GB/T19854-2018
爆炸性环境用工业车辆防爆技术通则
Generalrulesofexplosion-prooftechniquesofindustrialtrucksforexplosiveatmospheres
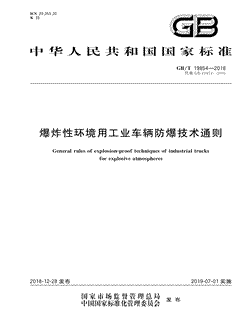
- 中国标准分类号(CCS)K35
- 国际标准分类号(ICS)29.260.20
- 实施日期2019-07-01
- 文件格式PDF
- 文本页数39页
- 文件大小2.98M
以图片形式预览爆炸性环境用工业车辆防爆技术通则
爆炸性环境用工业车辆防爆技术通则
国家标准 GB/T19854一2018 代替GB19854一2005 爆炸性环境用工业车辆防爆技术通则 Generalrulesofexplosion-profteehmiques ofindustrialtuckS forexplosiveatmospheres 2018-12-28发布 2019-07-01实施 国家市场监督管理总局 发布 币国国家标准化管理委员会国家标准
GB/T19854一2018 目 次 前言 范围 2 规范性引用文件 术语和定义 安全要求和安全措施 5 安全要求和安全措施的检验 l6 制造商向用户提供的资料 标志与标牌 附录A(资料性附录》车祸分级与场所分区的关系 18 19 附录B资料性附录本标准与相关标准关于车辆分级的对应关系 附录c(资料性附录用"设备保护级别"的方法对防爆设备进行危险评定的介绍 20 23 附录D(资料性附录蓄电池组电源装置防爆技术资料 附录E规范性附录使用说明牌 32 附录F资料性附录)蓄电池组电源装置的报废和更换 33 附录G(资料性附录GB3836.1一2010与GB12476.1一2013关于爆炸性粉尘环境用电气设备 防爆型式标注方法的对应关系 35 参考文献 36
GB/T19854一2018 前 言 本标准按照GB/T1.1一2009给出的规则起草
本标准代替GB19854一2005《爆炸性气体环境用工业车辆防爆技术通则》,与GB19854一2005相 比,主要技术变化如下 -增加了定义“故障”“预期故障”“罕见故障”(见3.9,3.9.1和3.9.2); 删除了定义“紧急制动功能”和“紧急制动装置”(见2005年版的3.7和3.8); 增加了Gc级车辆宜安装气体探测器的要求(见4.1.6.2); -增加了往复式内燃机的要求(见4.1.4.1、4.2.5.1、4.3.3.1,4.4.4.1); 修改了Gc,Gb蓄电池组的要求(见4.1.4.2、4.,2.5.2,2005年版的4.1.4.,2,4.2.5.2); -增加了De,Db蓄电池组的要求(见4.3.3.,2、4.4.4.2); 删除了附录“各种危险一览表”见2005年版的附录A); 修改了车辆分级方法见附录A,2005年版的附录G); 增加了附录“本标准与相关标准关于车辆分级的对应关系”见附录) 增加了附录“用"设备保护级别'的方法对防爆设备进行危险评定的介绍"见附录c); 删除了附录“本标准章条编号与EN1755;2000章条编号对照一览表”(见2005年版的附录E); 增加了附录“GB3836.12010与GB12476.1一2013关于爆炸性粉尘环境用电气设备防爆型 式标注方法的对应关系”(见附录G)
本标准由电器工业协会提出 本标准由全国防爆电气设备标准化技术委员会(sAc/Tc9)归口
本标准起草单位;南阳防爆电气研究所有限公司南阳二机防爆消防装备有限公司、国家防爆电气 产品质量监督检验中心、杭叉集团股份有限公司、衡阳合力工业车辆有限公司
本标准主要起草人;张显力、张朋、张刚黄晓平、黄嘉斌、刘姐云
本标准所代替标准的历次版本发布情况为 GB19854一2005
GB/T19854一2018 爆炸性环境用工业车辆防爆技术通则 范围 本标准规定了爆炸性环境用工业车辆,包括负载装卸装置(以下简称为车辆)的安全要求和安全措 施,以及这些安全要求和安全措施的检验等防爆技术要求
本标准适用于爆炸性环境用工业车辆的防爆结构设计,制造和检验
本标准不适用于煤矿井下用车辆和炸药粉尘环境用车辆
注1爆炸性环境分为 a)可能出现气体、蒸气或薄雾爆炸性气体的场所,分别定义为1区和2区; b5 可能出现可燃性粉尘的场所,分别定义为21区和22区
注2:车辆分级和场所分区之间的对应关系,如附录A所示
此外 a 气体,燕气或薄雾的爆炸性环境用I类车辆,按爆炸性环境内相应的气体混合物种类,还可进一步分类 为IA、IB和lC
标志为B的车辆可适用于要求标志为A的车辆的使用条件;标志为IC的车辆 可适用于要求标志为IA和lB的车辆的使用条件,但不适用于含有二硫化碳的可燃性气体和燕气的 场所
粉尘,飞絮的爆炸性环境用川类车辆,按爆炸性环境内相应的粉尘混合物种类,还可进一步分类为A、 b 川B和Ic
标志为IB的车辆可适用于要求标志为lA的车辆的使用条件;标志为c的车辆可适用 于要求标志为WA和WB的 辆 两的1 车 1使用条件 注3:车辆应用于混杂混合物的场所时,需能同时满足对气体、蒸气和薄雾的要求,以及对粉尘的要求
注4货叉,负载装卸装置或配用的附属装置是车辆的组成部件;安装在载重架或货叉上的附属装置不是车辆的组 成部件
规范性引用文件 下列文件对于本文件的应用是必不可少的
凡是注日期的引用文件,仅注日期的版本适用于本文 件
凡是不注日期的引用文件,其最新版本(包括所有的修改单)适用于本文件
GB/T1408.1绝缘材料电气强度试验方法第1部分:工频下试验 GB/T1410固体绝缘材料体积电阻率和表面电阻率试验方法 GB/T3836(所有部分)爆炸性环境 GB3836.1一2010爆炸性环境第1部分;设备通用要求 GB3836.22010爆炸性环境第2部分;由隔爆外壳“d”保护的设备 GB.3838.3一2010爆炸性环境第3部分由增安型"”保护的设备 GB3836.4一2010爆炸性环境第4部分;由本质安全型“;”保护的设备 GB3836.82014爆炸性环境第8部分;由“n”型保护的设备 GB3838.9一2014爆炸性环境第9部分;用浇封型“m"保护的设备 GB/T3836.15一2017爆炸性环境第15部分;电气装置的设计、,选型和安装 第18部分;本质安全电气系统 GB/T3836.182017爆炸性环境 GB/T3836.22一2017爆炸性环境第22部分:光辐射设备和传输系统的保护措施
GB/T19854一2018 GB/T4208一2017外壳防护等级(IP代码 GB/T10715带传动多楔带,联组V带及包括宽V带,六角带在内的单根V带抗静电带的导电 性;要求和试验方法 GB12476.12013可燃性粉尘环境用电气设备第1部分;通用要求 GB12176.4-2010可燃性粉尘环境用电气设备第4部分;本质安全型"iD" GB12476.5一2013可燃性粉尘环境用电气设备第5部分;外壳保护型“D" GB12176.6一2010可燃性粉尘环境用电气设备第G部分浇封保护型"mD" GB12476.7一2010可燃性粉尘环境用电气设备第7部分;正压保护型“pD” GB/T16855.12018机械安全控制系统安全相关部件第1部分;设计通则 GB20800.1一2006爆炸性环境用往复式内燃机防爆技术通则第1部分;可燃性气体和燕气环 境用I类内燃机 GB20800.2一2006爆炸性环境用往复式内燃机防爆技术通则第2部分可燃性粉尘环境用 I类内燃机 术语和定义 下列术语和定义适用于本文件
3.1 爆炸性环境explosiveatmospheres 在大气条件下,以气体、蒸气、薄雾、粉尘或纤维状的可燃性物质与空气形成的混合物,点燃后,燃烧 传至全部未燃混合物的环境
3.2 潜在爆炸性环境potentiallyexplosiveatmospheres -种由于场所条件和运行条件的影响可能引起爆炸的环境
3.3 最低点燃温度mintmmumignitotemperatures 3.3.1 爆炸性环境的最低点燃温度minimumignitiontemmperatureofanesplosiveatmsphere 在规定的试验条件下,可燃性气体或可燃性液体的蒸气的最低点燃温度,或者粉尘云的最低点燃 温度
3.3.2 可燃性气体或可燃性液体的)点燃温度ignitiontemperatureofacombustiblegasorofacom- bustibleliquid 在规定的试验条件下,可燃性气体或蒸气同空气形成的混合物发生点燃时热表面的最低温度
3.3.3 粉尘云的最低点燃温度minimumignitionteperatureofadusteoud 在试验炉内空气中所含粉尘云出现点燃时炉子内壁的最低温度
3.3.4 粉尘层的最低点燃温度 minimumignitiontemperatureofadustlayer 在热表面上规定厚度的粉尘层发生点燃时热表面的最低温度
GB/T19854一2018 3.4 最高表面温度maximumsurfaeetemperatures 在最不利运行条件下但在规定的容许范围内)工作时,设备接触爆炸性环境的任何部件或任何表 面所达到的最高温度
注1,制造商需编制产品标准.并在专门设计中考虑以下条件 -在有关防爆型式标准中规定的故障条件; 在有关专业标准中规定的运行条件,包括制造商认可的过载条件 制造商规定的其他运行条件
注2:由于防爆型式的不同,表面温度可以是外表面的,也可以是内表面的
3.5 级别eategory 3.5.1 Gc级车辆trueksofEPI.Ge 用于潜在爆炸性气体环境中2区的车辆
这种车辆所具有的防爆措施(见本标准相关条款),在正常运行工况下能保持所需的防爆水平
3.5.2 Gb级车辆trucksofEPLGb 用于潜在爆炸性气体环境中1区的车辆
这种车辆所具有的防爆措施(见本标准相关条款),在正常运行工况下和即使在本身发生可预见故 障时都能保持所需的防爆水平
3.5.3 Dc级车辆trueksofEPI.De 用于潜在爆炸粉尘性环境中22区的车辆
这种车辆所具有的防爆措施(见本标准相关条款),在正常运行工况下能保持所需的防爆水平
3.5,4 Db级车辆trueksofEPLDb 用于潜在爆炸性粉尘环境中21区的车辆
这种车辆所具有的防爆措施(见本标准相关条款),在正常运行工况下和即使在本身发生可预见故 障时都能保持所需的防爆水平
注1:本标准根据GB3836.12010对分级方法进行调整并直接列出定义
下文中有关条款随之调整
两种分级 方法的对应关系参见附录B. 注2;关于设备保护级别(EPL)的资料参见附录c 3.6 自动监控 automatiemonitoring 如果元件或组件发挥其功能的能力降低,或者过程条件改变引起危险时,确保起动安全措施的备用 安全功能
3.7 正常运行条件 normaloperatingconditions 车辆在坚实、平坦、水平、经处理过的表面上使用时的运行条件
3.8 行车制动器 sericebrake 用于正常操作条件下降低车辆速度的所有内置系统或设备(例如电气的、液压的或机械的或者它们 的组合
GB/T19854一2018 3.9 故障malfunection 设备或元件不能实现预定的防爆功能
注:本标准中所指的故障可由多种原因造成,包括: -设备的一个(或多个)部件或元件的失效; 外部干扰(例如,冲击,振动、电磁场); -设计误或有缺陷例如:软件出错); 电源或其他工作干扰 操作人员的误操作(尤其是手动设备). 3.9.1 预期故障expectelmafunetionm 在正常运行中出现的设备损坏或失效
3.9.2 罕见故障raremalfunetion 已知要发生,但仅在罕见情况下才会出现的故障类型
两个独立的预期故障,单独出现时不产生点 燃危险,但共同出现时产生点燃危险,它们被视为一个罕见故障
安全要求和安全措施 4.1Gc级车辆 4.1.1热表面 最高表面温度不应超过车辆使用场所内存在的爆炸性气体的最低点燃温度
为了不超过这个表面 温度限值,车辆的设计应能保证正常使用时的安全运行,或者,配置自动监控系统,以保证自动控制车辆 停止运行
不应采用隔热措施来降低表面温度
车辆应根据第6章的要求,按其最高表面温度来设置标志 -按表1规定划分温度组别;或者 实际最高表面温度
表1最高表面温度分组 温度组别 最高表面温度/C Tl 450 T2 300 T3 200 T4 135 100 T5 85 T6 车辆通常设计的使用环境温度为一20C十40C
在这种情况下,不需要附加标志
如果车辆设计的使用环境温度超出-20C十40C的范围,则制造商需在相关文件中给出特殊 的环境温度范围,并在产品铭牌中明确标示出,而且在防爆合格证编号后面还需加注附加标志“X”
GB/T19854一2018 4.1.2机械火花和机械间隙 在正常运行时,考虑到设计容差,旋转部件和其他部件之间的间隙应至少为运动部件最大直径的 1/100
如果配合部件的加工能保证尺寸的精度和稳定性,则间隙不需要超过5mm
但无论在哪种情 况下这个间隙都不应小于1" mm
4.1.3静电 4.1.3.1电位平衡 车辆上所有大于100cn的金属部件都应连接到车架上以保持电位平衡
如果这些部件固定牢 固,并与车架有良好的金属接触,则不必用单独的导体把这些部件连接到车架上
4.1.3.2接地 为了防止静电电荷积累,车辆上所有的金属部件都应对地有良好的导电性
按5.3的要求进行测 量时,车辆上所有的金属部件对地电阻不大于10`n.则满足上述要求 对于非机动车辆来说,采用接地连接条即可
4.1.3.3皮带 车辆上所有的传动皮带的电阻应符合GB/T10715的有关要求
4.1.4动力装置 4.1.4.1往复式内燃机 往复式内燃机应符合GB20800.1一2006的相关要求
注:本标准与GB20800.12006关于车辆分级的对应关系参见附录B
4.1.4.2蓄电池组 蓄电池组应符合GB/T3836的相关要求
注:蓄电池组防爆技术资料可参考附录D. 4.1.5电气安装 电气安装应符合GB/T3836.152017的有关要求 当电源电极与车架绝缘(I系统)时,电气安装应为双极式布线,但绝缘监控装置和本安线路除外
4.1.6电气设备 4.1.6.1总则 电气设备应符合GB3836.1一2010,GB3836.2一2010、GB3836.3一2010,GB3836.4一2010、 GB3836.82014、GB3836.92014的要求
4.1.6.2气体探测 为提高安全性,防止车辆进人与自身防爆等级不适应的爆炸性危险环境中,车辆宜安装气体探 测器
GB/T19854一2018 如果安装气体探测器,应符合下列要求 车辆底部应至少安装一个气体传感探头,并且有适当保护措施以防止机械损伤 a b在下列应用情况下,车辆上部还应安装另一个气体传感探头 -可燃性气体/蒸气密度小于空气时;或者 车辆上 驾驶位置高;和/或 -车辆负载装置上有电气设备
气体探测系统应配备报警装置,在达到校准气体最低爆炸下限(LEL)10%时应报警,在达到代 表车辆气体类别的校准气体爆炸下限(LEL)25%时,车辆应实现有控制的自动停车
4.1.7离合器 4.1.7.1 液压离合器 液压离合器,变矩器、静压传动和油冷却离合器应符合4.1.1对表面温度提出的要求
4.1.7.2 机械离合器 机械离合器的设计应使其在正常运行条件下由摩擦或撞击形成的火花不会散发出来
表面温度应 符合4.1.1规定的要求
4.1.7.3摩擦离合器 摩擦离合器摩擦部件所用材料应为非金属和铸铁,或者,非金属和与铸铁具有同样摩擦特性的材 料;不应使用轻金属合金
非金属化合物包含的金属重量不应超过0%,这些金属应为颗粒或细丝(颗粒中位粒径d向<10pm. 最大粒径dm<500pm;细丝标称直径;中mm<1004m,最大直径夕<5004m) 摩擦片应铆接或粘接到离合器的摩擦片底板上
摩擦片的摩擦面上不应有小孔或接点
摩擦片的温度不应上升到制造商规定的损坏温度
4.1.8制动器 概述 4.1.8.1 制动器应符合4.1.1对表面温度提出的要求
4.1.8.2摩擦制动器 摩擦制动器摩擦部件所用材料应为非金属和铸铁,或者,非金属和与铸铁具有同样摩擦特性的材 料;不应使用轻金属合金
非金属化合物包含的金属重量不应超过40%,这些金属应为颗粒或细丝(颗粒中位粒径d动<100m 最大粒径dm.<5004m n;细丝标称直径;中mm<1004m,最大直径中m<500"m). 摩擦片应铆接或粘接到制动器的摩擦片底板上
摩擦片的摩擦面上不应有小孔或接点
摩擦片的温度不应上升到制造商规定的损坏温度
4.1.8.3停车制动器 停车制动器应使用听觉或视觉警告装置来指示其使用状态
GB/T19854一2018 4.1.9负载装卸装置 负载装卸装置接触或可能接触地面或负载的所有表面都应用铜、铜锌合金、不锈钢或类似材料,或 者用非金属材料(例如橡胶或塑料)包覆
4.1.10液压系统 4.1.10.1 热表面 液压系统应符合4.1.1对表面温度提出的要求
4.1.10.2静电放电点燃 液压系统中尤其通过过滤器的液体会出现高密度的电荷
应对液压系统的所有部件,例如过滤器 组件、箱体、管道、软管等进行评定,确定出现过高电荷水平的可能性,并应采取足够的措施防止出现过 多的电荷
至少对过滤器组件需要考虑会产生过高的电荷水平
如果过滤器组件会出现过高的电荷水平,则 需要进行静电耗散、并与车架等电位连结
当按照5.3测量时,过滤器组件与大地间的电势电阻应不超 过10Q. 4.2Gb级车辆 4.2.1热表面 热表面应符合4.1.1规定的要求
4.2.2机械火花 对于发生摩擦或碰撞的由轻金属合金制成的旋转部件或其他部件,它们的质量分数和组分应符合 GB3836.1一2010中8.1的要求;或者,这些部件采取一种措施加以保护,以防止在出现可预见故障时发 生碰撞或摩擦
对于其他材料的限制要求,在离合器(4.2.8),制动器(4.2.9)和负载装卸装置(4.2.10)的具体要求中 都有明确的规定
4.2.3机械间隙 间隙应符合4.1.2提出的要求
另外,裸露的旋转部件的防护等级至少应为IP20(见GB/T4208 2017中4.1. 4.2.4静电 静电应符合4.1.3提出的要求
车轮轮胎的表面电阻,在相对湿度为50%时不应大于10'Q,并且应按GB3836,1一2010中26.13 的要求进行测量
这些要求不适用于行进速度小于6kmm/h的车辆
车辆上使用的塑料材料还应符合下列要求
如果塑料材料不会发生静电放电点燃,则这种材料也可以用于外部部件
这可通过下列任一种措 施来实现 在相对湿度为50%时表面电阻不大于10Q,并且按GB3836.1一2010中26.13的要求进行 测定;
GB/T19854一2018 -限制能够引起静电放电的表面面积小于100cm'IA和IB)或20cm'IC);如果塑料裸露 部分用接地金属框围住,则表面面积可为上述值的4倍 在非导电材料可能放电的表面下不超过2mm(IA和IB)或0.2mm(IC)处设置导电层或 网眼宽度不大于3cnm(lA和IB)或2cm(Ic)的金属丝网; -对于内嵌金属板的塑料材料,按GB/T1408.1l的要求,测量的介电强度击穿电压不大于4kV
4.2.5动力装置 4.2.5.1往复式内燃机 往复式内燃机应符合GB20800.1一2006的相关要求
注:本标准与GB20800,12006关于车辆分级的对应关系参见附录B
4.2.5.2蓄电池组 蓄电池组应符合GB/T3836的相关要求
注蓄电池组防爆技术资料可参考附录D 4.2.6电气安装 对于Gb级车辆,电气安装应符合4.1.5提出的要求
车辆应配置绝缘监控装置,并与车架相连,以监视漏电情况;或者,定期检测带电部分与车架之间的 绝缘电阻(见附录E)
另外,如果带电部件和车架之间的绝缘电阻小于500Q,则允许车辆有控制地运 行在行驶的道路上直到停止
4.2.7电气设备 电气设备应符合GB3836.1一2010,GB3836.22010,GB3836.32010(符合GB/T3836.15一2017 规定的Gb级设备),GB3836.4一2010,GB3836.9一2014,GB/T3836.182017,GB/T3836.222017的 要求
4.2.8离合器 4.2.8.1液压离合器 液压离合器应符合4.1.7.1规定的以及包括可预见故障的要求
4.2.8.2机械离合器 机械离合器应符合4.1.7.2规定的以及包括可预见故障的要求
4.2.8.3摩擦离合器 摩擦离合器应符合下列任一条的要求 油保护 a 在整个运行过程中,离合器都应浸在润滑液中
润滑液的液位应能被观察到
表面温度应能被自动监控(直接或间接)
控制系统应能防止表面温度超过设计的温度组别 2018中表10对3类提出的要求
井且应符合GBT1853. b 隔爆外壳保护 离合器外壳部件之间隔爆接合面的最小宽度和最大间隙应符合GB3836.2一2010的有关
GB/T19854一2018 要求
离合器的外壳应能 承受按GB3836.2一2010中15.1的要求进行试验时出现的过压; 防止按GB3836.22010中15.2的要求进行试验时由外壳内部向外壳外部传爆
4.2.9制动器 4.2.9.1 概述 制动器应符合4.2.1规定的对表面温度提出的要求
摩擦制动器的设计应使火花不会造成点燃 危险
4.2.9.2摩擦制动器 摩擦制动器应符合4.1.8.2提出的要求及下列任一条的要求 油保护 a 在整个运行过程中,制动器应浸在润滑液中
润滑液的液位应能被观察到
表面温度应能被自动监控(直接或间接)
控制系统应能防止表面温度超过设计的温度组别 并且应符合GB/T16855.1一2018中表10对3类提出的要求
隔爆外壳保护 b 制动器外壳部件之间隔爆接合面的最小宽度和最大间隙应符合GB3836.22010的有关 要求
制动器的外壳应能 承受按GB3836.2一2010中15.1的要求进行试验时出现的过压; 防止按GB3836,22010中15,2的要求进行试验时由外壳内部向外壳外部传爆
附加安全措施 制动器应符合下列要求
制动器摩擦部件所用材料应为非金属和铸铁,或者,非金属和与铸铁具有同样摩擦特性的材 料;不应使用轻金属合金
非金属化合物不应含有金属成分
在制动器摩擦片严重磨损或制动器有轴向窜动的情况下,系统应能避免制动器摩擦片底板与 相关金属部件发生接触、摩擦
车辆应配置控制系统,防止制动器表面温度超过4.2.1规定的设计温度组别
控制系统应符 GB/T16855.12018中表10对3类提出的要求
如果在试验周期中(见5.2.4)证实制动 合 器的表面温度不可能达到4.2.1规定的最高表面温度,则不必配置控制系统
如果使用热敏元件,则该元件应一放置到制动器摩擦片内摩擦面下不超过3mm(在新的时 候)处
当制动器摩擦片的温度到达T一10)K时T为按5.2.4的要求测得的最高表面温度),车辆应 能自动地有控制地停止
4.2.9.3停车制动器 停车制动器应符合4.1.8.3提出的要求
车辆应配置一种控制系统,防止在没有松开停车制动器的 情况下起动车辆
GB/T19854一2018 4.2.10负载装卸装置 负载装卸装置应符合4.1.9提出的要求
4.2.11液压系统 液压系统应符合4.1.10提出的要求
4.3De级车辆 4.3.1热表面 最高表面温度不应超过车辆使用场所内出现的可燃性粉尘的最低点燃温度
车辆应根据第7章的要求,按其最高表面温度来设置标志,并且应按其实际的最高表面温度给以明 确的标示
车辆的设计,应能保证正常使用时安全运行,或者,其监控系统应能在出现危险情况之前对正在运 行的车辆进行自动监控并使之停止运行
4.3.2机械火花和机械间隙 机械火花和机械间隙应符合4.1.2提出的要求
4.3.3动力装置 4.3.3.1往复式内燃机 往复式内燃机应符合GB20800.2一2006的相关要求
注本标准与GB20800.2一2006关于车辆分级的对应关系参见附录B. 4.3.3.2 蓄电池组 蓄电池组应符合GB/T3836的相关要求
注:蓄电池组防爆技术资料可参考附录D. 4.3.4电气安装 电气安装应符合GB12476.12013和GB/T3836.15一2017有关条款对粉尘防护,温度限制和布 线系统提出的要求
4.3.5电气设备 电气设备应符合GB12176! -2013、GB12476.42010、GB12476.52013、GB12476.62010和 GB12476.72010的要求;导电性粉尘的防护等级至少应为IP6X
4.3.6离合器 4.3.6.1液压离合器 液压离合器、变矩器、静压传动和油冷却离合器应符合4.3.1对表面温度提出的要求
4.3.6.2机械离合器 机械离合器的设计应使其在正常运行条件下由摩擦或碰撞产生的机械火花不会散发出来
表面温 10
GB/T19854一2018 度应符合4.3.1规定的要求
4.3.6.3摩擦离合器 摩擦离合器的外壳应符合GB/T4208一2017规定的防尘防护等级IP5x(第1种类型外壳);旋转 接合面的粉尘防护等级可为IP4X
注:第1种类型外壳定义为在设备的正常工作周期内,由于热循环的影响,使外壳内的空气压力低于周围空气压 力的外壳
4.3.7制动器 4.3.7.1 概述 制动器应符合4.3.1对表面温度提出的要求
4.3.7.2摩擦制动器 摩擦制动器的外壳应符合GB/T42082017规定的防尘保护等级IP5X(第1种类型外壳);旋转 接合面的粉尘防护等级可为IP4X
制动器摩擦部分所用材料应符合4.1.8.2提出的要求
4.3.7.3停车制动器 停车制动器应符合4.1.8.3提出的要求
4.3.8负载装卸装置 负载装卸装置应符合4.1.9提出的要求
4.3.9液压系统 液压系统应符合4.3.1对表面温度提出的要求
4,4D级车辆 4.4.1热表面 热表面应符合4.3.1提出的要求
4.4.2机械火花和机械间隙 机械火花和机械间隙应符合4.2.2和4.2.3提出的要求
4.4.3静电点燃 静电应符合4.l.3提出的要求
车轮轮胎的表面电阻,在相对湿度为50%时不应大于10'Q,并且应按照GB3836.1一2010中26.13 的要求进行测量
这些要求不适用于行驶速度小于6km/h的车辆
车辆上使用的塑料材料应符合下列要求
如果塑料材料不会发生静电放电点燃,则这种材料也可以用于外部部件
这可通过下列任一种措 施来实现 -在相对湿度为50%时,表面电阻不大于10'Q,并且按GB3836.1一2010中26.13的要求进行 测定; 1
GB/T19854一2018 -限制能引起静电放电的表面面积小于400 cm';如果塑料裸露部分用接地金属框围住,则表面 面积可为上述值的4倍; -绝缘电阻小于10'Q(按GB1410规定的方法,用有效面积为20cm”的圆电极来测量静电通过 绝缘表面对地放电的电阻); 金属部件上外部绝缘厚度不小于8mm(金属部件上,例如测量探头或类似零件上,外部塑料 层的厚度不小于8nmm,可避免发生刷形放电
当确定使用的最小绝缘厚度时,应考虑正常使 用中预计出现的磨损); 对于内嵌金属板的塑料材料,按GB/T1408.1的要求,测量的介电强度击穿电压不大于4kV
44.4动力装置 4.4.4.1往复式内燃机 往复式内燃机应符合GB20800.2一2006的相关要求
注:本标准与GB20800.2一2006关于车辆分级的对应关系参见附录B. 4.4.4.2蓄电池组 蓄电池组应符合GB/T3836的相关要求
注蓄电池组防爆技术资料可参考附录D 4.4.5电气安装 电气安装应符合4.3.4提出的要求
4.4.6电气设备 电气设备应符合4.3.5提出的要求
4.4.7离合器 摩擦离合器的外壳应符合下列任一要求: GB/T42082017规定的尘密防护等级IP6X(第1种类型外壳);旋转接合面的粉尘防护等级 可为IP5X; 4.2.8.3中a)规定的油保护要求; 4.2.8.3中b)规定的隔爆外壳保护要求,另外,还应符合GB/T42082017规定的尘密防护等 级IP6X(第1种类型外壳;旋转接合面的粉尘防护等级可为IP5X
4.4.8摩擦制动器 摩擦制动器的外壳应符合下列任一要求 GB/T42082017规定的尘密防护等级IP6X(第1种类型外壳);旋转接合面的粉尘防护等级 可为IP5X; 4.2.9.2中a)规定的油保护要求; 4.2.9.2中b)规定的隔爆外壳保护要求,另外,还应符合GB/T4208一2017规定的尘密防护等 级IP6x(第1种类型外壳);旋转接合面的粉尘防护等级可为IP5X 4.2.9.2中e)规定的附加安全措施
12
GB/T19854一2018 4.4.9停车制动器,负载装卸装置和液压系统 停车制动器、负载装卸装置和液压系统应分别符合4.3.7.3、4.3.8、4.3.9提出的要求
安全要求和安全措施的检验 5.1总则 为了确保符合第4章的要求,应按下列要求进行试验
5.2温度测量 5.2.1概述 制动器、离合器、液压系统、电动机及内燃机的表面温度应按5.2.4规定的要求进行测量
5.2.2试验条件 下面的试验程序适用于在正常运行条件(见3.7)下运行的车辆
当运行条件与3.7规定的正常运行条件不同时,应在特殊的条件下进行试验
试验时应把热敏元件埋放在出现最高温度的表面上来测量表面温度
此外,对于附加安全制动器,应测量其摩擦片的温度
5.2.3试验程序 适用于所有车辆(但不包括牵引车辆)的试验程序 5.2.3.1 各种车辆的试验程序分别如下: a 动力驱动和动力提升的车辆: 本试验程序不包括车辆的手动操作功能 车辆应沿图1所示的试验循环路径行驶,如下所述: 试验循环从A点开始,车辆不加负载,以安全且尽可能快的速度,后退行驶到B点
1 22 未加负载的车辆应前进行驶,从静止全速加速至额定车速之后,立即用行车制动器实施制 动,直至车辆有控制地停止在C点
从全速运行、减速运行到停止的这段行驶距离,对不 同型号的车辆则各不相同,但至少不应小于6m.
未加负载的车辆应安全地从C点前进行驶到D点,接着,在正常操作条件下以尽可能快 的速度从D点行驶到A点
在上述试验条件下,负载车辆应重复进行这一试验循环
在A点装上负载,负载应为 100%的额定载荷,并能自动固定
车辆停在A点后,应用最大额定起升速度把负载提升 到最高位置,然后降低高度,离开A点
车辆的其他功能,例如: 操作台可升降(如捡选车辆);或者 门架和(或)货叉可旋转90'(如侧面或正面堆垛的车辆);或者 门架和(或)货叉可伸缩;或者 专用属具
如果是由几个发动机、电动机控制的,则这些操作也应包括在试验程序内
上述过程就是一个试验循环
13
GB/T19854一2018 提升负载 前进 加速和减迷 后退 加速和减迷 前进 图1车辆试验循环路径 b 手动驱动和手动提升的车辆 这种车辆没有必要进行这项试验
动力驱动和手动提升的车辆 这种车辆应采用a)规定的试验程序,但在A点不提升负载
在A点不提升负载,但车辆应在A点停留10s
d 手动驱动和动力提升的车辆: 这种车辆不需进行驱动运行试验,但应进行负载提升试验,以最大额定起升速度把负载提升 至最高位置,然后下降
每停留10s重复进行一次提升试验
5.2.3.2适用于牵引车辆的试验程序 牵引车辆应按照下述试验步骤,沿图2所示的试验循环路径行驶 试验循环从B点开始,牵引车辆不挂拖车,从静止全速加速至额定车速,然后立即使用行车制 a 动器刹车直到牵引车辆有控制地停止在C点
从全速运行、减速运行到停止的这段行驶距 离,因每种牵引车辆型式不同而不同,但至少不应小于6m
牵引车辆不挂拖车,安全地从C点前进到D点,然后以正常运行条件下尽可能快的速度前进 b 行驶到A点
牵引车辆不挂拖车,从A点尽可能快地安全地后退行驶到B点
d 试验循环应在牵引车辆挂上拖车,在上述条件下(但从A点到B点为前进行驶)反复进行
牵 引车辆的荷载牵引力应百分之百地符合被试牵引车辆的牵引力
牵引车辆到B点停止后,拖 车应从牵引车辆上解除掉
上述过程就是一个试验循环 14
GB/T19854一2018 前进 加迷和减速 后退 前进 加速和减速 前进 图2牵引车辆试验循环路径 5.2.4测量 在下列规定的条件下,应在每完成5个试验循环之后进行温度测量 拨5.2.3.I中)的规定,在满找车辆到达A点后抛升负载之前进行测量;或者 按5.2.3.1中e)的规定,在满载车辆到达A点后进行测量;或者 按5.2.3.1中d)的规定,在负载下降后立即测量;或者 按5.2.3.2的规定,在牵引车辆牵引拖车到达B点后进行测量
在测量温度后,车辆直接继续进行下一个试验循环 试验一旦开始不得停止,一直进行到温升稳定在2K/h及以下(记录该值)
或者.G类车辆达到 4.1.1和4.2.1,D类车辆达到4.3.1和4.4.1中规定的表面温度之前过热装置已经动作为止,在这种情况 下,还应进行辅助测量,直至任一部分的温度开始降低时为止
对于附加安全制动器,应进行评定确定制动器制动鼓表面温度和制动器摩擦片温度之间的关系
5.2.5试验结果 如果将测得的温度修正到40C环境温度时的值,对于G类车辆,不大于4.1.1或4.2.1规定的最高 表面温度;对于D类车辆,不大于4.3.1或4.4.1规定的最高表面温度,或者,试验过程中过热装置已动 作,则认为车辆试验合格
在T1、T2和T3组车辆上配置的液压系统,不必测量其表面温度
当使用附加安全制动器时,如果温度监控系统在4.2.9.2中e)规定的温度组别时使车辆停止运行. 则认为这些制动器试验合格
5.3车辆接地 应对车辆进行对地电阻测量,确保其充分接地
在地面上放置一块绝缘板,绝缘板的电阻应大于10Q
在绝缘板上放置一块钢板,绝缘板应超出 钢板边缘至少50mm
将车辆停放在在钢板上,测量车辆所有金属部件和导电金属试验板之间的电 阻
车辆和轮胎上金属部件或用于接地的接地片上的测量点,应彻底清洁,应无锈蚀油脂漆和其他 污物
如果电阻低于或等于10'Q.,则试验电压应采用直流100V;如果电阻大于10'Q,则试验电压应采 用直流500V
所有的测量都应在相对湿度低于60%的条件下进行
测得的对地电阻应不超过10'Q. 15
GB/T19854一2018 5.4出厂温度试验 车辆出厂前,制造商应对每辆车辆进行左、右制动器(如果采用蹄式制动器的话)表面温度测试
试验应在正常运行条件下进行;试验时允许调整左、右制动器制动鼓与摩擦片之间的间隙
试验用 半导体点温计或红外测温计来测量制动器的表面温度
测试结果表明左、右制动器的表面温度相差不 超过5K,则认为左、右制动器制动鼓和摩擦片之间的间隙调整合格
制造商向用户提供的资料 制造商应提供车辆使用说明手册
说明手册除阐明普通车辆相关资料外,还应具体介绍本标准所 包含的对车辆的所有维护要求及车辆使用的限制条件
此外,说明手册还应根据潜在爆炸性环境用车辆的周围环境和工作制,规定定期检查的项目及时间 间隔
车辆和附属装置的正常使用及禁止使用项目(包括与爆炸性环境有关的)如下 操作控制装置和显示装置的功能; a 车辆投人使用之前的日常检查 b 车辆起动、驾驶和停车的说明 C 装卸负载的说明; 在坡道上操作的说明; 在使用车辆和附属装置过程中对可能出现的危险的警告, 车辆设计的运行气候条件; g 对认可的蓄电池和充电器的技术要求; h 安全使用蓄电池(包括在车辆上装卸和牢固固定)的方法 对运输作业提出的特殊要求, 对使用和维修人员进行的业务培训和资格认证 诊断和探测故障的安全程序 m检查和维护的类型和时间间隔;例如: 车辆的全面维护和清洁 旋转机械装置的固定,避免与固定部件接触; 风扇皮带的使用状况和松紧程度; 电气设备的损坏和老化情况 控制系统中传感器在设定范围的动作状态; 紧固件和接合面的紧密性和牢固性; 电气连接的可靠性 更换已损坏的挠性管; 检测车辆的绝缘电阻,建议每个工作班检测一次; 检 查更换已损坏的蓄电池组电源装置(参见附录F); 轮胎、滚轮和接地片的导电电阻; 制动器摩擦片的磨损情况; 座椅和非金属罩的表面电阻; 如果属具的覆盖物的厚度小于1mm时,更换属具或覆盖物; 更换磨损和已到使用年限的部件; 用户日记资料
16
GB/T19854一2018 推荐用户使用维护记录来记录这些检查的具体情况 a 认证过的备件的使用情况; b 车辆使用和维护所必须的图纸和示意图; 车辆重新组装和附属装置安装的过程 c d 试运行完成后的功能试验; 有故障车辆修复后重新试验的程序; e 长时期停用和存放车辆的说明
标志与标牌 7.1标志 在车辆的明显部位上应设置和车辆体积大小相适合的永久性的“Ex”标志,表示车辆为防爆型的
7.2标牌 7.2.1 铭牌 车辆应设置清晰的永久性铭牌,至少应包括如下内容 a 制造商名称; 产品名称和型号; b 编号或生产日期 c 出 d)车辆空载质量,不包括可拆卸属具及蓄电池式车辆的蓄电池,但包括货叉或与之成为一体的属 具;实际值与标示值不超过士5% 额定起重量; e 在最大提升高度和载荷中心距时的实际起重量; fD 如果使用其他提升高度和载荷中心距,则此时的实际起重量; h) 在每个可拆卸属具安装在制造商规定的不同提升高度和不同载荷中心距的实际起重量, 蓄电池式车辆允许的最大和最小蓄电池质量和供电电压 防爆合格证编号; k 表示防爆的专用标志“Ex”符号; 设备的防爆型式和分类 对于爆炸性气体环境用电气设备,设备的防爆型式和分类的标注方法按B3836.12010, 对于可燃性粉尘环境用电气设备,设备的防爆型式和分类的标注方法可按GB3836.1 2010,也可按GB12476.1一2013的要求标注设备的防爆型式和使用区域
两种标注方法 的对应关系参见附录G
m温度组别或最高表面温度 按表1所示的温度组别;或者 实际最高表面温度
注1:铭牌上可标志“防爆标志”,以代表k)m)的内容
其他规定的标记
n 7.2.2使用说明牌 在车辆的明显部位上应设置使用说明牌
使用说明牌的内容见附录E 17
GB/T19854一2018 附 录 A 资料性附录) 车辆分级与场所分区的关系 对于爆炸性气体环境 A.1 爆炸性气体环境分区的定义在GB3836.14中给出
车辆分级和爆炸性气体危险场所分区之间的 对应关系见表A.1
表A.1车辆分级和爆炸性气体危险场所分区 车辆分级 爆炸性气体危险场所分区 Gb 1区 Gc 2区 A.2对于可燃性粉尘环境 可燃性粉尘环境分区的定义在GB/T12476.3中给出
车辆分级和可燃性粉尘危险场所分区之间 的对应关系见表A.2
表A.2车辆分级和可燃性粉尘危险场所分区 可燃性粉尘危险场所分区 车辆分级 区 Db 21 22区 Dc 18
GB/T19854一2018 附录B 资料性附录 本标准与相关标准关于车辆分级的对应关系 本标准与GB20800,1-2006,GB20800.22006关于车辆分级的对应关系见表B.1
表B.1本标准与GB20800.1一2006.GB20800.2一2006关于车辆分级的对应关系 标准 车辆分级 F 本标准 Ge Gb Db 3G GB20800.1l一2006 2G 3D 2D GB20800.2一2006 19
GB/T19854一2018 附 录 C 资料性附录) 用“设备保护级别”的方法对防爆设备进行危险评定的介绍 本附录阐述了用“设备保护级别”(EPL)的方法,对设备危险进行评定的概念
EPL概念的引人能 够使现有的防爆设备选型有了替代方法
C.1 历史背景 人们历来认为不是所有的防爆型式都能提供相同的等级,以确保不出现可能的点燃
GB3836.15 2000安装标准对具体的危险区域规定了具体的防爆型式,其选型依据是统计学原理,即爆炸性环境出 现的可能性或频次越大,其要求的安全程度就越高,以避免点燃源可能形成点燃危险
危险场所通常不包括煤矿)根据危险程度划分区域,危险程度的界定是根据爆炸性环境出现的或 然率
通常情况下,它既不考虑爆炸潜在的因果关系,也不考虑其他因素,如物料毒性,而真正的危险评 定是要考虑所有因素的
不同区域选择设备历来都是以防爆型式为基础,在有些情况下,防爆型式又可按其使用的区域划分 为不同的保护等级,例如,本质安全型分为“ia”和“ib”保护等级,浇封型“m”标准中包括两个保护等级 “ma”和“mb” 过去,设备选型标准在设备的防爆型式和其可使用的区域之间已经形成了固定的关系
如先前所 述,在IEC的防爆标准体系中还从未考虑过爆炸潜在的因果关系,而这一因果关系又确实存在
为了弥补这一缺失,设备操作人员又常常凭直觉来判定将危险区域扩大(或限定),典型的例子是将 “1区型”船用设备安装于海上石油平台的2区,这样,即使是在完全出现非预期的气体长时间释放的情 况下船用设备依然能防爆
另一方面,如果形成爆炸性气体的量小,而爆炸对生命和财产产生的危害可 降低.那么,对于偏远的、安全可靠的业主来说,以“2区型”电动机驱动的小型泵站甚至在1区使用.可 能是合理的
随着IEC60079-26“0区用设备的附加要求”第一版的发布,情况就变得愈加复杂
在此之前,Exia 等级的设备被视为唯一可用于0区的设备
大家已经公认,根据内在的点燃危险识别和标志所有产品是有益的,这会更易于设备选型,适用时 能更适合用这种危险评定方法
c.2总则 已经引人了设备合格的危险评定方法,代替现有的、设备与危险区域之间规定的相对固定的方法
为方便起见,引人了设备保护级别体系,无论使用何种防爆型式,已经指明了设备内在的点燃危险
规定的设备保护级别如C.2.1C.2.3. C.2.1煤矿瓦斯气体环境I类 C.2.1.1EPLMa 安装在煤矿甲烧爆炸性环境中的设备,具有“很高”的保护级别.该等级具有足够的安全性,使设备 在正常运行、出现预期故障或罕见故障,甚至在气体突然出现设备仍带电的情况下均不可能成为点 燃源
注,典型的通讯电路和气体探测器将制成符合Ma的要求,例如,Exia等级的电话电路 20
GB/T19854一2018 c.2.1.2EPLMlb 安装在煤矿甲炕爆炸性环境中的设备,具有“高”的保护级别,该等级具有足够的安全性,使设备在 正常运行中或在气体突然出现和设备断电之间的时间内出现预期故障条件下不可能成为点燃源
注:典型的I类设备将制成符合Mb的要求,例如,Exd型电动机和开关
C.2.2气体I类) C.2.2.1EPLGa 爆炸性气体环境用设备,具有“很高”的保护级别,在正常运行、出现预期故障或罕见故障时不是点 燃源
c.2.2.2EPLGb 爆炸性气体环境用设备,具有“高”的保护级别,在正常运行或预期故障条件下不是点燃源
注:大多数标准的保护概念提出设备在这一保护级别 c.2.2.3EPL.Ge 爆炸性气体环境用设备,具有“一般”的保护级别,在正常运行中不是点燃源,也可采取一些附加保 护措施,保证在点燃源预期经常出现的情况下(例如灯具的故障)不会形成有效点燃
注,Exn型将是该保护级别的典型设备 C.2.3粉尘皿类) C.2.3.1EPLDn 爆炸性粉尘环境用设备,具有“很高”的保护级别,在正常运行、预期故障或罕见故障条件下不是点 燃源
C.2.3.2EPLDb 爆炸性粉尘环境用设备,具有“高”的保护级别,在正常运行中出现预期故障条件下不是点燃源
C.2.3.3EPLDe 爆炸性粉尘环境用设备,具有“一般”的保护级别,在正常运行过程中不是点燃源,也可采取一些附 加保护措施,保证在点燃源预期经常出现的情况下(例如灯具的故障)不会形成有效点燃
对于大多数情况,由于特有的潜在爆炸因果关系,预定下列情况适用于危险区域使用的设备(对煤 矿瓦斯环境不直接适用,因为区的概念通常不适用于煤矿)
见表C.1
表c.1EPL与区的传统对应关系(没有附加危险评定 区 设备保护级别 Ga Gb Ge Da" 20 Db 2l Dc 22
GB/T19854一2018 C3提供的防点燃危险 根据制造商为保护级别设立的运行参数,不同的设备保护级别必须能够起作用,见表C.2
表c.2提供的防点燃危险描述 设备保护级别 提供的保护 保护特性 运行条件 类别 Ma 当出现两个独立故障时,两个独立 很高 当出现爆炸性环境时设备依然运行 的保护或安全措施 I类 G8 当出现两个独立故障时,两个独立当用于0区、1区和2区时设备依然 很高 的保护或安全措施 运行 I类 Dn 当出现两个独立故障时,两个独立当用于20区.21区和22区时设备依 很高 的保护或安全措施 然运行 W类 Mb 高 适合正常操作和运行条件 当出现爆炸性环境时设备断电 !类 Gb 适合正常运行和经常出现干扰或 当用于1区和2区时设备依然运行 高 正常考虑故障的设备 类 适合正常运行和经常出现干扰或 Db 当用于21区和22区时设备依然运行 高 正常考虑故障的设备 Ge -般 适合正常运行 当用于2区时设备能防爆 I类 De -般 适合正常运行 当用于22区时设备依然运行 川类 C.4执行 -2017(包含可燃性粉尘环境原来的要求)引人了EPL概念,在设备选型中可使用 GB/T3836.15一 “危险评定”法代替传统方法,涉及到的危险场所分类标准中同样也要引人EPL的概念
对于爆炸性气体环境用防爆型式EP!要求附加标志,对于爆炸性粉尘环境,现有的在设备上标志 区域的方法由EPL代替
22
GB/T19854一2018 附 录 D 资料性附录 蓄电池组电源装置防爆技术资料 D.1范围 本附录提供了爆炸性环境用工业车辆的蓄电池组电源装置的相关防爆技术资料
本附录适用于爆炸性环境用工业车辆的蓄电池组电源装置(以下简称电源装置)防爆结构的设计、 制造和检验
按本附录制造的电源装置适用于爆炸性气体场所1区和可燃性粉尘场所21区
D.2术语和定义 D.2.1电源装置 按照本附录制造的特殊型铅酸蓄电池、蓄电池箱、接线盒(或插接装置)和连接导线组装在一起的电 源装置
D.2.2蓄电池箱 按照本附录制造的专供组装特殊型铅酸蓄电池的箱子,由箱体和箱盖组成
D.2.3特殊型铅酸蓄电池 按照本附录制造的专供组装电源装置的铅酸蓄电池
D.2.4特殊排气栓 按照本附录制造的专供特殊型铅酸蓄电池使用的排气栓
D.2.5连接导线 按照本附录制造的专供电源装置内特殊型铅酸蓄电池极柱连接使用的导线
D.3安全技术和安全措施 D.3.1特殊型铅酸蓄电池 D.3.1.1特殊型铅酸蓄电池(以下简称蓄电池)采用内部氢气不易积聚、在正常使用条件下电解液不能 溅出的结构,如装设特殊排气栓: 特殊排气栓具有良好的排气性能:在D.4.9的试验条件下,特殊排气栓的内部压力不大于 0.05kPa(干燥状态下)和0.15kPa(湿润状态下)
b 特殊排气栓具有可靠的隔爆性能;在D.4.10的试验条件下,特殊排气栓不传爆和损坏 D3.1.2蓄电池槽用耐电解液作用的、机械强度和绝缘性能好的塑料制成,能承受冲击能量不小于 7.5」的冲击试验和试验电压为10kV50Hz)的渗漏试验
D.3.1.3蓄电池盖制成液体和粉尘不易积聚的结构
蓄电池盖上极柱的绝缘凸台高度不小于10n mm 23
GB/T19854一2018 D.3.1.4蓄电池制成双极柱,即两个正极柱和两个负极柱,并且每个极柱能单独承受规定的回路电流
D3.1.5蓄电池的封口严密可靠,能承受D.4.5的气密性试验
D.3.1.6蓄电池的正极板采用耐酸绝缘材料的封底和上护套
如果采用铅封底,则加套由耐酸绝缘材 料制成的护套
D.3.1.7蓄电池的氢气析出量不大于0.5mL/Ahh). D.3.2蓄电池箱 D.3.2.1蓄电池箱的箱体和箱盖具有足够的机械强度
箱盖能承受冲击能量不小于75.0」的冲击 试验
金属结构的箱体和箱盖的内表面,均采用耐酸绝缘材料予以覆盖
覆盖层牢固可靠,在电源装置规 定的使用年限内不脱落、损坏
蓄电池箱制成氢气不易积聚的结构
蓄电池箱开设通风孔,通风孔的总面积宜按比率 D.3.2.2 40cm:'/(w
h)计算
箱盖在装配状态时与水平方向有约于的夹角
箱底制成利于电源装置内部垂 直方向上自然通风的结构
D.3.2.3蓄电池箱的底部可开设排液孔,并有防止电解液腐蚀箱底外表面的措施
蓄电池箱的防护等级符合GBy/T4208一2017中规定的IP23. D.3.2.4 蓄电池箱的箱体和箱盖设置用专用工具才能打开的锁紧机构
D.3.2.5 D.3.3接线盒或插接装置 D.3.3.1电源装置设置接线盒或插接装置 接线盒可以按GB3836.22010的规定制成隔爆型,也可以按GB3836.3一2010的规定制成 a 增安型;或者,按照GB12476.5一2013的规定制成外壳保护型 插接装置按GB3836.2一2010的规定制成隔爆型;或者,按照GB12476.52013的规定制成 b 外壳保护型
接线盒或插接装置的外壳防护等级 对于气体防爆型,至少为IP54; 对于粉尘防爆型,至少为IP65
D.3.3.2接线盒(或插接装置)牢固地固定在蓄电池箱上
从蓄电池箱内引出到接线盒(或插接装置 的导线有可靠的防止被损坏的保护措施
D.3.4连接导线 D.3.4.1连接导线所用电缆是阻燃的耐酸绝缘铜芯软电缆
电缆芯线与铅鳞合金接头采用铸接方法 连接,连接处进行压合处理和密封处理
D.3.4.2连接导线一端电缆芯线与铅锄合金接头之间的电阻,按D4.8的方法测定时,不应大于124Q 20"C D.3.5结构 电源装置中蓄电池的安装牢固可靠
蓄电池之间以及蓄电池与蓄电池箱之间采用耐酸绝缘材料制 成的隔离物隔开,并牢固塞紧
隔离物制成利于自然通风和箱底排液的结构
D3.6爬电距离 电源装置中相邻蓄电池之间的最大漏电电压,一般不超过24V,极柱之间的爬电距离不小于 35mm
如果最大放电电压超过24V,则每超过2V,爬电距离增加1mm 24
GB/T19854一2018 D.3.7双线连接 电源装置中蓄电池之间的电气连接和电源引出(至接线盒)均采用连接导线进行双线连接,并且每 根连接导线能单独承受规定的回路电流
D.3.8焊接 连接导线(或连接条)与蓄电池极柱的连接牢固可靠,例如,采用焊接的方法进行连接
连接后,连 接导线(或连接条)的铅锄合金接头与蓄电池极柱的上平面中心之间的连接电阻,按D.4.4的方法测定 时.,不大于20Q(20C) 连接后裸露带电部分加盖绝缘护罩
加盖绝缘护罩后,外壳防护等级 -对于气体防爆型,至少为IP54 对于粉尘防爆型,至少为IP65,而且,绝缘护罩至少将连接电缆的绝缘层包裹5mm
D.3.9氢气积聚浓度 在电源装置内部(除蓄电池外)任何地方,氢气积聚的浓度不超过0.3%体积比)
D.3.10电源装置绝缘性能 电源装置具有良好的绝缘性能
电源装置中蓄电池组对蓄电池箱体的绝缘电阻不小于 额定电压为60V及以下时,10kQ; aa b)额定电压为60V~100V时,15kQ D.3.11耐振动性能 电源装置具有良好的耐振动性能
D.4安全技术和安全措施的检验 D.4.1冲击试验 D.4.1.1概述 蓄电池槽和蓄电池箱盖进行冲击试验
冲击试验以试验重锤自由落下沿法线方向冲击被试样品的 方法进行
试验重锤由锤体和锤头组成
锤头的端部为直径25mm的半球形,材料为淬火钢
D.4.1.2蓄电池槽的冲击试验 D.4.1.2.1冲击试验在下列条件下进行 试验重锤的质量为1.0kg,冲击能量为7.5J,坠落高度由质量和冲击能量导出
冲击点在蓄电 a 池槽大侧面中心 试验分高温试验和低温试验
高温试验时,被试样品的试验温度高于蓄电池工作温度10C b 但至少为50;低温试验时,被试样品的试验温度为-20-28C
试验时分别将2个被试样品放人温度高于规定的试验温度10C的高温控制箱中,将2个被试 样品放人温度低于规定的试验温度5C的低温控制箱中,待温度稳定后,从控制箱中取出被试 样品放在平坦的水泥地面上或非弹性的试验台上,当被试样品的温度达到试验温度时,便即进 25
GB/T19854一2018 行冲击试验
D.4.1.2.2每个被试样品冲击1次,共试4个高温试验2个,低温试验2个)
试验结果以被试样品均 不发生破裂、损坏为合格
D.4.1.3蓄电池箱盖的冲击试验 冲击试验在下列条件下进行 D.4.1.3.1 试验重锤的质量为7.5kg,冲击能量为75.0J,坠落高度由质量和冲击能量导出
冲击点在箱 a 盖的结构薄弱处
b 试验时箱盖安装在蓄电池箱的箱体上
D.4.1.3.2试验时对箱盖冲击5处,每处冲击1次
试验结果以耐酸绝缘复盖层不发生破裂、损坏和箱 盖不出现影响使用的变形为合格
D.4.2氢气浓度试验 D.4.2.1概述 蓄电池进行氢气析出量试验;电源装置进行氢气积累浓度试验
D.4.2.2氢气析出量试验 D.4.2.2.1蓄电池氢气析出量试验在下列条件下进行: 放电前的电解液密度符合GB/T7403.1的规定
a b 充电结束静置1h~2h后开始放电,放电电流为1.25倍5小时率电流值的电流
放电过程中 电解液温度为37C一40C 放电持续时间同蓄电池端电压无关,放电3h停止 D.4.2.2.2试验时收集到的气体按式(D.1)求出氢气析出量,并折算到标准状态(30C、101kPa)时 的值: 303 V
H
H= D.1 3C 273十 101 式中 氢气析出量,单位为毫升(mL); -收集的气体总量,单位为毫升(mL); H -用气体分析仪或其他方法求得的气体总量中氢气所占的体积分数,以%表示; C 5小时率容量,单位为安培小时(Ah); 被测气体的温度,单位为摄氏度(C): 试验时的大气压力,单位为千帕(kPa). 1 D.4.2.2.3每个蓄电池试验2次,共试验2个
试验结果以按式(D.1)计算所得值均不超过本附录D.3.1.7 值为合格
D.4.2.3氢气积累浓度试验 D.4.2.3.1电源装置内部氢气积累浓度试验在下列条件下进行 电源装置放置在密闭的试验室内,且室内不得使用能引起空气流动的装置
试验室的容积为 a 电源装置体积的525倍
26
GB/T19854一2018 b)电源装置按正常工作状态装配完整,并充电至额定容量
c 充电结束静置1h一2h后开始放电,电流放电为1.25倍5小时率电流值的电流
每30min 测量一次电源装置内的氢气浓度,测点不少于5处
D.4.2.3.2被试样品1台,试验进行3h
试验结果以所测得的氢气浓度均不超过D.3.9的值为合格
D.4.3电源装置绝缘电阻测定 D.4.3.1电源装置绝缘电阻测定在下列条件下进行 a 电源装置按正常工作状态装配完整,并充电至额定容量
试验在电源装置充电结束后1h内进行(可用清水清洗,并允许揩干积液):用电压表测量蓄电 b 池组的总电压、正极对蓄电池箱箱体(地)的电压和负极对蓄电池箱箱体(地)的电压
测量用电压表的精度为0.5级例如C31-V型电压表),测量用量限的总内阻为25kQ 30kn. D.4.3.2绝缘电阻按式(D.2)从测得的电压值中计算求得 D.2 R;=Rl(C 式中 绝缘电阻,单位为千欧(kQ); R R 电压表测量用量限的总内阻,单位为千欧(kQ) 蓄电池组的总电压,单位为伏特(V); U -蓄电池组正极对蓄电池箱箱体(地)的电压,单位为伏特(V); U -蓄电池组负极对蓄电池箱箱体(地)的电压,单位为伏特(V)
D.4.3.3被试样品1台,试验1次
试验结果以按式(D.2)计算所得值不低于D.3.10的值为合格
D.4.4连接电阻测定 D.4.4.1电源装置中各个蓄电池极柱与连接导线(或连接条)的连接处进行连接电阻测定
连接电阻 测定在下列条件下进行 电源装置按正常工作状态装配完整
a b)用TZ型接触电阻检测仪及其配用的电压端一电流端间距为8mm的测笔进行测量
测笔分 别触及连接导线(或连接条)的铅锄合金接头和蓄电池极柱的上平面中心点,例如图D.1中的 A,B,C,D四点,其中,A,B为电压端,C,D为电流端 D.4.4.2连接电阻的测定结果按式(D.3)换算到20C时的值: 1.03Rm D.3 R120= 1十a(t一20 式中: 换算到20C时的连接电阻,单位为微欧(4Q); RH20 R 连接电阻的测量值,单位为微欧(4Q); 电阻温度系数,取0.00393,单位为每摄氏度(1/C); 测量时的环境温度,单位为摄氏度(C). D.4.4.3每台电源装置均进行连接电阻测定
测定结果以按式(D.3)计算所得值均不超过D.3.8的值 为合格
27
GB/T19854一2018 图D.1连接电阻测定 D.4.5气密性试验 D.4.5.1蓄电池气密性试验在下列条件下进行 蓄电池装配完整; aa D)在未灌装电解液的蓄电池内压人或抽出空气,使蓄电池内部气压和大气压相差20kPa
D.4.5.2每只蓄电池均需经过试验
试验结果以压力计读数在3s一5s时间内不发生变化为合格
D.4.6渗漏试验 D.4.6.1蓄电池槽的渗漏试验在下列条件下进行 a 将蓄电池槽放置在水池中,在蓄电池槽内外注人清水,水面距蓄电池槽边沿的距离不大于 15mm. b 将试验用的电极分别插人蓄电池槽内外的水中,然后在电极间施加10kV工频交流电压
D.4.6.2每个蓄电池槽均经过试验
试验结果以电压表读数在3s5s时间内稳定不变为合格
D.4.7蓄电池箱绝缘电阻测定 D.4.7.1蓄电池箱的绝缘电阻测定在下列条件下进行 a)将蓄电池箱内注满清水,水面距箱体上边沿的距离不大于15mm. b) 用500V级兆欧表进行测量,表笔一端插人水中,一端接在箱体的金属上 D.4.7.2每个蓄电池箱均经过试验
试验结果以所测得的绝缘电阻不小于5Mn为合格
D.4.8连接导线铸接电阻测定 D.4.8.1连接导线的铸接电阻测定在下列条件下进行 用TZ型接触电阻检测仪及其配用的电压端一电流端间距为8mm的测笔测量连接导线的总 a 电阻
b)当制造商按图D.2规定的结构制造连接导线时,测量点在能测得最小电阻的位置上
D.4.8.2连接导线一端芯线与铅锄合金接头之间的铸接电阻按式(D.4)计算求得 Lo” (D.4 Rc=(R2 ×10" 式中 R 铸接电阻,单位为微欧(Q); 28
GB/T19854一2018 R -测得的连接导线总电阻,单位为微欧(4Q); 连接导线的电缆计算长度,L0=L名一0.02,单位为米(m) Lo 连接导线中心距,单位为米m); Lz 连接导线的电缆芯线截面积,单位为平方毫米(mm='); mm?/m
-铜的电阻系数,取0.0169,单位为欧姆平方毫米每米(Q 20 说明 -铅锄合金接头 -连接导线
图D.2铸接电阻测定 D.4.8.3铸接电阻按式(D.5)换算到20C时的值: Re (D.5 Re l十a(t一20) 式中 换算到20C时的铸接电阻,单位为微欧(4n) Re
c0 Re -铸接电阻的测定值,单位为微欧(4Q); -电阻温度,取0.00393,单位为每摄氏度(1/C); -测量时的环境温度,单位为摄氏度(C). D.4.8.4每根连接导线均进行测定
测定结果以按式(D.5)计算所得的值均不超过D.3.4.2的值为 合格
D.4.9特殊排气栓透气性能试验 D.4.9.1特殊排气栓的透气性能试验在下列条件下进行 试验分别在排气栓处于干态和湿态情况下进行
a 在湿态试验时.将排气栓浸人密度为1.210g/em=1.220g/em的电解液中2min,取出后在 室温条件下放置10min
试验时按图D3所示系统对排气栓供气 气体流量按式(D.6)计算 A=1.2C (D.6 式中: A -气体流量,单位为毫升每分(mL/min); 1.2 系数,单位为毫升每分安时[mL/
Ah]; min 29
GB/T19854一2018 -蓄电池的额定容量(5小时率),单位为安培小时(Ah). D.4.9.2被试样品10个(干态试验5个,湿态试验5个),每个试验1次
试验结果以特殊排气栓内部 压力均不超过D.3.1.1.1的值为合格
D.4.10特殊排气栓隔爆性能试验 D.,4.10.1特殊排气栓的隔爆性能试验在下列条件下进行 a 特殊排气栓装在一个容积不小于1L的球形试验外壳上,将外壳置于爆炸试验罐内
b 在外壳内和试验罐内均充以(28士1)%体积分数)的氢一空气混合物
以放电火花点燃外壳 内的混合物
点燃位置在试验外壳的中心 D.4.10.2被试样品2个,每个试验10次
试验结果以特殊排气栓均不发生传爆和损坏为合格
说明 -U形压力计; -特殊排气栓; 橡皮塞; 流量计 -阀 气源
图D.3透气性试验 D.4.11电源装置温度测定 D.4.11.1概述 电源装置中蓄电池与蓄电池之间的连接导线和各个极柱的温度测定在被测点无粉尘覆盖和有粉尘 覆盖两种情况下进行
无粉尘覆盖时测得的温度标记为TAA型电气设备),有粉尘覆盖时测得的温 度标记为Tn(B型电气设备)
两种试验允许同时进行
D4.11.2试验条件 连接导线和各个极柱在下列条件下进行温度测定 电源装置放置在密闭的试验室内,且室内不得使用能引起空气流动的装置
试验室的容积为 a 电源装置体积的5倍25倍
b 电源装置按正常工作状态装配完整,并充电至额定容量
30
GB/T19854一2018 在电源装置中选择6处(一根连接导线和所连接的两个极柱为1处)覆以厚度为12.5mm 的 粉尘糊剂,模拟粉尘形成的状态
6处分别位于中间位置(2处)和周边
注粉尘糊剂由45%的粉尘(例如小麦粉)和55%的水(均按重量计)调制而成
d)充电结束静置1h~2h后开始放电,放电电流为1.25倍5小时率电流值的电流
待温度稳 定,且粉尘糊剂干燥后测量电源装置内的各连接导线和各极柱的温度
无粉尘覆盖时温度的测定按照a),b),d)进行
D.4.11.3 合格判据 试验结果以所测得的最高温度换算到规定最高环境温度时的值不超过车辆温度组别的温度值或可 燃性粉尘的最小点燃温度为合格
D.5标志和标牌 D.5.1标志 D.5.1.1电源装置上设置清晰的永久性标志“Ex”、铭牌和警告牌
蓄电池上至少标出;制造商名称、标志“Ex”、型号、出厂日期 D.5.1.2 D.5.2标牌 D.5.2.1 铭牌 铭牌包括下列内容制造商名称、产品名称、产品型号规格、防爆标志、防爆合格证编号、其他需要标 出的特殊要求和出厂日期
注:防爆标志见GB3836,1一2010或GB12476,1一2013
按本附录制造的蓄电池组电源装置定义为防爆特殊型蓄 电池电源装置
防爆标志举例;当电源装置通往外部的电缆引线是通过增安型接线盒引出,且电源装置的温 度不超过135时,防爆标志为ExselT4Gb
D.5.2.2警告牌 警告牌标出“危险场所,严禁打开!”字样
注:铭牌和警告牌见GB3836.l一2010
D.6试验报告 制造商在电源装置试制完成后,向检验机构送审下列试验报告 按GB/T7403.1规定的试验项目和试验方法提出的试验报告; 氢气析出量试验报告; 气密性试验报告; 蓄电池槽渗漏试验报告; 特殊排气栓透气性能试验报告; 蓄电池槽和蓄电池箱箱盖冲击试验报告; 蓄电池箱绝缘电阻检测报告; 连接电阻检测报告; 连接导线铸接电阻检测报告; 电源装置防护检测报告
31
GB/T19854一2018 附 录 E 规范性附录) 使用说明牌 使用说明牌应包括下列内容 非本职人员不得在爆炸危险场所驱车作业 a b) 车辆在爆炸危险场所中运行作业时严禁碰撞、冲击; 车辆在爆炸危险场所中运行作业时发生失控,应立即切断动力源 c 蓄电池组的充电应在安全场所进行
充电后,应用清水冲洗干净,应逐个检查连接导线的连接 d 状态; 蓄电池组(内燃机)在爆炸危险场所不得作为他用电源(动力源) e 严禁在爆炸危险场所中打开电气装置的盖子; fD 严禁在爆炸危险场所中进行维修作业 8 h 应定期检查带电部件与车体之间的绝缘情况,测得的绝缘电阻不得小于0.5MQ 其他应指出的内容
32
GB/T19854一2018 附录 F 资料性附录 蓄电池组电源装置的报废和更换 F.1范围 本附录提供了爆炸性环境用工业车辆的蓄电池组电源装置的报废和更换的相关资料
本附录适用于爆炸性环境用工业车辆的蓄电池组电源装置(以下简称电源装置)在运行过程中评判 报废及进行更换
F.2报废标准 F.2.1电源装置的报废 电源装置在车辆上运行期间凡出现下列情况之一者,即行报废: 参照D.4.3的测试方法求得电源装置的绝缘电阻小于式(F.1)计算值者 a R=0.025U (F.1 式中 电源装置的绝缘电阻,单位为千欧(kQ); U -以伏为单位表示的电源装置额定电压数值
b 参照D.4.4的测试方法(但测笔分别触及在被测极柱的上平面中心)测得两极柱上平面中心之 间的电阻大于式(F.2)计算值者 L, R=65十 -×10° (F.2 式中: -两极柱上平面中心之间的电阻,单位为微欧(4Q); L
连接导线的电缆计算长度,L2=Lo-0.02,单位为米(n m; L2 连接导线中心距,单位为米(m); S 连接导线的电缆芯线面积,单位为平方毫米(mm'); -铜的电阻系数,取0.0169,单位为欧姆平方毫米每米Q”mm'/m). 参照GB/T7403.1中规定的循环耐久试验测试方法测得电源装置中蓄电池容量小于 0.8C,时
F.2.2蓄电池箱的报废 在已报废的电源装置中,蓄电池箱凡出现下列情况之一者即行报废: 按照D.4.7的测试方法测量蓄电池箱的绝缘电阻小于5MQ者; b)蓄电池箱发生严重变形,影响重新组装蓄电池者
F.2.3报废的判断 电源装置和蓄电池箱报废与否,原则上由使用单位判断,如有困难时,则可会同制造商一起工作 33
GB/T19854一2018 F.3 更换程序 F,3.1电源装置的更换 F.3.1.1按照F.2.1,电源装置已经报废,及时进行更换
F.3.1.2更换工作由电源装置使用单位负责
使用单位使用和报废电源装置同型号的电源装置或根据 F.3.2修复的电源装置进行更换
更换工作在主管工程师指导下进行
如使用单位更换有困难时,则可 会同制造商一起进行
F.3.2蓄电池组的更换 F.3.2.1按照F.2.1,电源装置中蓄电池组已寿命终止,但蓄电池箱不符合F.2.2,仍可继续使用时,允许 更换蓄电池组
更换工作由电源装置使用单位提出,电源装置制造商负责
制造商使用和已报废蓄电池同制 F.3.2.2 造商生产的同种蓄电池组进行更换;重新组装起来的电源装置,除符合该产品技术条件,图样的相应要 求外,还要按照D,.4.3和D.4.4进行试验检查
F.4安全责任 按照本附录进行工作时,使用单位对电源装置更换后车辆安装部分的防爆安全性能负责,电源装置 制造商对蓄电池组更换后的电源装置的防爆安全性能负责 34
GB/T19854一2018 附 录 G 资料性附录 GB3836.1一2010与GB12476.1一2013关于爆炸性粉尘环境用电气设备 防爆型式标注方法的对应关系 表G.1列出了GB3836.12010与GB12476.1一2013关于爆炸性粉尘环境用电气设备防爆型式 标注方法的对应关系
表G.1GB3836.1一2010与GB12476.12013关于爆炸性粉尘环境用电气设备 防爆型式标注方法的对应关系 危险区域 可燃性粉尘类型 GB3836.12010 GB12476.1一2013 tDA20IP6X、tD2o t重ADa或ta重A 可燃性飞絮 iaD20 aADa或ia皿A ma川Da或ma川 maD20 t川BDa或taIB tDA20lP6X、tD20 非导电性粉尘 i远匪BDa或iaB 20区 iaD20 maD2o na 川Da或ma m tDA20IP6X、tD20 CDa或taIC 导电性粉尘 iaICDa或iaIC iaD20 l川Da或maI nmaD20 ma tDA21lP6X,tD21 tADb或tbA bmADb或bA ibD21 可燃性飞絮 nmbD21 mb ,助或mb"m pD21 pDb或b tDA21IP6x、tD21 BDb或tbB ibD21 bBDb或ibIB 21区 非导电性粉尘 mb川b或mbI mbD21 p川Db或pbl业 pD21 cDb或tbc tDA21IP6X,tD21 ibICDb或ibIC ibD21 导电性粉尘 mbDb或mbI mbD21 pD21 pDb或b t川ADe或tc川A tDA22lIP5X,tD22 ic IAD或ieA 可燃性飞絮 nmeD或nmeI p皿De或pc业 p22 t川BD或teI tDA22IP5X,tD22 ieBDe或ieB 22区 非导电性粉尘 m D或mc川 mc I D或eI p pD22 tICDe或tellC tDA22IP6X ieIcD或iec 导电性粉尘 mc De或me pD或p pD22 注符合1区危险环境要求的设备可适用手22区危险环境,符合20区危险环境要求的设备可适用手于1区、 22区危险环境
注2:标志皿B的设备可适用于A类设备的使用条件,标志lC的设备可适用于WA或B类设备的使用条件 35
GB/T19854一2018 考文献 参 [[1]GB3836.14爆炸性环境第14部分;场所分类爆炸性气体环境 [2]GB/T7403.1牵引用铅酸蓄电池第1部分;技术条件 [3]GB/T12476.3可燃性粉尘环境电气设备第3部分:存在或可能存在可燃性粉尘的场所 分类 36
爆炸性环境用工业车辆防爆技术通则GB/T19854-2018
在许多工业领域中,如石油、化工、冶金等行业,都存在着爆炸性环境的工作场所。在这些环境下,一旦发生爆炸事故,不仅会给人员带来伤害,还会造成财产损失。
因此,对于在爆炸性环境中使用的工业车辆,必须采取防爆措施以确保其安全运行。《爆炸性环境用工业车辆防爆技术通则GB/T19854-2018》就是为此而制定的标准。
该标准规定了爆炸性环境用工业车辆的分类、防爆要求和试验方法等内容。根据不同的爆炸性环境等级,标准对车辆的防爆措施和防护等级都做出了具体的要求。
此外,标准还规定了工业车辆在进入爆炸性环境前需要进行的检测和评估程序。通过对车辆进行全面的安全检查和评估,可以有效地减少因车辆本身存在隐患而导致的爆炸风险。
与此同时,《爆炸性环境用工业车辆防爆技术通则GB/T19854-2018》还要求车辆制造商必须提供完整的使用说明书和防爆证明文件。这些文件包括车辆的基本信息、安全使用规范以及防爆试验报告等内容。
总之,参照GB/T19854-2018标准,对于在爆炸性环境中使用的工业车辆,必须采取科学的防爆措施以确保人员和财产的安全。作为制造商和用户,我们都应该高度重视这一问题并积极采取防范措施。