GB/T33935-2017
立磨磨盘、磨辊衬板(辊套)修复规范
Verticalrollermill—Repairspecificationsforlinersofthegrindingtableandliners(rollsheath)ofthegrindingroller
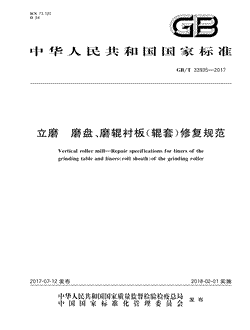
- 中国标准分类号(CCS)D94
- 国际标准分类号(ICS)73.120
- 实施日期2018-02-01
- 文件格式PDF
- 文本页数6页
- 文件大小431.08KB
以图片形式预览立磨磨盘、磨辊衬板(辊套)修复规范
立磨磨盘、磨辊衬板(辊套)修复规范
国家标准 GB/T33935一2017 立磨磨盘磨辑衬板(辑套)修复规范 vertiealrolermil一Repairspeeifieatonstorlmersfthe grindingtahleandliners(rollsheath)ofthegrindingroller 2017-07-12发布 2018-02-01实施 国家质量监督检验检疫总局 发布 国家标准化管理委员会国家标准
GB/33935一2017 立磨磨盘、磨辑衬板(辑套)修复规范 范围 本标准规定了立磨磨盘、磨辗衬板(锯套)修复的术语和定义、修复技术要求、修复质量检测,包装、 运输和贮存
本标准适用于立磨磨盘、磨衬板(套)的修复
规范性引用文件 下列文件对于本文件的应用是必不可少的
凡是注日期的引用文件,仅注日期的版本适用于本文 件
凡是不注日期的引用文件,其最新版本(包括所有的修改单)适用于本文件
GB/T984堆焊焊条 GB/T3375焊接术语 GB/T12470埋弧焊用低合金钢焊丝和焊剂 GB/T13384机电产品包装通用技术条件 GB/T17493低合金钢药芯焊丝 GB/T17854埋弧焊用不锈钢焊丝和焊剂 JB/T3223焊接材料质量管理规程 B/T5000.3重型机械通用技术条件第3部分;焊接件 术语和定义 GB/T3375界定的以及下列术语和定义适用于本文件
3.1 磨盘衬板tableliner 与物料直接接触的磨盘衬板,宜采用符合堆焊耐磨材料结构和高铬铸铁或镍硬铸铁材料
3.2 磨棍衬板rollliner 与物料直接接触的磨辐衬板,采用高铬铸铁或镍硬铸铁材料,分块结构或整体结构
3.3 磨辑辑套rollsheath 与物料直接接触的磨辐辐套,采用本体为铸钢件加堆焊耐磨材料的整体结构
3,4 在线修复on-linerepair 在磨盘、磨锯衬板(辐套)不拆出设备本体的情况下,在磨内将衬板或辐套磨损、损坏部位进行修复, 使耐磨部件恢复原有尺寸和性能的修复方法
3.5 离线修复ofr-linerepair 在磨盘、磨辐衬板(辐套)拆出设备本体的情况下,在具有对磨损、损坏部位修复能力的厂家进行修
GB/T33935一2017 复使耐磨部件恢复原有尺寸和性能的修复方法
修复技术要求 4.1修复方案 4.1.1立磨磨盘、磨辐衬板(辐套)的修复包括复合堆焊结构修复、整体高铬铸铁或镍硬铸铁材料(含分 块结构)修复
复合堆焊结构、整体高络铸铁或粲硬铸铁材料(含分块结构)修复应采用自动焊机堆焊的方法对 4.1.2 磨损、损坏部位进行修复,包括埋弧堆焊或明弧堆焊等
4.1.3对于局部小区域磨损、损坏部位可采用手工焊条电弧煤、手工半自动焊等方法堆焊修复
4.1.4对于复合堆焊结构如核对已磨损到铸钢件母体,应先进行打底层、过渡层的堆焊,然后再进行硬 面层堆焊
4.1.5对于衬板或轭套本体存在无法消除的影响焊接质量的缺陷时,应对衬板或套进行整体更换
4.2堆焊材料要求 4.2.1自动堆焊时,宜使用以钢带内包敷合金粉末轧制和拉拔而成的药芯焊丝,药芯焊丝的质量应符 合GB/T17493的规定
丝的药粉应填充均匀,填充率的变化不应大于1%
4.2.2堆焊前应对耐磨件基材的化学成分和力学性能进行核查,堆焊材料的化学成分应与耐磨件基材 材质成分相匹配,应满足堆焊后耐磨件的使用性能 4.2.3堆焊材料的形态应便于自动化、机械化、连续的操作方式,并与所使用的堆焊设备相匹配
4.2.4堆焊材料应有制造厂的质量合格证书,其质量应符合JB/T3223的要求
4.2.5药芯焊丝自动堆焊时,其熔敷率应控制在85%以上
埋弧自动焊时应保证焊剂与焊丝的配套使 用,焊剂的质量应符合GB/T17854和GB/T12470的规定
堆焊中使用的焊条应符合GB/T984的 要求
4.3施工模式 4.3.1施工模式分为在线修复和离线修复两种
4.3.2在线修复或离线修复的施工模式取决于耐磨件运转时间、磨损程度,堆焊时机、堆焊风险、产品 产量、物料性能、耗电量、费用和用户要求等的综合因素
4.3.3本施工模式和修复方法是针对离线修复的,在线修复应参照执行
4.4修复前的检测 4.4.1磨损后的磨盘、磨辐衬板(套)在修复前,首先用规尺按照图表进行磨损件的尺寸检查,判断磨 损程度,对复合堆焊结构核对是否磨损到铸钢件母体 4.4.2通过目视检查或探伤检验,确定磨损面是否可以进行堆焊处理
如存在贯通性裂纹、局部基体 磨穿、基体厚度过薄等可能导致工件整体破坏的缺陷时,不宜进行堆煤
4.4.3对确定可进行堆焊修复的磨盘、磨衬板(辗套),应核实堆炽前的母材材质成分、表面硬度,根 据尺寸检查的结果绘制磨损型线等原始数据
4.5堆焊修复前的准备 4.5.1确定修复内容、应达到的性能要求和结构尺寸
堆焊前应编制堆焊工艺措施,堆焊工艺措施应 包括以下内容;堆焊方法;堆焊操作人员要求;堆焊使用的设备及工装要求;堆焊材料的牌号、生产厂家、 材料成分等;堆焊顺序及工艺参数;试验性焊接的要求;要求的焊道形状;焊后检验要求
GB/33935一2017 4.5.2对磨损失效的磨盘、磨衬板(辐套)堆焊修复前应进行焊前处理,使用碳弧气刨等方式清除表 面上不完整的焊接硬层及疲劳层
清除过程中应注意衬板面的平整和套体的圆度,清除后辐套体的 圆度公差不应大于3mm
对已磨损至母材深度部分应先行修复
4.6自动堆焊时对堆焊及其辅助设备的要求 4.6.1焊接电源能保证长时间连续稳定工作 4.6.2操作机能实现自动焊枪的上下左右方向平稳移动
4.6.3变位机能实现水平方向的旋转和垂直方向的翻转
变位机和磨盘慢速驱动的速度需在堆焊所 需的范围内且可调节
4.7堆焊施工时对安全和环境的要求 4.7.1堆焊工作应遵守安全、防护、防火等规程的有关规定
4.7.2堆焊工作的环境温度不应低于5C,否则应采取相应措施
4.7.3堆焊施工不应破坏现场环境,不应对现场造成污染
4.7.4设备应具有遮弧功能,通过遮弧装置屏蔽明弧焊产生的弧光,避免弧光对操作人员的伤害和对 环境的污染
除尘系统应能对自动焊时释放的焊接烟尘进行收集净化 4.7.5 4.8堆焊修复的过程控制 4.8.1根据磨盘、磨辑衬板(套)的基材成分和成品耐磨性要求,选择合理的堆焊材料分别用于打底 层、过渡层和硬面层的堆焊
合适的焊道形状是宽11nmm14mm,高1.5mm~2.1mm的窄焊道,同一焊层的后一焊道覆 4.8.2 盖前一焊道的30%左右,下一焊层的焊道依次排列在上一焊层的两个焊道中间
4.8.3磨盘、磨辑衬板(套)的硬面层允许有微裂纹,锯面焊接硬度应达到58HRC62HRC
堆煤 过程中应边焊边检验焊道的裂纹情况,敲击检查焊层熔合情况及有无气泡等
4.8.4磨盘、磨辗衬板(辗套)的修复堆焊过程中,各堆焊层的层间(上层和下层)温度差应不超过100C; 堆焊后应注意缓冷,以每小时2C的速度降至室温
4.8.5药芯焊丝自动堆焊时,其熔敷率应控制在85%以上
4.8.6堆焊过程中应使用专用规尺测量,随时调整耐磨件的外形尺寸
4.9对焊接工作人员的职业技能要求 4.9.1焊接工作人员包括焊接技术人员,焊工和焊接检验人员
4.9.2焊接技术人员应具备一定的专业技术水平和较丰富实践经验,熟悉并认真执行本标准,并结合 实际情况编制堆焊工艺方案,负责记录、检查、整理堆焊技术资料等
4.9.3堆焊施工人员应持有特种作业证书;施焊前应掌握堆焊设备的使用方法,了解耐磨件的结构和 材料成分,熟悉堆焊材料的性能等,并通过满足实际堆焊条件的模拟练习后,严格按照给定的堆焊工艺 和焊接技术措施进行施焊
4.9.4焊接检验人员包括无损检验和理化检验人员
无损检验人员应具有I级及以上检验资格,理化 检验人员应具有相应检验项目的资格
修复质量检测 5.1堆焊修复后磨盘、磨辐衬板(辐套)表面应无熔渣、,弧坑、焊瘤、飞溅物、气孔以及贯通状裂纹等现
GB/T33935一2017 象;焊道成形美观、细致、均匀,并平滑过渡到母材
5.2堆焊修复后磨盘、磨衬板(辐套)的堆焊层允许存在一定数量的裂纹(10cm×10cm范围,30条 左右),不应存在贯穿性裂纹和密集型气孔等缺陷,表面硬度应达到58HRC~62HRC 5.3堆焊修复后磨盘、磨衬板(辐套)应符合设计图纸或约定的尺寸规定,堆焊修复后的外形公差应 符合JB/T5000.3的规定 5.4在物料易磨性中等的情况下,在线修复的磨盘、磨衬板(辐套)运行时间应达到新出厂产品寿命 的90%以上,离线修复后的磨盘、磨辐衬板(辗套)运行时间应达到新出厂产品寿命水平
包装、运输和贮存 6.1离线修复的磨盘、磨辐衬板(辐套)包装应符合GB/T13384的规定,并适应陆路、水路运输部门的 有关规定
6.2在线修复的磨盘、磨锯衬板(辐套)如不立即投人使用,应在所有加工面涂抹防锈漆
6.3贮存磨盘、磨辐衬板(辐套)的场地,应具备防锈、防腐蚀和防损伤的设施
贮存期长的磨盘、磨辐 衬板(轭套)应定期检查、维护
立磨磨盘、磨辊衬板(辊套)修复规范GB/T33935-2017
立磨磨盘、磨辊衬板(辊套)是工业生产中常用的磨料加工设备,在长时间使用后会出现磨损、裂纹等问题。GB/T33935-2017是中国制定的关于立磨磨盘、磨辊衬板(辊套)修复的规范标准,以下是GB/T33935-2017规范要求的详细解读。
一、适用范围
GB/T33935-2017规定了立磨磨盘、磨辊衬板(辊套)的修复技术要求、检验方法、试验规则、包装、标志等要素,适用于立式研磨机、三辊研磨机、球磨机等设备的维修。
二、技术要求
GB/T33935-2017规定了立磨磨盘、磨辊衬板(辊套)的修复技术要求如下:
- 修复后的磨盘、磨辊衬板应该具有与原件相同或更好的耐磨性、耐腐蚀性、抗冲击性、抗疲劳性等性能指标;
- 修复后的磨盘、磨辊衬板表面应该平整光滑,无气孔、缺陷、裂纹等缺陷;
- 修复后的磨盘、磨辊衬板的尺寸公差应该符合原件设计要求;
- 修复过程中使用的焊接材料、涂覆材料、胶合剂等应该符合国家相关标准。
三、检验方法
GB/T33935-2017规定了立磨磨盘、磨辊衬板(辊套)的检验方法如下:
- 外观检验:采用肉眼检查法,检查修复后磨盘、磨辊衬板表面是否平整光滑,无气孔、缺陷、裂纹等缺陷;
- 尺寸检验:采用量具进行测量,检查修复后的磨盘、磨辊衬板的尺寸公差是否符合原件设计要求;
- 性能检验:采用试验机进行测试,检查修复后的磨盘、磨辊衬板的耐磨性、耐腐蚀性、抗冲击性、抗疲劳性等性能指标是否符合要求。
四、试验规则
GB/T33935-2017规定了试验规则如下:
- 对于同一批次修复的磨盘、磨辊衬板,应该进行全面性能试验,不得少于5个样品;
- 试验时应该按照GB/T33935-2017规定的方法进行,测试数据应该符合要求,否则需要重新修复;
- 试验通过后,应该进行包装和标志,确保修复后的磨盘、磨辊衬板可以安全运输和正常使用。
总之,GB/T33935-2017是立磨磨盘、磨辊衬板(辊套)修复领域的重要规范标准,它为行业提供了技术保障和质量保证。企业在进行立磨磨盘、磨辊衬板(辊套)修复时,应该遵循GB/T33935-2017规范要求的各项内容,确保修复后的产品具有稳定可靠的性能。