GB/T16508.3-2013
锅壳锅炉第3部分:设计与强度计算
Shelllboilers―Part3:Designandstrengthcalculation
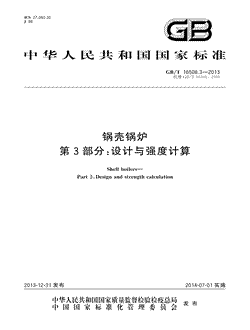
- 中国标准分类号(CCS)J98
- 国际标准分类号(ICS)27.060.30
- 实施日期2014-07-01
- 文件格式PDF
- 文本页数75页
- 文件大小3.96M
以图片形式预览锅壳锅炉第3部分:设计与强度计算
锅壳锅炉第3部分:设计与强度计算
国家标准 GB/T16508.3一2013 代替GB/T16508一1996 锅壳锅炉 第3部分:设计与强度计算 Shelboilers一 Part3:Designandstrengthealeulation 2013-12-31发布 2014-07-01实施 国家质量监督检验检疫总局 发布 国家标准化管理委员会国家标准
GB/T16508.3一2013 目 次 前言 范围 规范性引用文件 术语和定义 符号和单位 设计基本要求 承受内压力的圆筒形元件 承受外压力的圆筒形炉胆冲天管烟管和其他元件 6 2 凸形封头、炉胆顶、半球形炉胆和凸形管板 有拉撑(支撑,加固)的平板和管板 32 拉撑件和加固件 l0 11平端盖及盖板 46 下脚圈 12 13孔和孔的补强 50 媒制三通 l4 59 15决定元件最高允许工作压力的验证法 6 附录A(资料性附录)铸铁锅炉受压元件设计计算 66 附录B(资料性附录矩形集箱设计计算 68 附录c资料性附录)水管管板设计计算 72
GB/T16508.3一2013 前 言 GB/T16508《锅壳锅炉》分为以下8个部分 -第1部分:总则; 第2部分;材料; 第3部分:设计与强度计算; 第4部分;制造,检验和验收; 第5部分;安全附件和仪表; 第6部分;燃烧系统 第7部分;安装 第8部分运行
本部分为GB/T16508的第3部分 本部分按照GB/T1.1一2009给出的规则起草
本部分代替GB/T1608一1996K锅壳解炉受压元件强度计算》,在符合国家安全监察法规要求的 基础上,为锅炉产品的结构设计、强度计算提出了设计计算规则
本部分与GB/T165081996相比主要变化如下 本部分不限定额定燕汽压力范围,原标准范围规定额定燕汽压力范围不大于2.5MPa 增加了设计基本要求,并提出了设计技术指标要求; 删除了GB/T16508一1996中“材料”章节; 增加了“H型下角圈”; 允许在一定的条件下,对两个相邻大孔进行加强; 增加了“决定元件最高允许工作压力的验证法”章节; 增加了“水管管板”计算
本部分对应于EN12953《锅壳锅炉)的第3部分,主要差异如下 本部分包括了设计计算的一般要求、锅炉性能要求及能效要求; 本部分补强方法采用面积补强法;欧盟标准采用压力补强法
本部分由全国锅炉 压 ]容器标准化技术委员会(s.Ac/TC262)提出并归口
本部分起草单位:上海工业锅炉研究所、上海发电设备成套设计研究院、江苏双良锅炉有限公司,泰 山集团股份有限公司、张家港海陆重工有限公司、江苏太湖锅炉股份有限公司、无锡太湖锅炉有限公司、 张家港市江南锅炉压力容器有限公司、上海市特种设备监督检验技术研究院
本部分主要起草人;吴国妹、李春,施鸿飞、吴艳、雷钦祥、周冬雷,潘瑞林、顾利平,薛建光、吴钢、 张宏,高宏伟、蔡昊、王海荣、喻孟全 本部分所代替标准的历次版本发布情况为 -GB/T16508一1996
m
GB/T16508.3一2013 锅壳锅炉 第3部分;设计与强度计算 范围 GB/T16508的本部分规定了锅壳锅炉基本受压元件的设计和结构要求,并给出了铸铁锅炉附录 A),矩形集箱《附录B)和水管管板(附录c)的基本设计要求
本部分适用于承受内压圆筒形元件、承受外压圆筒形元件、封头、管板、拉撑件、下脚圈,以及开孔和 补强的设计计算
规范性引用文件 下列文件对于本文件的应用是必不可少的
凡是注日期的引用文件,仅注日期的版本适用于本文 件
凡是不注日期的引用文件,其最新版本(包括所有的修改单)适用于本文件 GB/T1576工业锅炉水质 GB/T2900.48电工名词术语锅炉 气瓶疲劳试验方法 GB/T9252 GB/T12145火力发电机组及燕汽动力设备水汽质量 GB13271锅炉大气污染物排放标准 GB/T16508.1一2013锅壳锅炉第1部分;总则 GB/T16508.2锅壳锅炉第2部分;材料 GB/T16508.4锅壳锅炉第4部分;制造、检验和验收 NB/T47013(JB/T4730)承压设备无损检测 TsGG0001锅炉安全技术监察规程 TsG;G0002锅炉节能技术监察管理规程 术语和定义 GB/T16508.1和GB/T2900.48界定的术语和定义适用于本文件
符号和单位 本部分中各章节通用的符号含义和单位如下: E 计算温度时材料的弹性模量,MPa 计算压力,MPa 校核计算最高允许工作压力,MPa; [] 锅炉额定压力,MPa; 声 工作压力,MPa; p -对应于计算压力下的介质饱和温度(热水锅炉为额定出水温度),C; 1 计算温度.C;
GB/r16508.3一2013 介质额定平均温度,C; lm0 设计附加压力(安全阀整定压力),MPa A 受压元件所受液柱静压力,MPa -p 介质流动阻力附加压力,MPa 公 修正系数; 许用应力,MPa [], 设计基本要求 5.1结构要求 5.1.1锅炉设计应遵守TsGG0001《锅炉安全技术监察规程》,TsGG0002《锅炉节能技术监督管理规 程》等安全技术规范,并应采用先进的技术,使产品满足安全、可靠、高效、经济和环保的要求
5.1.2按本部分的规定确定所需考虑的计算载荷及所需进行的载荷计算
按本部分中的有关强度计 算公式或应力分析计算公式和规定,确定受压元件的最小需要厚度
当采用试验或者其他计算方法确定锅炉受压元件强度时,应当将有关的技术资料和方案以及所做 试验的条件和数据提交国家质检总局特种设备安全技术委员会,由该技术委员会评审后,报国家质检总 局核准,才能进行试制试用 5.1.3筒体、炉胆壁厚和长度 5.1.3.1当锅壳内径大于1000mm时,锅壳的取用壁厚应不小于6 当锅壳内径不超过1000 mm5 mm时,锅壳筒体的取用壁厚应不小于4mm
5.1.3.2炉胆内径不应超过1800mm,其取用壁厚应不小于8mm,并且不大于22mm;当炉胆内径 小于或等于400mm时,其取用壁厚应不小于6mm;卧式内燃锅炉的回燃室,其简体的取用壁厚应不 小于10mm,并且不大于35mm. 5.1.3.3胀接连接的筒体、管板,取用壁厚应当不小于12mm
外径大于89mm的管子不应采用胀 接结构设计 卧式锅壳锅炉平直炉胆的计算长度应不超过2000 ,如果炉胆两端与管板扳边对接连接 mm, 时,平直炉胆的计算长度可以放大至3000mm 蒸汽锅炉的最低安全水位应高于最高火界100 ,但锅壳内径不大于1500mm的卧式锅壳 5.1. mm 锅炉的最低安全水位应高于最高火界75mm
锅炉的最低及最高安全水位应当在图样上标明
5.1.5受压部件(元件)结构的型式,开孔和焊缝的布置应尽量避免或减少复合应力和应力集中
使用 的焊缝类型应符合设计文件和GB/T16508.4
要进行无损检测的焊缝应设计成能够进行所要求的无 损检测的型式
. .1.6锅炉主要受压元件的主焊缝(锅壳,炉胆、回燃室,集箱等的纵向和环向焊缝,以及封头,管板、炉 胆顶和下脚圈的拼接焊缝等)应当采用全焊透的对接接头;锅炉受压元件的焊缝不得采用搭接结构;拉 撑件不应当采用拼接
锅壳内径大于1000mm时,应在筒体或者封头(管板上开设人孔;由于结构限制导致人员无 法进人锅炉时,可以只开设检查孔;对锅壳内布置有烟管的锅炉,人孔和检查孔的布置应当兼顾锅壳上 部和下部的检修需求;锅壳内径为800mm1000mm的锅壳锅炉,至少应当在筒体或者封头(管板 上开设一个检查孔;立式锅壳锅炉下部开设的手孔数量应当满足清理和检验的需要,其数量应当不少 于 3 个 55 .1.8对于有炉胆的锅炉,燃烧应在炉胆内完成
进人锅炉的水不得直接冲刷炉胆
炉胆内径大于 1400 mm或热量输人大于12Mw的锅炉,至少在炉内设3个测点进行温度测量
5.1.9水压试验压力应符合GB/T16508.1的规定
GB/T16508.3一2013 5.1.10腐蚀裕量 腐蚀裕量应符合如下规定 a)名义厚度心>20mm的受压元件以及所有平直部件,腐蚀裕量可为0mm 名义厚度<20mm的受压元件,可取0.5mm作为最小腐蚀裕量; b e)在可能发生严重腐蚀的情况下,应相应地增加腐蚀裕量的值 5.2性能要求 设计性能 5.2.1 5.2.1.1制造厂应保证锅炉在设计条件下达到额定燕发量或额定热功率,并提供锅炉经济运行负荷 范围
5.2.1.2在设计条件下运行,锅炉的燕汽品质应达到以下指标 饱和蒸汽锅炉的蒸汽湿度对水火管锅炉和锅壳锅炉不应大于4%;过热蒸汽锅炉过热器人口的蒸 汽湿度不应大于1%;过热燕汽含盐量不应大于0.5mg/lkg 工业用蒸汽锅炉的过热蒸汽温度的偏差应符合如下规定: 当 .<300时,其偏差范围为(-部C; a b 当300C<1.<350C时,其偏差范围为士20C; 当350C<.<400C时,其偏差范围为(-"C 5.2.1.3热水锅炉出水温度和回水温度偏差绝对值不应大于5C
5.3热效率 5.3.1设计时应采取有效的措施,以提高锅炉热效率并降低锅炉运行对环境产生的影响,锅炉应设置 必要的热工及环保监测的测点
5.3.2设计条件下锅炉热效率指标应不小于下列规定值 a)层状燃烧锅炉的热效率不应低于表1的规定; b) 燃油和燃气锅炉的热效率不应低于表2的规定 表中未列燃料的锅炉热效率指标由供需双方商定
表1层状燃烧锅炉热效率 锅炉容量D t/h或Mw 燃料收到基低位发热量 2
GB/r16508.3一2013 表2燃油和燃气锅炉热效率 钢炉容量D 燃料收到基 t/h或Mw 低位发热量 D<2或D<1.4 燃料品种 D -2或D>1.4 Qet.
锅炉热效率 k/ke 重油 86 88 轻油 88 90 88 90 注“气”是指天然气、城市煤气和液化石油气
5 排放要求 排烟处过量空气系数应符合如下的规定 对燃煤室燃炉及带膜式壁的燃煤层燃炉,排烟处过量空气系数不超过1.4 a 对其他燃煤层燃炉,排烟处过量空气系数不超过1.65 b 对正压燃烧的燃油(气)锅炉,排烟处过量空气系数不超过1.15; d)对负压燃烧的燃油(气)锅炉,排烟处过量空气系数不超过1.25
在锅炉系统设计时,锅炉配套辅机的驱动电机宜配有变频调速装置
5. 2 4.3锅炉设计排烟温度应符合下述要求 5 额定蒸发量小于1t/h的蒸汽锅炉,不高于230C; a 额定热功率小于0.7Mw的热水锅炉,不高于180C; b 额定蒸发量大于或者等于1t/h的蒸汽锅炉和额定热功率大于或等于0.7Mw的热水锅炉 不高于170C
5. .4.4锅炉应配置必要的脱硫除尘设备,锅炉宜配备脱硝设备,锅炉大气污染物的排放应符合 GB13271的规定
5.5许用应力 5.5.1本部分常用材料的许用应力[]按GB/T16508.2选取,用于设计计算时,有时还需考虑元件 结构特点和工作条件,按式(1)乘以修正系数 [o]=n[o] 5.5.2修正系数刀根据元件结构特点和工作条件,按表3选取
表3修正系数] 元件型式及工作条件 1.00 锅壳筒体和集箱筒体不受热(在烟道外或可靠绝热) 受热(烟温<600C 0.95 受热(姻温>600 0.90
GB/T16508.3一2013 表3(续 元件型式及工作条件 管子(管接头),孔圈 1.00 烟管 0.80 波形炉胆 0.60 凸形封头,炉胆顶,半球形炉胆,凸形管板 立式无冲天管锅炉与干汽室的凹面受压的凸形封头 1.00 立式无冲天管锅炉凸面受压的半球形炉胆 0.30 0. 立式无冲天管锅炉凸面受压的炉胆顶 .40 立式冲天管锅炉凸面受压的炉胆顶、 0.50 立式冲天管锅炉凹面受压的凸形封头 0.65 卧式内燃锅炉凹面受压的凸形封头 o .80 凸形管板的凸形部分 0.95 凸形管板的烟管管板部分 0.85 有拉撑的平板、姻管管板 0.85 拉撑件(拉杆、拉撑管,角撑板 0,60 加固横梁 1.00 孔盖 1.00 圆形集箱端盖 见表16 矩形集箱简板 1.25 矩形集箱端盖 0.75 5.6计算温度 5.6.1受压元件计算温度取内外壁温算术平均值中的最大值
若受压元件的计算温度低于250C时, 取250C
5.6.2受压元件的计算温度去
按热力计算确定
当锅炉给水质量符合GB/T1576或GB/T12145标 准时,计算温度可按表4确定
表4计算温度. 单位为摄氏度 受压元件型式及工作条件 防焦箱 t十110 直接受火焰辐射的锅壳简体,炉胆,炉胆顶,平板、管板,火箱板,集箱 十90 fmave 与温度900C以上烟气接触的壳筒体、回燃室、平板、管板,集箱 l+70 与温度600C一900C烟气接触的锅壳筒体,回燃室,平板,管板,集箱 十50 lmae 与温度低于600C烟气接触的锅壳简体、平板、管板、集箱 tm十25 水冷壁管 十50 lmave 对流管、拉撑管 la+25 不直接受烟气或火焰加热的元件 注,表中人仅适用于锅炉给水质量符合GB/T1576或GB/T12145的情况
GB/r16508.3一2013 5.7工作压力和计算压力 5.7.1工作压力按式(2)计算: p=户,十p十 5.7.2工质流动阻力-p取最大流量时计算元件至锅炉出口之间的压力降 5.7.3 当所受液柱静压力不大于(p,十p十Ap)的3%时,则取所受液柱静压力等于零
5.7.4受压元件的计算压力按式(3)计算 十公声 力>n 承受内压力的圆筒形元件 6.1范围 本章规定了承受内压的圆筒形元件,包括筒体,集箱、内压管子,大横水管等元件的设计计算方法和 结构要求
6.2符号与单位 计算斜向孔桥减弱系数时的两孔间在简体平均直径圆周方向上的弧长, mm 弯管工艺系数; ! b -弯管外侧厚度实际制造工艺减薄率; 厚度附加量,mm; 受压元件腐蚀裕量, C mm; 受压元件制造减薄量,mm; 受压元件钢材厚度负偏差, mm; D 锅壳筒体内径,mm 集箱筒体外径,mm; D -开孔直径,椭圆孔在相应节距方向上的尺寸,, d ,mm; 孔的当量直径,mm; d
d 相邻两孔直径的平均值, ,mm; 管子的外径,mm d. K 斜向孔桥的换算系数; K 弯管形状系数; 管子厚度下偏差(为负值时)与管子公称厚度的百分比绝对值,%. 7 两孔间在筒体轴线方向上的距离6与两孔间在筒体平均直径圆周方向上的弧长a的 比值; -弯管中心线的半径R与管子外径的比值; n -弯管校核计算最高允许计算压力,.MPa; [L] 弯管中心线的半径或圆弧集箱中心线的半径 R ,mm; 可不考虑孔间影响的相邻两孔的最小节距,mm; 纵向(轴向)相邻两孔的节距,或为火箱管板的内壁间距,mm -横向(环向)相邻两孔的节距, ,mm;
GB/T16508.3一2013 斜向相邻两孔的节距,mm 孔的轴线偏离筒体径向的角度,(); 受压元件名义厚度, mm; o 对接边缘厚度偏差,mm:; o 受压元件计算厚度,mm; 受压元件成品最小厚度,mm; o 制管弯成的弯管外侧的理论计算厚度 ,mm; o 弯管外侧的有效壁厚,mm; 弯管成品外侧的最小厚度,mm; omn 受压元件有效厚度,mm:; o 纵向孔桥减弱系数; 9 横向孔桥减弱系数; e 斜向孔桥减弱系数; o 斜向孔桥当量减弱系数; Pa 焊接接头系数; 9、 最小减弱系数; 9mim 校核部位的减弱系数
p 6.3锅壳和集箱筒体 6.3.1锅壳筒体计算厚度按式(4)计算: D o
2[a 壳筒体成品最小厚度按式(5)计算 om=o
C 锅壳简体名义厚度为圆整数,应满足 0>+C 6.3.2集箱简体理论计算厚度按式(7)计算 pD O
2em[a]十力 其成品最小需要厚度心按式(5)计算
集箱简体名义厚度应满足 0
十C 8 6.3.3校核计算时,锅壳筒体及集箱简体的最高允许工作压力按式(9),式(10)计算: 锅壳筒体 ea0 [[]= 十o
D. 集箱筒体 2e[ol 10 C]= D 式中有效厚度心
按式(11)计算 o
=一C 11
GB/r16508.3一2013 当
按式(11)计算时,取等于g;d也可取为各校核部位的实际测量厚度减去以后可能的腐 蚀诚薄量,此时式(9)中的(p.a.)/(D十),式(10)中的(你.司.)/(D.一司)应以最小值代人
此外由 式(9),式(10)算得的最高允许工作压力还应满足第13章孔的补强要求 6.4承受内压力管子 厚度计算 直管的理论计算厚度按式(12)计算: d
= 12 " 用钢管弯成的弯管,弯管外侧的理论计算厚度按式(13)计算 o
=Ko. 式中弯管形状系数K,按式(14)计算: 4R十d
(14 K R十2a 直管的名义厚度应满足 15 0>十C 由钢管弯成的弯管,弯管的名义厚度应满足 16 0>+C 6.4.2校核计算时,直管最高允许工作压力按式(17)计算 2[a] 17 [p]= dl
一心. 按式(18)计算 =心一C 18 心
.可取实际最小厚度减去腐蚀减薄值
弯管最高允许计算压力[p]、按式(19)计算 [
-,ge 19 弯管外侧的有效厚度心
按式(20)计算 =一 20 带弯管的管子的最高允许工作压力应取式(17)和式(19)中的较小值
6.5立式锅炉大横水管 立式锅炉大横水管(D为102 mm300mm)名义厚度和最高允许工作压力按式(21,式(22) 计算 pD 十3 21 44 33 44(Q 22 [p]一 D 6.6减弱系数及悍接接头系数 6.6.1式(4)和式(7)中的最小减弱系数g取纵向焊接接头系数
、纵向孔桥减弱系数9、两倍横向 孔桥减弱系数2p当2p>1时,取2'-1.00)及斜向孔桥当量碱弱系数g(当9,>1时,取9;=1.00
GB/T16508.3一2013 中的最小值
若孔桥位于焊缝上,应按6.9.3有关规定处理
6.6.2按锅炉制造技术条件检验合格的焊缝,其焊接接头系数g
按GB/T16508.1选取
若环向炽 缝上无孔,则环向焊接接头系数可不予考虑
6.6.3孔排中若相邻两孔的节距(纵向、横向或斜向)不小于按式(23)计算的值时,孔桥减弱系数可不 必计算
》=d
十2./干 23 式中d按式(29)确定
6.6.4相邻两孔的节距小于按式(23)确定的值,且两孔直径均不大于按13.3.6确定的未补强孔最 大允许直径时,应按6.6.6~6.6.12的规定计算孔桥减弱系数
若孔排中相邻两孔中的一孔大于按13.3.6确定的未补强孔最大允许直径,应在满足13.7.2所要 求的条件下,按13.3.713.3.9的规定按单孔进行补强
补强后按无孔处理
若相邻两孔均需要补强,其节距不应小于其平均直径的1.5倍
当相邻两孔均需要补强时,补强计算除符合13.3.713.3.9的规定以外,还应符合以下要求: a)加厚管接头的高度应为厚度的2.5倍 b)加厚管接头的焊脚尺寸应等于加厚管接头的厚度; 若两孔的节距小于两孔直径之和,导致它们的有效补强范围重叠,应按两孔总的补强面积不小 c 于各孔单独所需补强面积之和的方法进行补强
重叠部分补强面积不能重复计算
6.6.5对于立式锅炉筒体上的加煤孔、出渣孔等,均应按13.3..7一13.3.9的规定进行补强,补强后按 无孔处理
加煤孔圈、出渣孔圈等最小需要厚度按13.4.4确定
6.6.6等直径纵向相邻两孔(图1)的孔桥减弱系数按式(24)计算 (24 o 筒体轴线 图1纵向孔桥 6.6.7等直径横向相邻两孔图2)的孔桥减弱系数按式(25)计算 g 25
GB/r16508.3一2013 图2横向孔桥 6.6.8等直径斜向相邻两孔(图3)的孔桥当量减弱系数按式(26)计算 26 9
=Ke" 筒体躺线 图3斜向孔桥 斜向孔桥换算系数K按式(27)计算 K 27 (1十n 当n>2.4时,可取K=1,此时gi="
斜向孔桥减弱系数"按式(28)计算 "=S 28 式中=a1时,取仰=1.00s9也可按线算图(图4)直接查取 10o
GB/T16508.3一2013 l.0 0.15 -0.20- 0.25 0.30- .35 -0.40+ -0.45 -0.50 .0.55t -0.60 0.65 .7不 武 M 0.3 了 0.2 0.2 0.2 0.4 0.6 0.8 1.0 1.8 2.0 2.2 注图中虚线为各条曲线极小值的连线 d十d山 2a 筒体轴线 图4确定p,值的线算图 6.6.9若相邻两孔直径不同,在计算孔桥减弱系数时,式(24),式(25)及式(28)中的直径d取相邻两 孔的平均值d.,即 -山十山 d 29
GB/r16508.3一2013 6.6.10计算凹座开孔(图5)的孔桥减弱系数时,式24),式(25)及式28)中的直径d以当量直径d 代人,d
按式(30)计算 30 d
=d十"('一d A 式(30)中d,d参见图5
6.6.11如孔排中的孔为非径向孔(图6),计算孔桥减弱系数时,式(24),式(25)及式(28)中的直径d 以当量直径d
代人.d
按如下规定确定: 纵向孔桥 31) d
=dl 横向孔桥 32 dd cOSa 斜向孔桥 d
=d (33 VOa 非径向孔孔轴与径向夹角a不应大于45
非径向孔宜经机械加工或仿形气削成形
图5具有凹座的孔 筒体轴线 图6非径向孔 12
GB/T16508.3一2013 6.6.12对于椭圆孔,计算孔桥减弱系数时,孔径d按该孔沿相应节距方向上的尺寸确定
6.7附加厚度 锅壳筒体的厚度附加量c按式(34)计算 6.7.1 (34 C+C
十C C 腐蚀裕量与水侧的含氧量相关,也与烟气侧的含硫量相关,并与锅炉的设计寿命相关,腐蚀裕量的 附加厚度C一般取0.5mm,对厚度超过20mn的元件,腐蚀裕量可取0mm,若腐蚀减薄量超过 0.5 mm,则取实际可能的腐蚀减薄值
制造减薄量的附加厚度C应根据具体工艺情况而定:一般情况下,冷卷后冷校的锅壳筒体,可取为 零;冷卷后热校的锅壳筒体,可取为1mm;热卷后热校的锅壳筒体,可取为2mm 钢材厚度负偏差(为负值时)的附加厚度C按有关材料标准确定
6.7.2集箱简体的附加厚度 6.7.2.1设计计算时,集箱筒体的厚度附加量按式(38)计算
对于由钢管制成的直集箱筒体,C按6.7.1原则处理,C
取为零,C
按式(35)计算 mm 35 -(
十C 100 对于由钢管弯成的圆弧形集箱筒体,C按6.7.1原则处理,C,C分别按式(36)和式(37)计算 (36 1 一12n十 n 式中n为集箱中心线的弯曲半径与集箱简体外径的比值,当>4.5时,按直集箱处理
-(o
十C 37) 100 -m 6.7.2.2校核计算时,集箱筒体的厚度附加量C按式(38)计算 38 C=CC
十C 对于由钢管制成的直集箱筒体,C按6.7.1原则处理,C
取为零,C按式(39)计算 39) O" 对于由钢管弯成的圆弧形集箱简体,C按6.7.1原则处理,C按式39)计算
C按式(40)计算: (40 2(4M十工 式中n为弯管中心线半径与管子外径的比值
6.7.3承受内压力管子的附加厚度 6.7.3.1设计计算时,管子的厚度附加量按式(38)计算
对于直水管,C按6.7.1原则处理,对换热管C取零,C取为零,C按式(41)计算 C,= -(o
十C (41 -勿 对于由钢管弯成的弯管,C按6.7.1原则处理,对换热管C取零,C.,C分别按式(42)和式(44) 计算 a -(o十C C2 42 100 a 式中弯管工艺系数a按式(43)计算 25d
43) R 13
GB/r16508.3一2013 当弯管外侧厚度实际制造工艺减薄率b大于计算所得的a值时,a值应取弯管外侧厚度实际制造 工艺减薄率值
n (44 -(oe十C十Ca G,-" 办 6.7.3.2校核计算时,管子的厚度附加量C按式(38)计算
对于直管,C按6.7.1原则处理,对换热管C取零,C取为零,C按式(39)计算
对于由钢管弯成的弯管.C,按6.7.1原则处理,对换热管C,取零.,C,按式(39)计算.C,按式(45 计算: C" 45) G-C) 6.8厚度限制 6.8.1锅壳内径D大于1000mm时,锅壳筒体的名义厚度不宜小于6mm;锅壳内径D不大于 1000 mm时,锅壳筒体的名义厚度不宜小于4mm
6.8, 2 立式锅炉大横水管的名义厚度不宜小于6n mm 3 6.8. 不绝热的锅壳置于烟温不小于600C的烟道或炉膛内时,名义厚度不应大于表5所列数值
表5不绝热锅壳的最大允许厚度 单位为毫米 工作条件 最大允许厚度 在炯温大于900C的烟道或炉膛内 26 在烟温为600C一900之间的烟道内 30 6.8.4对于额定压力大于2.5MPa的锅炉,不绝热集箱筒体的厚度不应大于30 mm
6.8.5对于额定压力不大于2.5MPa的锅炉,不绝热集箱和防焦箱筒体的厚度不应大于表6所规定 的值
表6不绝热集箱和防焦箱筒体的最大允许厚度 单位为毫米 作 条 最大允许壁厚 在姻温大于900C的烟道或炉膛内 15 在烘温为600一900C之间的州道内 20 g 6. 结构要求 6.g9.1对于胀接管孔,孔桥减弱系数9、'及"均不应小于0.3;胀接管孔中心与焊缝边缘的距离不应 小于0.8d,且不小于0.5d十12mm;在纵焊缝上不得有胀接管孔,若需在环缝上开胀接管孔应符合 TsGG0001《锅炉安全技术监察规程》的要求
6.9.2胀接管子的锅简(壳)的厚度应不小于12mm
胀接管孔间的净距离不应小于19mm
外径大 于63.5mm的管子不宜采用胀接
6.9.3焊接管孔应尽量避免开在主焊缝上,并避免管孔焊缝边缘与相邻主焊缝边缘的净间距小于 10mm
如不能避兔时,应满足下列要求 距管孔中心1.5倍管孔直径(当管孔直径小于60mm时,为0.5d十60mm)范围内的主焊缝经 射线或者超声波检测合格,且孔周边不应有夹渣缺陷; b)管子或管接头焊后经热处理或局部热处理消除残余应力
14
GB/T16508.3一2013 此时,该部位的减弱系数取孔桥减弱系数与焊接接头系数的乘积
相邻焊接管孔焊缝边缘的净间距不宜小于6mm,如焊后经热处理或局部热处理,则不受此限 6.9. 锅壳筒体与扳边的平管板或凸形封头的连接型式如图7所示
6.9.5锅壳筒体与平管板采用坡口型角焊连接时,应符合如下规定 a)锅炉的额定压力应不大于2.5MPar b)烟温不大于600C部位(不受烟气冲刷部位,且采用可靠绝热时,可不受此限); 应采用全焊透,且坡口经过机械加工(参见图8),坡口段厚度不需强度校核 C d 卧式内燃锅炉锅壳、炉胆的管板与筒体的连接应当采用插人式的结构; 连接焊缝的厚度应不小于管板的厚度,且其焊缝背部能封焊的部位均应封焊,不能封焊的部位 应采用氧弧焊打底,并应保证焊透; f 焊缝应按NB/T47013(JB/T4730)的有关要求进行超声检测; 说明 当扳边元件内径小于或等于600mm时,直段长度应大于或等于25mm 当扳边元件内径大于600mm时,直段长度应大于或等于38mm; 对接边缘厚度偏差》'应当小于或等于(0.1十1),且小于或等于4mm 对扳边内半径r:平板或管板见9.3.1l;碟形封头见8.4.7; 当超过规定值时,应进行削薄,削薄长度不应小于削薄厚度的4倍
图7锅壳筒体与扳边的平管板或凸形封头的连接 15
GB/r16508.3一2013 6min 6min 1020 倚体 35"45 三510 r为10对应最小角度10" 平管板 平管板 "为5对应最大角度20 图8锅壳筒体与平管板连接的坡口型角焊结构(参考图 承受外压力的圆筒形炉胆、冲天管,烟管和其他元件 7.1范围 本章计算公式适用于承受外压不超过2.5MPa的炉胆,回燃室、冲天管,烟管等圆简形元件的设计 计算方法和结构要求 7.2符号和单位 炉胆内径, D mm D. -炉胆平均直径,波形炉胆平直部分的平均直径,mm 炉胆外径,mm; 计算温度时的弹性模量,MPa; 炉胆顶外高度,mm; -波纹截面对其自身中性轴的惯性矩, ,mm'; 加强圈对其自身中性轴的惯性矩,mm'; 膨胀环对其自身中性轴的惯性矩,mm' 所需要的惯性矩,mm'; 扳边元件直段长度,mm 炉胆的计算长度,mm 强度安全系数; 稳定安全系数; R 波形炉胆的波纹外半径,mm; 波纹炉胆的波纹中半径 R ,mm; 波形炉胆的波纹内半径,mm:; -波形炉胆的波纹节距,mm; 卧式平直炉胆圆度百分率; 4 W -波形炉胆的波纹深度,mm; 平炉胆计算长度的增值; N 中性轴.r一x与通过圆心的轴线 Zo.Z 的距离, .mm 半夹角,rad(弧度); 16
GB/T16508.3一2013 受压元件名义厚度,mm; 受压元件理论计算厚度 ,mm; 受压元件最小成品厚度,mm; h E o 受压元件设计厚度,mm 受压元件有效厚度,mm; 最小减弱系数
Pmimn 7.3圆筒形炉胆 7.3.1平直炉胆 7.3.1.1卧式平直炉胆设计厚度按式(46)式(48)计算,取两者较大值 O.2D区 旦 = l十1十- 46) 2 (+ 式中 pDn B (47 置 2RL1+ 或 Ln 十1 48 >D” 1.73E 式中,L为炉胆计算长度;n为炉胆强度安全系数;n为炉胆稳定安全系数,n、n按表8选取 7.3.1.2校核计算时,卧式平直炉胆的最高允许工作压力按式(49),式(50)计算,取两者较小值
Dm" 2R.(o 15L (49 [门= 03D. nDm 0. Dm丛 Dm 一11十 0.3 Lr3E@- 50) [p]- LDn 式中,L为炉胆计算长度;n为炉胆强度安全系数;n为炉胆稳定安全系数,ni、n按表8选取
7.3.1.3立式平直炉胆的设计厚度和最高允许工作压力按式(51),式(52)计算 pD 、=1.5 PmR D gimRmO 52 [- 6.6LD 1.5D 十2 RD2" 7.3.1.4立式平直炉胆上布置孔排时,最小减弱系数按以下规定确定 多横水管锅炉(图9),水冷炉排锅炉(图1o)的爷山=1.00,但
不应大于45",非径向孔宜经机 a 械加工或仿形气剖成形,两侧边缘管孔的媒缝尺寸应满足图40(拉撑管与平管板的连接》 要求; b)弯水管锅炉(图11)的e按7.3确定(带有冲天管时,取横向减弱系数e'=1.00);如采用坡口 型角焊,可按13.7的规定考虑管接头和焊缝对开孔的补强
17
GB/r16508.3一2013 图g多横水管锅炉 图10水冷炉排锅炉 图11弯水管锅炉 7.3.1.5炉胆的计算长度L按以下规定确定 a)炉胆与平管板或凸形封头连接处,若是扳边对接煤时,以扳边起点作为计算支点,即!的起算 点;若是坡口型角焊时,以角焊根部作为计算支点; b 平直炉胆用膨胀环连接时,以膨胀环中心线作为计算支点(图19): c 平直炉胆上煤以加强圈时,以加强圈横向中心线作为计算支点(图18) d)立式锅炉平直炉胆在环向装有拉杆时,如拉杆的节距不超过炉胆厚度的14倍,可取这一圈拉 杆的中心线作为计算支点,拉杆直径不应小于18mm; 立式锅炉平直炉胆与凸形炉胆顶相连时,计算支点如图12所示,其中X值按表7选取
表7x值 h
/D 0.17 0.20 0.25 0.30 0.40 0,50 x/D. 0.07 0.08 0.10 0.12 0.16 0.20 注相邻两个数值间的x/D采用算术内插法确定,数值保留到小数点后二位 18
GB/T16508.3一2013 U型下脚圈 s型下脚圈 H型下脚圈 图12立式锅炉平直炉胆计算长度L的起算点 7.3.1.6对于有锥度的平直炉胆(图13),内径D取D与D"之和的一半 7.3.1.7卧式平直炉胆的圆度百分率《按式(53)计算 20D-D. min (53 u= D.m、十D. 也可取u=1.2
7.3.1.8卧式平直炉胆强度安全系数n与稳定安全系数n按表8选取 表8安全系数n,n 锅炉级别 O 0.38MPa,且D<480MPamm1 3.5 3.9 其他情况 3.0 7.3.1.9计算温度
时的屈服点d按GB/T16508.2确定
7.3.1.10材料的弹性模量E按表9确定
表9材料的弹性模量E" 计算温度! 250 300 350 400 450 弹性模量E 195×10 91×10 86×10 181×10 178×10 MPa 注:相邻两数值间的E值采用算术内插法确定
19
GB/r16508.3一2013 7.3.1.11立式平直炉胆上的加煤孔、出渣孔等,均应按13.3的规定进行补强,补强后按无孔处理
图13带有锥度的平直炉胆 7.3.2波形炉胆 7.3.2.1波形炉胆的设计厚度按式(54)计算 D
. 十1 54 2[ 7.3.2.2校核计算时,最高允许工作压力按式(55)计算 2- [o] (55 []= D
20
GB/T16508.3一2013 150 AS s=150 =200 图14波形炉胆(参考图 7.3.2.3波形炉胆彼此连接处,各自平直部分的长度不应超过125mm(图15) 7.3.2.4波形炉胆与平管板或凸形封头连接处的平直部分长度不应超过250 mm,否则,按7.3.3.1 处理
不大于125 图15波形炉胆连接处平直部分尺寸 21
GB/r16508.3一2013 7.3.3平直与波形组合炉胆 7.3.3.1对于平直与波形组合炉胆(平直部分长度超过250mm),波形部分的设计厚度及最高允许计 算压力按式(54),式(55)计算;而平直部分的设计厚度与最高允许工作压力按式(46)式(50)计算,其 计算长度L取最边缘一节波纹的中心线至计算支点[7.3.1.5a)]之间的距离图16). 同时,要求最边缘一节波纹的惯性矩不小于按式(56)算出的需要惯性矩1',即: lD (56 1>I'= .3又I0 图16平直与波形组合炉胆平直部分的计算长度L. 由扇形圆环组成的波形炉胆中一节波纹对其自身中性轴.r一r(图17)的惯性矩1按式(57)计算 ,-展二 S (R:一)sind'十2e(R一广) -[2a'十sin(2a')]一 (57) 式(57)中R,r,a',a分别按式(58)式(61)计算 R
=R十 58 兰 厂=R 59 =arcsin 60 京 a=Rcosa 61 式(58)式(61)中R按式(62)计算 S Ww R 62 16W 22
GB/T16508.3一2013 图17波纹几何特性 常用波纹(图14)对其自身中性轴的惯性矩1如表10所示
表10波纹截面对其自身中性轴的惯性矩I 0'mm" /mm 图序号 10 11 12 13 14 15 16 17 18 19 20 21 22 节距15o 6 图14a 31.835
6 39.543.547.7 52 56.5 65,970,976,181.587 2 波深38 节距150 图14b 37.6 6.751.456,261.266,371.777.282.988,894.5101.3 波深4] 节距200 图l4e 129.2138.7147.5155.7163.3170.3176.8182.9188.4193.5198.3202.7206.8 波深75- 注:表中给出的I值已考虑了厚度减薄量,例如,对于=10mm,I值是按9mm计算的
7.3.3.2如式(56)未能满足,可在炉胆平直部分设置加强圈(图18)用以减小L,以满足式(56)的 要求
加强圈与膨胀环 7.3.4 加强圈截面对其自身中性轴的惯性矩!,按式(63)计算 7.3.4.1 h 63 l2一 其中为加强圈厚度(参照图22); h为加强圈高度(参照图22) 它不应小于按式(64)算出的需要惯性矩",即 A,D (64 !,>"= 一了 .33×10 式(64)中承压计算长度L
按各计算支点均分原则处理,例如对图18中加强圈,l
为L与L之和 的一半
23
GB/r16508.3一2013 Ls! 图18炉胆平直部分设置加强圈 7.3.4.2膨胀环(图19)截面对其自身中性轴的惯性矩!如表11所示,它不应小于按式(65)算出的需 要惯性矩",即 D. 65 I>'- 1.33×10° 式(65)中承压计算长度L按7.3.4.1所述原则处理
149 直 包 容 o 180 和-1的较小值 图19膨胀环(参考图 24
GB/T16508.3一2013 表11膨胀环对其自身中性轴的惯性矩1 mmm 心 图序号 10 ll 12 13 14 15 16 18 19 22 1o'mm 252 407430 454 图19a 189 210 231 273 295 317 339 361 384 图19b 130 44 159 174 190 204220 236252268 284301 318 图19c 114 128 141 155 170 186 204 222 24 260 280 301 322 注:表中给出的!值已考虑了厚度减薄量,例如,对于心=10mn,I值是按9mm计算的 7.3.5结构要求 7.3.5.1平直或波形炉胆的内径D不应大于1800nmm
7.3.5.2平直或波形炉胆的名义厚度不应小于8mm,且不应大于22mm;当炉胆内径不大于400m 时,其名义厚度应不小于6nmm 7.3.5.3卧式平直炉胆计算长度一般不宜超过2000mm,如炉胆两端均为扳边连接,则计算长度可放 大至3000mm
超过上述规定时,应采用膨胀环或波形炉胆来提高柔性,此时,波纹部分的长度应不小 于炉胆全长的1/3
7.3.5.4平直炉胆与波形炉胆的连接结构如图20所示
平直炉胆与波形炉胆的波纹顶部、底部或中 部对齐均可
说明,/见图7
图20波形炉胆与平直炉胆的连接 7.3.5.5卧式炉胆与平管板或凸形封头的连接结构如图2!所示
如采用坡口型角焊连接,应按6.9
5的规定处理
25
GB/r16508.3一2013 炉胆 说明:/见图7,"见97 ,3
N 图21卧式炉胆与平管板或凸形封头的连接 7.3.5.6加强圈的厚度应不小于,但不大于20或22mm[见图22a]
如大于22mm,应将底部 削薄,削薄后的根部厚度不应大于22mm[见图22b)]
加强圈高度h应不大于6o
加强圈与炉胆的 焊接应采用全焊透型(图22) 2 b 图22加强圈 7.4圆筒形湿背回燃室 7.4.1卧式内燃锅炉的回燃室筒体按卧式平直炉胆计算,如为焊接所需而削薄两端部时,削薄部分厚 度无需另行计算
7.4.2回燃室简体的名义厚度应不大于35mm,且不应小于10mm
7.5冲天管 7.5.1立式锅炉冲天管的设计厚度和最高允许工作压力按式(51),式(52)计算,取h=1.00;对于蒸 汽锅炉,附加厚度由2mm增至4mm. 7.5.2冲天管计算长度L按7.3.1.5a)处理
7.6烟管 7.6.1承受外压力烟管包括螺纹管)的名义厚度和最高允许工作压力按式66)计算或按表12,取其 中的较大值: dl
习 十C (66 2[o] 26
GB/T16508.3一2013 表12管子的最小公称厚度 单位为毫米 公称外径 名义厚度 d.25 25dl.76 2.5 76
锅壳锅炉第3部分:设计与强度计算GB/T16508.3-2013
锅壳锅炉是一种常见的工业锅炉,广泛应用于化工、制药、纺织、造纸、食品加工等领域。锅壳锅炉的设计和强度计算是保证其安全运行的关键,对于生产企业和用户单位都具有重要意义。
GB/T16508.3-2013《锅壳锅炉 第3部分:设计与强度计算》是我国锅炉行业的标准,规定了锅壳锅炉的设计原则、计算方法、材料选择、接头结构等内容。该标准适用于蒸汽压力不超过9.8MPa、蒸发量不超过20t/h的锅壳锅炉。
锅壳锅炉的设计需要考虑多方面因素,如受力情况、温度应力、振动和蠕变等。根据GB/T16508.3-2013标准,设计过程中应采用先进的计算方法,考虑锅炉的实际工作条件和使用环境,对各个部位进行强度计算和优化设计。
在锅壳锅炉的设计中,材料的选择也是至关重要的一环。根据GB/T16508.3-2013标准,应选择符合国家或行业标准的材料,并对其进行适当的热处理和检验。同时,在接头结构设计时,还应考虑焊接质量、防止应力集中等因素。
总之,锅壳锅炉的设计与强度计算是保证其安全运行的重要保证。遵循GB/T16508.3-2013标准,采用科学合理的计算方法和材料选择,对锅炉进行优化设计和检验,能够有效提高锅炉的安全性和可靠性,为生产企业和用户单位带来实际的经济效益。