GB/T34385-2017
辊式冷弯成形机械通用技术条件
Generaltechnicalspecificationsforcoldrollformingmachinery
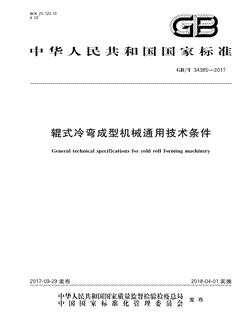
- 中国标准分类号(CCS)J62
- 国际标准分类号(ICS)25.120.10
- 实施日期2018-04-01
- 文件格式PDF
- 文本页数11页
- 文件大小755.62KB
以图片形式预览辊式冷弯成形机械通用技术条件
辊式冷弯成形机械通用技术条件
国家标准 GB/T34385一2017 辑式冷弯成型机械通用技术条件 speifeationsftorcoldrollftormingmachimery Generaltechnical 2017-09-29发布 2018-04-01实施 国家质量监督检验检疫总局 发布 国家标准化管理委员会国家标准
GB/34385一2017 辗式冷弯成型机械通用技术条件 范围 本标准规定了辑式冷弯成型机械的术语和定义、要求、试验方法、检验规则、标志、包装、运输和 贮存
本标准适用于将金属板连续压成金属压型板的冷弯成型机械(以下简称成型机
规范性引用文件 下列文件对于本文件的应用是必不可少的
凡是注日期的引用文件,仅注日期的版本适用于本文 件
凡是不注日期的引用文件,其最新版本(包括所有的修改单)适用于本文件
GB/T230.1金属材料洛氏硬度试验第1部分;试验方法(A,B,C,DE、F,G,H,K,N、T标 尺 GB/T1184一1996形状和位置公差未注公差值 GB/T1800.22009 产品几何技术规范(GPs)极限与配合第2部分:标准公差等级和孔、轴 极限偏差表 GB2894安全标志及其使用导则 GB/T3177产品儿何技术规范(GPS)光滑工件尺寸的检验 GB/T3766液压传动系统及其元件的通用规则和安全要求 GB/T4208一2017外壳防护等级(IP代码 GB5226.1一2008机械电气安全机械电气设备第1部分;通用技术条件 GB 6576机床润滑系统 气动系统通用技术条件 GB 7932 7935液压元件通用技术条件 GB 9969工业产品使用说明书总则 GB T 0923锻压机械精度检验通则 GB GB/T12754一2006彩色涂层钢板及钢带 T GB 12755建筑用压型钢板 GB T 13306标牌 GB 15706一2012机械安全设计通则风险评估与风险减小 GB/T1883 机械安全带防护装置的联锁装置设计和选择原则 GB/T23281锻压机械噪声声压级测量方法 JB/T5000.12重型机械通用技术条件第12部分涂装 装配通用技术要求 JB/T5994 JB/T8609锻压机械焊接件技术条件 JB/T9050.1圆柱齿轮碱速器通用技术条件 术语和定义 下列术语和定义适用于本文件
GB/T34385一2017 3.1 冷弯成型机械forminmachinery 通过顺序配置的多道次轧的作用,使金属板材/卷材按孔型道次顺序弯曲变形,以制成特定形状 断面的金属压型板的机械
3.2 轧辑roler 直接与金属板/带接触,通过孔型强迫金属板/带在横向截面上产生塑性变形
轧辑一般分为轴 部分和片部分
3.3 孔型pas 上下布置的扎辗组,其相对方向辑片外廓包络空间截面的形状 要求 4.1一般要求 4.1.1成型机应按规定程序批准的图样及技术文件制造
4.1.2成型机应具备技术文件所规定的使用性能和结构,造型和布局应考虑人类工效学的要求,应便 于使用,维修,装配拆卸和运输
4.1.3成型机零部件的材料应符合技术文件的规定
4.1.4煤接件应符合JB/T8609的规定
4.1.5用于成型机的配套件包括电气、液压和气动元件等)应符合技术文件的规定,具有产品合格证 明,并应与主机同时进行运转试验
4.1.6成型机出厂应保证完整性,并备有正常使用和维修的专用附件及备用易损件,特殊附件的供应 由供需双方商定
4.1.7成型机在保障安全与使用性能的前提下,应通过设计降低能源消耗
4.2环境适应性 成型机应能在以下非露天工作环境下正常工作: 温度:一10C40; a b 湿度空气相对湿度不大于95%(25C时) 工作电压;按用户要求设计电压士10%; c 工作场所不得有强磁场、电场干扰、腐蚀性气体和剧烈振动
d 4.3外观 4.3.1成型机表面不应有图样上未规定的凸起、凹陷、粗糙不平和其他损伤等缺陷,且不应有可能影响 使用性能和降低强度的缺陷存在
4.3.2镀件和发黑件等的色调应一致,保护层不应有脱落现象
4.3.3成型机的涂装应符合JB/T5000.12的规定
4.4装配 44.1成型机的装配应符合JB/T5994的规定 4.4.2成型机的外露件及外露结合面的边缘应整齐,不应有明显错位;电气、仪表等的柜,箱的组件的 门、盖周边与相关件的缝隙应均匀
4.4.3各种紧固措施应可靠,不应有松动现象
可能影响性能的紧固件应有可靠的防松措施
GB/34385一2017 4.4.4各种管路、电气线路应排列整齐,美观,不应与其他的零部件发生干涉摩擦,必要时应用管夹 固定
4.5结构与性能 4.5.1导向装置 成型机应设置人料定位导向装置
4.5.2机架 用于安装轧轭的机架焊接后应进行去应力处理,其强度和刚性应按所加工金属板最高屈服强度值 及最大厚度的2倍进行设计;整机装配后应能保证在20°的横向斜面上不倾翻
4.5.3机座 成型机的机座应能满足所加工金属板最高屈服强度值及最大厚度以上成型能力的强度和刚性,能 满足稳定性要求,装配前进行去应力处理
4.5.4轧辑 锯片的表面应根据所加工金属板的强度要求选择热处理工艺,表面硬度应不小于HRC45
4.5.4.1 4.5.4.2片的表面根据加工型材的要求宜采用电镀、发黑等表面处理
4.5.4.3孔型应保证带材输送平稳、顺畅,不得在压型板表面产生压伤、擦伤、划伤等影响使用的缺陷 4.5.4.4轭轴应有保证最大加工能力的强度和刚度
4.5.5 剪切装置 4.5.5.1剪切装置中刃口应进行热处理,硬度为HRC56HRC62,表面粗糙度应不大于Ral.6Am
4.5.5.2剪切装置在剪切过程中除剪切料头、料尾过程,其他剪切过程应无废料产生
剪切装置进行剪切工序后不得出现明显的毛刺
4.5.5.3 4.5.5.4成型后的压型板经剪切装置剪切后不应有明显变形
4.5.6传动系统 4.5.6.1基本要求 成型机成形应顺畅,无卡滞或阻碍
各传动部件运行平稳,无明显振动,无异常响声
液压,润滑系 统的油液不应有渗漏现象,气动系统不应有漏气现象
4.5.6.2减速器 减速器应符合JB/T9050.1的规定
4.5.6.3液压系统 成型机的液压系统应符合GB/T3766的规定
液压系统中所用的液压元件应符合GB/T7935的 规定 4.5.6.4气动系统 成型机的气动系统应符合GB/T7932的规定
4.5.6.5润滑系统 成型机的润滑系统应符合GB/T6576的规定
GB/T34385一2017 4.5.7数控系统 4.5.7.1 数控系统的硬件应稳定、可靠,符合系统通讯要求;软件的设计应简明、易懂、通用性强
4.5.7.2人机界面一般应包括工作参数设置、重要的生产工艺参数设置、设备故障和工艺操作提示等 内容
4.5.7.3数控系统应具有断电记忆功能和故障自诊断功能
4.5.7.4数控系统各位移坐标显示与实际位移的误差应符合技术文件的规定
其显示方法应直观,便 于操作者观察
4.5.7.5数控系统长度位移显示精度不应低于有关工作精度数值量级
4.5.7.6数控系统的最小设定量应能满足对工件工作精度修正的需要
4.6精度 4.6.1零部件加工精度 4.6.1.1轭轴轴身的圆跳动量应不大于0.030mm 4.6.1.2轭片厚度尺寸公差等级应符合GB/T1800.22009中IT7级的要求,片外径尺寸公差等级 应符合GB/T1800.2一2009中门级的要求
4.6.1.3轭片径向跳动量和轴向跳动量应不大于0.045mm
4.6.1.4成型机上基准面的平面度应不低于GB/T1184一1996中表B1中规定的8级要求
4.6.2成型机安装精度 4.6.2.1成型机上人料定位的装置,其定位精度不大于0.30mm
4.6.2.2成型机上孔型调整部件,其重复定位精度不大于士0.08mm 4.6.2.3成型机上轭轴安装孔之间的平行度应不低于GB/T1184一1996中表B3中规定的6级要求 同一轴上两孔的同轴度应不低于GB/T1184一1996中表B中规定的7级要求
4.6.2.4成型机上前后儡轴的平行度误差应不大于0,05mm
辐轴与成型中心线的垂直度误差应不大 于0.1mm
4.6.3工作精度 成型机加工后的压型板应符合表1的规定
表1工作精度 单位为毫米 允许偏差 序号 项目 截面高度<70 截面高度 70 波高 士1.5 士2.0 覆盖宽度 -2.0 波距 士2.0 横向剪切沿截面全宽 6,0(或1/100 侧向弯曲《在测量长度L,范围内 20.0 板长 5.0 注L,为测量长度,指板长扣除两端各0.5m后任选的10m长度,实际长度小于10m按实际长度进行折算
GB/34385一2017 4.7安全环保要求 4.7.1机械安全 4.7.1.1成型机应具备可靠的安全保护或防护装置,安全保护或防护装置的设计宜按GB/T15706一 2012中6.3.3的规定 4.7.1.2成型机的驱动部分应配置固定式防护装置
工作部位应配置移动式或固定式防护装置,防护 装置应能防止上肢接触到扎锯的旋转部位,助护装置关闭时应能易于观察到生产过醒
安全防护装置 宜采用联锁装置,带安全防护装置的联锁装置宜按GB/T18831的规定进行设计和选择
无法配备相 应的防护装置的部位,应采用警告标识进行警示
4.7.1.3成型机的醒目位置应配备启动,运行停止状态的声或光警示
4.7.1.4液压系统应设置可靠的压力安全保护装置 4.7.1.5正常操作时人员可接触到的外露部分应平整光滑,不应有可能导致人员伤害的尖锐棱角
4.7.1.6成型机控制部位和工作部位应设置紧急停止开关
紧急停止开关动作后不得自动启动
紧急 按钮的设置应符合GB5226.1的规定
4.7.1.7成型机工作时应有可靠的联锁保护措施
4.7.1.8成型机应有可靠的超载保护装置
当发生超负荷工况时,应能保证重要零件不至遭到损坏 4.7.2安全标志 成型机安全标志应符合GB2894的规定
4.7.3电气安全 4.7.3.1保护联结电路的连续性应符合GB5226.1一2008中18.2的要求
4.7.3.2动力电路导线和保护联结电路之间绝缘电阻应符合GB5226.1一2008中18.3的要求
4.7.3.3电气设备的所有电路导线和保护联结电路间耐压强度应符合GB5226.1一2008中18.4的 要求
4.7.3.4成型机所配置的电气设备其防护等级应不低于GB/T4208一2017中的IP54
4.7.4噪声 成型机空运转时的声音应正常,其A计权噪声声压级不应超过85dB(A),测量方法应符合 GB/T23281的规定
4.8标牌 4.8.1成型机的标牌固定位置应符合设计要求,并牢固,美观
4.8.2成型机应有标牌和润滑,操纵、安全等各种标牌和标志
标牌应符合GB/T13306的规定
4.9空运转要求 4.9.1成型机空运转中,各运动部件应运动灵活,无卡阻、碰撞,干涉及异常声响;各部件连接应牢固 无松动、断裂和变形现象
空运转后轧轴承温升不应超过35C,最高温度不应超过60C
液压系统温度应符合 4.9.2 GB/T3766的规定
4.10负荷试验要求 4.10.1成型机负荷试验中,各运动部件应运动灵活,无卡阻、碰撞、干涉及异常声响;各部件连接应牢
GB/T34385一2017 固,无松动、断裂和变形现象
4.10.2数控系统的各种控制程序功能和监测控制装置工作应正常,动作应灵敏可靠
负荷试验后加工的压型板应符合表1的规定 4.10.3 试验方法 5 5.1整机试验前要求 5.1.1原材料在投料前对配件或材料进行检验或验证
5.1.2成型机的零部件加工精度在装配前进行检验
5.1.3成型机的零部件安装精度在装配后进行检验
5.1.4 成型机的工作精度在进行负荷试验时进行检验 5.1.5空运转试验前应将成型机安装和调整到位,水平放置在平坦、平整的硬化地面 5.1.6试验应在非露天环境下进行
5.2外观和装配 成型机的外观和装配质量用目测和操纵进行检查
表面涂装按JB/T5000.12的规定进行试验
5.3结构与性能 5.3.1在负荷试验时按4.5的规定检查导向装置、机架、机座、轧、勇切装置、传动系统和数控系统
5.3.2辐片表面和剪切装置中刃口的硬度按GB/T230.1的规定进行试验
5.3.3表面粗糙度采用粗糙度对比样块进行检查
5.3.4剪切装置定长剪切长度误差采用钢卷尺进行检查
5.3.5成型机的减速器按JB/T9050.1的规定进行验证,液压系统按GB/T3766的规定进行验证,液 压元件按GB/T7935的规定进行验证;气动系统按GB/T7932的规定进行验证;润滑系统按GB/T6576 的规定进行验证
5.4数控系统检查 5.4.1在负荷试车过程中检查数控系统的硬件的稳定性、可靠性、系统通讯功能和软件设计是否简明 易懂、通用性强
5.4.2打开人机界面检查是否包括工作参数设置、重要的生产工艺参数设置、设备故障和工艺操作提 示等内容
5.4.3在负荷试验过程中强制断开电源,检查是否具有断电记忆功能,在系统出现故障时,是否具有故 障自诊断功能
5.4.4采用相应量具核对数控系统各位移坐标显示与实际位移的误差是否符合技术文件规定
其显 示方法是否直观,便于操作者观察
5.4.5在负荷试验过程中检查数控系统长度位移显示精度是否低于有关工作精度数值量级
5.4.6在负荷试验过程中验证数控系统的最小设定量是否能满足对工件工作精度修正的需要
5.5精度 按GB/T3177和GB/T10923的规定,检验成型机的零部件加工精度和安装精度
5.6安全环保检验 5.6.1机械安全试验 5.6.1.1成型机配置的安全防护装置用目测进行检查
GB/34385一2017 5.6.1.2紧急停止开关用实际操纵进行检查
5.6.1.3联锁保护和超载保护装置在负荷试验时进行检查 5.6.2安全标志 安全标志用目测进行检查
5.6.3电气安全检验 5.6.3.1 保护联结电路连续性按GB5226.1一2008中18.2的规定进行检验 5.6.3.2动力电路导线和保护联结电路之间绝缘电阻按GB5226.1一2008中18.3的规定进行检验 5.6.3.3电气设备的所有电路导线和保护联结电路间耐压强度按GB5226.1一2008中18.4的规定进 行检验
5.7标牌 按照GB/T13306的规定采用目测或测量进行检查
5.8空运转试验 5.8.1连续空运转时间2h,运转速度调整为最大设计速度的80%
无调速功能的按设计的最大速度 进行试验
5.8.2运转过程用目测检查成型机的各运动部件和连接部件
5.8.3按4.7.4的规定测量成型机的噪声声压值
5.8.4运转后用符合精度要求的温度计测量轧辐轴承及液压油箱内液压油的温度 5.9负荷试验 5.9.1试验用带材 试验用金属板应符合表2的规定 表2试验用材要求 序号 项目 用材要求 设计或供需双方约定的加工材料 材料品种 强度 按选定的材料品种中,选取中等屈服强度值的材料 延伸率 不低于所选取屈服强度型号所规定的限值 不小于设计或供需双方约定的最大厚度加工能力的60%;不大于设计或供 厚度 需双方约定的最小厚度加工能力的140% 宽度 压型板展开宽度,允许偏差应小于压型板精度要求 长度 能满足连续生产要求 特殊规定 金属板缺陷应不属于加工过程产生的损伤 注无设计或供需双方约定的,采用GB/T12754一2006规定的TD51D+Z彩涂板进行试验
5.9.2成型试验 成型机运转速度调整为最大设计速度的80%;无调速功能的,按设计的最大速度进行试验
连续
GB/T34385一2017 加工压型板长度不少于成型机的长度
运转过程用目测检查成型机的各运动部件和连接部件以及控制 系统的监测和控制功能
5.9.3压型板试验 成型机加工后的压型板精度按GB/T12755的规定进行
6 检验规则 6.1检验分类 检验分为出厂检验和型式检验
6.2出厂检验 每台成型机均应按表3规定的项目进行出厂检验,全部项目检验合格后方可出厂
6.3型式检验 6.3.1试验条件 有下列情况之一时,应进行型式检验: 新产品定型鉴定; a 老产品转厂生产时; b 正式生产的产品在结构、材料、工艺有较大改变,可能影响产品性能时; c 产品停产6个月以上再生产时 d 产品批量生产时每2年至少进行一次检验; e 国家质量监督机构提出要求时
6.3.2抽样 在出厂检验合格的产品中随机抽取1台进行检验 6.3.3判定规则 型式检验应按表3规定的项目进行检验,全部项目检验合格后为型式检验合格
6.4检验项目 成型机出厂检验、型式检验的检验项目见表3. 表3检验项目 序号 项目名称 要求 出厂检验 型式检验 外观 4.3 装配 4.4 结构与性能 4.5 精度 4.6 机械安全 4.7.l
GB/34385一2017 表3(续》 序号 项目名称 要求 出厂检验 型式检验 安全标志 4.7.2 4.7.3 电气安全 4.7.4 噪声 标牌 4.8 10 空运转要求 4.9 1 负荷试验要求 4.10 注:表中“、"表示进行此项检验
标志、包装、,运输和贮存 7.1产品标志 7.1.1成型机应在明显部位固定产品标牌及商标
7.1.2标牌标志的内容包括: 产品制造厂厂名或商标; aa 型号规格 b 执行标准号
c 7.2包装 7.2.1备件及工具应采用包装箱包装
随机技术文件应采用防潮材料密封
7.2.2随机技术文件包括 产品合格证; a b 产品使用说明书,并应符合GB/T9969的规定; 装箱单
c 7.3运输 成型机在运输过程中,不应有剧烈振动,撞击和倒放
运输时应注意防雨水、防尘埃和防止机械 损伤
7.4贮存 成型机应贮存在无腐蚀性气体,通风良好的室内或仓库内
辊式冷弯成形机械通用技术条件GB/T34385-2017
辊式冷弯成形机械是一种通过压力作用使金属板材等材料发生塑性变形,从而在一定角度范围内弯曲成所需形状的机械设备。该设备主要由上下两个滚轮和传动装置组成。
GB/T34385-2017标准规定了辊式冷弯成形机械的术语和定义、产品分类、型号和规格、技术要求、试验方法、检验规则以及标志、包装、运输和贮存等方面的内容,是保证辊式冷弯成形机械质量的重要标准。
该标准明确规定了辊式冷弯成形机械的技术性能、安全性能、使用要求等方面的具体要求。其中,技术性能包括机械结构、传动方式、控制系统、加工精度和加工速度等指标;安全性能包括电气安全、机械安全和使用安全等指标;使用要求包括操作要求、维护保养要求等指标。
在应用辊式冷弯成形机械时,需按照该标准进行正确选型、正确使用和正确维护保养,以确保设备的正常运行和延长设备寿命。
总之,GB/T34385-2017标准为辊式冷弯成形机械的设计、制造、检验、使用等方面提供了重要参考,对于推进我国辊式冷弯成形机械产业的发展和提高产品质量水平具有重要意义。