GB/T23567.1-2009
数控机床可靠性评定第1部分:总则
Reliabilityevaluationfornumericalcontrolmachinetools-Part1:Generalrule
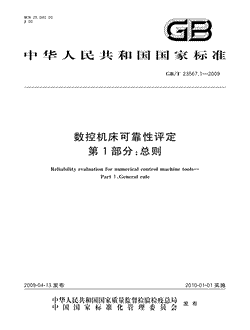
- 中国标准分类号(CCS)J50
- 国际标准分类号(ICS)25.040.20
- 实施日期2010-01-01
- 文件格式PDF
- 文本页数14页
- 文件大小675.92KB
以图片形式预览数控机床可靠性评定第1部分:总则
数控机床可靠性评定第1部分:总则
国家标准 GB/T23567.1一2009 数控机床可靠性评定 第 部分:总则 Reliabhiltyealuationfornumeriealcomtrlmaehimetls一 Part1:Generalrwle 2009-04-13发布 2010-01-01实施 国家质量监督检验检疫总局 发布 国家标准化管蹬委员会国家标准
GB/T23567.1一2009 目 次 前言 范围 规范性引用文件 术语和定义 故障判定 抽样 试验方式 试验条件 试验方法 故障监测 数据的采集 10 可靠性评定指标" 结果判定 12 附录A(规范性附录关于可靠性修正系数及 附录B(资料性附录可靠性试验运行记录 附录c资料性附录)可靠性试验故障记录 附录D(资料性附录)故障分析报告
GB/T23567.1一2009 前 言 GB/T23567《数控机床可靠性评定》分为以下八个部分 第1部分:总则; 第2部分;加工中心; 第3部分:数控车床; 第4部分:数控铁床; 第5部分;数控磨床; 第6部分:数控齿轮加工机床; 第7部分:五轴联动机床; 第8部分:复合加工机床
本部分为GB/T23567的第1部分
本部分的附录A为规范性附录,附录B附录C和附录D为资料性附录
本部分由机械工业联合会提出
本部分由全国金属切削机床标准化技术委员会(SAC/TC22)归口
本部分起草单位;北京机床研究所,国家机床质量监督检验中心 本部分主要起草人;张维,李样文,赵钦志、官端阳
GB/T23567.1一2009 数控机床可靠性评定 第1部分:总则 范围 GB/T23567的本部分规定了数控机床(以下简称机床)在进行可靠性验证、测定、评定时的故障判 定原则,抽样原则,试验方法、数据处理、结果评定的总的要求
本部分适用于数控机床产品的可靠性验证、测定、鉴定和评定
各类数控机床可根据本部分的原则补充编制相应的可靠性评定方法和要求
规范性引用文件 下列文件中的条款通过GB/T23567的本部分的引用而成为本部分的条款
凡是注日期的引用文 件,其随后所有的修改单(不包括勘误的内容)或修订版均不适用于本部分,然而,鼓励根据本部分达成 协议的各方研究是否可使用这些文件的最新版本
凡是不注日期的引用文件,其最新版本适用于本 部分
GB/T3187一1994可靠性、维修性术语 术语和定义 GB/T3187确立的以及下列术语和定义适用于GB/T23567的本部分 3.1 故障fault 产品不能执行规定功能的状态
预防性维修或其他计划性活动或缺乏外部资源的情况下除外
故障通常是产品本身失效后的状态,但也可能在失效前就存在
[GB/T3187一1994,4.2.1] 3.2 关联故障releyantfaut 在解释试验或工作结果或者计算可靠性量值时必须计人的故障
计人的准则应加以规定
[GB/T3187一1994,4.l.13 3.3 非关联故障non-relevantfault 在解释试验或工作结果或者计算可靠性量值时应予排除的故障 [GB/T3187一1994,4.l.14门 误用故障missefaut 使用中超出产品允许范围引起的故障 [GB/T3187一1994,4.2.6 3.5 误操作故障mishamdhnaut 由于对产品操作不当或粗心引起的故障
[G;B/T3187一1994,4.2.7]
GB/T23567.1一2009 3.6 间歇故障interittentfalt 产品未经任何修复性维修而在有限的持续时间内自行恢复规定功能的故障 这种故障往往是反复出现的
[GB/T3187一1994,4.2.17] 3.7 平均故障间隔时间MTBPmeantimebetweenfailures 相邻两故障间工作时间的平均值
3.8 IBr的观测值(点估计)observedTBr 产品总的累计工作时间除以关联故障数
MBr的验证区间demonstratedIBFinterval 在试验条件下真实MTBF的可能范围,即在所规定的置信度下对MTBF的区间估计
3.10 平均修复时间MTR meantimet0restoration 从发现故障到恢复规定性能所需时间的平均值
3.11 预防性维护preventivemaintenanee 为降低产品失效的概率或防止功能退化按预定的时间间隔或时间准则实施的维护
[GB/T3187一1994,5.7] 3.12 验证试验coplianeetest 验证产品的特性或性能是否符合规定要求的试验
[GB/T3187一1994,8.l.2 3.13 测定试验deerminationtest 确定产品特性值或性能值的试验
[GB/T3187一1994,8.1.3 3.14 定时截尾试验tinmetruneateltest 为缩短试验时间,试验进行到一定时间即行停止试验
故障判定 4.1故障的判定原则 4.1.1如果有若干功能丧失或性能指标超过了规定界限,而且它们是由同一个原因引起的,则判为机 床只产生了一个故障 4.1.2如果有一项功能丧失或性能指标超过了规定界限,而且它是由两个或更多独立的故障原因引 起,则每一个独立的故障均判为机床的一个故障
4.1.3如果在同一部位多次出现故障模式相同的间歇故障,则只判机床产生了- 一个故障
4.1.4故障模式相同,由同一个原因引起的重复发生的故障,则只判机床产生了一个故障
GB/T23567.1一2009 4.2故障的计数原则 4.2.1计数原则 4.2.1.1在计算机床的可靠性指标时,只计关联故障
4.2.1.2发生一次关联故障或符合4.1规定的故障应判定为一个故障次数
4.2.1.3停机监测或试验中止、结束时发现的故障,应计人故障数中 4.2.2不计数原则 4.2.2.1非关联故障不计数,但在考核时应作记录
非关联故障包括 安装不当引起的故障; n) b) 误用故障; e)误操作故障, 维修不当引起的故障 d e) 试验装置故障引起的故障; f)试验条件超过设计规定所造成的故障; 其他外界因素引起的故障
g 4.2.2.2按规定程序进行的预防性维修不作为故障计数,包括 a)按说明书规定的易损件的更换或损坏 b)必要的调整和调校
凡是不符合规定程序进行的任何维修和保养,均作为关联故障计数
4.2.2.3在规定考核期截止范围以外的故障不计数
抽样 5.1抽样原则 1.1样机应具有合格的性能和功能,或具有出厂合格证
5. 55 .1.2样机应为新产品或符合正常生产条件下生产的批量产品,并且为近两年内生产的产品
5.1.3样机应是按正常使用工况使用的产品
5.1.4样机试验单位应具有良好的设备管理手段
5 2 抽样数量 根据抽样原则,在产品中随机抽样
抽样数量按表1的规定
表1 试验方式 试验场试验 现场跟踪统计试验 抽样数量 >1台2台 年产量的5%或10台50台 试验方式 试验方案 6. .1.1机床可靠性测定包括试验场试验和现场跟踪统计试验两种方法,两者可任选其一 6.1.2对于新研制的产品应采用试验场试验
6.1.3采用无替换的定时截尾试验方案
6.2试验定时截尾时间 6.2.1采用试验场试验的每台样机累积相关试验时间T>500h 6.2.2采用现场跟踪统计试验的每台样机累积相关试验时间T>2000h
试验条件 7.1预检 7.1.1试验前,按机床使用说明书或技术文件进行检查,确认合格后,方可进行试验
GB/T23567.1一2009 7.1.2试验前,不允许对机床进行任何质量方面的特殊处理
7.2试验环境条件 试验环境条件应符合试验规程的规定
7.3试验场试验工况 7.3.1应尽量模拟机床的实际使用工况,并能充分暴露机床的故障
7.3.2采用加速方法进行试验的工况条件应符合下列要求 采用的加速方法应有明显的加速性 不能改变故障模式和故障机理; 已知加速系数
7.4现场跟踪统计试验工况 7.4.1机床的运行工况应具有代表性,并符合设计或产品说明书的规定
7.4.2选择的观察样机应尽可能在相似的工况条件下
7.5试验样机的预防性维护 试验过程中允许按规定程序进行预防性维护(如必须的更换、调整、润滑等. 试验方法 试验场试验 8.1.1试验内容 机床可靠性试验应至少包括以下内容 空运转试验 加载试验; 静刚度试验; -扭矩和功率加载试验; 典型试件切削试验; 空运转加速试验 安全试验
8.1.2 试验要求 8.1.2.1空运转试验 空运转试验按各类型机床技术条件标准的规定进行
8.1.2.2加载试验 8.1.2.2.1在模拟工作状态下,对机床进行加载试验
8.1.2.2.2试验时,施加的载荷至少超过正常使用的载荷
试验时,分别按规定的低、中,高载荷进行加载
中,高载荷加载的比例至少占50%以上
8 试验时,每次加载的保持时间至少为5min 8 5 每次加载的间隔时间不超过1min 8 2 2. 注,可根据各类机床特点施加相应的载荷 8 2 静刚度试验 8 2.3. 在模拟工作状态下,对机床进行静刚度加载试验
每个方向均应进行静刚度试验 8 2.3. 2 加载力不应超过设计规定的最高载荷
8 每个方向的加载力应分三挡进行加载,并且每挡加载力应重复三次 8.1.2 扭矩和功率加载试验 8.1.2.4.1在模拟工作状态下,在机床低速运转下进行扭矩加载试验;在机床高速运转下进行功率 试验
GB/T23567.1一2009 8.1.2.4.2试验时,施加的载荷至少超过正常使用的载荷
8.1.2.4.3试验时,分别按规定的低、中、高载荷进行加载
中,高载荷加载的比例至少占50%以上
注l:可根据各类机床特点进行相应试验,如磨床可不进行扭矩加载试验
注2;可根据各类机床特点施加相应的载荷
8.1.2.5典型试件切削试验 8.1.2.5.1加工有关标准规定的典型试件或其他试件,可参照企业提供的切削规范或规定的加工要 求,进行试件切削试验,考核机床在加工状态下的可靠性
8.1.2.5.2加工试件的数量由试验方确定
8.1.2.6空运转加速试验 在空运转试验内容基础上,数控程序的设置主轴采用中速和高速运转,并增加部件快速移动和主轴 高速运行的时间,增大冷却液体的喷射量,增加模拟切削运动等
安全试验 8.1.2.7.1安全试验按相关安全标准的规定进行
一般应包括安全防护装置、联锁装置、控制装置、运 动部件,排屑装置等试验
8.1.2.7.2机床动作安全试验的次数应至少20次,功能安全试验应至少10次,其他试验的次数按有 关规定进行
2 8. 现场跟踪统计试验 -般应在机床工作3个月后进行可靠性现场跟踪统计试验
如需跟踪早期故障和正常使用期故 障,可在机床开始工作起进行可靠性现场跟踪统计试验
故障监测 9 每8h检查一次样机的性能,包括噪声,温度和温升,油、气渗漏,部件运转情况等
9. 2 每4h检查工况条件,包括环境温度、相对温度、电源电压等
3 9. 试验场试验每台样机累积250h以及在试验前,试验结束后,检查和记录样机的精度 9 试验过程中一旦发生故障,应立即停机检查
10 数据的采集 10.1试验场试验 10.1.1试验过程中应随时检查机床运行的情况,并做好记录(见附录B)
记录应准确,凡涂改之处应 有记录人的签章并说明理由 10.1.2一旦发生故障,检验人员应根据故障判定原则、计数原则,对故障立即进行记录,并填写“故障 记录表”(见附录C)、“故障分析报告”(见附录D)
10.1.3在试验过程中,达到寿命期限的耗损件和配套件的更换不计故障,但应作记录
10.2现场跟踪试验 10.2.1机床可靠性现场跟踪试验的数据采集点应至少2个3个
10.2.2试验过程中可由试验方或组织用户检查机床运行的情况,并做好记录(见附录B)
记录应准 确,凡涂改之处应有记录人的签章并说明理由
10.2.3由用户进行数据采集时,应对用户进行培训,使用户明确有关定义和含义,掌握故障判定原则 并应向用户提供机床的故障记录表和故障分析报告
10.2.4试验方应定期到用户现场了解情况,并对具体问题予以指导,同时应定期或一次性对用户的记 录和报告进行回收并负责保存
10.2.5一旦发生故障,检验方或用户应根据故障判定原则、计数原则,对故障立即进行记录,并填写 “故障记录表”见附录C)、“故障分析报告”见附录D
GB/T23567.1一2009 10.2.6对于达到寿命期限的耗损件和配套件的更换不计故障,但应作记录
10.2.7若观察期间未发现故障,或中途停止试验,可根据有关方法(如累积故障法等)处理中断数据
11 可靠性评定指标 11.1平均故障间隔时间MTBF(指数分布 注:对于符合其他分布的如威布尔分布,按这些分布的有关要求进行评定 11.1.1 MTBF的点估计 习T e 人 7 习" 式中 -MTBF的点估计值 N 样机数; 7 -评定周期内第j台机床的累积工作时间,单位为小时(h) 评定周期内第j台机床的累积故障数 -可靠性修正系数
如果到定时截尾试验时间,机床没有出现故障,则MTBF的点估计为 m=3T 式中: -MTBF的点估计值 N T -定时截尾试验总试验时间,单位为小时(h)
11.1.2MIB的区间点估计 3 m mC nmC 7u 式中: -MTBF的单侧置信下限, m -MTBF的单侧置信上限, 777u -MF的点估计值(见公式1) m7 C -定时截尾时MTF置信下限系数(见表2) 定时截尾时MTF置信上限系数(见表2) Cu 表2定时截尾计算MIITBF时双侧(或单侧)的置信系数C、C 置信区间 累积 40%双侧 60%双侧 80%双侧 90%双侧 故障 70% 70% 80% 80% 90% 90% 95% 95% 数" 单侧下限 单侧下限 单侧上限 单侧下限 单侧上限 单侧下限 单侧上限 单侧下限 0.41o 2.804 0,334 4.481 0,257 9,491 0.211 19.417 1.803 0.467 0.376 0.317 0.553 2.426 3.761 5.658 0.630 1.568 0.544 1.955 0.449 2.722 0.387 3.659 0.679 1.447 0,595 1.742 0,500 2.293 0,437 2.930 0.714 1.376 0.632 1.618 0.539 2.055 0.476 2.534 0.74o 1.328 0,661 1.537 0,570 1.904 0.507 2.294 0.76o 1.294 0.684 1.479 0.595 1.797 0.534 2.132
GB/T23567.1一2009 表2(续 置 区间 信 累积 40%双侧 60%双侧 80%双侧 90%双侧 故障 70% 70% 80% 80% 90% 90% 95% 95% 数r 单侧下限 单侧上限 单侧下限 单侧上限 单侧下限 单侧上限 单侧下限 单侧下限 0.777 0,616 1.718 0.556 l.267 0.703 l,435 2.008 1.247 0.719 1.657 0.573 0.790 l
400 0.634 1.916 10 0.802 1.230 0.733 1.372 0.649 1.607 0.590 l.842 0.812 1.215 0.744 0.663 1.567 0.603 l.349 1.783 0.755 0.675 o.615 12 0.821 1.203 1.329 1.533 l,733 0.828 0.764 1.312 0.686 1.504 0.627 13 l.193 l.689 0,772 0.835 1.184 .297 0.696 1,478 0.639 1,653 15 1.176 0.780 0.705 .456 0.649 0.84l l.284 l.623 0.847 0.787 1.272 0.713 1.437 0.659 16 1.169 1.597 17 0.852 1.163 0.793 .262 0.720 1.419 0.668 l,597 1.157 0,727 .676 18 0.856 0.799 .253 l.404 l.548 1.152 19 0.861 0.804 .244 0.734 1.390 0.683 l,528 1.147 20 0.864 0.809 .237 0.740 ,377 0.689 l.508 1.115 30 0.891 .185 0.783 0.844 1.291 0.737 1.389 11.2平均修复时间MTR 当 5 MTTR 心 式中 样品数: 评定内第台机床的累积修复时间,单位为小时(h); tR -评定周期内第台机床的累积故障数
12 结果判定 12.1可靠性验证试验 12.1.1当试验进行到规定的试验时间,试验可结束 12.1.2验证试验主要是暴露缺陷,并验证采取措施的有效性
12.1.3根据试验累计时间和故障数计算MTBF和MTTR数值
12.1.4达到规定的指标和要求,可结束试验,判定试验合格;否则应采取措施重新试验,再达不到规定 的指标和要求,则判定试验不合格
12.1.5也可根据协议要求,判定机床可靠性接收或拒收 12.1.6如在试验期间未发生关联故障,则判定机床的可靠性符合要求
12.2可靠性测定试验 12.2.1当试验进行到规定的试验时间,试验可结束
12.2.2根据试验累计时间和故障数计算MTBF和MTTR数值
GB/T23567.1一2009 附 录A 规范性附录 关于可靠性修正系数h A.1可靠性修正系数人见公式A.1
A.1 k八kks 式中 加速系数(与强化条件有关) k 工况系数(与转速、工作期限、功率、环境等有关); kr -寿命系数(与材料,受载等有关)
ks 注:上述系数根据具体情况可全部或部分使用
GB/T23567.1一2009 B 附 录 资料性附录 可靠性试验运行记录 B.1可靠性试验运行记录表见表B.1
表B.1可靠性试验运行记录表 盖章 产品名称 产品型号 出厂编号 制造单位 出厂日期 试验日期 年 月 日 时 至 年 月 日 时 机床运行时间/h 故障停机 恢复使用时 预防性 试验者 日期 班次 开始时间 时间 维修时间 签字 开始 结束 注:每台产品填写一份表格,表可续页
GB/T23567.1一2009 c 附 录 资料性附录 可靠性试验故障记录 C.1可靠性试验故障记录表见表C.1
表C.1可靠性试验故障记录表 产品名称 产品型号 出厂编号 制造单位 出厂日期 年 月 日 至 年 月 日 试验日期 时 时 现场工况 条件 序号 故障发现时间 故障部位 故障现象 采取措施 修复时间 累计工作时间Ah 累计故障数 累计修复时间/h 注:每台产品填写一份表格,表可续页
试验者(签字) 填表人(签字): 试验单位(盖章) 年 月 日 10
GB/T23567.1一2009 D 附 录 资料性附录 故障分析报告 D.1故障分析报告见表D.1
表D.1故障分析报告 产品名称 出厂编号 产品型号 出厂日期 制造单位 发现故障时间 累计工作时间 修复时间 故障现象 故障描述 故障原因 口 设计问题 零件质量问题 动力源问题 口 制造间题 口 误操作 口 松脱 口 口 口 口 装配问题 试验装置问题 损坏 选用不当 渗漏 从属故障 口 口 口 口 超负荷 失效、退化、磨损 其他 故障分类 非关联故障 关联故障 对故障采取的措施 设计更改 口 工艺更改 更换零件 材料更改 调整 填表人:(签字 试验单位;盖章 年 日 月