GB/T35449-2017
自动定量装车系统
Automaticquantitativeloadingvehiclesystem
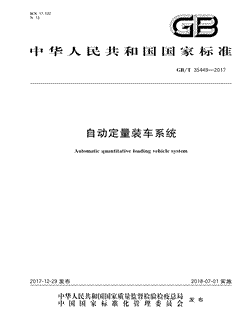
- 中国标准分类号(CCS)N13
- 国际标准分类号(ICS)17.100
- 实施日期2018-07-01
- 文件格式PDF
- 文本页数26页
- 文件大小1.64M
以图片形式预览自动定量装车系统
自动定量装车系统
国家标准 GB/T35449一2017 自动定量装车系统 Automaticquantitativeloadingvehiclesystem 2017-12-29发布 2018-07-01实施 中华人民共利国国家质量监督检验检疙总局 发布 国家标准化管理委员会国家标准
GB/35449一2017 目 次 前言 范围 2 规范性引用文件 术语和定义、符号 3.1术语和定义 3.2符号 产品型号与规格 基本结构型式 4 4." 型号 4.3规格 5 计量要求 5.l准确度等级 5.2误差范围 5.3分度值d、累计分度值d .!静态称量的最大允许误差 5.5最小秤量(Min) 5.6重复性 5.7 影响因子(称重装置 5.8电子衡器的要求 技术要求 6.1操作的适用性 6.2操作的安全性 6.3机械设备 6.4动力系统 6.5电气与控制系统 6.6称量系统 6.7其他 6.8置零装置 6.9作为控制衡器使用的功能 6.10机械装置的制造 试验方法 l0 7.1单次装料质量的确定 10 7.2物料试验的实施 10 7.3装料次数 10 7.4物料的试验方法 1l 7.5试验装料的质量
GB/T35449一2017 7.6动力系统试验 7.7电气与控制系统试验 8 检验规则 8.1型式检验 8.2出厂检验 12 标志,包装、运输和贮存 12 9.1标志 13 9.2包装 13 9.3运输 13 9.4贮存 附录A规范性附录自动定量装车系统试验方法 I
GB/35449一2017 前 言 本标准按照GB/T1.1一2009给出的规则起草
本标准参照国际建议OIMLR107-1:2007《非连续累计自动衡器》和OIMLR61-1:2004《重力式自 动装料衡器》制定,主要内容包括 -准确度等级采用OIML
R107《非连续累计自动衡器见5.1); 最大允许误差采用OIML.RI07《非连续累计自动衡器见5.2) -最大允许预设值误差参照OIMLR61《重力式自动装料衡器见5.2); 累计分度值采用OIMLR107(《非连续累计自动衡器见5.3); -最小秤量采用OIMIR61《重力式自动装料衡器见5.5); 技术要求参照oMLR107飞非连续累计自动衡器(见6.6- 6.8); 物料的试验方法参照OIMLR61《重力式自动装料衡器见7.4)
本标准由轻工业联合会提出
本标准由全国衡器标准化技术委员会(SAc/TC97)归口
本标准负责起草单位;山东博润工业技术股份有限公司
本标准参加起草单位;山东省计量科学研究院、天地科技股份有限公司、山东金钟科技集团股份有 限公司北京高登衡器有限公司
本标准主要起草人;孙世军、鲁新光,谢新兵、席启明、范韶辰、张涛
GB/35449一2017 自动定量装车系统 范围 本标准规定了自动定量装车系统(以下简称装车系统)的术语和定义,产品型号,计量要求,技术要 求,试验方法,检验规则及标志、包装、运输和贮存
本标准适用于非粘连性散装物料(如煤炭)的火车、汽车装车系统
本标准所指的装车系统是一种可按预设值顺序表,在车辆(火车/汽车)行进过程中完成散料物料分 离、称量、装料和累计的自动衡器
规范性引用文件 下列文件对于本文件的应用是必不可少的
凡是注日期的引用文件,仅注日期的版本适用于本文 件
凡是不注日期的引用文件,其最新版本(包括所有的修改单)适用于本文件
GB/T191包装储运图示标志 GB/T3766液压传动系统及其元件的通用规则和安全要求 GB/T4167砝码 GB5226.1 机械电气安全机械电气设备第1部分;通用技术条件 2008称重传感器 GB/T7551 GB/T7724电子称重仪表 GB/T7932气动系统通用技术条件 GB/T9969工业产品使用说明书总则 GB/T13384机电产品包装通用技术条件 GB14249.1电子衡器安全要求 GB/T14250衡器术语 GB/T15395电子设备机柜通用技术条件 GB/T23111-2008非自动衡器 GB/T26389衡器产品型号编制方法 1588.1轻工机械焊接件通用技术条件 /T QB/ QB/T1588.2轻工机械切削加工件通用技术条件 QB/T1588.3轻工机械装配通用技术条件 QB/T1588.4!轻工机械涂漆通用技术条件 术语和定义、符号 3.1术语和定义 GB/T14250界定的以及下列术语和定义适用于本文件
3.1.1 装料质量oadingmass 根据待装车厢的额定装料质量设定单个或多个装车目标值,装车系统通过自动控制装置,将目标值
GB/T35449一2017 要求的物料装人车厢内,装人车厢内的实际物料显示质量即为装料质量 3.1.2 单次装料singleloading 装车系统单次或多次装料完成单节车厢或单辆车装料的过程
3.1.3 累计装料wholeloading 完成整列(或编组)车或规定装料车(或车厢)数的整个过程
3.1.4 value 预设值present 规定装料的标称值,由自动定量装车系统自动采集数据输人或由操作人员借助装料设定装置预设 的以质量单位表示的值
3.1.5 分度值sealeinterval 以质量单位表示的相邻的两个示值之间的差值 3.1.6 累计分度值totalizationsaleinteryal d 总累计装置或部分累计装置以质量单位表示的两个相邻示值的差值
3.1.7 最大秤量maximumeapaeity 定量装车系统在正常使用过程中允许称量的最大载荷
它是由称量仓允许盛放的最大质量的物料 决定的
3.1.8 ebin 缓冲仓srge 具有上下开放口的容器,用于存储待装物料并可以给称量仓供料,以保证后续称量过程连续性的容 器
上端为进料口接收来自于进料装置的预装物料,下端设有可控人料闸门用于将物料卸人称量仓 3.1.9 称量仓weighbin 作为装车系统计量装置的承载器,是具有上下开放口的斗式容器,用于承载被称物料
3.1.10 入料闸门feedgate 用于给称量仓配料的闸门
根据称量系统的实时检测结果,通过控制闸门的开合位置,调整、截断 进人称量仓内物料的装置
3.1.11 卸料闸门dischargegate 用于给称量仓卸料的闸门
通过控制闸门的开合位置,及时将称量仓内的物料卸人待装车厢内;当 闸门关闭时,能够保证下一次称量过程及时开始
3.1.12 可控调节执行器controllableaetwator 可控调节执行器由动作元件、电磁阀、位置检测装置组合而成,用来直接驱动闸门的开、关动作,实 现闸门开关速度和开关位置的检测和控制,以完成控制系统所设定的目标动作
GB/35449一2017 3.1.13 装料溜槽loadingchute 用于引导称量仓内的物料能够装人指定的车厢内的溜槽,并根据控制系统的检测信息,及时调整高 度,以适应不同高度的车厢
3.1.14 称量系统weighingsystem 参与被称载荷质量检测的装置,它包括称量仓、称重传感器、电子称重仪表、称重控制软件等
3.1.15 自动定量装车系统automatiequantitativeloadingvehieesystem 依据车厢(辆)的预装料量和车辆顺序形成的预设值顺序表,通过自动称量,把一批散状物料按照预 设值顺序表,分成预定的质量,并将其依次装人车厢(辆)的衡器
它主要由机械装置、称量系统、动力系 统、控制系统等构成
3.1.16 自动称量时的单次装料误差deviationforautomatieweiehing 装料质量的显示值与约定真值的差 3.2符号 下列符号适用于本文件
=示值 一第n次示值 =载荷 公L 一到下一个闪变点的附加载荷 P =I十0.5e一公L=化整前的示值(数字示值 =I一L或P一L=误差 MPE一最大允许误差 -装车质量的预设值 ” EUT=被测衡器 预设值误差设定误差 se MPSE=最大允许设定误差 一装车质量的约定真值 产品型号与规格 4.1基本结构型式 产品的基本结构型式如图1所示
GB/T35449一2017 缓冲仓 入料闸门 称重传感器 称量仓 卸料闸门 标准祛码 装车液糟 建筑结构 待装车厢 图1自动定量装车系统基本结构示意图 4.2型号 按GB/T26389编制,企业也可根据自身情况自行编制
4.3规格 装车系统的规格以最大秤量表示,单位为kg或t
5 计量要求 5.1准确度等级 自动定量装车系统分为三个准确度等级;0.5级、1级、2级
5.2误差范围 5.2.1最大允许误差 每个准确度等级的最大允许误差应为表1中的对应值
表1装料的最大允许误差 准确度等级 单次装料允许误差 最大允许预设值误差 0.5级 士0,25% 士0,5% 1级 士1% 士0.5% 2级 士l.0% 士2% 5.2.2单次装料的最大误差 单次装料量的显示值与此次装料约定真值之间的差值应不超过表1中单次装料允许误差的规定
5.2.3最大允许预设值误差 单次装料预设值与此次装料约定真值之差应不超过表1中最大允许预设值误差的规定
GB/35449一2017 5.2.4累计装料的最大允许误差 在完成一列(或一组)车装车后,装车系统累计示值与约定真值之差应不超过表1中单次装料允许 误差的规定
5.3分度值d、累计分度值d 分度值d、累计分度值d,以包含质量单位的下列数字之一表示;1×1o*,2×10*,5×10f(K为正 整数、负整数或零)
累计分度值d,应符合 不小于最大秤量的0.01%;和 a b)不大于最大秤量的0.2%
5.4静态称量的最大允许误差 静态称量时,最大允许误差应符合表2的规定
表2静态称量的最大允许误差 0.5(用分度值 l,2(用分度值 准确度等级 最大允许误差 表示的载荷m) 表示的载荷m 0
GB/35449一2017 证系统正确安装并在约定的环境下使用时,保证其计量特性要求
操作方式,待装车厢或约定物料需发生较大差异的变更时,应经原生产单位认可,必要时应重新进 行检验
6.2操作的安全性 系统的绝缘电阻、,耐压要求、泄露电流、防电击等安全性要求,应满足GB14249.1的要求
自动定量装车系统不应具有易于被欺骗性使用的特征
系统内的部件、接口、软件设备等均应具备安全措施,以禁止非法访问或删除,或通过自动检查跟踪 或类似功能来检测并记录非法访问记录
对软件部分的设定或修改均应设置相关权限,系统的称重和调试软件应内置固化,仪表能隔绝参数 的非法调整,自动记载并保存每次参数调整的数据和时间
对硬件部分做的任何修改都应是可以识别并不得影响计量性能
6.3机械设备 6.3.1缓冲仓 仓体锥角应大于物料静态安息角,保证物料落料顺畅
6.3.2入料闸门 人料闸门应设置在缓冲仓下部落料口处,必要时应配置可控调节执行器
人料闸门关闭后应能截 断缓冲仓内的物料流,以实现准确称量
6.3.3称量仓 仓体锥角应大于物料静态安息角,保证物料落料顺畅
称量仓和卸料闸门的组合体应仅通过称重 传感器与支承结构进行刚性连接,其余部位与周围部件应为软连接
称量仓应配置相应的空间或设施便于安全可靠地放置标准器
如果这些设施不是固定设施,则应 将其放置在称量仓的附近
6.3.4卸料闸门 卸料闸门应设置在称量仓下部落料口处,并应配置可挖调节执行器
卸料闸门关闭后应能截断称 量仓内的物料流,不漏料
必要时,其开口大小能通过可控调节执行器进行实时控制
6.3.5装料溜槽 装料溜槽用于引导称量仓内的物料能够装人指定的车厢辆)内
其动作应与装料车厢的运动相配 合,避免发生碰撞
6.4动力系统 动力系统设计应符合GB/T3766或GB/T7932的规定
应配备有蓄能装置,能够保证系统断电 后自动关闭闸门并使各运动部件回归到初始状态
6.5电气与控制系统 6.5.1电气与控制系统组成 电气与控制系统应配备;配电柜,料位指示装置、料位限位传感器、进站测速传感器、进出站信号
GB/T35449一2017 灯等
6.5.2控制方式 系统应具备自动/半自动/手动的控制方式
6.5.3控制系统 控制系统应能够控制各部件的动作,并实现上料、称量、卸料、装车、自动采集并记录数据等全过程 控制,应能够完成数据采集和汇总处理
其安全性应符合GB5226.1的要求
6.6称量系统 6.6.1称量系统组成 称量系统应包括称重传感器、电子称重仪表、接线盒、称重控制软件、上位机、标准器等
6.6.2称重传感器 所使用的称重传感器应符合GB/T75512008中的有关要求,其中湿度要求应符合GB/T7551 2008中5.5.3的规定 6.6.3电子称重仪表 电子称重仪表应具有合格证书和使用说明书,相应指标应符合GB/T7724中影响因子,抗干扰、供 电电源及安全性能的相关要求
6.6.4称重结果的指示 装车系统的显示和打印应清晰、准确、可靠显示和打印内容为数字及相应的质量单位名称或符号
显示和打印装置应符合下列要求 称量值显示与打印值一致 b)为了使用目的,打印应清晰,永久
6.6.5标准器 标准器应采用符合GB/T4167的砝码,其精度优于装车系统静态称量状态下允许误差的1/3
标 准器的配置数量应符合表3中规定的数量
表3系统配置的标准器数量 最大秤量Max 标准器的最小量 Max<5t Max 5t
GB/T35449一2017 试验方法 7.1单次装料质量的确定 单次装料质量采用以下方法确定 使用7.4.1分离试验法来确定单次装料的质量;或 使用7.4.2集成试验法来确定单次装料的质量
7.2物料试验的实施 7.2.1装料质量的值 装料试验使用的载荷应等于或接近称量仓最大秤量及等于或接近最小秤量
7.2.2试验载荷的类型 自动定量装车系统用于试验的载荷应符合系统设计时所适用的典型物料 7.2.3试验条件 在开始试验前,自动装车系统应达到制造商说明书中规定的稳定运行状态
7.2.4标准砝码的替代 标准砝码的替代仅在装车系统用于集成控制衡器的静态试验时进行
可使用系统配置的砝码或其他稳定的载荷代替标准砝码,在以下情况下标准砝码的量可以减少: 如果重复性<0.2d,时,可减少到1/10Max的标准砝码; 重复性由系统配置的砝码或其他稳定的载荷)在承载器上放置3次确定 7.3装料次数 自动定量装车系统试验装车的最少次数为5个单次装料
一组预设值中,至少应包括接近最大秤 量、最小秤量及常用秤量
7.4物料的试验方法 7.4.1分离试验法 -台分离的控制衡器对单车装料质量进行称量,其结果作为检验载荷质量的约定真值
使用一 7.4.2集成试验法 7.4.2.1 -般要求 集成试验法是用被测的装车系统来确定试验装车质量的约定真值
集成试验法应选用下述装置之 -来实施 -种专门设计的指示装置;或 a) b 用标准砝码来确定化整误差的指示装置 无论对于分离试验还是集成试验,试验方法的总不确定度应不大于装车系统最大允许误差的1/3
7.4.2.2自动运行的中断 试验装车过程中,自动装车操作应该是运行的
10
GB/35449一2017 自动定量装车系统的装车质量在称量仓上被称量,所以在每个装车周期内,自动运行应中断两次
分别在 a 称量仓装料之后; b)称量仓卸料之后 卸料前满载)中断 在停止加料并且称量仓装料完毕后,应立即中断自运行
待称量仓稳定后,记录显示的装 料示值,然后将装车系统恢复到自动运行状态
卸料后(空载)中断 郎料完毕,并且称量仓已准备好接收下一装料前,这时应中断自动运行
待称量仓稳定 后,记录显示的装料示值,然后将装车系统恢复到自动运行状态
7.5试验装料的质量 试验装料应在控制衡器上进行称量,其结果应视为试验装料的约定真值
通过与预设值、显示值和 累计值的结合,得出装车系统的误差
7.6动力系统试验 在空载运行条件下,将系统断电,检查动力系统的各项动作 7.7电气与控制系统试验 在空载运行条件下,检查电气与控制系统
检验规则 8.1型式检验 在下列情况下装车系统需进行型式检验 8.1.1 新产品的试制定型鉴定; 设计、工艺、关键元器件有重大改变后的首台产品
8.1.2型式检验时,应对本标准规定的全部计量要求、技术要求进行检验,检验按照附录A的要求 进行
8.2出厂检验 出厂检验项目 外观检查; 标志; 自动定量装车系统应在出厂并安装完成后进行检验,检验项目见表4中的规定检验合格后 发放产品合格证
11
GB/T35449一2017 表4出厂检验项目 本标准对应章条 序号 检验项目 技术要求 检验方法 外观 目测 6.6,6.l0 9.1.1,9.1.2 目测 标志 预热时间 5.8.3 A.6.1 置零准确度 6.8.2 A.6.2.3 单次装料试验(常温下 5.2.2 A.7.3.2或A.7.4.3 最大允许预设值误差(常温下) 5.2.3 A.7.3.3或A.7.4.4 累计装料试验 5.2.4 A.7.3,4或A.7,4,5 g 标志、包装、运输和贮存 g.1标志 9.1.1完整表示的标志 完整表示的标志应包括以下内容 制造商的商标或名称 -进口商的商标或名称(若适用); 装车系统的制造日期; 装车系统的序列号和型号; 物料标示; 电源电压,V:; 电源频率(若适用),Hz 气压/液压(若适用),kPa/MPa: 产品国家标准号
9.1.2用符号表示的标记 用符号表示的标记应包括 符合国家要求的型式批准号(若适用); 准确度等级符号; 分度值; 最大秤量Max=kg或t -最小秤量Min=kg或t; 累计分度值d=kg或t; 温度范围C~C g.1.3说明性标志的要求 在正常使用条件下,说明性标志应牢固可靠,清晰易读
说明性标志应集中在装车系统醒目的位置,可置于永久固定在指示装置附近的铭牌或粘贴标签上, 12
GB/35449一2017 或置于装车系统本身不可移动的部件上
9.2包装 9.2.1整机或部件(控制系统)需用质地牢靠的材料进行包装,体积庞大的结构件,允许裸装,但均应有 防潮和防震措施
其中电子称重仪表和称重传感器应垫以松散、防止窜动的缓冲材料包好后放人箱内
动力(液压和气动)系统应按其标准要求包装
包装方法应符合GB/T13384的要求,包装储运图示标 志应符合GB/T191的要求
g.2.2不便于装箱的零部件应捆扎牢固 9.2.3所有包装材料不应引起产品的油漆件或电镀件等表面色泽改变和腐蚀
9.2.4随机资料应包括 产品合格证; a b 使用说明书; c 装箱单; d)总装图
使用说明书的内容应符合GB/T9969的编制要求
9.3运输 在运输、装卸时应小心轻放,禁止抛掷、碰撞和倒置,防止剧烈震动和雨淋 9.4贮存 9.4.1电子称重仪表的贮存应符合GB/T7724
称重传感器的贮存应符合GB/T7551的要求
动力 液压和气动)系统的贮存应符合GB/T3766或GB/T7932的要求
9.4.2其他部件在室外存放时,应防止雨淋和受潮
13
GB/T35449一2017 附 录 A 规范性附录) 自动定量装车系统试验方法 A.1 型式检验检查 A.1.1 文件 检查所提交的文件是否适当和正确
包括图纸、标准、说明书、系统电气图等必要的文件
A.1.2结构与文件的对比 检查自动定量装车系统各装置,确保与所提供的文件相符 A.1.3计量要求 检查自动定量装车系统的计量特性,确保与第5章中的要求相符
A.1.4技术要求 检查自动定量装车系统的技术要求,确保与第6章中的要求相符
A.2出厂检验审查 依据制造商流程管理和检验规范进行
A.3通用试验要求 A.3.1供电电源(5.7.2或5.7.3) 接通被测自动定量装车系统(EUT)的电源,预热时间应不小于厂家规定的时间,并在每个试验期 间保持对EUT一直通电
A.3.2置零(6.8 单次试验前,使用自动或半自动置零装置调整EUT零点,使其尽可能接近实际零点,整个试验期 间都不允许重新置零,除非出现显著增差
自动置零装置的状态应符合每个试验的规定
A.3.3温度(5.7.1 试验应在稳定的环境温度下进行,通常为正常环境温度,除非另有规定
试验期间所记录的极限温 度之差不超过自动定量装车系统规定温度范围的1/5,且不大于5C,其变化速率不超过5C/h,才可 认为温度稳定
电子称重仪表上应没有凝露
A.3.4恢复 单次试验结束后,应在下一试验开始前使自动定量装车系统有充分的时间恢复 14
GB/35449一2017 A.3.5预加载 除了A.5.1预热)中的试验,在单次称量试验进行之前,称量仓应预先加载到最大秤量
A.3.6控制衡器(6.9) A.3.6.1试验系统的准确度(6.6.5) 用于试验的控制衡器和标准砝码,应保证其所确定的试验载荷和装车质量的误差不大于物料试验 中所要求的装车系统的1/3MPE 试验系统的准确度要求取决于误差范围,而误差范围又由准确度等级决定,然而,准确度等级又通 过试验的结果来判定
所以在开始进行试验之前,有必要让执行试验的计量人员知道可以取得的最高 准确度等级
A.3.6.2用标准砝码确定示值化整误差 A.3.6.2.1确定示值化整前误差的一般方法 对于分度值为d的自动定量装车系统,可以采用在分度值之间插人闪变点的方法,确定系统在化 整前的示值
对于装车系统称量仓上某一确定的载荷L,其示值为I
逐一加放0.1l的附加砝码直至示值明 显地增加了一个d,变成(1十d)
所加的附加砝码为L,化整前的示值为P,则P由下列公式给出 P=I十0.5dl一L 化整前的误差为:E=P一L=I十0.5l一L一L 示例:一台d=50kg的装车系统,加放80000kg的载荷L,示值1为80000kg
逐一加放5kg的砝码,示值由 kg变为 180050kg时,附加砝码为15kg,代人上述公式得 80000 P=(80000十25-15)kg=80010kg 因此,化整前的实际示值为80010kg,化整前的示值误差为 E=(80010一80000)kg=十10kg A.3.6.2.2零点误差的修正 用A.3.6.2.1中的方法来计算零载荷的误差E
用A.3.6.2.1中的方法来计算载荷为L的误差E 化整前的修正误差E
为 E
=E一E 示例:如果对于A.3.6.2.1中的例子,零载荷的误差为 E
=十5kg 修正误差为 E=[十10一(十5)]kg=十5kg A.4型式检验(8.1 通常型式检验应做下列试验 -型式试验检查(A.1); -影响因子和抗干扰试验(A.6); -物料试验(A.7.1). 15
GB/T35449一2017 A.5静态试验 A.5.1预热时间(5.8.3) 预热时间应满足制造厂家说明书要求的预热时间
预热时间内自动操作应被禁止
A.5.2置零(6.8) A.5.2.1概述 置零可以有多种方式,例如 半自动;接通电源时自动;自动运行启动时自动; 作为称量周期的一部分自动
如果有多种置零方式,且明确知道每种方式都采用相同的步骤,则通常只用其中一种方式对置零准 确度进行试验
如果置零作为自动称量周期的一部分来设定,那么这种方式也应进行试验
为了试验 自动置零,在试验之前有必要让装车系统运行通过自动周期的相应部分,然后停止装车系统的运行
A.5.2.2置零范围 A.5.2.2.1初始置零范围 按以下方式分别确定相应的初始置零范围 a)正向范围 置零可用信号模拟器来对电子称重仪表进行模拟置零操作
将信号模拟器接人电子称重仪表中,关闭电子称重仪表的零点追踪功能,设定电子称重仪表的最大 量程和分度值
调节信号模拟器给电子称重仪表增加“模拟载荷”,然后将电子称重仪表置零
继续增加“模拟载 荷”,直到将一个“模拟载荷”增加到电子称重仪表后,电子称重仪表无法置零
能够被重新置零的最大 “模拟载荷”即为初始置零的正向范围
b)负向范围 重新置零后调节信号模拟器给电子称重仪表增加负的“模拟载荷”,然后将电子称重仪表置零
继 续增加负的“模拟载荷”,直到将一个负的“模拟载荷”增加到电子称重仪表后,电子称重仪表无法置零
能够被重新置零的最小负的“模拟载荷”即为初始置零的负向范围
A.5.2.2.2自动置零范围 在称量仓上逐步增加试验用砝码,每增加一个砝码,使系统运行相应的自动循环部分,观察系统是 否能自动置零
能够置零的最大载荷就是自动置零范围
A.5.2.3置零准确度 进行置零准确度试验前应先关闭仪表零点追踪: a 当称量仓空载时,按A.5.2.1中规定的方式使装车系统置零 向称量仓上加小砝码,以确定从零点到零点之上一个分度值的变化所需的附加小肤码值 b c 按A.3.6.2.1中规定的方法来计算零点误差 d 验证置零误差在6.8.2规定的范围内
16
GB/35449一2017 A.5.3静态称量的试验方法(5.4 向称量仓逐渐加载从零点至最大秤量的砝码,再逆顺序卸载至零点
选择的试验载荷应包括接近 最大秤量和最小秤量的值、常用秤量点
如果标准砝码不能达到最大秤量,可按7.2.4的要求进行标准砝码的替代
注意加卸砝码时,应逐渐地递增或递减
A.6影响因子和抗干扰试验(5.7 A.6.1概述 通常对于自动称量物料的自动定量装车系统不可能进行影响因子或抗干扰试验,所以应按本标准 规定的静态或模拟条件对装车系统进行影响因子试验或干扰试验
用于试验的模拟器应包括称重系统 中的所有电子装置
称重模拟器应包括称重传感器并含有施加标准试验载荷的方法
A.6.2规定(静态)温度(5.7.1) 测试应按GB/T23111一2008中A.5.3.1要求进行
如装车系统具有零点跟踪装置,测试时不能运行或超出其工作范围 A.6.3湿热、稳态(5.7.1 按GB/T231l1一2008中B.2要求进行
如装车系统具有零点跟踪装置,测试时不能运行或超出其工作范围
A.6.4交流电源电压变化试验(5.7.2) 按GB/T23111一2008中A.5,4.1要求进行
如装车系统具有零点跟踪装置,测试时可以运行
A.6.5抗干扰性能测试(5.8.2) A.6.5.1 般要求 各项试验中出现下述a),b),.c)情况判为合格,d)及其他情况判为不合格: 装车系统在经受干扰时,示值变化应不大于le; a b 装车系统在经受干扰时,功能暂时丧失或性能暂时降低(如;装车系统的示值显示闪变而无法 读准;装车系统的显示器黑屏或无显示;装车系统的示值出现跳变,即使示值变化超过了le, 但在干扰停止后装车系统能自行恢复,无需操作者干预; 装车系统在经受干扰时,功能暂时丧失或性能暂时降低,并报警
在干扰停止后,通过操作者 干预(如:按复位键或重新开机)才能使装车系统恢复到原来示值的正常状态 因硬件或软件损坏,或数据丢失而造成不能恢复至正常状态的功能降低或丧失
被测装车系 统的通电时间应等于或大于制造厂商规定的预热时间,并保持被测装车系统在整个试验期间 处于通电状态
在每项试验前,尽可能地使被测装车系统调整至接近于实际零点
若装车系统配备了接口,试验中 应将适当的外围设备、外部设备连接至各个不同的接口上
所有试验记录应包含试验时的环境条件
并在试验期间的任何时候不再重新调整零点,出现上述抗干扰要求中的b)和c)情况除外
记录在各种 试验条件下的零点示值误差,对所有载荷的示值进行修正,获得修正后的称量结果
17
GB/T35449一2017 A.6.5.2静电放电抗扰度试验 按GB/T231l1一2008中B.3.4要求进行
A.6.5.3射频电磁场辐射抗扰度试验 按GB/T231112008中B3.5要求进行
A.6.5.4电快速瞬变脉冲群抗扰度试验 对电网电源供电电源线的测试按GB/T23111一2008中B.3.2要求进行
A.6.5.5浪涌抗扰度试验 按GB/T231ll一2008中B.3.3要求进行
A.6.5.6射频场感应传导骚扰抗扰度试验 按GB/T231l1一2008中B.3.6要求进行
A.6.5.7电压暂降短时中断抗扰度试验 对电网电源供电部分的测试按GB/T23111一2008中B.3.1要求进行
物料试验程序 A.7 A.7.1型式检验时的物料试验(8.1) 使用物料的运行试验应在一台完整的自动定量装车系统上进行,以确定其是否符合第6章的技术 要求
用作试验载荷的物料应符合7.2.2的规定
A.7.2出厂检验的物料试验(8.2 使用物料的运行试验应当在一台完整,完全组装且已安装在实际使用地点的自动定量装车系统上 进行
对物料试验的要求: -试验载荷和装料质量应符合7.2.1中要求; 载荷类型应符合7.2.2要求; 物料试验的条件按7.2.3的规定; 装料次数应符合7.3的要求
应根据试验结果通过计算确定准确度等级
A.7.3分离试验法(7.4.1 A.7.3.1操作程序 在分离控制衡器上称量试验组中每节车厢的空载质量值,必要时使用标准砝码评定化整误差 a 并记录P 装料前
b 根据试验组中每节车辆空载值和相应规定的预设值F,对每节车厢进行设定,形成预设值顺 序表
按照规定的运行状态,运行装车系统,并至少完成5个单次装料过程,记录装车系统主累计初 18
GB/35449一2017 始示值I初给果计
装料秤量的选择,应符合7.3的要求
d) 对每节(辆)车厢进行规定数量的装料物料卸人车厢中),记录每次装料示值I
在分离的控制衡器上分别确定每个装满物料车厢的满载质量值,必要时使用标准砝码评定化 e 整误差,并记录P张料后
记录装车系统的累计示值I最终默
f A.7.3.2单次装料误差 单次装料约定真值P a 单次装料约定真值是在分离控制衡器上称量得到的装料后满载车辆化整前示值P我料s与装料前空 载车辆化整前示值P我料前之差,见式(A.1). P=P P" (A.1 装料馆 装料前 式中: 单次装料约定真值; P 车辆满载时质量值; 装料后 尸数科前 车辆空载时质量值 b)计算单次装料误差E 单次装料误差等于单次装车系统示值1与该次装料约定真值尸之差,与约定真值尸的比值
按 照式A.2)计算
E一 -×100% A.2 式中: -单次装料误差; 单次装料约定真值; -单次装料示值
以试验组中单次装料的最大误差值作为该项试验结果
A.7.3.3预设值误差
单次预设值误差为单次装料预设值F,(见A7.3.1中b)条)与此次装料约定真值尸之差,与约定真 值P的比值
按照式(A.3)计算
F ×100% (A.3 e 式中 单次装料预设值误差; se 单次装料约定真值; P 单次装料预设值
F 以试验组中单次装料预设值误差最大值作为该项检定结果
累计装料误差 A.7.3.4 计算累计装料约定真值P a 累计 装料总量的约定真值为一个试验组中每次装料约定真值之和,见式(A. (A.4 P累计 式中: P累计 累计装料约定真值; 单次装料约定真值; 试验组中单次装料次数
19
GB/T35449一2017 D)计算装车系统累计示值I果计 装车系统累计示值为一个试验组装料完成后最终累计示值I最终累与初始累计示值I打始暴许之间的 差值,见式(A.5)
I累计=I最终累 A.5) I帮着紧的 式中 初始累计示值; I初始累计 I最终累 最终累计示值; 累计装料示值
1累计 计算累计装料误差E# c 累计装料误差等于累计示值与累计装料约定真值之差,与累计装料约定真值P眼之比
按照式 A.6)计算
P紧 I出 累 E职说 ×100% A.) P 累计 式中 E累计 累计装料称量误差
A.7.4集成试验法 A.7.4.1用于集成控制衡器的静态检验 在物料试验前,为使确定装料质量的误差符合A.3.6.1要求的控制衡器准确度,应对作为集成控制 衡器的装车系统进行静态检验
主要按照以下方式进行: 操作程序 a 从零点施加标准砝码(或载荷)至最大秤量,在加卸时应逐渐地递增或递减,记录示值误差并在物料 试验中确定误差时应用
至少选择5个不同的试验载荷,应包括最大秤量和最小秤量、常用秤量点
如果标准砝码不能达到最大秤量,可采用以下方法进行标准砝码的替代 b 根据7.2.4规定检查装车系统重复性,以确定允许的替代物量
重复性测试是选择按 6.6.5要求系统配置的最大量的砝码,对系统进行3次测试,其结果应符合5.6的要求
从零点加放标准砝码直至标准砝码的最大量,建议使用系统配置的砝码,并确定化整误 2 差,然后卸下砝码回到无载荷时的示值
用物料替代上一步所施加砝码的量,并找到用于确定误差的相同闪变点
3 再在装车系统上累加一定数量标准砝码,建议使用系统配置的砝码,并确定化整误差,然 后卸下砝码回到无标准砝码时的示值
5)用替代物料替代上一步所施加砝码的量,直到找到用于确定误差的相同闪变点
6)重复4)和5),直到达到装车系统的最大秤量 7) 按相反的顺序卸载,卸下物料前需用哒码确定化整误差,然后加上哒码直到找到相同的 卸下物料前称量点的闪变点
重复卸载直到回到装车系统上无载荷
注意:加卸砝码时,应逐渐地递增或递减
A.7.4.2集成试验法操作程序 集成试验法操作程序如下 a 根据试验组中每节车辆空载值(该值来源于其他设备)和7.3规定的预设值Fp对每节车厢装 料量进行设定,形成预设值顺序表 20
GB/35449一2017 b 按照7.2.3规定试验条件运行装车系统,至少完成5个单次装料过程,在称量仓满载且卸料前 中断操作系统
当装车系统和辅助设备完全稳定后,观察并记录称量仓的静态控制称量示值I拉刻知料前和累计 初始示值I初的果什,如果必要,可用标准砝码得到化整前示值
d 运行系统,将物料装人单节(辆)车厢,当称量仓卸料完成后进行中断操作
记录卸料后的静态控制称量示值I我胡那料后和装车系统的累计指示装置上此次装料示值! e f 当试验组的装车完成后,记录装车系统累计装料示值I最终累许
A.7.4.3单次装料误差 计算步骤如下: 计算单次装料约定真值 a 单次装料约定真值是单次装料的静态控制称量值之差,也就是称量仓卸料前静态控制称量示值 和卸料后静态控制称量示值P 之差,见式(A.7
P 控制卸料前" 控制卸料后 A.7 户控制=力控制部料前一力控制卸料后 式中: -单次装料约定真值 控M -单次卸料前静态控制称量示值; 力控制卸料 单次卸料后静态控制称量示值 声控制卸料后 b)计算单次装料误差E 单次装料误差为单次装料示值I与此次装料的约定真值之差,与此次装料的约定真值之比
按照 式(A.8)计算
P整让 E A.8 ×100% '教制 式中 -单次装料误差; 单次装料的约定真值 P控刻 -单次装料示值
以试验组中单次装料的最大误差值作为该项试验结果
A.7.4.4预设值误差 单次预设值误差为单次装料预设值与此次装料的约定真值之差,与此次装料的约定真值之比
按 照式(A.9)计算
P ×100% (A.9 Se= P控制 式中 -预设值误差; se -单次装料约定真值 P控制 F -单次装料预设值
以试验组中单次装料预设值误差最大值作为该项试验结果
A.7.4.5累计装料误差 计算步骤如下: 计算累计装料约定真值P教制果
GB/T35449一2017 累计装料约定真值为一个检定组中每次装料的约定真值之和,见式A.10) P (A.10 P我前 控制累计 式中: 累计装料约定真值; P控制累 检定组中单次装料次数
计算装车系统累计示值I整 b 装车系统累计示值为一个试验组装料完成后最终累计示值e的到#与初始累计示值I跳到#之间的 差值,按照式(A.5)计算
计算累计装料误差 c 累计装料误差等于装车系统累计示值与累计装料约定真值之差,与累计装料约定真值之比
按照 式(A.11)计算
P 累计 控刻累止 E联饼 ×100% A.11 控制累计 式中: E架计 累计装料误差; P 累计装料约定真值; 控制累计 累计装料示值
!累计
自动定量装车系统GB/T35449-2017
随着物流行业的不断发展,越来越多的企业开始关注如何提高装卸效率。而自动定量装车系统正是众多解决方案之一。该系统能够通过自动化技术实现货物的快速装车、准确定量等功能,为企业的物流管理提供了便利和支持。
为保证自动定量装车系统的质量和安全性,GB/T35449-2017标准对该产品进行了规范。该标准包括了自动定量装车系统的定义、分类、要求、试验方法、标志、包装、运输和储存等多个方面内容。
根据该标准的要求,自动定量装车系统应该满足以下条件:
- 自动定量装车系统应该采用符合国家标准的零部件和材料,以确保其质量和安全性。
- 自动定量装车系统应该具有良好的适用性和稳定性,能够适应不同种类货物的装车需求。
- 自动定量装车系统应该具有准确的称重功能,以确保货物装车时的准确性。
- 自动定量装车系统应该具有良好的安全保护措施,能够避免在使用过程中出现任何安全问题。
除此之外,标准还要求对自动定量装车系统进行多项试验,以确保其质量和安全性。这些试验包括称重准确度试验、稳定性试验、安全保护试验等。
综上所述,GB/T35449-2017标准为自动定量装车系统的质量和安全提供了重要的保障。在选购自动定量装车系统时,企业应该注意选择符合标准的产品,并根据产品说明书正确使用。