GB/T34651-2017
全断面隧道掘进机土压平衡盾构机
Fullfacetunnelboringmachine—Earthpressurebalanceshieldmachine
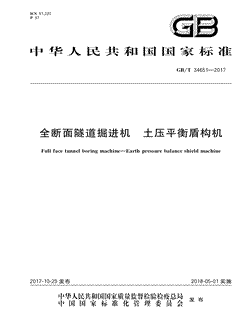
- 中国标准分类号(CCS)P97
- 国际标准分类号(ICS)91.220
- 实施日期2018-05-01
- 文件格式PDF
- 文本页数27页
- 文件大小1.67M
以图片形式预览全断面隧道掘进机土压平衡盾构机
全断面隧道掘进机土压平衡盾构机
国家标准 GB/T34651一2017 全断面隧道掘进机土压平衡盾构机 Fulfaeetumnelboringmachine一Earthpressurebalaneeshieldmachine 2017-10-25发布 2018-05-01实施 国家质量监督检验检疫总局 发布 国家标准化管理委员会国家标准
GB/34651一2017 前 言 本标准按照GB/T1.1一2009给出的规则起草
本标准由机械工业联合会提出 本标准由全国建筑施工机械与设备标准化技术委员会(SAC/TC328)归口
本标准起草单位:中铁工程装备集团有限公司、中铁隧道集团有限公司、中铁一局集团城市轨道交 通工程有限公司、石家庄铁道大学、中交天和机械设备制造有限公司、上海隧道工程有限公司机械制造 分公司、北京建筑机械化研究院、铁建重工集团有限公司、北方重工集团有限公司、水利水电第 三工程局有限公司 本标准主要起草人:李建斌、李光、康宝生、王江卡、郭京波、高光辉,黄健、李静、程永亮、王建刚、 王鹏禹,赵振威,贾连辉,张宏达、党西锋、杨绍普、肖军、沈建华,刘双,麻成标、,陶磊,黄继敏
GB/34651一2017 全断面隧道掘进机土压平衡盾构机 范围 本标准规定了土压平衡盾构机的术语和定义,基本参数与型号、技术要求、试验方法、检验规则、随 行文件、标志、包装和运输
本标准适用于圆形断面土压平衡盾构机
规范性引用文件 下列文件对于本文件的应用是必不可少的
凡是注日期的引用文件,仅注日期的版本适用于本文 件
凡是不注日期的引用文件,其最新版本(包括所有的修改单)适用于本文件
GB/T150(所有部分压力容器 GB/T191包装储运图示标志 GB/T3766液压传动系统及其元件的通用规则和安全要求 GB5226.1机械电气安全机械电气设备第1部分;通用技术条件 GB5226.3机械安全机械电气设备第11部分电压高于1000Va.c.或1500vd.c但不超过 36kV的高压设备的技术条件 GB/T6388运输包装收发货标志 GB/T7932气动系统通用技术条件 GB/T10595带式输送机 GB/T13306标牌 GB/T13384机电产品包装通用技术条件 T GB 14039液压传动油液固体颗粒污染等级代号 17301土方机械操作和维修空间棱角倒钝 GB GB/T20082液压传动液体污染采用光学显微镜测定颗粒污染度的方法 GB/T34650全断面隧道掘进机盾构机安全要求 GB/T34354全断面隧道掘进机术语和商业规格 GB50150电气装置安装工程电气设备交接试验标准 GB50168一2006电气装置安装工程电缆线路施工及验收规范 重型机械通用技术条件第3部分;媒接件 JB/T5000.3 JB/T5000.10重型机械通用技术条件第10部分;装配 B/T5000.11重型机械通用技术条件第11部分;配管 JB/T10205液压缸 术语和定义 GB/T34354界定的以及下列术语和定义适用于本文件
为了便于使用,以下重复列出了 GB/T34354中的某些术语和定义
GB/T34651一2017 3.1 土压平衡盾构机 earthpressurebalaneeshieldmachine;EPB 以渣土为主要介质平衡隧道开挖面地层压力、通过螺旋输送机出渣的盾构机
[GB/T34354一2017,定义2.8 3.2 标称直径nominaldiameter 前盾外径
3.3 开挖直径exeavationdiameter 刀盘旋转一周,最外端新刀(不包括超挖刀)刀刃形成的轨迹直径
3.4 装机功率installedpower 整机用电设备额定功率的总和
3.5 maximummworkinm 最大工作扭矩 ingtorque 刀盘在工作转速范围内,主驱动单元能够输出的可持续工作的最大扭矩 3.6 脱困扭矩breakingouttorqe 刀盘在最大工作扭矩工况下无法转动时,主驱动单元所能够短时输出的最大扭矩 3.7 扭矩系数torqecoefficient 刀盘最大工作扭矩(kN
nm)与刀盘开挖直径(m)三次方的比值
3.8 前闸门guilotinegate 在土仓和螺旋输送机之间隔断渣土的装置,具有开关功能 3.9 后闸门ditsehareate 螺旋输送机出渣闸门
3.10 reamercutter;overeutter 超挖刀 伸出刀盘外周对开挖直径外土体进行超挖的刀具
3.11 仿形刀copyeutter 按设定超挖轨迹进行切削的超挖刀
3.12 浆液注入率groutinjeetionrate 浆液注人的体积占开挖直径与管片外径之间空隙体积的百分比 基本参数与型号 4.1基本参数 土压平衡盾构机基本参数如下 -标称直径,单位为毫米(mm);
GB/34651一2017 开挖直径,单位为毫米(mm) -刀盘最大转速,单位为转每分(r/min); 刀盘驱动功率,单位为千瓦(kw); -设计最大推进速度,单位为毫米每分(mm/ /min; 最大推力,单位为千牛(kN); 适应管片尺寸(外径/内径-宽度),单位为毫米( mm; 总长度,单位为米(m); 总质量,单位为千克(kg); 主机长度,单位为米(m) 主机质量,单位为千克(kg); 最小水平转弯半径,单位为米(m); 允许最大坡度,%; 最大不可分割什重量,单位为千克(ke). 最大不可分割件尺寸(长×宽×高),单位为毫米(mm); 最大工作压力,单位为兆帕(MPa) 装机功率,单位为千瓦(hw. 4.2产品型号 产品型号由产品代号和主参数组成,主参数为标称直径,其表示方法如下 -主参数;用阿拉伯数字表示,单位为毫米(mm) 产品代号;由制造商自行规定,用大写英文字母表示 4.3结构示意图 土压平衡盾构机示意图如图1所示
GB/T34651一2017 5 t 空 式 吧 5 " 艳 三 S 二 堂 豆 菜 恭 集 士 温 号 知 二
GB/34651一2017 技术要求 5.1 般要求 5.1.1焊接件应符合JB/T5000.3的规定
5.1.2装配应符合JB/T5000.10的规定
5.1.3管路装配应符合JB/T5000.11的规定
5.1.4开挖直径偏差范围应为0mm一 十4mm
5.1.5部件不能满足运输要求时应进行分块设计
5.1.6设备应能在工作环境温度5C50C、相对湿度小于90%的条件下正常使用
5.1.7设备设计应为智能化制造、绿色环保、再制造提供条件
5.2刀盘与刀具 5.2.1除刀盘最外端新刀外,其他刀具的安装半径偏差范围应为一2mm+2mm
5.2.2正面刀的刀刃高度偏差不应大于2mm. 5.2.3刀盘的强度和刚度应满足设计要求 5.2.4刀盘最外侧刀具相对前盾的高差应满足设计要求
5.2.5滚刀挡圈侧宜朝向刀盘中心位置
5.2.6刀盘宜设有旋转角度指示装置
5.2.7刀盘宜配置超挖刀或仿形刀,超挖量应符合设计要求
5.2.8刀盘应设置搅拌装置和用于渣土改良的注人孔
5.2.9宜设置磨损检测装置
5.2.10刀盘内部管路耐压性能应符合JB/T5000.11的规定
5.3盾体 5.3.1盾体外径偏差和圆柱度应符合设计要求
5.3.2盾体的强度和刚度应满足设计要求
5.3.3水土压力在不大于0.4MPa时盾尾刷不应少于3道,大于0.4MPa时盾尾刷不宜少于4道
5.3.4盾尾同一个油脂腔两个相邻的油脂孔的弧线长度不宜大于3.5 m
5.3.5盾体和土仓隔板宜设置超前注浆孔
5.3.6盾体应设有径向注人孔
5.3.7当开挖直径大于4500mm时,宜配置前闸门
5.3.8土仓隔板应预留风、水、电通道和渣土改良注人孔
5.3.9土压传感器宜满足带压更换需要
5.4主驱动单元 5.4.1主轴承设计寿命不应小于10000h
5.4.2扭矩系数不宜小于18,刀盘装备扭矩计算方法参见附录A
5.4.3脱困扭矩不应小于最大工作扭矩的1.2倍
5.4.4应具有扭矩限制功能
5.4.5应能够双向旋转,具有无级调速功能,最大转速应满足设计要求
5.4.6应具有慢速点动功能,点动转速不应大于0.2r/min. 5.4.7齿轮油润滑系统应设置磁性过滤器及冷却装置
GB/T34651一2017 5.4.8油脂密封润滑系统应具备压力和流量检测报警功能 5.4.9主驱动系统与推进系统应具有联锁控制功能
5.5人舱 5.5.1应由具备专业资质的制造商设计制造,并满足GB/T150的要求
5.5.2应进行气密性试验,保压30min,压力下降值不应大于最大工作压力的6%
5.5.3舱内和舱外应设置独立的加、减压控制系统
5.5.4应设置安全阀,安全阀设定压力为最大工作压力的1.1倍
5.5.5舱内和舱外应设置机械式应急排气阀,配置永久性红色警示标记
5.5.6 人舱宜位于盾体中/上部,与土仓连接的舱门应朝人舱方向开启
5.5.7舱外及各舱室应配备不少于两套通信系统,其中一套在供电系统断电时仍能正常通信
5.5.8 人舱或与人舱相连通的盾体封闭舱室内应设置刀盘动作现地控制装置,与主控室控制具有互锁 功能 5.5.9舱内应设置水、气接口,不应设置电气插拔装置
5.6推进系统 5.6.1 单位开挖面积(m=)的最大推力不应小于1000kN
5.6.2最大推力应满足设计要求,装备推力计算方法参见附录B. 推进液压缸中心轴线宜与管片厚度中心重合
5.6.3 5.6.4最大推进速度应满足设计要求
推进模式下的推进液压缸伸出速度应连续可调
5.6.5 5.6.6管片拼装模式下的推进液压缸伸缩速度应满足设计要求
5.6.7推进系统应具有防后退功能 5.6.8推进液压缸行程应满足管片拼装的需要,行程偏差不应大于士2mm
5.7管片拼装机 5.7.1应具有管片的抓持、提升、平移、回转及定位功能,回转速度应满足设计要求
5.7.2采用机械锁固的抓取装置安全系数不应小于1.5,非机械锁固的抓取装置安全系数不应小于 2.5
5.7.3应进行载荷试验,静载试验载荷为设计最重管片重量的1.25倍,动载试验载荷为设计最重管片 重量的1.1倍
5.7.4在断电情况下,真空吸盘式管片拼装机应保证吸持管片的时间不小于20min,且真空度不低 80%
于 5.7.5沿周向顺时针、逆时针旋转角度不应小于200°" 5.7.6纵向行程宜满足在隧道内更换两道盾尾刷的需要
5.7.7宜具备有线,无线两种控制方式,无线遥控有效控制范围应覆盖工作区域
5.7.8应配置制动装置
5.8螺旋输送机 5.8.1设计最大出渣量应满足最大推进速度时的出渣需要
5.8.2应具有双向旋转和无级调速功能,最大转速应满足设计要求 5.8.3伸缩与前闸门开关动作应具有联锁控制功能
5.8.4伸缩量应满足前闸门关闭要求
GB/34651一2017 5.8.5后闸门应具有开度调节及断电自动关闭功能,断电自动关闭时间不应大于20s
5.8.6应设置渣土改良注人孔和检修窗口
5.9带式输送机 5.9.1应符合GB/T10595的规定 5.9.2输送能力不应小于螺旋输送机出渣能力
5.9.3宜采用变频驱动或液压驱动
5.9.4斜坡段倾角不宜大于12"
5.9.5应配置刮渣及清洗装置
5.10辅助系统 5.10.1铵接系统应满足隧道施工最小转弯半径要求
5.10.2主动钞接最大推力不应小于推进系统最大推力的70%
采用机械锁固的管片吊机抓取装置安全系数不应小于1.5,非机械锁固的管片吊机抓取装置安 5.10.3 全系数不应小于2.5
5.10.4应对管片吊机进行载荷试验,静载试验载荷为设计最重管片重量的1.25倍,动载试验载荷为设 计最重管片重量的1.1倍
5.10.5在断电状态下,真空吸盘式管片吊机应保证吸持管片的时间不小于10min. 5.10.6注浆系统能力应按不低于150%的浆液注人率计算
5.10.7注浆系统应具有泵体和注浆管路清洗功能
5.10.8同步注浆系统应具有压力控制、流量控制及自动计量功能,并具有手动和自动控制模式
5.10.9宜配置泡沫系统,并宜采用单管单泵形式
5.10.10气动系统应符合GB/T7932的规定
5.10.11空气压缩机额定压力不应低于0.8MPa 5.10.12 气压缩机排气量不应低于设备同时工作时最大用气量的1.5倍
空 5.10.13给排水系统应能满足正常施工需要
5.10.14宜采用内外循环水冷却方式,内循环水应采用软水
5.10.15应配备满足延伸要求的水管储存装置
5.10.16应配备二次通风系统,后配套拖车尾端的回风速度不应小于0.3m/s
5.10.17储风筒风管储存长度不应小于100m,应配备升降装置
5.11液压系统 5.11.1液压系统应符合GB/T3766的规定
5.11.2液压缸应符合JB/T10205的规定
5.11.3应设置液压油冷却及油温检测装置
5.11.4油液固体颗粒污染等级不应低于GB/T14039规定的一/18/15.
5.12电气系统 5.12.1低压配电系统平均功率因数不应低于0.9 5.12.2低压供配电应具有两级漏电保护、短路保护、过载保护,缺相保护和相序保护功能 5.12.3高压开关柜应具有短路、过载等保护功能,宜具有外部分励脱扣装置
5.12.4主驱动电机及照明灯具防护等级不应低于IP65,其他电气设备外壳防护等级不应低于IP55
5.12.5控制系统应采用集散方式,通信系统应采用现场总线网络方式
GB/T34651一2017 5.12.6控制电源应采用稳压电源
5.12.7盾体内部管片拼装机区域的照度不应低于100lx;主控室内照度不应低于150lx
5.12.8通道应配置应急照明设备,应急照明最低照度不应小于15lx,应急照明时间不应小于1h
5.12.9电气设备及线路的绝缘电阻应符合GB50150的规定
5.12.10电缆的敷设应符合GB50168一2006中5.l,5.3,5.4,6.1,6.,2的规定
5.12.11应配备满足延伸要求的高压电缆储存装置
5.12.12主机及后配套拖车应配置备用电源插座
5.13数据采集系统 5.13.1应具有实时监控、实时/历史曲线显示、报警及主控室重要操作和重要历史数据的记录及查询、 掘进数据报表生成等功能
5.13.2信息储存容量不应小于500G
5.13.3应有远程数据传输接口
5.13.4应配置不间断电源,不间断电源的供电时间不应低于1h
5.14导向系统 5.14.1应具有设计轴线管理,空间位置检测、姿态检测、图形显示、测量基点校核及与主机控制系统通 信的功能
5.142直线段有效测量距离不应小于20m,角度渊量精度不应低于" 5.15职业健康与环境安全 5.15.1设备安全要求应符合GB/T34650的规定
5.15.2主控室应具有隔热、隔音、减震功能,并配置空调设备,主控室内的噪声不应高于70dB(A
5.15.3电气装置应符合GB5226.1.GB5226.3的要求
5.15.4高压电设备应配置防护隔离装置
5
.15.5操作维护区域内的棱角应符合GB/T17301的规定
5.15.6声音报警装置输出的最低声级值应比施工环境噪声至少高出10dBA). 5.15.7螺旋输送机出渣口处应配置气体监测系统,至少能检测O..CH,和Hs气体的浓度
5.15.8人舱应配置气体检测装置,至少能检测O.,CH.co和co气体的浓度 5.15.9在存在安全风险且人员易于接触的区域应设置急停装置
5.15.10后配套拖车出人口、主控室内应设置紧急信息指示牌,应包括疏散路线、救护设备和灭火设备 存放位置等 5.15.1应配登检熟盾体滚转角度的装置
5.15.12主控室、人舱及带式输送机卸料口应配置电话通信系统
5.15.13螺旋输送机出渣口及带式输送机卸料口应配置视频监视设备,主控室设置显示终端 5.15.14盾体和后配套拖车应配置灭火器
5.15.15人员带压进仓时,进人仓内的气体应符合人员呼吸要求
试验方法 o 6.1试验条件 6.1.1环境温度宜为5C35C 6.1.2试验场地应满足承载设备要求
GB/34651一2017 6.1.3试验用仪器仪表应校准,仪器仪表包括;全站仪,钢卷尺,钢直尺、直角尺、吊线锤、秒表、油压表、 气压表,兆欧表、照度仪、声级计和风速仪等
6.2目测检查 6.2.1检查范围应包括设备的布置状态,动作状态和显示状态
6.2.2检查不应拆解部件
6.3数据采集 试验检测时,单项数据采集不应少于3次,并与规定值进行比对
6.4开挖直径 在刀盘已安装到土压平衡盾构机的条件下,选定并标识水平及垂直方向基点,旋转刀盘,使用全站 仪测量开挖直径
6.5刀盘与刀具 6.5.1高差检测 检测步骤如下 将检测装置固定在刀盘最外侧刀具位置,见图2 a 用钢直尺测量最外倒刀具刀刃与检测装置的径向距离
,测量结果记人表c.I b 将前盾等分为12个检测区域,缓慢转动刀盘,用钢直尺测量各区域检测装置与前盾的最小距 离y,测量结果记人表c.1
说明 -前盾; -刀盘; -最外侧刀具; -检测装置
图2刀具相对前盾高差检测示意图
GB/T34651一2017 6.5.2刀具安装半径 检测步骤如下 将刀盘水平放置,以法兰面为基准调至水平; a b 将测量工装固定于刀盘面板中心,调平工装测量面; 直角尺水平边紧靠测量工装,竖直边与刀具刀刃中心线对齐,见图3 c d 记录直角尺对应工装上的刻度值 依次测出每件刀具的安装半径,并与设计值比对
说明 测量工装; 直角尺 刀具; 刀盘; 水平基准面 图3刀具安装半径和刀具高度检测示意图 6.5.3刀具高度 检测步骤如下 aa 将刀盘水平放置,以法兰面为基准调至水平; b) 将测量工装固定于刀盘面板中心,调平工装测量面 直角尺水平边紧靠测量工装,竖直边与刀具刀刃最高点对齐,见图3 c 记录直角尺水平边到刀具最高点的刻度值 d e 依次测出每件刀具的高度尺寸,并与设计值比对
6.5.4管路耐压 按JB/T5000.1ll中的方法进行刀盘内部管路耐压试验
6.6盾体 6.6.1盾体外径 检测方法如下 10
GB/34651一2017 将盾体放置在水平平台上,初定测量中心,将测量工装安装于盾体顶部,见图4 a b 50mm 将吊线锤固定于测量工装上,距离盾体外圆301 n处,使线锤方向与测量工装上的 mm一 整数刻度线重合; 沿周向每隔30"分别用钢直尺测出外圆面与线锤间距a,计算吊线锤对应刻度值与各测量值的 差值,得到盾体半径值,拟合盾体外圆轨迹,确定测量中心,将测量工装重新找正 d 再次测量a值,计算得出盾体半径值,并与设计值比对; 计算得出盾体外径
e 说明: -盾体(前盾/中盾/尾盾). -测量工装; -吊线锤; -水平平台面 图4盾体外径检测示意图 6.6.2盾体圆柱度 检测方法如下 根据6.6.1的测量方法,分别测量a一d值(a一d位置的高度间隔约为三分之一盾体高度).记 a 人表C.2,见图4:; 根据ad各位置平面的测量值,计算最大值与最小值的差值,得到盾体圆度:a b nin -c和dm-da,并与设计值进行比对 根据a),b)测得的直线度和圆度,计算得出圆柱度
6.7 主驱动单元 6.7.1主轴承寿命 检查并核对主轴承厂家提供的寿命计算文件
6.7.2最大转速 刀盘顺/逆时针旋转,转速由零调至最大,在刀盘旋转平稳后,用秒表记录刀盘旋转3圈的时间,计 11
GB/T34651一2017 算刀盘正:/反转最大转速,并与设计值进行比对
6.7.3点动转速 点动状态下刀盘慢速旋转,用秒表测量刀盘旋转一圈所用时间,计算刀盘转速
6.8人舱 人舱气密性的检测方法如下: a 关闭舱门; b)打开舱室进气阀; c 将试验压力设定为最大工作压力 d 关闭进气球阀,保压30 ,记录压力下降值
mln 6.9推进系统 6.9.1最大推进速度 在空载状态下,控制所有推进液压缸同时伸出,用秒表测量全部达到最大行程时间,计算得出最大 推进速度
6.9.2速度连续可调 在空载状态下,依次伸出各分区带有位移传感器的推进液压缸,伸出过程中旋转推进速度旋钮,观 察速度显示值
伸缩速度 6.9.3 在管片拼装模式下,推进液压缸全行程伸、缩,使用秒表记录伸、缩时间,分别计算得出伸、缩速度 6.10管片拼装机 6.10.1抓取装置安全系数 检查并核对抓取装置安全系数的计算文件
6.10.2回转速度 在管片拼装机抓取设计最重管片状态下,进行提升、平移、回转及定位动作,使用秒表记录回转时 间,计算得出回转速度
6.10.3载荷试验 载荷试验包括静载试验和动载试验,试验方法如下 静载试验;抓取机构静载试验载荷为设计最重管片的1.25倍,抓取时间10min以上,观察管 a 片拼装机的状态
b 动载试验;抓取机构动载试验载荷为设计最重管片的1.1倍,分别进行全行程的提升、平移、回 转及定位动作,观察管片拼装机的运行状态
6.10.4吸持状态检测 在真空吸盘式管片拼装机吸持设计最重管片状态下,切断动力源,20min后观察管片的吸持状态 及真空表显示值 12
GB/34651一2017 6.10.5制动性能 在管片拼装机抓取设计最重管片状态下,旋转过程中关闭动力源,检查制动性能
6.11螺旋输送机 6.11.1转速检测 在螺旋输送机正向及反向旋转状态下,转速由零调至最大,分别使用秒表测量1 min内旋转圈数或 旋转5圈10圈所用的时间,计算得出转速 6.11.2后闸门应急关闭 在螺旋输送机后闸门打开至最大状态下,使用秒表测量断电后闸门关闭时间
6.12最小转弯半径 采用计算机模拟方法验证最小转弯半径有效性
6.13管片吊机载荷试验 管片吊机载荷试验包括静载试验和动载试验,试验方法如下 静载试验:抓取机构静载试验载荷为最大管片重量的1.25倍,抓起悬空高度不应低于50mm aa 悬空时间不应少于10min,观察吊机的状态
动载试验;抓取机构动载试验载荷为最大管片重量的1.1倍,至少观察3个吊运循环内吊机的 b 运行状态,试验应包括对各机构在整个运动范围内作反复起动和制动,加速度和速度应控制在 设计范围内
6.14二次通风系统回风速度 在隧道施工及二次风机运行正常的状态下,使用风速仪检测后配套拖车尾端回风速度
6.15污染度检测 按照GB/T20082的规定对液压油进行污染度检测
6.16电气系统 6.16.1照明检测 在通电状态下,使用照度仪测量工作区域和人行通道的照度
6.16.2应急照明 在断电状态下,使用照度仪测量照度值
6.16.3绝缘检测 使用兆欧表检测电气设备和线路的绝缘电阻值
6.17职业健康与环境安全 6.17.1 噪声检测 在掘进作业状态下,使用声级计检测主控室内噪声,检测方法按照GB/T34650的规定执行
13
GB/T34651一2017 6.17.2气体监测 使用标准气体对气体监测系统进行测试
6.17.3急停检测 分别按下急停开关,检查相应系统运行状态
检验规则 7.1检验分类 检验分为出厂检验、工地检验和型式检验
7.2出厂检验 7.2.1出厂检验由制造商质量检验部门进行,检验合格后出具出厂检验合格证 7.2.2检验项目见表1
7.3工地检验 工地检验包括工地组装检验和试掘进检验 7.3.1 工地组装调试完毕后,由制造商和用户联合进行工地组装检验
7.3.2 7.3.3在完成制造商和用户协议约定的掘进距离后进行试掘进检验,检验合格后出具验收证书
7.3.4检验项目见表1
7.4型式检验 7.4.1有下列情况之一时,应进行型式检验
制造商或用户有需求时; a b) 结构、工艺和材料有较大改变,有可能影响产品性能时: 出厂检验与上次型式试验有较大差异时 c d) 国家质量监督管理部门提出型式检验要求时
7.4.2如果属7.4.1中a),d)两种情况,应检验表1规定的全部项目;如果属7.4.1中b),e)的情况,应进 行专用功能检验
表1检验项目分类表 工地检验 出 检验项目 技术要求 试验方法 序号 类别 工地组装 试掘进 检验 检验 检验 5.1. 整机 开挖直径 6.4 5.2.4 6.5.1 高差检测 刀具安装半径 5.2. 6.5.2 刀盘与刀具 刀具高度 5.2.2 6.5.3 管路耐压 5,2.10 6.5.4 14
GB/34651一2017 表1(续》 工地检验 出 序号 类别 检验项目 技术要求 试验方法 工地组装 试掘进 检验 检验 检验 盾体外径 5.3. 6.6.l 盾体 盾体圆柱度 5.3. 6.6.2 主轴承寿命 5.4.1 6.7.l 最大转速 5,4.5 6.7.2 主驱动单元 点动转浊 10 5,4.6 6,7.3 1 联锁控制 5,4.9 6,2 6.8 12 气密性 5.5.2 人舱 5.5.8 6.2 13 互锁检测 最大推进速度 5.6.4 6.9.1 14 15 推进系统 速度连续可调 5.6.5 6.9.2 16 伸缩速度 5.6.6 6.9.3 6.10.l 17 抓取装置安全系数 5.7.2 18 动作检测 5.7.1 6,2 管片拼装机 6.10.2 回转速度 5.7.1 19 20 5.7.3 6.10.3 载荷试验 吸持状态检测 6.10.4 5.7.4 管片拼装机 22 制动性能 5.7.8 6.10.5 23 转速检测 5.8,2 6.11.1 24 螺旋输送机 联锁检测 5.8.3 6.2 后闸门应急关闭 25 5.8.5 6.ll.2 5.10.1 6.12 26 最小转弯半径 5.10.,4 6.13 27 管片吊机载荷试验 28 5.10.5 6.2 管片吊机吸持状态 辅助系统 29 空气压缩机额定压力 5.10,11 6,2 二次通风系统 5.10.16 6.14 30 回风速度 液压系统 污染度检测 37 5.l1,4 6.15 5,12.7 32 照明检测 6.16.1 33 5.12.8 6.16.2 应急照明 电气系统 34 5.12.9 6.16.3 绝缘检测 噪声检测 5.15.2 6.17.1 35 15
GB/T34651一2017 表1续 工地检验 出 序号 类别 检验项目 技术要求 试验方法 试掘进 工地组装 检验 检验 检验 螺旋输送机出渣 5.15.7 6.17.2 36 口气体检测 37 5.15.8 6.17.2 人舱气体检测 电气系统 38 急停检测 5.15.9 6.17.3 39 紧急信息指示牌 5.15.10 6.2 40 视频监视设备 5.15.13 6.2 7.5判定规则 产品检验结果全部符合本标准所有技术要求者判为产品合格
8 随行文件 8.1随行文件应包括: 出厂检验合格证; 产品质量证明书 产品使用说明书; 产品维护保养手册; 主要部件装配尺寸图 电气系统、液压系统、辅助系统原理图: 外购主要部件随机资料 随机配件清单; 易损易耗件清单; 随机工具清单
8.2产品维护保养手册应包括产品的适用范围、结构功能说明、维护保养,以及操作规程等内容
9 标志、包装和运输 9.1标志 9.1.1设备出厂时,应在显著位置喷涂或粘贴产品标牌和有关标志,产品标牌和标志应符合GB/T13306 的规定
在标牌上至少应标出如下内容 设备名称; 设备型号; 出厂编号; 出厂日期 装机功率; 16
GB/34651一2017 供电电压; 整机重量; 制造商名称; 制造商地址
9.1.2应有警告和安全标志,起吊标志、润滑指示标记、操作及工作位置指示标记
警示标志和标语应 按照GB/T34650的规定执行
9.2包装和运输 9.2.1包装应符合GB/T13384的规定,并适合陆路运输,水路运输或航空运输及装卸的要求
9.2.2包装运输图示标志应符合GB/T191及GB/T6388的规定,其主要内容包括 收货站及收货单位名称 发货站及发货单位名称; 产品名称和型号 重量、箱号及外形尺寸; 起吊作业标志 g.2.3设备运输应符合铁路、公路和航运的规定
17
GB/T34651一2017 附 录 A 资料性附录 刀盘装备扭矩计算方法 设计扭矩计算法 A.1 A.1.1刀盘装备扭矩 刀盘装备扭矩按式(A.1)计算 T=k×T十T
十T
十T十T十T
十T,) A.1) 式中 T 刀盘装备扭矩,单位为牛米(N
m 系数; 刀盘的切削扭矩,单位为牛米(N
m); 刀盘正面的摩擦力矩,单位为牛米(Nm); T 刀盘背面的摩擦力矩,单位为牛米(N ,m T -刀盘圆周的摩擦力矩,单位为牛米(N
m); T 仓内搅拌力矩,单位为牛米(Nm); T 主轴承旋转阻力矩,单位为牛米(N
m; 驱动密封装置摩擦力矩,单位为牛米(Nm).
T A.1.2刀盘的切削扭矩 刀盘的切削扭矩计算按式A.2)计算 下-xD;义" × A.2 q 式中 D. -刀盘直径,单位为米(m); 土层的剪切强度,单位为帕(Pa); Vm 推进速度,单位为米每分( m/min; 刀盘转速,单位为转每分(r/ min
A.1.3刀盘正面的摩擦力矩 刀盘正面的摩擦力矩按式(A.3)计算 了-号xo 一 -a)×",×R'×P 式中 -刀盘开口率; 土层和刀盘之间的摩擦系数; p R 刀盘开挖半径,单位为米(m); 刀盘正面水平土压,单位为帕(Pa). P A.1.4刀盘背面的摩擦力矩 刀盘背面摩擦力矩近似等于刀盘正面摩擦阻力矩的50%,按式(A.4)计算: 18
GB/34651一2017 A.4 T,=0.5×T A.1.5刀盘圆周的摩擦力矩 刀盘圆周的摩擦力矩按式(A.5)计算 T=R×开×D×B×P,×" A.5 式中 -刀盘边缘宽度,单位为米(m) B P,-刀盘圆周土压,按埋深取值,单位为帕(Pa)
A.1.6仓内的搅拌力矩 仓内搅拌力矩由刀盘搅拌棒及刀盘扭腿搅动仓内渣土产生的扭矩和摩擦产生的力矩组成,按式 A.6)计算 T
=习R.Pl,h、+习R.",Pl.b,十习R.",Pl.b习R.Pl.h
A.6 式中 搅拌棒安装半径,单位为米(n R m; 搅拌棒的长度,单位为米(m) 搅拌棒厚度,单位为米(m): n 搅拌棒的宽度,单位为米(m); 刀盘扭腿长度,单位为米(m); 刀盘扭腿宽度,单位为米(G m; 刀盘扭腿的安装半径,单位为米(m); 刀盘扭腿厚度,单位为米m)
n A.1.7主轴承旋转阻力矩 主轴承旋转阻力矩T
,按式(A.7)计算 T
= (A.7 =".×R1×(GP 式中 主轴承滚动摩擦系数; 从 主轴承滚动半径,单位为米(m); R 刀盘自重,单位为牛(N). P,=(1一a)×开×R'×P A.8 式中 刀盘贯人荷载,单位为牛(N)
A.1.8密封装置摩擦力矩 密封装置摩擦力矩T按式(A.9)计算 T;=习2开×从m×F×ni×R A.9 式中: 密封与钢之间的摩擦系数,与密封材料特性有关 从m F 密封的推力,单位为牛(N); 密封数量; n 密封的安装半径,单位为米(m). R 19
GB/T34651一2017 A.2经验计算法 经验计算法按式(A.10)计算刀盘装备扭矩 (A.10 T=B×D×10 式中 扭矩系数; D 刀盘开挖直径,单位为米(m). 20
GB/34651一2017 附录 B (资料性附录 装备推力计算方法 B.1装备推力计算法 B.1.1 装备推力 装备推力根据式(B.1)计算 (B.1 F=k×(F+FF
+F十F 式中: -装备推力,单位为千牛(kN); 系数; F -盾体摩擦力,单位为千牛(kN); -尾刷与管片间摩擦力,单位为千牛(kN); 厂 F 开挖面支撑压力,单位为千牛(kN). 后配套拖车拖拉力,单位为千牛(kN); ! 刀具推力,单位为千牛(kN)
厂 B.1.2盾体摩擦力 盾体与地层间的摩擦阻力按式(B.2)计算 F=0.235×开×D×L×(2P
十2K
×P十K×y×D)×4十w×"B.2) 式中: -盾构机外径,单位为米(m) D -盾构机主机长度,单位为米(m) 盾构机顶部竖直土压,单位为千帕(kPa); P K
掘削断面处土体侧向土压系数; 土体浮重度,单位为千牛每立方米(kN/m=); W -盾构机主机重量,单位为千牛(kN); -地层与盾体外壳间摩擦系数
B.1.3尾刷与管片间的摩擦力 盾尾与管片间的摩擦力按式(B.3)计算 F=n×w.×"g十不×D,×b×户×n×A B3 式中: -盾尾内管片的环数; n w
-环管片的重量,单位为千牛(kN); 管片与盾尾间的摩擦系数; 12 管片外径.单位为米(m)7 D. -单道盾尾油脂腔与管片接触长度,单位为米(m); -盾尾密封油脂压力,单位为千帕(kPa); p3 21
GB/T34651一2017 盾尾油脂腔数量; n -管片与盾尾密封刷的摩擦系数
从 B1.4开挖面的支撑压力 开挖面的支撑压力按式(B.4)计算 (B,.4 F
=开×D'×P./4 式中 P -实际掘进土压,单位为千帕(kPa)
B.1.5后配套拖车的拖拉力 后配套的拖拉力按式(B.5)计算: B.5 F,=w×" 式中 W 后备套的自重,单位为千牛(kN) 后备套拖车与轨道的摩擦系数
B.1.6刀具推力 刀具推力按式(B.6)计算 F
=习n.×F
(B.6 式中 刀具数量; F 单把刀具最大贯人阻力,单位为千牛(kN)
B.2经验计算法 经验计算法按式(B.7)计算装备推力 B.7 F-=xxP" 式中 装备推力,单位为千牛(N). D 刀盘开挖直径,单位为米(m); p 单位掘削面上的经验推力,单位为千牛每平方米(kN/m'),土压平衡盾构机P一般为 1000kN/m'1300kN/m
22
GB/34651一2017 附录 C (资料性附录) 检查记录表 刀盘最外侧刀具与前盾高差记录表见表C.1
表C.1刀盘最外侧刀具与前盾高差记录表 编 号 检验地点 盾构机型号 其 他 测量日期 检验人员 区域序号 .r值 y值 -r]值 l0 11 12 检测结果判定 盾体外径和圆柱度测量记录表见表C.2
表C.2盾体外径和圆柱度测量记录表 编 检验地点 盾构机型号 检验人员 测量日期 其 他 实测值 盾体 位置 圆度 名称 平面 30 60" 90° 120" 150”180" 210°240" 270°300 330Lmax一min 前盾 中盾 23
GB/T34651一2017 表C.2(续 编 号 盾构机型号 检验地点 其 测量日期 检验人员 他 实测值 圆度 盾体 位置 名称 平面 30” 60" 90” 120" 150”180" 210°240" 270°300' [max-min 330° 尾盾 检测结果 判定 24