GB/T14515-2019
单、双面挠性印制板分规范
Sectionalspecificationforsingleanddoublesidedflexibleprintedboard
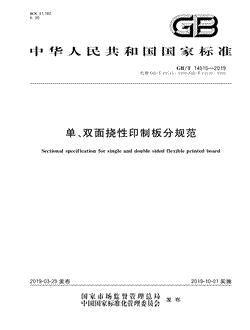
- 中国标准分类号(CCS)L30
- 国际标准分类号(ICS)31.180
- 实施日期2019-10-01
- 文件格式PDF
- 文本页数49页
- 文件大小4.61M
以图片形式预览单、双面挠性印制板分规范
单、双面挠性印制板分规范
GB/T14515一2019 单位为毫米 37.24 0.05
36.4 35.6CO.IX356 0.02 ACF连接端部位 a 4.8 0.15 05 0.3 11.4 0.3UNE 印制插头部位 QFP连接端子部位 图27 节距的累计公差示意图 4.6.7孔中心距 孔中心距应符合表33要求
表33孔中心距公差 等级 孔中心距 公差 <100mm 士0,30mm 1级.2级 士0.3% el00mm 3级 应符合供需双方的协商 导线到板边缘最小距离 4.6.8 导体到印制板边缘的最小距离应符合表34的要求
表34导线到板边缘最小距离 等级 导线到板边缘最小距离 l级2级 导线到板边缘最小距离应不小于0.5mm 应符合供需双方的协商 3级 4.6.9位置公差 4.6.9.1孔位的公差 成品的孔位相对于基准图形或基准孔的公差,当涉及设计尺寸小于100mm时,公差土0.3mm,大 20
国家标准 GB/T14515一2019 代替GB/T14515一1993,GB/T145161993 单、双面挠性印制板分规范 speeifieationforsingleanddoublesidellexibleprinted Sectional b0ard 2019-03-25发布 2019-10-01实施 国家市场监督管理总局 发布 币国国家标准化管理委员会国家标准
GB/14515一2019 目 次 前言 范围 规范性引用文件 2 3 应用等级 要求 4.1通则 .2优先顺序 4.s 材料 设计 4.4 4.5外观要求及检验方法 4.5.1检验方法 4.5.2导线外观 4.5.3覆盖层及覆盖涂层外观 4.5.4镀层外观 4.5.5外形边缘和冲切孔的外观 12 4.5.增强材料的外观 13 4.5.7其他 14 4.6尺寸检验方法和要求 18 4.6.1检验方法 18 46.2外形尺寸 18 ..3厚度 18 4.6.4孔 18 4.6.5导线宽度 19 4.6.6导体节距的累积公差 19 孔中心距 4.6.7 20 4.6.8导线到板边缘最小距离 20 4.6.9 位置公差 220 4.6.10板与增强材料对压敏胶或热固粘接剂的偏移(包括粘接剂的溢出 22 4.6.11镀覆孔的镀铜层最小厚度 2 2: 4.7物理性能及检验方法 4.7.1剥离强度及检验方法 22 4.7.2拉脱强度及检验方法 228 4.7.3镀层附着力及检验方法 24 4.7.4 可焊性及检验方法 24 4.7.5耐挠曲性及检验方法 24 4.7.6耐折性及检验方法 24 25 4.8化学性能及检验方法
GB/T14515一2019 25 4.8.1化学性能检验方法 4.8.2化学性能要求 25 4.9电性能及检验方法 225 4.9.1 电性能检验方法 25 2 4.9.2电性能要求 8 4.10环境性能及检验方法 26 4.10.1环境性能检验方法 26 4.10.2环境性能要求 27 4.11清洁度及检验方法 27 4.l1.1清洁度检验方法 27 4.11.2清洁度要求 27 4.12阻燃性及检验方法 27 4.12.1阻燃性检验方法 27 4.12.2阻燃性检验要求 5 27 质量保证规定 5.1通则 27 5.2质量评定 27 5.3检验条件 28 5.4能力批准 28 .5整定批准 29 5.5.1通则 29 5.5.2样本大小 29 5.5.3检验程序 29 5.5,4不合格 30 5.5.5不合格处理 30 5.5.6鉴定资格的保持 30 5.6质量一致性检验 30 5.6.1通则 30 5.6.2逐批检验 30 5.6.3周期检验 32 交付要求 33 6.1包装要求 33 6.2运输及装卸 34 6.3储存 34 6.4使用 34 附录A规范性附录温度循环试验方法 35 37 附录B规范性附录离子迁移试验方法 39 附录c规范性附录晶须检测试验方法 附录D(规范性附录综合测试图形与尺寸 4 附录E资料性附录聚酰亚胺基挠性印制板使用说明
GB/14515一2019 前 言 本标准按照GB/T1.1一2009给出的规则起草
本标准代替GB/T14515一1993《有贯穿连接的单、双面挠性印制板技术条件》和GB/T14516 1993《无贯穿连接的单,双面挠性印制板技术条件》
与GB/T14515一1993和GB/T14516一1993相 比,主要技术变化如下 修改了范围一章的内容(见第1章,GB/T14515一1993和GB/T14516一1993的第1章); -增加了印制板应用等级(见第3章 增加了优先顺序(见4.2); 增加了印制板材料可重复、可回收或环保材料的要求(见4.3); -增加了设计的要求见4.4) 增加了导体节距的累积公差见4.6.6); -增加了覆盖层或覆盖涂层的重合度(见表35) -增加了镀覆孔的镀铜层最小厚度见表38); 增加了质量保证规定(见第5章); 增加了交付要求(见第6章) 请注意本文件的某些内容可能涉及专利
本文件的发布机构不承担识别这些专利的责任 本标准由全国印制电路标准化技术委员会(sAc/Tc47)归口
本标准起草单位;福建闽威电路板实业有限公司、珠海元盛电子科技股份有限公司
本标准主要起草人;朱民,何波
本标准所代替标准的历次版本发布情况为 GB/T14515一1993; GB/T145161993
GB/T14515一2019 单、双面挠性印制板分规范 范围 本标准规定了单,双面挠性印制板(以下简称挠性印制板或FPC)的应用等级、性能要求,质量保证 规定、交付规定等
本标准适用于使用了单、双面聚酯薄膜或聚酰亚胶薄膜覆铜箱层压板(包括无粘接剂型)的挠性印 制板
规范性引用文件 下列文件对于本文件的应用是必不可少的
凡是注日期的引用文件,仅注日期的版本适用于本文 件
凡是不注日期的引用文件,其最新版本(包括所有的修改单)适用于本文件
GB/T2423.17一2008电工电子产品环境试验第2部分;试验方法试验Ka;盐雾 GB/T4677一2002印制板测试方法 GB/T13555挠性印制电路用聚酰亚胺薄膜覆铜板 GB/T13556挠性印制电路用聚酯薄膜覆铜板 GB/T13557一2017印制电路用挠性覆铜箱材料试验方法 GB/T16261一2017印制板总规范 合格鉴定用测试图形和布设总图 S20828 应用等级 本标准规定的产晶分为三个应用等级
顾客有责任在其合同或采购文件中规定每种产品的等级要 求,必要时应指出特定参数的例外要求
具体分级如下 a 1级;一般电子产品 对外观要求较低而主要要求印制板有完整的功能的产品,包括消费类产品、某些计算机及其外 部设备
2级;耐用电子产品 b 要求高性能、较长使用寿命以及不间断工作的非关键性设备用产品,包括通讯设备,复杂的商 用机器、仪器
3级;高可靠性电子产品 持续工作于严酷环境的、不能停机的或用于生命维持系统的、需要时可以随时工作的关键性设 备用产品,其对加工印制板使用的材料、工艺、检验和试验都有更高的要求
要求 4.1通则 除另有规定外,单,双面挠性印制板应符合本标准规定的特定性能等级的所有要求
GB/T14515一2019 4.2优先顺序 当本标准的要求与其他文件要求有矛盾时,文件采用的优先顺序如下 a 印制板采购文件; b 适用的印制板分规范; c 印制板总规范 d 其他文件 4.3材料 按本标准提供的印制板所使用的材料应符合GB/T13555,GB/T13556等材料规范和印制板采购 文件的规定,承制方应使用符合本标准规定的性能要求的材料
在满足印制板性能要求条件下,应最大程度采用可重复利用、可回收或环保型材料,以有助于清洁 生产和降低整个产品生命周期的成本
4.4设计 印制板应符合相关设计规范的要求
除非另有规定,如果印制板采购文件中对个别设计参数没有 作出规定,那么印制板的设计、测试图形的设计、数量、位置和用途应按照s20828的规定,并反映印制 板设计的最薄弱的环节
4.5外观要求及检验方法 4.5.1检验方法 外观应在常态条件下,使用4.5/4.5的正常或娇正视力及3倍~10倍的放大镜进行目检(仲裁检验 用10倍的放大镜
4.5.2导线外观 4.5.2.1开路或短路 挠性印制板不应有开路或短路
4.5.2.2导体缺损 4.5.2.2.1导线缺口或针孔 导线应符合以下要求: 宽度为w的导线上所允许的缺口或针孔如图1所示,其缺损的宽度(w)及长度()应符合 a 表1的要求
表1允许的缺口和针孔 等级 缺口或针孔 w
GB/T14515一2019 表2允许的导线间的残留铜或突出部分 导线间的残留铜或突出部分 等级 1级、2级 (S十S)或S1>S/2 +S,)或s>2s/3 3级 S,十 4.5.2.2.3宽阔区域内的残留铜或突出 宽阔区域是指导体图形周围的0.375mm范围内不进行布线的区域,如图5所示
在此区域内的残留铜或突出部分距印制板外缘的距离(c)应不小于0.125mm;在此区域内的残留 铜或突出部分与相邻导体图形的距离(d)应不小于0.125n mm
残铜 突出 b 图5在宽阔空间处的残留铜或突出 4.5.2.2.4凹坑 厚度为!的导线表面因腐蚀所产生的凹坑如图6所示,其深度(e)应符合表3的要求
凹坑不允许 横跨导线宽度
不可接受 可接受 可接受 可接受 可接受的凹坑 b 不可接受的凹坑 图6凹坑 表3凹坑 等级 导线表面的凹坑深度 1级.2级 3级 5 4.5.2.2.5分层 导体宽度(W)的分层如图7所示,宽度(w)及长度()应符合表4的要求
GB/14515一2019 图7分层 表4允许的分层 等级 导体分层 有覆盖层保护时 动态弯曲部位:不允许有分层现象 其他部位:lw及w
GB/14515一2019 印制插头部位 导体部位 图10夹杂 表8非导电性夹杂允许值 单位为毫米 等级 厚度 宽度w 长度1 W<0.3 1级 !0.1 l3 w<0.2 l2 2级 10.05 ws0.05 3级 10.05 <1时不应有横跨三根导体的异物 4.5.3.3分层及剥离 沿印制板四周边缘不应有目视可见的覆盖层或覆盖涂层的分层或剥离,如图11所示
分层 剥窝 图11覆盖(涂)层的分层及剥离 4.5.3.4覆盖层粘接剂的溢出、覆盖涂层或感光性阻焊剂的渗出 渗出的具体要求如下: 覆盖层粘接剂的溢出、覆盖涂层或光性阻焊剂渗出如图12b)所示的尺寸()应符合表9要求
a b 在连接盘部位覆盖层的偏移及孔的偏移应能保证连接盘最小可焊环宽(W)如图12a)所示,且 符合表10的要求
GB/T14515一2019 连接盘部位 印制板插头部位 a b 图12覆盖层粘接剂的溢出、覆盖涂层及感光性阻焊剂的渗出 表9覆盖层粘接剂溢出、覆盖涂层及感光性阻焊剂的渗出 单位为毫米 等级 覆盖层粘接剂的溢出及覆盖涂层的渗出 渗出 1级,2级 <0.3 3级 <0.2 /<0. 表10连接盘的最小可焊环宽 单位为毫米 等级 最小可焊环宽 1级 粘接剂的溢出及覆盖涂层的渗出允许至孔圆的1/3 2级 w>0.05 w>0.l 3级 4.5.3.5覆盖涂层及感光性阻焊跳印(飞白 在进行可焊性试验时,覆盖涂层及感光性阻焊跳印(飞白)处的导体上不应有焊料附着
4.5.4镀层外观 4.5.4.1 镀涂层缺损 镀涂层缺损的接收条件如下: 镀涂层缺损形式 a 镀涂层缺损形式如图13所示
GB/T14515一2019 镀层 镀层缺陷 镀层缺陷 镀层 镀层缺陷 镀层 印制插头区域 印制插头 连接盘 连接盘孔 镀层 镀层缺陷 镀层 镀层 损镀层 镀层缺陷 d 集成电路接触点 ACF接触区域 指定点接触 图13镀涂层缺陷 b 镀金层缺损 镀金层缺损应符合表11和表12的要求
表11镀金层缺损 等级 锻 金 在图13中的举例 连接盘部位的镀金层缺陷如图13所示)应在全部镀金层面积(不包括因粘 图13b)和图13c 接剂渗出而无镀金层的面积部分)的10%以下 图13a) 接触部位的镀金层不应有缺陷,触点外围如图13f)的镀金层缺陷,应在全部 镀金层面积的1/4以下;在印制插头部位如图13a),关键部位(即金手指的中 图13d 间1/3处)不允许有缺陷,非关键部位要求同触点外围 图 13f 直接接触部位,放大镜检验应无缺陷包括麻点、凹坑、针孔、气泡 图13d)和图13e 如图14所示,宽度(w),长度(L)的镀金层缺陷对成品线导体宽度(w)符合表12的要求 图14镀金层缺陷的长宽
GB/T14515一2019 表12镀金层缺陷处的宽度和长度 单位为毫米 成品导线宽度w 接触区缺陷 w<0.30 0.30
GB/T14515一2019 b 可焊性镀层 外表焊料镀层表面不应发黑黑化. 4.5.5外形边缘和冲切孔的外观 4.5.5.1撕裂或缺口 不应有撕裂或缺口如图17所示
但在切口的拐角处允许有裸眼看不出的撕裂或缺口
4.5.5.2毛刺 毛刺如图18所示的高度(n)应不超过0.1 mm
不应有可能会造成电气短路的导线端面的毛刺
4.5.5.3丝状毛刺 非导电性丝状毛刺如图19所示
位于外形边缘部位的丝状毛刺长度()应不大于1.0mm,位于 孔处的丝状毛刺垂度(.)应不大于0.3mm,毛刺应不容易脱落
撕裂、缺口 图17撕裂、缺口 毛刺 图18毛刺 丝状毛刺 b 外形边缘部位的丝状毛刺 孔处的丝状毛刺 图19丝状毛刺 12
GB/14515一2019 4.5.6增强材料的外观 4.5.6.1与增强材料之间的夹杂物 与增强材料之间夹杂物的合格判据如下 挠性印制板与增强材料之间的夹杂物如图20所示
引起的突出p)应不大于0.1mm
夹杂 a 物引起的厚度变化不应使印制板与增强材料的总厚超出规定值
b 夹杂物的大小应不大于挠性印制板与增强材料粘接面积的5%
不应有与元件孔或外形边缘相连接的夹杂物
c d)外形边缘伸出的丝状非导电性夹杂物的长度()应不大于1.0n mm
丝状非导电性异物 不可 可 粘接增强材料的部位 图20印制板与增强材料之间的夹杂物 4.5.6.2增强材料与印制板间的气泡 增强材料与挠性印制板间气泡如图21所示
在使用热固粘接剂时,气泡应不大于所粘接增强材料 面积的10%;在使用其他类型粘接剂时,气泡应不大于所粘接增强材料面积的1/3
在印制插头端部不 应有气泡和翘起
粘贴增强材料部位 气泡 增强材料中央处 FPc 印制插头端部外层翘起 气泡 粘接剂 增强材料 印制插头的插入端 增加材料的边缘处 图21印制板与增强材料间的气泡 13
GB/T14515一2019 4.5.6.3增强材料的缺陷 增强材料的合格判据如下 裂缝 a 裂缝如图22所示,应符合表17的要求
裂缝 图22裂缝示意图 表17裂缝合格判据 裂 等级 缝 1级 不应有影响使用的裂缝 2级、3级 不应有贯穿增强材料的孔与孔间的裂缝及贯穿孔与外形的裂缝 缺损 b 增强材料的缺损如图23所示,长度()应小于1mm
缺损 缺损 图23缺损 划痕 c 除另有规定,划痕由供需双方协商
4.5.7其他 4.5.7.1表面附着物(不包括导体裸露部位 表面附着物应符合以下要求 热固型粘接剂 a 14
GB/14515一2019 表面的热固型粘接剂应符合表18的要求
表18表面热固型粘接剂 等级 表面热固型粘接剂 在覆盖层或覆盖涂层表面允许有用蘸异丙醇的棉球棒擦拭不掉的已固化的粘接剂、覆盖层或 1级2级 覆盖涂层的碎片及纤维
当有总厚度要求时,包括表面粘接剂的总厚度应符合规定要求 3级 表面不应有目视可见的残留的粘接剂 b 助焊剂残留 表面残留的助焊剂应符合表19的要求
表19表面残留的助焊剂 等级 残留的助焊剂 1级、2级 用蘸异丙醇的棉球棒擦拭时,不应被污染 3级 表面不应有目视可见的残留助焊剂 残留的金属颗粒 以下要求仅适用于即使金属颗粒(焊料、铝、铜等)脱落也不会引起产品故障的场合
且在适当 的条件下,挠性印制板用户的处理方法有能力除去残留的金属颗粒
残留的金属应符合表20 的要求
表20残留的金属颗粒 等级 残留的金属颗粒 允许存在用超声波洗净lmin而脱落的金属颗粒 允许的金属颗粒直径(d)及个数应符合以下要求 1级 0.1mm
GB/T14515一2019 基底膜表面划痕 基底膜划痕的截面 b 图26基底膜划痕 表24允许的基底膜划痕 等级 基底膜划痕 1级、2级 i<1/3 3级 i<1/5 4.5.7.5覆盖层及覆盖涂层外观 覆盖层及覆盖涂层外观应符合以下要求 a 覆盖层及覆盖涂层压痕 覆盖层及覆盖涂层压痕如图25所示,应符合表25的要求
表25覆盖层及覆盖涂层压痕深度 等级 压痕的深度 压痕深度不大于0,10mm 1级、2级 当其深度难于测量时,可用测量背面突出的高度代替 3级 薄膜两面不应有目视可见的压痕 b 覆盖层及覆盖涂层划痕 覆盖层或覆盖涂层表面不应有严重划痕、裂缝、破裂及粘接层的剥落,在反复弯曲部位的划 痕,不应影响弯曲性能
在覆盖层或覆盖涂层上有划痕如图26所示,其深度()相对于覆盖层 或覆盖涂层厚度(t),应符合表26的要求
表26覆盖层及覆盖涂层划痕深度 等级 划痕深度 1级 不应露出导线 2级 划痕深度is1/3 3级 划痕深度i<1/5 注覆盖涂层的厚度等于挠性印制板的总厚度减去无覆盖涂层部位的厚度 4.5.7.6标记符号 标记符号应能识别
17
GB/T14515一2019 4.6尺寸检验方法和要求 4.6.1检验方法 挠性印制板的尺寸检验方法应符合GB/T13557一2017的第6章的方法进行检验
检验应在放大 倍数最小为3倍的光学仪器下进行,如果有不清楚的缺陷,可以改用更高放大倍数的放大镜来检验
对 于有尺寸要求的精确测量,可采用带十字标线和刻度的光学仪器
如果采购文件有特殊要求,应采用采 购文件规定的放大倍数的放大镜
尺寸检验应采用满足精度要求的量具
4.6.2外形尺寸 尺寸(长和宽)公差应符合表27的要求
表27外形尺寸公差 等级 外形尺寸 公差 小于或等于100mm 士0.30mm 级、,2级 大于100mm 士0.3% 3级 由供需双方协商 4.6.3厚度 厚度公差应符合表28的要求
表28厚度的公差 等级 厚度 公差 大于或等于0,15mm 士20% 1级、2级 小于0.15mm" 由供需双方协商 3级 由供需双方协商 4.6.4 孔 4.6.4.1孔的一般要求 孔的一般要求如下: 对于1级,2级产品孔的要求应符合4.6.4.2、4.6.4.3的要求; a b)对于3级产品孔的要求超过4.6.4.2、4.6.4.3的范围时,由供需双方协商
4.6.4.2成品孔径公差 成品孔径()公差应符合表29要求
18
GB/T14515一2019 表29孔径公差 孔径 公差 mm mmmm 0.8 士0.20 0.2/<0.8 士0.10 1<0.2 士0.05 4.6.4.3镀覆孔 作为双面挠性印制板镀覆孔的导通应仅为圆孔并应符合表30的要求
表30镀覆孔 单位为毫米 导通孔的要求 等级 1级 镀后的最小导覆孔孔径应为0.5,公差应为士0.08 2级 镀后的最小导覆孔孔径应为0.4,公差应为士0.08 3级 由供需双方协商 4.6.5导线宽度 导线宽度(W)及公差应符合表31的要求
表31导体宽度及公差 导体宽度 公差 w0.05mm 由供需双方协商 0.05mm
GB/T14515一2019 于或等于100mm,公差是设计尺寸的士0.3%以内,但不包括导通孔孔位公差 4.6.9.2孔与连接盘之间的重合度 成品的有效最小连接盘环宽(d)如图28所示,应符合表10最小可焊环宽(w)的要求
连接盘 无覆盖层(或覆盖涂层 有覆盖层(或覆盖涂层 b 图28孔与连接盘的重合度 4.6.9.3连接盘与覆盖层或覆盖涂层的重合度 覆盖层或覆盖涂层对于连接盘的覆盖(e)如图29所示,应符合表35的要求
S 州垫 孔 -连接盘 覆盖层或覆盖涂层 覆盖层或覆盖涂层 连接盘覆盖层重合度 焊垫覆盖层重合度 图29覆盖层或覆盖涂层的重合度 表35覆盖层或覆盖涂层的重合度 等级 焊垫的有效面积 连接盘的最小可焊环宽 1级 覆盖层或覆盖涂层的覆盖允许至孔圆的1/3 应在设计面积的75%以上 2级 0.05mm 3级 习 0.1mm 由供需双方协商确定 4.6.9.4增强材料与挠性印制板的位置重合度 增强材料与挠性印制板的位置重合度应符合以下要求 孔的重合度 a 增强材料与挠性印制板孔之间的孔偏移(w)的差(D-w)应在孔径(D)的公差范围内,如 图30所示
21
GB/T14515一2019 (平面图 挠性印制板的孔位置 增强材料孔的位置 挠性印制板 增强材料 剖面图 图30孔的重合度 外形的偏移 b 增强材料对外形的偏移()如图31所示,应符合表36的要求
挠性印制板 增强材料 图31外形偏移 表36允许的外形偏移 单位为毫米 等级 允许偏移 1级 i二士0.5 2级 <士0.3 3级 夭土02 4.6.9.5冲切外形的偏移 冲切外形的偏移应符合表37的要求
表37冲切外形的偏移 等级 冲切外形的偏移 1级,2级 外形不应与导线相切,但不包括电镀工艺导线,增强用独立连接盘和增强用导线 边缘导线与外形的间距应大于0.1mm,但不包括电镀工艺导线,增强用独立连接盘和增强用 3级 导线 4.6.10板与增强材料对压敏胶或热固粘接剂的偏移(包括粘接剂的溢出 挠性印制板与增强材料之间的压敏胶或热固粘接剂的偏移(V)(包括粘接剂的溢出)如图32所示, 应不大于士0.5 mm 22
GB/T14515一2019 粘接剂 挠性印制板 增强材料 图32挠性印制板与增强材料之间的压敏或热固粘接剂的偏移包括粘接剂的溢出 4.6.11镀覆孔的镀铜层最小厚度 镀覆孔的镀饷层最小厚度应大于0.005mm,符合表38的要求
表38镀覆孔的镀铜层最小厚度 单位为毫米 等级 厚度 1级 >0.005 2级 >0,012 3级 3 0.020 4.7物理性能及检验方法 4.7.1剥离强度及检验方法 4.7.1.1剥离强度检验方法 剥离强度检验方法如下 导线剥离强度检验应按GB/T13557一2017中7.2的方法进行 a b 覆盖层剥离强度检验先把宽10mm试样粘接于铜箔光泽面上,再按GB/T13557一2017中 7.2的方法进行 增强材料剥离强度检验先把宽10mm试样粘接于铜箔光泽面上,再按GB/T13557一2017中 7.2的方法进行
4.7.1.2剥离强度要求 剥离强度要求如下 导线剥离强度应不小于0.49N/m mm; aa 5 覆盖层剥离强度应不小于0.34N/mm; 增强材料剥离强度;热固型粘接剂不小于0.34N/mm,压敏粘接剂不小于0.15N/n mm 4.7.2拉脱强度及检验方法 4.7.2.1拉脱强度检验方法 拉脱强度检验方法如下: a 非镀覆孔焊盘的拉脱强度应按GB/T4677一2002中7.2.1的方法进行; b 无焊盘镀覆孔的拉脱强度应按GB/T4677一2002中7.2.2的方法进行
4.7.2.2拉脱强度要求 非镀覆孔焊盘或无焊盘镀覆孔的拉脱强度测试结果应符合表39的要求
23
GB/T14515一2019 表39拉脱强度 等级 拉脱强度 1级 无规定 2级、3级 大于或等于1N/mm 4.7.3镀层附着力及检验方法 4.7.3.1 镀层附着力检验方法 镀层附着力检验应按GB/T4677一2002中8.1.的方法进行 4.7.3.2镀层附着力要求 不应有镀层剥落现象 4.7.4可焊性及检验方法 4.7.4.1可焊性检验方法 可焊性检验应按GB/T4677一2002中8.2的方法进行
4.7.4.2可焊性检验要求 试验后焊接面积应大于全部电镀面积的95%(此要求不适用于聚酯挠性印制板)
4.7.5耐挠曲性及检验方法 4.7.5.1耐挠曲性检验方法 耐挠曲性检验方法如下: 有覆盖层的印制板试验前应根据供需双方协定的挠曲半径、往返挠曲速率和往返弯曲次数要 a 求进行 b 弯曲速率推荐为1000次每分钟或更高,以节省试验时间; 耐挠曲性检验应按GB/T13557一2017中7.3的方法进行
c 4.7.5.2耐挠曲性要求 经试验后印制板表面无裂缝,起泡、微裂纹或分层等缺陷
4.7.6耐折性及检验方法 4.7.6.1 耐折性检验方法 耐折性检验方法如下 a 有覆盖层的印制板试验前应根据供需双方协定的折曲半径,负荷和折弯次数要求进行 b)耐折性检验应按GB/T13557一2017中7.4的方法进行
4.7.6.2耐折性要求 经试验后印制板表面无裂缝、起泡、微裂纹或分层等缺陷
24
GB/14515一2019 4.8化学性能及检验方法 4.8.1化学性能检验方法 化学性能检验应按GB/T13557一2017中8.1.3的方法进行
4.8.2化学性能要求 经化学性能测试后的试样不应有分层或隆起,字符不应有显著的损伤
4.9电性能及检验方法 电性能检验方法 4.9.1 4.9.1.1导线电阻 导线电阻按GB/T4677一2002中6,.1.1方法3a进行
4.9.1.2表面绝缘电阻 表面绝缘电阻检验方法如下: 验收态按GB/T4677一2002中6.1.1方法3a进行; a b 湿热处理后按GB/T13557一2017中湿热试验方法进行
4.9.1.3表面耐电压 表面耐电压检验方法按GB/T4677一2002中6,.5.1方法进行
4.9.1.4开路和短路 开路和短路检验方法按GB/T4677一2002中6.2.2(电路连通性)和6.2.1(电路绝缘性)方法进行
4.9.2电性能要求 4.9.2.1导线电阻要求 应由供需双方商定
4.9.2.2表面绝缘电阻要求 表面绝缘电阻应符合以下要求 验收态时,不小于5×10”Q a b)湿热处理后,应符合表40的要求 表40湿热处理后表面绝缘电阻 等级 表面绝缘电阻 1级、2级 >1×10*Q 3级 >5×10”Q 4.9.2.3表面耐电压验要求 当施加500VAC时,不应有飞弧发生
25
GB/T14515一2019 4.9.2.4开路和短路要求 当电阻10Q应作为“开路”;电阻2MQ应作为“短路” 4.10环境性能及检验方法 4.10.1环境性能检验方法 4.10.1.1温度循环检验方法 温度循环试验中试样经受的测试条件见附录A
具体参数值的测试方法依据供需双方商定 4.10.1.2耐湿检验方法 耐湿检验方法如下 恒定湿热后的耐湿检验方法应按GB/T13557一2017中耐湿性方法进行 a b) 交变湿热后的耐湿检验方法应按GB/T13557一2017中耐湿性方法进行
4.10.1.3耐热冲击检验方法 耐热冲击检验方法如下 高温浸请后的耐热冲击检验应按GB/T467一202中9.2.3(热应力浮媒)的方法进行 a b)高低温循环后的耐热冲击检验应按GB/T4677一2002中9.2(热应力)的方法进行
4.10.1.4镀覆孔的耐热冲击检验方法 镀覆孔的耐热冲击检验应按GB/T4677一2002中9.2热应力)的方法进行 4.10.1.5耐离子迁移检验方法 耐离子迁移检验方法见附录B. 4.10.1.6晶须检验方法 晶须检验方法见附录C
4.10.1.7耐盐雾检验方法 耐盐雾检验的试验条件按GB/T2423.17一2008中的试验Ka;盐雾试验方法进行;测试方法按供 需双方商定
4.10.2环境性能要求 温度循环 4.10.2.1 应满足供需双方协定的参数项目和试验前后的性能变化
4.10.2.2耐湿 应满足供需双方协定的项目、试验条件和试验前后的要求
4.10.2.3耐热冲击 应满足供需双方协定的项目,试验条件和试验前后的要求
26
GB/14515一2019 4.10.2.4镀覆孔的耐热冲击 试验后的镀通孔电阻变化率应不大于20%
4.10.2.5耐离子迁移 试验后的电阻应不小于10n. 4.10.2.6晶须 应供需双方商定
4.10.2.7 耐盐雾 测试项目和参数指标应符合供需双方商定
4.11清洁度及检验方法 4.11.1清洁度检验方法 印制板清洁度应按GB/T4677一2002中第10章的方法进行
4.11.2清洁度要求 除非另有规定印制板的离子污染度应不超过1.50严g/em氧(离子当量) 4.12阻燃性及检验方法 4.12.1阻燃性检验方法 阻燃性应按GB/T13557一2017中10.2方法进行
4.12.2阻燃性检验要求 应符合采用基材的阻燃等级
质量保证规定 5.1通则 按照本标准交付的单、,双面挠性印制板应满足第3章和第4章的要求
制造厂有责任验证其按本 标准交付的印制板满足第3章的要求
5.2质量评定 质量评定应按照GB/T162612017中第5章的要求进行
质量评定可选用能力批准、鉴定批准 或由承制方和顾客双方商定的其他质量评定方式
能力批准和鉴定批准的要求和相关信息可以用于第 二方,第三方的认证或承制方关于相应类型印制板的内部声明
依据所选用的质量评定方式,质量评定程序可由能力鉴定检验、产品鉴定检验、质量一致性检验或 合适的过程控制检验等检验方式构成
质量一致性检验包括逐批检验和周期检验
能力鉴定检验通过 能力鉴定单元的综合测试板(CTB)、附连测试板或合适的在制印制板(PPB)来完成
产品的鉴定检验 通过附连测试板或合适的在制成品)印制板来完成
27
GB/T14515一2019 能力批准和鉴定检验的相关信息和要求可以用于第二方、第三方认证或制造厂关于相应类型印制 板的内部声明
5.3检验条件 检验应符合GB/T4677一2002中第4章的规定
5.4能力批准 除非另有规定,应在相关主管部门或权威机构认可的情况下采用此质量评定方式
能力批准的程序按GB/T162612017中附录A的规定细化后实施
能力批准应通过鉴定检验 证实其加工一类产品能力的符合性,包括产品能力和工艺能力
除非另有规定,能力鉴定检验的检验项 、检验顺序、鉴定单元的综合测试板或测试图形的数量和允许失效数应符合表41的规定
除非另有 目 1、 规定,检验样品或测试图形按S20828的要求在实际生产环境中制造中,其复杂性<印制板的层数、厚 度、导线宽度和间距、图形复杂性、孔的尺寸、孔的数量、孔的类型、孔的位置以及这些参数的公差等)应 能代表申请批准的产品能力和工艺能力
除非另有规定,能力鉴定资格的维持应符合5.6的规定
表41鉴定检验表 检验要求检验万法 序号 检验项目 样本类型 章,条号 章、条号 导线外观 4.5,2 成品板 覆盖层及覆盖涂层外观 成品板 4.5.3 镀层外观 4.5,4 成品板 外观 4.5.1 4.5,5 外形边缘和冲切孔的外观 成品板 增强材料的外观 4.5.6 成品板 其他 4.5.7 成品板 4.6.2 外形尺寸 成品板 厚度 4.6.3 成品板 4.6.4 成品板 4.6.5 导线宽度 成品板 导体节距的累积公差 成品板 1 4.6.6 尺寸 4.6,1 12 孔中心距 .6.7 成品板 13 导线到板边缘的最小距离 4.6.8 成品板 14 位置公差 4.6.9 成品板 15 板与增强材料对压敏胶或热固粘接剂的偏移 4,6.10 成品板 镀覆孔的镀铜层最小厚度 成品板 16 4.,6.l1 17 剥离强度 4.7.1.2 4.7.1.1 成品板、附连测试板 18 拉脱强度 4.7.2.2 4.7.2.1 成品板、测试图形J 4.7.3.1 成品板、测试图形 K 19 镀层附着力 4.7.3.2 物理性能 20 可焊性 4.7.4,2 4.7.4.1 成品板、测试图形1 21 耐挠曲性 4.7.5.2 4.7.5.1 成品板、测试图形X 22 耐折性 4.7.6.2 4.7.6.1 成品板,测试图形X 28
GB/T14515一2019 表41(续 检验要求检验方法 序号 检验项目 样本类型 章、条号 章、条号 23 化学性能化学性 4.8.2 4.8.I 成品板、任意附连测试板 24 导线电阳 4.9.2.1 4.9.l.l 成品板、附连测试板 成品板,附连测试板 表面绝缘电阻 4.9.1.2 25 4.9.2.2 电性能 26 成品板,测试图形E 表面耐电压 4.9.2.3 4.9.1.3 开路和短路 4.9.2.4 4.9.1.4 成品板 28 4.10.2.1 4.10.1.1 温度循环 成品板、附连测试板 29 耐湿 4.10.2.2 4.10.1.2 成品板、测试图形E 耐热冲击 4.10.2.3 4.10.1.3 30 成品板、测试图形Y 31 环境性能镀覆孔的耐热冲击 4.10.2.4 4.10.1.4 成品板、测试图形D 32 耐离子迁移 4.10.2.5 4.10.1.5 附连测试板附录B 晶须 附连测试板(附录c) 33 4.10.2.6 4.10.l.6 4.10.2." 4.10.1.7 耐盐雾 成品板、,附连测试板 34 35 4.11.2 4.l1.1 清洁度清诘度 成品板,附连测试板 36 阻燃性 阻燃性 4.12.2 4.12.1 附连测试板 37 清洁度 清沽度 4.11.2 4.11.1 成品板、附连测试板 38 阻燃性 阻燃性 4.12.2 4.12.1 附连测试板 5.5鉴定批准 5.5.1通则 鉴定批准应符合GB/T162612017中附录B的要求
鉴定检验应在鉴定机构认可或由承制方与 顾客共同协商确定的实验室进行
鉴定检验的试样应是由印制板正常生产中使用的材料、设备和工艺 所生产的附连测试板或合适的成品印制板(PPB)
鉴定合格资格的保持周期为12个月
如果检验结果表明已鉴定合格的产品不符合本标准的规定 或连续两个周期内已鉴定合格的产品未生产,则丧失鉴定合格资格
5.5.2样本大小 提交鉴定检验的同一型号的成品印制板、附连测试板均至少为6个,且一个成品印制板只有一个图 形
鉴定检验的样品和测试图形要求应符合表41规定
测试图形列表见附录D. 5.5.3检验程序 按照表41给定的顺序进行检验
表中的外观、尺寸和电性能中的“开路和短路”项目均为非破坏性检验,因此其对应的所有样品即 3个样品)都需要通过检验
耐离子迁移性、晶须和阻燃性只能由仅有一个特定测试图形的附连测试板 测试;每个项目应制作5个样品
其他项目的样品数为3
29
GB/T14515一2019 5.5.4不合格 若有一个检验项目中的一个样品(不管是成品板还是附连测试板)不合格,则产品鉴定失败,不能给 予鉴定合格
5.5.5不合格处理 如果不合格是由于设备或人为操作错误造成,允许同一批次印制板的其他样本或附加样本重新提 交鉴定,并应通知鉴定机构 5.5.6鉴定资格的保持 为保持鉴定合格资格,每12个月承制方应向鉴定机构或用户提交涵盖下列内容的报告 a 质量保证大纲符合规定; b)产品的设计未作更改; c 产品详细规范的要求未作会影响产品特性的更改(存在详细规范时) d 质量一致性检验均合格 5.6质量一致性检验 5.6.1通则 质量一致性检验包括逐批检验(交付检验)和周期检验 5.6.2逐批检验 检验批 5.6.2.1 个检验批应由使用相同材料,采用相同工艺过程,相同结构或结构类似,在一个月内生产并一次 提交检验的全部印制板组成
具有所有下列共同特征的印制板为结构类似 同类型的基材 a b) 同类型的印制板; 同类型的镀层和涂覆层; c d 产品的复杂性相似
5.6.2.2可追溯性 各检验批应保持可追溯性
进行质量一致性检验的附连测试板应可追溯至相应的成品板
5.6.2.3检验项目 按本标准生产和交付的印制板每批均应通过表42中规定的所有检验项目
按照各个检验项目进 行逐批检验时,对检验次序没有要求
因为附连测试板与成品板是一一对应的,因此其抽样方式也应与 成品板保持一致 当表42中指明为“抽样”时,使用表43中规定的C=0零验收数抽样方案
表42中,抽样后括号 内的数值就是表43中AQL值
30
GB/T14515一2019 表42逐批检验表 测试试样 检验频度 检验要求检验方法 序号 检验项目 成品附连 章、条号 章将条号 1级 2级 3级 板 洲试版 导线外观 4.5.2 抽样(0.15抽样(0.1抽样(0.1) 4.5.3 覆盖层及覆盖涂层外观 抽样(0,25抽样(0.15抽样(0.15) 镀层外观 4.5.4 抽样(0.40抽样(0.25抽样(0.25 4.5.1 外形边缘和冲切孔的外观 4.5,5 抽样(0.40抽样(0.25抽样(0.25 增强材料的外观 4.5,6 抽样(0,65抽样(0,40抽样(0,40) 其他 抽样(6.5)抽样(6.5抽样(4.o 4.5.7 4.6.2 外形尺寸 抽样(6.5)抽样(6.5)抽样(4.0) 4.6.3 抽样(6.5 厚度 抽样(6,.5)抽样(4.o 孔 4.6. 抽样(6.5抽样(6.5) 抽样(4.0 10 导线宽度 4.6.5 抽样(2.5抽样(2.5) 抽样(1.5 11 导体节距的累积公差 4.6,6 抽样(2.5)抽样(2.5 抽样(1.5 4.6.1 12 孔中心距 4,6.7 抽样(2.5)抽样(2.5 抽样(1.5) 导线到板边缘的最小距离 抽样(2.5)抽样(2.5) 抽样(G 1.5 13 4,6,8 14 位置公差 4.6.9 抽样(2.5)抽样(2.5)抽样(a 5 板与增强材料压敏胶或热固 4.6.10 抽样(4.0)抽样(4.0) 抽样(2.5 15 粘接剂的偏移 镀覆孔的镀铜层最小厚度 抽样(4.0抽样(4.0抽样(2.5) 16 4.6.l1 17 4.7.3. 镀层附着力 抽样(6.5)抽样(G.5)抽样(4 4.7.3.2 4.0 18 4.7.4.2 4.7.4.1 可焊性 抽样(6.5抽样(6,.5)抽样(4.o 19 耐热冲击性(高温浸溃 4.10.2.34.10.1.3a) 抽样(6.5)抽样(6.5) 抽样(4.0 20 镀覆孔的耐热冲击 4.10.2.4 4.10.1.4 抽样(6.5)抽样(6.5 抽样(4.0) 5.6.2.4抽样方案 抽样方案应按表43的规定
表43抽样方案 接收质量限AQL" 批量 0.15 0.25 0.10 0.40 0.65 1.5 2.5 4.0 6.5 (5 3 2 1 9~15 (13) 6~25 20 13 26~50 32) 20 13 5190 80 50 32 20 13 12 31
GB/T14515一2019 表43(续 接收质量限AQL 批量 0,10 0,15 0.25 0,40 0,65 l.0 1.5 2.5 4.0 6.5 32 20 13 12 11 91150 125 80 50 281一500 47 12 25 80 50 48 29 21 10 5011200 25 80 75 73 4?7 34 27 19 15 12 20l3200 73 3 24 17 53 42 1 25 120 116 320110000 86 68 23 16 192 189 1l6 50 38 29 77 294 189 108 60 46 35 29 10000以上 135 注:如果该批的样本足够大,可以使用表43的值
如果该批的数量小于抽样数,则检验整个批次,见表中的“b” 如果样本没有发现缺陷,整个批次都可以接收
如果样本发现一个或更多缺陷,整个批次都拒收
5.6.2.5合格判据 如果试样全部符合要求,则判定该产品合格,通过逐批检验的印制板可以交付
5.6.2.6不合格处理 如果一个或多个试样不合格,则该批印制板拒收,所有不合格产品不应交付
加严检验时,需将按 照表43,将AQL等级向左加严1级
对重新检验批应清晰标明为复验批,并与新的批严格区分
如被拒收产品的缺陷不可纠正或复验不合格,则该批不得交付
5.6.3周期检验 5.6.3.1检验项目 周期检验项目应符合表44的要求
5.6.3.2抽样方案 周期检验的样本大小为2个
周期检验的样品应从通过逐批检验的检验批中抽取相应的附连测 试板
5.6.3.3合格判据 如果有一个或多个样本单位未通过周期检验,则该型产品周期检验为不合格,并且其他使用相同材 料和加工工艺生产的同一周期产品均认为失效
表44周期检验 样本类型 检验频度 检验要求检验方法 序号 检验项目 附连 章,条号 章,条号成品板 1级 3级 2级 测试 剥离强度 4.7.1.2 4.7.1.1 需要时 每月 每月 拉脱强度 4.7.2.2 4.7.2.1 需要时 每月 每月 32
GB/T14515一2019 表44(续 样本类型 检验频度 检验要求检验方法 序号 检验项目 附连 章,条号 级 3级 章,条号成品板 2级 测试 表面绝缘电阻 验收态 4.9,2.2a4.9.1.,2a 需要时 每月 每月 每月 每月 表面耐电压 4.9,2.3 需要时 4.9.l.3 4.7.5.2 4.7.5.1 耐挠曲性 需要时每季度每季度 耐折性 4.7.6.2 4.7.6.1 需要时每季度每季度 耐化学性 4.8.2 4.8.l 需要时每季度每季度 4.9.2.2b4.9.1.2) 需要时每半年每半年 表面绝缘电阻 湿热处理后 耐湿性 4.10.2.2 4.10.1.2 需要时每半年每半年 耐热冲击 10 高低温循环 4.10,2.3 4.10.2.3 需要时每半年 每半年 4.12.2 4.12.1 阻燃性 需要时每半年每半年 1 导线电阻 4.9.2.1 12 4.9.1.1 需要时需要时需要时 13 温度循环 4.10.2.1 4.10.1.1 需要时需要时需要时 14 4.10.1.5 耐离子迁移性 4.l0.2.5 需要时需要时需要时 15 晶须 4.10.2.6 4.10.1.6 需要时需要时需要时 盐雾测试 4.10.2.7 需要时需要时需要时 16 4.10.1.7 1" 4.l1.1 清洁度 4.11.2 需要时需要时需要时 5.6.3.4不合格处理 如果有样品未通过周期检验,则应 立即停止产品交货和逐批检验 a b 查明失效原因,在材料、工艺或其他方面提出纠正措施" 完成纠正措施后,重新生产并抽取样品进行周期检验 c d)逐批检验可以重新开始,但应在周期检验重新检验合格后,产品才能交货
如果周期重新检 验不合格,则应将检验结果报告鉴定机构或用户方
6 交付要求 6.1包装要求 包装应符合表45的要求
表45包装 包 装 等级 1级 产品的包装应满足运输中产品不受损伤 2级 除满足1级产品包装要求外,还应保证产品在室温条件下储存中具有防潮性能 除1级和2级包装要求外,应包括供需双方协商的其他包装要求 3级 33
GB/T14515一2019 6.2运输及装卸 印制板的运输和装卸应符合相关文件的规定或供需双方协商
6.3储存 挠性印制板应在温度22C士5C,相对湿度不大于85%的场所储存
6.4使用 使用说明书示例参见附录E
使用说明书是为了防止客户在使用挠性印制板时发生故障所应注意 的要点
34
GB/14515一2019 附 录 A 规范性附录) 温度循环试验方法 A.1概述 本方法仅适用挠性印制电路板温度循环试验
A.2试验样品 与本标准规定的试验项目对应的测试样板、测试图形,或者挠性印制板上规定的个别部位
A.3试验设备 能从第1步骤调整到第3步骤所示温度并保持低温和高温的试验箱
若一体式高低温试验箱 最佳
A.4试验条件 试验条件应符合表A.1规定
温度循环试验条件 表A.1 温度 温度 时间 温度 时间 时间 步骤 "C min min min -65士3 -55士3 -65士3 30 30 30 20士15 10~15 20士15 10~15 20士15 10~15 30 30 125土3 100士2 30 100士2 20士15 1015 20士15 1015 20士15 1015 A.5试验程序 样品是按本标准规定的试验项目测试后,从表A.1中选定温度条件
步骤1~步骤4的操作过醒 为一个循环,循环次数应在详细规范中规定
除非另有规定,应为五次循环
随后开始规定的测试
A.6试验报告 试验报告应包括以下内容: 样品名称,型号、批号及制造单位或送样单位 a b 试验设备的型号、名称; 35
GB/T14515一2019 试验方法中规定的报告内容 c d 试验的环境条件; 试验温度循环条件,与规定试验方法的任何偏离; e fD 试验日期,试验人员
36
GB/14515一2019 附录 B 规范性附录 离子迁移试验方法 B.1概述 本方法仅适用挠性印制电路板离子迁移试验
B.2试验样品 样品结构应像图B.1所描绘的样品一样,有细节图解,具体包括以下几个方面 样品的材料应与被评价产品一致,包括覆盖膜以及覆盖涂层; aa b 模型指状组合的数量为75; 样品导线宽度/距离应在60/60Mm到100/100m之间,并且应在用户与供应商之间达成 共识 d 试验样品的数量从110不等,并且应在用户与供应商之间达成共识
-20 5 20 60um100m 注1,点状圈表明覆盖膜及覆盖涂层的开口
注2:未标注的单位为mm.
图B.1离子迁移试验样品的结构 37
GB/T14515一2019 B.3 试验设备 试验设备应能够将温度和相对湿度保持在85C士2C和85%士3%,应使用绝缘试验仪对绝缘电阻! 进行测量
B.4试验条件 试验条件如下 温度/湿度:85C/85%; a b 外加电压;l5V或50V直流电,应在用户与供应商之间达成共识; 持续时间:250h,或500h,或1000h,应在用户与供应商之间达成共识
B.5 试验程序 使用图B设计的电路在外加直流电压为15V或50V的情况下,对样品的绝缘电阻进行测量
B.6试验报告 试验报告应包括以下内容 样品名称、型号、批号及制造单位或送样单位; a 试验设备的型号、名称; b 试验方法中规定的报告内容 c 试验的环境条件; d 绝缘电阻的平均值,与规定试验方法的任何偏离 e 试验日期、试验人员
38
GB/14515一2019 录 附 C 规范性附录 晶须检测试验方法 概述 C.1 本方法仅适用于挠性印制板在机械外应力作用下的晶须检测试验
试验样品 C.2 样品即被当作连接器的挠性印制板的接触面部分,应在用户与供应商之间达成共识,推荐的样品数 量N=5.
C.3试验设备 晶须检测设备的结构如图c.1和图c.2所示
一台扫描电镜(SEM)(或一台金相显微镜)(放大倍 数×100或更高) 维氏硬度计压徘 挠性印制板的接触面 图c.1检测设备的基本结构 维氏硬度计压维 样品 图c.2检测设备结构 39
GB/T14515一2019 C.4试验条件 试验条件如下 温度:室温,25C士5C; a b)相对湿度:55%士30%; c 样品质量;200g士10g; d 检测时间:第一次的推荐试验时间是96h
经用户与供应商达成共识后试验时间可以延长
C.5试验程序 试验程序如下 使用扫描电镜(SEM),记录长度超过504m的晶须的数量; a b 长度小于504m的晶须的数量应经过用户与供应商协商后达成共识; c 本检测试验不是晶须生长的定量绝对检测,而是定量相对检测; 应注意使摆动不干扰检测
比较理想的晶须生长试验是不用加稠剂和/或胶粘剂,因为这些材 d 料可能会影响到晶须生长; 还应引起重视的是,晶须开始生长所需要的时间可能与镀锡的印刷板不同 应确保维氏硬度计压锥的尖端干净,无灰尘; 推荐为晶须生长做一次挠性板连接器插人测试 8 除了阐述晶须生长机理的文件所描述的外应力情况下的晶须生长试验之外,在由温度、湿度 h 及/或热冲击引起的内应力情况下应进行晶须生长试验
C.6试验报告 试验报告应包括以下内容 样品名称,型号,批号及制造单位或送样单位 a 试验设备的型号、名称; b 试验方法中规定的报告内容; c 试验的环境条件 d 晶须数量,与规定试验方法的任何偏离 e 试验日期、试验人员
40
GB/14515一2019 附 录 D 规范性附录 综合测试图形与尺寸 D.1概述 本附录仅适用于挠性印制板综合测试图形与尺寸
D.2试验样品 D.2.1试样 试样为印制板的成品板或半成品板,也可以是测试板
D.2.2测试图形 测试图形中图形分别用来进行质量一致性检验所用某项试验的单个测试图形,图形见图D.1和 图D.2
D.2.3测试图形尺寸 测试图形尺寸的要求见表D.1
表D.1测试图形的尺寸 孔径 窗孔直径连接盘直径 试样 试验 mm mm mm 2.0 1.8 0,8 重合度,可靠性 4.0 2.0 4.2 2.5 2.5 1. 镀层厚度 2.0 2.0 0.8 D 镀覆孔 2.5 0,8 2.0 0.8 绝缘电阻,耐电压 导线粘度、间距,宽度、缺陷、微粒 G 剥离强度 拉脱强度 4.0 l.3 镀层性能 X 耐弯曲性、耐折性 2.5 4.0 1.3 耐热冲击性 1
GB/T14515一2019 单位为毫米 90.00 30.00 30.0o I5.0ol5.00 25.0o oooO ooooooo oooo o0oooo g ooooooo ooooooo 有覆盖层部分 无覆盖层部分 ooooooo ooooooo 1ooo ooooooo ooooooo oooO 图D.1 综合测试图形与尺寸 42
GB/T14515一2019 单位为毫米 样 试样G 试样 试样 空心佛钉 郑放直径2.0 金属化孔郑盘 7.5 焊盘直径3.0 焊盘直径止 1.8 焊盘直径2.5 X5.0 3x5.0 样G 试样K 试样D 导线 试样Y 8 品 两面 9.0 尊 20 -5.0 越基 试样 试样E 章盛直径4.0 2.5 1.0 10x7.5 100 试样x 州盘直径4n 导线宽3.0占 6.35 图D.2详细尺寸 43
GB/T14515一2019 录 附 资料性附录) 聚酷亚胺基挠性印制板使用说明 E.1储存及使用 产品在储存或使用过程中,当受潮或碰上化学药品时,为避免挠性印制板变色及劣化,需进行除湿 或把化学药品清除干净
导线防氧化处理的有效期是在制造后,在控制温湿度的房间内保存6个月,电镀、焊膏的场合有效 期 -年
产品拆封烘烤后,在相应的温湿度贮存条件下就在24h内使用安装)
E.2元件安装及安装至设备内 请调节好插装、紧固镖钉或铆钉接力
用力过大会造成挠性印制板基材破裂
E.3焊接作业 E.3.1 前处理 聚酰亚胶挠性印制板的基底膜及聚酰亚胺覆盖层非常容易吸潮,单张薄膜约经4h吸潮即饱和
如果在这种状态下进行回流焊或波峰焊时,由于温度急剧变化,极易造成FPC起泡分层
安装元件前 宜进行预烘前处理,以除去湿气,避免挠性印制板焊接时起泡分层
根据FPC的不同结构,预干燥条件 宜按照表E.1设置
推荐预干燥处理条件 表E.1 FPC 图形构成 增强材料 预干燥温度 干燥时间 无 80C >30min 仅有细线路图形、 单面 薄膜 80 " 例如信号线 玻璃布环氧板等 120 心 无 80C >30min 仅有细线路图形 80 薄膜 >1b 例如信号线 环氧玻璃布板等 >1h C 120 双面 无 120C >30min 有宽线路图形 >1h 薄膜 120C 例如接地线等场合 120C 环氧玻璃布板等 >2h 挠性印制板结构,图形不同,干燥时间也有所不同,这是因为结构不同,聚酰亚胺层与粘接剂层的水 分去除会产生干燥时间的差异
干燥后的FPC如果放置在一般环境(空调房内)下,宜在干燥后的当天完成组装焊接
如果在干燥 后的第二天进行焊接,宜将FPC放人防潮袋内保存,并在防潮袋内放人硅胶类干燥剂并密封,这样使用 期限可延长至一个月防潮袋种类不同,保存期限会有所变化而不同. 44
GB/T14515一2019 另外,回流爆后,如果放置一天后,再进行手工媒或波峰焊时,应重新在80C烘干1h后再进行 焊接
E.3.2焊接作业 如果焊接温度过高,时间过长,容易引起挠性印制板起泡分层
在加热过程中,使挠性印制板过度弯曲,烙铁头用力过大,都可能造成连接盘分层
调节至与FPC 相适应的工艺条件及作业场所条件
在进行作业时注意防止烫伤
为防止细小焊球及焊剂的飞溅,操作人员宜配戴防护眼镜
E.4废弃物的处理 废弃物按规定处理,不随便抛弃至未经允许的地方或水中,未经允许不得燃烧处理