造通用技术要求 范围 本标准规定了高精度齿轮抗疲劳制造重要环节的一般技术要求,主要包括设计含润滑、材料与热 ,表面处理、检测与试验等方面 处理、机加工 本标准适用于以下条件的齿轮,其他的金属齿轮产品亦可参考使用 mmm40mm; 模数:l mm2000mm; 直径范围:20 -齿部精度;不低于6级[GB/T10095(所有部分], 规范性引用文件 下列文件对于本文件的应用是必不可少的
凡是注日期的引用文件,仅注日期的版本适用于本文 件
凡是不注日期的引用文件,其最新版本(包括所有的修改单)适用于本文件 GB/T699优质碳素结构钢 GB/T2821 齿轮几何要素代号 GB/T3077合金结构钢 GB/T3141工业液体润滑剂Is0黏度分类 GB/T3374(所有部分齿轮术语和定义 GB/T3480渐开线圆柱齿轮承载能力计算方法 GB/T3480.1直齿轮和斜齿轮承载能力计算第1部分;基本原理、概述及通用影响系数 GB/T3480.5直齿轮和斜齿轮承载能力计算第5部分:材料的强度和质量 GB/T3480.6直齿轮和斜齿轮承载能力计算第6部分;变载荷条件下的使用寿命计算 GB/T3481齿轮轮齿磨损和损伤术语 GB5903工业闭式齿轮油 GB/T6394金属平均晶粒度测定方法 GB/T6402钢锻件超声检测方法 GB/T6404(所有部分齿轮装置的验收规范 GB/Z6413所有部分圆柱齿轮、锥齿轮和准双曲面齿轮胶合承载能力计算方法 GB/T7232金属热处理工艺术语 GB/T7631.7润滑剂和有关产品(L类)的分类第7部分:C组(齿轮 GB/T8121热处理工艺材料术语 GB 10062(所有部分锥齿轮承载能力计算方法 GB/T10063通用机械渐开线圆柱齿轮承载能力简化计算方法 GB/T10087圆柱蜗杆基本齿廓 GB/T10089圆柱蜗杆、蜗轮精度 GB/T10095(所有部分圆柱齿轮精度制 GB/T10096齿条精度 GB11120涡轮机油
GB/T39332一2020 GB/T12369直齿及斜齿锥齿轮基本齿廓 GB/T12759双圆弧圆柱齿轮基本齿廓 GB/T13298金属显微组织检验方法 GB/T13304.2钢分类第2部分;按主要质量等级和主要性能或使用特性的分类 GB/T13799双圆弧圆柱齿轮承载能力计算方法 GB13895重负荷车辆齿轮油(GL-5) GB 3924渐开线圆柱齿轮精度检验细则 GB/T14229齿轮接触疲劳强度试验方法 GB/T14230齿轮弯曲疲劳强度试验方法 GB/T14231齿轮装置效率测定方法 GB/T15753圆弧圆柱齿轮精度 GB/T16848直廓环面蜗杆、蜗轮精度 GB/T17107 锻件用结构钢牌号租力学性能 GB/T17879齿轮磨削后表面回火的浸蚀检验 圆柱齿轮 GB/Z18620(所有部分 检验实施规范 GB/T19406渐开线直齿和斜齿圆柱齿轮承载能力计算方法工业齿轮应用 GB 25744钢件渗碳火回火金相检验 GB/T28767车辆齿轮油分类 GB/T35089机器人用精密齿轮传动装置试验方法 齿轮齿轮测量仪的评价 GB 37161l 33923行星齿轮传动设计方法 GB 承载能力一般系数计算 HB 89.l 航空锥齿轮 HB/Z89.2航空锥齿轮齿面接触疲劳强度计算 89.3航空雉齿轮轮齿弯曲疲劳强度计算 HB HB/Z89.!航空锥齿轮胶合承载能力计算 重型机械通用技术条件第14部分铸钢件无损检测 JB/T5000.14 JB/T5000.15重型机械通用技术条件第15部分;锻钢件无损检测 JB/T5078高速齿轮材料选择及热处理质量控制的一般规定 JB/T6077齿轮调质工艺及其质量控制 JB/T6078齿轮装置质量检验总则 JB/T6395大型齿轮、齿圈锻件技术条件 JB/T7516齿轮气体渗碳热处理工艺及其质量控制 JB/T7929齿轮传动装置清洁度 JB/T8830高速渐开线圆柱齿轮和类似要求齿轮承载能力计算方法 JB/T8831 工业闭式齿轮的润滑油选用方法 JB/T9171 齿轮火焰及感应淖火工艺及其质量控制 9172齿轮渗氮、氮碳共渗工艺及其质量控制 9173齿轮碳氮共渗工艺及其质量控制 JB/T9204 钢件感应淬火金相检验 JB/T10419摆线针轮行星传动摆线齿轮和针轮精度 JB/T10424摩托车齿轮材料及热处理质量检验的一般规定 JT/T224中负荷车辆齿轮油 NB/SH/T0467合成工业齿轮油
GB/39332一2020 NB/SH/T0586工业闭式齿轮油换油指标 NB/T47013.3承压设备无损检测第3部分;超声检测 NB/T47013.4承压设备无损检测第4部分:;磁粉检测 NB/T47013.5承压设备无损检测第5部分:渗透检测 QC/T262汽车渗碳齿轮金相检验 SH/T0094蜗轮蜗杆油 SH/To13810号仪表油 SH/T0362抗氨汽轮机油 NB/SH/T0454特种精密仪表油规范 SH/T04654122号高低温仪表油 术语和定义 下列术语和定义适用于本文件
3.1 磨削烧伤grndingbunnm 在磨削过程中产生的局部瞬时高温使得轮齿表层的金相组织发生变化
注:在瞬时高温的作用下,被磨削轮齿的表层发生了不均匀回火或二次淬火现象
3.2 观色法visualobservaton 根据目测轮齿表面所呈现的颜色来判定磨削烧伤程度的方法
3.3 酸蚀法acidetehing 通过对轮齿表面进行酸蚀,而后根据所呈现的颜色来判定磨削烧伤程度的方法
3.4 金相检测法metallographicmeasurement 通过对磨削后轮齿表层材料进行显微组织分析来判定磨削烧伤程度的方法
3.5 油膜比厚fimthiekn nessSratio 最小油膜厚度与两啮合齿面的综合粗糙度和之比
3.6 齿面磨损surtaeweur 当一对啃合轮齿作相对滑动或滚动时出现的表面材料移失的现象
3.7 闪温nash temperature 齿面接触过程中因运动摩擦热引起的瞬时温升
3.8 成沟点chanmelpoint 在某温度点,润滑油将被冷却至半固体状态,此时以一定宽度的刀片从油中垂直划过,油面可以形 成沟状
3.9 弧高度areheight 被测试片在弹丸的冲击下表层发生塑性形变导致其向喷丸面呈球面状弯曲后,切人球面的特定基
GB/T39332一2020 准面到球面最高点之间的距离
3.10 弧高度试片 heettstrp are 以弧高度值综合度量喷丸工艺参数的一种专用的量规
注:分为标准弧高度试片(Almen试片)和非标准弧高度试片两类
前者用70号弹簧钢制成,共有三种尺寸规格, 即N,A和C型试片,最常用的是A型试片;后者的尺寸或材料为特殊制备,通过试验标定其弧高度值(或喷丸 强度)与标准试片弧高度值之间的对应关系
3.11 弧高度曲线archeightcurve 在喷丸工艺参数不变情况下,同一类型试片分别接受不同时长的喷丸,获得一组弧高度值随喷丸时 长变化的数据,据此绘制的“弧高度值-时间”曲线
3.12 喷丸强度shotpeeningintensity 弧高度曲线上存在饱和点,当一倍于饱和点的喷丸时间下狐高度值增量等于饱和点处弧高值的 0%时,该饱和点处的弧高度值
3.13 覆盖率coveragerate 受喷工件表面弹坑占据面积与受喷总面积之比,通常以百分比表示
注1:达到98%即可定义为100%的覆盖率,喷丸时间达到2倍于100%覆盖率时定义为200%的覆盖率,以此类推
注2:实际生产中可以用10倍放大镜目视检查覆盖率,亦可采用与标准喷丸件(或标准试块)对比进行检查
在对 覆盖率质量有争议时,可对其50倍金相显微镜照片进行图像分析,求出覆盖率的数值
设计 4.1几何设计 可依据以下标准: GB/T2821、GB/T3374所有部分),GB/T10087.GB/T12369,GB/T12759.
4.2强度计算 可依据以下标准: GB/T3480,GB/T3480.1',GB/T3480.5,GB/T3480.6,GB/T10062(所有部分),GB/T10063 GB/T13799,GB/T19406,GB/33923、HB/Z89.1、HB/Z89.2,HB/Z89.3,HB/Z89.4,JB/T8830
4.3精度确定 可依据以下标准: GB/T10089,GB/T10095(所有部分),GB/T10096,GB/T15753,GB/T16848JB/T10419.
4.4润滑设计 4.4.1设计基础 润滑设计是齿轮传动设计中的重要组成部分,设计者应充分了解以下有关内容 -润滑剂是啮合齿面之间的重要介质,可有效避免两齿面直接接触 1) 编制中的GB/T3480.2和GB/T3480.3将与GB/T3480.1一起共同代替GB/T348o
GB/39332一2020 -齿轮传动中滚动摩擦与滑动摩擦并存,且随啮合位置改变; 齿轮传递载荷较大时,齿面产生的摩擦热使得油温上升,从而加速油膜的破坏,故齿轮经常处 于边界润滑和混合润滑状态; -齿面当量曲率半径较小时,油楔形成条件较差; -齿轮润滑是间歇性的,每次啮合都会重新建立动压油膜 齿轮的材料、热处理、机加工、装配齿形及齿面形貌等对润滑性能影响很大; 齿轮润滑剂种类及润滑方式,对润滑效果影响很大; 主要的齿面损伤(如点蚀、胶合、磨损等)与润滑剂及润滑状态关系密切
4.4.2设计规范 可依据以下标准(不限于).: GB/3141,GB/T3481,GB5903,GB/Z6413(所有部分),GB/T7631.7,GB11120,GB13895 GB/T28767、HB/Z89.4、JT/T224、NB/SH/T0467、NB/SH/T0586、SH/T0094、SH/T0138 SH/T0362、NB/SH/T0454,SH/T0465
4.4.3油膜比厚与润滑状态 齿轮的润滑状态通常根据油膜比厚入分为边界润滑、混合润滑和全膜润滑三种,分类阔值应根据齿 面材料、粗糙度,润滑油品种类等综合考虑
油膜比厚按式(1)计算 入=hmim/ai十o 式中 最小油膜厚度,单位为微米(4m); hm 主动齿轮齿面粗糙度值Ra,单位为微米(um); 被动齿轮齿面粗糙度值Ra-g,单位为微米(Mm)
-般认为: 当入<1时,齿轮处于边界润滑状态
此时,油膜添加剂与齿面间形成的物理吸附膜、化学吸附 膜或化学反应膜在齿轮润滑中起到主导作用
典型的油膜厚度为0.0011 Am0.050m b 当1<入<3时,齿轮处于混合润滑状态
此时,润滑油中通常应添加适量的极压添加剂,齿面 负载由动压油膜和齿面粗糙峰点共同承担
当入>3,齿轮处于全膜润滑状态
此时,润滑剂的黏度起主导作用,油膜厚度远大于齿面粗糙 度,两啃合表面完全被连续的动压油膜隔开
典型的油膜厚度大于0.1m 齿轮的润滑状态往往随着轮齿的啮人到啮出在以上三个状态中渐变和转化,润滑设计应追求全膜 润滑状态并尽量延长它,同时应减少边界润滑状态,特别应避免极端的干接触状态(入=0). 4.4.4损伤与润滑 4.4.4.1 齿轮损伤 齿轮的材料、结构、精度、表面状态等基本要素在使用过程中可能受到损伤
常见的齿轮损伤形式有齿面接触疲劳点蚀与裂纹、齿根弯曲疲劳、齿面磨损、齿面胶合等,具体形 式见GB/T3481 4.4.4.2润滑作用 润滑对于齿轮的正常工作影响较大,主要表现为
GB/T39332一2020 对于齿面胶合:润滑对于抗拒齿面胶合作用极大,油品的黏度、添加剂、供油量、润滑方式等都 a 有影响,抑制或减少闪温的发生
计算方法可见GB/Z6413(所有部分)和HB/Z89.4
b 对于齿面磨损:齿面磨损与齿轮传动形式(开式或闭式,齿形是否修形、润滑方式、工作温 度、齿面材料及热处理等诸多因素有关,其中润滑对齿面磨损的影响尤为显著
对于齿面疲劳点蚀:润滑方式中润滑油黏度、减摩剂,基础油分子结构,滑动摩擦力、润滑方式、 腐蚀剂等因索对于延缓齿面点蚀均有较大的作用
计算方法可见GB/T3480,GB/T10062.2 和HB/Z89.2 对于振动和噪声;供油充足、黏度较高、润滑良好时,齿轮振动与噪声会明显下降
另外,极压 剂、减摩剂等对减振降噪具有一定的作用
对于传动效率;齿轮传动的功耗主要由齿面摩擦和搅油(或甩油)引起,合理的润滑方式和良好 的润滑条件可以有效地减少传动功耗,提高传动效率
fD 对于齿面烧伤和轮齿热屈服;润滑油选择不当或供油不足时,局部的高温(闪温)易造成齿面烧 伤,且高温还易产生热屈服,造成传动失效
通过良好的润滑,加上改进齿轮材质和热处理合 理修形等,可避免轮齿发生热屈服 4.4.5润滑油品 4.4.5.1 分类和指标 4.4.5.1.1按用途分为工业齿轮油和车辆齿轮油两类,按指标分为黏度等级和质量等级两类
工业齿 轮油又分为闭式齿轮油、蜗轮蜗杆油,车辆齿轮油的分类见GB/T28767
另外,高速齿轮箱可选用汽 轮机油(透平油. 4.4.5.1.2润滑油的要求如下: 工业闭式齿轮油的规格见GB5903; 合成工业齿轮油的规格见NB/SH/T0467; -蜗轮蜗杆油的规格见SH/T0094; L-TSA汽轮机油防锈汽轮机油)的规格见GB11120; 抗氨汽轮机油的规格见SH/T0362 中负荷车辆齿轮油(GL-4)的规格见JT/T224:; 重负荷车辆齿轮油(Gl-5)的规格见GB13895
4.4.5.2油品选用 各类油品的适用范围如下 闭式工业齿轮油;见JB/T8831,其中包含润滑油种类、黏度、润滑方式等选择
适用于渐开线 a 圆柱齿轮、圆弧圆柱齿轮及锥齿轮
车辆齿轮油;可参考汽车后桥齿轮负载和气温环境选择
负荷小、,环境温度低时宜选用成沟点 b 较低、黏度较小的齿轮油,负荷大、环境温度高时宜选用黏度较大的齿轮油
蜗轮蜗杆油;蜗轮蜗杆传动油膜形成困难、发热量大、效率低,宜选用黏度较大的涧滑油,见 sH/T0094
仪表润滑油;仪表齿轮传动精度要求较高,传递力矩和功耗较小,抗干扰能力差
润滑油要求 d 具有良好的抗老化抗低温、抗磨损性能,摩擦阻力小,且不易挥发和变质
宜选择仪表润滑 油,见SH/T0138,SH/T0454和SH/T0465
4.4.5.3油品选用注意事项 由于影响齿轮润滑状态的因素极为复杂,选择油品种类和黏度级别时,应结合实践经验考虑以下重
GB/39332一2020 要因素 齿轮啃合形态;渐开线圆柱齿轮传动的啃合线与滑动速度方向垂直,具有较好的形成油膜的楔 形条件;蜗轮蜗杆、锥齿轮等交错轴传动方式中,其啮合线与相对速度方向的夹角较小,不利于 形成油楔,宜选用黏度较高且含有一定添加剂的润滑油
负载和速度:高速轻载齿轮传动中,形成动压油膜的条件较好,宜选用低黏度不含极压添加剂 的润滑油;重载(尤其低速重载)形成动压油膜的条件较差,宜选用高黏度且含极压添加剂的润 滑油
润滑状态;边界润滑状态下,宜选用含极压抗磨剂的润滑油;全膜润滑状态下,黏度越高,油膜 越厚;混合润滑状态下,宜选用黏度适中且含少量添加剂的润滑油
工况条件;在高温、,潮湿的环境下,宜选用较强的抗氧化、抗乳化、抗泡性和防锈性能的油品;环 境温度和工作温度均较高时,宜选用黏度较大、黏温系数较小(黏度指数较大)且氧化安定性和 热稳定性较好的油品;低温时,宜选用凝点、倾点或成沟点较低且流动性较好的润滑油
4.4.5.4润滑系统设计 4.4.5.4.1基本要求 设计者至少应考虑以下问题: 通过调整系统涧滑剂的品种、黏度等参数,确保供油充足,连续 通过设立有效的密封和过滤装置,保持润滑油清洁,防尘防水,防止端泄与环境污染,提高系统 可靠性; 通过采取标准化和通用化结构,便于系统调整、检测、维修和更换润滑剂 通过使用工作预警装置,稳定系统油压,及时发现润滑故障; -通过选取冷热交换器,稳定、控制系统油温
4.4.5.4.2润滑方式 选择合适的润滑方式,可以保证齿轮副得到良好的润滑,提高齿轮寿命,减少润滑剂消耗等
常用 的润滑方式有油浴润滑、喷油润滑.油雾润滑、离心润滑,脂润滑,固体润滑、固液混合润滑等,可做如下 选择 对于中低速齿轮传动,宜采用油浴润滑和喷油润滑, -对于高速齿轮传动,宜采用压力喷油润滑,超高速传动则采用油气二相润滑 对于航天精密传动,可采用固体润滑
4.4.5.4.3润滑油的净化 常用方法的有过滤、沉淀、离心,粘附、磁选等,其中过滤净化的应用最为广泛
选用过滤器时,应至 少考虑以下因素 -油液,滤芯和壳体材料的相容性; 过滤精度; 通油能力; 油温; -滤芯的清洗和更换
材料与热处理 5 5.1原材料 可依据以下标准(不限于):
GB/T39332一2020 GB/T699,GB/T3077、GB/T3480,GB/T3480.5
5.2锻件 可依据以下标准(不限于): GB/T13304.2,GB/T17107、JB/T5078、JB/T6395、JB/T1042!
5.3热处理 可依据以下标准(不限于): GB/T7232、GB/T8121、GB/T25744、JB/T6077、JB/T7516、JB/T9171、JB/T9172、JB/T9173、 JB/T9204
o 机加工 6.1磨齿 机加工是实现齿轮从毛坯(铸、锻、棒料等)到成品物理减材的主要手段
由于在加工过程中原材料 的内部应力不断释放或叠加,对成品齿轮从表面到内部都有不同程度的正向或负向影响,其中磨齿造成 的齿面磨削烧伤、微裂纹和磨齿时齿根圃角的不当处理,会大大地降低齿轮的使用寿命
磨齿后的齿面损伤检测方法可依据GB/T13298,GB/T17879,或可参见HB77172002. 6.2磨削烧伤和磨削裂纹 磨齿机的操作者应了解以下内容 磨齿裂纹的产生主要来自磨削后轮齿的表面残余应力
磨削裂纹通常因磨削烧伤产生,而磨 a 削烧伤不一定产生磨削裂纹
b 磨削烧伤由于氧化膜厚度的不同在白光照射下会呈现出不同的颜色,对应烧伤程度由轻到重 排列顺序为;浅黄色、褐色、浅蓝色、蓝色、蓝黑色
裂纹在齿面垂直于螺旋线方向,裂纹彼此相互平行
其分布一般有以下形式 裂纹自齿顶沿齿高方向呈短线型或长短线交替型分布,长度在1nmm~5mm; -裂纹在节圆上部沿齿高呈短线型分布 裂纹自齿顶至节圆上部呈龟裂状(封闭网络状)分布 6.3磨削烧伤和磨削裂纹的检查方法 6.3.1概述 检查方法主要包括以下几种;观色法、酸蚀法、表层显微硬度试验法、残余应力测定法、金相检测法 和磁弹法
为保证检测结果的准确性和可靠性,必要时应采用两种或两种以上的方法配合使用
6.3.2观色法(目测法 应首先按照6.2b)和6.2c)的说明直观判断齿面是否有磨削烧伤、磨削裂纹以及烧伤程度等
由于轮齿表面受热氧化的情况非常复杂,比如当修复重磨时工件表面有时不会呈现其他颜色,这并 不能肯定轮齿表面无磨削烧伤,因此该方法不宜单独使用
6.3.3酸蚀法 磨削烧伤大多为回火烧伤,产生的回火索氏体在酸蚀后呈黑色
磨削有时也会产生二次淬火烧伤
GB/39332一2020 产生淖火马氏体及其他少量组织
因此可根据酸蚀后工件表面颜色来确定磨削烧伤的程度,操作方法 见GB/T17879. 由于被检工件经酸蚀后,即使无问题也不能不加处理地直接使用,所以传统的酸蚀法作为一种破坏 性的检测方法,仅适用于抽样检验
6.3.4表层显微硬度试验法 一般情况下,发生回火烧伤,齿面表层或次表层显微硬度会显著下降
下降越多,磨削烧伤就越严 重
表层显微硬度的测量可以一定程度地反映磨削烧伤的程度,且反应灵敏,数值可靠
由于该种方法需要制作金相试样,属于破坏性检验,仅适用于抽样检验
6.3.5残余应力测定法 利用x射线衍射应力分析来测定轮齿表面的残余应力,可以比较全面地反映磨削烧伤情况
但该 方法在技术上较为复杂
6.3.6金相检测法 金相检测法和硬度试验法相结合是一种较为准确、可靠的磨削烧伤检测方法,操作方法见 GB/T13298
由于金相检测时通常需要在被检部位取样,属于破坏性检验,其应用受到一定的限制 6.3.7磁弹法 磨削烧伤会导致工件磁结构内的磁序发生变化,因此可以用磁弹法探测工件表面烧伤的程度
该法有以下特点 属于无损检测 方便快速,精确度高,磨削烧伤值可以直接从仪器上读出; 在磨齿机上配备探头夹持工装后,借助机床的运动机构可以实现自动化在线检测操作,显著提 高检测效率 6.4磨齿工艺的基本要求 6.4.1切削当量o 切削当量Q
综合了磨齿工艺主要参数的匹配度,计算见式(2): Q 式中: Q, -切削当量,单位为立方毫米每分(mm'/min)3 -磨削速度,单位为立方毫米每分(mm/min); 磨削厚度,单位为毫米(mm); -磨削接触面宽度,单位为毫米(mm)
Q.在实际应用中的标准值为1nmm/min~10mm/min
鉴于渐开线性质及成型磨齿原理,磨齿 一直属于变量,所以不能固化每 过程中的、和b 个循环的Q、值,应考虑砂轮和轮齿接触面的变化对 切削当量Q
值的影响,避免齿面烧伤
6.4.2砂轮 根据轮齿模数和齿轮材料的不同,砂轮选用的型号要有所不同,主要是砂轮的硬度、粒度、组织号、
GB/T39332一2020 磨料及结合剂的不同组合
砂轮硬度可选择Q号,H号、J号,K号、L
号或M号; a 粒度可选择30井36井、40井、46井、54井、60井、70井80井或90井; b 8 组织号可选择3号、4号,5号,6号或7号 磨料可选择SG、wA、SA,MA或PA; d 结合剂可选择V; e fD 线速度可选择30m/s一50m/s 6.4.3冷却液 磨削冷却液(切削液)应选择含有极压添加剂的油品否则会使烧伤几率成倍增加
冷却液的黏度 应在10井一20井
黏度过高时,流动性差,不利于带走磨削热;黏度过低时,冷却液对齿面粗糙度的不 利影响较大
冷却液喷嘴宜使用上下两对,反复调整,应使冷却液喷射在磨削区域,压力应大于5MPa 6.4.4金刚修整轮 金刚修整轮是否锋利不但对磨削后齿轮的几何精度产生影响,对磨齿烧伤也会起到非常大的作用
锋利的金刚修整轮能够去除磨损的砂粒使砂轮保持锋利状态,减小切削时热量的产生
粗磨齿修整砂轮时,应使金刚修整轮和砂粒运动方向相反,令相对速度加快,以达到砂轮锋利的效 果;精磨齿修整砂轮时,应使金刚修整轮和砂粒运动方向一致,令相对速度降低,以达到保证几何精度的 要求
6.4.5机床精度 磨齿机主轴及工作台的不平稳运动在微观中会形成切向敲击,这种敲击不但会产生磨削振纹,还会 增加磨削热,进而导致齿面烧伤
磨齿机的安装、各部件的运动精度(特别是主轴的径向跳动和轴向跳 动)应严格遵守机床的出厂要求
6.5磨削裂纹的规避 6.5.1热处理 主要应控制表层碳浓度、奥氏体晶粒度和回火工艺
具体要求如下: 表层碳浓度;应根据齿轮材质要求使表面含碳量降到0.80%~1.00%,相应的碳化物和残余奥 a 氏体都应控制在3级(Qc/T262)以下
奥氏体晶粒度;可降低渗碳温度及淖火温度,以获得细小或隐品的马氏体组织
同时从源头开 b 始控制,原材料和锻坯晶粒度的要求应细小,宜选择6级8级(GB/T6394)
回火工艺;根据实际情况适当提高回火温度、延长保温时间,降低獐火应力,尤其在冬天,通常 应补充二次回火
6.5.2磨齿准备 主要应考虑磨削用量、磨削余量.冷却液、砂轮的选择与修整
具体要求如下 磨削用量:磨削深度进给量与磨削区的温度大致成正比,并且也是这几个磨削用量中对磨削区 a 温度影响最大的因素
因此,在保证加工效率的情况下应尽量减小进给量
从降低磨削热的 角度来看,宜选择较大的工作台展成速度和砂轮冲程次数;而砂轮转速应根据模数而定,通常 不宜选得过大
10
GB/39332一2020 b 磨削余量;应控制热处理前滚齿公法线留量和轮齿表面光洁度,应在热处理过程中采取防变形 措施,热处理后的车渗碳层,加工磨削基准的过程中应取多点找正齿部节圆,使齿面各部余量 分布均匀 冷却液;不应选用乳化液,因为冷却较为强烈,会加剧磨削区的热胀冷缩现象,产生较大的内应 力
应选用适当牌号的机油,冷却比较柔和,产生的内应力较小 砂轮;由于工件硬度较高,应选用硬度较软,组织疏散和磨料脆性较大的砂轮,提高自锐性,以 保持其良好的切削能力;在保证齿面光洁度的前提下,应选择粒度较粗的砂轮;应合理选择砂 轮修整用量,并及时修整
6.5.3磨齿操作 6.5.3.1烧伤的发现 早期发现烧伤是挽救工件不致报废的有效方法
第一次磨削循环存在工件变形过大、磨削很不均匀的风险,应仔细观察磨削载荷和声音变化如有 异常及时调整磨削参数
从第二次循环开始调整冷却油嘴位置,使磨削油喷射在齿节圆位置下方
每 -次循环结束应仔细观察磨削齿面,特别是在砂轮修整周期磨齿到最后一齿,用白纸映光仔细检查,如 发现泛黄或局部有色差变化应及时减小磨削当量
6.5.3.2烧伤的挽救 如果发现裂纹已经产生应马上停止磨削,及时对工件进行低温回火处理,防止裂纹进一步扩大
以 下经验可供参考 -20CrMnMo材料的齿轮磨削时极易产生烧伤、裂纹
表现为磨后停放几个小时,由于应力的 释放渗碳层经常出现裂纹,由浅至深,由少到多,先出现在平行于螺旋线方向,最终会形成网状 裂纹,使齿轮报废
磨齿时需要增加砂轮修整次数,第一刀粗磨适当增加后退量,减小所有循 环进给量,避免裂纹前期产生 20Cr2Ni4材料的齿轮磨削时由于材料黏度强,易堵塞砂轮空隙,进而产生烧伤
磨齿时需要 增加砂轮修整次数,减小精磨进给量
17CrNiMo6(或18CrNiMo7-6,或17Cr2Ni2Mo)材料的齿轮磨削时易产生回火层,应减小粗磨 最后一次循环的进给量
表面处理 7.1喷丸强化 7.1.1总述 喷丸强化可以改变或增加轮齿根部的压应力,提升齿轮的弯曲疲劳强度
工艺要求可参见JB/T1o174一2008 7.1.2设备与控制 7.1.2.1喷丸机 各种结构的喷丸机均应满足以下要求 保证稳定、可重复的喷丸强度和均匀覆盖率,喷丸强度为0.20Amm~0.70Amm a 提供弹丸尺寸筛选和破碎弹丸分选装置; b 提供干燥、稳定的弹丸流,并在导丸管路系统中装有弹丸流的指示装置,以及断流指示或警 c 11
GB/T39332一2020 报器 d 机械离心式喷丸机的离心轮转速可调节,通常范围600r/min4500r/min e 气动式喷丸机的气路系统中提供气压稳定器 完成喷丸后,零件表面上无任何水气和油污痕迹; f) 喷丸室内提供可供零件(或喷嘴)作简单运转的装置,以使零件被喷区域表面能得到均匀的 g 覆盖 从喷嘴(或离心轮)喷射出的弹丸流的中心线与零件外表面被喷区域表面的法线之间的夹角小 h 于30"; 可自动控制零件的喷丸时间 提供抽风除尘装置,确保喷丸室在工作期间处于负压,并保证经过除尘装置排出的气体符合环 保要求
正常喷丸应使用自动控制喷丸机,当对零件进行补喷操作时方可使用手工喷丸机
手工喷丸机至 少应满足上述a),c),),h)和j)中规定的要求 7.1.2.2工装 为确保被喷零件的指定喷丸区可以获得所规定的喷丸强度和均匀覆盖率,喷丸工装应满足以下 要求 可以保证工件在喷丸室内做特定方式的运动如水平或垂直方向的直线运动、圆周运动、往复 a 摆动等) b 可以用来测定模拟工件所需喷丸部位的喷丸强度和覆盖率
7.1.2.3模拟工件 为达到规定的喷丸要求,需要通过模拟工件来调整工艺参数,检验强化质量
模拟工件应满足以下 要求 可以以实际零件为模拟工件,或采用多种型材组合; a b 可以安装在承载工件的工装上 被固定的试片位置与数目满足规定要求,试片与喷嘴(或离心轮)之间的距离等于被喷工件表 c 面与喷嘴的距离
7.1.3被喷工件 工件要求 除了特殊注明外(例如需要对部分喷丸表面进行再加工),喷丸前工件尺寸及表面粗糙度应满 a 足图纸或工艺上的全部要求,如发现通过喷丸可能被掩盖的缺陷时,应交质量部门处理 b 喷丸前工件应完成旨在达到规定力学性能的热处理 喷丸前工件表面应清洁、干燥,无油污必要时可采用无腐蚀性清洗剂清洗 c 除另有规定,工件应在不受外力的状态下(工装夹紧力除外)接受喷丸 d 除特殊情况,喷丸后工件的指定表面不应以任何切削方式进行表面去层加工 e 喷丸后工件的指定表面如果必须进行加工时,只允许琦磨或研磨去层,去层深度不应超过 f 1/10~1/5残余压应力层深度
7.1.4操作准备 7.1.4.1工艺文件 文件内容应包括喷丸工艺的全过程
12
GB/39332一2020 7.1.4.2设备的检查与调整 操作要求 a 目视检查喷嘴是否塔塞,是否有腐蚀物.油脂等.必要时应加以清洗和清除 b 喷丸机内的弹丸数量应满足连续喷丸的要求; 弹丸筛选和分选机构应正常工作 c 工件和工装应分别满足7.1.3和7.1.2.2的要求
d 7.1.4.3喷丸强度和覆盖率的检查与调整 操作要求 喷丸强度小于0.15Amm时,应采用N型试片测量喷丸强度;喷丸强度在0.15Amm一0.60Ammm aa 之间时,应采用A型试片;喷丸强度处大于0.60Amm时,应采用C型试片
b 将试片夹具分别固定在规定的各个喷丸部位的模拟工件上,再把模拟工件固定在夹具上
调整喷嘴(或离心轮)至各试片之间距离和角度(喷嘴至试片距离100nmm一200mm).开动运 转机构进行喷丸
卸下试片以非喷丸面为基准面测量其弧高值
用一组试片经不同时长(或 次数)喷丸之后,获得弧高度曲线,饱和点弧高即喷丸强度
当由以上步骤测得的喷丸强度高于或低于规定值时.则应调整工艺参数(如弹丸速度等),直至 达到规定值为止
用10倍放大镜检查零件表面的覆盖率,可以采用与工件材料相同的板材料在固定试片夹具附 近与试片同时喷丸的方法,测定覆盖率
调整各工艺参数,直至覆盖率达到图纸规定为止
7.1.4.4非喷丸区保护 操作要求 对于面积较大非喷丸区,可以采用金属板或橡皮板加以遮蔽保护; a b对于面积较小非喷丸区,可以采用厚度约1mm的橡胶薄膜、胶带或胶布等进行遮蔽保护 7.1.5喷丸与质量控制 7.1.5.1完成以上准备并检验合格后,方可开始对工件进行喷丸操作
7.1.5.2在生产中,检验喷丸强度和覆盖率的时间间隔应按以下规定 a 当一批工件完成喷丸时,最后一个工件再进行一次检验, b) 每连续工作一段时间(如8h)后,暂停喷丸进行一次检验,检验合格才可继续喷丸处理: 质检员认为必要时,随时可以进行检验
c 7.1.5.3覆盖率的检验方法应按以下规定: 依照3.13的说明检验覆盖率 aa b) 工件各区域的覆盖率与相关部门提供的标准试块持续对比
7.1.5.4同一种工件提交检验时 对于首批喷丸工件,应附上首次做过的一组或几组)弧高度曲线试片或其等同试片即非标准 a 试片); b对于后续喷丸工件,只需附上一片(或几片)作过喷丸强化的试片或其等同试片(即非标准 试片. 13
GB/T39332一2020 7.1.5.5如果提交的喷丸强度或覆盖率低于规定要求,应对工件做补教喷丸处理
7.1.5.6如果提交的喷丸强度或覆盖率高于规定要求,工件应交质量部门处理 7.1.5.7补救喷丸所采用的强化工艺参数应符合规定,而喷丸强度应采用规定的下限
7.1.5.8每一批号的工件的首件喷丸合格时,应记录以下科目. 工件图号; a 工件的批次号; b 本批次工件的总数; c d 喷丸日期 喷丸机型号与工厂设备编号 fD 弹丸材料、尺寸及硬度; 喷嘴(或离心轮)数目及与工件(或模拟件)各部位之间的距离与角度(附草图) g h 各个喷嘴的空气压力或离心轮转速(附草图); 工件各个部位规定的喷丸强度和实际的喷丸强度(试片多时附草图和试片编号说明) 实际的覆盖率; k 次装机单个(或多个)工件在喷丸室内的喷丸总时间(即零件被喷表面处于弹丸流和离开喷 丸流的时间之和)
7.1.6喷丸后处理 应做到以下事项 清除工件部位的弹丸及粉尘(清除方式可采用棉纱擦或压缩空气吹); aa b) 必要时可采用无腐蚀性清洗剂清洗零件表面; 如需对喷丸后的工件加热处理,限制最高加热温度,不超过该工件的服役温度 c 工件的喷丸区内不做硬度实验 d 精加工件进行防锈处理
7.2齿面光整 是将工件和磨具置于材料箱中,在复杂的相对运动作用下,磨具始终以一定的压力对工件的各表面 进行碰撞、滚挤,刻划和微量磨削,从而细化表面形貌,改善力学性能,提升轮齿的接触疲劳强度
其工艺要求可参见JB/T110822011
8 检测与试验 8.1齿轮精度测量 可依据以下标准: GB/T13924,GB/T37161,GB/Z18620(所有部分). 8.2齿轮装置试验 可依据以下标准(不限于) GB/T6404所有部分)、GB/T14229、GB/T14230、GB/T14231、GB/T35089、JB/T6078、 JB/T7929 14
GB/39332一2020 8.3齿轮探伤检测 8.3.1 毛坯探伤 可依据以下标准(不限于: GB/T6402,JB/T5000.14、JB/T5000.15
8.3.2 齿部探伤 可依据以下标准(不限于).: NB/T47013.3、NB/T47013,4、NB/T47013.5
15
GB/T39332一2020 考文献 参 [1]HB7717一2002航空钢制件磨削烧伤酸侵蚀检查 [[2]JB/T10174一2008钢铁零件强化喷丸的质量检验方法 [3]JB/T11082一2011内燃机零部件表面光整加工技术条件 16
高精度齿轮抗疲劳制造通用技术要求GB/T39332-2020
随着工业生产水平的不断提升,越来越多的设备需要高精度齿轮进行传动。然而,齿轮在长时间高速运转过程中容易出现疲劳断裂等问题,对设备的正常运行带来严重的影响。因此,如何保证齿轮的抗疲劳性能成为制造业界关注的焦点之一。
为此,《高精度齿轮抗疲劳制造通用技术要求GB/T39332-2020》应运而生。该标准自2020年12月1日起生效,旨在统一齿轮抗疲劳制造的技术要求和测试方法,提高齿轮的可靠性和使用寿命。
主要内容
该标准涉及了齿轮的制造、加工、检测等多个方面,其中主要包括以下方面:
- 齿轮制造的基本要求
- 齿轮的尺寸公差
- 齿轮的硬度和表面质量
- 齿轮的热处理
- 齿轮的抗疲劳性能评定方法
这些方面的规定都是为了保证齿轮的稳定性和可靠性。此外,对于一些特殊形式的齿轮,如锥齿轮、蜗杆齿轮等,还有专门的技术要求。
意义
《高精度齿轮抗疲劳制造通用技术要求GB/T39332-2020》的发布,对于提高齿轮制造业 [Network Error]习和遵守该标准,努力提高齿轮的制造质量,为推进制造业的高质量发展做出自己的贡献。