GB/T13393-2008
验收抽样检验导则
Guidetoacceptancesamplinginspection
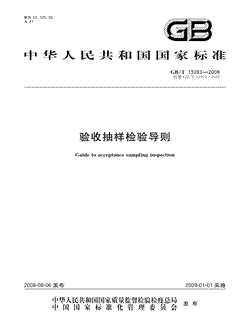
- 中国标准分类号(CCS)A41
- 国际标准分类号(ICS)03.120.30
- 实施日期2009-01-01
- 文件格式PDF
- 文本页数15页
- 文件大小679.15KB
以图片形式预览验收抽样检验导则
验收抽样检验导则
国家标准 GB/13393一2008 代替GB/T133931992 验收抽样检验导则 Guidetoacceptaneesamplinginspectiom 2008-08-06发布 2009-01-01实施 国家质量监督检验检疫总局 发布 国家标准化管蹬委员会国家标准
GB/T13393一2008 目 次 前言 范围 规范性引用文件 术语、定义和符号 术语和定义 符号 影响选择的市场情况和生产条件 市场情况 生产条件 选择抽样方案的协商程序 影响抽样方案选择的其他因素 6. 不合格品百分数检验和每百单位产品不合格数检验 生产方风险和使用方风险 AQL、PRQ、IQ和CRQ值的选取 检验水平的确定 抽样检验方法的比较 计数抽样检验与计量抽样检验 -次、二次、多次和序贯抽样方案 OC曲线的作用 采用验收抽样国家标准的效益 参考文献 12
GB/T13393一2008 前 言 本标准代替GB/T13393一1992《抽样检查导则》. 本标准与GB/T133931992的主要差别: a)按照GB/T1.1一2000的要求重新起草了标准文本
b)为便于标准的理解,增加了相关的、术语、定义和符号
为适应抽样检验标准系列的发展,增强标准的操作性,重新设计了标准的技术架构
增加了第 5、6、7、8章
d)删除了原标准的附录A,并将其内容整合到了标准正文中
本标准由标准化研究院提出
本标准由全国统计方法应用标准化技术委员会归口
本标准起草单位;人民解放军军械工程学院.标准化研究院、科学院数学与系统科学 研究院,福州春伦茶业有限公司
本标准主要起草人;张玉柱、于振凡陈敏、丁文兴.冯士雍、傅天龙
本标准于1992年首次发布,本次为第一次修订
业
GB/T13393一2008 验收抽样检验导则 范围 本标准规定了验收抽样检验中选择抽样系统,抽样计划及抽样方案的导则
给出一些指导性的表 表1,表2a,表2b及表3),便于使用者选择一种合适的抽样系统、抽样计划和抽样方案
本标准适用于批产品(如材料,零件,部件、整机和系统)的验收抽样检验,也可用于对连续提交的在 制品的验收抽样检验
规范性引用文件 下列文件中的条款通过本标准的引用而成为本标准的条款
凡是注日期的引用文件,其随后所有 的修改单(不包括勘误的内容)或修订版均不适用于本标准,然而,鼓励根据本标准达成协议的各方研究 是否可使用这些文件的最新版本
凡是不注日期的引用文件,其最新版本适用于本标准
GB/T2828.1计数抽样检验程序第1部分;按接收质量限AQL检索的逐批检验抽样计划 (GB/T2828.12003,ISO2859-l:l999,IDT G;B/T2828.2计数抽样检验程序第2部分:按极限质量(LQ)检索的孤立批检验抽样方案 GB/T2828.2一2008,ISO2859-2;1985,NEQ) GB/2828.3计数抽样检验程序第3部分;跳批抽样程序(GB/T2828.32008,ISO2859-3: 2005,IDT GB/T6378.1计量抽样检验程序第1部分;按接收质量限(AQL)检索的对单一质量特性和单 个AQL的逐批检验的一次抽样方案(GB/T6378.1一2008,ISO3951-1:2005,IDT GB/T8051计数序贯抽样检验方案(GB/T8051一2008,IsO8422;2006,IDT GB/T8052单水平和多水平计数连续抽样检验程序及表 GB/T8054计量标准型一次抽样检验程序及表 GB/T13262不合格品百分数的计数标准型一次抽样检验程序及抽样表 GB/T13264不合格品百分数的小批计数抽样检验程序及抽样表 统计学词汇及符号第1部分一般统计术语与用于概率的术语 ISO3534-l:2006 ISO3534-2:2006统计学词汇及符号第2部分:应用统计 术语、定义和符号 术语和定义 下列术语和定义适用于本标准
3.1.1 验收抽样系统acceptance samplingsystem 验收抽样方案、验收抽样计划及用于选择合适的抽样方案或抽样计划的准则的集合
[ISO3534-2:2006中的4.3.1] 3.1.2 验收抽样计划acceptaneesamplingscheme 验收抽样方案与从一个抽样方案转为另一个抽样方案的转移规则的组合
[ISO3534-2:2006中的4.3.2]
GB/T13393一2008 3.1.3 验收抽样方案aceptaneesamplingpanm 由所使用的样本量及相应的接收准则组成的方案
[IsO3534-2;2006中的4.3.3] 3.1.4 操作特性曲线operatingcharacteristiccurve oC曲线oc curve 对给定[验收]抽样方案,表示产品的接收概率与其质量水平之间关系的曲线
[ISO3534-2:2006中的4.5.1] 3.1.5 检验水平 inspectionlevel 预先设定的,反映样本量和批量关系的与验收抽样计划检验量有关的指数
注1:如果经验表明较低和(或)较高鉴别力的操作特性曲线是适宜的,则可选择相应的较低和(或)较高的检验 水平
注2:该术语不应与抽样严格度相混淆
抽样严格度与自动运作的转移规则有关
ISO3534-2:2006中的4.3.5] 3.1.6 鉴别比diserimimationratio 《验收抽样)使用方风险质量与生产方风险质量之比 ISO3534-2:2006中的4.6.12] 3.1.7 接收质量限 qualitylimit acceptance 验收抽样)可容忍的最差质量水平
注l:本概念仅适用于诸如GB/T2828.1和GB/T6378带有转移规则和暂停规则的验收抽样计划
注2虽然具有与接收质量限一样质量水平的某些个别批,能以相当高的概率接收,但是,指定接收质量限并非暗示 它是所需要的质量水平
注3在有些标准(如GB/T2828.1)中出现的带有转移规则和暂停规则的[验收]抽样检验计划,其设计目的是激励 供方具有比接收质量限一致地好的过程平均
若供方做不到,则从正常检验转移到加严检验的概率很高
旦执行加严检验,除非采取改进过程的行动,则根据转移规则有很大的可能暂停抽样检验
注4:不再推荐将缩略语AQL表示“可接收质量水平(acceptablequalitylevel)” [ISO3534-2:2006中的4.6.15] 3.1.8 平均检出质量 aVerage outgoingqality 《验收抽样)对于给定的产品质量,检出产品的预期平均质量水平
注l:除非另有规定,平均检出质量是用所有接收批的产品加上通过100%检验将所有不接收批中的不合格品用合 格品替换来计算的 注2:这些术语和定义,仅用于如下情况;在对不接收批进行100%检验的情况下,被剔除的不合格品能用合格品 替代 注3:平均检出质量的一个常用近似值是“给定的过程质量乘以接收概率”
该公式对接收数为0的方案是精确的 但对其他情况估计值偏高
[ISO3534-2:2006中的4.7.1] 3.1.9 平均检出质量上限averageoutgoingqualitylimit 《验收抽样》对给定的验收抽样方案,且规定剔换不接收批中的所有不合格品除非规范另有规定
GB/13393一2008 情形下,对产品所有可能的质量水平,平均检出质量的最大值
[ISO3534-2:2006中的4.7.2] 3.1.10 极限质量lim ingquality 验收抽样〉在对孤立批进行[验收]抽样检验时,应将其限制在低接收概率的质量水平 [ISO3534-2:2006中的4.6.13] 3.1.11 生产方风险producer'srisk 《验收抽样)当质量水平为可接收时,但不被[验收]抽样方案接收的概率
注1,质量水平可与不合格(不合格品)率有关,并且和AQL.比较起来是可接收的 注2:为解释生产方风险需已知所涉及的质量水平
[Is03534-2:2006中的4.6.4] 3.1.12 生产方风险质量pder'sriskqalts 验收抽样》对于验收抽样方案,与规定的生产方风险相对应的批或过程的质量水平
注1;必须规定操作特性曲线的类型
注2:生产方风险一般规定为5% [IsO3534-2;2006中的4.6.10] 3.1.13 consumer'srisk 使用方风险 验收抽样)当质量水平为不满意值时,但被验收抽样方案接收的概率
注,质量水平可与不合格(不合格品)率有关,且与L.QL比较是不满意的
ISO3534-2:2006中的4.6.2] 3.1.14 使用方风险质量consumer'sriskquality 验收抽样〉对于验收抽样方案,与规定的使用方风险相对应的批或过程的质量水平
注:使用方风险一般规定为10%
[Is03534-2:2006中的4.6.9] 3.2符号 AQL接收质量限 A0QL平均检出质量上限 PR生产方风险 PRQ生产方风险质量 CR使用方风险 CRQ使用方风险质量 LQ极限质量 IL检验水平 oC操作特性曲线 影响选择的市场情况和生产条件 市场情况 为选取合适的抽样系统、抽样计划及抽样方案,至少应考虑下述市场情况 (a)生产被认为是连续的,而且采购方能对供方产品质量改进产生影响
GB/T13393一2008 b产品被接收后,供方仍然负责; e)接收少量不合格品就可能造成重大损失或产生严重危害; d)由于产品来源单一,批不接收可能造成(采购方)工厂倒闭或重大的经济损失; e)单位产品的检验技术复杂,费用很高; f检验具有破坏性
相反的情况如: a)采购方不能对供方产品质量改进产生影响 b产品一旦被接收,供方不再负责; e不合格品可能造成的经济损失或危害较小,或不合格品在使用或组装过程中容易被识别并 剔除; 等效产品的来源多.容易得到 d ei单位产品的检验费用不高; Gf检验没有破坏性
生产条件 4.2 除了市场情况外,下述生产条件也对验收抽样系统、抽样计划及抽样方案的选取产生影响 (g供方的产品质量一贯很好 h有条件采用随机抽样抽取样本 (i 检验逃度快,费用不高" 需要知道产品特性分布的形状、位置和散布程度; 0 (k)产品特性服从正态分布(或可转换为正态分布)
相反的情况见表2b
在表1表2a和表2b中概括指出各种不同检验场合、影响选择的市场情况及生产条件下可采用的 抽样标准和方案
在表3中包括使用表2a和表2b时的一些注解
表1选择验收抽样系统、计划或方案的指导 检验场合 影响选择方案的条件 可利用的抽样方案 有关的抽样标准或方案 100%检验 贵重品 (计数)AQL.方案 GB/T2828. 或 c),(f 计量)AQL方案 GB/T6378.1 GB/T8051,GB/T13264 危险品 计数)标准型方案 计量)标准型方案 GB/T8054 GB/T2828.1 计数)AQL方案 最终检验 a),( 计数)跳批方案 GB/T2828.3 GB/T6378.1 计量)AQL.方案 GB/T8051,GB/T13262 没有所检验产品的历史 (计数)标准型方案 (ai),(e),(e),(f),(c) 质量信息 计量)标准型方案 GB/T8054 平均检出质量上限为 A0QL方案 挑选型 a),(e),( 质量参数 计数)AQL方案 GB/T2828. 小批量 e),( GB/T13264 计数)标准型方案 所接到产品的质量良好 GB/T2828,3 b),(c 计数)跳批方案 连续提交的在制品 f),(g),(i) 连续抽样方案 GB/T8052
GB/13393一2008 表2a按市场情况和生产条件选择验收抽样系统、计划或方案的指导 可采用的抽样标准或方案 市场情况或生产条件 a)采购方可通过反馈促进供方改进产品质量 GB/T2828.1.,GB/T2828.3,GB/T6378.l.,GB/T8051 GB/T2828.1,GB/T2828.3,GB/T6378.1.GB/T8051 产品被接收后,供方仍然负责 b) GB/T8051,(GB/T13264.GB/T13262 c 接收少量不合格品就可造成重大经济损失或严重危害 (d有一批不接收可能造成经济损失和工厂倒闭 A0QL方案 (e单位产品的检验费用很大 GB/T6378.1 f检验带有破坏性 GB/T6378.1 g产品质量一贯很好 GB/T2828.3 h 容易抽取随机样本 GB/T2828.1的二次或五次方案,GB/T 805 检验速度快 GB/T2828. 1的二次或五次方案,GB/T8051 GB/T6378.1 需要知道产品特性的分布的形状.位置和散布程度 (k)产品特性的分布是正态的 GB/T6378.1.GB/T8054 表2b按市场情况和生产条件选择验收抽样系统计划或方案的指导 可采用的抽样标准或方案 市场情况或生产条件 (a采购方不能通过反饥影响供方改进产品质量;单批或 GB/T8051,GB/T13264.,GB/T8054.GB/T13262 孤立批的检验 b产品一旦被接收,供方不再负责 GB/T8051,GB/T13264,GB/T8054,GB/T13262 GB/T 2828.1,GBT6378.1,GBT8031. (c接收少量不合格品不会造成重大损失 GB/T2828.3 等效产品的来源很多 考虑其他因索 单位产品的检验费用不大 考虑其他因素 检验没有破坏性 考虑其他因素 GB/T2828.1,GB/T8051,GB/T6378.1的加严检验 没有供方产品的质量历史信息;或质量历史不佳 GB/T2828.1的一次抽样,GB/T6378. h随机抽样困难或费用昂贵 检验费时或费用昂贵 GB/2828.1的一次抽样,GB/T6378.1 i产品特性分布的形状、位置和散布程度不重要 计数抽样,计量抽样(考虑其他因素 k1产品特性分布未知或非正态 计数抽样 表3表2a和表2b的指导性注解 所有抽样标准都可采用(见第2章)
选取合适的方案还依赖另一些因素
因此,需要较长的过程 a.b 由于个别批的质量较重要,可使用计数(或计量)标准型抽样方案
要使抽样方案具有适当的鉴别力 a),(b 鉴别比要低些)(见7.37 有些场合(如自动化检验)可采用100%检验 需抽样方案的CRQ值比较低,鉴别力适当高(见6.2,6.3,6.4,7.3) 采用挑选型抽样方案,以A0QL为质量参数,这种场合需要较多的管理工作,当抽样检验判为不接收时 更是如此 计量一次或计量序贯抽样是主要选择对象,如采用计数抽样,可采用二次,五次或序贯抽样(见7.1,7.2) e),( 如果信任供方,可由供方采用跳批检验或放宽检验,在抽样计划中,转移规则是基本的保证
GB/T13393一2008 表3(续 如管理不复杂,费用也不高,采用序贯、五次或二次抽样(见7.1,7.2) h),(i 这种情形多半需要计量检验和计量抽样
无论计数抽样或计量抽样都应注意PR,CR,PRQ和cRQ 见6.2,6.3,6.4 这种情形涉及到所考虑的产品特性是正态分布的
但检验可是计量的,也可是计数的
接收准则根据 k 对该分布的了解来决定(见6.2,6.3,6.4) 所有抽样标准都可采用(见第2章)
选取合适的方案还依赖另一些因素
因此,需要较长的过程
抽 c 样方案的鉴别比可适当大些,样本量可适当小些 d),(e. 没有补充注解 ),(G 如果是连续批则使用转移规则,并从加严检验开始,当质量得到肯定时转为正常检验 g 当随机抽样困难时最好采用一次抽样
二次或五次抽样可与子样本选取规则同时使用
序贯抽样宜 h 采用截尾办法 (i 采用风险较大的小样本,但要在长期质量控制的情况下 所有计数抽样标准都可采用
选取合适的方案还依赖另一些因索
如果检验是计量的,可将计量值转 (ki 换为计数值
如长期内可得到关于分布的信息,可使用计量抽样
在刚开始供货的情况下,没有关于 分布的信息,使用计量抽样可能增加风险 注1,当供方对经过抽样检验判为接收的批仍然负责时(见4.1(b),在计数检验的情形可采用GB/T2828.1. GB/T8051或GB/T .1(见表2a)
如果产品被接收后,供方 2828.3;在计量检验的情形,可采用GB/T6378, 不再负责,为保证批质量,在计数检验的情形可采用GB/T8051,GB/T13264,GB/T13262;在计量检验的情 形可采用GB/T8054(见表2b)
选取合适的方案还依赖另一些因素(见表3 注2;在产品来源单一,批不接收可能造成经济损失或工厂倒闭的情况下(见4.1(d)),如果检验费用不高,而且没 有破坏性(见4.1(e),4.1(),可采用AOQL方案见表2a(d)),以平均检出质量上限A0QL为质量参 数
当批不接收时进行全数检验,并以合格品替换批中的不合格品
如果等效产品的来源很多(见4.1 (d)),在考虑其他因素后,选取合适的方案
选择抽样方案的协商程序 供方和采购方应根据产品的质量要求,交付和验收的规定,经协商选用合理的验收抽样方案
具体 协商程序如下 明确单位产品是否符合规定的判据及什么是合格品和不合格品 a b 明确是要求每个单位产品都合格还是批合格
如要求每个单位产品都合格则不能采用验收 抽样; 选用抽样方案应以供方与采购方都可接受的风险因素为基础
同时考虑平均样本量等其他因 素
供方应了解批质量符合要求时被接收的概率;采购方应了解批质量劣于某规定质量时被 接收的概率; 明确抽样方案及批合格与否的判据
影响抽样方案选择的其他因素 不合格品百分数检验和每百单位产品不合格数检验 6
为确定使用不合格品百分数检验还是每百单位产品不合格数检验应考虑如下因素 不合格品百分数检验所关心的是单位产品上有无不合格,一个单位产品上有一个不合格和有 多个不合格都作为一个不合格品处理
b)每百单位产品不合格数检验需对所检单位产品上的每个不合格计数
如果一个单位产品上
GB/13393一2008 可能出现无数个不合格(比如一件铸件上的疵点或针孔),应使用每百单位产品不合格数检验
对某种产品的检验仅使用不合格品百分数检验和每百单位产品不合格数检验中的一种,比经 常从一种变到另一种要好
保存记录对改进产品质量很重要
从保存记录的角度看,每百单位不合格数检验较好
这种 记录包含所有与不合格有关的信息
如采用不合格品百分数检验,有些不合格可能被遗漏
除非产品质量极好,或每个特性的符合性极好,采用每百单位产品不合格数检验时,不合格类 别越多,批不接收的机会越大
6.2生产方风险和使用方风险 采用验收抽样所带来的风险可以计算
由于样本仅构成批的一小部分,验收抽样可能给生产方和 使用方带来风险
一个好批可能不被接收,犯这种错误的概率称为生产方风险(用PR表示);反之, 个坏批可能被接收,犯这种错误的概率称为使用方风险用CR表示)
利用抽样方案的OC曲线,当已知批或过程质量时可读出批(或过程)被接收的概率
对于某 -规定的好质量,生产方要求以高概率接收,这个好质量称为生产方风险质量(用PRQ表示),相应的 不接收概牢即为生产方风险;另方面,对于某一规定的劣质量,使用方要求以低概率技收,这个劣质量称 为使用方风险质量(用cRQ表示),相应的接收概率即为使用方风险(见图1利图2) 1.0 生产方风险 生产方风险点PRP 使用方风险点CRP 使用方风险 R 生产方风险 质量 使用方风险 批 质量PRo 质量CRO7 降低 图1由生产方风险质量PRQ和使用方风险质量CRQ确定的oC曲线 0 生产方风险 生产方风险点(PRP 使用方风险点(CRP) 使用方风险 接收质量限 极限质量 批过程质量 Lo AQL 降低 图2由接收质量限(AQL)和极限质量(LQ)确定的0C曲线
GB/T13393一2008 6.3AQL、PRQ.LQ和CRQ值的选取 6.3.1AQL和PQ的选取 AQL和PRQ都是为了抽样检验的目的而规定的可允许的质量指标,其差别在于;PRQ表示某个 批的质量,而AQL则表示某个过程或一系列批的质量水平 指定AQL(或PRQ)时应考虑如下因素: 要求供方的批平均质量或批质量)不劣于AQL(或PRQ),而且此质量是可达到的;对于采购 方,AQL或PRQ)是一个合理的质量,是满足要求与能够买得起之间的折衷
b)如果需要的产品很容易买到,不合格品可用合格品替换,AQL值可适当大些,反之,一个不合 格品可能引起设备上的某一重要构件失效,又不能用合格品替换时应使用较小的AQL(或 PRQ 考虑整机中包含多少个零部件
如一台设备包括三个零部件,要求设备的不合格品百分数为 1%,则各零部件的不合格品百分数必须更小
整机的不合格率不是由各零部件不合格品百分 数简单相加得到的
如果整机包括n个同样重要的零件,而且如有一个零件失效会使整机失效,则整机的不合格品率 用小数表示)X与零件的不合格品率(用小数表示)r之间有如下的关系: X=1 通过分析以往数据来估计过程平均,将此估计值或略小于它的某个数值定为AQL d e)当给定AQL时,如果所选抽样方案的OC曲线的尾部不能满足使用方的要求,则需指定某个 更严格的AQL 不一定总是先选定AQL再做其他选择
必要时可采用“反推”方法,按其他准则选定一个抽样 方案,然后通过抽样方案表反推出所需的AQL值
使用反推法时,宜考虑OC曲线上某个接收概率低的重要的点,或考虑其他的经济准则
g)把类似产品的某个已知的满意质量水平(或质量)定为AQL(或PRQ h 暂时指定一个AQL或PRQ),然后根据使用情况和经验进行调整
建立一个费用模型,选择AQL(或PRQ)使总费用最小 i 6.3.2LQ和CRQ的选取 LQ和CRQ是为了抽样检验的目的,限制在某一低接收概率的质量水平 指定lQ和CRQ的方法与指定AQL.和PRQ类似
检验水平的确定 检验水平(IL)是抽样计划的相对检验量指标,把样本量与批量联系起来
指定IL应考虑如下因素: 在指定AQL(或PRQ)后,通过考虑IQ(或CRQ)来确定检验水平
比如,在GB/T2828.1中 首先找出最接近满足对AQL和IQ要求的正常检验方案的OC曲线,以及OC曲线所对应的 AQL和判定数组,然后由正常检验抽样方案表找到相应的样本量字码,最后在样本量字码表 中找出与此样本量字码及给定的批量范围所对应的检验水平
如果表中没有检验水平与该字 码和批量范围相对应,需重新考虑AQL和或)IQ值,或放弃这种做法
由于经济原因或试验带有破坏性有时不得不使用低检验水平,比如GB/T2828.1中的S-1
此时,抽样方案的鉴别力降低了
然而,如果有连续批系列的检验记录,利用样本的累积结果 也许可说明该检验水平是可以接受的
GB/T8054主要用于孤立批检验,不使用检验水平检索抽样方案
此时,生产方和使用方都 应重视生产方风险质量和使用方风险质量
GB/T13393一2008 抽样检验方法的比较 计数抽样检验与计量抽样检验 如果观察值服从正态分布,计量抽样检验比计数抽样检验有某些优点
为使生产方(或使用方)得 到某种质量保护,前者所需的样本较小,并能提供有关产品质量的更多信息;后者则不受分布形式假定 的限制,使用较为简便,易为检验员理解和接受
如果验证正态性有困难或希望使用简便而宁可多检验 几个样品;或者检验指标较多,都采用计量抽样检验过于繁琐,可将计量值转换为计数值,然后采用计数 抽样检验
当检验费用很高或检验带有破坏性时,采用计量抽样检验比计数抽样检验有实质上的优越性
如 果检验指标较多,也可考虑对大多数的检验指标采用计数抽样检验,仅对一两个重要指标采用计量抽样 检验
表4给出GB/T2828.1和GB/T6378.1中,当使用检验水平和正常检验一次抽样方案时,几个 样本量字码相应的样本量
表4样本量比较 样本量 样本量字码 GB/T2828.1 GB/T6378.1(a未知 GB/T6378.1(已知 不超过3 20 10 不超过7 不超过14 H 50 20 125 50 不超过33 N 500 150o 不超过95 7.2一次、二次、多次和序贯抽样方案 对于接收数不为零的一次抽样方案可找到一个二次或多次抽样方案,使它们的oc曲线很接近
因此,为比较一次、二次和多次抽样方案只考虑OC曲线是不够的,需综合考虑如下的一些特性 a)简单性;一次抽样方案最容易解释和使用
二次抽样方案有可能抽取第二样本,管理稍麻烦
多次抽样方案和序贯抽样方案更复杂
b)检验量的变异;一次抽样方案的样本量是固定的,因而能预知检验量
二次,多次及序贯抽样 方案的检验量随着前面一些样本的检验结果而变化;但是对任何给定的投人质量可算出平均 抽样个数
投人质量特别好或特别坏时平均抽样个数最少 抽取样品的难易;抽取第二样本有时很方便,抽两个样本并不比抽取具有联合样本量的一个样 本麻烦
但是,有时抽样很费时间,抽取第一样本后,再打乱批中剩余部分去抽取第二样本很 难做到
这时最好采用一次抽样 试验的历时:如果试验历时长,并且有可能同时试验较多样品,采用一次抽样方案较好
如果 -次只能试验一、二件样品,可考虑使用二次,多次或序贯抽样方案
不合格种类;产品不合格的种类多,则二次和多次抽样就更复杂
比如,产品的所有质量特性 都要求检验第一样本,其中有些质量特性还可能要检验第二样本、,第三样本等,此时难以有效 使用劳动力和检验设备
通常,复杂的检验需要简单的抽样方案;比较复杂的抽样方案用于简单的检验,则能收到很好的 效果
示例1为了检验肉类罐头的保存质量,把若干罐放在特定的环境条件下贮藏三周
考虑选用三种抽样方案;抽80 罐试验的一次抽样方案,抽每个样本包括50罐的二次抽样方案和每个样本包括20罐的五次抽样方案
如果使用一次抽 样方案,试验三周可得到结果;采用二次抽样,可能三周内得到结果,也可能需要六周;采用五次抽样,有可能需要试验三
GB/T13393一2008 个半月;如果采用序贯试验就更不现实了
所以,选择一次抽样方案是恰当的
示例2为了作某项破坏性试验,试验站可得到批中所有产品,但试验设备每次只能容纳一件产品
由于主要费用 是试验产品的被破坏,希望在满足对抽样特性的要求下尽可能减少破坏
由于每次只能试验一件产品,采用多次或序贯抽样都可以省时间、减少平均抽样个数
在图3中,给出了样本量为200,接收数为3,拒收数为4的一次抽样方案及其等效二次抽样方案 和五次抽样方案的OC曲线
100F 80 -次与五次 60 40 二次 20 10 ll 12 /AQ 图3一次、二次和五次抽样方案的0C曲线 f 平均样本量;在GB/T2838.1中给出了二次租五次抽样方案的平均样本量出线
对于序贯抽 样方案,在GB/T8051给出了截尾序贯方案的平均抽样个数表
图4给出了与样本量为200,接收数为3,拒收数为4的与一次抽样方案等效的二次和五次抽样方 案的平均样本量曲线
200 一次 二次 60 五次 120 N 样本量字码L,AQL=0.65%
为提交产品的不合格品百分数;ASN为平均样本量
图4与一次方案等效的二次和五次抽样方案的平均样本量曲线 由图4可见.当提交检验批的质量优良或质量低劣时,平均样本量的节约可能达到或超过50%
二次和五次抽样方案所要检验的单位产品的个数都有上限,而序贯抽样方案如不引进截尾规则,一般没 有这样的界限
二次、五次和序贯抽样为显著节约样本量提供了机会,但是,由于使用和管理上的困难,五次和序贯 10
GB/T13393一2008 抽样使用的比较少
随着管理水平和自动化生产程度的提高,五次和序贯抽样将逐步地得到广泛的 应用
7.3oC曲线的作用 每个抽样方案都有相应的OC曲线
为了比较不同抽样方案可比较它们的OC曲线,或者由Oc 曲线导出的一些因子,如A0QL.及鉴别比等
CRQ/PRQ是鉴别比的一个数值指标,此数值越大OC曲线越平缓,抽样方案的鉴别力越低;此数 值越小,OC曲线越陡峭,抽样方案的鉴别力越高
这个指标可用于选择和比较抽样方案
采用验收抽样国家标准的效益 采用验收抽样的主要动力是经济性,既保证被接收批具有一定质量,又可显著节约检验工作量和检 验费用
验收抽样要冒风险
生产方和使用方都希望使自己的风险最小
这就需要合理地选择抽样方案、 控制各自的风险
在产品标准中规定一些统计上完善的验收规则,适当运用验收抽样国家标准,对双方 都有利
非标准化的抽样方法(如百分比抽样等)往往缺乏理论依据
验收抽样国家标准有可靠的理论依 据
采用验收抽样国家标准可以节约主观讨论的时间,在国际贸易中尤为重要
1l
GB/T13393一2008 参 考 文献 [1]于振凡,马毅林,冯士雍,丁文兴.产品质量抽样检验.北京:标准出版社,2008. [2]张玉柱.产品质量检验标准选择与方案制定.北京:标准出版社,2005 12