GB/T34904-2017
球墨铸铁件超声检测
Spheroidalgraphiteironcastings—Ultrasonictesting
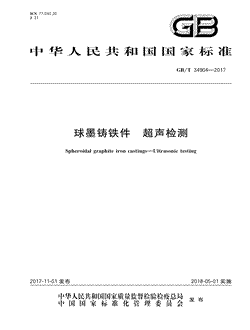
- 中国标准分类号(CCS)J31
- 国际标准分类号(ICS)77.040.20
- 实施日期2018-05-01
- 文件格式PDF
- 文本页数12页
- 文件大小1.08M
以图片形式预览球墨铸铁件超声检测
球墨铸铁件超声检测
国家标准 GB/T34904一2017 球墨铸铁件超声检测 Spheroidalgraphiteironeastings一Utrasonietestig 2017-11-01发布 2018-05-01实施 国家质量监督检验检疫总局 发布 国家标准化管理委员会国家标准
GB/34904一2017 前 言 本标准按照GB/T1.1一2009给出的规则起草
本标准由全国铸造标准化技术委员会(SAC/TC54)提出并归口
本标准负责起草单位:江苏吉鑫风能科技股份有限公司
本标准参加起草单位:大唐集团科学技术研究院有限公司华东分公司、兰州兰石铸锻有限责任公 司安徽省机械科学研究所、江苏钢锐精密机械有限公司、慈溪汇丽机电股份有限公司、马鞍山市海天重 工科技发展有限公司、沈阳铸造研究所
本标准主要起草人;李小青、倪满生、蒋春宏、刘雪波刘强虎,目兴义、郭宗山、梁立胜、罗宇 孙爱民、李兴捷
GB/34904一2017 球墨铸铁件超声检测 范围 本标准规定了球墨铸铁件超声检测的术语和定义、一般要求和检测方法
本标准适用于一般用途球墨铸铁件且厚度在10mm500mm范围内的球墨铸铁件缺陷的超声 检测
本标准不适用于球墨铸铁球化率的检测和穿透技术的检测方法
规范性引用文件 下列文件对于本文件的应用是必不可少的
凡是注日期的引用文件,仅注日期的版本适用于本文 凡是不注日期的引用文件,其最新版本(包括所有的修改单)适用于本文件
件
GB/T9445无损检测人员资格鉴定与认证 GB/T12604.1无损检测术语超声检测 GB/T19799.1无损检测超声检测1号校准试块 号校准试块 GB/T19799.2无损检测超声检测 2 GB/T27664.1无损检测超声检测设备的性能与检验第1部分:;仪器 GB/T27664.2无损检测超声检测设备的性能与检验第2部分;探头 超声检甜设备的性能与检验第了部分组合设愉 GB/T27664.3无损检测 JB/T9219球墨铸铁超声声速测定方法 术语和定义 GB/T12604.1界定的以及下列术语和定义适用于本文件
3.1 浮渣dross 铸件边缘区的细微夹渣物氧化物、硫化物等),密度比熔融金属小,结集在熔池表面或铸件表面的 熔渣
-般要求 4.1订货信息 订货时需方应提供下列信息 球墨铸铁件超声检测的区域、数量或百分数; a b球墨铸铁件各部位的质量等级; 检测工艺要求; c 是否有其他检测的特殊要求
d 4.2人员资质 超声检测人员应依据GB/T9445或其他等效标准的规定,取得相应资格证书
GB/T34904一2017 4.3检测设备 4.3.1超声检测仪 4.3.1.1超声检测仪的性能应满足GB/T27664.1规定的要求,并具备下列特性 范围钢中纵波和横波,至少在10mm和2000mm内可连续选择; aa b 增益;范围调整在80dB以上,步进级每档不大于2dB,精度1dB; c 至少满足双晶和单晶两种探头可调,同时满足探头从0.5MHz5MHz标称频率,可调换 使用
4.3.1.2操作人员应根据GB/T27664.3定期检查超声检测组合设备
4.3.2探头 4.3.2.1双晶探头应用于检测靠近测试表面的区域,检测近表面的缺陷时,可使用双晶探头或斜探头
4.3.2.2对于特殊的儿何形状,可使用斜探头进行检测
斜探头标称的折射角一般在45"一70"范围之 内,斜探头可检测的声程最大为100mm
4.3.3超声检测仪和探头 4.3.3.1 仅器和探头频半应分别符合GB/T27642和cBT276l.a 4.3.3.2高频率探头通常用于检测薄壁或高质量要求的铸件
铸件壁厚分区如图1所示 说明 边缘区 -中心区; 壁厚; a=1/5(最小5mm,最大30mm
图1铸件壁厚截面分区 4.3.3.3如果已知球墨铸铁件的声速,可根据声速确定探头的折射角,见图2
GB/34904一2017 12 Yl4 90 Bo 85" 80 75 70 70 65" 60 60" 50 50 45 40 40" 35” 30 20 2400 25002600 2700280029003000 3100 3255 3200 说明 Y -球墨铸铁的折射角a. 横波声速Cm,单位为米每秒m/s); Y2 俐的标称折射角; 同步的纵波和横波
图2已知钢的折射角确定斜探头在球墨铸铁中的折射角 4.3.3.4使用两个同样的探头精确测定折射角度,如图3所示
说明 =arctan 2 铸件的折射角; 在最大信号处斜探头的探头人射点的距离; -壁厚最终装配尺寸); 同型号的斜探头: 试样或参考试块 图3用斜探头确定球墨铸铁的折射角 已知折射角a,根据式(1),可以确定球墨铸铁横波声速
GB/T34904一2017 sina C
=3255× sina 式中 铸件横波声速,单位为米每秒(m/s); C
钢横波声速,单位为米每秒(m/s).; 3255 铸件折射角度,单位为度('); 钢折射角度,单位为度('). 4.3.4耦合剂 合剂应能润湿检测区域,保证探头与被检测面之间有最佳的声波传递效果
在进行校准和随后 所有的检测时,应使用相同的合剂
4.4铸件检测表面准备 被检测的铸件表面应与探头达到满意的耦合效果(例如铸态表面,抛丸表面、清理打磨表面或加工 表面). 4.5仪器校准 4.5.1参考反射体 4.5.1.1超声设备灵敏度设定需利用一个恰当的参考反射体,例如铸件本身的平行面、平底孔试块、长 横孔试块或根据GB/T19799.1和GB/T19799.2制作的参考试块等
4.5.1.2利用参考反射体来制作参考曲线时,应根据不同材料的声能衰减、表面质量和材料声速来确定 转移补偿
表1规定了铸件不同厚度的参考反射体可探测的最小平底孔直径的信号水平
表1超声可探性要求 检测区域铸件壁厚/mmm 符合5.1的可探测的最小平底孔直径/mm l1020 >20~100 >100250 10 >250500 4.5.2参考试块法 4.5.2.1 选用球墨铸铁参考试块 4.5.2.1.1参考试块应具备与被检测的铸件相同的超声特征,厚度应与被检测铸件的壁厚相当,表面特 性(表面光洁度)也要相同,试块的面应是平的和平行的
4.5.2.1.2参考试块应具有符合表1的平底孔或等效的长横孔作为参考反射体,利用式(2)可以进行由 平底孔直径到长横孔直径的换算 4935×Dm1 D 式中 长横孔直径,单位为毫米(mm) Da
GB/34904一2017 -平底孔直径,单位为毫米(mm); DrBH -波长,单位为毫米(mm); -声程长度,单位为毫米( mm 此公式仅适用于Dq>2A,S>5倍近场长度的单晶探头
4.5.2.2选用标准钢参考试块 当使用标准的钢参考试块设定灵敏度时,应考虑铸件和校准试块的声速、声衰减和表面质量的 不同
4.5.3选用DGS法 直接利用铸件本身的平行面作为参考反射体,使用针对球墨铸铁计算出的DGS图(有些探头自带 来进行超声设备灵敏度的设定 检测方法 5.1材料 5.1.1小铸件,一般铸件重量<500kg;大铸件,一般铸件重量>500kg
小铸件的质量等级执行表" 和表3,大铸件执行表4和表5,适用于铸件不同壁厚区域 5.1.2操作人员应根据JB/T9219检查球墨铸铁件的纵波声速,纵波声速应>5500m/s 5.1.3材料的超声可探性可通过比较参考反射体回波高度(通常是第一次底波)和噪声信号来评价
评价时应选择球墨铸铁件具有代表性的区域,该区域应是上下面平行的最终表面和最大厚度
5.1.4被检材料的第一次底波高度至少要比草状回波高6dB
若达不到时,需将探测到的平底孔或横 孔直径在检测报告中说明
表2小铸件缺陷严重度等级划分 严重度等级 标记 单位 50 检测区域壁厚 <50 >50 <50 >50 <50 50 >50 mm 缺陷最大厚度占 % 15 20 25 30 壁厚的百分比 边缘区缺陷最大长度 mm l0 l6 25 35 70 200 500 500 125o0 边缘区缺陷最大面积 70 200 mm 中心区缺陷最大长度 12 12 20 20 32 32 45 mm 中心区缺陷最大面积 125 300 300 800 800 2000 2000 4000 mmm 注1:关于浮渣见表3. 注2:按球墨铸铁件最终使用尺寸进行区域划分,边缘区见图1
注 允许最多有2个表中规定面积的指示缺陷 3 不能有超过表6规定范围的指示缺陷
GB/T34904一2017 表3小铸件非加工区域浮渣最大允许厚度 严重度等级 标记 占壁厚的 10 15 20 百分比/% 不能有超过表6规定范围的指示缺陷 表4大铸件缺陷严重度等级划分 严重度等级 标记 单位 01 50 50 50 50" 200 50 50 200 50 200 检测区域壁厚 rmm 50 >200 200 200 200 200 缺陷最大厚度、 % 15 25 20 30 占壁厚的百分比 边缘区缺陷 500 800600100o1000100020002000 300 mm 最大面积 中心区缺陷 mm 2500500o1000o1000o150002000o1500o200003000020000 最大面积 缺陷总面积占 10 10 10 10 15 15 15 20 20 15 20 30 检测区域百分比 注1;关于浮渣参阅表5
注2:按球墨铸铁件最终使用尺寸进行区域划分,边缘区见图1
不能有超过表6规定范围的指示缺陷
表5大铸件非加工区域浮渣最大允许厚度 严重度等级 标记 01 占壁厚的 10 15 20 25 百分比/% 不能有超过表6规定范围的指示缺陷
5.2检测程序 5.2.1探测和扫查方向选择 5.2.1.1人射方向和探头的选择很大程度上取决于铸件形状,缺陷的性质和位置,检测程序由铸件生产 商和有经验的操作者来制定
GB/34904一2017 5.2.1.2探头扫查时要有重叠,扫查速度不应超过150 mm/s,相邻两次扫查相互重叠区约为探头晶片 尺寸的15%
5.2.2探测和扫查灵敏度设定 5.2.2.1 探测灵敏度 对于待检铸件的壁厚范围,表6给出最大壁厚的平底孔或等效横孔的回波高度应不小于屏幕高度 的40%
如果无法设定这种最小的探测灵敏度,应在检测报告里注明
表6被评估的超声指示缺陷 评估范围 检测区域的件壁厚/mmm 符合5.1的最小可探测 回波高度大于噪声级 底波衰减/dB最小 平底孔直径/mm 以上/dB最小) >l020 >20~100 20 >100一250 12 250500 10 仅用于因铸件几何形状不能获得底波的区域
5.2.2.2 扫查灵敏度 搜索不连续时,扫查灵敏度的设定可以提高至草状回波在屏幕上刚刚可见,或者也可在最小灵敏度 上直接加6dB. 5.2.3 评定不同类型缺嗡 在铸件检测中需要评定以下两种指示(证明不是由于铸件形状或稠合造成的) 5.2.3.1 底波衰减 中间回波
各种类型的指示可单独出现也可能同时出现
5.2.3.2加工面上的缺陷,如加工后会露头,无论大小都需要在报告中记录
5.2.4缺陷尺寸确定 5.2.4.1总述 如果缺陷的间距小于最大缺陷的长度,相邻的缺陷视为一个缺陷
5.2.4.2确定投射在表面的缺陷尺寸 5.2.4.2.1针对根据表2,表4由于中间回波高度(见表6)需记录的缺陷,确定其表面尺寸时,探头应在 检测区域上方移动,画出比回波峰值低6dE信号点
5.2.4.2.2针对底波衰减的情况,探头应在检测表面移动,确定那些根据表6底波衰减12dB或20dB 的点
5.2.4.2.3两种情况确定的点都应精确的标记例如直探头为探头中心,斜探头为探头人射点,可以在 缺陷部位使用最小声束直径的探头),标记点之间的连线给出了缺陷可测量的尺寸
GB/T34904一2017 5.2.4.2.4使用斜探头时,只要铸件形状允许,缺陷边缘点应尽可能投射到铸件的检测表面上
5.2.4.3确定壁厚方向的缺陷尺寸 对于根据表2,表4由于中间回波高度(见表6)需记录厚度方向尺寸的缺陷[5.2.5.1b),d)],使用直 探头从两面(见图4)测量缺陷在壁厚方向到检测表面的距离
说明 扫描位置; 扫描位置; -从扫描位置a开始的a扫描; 从扫描位置b开始的b扫描 S -声程长度,单位为毫米(mm):; -声程长度,单位为毫米(mm); S. -壁厚最终装配尺寸),单位为毫米mm)
深度方向尺寸大小D='-(s,十s)) 图4使用直探头确定壁厚方向缺陷尺寸 5.2.4.4确定壁厚方向浮渣层厚度 使用直探头从浮渣层的对面(见图5)测量浮渣层厚度
5.2.5缺陷评估和记录 5.2.5.1 缺陷的评估和记录条件 当所有底波衰减或缺陷回波高度达到或超过表6规定的范围极限值时,都应当进行评估,如果其值 超过表2,表3或表4,表5各自规定的范围极限的75%,应记录[见下文a),b),c),d),e)描述],其位置 和标注应在检测报告中注明,记录的缺陷位置可用网格、图纸或照片描述
GB/34904一2017 无中间回波但底波衰减>评估限值;通过底波衰减来确定缺陷面积 a b 中间回波>评估限值并且底波衰减>评估限值;通过中间回波和底波衰减来确定缺陷面积,取 两者的并集,同时要通过超过评估水平的中间回波来确定缺陷的厚度方向尺寸 中间回波<评估限值并且底波衰减>评估限值;通过底波衰减来确定缺陷面积 c d 中间回波>评估限值并且底波衰减一评估限值;通过中间回波来确定缺陷面积,同时要通过超 过评估水平的中间回波来确定缺陷的厚度方向尺寸; 中间回波<评估限值并且底波衰减一评估限值;无需记录
5.2.5.2特殊缺陷的记录和评定 5.2.5.2.1当缺陷同时位于边缘区和中心区时,以下规定适用 如果缺陷>50%在边缘区,则计为边缘区缺陷,缺陷面积参照边缘区的验收条件翻倍后验收 如果缺陷<50%在边缘区,则计为中心区缺陷,缺陷面积参照中心区的验收条件减半后验收 b 5.2.5.2.2如铸件壁厚<10mm,总的壁厚均为边缘区
5.2.5.2.3如果分别同时存在表2和表3或表4和表5的缺陷指示,则分别记录,按照最严重的缺陷指 示评定质量等级
说明: 壁厚(最终装配尺寸,单位为毫米(n mm); 声程长度,单位为毫米(mm); S 浮渣厚度,单位为毫米(mm)
图5使用直探头确定壁厚方向浮渣厚度
GB/T34904一2017 5.2.5.3验证记录的指示缺陷 如需对缺陷进一步分析,包括其类型、形状、尺寸和位置,可以通过改变探头频率、大小或改变检测 程序来进行,也可使用射线探伤或其他方法检测
5.3检测报告 检测报告应包含以下信息 执行标准; a b 被检测铸件的特征(如名称,编号、材质、热处理状态、探伤面的表面粗糙度等) 检测范围; c d 使用的检测设备类型; 使用的探头 关于检测区域的检测方法 灵敏度设定所需的所有数据; g h 超声检渊合适性的结果, 关于所有被记录的缺陷的典型特征信息(例如底波衰减、壁厚方向的位置、尺寸、长度,面积和 缺陷当量大小)和其位置描述(图纸或照片); 缺陷的质量等级评定及检测结论 k)检测人员、日期和负责人的签名 0
球墨铸铁件超声检测GB/T34904-2017
球墨铸铁件是一种高强度、高韧性的铸造材料,在工业生产中得到广泛应用。由于球墨铸铁件通常用于承受重要载荷,因此其质量控制至关重要。超声检测是一种非破坏性的检测方法,可以有效地检测球墨铸铁件中的缺陷,保证其质量。
GB/T34904-2017标准介绍
GB/T34904-2017是中国国家标准化委员会发布的新版球墨铸铁件超声检测标准,取代了2008年颁布的旧版标准。该标准规定了球墨铸铁件超声检测的技术要求、检测分类、检测报告等内容。
技术要求
GB/T34904-2017标准规定,球墨铸铁件的超声检测应该采用脉冲回波法或者全波整幅法。其中,脉冲回波法适用于探测直径大于等于20mm的缺陷;全波整幅法适用于探测直径小于20mm的缺陷。此外,标准还规定了探头的选择、检测灵敏度、检测评定等技术要求。
检测分类
GB/T34904-2017标准将球墨铸铁件的超声检测分为三类:A类、B类、C类。其中,A类表示对球墨铸铁件进行全面检测,包括表面和内部的所有区域;B类表示对球墨铸铁件进行抽样检测,只检测一部分区域;C类表示对球墨铸铁件进行目视检验,不做超声检测。
检测报告
根据GB/T34904-2017标准,球墨铸铁件的超声检测报告应包括以下内容:被检测件的名称、型号、数量、检测机构名称、检测人员姓名、检测日期、检测结果等信息。检测结果应标明缺陷位置、形状、大小、数量、类型等详细信息。
球墨铸铁件超声检测流程
球墨铸铁件超声检测的流程包括以下几个步骤:
- 确定被检测件的材料和规格;
- 选择合适的探头和检测方法;
- 对被检测件进行表面处理,去除杂质和锈蚀层;
- 进行超声探伤,并记录缺陷位置、形状、大小等信息;
- 评定缺陷级别,根据GB/T34904-2017标准确定缺陷是否达到报废标准;
- 编写检测报告,并将结果反馈给客户。
总结
球墨铸铁件超声检测是一种重要的质量控制手段,可以有效地发现球墨铸铁件中的缺陷。GB/T34904-2017标准对球墨铸铁件超声检测进行了全面规范,详细介绍了技术要求、检测分类和检测报告等方面的内容。在进行球墨铸铁件超声检测时,应严格按照标准要求进行操作,确保检测结果的准确性和可靠性。