GB/T34275-2017
压力管道规范长输管道
Pressurepipingcode—Long-distancepipeline
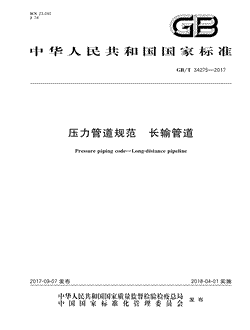
- 中国标准分类号(CCS)J74
- 国际标准分类号(ICS)23.040
- 实施日期2018-04-01
- 文件格式PDF
- 文本页数146页
- 文件大小13.39M
以图片形式预览压力管道规范长输管道
压力管道规范长输管道
国家标准 GB/T34275一2017 压力管道规范长输管道 Presurepipingeode一Longdistaneepipeine 2017-09-07发布 2018-04-01实施 国家质量监督检验检疫总局 发布 国家标准化管理委员会国家标准
GB/34275一2017 前 言 本标准按照GB/T1.1一2009给出的规则起草
本标准由全国锅炉压力容器标准化技术委员会(SAC/TC262)提出并归口
本标准起草单位:石油天然气管道局、国家质检总局特种设备安全监察局,特种设备检测 研究院、全国化工设备设计技术中心站、中石化上海工程有限公司
本标准主要起草人;续理、修长征、孙宇,寿比南、黄正林、许砚新、冯斌、魏国昌、徐进、门建新、古桢、 马红听、蔡暖妹、应道宴、王昊肠、尤子涵
GB/34275一2017 压力管道规范长输管道 范围 本标准规定了长输油气)商品介质管道(GA类)建设、投产,在役管道的运行、维修及检验等技术 要求
本标准适用于长输管道建设的设计、材料、安装、无损检测、投产和在役管道的运行,维修及检验
本长输管道系指产地、储存库、用户间的用于输送(油气)商品介质的管道
本标准适用的管道系统范围 见图1所示
油气田集输管道符合本标准的相关条件的可执行本标准
本标准不适用于公用管道(GB类),工业管道(GC类),动力管道(GD类);也不适用于其他类型的 管道,如电气(电讯)专用的管道、军事装备和核设施的管道,海上设施和矿井的管道、移动设备上的管 道、石油、天然气,地热等勘探和采掘装置的管道、城镇的门站后所属的燃气管网
注:依据TsGD3001《压力管道安装许可规则GA类为长输油气)管道,GB类为公用管道,GC类为工业管道,GD 类为动力管道 图例 本系统适用的管道系统 与其他设施的连接 处理姑 本标准不适用的管道 液体 中 本标准包括的站/场区域 暴站 亡 压缩机站 阔站亡 阀站 罐区口 储库 减压站 分配系统 分配系统 说明:管道系统在与其他设施的连接处和分支处,宜设置一个隔离阀
图1本标准适用的管道系统范围 规范性引用文件 下列文件对于本文件的应用是必不可少的
凡是注日期的引用文件,仅注日期的版本适用于本文
GB/T34275一2017 件
凡是不注日期的引用文件,其最新版本(包括所有的修改单)适用于本文件
GB/T2887计算机场地通用规范 GB/T3620.1钛及钛合金牌号和化学成分 GB/T5117非合金钢及细晶粒钢焊条 GB6722爆破安全规程 GB/T8110气体保护电弧焊用碳钢、低合金钢焊丝 GB/T8163输送流体用无缝钢管 GB8978污水综合排放标准 GB/T9361计算机场地安全要求 GB/T9711石油天然气工业管线输送系统用钢管 GB1l174液化石油气 GB/T12459钢制对焊无缝管件 GB/T13401钢板制对焊管件 GB/T13402大直径钢制管法兰 GB/T14549电能质量公用电网谐波 GB/T16805液体石油管道压力试验 GB/T17493低合金钢药芯焊丝 GB17820天然气 GB18306地震动参数区划图 GB/T192852014埋地钢质管道腐蚀防护工程检验 GB/T19326锻制承插煤,螺纹和对煤支管座 GB/T19624在用含缺陷压力容器安全评定 GB/T19672管线阀门技术条件 GB/T20173石油天然气工业管道输送系统管道阀门 GB/T20801(所有部分)压力管道规范工业管道 GB/T21246埋地钢质管道阴极保护参数测量方法 GB/T21447钢质管道外腐蚀控制规范 GB/T21448埋地钢质管道阴极保护技术规范 GB/T26480阀门的检验和试验 GB/T27512埋地钢质管道风险评估方法 GB/T27699钢质管道内检测技术规范 GB/T28055钢质管道带压封堵技术规范 G;B/T29168.1石油天然气工业管道输送系统用感应加热弯管、管件和法兰第1部分;感应 加热弯管 GB/T29168.2石油天然气工业管道输送系统用感应加热弯管、管件和法兰第2部分;管件 GB/T29168.3石油天然气工业管道输送系统用感应加热弯管、管件和法兰第3部分;法兰 GB/T30582一2014基于风险的埋地钢质管道外损伤检验与评价 GB/T31032钢质管道焊接及验收 GB50007建筑地基基础设计规范 GB50009 建筑结构背载规范 GB50010混凝土结构设计规范
GB/34275一2017 GB50016建筑设计防火规范 GB50017钢结构设计规范 GB50055通用用电设备配电设计规范 GB50057建筑物防雷设计规范 GB50058爆炸危险环境电力装置设计规范 GB50086岩土锚杆与喷射混凝土支护工程技术规范 GB50093自动化仪表工程施工及质量验收规范 GB50135高耸结构设计规范 GB50140建筑灭火器配置设计规范 GB50147电气装置安装工程高压电器施工及验收规范 GB50148电气装置安装工程电力变压器、油浸电抗器、互感器施工及验收规范 GB50149电气装置安装工程母线装置施工及验收规范 GB5016o石油化工企业设计防火规范 GE50168电气装置安装工程电缆线路施工及验收规范 GB50169 电 气装置安装工程接地装置施工及验收规范 GB50170 电 气装置安装工程旋转电机施工及验收规范 GB50171电气装置安装工程盘、柜及二次回路接线施工及验收规范 GB50172电气装置安装工程蓄电池施工及验收规范 GB50173电气装置安装工程66kV及以下架空电力线路施工及验收规范 GB50183石油天然气工程设计防火规范 GB50204混凝土结构工程施工质量验收规范 GB50205钢结构工程施工质量验收规范 GB50236现场设备、工业管道焊接工程施工规范 GB50242建筑给水排水及采暖工程施工质量验收规范 GB50243通风与空调工程施工质量验收规范 GB50251输气管道工程设计规范 GB50253输油管道工程设计规范 GB50254电气装置安装工程低压电器施工及验收规范 电力变流设备施工及验收规范 GB50255电气装置安装工程 GB50256电气装置安装工程起重机电气装置施工及验收规范 GB50257 电气装置安装工程爆炸和火灾危险环境电气装置施工及验收规范 GB50369油气长输管道工程施工及验收规范 GB50423油气输送管道穿越工程设计规范 GB50424油气输送管道穿越工程施工规范 GB50459油气输送管道跨越工程设计规范 GB50460油气输送管道跨越工程施工规范 GB50461 石油化工静设备安装工程施工质量验收规范 GB50470油气输送管道线路工程抗震技术规范 GB/T50538埋地钢质管道防腐保温层技术标准 GB/T50539油气输送管道工程测量规范 GB50540石油天然气站内工艺管道工程施工规范
GB/T34275一2017 GB50568油气田及管道岩土工程勘察规范 GB/T50698埋地钢质管道交流干扰防护技术标准 GB/T50818石油天然气管道工程全自动超声波检测技术规范 GB50991埋地钢质管道直流干扰防护技术标准 TGD62公路钢筋混凝土及预应力混凝土桥涵设计规范 GJ94建筑桩基技术规范 JB/T1308.2PN2500超高压阀门和管件第2部分;阀门、管件和紧固件 JB4732钢制压力容器分析设计标准 NB/T47008承压设备用碳素钢和合金钢锻件 NB/T47013.1l一47013.6承压设备无损检测 sH/T3542石油化工静设备安装工程施工技术规程 sY/T0087.1一20o6钢制管道及储罐腐蚀评价标准埋地俐质管道外腐蚀直接评价 0095埋地镁牺牲阳极试样试验室评价的试验方法 SY sY/T0403输油泵组安装技术规范 SY 加热炉工程施工及验收规范 SY 0460天然气净化装置设备与管道安装工程施工技术规范 SY 0510钢制对焊管件规范 SY 0516绝缘接头与绝缘法兰技术规范 导热油加热炉系统规范 SY7T0524 管式加热炉规范 SY 0538 sY/T0609优质钢制对焊管件规范 4108输油(气)管道同沟敷设光缆(硅芯管)设计及施工规范 4109石油天然气钢质管道无损检测 SY/T4111天然气压缩机(组)安装工程施工技术规范 SY4203石油天然气建设工程施工质量验收规范站内工艺管道工程 sY4207石油天然气建设工程施工质量验收规范管道穿跨越工程 sY4208石油天然气建设工程施工质量验收规范输油输气管道线路工程 SY/T5262火简式加热炉规范 SY/T5767 原油管道添加降凝剂输送技术规范 SY/T6793油气输送管道线路工程水工保护设计规范 SY/T6884油气管道穿越工程竖井设计规范 SY7513出矿原油技术条件 TSGZ6002特种设备焊接操作人员考核细则 TSGD7003压力管道定期检验规则长输(油气)管道 AsMEB31.8输气和配气管道系统(Gastransmissionanddistributionpipingsystems) 术语和定义 下列术语和定义适用于本文件
3. 长输管道Iomg" distaneepipeline 产地、储存库、用户间的用于输送油气)商品介质的管道
GB/34275一2017 3.2 油气)商品介质oilandgas 符合国家相关标准要求的原油、成品油,天然气和液化石油气
3.3 公称压力(PNnominalpressure 由字母PN和无因次整数数字组合的压力标记,代表管道组成件的允许的压力等级
3.4 公称尺寸(DN nominaldliameter 由字母DN和无因次整数数字组合的尺寸标识,这个数字与端部连接件的孔径和外径等特征尺寸 直接相关(以mm计) 3.5 弹性敷设pipelayingwithelasticbending 管道在外力或自重作用下产生弹性弯曲变形,利用这种变形进行管道敷设的一种方式
3.6 水露点waterdewpoint 气体在一定压力下析出第一滴水时的温度
3.7 胫露点hydroearbon dewpoint 气体在一定压力下析出第一滴液态经时的温度 3.8 冷弯管coldbends 在不加热条件下,用模具(或夹具)将直管弯制成需要角度的弯管
3.9 热煨弯管hotbends 在加热条件下,在夹具上将直管弯曲成需要角度的弯管 3.10 弯头ebow 曲率半径小于4倍公称直径的弯曲管段
3.11 管道piping 由管道组成件和管道支撑件组成,用于输送,分配混合,分离、排放、计量、控制或制止流体流动的 钢管、管件,法兰、螺栓连接、垫片,阀门和其他组成件或受压部件的装配总成 3.12 管道组成件pipingcomponents 用于连接或装配成压力密封的管道系统机械元件,包括钢管、管件,法兰,垫片、紧固件、阀门,安全 保护设施以及诸如膨胀节、挠性接头、耐压软管、过滤器、管路中的仪表(如孔板)和分离器等
3.13 管件ppefitings 弯头、弯管、三通、异径接头和管封头等管道上各种异形连接件的统称
GB/T34275一2017 3.14 管道附件pipeaxiliaries 管件、法兰、阀门及其组合件,绝缘法兰、绝缘接头等管道专用部件的统称
3.15 固定件pipesupportingfixtures 将输送管或结构附件的载荷传递给支承构筑物或支承设备的各种零件,包括悬吊类固定件,如吊 杆、弹簧吊、竖向支撑、平衡块、紧线螺丝、支撑杆,链条、导向支座和锚固件等;支承类固定件,如鞍形支 座底座、滚筒、托架、滑动支座、限位支座、固定支座等; 3.16 结构附件ppesuppwrtmgsructuralataehments 焊接在、栓接在或夹持在输送管上的零件,例如管夹吊耳吊环、卡箍、U形夹、箍带及裙座等
3.17 管架pipesupport 支承管道的构筑物,管道通过支承固定件、结构附件将荷重和推力传递到管架上
管架由钢结构或 钢筋混凝土结构的立柱、横梁或框架所构成,独立固定在基础上,也可固定在设备上或墙上
按类型分 有;独柱式,双柱式和悬臂式等
3.18 绝缘接头insulatingjoint 对同时具有埋地钢质管道要求的密封性能和电法腐蚀防护工程要求的电绝缘性能接头的统称,它 包括上、下导管,套筒,绝缘件、密封件、绝缘涂层
在绝缘接头的上、下导管对接端面间,夹有绝缘件和 密封件,形成具有绝缘性能的双密封结构,套筒采用坡口媒接或与上导管直接焊接两种形式,将绝缘件 和上、下导管牢固封裹在里面,保证了良好的绝缘效果和承压能力
3.19 快开盲板fastopeningbindl 用于压力管道的圆形开口上并能实现快速开启和关闭的一种机械装置
3.20 橇装设备prytopachequipmment 将机泵和工艺管道等在工厂组装到钢质底座,整体拉运到现场、直接安装在基础的成套设备
3.21 cell 管道单元pipee 采用预制的方法,将管道、管道附件按照设计的要求进行部分组装而成的单元
3.22 输油泵机组ipum mmpset 输送原油成品油的泵组及驱动系统、润滑油系统、电气仪表系统等以及钢结构的总称
3.23 压缩机机组air-compressset 压缩介质为气体的压缩机及其驱动系统、冷却系统、润滑油系统、电气仪表系统以及钢结构的总称
3.24 压力试验pressuretest 以液态或气体作为介质,对管道逐步加压,达到规定的压力,以检验管道运行安全性和严密性的 试验
GB/34275一2017 3.25 干空气dryair 在一定压力和温度条件下的空气,即露点低于一40C的空气
3.26 干空气干燥法dryairdrying 通过持续地向管道内注人干空气进行清扫,使残留在管道内的水分蒸发,并将蒸发后的湿空气置换 出管道外,从而达到管道干燥目的的施工方法
3.27 真空干燥法vacuumdrying 水的沸点随压力的降低而降低,在压力很低的情况下,水可以在很低的温度下沸腾汽化
利用这一 原理,在控制条件下用真空泵不断地抽取管道内的气体,降低管道中的压力直至达到管壁温度下水的饱 和蒸汽压,此时残留在管道内壁上的水沸腾而迅速汽化,汽化后的水蒸气随后被真空泵抽出的施工 方法
3.28 液氮干燥法liquefiedmitrogendrying 液氮经汽化器汽化,加热器加热后以不低于50C的温度进人管道进行低压间断性清扫,管道内的 水分与干燥氮气混合后被带出管道,从而达到管道干燥目的的施工方法
3.29 单线图 is0metric diugram 将每条管道按照轴侧投影的绘制方法,画成以单线表示的管道空视图
3.30 预燥接工艺规程pelimimarywelinr roeedurespeeifieation 按照工程设计要求,根据焊接试验结果或其他类似工程经验,由焊接试验单位编制的用于焊接工艺 评定的焊接工艺指导性文件
3.31 ualification 焊接工艺评定weldin ingpr0cedure9qu 在工程焊接前,为验证所拟定的焊件焊接工艺的正确性而进行的试验过程及结果评价
在本标准 中,焊接工艺评定是指为使焊接接头的力学性能、弯曲性能或堆焊层的化学成分符合规定对预焊接工艺 进行验证性试验和结果评价的过程
3.32 焊接工艺规程weldingproeedurespeeifieation 根据评定合格的焊接工艺编制的用于工程施工的一整套详细的焊接技术规定和程序
3.33 根焊 r0otbead 为管与管,管与管件,管件与管件之间焊接时的第一层焊道
3.34 热焊hotbhead 为了防止根部冷裂纹或根部烧穿,而在根焊完成后立即进行的第二层焊道
3.35 填充焊fillerbhead 在根焊或热焊完成后,盖面焊之前的焊道
GB/T34275一2017 3.36 盖面燥ceapbeadl 最外面一层的成型焊道
3.37 多道焊(排焊multi-passweding 熔敷两条或两条以上的焊道而完成一层焊缝所进行的焊接 3.38 焊接缺陷welddefeet 在焊接接头与母材中,无损检测标准不允许存在的不连续部位
3.39 焊接缺欠weldimperfeetion" 在焊接接头与母材中,无损检测标准允许存在的不连续部位
3.40 修补patching 对发现的表面非裂纹缺陷进行的修复
3.41 返修焊repairwelding 对发现的表面裂纹缺陷及经无损检测发现的缺陷进行的修补煤接
3.42 死口setwedingline 管道线路焊接施工中,两个管端在组对时,只能在二维平面进行调整,轴向位置不能调整,焊接后参 加试压的焊口
3.43 金口setwedinglimenoattendaneepressretest 管道线路焊接施工中,两个管端在组对时,只能在二维平面进行调整,轴向位置不能调整,焊接后只 进行无损检测,不参加试压的焊口 3.44 投产commmissioning 与管道系统最初充装管输流体有关的活动 3.45 在役管道in-servieeppelne 已经投产输送流体的管道
3.46 uisition 自动化仪表(SCADA)系统superyisorycontrolanddataacqut 数据采集与监视控制系统,无论规模大小都由三部分组成:位于调度控制中心的主端调度装置 MTU),位于各站场的远程终端装置(RTU)和连接它们的通信系统
使用scADA系统可对指定设 施提供连续监测,并从控制中心对这些设施进行操作控制
3.47 A型套袖typeAsleeve 由放置在管道损伤部位的两个半圆的柱状管或两片适当弯曲的钢板,并经侧缝焊接组合成
用作 管道损伤部位的加强件,不用焊接可直接安装在管道上
GB/34275一2017 3.48 型套袖typeBsleeve B 由放置在管道损伤部位的两个半圆的柱状管或两片适当弯曲的钢板,并经侧缝焊接组合成
其末 端应与管道进行焊接,套袖侧缝宜采用对接焊接方式
3.49 动火hotwork 在油气、易燃易爆危险区域内和油气容器、管线、设备或盛装易燃易爆物品的容器上,使用焊接,割 等工具,能直接和间接产生明火的施工作业
3.50 置换displacement 用清水、蒸汽,氮气或其他惰性气体将作业管道、设备内部可燃气体替换出来的一种方法
3.51 金属损失metal-lossfteatures 因金属消失导致的管道壁厚减薄
金属损失通常是由于腐蚀、机械损伤及管材缺陷造成的 3.52 管道内检测(L)in-lineinspeetion 利用在管道内运行的可实时采集并记录管道信息的检测器所完成的检测
3.53 几何变形检测gometryinspeetiom 以检测管道的几何变形情况为目的所实施的管道内检测
3.54 金属损失检测metalssinspection 以检测管壁金属损失为目的所实施的管道内检测
3.55 管道特征pipelinefeature 管道上存在的管壁金属损失,凹陷、椭圆度变形、管道附属设施及制造缺陷等
3.56 标定ealibrate 对检测设备的力学性能和检测性能进行测试与调整
3.57 设标marking 为实现对检测出的管道特征精确定位而设置地面测量标记点的工作
3.58 清管pigeing 使用可在管道内独立运行的设备,清理管道内杂质、积垢及凝蜡的工作
3.59 测径板gaugeplate 用于初步测量管径变化的,可产生不可恢复变形的软质金属盘
3.60 检测概率(OD)probabilityofdeteetiom 检测器检测出管道特征的概率
GB/T34275一2017 3.61 可信度(Conf.eonfidenee 检验报告数据与管道实际情况的符合程度
3.62 验证verifieation" 对检测结果进行复核的方式
3.63 腐蚀活性点corrosionaetivity 腐蚀正在进行,并以一定速率发展的部位,该发展速率足以导致管道在设计寿命内的承压能力 降低
3.64 防腐层缺陷eoatingftault 防腐层上所有的异常,包括剥离区和漏点等
3.65 漏点holiday 防腐层不连续处(孔,使管体表面暴露于环境中
3.66 密间距电位测量法eose-intervalpotentialsurvey;Is 沿着管顶地表,以密间隔(1m3m)移动参比电极测量管地电位的方法
3.67 直流电位梯度direeeurremtvotagegradient;DCvG 通过沿管道或环绕管道的由防腐层破损点漏泄的直流电流所产生的土壤中直流电压梯度的变化, 来确定防腐层缺陷位置、大小以及表征腐蚀活性的地表测量方法
3.68 alenatmgc 交流电位梯度 currentvoltagegradient;ACVG 通过沿管道或环绕管道的由防腐层破损点漏泄的交流电流所产生的土壤中交流电压梯度变化,来 确定防腐层缺陷位置的地表测量方法
3.69 管地电位thepipe-to-soilpotential 管道与其相邻电解质(土壤)的电位差
3.70 断电电位ofrpotential 断电瞬间测得的构筑物对电解质(土壤)电位
3.71 交流电流衰减法altermatingcurrentattenuationsurvey 在现场应用电磁感应原理,采用专用仪器测量管内信号产生的电磁辐射,通过测量出的信号电流衰 减变化,来评价管道防腐层总体情况的地表测量方法
收集到的数据可能包括管道位置、埋深,异常位 置和异常类型
10
GB/34275一2017 材料 一般规定 4.1 4.1.1按本标准建造的油气管道系统,所有作为永久性组成部分的材料,在规定的使用条件下,应适 用、安全
所有这些材料应遵守有关技术条件,标准和本标准的要求
4.1.2按本标准制造的钢管或管件等适用于输送原油、成品油
输油管道输送原油的质量应符合 SY7513的规定,输气管道输送天然气的质量应符合GB17820的规定,输送液态液化石油气的质量应 符合GB11174的规定,输送成品油的质量应符合国家现行产品标准
不适用于输送酸性天然气或其 他腐蚀性介质的管道,也不包括基于应变设计地区使用的抗大变形钢管
4.1.3油气管道设计应根据具体条件(包括制造/制作、安装,介质、工况、工作环境和试验等)以及材料 使用要求,选用合适的管道组成件材料 4.1.4油气管道组成件以及其他结构,元件的材质,应根据设计压力、温度和储运介质的物理化学性质 等因素,经技术、经济综合比较分析后确定
4.1.5管道组成件应当逐件采用标志进行标记,标志内容一般包括制造单位代号或商标许可标志、材 料牌号或强度等级、规格、炉批号,产品编号等
产品规格较小,无法标记全部内容时,可采用标签或 按照相关要求省略部分内容
产品标志应当能够追溯到产品质量证明文件
4.1.6油气管道所用材料、管道附件和设备的材质、规格和型号应符合设计要求,所有压力管道元件制 造产品应具有压力管道元件制造的许可,其质量性能应符合本标准所列标准最新版本的规定,并具备产 品质量证明文件,以及材质使用说明书,进口物资应有商检报告
实行监督检验的管道组成件,还应提 供特种设备检验检测机构出具的监督检验证书
质量证明文件除包括产品合格证外,一般还应包括以 下内容: 材料化学成分; a b 材料及焊接接头力学性能; 热处理状态 c 无损检测结果; d 压力试验结果(适用于有关安全技术规范及其相应标准或者合同有规定的) e 型式试验结果(适用于有型式试验要求的 产品标准或用户规定的其他检验项目
g 4.1.7油气管道工程所用的材料、管道附件、设备在使用前,应核对其规格、材质,型号,并应进行外观 检查
4.1.8对材料有复检要求或对材料的质量有疑问时,应按照相关规范的规定对材料进行复检
牌号及 质量性能不明的材料不应用于管道承压)组成件,不合格的材料、管道附件,设备不应安装使用
4.2基本要求 42.1油气管道用钢应采用镇静钢,采用吹氧转炉工艺或电炉冶炼工艺冶炼,经协议也可采用其他相 当的炼钢工艺 4.2.2油气管道组成件用材料应有足够的强度、塑性和韧性,在最低使用温度下应具备足够的抗脆断 能力
4.2.3油气管道组成件用材料应具有足够的稳定性,包括化学性能、力学性能、耐蚀和耐磨性能、抗疲 劳性能等 1
GB/T34275一2017 4.2.4油气管道组成件用材料应适合相应的制造、制作和安装,包括焊接、冷热加工与热处理以及焊接 性等方面的要求
油气管道组成件所使用的焊接材料(煤条,爆丝,焊剂、保护气体等)应符合设计要求,其性能应 4.2.5 与母体材料保持良好的强度与韧性匹配;应进行焊接材料与焊接方法相适应的焊接工艺评定
并根据 合格的煤接工艺评定编制焊接工艺规程
4.2.6油气管道组成件用焊接材料的质量和检验要求应符合GB/T5117,GB/T8110和GB/T17493 等相关标准的规定
对不同生产厂家、不同规格、型号的焊接材料应按照批次、批号分别进行检查 4.2.7当管道组成件采用几种不同的材料组合使用时,应考虑可能产生的不利影响
4.2.8管道组成件的外观应完好无损伤,不应有毛刺、划痕、砂眼及气孔等超标缺陷
4.2.9管道组成件的尺寸偏差应符合现行国家或行业标准的有关规定
4.2.10管道元件用材料及其制造、安装(含现场制作)的技术要求和使用条件不符合本标准规定时,应 当在学习借鉴和实验研究的基础上,将所做试验的依据、条件、数据、结果和第三方的检验报告及其他有 关的技术资料报省级质量技术监督部门审核,国家质量监督检验检疫总局(以下简称国家质检总局)批 准后,方可进行试制试用
4.2.11管道组成件及管道支承固定件、结构附件在施工过程中应妥善保管,不应混淆或损坏,其色标 或标记应明显清晰
防腐后,应对材料表面的标记进行移植
4.3线路用钢管及管件 4.3.1线路用钢管 4.3.1.1天然气管道线路用钢管产品等级应为GB/T9711PSL2级,原油和成品油管道线路用钢管产 品等级宜选GB/T9711PSL2级,其钢管钢级包括GB/T9711中的L.290/X42L.555/X80钢级
选用 钢管产品的质量性能应符合本标准与GB/T9711的规定
4.3.1.2油气管道线路用钢管应综合考虑管道直径壁厚、制造技术成熟度、使用要求及经济适用性,选 择合适的高频焊(HFw)、螺旋缝埋弧焊(SAwH)和直缝埋弧焊(SAwL)包括UOE.JcOE,RBE成形 等)3种类型的钢管
不同管型钢管的规格范围见表1
4.3.1.3为了区别管线的重要程度,根据设计压力、管径将输送原油、成品油和天然气管道划分为不同 级别,见表2,并根据不同级别提出钢管的性能和检验的不同要求
4.3.1.4用于生产螺旋缝埋弧焊钢管的板卷的宽度不得小于钢管外径的1.0倍,也不得大于钢管外径 的2.5倍
钢板或板卷不应含有任何补焊焊缝,制管过程中也不允许进行补煤
4.3.1.5对于不同等级的油气管道用钢,其炼制工艺与夹杂物等的控制要求见表3
对于L485/X70、 L555/X80钢级管线钢,其显微组织应为针状铁素体型 4.3.1.6对于壁厚不大于25.0mm的钢管,其化学成分应符合表4的要求
对于壁厚大于25.0mm的 钢管,其化学成分可参考表4的要求,也可协商确定
表1不同管型钢管的推荐规格范围 尺寸范围 mm 种类 钢级及纲种 最大壁厚 管长 管径 常用 理论 常用 最大 HFW 碳钢及低合金钢 L290/X42L555/X80 219.l610 19 12000 18000 12
GB/34275一2017 表1(续 尺寸范围 mm 种类 钢级及钢种 最大壁厚 管长 管径 常用 理论 常用 最大 碳钢及低合金钢 40 12000 18000 SAW1 L290/X42~L555/X80 5081219 28 sAwH L.290/X42~L555/X8o 碳钢及低合金钢 355.6一1219 20 25 12000 18000 表2油气输送管道级别的划分 管径/mm1 设计压力 管道类型 MPa 508 508~914 9141422 <6.3 原油管道 >6.3 <6,3 成品油管道 6.3 6.3 -8 天然气管道 6.3~ >8 表3油气管道用钢技术要求 管道种类 技术要求 1)制管用的俐材应采用吹氧碱性转炉工艺或电炉工艺冶炼
俐应为细品粒的镇静俐,品粒 尺寸应为ASTME112(或GB/T4335)No.7级或更细; 1,23级输气管道 2)对于3级输气管道用钢管,钢中A,B.c,D类非金属夹杂物级别均不应大于2级; 3)带状组织应不大于3级 1)制管用的钢材须为吹氧转炉或电炉冶炼并经真空脱气、钙和微钛处理的细晶粒(X70及以 上钢级No.10级或更细.x70以下钢级No.8级或更细)纯净镇静钢 4、5级输气管道 2)制管用钢板须用热机械控轧工艺(TMCP)生产; 3)钢中A,B,C,D类非金属夹杂物级别均不应大于2级; 4)带状组织应不大于3级 1)制管用的钢材应采用吹氧碱性转炉工艺或电炉工艺冶炼
钢应为细晶粒的镇静钢,晶粒 尺寸应为AsTMEl12(或GB/T4335)No.7级或更细: 3级原油管道 2)制管用钢板宜采用热机械控轧工艺(TMCP)生产; 3,4级成品油管道 3)钢中A,B.c,D类非金属夹杂物级别均不应大于2.5级 4)带状组织应不大于3级 13
GB/T34275一2017 表4壁厚不大于25.0mm钢管的化学成分 根据熔炼分析和产品分析的最大质量分数 最大碳当量" % 钢号 Si Mn" P ND T 其他 CEnw CEpm 焊接钢管 L290或X42 0.22 0,45 1.30 0.025 0,015 0.05 0.05 0.04 0,43 0.25 L360或X52 0,.22 0.45 1.40 0.025 0.015 0,43 0.25 L390或X56 0,.22 0.45 1.40 0.025 0.015 0,43 0.25 L415或X60 0.12 0.45 1.60" 0.025 0.015 0,43 0.25 L450或x65 0.12 0.45 1.60 0.025 0.015 0,43 0.25 L485或X70 0.12 0.45 1.70" 0.025 0.015 0.43 0.25 L.555或X80 0.12 0.45 1.85 0.025 0.015 0.43" 0.25 根据产品分析
如果碳的质量分数大于0.12%,则cEm极限适用;如果碳的质量分数小于或等于0.12%,则 CEp极限适用
碳含量比规定最大质量分数每降低0,01%,则允许含量比规定最大质量分数增加0.05%,但对于大于或等 于I290或x42小于或等于L360或x52的钢级,最大值不应超过1.65%;对于大于L360或X52小于L485或 X70的钢级,最大值不应超过1.75%;对于大于或等于L485或X70俐级小于或等于L555或X80的俐级, ,最 大值不应超过2.00%
钯、饥和钛的总含量不应超过0.15%
除非另有规定,铜的最大含量为0.50%,镍的最大含量为0.30%,铬的最大含量为0.30%,钼的最大含量为 0.15%,对于L360/X52及以下钢级,不应有意加人铜、铬和镍
除非另有协议
除非另有协议,锯,饥和钛的总含量不应超过0.15%
除非另有规定,铜的最大含量为0.50%,镍的最大含量为0.50%,铬的最大含量为0.50%,钼的最大含量为 0.50%
除非另有规定,铜的最大含量为0.50%,镍的最大含量为1.00%,铬的最大含量为0.50%,钼的最大含量为 0.50%
除非另有规定,不得有意加人B,残留B含量应s0,001%
4.3.1.7应根据钢管的不同使用环境,对钢管进行冷扩径
机械扩径过程中,应采用适当的措施,防止 内扩径装置与焊缝相接触
不同介质与不同制造型式的钢管扩径应满足下列的要求 对于3级原油管道和3级、4级成品油管道用直缝埋弧焊管,应采用全长冷扩径,扩径率不大 a 于1.5%
对于天然气管道用直缝埋弧焊管,应采用全长冷扩径,冷扩径技术要求见表5
b 管径不小于711mm螺旋埋弧焊管管端150nmm范围内宜进行冷扩径,扩径率不大于0.6%
c 14
GB/34275一2017 表5钢管冷扩径技术要求 钢管种类 技术要求 直缝埋弧焊钢管应全长扩径
扩径量范围为0.4%~1.4%
即 扩径后外径-扩径前外径 埋弧炽(SAw 0.,4%< ×100%<1.4% 扩径前外径 管径不小于71lmm螺旋缝埋弧焊管管端150mm范围内宜冷扩径;管端扩径量范围为0%0.6% 可采用扩径或减径的方法将俐管定径至最终尺寸
定径比s,不超过1.5%,即 高频焊(HFW 定径后外径一定径前外径 ×100%<1.5% 钢管规定外宿 4.3.1.8应对每根钢管进行静水压试验,试验过程中整个媒缝或管体无泄漏,试验后无形状的变化和管 壁凸起
试验压力应按GB/T9711的有关规定确定
D小于或等于457mm的钢管,试验压力下的保 持时间应不小于5s;D大于457mm小于或等于914mm的钢管,试验压力下的保持时间应不小于 0s;D大于914mm小于或等于1422mm的钢管,试验压力下的保持时间应不小于15s
当环向应 力达到规定最小屈服强度的95%时,试验压力保持时间应不小于15s 4.3.1.9应从钢管上截取样品进行拉伸试验、弯曲试验和压扁试验等力学性能试验,钢管的拉伸性能应 符合表6对相应钢级的要求
试验方法应符合GB/T9711或设计的相关规定
表6钢管的拉伸性能要求 管体 媒接接头 屈服强度 抗拉强度" 标距长度为50mm 俐级 最小抗拉强度 最大屈强比 R-/MPa Rw.s/MPa 的最小伸长率 R0.,s/R R/MPa 最小 最大 最小 最大 Afmin/% L290N或x2N L290Q或X42Q 290 495 415 760 0,.93 415 L290M或X42M L360N或X52N 360o 530 460 76o 0.93 46o .360Q或X52Q L360M或X52M L390N或X56N 545 Q或X56Q L390Q 390 490 760 0.93 490 L.390M或X56M L415N或X60N 565 520 760 520 L415Q或X60Q 415 0,.93 I415M或X6oM L450Q或X65Q 450 600 535 760 0.93 535 1450M或X65M L485Q或X70Q 485 635 570 76o 0.93 570 1485M或X70M L555Q或X8oQ 555 705 625 8825 0.93 625 L.555M或X8oM 15
GB/T34275一2017 表6(续 管体 媒接接头 屈服强皮 抗拉强度 标距长度为50mm 钢级 最大屈强比 最小抗拉强度 Rms/MPa R./MP 的最小伸长率 R/MPa Ra;/R. Ai/% 最小 最大 最小 最大 规定最小伸长率Amm应按下式计算确定 A9 Anmin=C U0 式中 采用国际单位制为1940; A 适用的拉伸试样横截面积,单位为平方毫米(mm=),按下列方法确定 对于圆棒试样,直径为12.5mm和8.9mm的试样为130mm';直径为6.4mm的试样为65mm 2 对于全截面试样,取 和b)采用钢管规定外径和规定壁厚计算的试样横截面积两者中的 a)485mm" 较小者,圆整到最接近的10mm'; 3 对于条形试样,取a)485mm和b)采用试样规定宽度和钢管规定壁厚计算的试样横截面积两者中 的较小者,圆整到最接近的10mmr -规定最小抗拉强度,单位为兆帕(MPa).
4.3.1.10应从钢管上截取样品进行cvN冲击试验、DwTT试验拉伸试验
对于天然气输送管道,应 对管体提出防止裂纹长程扩展的止裂韧性要求;对于焊缝、热影响区则提出防止启裂的韧性要求
天然 气管道防止长程裂纹扩展的止裂韧性冲击功值要求应按表7所述的方法来确定,必要时应对要求值进 行修正 对于3级及以下级别天然气管道用钢管的焊缝和热影响区,3个试样夏比冲击功平均最小值 a 0J,单个试样最小值为30J
b 对于4级天然气管道用钢管的焊缝和热影响区,3个试样夏比冲击功平均最小值为60J,单个 试样最小值为45
对于5级天然气管道用钢管的焊缝和热影响区,3个试样夏比冲击功平均最小值为80J,单个 试样最小值为60J
试验温度与管体试验温度相同
对于原油与成品油管道,钢管与焊缝及热影响区的cVN冲击值应符合表8对相应钢级的 d 要求
油气管道用钢管管体CVN冲击试验断口剪切面积应符合表9的要求
e fD 对于埋地天然气管道,钢管CVN冲击试验温度为一5C
对于埋地原油管道和成品油管道 钢管夏比冲击试验温度为0C
如果管道钢管的最低设计温度低于0C,可在最低设计温度 下进行试验 对于锅级不低于x52,管径在508" nmm一1422mm之间的钢管,应进行落锤撕裂试验
落锤 撕裂试验(DwTT)的剪切面积要求和试验温度如表10所示
16
GB/34275一2017 表7确定陆上埋地输气管线用钢管延性断裂止裂CVN夏比冲击功值的方法 序号 方法 来源 内容 适用范围 18 D Kv=C×i× 式中 钢级
GB/T34275一2017 表10落锤撕裂试验要求 DwTT最小剪切面积百分比/(sA%) 管道级别 试验温度" 单个值 2个试样平均值 60 1级原油、成品油和天然气管道 40 80 60 2级、3级原油和成品油和天然气管道 4级成品油管道和4级、5级天然气管道 85 70 如果管道钢管的最低设计温度低于0C,可在最低设计温度下进行试验
壁厚超过25.4mm的钢管,由购方和制造商双方另行协商确定
4.3.1.11 对于HFW钢管,应做压扁试验
其试验结果应符合下列要求 对于壁厚大于或等于12.7mm,钢级大于或等于L415/X60的钢管,板间距离达到钢管原始外 a 径的66%时,焊缝应不出现开裂
对于钢管钢级和规定壁厚的所有其他组合,板间距离达到 钢管原始外径的50%时,焊缝应不出现开裂
b 对于直径与壁厚比值大于10的钢管,板间距离达到钢管原始外径的33%时,除焊缝之外的金 属不应出现裂纹或断裂
对所有钢管,继续压扁,直到钢管的管壁贴合为止,在整个压扁试验过程中,不得出现分层或过 烧金属的迹象
4.3.1.12所有规格的埋弧焊钢管焊缝应进行导向弯曲试验
试验过程中试样边缘出现的裂纹,只要其 n,应视为试验合格;如试样出现其下列任一种状况时,应视为试验不合格 长度不超过6.4mm 完全断裂; a 在焊缝金属处出现任何长度大于3.2mm的裂纹或断裂,无论深度如何 b 在母材金属、热影响区或熔合线处出现任何长度大于3.2mm,深度大于规定壁厚的12.5%的 C 裂纹或断裂
4.3.1.13为了控制钢管的残余应力,可采用切环法对残余应力进行检测
选取长度为200mm左右的 管段,在距焊缝100mm处沿钢管纵向切开,然后测量管段周向张开量(切口张开间距)
不同运行压 力,不同管径情况下钢管切口张开间距应满足表11要求
表11切口张开量要求 最大切口张开量/mm 运行压力 管径/mm MPa 323.9一762 >762 <6.3 8o 100 6.38 8o 100 8o 90 4.3.1.14油气输送用钢管的检验,应按制管标准检查钢管的外径、壁厚,圆度等钢管尺寸偏差,尺寸偏 差应符合表12要求,设计或购方有特殊要求时,按照订货要求执行
钢管表面不应有裂纹、结疤、折叠 以及其他深度超过公称壁厚偏差的缺陷
钢管如有凿痕、槽痕、凹坑、变形或压扁等有害缺陷应按下列 方法修复或消除后使用: 18
GB/34275一2017 凿痕、槽痕可用砂轮磨去,但磨剩的厚度不应小于材料标准允许的最小厚度,否则,应将受损部 a 分整段切除
凹坑的深度不应超过公称管径2%
凹坑位于纵向焊缝或环向焊缝处,应将凹坑处管子受损 b 部分整段切除
变形或压扁的管段超过制管标准规定时,应修复,不能修复的应废弃
弯管端部应标注弯曲角 度、钢管外径、壁厚、曲率半径及材质等参数
凡标注不明或不符合设计要求的不应使用
表12钢管尺寸偏差要求 椭圆度 钢管直径D 要求级别 管端直径公差 管体直径偏差 mmm 管端 管体 士0.75%D, 士0,5%D 219.1
GB/T34275一2017 表13热煨弯管、冷弯弯管的外观和主要尺寸要求 种类 曲率半径 外观和主要尺寸 其他规定 无褶皱、裂纹、重皮、机械损伤;两端椭圆度小于或等于 1.0%,其他部位的椭圆度不应大于2%,外径偏差十2.应满足清管器和探测仪器颗利 >4D 热偎弯管 -1,壁厚减薄量<9%壁厚,弯曲半径小于或等于通过;端部直管段>1D且不小 1000mm时,允许偏差为士5mm;弯曲半径大于于0.5m 1000mm时,允许偏差为士0,5%,弯曲平面度7.0mm 无裂纹,机械损伤,弯管椭圆度小于2.0%,弯曲角度误 冷弯弯管 差在士0.2",其平面度不大于8mm冷弯管州折深度<端部2m的直管段 30DN 3mmm 注D为管道外径,DV为冷弯弯管的公称直径 4.4站场用钢管及附件 4.4.1站场用钢管 4.4.1.1站场内管道所用钢管宜采用油气输送钢管,钢管的规格与性能应符合本标准和GB/T9711的 规定;站场内管道采用油气输送钢管有困难时,也可采用设计规定的相关标准的钢管
4.4.1.2站场用钢管选型的基本要求 对于钢管公称直径小于或等于300mm时,宜采用无缝钢管; a 对于钢管公称直径大于300mm小于或等于600mm时,宜选用高频电阻焊钢管,也可选用螺 b 旋缝埋弧煤钢管或直缝埋狐媒钢管; c 对于钢管公称直径大于500mm时,宜选用螺旋缝埋弧焊钢管或直缝埋弧焊钢管
4.4.1.3 钢管用钢材须为纯净镇静钢,L485/X70强度级别材料晶粒度应为No.10级或更细;L450/X65 I360/" L360/X52强度级别材料品粒度应为No.8级或更细;低于 /X52强度级别材料晶粒度应为No.6级或 更细
无缝管用钢材应为吹氧转炉或电炉冶炼、晶品粒应为No.,6级或更细的纯净镇静钢
4.4.1.4钢材中A、B.C、D类非金属夹杂物级别限定如表14所示
L485/X70强度级别钢材带状组织 评定应不大于3级
L450/X65及以下强度级别钢材带状组织评定结果应不大于4.5级
表14非金属夹杂物级别限定 别 级 钢级 薄 早 薄 厚 薄 厚 薄 厚 L485/X70 <2.0 2.0 二2.0 <2.0 二2.0 2.0 <2.0 2.0 其他 2.5 2.5 2.5 2.5 二2.5 2.5 二2.5 2.5 4.4.1.5对于外径为ll4.3mm及以上的站场用钢管,其夏比冲击试验按GB/T9711相关要求进行;当 钢管外径为70mm~114.3mm,且壁厚不小于6.5mm时,应取纵向试样进行夏比冲击韧性试验
夏 比冲击试验温度选取原则应满足下列要求 钢管及其焊缝的夏比冲击试验温度应考虑当地最低环境温度(最低环境温度可按该地区气象 a 资料,取历年来月平均最低气温的最低值
月平均最低气温是指当月各天的最低气温值相加 20
GB/34275一2017 后除以当月的天数),试验温度应不高于管线通过地区当地最低环境温度,试验温度一般取 -10C、-20C或一30C,且冲击功应满足表15的要求
剪切面积百分数仅提供数据供参考
b 当最低环境温度低于一30C时,试验温度取一45C,或/和采取保温或伴热等工艺措施,确保 采取工艺措施后管道壁温度不低于一30C
冲击功也应满足表15的要求
站场埋地钢管应在一5C下进行夏比冲击韧性试验
如果协议在更低的试验温度下进行夏比冲击试验,其在该温度下的夏比冲击功满足规定的冲 d 击试验结果要求,可认为该试验合格
表15夏比冲击韧性要求(10mmx10mmx55mmm) 各种强度级别钢管夏比冲击功"刀 管径 取样位置 试验温度 >B/1245 D/mnm B/L.245 X80/L555 X70/I485 27(20) 27(20) 焊接接头 508 管体母材 27(20) 40(30) -5 焊接接头 27(20) >508 -10C 762 管体母材 54(40) -20C >762 焊接接头 40(30) -30 914 管体母材 80(60) c -45 媒接接头 40(30) 50(40 >914 <1219 80(6o) 90(75) 管体母材 夏比冲击功数值,括号外为3个试样最小平均值,括号内为单个试样最小值
4.4.1.6站场用钢管应按照GB/T9711进行落锤撕裂试验(DwTT),其在0C下的断口剪切面积的最 小百分数要求见表16
表16DwTr(落锤撕裂试验)剪切面积的最小百分数要求 试验温度 两个试样最小平均值 " 0 40 4.4.1.7站场用钢管外径的允许偏差为十0.5%D-0.15%D,但钢管外径的正偏差最大为4.0mm; 100nmm以内管端外径允许偏差为十1.6mm-0.,5nmm;钢管一端的外径与另一端外径之差不得大于 2.0mtm
距管端100mm范围内钢管的椭圆度即最大外径与最小外径之差与公称外径的比值)应不 大于0.6%,其余部分椭圆度应不大于1.2%.
4.4.1.8站场用钢管壁厚允许偏差应为公称壁厚的一3%~十7%
无缝管壁厚允许偏差应为公称壁厚 的一10%十12.5%
4.4.2站场用管道附件 4.4.2.1用于制造站场用管件的原材料应是采用吹氧转炉或电炉冶炼的全镇静钢,且具有要求的韧性 和热处理状态,并适合与油气输送管道用钢管及管件进行现场焊接 4.4.2.2制造管件的原材料应为各类锻件,板材,无缝管或有填充金属的焊接钢管
弯头本体不应有丁 21
GB/T34275一2017 字或环形焊缝
4.4.2.3制造管件的原材料应为焊接性良好的碳钢或低合金高强度钢,当管件与连接钢管焊接需要预 热时,制造商应说明规定的预热条件,并在管件上做出永久性标记 4.4.2.4制造商采用的管件制造材料,其化学成分、力学性能及检验应符合GB/T29168.2的要求
为 了满足产品性能要求,用低合金高强度钢制作的管件,其合金元素的选用应由购方和制造商协商确定、 并由制造商按所供管件强度级别分别做出适用性评价报告
444.2.5管件可采用压制拔制、冲压,挤压,焊接等加工工艺进行制造,所采用的工艺,应保证不产生裂 纹缺陷和其他有碍于使用的损伤
若供方采用冷成型方式制造管件,应经过购方认可
4.4.2.6管件所用焊接材料在产品热处理后,其焊接接头拉伸性能和夏比冲击韧性应满足4.4.2.7和 4.4.2.8的要求
4,4.2.7成品管件母材的棒状、全壁厚矩形和焊接接头的全壁厚矩形拉伸试验结果应符合 GB/T29168.2的要求
4.4.2.8成品管件的母材,焊缝及热影响区在试验温度下的夏比V型缺口冲击韧性试验结果应符合 表19的要求
夏比冲击试验温度选取原则如下 管件夏比冲击试验温度应考虑当地最低环境温度,试验温度应低于管线通过地区当地最低环 a -20C或一30c,且冲击功应满足表17的要求
境温度,试验温度一般取一10C 当最低环境温度低于一30C时,试验温度取一45C,或采取保温或伴热等工艺措施,当采取 b 工艺措施后管道壁温度应不低于一30C
冲击功亦应满足表17的要求
埋地管件应在一5C下进行夏比冲击韧性试验
c d)允许采用更低试验温度进行夏比冲击试验,但其在该温度下夏比功应满足规定冲击试验结果 要求
表17管件夏比冲击韧性要求 夏比冲击功 剪切面积 试样位置 强度等级 试验温度 SA% 单个试样最小值 三个试样最小平均值 60 I.555/X80 45 " -5 提供数据 母材 L485/X70 40 30 10C L.245/B -20 50 L.555/X80 -30 焊缝、 /X70 提供数据 L485/ -45 热影响区 40 30 >L.245/B 4.4.2.9站场钢制管法兰用材料应遵循下列原则选用 满足压力和温度要求,材质从低级向高级选用 a b)满足介质要求;碳钢与低合金钢一般优先采用16Mn;不锈钢一般优先采用材料304 0Crl8Ni9); 管法兰材料一般应采取锻制,但板式平法兰、法兰盖可用钢板制作; c d 材料选用应注明标准号,表明是钢板还是锻件
站场钢制管法兰用材料应为镇静钢,其制造及热处理、化学成分及力学性能检验等应符合 4.4.2.10 G;B/T29168.3的要求
22
GB/34275一2017 4.4.2.11 站场用钢制管件的尺寸、公差、技术要求、检验、标志和包装,应符合GB/T12459 GB/T13401和sY/T0609与sY/T0510的规定
站场用管道附件质量要求 4.4.3 4.4.3.1管件、紧固件的检验应符合下列规定 管件、紧固件尺寸偏差应符合国家现行有关标准的规定; a 管件及紧固件使用前,应核对其制造厂的出厂合格证、质量证明文件; b c 应按设计图纸(文件)核对管件所标注管径壁厚、压力等级、材质等参数 管件及紧固件技术要求应符合设计要求,设计无要求时应符合JB/T1308.2的有关规定
d) 4.4.3.2弯头、异径管、三通、管帽的质量应符合以下条件 a 管件表面不应有裂纹,过热,过烧等; b 管件内外表面应光滑、无有损强度及外观的缺陷,如结疤、划痕、起皮等; 不应用焊接方式对管件焊缝错边超标部分进行修补; c 弯头、三通、异径管、管帽的尺寸和几何形状误差值应符合设计及sY/T0609与sY/T0510 d 的规定; 弯头的端面倾斜偏差、弯曲角度偏差及圆度、曲率半径偏差,应符合表18的要求 表18弯头允许偏差 公称直径 mm 检查项目 25~65 80100 125~200 >250 端面倾斜 S1.0 <1.0 <1.5 <1.5 mm 曲率半径 士2 士3 士4 士5 mm 弯曲角度 士1" 士I 士1 士1 圆度 <公称直径的1% 弯头壁厚减薄量应小于厚度的10%,且实测厚度不应小于设计计算壁厚; mm2mm
弯头坡口角度应满足设计规格书或焊接工艺要求,宜为35"士5",钝边宜为1" g 4.4.3.3异径管、三通,管帽等管件的质量应符合sY/T0609与SY/T0510的规定 4.4.3.4法兰的质量应符合下列要求 法兰的尺寸和几何形状误差值应符合设计及相关标准的规定 a b 法兰密封面应光滑、平整,不应有毛刺、径向划痕、砂眼及气孔 对焊法兰的尾部坡口处不应有碰伤 螺纹法兰的螺纹应完好; d e 法兰连接件螺栓、螺母,垫片等应符合装配要求,不应有影响装配的划痕,毛刺,翘边等 4.4.3.5支管座的质量应符合GB/T19326的规定,并应满足下列要求: a 支管座的外观不应有裂纹、,过烧、重皮、结疤、夹渣和大于接管壁厚5%的机械划痕或凹坑
焊 接玻口应光滑过渡
玻口围应清洁,无锈斑
b 支管座的壁厚等级,无损检测等应符合现行国家标准的规定
23
GB/T34275一2017 支管座尺寸允许偏差应符合表19的规定
表19支管座尺寸允许偏差 单位为毫米 公称直径 项目 类型 -20 25一100 125一300 350一600 极限偏差 士1.6 士3.2 结构高度 所有支管座 士0.8 士4.8 支管公称壁厚 不小于公称壁厚的87.5% 与支管连接处的端部外径 对煤支管座 十0.8,一0.4 十1.6,一0.8 与支管连接处的端部内径 士0.4 士0.8 承插孔直径 +0.5,0 承插焊直管座 流通孔径 +1.5,0 4.4.3.6绝缘接头(法兰质量应符合下列要求: a 绝缘接头(法兰)外观应平整、端部坡口内测以及锻件本体内侧应与所接管道的内侧齐平
对 焊坡口不应有严重的损伤
b)表面涂层用设计规定的绝缘电压值进行电火花检测应无漏电
c 绝缘接头压力等级应符合设计要求
绝缘接头的绝缘电阻值应大于10MQ
4.4.3.7汇管的质量应符合下列要求 管汇外观不应有裂纹、伤痕、毛刺,内部锈斑与污物;管汇的内部应清洁
对焊坡口不应有损伤 a 管汇支管间距尺寸误差应符合设计及相关标准的规定
b 管汇由锻制三通或四通制作时其扳边端口应平齐,扳边高度应高于扳边口外轮廓线的曲率半径, c 与支管内径相匹配的开孔内径拔梢段的锥度不小于1:3;扳边端口的坡口尺寸应符合设计要求
4.4.3.8紧固件质量应符合下列要求: 外观不应有裂纹、重皮、伤痕、毛刺、砂眼及气孔 a b 尺寸应符合设计要求; c 材质应符合设计要求; d 用于管道上的螺栓、螺母应符合国家现行有关标准的规定,使用前应从每批中各取两根(个) 进行硬度检查,不合格时加倍检查;仍有不合格时,逐根(个)检查,不合格者不应使用
螺栓 硬度不合格,取最高、最低各一根校验机械性能,若有不合格,取硬度相近的螺栓加倍校验,仍 有不合格,则该批螺栓不应使用
4.4.3.9支吊架的检验及其质量要求应符合下列规定 a 支吊架表面应无毛刺、铁锈、裂纹,漏焊,表面气孔等; 支吊架用的弹簧表面不应有裂纹、折叠,分层、锈蚀等缺陷,工作圈数偏差不应超过半圈; b 自由状态时,弹簧各圈节距均匀,其节距允许偏差不应大于平均节距的10%; c d)弹簧两端支撑面与弹簧轴线应垂直,其允许偏差不应大于自由高度的2%
4.4.3.10管线补偿器检验应按出厂说明书和设计要求进行,其尺寸偏差应符合下列要求 “"“1”形补偿器的弯曲钢管的圆度不应大于外径的8%,壁厚减薄量不应大于公称壁厚的 a 15%,且壁厚不小于设计壁厚, D)“I”形补偿器悬臂长度允许偏差为士10mm;平面翘曲每米允许偏差为士3mm,且总长平面 24
GB/34275一2017 翘曲允许偏差为士10mm 4.5阀门 45.1阀门的设计、制造、,测试等应符合GB/T19672,GB/T20173及相关标准的要求
阀门的检验应符合GB/T26480的要求 4.5.2 4.5.3应有产品合格证,带有伺服机械装置的阀门应有安装使用说明书
4.5.4现场安装的阀门应逐个进行外观检查,其外观质量应符合下列要求: 阀体、阀盖、阀外表面无气孔、砂眼、裂纹等; aa 垫片,填料应满足介质要求,安装应正确, b 丝杆、手轮、手柄无毛刺、划痕,且传动机构操作灵活、指示正确 c d 铭牌完好无缺,标识清晰完整; 备品备件应数量齐全、完好无损
e 4.5.5阀门应按要求进行试压检验,强度和密封试验应符合下列要求 工厂阀门压力试验应按工厂制造阀门依据的标准进行,并由买方在工厂内监督制造和试压
a 依据标准为GB/T26480
需要现场进行阀门压力试验应按使用说明书要求执行,无要求时按下列要求执行 试压用压力表精度不应低于1.0级,表的量程应为被测压力(最大值)的1.5倍~2倍,并 应经检定合格
阀门应用洁净水为介质进行强度和密封试验,强度试验压力应为管道设计压力的1.5倍 稳压时间应大于5min,壳体,垫片,填料等不渗漏,不变形,无损坏,压力不降为合格
密 封试验压力应为设计压力,稳压15min,不内漏压力不降为合格
3 止回阀,截止阀可按流向进行强度和密封试验
止回阀应按逆流向做密封试验、顺流向 做强度试验,截止阀可按顺流向进行强度和密封试验
阀门试压合格后,应排除内部积水包括中腔),密封面应涂保护层,关闭阀门,封闭出人 口,并应填写阀门试压记录
安全阀安装前应由取得资质认定的单位进行调试
调试合格后应铅封,并应有合格的标识
安 4.5.6 装后保留铅封
4.5.7液压球阀驱动装置,应按出厂说明书进行检查,压力油应在油标2/3处,各部驱动灵活
4.5.8电(液)驱动阀应按使用说明书检查其驱动装置,传动装置应灵活;电气部分、液压管路应无故 障;液压油、,润滑油应足量、合格
4.6焊接材料 焊接材料应符合下列规定 焊材的品种和型号应符合焊接工艺规程的要求,焊材包装应完好,标识应清晰; aa 焊条应无破损、霉变、油污、锈蚀;焊丝应无锈蚀和折弯;焊剂应无变质现象;保护气体的纯度 b 和干燥度应满足焊接工艺规程的要求; 焊接材料生产厂商应随货提供必要的质量证明文件,工程使用前采购方应对不同批号的媒接 材料进行复检; 保护气体应达到规定的纯度
二氧化碳气体纯度不宜低于99.5%,含水量和含氧量不超过 0.1%,气路系统中应设置干燥器和预热装置
氯气纯度不宜低于99.96%
25
GB/T34275一2017 4.7防腐及补口用材料 4.7.1线路管体外防腐材料可采用三层结构聚乙烯外防腐层、单层环氧粉末外防腐层、双层熔结环氧 粉末外防腐层等结构
应根据环境条件及工况要求选择适宜的外防腐层材料,防腐材料的质量性能应 符合有关技术条件、标准的要求
4.7.2站场工艺管道埋地主管道可采用与线路外防腐材料相同的材料,也可采用无溶剂环氧液体防腐 再缠绕增强型聚丙烯冷缠带
其他管道可采用无溶剂环氧液体防腐,异型连接件可采用粘弹体防腐,地 上管道防腐涂层面层应采用耐候涂层 4.7.3管体外防腐层补口材料可采用辐射交联聚乙烯热收缩套/带(以下简称热收缩套/带、热缩压敏 带,无溶剂聚胺脂和无溶剂环氧液体补口涂料等
应根据环境条件及工况要求选择适宜的外防腐层补 口材料,外防腐层补口材料的质量性能应符合有关技术条件、标准的要求
4.7.4管道防腐用材料的技术要求和使用条件不符合本标准规定时,应当在学习借鉴和实验研究的基 础上,将所做试验的依据、条件、数据、结果进行评价,并进行相关现场试验后,经设计允许方可试用
并 满足下列要求 管体防腐层材料的技术性能应满足管道的使用要求且具有成熟的施工工艺 a b)防腐补口材料应与管体防腐层材料相同或相容,且施工工艺应能适应具体工程的现场施工环 境及施工条件
4.8阴极保护材料 4.8.1强制电流系统的辅助阳极有;高硅铸铁阳极、石墨阳极、钢铁阳极、柔性阳极、金属氧化物阳极 等,其主要性能应符合以下要求 高硅铸铁阳极的化学成分应符合表20的规定,阳极的允许电流密度为5A/m80A/m,消耗 a 率应小于0.5kg/(Aa)
阳极引出线与阳极的接触电阻应小于0.01Q,拉脱力数值应大于阳极 自身质量的1.5倍,接头密封可靠;阳极引线长度不应小于1.5m,阳极表面应无明显缺陷
表20高硅铸铁阳极化学成分 主要化学成分的质量分数/% 杂质质量分数/% 序号 类型 Si Mn C Fe 14.2515.25 0.801.05 s0.25 普通 0.51.5 余量 s0.1 14.25~15.25 s0.,25 加允 0.51.5 0.8l,4 45 余量 0.l b)石墨阳极的石墨化程度不应小于81%,灰分应不大于0.5%,阳极宜经亚麻油或石蜡浸渎处 理,阳极的性能应符合表21的规定
阳极引出电缆与阳极接触电阻应小于0.01Q,拉脱力数 值应大于阳极自身质量的1.5倍,接头密封可靠;阳极引线长度不应小于1.5m阳极表面应无 明显缺陷 表21石墨阳极主要性能 密度 电阻率 气孔率 消耗率 允许电流密度 g/m Qmm'/m % kg/(Aa) A/m 1.7~2.2 9.5~l1.0 25~30 0.6 5一l0 26
GB/34275一2017 柔性阳极是由导电聚合物包覆在铜芯上构成,其性能应符合表22的规定,阳极铜芯截面积为 16mm,阳极外径为13mm 表22柔性阳极主要性能 最大输出线电流密度/(mA/m) 最低施工温度 最小弯曲半径 无填充料 有填充料 mm 52 82 -18 150 钢铁阳极是指角钢扁钢、槽钢、钢管制作的阳极或其他用作阳极的废弃钢铁构筑物,理论阳 极的消耗率为9.1kg/Aa)10kg/Aa). 混合金属氧化物阳极基体材料采用工业纯钛,其化学成分应不低于GB/T3620.1中对TA2的 要求,在土壤环境中(带有填料)金属氧化物阳极的工作电流密度为100A/m,阳极与电缆接 头的接触电阻应小于0.01Q.
4.8.2强制电流系统的辅助阳极有:锌合金牺牲阳极和镁合金牺牲阳极等,其主要性能应符合以下 要求 锌合金牺牲阳极的成分见表23,其棒状锌合金牺牲阳极的电化学性能见表24,带状锌合金牺 a 牲阳极的电化学性能见表25,带状锌合金牺牲阳极的规格尺寸见表26,带状锌合金牺牲阳极 截面示意图见图2
表23锌合金牺牲阳极化学成分 锌合金主要化学成分的质量分数 /% 高纯锌主要化学成分的质量分数/% 元素 A 0.1一1.5 0.005 Cd 0.0250.07 s0.003 Fe S0,005 <0,0014 Pb <0.006 <0,003 Cu 0.005 S0.002 其他杂质 总含量0.1 Zn 余量 余量 表24棒状锌合金牺牲阳极电化学性能 性能 锌合金、高纯锌 备注 密度/g/m 7.14 开路电位/V 1.03 相对SCE 理论电容量/[Ah)/kg 820 电流效率/% 95 在海水中 发生电容量/[(Ah)/kg 780 条件下 3mAcm 消耗率/[kg/(A a 11.88 27
压力管道规范长输管道GB/T34275-2017
作为目前我国长输管道工程建设中最主要的管道类型之一,压力管道的规范非常重要。而在这方面,GB/T34275-2017规范则是当前国内较为权威的规范之一。
该规范对于压力管道的设计、材料选择、制造、安装、检验、验收以及使用和维护等方面都做出了详细规定。其中,特别强调了对于高强度钢管的使用,对于焊接和无缝钢管的区分以及使用方面也有相应的规范和要求。
此外,在施工和验收方面,规范也提出了详细的要求。例如,规范中规定了压力管道的施工必须由经专业培训合格的作业人员进行;在验收方面,则要求对于管道的材料、制造、尺寸、结构、焊缝和无损检测等方面都必须进行严格检查。
总体来说,GB/T34275-2017规范是我国目前长输管道建设中不可或缺的重要规范之一。而在实际应用时,也需要加强对相关规范的理解和贯彻,以确保长输管道工程建设的安全和可靠性。