GB/T32563-2016
无损检测超声检测相控阵超声检测方法
Non-destructivetesting—Ultrasonictesting—Testmethodforphased-arrayultrasonictesting
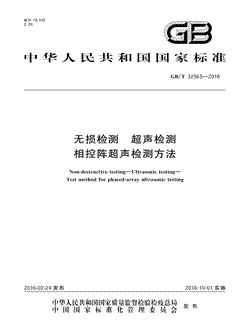
- 中国标准分类号(CCS)J04
- 国际标准分类号(ICS)19.100
- 实施日期2016-10-01
- 文件格式PDF
- 文本页数22页
- 文件大小1.09M
以图片形式预览无损检测超声检测相控阵超声检测方法
无损检测超声检测相控阵超声检测方法
国家标准 GB/T325632016 超声检测 无损检测 相控阵超声检测方法 Non-destrctivetesting一Ultrasonmictesting Ieslmethodforphasetarrayurasonietesting 2016-02-24发布 2016-10-01实施 中毕人民共和国国家质量监督检验检疫总局 发布 中 国国家标准化管厘委员会国家标准
GB/T32563一2016 目 次 前言 引言 范围 规范性引用文件 术语和定义 检测技术等级 检测人员 检测设备 试块 基本要求 检测准备 l0 检测系统的设置和校准 11 检测 12 检测数据的分析和解释 l3 检测报告 附录A(规范性附录相控阵探头晶片灵敏度差异与有效性测试 5 -" 附录B规范性附录相控阵检测系统定位精度测试" 附录c(资料性附录常见其他形式焊接接头推荐的扫查位置
GB/T32563一2016 前 言 本标准按照GB/T1.1一2009给出的规则起草
本标准由全国无损检测标准化技术委员会(SAc/Tc56)提出并归口
本标准起草单位;江苏省特种设备安全监督检验研究院、艾默生过程管理(天津)阀门有限公司、上 海材料研究所、特种设备检测研究院、广州多浦乐电子科技有限公司、奥林巴斯()有限公司、北 京福马智恒检测技术有限公司,浙江省特种设备检验研究院、北京欧宁航宇检测技术有限公司、矩阵科 工检测技术(北京)有限公司,北京邹展麓城科技有限公司、江苏省特种设备安全监督检验研究院张家港 分院,西南交通大学、航空工业集团公司北京航空材料研究院、北京理工大学,南京航空航天大学、 广东省特种设备检测研究院中山检测院、江苏中特创业设备检测有限公司、汕头市超声仪器研究所有限 公司,山东瑞祥模具有限公司、上海船舶工程质量检测有限公司、烟台富润实业有限公司
本标准主要起草人;强天鹏、孙忠波、金宇飞、郑晖、纪轩荣、王晓宁,郑振顺、郭伟灿,郑凯、徐智、 江运喜,李剑峰、许建芹将俞燕萍,涂春磊、王飞、高晓蓉,史亦韦、徐春广,王海涛、富阳,龚成刚陈和坤、 魏忠瑞、邵建华、杨先明
GB/T32563一2016 引 言 本标准提及的相控阵超声是指工业检测使用的相控阵超声技术,虽然相控阵超声属于脉冲反射法 检测范哧,但是在声场特性、检测应用、信号处理与成像、性能和功能等许多方面,相控阵与常规脉冲反 射法有很大不同
相控阵超声使用的探头是由若干压电晶片组成阵列换能器,通过电子系统控制阵列中的各个晶片 按照一定的延时法则发射和接收超声波,从而实现声束的扫描、偏转与聚焦等功能
利用扫描特性,相 控阵技术可以在探头不移动的情况下实现对被检测区域的扫查;利用偏转特性,相控阵技术不仅可以在 探头不移动的情况下实现对被检测区域的扫查,而且可以激发多角度声束对检测区域进行较大面积覆 盖,从而提高检测效率及缺陷检出率;利用聚焦特性,相控阵技术可以提高声场信号强度、回波信号幅度 和信噪比,从而提高缺陷检出率,以及缺陷深度、长度的测量精度
相控阵超声检测系统是高性能的数字 的数字化仪器,能够实现检测全过程信号的记录
通过对信号进行 处理,系统能生成和显示不同方向投影的高质量的图像
正因为相控阵超声与常规超声方法同是基于脉冲反射法检测,因此在本标准的试块、检测级别,以 及缺陷的定量等内容部分参考了常规超声标准
但相控阵技术又是与常规超声差异很大的先进技术, 所以在仪器系统校准、探头参数选择、扫描和扫查方法、工艺参数选择,增益补偿和灵敏度设定等方面标 准给出了与常规超声不同的新规定
I
GB/T32563一2016 无损检测超声检测 相控阵超声检测方法 范围 本标准规定了利用手工扫查或自动(半自动)扫查的一维线阵相控阵超声技术应用基本原则,进行 检测时工艺参数的选用规则,以及确定缺陷位置及尺寸的方法
本标准适用于厚度为6mm~200mm的细晶钢焊接接头
对于其他金属细晶材料焊接接头,在考 虑声速的变化后,也可参照本标准
对于厚度超出以上范围的焊接接头,在通过演示证明仪器系统具有 足够的检测能力后,也可参照本标准
对于奥氏体不锈钢等粗晶焊接接头,在考虑信噪比和声速各向异 性的影响后,也可参照本标准
对于其他结构件、压延件、锻件,在选择合适的试块、校准方法和扫查方法后,也可参照本标准
使用二维相控阵超声探头进行检测,在考虑声场特性变化及其给系统校准和检测带来的影响后,也 可参照本标准
规范性引用文件 下列文件对于本文件的应用是必不可少的
凡是注日期的引用文件,仅注日期的版本适用于本文 件
凡是不注日期的引用文件,其最新版本(包括所有的修改单)适用于本文件 GB/T9445无损检测人员资格鉴定与认证 GB/T12604.1无损检测术语超声检测 GB/T23905无损检测超声检测用试块 JB/T11731无损检测超声相控阵探头通用技术条件 NB/T47013.3 承压设备无拔检渊第3部分;超声检割 术语和定义 GB/T9445和GB/T12604.!界定的以及下列术语和定义适用于本文件
3.1 晶片间距piteh 两个相邻品片的同侧边或者中心之间的距离(见图1
3.2 晶片间隙spacebetweenelements,gapbetweenelements 两个相邻晶片间的空隙(见图1
3.3 激发孔径actieaperture 单次激发晶片组的总长度
即 激发孔径L=n×c一d 式中: 激发孔径 L
GB/T325632016 -激发晶片数量; 晶片间距 晶片间隙
阵列方向 说明 个晶片的宽度; 晶片间距; 个晶片的长度 -晶片间隙
图1线阵列相控阵探头参数 聚焦法则focallaw 通过控制激发晶片数量,以及施加到每个晶片上的发射和接收延时,实现波束的偏转和聚焦的算法 或相应程序
3.5 电子扫描eleetronicscan E扫描 以电子方式实现对工件的扫查,即通过聚焦法则实现波束的移动或角度偏转,使之扫过工件中被检 测区域
3.6 线扫描electroniclinearscan 线形扫描 以相同的聚焦法则施加在相控阵探头中的不同晶片组,每组激活晶片产生某一特定角度的声束,通 过改变起始激活晶片的位置,使该声束沿晶片阵列方向前后移动,以实现类似常规手动超声波检测探头 前后移动的检测效果(见图2)
线扫描包括垂直人射线扫描和倾斜人射线扫描两种
3.7 扇扫描eleetronicseetorialscanm 变角度扫描 用特定的聚焦法则激发相控阵探头中的部分相邻或全部晶片,使激发晶片组形成的声束在设定的 角度范围内以一定的步进值变换角度扫过扇形区域(见图3)
3.8 机械扫查meehaniealscanm 以机械方式实现对工件的扫查,即通过移动探头实现波束的移动,使之扫过工件中被检测区域
GB/T32563一2016 图2相控阵倾斜入射的电子线扫描检测焊缝的示意图 图3相控阵扇扫描检测焊缝的示意图 3.9 沿线扫查meehaniealscanalongtheline 相控阵探头晶片阵列方向与探头移动方向垂直或成一定角度的机械扫查方式
如;焊缝检测时,晶 片阵列方向垂直于焊缝轴线或与轴线成一定角度(斜向扫查),探头前沿离开焊缝中心一定距离s,沿焊 缝轴线方向平移.以获得声束覆盖范围内焊缝的信息(见图4)
沿线栅格扫查 沿线扫查 图4沿线扫查(左)和沿线栅格扫查(右
GB/T325632016 3.10 沿线栅格扫查multiplescanalongtheline 多次沿线扫查,探头按照栅格式的轨迹行进,以实现对检测部位的全面覆盖或多重覆盖
如图4右 所示,对同一焊缝采用多个不同的s值沿线扫查即形成沿线栅格扫查
3.11 角度增益修正anglecoreetedgainm ACG 扇扫描时,因楔块衰减差异晶片间差异及声压往复透射率差异等因素导致不同角度声束对相同声 程处相同尺寸的反射体的回波幅度存在差异,利用软件对该差异进行修正,使之达到相同幅值
3.12 时间增益修正timecoreetelgain TCG 对不同声程处相同尺寸反射体的回波进行增益修正,使之达到相同幅值
3.13 坐标coordinates 相控阵检测规定的检测起始参考点O点和X,Y和Z坐标的含义(见图5). 3.14 S型显示S-display 由扇扫描声束组成的扇面形状的图像显示,图像中横坐标表示离开探头前沿的距离,纵坐标表示深 度,沿扇面弧线方向的坐标表示角度
焊缝检测时,S型显示显示的是探头前方焊缝的横截面信息(见 图3 c型显示 扫查面 B型显示 底面 说明 设定的检测起始参考点 O X -沿焊缝长度方向的坐标 y 扫查面上沿焊缝宽度方向的坐标 垂直于扫查面沿焊缝厚度方向的坐标
图5坐标的定义 3.15 B型显示B-display 工件的侧面投影显示方式,图像中横坐标表示沿线扫查移动的距离,纵坐标表示深度
焊缝检测
GB/T32563一2016 时,B型显示表示检测区域在X-O-Z平面的投影(见图5)
3.16 C型显示c-display 工件的平面投影显示方式,图像中横坐标表示沿线扫查移动的距离,纵坐标表示离开探头前沿的距 离
媒缝检测时,C型显示表示检测区域在X-O-Y平面的投影(见图5)
检测技术等级 焊接接头的相控阵检测技术分为A、B,C三个检测技术等级,不同技术等级对应于不同的缺陷检 出率
4.2焊接接头不同技术等级要求的不同角度的声束覆盖次数: a)A级应保证相控阵声束对检测区域实现一次以上全覆盖
B级应保证相控阵声束对检测区域实现不同角度扫射两次以上全覆盖
b) C级应保证相控阵声束对检测区域实现不同角度扫射三次以上全覆盖
c) 可通过选择不同扫查面、扫查方式、扫查路径和扫描方式来实现上述覆盖 d 当要求对检测区域进行两次以上覆盖时,应尽可能使至少其中两次覆盖的声束来自大致相互 垂直的两个方向
若因条件限制不能实现,则允许来自一个方向,但任两次覆盖的声束夹角不 得小于10°
c级扫查的其中一次扫射可将探头置于焊缝表面上实施扫查,采用此种扫查需要将媒缝余高 磨平
4.3焊接接头不同技术等级要求的信噪比 A级不要求制作模拟试块
在对比试块上测量信噪比,应保证所有声束拟采用的声程范围内 a 2横孔的信噪比大于9dB B级是否制作模拟试块由合同双方商定,模拟试块的制作要求见7.3
在试块上测量信噪比 应保证所有声束拟采用的声程范围内62横孔的信噪比大于12dB C级要求制作模拟试块(见7.3)
在模拟试块上测量信噪比,应保证所有声束拟采用的声程范 围内2横孔的信噪比大于12dB 4.4其他结构形式的工件扫查可以参照接接头的规定区分检测技术等级,也可以不区分检测技术等 级,但至少要求对检测区域全覆盖,且信噪比大于9dB 检测人员 从事相控阵检测的人员至少应符合GB/T9445或等效标准的要求,应通过有关相控阵检测技术 5.1 的专门培训并取得相应证书 5.2相控阵检测人员应熟悉所使用的检测设备
5.3 相控阵检测人员应具有实际检测经验并掌握一定的金属材料及加工的基础知识 检测设备 6.1总则 相控阵检测设备包括仪器、探头、软件、扫查装置和附件,上述各项应成套或单独具有产品合格证或 制造厂出具的合格文件
GB/T325632016 6.2超声相控阵仪器 6.2.1相控阵仪器应为计算机控制的含有多个独立的脉冲发射/接收通道的脉冲反射型仪器,其放大 器的增益调节步进不应大于1dB 6.2.2相控阵仪器应配备与其硬件相匹配的延时控制和成像软件 一3dB带宽下限不高于1MHz,上限不低于15MHH
6.2.3 6.2.4采样频率不应小于探头中心频率的6倍
6.2.5幅度模数转换位数应不小于8位
6.2.6仪器的水平线性误差不大于1%,垂直线性误差不大于5% 6.2.7所有激励通道的发射脉冲电压具有一致性,最大偏移量应不大于设置值的5%
6.2.8各通道的发射脉冲延迟精度不大于5ns
6.3软件 软件至少应有A,S,B.,C型显示的功能,且具有在扫描图像上对缺陷定位,定量及分析功能
6.3.1 6.3.2能够存储、调出A,s,B,C图像,并能将存储的检测数据复制到外部存储空间中
6.3.3仪器软件应具有聚焦法则计算功能、ACG校准功能,以及TcG(或DAC)校准功能
6.3.4仪器的数据采集和扫查装置的移动同步,扫查步进值应可调,其最小值应不大于0.5mm.
6.3.5仪器应能存储和分辨各A扫描信号之间相对位置的信息,如编码器位置
6.3.6离线分析软件中应能对检测时关键参数设置进行查看
相控阵探头 6.4.1相控阵探头应符合JB/T11731
相控阵探头应由多个品片(一般不少于8个)组成阵列,探头可 加装用以辅助声束偏转的楔块或延迟块
6.4.2探头实测中心频率与标称频率间的误差应不大于10%
6.4.3探头一6dB相对频带宽度不小于55%
6.4.4采购验收相控阵探头时,同一探头晶片间灵敏度最大差值不大于4dB,且不应存在坏晶片(相控 阵探头晶片的灵敏度差异、有效性测试方法和坏晶片定义见附录A)
6.4.5使用中的相控阵探头如出现坏晶片,可在选择激发孔径范围时设法避开坏晶片;如无法避开,则 要求在扫查使用的每个声束组中,损坏晶片不应超过总使用晶片数的12.5%,且没有连续损坏晶片;如 果晶片的损坏超过上述规定,可通过仿真软件计算且通过试块测试,确认坏晶片对声场和检测灵敏度 信噪比无明显不利影响,才允许使用
6.5仪器校准 相控阵仪器的性能指标应定期进行校准,校准方法见附录A和附录B
校准周期由使用单位 决定
6.6扫查装置 6.6.1扫查装置应具有确定探头位置的功能,可通过步进电机或位置传感器实现对位置的探测与控 制,位置分辨力应符合工艺要求
6.6.2夹持部分应确保探头与位置传感器同步运动
6.6.3为提高探头运动轨迹与拟扫查轨迹的一致性和数据采集的一致性,应尽可能使用导向装置
6.6.4驱动部分可以采用电机或人工驱动
GB/T32563一2016 试块 7.1试块包括校准试块和模拟试块,试块的一般要求应满足GB/T23905
7.2校准试块用于声速、楔块延时、ACG及TcG的校准,也可用于检测灵敏度的校准,,可采用 NB/T47013.3所述的CSK-IA试块、CSK-A试块.CSK-皿A试块、圆弧孔试块,或与之功能类似的 其他试块
7.3本标准推荐采用CSK-A试块作为灵敏度校准试块
若要求使用其他试块作为灵敏度试块,应 在合同中拟定,且检测准备及实施时应考虑到模拟试块横孔直径(见4.3和7.4)、扫查灵敏度设置(见 10.1、10.2和10.4)等的差异 模拟试块用于检测灵敏度的校准,信噪比的评价,同时可验证检测工艺的有效性
模拟试块的材 7.4 质、形状、结构,厚度,以及焊接坡口型式和焊接工艺应与实际检测的工件相同或相近,应在检测区域内 设置适当的位置设置反射体,反射体应包括用于信噪比测量和灵敏度校准的2×40的横孔,以及其他 机械加工的模拟缺陷和焊接产生的自然缺陷
7.5采用自动(半自动)扫查的检测,应采用模拟试块验证检测工艺的有效性
基本要求 8.1相控阵检测工艺规程 8.1.1检测前,应根据本标准编制相控阵检测工艺规程
8.1.2相控阵检测工艺规程至少应包括以下内容 a 适用范围和对被检工件的要求; b)遵循的规范标准和包含的检测技术等级 被检工件情况(名称、材质,成型方法,坡口形状尺寸,焊接情况热处理情况、母材检测情况等 c 检测的目的、检测覆盖区域、检测时机、采用的规范标准和检测技术等级 对检测人员资格和能力的要求,检测人员培训和工艺验证试验要求; 对检测设备(仪器、探头,试块)的要求 检测参数及要求;包括检测覆盖区域、检测时机、仪器、探头及楔块的参数设置或选择、扫查方 法(机械扫查及电子扫描)的选择、扫查面的确定探头位置的确定、扫查面的准备等,以及检测 系统的设置(激发孔径、扇扫角度和步进、线扫步进、聚焦,时间窗口,灵敏度等)和校准(灵敏 度、位置传感器等)方法,横向缺陷的补充检测方法(必要时); h)扫查示意图(SP):图中应标明工件厚度、焊缝坡口形状、扫查面、探头位置、扫查移动方向和移 动范围、扫描波束角度和覆盖范围等; i 检测温度、扫查速度、数据质量要求; 扫查和数据采集过程的一般要求; k)对数据分析,缺陷评定与记录报告的一般要求
8.2工艺验证试验 工艺验证试验为;制作与被检工件相同或相似的带有缺陷的模拟试件,将拟采用的检测工艺应 8.2.1 用到模拟试件上,以验证拟采用工艺的有效性
工艺验证试验结果应确保能够清楚地显示和测量模拟 试块中的缺陷或反射体
8.2.2符合以下情况之一时应进行工艺验证试验,试验应在模拟试块上进行: a)按C级实施检测的焊接接头;
GB/T325632016 b)按B级采用自动或半自动扫查的批量检测; e)结构和形状复杂的工件; d)信噪比和声速与细晶粒钢差异明细的非细晶粒钢工件检测 e)检测条件(例如检测面)不能满足检测等级要求时 合同要求进行
fD 8.2.3经合同双方同意,可使用经过认证的相控阵仿真软件计算部分或全部代替工艺验证试验内容 8.3焊接接头横向缺陷检测 8.3.1当符合以下条件之一时应进行横向缺陷检测 C级检测; a b)有横向裂纹发生倾向时; c所选用的检测等级有要求时; d)合同或设计文件规定要求进行时 8.3.2对横向缺陷进行检测,当焊缝没有磨平时,可将探头放在靠近焊缝的母材,与焊缝轴线成10" 15"夹角(如图6左),采用扇扫描十沿线扫查方式进行检测
当焊缝磨平时,可采用探头放在焊缝上(如 图6右),采用扇扫描十沿线扫查方式进行检测
扫 扫 t 方 向 向 图6横向缺陷扫查示意图 检测准备 9.1检测区域 炽接接头检测区域应包含焊缝本身宽度加上两侧各10mm或实际热影响区宽度(取较大值)
9.2扫查方式选择 焊接接头首次检测推荐采用以下机械扫查与电子扫描的结合方式 沿线扫查十扇扫描 a b)沿线扫查十线扫描十扇扫描; 沿线栅格扫查十扇扫描
对可疑部位,可采用扇扫描,结合锯齿,前后,左右、,旋转、环绕等各种扫查方式进行检测
9.3探头及楔块的选择 g.3.1根据工件厚度、材质、检测位置、检测面形状以及检测使用的声束类型选择相控阵探头的频率、 晶片数量、晶片间距、晶片尺寸、形状以及楔块规格等
GB/T32563一2016 9.3.2相控阵探头参数的选择可参照表1,通常单次激发的晶片数不少于8个
表1推荐采用的探头参数 最大探测厚度/mm 频率/MHz 晶片间距/mm 偏转方向孔径尺寸/mm 6T<15 15一5 0.8一0.3 5一10 15T50 104 825 1.0~0.5 50
GB/T32563一2016 11 检测 11.1依照工艺设计将检测系统的硬件及软件置于检测状态,将探头摆放到要求的位置,沿设计的路径 进行扫查
扫查过程中应采取一定的措施(如提前画出探头轨迹或参考线,使用导向轨道或使用磁条导 向)使探头沿预定轨迹移动,过程中探头位置与预定轨迹的偏离量不能超过S值的15%
11.2扫查时应保证扫查速度小于或等于最大扫查速度v,同时保证合效果和满足数据采集的要 求
最大扫查速度按式(1)计算 PRF -A.?" U N
A 式中: -最大扫查速度,单位为毫米每秒(mm/s); Umn PRF -激发探头的脉冲重复频率,单位为赫兹(H2); -设置的扫查步进值,单位为毫米(mm); A. N -设置的信号平均次数; A -A扫描的数量(如扇扫描时,激发如35"75"的扇扫描,角度步进为1",则A=4l;又如线 扫描时,探头总体晶片数量为64,同时激发16晶片,扫查步进为1,则A=49). 11.3若需对工件在长度方向进行分段扫查,则各段扫查区的重叠范围至少为20n 对于环状工件 mm
如环焊缝),扫查停止位置应越过起始位置至少20m mm
11.4扫查过程中应保持稳定的合,有稠合监控功能的仪器可开启此功能,若怀疑鹏合不好,应重新 扫查该段区域
12 检测数据的分析和解释 12.1 检测数据的有效性评价 分析数据之前应对所采集的数据进行评估以确定其有效性,数据至少应满足以下要求 12.1.1 数据是基于扫查步进的设置而采集的 a b采集的数据量满足所检测焊缝长度的要求 e)数据丢失量不得超过整个扫查的5%,且不准许相邻数据连续丢失 d)扫查图像中合不良不得超过整个扫查的5%,单个耦合不良长度不得超过2mm 12.1.2若数据无效,应纠正后重新进行扫查
12.2缺陷的测量 12.2.1总则 结合B型显示,C型显示、扇扫描及A扫描显示,对缺陷的位置、幅度、长度进行测量
可采用各种聚焦方法提高定量精度
可采用锯齿、转角,环绕等各种扫查方法提高定量精度和辅助定性
12.2.2回波幅度确定 扇扫描时,找到不同位置扇扫描的不同角度A扫描中缺陷的最高回波幅度作为该缺陷的幅度
线 扫描时,找到不同孔径组合时,缺陷最高回波幅度作为该缺陷的幅度
13
GB/T325632016 12.2.3缺陷长度确定 若缺陷最高幅度未超过满屏100%,则以此幅度为基准,找到此缺陷不同角度A扫描回波幅度降低 6dB的最大长度作为该缺陷的长度
若缺陷最高幅度超过满屏100%,则找到此缺陷不同角度A扫描回波幅度降低到定量线时的最大 长度作为此缺陷的长度
12.3缺陷的评定 缺陷的评定由合同双方商定,或参照有关常规超声标准 检测报告 1 检测报告至少应包括如下内容 a)委托单位 检测标准 D 被检工件:名称,编号,规格、材质,坡口形式,焊接方法和热处理状况 c d)检测设备:仪器型号及编号、扫查装置包括编码器、试块、耦合剂 检测条件:检测工艺卡编号,探头参数及楔块选择、扫查方式(S或E),聚焦法则的设定、检测 使用的波型、检测系统的设置,系统性能试验报告,角度增益修正文件,温度 f 检测示意图:探头扫查表面、检测区域以及所发现的缺陷位置和分布; 检测数据;数据文件名称、缺陷位置与尺寸、质量级别及缺陷部位的图像(s扫描或B扫描等, 以能够真实反映缺陷情况为原则); h 检测结论 iD 检测人员和责任人员签字; 检测日期
j 14
GB/T32563一2016 附录A 规范性附录 相控阵探头晶片灵敏度差异与有效性测试 一般要求 A.1 本测试要求仪器软件能够对相控阵探头的每个晶片进行逐一激发
测试时探头不应加装楔块或延 时块
为减少晶片磨损而附加的保护贴膜应均匀一致,不影响测试结果
A.2测试方法 A.2.1将相控阵探头均匀稳定地耦合在csK-lA-1试块40mm厚度(或等效试块)表面,单独激发第 一个晶片,得到40mm大平底回波
A.2.2调节增益值使40mm的底面回波达到80%满屏高度,记录此时的增益值 A.2.3单独激发下一个晶片,并重复A.2.2,直至最后一个晶片
A.3坏晶片 以下晶片被认定为坏品片 a)未见底面回波信号的晶片; b) 有底面回波信号但信噪比小于12dB的晶片 c 同一阵列中灵敏度明细偏低,比其他晶片的平均灵敏度低9dB以上的晶片
A.4复核 若测试发现各晶片的增益值离散性较大,最大与最小增益值之差>4dB时,应确认稠合一致性及 稳定性,然后按A.2规定的方法重新测试,进行复核
15
GB/T32563一2016 附录B 规范性附录 相控阵检测系统定位精度测试 B.1 一般要求 B.1.1本测试应在检测前、检测过程中以及检测结束后进行
B.1.2不加装楔块或延时块时,本测试可评价仪器软件对声束合成的控制精度
加装楔块或延时块 时,本测试可反映楔块或延时块的磨损,以确定是否需要更换或再校准
B.2测试方法 B.2.1不加装楔块或延时块时 将相控阵探头稳定地稠合到图B1的试块上,并将欲测试晶片组的孔径中心与10o B.2.1.1 mm等声 程孔的声程中心重合
B2.1.2设置扇扫描角度范围一80一80,保存等声程孔的扇扫描图像 B.2.1.3在软件中测量各孔的回波声程及角度,与实际值相比较
B.2.2加装楔块或延时块时 设置教硬件组合,以得到拟用于检测的声束范围
B.2.2.1 B2.2.2在拟用于检测的声束范围内,对靠近的两侧边缘声束及居中间位置的声束分别进行单独激发
B.2.2.3将相控阵探头置于图B1的试块表面,以所选取的声束找到与该声束相同角度位置的孔的最 高回波,记录仪器中测得的孔的位置信息,并与实际值相比较
约20mm o 横孔直径1mmm 半径25mm 横孔直径2mm 半径50mm 0 2.5" 2.5° 图B.1相控阵试块 l6
GB/T32563一2016 附 录c 资料性附录 常见其他形式焊接接头推荐的扫查位置 图c.1一图c.4提供了常见形式焊接接头推荐的扫查位置,可根据被检工件的状态选择不同的方 案,着一个位置扫查或单次扫查不能满足要求时,则宜采取增加扫查位置或增加电子扫描方式等有效的 方法,以达到对检测区域全覆盖的要求
图c.1T型焊接接头 图c.2角接焊接接头 17
GB/T32563一2016 图c.3安放式焊接接头 图C.4插入式焊接接头 18
无损检测超声检测相控阵超声检测方法GB/T32563-2016
相控阵超声检测技术是近年来发展迅速的一种超声检测技术。与传统的单元扫描超声检测技术相比,相控阵超声检测技术具有灵敏度高、分辨率高、可操作性强等优点。
GB/T32563-2016标准规定了相控阵超声检测方法的技术要求和检测步骤。首先,它明确了相控阵超声检测的适用范围和定义。然后,标准对相控阵超声检测设备的性能要求进行了详细说明,包括了其频率范围、脉冲宽度、增益等方面。此外,标准还规定了相控阵超声检测中需要注意的一些问题,例如:在检测不同材料时需要进行不同的参数设置。
相控阵超声检测方法的步骤主要包括以下几个方面:
- 选择适当的探头和扫描方式
- 设置超声检测系统的参数,如采样频率、带宽、起始角度、步进角度等
- 进行探头校准和灵敏度校准
- 进行标定块校验和误差评估
- 进行实际检测
- 数据处理和分析,包括图像重构、缺陷检出等
- 制定评价标准和报告
总之,GB/T32563-2016标准为相控阵超声检测提供了详细的技术要求和操作步骤,对于保证无损检测质量具有重要意义。