GB/T39208-2020
可伸缩式全回转舵桨装置安装与调试规程
Codeofpracticeforinstallationandcommissioningofretractableazimuththruster
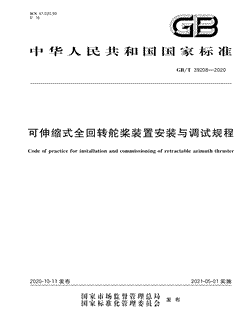
- 中国标准分类号(CCS)U16
- 国际标准分类号(ICS)47.020.99
- 实施日期2021-05-01
- 文件格式PDF
- 文本页数23页
- 文件大小1.72M
以图片形式预览可伸缩式全回转舵桨装置安装与调试规程
可伸缩式全回转舵桨装置安装与调试规程
国家标准 GB/T39208一2020 可伸缩式全回转舵桨装置安装与调试规程 Codeofpractieefrinstallatioandcommissiomingofretraetableuimuththruster 2020-10-11发布 2021-05-01实施 国家市场监督管理总局 发布 国家标涯花管理委员会国家标准
GB/39208一2020 目 次 前言 范围 2 规范性引用文件 术语和定义 安装前准备 4.1文件 4.2人员 .3工装、工具及设备 环境条件 4.5安装条件 安装质量要求 5.l安装精度要求 完整性 5.2 5.3焊缝质量 5.4密封性 5.5紧固性 安装程序 6.1安装流程图 6.2定位基准 6.3加工伸缩桨安装基座面 6.4伸缩桨底板安装 6.5导杆及水下支撑安装 6.6推进电机对中及安装 6.7下水后对中复查及最终安装 安装检验 调试 8 8.1 -般要求 8.2系泊调试 8.3航行调试 12 15 附录A资料性附录系泊调试记录表 20 附录B资料性附录)航行调试记录表
GB/39208一2020 前 言 本标准按照GB/T1.1一2009给出的规则起草
本标准由全国海祥船标准化技术委员会(SAC/TC12)提出并归口 本标准起草单位;中船黄埔文冲船舶有限公司、船舶工业综合技术经济研究院、广船国际有限 公司
本标准主要起草人:卓宁宁,李真刚、饶宇中,蒋勇刚、姜本俭,吴德梅,刘伟、戴雁航、徐柱、王银行、 陆小科、李万德、江金芬、张馨予
GB/39208一2020 可伸缩式全回转舵桨装置安装与调试规程 范围 本标准规定了可伸缩式全回转舵桨装置(以下简称“伸缩桨”)的安装前准备、安装质量要求,安装过 程、检验及安装后的调试规程等
本标准适用于可伸缩式全回转舵桨装置的安装与调试
规范性引用文件 下列文件对于本文件的应用是必不可少的
凡是注日期的引用文件,仅注日期的版本适用于本文 件
凡是不注日期的引用文件,其最新版本(包括所有的修改单)适用于本文件
GB/T340002016造船质量标准 CB/T31902019钢质船体结构焊接坡口型式及尺寸 CB/T3558一2011船舶钢焊缝射线检测工艺和质量分级 CB/T3559一2011船舶钢焊缝超声波检测工艺和质量分级 CB/T3802船体焊缝表面质量检验要求 船舶电气设备安装工艺 CB/T39092019 CB20112装船设备保护要求 术语和定义 下列术语和定义适用于本文件 3.1 可伸缩式全回转舵桨装置retractableazimuththruster 伸缩桨 通过液压油缸实现垂向伸缩并可做360"全回转的舵桨装置 注,主要由桨叶,导流罩,推进电机,推进电机底座,舱内导杆,弹性铀,伸缩桨安装底板,伸缩桨安装基座,水下支撑 基座等部件组成
根据推进电机与舵桨总体布置的不同,主要分为以下几种形式 l位于伸缩桨装置上方(立式)或者侧方(卧式),伸缩过程中,通过离合器或弹性 推进电机固定式:推进电机 轴等装置实现推进电机与伸缩桨装置的正常工作; b推进电机随动式:推进电机位于伸缩桨装置上方,伸缩过程中,推进电机跟随舵桨上下移动
推进电机固定立式伸缩桨典型布置如图1所示;推进电机固定卧式伸缩桨典型布置如图2所示;推进电机随动 立式伸缩桨典型布置如图3所示
GB/T39208一2020 说明 推进电机 推进电机底座; 弹性轴; -舱内导杆; 伸缩桨安装底板 伸缩桨安装基座, 水下导杆; 水下支撑基座 桨叶; 10- 导流罩.
图1推进电机固定立式伸缩桨典型布置图
GB/39208一2020 说明: 推进电机; 推进电机底座; 弹性轴; 舱内导杆; 伸缩桨安装底板; 伸缩桨安装基座 水下导杆; 水下支撑基座; 桨叶; 10 -导流罩
图2推进电机固定卧式伸缩桨典型布置图
GB/T39208一2020 帮士=班==需 说明 推进电机 推进电机底座; 弹性轴; -舱内导杆; 伸缩桨安装底板; -伸缩桨安装基座; 水下导杆; 8 水下支撑基座; 9 桨叶; 导流罩 10 图3推进电机随动立式伸缩桨典型布置图 安装前准备 4.1文件 伸缩桨安装前应准备好下列图样和工艺文件
GB/39208一2020 伸缩桨设备资料; a b 伸缩桨安装图 c 伸缩桨安装工艺文件; d)安装部位船体结构图及相关基座图 焊接原则工艺 e 4.2人员 伸缩桨安装的人员要求如下 a 从事伸缩桨安装的施工人员应熟悉相关的图样和工艺文件 b)施工人员应具备认定的相关专业技能资格,并经考核合格后持证上岗
4.3工装、工具及设备 4.3.1伸缩桨安装用的主要工装包括 吊运工装; a 定位工装 b c 调整工装 伸缩桨安装用的主要工具和设备包括量具,起重工具、对中工具、扭矩工具、打磨及焊接工具等; 4.3.2 工具及设备的量程、精度等级均应满足要求且在检定合格期内
4.4环境条件 4.4.1安装场所应照明充足、通风良好,且具有满足要求的作业空间等
4.4.2伸缩桨中各组成设备在仓储期间、装卸运输过程期间,均应按照CB20112的相关要求采取防 尘、,防潮、防震动、防火、防腐蚀、防油水滴落或喷射及机械损伤等保护措施 4.5安装条件 4.5.1推进电机、伸缩桨等设备可在整船成型后或总段阶段安装,船体建造状态应满足GB/T34000 2016中5.1的相关要求
4.5.2船体建造部门所提交的中心线、基线、基准点等相关技术数据和位置应经报验合格
4.5.3伸缩桨周边区域船体装焊和火工矫正结束,并报验合格
4.5.4伸缩桨安装基座面板加工及安装精度符合相关图样的要求,并报验合格 4.5.5推进电机基座的加工及安装精度符合相关图样的要求,并报验合格
4.5.6检查设备的完整性和外观,核对设备的安装尺寸,应符合相关图样要求
4.5.7检查设备文件和证书,应齐全,并做好记录
4.5.8核对推进电机、伸缩桨的旋转方向,应符合相关图样要求,并报验合格
4.5.9吊装应根据现场条件,提前制定合适的吊装方案,并经设备厂、船东及工厂相关安全部门认可
5 安装质量要求 5.1安装精度要求 伸缩桨安装精度要求应符合表1
GB/T39208一2020 表1伸缩桨安装精度要求 参数名称 允许偏差 备 注 相对于理论线 推进电机基座面、伸缩桨安装基座面与理论安装面高度偏差 士5mm 伸缩桨安装基座面与伸缩桨中心线垂直度 需符合设备厂要求 s1/1000 S1mm 密封圈接触区域,需符合设备厂要求 伸缩桨安装基座面板平面度 二2mm 非密封圈接触区域,需符合设备厂要求 推进电机输出端与伸缩桨输人端轴向偏差 符合设备厂要求 推进电机输出端与伸缩桨输人端径向偏差 符合设备厂要求 推进电机输出端与伸缩桨输人端曲折偏差 符合设备厂要求 5.2完整性 伸缩桨的安装应符合相关图样和工艺文件的要求
5.3焊缝质量 5.3.1焊缝尺寸应符合相关图样文件或CB/T3802的技术要求,焊接应严格按照相应接头的焊接工艺 规程进行,焊缝表面应成形均匀,焊道与焊道、焊道与母材之间应平滑过渡
5.3.2焊缝偏差应符合GB/T340002016中5.1.7的技术要求 5.3.3焊接坡口应符合相关图样文件或CB/T31902019第2章,第3章的技术要求
5.3.4装配及定位焊参照GB/T340002016中5.1.6和5.1.7.8相关要求进行,焊点长度及间距应 均匀
5.3.5焊缝不应存在裂纹,未焊透、夹杂、未填满、气孔、咬边、焊穿、焊坑和焊瘤等缺陷
射线检测质量 达到CB/T35582011规定的级,超声波检测质量达到CB/T3559一2011规定的级 5.4密封性 伸缩桨传动总成部位安装完成后应做气密性调试,试验压力参照各设备技术要求,一般不大于 0.05MPa,通过肥皂水或着色法检查密封面处,保压15min,无气泡产生,压力应无明显下降
5.5紧固性 设备各连接螺栓扭矩应满足相关图样文件或表2要求 安装程序 6.1安装流程图 见图4
GB/39208一2020 导杆及水下 加工伸缩浆 伸缩桨底板 定位基准 安装基座面 支撑安装 安装 推进电机 下水后对中复 对中及安装 查及最终安装 图4安装流程图 6.2定位基准 6.2.1根据船体理论线及伸缩桨安装图,定位伸缩桨及推进电机 6.2.2根据伸缩桨安装图,利用全站仪或通过打水平管的方法找出定位基准点,并做好标记 6.3加工伸缩桨安装基座面 6.3.1安装机加工设备,确保机加工设备中心线与伸缩桨安装基座中心线对正
6.3.2机加工设备安装合格后,针对伸缩桨安装基座面板进行平面加工
6.3.3伸缩桨基座面板加工完成后,平面度应满足相关图样文件或表1要求,且面板厚度应不小于理 论面板厚度
6.3.4基座面板密封圈安装区域按船体相关要求涂装
6.4伸缩桨底板安装 伸缩桨安装基座检验合格后,按照相关阁样文件要求安装伸缩浆底板及喘封间
6.4.1 利用顶升螺丝调整伸缩桨底板安装高度,伸缩桨底板下表面与安装基座上表面之间的间距应满 6.4.2 足规定间距值士2mm
6.4.3依据伸缩桨底板螺孔位置,配较螺栓孔
6.4.4清洁伸缩桨底板及安装基座的接触面,安装环氧挡板并进行环氧垫片的灌注
6.4.5拧紧伸缩桨底板安装螺栓,螺栓扭矩参照相关图样文件或表2要求
6.5导杆及水下支撑安装 6.5.1将舱内导杆上下两端分别与导杆底座、伸缩桨安装底板临时固定连接, 6.5.2进行全行程伸缩动作,伸缩过程中伸缩桨应无卡阻现象,且导杆与套筒四周间隙均匀,测量导杆 上下端部调整垫片厚度,加工并安装调整垫片
6.5.3根据水下导杆固定端的实际位置,测量定位水下支撑座,按照5.3的要求进行水下支撑座的焊 接,测量,加工并安装水下支撑座的调整垫片
6.5.4安装舱内导杆与导杆底座,水下导杆与水下支撑基座的连接螺栓,螺栓扭矩参照相关图样文件 或表2要求
GB/T39208一2020 表2螺栓扭矩表 单位为牛米 组1(8.8级 组2(不锈钢 组3(10.9级 组4(12.9级 螺栓 干式 湿式 干式 湿式 干式 湿式 干式 湿式 M3 1.75 0.87 0.66 1.55 1.25 0,9 2.l M4 2.85 4.8 1.5 3.6 2.1 M5 5.6 3.9 2.95 7.8 5,8 9,4 4.2 M6 9,7 7.3 6.8 5.2 13.5 10 6.5 12 17 39 M8 23.5 16.5 12.5 33 24 29 47 49 M10 35 33 25 66 79 59 87 57 43 M12 60 l15 86 135 00 M14 130 180 95 135 215 160 90 68 M16 195 145 185 135 275 200 330 240 M18 270 200 255 190 380 28o 460 340 M20 380 28o 350 265 530 390 640 480 M24 650 490 610 460 920 690 1100 800 660 1000 1200 M27 950 700 890 1350 1600 M30 1300 950 1200 910 1800 1360 2200 1600 M36 2250 1650 2100 550 3200 2400 3800 2800 M39 2900 2150 2700 2000 4l00 3000 4900 3600 M42 2700 8400 2500 5100 3800 6100 4500 3600 M48 5400 4000 5100 3800 7600 6700 9100 6800 6.6推进电机对中及安装 6.6.1采用百分表、塞尺等工具测量推进电机输出端与伸缩桨输人端轴向偏差,径向偏差及曲折偏 差,需满足相关图样文件或表1要求
6.6.2对中报验合格后,测量,制作并安装推进电机与推进电机底座的调整垫片
螺栓扭矩参照相关 图样文件或表2要求
6.7下水后对中复查及最终安装 6.7.1船舶下水后,重新复查对中数据,并再次完成全行程伸缩动作,确保伸缩过程中无卡阻现象
6.7.2复查合格后,安装联轴器,螺栓扭矩参照相关图样文件或表2要求
6.7.3伸缩桨收起至存储位置
6.7.4其他安全事项符合相关要求
安装检验 7.1通过核查设备资料、工艺文件等相关图样,检查设备型号、规格的正确性及设备的完整性
7.2利用平面测量仪、百分表、塞尺或其他有效测量工具,测量安装基座面平面度、垂直度、对中精度,
GB/39208一2020 其偏差应满足相关图样文件或表1要求
7.3采用磁粉、超声波或其他有效方法检查主要基座焊缝质量,应满足5.3的相关要求
7.4采用扭矩法、螺母转角法或其他有效方法检查连接螺栓的扭矩,应满足第日章及表2的相关要求
7.5使用欧姆表(电流表)检测推进电机接地情况,结果应满足CB/T39092019中第10章的相关 要求
8 调试 8.1 -般要求 8.1.1调试前,按照设备厂提供的检查表完成各项检查,并经设备服务工程师签字确认
8.1.2调试前,相关舱室通风、照明应满足安全要求
8.1.3调试前,油、气、水等辅助系统完整性、密性、清洁度等应报验合格
8.1.4调试使用的各种测试仪器和仪表,其精度等级应具有检验资质单位鉴定的合格证明
8.1.5在调试规程中应做好各种测试记录,记录好设备,元件各参数以及各测试报警点等,整理出有关 技术文件和报告.作为检验、交船的技术文件和资料提交
8.2系泊调试 8.2.1调试目的 在系泊状态下,检查伸缩桨及其附属设备的安装正确性、完整性以及主要功能、性能指标等是否符 合规定的使用要求
8.2.2调试用文件 系泊调试用文件主要如下 伸缩桨安装图; a 伸缩桨液压系统原理布置图 b 伸缩桨润滑系统原理布置图 c d 伸缩桨遥控和监测、报警项目汇总表; 伸缩桨遥控和监测、报警电气线路图 e 伸缩桨使用说明书 系泊调试大纲 g h)其他有关调试技术文件
8.2.3调试用仪表、仪器和工具 系泊调试用仪表、仪器和工具包括:万用表、绝缘表、钳表、转速表秒表、测温枪、对讲机、力矩扳手、 温度校验仪、压力校验仪、振动检验仪等工具
仪表、仪器和工具的量程、精度等级均满足要求且在检定 合格期内
8.2.4调试人员 系泊调试的人员要求如下 从事伸缩桨安装的系泊调试人员应熟悉相关的图样和调试文件 aa b)系泊调试人员应具备认定的相关专业技能资格,并经考核合格后持证上岗
8.2.5调试环境 系泊调试环境应满足如下要求:
GB/T39208一2020 a码头系缆设施安全可靠,调试水域无漂浮杂物; b调试水域开阔,水深满足伸缩要求; 相关设备舱室内格栅、铺板、扶手等铺设完整,垃圾和油污水清理干净,无安全隐患
c 8.2.6调试条件 8.2.6.1 船舶条件 系泊调试开始前船舶应达到如下条件 船舶状态符合系泊调试要求 a b)所有为伸缩桨服务的辅助系统应能可靠工作,调试期间冷却水、供气及供电应正常
8.2.6.2伸缩桨的调试条件 伸缩桨的系泊调试应满足如下条件 伸缩桨安装及密性报验合格,相关电缆敷设、管路安装验收合格,调试结束 a 为伸缩桨服务的辅助机械装置、泵及管系已经具备运转条件,液压系统油路清洁合格 b 调试用的滑油、液压油、冷却水、油脂等,应符合装置使用说明书的要求并加注完毕; c d 伸缩桨推进电机及其遥控、监渊.报瞥装置应调试完毕, 伸缩桨的舵角指示器按要求调整完毕并锁定(适用于调距桨)
e 8.2.7调试 8.2.7.1 调试项目 系泊调试项目一般为: 本地控制系统接口调试; a b 远程遥控系统接口调试; c 辅助系统调试; 锁轴装置效用调试; d 伸缩桨全回转效用调试; 伸缩桨伸缩效用调试 螺距校准调试(适用于调距桨); g 转速校准调试 h 报警及监测功能调试; 负荷调试 i 控制位置转换调试
k 8.2.7.2本地控制系统接口调试 利用本地控制按钮,检查伸缩桨以下功能 启动各辅助泵组,应能正常启停; a b 进行伸缩桨全回转动作,系统应能正常响应; 进行伸缩桨调距动作,系统应能正常响应(适用于调距桨); c d 进行伸缩桨伸缩动作试,系统应能正常响应; 进行锁轴功能调试,系统应能正常响应
8.2.7.3远程遥控系统接口调试 利用遥控控制按钮,检查伸缩桨如下功能: 10
GB/39208一2020 启动各辅助泵组,应能正常启停; a b 分别在随动和非随动模式下,进行伸缩桨全回转动作,系统应能正常响应 分别在随动和非随动模式下,进行伸缩桨调距动作,系统应能正常响应(适用于调距桨); e d)进行伸缩桨伸缩动作,系统应能正常响应; 进行锁轴功能调试,系统应能正常响应 e fD 在动力定位模式、单手柄联合操作模式和自动导航模式下,分别进行伸缩桨的回转、调螺距和 伸缩动作,系统应能正常响应
8.2.7.4辅助系统调试 辅助系统主要包括全回转液压系统、滑油润滑系统、调距液压系统(适用于调距桨)和伸缩液压系统 等,调试过程主要如下 测量各润滑油泵,液压泵等电气设备试验前、后的冷,热态绝缘电阻 a 在规定工况下,启动相关系组,连续运转不小于30 b 调试中测量系统的工作压力,油温、 m1n
水温、推进电机起动电流、工作电流、工作电压、转速等参数,应满足设备参数及相关图样参数 要求; 检查泵组、管系和仪表有无异常振动、响声,发热和泄漏现象 d)按设计要求调整泵和管路上安全阀的动作压力,连试3次(阀可在车间内完成调试),均应正确 可靠,合格后铅封 参照附录A中表A.1填写调试结果
8.2.7.5锁轴装置效用调试 锁轴装置效用调试过程主要如下 检查锁轴装置状态指示,应与实际状态一致; aa 进行锁轴装置同伸缩桨启动装置的联锁效能试验,当锁轴装置处于锁止状态时,伸缩桨应无 b 法启动 进行锁轴效用试验,在伸缩桨停止工作时,启用锁轴装置,检查伸缩桨的工作状态,应贴合紧密 无间隙或松动
参照表A.2填写调试结果
8.2.7.6伸缩桨全回转效用调试 伸缩桨全回转效用调试过程主要如下 分别利用本地及远程控制按钮进行伸缩桨全回转动作,检查响应是否正常 a b)检查伸缩桨回转方向与指示灯显示是否一致 分别利用本地及远程控制按钮进行应急停车操作,伸缩桨应可以实现停车
c 参照表A.2填写调试结果
8.2.7.7伸缩桨伸缩效用调试 伸缩桨伸缩效用调试过程主要如下: 调试前伸缩桨应处于伸缩模式状态; aa b 调试前检查伸缩桨应处于停车位置; 分别利用本地及远程控制按钮进行伸缩调试,伸出到位后,检查伸缩桨指示是否正常; c d 分别利用本地及远程控制按钮进行应急停车操作,伸缩桨应可以实现停车; 如设置有离合器,在伸缩桨伸缩过程中离合器应处于脱离状态,离合器使用应正常
1
GB/T39208一2020 参照表A.2填写调试结果
8.2.7.8螺距校准调试(适用于调距桨 螺距校准调试过程主要如下: a 进行伸缩桨调螺距调试,检查功能是否正常,检查螺距指示信息是否与实际一致; b)检查螺距指示、零位指示是否正常
参照表A.2填写调试结果
8.2.7.9转速校准调试 检查转速指示信息是否与实际一致 参照表A.2填写调试结果
8.2.7.10报警及监测功能调试 报警及监测功能调试包括对全回转液压系统、滑油润滑系统、调距液压系统(适用于调距桨)密封 各辅助泵组及其他功能性报警监测功能进行模拟检测系统温度、压力、液位的高低位报警,过载报警、,失 电报警等的调试
参照表A.3填写调试结果
8.2.7.11 负荷调试 负荷调试过程主要如下 调距桨:在零螺距下,装置运转不小于0.5h,记录各运行参数; a b) 定距桨;在最小转速下,装置运转不小于0.5h,记录各运行参数, 在25%负载下,伸缩桨运转不小于1h,记录各运行参数; c 以上试验合格后,在50%负载情况下,伸缩桨运行2h,稳定后,记录各运行参数;检查各系统 d 的运行情况是否良好
参照表A.4填写调试结果
注,25%,50%负载调试,若码头缆桩实际承载能力不满足负荷试验要求,可在航行试验阶段进行
8.2.7.12控制位置转换调试 控制位置转换调试包括对伸缩桨本地控制面板与各遥控控制台前架控台、后驾控台、两翼驾控台 之间的转换功能进行调试,调试过程主要如下 a 各遥控控制站与本地控制面板之间的操舵转换应能方便迅速地进行,且不允许引起伸缩桨运 行状态的明显变化; b 在任何情况下只有一个控制站有效,且在任何控制站均能显示当前控制站的位置;转换时备 指示灯、蜂鸣器均应按规定发出声光信号
参照表A.5填写调试结果
8.3航行调试 8.3.1调试目的 在航行状态下,检查伸缩桨及其附属设备的工作协调性、稳定性、安全性以及主要功能、性能指标等 是否符合规定的使用要求
12
GB/39208一2020 8.3.2调试用文件 航行调试用文件主要如下 伸缩桨安装图; a b)伸缩桨液压系统原理布置图 伸缩桨润滑系统原理布置图; c 伸缩桨遥控和监测、报警项目汇总表; d 伸缩桨遥控和监测报警电气线路图 e 伸缩桨使用说明书 相关航行调试技术文件
g 8.3.3调试用仪表、仪器和工具 航行调试用仪表、仪器和工具包括:万用表、绝缘表、钳表、转速表、秒表,测温枪、对讲机、力矩扳手、 温度校验仪、压力校验仪、振动检验仪等工具
仪表、仪器和工具的量程、精度等级均满足要求且在检定 合格期内
8.3.4调试人员 航行调试的人员要求如下 从事伸缩桨安装的航行调试人员应熟悉相关的图样和调试文件; a b)航行调试人员应具备认定的相关专业技能资格,并经考核合格后持证上岗
8.3.5调试环境 调试应满足以下环境要求 航行水域开阔,水深满足调试要求,水域无漂浮杂物 a 海况符合设计相关规定要求; b 相关设备舱室内格棚、铺板、扶手等铺设完整,垃圾和油污水清理干净,无安全隐患
c 8.3.6调试条件 航行调试应满足以下条件 伸缩桨系泊调试合格; a b 船舶调试状态应满足设计相关规定要求
8.3.7调试 8.3.7.1 调试项目 航行调试项目如下 a)负荷调试; b) 额定功率校准调试 螺距校准调试(适用于调距桨); c d)调距及调速时间测定调试 控制位置转换调试
e 8.3.7.2负荷调试 负荷调试过程主要如下 13
GB/T39208一2020 伸缩桨可在75%、100%等负载工况下,各运行2h,记录各运行参数,并检查系统的运行情况 a 是否良好; D)在满负载工况下,进行舵桨全回转调试,检查舵桨装置相应及运转是否正常
参照表A.4填写调试结果
8.3.7.3额定功率校准调试 额定功率校准调试过程主要如下 在船舶最大航速,满负荷工况下,记录正倒车状态下的额定功率、最大转速; a b)检查负载控制功能是否正常; c 进行降螺距功能调试(适用于调距桨 参照附录B中表B.1填写调试结果
8.3.7.4螺距校准调试(适用于调距桨 在满负荷工况下,重新检查伸缩桨螺距指示是否正常,并标定螺距0位和100%螺距
参照表B.2填写调试结果
8.3.7.5调距及调速时间测定调试 针对调距桨,测量并记录以下时间 8.3.7.5.1 a) 零螺距调至全螺距时间; b 全螺距调至零螺距时间 零螺距调至全速倒车时间 e d 全速倒车调至零螺距时间
8.3.7.5.2针对定距桨,测量并记录以下时间: 停止状态至最大转速的时间 a b 最大转速至停止状态的时间 停止状态至全反推的时间 c d 全反推至停止状态的时间
8.3.7.5.3参照表B.3填写调试结果
8.3.7.6控制位置转换调试 在航行状态满负荷工况下,按照8.2.7.8进行控制转换功能调试
参照表A.5填写调试结果
14
GB/39208一2020 附 录 A 资料性附录 系泊调试记录表 A.1辅助系统调试数据记录见表A.1
表A.1辅助系统调试数据记录表 调试项目 测量值 0"360"全回转时间/s 正转: 反转: 系统启动压力/MPa 系统工作压力/MPa 安全阀压力/MPa 油温/C 冷却水温度/C 环境温度/C 在应急停车模式或者船速小于7kn情况下测量液压系统驱动压力值 全回转液压系统 正转0°~30"/MPa 30?/MP 反转0"~ 电机起动电流/A 电机工作电流/A 电机工作电压/V 电机转速/(r/min 电气控制箱绝缘电阻试验前/MQ 电气控制箱绝缘电阻试验后/MQ 滑油系统工作压力/MPa 系统静压力/MP% 安全阀压力/MPa 油温/ 冷却水温度/C 环境温度/C 滑油润滑系统 电机起动电流/A 电机工作电流/A 电机工作电压/V 电机转速/r/min 电气控制箱绝缘电阻(试验前)/MQ 电气控制箱绝缘电阻(试验后/MQ 15
GB/T39208一2020 表A.1(续) 调试项目 测量值 调螺距时间0%一100%正转/s 调螺距时间0%100%反转/s 系统启动压力/MPa 系统工作压力/MPa 安全阀压力/MPa 油温/ 冷却水温度/ /C 环境温度 舵桨最大转速下,测量各螺距区间系统工作压力 反转/MPa 正转/MPa 调距液压系统适用于调距桨 025% T -25% >25%50% >25%~50% >50%75% >50%~75% >75%100% >75%~l00% 电机起动电流/ 电机工作电流/A 电机工作电压/V 电机转速/(r/min 电气控制箱绝缘电阻(试验前/Mn 电气控制箱绝缘电阻试验后/MQ 舵桨伸出到位时间/s 伸出时系统工作压力/MPa 舵桨收缩到位时间/s 收缩时系统工作压力/MPa 安全阀压力/MPa 油温/ 冷却水温度/C 伸缩液压系统 环境温度/C 电机起动电流/A 电机工作电流/A 电机工作电压/V 电机转速/r/min 电气控制箱绝缘电阻试验前/MQ 电气控制箱绝缘电阻试验后/Mn 调试人员: 调试日期: 16
GB/39208一2020 伸缩桨效用调试检查表见表A.2
表A.2伸缩桨效用调试检查表 序号 项目 调试内容 结果 检查在装置伸缩过程中锁轴装置是否处于脱离状态 锁轴装置 效用调试 检查锁轴装置是否可以正常使用 利用控制按钮进行舵桨全回转调试,检查响应是否正常 伸缩桨 全回转效检查舵桨回转方向与指示灯显示是否一致 用调试 检查舵桨停车位置指示是否正常 检查装置是否处于伸缩模式状态 伸缩桨 检查舵桨是否处于停车位置 伸缩效 进行舵桨伸出调试,伸出到位后,检查舵桨指示是否显示为伸出状态 用调试 进行舵桨缩进调试,利用应急停车按钮,检查装置是否可以实现停车 利用调距按钮进行舵桨调螺距调试,检查功能是否正常 螺距校准 调试(适用检查调距指示是否正常 于调距桨 检查螺距零位指示是否正常 进行舵桨转速调试,检查功能是否正常 转速校 准调试 检查转速指示是否正常 调试人员: 调试日期: A.3报警及监测功能调试记录见表A.3 表A.3报警及监测功能调试记录表 序号 项目 调试内容 结果 油压力低报警 油滤器堵塞报警 全回转液压系统 油温高报瞥 油液位低报警 油压力低报警 油滤器堵塞报警 滑油润滑系统 油温高报警 油液位低报警 袖压力低报警 调距液压系统 油滤器堵塞报警 10 适用于调距桨 11 油温高报警 12 气源压力低报警 13 密封报警 气源压高低报警 l4 油液位低报警 17
GB/T39208一2020 表A.3(续) 序号 项目 调试内容 结果 断相 15 各辅助泵组 失电报警 l6 17 过载报警 18 失电报警 19 回转模式失效报警 20 调距模式失效报警 其他功能性监测 伸缩模式失效报警 21 22 刹车失效报警 舵桨存储状态异常报警 23 调试人员 调试日期 A.4负荷调试记录见表A.4
表A.4负荷调试记录表 冷却水冷却水冷却器冷却器 运行 液压泵 工作 轴承 环境 转速 进口 出口 进口 出口 负荷 时间 组油温 压力 温度 温度 备注 r/min 温度 温度 油温 油温 /min /MPa C 零螺距 15 最低 系泊调试进行 30 转速 15 25% 系泊或航行 30 负载 调试进行 45 60 20 40 50% 系泊或航行 调试进行 负载 60 90 120 18
GB/39208一2020 表A.4(续 冷却水冷却水冷却器冷却器 运行 液压裂 工作 轴承 环境 转速 进口 出口 进口 出口 负荷 时间 组油温 压力 温度 温度 备注 /(r/min) 温度 温度 油温 油温 /MPa /min " 20 40 75% 负载 60 90 120 结果 20 舵桨全 40 100% 回转及 负载 6o 响应是 否正常" 90 120 调试人员: 调试日期: A.5控制位置转换调试记录表见表A.5
表A.5控制位置转换调试记录表 结果 序号 控制位置 调试要求 系泊调试 航行调试 声、光信号 前驾控台一本地控制面板 设备运行状态 声、光信号 后驾控台-本地控制面板 设备运行状态 声,光信号 两翼驾控台--本地控制面板 设备运行状态 声、光信号 本地控制面板-前驾控台 设备运行状态 声、光信号 本地控制面板-后驾控台 设备运行状态 声,光信号 本地控制面板-两翼驾控台 设备运行状态 调试人员" 调试日期 19
GB/T39208一2020 附 录 B 资料性附录) 航行调试记录表 额定功率校准调试记录见表B.1
B.1 表B.1额定功率校准调试记录表 序号 项目 调试项目 测量值 额定功率/kw 倒车最大功率/kw 额定功率 校准调试 正车最大转速/(r/mim) 倒车最大转速八 r/min 调试人员 调试日期 B.2螺距校准调试记录见表B.2 表B.2螺距校准检查表 序号 项目 调试内容 结果 再次检查零螺距设置是否正确 螺距校准调试 适用于调距桨 检查螺距指示是否匹 调试人员: 调试日期 调距及调速时间测定调试记录见表B.3
B.3 表B.3调距及调速时间测定记录表 序号 调试内容 结果/s 零距调至全螺距时间 全螺距调至零螺距时间 调距桨 零螺距调至全速倒车时间 全速倒车调至零螺距时间 停止状态至最大转迷的时间 最大转速至停止状态的时间 定距桨 停止状态至全反推的时间 全反推至停止状态的时间 调试人员: 调试日期: 20
可伸缩式全回转舵桨装置安装与调试规程
引言
可伸缩式全回转舵桨已经成为现代船舶的重要推进方式之一,其具有灵活性强、效率高等优点。然而,由于其结构复杂、安装难度较大等原因,对于普通操作人员来说,往往需要进行专业培训才能进行操作。
一、安装规程
1. 安装前准备
在安装可伸缩式全回转舵桨前,需要对其进行相关检查和准备工作。其中包括:
- 确认船舶设计方案和图纸,并确认所需安装位置;
- 检查舵桨本体是否符合相关标准要求;
- 准备好各种安装工具和设备。
2. 安装过程
(1)将舵桨本体悬挂在安装位置,调整好水平度;
(2)根据船舶设计方案,在舵桨本体上进行切割,并将可伸缩式部分插入其中;
(3)安装伸缩机构和回转机构,注意不要损坏舵桨本体;
(4)进行调整和测试,确保舵桨的安装和运行正常。
二、调试规程
1. 调试前准备
在进行可伸缩式全回转舵桨的调试前,需要对其进行相关检查和准备工作。其中包括:
- 确认船舶设计方案和图纸,并检查舵桨本体和机械设备是否符合相关标准要求;
- 准备好各种调试工具和设备。
2. 调试方法
(1)启动船舶系统,并使舵桨旋转到最大角度;
(2)通过控制系统,逐渐调整全回转舵桨的角度和速度;
(3)进行相应的测试,例如推力测试、转向测试等;
(4)根据测试结果,适当调整舵桨的角度和速度;
(5)继续进行测试,直至舵桨运行稳定,达到预期效果。
三、注意事项
在进行可伸缩式全回转舵桨的安装和调试过程中,需要注意以下几点:
- 必须按照相关标准和规程进行操作,确保安全和有效性;
- 在操作前,必须对所需设备和工具进行全面检查和准备;
- 在选择安装位置时,要考虑舵桨的重量和安全性;
- 在调试过程中,要进行充分的测试和监测,确保舵桨正常运行。
四、总结
可伸缩式全回转舵桨装置是现代船舶推进技术的重要代表之一,安装规程和调试规程是可伸缩式全回转舵桨装置使用过程中非常重要的环节,必须严格按照相关规程操作。在安装过程中,需要进行充分的准备工作和检查,确保舵桨安装的位置合理、安全性和有效性。在调试过程中,需要逐步调整舵桨的角度和速度,进行相应测试并根据测试结果进行调整。 二,为了更好地保证舵桨的正常运行,还需要注意以下事项:必须按照标准和规程进行操作;在操作前必须对设备和工具进行全面检查和准备;在选择安装位置时要考虑舵桨的重量和安全性;在调试过程中要进行充分的测试和监测,确保舵桨正常运行。 三,以上是可伸缩式全回转舵桨装置安装和调试规程的基本内容,希望能够对专业人士有所帮助,提高操作水平和效率。