GB/T23257-2017
埋地钢质管道聚乙烯防腐层
Polyethylenecoatingforburiedsteelpipeline
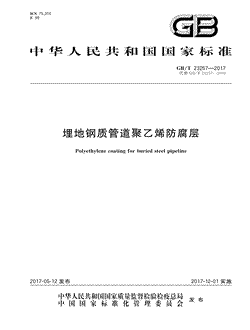
- 中国标准分类号(CCS)E98
- 国际标准分类号(ICS)75.200
- 实施日期2017-12-01
- 文件格式PDF
- 文本页数41页
- 文件大小2.61M
以图片形式预览埋地钢质管道聚乙烯防腐层
埋地钢质管道聚乙烯防腐层
国家标准 GB/T23257一2017 代替GB/T23257一2009 埋地钢质管道聚乙烯防腐层 Polyethyleneeoatimgforburiedsteelipeline 2017-05-12发布 2017-12-01实施 中华人民共利国国家质量监督检验检疙总局 发布 国家标准化管理委员会国家标准
GB/T23257一2017 34 附录N规范性附录热收缩带(套)耐热冲击试验方法 35 附录O(规范性附录热熔胶的脆化温度试验方法 36 附录P规范性附录补口防腐层耐热水浸泡试验方法 37 附录Q规范性附录补口防腐层热老化试验方法
GB/T23257一2017 前 言 本标准按照GB/T1.1一2009给出的规则起草
本标准代替GB/T23257一2009《埋地钢质管道聚乙烯防腐层》
与G;B/T23257一2009相比,主要 技术变化如下 调整了范围中挤压聚乙烯防腐层分类的最高温度定义,由“最高使用温度”调整为“最高设计温 度”,温度值分别由50C调整为60,70C调整为80(见第1章 -增加了术语和定义(见第3章); 修改了环氧粉末涂料热特性指标(见表2); 修改了聚乙烯专用料的拉伸性能要求(见表5); 补充修改了聚乙烯防腐层的性能要求见表7); 补充修改了热收缩带补口材料的性能要求(见表l1) -增加了补口施工准备和补口工艺评定要求(见9.2); 修订了部分附录试验方法(见附录B、附录K); -增加了附录试验方法(见附录G附录M、附录Q)
本标准由石油天然气集团公司提出
本标准由全国石油天然气标准化技术委员会(SAC/TcC355)归口
本标准负责起草单位;石油集团工程技术研究院、石油集团海祥工程有限公司
本标准参加起草单位;宝鸡石油钢管有限责任公司、大庆油田工程建设有限公司天宇设计院 本标准主要起草人;张其滨、刘金霞、赫连建峰、温宏伟、陈守平、史惠辉
本标准所代替标准的历次版本发布情况为: GB/T23257一2009
GB/T23257一2017 埋地钢质管道聚乙烯防腐层 范围 本标准规定了钢质管道挤压聚乙烯防腐层及辐射交联聚乙烯热收缩带(套)补口的最低技术要求
本标准适用于埋地钢质管道挤压聚乙烯防腐层的设计、生产和检验,及其现场补口的设计、施工和 检验
其他敷设形式的管道挤压聚乙烯防腐层可参照执行
挤压聚乙烯防腐层可分为最高设计温度不超过60C的常温型(N)和最高设计温度不超过80的 高温型(H)两类
规范性引用文件 下列文件对于本文件的应用是必不可少的
凡是注日期的引用文件,仅注日期的版本适用于本文 件
凡是不注日期的引用文件,其最新版本(包括所有的修改单)适用于本文件
GB/T1040.2塑料拉伸性能的测定第2部分模塑和挤塑塑料的试验条件 GB/T1408.!绝缘材料电气强度试验方法第1部分;工频下试验 GB/T1410固体绝缘材料体积电阻率和表面电阻率试验方法 GB/T1633热塑性塑料维卡软化温度(VST)的测定 GB/T1725色漆、清漆和塑料不挥发物含量的测定 GB 1842塑料聚乙烯环境应力开裂试验方法 3682热塑性塑料熔体质量流动速率和熔体体积流动速率的测定 T GB 4472化工产品密度、相对密度的测定 GB GB/T5470塑料冲击法脆化温度的测定 GB6514涂装作业安全规程涂漆工艺安全及其通风净化 GB/T655!电气绝缘用树脂基反应复合物第2部分试验方法电气用涂敷粉末方法 GB/T7124胶粘剂拉伸剪切强度的测定(刚性材料对刚性材料) GB7692涂装作业安全规程涂漆前处理工艺安全及其通风净化 GB/T8923.1涂覆涂料前钢材表面处理表面清洁度的目视评定第1部分:未涂覆过的钢材 表面和全面清除原有涂层后的钢材表面的锈蚀等级和处理等级 GB/T13021聚乙烯管材和管件炭黑含量的测定(热失重法 GB/T15332热熔胶粘剂软化点的测定环球法 GB/T18570.3涂覆涂料前钢材表面处理表面清洁度的评定试验第3部分;涂覆涂料前钢材 表面的灰尘评定(压敏粘带法) GB/T18570.9涂覆涂料前钢材表面处理表面清洁度的评定试验第9部分:水溶性盐的现场 电导率测定法 工业企业嗓声控制设计规范 GB/T50087 GB50369油气长输管道工程施工及验收规范 术语和定义 下列术语和定义适用于本文件
GB/T23257一2017 3.1 挤压聚乙烯防腐层extrudedpolyethylenecoating 在挤出机中通过加热、加压使聚乙烯以流动状态连续通过挤出口模成型包覆在管道上而形成的防 腐层,包覆方式包括纵向挤出包覆和侧向缠绕包覆
3.2 最高设计温度maxiumdesigntemperature 在管道运输、搬运,施工及运行过程中防腐层可能达到的最高温度
3.3 最高运行温度nmaximumoperationtemperature 管道或者管线系统在运行过程中所达到的最高温度
注:最高运行温度不超过最高设计温度
3.4 pwwdereoating tpplhed 低温涂敷环氧粉末涂料low temperature; ep0Xp0 用作本标准规定的三层结构聚乙烯防腐层底层,并可在低于200C以下涂敷施工的环氧粉末涂料
3.5 断裂标称应变nominaltensilestrainatbreak 与拉伸断裂应力相对应的拉伸标称应变
3.6 内聚破坏cohesivefailure 胶粘层自身破裂,在两个被粘物表面均有胶粘剂粘结存在 3. 界面破坏interfaeialftailure 胶粘层与被粘物界面处发生目视可见的破坏现象
防腐层结构 4.1挤压聚乙烯防腐层分二层结构和三层结构两种
二层结构的底层为胶粘剂层,外层为聚乙烯层; 三层结构的底层通常为环氧粉末涂层,中间层为胶粘剂层,外层为聚乙郁层
DN500以上的管道不宜 采用两层结构聚乙烯防腐层
4.2防腐层的最小厚度应符合表1的规定
焊缝部位的防腐层厚度不应小于表1规定值的80%
应 根据管道建设环境和运行条件,选择防腐层等级
表1防腐层的厚度 防腐层最小厚度 环氧涂层 胶粘剂层 钢管公称直径 mm DN Am mm 加强级(S) 普通级(G DN<100 1,8 2.5 00DN<250 2." 120 2.0 250
GB/T23257一2017 5 材料 5.1钢管 5.1.1钢管应符合现行有关钢管标准或订货技术条件的规定,并有出厂合格证
5.1.2应对钢管逐根进行外观检查
外观质量应符合现行有关标准或订货技术条件的规定,不合格的 钢管不应涂敷防腐层
5.2防腐层材料 5.2.1 -般规定 5.2.1.1防腐层各种原材料均应有出厂质量证明书及检验报告、使用说明书、安全数据单、出厂合格证、 生产日期及有效期
环氧粉末涂料供应商应提供产品的热特性曲线等资料
5.2.1.2防腐层的各种原材料均应包装完好,应按产品说明书的要求存放
5.2.1.3每种牌(型)号的环氧粉末涂料胶粘剂以及聚乙烯专用料,在使用前均应由通过国家计量认 证的检验机构,按5.2规定的相应性能项目进行检测
性能检测结果达到本标准规定要求的材料方可 使用
5.2.2环氧粉末涂料 环氧粉末涂料及其涂层的性能应符合表2和表3的规定
涂敷厂对每一生产批(不超过20t)环氧 粉末涂料均应按表2和表3(不包括65C,30d阴极剥离)的规定进行质量复检,表3第3项应不定期 复检
钢管有低温涂敷要求时,应采用低温涂敷环氧粉末涂料,性能应符合表2和表3的规定
表2环氧粉末涂料的性能指标 项目 性能指标 试验方法 粒径分布 150m筛上粉末3.0 GB/T6554 250m筛上粉末 0.2 不挥发分含量(105 99.4 GB/T6554 密度 1.30~1.50且符合厂家给定值士0.05 GB/T4472 g/em" 胶化时间 GBT6554 >12且符合厂家给定值士20% 固化时间 附录A min AH 45 J/g 热特性 附录B Tg >98 注,环氧粉末涂料胶化时间和固化时间的测试温度为产品说明书指定的涂敷温度
未指定时,常温涂敷粉末试 验温度为200C,低温涂敷粉末试验温度低于200c
GB/T23257一2017 表3熔结环氧涂层的性能指标 项目 性能指标 试验方法 附着力 附录C 级 阴极剥离(65,48) 附录D mm 阴极剥离(65,30d 15 附录D mm 抗弯曲(一20C,2.5") 无裂纹 附录E 注实验室喷涂试件的涂层厚度应为300m一4004m,涂敷温度为产品说明书指定的温度
未指定时,常温涂 敷粉末涂敷温度为200C,低温涂敷粉末涂敷温度低于200C 5.2.3胶粘剂 胶粘剂的性能应符合表4的规定
涂敷厂对每一生产批(不超过30t)胶粘剂均应按照表4的规定 进行质量复检
二层结构聚乙烯防腐层采用热熔胶型胶粘剂时,应根据工程要求确定适当的技术性能 指标
表4胶粘剂的性能指标 项目 性能指标 试验方法 密度 0.920~0.950 GB/T4472 g/cm 熔体流动速率190C,2.16kg GB/T3682 g/10min 维卡软化点(A0,9.8N GB/T1633 e90 脆化温度 50 GB/T5470 氧化诱导期(200C) >10 附录F min 含水率 附录G S0,l % 拉伸强度" GB/T1040.2 MPa 断裂标称应变 >600 GB/T1040.2 % 拉伸速度50 mm/min
GB/T23257一2017 5.2.4聚乙烯 聚乙烯专用料及其压制片材的性能应符合表5和表6的规定
涂敷厂对每一生产批(不超过500)聚 乙烯专用料,应对表5规定的前5项和表6规定的前4项性能进行质量复验,需要时,也可对其他性能 进行复验
表5聚乙烯专用料的性能指标 项目 性能指标 试验方法 密度 0.9400.960 GB/T4472 g/em 熔体流动速率(190C,2.16kg >0.15 GB/T3682 g/10min 碳黑含量 -2.0 GB/T13021 含水率 0,1 附录G % 氧化诱导期(220C) 30 附录F min 耐热老化'(100C,4800h) 二35 GB/T3682 耐热老化指标为试验前与试验后的熔体流动速率变化率
表6聚乙烯专用料的压制片材性能指标 项目 性能指标 试验方法 拉伸屈服强度" 15 GB/T1040.2 MPa 拉伸强度 >22 GB/T1040.2 MPa 断裂标称应变" >600 GB/T1040.2 维卡软化点(A,9.8N GB/T1633 >110 脆化温度 65 GB/T5470 电气强度 GB/T1408.1 >25 MV/nm 体积电阻率 >1×10 GB/T1410 O m 耐环境应力开裂(Fa GBT1842 >l000
GB/T23257一2017 表6(续 项目 性能指标 试验方法 压痕硬度 附录H mm 23C 0.2 S0.3 60或80 耐化学介质腐蚀"(浸泡7山) 附录l % >85 10%HCI 0%NaoH >85 10%NaCI >85 耐紫外光老化(336h) >80 附录 % 拉伸速度50mm/min
0c 常温型,试验条件为60C;高温型,试验条件为80 耐化学介质腐蚀及耐紫外光老化指标为试验后的拉伸强度和断裂标称应变的保持率
5.3工艺评定试验 5.3.1涂敷厂应用所选定的防腐层材料在涂敷生产线上进行工艺评定试验,并对防腐层性能进行检 测
当防腐层材料生产厂家或牌(型)号或钢管管径改变或壁厚增大时,应重新进行工艺评定试验
工 艺评定试验合格后,涂敷厂应按照工艺评定试验确定的工艺参数进行防腐层涂敷生产
5.3.2聚乙烯层及防腐层性能应符合表7和表8的规定 5.3.2.1按确定的工艺参数涂敷聚乙烯层并进行性能检测,用于性能检测的聚乙烯层应不含胶和环氧 粉末层,结果应符合表7的规定 表7聚乙烯层的性能指标 项 性能指标 试验方法 轴向 20 MPa 周向 拉伸强度" 20 GB/T1040.2 MPa 偏差" <15 % 断裂标称应变 600 GB/T1040.2 % 压痕硬度 mn 附录H 23 S0.2 60亿或80C) 0.3
GB/T23257一2017 表7(续 项 性能指标 试验方法 耐环境应力开裂(Fn GB/T1842 >1l000 热稳定性“_MFR GB/T3682 拉伸速度50mm/min
偏差为轴向和周向拉伸强度的差值与两者中较低者之比 常温型,试验条件为60;高温型,试验条件为80
聚乙烯挤出前后熔体流动速率变化率
5.3.2.2从防腐管或在同一工艺条件下涂敷的试验管段上截取试件对防腐层整体性能进行检测,检测 结果应符合表&的规定 表8防腐层的性能指标 性能指标 目 试验方法 项 二层结构 三层结构 剥离强度 N/cm 70 >I00(内聚破坏) 附录K 20C士5C) >35 >70(内聚破坏 60"C士5"C 阴极剥离(65C,48h) <15 附录D mm 阴极剥离(最高运行温度,30d小) 附录D mm 环氧粉末底层热特性 玻璃化温度变化值ATg 附录B 冲击强度 附录1 J/mmm 聚乙烯无开裂 附录E 抗弯曲(一30C,2.5 耐热水浸泡(80C 翘边深度平均<2mm且最大 附录M ,48h 3mm 防腐层涂敷 6.1 锻管表面处理应符合下列要求 在防腐层涂敷前,先清除钢管表面的油脂和污垢等附着物,然后进行抛喷)射除锈
在进行 抛(喷)射除锈前,钢管表面温度应不低于露点温度以上3
除锈质量应达到GB/T8923.1
GB/T23257一2017 中规定的Sa2%级要求,锚纹深度达到50m一90 m
钢管表面的焊渣,毛刺等应清除干净
b 应将钢管表面附着的灰尘及磨料清扫干净
钢管表面的灰尘度应不低于GB/T18570.3规定 的2级
抛(喷)射除锈后的钢管应按GB/T18570.9规定的方法或其他适宜的方法检测钢管表面的盐 分含量,钢管表面的盐分不应超过20mg/ /m
如果钢管表面盐分含量超过20mg/'m,应采 用适宜的方法处理至合格
d 钢管表面处理后应防止钢管表面受潮、生锈或二次污染
表面处理后的钢管最迟应在4h内 进行涂敷,超过4h或当出现返锈或表面污染时,应重新进行表面处理
6.2开始防腐层涂敷时,先用试验管段在生产线上依次调节预热温度及防腐层各层厚度,各项参数达 到要求后方可开始正式涂敷
6.3应用无污染的热源对钢管加热至确定的涂敷温度,最高加热温度应低于钢管加热温度限制
6.4环氧粉末应均匀涂敷在钢管表面
回收环氧粉未的使用及其添加比例应按表2和表3规定的性 能进行检验后确认
胶粘剂涂敷应在环氧粉未胶化过程中进行
6.5 采用侧向缠绕工艺时,应确保搭接部分的聚乙烯及焊缝两侧的聚乙烯完全锯压密实无空洞,锯压 6.6 时应避免损伤聚乙烯层表面 聚乙希层包覆后应用水冷却至钢管温度不高于60C,并确保熔结环氧涂层固化完全
6.8防腐层涂敷完成后,应除去管端部位的防腐层
管端预留长度宜为100mm一10mm.并满足实 际焊接和检验要求
聚乙烯层端面应形成不大于30°的倒角,聚乙烯层端部外宜保留10mm30mm 的环氧粉末涂层 6.9涂敷采用热熔胶的二层结构聚乙烯防腐层时,应根据涂敷作业线的特点制定详细可行的工艺方 案,并在涂敷作业中严格执行
质量检验 7.1钢管表面处理的质量检验应符合下列要求 抛(喷)射除锈后的钢管应逐根进行表面除锈等级检验,用GB/T8923.1中相应的照片或标准 a 板进行目视比较,表面除锈质量应达到Sa2%级的要求;表面锚纹深度应每班(不超过12h)至 少测量两次,每次测量两根钢管,宜采用粗糙度测量仪或锚纹深度测试纸测量,锚纹深度应达 到504mm~90m;表面处理前的钢管表面温度应进行监测,钢管表面温度应不低于露点温度 以上3C 钢管表面灰尘度应每班(不超过12h)至少检测两次,每次检测两根钢管
应按照GB/T18570.3 规定的方法进行表面灰尘度评定,表面灰尘度应不低于2级
每批进厂的钢管在表面处理后应至少抽测2根钢管表面的盐分
钢管经海运、海边堆放或涂 敷施工现场处于盐碱地带时,每班(不超过12h)应至少检测2根钢管表面的盐分
按照 GB/T18570.9规定的方法或其他适宜的方法进行钢管表面盐分的测定,钢管表面的盐分应不 超过20mg/mr 7.2除锈后,应检查钢管表面缺陷,钢管表面缺陷和不规则重皮、损伤、划伤等)未经修复后不应涂敷 7.3涂敷过程中应对钢管加热温度进行连续监测,钢管的加热温度等工艺参数应符合确定的参数
7.4防腐层外观应逐根目测检查
聚乙烯层表面应平滑,无暗泡、无麻点、无皱折、无裂纹,色泽应均 匀,防腐管端应无翘边
7.5防腐层的漏点应按采用在线电火花检漏仪进行连续检查,检漏电压为25kV,无漏点为合格
单 管有两个或两个以下漏点时,可按第9章的规定进行修补;单管有两个以上漏点或单个漏点沿轴向尺寸
GB/T23257一2017 大于300mm时,该防腐管为不合格
7.6连续生产的钢管防腐层厚度至少应检测第1根,第5根、第10根,之后每10根至少测一根
宜采 用磁性测厚仪或电子测厚仪测量钢管3个截面圆周方向均匀分布的4点的防腐层厚度,同时应检测焊 缝处的防腐层厚度,结果应符合4.2的规定
7.7防腐层的粘结力按附录K的方法通过测定剥离强度进行检验
每班(不超过12h)至少在两个温 度条件下各抽测一次,结果应符合表8的规定
7.8每班(不超过12h)至少应测量一次三层结构防腐管的环氧粉末层厚度及热特性,结果应分别符合 表1和表8的规定
7.9每连续涂敷生产的第10km,20km,30km的防腐管均应按附录D的方法进行一次48h的阴极 剥离试验.之后每50km进行一次阴极剥离试验.结果应符合表8的规定
如不合格,应在前一次检验 合格后涂敷的防腐管中加倍取样检验
加倍检验全部合格时,该两次检测区间生产的防腐管为合格;仍 有不合格时,该两次检剥区间生产的批防腐管为不合格
7.10每连续涂敷生产50kn防腐管应截取聚乙熔层样品,按GB/1040.2检验其拉伸强度和断裂标 称应变,结果应符合表了的规定
若不合格,应在前一次检验合焰后涂教的防腐管中加信取样检验
加 倍检验全部合格时,该两次检测区间生产的防腐管为合格;仍有不合格时,该两次检测区间生产的批防 腐管为不合格
8 标志、堆放和搬运 8.1 检验合格的防腐管应在距管端约400mm处标有产品标志
产品标志应包括-脑腐层结构,防腐 层类型、防腐等级、执行标准,制造厂名(代号、生产日期等,并将钢管标志信息移置到防腐层表面
8.2挤压聚乙烯防腐管的吊装,应采用尼龙吊带或其他不损坏防腐层的吊具
8.3堆放时,防腐管底部应采用两道(或以上)支垫垫起,支垫间距为4m81 m,支垫最小宽度为 100mm n,防腐管离地面不应少于100mm,支垫与防腐管之间以及防腐管相互之间应垫上柔性隔离物
运输时,宜使用尼龙带等捆绑固定,装车过程中应避免硬物混人管垛
8.4挤压聚乙烯防腐管的允许堆放层数应符合表9的规定
表9挤压聚乙烯防腐管的允许堆放层数 公称直径DNDN<200200
GB/T23257一2017 缩率应不小于15%;热收缩套的周向收缩率应不小于50%
其性能应符合表11和表12的规定
g.1.3每一牌号的热收缩带(套)及其配套环氧底漆,使用前且每年至少应按表10,表11和表12规定 的项目进行一次全面检验
使用过程中,每批(不超过5000个)到货,应对表10、表11中耐环境应力开 裂除外的项目和表12的剥离强度等性能进行复检,性能应达到规定的要求
表10热收缩带(套)的厚度 单位为毫米 基材类型 适用管径DN 基材 胶层 <400 >1.2 普通型 >1.0 >400 >1.5 高密度型 >1.0 >1.5 表11热收缩带(套)的性能指标 项 性能指标 试验方法 基材性能" 普通型 17 GB/T1040.2 拉伸强度 MPa 高密度型 >20 GB/T1040.2 断裂标称应变 >400 GB/T1040.2 GB/T1633 普通型 90 维卡软化点(A,9.8N 高密度型 GB/T1633 >100 脆化温度 GB/T5470 65 电气强度 25 GB/T1408.1 MV/m 体积电阻率 >1×10 GB/T1410 Qm 耐环境应力开裂(F GB/T >l000 1842 耐化学介质腐蚀'(浸泡7d % 10%HCI 85 附录1 10%NaoH 85 10%NaC 85 耐热老化(150,21d >14 拉伸强度 MPa GB/T1040.2 断裂标称应变 >300 GB/T1040.2 % 10
GB/T23257一2017 表11(续 项 性能指标 试验方法 热冲击(225.4h) 无裂纹,无流淌,无垂滴 附录N 胶层性能 胶软化点(环球法 多最高运行温度十40 GB/T15332 且不低于90U 23 >1.0 GB/T7124 搭接剪切强度(钢/钢 MPa 最高运行温度 >0,07 GB/T7124 23 >1.0 GB/T7124 搭接剪切强度(PE/PE) MPa 最高运行温度 2 20.07 GB/T7124 脆化温度 s-15 附录O 底漆性能 不挥发物含量 95 GBT1725 剪切强度 >5.0 GB/T7124d MPa 阴极剥离65,48h)y 附录D mm 阴极剥离23,,30d)" 附录D 15 mmm 除热冲击外,基材性能需经过200C土5C,5min自由收缩后进行测定,拉伸试验速度为50mm/min
耐化学介质腐蚀指标为试验后的拉伸强度和断裂标称应变的保持率 拉伸速度为10mm/min 拉伸速度为2" mmm/min 底漆涂层厚度3004m400m 表12热收缩带(套)安装系统的性能指标 项 性能指标 试验方法 抗冲击强度 附录L 15 23 >50(内聚破坏) 附录K 剥离强度(对管体) N/cm 附录K 最高运行温度 >3(内聚破坏 剥离强度 附录K >50(内聚破坏 对搭接部位聚乙烯层) 最高运行温度 >3(内聚破坏) 附录K Nem 1
GB/T23257一2017 表12(续 项 性能指标 试验方法 阴极剥离(最高运行温度,30d 附录D 20 mm 耐热水浸泡(最高运行温度,30d 附录P 剥离强度保持率(对底漆钢,对管体涂层) 75 附录K % 耐热水浸泡最高运行温度,120山) 附录P 无鼓泡、无剥离,膜下无水 附热老化'最高运行温度十20C,lo小y 剥离强度保持率(Po/P,对底漆钢,对管体涂层 附录Q >75 9.2补口施工准备 9.2.1补口施工开工前,应编制补口施工工艺规程APS),并按施工工艺规程进行工艺评定试验 PQT)验证
9.2.2补口施工工艺规程(APS)应根据设计要求、热收缩带(套)使用说明书、标准规范要求和补口施 工经验等进行编制
9.2.3补口施工工艺规程(APs)应通过工艺评定试验(PQT)进行验证 工艺评定试验(PQT)应在具有代表性的管道上进行,宜采用与实际工程用管同管径同壁厚同 a 防腐层的管道
b)工艺评定试验(PQ)应在涂敷管体防腐层的管道上至少3个试验口进行
试验口的长度应与 实际补口长度一致
试验口没有环向焊道时,应在试验口的中间加上一个模拟现场焊缝的环 形圈
工艺评定试验(PQT)使用的所有工具和设备类型应与实际补口施工中使用的相同 c d 补口区域进行加热时,应避免对管体防腐层产生起泡或剥离等可见破坏现象
工艺评定试验(PQT)期间的热收缩带(套)安装时间应与预估的现场补口时间相当
工艺评 定试验不在工程现场进行时,应考虑评定试验环境与实际施工环境和作业条件的差异
进行工艺评定试验(PQT)时的检验项目,试验方法和验收指标应符合本标准补口施工及检验 中的相关规定
工艺评定试验(PQT)结束后,应提交完整的评定试验结果报告
g.3补口施工 9.3.1当存在下列情况之一,且无有效措施时.不应进行露天补口施工 雨天、雪天、风沙天; a b) 风力达到5级以上; c 相对湿度大于85% d)环境温度低于0C
g.3.2补口施工可采用人工或机具安装方式
应采用无污染的加热方式对钢管表面补口部位进行加 热,大口径管道宜采用机具加热方式
加热不应造成钢管表面污染,不应损坏管体防腐层
12
GB/T23257一2017 g.3.3应对口进行清理,环向焊缝及其附近的毛刺焊渣、飞溅物,焊瘤等应清理干净
补口处的污 物,油和杂质应清理干净;防腐层端部有翘边、生锈、开裂等缺陷时,应进行清理
g.3.4在进行表面磨料喷砂除锈前,应使用无污染的热源将补口部位的钢管预热至露点以上至少5C 的温度
9.3.5补口部位的喷砂除锈应采用适宜的磨料,粒度均匀,且应干燥、清洁、无杂质
补口部位的表面 除锈等级应达到GB/T8923.1规定的Sa2%级,锚纹深度应达到40m一90m
除锈后应清除表面灰 尘,表面灰尘度等级应不低于GB/T18570.3规定的3级
9.3.6补口部位钢管表面处理与补口施工间隔时间不宜超过2h,表面返锈时,应重新进行表面处理 9.3.7补口搭接部位的聚乙烯层应打磨至表面粗糙,粗糙程度应符合热收缩带(套)使用说明书的 要求
9.3.8按热收缩带套)产品说明书的要求控制预热温度
加热后应采用接触式测温仪或经接触式测 温仪校准的红外线测温仪测温,应至少分别测量补口部位钢管表面、聚乙烯防腐层表面周向均匀分布 个点的温度,结果均应符合产品说明书的要求
用红外测温仪测温时,应根据校准结果对测量的数据 进行修正
应按照产品使用说明书和补口施工工艺规程的要求调配底漆并均匀涂刷,底漆的湿膜厚度应不 9.3.9 小于150Am
热收缩带加热,宜控制火焰强度,缓慢加热,不应对热收缩带上任意一点长时间烘烤 9.3.10 收缩过 程中用指压法检查胶的流动性,手指压痕应自动消失
9.3.11收缩后,热收缩带(套)与聚乙烯层搭接宽度应不小于100mm;采用热收缩带时,应采用固定 片固定,周向搭接宽度应不小于80mm
9.4补口质量检验 补口质量应检验外观、漏点及剥离强度等三项内容,检验宜在补口安装24h后进行 补口的外观应逐个目测检查,热收缩带(套)表面应平整、无皱折、无气泡,无空鼓,无烧焦炭化 a 等现象;热收缩带(套)周向应有胶粘剂均匀溢出
固定片与热收缩带搭接部位的滑移量不应 大于5mm; 每一个补口均应用电火花检漏仪进行漏点检查
检漏电压为15kV
若有漏点,应重新补口 b 并检漏,直至合格 补口后热收缩带(套)的剥离强度按附录K规定的方法进行检测
检验时的管体温度宜为 15C一25C,对钢管和聚乙烯防腐层的剥离强度都应不小于50N/em并80%表面呈内聚破 坏,当剥离强度超过100N/em时,可以呈界面破坏,剥离面的底漆应完整附着在钢管表面
每100个补口至少抽测一个口,如不合格,应加倍抽测
加倍抽测仍有不合格时,则对应的 00个补口应全部返修
9.5补伤 9.5.1补伤可采用辐射交联聚乙烯补伤片、热收缩带,聚乙烯粉末,热熔修补棒和粘弹体加外护等 方式
9.5.2对于小于或等于30mm的损伤,可采用辐射交联聚乙烯补伤片修补
补伤片的性能应达到热收 缩带的规定,补伤片对聚乙烯的剥离强度应不低于50N/cem
9.5.3修补时,应先除去损伤部位的污物,并将该处的聚乙烯层打毛
然后将损伤部位的聚乙烯层修 切圆滑,边缘应形成钝角,在孔内填满与补伤片配套的胶粘剂,然后贴上补伤片
补伤片的大小应保 证其边缘距聚乙烯层的孔洞边缘不小于100mm
贴补时应边加热边用子滚压或戴耐热手套用手挤 压,排出空气,直至补伤片四周胶粘剂均匀溢出
13
GB/T23257一2017 g.5.4对于大于30mm的损伤,可按照9.5.2的规定贴补伤片,然后在修补处包覆一条热收缩带,包覆 宽度应比补伤片的两边至少各大50 0mm g.5.5对于直径不超过10mm的漏点或损伤深度不超过管体防腐层厚度50%的损伤,在预制厂内可 用与管体防腐层配套的聚乙烯粉末或热熔修补棒修补,施工现场宜用热熔修补棒修补
g.5.6补伤质量应检验外观、漏点及剥离强度等三项内容 补伤后的外观应逐个检查,表面应平整,无皱折,无气泡,无烧焦碳化等现象;补伤片四周应粘 a 结密封良好
不合格的应重补; b 每一个补伤处均应用电火花检漏仪进行漏点检查,检漏电压为15kV
若不合格,应重新修 补并检漏,直至合格; 采用补伤片补伤的剥离强度按附录K规定的方法进行检验,管体温度为1525时的剥 离强度应不低于50N/em
涂敷厂生产过程的补伤,补伤应在白天进行,每天抽测不少于1处补伤的粘结力,不合格时,应 9.5.7 加倍抽查
加倍抽查仍出现不合格时,当天的补伤全部返工
现场施工过程的补伤,每20个补伤抽查一处剥离强度,不合格时,应加倍抽查
加倍抽查仍出 9.5.8 现不合格时,则对应的20个补伤应全部返修
10下沟回填 0.1防腐管下沟前,应用电火花检漏仪对管线全部进行检漏,检漏电压为15kVv
如有漏点应进行 修补至合格,并填写记录
0.2挤压聚乙烯防腐管的下沟回填应符合GB50369的规定 安全,卫生和环境保护 1 11.1涂敷生产的安全、环保应符合GB7692的要求
11.2钢质管道除锈、涂敷生产过程中,各种设备产生的噪声,应符合GB/T50087的有关规定 11.3钢质管道除锈,涂敷生产过程中,空气中粉尘含量不得超过GBZ1的规定
11.4钢质管道除锈、涂敷生产过程中,空气中有害物质浓度不应超过8mg/m' 11.5涂敷区电气设备应符合国家有关爆炸危险场所电气设备的安全规定,操作部分应设触电保护器
11.6钢质管道除锈,涂敷生产过程中,所有机械设施的转动和运动部位应设置保护
11.7防腐管的运输和施工过程中的安全、卫生和环境保护应符合GB50369等标准的规定
11.8所有操作人员应按规定配戴劳动防护用品
12 交工文件 交工文件应包括 防腐层原材料、防腐管的出厂合格证及质量检验报告; a 补口材料出厂合格证及质量检验报告 b 补口、补伤施工记录及检验报告; c d 建设单位所需的其他有关资料
14
GB/T23257一2017 录 附 A 规范性附录 环氧粉末的固化时间试验方法 A.1仪器设备 本试验需要的设备应符合下列要求 电热板,温度精度为士3c a b 金属板尺寸为150mm×150mm×25mm; 接触式温度计; c d 计时器; 拉延板(形状见图A.1) e 缺口(25土)mm×约0.9mm 图A.1拉延板 f 锻子(小钳子); g刮刀 h)通用小刀; 差示扫描量热仪(DSC)
A.2试验步骤 加热金属板并保持温度在规定温度士3c
A.2.1 A.2.2在金属板上用拉延板把环氧粉末迅速铺开,涂敷成一层薄膜,使膜厚在300um一400m之间, 当金属板上的粉末开始熔化时,立即起动计时器开始计时
A.2.3趁涂膜未完全胶化之前,用一把通用小刀或刮刀在膜上将涂膜划分为10条带状,如图A.2 所示
15
GB/T23257一2017 涂层 用刀划分涂层 金属板 图A.2涂层平板划线 A.2.4经过30s士3s以后,用通用小刀取下第1条涂膜带,并立即淬人冷水中
A25每经过0士3
,重复一次A24中的操作
注意应按从最初拉延开始的先后顺序取下,辫冷 并按顺序摆放
A.2.6使用一台“差示扫描量热仪"(DsC),按附录B的要求,测定涂膜的ATg(玻璃化温度的变化值) 或转化百分率c 绘出时间对ATg或时间对转化百分率的曲线
A.2.7 A.3试验结果 对应Tg为2C的时间或对应0%转化百分率的时间( 16
GB/T23257一2017 录 附 B 规范性附录 环氧粉末及其防腐层的热特性试验方法 B.1范围 本试验适用于测定环氧粉末及其防腐层的玻璃化转变温度(Tg)和反应热(H)
B.2仪器设备 本试验需要的设备应符合如下规定: 带制冷设备的差示扫描量热仪(DSC仪); aa b 分析天平,精确到0.1mg; c 试样密封器; d 带盖铝制试样皿
B.3试验步骤 B.3.1取10mg士1mg的环氧粉末或防腐层作试样,放人预先称好的试样皿中,盖上盖子密封试样并 称量,试样的质量精确到0.1mg
B.3.2将试样和参照物放人差示扫描量热仪的以干燥惰性气体保护的测量池中
B.3.3对环氧粉末试样,按下列程序完成其热扫描 以20C/min的速率对试样加热,从25C士5C加热到70C士5C,然后将试样急冷到25C士 b 以20C/min的速率对同一试样加热,从25C士5C加热到285C士10,然后将试样急冷 到25C士5C
以20/min的速率对试样加热,从25C士5加热到150笔士10
B.3.4对防腐层试样,按下列程序完成其热扫描 以20C/min的速率对试样加热,从25C士5C加热到l10C士5C,在11o C时保持 a 1.5min,然后将试样急冷到25C士5C 以20c/min的速率对同一试样加热,从25C士5加热到285C士10C,然后将试样急冷 b 到25C士5C 以20C/nmin的速率对试样加热,从25C士5加热到150C士10C
B.4 试验结果 B.4.1对应于B.3.3中程序b)和程序c)与B.3.4中程序b)和程序e)所得的每一个热扫描线,确定其相 应的T(midlroib)值,分别为Ts.Te、Te.Tg,I,值是玻璃化转变过醒晶度范围的中值
此外;,还 可确定相应的反应放热量H(见图B.1和图B.2)
17
GB/T23257一2017 AH b) Tg 温度/C 图B1对环氧粉末热扫描 AH 温度/ 图B.2对涂层热扫描 B.4.2对于防腐层,用式(B.1)计算出Tg值的变化 Tg=Tg,一Tg B.1 式中 ATg -Tg值的变化,单位为摄氏度(C); Tg 由B.3.4过程b)扫描得到的Tg值,单位为摄氏度(C); 18
GB/T23257一2017 Tg -由B.3.4过程c)扫描得到的Tg值,单位为摄氏度(C) B.4.3对于防腐层,用式(B.2)计算出固化百分率: H-sH ×100% H 式中: C -固化百分率; H 由B.3.3过程b)热扫描得到的反应放热量,单位为焦耳每克(/g); 公H-由B3.4过程b)热扫描得到的反应放热量,单位为焦耳每克J/g) 19
GB/T23257一2017 录 附 规范性附录) 防腐层的附着力测定方法 C.1仪器设备 本试验仪器设备应符合如下规定 烘箱或水浴,精度范围士3C; a b) 电火花检漏仪;量程0~30kV; 磁性测厚仪;量程0.01mm5mm,在1mm以下的分度值为1m;在1mm以上的分度值为 c 0.01mm; 耐热容器 d 温度计 e D 通用小刀
C.2试件 试件尺寸约为100mm×100mmX6mm, ,每组试件3件
试验步骤 C.3.1用电火花检漏仪对试件进行漏点检查,检漏电压按5V/m计算,无漏点的试件才可进行试验 将试件放人耐热容器内,加人足够的水,使试件充分浸没,加热至75C士3,恒温48h,取出试件
C.3.2当试件仍温热时,立即用小刀在涂层上划一约301 mm×15mm的长方形,划透防腐层至基材 在1h内将试件冷却至室温后,从长方形的任一角将刀尖插人防腐层下面,以水平推力撬剥涂层,连续 推进刀尖至长方形内防腐层全部撬离或显出明显的抗撬性能为止
C.4结果评定 按下列分级标准评定防腐层的附着力等级: 一涂层明显的不能橇利" a 1级 被撬剥的涂层小于或等于50%; b)2级 被撬剥的涂层大于50%,但涂层对水平力表现出明显的抗撬剥性; c 3级 涂层很容易被撬剥成条状或大块碎屑 d 4级 涂层成一整片被剥离下来
e 5级 以3个试件中级别最低的,作为该组试件的附着力级别
20
GB/T23257一2017 录 附 D 规范性附录 防腐层阴极剥离试验方法 D.1设备和材料 本试验的主要仪器设备和材料应符合如下规定: 可调直流稳压电源;0V~6V
a b 恒温装置;温控范围室温~100C,温控精度士3C 磁性测厚仪;量程0.01mm~5mm,在1mm以下的分度值为1Mm;在1mm以上的分度值 为0.01mm
d 电火花检漏仪;量程0~30kV
游标卡尺:量程02001 mm,精度0.02mm. ee fD 塑料圆筒:75mm. 辅助电极:可采用铂电极等惰性材料
g h) 参比电极:具有稳定的电位值且适用于试验温度条件,一般温度条件下可采用饱和甘汞电极 氯化钠:化学纯
D.2试件制备 D.2.1试件的规格和数量应符合如下规定 实验室制备的平板试件尺寸为100mm×100mm×6mm a b 管段加工成的试件尺寸为150mm×150mm 1×管壁厚,其中两个150 分别为沿管子轴向 mm 和圆周方向的切割宽度
热收缩带(套)补口试件可采用管状试件; 每组试件应不少于2个
Mm400 D.2.2按所检验防腐层的涂敷要求制备防腐层试件
单层环氧粉末防腐层厚度300 m,热 m400Am
收缩带底漆厚度300 D.3试验步骤 用电火花检漏仪对试件进行针孔检查,试件为单层环氧粉末或热收缩带(套)底漆时,检漏电压 D.3.1 为5V/um;试件为聚乙烯三层结构时,检漏电压为25kV;试件为热收缩带(套)防腐层时,检漏电压为 无针孔的试件才可用于试验
15kV
D.3.2在试件中部钻一个试验孔,钻透防腐层,露出基材
试件为单层环氧粉末或热收缩带(套)底漆 时,试验孔直径为3.2mm;试件为聚乙烯防腐层或热收缩带(套)防腐层时,试验孔直径为.4mm. D.3.3用密封胶将预制好的塑料圆简与试件同心粘结,形成以试件为底的试验槽,槽内加人浓度为 3%质量分数)的氯化钠溶液,至槽高的4/5处,试验过程添加蒸懈水保持液位,试验过程中,保持溶液 pH值在6~9范围
D.3.4将试件与直流稳压电源的负极相连接;将辅助电极插人溶液,并与直流稳压电源的正极连接 如图D.,1)
21
GB/T23257一2017 铂电极 甘汞电极 导电液 电压表 塑料桶 涂层 试验孔 试件 可调直流电源 防腐层阴极剥离试验示意图 图D.1 D.3.5使试件电位控制在一1.5V相对于饱和甘汞电极)
控制试验温度为规定的温度
试验周期结束,取下试件并冷却至室温.冷却时间不少于1h用小刀以试验孔为中心沿360"圆 D.3.6 周的八个等分,向外划割涂层,要划透防腐层,露出基材,划割距离至少为20mm(如图D,2)
图D.2在试件上划透涂层的放射线 D.3.7用小刀从试验孔处插人防腐层下面,以水平力沿划割线撬剥涂层,直至涂层表现出明显的抗撬 剥性为止
D.4试验结果 从试验孔边缘开始,测量每条划割线的剥离距离,并求出其平均值,即为该试件的阴极剥离距离
用两个平行试验试件阴极剥离距离的算术平均值表示,精确至0.1 mm 22
GB/T23257一2017 录 附 E 规范性附录 防腐层抗弯曲试验方法 B.1仪器设备 本试验仪器设备应符合如下规定 弯曲试验机:主要由压力机及弯曲角为2.5的弯曲模具(包括凸模和凹模)组成
其中凸模的 a 曲率半径按式(E.1)确定: R -22.431 E.1 式中 R 凸模半径,单位为毫米(mm); 试件有效厚度,单位为毫米(mm),包括试样实际厚度以及任何的曲度图E.1)
说明 -有效厚度; 实际厚度
图E.1试件有效厚度 低温箱;最低温度为一40C,控温精度士3C
b E.2试件 实验室喷涂粉末防腐层试件尺寸为200mm×25nmm×6mm
从试验管段或实际防腐管上截取 试件,并加工成25nmm×200mm×管壁厚,其中200mm为沿管子轴向切割长度,试件边缘应光滑无 缺陷
每组试件不少于3个
E.3试验步骤 E.3.1将试件放人低温箱,冷却至规定的试验温度并保持1h以上
B.3.2把试件放到弯曲试验机上进行弯曲试验,每个试件的弯曲试验应在30s内完成 E.3.3将弯曲后的试件在室温下放置2h以上,用目测法检查防腐层 23
GB/T23257一2017 E.4结果评定 对于环氧涂层,当3个试件的涂层均无裂纹时,该样品的弯曲性能为合格
对于聚乙烯防腐层,当3个试件聚乙烯均无开裂时,该样品的弯曲性能为合格
24
GB/T23257一2017 附录 F 规范性附录 氧化诱导期测定方法 F.1仪器设备 本试验仪器设备应符合如下规定 差示扫描量热仪(DsC);能记录热流或温差随时间的变化曲线,精度0.1min
aa b 自动气体开关;能在1min内迅速切换高纯氮气和氧气,并能控制气体流量
电子天平;精度0.1 c mg
F.2试验步骤 F.2.1将聚乙烯或胶粘剂压制成约250Hm的薄片
F.2.2切取5gl0mg样片,准确称量后放人DSC仪配套的无盖铝制堆蜗中
F.2.3将盛样堆蜗和参比堆蜗放人DsC仪的测量池中
F.2.4按下列设定进行DsC扫描 室温,通氮气5min,氮气流量设定为50ml士5ml a 以20C/min的速率对测量池加热,从室温加热到指定的测量氧化诱导期温度
加热过程中 b 持续通氮气流量为50ml士5mL
温度达到指定温度后,但溢,同时继续通卸气5min 将气体切换到氧气,流量设定为50ml士5mL,切换的瞬间为氧化诱导期测定的开始时间
d e 在流量为50ml士5ml的氧气环境下,恒温至出现快速放热曲线后至少2min
fD 测量结束,将气体切换到氮气,冷却测量池到室温
F3试验结果 扫描曲线的Y轴为热流,X轴为时间
延长基线,与氧化反应放热曲线相交,交点对应的时间即为指定温度下的氧化诱导期,如图F.1所示
l.5 1.0 0.5 0.0 时间零点 交点 _o. 20 40 60 80 00 120 时间/min 图F.1氧化诱导期的确定 25
GB/T23257一2017 附 录 G 规范性附录) 塑料含水率测定试验方法 G.1仪器设备 本试验仪器设备应符合如下规定 烘箱,精度范围土2C; a b)天平;精度1mg
G.2试验步骤 G.2.1将培养皿在105C士2C的烘箱中干燥0.5h,取出,在干燥器中冷却后称量
G.2.2在培养皿中加人约5g的样品,称量
G.2.3将盛有样品的培养皿放人105C士2C的烘箱中,烘3h,取出,放人干燥器中冷却后,称量
G.2.4每个试样进行两次测定
G.3结果 G.3.1含水率按式(G.1)计算 ,)/(m,一m,]x100% G.1 C=[(mi一m. S 式中 C 含水率; -培养皿质量,单位为克(g); m 培养皿和样品质量,单位为克(g); n -干燥后培养皿和样品质量,单位为克(g)
n G.3.2结果为两次测量的算术平均值
26
埋地钢质管道聚乙烯防腐层GB/T23257-2017标准解读
埋地钢质管道是一种常见的输送油气等物质的管道,而聚乙烯防腐层则是对于钢管进行防腐处理的重要手段之一。GB/T23257-2017标准作为埋地钢质管道聚乙烯防腐层的国家标准,对于保障产品质量、提高企业竞争力具有非常重要的意义。下面将从以下几个方面进行阐述:
一、标准的背景
随着工业的发展,埋地钢质管道在输送油气等物质的行业中得到了广泛的应用。然而,由于钢管容易受到环境因素的影响,如潮湿、腐蚀等,导致其使用寿命缩短,从而增加了企业的维修成本。为了延长钢管的使用寿命,提高产品质量,制定出了GB/T23257-2017标准。
二、标准的意义
GB/T23257-2017标准的颁布,使得埋地钢质管道聚乙烯防腐层的生产和检测都具备了统一的标准和规范。通过实施该标准,可以有效地保障埋地钢质管道的质量,降低企业的生产成本,提高其核心竞争力。
三、标准的应用
GB/T23257-2017标准主要适用于埋地钢质管道聚乙烯防腐层的生产、质量控制和检测等环节。在生产过程中,应根据该标准要求选择合适的原材料进行生产,并且掌握好专业的生产技术;在产品的质量控制和检测方面,应按照该标准要求进行各项测试和评估,确保产品的符合性。
四、标准的技术细节
GB/T23257-2017标准主要涉及聚乙烯防腐层的物理和机械性能测试、化学分析和耐受性测试等内容。具体包括:厚度测量、附着力测试、拉伸强度测试、热老化试验等各项指标。对于上述指标的测试,该标准也有具体的测试方法和要求。
结语
GB/T23257-2017标准的实施,为埋地钢质管道聚乙烯防腐层产品的生产和检测提供了更加系统化和规范化的指导和要求。企业应该积极采取相应措施,确保自身生产过程符合标准要求,提高产品质量和市场竞争力。
埋地钢质管道聚乙烯防腐层的相关资料
- 埋地钢质管道风险评估方法GB/T27512-2011
- 埋地钢质管道腐蚀防护工程检验GB/T19285-2014
- 基于风险的埋地钢质管道外损伤检验与评价GB/T30582-2014解读
- 埋地钢质管道聚乙烯防腐层GB/T23257-2017标准解读
- 深入了解埋地钢质管道阴极保护技术规范GB/T21448-2017
- 埋地钢质管道聚乙烯防腐层GB/T23257-2017标准解读
- 埋地钢质管道聚乙烯防腐层GB/T23257-2017标准解读
- 旅游餐馆设施与服务等级划分GB/T26361-2010
- 新鲜蔬菜贮藏与运输准则GB/T26432-2010
- 粮油加工环境要求GB/T26433-2010
- 设备工程监理规范GB/T26429-2010
- 实验室质量控制利用统计质量保证和控制图技术评价分析测量系统的性能GB/T27407-2010
- 原铝生产用煅后石油焦检测方法——二甲苯中密度的测定比重瓶法GB/T26310.1-2010
- 氧化镍化学分析方法中的电沉积法测定镍量——GB/T26305-2010
- 绝对发光强度分布的测量方法GB/T26184-2010
- 电气绝缘材料在辐射环境下的应用分级体系
- 无损检测射线照相底片数字化系统的质量鉴定第2部分:最低要求GB/T26141.2-2010
- 钢的低倍组织及缺陷酸蚀检验法GB/T226-2015
- 输送带覆盖层性能类别GB/T33525-2017
- 工业通信网络现场总线规范类型23:CC-LinkIE规范第3部分:CC-LinkIE通信行规GB/T33537.3-2017
- 埋地钢质管道聚乙烯防腐层GB/T23257-2017标准解读
- 里子绸GB/T22842-2017的意义和应用