GB/T25707-2010
液压防爆提升机和提升绞车
Hydraulicdefenceexplosionminehoistsandminewinders
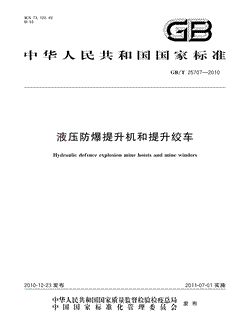
- 中国标准分类号(CCS)D93
- 国际标准分类号(ICS)73.100.40
- 实施日期2011-07-01
- 文件格式PDF
- 文本页数15页
- 文件大小373.30KB
以图片形式预览液压防爆提升机和提升绞车
液压防爆提升机和提升绞车
国家标准 GB/T25707一2010 液压防爆提升机和提升绞车 Hydraulicdefeneeexplosionminehoistsanlminewinders 2010-12-23发布 2011-07-01实施 国家质量监督检验检疫总局 发布 国家标准化管理委员会国家标准
GB/T25707一2010 前 言 本标准的附录A为资料性附录
本标准由机械工业联合会提出 本标准由全国矿山机械标准化技术委员会(SAC/TC88)归口
本标准起草单位:洛阳中重自动化工程有限责任公司、株洲力达液压机械有限责任公司、山西新富 升机器制造有限公司、洛阳矿山机械工程设计研究院有限责任公司
本标准主要起草人:张凤林,李建设,张兰俊、刘大华,左达、张步斌,杨现利
GB/T25707一2010 液压防爆提升机和提升绞车 范围 本标准规定了液压防爆提升机和提升绞车的型式与基本参数、技术要求、试验方法、检验规则、包 装、运输和贮存
本标准适用于在有煤尘、瓦斯等爆炸性气体环境使用的煤矿井下及其他需要防爆的场所作提升、下 放物料和运输人员的液压防爆提升机和提升绞车
规范性引用文件 下列文件中的条款通过本标准的引用而成为本标准的条款
凡是注日期的引用文件.其随后所有 的修改单(不包括勘误的内容)或修订版均不适用于本标准,然而,鼓励根据本标准达成协议的各方研究 是否可使用这些文件的最新版本
凡是不注日期的引用文件,其最新版本适用于本标准
GB/T191包装储运图示标志(GB/T191一2008,ISo780;1997,MOD) GB2894安全标志及其使用导则 GB/T3766液压系统通用技术条件(GB/T3766一2001,eqvIS04413:1998) 2000. (GB38361爆炸性气体环境用电气设备第1部分:通用要求GB3836. IEC60079-0:l998 eqV GB3836.2 爆炸性气体环境用电气设备第2部分:隔爆型“d”GB3836.2一2000, IEC60079-l;1990) eqV GB3836.4爆炸性气体环境用电气设备第4部分:本质安全型“;”GB3836.4一2000. eqvIEC60079-1ll:1999 GB/T4879防锈包装 GB/T7935 液压元件通用技术条件 GB/T8923一1988涂装前钢材表面锈蚀等级和除锈等级 GB/T9969工业产品使用说明书总则 圆柱齿轮精度制第1部分,轮齿同侧齿面偏差的定义和允许值 GB/T10095 GB/T10095.l一2008,ISO1328-l:1995,IDT GB/T10095.2圆柱齿轮精度制第2部分;径向综合偏差与径向跳动的定义和允许值 GB/T10095.22008,Iso1328-2:1997,IDTy GB/T11345一1989钢焊缝手工超声波探伤方法和探伤结果分级 GB/T13306标牌 GB/T13325机器和设备辐射的噪声操作者位置噪声测量的基本准则工程级 (GB/T133251991.neqISO6081:1986) GB/T140392002液压传动油液固体颗粒污染等级代号(ISO4406;1999,MOD) GB/T15706.2机械安全基本概念与设计通则第2部分;技术原则(GB/T15706.2一2007 ISO12100-2;2003,IDT) GB/T16855.1机械安全控制系统有关安全部件第1部分设计通则(GB/T16855.1 2008,ISO13849-1:2006,IDT) GB/T17489液压颗粒污染分析从工作系统管路中提取液样GB/T17489一1998 idtISO4021:l9927
GB/T25707一2010 GB20181矿井提升机和矿用提升绞车安全要求 GB/T20961单绳缠绕式矿井提升机 AQ1043矿用产品安全标志标识 JB/T1581汽轮机、汽轮发电机转子和主轴锻件超声波探伤方法 JB/T3721矿井提升机盘形制动器闸瓦 JB/T3812矿井提升机和矿用绞车盘形制动器用碟形弹簧 JB/T5000.13重型机械通用技术条件第13部分;包装 7888. JTP型矿用提升绞车 JB/T79291999齿轮传动装置清洁度 JB8519矿井提升机和矿用提升绞车盘形制动器 MT113煤矿井下用聚合物制品阻燃抗静电性通用试验方法和判定规则 MT/T776煤矿机械液压系统总成出厂检验规范 《煤矿安全规程)2010年版 型式与基本参数 3.1型式 产品采用隔爆鼠笼式异步电动机带动双向变量液压泵,通过闭式液压回路驱动液压马达旋转,经齿 轮减速器或直接带动卷简旋转
3.2型号标记 口×口口旱口 马 口Y 产品改进序号(用A,B,C表示) -控制方式;电液比例控制为D,液压比例控制省略 传动方式;减速器传动为J,液压马达直接传动为Z -卷筒宽度,单位为m -卷筒直径,单位为m -防爆 液压传动代号 -K为提升机(卷简直径>2m) T为提升绞车(卷筒直径<2m) -卷扬机类 -卷筒个数(单卷筒省略 3.3标记示例 卷筒直径2.5m,卷筒宽度2m,减速器传动,电液比例控制的单卷筒液压防爆提升机标记为
JKYB-2.5×2J(D)液压防爆提升机 b)卷简直径1.6m,卷简宽度1.2m,低速液压马达直接驱动,液压比例控制的双卷简液压防爆 提升绞车标记为 2JTYB-1.6×1.2Z液压防爆提升绞车 o 基本参数 液压防爆提升机和提升绞车的基本参数应优先选用表1中数值
GB/T25707一2010 表1液压防爆提升机和提升绞车基本参数 最大提升高度或斜长 卷筒 钢丝绳 钢丝绳最大直径时) 最大提 升速度 产品型号 -层 二层 三层 最大静最大静 最大 直径 宽度 个 缠绕 缠绕 缠绕 张力张力差 直径 数 kN kN mm m/s JTYB1.2×1 123 275 447 1.0 1.2 30 30 20 2.5 JTYB1.2X 1.2 157 345 553 2JTYB1.2×0.8 0.8 89 206 342 30 20 20 1.2 2.5 2TYB-1.2×1 123 275 447 1.0 TYB1.6×1. ..2 178 385 617 1.6 45 45 24 JTYB1.6×1.5 236 503 796 2YB1. 120 268 6×0.9 0.9 439 45 24 30 2JTYB-1.6×X1 2 1.2 178 385 61n JKYB2×1.5 1.5 255 538 854 2.0 60 60 28 3.5 JKYB2×1.8 1.8 318 666 1047 2JKYB2×! 151 327 532 2.0 60 40 28 3.5 2]KYB2×1.25 1.25 203 432 693 JKYB-2.5×2 2.0 36o 747 1175 JKYB-2.5×2.3 2.5 2.3 423 876 1371 90 90 34 JKYB-2.5×2.5 2.5 466 962 1501 2JKYB2.5×1.2 1.2 190 403 654 2]JKYB-2.5×1.5 1.5 55 34 2.5 253 532 849 90 1177 2JKYB2.5×2 2.0 360 747 JKYB3×2.2 2.2 41 848 1334 40 JKYB3×2.5 3.0 2.5 477 981 1536 120 120 4.5 JKYB3×2.8 2.8 542 1114 1737 538 863 2]JKYB3×1.5 1.5 257 2]JKYB3×1.8 3.0 323 671 1065 120 80 40 4.5 2]KYB3×2 2.0 367 760 1199 1629 JKYB3.5×2.5 2.5 507 1040 JKYB3.5×2.8 3.5 57? 1182 1844 150 150 2.8 44 JKYB3.5×3 3.0 624 276 1987 2JKYB3.5×1.7 320 661 1055 4!4 2JKYB3.5×2.1 3.5 2.1 413 851 1342 150 100 2JKYB3.5×2.5 507 1040 1629
GB/T25707一2010 表1(续 最大提升高度或斜长 卷简筒 钢丝绳 钢丝绳最大直径时 最大提 升速度 产品型号 -层 二层 三层 最大静最大静 最大 直径 宽度 缠绕 缠绕 缠绕 张力张力差 直径 数 kN kN mm m/sS JKYB4×3 3.0 655 1336 2081 48 180 180 4.0 778 JKYB4×3.5 3.5 1585 2458 2]KYB" 3-4×2.1 2.1 433 888 1403 4.0 48 180 120 2JKYB-4×2.5 532 1087 1704 注:提升高度的计算公式参见附录A
技术要求 工作条件 产品工作时,环境空气中的瓦斯、煤尘等不应超过《煤矿安全规程》中所规定的浓度
4.1.2环境温度;机房5C一40C,酮室5一30C;环境空气相对湿度不大于85%(20C士5C 时. 4.1.3海拔高度不超过1000m
对于海拔高度超过1000m的使用场合,需要考虑到空气冷却作用 和介电强度的下降,选用的电气设备应根据制造厂和用户的协议进行设计和使用
4.1.4操作位置的照度不应低于100lx
4.2基本要求 4.2.1产品主要技术参数和技术要求应符合本标准的规定,且适应于提升系统运行要求,并按照经规 定程序批准的图样及技术文件制造、安装和使用
.2.2产品应符合《煤矿安全规程》和GB20181的有关规定
4. 4.2.3产品的电气设备应符合GB3836.1,GB3836.2和GB3836.4的有关规定,且应经国家授权的 防爆检验机构进行防爆检验,并取得矿用产品安全标志证书
4.2.4选用的非金属材料应符合MT113的规定 4.2.5液压元件应符合GB/T7935的有关规定
4.2.6液压系统应符合GB/T3766的有关规定 4.2.7外购配套件应有合格证、使用说明书;属安全标志管理的产品应具备有效的矿用产品安全标志 证书
4.2.8 所用材料均应附有质量保证书,必要时应进行化验或鉴别,确认合格后方可使用 4.2.9锐边、尖角和凸出部分的设计应符合GB/T15706.2的规定
4.2.10产品的控制系统安全部分应符合GB/T16855.1的要求
产品的通用件、易损件、备用件应保证质量与互换性
42m 42.12产品所有的原材料、标准件,外购件均应符合现行有关国家标准或行业标准的规定 4.2.13本标准未规定的机械加工和装配等技术要求,均应符合现行有关国家标准或行业标准的规定 4.2.14产品各部件应有便于起吊和安装的起吊悬挂装置
43整机性能要求 43.1产品启动、运行、换向和停车应平稳、可靠,无冲击振动和异常声响,液压系统无渗漏现象
产品应具有远距离液控(或电控)操纵和无级调速的性能
4. .3. 2 3 4.3
操纵台位置处的噪声,其声压级不应大于88dBA
GB/T25707一2010 4.3.4产品在空负荷试验、负荷试验和超负荷试验中应运转平稳、可靠,无爬行和异常响声
各轴承处 温升不应超过40C,最高温度不应超过75C
各部温升及液压,润滑系统压力应正常
43.5钢丝绳安全系数、卷简直径与钢丝绳直径之比,卷筒直径与钢丝绳中最粗钢丝的直径之比、卷简 上的钢丝绳缠绕层数提升容器的最大速度和最大加、减速度应符合《煤矿安全规程》的相关规定
外观质量 4.4.1产品涂漆前,钢制件的表面除锈质量应符合GB/T8923一1988中St2级的规定
4.4.2涂漆层的外观不允许有气泡、裂纹、脱落、流挂及漏涂等影响美观的缺陷
安全保护 4. .5 4.5.1产品外露回转部位应设防护装置
4.5.2产品应设置过卷,过速、过负荷,欠电压、限速(速度超过3m/s),减速、零位联锁,超油压、深度 指示器失效,闸间隙,弹簧疲劳、松绳报警和紧急制动等安全保护装置及紧急制动停车开关,安全保护要 求应符合《煤矿安全规程》和GB20181的有关规定
4.5.3 防止过卷装置、防止过速装置、限速装置和减速功能保护装置应设置为相互独立的双线型式可 与井简相应位置发讯装置配合 4.5.4产品应设置主电机及辅助电机的启动和停止、调绳离合器的离合等机械或电气联锁机构
4.5.5高压系统用软管应标明许用压力;在操作位置附近的高压软管应安装护罩
4.5.6产品应设置总停开关
4.5.7 动力供给中断或中断后重新供给,只能通过手工操纵才能重新启动;当动力供给故障或液压系 统压力下降时,应有保护措施,以免发生危险
保护装置和防护措施应保障有效
4.5.8产品应加设定车装置
主轴装置 主轴装置的制造装配要求应符合GB20181,GB/T20961和JB/T7888,1的有关规定
主轴应 采用锻件
主轴应进行超声波探伤检验,内部不允许有白点和裂纹,其夹渣和非裂纹性缺陷要求如下 4.6.2 在主轴轴心2/3直径范围内的单个,"零尾,分散性缺陷和密集性缺陷,应符合表2的规定; 表2主轴缺陷限定值 允许存在的单个、 允许存在的 被探截面直径 分散性缺陷 密集性缺陷 零件 起始灵敏度 名称 mm 最大当量直径 最大当量直径/占截面总面积 mm 个数/100cm % mm mm <400 6 10 4 主轴 3 >400 8 10 6 b 在主轴轴心2/3直径以外范围,允许存在不大于5mm的当量单个,分散性缺陷6个;允许存 在小于4mm的当量密集性缺陷,但缺陷区面积不应超过被探面积的5%
4.6.3卷简的主要焊缝均应进行超声波探伤检验,内在质量应达到GB/T11345一1989中级焊缝规 定
焊后应进行整体退火或去应力处理
4.6.4钢丝绳绳头固定在卷简上,应有特备的容绳或卡绳装置,不应系在卷筒轴上;出绳孔应光滑,不 应有锐利的边缘;钢丝绳的弯曲不应形成锐角
4.6.5卷筒挡绳板外缘高出钢丝绳最外缠绕层的高度不应小于钢丝绳直径的2.5倍;卷筒上应设有带 绳槽的衬板
4.6.6卷筒上缠绕层数达到两层及两层以上时,钢丝绳层间过渡区应设置层间过渡块
4.6.7装配后卷简外圆径向跳动量及制动盘端面全跳动量应符合表3的规定
GB/T25707一2010 表3卷筒跳动量 直径/m 项 2一3.5 >3.5 卷简径向全跳动量/mmm <4.0 <5.o 7.0 制动盘端面全跳动量/mm 0.4 4.6.8制动盘表面不应有影响使用性能的缺陷;制动盘表面粗糙度参数Ra的最大允许值为3.2" 技m
4.6.9主轴左端部明显位置处应打上主轴编号
盘形制动器 盘形制动器应动作灵敏、制动平稳、安全可靠,性能应符合JB8519的有关规定
盘形制动器应设置闸间隙和弹簧疲劳保护装置
盘形制动器活塞和闸瓦在设计油压下应同时动作,不应有爬行、卡住现象
在无负荷条件下,盘形制动器活塞最低动作压力不应超过0.3MPa 盘形制动器碟形弹簧应符合JB/T3812的规定
盘形制动器闸瓦应符合JB/T3721的规定
制动闸瓦应采用符合设计要求的材料,与制动盘的设计摩擦系数应根据实测确定,不应低于 7.6.2制动闸瓦不允许有影响使用性能的龟裂,起泡,分层等缺陷
制动闸瓦不应拉毛或刮伤试验盘
制动闸瓦在摩擦试验时,不应发生有焰燃烧和无焰燃烧现象
盘形制动器应装设排气装置
盘形制动器在1.25倍设计压力下保持10min,各密封处不应有渗漏油现象
4.8制动性能 工作制动和安全制动在制动状态时,所产生的制动力矩与实际提升最大静荷重旋转力矩之比均 4.8.1 不应小于3
在调整双卷筒旋转相对位置时,制动器在制动盘上所产生的制动力矩,不应小于该卷简所 悬重量(钢丝绳重量与提升容器重量之和)形成的旋转力矩的1.2倍
4.8.2安全制动时的制动减速度应符合表4的规定
自然减速度按公式(1)进行计算
表4安全制动减速度 单位为米每二次方秒 倾角0 运行状态 0<15” 15"030" 0>30” 上提重载 下放重载 >0.75 >0.3A
>1.5 A
= g(sin0十fcos0) 式中: 自然减速度,单位为米每二次方秒m/s 重力加速度,单位为米每二次方秒m/s; -井巷倾角,单位为("); -绳端载荷的运行阻力系数,一般取0.0100.015
4.8.3产品应具备不离开座位即能操纵的工作制动(常用闸)和安全制动(保险闸)两种功能,且彼此能 各自独立而可靠地实施
安全制动除操作者操作外,还应能自动制动,并在自动制动的同时断开电源
4.8.4盘形制动器安全制动空行程时间不大于0.3s
保险闸施闸时,闸瓦不应发生显著的弹性摆动 4.8.5工作闸和安全闸共用一套闸瓦时,其操纵和控制机构必须分开
GB/T25707一2010 4.8.6松闸和制动操纵机构与提升机操纵机构之间应设置联锁装置
4.8.7双卷筒的每个卷筒应有其各自独立的安全闸,两套安全闸的控制回路应能独立控制,而在正常 提升时能同步动作
4.8.8产品安全制动应安全可靠
应具有可调二级制动功能,即第一级制动油压和作用时间可根据需 要调整
4.8.9盘形制动器闸瓦与制动盘的接触面积不应小于60%
4.8.10制动器松闸时,闸瓦与制动盘单侧间隙不应大于2mm 4.8.11制动盘工作面不应有影响摩擦系数的介质(如油、水等)
深度指示器 4.9.1深度指示器应能准确地指示出提升容器在井筒中的位置,指示应清晰,并能迅速而准确地发出 减速,停车及过卷等对应的控制信号和报警信号 492 机械式深度指示器所指示的提升容器实际位置误差应满足容器停车要求,在运转中应灵活,平 稳,不应有卡阻和振动现象
减速、限速及过卷装置应动作灵活、可靠,并能及时、准确复位
4.9. 3 数字式深度指示器的显示精度应为cm级
数字式深度指示器应有位置校正和判断显示数据 正确的措施,信号应由可编程序控制器(PLC)或微机直接发出
.10操纵台 又 4.10.1操作手柄在全行程范围内操纵灵活、零位定位准确、可靠
4.10.2操作手柄操作力不应大于50N
10.3操作台应设紧急制动按钮
紧急制动按钮应醒目,方便
4.10.4操纵台在机房内的安装位置,应能保证司机可清晰地观察到深度指示器指示标记及提升钢丝绳
操作油缸装置应便于调节,活塞运动灵活
减速器和减速器润滑系统 减速器渐开线齿轮制造精度,应符合GB/T10095.1和GB/T10095.2的有关规定
减速器主要零部件应作磁粉和超声波探伤检验,不应有影响机械性能的白点、疏松、裂纹等缺陷 减速器应运转平稳,不应有周期性冲击及不正常噪声
减速器各密封处和结合面处不应有渗油现象
减速器润滑系统油液过滤精度应不低于25m
减速器清洁度应符合JB/T79291999中J级要求
减速器轴承温升不应超过40C,最高不应超过75C
4-11.8减速器集中润滑系统耐压试验压力为1.5p保压5min,系统各处不应有永水久变形及漏油、渗 油现象
4.12 液压系统 4.12.1液压控制系统应安全可靠,无级调速、启动换向平稳、监测仪表齐全,操作手柄应设置零位联锁 保护装置
4.12.2液压系统(包括主回路、辅助回路,调绳回路)在表5规定的压力下进行耐压试验
保压5min. 系统各处不应有永久变形及漏油、渗油现象
表5试验压力 系统工作压力p/MP 压力p/MPa <16 16<25 25
GB/T25707一2010 4.12.4液压系统在正常工作时.油温温升不应超过34C,最高油温不应超过70C
4.12.5液压油运动黏度为40mm'/s110nmm/s(油温40C时. 4.12.6液压系统的清洁度,不应低于GB/T14039一2002中的一/18/15级规定
4.13调绳性能 4.13.1调绳离合器在工作压力下应动作灵活、离合自如、动作可靠
4.13.2调绳离合器进行耐压试验时,各密封处和管路系统不应有渗油现象
4.13.3在调绳时,活动卷筒的盘形制动器应处于安全制动状态,固定卷简的盘形制动器应仍能正常 操作 4.14电控系统 .14.1电控系统主电路应选用有矿用产品安全标志的隔爆型电气元件,如;电机、电磁启动器、电磁阀 和本安电源(控制电源) 4.14.2本安回路及其电气配套件应符合GB3836.1和GB3836.4的有关规定
本安回路的关联设 备应通过有资质的防爆检验站所进行的关联试验
4.15标志 4.15.1产品应按图样规定在明显位置固定产品标牌和煤矿矿用产品安全标志牌
4.15.2产品标牌的型式和尺寸应符合GB/T13306的规定;矿用产品安全标志标识的型式和尺寸应 符合AQ1043的有关规定
4.15.3标牌的内容如下: a) 制造厂名称及地址; D 产品名称及型号 c)主要技术参数; 产品执行标准编号; d 制造日期与出厂编号; e “MA”标志和矿用产品安全标志编号 f 在产品安装场所有潜在危险存在时,应设置安全警告标志
安全警告标志应符合GB2894的 4.15.4 规定 4.15.5标牌应采用铜或不锈钢材质制作
16 产品使用说明书 16.1产品使用说明书应包括机械、液压和电气几方面内容,其编写应符合GB/T9969的有关规定
16.2产品使用说明书应包括如下内容 品名称、主要用途及适用范围 产 a) b) 产品的工作条件和环境要求; 产品特点 产品型号、规格和主要技术参数 产品结构特征及工作原理,结构示意图(包括总图,主要部件结构图、液压原理图电气原理图、 气接线图、备件和易损件清单等); 电 系统说明(机械传动系统,液压系统、润滑系统电气控制系统及其他系统) 安装与调试方法 h)使用与操作方法; 维护与保养方法; 常见故障分析及排除方法 k)安全保护装置及事故处理方法; l 外形尺寸及质量
GB/T25707一2010 4.16.3使用说明书还应以醒目的方式给出使用与维护中预防危险的特别说明和安全警示语
4.17产品成套供货范围 4.17.1产品成套供货范围包括全套机械、液压和电气设备、一次性随机备件及专用工具
4.17.2随机供应的图样和技术文件 a)成套发货表及装箱清单以及备件目录等; b 产品合格证; 煤矿矿用产品安全标志证书复印件 d)使用说明书 总图; e 基础图 f 主轴装置装配图; g h)主要电气配套件使用说明书
试验方法 5.1产品试验应在额定电压下进行(极限偏差为额定电压的士5%)
5.2主轴内部缺陷超声波探伤检验应按照JB/T1581规定的方法进行
5.3卷筒的主要焊缝超声波探伤检验应按照GB/T11345规定的方法进行 5.4卷简和制动盘形位公差测量;在空转试验时,用划针盘和钢尺测量卷简径向圆跳动,用百分表测量 制动盘端面全跳动
5.5盘形制动器按JB8519有关规定进行试验
5.6操作性能试验 5.6.1在运转过程中,扳动操作手柄进行提升、下放各3次以上,根据手感,观察操作手把是否灵敏、 可靠 5.6.2手柄操作力测定试验;应用精度不低于2级的测力仪器测定手把操纵力
测定时测力仪器应与 操纵杆保持垂直
5.7液压系统试验 5.7.1液压系统耐压试验和密封试验按MT/T776的有关规定进行
液压系统油液清洁度检测按GB/T17489和MT/T776有关规定进行
5.7.2 减速器出厂空负荷试验 8.1减速器应在额定转速和空负荷下进行正反向各2h的运转试验
5 5 .8.2减速器清洁度测定应按JB/T7929的有关规定执行,用sSw0.063/0.045滤网,采用过滤烘干 称重法测定,天平的误差不应大于5mg
制动性能试验 5.9.1盘形制动器灵敏、可靠性试验应在额定负荷工况下,连续进行开、合闸试验
5.9.2最大制动力矩测定应用精度不低于2级的测量装置进行测定
每套盘形制动器应单独测定 5.9.3盘形制动器接触面积测定应用游标卡尺等仪器设备测量盘形制动器接触斑点的长度,计算接触 面积
5.9.4盘形制动器空行程时间测定应用精度不低于士1/100s的测试仪器进行测定
5.10制动闸瓦试验 5.10.1制动闸瓦阻燃抗静电性能试验应按MT113的有关规定执行;摩擦试验采用专用摩擦火花测 试装置进行测定
5.10.2制动闸瓦与制动盘的摩擦系数应按JB/T3721的规定检测
GB/T25707一2010 5.11安全保护装置试验 5.11.1卷筒挡绳板外缘高出钢丝绳最外缠绕层的高度为钢丝绳直径倍数的检查,测量挡绳板外缘高 出最外1层钢丝绳的高度,取其平均值并除以钢丝绳直径
5.11.2过卷保护性能试验应使提升机和提升绞车以很慢速度开过过卷位置,观察过卷保护装置是否 动作并报警
5.11.3过速保护性能试验可采用模拟设置的方法进行;调低提升机和提升绞车速度保护值,在运行状 态下观察超速保护装置是否动作并报警
.11.4减速(限速)点未减速(限速)保护性能试验应开动提升机和提升绞车进行提升或下放,并使绳 o 速大于2m/s,强制动作减速(限速)保护开关,观察减速(限速)保护装置是否动作并报警
5. 11.5零位联锁保护性能试验;在主电机停止工况下,推动操作手柄离开零位,启动辅助泵电机,观察 能否起动辅助泵电机
5. .11.6过负荷保护试验:人为使主回路压力过负荷,观察液压系统超油压保护装置是否动作
5.11.7欠电压保护试验:人为调低电磁启动器输人电压,观察电磁启动器的联锁保护动作 5. ..11.8闸间隙和弹簧疲劳保护试验;人为接通闸间隙或弹簧疲劳保护开关,观察报警装置是否报警 5.11.9松绳报警试验:人为动作松绳保护装置,观察报警装置是否报警
5.11.10深度指示器失效保护试验:人为发出深度指示器失效信号,观察保护装置是否动作并报警
紧急制动停车开关灵敏可靠性试验,应在开动辅泵和主泵后,操作紧急制动开关,应能切断电 5.11.11 源,使主暴停机
然后,开动提升机,在额定工况下进行提升和下放,再操作紧忽制动开关,应能切断电 源,盘形制动器抱闸、停机
课绳离合器试验 5.12 5.12.1调绳离合器系统按表5规定的要求进行耐压试验,保持10min. 5.12.2闸住活动卷筒,在不同位置平稳脱开和闭合离合器 5.13空运转试验 不挂钢丝绳和容器,使提升机以额定转速正、反向各运转30min,在空运转过程中,观察各部动作、 响声,振动,温度、渗漏等
负荷试验 5.14 试验方法;试验时,挂上钢丝绳和容器,在额定转速下,按额定负荷的25%、50%,75%各运转 5. 1h,满载连续运转不少于2h(双卷筒提升机当有载容器运转1h以后,将载荷换装给空容器再运转 h)
满负荷试验前,应全面检查各部件
4.2最大静拉力、静拉力差测定应将精度不低于2级的测力装置连接在钢丝绳与卷筒相切处进行 5 测量
5 14.3操纵台位置噪声测定应按GB/T13325的规定执行;用精度不低于士1dB(A)的测量仪器进行 测定
5.14 最大提升速度测定应用精度不低于2级的测速装置进行测量
测量时应将操作手柄放至最大 速度位置
5.14.5温度测定应在试验前和试验后3nmin内,用精度不低于士0.5%测温仪器进行测定
试验前和 试验后油池的温度差即为油箱温升
5.14.6紧急制动减速度测定应用精度不低于2级的测速装置进行测量
先测最大速度,再操作紧急 制动停车开关进行制动,测量紧急制动时的总时间和空行程时间,将最大速度除以总时间和空行程时间 之差即为紧急制动减速度
5. .15超负荷试验 超负荷试验应在满负荷试验合格后进行,试验负荷为额定负荷的110%,进行提升和下放,并检查 各部位
10
GB/T25707一2010 检验规则 6.1检验分类 产品试验分为型式检验和出厂检验
6.2出厂检验 6.2.1所有产品应经制造厂检验部门检验合格,并附产品合格证后方可出厂
6.2.2若检验项目有一项不合格,则认为被检产品不合格
6.2.3出厂检验项目见表6
6.3型式检验 6.3.1凡属下列情况之一者,应进行型式检验 a)新产品试制定型鉴定或老产品转厂生产时 b正式生产后,产品结构、材料、工艺有较大改变,可能影响产品性能时 正常生产后的定期检验 c d)长期停产后恢复生产时 出厂检验结果与上次型式检验有较大差异时; 8 国家质量监督检验机构或国家安全监察部门提出型式检验要求时
f 6.3.2型式检验抽样在出厂检验合格的提升机中随机抽取一台
6.3.3若检验项目有一项不合格,则认为被检验产品不合格
6.3.4进行动作检验时,动作次数不应少于3次
6.3.5型式检验项目见表6
表6检验项目 检验类别 序号 检验项目 检验要求 检验方法 出厂检验 型式检验 超声波检验 4.6.2、4.6.3 5.2、5.3 外观质量 目测 4.4 主轴装置 5,4 4.6 5.5 盘形制动器 操纵性能 4.1o 5.6 4.12.14.12.4 5.7.1 液压系统 4.12.6 5.7.2 减速器出厂空负荷 4.11.3、4.11.6 跑合试验 减速器润滑系统 4.l1.8 5.7.1 制动性能 4.8 5.9 制动闸瓦摩擦性能试验 10 4.7.6 5.10 深度指示器系统 目测 12 安全保护装置 4.5 5.11 13 调绳性能 4.13 5.12 14 4.3.1、4.3.4 5.13 空负荷试验 15 负荷试验 4.3.14.3.4 5.14
GB/T25707一2010 表6(续 检验类别 序号 检验项目 检验要求 检验方法 出厂检验 型式检验 16 4.3.14.3.4 5.15 超负荷试验 注1:序号1项目,可检查制造过程检验记录、探伤报告、合格证
注2序号7项目,无减速器的无此项 注3:序号8项目,无减速器和减速器无集中润滑装置无此项
注4:序号13项目,单卷简无此项
注5 “么”表示必检项目;“”表示不检项目 包装、运输和贮存 7.1产品包装应符合JB/T5000.13的规定,包装文字和标志应符合GB/T191的规定
7.2产品外露加工表面应进行防锈处理,并符合GB/T4879的规定
7.3产品的包装应符合陆路或水路运输要求
7.4产品在运输过程中应防止碰撞损坏 7.5产品不应露天存放,不应接触腐蚀性物品及热源 7.6产品每存放一年应进行一次养护
12
GB/T25707一2010 附录A 资料性附录 提升高度或斜长计算公式 提升高度或斜长的计算公式如表A.1所示
表A.1提升高度或斜长计算公式 单位为米 项 目 说 明 计算公式 H 提升高度; B一0.5dl一b 卷筒直径 D -层 H -")D-L Dp一钢丝绳平均缠绕直径; B 卷筒宽度 2B一(2一0.5)d一20 钢丝绳直径; H 二层 是]D, nm十川 出绳孔中心至滚筒挡绳板内侧的 距离=台+20r BB二3-O.5)d二3 三层 ]D, H nm十川 -多层缠绕供移动用的绳圈,n=4; -摩擦绳圈,n =3; 7Im 缠绕层数; 平均缠绕 V/=干e D,=D十 试验绳长度L.=30mr 直径 绳间间隙[=2mm一3mm 13