GB/T35072-2018
石油天然气工业用耐腐蚀合金复合管件
Corrosionresistantalloybimetalfittingsforpetroleumandnaturalgasindustries
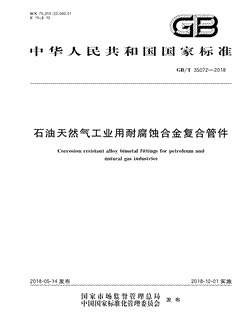
- 中国标准分类号(CCS)E16;J15
- 国际标准分类号(ICS)75.200;23.040.01
- 实施日期2018-12-01
- 文件格式PDF
- 文本页数41页
- 文件大小3.17M
以图片形式预览石油天然气工业用耐腐蚀合金复合管件
石油天然气工业用耐腐蚀合金复合管件
国家标准 GB/T35072一2018 石油天然气工业用耐腐蚀合金复合管件 lfitnsforpetrolemand Corrosionresistantaloybimetal gasindustries natural 2018-05-14发布 2018-12-01实施 国家市场监督管理总局 发布 国家标准化管理委员会国家标准
GB/35072一2018 目 次 前言 范围 规范性引用文件 术语和定义、符号、代号和缩略语 3.1术语和定义 3.2符号和代号 3.3缩略语 种类与代号 设计 尺寸与公差 o 6.1标准尺寸 6.2壁厚 6.3内径 6.4椭圆度 6.5公差 材料 7.1基层 7.2内覆层 7.3复合板 7.4母管 l0 制造 8 ll -般规定 8.l .2煤接 12 8.3热处理 12 8. 校圆 12 12 8.5管端 8.6表面处理 13 8.7工艺评定 13 技术要求和检验方法 13 9.1 -般规定 13 9.2几何尺寸 14 9.3化学成分 15 9.4拉伸性能 15 9.5CVN冲击韧性 16 9.6导向弯曲试验 17 17 9.7全截面维氏硬度 19 9.8表面硬度
GB/T35072一2018 19 9.9焊缝宏观检查和金相组织检验 20 9.10内覆层剪切结合强度 20 9.11晶间腐蚀试验 20 9.12基层材料腐蚀试验 20 9.13内覆层材料腐蚀试验 20 9.14静水压试验 21 9.15设计验证试验 10无损检测 22 m 0.1 -般要求 0.2表面检测 22 23 0.3管体和焊缝 2: 0.4管端 23 0.5管端剩磁 1 表面质量、缺欠和缺陷处理 223 3 l1.1表面质量 23 1l.2缺欠和缺陷处理 24 12标志 24 2.l标志方法 12.2标志位置 24 12.3标志内窑 24 12.4标志示例 24 13运输与防护 25 14 文件 25 附录A规范性附录)内覆层材料腐蚀试验方法 26 附录B(规范性附录制造工艺评定 29 附录c(资料性附录)复合管件检验和试验取样位置 31 附录D(资料性附录)基层材料腐蚀试验方法 35 参考文献 37
GB/35072一2018 前 言 本标准按照GB/T1.1一2009给出的规则起草
请注意本文件的某些内容可能涉及专利
本文件的发布机构不承担识别这些专利的责任
本标准由全国石油天然气标准化技术委员会(SAC/Tc355)提出并归口 本标准起草单位:石油天然气集团公司石油管工程技术研究院、郑州万达重工股份有限公司、 浙江久立特材科技股份有限公司、石油天然气股份有限公司塔里木油田分公司、石油工程建设 有限公司西南分公司、沧州隆泰迪管道科技有限公司、西安向阳航天材料股份有限公司、河北沧海核装 备科技股份有限公司、石油化工股份有限公司西北油田分公司
本标准主要起草人;魏斌、李为卫、戚东涛,冯耀荣、马秋荣、方伟,秦长毅、李发根,李循迹、李亚军、 李先明、,雏定明、张付峰、任保剑、陈庆标、杨立建、王春建、李华军、孟庆云、羊东明、杨志勇
GB/35072一2018 石油天然气工业用耐腐烛合金复合管件 范围 本标准规定了石油天然气工业管道输送系统用公称直径DN50DN800以耐腐蚀合金作为内覆 层的冶金复合管件的设计、几何尺寸、材料、制造工艺、技术要求和检验方法、NDT、表面质量与缺陷处 理、标志运输和防护等基本要求
本标准适用于石油天然气工业领域输送管道以及工艺管道输送含有腐蚀性介质的石油,天然气和 水等单相或多相流体用耐腐蚀合金复合管件,其他领域也可参照使用
本标准复合管件包括弯头、三 通、异径接头和管帽
规范性引用文件 下列文件对于本文件的应用是必不可少的
凡是注日期的引用文件,仅注日期的版本适用于本文 件
凡是不注日期的引用文件,其最新版本(包括所有的修改单)适用于本文件
GB/T228.1金属材料拉伸试验第1部分:室温试验方法 GB/T228.2金属材料拉伸试验第2部分;高温试验方法 GB/T229金属材料夏比摆锤冲击试验方法 GB/T232金属材料弯曲试验方法 GB/T4340.1金属材料维氏硬度试验第1部分;试验方法 GB/T6394金属平均晶粒度测定方法 GB/T6396复合钢板力学及工艺性能试验方法 GB/T8923.1一2011涂覆涂料前钢材表面处理表面清洁度的目视评定第1部分:未涂覆过 的钢材表面和全面清除原有涂层后的钢材表面的锈蚀等级和处理等级 GB/T9445一2015无损检测人员资格鉴定与认证 GB/T10561钢中非金属夹杂物含量的测定标准评级图显微检验法 GB/T12459钢制对焊管件类型与参数 GB/T13401 钢制对焊管件技术规范 GB T 15970.2金属和合金的腐蚀应力腐蚀试验第2部分;弯梁试样的制备和应用 GB 17394.1金属材料里氏硬度试验第1部分:试验方法 GB/T17600.1钢的伸长率换算第1部分;碳素钢和低合金钢 GB/T18590金属和合金的腐蚀点蚀评定方法 GB/T29168.2石油天然气工业管道输送系统用感应加热弯管管件和法兰第2部分;管件 GB50251输气管道工程设计规范 GB50253输油管道工程设计规范 NB/T47002.1一2009压力容器用爆炸焊接复合板第1部分:不锈钢-钢复合板 NB/T47002.2一2009压力容器用爆炸焊接复合板第2部分:镍-钢复合板 NB/T47013.2一2015承压设备无损检测第2部分;射线检测 NB/T47013.3承压设备无损检测第3部分;超声检测 NB/T47013.4一2015承压设备无损检测第4部分;磁粉检测
GB/T35072一2018 NB/T47013.5一2015承压设备无损检测第5部分;渗透检测 NB/T47013.7承压设备无损检测第7部分;目视检测 NB/T47014承压设备焊接工艺评定 NB/T47015压力容器接规程 sY/T4109石油天然气钢质管道无损检测 sY/T5257油气输送用感应加热弯管 sY/T6423.1一2013石油天然气工业钢管无损检测方法第1部分;焊接钢管焊缝缺欠的射 线检测 SY/T6423.,2一2013石油天然气工业钢管无损检测方法第2部分;焊接钢管焊缝纵向和/或 横向缺欠的自动超声检测 sY/T6423.4石油天然气工业钢管无损检测方法第4部分;无缝和焊接钢管分层缺欠的自 动超声波检测 TSGZ6002特种设备焊接操作人员考核细则 IsO15156-1石油天然气工业油气开采中用于含H,S环境下的材料第1部分;抗裂材料选 择的一般原则Petroleumandnaturalgasindustries一MaterialsforuseinHS-containing environmentsin.oilandgasprodueionPart1,General prineiplesforselectionof cracking-rtesistanmt material) ISO15156-2石油天然气工业油气开采中用于含H,S环境下的材料第2部分;抗裂碳钢和 低合金钢以及铸铁的使用(Petroleum" andnatural sindustriesMaterialsforuseinHS-containi gas ing oilandgasprodu uetionPart2Cracking-resistantcarbonandlow-alloy steels,and environmentsin heuseofcastirons APISpee5L;2012管线钢管规范(Speeifieationforlinepipe) APISpee5LD内覆或衬里耐腐蚀合金复合钢管规范(SpeeifeationforCRAcladorlinedsteel pipe ASTMA263;2012铬不锈钢复合钢板标准规范(Standardspeeifcationforstainlesschromium steel-cladplate) 铬镍不锈钢复合钢板标准规范Standardspeifceationforstainmles ASTMA264:2012 dhromium-nickelsteelcladplate' ASTMA265:2012 specificationfornickeland 镍与镍基合金复合钢板标准规范Standard nickel-basealoyeladsteelplate) testmethods, AsTMA751钢产品化学分析的试验方法规程和术语(Standard practices,and forchemicalanalysisofsteelproduet) terminology ASTME340金属和合金宏观腐蚀的标准试验方法Standardpraeticeformacroetchingmetals andalloys) ASTME353不锈钢、耐热、马氏体和其他类似的铬-镍-铁合金的化学分析标准测试方法 Standardtestmethodsforchemicalanalysisofstainless,heat-resistingmaragingandothersimilar chromium-nickel-ironaloys AsTMES62用系统人工点计数法测定体积分数的试验方法(Standardtestmethodfordetermi ningvolumefractionbysystematicmanualpointcount)
GB/35072一2018 术语和定义、符号、代号和缩略语 3.1术语和定义 下列术语和定义适用于本文件
3.1.1 购方purehaser 业主并包括其代理人、检查人员以及其他被授权的代表
3.1.2 制造商manufaeturer 按本标准的要求,负责生产复合管件且对产品做标志的工厂或公司
3.1.3 冶金复合ead 通过热轧、爆炸、堆焊等复合工艺,使耐腐蚀合金与碳钢或低合金钢的接触界面形成原子相互扩散 而形成的结合
3.1.4 基层backinglayer 复合板、复合管或复合管件的承受力学载荷或承压部分,由碳钢或低合金钢材料制成
3.1.5 内覆层cladlayer 通过冶金复合方式结合在碳钢或低合金钢基层材料表面的耐腐蚀合金材料部分
3.1.6 同类复合管件bimetalfntinesfsameype -组具有相同代号的弯头、三通、异径接头或管帽
3.1.7 外弧侧extrados 弯头弯曲段的外侧部分
3.1.8 内弧侧 intr0ad0s 弯头弯曲段的内侧部分
3.1.9 直管段tangent 管件端部的直管部分 3.1.10 耐腐蚀合金复合管件corrosionresistantalloybimetalfitings 按照基层材料承压,内覆层材料防腐蚀的原则,由碳钢或低合金钢作为基层材料、耐腐蚀合金作为 内层复合而成的管件,简称复合管件
3.1.11 耐腐蚀合金eoostonresistantaloy 用于制造复合板、母管和复合管件内覆层的不锈钢、镍基合金等耐腐蚀合金材料的统称
3.1.12 母管motherpipe 用于制造耐腐蚀合金复合管件的冶金复合直管
GB/T35072一2018 3.1.13 未结合 unbound 基层与耐腐蚀合金层之间的未黏接
3.1.14 酸性环境 SOurenvirOment HS分压大于或等于0.3kPa并能够引起如IsO15156-2所规定的碳钢或低合金钢材料发生SsC 和HIC失效形式的含石油、天然气和水等介质的单相或多相流体环境
3.1.15 剪切结合强度 shearbondstrength 使以冶金结合的复合板、复合管或复合管件的内覆层与基层发生分离的单位接触面积所需要的切 向应力
3.1.16 抗点蚀当量数pttin ingresistanceequivalentnumber 用以反映和预测耐腐蚀合金的抗点蚀能力,依据合金化学成分中Cr、Mow和N元素的含量 来定 注;详细的信息见ISO15156-3
3.2符号和代号 下列符号和代号适用于本文件
-90"弯头中心至端面长度,单位为毫米(mm); B -45"弯头中心至端面长度,单位为毫米mm): 三通中心至端面长度(管程),单位为毫米(mm); D.D 复合管件端部外径,单位为毫米(mm); 复合管件端部名义内径,单位为毫米(mm) 复合管件横截面上的最大外径,单位为毫米(mm); Dma 复合管件横截面上的最小外径,单位为毫米(mm) 复合管件横截面处名义外径,单位为毫米( mm; 与复合管件相连接管子的名义外径,单位为毫米(n D mm
DN 公制单位的复合管件公称直径,为非测量值,单位为毫米(n mm; E,E 管帽背面至端面长度,单位为毫米(m mm 复合管件焊接端坡口内覆层伸出长度,单位为毫米(n mm; -异径接头端面至端面长度,单位为毫米(mm n; H 三通中心至端面长度(出口),单位为毫米( mm; 椭圆度; 复合管件验证试验计算最小强度,单位为兆帕(MPa) Q 复合管件形位公差,端面垂直度,单位为毫米(mm); 抗拉强度 总伸长率0.5%的屈服强度 os -腐蚀试样面积,单位为平方毫米(mm=); 复合管件内覆层公称壁厚,单位为毫米(mr m; -复合管件基层公称壁厚,单位为毫米(mr m; t T 腐蚀试验时间,单位为天(d); 与复合管件相连接管子的公称壁厚或复合管的基层公称壁厚,单位为毫来(m m;
GB/35072一2018 U -形位公差,复合管件平面度,单位为毫米(mm); -平均腐蚀速率,单位为毫米每年(mm/a); veor 复合管件基层材料的实际抗拉强度(当复合管件基层材料的实际拉伸强度小于连接管的名 义最小抗拉强度时,按连接管的名义最小抗拉强度计算),单位为兆帕(MPa)5 设计验证试验系数; AW -腐蚀试样的质量损失,单位为克(g); 腐蚀试样材料的密度,单位为克每立方厘米(g/em 3.3缩略语 下列缩略语适用于本文件
AUT自动超声检测(automaticultrasonictesting CLR裂纹长度率(craeklengthratio) csR裂纹敏感率(eracksensitvityratio) CTR裂纹厚度率(erackthickne eSSratio cVN夏比V缺HGhampwVmah HAZ热影响区(heatalfectedzone) nc复敬开裂Codtogaimcaf lcrnacking) MQ广制造工艺评定试狼 nalificationtest manulacturingprocedurequal MPs制造工艺规范 faeturingprocedurespeeifeation) manu 磁粉检测magnetietesting " 无损检测(nondestruetivetesting PREN抗点蚀当量数(pittingresistanceequivalentnumber) 渗透检测(penetranttesting PmT Rr 射线检测radiographictesting Scc应力腐蚀开裂(stresscorosioneraekine SMYs规定最小屈服强度(specifedminimumyieldstrength) stresscracking SSC硫化物应力开裂(sulfide TIG铐极惰性气体保护焊(ungstem inertgasarcwelding UT超声波检测(ultrasonictestin ing 种类与代号 本标准所包含的耐腐蚀合金复合管件种类及代号见表1
表1复合管件的种类和代号 种类 类型 代号 45E(L 45"弯头 长半径 长半径 90E(L 90"弯头 短半径 90E(S) 同心 R(C 异径接头(大小头) 偏心 R(E)
GB/T35072一2018 表1(续》 种类 类型 代号 等径 T(S) 三通 T(R 异径 管帽 5 设计 5.1复合管件设计文件应至少包括设计图和强度计算文件
复合管件的设计参数应与相连管道的设 计参数一致
5.2复合管件强度和选材设计应遵循基层承压、内覆层防腐蚀的原则
5.3复合管件应依据输送流体的压力和温度进行强度设计,应优先采用GB50251,GB50253或国家 认可的压力容器或压力管道规范规定的计算分析方法确定基层公称壁厚,也可按照9.15规定的验证试 验方法确定复合管件基层壁厚,复合管件承受内压的能力应不低于连接管道的耐压能力
此外,设计者 还应依据GB50251或GB50253规定考虑其他载荷,包括静态和动态载荷,以及所在管线的压力试验 条件
5.4采用复合板卷制成型的复合管件的内覆层最小设计壁厚应不小于2.5mm,采用堆焊工艺制造的 复合管件的内覆层最小设计壁厚应不小于3.01 mm
5.5复合管件的材料选择应考虑输送流体的腐蚀性,并遵循以下原则 若输送流体含有HS且属于酸性环境,应由购方与制造商协议确定复合管件基层是否需要满 a 足ISO15156-1和ISO15156-2要求
b 若输送流体含有Hs,CO.,CI等一种或多种腐蚀性介质,内覆层应具有抗SsC和/或sSCC 抗失重腐蚀和点腐蚀能力,应确保内覆层材料能够满足附录A要求 6 尺寸与公差 6.1标准尺寸 除本标准另有规定外,复合管件应符合GB/T12459或GB/T13401规定的几何尺寸,复合管件端 部外径分为I和I两个系列,I系列为国际通用系列,在书写标志时“I”可以省略,且应优先选用 系列 6.2壁厚 6.2.1若采用5.3规定的计算分析方法确定复合管件基层壁厚,基层最小壁厚可比其公称壁厚小 0.25mm.孤立的非连续局部减薄处或经修磨后部位的基层剩余壁厚应不小于公称壁厚的87.5%
6.2.2复合管件内覆层壁厚应不低于最小设计壁厚要求,内覆层壁厚仅允许正偏差且偏差不大于 1.0mm 6.3内径 距离管端50mm范围内复合管件内径应与相连管线内径一致,且距离管端50mm范围内的内径 允许最大偏差为士0.5mm.
GB/35072一2018 6.4椭圆度 对于所有复合管件,距管端100mm范围内,椭圆度O应不大于0.5%;对于所有弯头,弯曲段的椭 圆度o应不大于2.5%
椭圆度0按式(1)计算 D Dmin" O一 ×100% D 式中 椭圆度; D 复合管件横截面上的最大外径,单位为毫米(n mm -复合管件横截面上的最小外径,单位为毫米(m D mm; mn D -复合管件横截面处名义外径,单位为毫米( mm
6.5公差 6.5.1复合管件尺寸的极限偏差应符合图1和表2的规定
6.5.2复合管件的形位公差应符合图2和表3的规定
表2复合管件尺寸的极限偏差 单位为毫米 公称直径DN范围 50~65 80100 125~200 250450 500600 650800 项目 管件种类 公差 十4.0 十6.4 十6.4 +1.0 十2.0 端部外径,D 、D 士1.6 一0,8 -1.2 2.5 一4.8 端部内径 距离管端50mm范围内允许最大偏差为士0.5mm 所有管件 最小壁厚为t自一0.25mm1 基层壁厚" 十l,0 内覆层壁厚 端部椭圆度 距离管端100mm内不超过0,5% 弯曲段椭圆度 所有弯头 不大于2.,5% 45"弯头 中心至端面 90"弯头 士2.0 士3.0 尺寸,A、B、,C、M 三通 端面至端面长度,H 异径接头 士2.0 士3.0 背面至端面长度,E或E 管帽 士3.0 士5,0 当需要增加复合管件基层壁厚以满足抗内压要求时,该公差可能不适用于成型复合管件的局部区域 采用计算分析方法确定的基层最小壁厚为基层公称壁厚减去0.25mm.但不包括6.2.1所允许的孤立的非 连续局部减薄情况
GB/T35072一2018 45"弯头 90"弯头 a 等径三通 异径三通 偏心异径接头 同心异径接头 管帽 图1复合管件几何尺寸示意图
GB/35072一2018 弯头 oI h)三通 图2复合管件的形位公差示意图 表3复合管件的形位公差 单位为毫米 公称直径[DN范围 项目 管件种类 50100 125200 250~300 350400 450600 650800 公差 弯头、异径 端面垂直度Q 士0,8 士1.6 土2.4 士3,2 士4.8 接头、三通 复合管件平 45"和90"弯头 士1.6 土3.2 士4.8 士6.4 士9.5 士12.5 面度U 三通 材料 7.1基层 7.1.1复合管件的基层材料应选用与其相连接的管线管具有相同或相近的钢级、化学成分和力学性能 的碳钢或低合金钢,基层材料的化学成分和力学性能应满足APISpec5L;2012中PsL2要求
经购方 与制造商协议,基层也可选择GB/T12459或GB/T13401规定的碳钢和低合金钢材料并满足相应的
GB/T35072一2018 标准要求
7.1.2若复合管件输送流体中含Hs且属于酸性环境,应由购方与制造厂协议确定复合管件基层母材 和焊缝是否需要满足APISpec5L;2012附录H,ISO15156-1和ISO15156-2相关要求
7.2内覆层 7.2.1复合管件内覆层应优先选用APISpec5LD规定的奥氏体不锈钢或镍基合金,且应符合APl Spec5L.D对化学成分的要求,与流体接触的耐腐蚀合金焊缝金属或采用堆焊工艺制造的耐腐蚀合金内 覆层也应符合APISpee5LD对化学成分的要求
经购方与制造商协议,内覆层也可选择其他耐腐蚀 合金材料并满足相应的标准要求
7.2.2如购方对内覆层耐腐蚀合金材料的PREN最小值有规定,产品分析结果也应满足此要求
7.3复合板 用于制造母管的不锈钢-钢复合板应符合NB/T47002.1一2009,AsTMA283;2012或ASTM 7.3.1 A264,2012,镶基合金-钢复合板应符合 NB/T47002.2一2009或ASTMA265;2012
若 NB/T47002.12009、NB/T47002.22009、ASTMA263:2012、ASTMA264:2012、ASTMA265: 2012有不一致之处由购方与制造商协商确定
用于制造母管的复合板宜采用爆炸复合法,轧制复合法或经购方与制造商协商确定的其他冶金 7.3.2 复合制造工艺
7.3.3在热处理并经校平后应按照NB/T47013.3对复合板逐张进行100%UT,检测基层和覆层界面 结合状态,不锈钢-钢复合板检测结果应符合NB/T47002.1-2009中B1级要求或ASTMA263;2012 AsTM1A264:2012中1级要求镍基合金-钢复合板检测结果应符合NB/T47002.2一2009中1级要 求或AsTMA265;2012中1级要求
经购方与制造商协议,也可采用AUT技术检测复合板结合 状态
7.3.4允许对复合板结合状态未达到7.3.3规定要求的未结合区覆层进行补煤,但复合板覆层拼接煤 缝及焊缝两侧50mm范围内不应补
补炽应按照评定合格的炽接工艺进行,补焊后部位材料的耐腐 蚀性能应不低于母材,补焊后区域应进行UT和PT检验,UT结果应符合7.3.3要求,PT结果应符合 NB/T47013.5一2015中I级要求
同一部位只允许补煤一次
7.3.5复合板基层不应存在拼接焊缝,单张复合板覆层拼接焊缝不得超过一条,且覆层拼接工艺应按 照评定合格的焊接工艺完成,确保覆层拼接焊缝的力学性能和耐腐蚀性能不低于覆层母材要求,且不得 影响基层与覆层之间界面结合质量等级
7.3.6复合板制应依据GB/T 进行剪切结合强度试验,最低剪切结合强度应不低于210MPa
6396 7.3.7制造复合板的材料均应有质量合格证明书,其检验项目应符合相关标准的规定或订货技术要 求,制造商应对复合板进厂后按本标准相应要求进行复验,对具有同一质量保证体系且和复合管件为同 -制造商生产的复合板可不再做人厂复验
复验应满足以下要求 对复合板逐张进行外观、工艺质量、几何尺寸、内覆层界面结合状态100%UT检验; a 按同基层熔炼批、同内覆层熔炼批、同钢级、同规格、同制造工艺和同热处理工艺为一批对复合 b 板进行抽检,每批不多于50张抽检1张,抽检复检项目包括;基层和内覆层化学成分、基层拉 伸性能、基层冲击韧性和内覆层剪切结合强度试验 复合板内外表面不应有铜,铝、锡,铅、锌等低熔点金属污染,耐腐蚀合金层表面不应有铁离子 污染,如果产生,应采用有效的方法进行清除和检验
7.4母管 7.4.1母管除应满足APISpec5LD的要求外,还应满足本标准的要求,两者若有不一致之处,应以最 10
GB/35072一2018 严格的要求执行
7.4.2母管可以是无缝管,也可以是仅有一条熔化金属填充焊缝的直缝接管,内覆层与基层之间应 为冶金复合,母管宜采用以下制造工艺 由满足7.3要求的复合板卷制成型焊接; a b 在无缝钢管或仅有一条熔化金属填充焊缝的直缝焊接钢管内表面堆焊耐腐蚀合金层; 经购方与制造商协商确定的其他冶金复合方式
c 7.4.3 不应采用对接复合管(将两根复合管对接焊在一起)制造母管,也不准许母管基层存在环向 焊缝
7.4,4对复合板制母管应依据GB/T6396进行剪切结合强度试验,最低剪切结合强度应不低于 210MPa,试样宜在远离焊缝的结构连续部位取样
7.4.5除内覆层为堆煤工艺制造的母管外,其他工艺制造的母管在出厂前,应使用能定位缺陷位置的 UT方法按照NB/T47013.3要求对母管逐根进行100%UT,检测母管基层与内覆层界面结合状态,检 测结果应不低于7.3.3规定的相应复合板的要求
7.4.6母管出厂前,对存在焊缝的母管应按照sY/T6423.1一2013要求逐根对所有焊缝进行100% -2013要求进行100%UT,验收等级均为I级 RT以及按照SY/T6423.2 制造复合管件的原材料均应有质量合格证明书,制造商应对母管进厂后按本标准相应要求进行 7.4.7 复验,.对具有同一质疑保证体系且相复合管件为同一制造商生产的母管可不再做人厂 二复验
复验应满 足以下要求 对母管逐根进行外观、工艺质量、几何尺寸、内覆层界面结合状态100%UT(内覆层为堆焊工 a 艺制造的母管除外)和焊缝100%RT; 按同基层熔炼批、同内覆层熔炼批、同钢级、同规格、同制造工艺和同热处理工艺为一批进行抽 b 检,DN<500mm时每批不多于100根抽检1根,DN>500mm时每批不多于50根抽检1根. 抽检复检项目包括;基层和内覆层化学成分,基层母材纵向和横向(若可以取样)拉伸性能以及 焊缝横向(若可以取样)拉伸性能、基层冲击韧性和内覆层剪切结合强度试验(内覆层为堆焊工 艺制造的母管可不做); 母管内外表面不应有铜、铝、锡、铅、锌等低熔点金属污染,耐腐蚀合金层表面不应有铁离子污 染,如果产生,应采用有效的方法进行清除和检验
制造 8 8.1一般规定 8.1.1复合管件基层与内覆层之间应为冶金复合方式,宜采用以下制造工艺 采用满足7.3要求的复合板经冷加工或热加工工艺成型后再焊接; a 采用满足7.4要求的母管经冷加工或热加工工艺成型 b 采用碳钢或低合金钢管件堆焊内覆层的方法制造,钢制管件应符合GB/T12459,GB/T13401 c 或GB/T29168.2要求
8.1.2制造复合管件所采用冷加工或热加工工艺包括弯制、压制拔制、冲压、挤压、焊接或经购方与制 造商协商确定的其他工艺,所采用的工艺,应保证复合管件不产生裂纹和其他影响安全的缺陷,表面外 形应圆滑过渡
8.1.3复合管件在制造、储存和运输过程中,应采取有效的措施防止耐腐蚀合金层表面产生铁离子污 染
如果产生,应采用有效的方法进行清除和检验,并报告购方
1
GB/T35072一2018 8.2焊接 8.2.1复合管件所有焊缝和堆焊(包括返修焊缝)应由考核合格的焊工按照评定合格的焊接工艺完成
制造复合管件所采用的所有焊接工艺规程应满足NB/T47015,焊接工艺评定应按照NB/T47014进 行,焊工考试应按TsSG:Z6002进行
8.2.2根据复合管件公称尺寸和制造方法的不同,允许在壳体上有一条或两条纵向焊缝,对弯头,异径 接头和三通,当DN<450mm时,可有一条纵向焊缝;当DN>450 nmm时,可有两条纵向焊缝
复合管 件焊缝的位置应符合GB/T13401的要求
8.2.3复合管件上的焊缝应为对接焊缝,焊缝的对接坡口尺寸宜符合GB/T985或GB/T986要求,所 有对接焊缝应为全焊透结构,应采用熔化焊工艺,应优先采用自动焊,宜选用双面焊工艺
坡口宜采用 机械加工方法,若采用热切割法应去除坡口表面的氧化皮并打磨平整
8.2.4堆焊应采用冷/热丝TIG焊接或其他热输人量较少的焊接方法,应采用多层堆焊,前后相邻堆焊 层间的搭接长度应不小于每层堆焊层宽度的30%,且焊道的不平度和相邻焊道之间的凹下量都应不大 于0.5mm
堆焊层的厚度应满足6.2.1要求,化学成分应满足7.2要求
8.3热处理 对采用钢制管件进行内表面堆焊耐腐蚀合金层工艺制造的复合管件,成形后的钢制管件应进行 8.3.1 热处理,钢制管件制造商应提供热处理工艺报告,在保证内覆层堆界工艺不影响基层各项性能的前提 下,堆焊后的复合管件可不再进行热处理 8.3.2采用冷成形的复合管件,成形后应进行消除应力的热处理
8.3.3热加工成型的复合管件,应根据材质和加工过程,由购方和制造商协商确定不进行热处理或选 择合适处理工艺
8.3.4热处理炉应至少每年鉴定一次,热电偶每半年鉴定一次
热处理时炉温的温差应控制在士10c 以内
测温时,热电偶可直接和复合管件相连接,或者与复合管件有相同温度的材料相连接
8.4校圆 允许对复合管件端部使用冷校圆,当DN<600mm时,冷校圆时径向永久变形量应不大于1.5%D 或1.5%D,)或8mm中的两者较小值;当DN>600nmm时,冷校圆时径向永久变形量应不大于1.5% D(或1.5%D)或17mm中的两者较小值
不应采用冷扩径方式调整复合管件管端内径
8.5管端 8.5.1复合管件焊端坡口应机加工成形,焊端坡口型式应与相连管线坡口形式一致,坡口形式应按照 GB50251或GB50253和焊接工艺评定结果确定
8.5.2当复合管件设计图或购方对管端坡口未作规定,且复合管件焊端总壁厚(十tn)与相连管道等壁 厚时,当t十tg<22mm时,其坡口型式与尺寸可按图3a)所示加工为V型坡口;当1十tn>22mm时. 其坡口型式与尺寸可按图3b)所示加工为双V型坡口
若内覆层为高镍含量的耐腐蚀合金,焊端坡口 可适当提高斜度;对于基层公称壁厚小于5mm的复合管件,焊端坡口可加工成略有斜边或直边型式; 根据购方要求,可对管端进行堆焊处理,堆焊工艺和堆焊材料由供需双方协商确定
8.5.3当复合管件焊端总壁厚(/十1 1十tn)超过相连接管道壁厚2 及以上时,复合管件焊端宜做外削边 mm 处理,外削边尺寸与坡口结构应由购方与制造商协商确定
8.5.4复合管件距端面100mm范围内的内外焊缝余高均应去除,去除后内外焊道剩余高度应不大于 0.5mm,但不得低于管体表面,焊缝磨削去除时,不得明显伤及管体,且应圆滑过渡
8.5.5根据购方要求,可在6.1所规定复合管件标准尺寸基础上,焊接端直管段的长度增加不小于 12
GB/35072一2018 30 mm
30"士2.5" 10"士I 37.5"土2.5 V型坡口 双V型坡口 a b 说明 D 复合管件端部外径,单位为毫米( mm 复合管件端部名义内径,单位为毫米(mm) -复合管件焊接端坡口内覆层伸出长度,单位为毫米(tmm),宜为2,5mm~3.5mm; 复合管件内覆层公称壁厚,单位为毫米( mm) 复合管件基层公称壁厚,单位为毫米(mnm) '! 图3复合管件焊接坡口示意图 8.6表面处理 复合管件最终检验前应进行表面清理,外表面宜采用钢丸喷砂除锈,内表面宜采用喷玻璃砂除锈
内外表面清理完成后应对耐腐蚀合金内覆层进行酸洗钝化处理,酸洗钝化处理后再用自来水(氯离子含 量低于25mg/L)进行最终清洗
表面清理完成后,内外表面应完全干燥
8.7 工艺评定 复合管件正式生产前,应对不同材质和不同规格的试制复合管件按照附录B进行制造工艺评定 并编制用于复合管件正式生产的制造工艺规程(MPS)
技术要求和检验方法 9.1 般规定 9.1.1试验与检验项目 9.1.1.1检验与试验应在复合管件下线24h后进行
除在试验方法中另有规定外,试样应在室温环境 下进行状态调节
9.1.1.2按照本标准供货的复合管件应进行制造工艺评定和批次检验,检验和试验项目如表4所列,取 样位置和数量宜参照附录C进行
g.1.2检验频次 g.1.2.1在制造工艺评定阶段,不同种类、不同钢级、不同熔炼炉批次的基层和内覆层材料、不同公称直 径、不同制造工艺、不同热处理工艺,不同公称壁厚(包括基层和内覆层)的试制复合管件应各抽取不少 13
GB/T35072一2018 于2根成品复合管件进行MPQT
也可由供需双方协商确定检验频次
g.1.2.2正式生产阶段,同钢级同一熔炼炉批次的母管(包括基层和内覆层)材料、相同制造工艺,相同 热处理工艺、同一公称壁厚(包括基层和内覆层)、同一公称直径的同类复合管件,DN一400nmm时,不 多于100件为一批,DN>400mm时,不多于50件为一批,每批应抽取不少于1件成品复合管件进行检 验
也可由供需双方协商确定检验频次
9.1.3合格性验收与复验 在正式生产批次检验中,若不合格项为化学成分、物理试验或腐蚀试验,由购方选择,可在同一复合 管件上两倍取样复验不合格项,或在同批次复合管件中重新两倍抽样并分别取样复验不合格项,或对该 批复合管件重新进行一次热处理并重新按本标准进行物理试验和腐蚀试验
若上述复验或重新检验合 格,则该批复合管件相应检验项目合格,否则该批复合管件应判为不合格
重新热处理仅允许进行 次
但对重新检验或复验中,因抗拉强度或屈服强度不合格的该批复合管件,允许经设计方同意后降低 压力等级使用
9.2几何尺寸 复合管件应逐根进行几何尺寸检测,几何尺寸及尺寸公差应符合第G章的要求 9.2.1 表4复合管件试验和检验项目汇总表 类型 检验项目 技术要求与检验方法 检验频次 标准尺寸 6.l,6.5.9.2 6.2.1,6.5,9.2 基层壁厚 6.2.2,6.5,9.2 内覆层壁厚 内径 6.3,6.5,9.2 几何尺寸 椭圆度 6.4,6.5,9.2 复合管件平面度 6.5,9,2 6.5.9.2 端面垂直度 管端 8.5 0和T 7.1,9.3 基层 化学成分 内覆层 O和T 7.2,9.3 拉伸性能 0和T 7.1,9.4 冲击韧性 0和T 7.l,9.5 导向弯曲试验 0和T 9,6 物理试验 全截面维氏硬度 o和T 9.7 表面硬度 Q和 T 9.8 和T 9,9 焊缝宏观检查与金相组织检验 内覆层剪切结合强度 O和T 9,.10 晶间腐蚀试验 0和T 9.ll 腐蚀试验 基层材料腐蚀试验 协商 9.12,参见附录D 内覆层材料腐蚀试验 0和T 9.13,附录A 14
GB/35072一2018 表4(续》 类型 检验项目 检验频次 技术要求与检验方法 外表面(M或PT 10.2" 内表面(PT 10.2 基层与内覆层界面结合状态(UT 10.3 NDT 焊缝(UT和RT 10.3 外弧侧横向裂纹(UT 10,3 管蹦分层UT和T 10.4 10.5 管淄剩磁 外观检查 表面质量、缺欠和缺陷处理 章 第11 静水压试验 协商 9,14 设计验证试验 9.15 -正式生产阶段,进行批次检验时,按照9.1.2.2要求抽取1根成品复合管件
-制造工艺评定阶段和正式生产阶段,对每根成品复合管件要求 正式生产阶段,进行批次检验时,每批应抽3%且不少于2根成品复合管件
Q 制造工艺评定阶段,按照9,1.2.1要求抽取不少于2根成品复合管件
复合管件壁厚检验应满足以下要求 9.2.2 a 对于正式生产阶段每根复合管件,基层壁厚宜依据ASTME797采用手动超声脉冲回波法测量,内 覆层壁厚宜依据ASTMB499采用电磁法测量,每个部位应至少均匀测量3点,测量部位应包括 三通的主管与支管过渡区域,主管中心线处以及主管底部 1) 弯头外弧侧内狐侧以及中心线(中性区)处; 2 3 异径接头大头,小头和过渡部位(若有); 4)管帽的顶部和端部
b 在制造工艺评定和正式生产批次检验中,应采用金相法对基层壁厚和内覆层壁厚进行检测 检测部位至少应包括9.2.2a)所列部位
9.2.3对复合管件距离管端50mm范围的内径应使用环规、卡规或光学测量仪器进行检测,检测结果 应满足6.3
9.2.4端面垂直度、复合管件平面度的检测方法可依据sY/T5257进行
9.3化学成分 9.3.1成品复合管件的基层化学成分分析应满足7.1要求,内覆层的化学成分应满足7.2要求
由购方选择,用于化学分析的试样可取自成品复合管件或母管或复合板
对于直缝焊接复合管 9.3.2 件或母管,基层和内覆层母材的取样位置应与焊缝至少相隔90",内覆层媒缝化学分析试样应取自内覆 层焊缝中心 9.3.3堆焊层的化学成分分析试样应取自堆焊层中间,即距表面1.0mm以下,距离熔合线1.0mm以 上,需分析的元素应包括但不限于c,Mn,Cr、,Ni、Mo,P,S和Fe,并应符合7.2要求,还应满足元素Cr、 Ni,Mo成分的测量值不应低于填充金属成分的90%,且元素Fe的稀释率不应超过5%
9.3.4与化学成分分析有关的方法和过程应按照AsTMA751或ASTME353执行
g.4拉伸性能 g.4.1成品复合管件基层的拉伸性能应满足7.1要求
15
GB/T35072一2018 g.4.2基层材料的拉伸试验宜参照附录C推荐位置取样,母材取横向和/或纵向拉伸试样,进行材料 R,Ro.和伸长率性能指标检测,焊缝取横向拉伸试样,进行R性能指标检测
若管件尺寸不足以提 供上述位置拉伸试样,则由购方选择,试样可取自制造管件的母管、复合板、钢制管件(仅对内覆层堆焊 工艺制造的管件)或者不要求进行该位置拉伸试验
g.4.3拉伸试样可采用AP ec5L:2012中规定的板状或圆棒试样,试样上的耐腐蚀合金层应予以清 Sp 除,焊缝应磨平,拉伸试验报告应注明试样的类型、规格以及取样位置
g.44常温下拉伸试验应按照GB/T228.1和GB/T17600.1的规定进行
如果最高设计温度超过 C,应依据GB/T228.2规定的方法对基层材料进行高温拉伸试验,合格性判据由购方和制造商协 100 商确定 9.4.5本标准只对基层材料的拉伸性能作了规定,购方和制造商也可协商确定耐腐蚀合金层及其与基 层复合后的力学性能
9.5cVN冲击韧性 9.5.1成品复合管件基层材料的CVN冲击试验,宜参照附录C推荐位置取样,试样上的耐腐蚀合金层 应在试验前清除,每组冲击试样应由3个相邻的毛坯样品加工而成,并且是从未展平的同一试块上 取样
9.5.2CVN冲击试样应符合GB/T229的规定,缺口的轴线应垂直于管件表面,如果管件尺寸允许,应 优先选用标准横向全尺寸试样,其次采用较小尺寸的10mm×7.5mm或10mm×5.0mm的横向试 样;若无法取得横向试样,依次采用标准尺寸或宽度不小于7.5mm,5.0mm的较小尺寸纵向试样
若 管件尺寸不足以提供最小宽度为5.0mm的纵向试样,则不要求进行CVN冲击试验
9.5.3正常情况下,爆缝中心和HAZ的cVN冲击试样缺口位置应如图4所示,当存在焊偏时,焊缝及 HAZ上截取的试样的刻槽轴线应如图5所示
焊缝试样的刻槽轴线应位于外焊道中心线上或尽可能 靠近该中心线,HAZ试样的刻槽轴线应尽可能靠近外焊道边缘
每个试样应在开缺口之前,应通过腐 蚀方法确定合适的开缺口位置
说明 HAZ冲击试样缺口位置-试样上表而与外媒道熔合线交界; CVN冲击试样缺口中心线; -焊缝金属冲击试样缺口位置-外焊道中心 图4CVN试样在悍缝中心和HAz取样位置 16
GB/35072一2018 说明: 焊偏量 -HAZ冲击试样缺口位置,偏向内焊道一侧; -焊缝金属冲击试样缺口位置,位于外焊道中心 图5存在焊偏时CVN试样在悍缝和HA乙取样位置 9.5.4cVN冲击试验应依据GB/T229进行,除非协议,cVN冲击试验温度宜取-20C或最低设计 温度
9.5.5除非协议,成品复合管件的基层材料(母材与焊缝)在试验温度下CVN冲击吸收能应满足如下 要求 对于L245/BL485/X70钢级横向全尺寸标准试样,最小平均值不低于40J,单个试样最小值 a 不低于30J,并报告剪切面积数据; 对于纵向试样,最小平均值和单个试样最小值应不低于相应横向试样规定值的1.5倍 b mm×7.5mm 1或10mm×5.0mm 采用较小尺寸的10n 试样,其冲击吸收能要求值分别为全尺 寸规定值的0.75和0.5; d 若选用其他碳钢或低合金钢,由购方与制造商协商确定验收指标
9.6导向弯曲试验 9.6.1带有焊缝的复合管件的导向弯曲试验宜参照附录C推荐位置取样,取一个面弯和背弯试样
试 样应按照GB/T232制备,复合管件总壁厚(t十t)不大于19mm时,可经冷压平作成全厚度平板试样; 若复合管件壁厚(十tw)大于19mm,可从完全受拉面的反面加工成厚度18mm的矩形横截面试样 试样上不应有补焊焊缝,焊缝两面余高应去除,背弯试样的耐腐蚀合金层应保留
9.6.2试验方法依据APIn pec5L;2012进行,弯模几何尺寸应符合APISpee5L;2012对与管件基层 同钢级管材的规定,且弯模直径不超过试样厚度的6倍
面弯、背弯试样在弯模内弯曲约180",焊缝位 于试样中部
g.6.3导向弯曲试验结果满足以下要求为合格;试样不应完全断裂;在焊缝、HAZ和母材处,不应出现 任何长度大于3.2mm的裂纹;起源于试样边缘的裂纹,在任何方向上裂纹长度应不大于6.4mm,但由 于夹渣或缺陷引起的边缘开裂,该试样视为不合格,应重新取样进行试验
9.7全截面维氏硬度 9.7.1复合管件的全截面硬度检测试验宜参照附录C取样,对于有纵向焊缝的管件,焊缝横截面硬度 检测压痕位置如图6a)所示
除非协议,未受到热影响的母材硬度压痕间距应为1mm,HAZ和焊缝 的硬度压痕间距应为0.75mm,距熔合线最近的高温HAZ硬度点离熔合线的距离不应超过0.5 mm
17
GB/T35072一2018 9.7.2对于采用堆焊工艺制造的复合管件,全截面硬度检测点如图6b)所示,除非协议,硬度压痕间距 应为1mm g.7.3全截面硬度检测依据GB/T4340.1要求进行维氏10kg硬度试验
基层及耐腐蚀合金层维氏硬 度值应符合表5要求
基层" 内覆层 带有焊缝的复合管件 基层 内覆层 堆爆工艺制造的复合管件 b 说明: 线1内覆层一侧距离基层与内覆层界面熔合线w,w=1.0mm,十0.0,一0.5mmt 线2 基层一侧距离基层与内覆层界面熔合线W,w=1.0mm,0.0,一0.5mm; 线3 基层中间壁厚处,w为基层壁厚的二分之一; 线4 距离基层外表面w,W=1.5mm,十0.5mm,一-0.0; 线5 距离堆煤层外表面W.,W;=1.5mm,十0.0,一0.5mm
图6复合管件全截面硬度检验压痕位置 18
GB/35072一2018 表5复合管件全截面硬度检测要求 材料类型 硬度要求 L360/X52及其以下钢级不超过240HVm,L.390/X56及 基层母材和焊缝(碳钢或低合金钢) 其以上钢级不超过248HVn,另有协议除外 内覆层母材和炽缝(奥氏体不锈钢 不超过300HVo 内覆层母材和焊缝[镍基合金,如825合金(L.c2242),625 不超过345HVm 合金(LC2262力] 注;不锈钢和有色金属维氏硬度与其他硬度的转换系数和与碳钢使用的系数不同
.8表面硬度 9.8.1每根成品复合管件基层外表面应采用便携式里氏硬度计进行宏观硬度检测,检测方法按照 GB/T17394.1进行,合格性验收指标由制造商与购方协商确定
9.8.2对于正式生产阶段的复合管件,每批应抽3%且不少于2根进行表面硬度检测,每个位置取 个5个等间距硬度点的读数为平均值,检测结果若有1根不合格,应加倍检验,若仍有1根不合格 33 应逐根检测
表面硬度的测量部位应包括 三通的主管与支管过渡区域、主管中心线处以及主管底部 a b)弯头外弧侧、内弧侧以及中心线(中性区)处; 异径接头大头、小头和过渡部位(若有); ce 焊缝及其HAZ; d 管帽的顶部和端部 e 9.8.3用于MPs的试制复合管件,在各检测部位上不少于3个点读数的平均值可被作为正式批量生 产复合管件制定表面硬度检测合格性验收指标的依据 g.9焊缝宏观检查和金相组织检验 9.9.1对带有焊缝的复合管件应采用宏观照相对内外焊缝横向截面进行检查,取样位置宜参照附录C 进行,试样横截面应包括焊缝两侧的焊接熔合线、HAZ及母材,且应抛光至14m,酸蚀后使用光学显微 镜(放大10倍或按协议要求)进行检查,焊缝区域不应存在缺陷,内外焊道应充分熔合,焊缝的几何尺寸 和工艺缺陷应符合表6要求
9.9.2在制造工艺评定和正式生产批次检验中,应在不低于200倍放大条件下对复合管件母材和焊缝 的横截面进行金相检验,金相检验部位与全截面硬度检测部位一致,金相试样按AsTME340的规定制 备,晶粒度按GB/T6394进行评定,夹杂物等级按GB/T10561进行评定
g.9.3对于有纵向焊缝的成品复合管件,弯曲段不同部位的母材焊缝和HAZ的显微组织应基本 致,无有害相,基层和内覆层的平均晶粒度应不低于6级
表6焊缝金相检验验收条件 缺陷类型 纵向焊缝 堆焊层 焊缝熔合情况 充分熔合 充分熔合 基管的焊缝咬边 <0.4mm 内覆层的焊缝咬边 0.4mm <0.4mm 19
GB/T35072一2018 表6续) 缺陷类 纵向焊缝 堆焊层 型 基层纵向焊缝错边量 <1.5mm 耐腐蚀合金层纵向焊缝错边 S0.5mm 耐腐蚀合金层焊缝的连续性 100%连续 裂纹 不准许 不准许 焊偏 0.15tB且<3.0mm 交互熔深 mm 2mm 外焊缝高度 3mm 内覆层焊缝余高 0.5mm 有害金属间相 不准许 不准许 S31603奥氏体不锈钢媒后铁素体含量点计数法一ASTME562) 5%13% 5%13% 9.10内覆层剪切结合强度 9.10.1对复合板制管件应依据GB/T6396进行剪切结合强度试验,最低剪切结合强度应不低于 200MPa
9.10.2试样宜在远离焊缝、结构连续部位取样,具体取样位置宜参照附录C进行
9.11晶间腐蚀试验 g.11.1复合管件内覆层应进行晶间腐蚀试验,若内覆层为奥氏体不锈钢,宜依照GB/T43342008方 法B或方法E进行晶间腐蚀试验,若内覆层为镍基合金,宜依照GB/T4334一2008方法B或方法C进 行晶间腐蚀试验
经购方和制造商协商,也可选用其他试验方法 9.11.2晶间腐蚀试样应由耐腐蚀合金层上截取,具体取样位置宜参照附录C进行,如采用火焰切剐试 样,应对试样的切割边缘进行机械加工或修磨
除非需压平,试样应在原始状态下进行试验
试样上存 在的任何刻痕,应使用粒度为120的无铁氧化铝磨料采用机械方法去除,或使用化学方法去除
9.11.3若采用GB/T4334一2008方法E,试样经腐蚀后应在不低于10倍放大条件下检查弯曲试样是 否存在裂纹,如果对结果有疑问,应将试样放在150倍一500倍显微镜下进行检查,不出现裂纹为合格
g.11.4若采用GB/T4334一2008方法B或方法C,最低验收标准由制造商与购方协商确定
9.12基层材料腐蚀试验 对于输送含有HS腐蚀性介质的复合管件,若输送介质属于酸性环境,应由购方与制造厂协议确 定是否需要在制造工艺评定和正式生产批次检验中,对复合管件基层母材和焊缝进行HIC试验和SsC 试验,腐蚀评价方法宜参照附录D进行
9.13内覆层材料腐蚀试验 在制造工艺评定和正式生产批次检验中,应根据内覆层材料类型和使用工况环境对内覆层进行耐 腐蚀性能评价,腐蚀评价方法应依据附录A进行
g.14静水压试验 g.14.1对正式生产的复合管件,出厂前不要求在制造单位进行水压试验,但制造商应承担复合管件在 20
GB/35072一2018 现场安装后符合静水压试验要求的责任
g.14.2若购方要求进行静水压试验,试验方法宜按照APISpee5L;2012或双方协议确定
静水压试 验的验收要求为:试验压力为复合管件设计压力的150%,稳压时间不少于10s,试样不得有破裂和渗 漏,或有碍于使用的其他损害
9.15设计验证试验 9.15.1 一般要求 在制造工艺评定阶段,制造商应对复合管件按照9.15.29.15.7进行设计验证试验
设计验证试 验方法为爆破试验
制造商的产品档案中应存有设计验证试验过程记录或已有成功验证试验的记录资 料,并随产品一并提供给购方
9.15.2试样 应取2根或3根复合管件用于爆破试验,选作试验的复合管件,应保留耐腐蚀合金层,并按照本标 准对其进行几何尺寸、表面质量和NDT检验,检验结果应符合本标准要求,另外检验报告中应标明复 合管件材料类型、几何尺寸、强度等级、炉批号及热处理状态
9.15.3试验组件 9.15.3.1 试验组件中的每一件管帽、有缝或无缝直管短节,其壁厚应与试验复合管件的壁厚相匹配, 理论计算爆破强度应不小于试验复合管件计算爆破强度的105%
9.15.3.2煤接过程中,试验管件、直管短节和管帽之间对接煤接时,距离管端50m范围内复合管件 内径应与相连直管短节和管帽内径一致,端部的内壁错边量应不大于1.5mm
直管短节的长度至少应 为直管短节外径的一倍,当直管短节的长度超过短节外径时,可以对短节采取外补强加固措施,确保直 管短节不会提前失效
9.15.4流体介质 试验用介质宜用自来水,水中的氯离子的含量应低于25mg/L
9.15.5验证试验强度计算 复合管件水压爆破试验应按基层材料规格与钢级进行,验证试验的强度计算应按式(2)确定 P=2o,t/D 式中 复合管件验证试验计算最小强度,单位为兆帕(MPa) 复合管件基层材料的实际抗拉强度(当管件基层材料的实际拉伸强度小于连接管的名义 o 最小抗拉强度时,按连接管的名义最小抗拉强度计算),单位为兆帕(MPa); 与复合管件相连接的管子的公称壁厚或复合钢管的基层公称壁厚,单位为毫米(mm); 设计验证试验系数,若试验次数为2,内=1.05;若试验次数为3,夕=1; 与复合管件相连接管子的名义外径,单位为毫米(mm)
D 9.15.6试验程序 g.15.6.1试验组件组装及检测 复合管件爆破试验组件焊接和组装完成后,应对全部试验组件的焊缝按照NB/T47013.2一2015 进行100%RT,验收等级为I级,检验合格后再向试验组件内注水进行爆破试验
21
GB/T35072一2018 g.15.6.2试验方法与要求 试验泵的输出能力应是按照式(2)计算的验证压力的1.25倍,压力测试范围应为计算验证压力或 规定压力的1.5倍一4倍,压力测量设备应在6个月校准期内
水压试验过程中应连续增压,升压速度不超过2.75MPa/min
当所有试件的爆破试验结果满足下 列条件之一时,爆破试验判定为成功 试件的爆破压力不低于式(2)的计算爆破压力; ? D)试件的最终试验压力达到式(2)的计算爆破压力的105%时,试件未爆破
9.15.7试验结果的可用性 9.15.7.1 总则 按本标准要求进行的设计验证试验,其合格的试验结果可以验证以下范围内其他同类复合管件
9.15.7.2材料强度等级 由不同强度等级碳钢或低合金钢作为基层材料制成的同类复合管件,其耐压能力与基层材料的拉 伸强度成正比
因此只需对一个强度等级的复合管件进行试验即可验证其他几何结构相同或相似、且 为相同制造工艺的同类复合管件
9.15.7.3几何尺寸 个合格的试验验证复合管件可代表以下所述范围内具有相似几何结构的复合管件 公称直径IDN为试脸复合管件DN的05倍一?倍的同类复合管件 a) b) 基层壁厚与外径比值为试验管件基层壁厚与外径比值0.5倍一3倍的同类复合管件; 较短曲率半径的试验复合弯头,可以验证符合本标准的较长曲率半径复合弯头
c 10 无损检测 0.1一般要求 0.1.1NDT应在复合管件最终热处理完成后24h后进行,NDT前,应采用喷沙、打磨等方法去除复 合管件表面的氧化皮及其他污物,并保证其表面质量可满足NDT要求
0.1.2NDT人员应按GB/T94452015或其他等效标准进行评定,上次评定合格的检测人员如从事 该项NDT工作未超过12个月,其资质应重新评定
显示结果的评定应在I、级人员的监督下由 I级人员进行,或直接由I、级人员评定
0.2表面检测 10.2.1应对每件复合管件的外表面按照NB/T47013.4一2015进行100%MT或者按照 NB/T47013.52015进行100%PT,验收等级均为I级
检测发现的缺陷应进行修磨处理并圆滑过 渡
修磨部位应进行100%MT或100%PT,确认缺陷已经完全消除后,按照9.2.2a)采用手动超声脉 冲回波法对修磨部位测厚,最小剩余壁厚应满足6.2.1要求
0.2.2复合管件内表面应按NB/T47013.5一2015要求进行100%PT,验收等级为I级
若经购方 与制造商协商,复合管件内表面也可按照NB/T47013.7进行目视检测,对于不便于直接目视位置应采 用内窥镜或协议确定的其他计算机成像技术进行检测,内表面不应有裂纹,坑点及其他缺陷存在
22
GB/35072一2018 0.3管体和焊缝 10.3.1所有复合管件应按照NB/T47013.3要求逐根进行100%UT,检测基层和内覆层界面结合状 态,检测结果应不低于7.3.3规定的复合板或7.4.5规定的母管相应要求
10.32对存在煤缝的复合管件应逐根对所有焊缝按照sYTet28.1一2013要求进行100%RT以及 -2013要求进行100%UT,验收等级均为I级
按照SY/T6423.2一 应采用手动UT对复合管件的弯曲段外弧侧进行横向裂纹缺陷检测,检测结果应满足 10.3.3 sY/T5257要求
10.4管端 10.4.1每根复合管件距离管端50nmm范围内,应按照sY/T6423.4采用手动UT进行分层检查
10.4.2对每根复合管件整个坡口面应采用PT进行分层检查,PT方法宜按sY/T4109进行
0.5管端剩磁 复合管件出厂前,应逐根按照APSpec5L规定测量并记录成品复合管件的管端剩磁,管端剩磁 强度应不超过15Gs,如大于15Gs,应对管端重新按照APISpee5L进行消磁处理,直至满足本标准 要求
表面质量、缺欠和缺陷处理 1.1表面质量 出厂前应逐根对复合管件表面质量按照NB/T47013.7进行目视检测,在目视检测前复合管件外 表面应达到GB/T8923.1一2011所规定的Sa2级
复合管件表面质量应符合下列要求 内、外表面应清洁,不得有污垢、油脂、油漆、氧化皮等外来物; a b)内、外表面应光滑平整,不得有裂纹、硬点,电弧烧伤、过热、过烧等缺陷存在,焊缝不得有未熔 合,未焊透、咬边等缺陷,基层表面不得有深度超过基层公称壁厚5%且深度大于0.8mm的凿 痕、折叠、分层等缺陷存在,内覆层表面不得有凿痕、折叠、凹坑和机械划痕等缺陷存在 内、外焊缝余高应符合表6的规定
1.2缺欠和缺陷处理 11.2.1复合管件内、外表面存在的尖缺口、凿痕和其他能引起较大应力集中的划痕应修磨并圆滑过 渡,修磨后的部位应进行100%MT或100%PT以确认缺陷已经完全消除
平滑,孤立的圆底凹痕可 以不修磨
焊缝打磨后,焊缝表面应不低于母材表面
耐腐蚀合金内覆层的修磨应采用专用的砂轮片, 以防止耐腐蚀合金被污染
修磨后应对修磨部位按照9.2.2a)要求测厚,最小剩余壁厚应满足6.2 要求
1.2.2复合管件上任何裂纹、过烧、过热或硬点判定为不合格,不准许修磨或焊接修补;不准许采用锤 击或补炽修补凹痕;基层母材上深度超过12%基层公称壁厚或大于1.6mm的凹坑或机械划痕判定为 不合格,不准许修补
11.2.3复合管件的修补焊接应满足以下要求 未达到10.3.1要求的内覆层未结合区允许进行焊接修补,修复焊接前应采用打磨方法将未结 a 合缺陷彻底清除掉,并进行PT检验以确认缺陷已清除,对补焊后区域应进行UT和PT检验, UT结果应符合7.3.3要求,PT结果应符合NB/T47013.5一2015中I级要求; b 除非协议,距管端200mm以内的耐腐蚀合金层纵向焊缝不准许进行焊接修补,单根复合管件 23
GB/T35072一2018 耐腐蚀合金层纵向焊缝的焊接修补点应不多于3处,单个修补点长度应不小于50mm,修补 焊缝相邻间距应不小于100mm,且修补焊缝总长度应不大于复合管件焊缝总长度的5%;煤 缝补焊后应进行PT检验且应符合NB/T47013.5一2015中级要求; 一般不准许对复合管件基层母材任何部分进行焊接修补,经购方同意,对基层焊缝非裂纹缺陷 允许在同一位置采用一次焊接修补,修补后的焊缝应进行UT和RT检验,并满足10.3.2 要求: d 应由有资质的焊工按经评定合格的煤接工艺进行补煤,并作出补焊记录,补焊记录应附在产品 质量证明书中 同一缺陷位置最多只能有一次焊接修补; 内覆层修补焊接后部位的耐腐蚀性能应不低于母材,内覆层各部位焊接修补部位的总面积应 不大于单根复合管件内覆层总面积的1% 静水压试验后不准许任何焊接修补
8 标志 12 12.1标志方法 应采用模版喷涂法进行标记,字体与颜色应易于辨认,标志应清楚和耐久
不应采用冷,热字冲模 锤印标志
12.2标志位置 复合管件尺寸允许情况下,应从距管端100mm处开始,在复合管件内,外表面做标志,外表面标志 应在复合管件的侧面中心线附近,且易于观察的部位,标志应避开高应力区和焊缝部位
12.3标志内容 在复合管件上按顺序清楚地标明以下内容: 制造厂名或商标; a 公称尺寸,包括外径系列,外径为I系列时,不单独标记;外径为系列时,应进行标记 b 壁厚,包括基层壁厚或壁厚等级与内覆层的公称壁厚; c 基层与内覆层材料牌号; 产品代号(见表1): e fD 产品编号,每根复合管件应标识唯一编号以便于追溯,如复合管件尺寸过小无法满足,可经购 方与制造商协商采用其他标识方法; 本标准编号
日 当复合管件规格不能对上述所列内容进行完整标志,可逆上述顺序省略识别标志或采用标签标志 12.4标志示例 示例1:公称尺寸DN100,外径为I系列,基层壁厚等级Sch40,基体材料牌号为X60,耐腐蚀合金内覆层材料牌号为 316L..内覆层公称壁厚为2.5mm,90"短半径弯头,其标志为 制造商名称或商标DN100-Seh40(2.5)-x60/316L-90E(S)产品编号GB/T35072 示例2;公称尺寸DN100×80、外径为系列基层壁厚等级Sch80将基层材料牌号为X52、内覆层材料牌号为UNS N8825,公称壁厚为2.5mm,同心异径接头的标志为 制造商名称或商标DN100×80ISch802.5)-X52/NO8825-R(C产品编号(GB/T35072 示例3;公称尺寸DNI00,外径为I系列,基层壁厚为5mm,材料牌号为16MnR,内覆层材料牌号为UNss31603 24
GB/35072一2018 公称壁厚为3mm,90"短半径弯头,其标志为 制造商名称或商标DNI00-5(3)-16MnR/S31603-90E(S)产品编号GB/T35072 3运输与防护 13.1装运前,复合管件内、外表面应保持清洁与干燥,可采用防锈剂防止坡口或管端产生锈蚀,应采用 管端保护器或其他保护装置对管端进行有效保护,避免搬运和运输过程中对成型坡口和复合管件内部 造成机械损伤和污染
应确保复合管件在包装、搬运、运输和储存过程中免受机械损伤和环境侵蚀,确保复合管件内、外 13.2 表面免受铜、铝、锡、铅、锌等低熔点金属污染,应避免铁离子污染耐腐蚀合金层表面,如果产生,应采用 有效的方法进行清除和检验
13.3制造商应以书面的形式提交复合管件包装、搬运、运输和储存方法说明或图纸供购方审查,装运 至少应符合公路、铁路或海路运输的要求
14文件 14.1按规定应进行的所有试验和检验,均应在交货前完成,并向购方提供完整的检测文件 14.2按本标准生产的复合管件,每批均应有产品质量合格证明书,质量合格证明书至少应包括 制造商名称与制造日期 a 产品名称、规格、制造标准号 b 原材料检验报告; c 产品外形尺寸检测报告; d 产品化学成分和物理试验报告, 内覆层材料腐蚀试验报告; fD 产品NDT报告; g h) 热处理报告; 由购方指定的其他文件
' 25
GB/T35072一2018 附 录 A 规范性附录) 内覆层材料腐蚀试验方法 A.1一般要求 复合管件内覆层材料腐蚀试验包括内覆层母材和焊缝或耐腐蚀合金堆焊层的SSC和/或SCC试 验、失重腐蚀和点腐蚀试验
A.2SSC/ScC试验 A.2.1一般要求 根据复合管件预期输送流体工况环境,由购方选择,可采取以下三种途径其中一种评价内覆层材料 的ssc/SCC性能 如果复合管件内覆层材质满足ISO15156-3;2015附录A要求,可不进行SsC/scC试验评价
a so15156-3;2015附录A给出了耐腐蚀合金材料不发生ssC/scC允许的冶金状态、Hs分 压、温度、氯离子浓度和元素硫的环境限制
允许基于满意的现场使用经验的评定,该评定应遵循1so15156-1的规定
现场使用经验评 b 定应满足如下要求: 耐腐蚀合金材料的描述应包括但不限于如下信息化学成分、制造方法、产品形式、强度 硬度、冷加工、热处理状态和微观组织
复合管件的内覆层应与提供的现场经验所使用材 料信息相一致 已获得经验的使用环境描述应包括但不限于如下要求;总压、,CO分压,H,S分压、pH 值、溶解的氯化物或其他卤化物浓度,元素硫或其他氧化物浓度、温度、电偶效应、应力状 态和材料与介质接触时间,以及由于环境控制措施失效造成的材质接触环境条件
设备现场连续成功运行应不少于2a,且应包括现场使用之后由第三方对设备全面检查评 估结果
复合管件预期使用环境苛刻程度不能超过现场经验所提供的环境条件
4 5 现场满意的应用经验可由设备使用方或复合管件制造方提供,但应获得购方和管线设计 方认可,耐腐蚀合金材料现场使用经验应有完整的文件记载
如果A.2.1中a)和b)无法满足要求,应依据A.2.2一A.2.7规定的方法进行试验
A.2.2试验方法 依据GB/T15970.2采用四点弯曲法对内覆层进行耐ssC/SCC试验
试样加载应力为材料的 00%Rw,Rw,表示屈服强度)
若征得购买方同意并有证明文件,可选择较低的加载应力
对于焊接试样,缝应位于试样中心部位,通常用母材的屈服强度来确定试验应力,当焊缝区的屈 服强度低于母材的屈服强度时,应采用焊接区的屈服强度来确定试验应力
A.2.3试验环境 SsC/sCC试验应在复合管件输送介质模拟环境中进行,通常采用高压釜实现高压或高温高压输送 26
石油天然气工业用耐腐蚀合金复合管件GB/T35072-2018
作为石油天然气工业中不可或缺的一部分,耐腐蚀管道的使用对于保障生产和环境保护至关重要。而在各类耐腐蚀管道中,耐腐蚀合金复合管件因具有良好的抗腐蚀性、耐高温性以及优异的机械性能而备受青睐。 GB/T35072-2018是我国针对石油天然气工业用耐腐蚀合金复合管件制定的标准,该标准主要包括以下内容: 1.耐腐蚀合金复合管件的分类、符号和名称 2.材料选型和表面处理 3.制造技术和工艺要求 4.质量检验和试验方法 5.安装与使用 该标准的发布,对于规范石油天然气工业用耐腐蚀合金复合管件的生产、使用和管理具有重要意义。在材料选型方面,标准明确了不同种类的耐腐蚀合金复合管件应选用的材料,并要求其应满足相应的化学成分、力学性能、抗腐蚀性等技术指标。 在制造工艺方面,标准要求生产企业应采取合理的制造工艺,确保耐腐蚀合金复合管件的质量可靠,并应进行相应的质量检验和试验,以确保产品符合规定的技术要求。 在安装与使用方面,标准强调了安装质量的重要性,要求在安装过程中应注意防止管件表面损伤、避免管道变形、保证密封性等。同时,在使用过程中,应根据实际情况合理选择管件类型和规格,以确保其正常运行和长期使用。 总之,GB/T35072-2018标准的发布,将进一步促进石油天然气工业用耐腐蚀合金复合管件的规范化和标准化,提高生产效率和安全性。在未来的发展中,我们相信这一标准将会在石油天然气工业中发挥越来越重要的作用。