GB/T36697-2018
铸造起重机报废条件
Discardqualificationforladlecrane
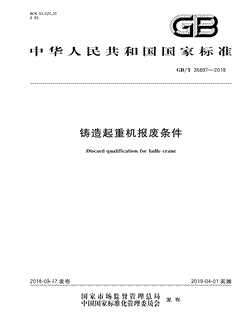
- 中国标准分类号(CCS)J80
- 国际标准分类号(ICS)53.020.20
- 实施日期2019-04-01
- 文件格式PDF
- 文本页数22页
- 文件大小1.46M
以图片形式预览铸造起重机报废条件
铸造起重机报废条件
国家标准 GB/T36697一2018 铸造起重机报废条件 Discardqualifieationforladleerane 2018-09-17发布 2019-04-01实施 国家市场监督管理总局 发布 币国国家标准化管理委员会国家标准
GB/T36697一2018 次 目 前言 范围 2 规范性引用文件 3 术语和定义 报废条件 整机报废评价方法 # 报废后的处置 附录A资料性附录铸造起重机设计寿命计算方法 附录B(资料性附录》铸造起重机使用寿命影响因素 附录C规范性附录铸造起重机主要零部件报废条件 铸造起重机剩余寿命评价方法 附录D规范性附录 参考文献 19
GB/36697一2018 前 言 本标准按照GB/T1.1一2009给出的规则起草
本标准由机械工业联合会提出
本标准由全国起重机械标准化技术委员会(SAC/TC227)归口
本标准负责起草单位:太原重型机械集团工程技术研发有限公司、北京起重运输机械设计研究院有 限公司、太原科技大学、国家起重运输机械质量监督检验中心
本标准参加起草单位:北京起重运输机械设计研究院河南分院、大连华锐重工集团股份有限公司、 河南省矿山起重机有限公司、科尼起重设备(上海)有限公司太原钢铁(集团)有限公司河南卫华机械 工程研究院有限公司、法兰泰克重工股份有限公司、山起重型机械股份公司、宁波市凹凸重工有限公司、 重庆起重机厂有限责任公司、江西起重机械总厂,河南巨人起重机集团有限公司、宝山钢铁股份有限公 司、上海金艺检测技术有限公司、宝钢股份武钢有限公司
本标准主要起草人;顾翠云,尚洪,徐格宁,赵春晖,申昌宏,王顺亭,顾红泽、,陶天华,连晋华、林夫奎 刘焕江、须雷、曾令,任海涛、周继红,王首成,董青,王久元,吴军、袁秀峰、刘永庆,赵学明、罗祯利,刘晓生、 高征、陈贤波、李继承、陈驰中、阎少泉、于万成、阎颖、王照峰
GB/36697一2018 铸造起重机报废条件 范围 本标准规定了铸造起重机的报废条件及评价方法
本标准适用于吊运熔融金属的起重机
规范性引用文件 下列文件对于本文件的应用是必不可少的
凡是注日期的引用文件,仅注日期的版本适用于本文 件
凡是不注日期的引用文件,其最新版本(包括所有的修改单)适用于本文件
GB/T3811起重机设计规范 GB/T5972起重机钢丝绳保养、维护、检验和报废 GB/T6067.1一2010起重机械安全规程第1部分:总则 GB/T6974.1起重机术语第1部分:通用术语 GB/T6974.5起重机术语第5部分桥式和门式起重机 GB/T14405一2011通用桥式起重机 GB/T14711一2013中小型旋转电机通用安全要求 GB/T30024起重机金属结构能力验证 术语和定义 GB/T6974.1和GB/T6974.5界定的以及下列术语和定义适用于本文件
3.1 主体结构件mainstructure 其失效将导致整机丧失使用功能的起重机主要承载结构(主梁和端梁)
3.2 设计寿命designlife 基于起重机初始设计要求的载荷循环数、载荷谱条件下的许用工作时间
3.3 使用寿命servieelite 在实际工作循环数,载荷谱条件下,起重机从投人使用至达到报废条件的实际工作时间
3,4 剩余寿命remaininglife 起重机从当前时间到其报废为止的工作时间,即使用寿命与已使用时间的差值
报废条件 4.1整机报废条件 4.1.1设计寿命计算 铸造起重机总工作循环次数应按GB/T3811的规定进行选取
主炼钢生产线上铸造起重机设计
GB/T36697一2018 寿命的计算方法参见附录A 4.1.2使用寿命影响因素 影响铸造起重机使用寿命的主要因素包括构造形式、载荷状态、设计应力、制造工艺、安装质量、轨 道误差、工作环境、操作方式、维护保养等
轨道接头缺陷对使用寿命影响较大,其影响程度参见附录B. 4.1.3整机报废原则 主体结构件的报废决定整机的报废
机械零部件、电气元器件、安全防护装置等主要零部件具有可 更换性,不决定整机的报废
4.1.4整机报废判定准则 铸造起重机达到下列条件之一时,应报废: 起重机主体结构件达到报废条件时; a 起重机主体结构件预期剩余寿命小于18个月时
b) 4.2主要零部件报废条件 与铸造起重机安全运行直接关联的主要零部件达到报废条件时,应及时更换,不应影响铸造起重机 的安全性能
主要零部件的报废条件应按附录C的规定执行
5 整机报废评价方法 5.1总则 铸造起重机整机报废可采用下列方法进行评价 主体结构件报废限值条件评价法 a b 主体结构件剩余寿命报废评价法
5.2主体结构件报废限值条件评价方法 5.2.1主体结构件报废条件 5.2.1.1塑性变形 当主体结构件产生塑性变形,致使工作机构不能正常地安全运行时,应报废
5.2.1.2静态刚性 当铸造起重机小车起吊额定载荷位于跨中,与载荷试验时的原始下挠值(或设计计算下挠值)相比 主梁下挠值增加量达到或超过跨度的0.15/1000时,应报废
5.2.1.3稳定性 主梁的水平方向弯曲值、上翼缘板的水平偏斜值、腹板的垂直偏斜值等检测值达到或超过 5.2.1.3.1 GB/T14405-2011中5.7规定值的140%时,不准许修复,应报废
5.2.1.3.2主梁腹板的局部翘曲值达到或超过GB/T14405一201l中5.7规定值的140%时,如不能修 复,应报废
GB/36697一2018 5.2.1.4裂纹 5.2.1.4.1对于主梁跨中1/5长度范围内,在承受拉应力的下翼缘板或腹板上距离下翼缘板1/5高度 范围内,母材出现与主梁长度方向夹角大于45"的目测可见裂纹时,不准许修复,应报废 5.2.1.4.2主梁承受非对称循环交变应力,根据应力循环特性均值r=0.28,最大应力.(疲劳许用应 力[o,],焊接构件应力集中情况等级、材料的断裂韧性Kc、几何修正系数Y按式(D.6)计算得出的临 界裂纹长度见表1
应力越大,临界裂纹长度越小
表1铸造起重机常用结构临界裂纹长度 临界裂纹长度a 媒接构件 儿何修正系数Y 断裂韧性Ke 疲劳许用应力[d nmmm 应力集中 材料 工作级别 MPa MPavm 情况等级 中心裂纹边缘裂纹 边缘裂纹 中心裂纹 K0 228.0 101 81 97 K1 22 208.2 Q235 129 K2 181.3 161 128 K3 136.6 283 226 E6 Ko 239.7 47 37 KI 218.0 57 45 Q345 92.7 61 K2 188.6 76 138 K33 140.7 110 Ko 193.3 14 13 K1 175.6 171 136 Q235 129 K2 152.4 228 181 K33 1l3.8 409 326 E7 1.12 53 Ko 201.7 67 65 K1 182.5 82 Q345 92. 87 K2 157.5 110 K33 116.6 201 160 Ko 162.9 199 159 K1 148.0 241 192 12s Q235 K2 127.4 326 260 K3 94.4 594 473 E8 Ko 168.8 96 76 17 K1 93 152.9 Q345 92.7 K2 131.0 159 127 96.4 K33 294 234 注1中心裂纹 板内区域的裂纹
注2:边缘裂纹 板边区域的裂纹
注3,媒接构件应力集中情况等级参见GB/T3811一2008的5.8.3及附录o.
GB/T36697一2018 5.2.1.4.3对于5.2.1.4.1规定外的其他主要受力部分母材和焊缝的裂纹,应根据受力情况和裂纹情况 采取阻止措施,并采取加强或改变应力分布等措施修复
如果不能修复或同一位置修复超过三次,应报 废
当裂纹达到表1的临界裂纹长度时,应停止使用
5.2.1.5构件腐蚀 主要受力构件发生腐蚀时,应进行检查,测量和强度核算
当主要受力构件断面腐蚀达设计厚度的 10%时,如不能修复,应报废
主要受力构件的连接处发生腐蚀时,应进行检查、,测量和强度核算
当连接处的强度不能满足设计 要求时,应进行修复
如不能修复,应报废
5.2.1.6钞轴孔磨损 端梁上的轴孔因磨损变形,在任意方向上的直径大于设计直径的7%时,如不能修复,应报废
5.2.2主体结构件报废条件评价方法 5.2.2.1 塑性变形 起升机构起吊额定载荷,按产品使用说明书的规定,进行铸造起重机运行机构、小车运行机构,起升 机构的联合动作,检查是否存在因主梁,端梁的塑性变形导致各机构不能正常起动、运行和停止
5.2.2.2静态刚性 根据GB/T14405一2011中6.9.4规定的方法测量主梁下挠值 5.2.2.3稳定性 根据GB/T14405一2011中6.2.3.1规定的方法测量主梁水平方向弯曲值,根据GB/T14405 2011中5.7规定的方法测量主梁上翼缘板的水平偏斜值、腹板的垂直偏斜值、主梁腹板的局部翘曲值
5.2.2.4裂纹 应采用适宜的检测方法检查主体结构件母材及焊缝是否存在裂纹,以及裂纹尺寸、位置、方向等 参数: 目视或借助望远镜、照相机、窥视镜、视频系统等辅助设备进行观察,或采用声发射方法检测 a 根据具体位置选择无损检测方法 b 磁粉检测MT;主体结构件表面及近表面裂纹检测; 渗透检测PT;主体结构件表面、近表面及开口处裂纹检测 -超声检测UT;主体结构件及媒缝内部裂纹检测 射线检测RT:主体结构件及焊缝内部裂纹检测
5.2.2.5构件腐蚀 清除构件表面锈蚀层,测量母材断面厚度,将母材厚度实测值与设计值进行对比,得出母材厚度锈 蚀比值,测量三次取平均值
5.2.2.6铵轴孔磨损 对端梁上的轴孔磨损量进行检查和测量,将轴孔在任意方向上的直径实测值与设计值进行比较,得 出轴孔直径增加量,测量三次取平均值
GB/36697一2018 5.3主体结构件剩余寿命报废评价方法 5.3.1确定铸造起重机的设计寿命可以采用下列方法 设计文件应明确设计寿命,设计文件由制造商提供; a b)参照附录A计算设计寿命
5.3.2主体结构件设计寿命应根据工作循环数和载荷谱数据的获取方式按表2的规定折减
折减后 的设计寿命为折减系数乘以设计寿命
表2铸造起重机设计寿命折减系数 序号 数据获取方式 折减系数 铸造起重机带有安全监控管理系统,该系统在使用时能够自动采集 1.0 工作循环数和载荷谱,且操作人员无法关闭该系统 根据铸造起重机工艺流程,计算工作循环数和载荷谱 0.9 根据生产线年产量数据,估算工作循环数和载荷谐 0.8 5.3.3当起重机已使用时间达到设计寿命的50%时,应进行首次剩余寿命评估,评价方法见附录D
剩余寿命的下次评估时间可按已使用时间达到上次剩余寿命评价结果的50%递推确定,也可由用户根 据评估结果和起重机使用工况采取其他更安全的处理方式
报废后的处置 6 对于达到报废条件的起重机,使用单位至少应采取下列措施 解体、消除其功能,并保留解体前、后的照片或视频; a b)办理注销登记手续
GB/T36697一2018 附 录 A 资料性附录) 铸造起重机设计寿命计算方法 铸造起重机设计寿命计算方法 铸造起重机的一个工作循环是指从地面起吊一个物品起,到开始起吊下一个物品时止,包括起升机 构升降,起重机运行、小车运行及正常的停歇在内的一个完整的工作过程
对于主炼钢生产线上的一台 特定的铸造起重机,在每个工艺流程之内的工作循环数、每天完成的工艺流程数、每年工作天数均为固 定的情况下,按式(A.1)和式(A.2)计算每天工作循环数N以及载荷谱系数K, (A.1 N=Na十No1 Na1/m1 No/me (A.2 K lg iQ 式中 满包质量,单位为千克(kg); m1 空包质量,单位为千克(kg) me3: -每天起吊满包的次数; Nat N 每天起吊空包的次数; NQ 额定起重量,单位为千克(kg).
mo 当主体结构件的设计应力与按GB/T38112008中表33规定的拉伸和压缩疲劳许用应力的基本 值计算得到的疲劳许用应力一致时,按GB/T3811一2008中表1、表3的规定选取相应工作级别的起重 机工作循环总次数cT
当载荷谱系数K,、每天工作循环次数N.每年工作天数1确定的情况下,可 以由工作循环总次数按式(A.3)折算成工作年数T (A.3 设计应力的大小直接影响铸造起重机的设计寿命,而设计寿命决定使用寿命的固有属性
降低设 计应力可以延长铸造起重机的设计寿命
A.2铸造起重机设计寿命计算示例 已知;一台工作级别为A8,额定起重量mq= -125t的铸造起重机,空钢包自重m=45t,每天起吊 一60,满包重量mau=125t每天起吊满包次数Mw一70,每年工作天数/一350. 空包次数No8 按式(A.1)和式(A.2)计算每天工作循环次数Na、载荷谱系数K, N
=No十Ne=70十60=130(次 No/me 60/45 1Q =0.56 K,= -H绘 -兴 1305 lQ 1Q 根据GB/T3811一2008的表2,K在0.5~1.0之间对应载荷状态级别为Q4;根据GB/T3811 2008的表3,载荷状态级别Q4、工作级别A8对应起重机使用等级为U6;根据GB/T3811一2008的 表1,使用等级为U6对应起重机总工作循环次数5.00x10
GB/T36697一2018 附 录 B 资料性附录) 铸造起重机使用寿命影响因素 B.1总则 铸造起重机使用寿命受构造形式、载荷状态、设计应力、制造工艺、安装质量、轨道误差、工作环境、 操作方式、维护保养等综合因素影响
使用单位应按GB/T28264的规定设置安全监控管理系统,按 GB/T10183.1的规定控制轨道公差,按GB/T31052.1.GB/T31052.5的规定进行检查与维护
B.2轨道接头状态对疲劳剩余寿命的影响度D 起重机轨道接头高低差和间隙产生的运行冲击系数按GB/T22437.12008的式(D.10)和 式(D.11计算,也可按GB/T3811一2008的式(9)进行计算
剩余寿命的影响度D按式(B.1)计算 D (B.1 么 式中 轨道接头无缺陷情况下疲劳剩余寿命,单位为循环次数 L -轨道接头有缺陷情况下疲劳剩余寿命,单位为循环次数
L2 起重机运行轨道接头有缺陷情况下,轨道接头高低差,运行冲击系数及对疲劳剩余寿命的影响度 D见表B.1
轨道接头高低差的增大引起运行冲击系数的增大,从而导致疲劳剩余寿命影响度的提高
表B1轨道接头轨道高低差、运行冲击系数及对疲劳剩余寿命的影响度D 轨道接头高低差/mm 10 运行冲击系数中 GB/T38112008 1.l8l.21 l.231.251.27 1.291.30 .32l.33 1.34 式(9) 0.37 0.45 0.520.550.57 疲劳剩余寿命的影响度0.24 0.32 0.43 0.48 0.50 1.061.13 1.191.25 1.31 1.37 1.43 .491.55 1.60 运行冲击系数中 GB/T22437.12008 式(D.10) 疲劳剩余寿命的影响度D0.230.370.510.600.680.720.770.8o0.840.86
GB/36697一2018 录 附 C 规范性附录 铸造起重机主要零部件报废条件 C.1卷筒 卷简出现下列情况之一时,应报废: 影响性能的表面缺陷,如裂纹等; a b 筒壁磨损量达到原壁厚的20%; 绳槽有缺损或不正常磨损
c C.2滑轮 滑轮出现下列情况之一时,应报废: 影响性能的表面缺陷,如裂纹等; a b 轮槽不均匀磨损量达到3 mm; 轮槽壁厚磨损量达到原壁厚的20%; c d 因磨损使轮槽底部直径减少量达到钢丝绳直径的40%; 轮毂与轴承、轴与轴承出现明显滑移间隙或位移,无法修复时
e 钢丝绳组件 c31起升开机构任意一根蝌丝绳达到报废条件时,应里换同一起升机构所有的钢丝继. c.3.2钢丝绳的报废条件应符合GB/T5972的规定,其中断丝数在GB/T5972规定的基础上折 减50%
c.3.3钢丝绳用楔型接头、普通套环、重型套环,压板、钢丝绳夹座等连接件,当出现下列情况之一时不 准许修复,应报废; 表面裂纹 a b) 绳槽表面磨损量达到钢丝绳直径的5% 轴孔磨损量达到设计直径的5% c 明显塑性变形
d C.4制动器 C.4.1驱动装置、制动弹簧、传动构件、制动衬垫应按GB/T6067.1一2010中4.2.6.7的规定进行报废
C.4.2推动器出现下列情况之一时,应报废: -液压系统严重漏油,致使压力不足影响正常工作; 对地绝缘电阻低于1M. C.4.3制动轮(盘)出现下列情况之一时,应报废: 影响性能的表面裂纹等缺陷 a b 起升机构的制动轮制动面厚度磨损量达原厚度25%,其他机构的制动轮制动面厚度磨损量达
GB/T36697一2018 原厚度40% 起升机构的制动盘制动面厚度磨损量达到1.5mm,其他机构的制动盘制动面厚度磨损量达到 2 mm d 轮盘)面凹凸不平度达到1.5 mm
c.5减速器 C.5.1箱体 箱体出现下列情况之一时,应报废 裂纹; a b) 严重漏油影响正常使用,无法修复时
C.5.2传动齿轮 传动齿轮出现下列情况之一时,应报废: a 轮齿塑性变形造成齿面的峰或谷比理论齿形高于或低于轮齿模数的20%;轮齿折断大于或等 于齿宽的1/5,轮齿裂纹大于或等于齿宽的1/8;轮齿的裂纹未达到报废标准时,应设法除掉, 制止发展,对于起升机构除外; b 对于起升机构:齿面点蚀面积达到轮齿工作面积的25%,或20%以上点蚀坑最大尺寸达到0.1 模数,或20%的点蚀坑深度达到0.05模数; 对于除起升机构外的其他机构;齿面点蚀面积达到轮齿工作面积的50%,或20%以上点蚀坑 最大尺寸达0.2模数,或20%以上的点蚀坑深度达到0.15模数 齿面胶合面积达工作齿面面积的20%及胶合沟痕的深度达0.1模数; d 齿面剥落判定准则与齿面点蚀的判断准则相同 e 对于起升机构的齿轮齿根两侧磨损量之和达到0.05模数,对于其他机构齿轮齿根两侧磨损量 D 之和达到0.15模数
c.6轴类零件 轴类零件主要包括起升机构钢丝绳平衡杠杆钞轴、滑轮轴、卷筒轴、吊钩轴、吊叉轴、传动轴等,当出 现下列情况之一时不准许修复,应报废 表面裂纹; a b)平衡杠杆较轴、吊钩轴、吊叉轴表面磨损量达到设计直径的3%; c 明显塑性变形
联轴器 联轴器出现下列情况之一时,应报废 主要受力零件出现裂纹; a b 齿式联轴器轮齿断裂; 齿式联轴器齿厚磨损量;对于起升机构达到齿厚的10%,其他机构达到齿厚的20%; c d 万向联轴器十字轴轴向窜动达到1mm; 万向联轴器的花键磨损量达到原齿厚的10%; 卷筒联轴器磨损量指针达到规定极限值
10
GB/36697一2018 C.8叠片式吊钩 C.8.1叠片式吊钩出现下列情况之一时,应报废 表面裂纹; a b 吊钩的危险断面及钩颈处有塑性变形,或每一钩片侧向变形的弯曲半径小于板厚的10倍; 危险断面的磨损量达到设计尺寸的5%; c d 钩片之间间隙大于1.5" ,或铆钉、柱销松动,无法修复时 mm, e 钩片板材金相组织发生明显变化,或蠕变
板钩衬套磨损量达到设计尺寸的50%时,衬套应报废 C.8.2 C.9 吊叉 吊叉出现下列情况之一时,应报废: a 表面裂纹; b轴孔磨损量达到设计直径的5% 明显塑性变形; c 主要受力板材金相组织发生明显变化,或蠕变
d C.10起重横梁 起重横梁出现下列情况之一时,应报废 主要受力板材和焊缝出现表面裂纹,不能修复时; aa b)轴孔磨损量达到设计直径的5% 盖板和腹板出现塑性变形,板面侧向变形超过板材厚度 c 主要受力板材金相组织发生明显变化,或蠕变
d C.11锻造吊钩 锻造吊钩出现下列情况之一时,应报废: 表面裂纹; a 钩口的开口尺寸超过使用前基本尺寸的10% b 钩身的扭转变形角度达到10°; c 钩柄产生塑性变形; d 危险断面的磨损量达到设计尺寸的5%; e 钩柄直径腐蚀达到设计直径的5%
c.12吊钩横梁 吊钩横梁出现下列情况之一时,应报废: 表面裂纹; a b 磨损量达到设计尺寸的3%; 明显塑性变形
11
GB/T36697一2018 c.13钢丝绳平衡杠杆 钢丝绳平衡杠杆出现下列情况之一时,应报废: 表面裂纹; a b)轴孔磨损量达到设计直径的5%; c 厚度减小量达到设计尺寸的5% d 明显塑性变形
C.14小车架 小车架出现下列情况之一时,如不能修复应报废: 对于起升机构诚速器下箱体与小车架焊接为一体的结构,因变形导致变速齿轮不能正常呐合 a 或减速器箱体严重漏油; b 对于小车架母材和焊缝的裂纹,应根据受力情况和裂纹情况采取阻止措施,并采取加强或改 空垃力分布等撒施修复.如不能修复或同一位冒修复越过三次,应报废" 当小车架产生塑性变形,致使工作机构不能正常地安全运行
C.15电动机 电动机出现下列情况之一时,如不能修复应报废 电动机转子断条; a 线圈(绕组)短路或断路; b 电动机外壳或基座有影响安全的裂纹; c 电动机定子与转子发生扫膛, d 在正常使用条件下,电动机绝缘电阻下降,冷态未达1Mn,热态未达0.69Mn: e 在正常使用条件下,电动机工作时过热现象严重,经常超过GB/T14711一2013中表7规定的 fD 温度限值
C.16起重量限制器(含电子秤的超载功能》 起重量限制器(含超载功能)出现下列情况之一时,如不能修复应报废 在规定的载荷情况下,不能发出正确的报警或停车信号; a 起重量限制器系统精度低于5%,经调整后仍无法达到5%
12
GB/36697一2018 录 附 D 规范性附录 铸造起重机剩余寿命评价方法 D.1总则 铸造起重机主体结构件疲劳剩余寿命评价方法包含有裂纹情况和无裂纹情况
对于无裂纹情况 采用基于名义应力的结构细部疲劳寿命评估方法;对于有裂纹情况,采用基于断裂力学-疲劳累积损伤 的疲劳寿命评估方法
D.2疲劳危险点的位置 铸造起重机金属结构疲劳失效多发于疲劳性能薄弱、应力最大或应力集中处
通过对铸造起重机 金属结构的理论计算、有限元分析和模型梁试验,确定应定期检测的疲劳危险截面上的疲劳危险点.见 图D.1
图D.1 主梁疲劳危险点 D.3无裂纹情况 D.3.1疲劳强度Aa一N曲线 基于名义应力的结构细部疲劳强度按构件的非焊接件、焊缝接头形式,加载方向进行分类
以&- N曲线表征金属结构焊接接头的疲劳强度
其中,特征疲劳强度A
为在恒定应力范围下的应力循环 次数为2×10'次,可靠性概率为P,=97.7%(平均值减去由正态分布和单边检验得到的两个标准差 13
GB/T36697一2018 时的疲劳强度,如图D.2所示
Ao 104 10s 2X10s5×10 双斜率折线 川=3 Ao m=5 Ao
2x10y" 2x10 b 单斜率直线 说明 恒定应力范围的疲劳极限" 疲劳强度曲线的斜率常数 lgN; gA
在lg/Ig表示法中,该曲线的斜率为一1/m 图D.2Ar-N曲线和Ao
示图 金属结构母材和炽接接头的特征疲劳强度A
值以及Ag一N曲线的斜率常数m按GB/30024 的规定选取
D.3.2使用寿命计算 根据疲劳危险点焊接接头的Ao一N曲线,使用寿命按式(D.1)计算 N (D.1 o" 式中 使用寿命(总循环次数); N 名义应力变程; o 14
GB/36697一2018 常数,见表D.1和表D.2
表D.1具有双斜率折线的常数c 名义应力变程Aa 具有双斜率折线的常数c 特征疲劳强度 循环次数小于L点的心
-N曲线循环次数大于L点的g-N曲线 5×10”循环次数下的疲劳强度 Aa MPa 3 m=5 m一 MPa 40 29.5 1.28×10 1.l1×10 45 1.82×10" 33.2 2.00×10 50 36.8 2.50×10" 3.39×1o 56 41.3 3.51×10" 5,.98×10 63 46.4 5.00×10m 1.08×1018 7.16×1o 1.96×108 71 52.3 108 80 58.9 10e 1.02× 3.56X 90 10e 66.3 1.46× 6.41×10 o8 100 73.7 2,00×10" 1.09×10" 112 82.5 2.81×10 1.91×10" 125 92.1 3,91×10' 3.31×1o" 140 103.2 5.49×10'2 5.84×1o" 180o 132.6 1.17×10'8 2.05×10 表D.2具有单斜率直线的常数c 名义应力变程 具有单斜率直线的常数C 特征疲劳强度a 5×10循环次数下的疲劳强度 m=5 MPa MPa 63 52.45 1.98X10 71 59,1ll 3.61×10 80 66.60 6.55×10 90 74.93 1.18×10" 100 83.26 2.00×1o" 112 93,25 3,52×101" 6.10×1o" 125 104.07 116.56 1.08×1o1? 140 16o 133.21 2.10×101 3.78×1o17 180 149.86 6.40x1o” 200 166.51 15
GB/T36697一2018 表D.2(续) 名义应力变程 具有单斜率直线的常数C 特征疲劳强度Aa 5×10'循环次数下的疲劳强度 m=5 MPa MPa 225 187.32 1.15×10" 250 208.14 1.95×1o" 280 233.11 3,44×1o8 262.25 6.20×1o' 315 D.3.3疲劳剩余寿命计算 疲劳剩余寿命按式(D.2)计算
N=N一N (D.2 式中: N -疲劳剩余寿命,单位为循环次数 N
已使用的时间,单位为循环次数
注对于应力范围保持不变的常幅疲劳,可按上述方法进行疲劳寿命计算;对于变幅疲劳,可结合Palmgren-Miner 线性累积损伤进行疲劳寿命计算
D.4有裂纹情况 D.4.1疲劳危险点处应力谱的获取 铸造起重机金属结构疲劳危险点各工作循环过程中的第一主应力时间历程按式(D.3),式(D.4)及 式(D.5)进行计算
采用雨流计数法获取该起重机金属结构疲劳危险点的双参应力谱,包括应力均值谱 和应力幅值谱
铸造起重机金属结构疲劳危险点的正应力按式(D.3)计算 -L 岂 口= (D.3 式中 -疲劳危险点的正应力(拉应力为正,压应力为负),单位为兆帕(MPa); M,,.M 分别为疲劳危险点所在截面对y,r轴的弯矩,单位为牛毫米(N mm w,、W 分别为疲劳危险点所在截面对y、r轴的抗弯截面模量,单位为立方毫米(mmi). 铸造起重机金属结构疲劳危险点的切应力按式(D4)计算 FS D.4) 6 式中 疲劳危险点的切应力,单位为兆帕(MPa). F 疲劳危险点所处截面的剪力,单位为牛顿(N); S 疲劳危险点所处截面的静矩,单位为立方毫米(mm'); mm'); 疲劳危险点所处截面的惯性矩,单位为四次方毫米( 腹板厚度,单位为毫米(mm). 16
GB/36697一2018 在多轴复杂应力状态下,疲劳裂纹通常发生在应力三维度最大处,裂纹扩展方向为最大拉应力即 第 主应力)垂直方向,因此应将疲劳危险点的正应力及切应力按式(D.5)转换为第一主应力 十T " 十+、G" o!= D.5 式中: 疲劳危险点的第一主应力,单位为兆帕(MPa)
G 起重机金属结构疲劳危险点的应力谱应从所有工作循环的应力-时间历程中获取
D.4.2疲劳剩余寿命计算 在给定载荷作用下,根据线弹性断裂判定准则,结构件发生疲劳断裂时的临界裂纹长度a按 式(D.6计算 Kc (D.6) a1= Yo 式中: Ke 材料的断裂韧性; -几何修正系数,对于中心裂纹,Y=1;对于边缘裂纹,Y=1.12
为消除平均应力的影响,根据等效损伤原则,采用式(D.7)将所有幅值应力转化为循环特性r=0下 的应力变程Ao D.7 -口rm o A 6 1十 式中 r=一1时的材料疲劳极限,单位为兆帕(MPa) -材料的抗拉极限,单位为兆帕(MPa); a 循环特性厂时的应力均值,单位为兆帕(MPa); om 循环特性为r时的应力幅值,单位为兆帕(MPa); 循环特性r=0下的应力变程
Ao
当载荷为变幅载荷时,根据等寿命原则,采用Miner应力幅等效法,按式(D.8)将变幅载荷转化为 等幅载荷 口-“a D.8 式中 各级应力幅与循环次数N的比值; a 各级应力幅值
, 起重机主体结构疲劳剩余寿命按式(D.9)进行计算 mn
丰2 5 a8" a9.Sme-" YA
r"0.5m
一1 (D.9 =2 ln(a1/a0 m YAV元) 17
GB/T36697一2018 式中 初始裂纹长度; l0 a 临界裂纹长度; C、m 裂纹扩展速率参数,见表D.3
表D.3材料性能参数表 裂纹抄展门槛值K 裂纹扩展速率参数 断裂韧性Ke 屈服强度 抗拉强度 R=0) 材料 MPa MPa MPam c.X10-" n MPa丽 Q235 235 370 5.96 129 2.61 Q345 345 470 6.04 92." 1,06 4.66 18
GB/36697一2018 参考文献 [1]GB/T10183.1起重机车轮及大车和小车轨道公差第1部分;总则 [[2]GB/T22437.12008起重机载荷与载荷组合的设计原则第1部分;总则 [3] GB/T28264起重机械安全监控管理系统 [[4]GB/T31052.1起重机械检查与维护规程第1部分;总则 [[5]GB/T31052.5起重机械检查与维护规程第5部分;桥式和门式起重机