GB/T30968.1-2014
聚合物基复合材料层合板开孔/受载孔性能试验方法第1部分:挤压性能试验方法
Testmethodforopen-hole/loaded-holeofpolymermatrixcompositelaminates—Part1:Testmethodofbearingresponse
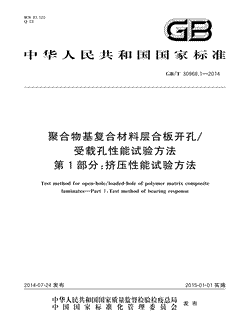
- 中国标准分类号(CCS)Q23
- 国际标准分类号(ICS)83.120
- 实施日期2015-01-01
- 文件格式PDF
- 文本页数17页
- 文件大小482.81KB
以图片形式预览聚合物基复合材料层合板开孔/受载孔性能试验方法第1部分:挤压性能试验方法
聚合物基复合材料层合板开孔/受载孔性能试验方法第1部分:挤压性能试验方法
国家标准 GB/T30968.1一2014 聚合物基复合材料层合板开孔/ 受载孔性能试验方法 第1部分:挤压性能试验方法 Testmethodforopen-hole/Ioaded-holeofpolymermatrixcomp0site 1:Iestmethodofbearingresponse aminates一Part 2014-07-24发布 2015-01-01实施 国家质量监督检监检疫总局 发布 国家标准花管理委员会国家标准
GB/T30968.1一2014 前 言 GB/T30968《聚合物基复合材料层合板开孔/受载孔性能试验方法》分为4部分 -第1部分:挤压性能试验方法; 第2部分:充填孔拉伸和压缩试验方法; 第3部分:开孔拉伸强度试验方法; 第4部分;开孔压缩强度试验方法 本部分为GB/T30968的第1部分
本部分按照GB/Tl.l一209给出的规则起收
本部分由建筑材料联合会、航空工业集团公司提出 本部分由全国纤维增强塑料标准化技术委员会(sAC/Tc39)、全国航空器标准化技术委员会 SAC/TC435)归口
本部分起草单位;飞机强度研究所、航空工业集团公司北京航空材料研究院
本部分主要起草人;杨胜春,沈真,张子龙、肖媚,孙坚石、周建锋、张立鹏、王俭
GB/T30968.1一2014 聚合物基复合材料层合板开孔/ 受载孔性能试验方法 第1部分挤压性能试验方法 范围 GB/T30968的本部分规定了聚合物基复合材料层合板挤压性能试验方法的试验设备、试样、试验 步骤、计算和试验报告
本部分适用于连续纤维增强聚合物基复合材料层合板挤压性能的测定
本标准的方法A适用于 材料评价和比较,方法B和方法C适用于评价具体的连接构型和建立设计许用值数据 规范性引用文件 下列文件对于本文件的应用是必不可少的
凡是注日期的引用文件仅注日期的版本适用于本文 凡是不注日期的引用文件,其最新版本(包括所有的修改单)适用于本文件
件
GB/T1446纤维增强塑料性能试验方法总则 GB/T3961纤维增强塑料术语 术语和定义 GB/T3961界定的术语和定义适用于本文件
挤压面积 hearingarean 受载孔的直径与试样厚度的乘积
3.2 孔径厚度比diametertothicknessratio 孔径与试样厚度之比,用尺寸的名义值或实际测量值确定 3.3 端距比eueedistaee ratio 孔中心到试样端部之间的距离与孔径之比,用尺寸的名义值或实际测量值确定 3.4 宽度孔径比widthtodiameterratio 试样宽度与孔径之比,用尺寸的名义值或实际测量值确定
3.5 挤压应变bearingstrain 挤压载荷方向挤压孔的变形与孔径之比 3.6 bearin 挤压应力 ingstress 单位挤压面积承受的挤压载荷
GB/T30968.1一2014 3 挤压刚度 bearingchordstirfness 挤压应力/挤压应变曲线线性部分上两个指定的挤压应力或挤压应变点之间的连线的斜率 3.8 bear 挤压强度 arngstrengtt 挤压应力/应变曲线斜率出现明显变化时的挤压应力值
3.9 条件挤压强度offsetbhearin strengt ng 过挤压应变轴上偏离零点的规定挤压应变值点,作平行于挤压应力/挤压应变曲线线性段的直线 弦线刚度线,该直线与挤压应力挤压应变曲线交点所对应的挤压应力值
一般取2%偏离零点的挤 压应变确定条件挤压强度
3.10 极限挤压强度ultimteberima strength 试样承受最大载荷时的挤压应力值 方法原理 对紧固件采用双剪(方法A)或单剪(方法B和方法C)方式施加载荷,使紧固件和层合板试样的孔 表面接触,形成挤压面,进而测得层合板试样孔边的挤压性能
试验设备 5.1试验机与测试仪器 试验机和测试仪器应符合GB/T1446的规定
5.2环境箱 环境箱的控制精度应满足试验要求,经计量检定合格,并在有效期内使用
5.3扭矩扳手 扭矩扳手的精度应满足试验要求,经计量检定合格,并在有效期内使用 5.4试验夹具 方法A(双剪法)的试验夹具见图1和图2,方法C(有夹具单剪法)的试验夹具见图3图6
GB/T30968.1一2014 说明 垫板" -双剪夹具; 试样
图1方法A双剪法)试验夹具与试样的装配示意图 尺寸代号 尺寸值/mm 200 50 36 20 图2方法A(双剪法)试验夹具示意图
GB/T30968.1一2014 说明: 夹持面; 长夹板; 支持板; 短夹板; 试样; 垫板
图3方法C试验夹具组合件示意图 单位为毫米 E 93 HAB 10o 236 注1D采用高速氧燃料(HvoF)工艺或电火花沉淀(EsD)进行热喷涂表面处理
注2:除标准以外,其余公差为士0.3mm
图4方法C试验夹具的长夹板示意图
GB/T30968.1一2014 单位为毫米 工.?A回 R 品 回 100 10 丽 注1:D>采用高速氧燃料(HVOF)工艺或电火花沉淀(ESD)进行热喷涂表面处理
注2除标准以外,其余公差为士0.3; mm
图5方法C试验夹具的短夹板示意图 单位为毫米 A 妙 80 图6方法C试验夹具的支持板示意图
GB/T30968.1一2014 试样 6.1 铺层形式 试样为对称均衡的多向层合板 6.2试样形状与尺寸 6.2.1方法A 方法A的试样形状与尺寸分别见图7和表1 Z0C囚 铺层方向公差为相对于基准面小于士0.5;机械加工边缘的粗糙度Ra值不超过3.2" 2m
图7双剪法试样示意图 表1双剪法试样几何尺寸要求 参数 要求 试样铺层形式 准各向同性 宽度孔径比(u/D) 端距孔径比(e/D) 35 厚度h/mm 紧固件直径d/mm 68 孔径D/mm 6M" 长度L/mnm 135 宽度w/mm 36士1 端距e/mm 18士1 紧固件拧紧力矩/(Nm) 3士0.3 6.2.2方法B 方法B的试样形状与尺寸分别见图8.图9,表2和表3
着双钉试样采用沉头紧固件,则试样的每 侧均应布置一个沉头
GB/T30968.1一2014 6.2.3方法c 方法C的试样形状与尺寸分别见图8,图9,表2和表3
若双钉试样采用沉头紧固件,则试样的每 -侧均应布置一个沉头
0.0RA 铺层方向公差为;相对于基准面小于士0.5;机械加工边缘的粗糙度Ra值不超过3.2m.
图8单剪、单紧固件试样示意图 表2单钉单剪试样几何尺寸要求 要求 参数 方法B(无夹具 方法c(有夹具 紧固件形状 凸头.沉头 凸头.沉头 宽度孔径比(w/D) 端距孔径比(e/D 紧固件直径d/mm 688 688 孔径D/mm 68 6a8 26 26 厚度h/mm 长度L/mm 135 186 宽度w/mm 36士1 36士1 端距e/mm 18士1 18士1 垫板长度s/mm 75 126 紧固件拧紧力矩/(Nm) 3士0.3 3士0.3
GB/T30968.1一2014 Z购 铺层方向公差为;相对于基准面小于士0,5";机械加工边缘的粗糙度R值不超过3,2A" 图g单剪双紧固件试样示意图 表3双钉单剪试样几何尺寸要求 试样标准尺寸 方法B(无夹具 方法C(有夹具 紧固件形状 凸头、沉头 凸头、沉头 宽度孔径比(w/ D 端距孔径比(e/D) 紧固件直径d/ 6t快出 6t83 /mm 孔径D/mmm 6松8 6t"湖 厚度/mm 26 26 长度L/mm 204 204 宽度w/mm 36士1 36士1 端距e/mm 18士1 18士1 垫板长度, /mm 108 108 紧固件拧紧力矩/(N
m 3士0.3 3士0.3 6.3垫板材料 对于无试验夹具的单剪试样,推荐采用连续玻璃纤维增强的聚合物基[士45]
层合板
对于有试 验夹具的单剪试样,垫板材料推荐采用与试样相同的材料制成
6.4胶粘剂 将垫板与试样粘接时,可采用能满足环境要求的高伸长率的(韧性的)胶粘剂
若采用试验夹具,则 不需要将垫板与试样粘接
6.5试样制备 试样制备按GB/T1446的规定
制孔时应避免孔周围的材料出现分层或其他损伤
GB/T30968.1一2014 6.6试样数量 每组有效试样应不少于5个
试验条件 7.1试验环境条件 7.1.1实验室标准环境条件 实验室标准环境条件应满足GB/T1446的规定 7.1.2非实验室标准环境条件 7.1.2.1高温试验环境条件 首先将环境箱和试验夹具预热到规定的试验温度,然后将试样加热到规定的试验温度,并用与试样 工作段直接接触的温度传感器加以校验
对干态试样,在试样达到试验温度后,保温5min~10min开 始试验;对湿态试样,在试样达到试验温度后,保温2min3min开始试验
试验中试样温度保持在规 定试验温度的(3C范围内
7.1.2.2低温(低于0C)试验环境条件 首先将环境箱和试验夹具冷却到规定的试验温度,然后将试样冷却到规定的试验温度,并用与试样 工作段直接接触的温度传感器加以校验
在试样达到试验温度后,保温5min10min开始试验
试 验中试样温度保持在规定试验温度的土3C范围内
7.2试样状态调节 7.2.1干态试样状态调节 试验前,试样在实验室标准环境条件下至少放置24h
7.2.2湿态试样状态调节 试验前,应在规定的温度和湿度条件下使试样达到所要求的吸湿状态
推荐的温度和湿度条件 如下 温度:70C士3; a b)相对湿度;85%士5%. 湿态试样状态调节结束后,应将试样用湿布包裹放人密封袋内,直到进行力学试验,试样在密封袋 内的储存时间应不超过14d
试验步骤 8.1方法A双剪法 8.1.1试验前准备 8.1.1.1按GB/T1446的规定检查试样外观,对每个试样编号 8.1.1.2按7.2的规定对试样进行状态调节
GB/T30968.1一2014 8.1.1.3在最终的试样机械加工和状态调节后,测量孔附近的试样宽度w,试样厚度h、孔径D、从孔边 缘到试样侧边的最短距离和孔边缘到试样端部的距离g
试样厚度测量精确到0.01 ,其余尺寸 mm 测量精确到0.02 mm
8.1.2试样安装 8.1.2.1通过紧固件,将试样与双剪夹具装配在一起,用扭矩扳手将紧固件拧紧到所需的值
8.1.2.2将试样-夹具组合件夹持于试验机夹头中,并使试样中心线与试验机夹头中心线保持一致
8.1.2.3按照图10的要求安装引伸计
8.1.3试验 8.1.3.1对于在实验室标准环境条件下进行的试验,按7.1.1的规定进行;而对于在非实验室标准环境 条件下进行的试验,则按7.1.2的规定进行
8.1.3.2以1mm/min~2mm/min的加载速度对试样连续加载,直到试样破坏
连续测量并记录试 样的载荷-孔位移曲线和失效模式
若出现过渡区域或单层的初始破坏,则记录该点的载荷和损伤模 式
若试样破坏,则记录试样的失效模式,最大载荷及尽可能接近破坏瞬间的孔的位移
8.1.3.3失效模式的描述采用表4和图12所示的三字符式失效代码,其中复合失效模式用代码M和 其后括号内每个相应失效形式的代码来表示,如对于同时出现局部挤压和劈裂失效模式的[45/0/ 45//90.]预浸带层合板,可用M(BC)1I表示其失效模式
标 距 长 度 图10双剪挤压试验引伸计安装示意图 8.2方法B(无夹具单剪法 8.2.1试验前准备 8.2.1.1按GB/T1446的规定检查试样外观,对每个试样编号
8.2.1.2按7.2的规定对试样进行状态调节 8.2.1.3在最终的试样机械加工和状态调节后,测量孔附近的试样宽度w,试样厚度h、孔径D、从孔边 缘到试样侧边的最短距离和孔边缘到试样端部的距离片
试样厚度测量精确到0.01mm,其余尺寸 测量精确到0.02mm
8.2.2试样安装 8.2.2.1通过紧固件,将试样装配在一起,用扭矩扳手将紧固件拧紧到所需的值
GB/T30968.1一2014 8.2.2.2将试样夹持于试验机夹头中,并使试样的中心线与试验机夹头的中心线保持一致
8.2.2.3按照图11的要求安装引伸计
8.2.3试验 8.2.3.1对于在实验室标准环境条件下进行的试验,按7.1.1的规定进行;而对于在非实验室标准环境 条件下进行的试验,则按7.1.2的规定进行
8.2.3.2以1mm/min~2mm/min的加载速度对试样连续加载,直到试样破坏
连续测量并记录试 样的载荷-孔位移曲线和失效模式
若出现过渡区域或单层的初始破坏,则记录该点的载荷和损伤模 式
若试样破坏,则记录试样的失效模式、最大载荷及尽可能接近破坏瞬间的孔的位移 8.2.3.3失效模式的描述采用表4和图12所示的三字符式失效代码,其中复合失效模式用代码M和 其后括号内每个相应失效形式的代码来表示,如对于同时出现局部挤压和劈裂失效模式的[45./0 5./90.],预浸带层合板,可用M(BC)11表示其失效模式
长 度 标 跳 长 度 单钉单剪 b 双钉单剪 图11单剪挤压试验引伸计安装示意图 8.3方法c(有夹具单剪法 8.3.1试验前准备 8.3.1.1按GB/T1446的规定检查试样外观,对每个试样编号
8.3.1.2按7.2的规定对试样进行状态调节
8.3.1.3在最终的试样机械加工和状态调节后,测量孔附近的试样宽度w,试样厚度h、孔径D、从孔边 缘到试样侧边的最短距离f和孔边缘到试样端部的距离g
试样厚度测量精确到0.01mm,其余尺寸 测量精确到0.02mm 8.3.2试样安装 8.3.2.1通过紧固件,将试样装配在一起,用扭矩扳手将紧固件拧紧到所需的值
将试样安装于试验夹具中,使试样两端与夹具两端平齐
夹具安装时拧紧4个螺栓,使试样 8.3.2.2 的位置保持不动,保证夹具的支撑板和长夹板之间以及试样工作段和夹具的长夹板之间的间隙均不大 然后用扭矩扳手拧紧4个螺栓到7N 于0.l0mm
m士0.5Nm
8.3.2.3将试样-夹具组合件夹持于试验机夹头中,并使试样中心线与试验机夹头中心线保持一致 1
GB/T30968.1一2014 8.3.2.4按照图11的要求安装引伸计
8.3.3试验 8.3.3.1对于在实验室标准环境条件下进行的试验,按7.1.1的规定进行;而对于在非实验室标准环境 条件下进行的试验,则按7.1.2的规定进行
8.3.3.2以1mm/ 1/min一2mm/min的加载速度对试样连续加载,直到试样破坏
连续测量并记录试 样的载荷-孔位移曲线和失效模式
若出现过渡区域或单层的初始破坏,则记录该点的载荷和损伤模 式
若试样破坏,则记录试样的失效模式,最大载荷及尽可能接近破坏瞬间的孔的位移 8.3.3.3失效模式的描述采用表4和图12所示的三字符式失效代码,其中复合失效模式用代码M和 其后括号内每个相应失效形式的代码来表示,如对于同时出现局部挤压和劈裂失效模式的[5./0, -45,/90]
预浸带层合板,可用MEC)1l表示其失效模式 表4挤压试验失效代码 第一个字符 第二个字符 第三个字符 失效形式 代码 失效区域 代码 失效位置 代码 挤压 近端距孔 螺栓头一侧 B N 横向净拉断 远端距孔 螺母一侧 剪出 两个孔 其他 劈裂 紧固件 撕脱 其他 紧固件或销钉 复合模式 Mxy2 其他 s a b) o 剪出 挤压 横向净拉断 d 劈裂 撕脱 图12挤压试验失效模式示意图 12
GB/T30968.1一2014 计算 9.1挤压应力和极限挤压强度 挤压应力和极限挤压强度分别按式(1)和式(2)计算,结果保留3位有效数字 P dm D P m#x D 式中: 试样的挤压应力,单位为兆帕(MPa); dm 试样的极限挤压强度,单位为兆帕(MPa); 口 试样承受的载荷,单位为牛顿(N) ? 试样承受的最大载荷,单位为牛顿(N); Fnax 紧固件数量
9.2挤压应变 挤压应变按式(3)计算,结果保留3位有效数字: En RD 式中: 挤压应变,单位为毫米每毫米(mm/mm); 引伸计的位移,单位为毫米(mm) 单剪-双剪系数,对于单剪试样,K=2;对于双剪试样,K=1
K 9.3挤压刚度 挤压刚度按式(4)计算,结果保留3位有效数字 Aa E;= e 式中: 挤压应力挤压应变曲线中初始线性段的对应A上L的挤压应力增量,单位为兆帕(MPa)5 Ao -挤压应力-挤压应变曲线中初始线性段的挤压应变增量
AE 9.4有效原点 弦线刚度直线与挤压应变轴的交点为有效原点,其目的是用于确定条件挤压强度和极限挤压强度
9.5极限挤压应变 基于新的有效原点,对挤压应力/挤压应变数据进行修正后,记录最大载荷时的挤压应变作为极限 挤压应变,记录结果取三位有效数字
9.6条件挤压强度 基于新的有效原点,对挤压应力/挤压应变数据进行修正后,将弦线刚度线沿挤压应变轴从原点平 移到指定的挤压应变的偏移量,确定该直线与挤压应力/挤压应变曲线的交点
该点的挤压应力值即为 13
GB/T30968.1一2014 条件挤压强度口imx,见图13
90o "%/偏移量 800 700 极限挤压强度 600 条件挤压强度 500 400 300 200 00 有效原点 -20000 20000400006000080000100000 挤压应变(×10' 图13条件挤压强度确定方法示意图 9.7初始峰值挤压强度 某些挤压试验会出现一个初始峰值挤压应力,随后有挤压应力的剧烈下降和其后的孔变形,使得条 件挤压强度小于初始峰值挤压应力
在进一步的孔变形之后,若再继续加载到高于初始峰值的挤压应 力水平,则除了条件和极限挤压强度之外,还应记录作为初始峰值挤压强度的初始峰值挤压应力
但 是,若初始峰值挤压应力就是试样的极限挤压强度,则不需要报告初始峰值挤压强度和条件挤压强度
9.8统计 对于每一组试验,按GB/T1446的规定计算每一种测量性能的算术平均值、标准差和离散系数
10 试验报告 试验报告一般包括下列内容 a)试验项目名称,执行标准和方法; b)试验人员、试验时间和地点; 试样来源及制备情况,材料(包括复合材料、紧固件和垫板)品种及规格 e) 试样铺层形式,编号,形状和尺寸、外观质量及数量; d e)试验温度、相对湿度、试样状态调节参数和结果; f 试验设备及仪器的型号、,规格及计量情况: g)与本标准的不同之处,试验时出现的异常情况 h)试验结果,包括 1 紧固件的拧紧力矩; 2 每个试样的最大载荷值或破坏载荷值; 14
GB/T30968.1一2014 每个试样的极限挤压强度及样本的算术平均值、标准差和离散系数 3 4! 每个试样的条件挤压强度及样本的算术平均值、标准差和离散系数 5 计算条件挤压强度的应变偏移量; 6 每个试样的失效模式
聚合物基复合材料层合板开孔/受载孔性能试验方法第1部分:挤压性能试验方法GB/T30968.1-2014
一、试验原理
本试验是针对聚合物基复合材料层合板在实际使用中可能遇到的开孔或受载孔情况,通过挤压试验来评估材料的抗压性能。试验可以用于研究材料的设计、优化以及质量控制。
二、试样制备
制备符合标准要求的试样。样品应根据产品设计图纸进行加工,试样应具有足够的代表性。在试样上开一个直径为10mm的孔,位置应与产品设计图纸一致。
三、试验设备
3.1 试验机
试验机应满足标准要求,并具备足够的负荷能力。
3.2 夹具
夹具应能够确保试样在挤压过程中不发生滑移或旋转。
四、试验步骤
4.1 装夹试样
将试样放入夹具中,夹紧试样。装好后检查试样是否正确安装。
4.2 开始试验
开启试验机,在规定的速度下进行试验,直至试样破坏为止。试验过程中应记录试样的最大承载能力和变形情况等数据。
4.3 结束试验
试验结束后,关闭试验机,取出试样并对其进行表面检查。记录试样的破坏形态和位置等信息。
五、试验结果的评定
5.1 抗压强度
抗压强度可通过试验中记录的试样最大承载能力和试样面积计算得到。
5.2 变形率
试验中还应记录试样的变形情况,计算出变形率。
5.3 破坏形态
评估试样在挤压过程中的破坏形态,并结合试验数据进行分析。