GB/T38657-2020
核电厂常规岛低压加热器技术条件
Specificationsforlowpressurefeedwaterheaterforconventionalislandinnuclearpowerstation
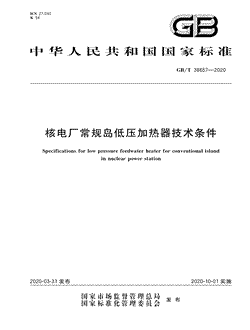
- 中国标准分类号(CCS)K54
- 国际标准分类号(ICS)27.040
- 实施日期2020-10-01
- 文件格式PDF
- 文本页数34页
- 文件大小3.29M
以图片形式预览核电厂常规岛低压加热器技术条件
核电厂常规岛低压加热器技术条件
国家标准 GB/T38657一2020 核电厂常规岛低压加热器技术条件 Speeifieationsforlowpressurefeedwater heaterforc0nventionalisland innuelearpowerstation 2020-03-31发布 2020-10-01实施 国家市场监督管理总局 发布 国家标涯花管理委员会国家标准
GB/T38657一2020 次 目 前言 范围 2 规范性引用文件 术语和定义 性能及设计要求 材料 25 制造 6 检查及验收 29 性能试验 31 31 油漆、标志、包装与运输
GB/38657一2020 前 言 本标准按照GB/T1.1一2009给出的规则起草
本标准由电器工业协会提出
本标准由全国汽轮机标准化技术委员会(SAC/TC172)归口
本标准起草单位:上海发电设备成套设计研究院有限责任公司、东方电气集团东方锅炉股份有限公 司、国核电力规划设计研究院有限公司、哈尔滨锅炉厂有限责任公司,东方电气集团东方汽轮机有限公 司、哈尔滨汽轮机厂有限责任公司、上海电气电站设备有限公司上海电站辅机厂、东方电气股份有限 公司
本标准主要起草人:陈鑫、邓科、刘军良、袁宁,赵洽军、杨小川,刘瑞梅、陆毅、高秀志、陈达平、王新红、 许宝军、张志鹏、胡方陈健、张义
GB/T38657一2020 核电厂常规岛低压加热器技术条件 范围 本标准规定了核电厂常规岛低压加热器(以下简称低加)的性能及设计要求、材料、制造、检验、验 收、性能试验及油漆、标志、包装与运输要求
本标准适用于U形管式低压加热器 规范性引用文件 下列文件对于本文件的应用是必不可少的
凡是注日期的引用文件,仅注日期的版本适用于本文 件
凡是不注日期的引用文件,其最新版本(包括所有的修改单)适用于本文件 GB/T150.1一201l压力容器第1部分;通用要求 压力容器第2部分;材料 GB/T150.22011 GB/T150.32011压力容器第3部分;设计 GB/T150.4压力容器第4部分:制造、检验和验收 GB/T151一2014热交换器 GB/T18042000 -般公差未注公差的线性和角度尺寸的公差 GB/T8923.1一2011涂覆涂料前钢材表面处理表面清洁度的目视评定第1部分:未涂覆过 的钢材表面和全面清除原有涂层后的钢材表面的锈蚀等级和处理等级 GB/T24593锅炉和热交换器用奥氏体不锈钢焊接钢管 GB/T25198压力容器封头 GB/T26929压力容器术语 GB/T29465浮头式热交换器用外头盖侧法兰 HG/T20592钢制管法兰(PN系列 HG;/T20615钢制管法兰(Class系列 JB/T4711压力容器涂敷与运输包装 JB/T5862汽轮机表面式给水加热器性能试验规程 NB/T47008承压设备用碳素钢和合金钢锻件 NB/T47010承压设备用不锈钢和耐热钢锻件 NB/T47013.22015承压设备无损检测第2部分;射线检测 NB/T47013.32015承压设备无损检测第3部分:超声检测 47013.4一2015承压设备无损检测第4部分;磁粉检测 NB/T47013.5一2015承压设备无损检测第5部分;渗透检测 NB/T47013.8一2012承压设备无损检测第8部分;泄漏检测 NB/T47013.102015承压设备无损检测第10部分;衍射时差法超声检测 NB/T47014承压设备焊接工艺评定 NB/T47015压力容器焊接规程 NB/T47018承压设备用焊接材料订货技术条件 NB/T47021甲型平焊法兰
GB/T38657一2020 NB/T47022乙型平焊法兰 NB/T47023长颈对焊法兰 NB/T47041塔式容器 NB/T47065,1容器支座第1部分;鞍式支座 NB/T47065.3 容器支座第又部分;耳式支摩 给水加热器用奥氏体不锈钢焊接钢管 YB/T4223 TSG21一2016固定式压力容器安全技术监察规程 3 术语和定义 GB/T150.1一2011,GB/T151一2014和GB/T26929界定的以及下列术语和定义适用于本文件
3.1 常规岛conventionalisland;CI 核电厂汽轮发电机组、配套设施及所在厂房的总称
3.2 低压加热器lowpressurefeedwaterheater 利用汽轮机低压段的抽汽来加热给水的换热器
注:低压加热器属于管壳公式换热器,是位于给水回热系统凝结水系与除氧器之间的给水加热器
3.3 设计压力desigpressure 设定的容器顶部的最高压力
注1,与相应的设计温度一起作为容器的基本设计载荷条件,其值大于或等于最高工作压力
注2:管程和壳程分别设定设计压力
3.4 管程设计温度tuhesidedesigntemperature 管箱壳体(或封头)及其他受压零件设计时设定的温度 注1,管程设计温度同时也是换热管的设计温度 注2:管程设计温度与管程设计压力一起作为管程设计载荷条件
3.5 壳程设计温度shellsidedesigntemperature 壳程壳体、封头及其他受压零件设计时设定的温度
注;壳程设计温度与壳程设计压力一起作为壳程设计载荷条件
3.6 终端温差terminaltemperaturedifterence;TD 进口处抽汽压力下的饱和温度与给水出口温度之差 注终端温差也可称为"上端差" 3.7 ;DcCA 疏水冷却段端差 drainsuhcoolerapproach; 疏水出口温度与给水进口温度之差
注:疏水冷却段端差也可称为“下端差”
3.8 凝结段condensingzone 通过蒸汽凝结加热给水的区段
GB/38657一2020 3.9 疏水冷却段 drainsubeolingzone;Dc 把疏水的热量传给给水,使凝结段的疏水温度降到低于饱和温度的区段
3.10 壳程压降shellsidepressuredrop 介质流经壳程的压力损失
3.11 管程压降tubesidepressuredrop 介质流经管程的压力损失
3.12 疏水drains 从较高压力级进人壳体的凝结水与加热器自身凝结水的总称 3.13 换热面积heattransferarea 3.13.1 计算换热面积efeetieare:n 以换热管外径为基准,扣除不参与换热的换热管长度后,计算得到的外表面积
3.13.2 公称换热面积 n0minalarea 圆整为整数后的计算换热面积 注:公称换热面积在设计总图中列出,并在铭牌上表示
3.14 满水时间waterfilleltime 加热器壳侧水位从最高液位上涨到顶部全充满水的时间
注:满水时间取下述流量较大情况下的时间: 两根换热管破裂(四个断口)的爆管量; 0%的给水流量.
3.15 共用旁踏sharedpas 低压加热器共用的管侧旁路系统 3.16 性能设计工况performancedesigncondition 以用户或设计委托方指定的考核性能指标进行传热计算的工况
注1:性能设计工况一般为汽轮机最大连续出力运行工况(TMCR工况) 注2:用户或设计委托方也可指定某一工况作为性能设计工况
3.17 强度设计工况strengthdesigncoditiom 以满足强度安全进行强度计算的工况
注1,强度设计工况一般为闵门全开工况(Vwo工况》 注2用户或设计委托方也可指定某一工况作为强度设计工况
3.18 污垢热阻roins resistance 换热面上沉积物所产生的传热阻力
GB/T38657一2020 性能及设计要求 4.1 一般规定 4.1.1设计条件 4.1.1.1用户或设计委托方应确定设计条件(见表1. 表1设计条件 建造规范项目 要求执行的建造规范内容 安装形式(卧式、正立式,倒立式》 安装位置(室内或室外 形式(或级数) 布置形式(单列或多列) 空间极限总长度加上检修所需空间 给水流量 给水进、出口温度 管程设计参数 给水进、出口熔值 包括运行时可能出现的各种工况 给水管道尺寸 管程设计压力 各加热燕汽流量 各加热蒸汽压力 各加热蒸汽温度 壳程设计参数 各加热蒸汽烙值 包括运行时可能出现的各种工况 各疏水进、出流量 各疏水进、出温度 各疏水进、出熔他 终端温差 端差 包括运行时可能出现的各种工况 疏水冷却段端差 水质 氯离子含量<25mg/L 安装位置气象特征与环境条件 安装位置地震基本烈度和设计基本地震加速度 安装位置场地土类别 其他 是否安装在凝汽器喉部 设计使用寿命 噪声标准
GB/38657一2020 4.1.1.2适宜时,用户或设计委托方可提出设计条件的补充项目(见表2). 表2设计条件补充项目 建造规范项目 要求执行的建造规范内容 壳体材质 管箱材质 材质 管板材质 换热管材质 其他部件材质 管程压降 压降 壳程压降 备用管 备用管子数量 管程设计温度 壳程设计压力 设计参数 壳程设计温度 耐压试验压力 污垢热阻 nm'/w,疏水冷却 用户或设计委托方未提供污垢热阻时,换热管内表面的污垢热阻可取不低于3.52x10-" <10-m
c/w 段换热管外表面的污垢热阻可取不低于5.28.x 4.1.2载荷 4.1.2.1设计时应考虑下列载荷 -内压,外压或最大压差; -膨胀量不同引起的作用力; 液柱静压力(液柱静压力小于设计压力的5%时,可忽略不计
4.1.2.2适用时应考虑下列因素: 自重及正常工作条件下或耐压试验状态下内装介质的重力载荷; 附属设备及隔热材料村里、管道,扶梯,平台等的重力载荷" 风、雪,地震载荷, 支座及其他型式支承件的反作用力 连接管道和其他部件的作用力; 温度梯度引起的作用力; 冲击载荷(包括压力急剧波动引起的冲击载荷,流体冲击引起的反力等); 运输或吊装时的作用力
4.1.3设计压力 4.1.3.1管程设计压力 管程设计压力应满足下列要求 大于或等于凝结水泵最小流量下的出口压力 大于或等于凝结水系统设计压力
GB/T38657一2020 4.1.3.2壳程设计压力 壳程设计压力满足下列要求 壳程设计压力不应低于各工况壳程最大运行压力的115%
壳侧运行压力低于大气压时,设计压力还应包括全真空压力
4.1.4设计温度 4.1.4.1管程设计温度 管程设计温度不应低于壳程设计压力下的燕汽饱和温度 4.1.4.2壳程设计温度 具有过热蒸汽冷却段时,在熔嫡图上,从强度设计工况的抽汽压力和温度处,作等饷线与设计压力 线相交,其壳体短节设计温度应不低于该交点处的温度其余部分壳体的设计温度应不低于设计压力下 的蒸汽饱和温度
没有设置过热蒸汽冷却段时,壳程设计温度应不低于壳程介质最高工作温度
4.1.5厚度附加量 厚度附加量按式(1)确定
4.1.5.1 C=C十C 式中: -厚度附加量,单位为毫米(m 1m; 材料厚度下极限偏差(见4.1.5.2),单位为毫米(mm); G G 腐蚀裕量(见4.1.5.3),单位为毫米(mm). 4.1.5.2板材或管材的厚度下极限偏差应符合相应材料标准的规定
4.1.5.3腐蚀裕量按下列原则考虑和选取 管板、浮头法兰和球冠形封头的两面均应考虑; 管箱平盖、凸形封头、管箱和壳体内表面应考虑; 管板和管箱平盖上开槽时,可将高出隔板槽底面的金属作为腐蚀裕量,但当腐蚀裕量大于槽深 时,还应加上两者的差值; 设备法兰和管法兰的内径面应考虑; 换热管、钩圈、浮头螺栓和纵向隔板(一般不考虑): 分程隔板的两面均应考虑; 拉杆、定距管、折流板和支持板等非受压元件(一般不考虑) 碳素钢或低合金钢制低加,壳程筒身腐蚀裕量不小于3mm; 对有均匀腐蚀或磨损的元件,应根据预期的设计使用年限和介质对金属材料的腐蚀速率(及磨 蚀速率)确定; 各元件受到的腐蚀程度不同时,可采用不同的腐蚀裕量
4.1.6许用应力 4.1.6.1材料的许用应力应按GB/T150.1一2011中表1,表2确定
4.1.6.2受压元件用钢材的许用应力值应按GB/T150.2一2011选取 4.1.6.3复合钢板的许用应力应按GB/T150.1一2011中4.4.3确定
4.1.6.4圆筒许用轴向压缩应力应按GB/T150.1一2011中4.4.5和相关标准确定
4.1.6.5需要考虑地震载荷或风载荷与4.1.2的载荷组合时,允许元件的设计应力不超过许用应力的
GB/38657一2020 1.2倍,其组合要求按相应标准的规定
4.1.7耐压试验 耐压试验的要求和试验压力应符合GB/T150.12011中4.6的要求
4.1.7.1 4.1.7.2耐压试验的种类和要求应在图样上注明
4.1.7.3按压差设计的低加,应在图样上提出压力试验时升、降压的具体要求 4.1.7.4应在图样上提出管接头的试验方法和压力
4.1.7.5试验时应在试验位置的最高点设置排气孔,排气孔应是设备接头或液压试验端盖的一部分,其 位置应利于设备充人试验介质时将气体完全排出
4.1.8封口焊检漏试验 4.1.8.1换热管与管板的封口焊应进行空气检漏及氨检漏试验,氮检漏允许漏率指标小于10-Pam'/s. 4.1.8.2检漏试验的种类和要求应在图样上注明
4.2结构设计 4.2.1结构型式 U形管式低加典型结构示意见图1
10 14 15 16 管箱、壳程法兰夹持管板 15 16 管板兼做壳程法兰 图1U形管式低加典型结构示意图
GB/T38657一2020 15 16 24 2117 管板与管箱,壳程焊接 说明: -管箱封头; 壳程法兰; 13 -拉杆; 19 -固定支座; 管箱壳体; -放气管, 20 壳程壳体; l4 -给水进口; 15 -放气管/仪表管 蒸汽进口管; -壳程封头; 21 -分程隔板; 22 给水出口; 10 防冲板; 16 -活动支座; -管板; 管箱法兰; 11 折流板/支持板; 17 -放水管/仪表管; 23 -管板; 12 24 管板; 换热管; 18 -疏水出口管; 人孔/检修孔
图1续) 4.2.2管程 4.2.2.1管板上换热管孔的布置 换热管常用排列形式见图2
正三角形排列30° 转角正三角形排列60") b 88 正方形排列90° 转角正方形排列(45° d 图2换热管排列形式示意图 换热管中心距按GB/T151一2014中6.3.1.2的规定
布管限定圆直径按GB/T151一2014中6.3.1.3的规定
GB/38657一2020 4.2.2.2管程分程 4.2.2.2.1管程数一般有1,2、4、6,8,1012共7种,常用的分程布置形式按GB/T151一2014中图6-12 4.2.2.2.2多管程结构应尽可能使各管程的换热管数相近,分程隔板槽形状简单、密封面长度较短
4.2.2.3管箱 管箱应符合下列要求: 多管程管箱平盖上的分程隔板槽结构尺寸应与管板的分程隔板槽一致,见4.2.2.8.3.2:; -管箱平盖与管箱的连接紧固件宜采用双头螺柱; 采用轴向人口接管的管箱,接管中心线处的最小深度不应小于接管内径的1/3 1pw'>9000kg/m”s)时,采用轴向人口接管的管箱宜设置防冲结构; 管箱可采用简节与椭圆封头组合形式,也可直接采用半球形封头形式,其计算方法按GB/T150.3- 2011的规定
注:p -管箱人口管的流体密度,单位为千克每立方米kg/m'); 管箱人口管的流体速度,单位为米每秒(m/s). 4.2.2.4分程隔板 分程隔板及与管板的连接结构应符合下列要求 分程隔板结构要求按GB/T151一2014中6.3.6的规定; 当管箱与管板不要求分离时,分程隔板与管板可采用焊接连接
4.2.2.5检修人孔 管箱的检修人孔可采用法兰密封人孔
4.2.2.6给水管及其他开口设置 4.2.2.6.1管箱应设置给水进口管、给水出口管、放气管放水管和检修孔,其要求见表3
表3管箱上管口的设置 接管 安装位置 管径要求 给水进口管 换热管流程人口 满足流速要求 给水出口管 换热管流程出口 满足流速要求 管箱顶部或顶部给水管上 >DN20 放气管 管箱底部或底部给水管上 放水管 >DN20 D400 检修孔 封头(设备已具备检修条件时,可不设 注:DN 公称尺寸,用于管道系统元件的字母和数字组合的尺寸标识,后跟无量纲的整数数字 4.2.2.6.2管侧安全阀接口可设置于管箱上或设置于系统管道上,其管径应大于或等于DN20
4.2.2.6.3接管与管箱的连接及其他要求按GB/T151一2014中6.13的规定
4.2.2.7换热管 换热管除应符合GB/T151一2014中6.4的I级管束的规定外同时符合下列要求 -换热管宜采用奥氏体不锈钢管;
GB/T38657一2020 -满足有效换热面积之外的管子数量不低于管子总数量的5% 换热管按最小或平均壁厚标注在图样及设备技术规格书中
4.2.2.8管板 4.2.2.8.1管孔 管孔按GB/T151一2014中6.5.1的I级管束管板管孔的规定
4.2.2.8.2拉杆孔 焊接连接的拉杆孔示意见图3a),拉杆孔深度L,宜大于拉杆直径的d
拉杆孔直径按式(2 确定
d=l,十1.0 式中 拉杆孔直径,单位为毫米mm); dl 拉杆直径,单位为毫米(mm)
螺纹连接的拉杆螺纹孔示意见图3b),螺纹深度L
应大于拉杆螺纹长度L.
12×45” 2X45” 焊接连接的拉杆孔示意 螺纹连接的拉杆孔示意 b 说明 -拉杆孔直径,单位为毫米(mm); d1 ! 拉杆孔深度,单位为毫米(mm); L? -拉杆孔螺纹深度,单位为毫米mm); 拉杆螺纹长度,单位为毫米(mm). 图3拉杆孔示意图 4.2.2.8.3法兰连接的管板密封面 4.2.2.8.3.1固定管板与标准容器法兰配合时,管板密封面结构尺寸应按NB/T47021,NB/T47022或 NB/T47023的规定确定
4.2.2.8.3.2分程隔板槽的尺寸按下列要求确定 槽深应大于垫片厚度,且不宜小于4mm,隔板槽密封面应与环形密封面平齐 槽宽a宜为8mm~14mm; 多管程的隔板槽倒角不应妨碍垫片的安装;隔板槽拐角处的倒角宜为45"(见图4),倒角尺寸b 宜大于分程垫片的圆角半径R 10
GB/38657一2020 说明 分程隔板槽宽,单位为毫米(mm); 分程隔板槽倒角尺寸,单位为毫米(mm): R 分程垫片的圆角半径,单位为毫米(mm)
图4管板的分程隔板槽示意图 4.2.2.8.4管板堆焊层 管板与换热管的连接面宜堆煤,堆焊层厚度大于或等于3mm,材质与换热管同类 4.2.2.9换热管与管板的连接 4.2.2.9.1换热管与管板的最小泄漏通道为每个角焊缝的最小泄漏通径(即角焊缝厚度),单个值应大 于或等于换热管名义厚度()的三分之二
4.2.2.9.2胀接及焊接结构尺寸按GB/T1512014中6.6的规定或采用其他可靠的连接结构尺寸 4.2.2.10管板与管箱,壳体的焊接连接 管板与管箱、壳体的焊接连接可根据设计条件、设备结构等因素选用GB/T1512014中附录I所 示结构,也可采用其他可靠的连接结构
4.2.3壳程 4.2.3.1管系的布置" 应由凝结段、疏水冷却段两段组成,适宜时可由其中一段单独组成,还可附加单独的疏水箱 4.2.3.2导流和防冲设置 导流和防冲设置应符合下列要求 导流和防冲按GB/T151一2014中6.8.1的规定 燕汽进口接管和疏水进口接管下方应设置防冲结构,管束上的防冲板半径应大于或等于接管 中心到介质出口处发散角45处的尺寸 -切向进汽用防冲板宜采用弧形分段结构,并防止湿燕汽直接冲击液面
1
GB/T38657一2020 4.2.3.3折流板和支持板 折流板和支持板按GB/T151一2014中6.8.2的I级管束规定
4.2.3.4防短路结构 防短路结构按GB/T151一2014中6.8.3的规定
4.2.3.5拉杆、定距管 拉杆,定距管按GB/T151一2014中6.8.5的规定
4.2.3.6滑道 滑道按GB/T151一2014中6.8.6的规定,也可采用其他可靠的结构
4.2.3.7壳体 壳体尺寸除满足强度和结构要求外,还应满足各类蒸汽和疏水进人的扩容要求,满水时间宜在 60s~ -120s
4.2.3.8接管及其他开口 4.2.3.8.1壳体至少应设置蒸汽进口管、疏水出口管、启动放气管、运行排气管、放水管、安全阀接口;紧 急疏水管,疏水人口管根据需要设置,要求见表4
表4壳体上管口的设置 接管 安装位置 管径要求 壳体顶部 满足流速要求 蒸汽进口管 壳体底部,当具有疏水冷却段时,也可位 子 疏水出口管 满足流速要求 壳体侧面 壳体顶部,当管道布置有特殊要求时,其段 启动放气管 >DN20 内顶部位置也需设置(侧向疏水出口除外 按内部结构设计 排放能力为进人蒸汽量的0,5% 运行排气管 放水管 壳体底部 >DN20 安全阀接管 壳体顶部 满足泄放量要求 紧急疏水管 壳体底部 满足疏水出口管的流速要求 疏水人口管 壳体凝结段具有扩容空间的位置 满足流速要求 液位测量接口 壳体侧面或顶部 满足仪控要求 压力,温度测点 壳体/介质出、人管口侧面或顶部 满足仅控要求 4.2.3.8.2接管与壳体的连接及其他要求按GB/T151一2014中6.13的规定 4.2.4设备及接管法兰 4.2.4.1 设备法兰设计应符合GB/T150.3一2011的规定
4.2.4.2设备法兰应优先选用NB/T47021,NB/T47022、NB/T47023,GB/T29465的法兰
12
GB/38657一2020 4.2.4.3接管法兰应优先选用HG/T20592,HG;/T20615的法兰
4.2.4.4非标设计时,应优先选用相关标准的法兰连接尺寸
4.2.5密封及垫片 4.2.5.1密封结构及垫片应根据工作条件(介质、温度、压力)按相关标准进行设计或选用
4.2.5.2管法兰垫片、管箱垫片、管箱侧垫片按相关标准选用
4.2.5.3金属平垫片、金属波齿复合垫片、椭圆垫、八角垫,透镜垫等按相关标准进行设计、选用
4.2.5.4有成熟使用经验时,也可采用其他密封结构
4.2.6支座 4.2.6.1卧式低加支座 卧式低加鞍式支座布置见图5,布置原则如下 公称长度小于或等于3m时,鞍座间距L,宜取公称长度的40%一60%; 公称长度大于3m时,鞍座间距L;宜取公称长度50%70% 宜使L
和L
相近 必要时,应对支座和壳体进行强度和稳定性校核; 确定鞍座与相邻接管的距离时应考虑鞍座基础及保温的影响 a 管箱,壳程法兰夹持管板 管板兼做壳程法兰 b 图5鞍式支座布置示意图 13
GB/T38657一2020 管板与管箱、,壳程焊接 说明: -固定鞍座 -活动鞍座
图5(续) 鞍式支座可按NB/T47065.1选用
4.2.6.2立式低加支座 4.2.6.2.1立式低加支座包括耳公式支座和裙式支座,见图6. 4.2.6.2.2耳式支座可按NB/T47065.3选用,布置原则如下 壳程壳体公称直径小于或等于DN800时,至少应设置2个支座,且应对称布置 壳程壳体公称直径大于DN800时,至少应设置4个支座,且应均匀布置
经考虑各种载荷及其组合载荷影响,并经强度校核确认,支座数量可少于上述要求
4.2.6.2.3裙式支座可按NB/T47041进行设计
耳式支座示意 裙式支座示意 说明 -耳式支座; 裙式支座 图6立式支座布置示意图 14
GB/38657一2020 4.2.7设备附件 4.2.7.1管箱平盖应设置吊耳等起吊附件
4.2.7.2可抽管束的固定管板上宜设置吊环螺钉,正常操作时,采用丝堵和垫片保护螺钉孔,维修时换 装吊环螺钉抽装管束
4.2.7.3设备法兰夹持的管板外缘上宜设置防松支耳,防松支耳与带肩双头螺柱配套使用(如图7所 示),防松支耳应对称均布,推荐数量如下 -公称直径小于或等于DN800时,至少设置2个 -公称直径为DN900DN2000时,至少设置4个; 公称直径大于DN2000时,可适当增加数量
说明 带肩双头螺柱; -防松支耳
图7防松支耳与带肩螺柱示意图 4.2.8保温 表面温度超过50C的设备应进行保温
环境温度不高于25C时,设备保温结构外表面温度不应 超过50C;环境温度高于25C时,保温结构外表面温度可比环境温度高25C 4.2.9疏水箱 4.2.9.1可设置单独的疏水箱
4.2.9.2疏水箱的设计压力和设计温度不应低于与其相连的几台低加中壳程的最高设计压力和最高设 计温度,同时还应考虑真空状态下的外压校核
4.2.9.3疏水箱的有效容积应能满足性能设计工况下系统长期稳定的疏水要求,并能适应非正常工况 下短时疏水要求
4.2.9.4疏水箱应设置汽平衡管道与相应低加连通 4.2.9.5疏水箱应能承受各种工况下疏水的热冲击,应采用扩散器,内衬等措施防止进人流体对设备的 冲蚀
4.2.9.6疏水箱壳体的管口,应按表5要求进行设置 15
GB/T38657一2020 表5疏水箱壳体上管口的设置 管径要求 安装位置 接管 疏水人口管 壳体具有扩容空间的位置 满足流速要求 疏水出口管 壳体底部 满足流速要求 壳体底部 紧急疏水管 满足疏水出口管的流速要求 汽平衡口 按内部结构设计 满足最恶劣工况闪蒸量流速要求 启动放气管 壳体顶部 >DN20 D20 放水管 壳体底部 液位测量接口 壳体侧面或顶部 满足仪控要求 壳体/介质出,人管口侧面或顶部 满足仪控要求 压力、温度测点 安全阀接管" 壳体顶部 满足泄放量要求 检修孔 满足检修要求 当与疏水箱相连接的低加满足GB/T150.l一2011附录B的B.3.3要求时,可取消
设计计算 4.3.1承压壳体与隔板 承压壳体与隔板的计算应符合GB/T151一2014中7.1的规定 4.3.2开孔补强 开孔补强应符合GB/T150.3一2011第6章的规定
4.3.3换热管 换热管的计算应符合GB/T151 -2014中7.3的规定
4.3.4管板 管板的计算应符合GB/T151一2014中7.4或其他相关标准的规定
4.3.5振动 振动计算参见GB/T1512014附录C 4.3.6人孔密封 人孔密封计算参见GB/T150.3一2011附录C 4.3.7圆筒形壳程和管程的接管荷载 文件要求 4.3.7.1 接管允许载荷应在设计文件中列出
4.3.7.2管道实际应力超过接管允许值的处理 管道实际应力或载荷超过接管允许载荷值时,应采取补强措施
16
GB/38657一2020 43.7.3接管的力和力矩计算 4.3.7.3.1外加载荷作用在球形壳体或圆筒形壳体上所引起的局部力和力矩示意如图8所示
F"RRF McM MeM b 正视图或平面图 横截面图 说明: -壳体; 2 接管; -最大径向合力 FRRe MRcs 最大周向合力矩; -最大纵向合力矩 Mwx -接管口端部外半径; ro R
-壳体平均半径
图8局部力和力矩示意图 4.3.7.3.2无因次数8丫按式(3)和式(4)计算,根据和7从图9、图10和图11中查到a、习和A
=0.875 货 3 3 ,-" 式中: 无因次数 接管口端部外半径,单位为米(m); r 壳体平均半径,单位为米(n m; R T 壳体厚度,单位为米(m); 无因次数 17
GB/T38657?2020 10 000 0o0 80000 70000 60000 50000 40000 30000 20000 000 " 000 00 6000 5000 4000 3000 2000 =300 700 600 500 400 =100 300 50 200 '" 80 70 G0 50 40 30 20 10 0.05 O.I0 0.I5 0.20 0.25 0.30 0.35 0.40 0.45 0.50 0.55 0.60 ?9a? 18
GB/T38657?2020 0do0 000 60000 50000 40000 30000 =300 20000 000 00oy 60o 500o 4000 100 3000 2000 000 01 00 0o 400 300 200 " 8Oy 0 40 30 20 0. 0.05 0.10 0.15 0.20 0.25 0.30 0.35 0.40 0.50 0.55 0.60 0,45 ?10? 19
GB/T38657?2020 0000 60000 50000 40000 30000 20000 8 8000 700 6 000 5 000 4000 3 000 =300 2000 Y - 6o0 s00 400 300 200 40 30 20 " 0.05 0.10 0.15 0.20 0.25 0.30 0.35 0.40 0.45 0.50 0.55 0.60 ?11A? 20
GB/38657一2020 4.3.7.3.3设计压力产生的应力应取a与[][壳体材料在设计温度下的许用应力,单位为兆帕(MPa] 中的较小者,按式(5)计算
,-一(R
- 5 " 式中: 由设计压力产生的应力,单位为兆帕(MPa); P -设计压力,单位为兆帕(MPa); R 壳体平均半径,单位为米(m): 壳体厚度,单位为米(m)
4.3.7.3.4 接管的最大径向合力按式(6)计算
R (S、 Fe 式中: F 最大径向合力,单位为牛顿(N); RRr 壳体平均半径,单位为米(m); Rm S -设计温度下壳体材料的屈服强度,单位为兆帕(MPa); 由设计压力产生的应力,单位为兆帕(MPa); 无因次数
a 4.3.7.3.5 接管的最大周向合力矩按式(7)计算 R品rS Meu= 式中 M 最大周向合力矩,单位为牛顿米(N m; RcM R -壳体平均半径,单位为米(m); 接管口端部外半径,单位为米(m); r
s, -设计温度下壳体材料的屈服强度,单位为兆帕(MPa) 无因次数
4.3.7.3.6接管的最大纵向合力矩按式(8)计算
R. M (S, a 式中 M8 -最大纵向合力矩,单位为牛顿米(N m; RLM R -壳体平均半径,单位为米(m) 接管口端部外半径,单位为米(m); r
-设计温度下壳体材料的屈服强度,单位为兆帕(MPa); -由设计压力产生的应力,单位为兆帕(MPa); 无因次数
4.3.7.3.7接管允许载荷应在图12所示以坐标原点、F郎和M为界限的三角形面积内
Fe,Me按 式(9)和式(10)取值
21
GB/T38657一2020 F M 图12接管允许载荷范围 FRF=|FRRe 式中 Fe -最大合力,单位为牛顿(N). 最大径向合力,单位为牛顿(N)
FRRF (10 M=min(Mew|,M.M| 式中 M 最大合力矩,单位为牛顿米(N m; M 最大周向合力矩,单位为牛顿米(N
m); cM M贼.x -最大纵向合力矩,单位为牛顿米(N m 4.3.7.3.8外加载荷位于图12所示三角形区域外时,应复核外加载荷包括r、y,、各方向的力及其合 成力和合成力矩)是否均位于安全系数取1的三角形区域内
4.4安全装置 4.4.1壳程和管程的超压泄放装置 44.1.1管程给水进、出口之间至少应设置一只DN20的安全阀,共用旁路设置的多级低加管程可共 用一只管程安全阀,也可单独设置
4412壳程应至少设置一只安全阀,其泄放量拨下述流量的较大者,并留10%余量 凝结水流量的10% 当一根换热管完全断裂产生两个断口时的给水流量G,按式(11)计算
G=64×10-"d、PP/y 11 式中 给水流量,单位为千克每秒(kg/s); G 换热管内径,单位为毫米(mm) d -管侧设计压力,单位为兆帕(MPa); P P 壳程设计压力,单位为兆帕(MPa) 换热管内水比容,单位为立方米每千克(m'/kg). 4.4.2液位测量装置 4.4.2.1应设置液位测量装置,一般按以下五挡水位设置 正常水位 -正常运行时的水位 a 22
GB/38657一2020 b 低一水位 疏水阀完全关闭的水位; 高一水位 -报警及危急疏水阀开始打开的水位 c d)高二水位 危急疏水阀完全打开的水位; 高三水位 解列的水位
e 4.4.2.2低加水位控制仪表装置可采用集箱母管结构或独立接管结构,如采用集箱母管结构,设备引出 管规格应大于或等于DN50
4.4.3压力测量装置 管程和壳程应至少各设置一个压力测量装置,宜设置于给水出口管和蒸汽进口管上
疏水箱壳程的介质出、人口宜各设置一个压力测量装置 4.4.4温度测量装置 管程和壳程应至少各设置一个温度测量装置,宜设置于给水出口管和蒸汽进口管上
疏水箱壳程的介质出、人口宜各设置一个温度测量装置
4.5性能 4.5.1温度 性能设计工况下,低加总温升不应低于设计值4C
4.5.2端差 上端差应大于或等于2; 4.5.2.1 45.2.2下端差要求如下 卧式或倒立式低加的下端差应大于或等于5.6C; 正立式低加的下端差应大于或等于8C 下端差小于5.6C时,应采用外置式疏水冷却器
4.5.3流速 4.5.3.1换热管内流速 性能设计工况及平均温度(给水进口和给水出口温度的算术平均值)下,通过不锈钢换热管内的给 水流速不应超过3m/s
4.5.3.2接管介质流速 性能设计工况下,按内径选择接管,管内介质流速不应超过表6的规定
表6接管介质流速 接管 流速极限 给水进、出口 6.0m/s 过冷疏水 1.2m/s 1.2m/s 疏水出口 水位受控 饱和疏水 水位不受控 0.6m/s 23
GB/T38657一2020 表6(续 接管 流速极限 两相流体的质量流速 nminl77. 疏水进口 16vp,l220}kg/m'
s) 含高湿度 扩容后的蒸汽质量流速及蒸汽流速 45.7m/s .RM kg/m,s) 蒸汽进口) 扩容后的液体流速 1.2m/s 燕汽进口 48.7/p”m/s 混合物密度,单位为千克每立方米(kg/m'). 注:p 蒸汽进口绝对压力,单位为兆帕(MPa)
4.5.4压降 4.5.4.1管程压降 性能设计工况下,每台低加管程压降不应超过0.15MPa
4.5.4.2壳程压降 性能设计工况下,低加壳侧压降应符合下列规定 总压降不超过加热器级间压差的30% a b)每一段的压降不超过35kPa; 当疏水管线损失或静压力占级间压差比例较大的情况下,用户可以提出比a)和b)低的压 c 降值
4.5.5噪声 离设备外表面1m处,噪声应小于85dB(A). 4.5.6事故工况 双列布置的情况下,因事故造成一列解列时,另一列管侧应具备短时承受本列原流量的150%倍的 能力
5 材料 5.1选用及代用规定 5.1.1受压部件材料应符合GB/T150.2一2011及相关标准的规定,受压部件不应使用铸件
5.1.2制造单位对主要受压元件的材料代用,应事先获得原设计单位的书面批准,并应在竣工图上做 详细记录
受压元件用钢应附有钢材生产单位的钢材质量证明书原件或者加盖了材料经营单位公章和经 5.1.3 办负责人签字(章)的复印件,容器制造单位应按质量证明书对钢材进行验收
容器制造单位应对下列 材料进行人厂复验,复验结果应符合相应材料标准的规定和设计文件的要求 -类压力容器的级锻件; 用于主要受压死件的境外牌号材料 设计文件要求进行复验的材料 5.1.4焊接材料应符合NB/T47018及设计文件的规定
容器制造单位应对焊接材料进行人厂复验 复验结果应符合制造单位规定
24
GB/38657一2020 5.2标志及移植 受压元件的材料应有可追溯标志
制造过程中,如原标志被裁掉或材料分成几块时,应在材料分割 前完成标志移植
5.3其他要求 5.3.1换热管束应满足GB/T24593或YB/T4223或其他相关标准的要求
5.3.2主要受压元件采用未列人TSG21一2016规定的协调标准的材料,应按照相关标准的规定通过 技术评审,方可使用
5.3.3主要受压元件采用已列人TsG212016规定的协调标准的材料,抗拉强度下限值大于或等于 540MPa的材料及用于压力容器设计温度低于一40的低合金钢,如果材料制造单位没有该钢材的制 造或者压力容器应用业绩,应按相关标准的规定通过技术评审,方可使用
5.3.4主要受压元件用碳钢、碳锰钢,非含Cr低合金钢,Cr含量应控制在0.15%一0,.30%之间
5.4锻件要求 锻件应符合NB/T47008或NB/T47010的规定,锻件的级别应符合GB/T150.2一2011中6.13 的规定 制造 6.1冷、热加工成形与组装 6.1.1封头和筒体 6.1.1.1封头允许有一条拼接焊缝,拼接焊缝内、外表面在成形前应打磨至与母材平齐
6.1.1.2封头成形后,拼接焊缝应按NB/T47013.2一2015进行100%射线检测,合格级别级
6.1.1.3封头成形、热处理、无损检测应符合设计图样和GB/T25198的要求
6.1.1.4简体卷制时,外圆周长的允许上极限偏差为10mm;下极限偏差为零
6.1.1.5筒体的同一截面上最大直径与最小直径之差e<0.5%DN,且应符合下列规定: 公称尺寸小于或等于DN1200时,其值不得大于5mm 公称尺寸为DN1200~DN2000时,其值不得大于7mm; 公称尺寸大于DN2000时,其值不得大于12mm
6.1.1.6筒体直线度检查,应通过中心线的水平和垂直面,即沿圆周0°,90*,180",270°四个部位测量
直线度允许偏差为筒体总长度L的0.1%,且应符合下列规定 -L小于或等于6o00mm时,其值应小于或等于4.5mm; -L大于6000mm时,其值应小于或等于8mm
6.1.2换热管 6.1.2.1换热管的外观和尺寸极限偏差应符合GB/T151一2014中I级管束和设计文件的要求
6.1.2.2换热管不应环向拼接
管材应无缺陷;有缺陷的管材不应修复后使用
注,缺陷包括分层,撕裂,瑕疵、开裂,裂缝,凹痕有害的划痕,环纹、裂纹,折叠和刻痕等 6.1.2.3换热管不宜热弯,冷弯后应按GB/T151一2014进行热处理
6.1.2.4换热管弯制后,当(R/d)>1.5及工艺稳定时,对每种通球直径抽取其最小弯曲半径管子数的 5%,且不少于2根进行通球检查,以钢球通过为合格
钢球直径按表7选取
25
GB/T38657一2020 表7钢球直径 弯管半径R R<2,5l 2.5d
GB/38657一2020 终钻后应抽查大于或等于60"管板中心角区域内的孔桥宽度,B值的合格率应大于或等于 96%,Bm的数量应控制在4%之内,未达到要求时应进行100%检查 6.13.3管板管孔表面粗糙度Ra6.3,管板孔表面应清理干净,不应有影响胀接或焊接连接质量的毛 刺、铁屑、锈斑,油污等,且不应有贯通的纵向或螺旋状刻痕
折流板和支持板的管孔直径极限偏差应符合表10的规定,最大超差0.1mm的管孔数不得超 6.1.3.4 过管孔总数的4%
抽查一块折流板或支持板大于或等于60"管板中心角区域内的管孔,未达到要求时 应进行100%检查
6.1.3.5折流板和支持板机械加工表面粗糙度Ra12.5;外圆两侧面的尖角应倒钝;应去除折流板和支 持板上的毛刺
6.1.3.6折流板、支持板与管板上的管孔应与管束同心,且管孔两侧应倒角处理
表g管束孔桥宽度 单位为毫米 换热管外径 孔中心距 管孔直径 名义孔桥宽度 允许孔桥宽度" 最小孔桥宽度 B da S-d B 15,88 20,64 16.08 4.56 3,22 2.,74 15,88 22 16.08 5,.92 4.58 3.55 15,88 22.23 16.08 6,15 4.81 3.69 16 21 16.25 4.75 3,18 2.85 16 22 16.25 5.75 4.17 3.45 19 19.25 24 4.75 3.31 2.85 19 25 19.25 5.75 4.30 3.45 25 32 25.25 6,75 5,47 4.05 为管板厚度>160mm 时允许的孔桥宽度
表10管孔直径及极限偏差 单位为毫米 折流板和支持板 换热管外径 孔径 极限偏差 0.20 15.88 16.28 16 16.40 十0.30 19 19.40 25 25.40 6.1.4对接 6.1.4.1封头、简体及管板对接时,厚板的削薄量应符合GB/150.4的规定
6.1.4.2封头、筒体及管板对接时,其纵环缝对口错边量应符合GB/T150.4的规定 6.1.5管束的组装 6.1.5.1管系立架后,穿管前应确认所有隔板与管板之间对应管孔的同轴度
6.1.5.2拉杆上的螺母应拧紧,以免在装人或抽出管束时,因折流板窜动而损伤换热管 6.1.5.3穿管时不应强行敲打,换热管表面不应出现凹瘪或划伤
6.1.5.4除换热管与管板间以焊接连接外,其他任何零件均不得与换热管相焊
27
核电厂常规岛低压加热器技术条件GB/T38657-2020
随着能源需求的不断增长,核电厂作为一种清洁、高效的能源供应方式得到了广泛的应用。在核电站的发电过程中,低压加热器是非常重要的设备之一,它负责将水从锅炉中加热后送入蒸汽发生器以产生蒸汽,进而驱动涡轮机发电。因此,低压加热器的性能、安全性和可靠性对于核电站的运行至关重要。
常规岛低压加热器技术条件GB/T38657-2020
为了提高核电站低压加热器的标准化水平,国家标准化管理委员会发布了《核电厂常规岛低压加热器技术条件GB/T38657-2020》标准。该标准规定了核电站低压加热器的技术要求、试验方法、检验规则和标志、包装、运输等方面的内容。
根据该标准,核电站低压加热器主要由加热管束、支撑件、壳体、法兰、密封件、进出口连接件等部分组成。其中,加热管束是低压加热器的关键部件之一,其性能对低压加热器的整体性能有着重要的影响。
除此之外,标准还规定了低压加热器的使用环境条件,包括温度、湿度、气压等参数。此外,标准还规定了低压加热器在交付前需要进行的试验项目和试验方法,以确保低压加热器的性能符合标准要求。
结语
总之,低压加热器作为核电站发电过程中的重要设备,其安全性、可靠性和性能表现对于核电站的运行至关重要。《核电厂常规岛低压加热器技术条件GB/T38657-2020》标准的发布,将有助于提高核电站低压加热器的标准化水平,进而提高其性能和可靠性。