GB/T38535-2020
纤维增强树脂基复合材料工业计算机层析成像(CT)检测方法
Testmethodonfiberreinforcedresinmatrixcompositesbyindustrialcomputedtomography(CT)
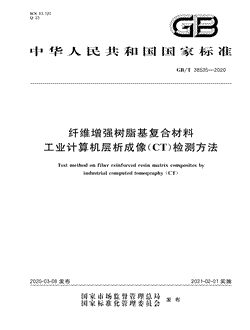
- 中国标准分类号(CCS)Q23
- 国际标准分类号(ICS)83.120
- 实施日期2021-02-01
- 文件格式PDF
- 文本页数15页
- 文件大小1.48M
以图片形式预览纤维增强树脂基复合材料工业计算机层析成像(CT)检测方法
纤维增强树脂基复合材料工业计算机层析成像(CT)检测方法
国家标准 GB/T38535一2020 纤维增强树脂基复合材料 工业计算机层析成像(CT)检测方法 Testmethodonfiberreinforeedresinmatrixeompositesby industrialcomputedtomographyCT 2020-03-06发布 2021-02-01实施 国家市场监督管理总局 发布 国家标涯花管理委员会国家标准
GB/38535一2020 前 言 本标准按照GB/T1.1一2009给出的规则起草
本标准由建筑材料联合会提出 本标准由全国纤维增强塑料标准化技术委员会(SAC/TC39)归口
本标准起草单位:兵器工业集团第五三研究所、常州天马集团有限公司、北京玻璃钢研究设计 院有限公司,山东祥瑞模具有限公司、兵器科学院宁波分院、矩阵科工检测技术(北京)有限公司、 航发北京航空材料研究院、航天材料与工艺研究所、西安航天复合材料研究所、天津三英精密仪器 股份有限公司、首都师范大学、北京航空航天大学
本标准主要起草人:赵付宝、王从科、董方旭、吕秀莲、汤振鹤、孟凡宝、朱忠裕、杨节标、倪培君、 刘莹、何方成、金虎
GB/38535一2020 纤维增强树脂基复合材料 工业计算机层析成像(CT)检测方法 范围 本标准规定了纤维增强树脂基复合材料工业计算机层析成像(CT)检测的检测原理、一般要求、检 测系统、对比试样、检测程序、结果评定、记录与报告等
本标准适用于纤维增强树脂基复合材料分层、裂纹、气孔、夹杂等内部缺陷的工业计算机层析成像 以下简称工业cT)检测
规范性引用文件 下列文件对于本文件的应用是必不可少的
凡是注日期的引用文件,仅注日期的版本适用于本文 件
凡是不注日期的引用文件,其最新版本(包括所有的修改单)适用于本文件
GB18871电离辐射防护与辐射源安全基本标准 GB/T29069无损检测工业计算机层析成像(CT)系统性能测试方法 GB/T29070无损检测工业计算机层析成像(cT)检测通用要求 GBZ98放射工作人员健康要求 GBZ117工业X射线探伤放射防护要求 检测原理 x射线透照被检件的某一截面,能量发生衰减,通过探测器采集射线衰减信息,将衰减信息输人计 算机,利用图像重建算法得到被检件截面透射后的二维或三维图像 -般要求 4.1检测人员 4.1.1从事纤维增强树脂基复合材料工业CT检测的人员应取得相应的技术资格证书
4.1.2检测人员的健康状况应符合GBZ98的规定,并经过辐射防护知识培训,取得资格证书
4.1.3检测人员在工作时,应佩戴个人剂量计,个人剂量计应定期送有关部门进行检测,检测人员的吸 收剂量限值应符合GB18871的规定
4.2检测环境 4.2.1检测室辐射防护安全要求应符合GBZ117,GB18871中的规定 4.2.2检测室温度10C一35C、相对湿度小于85%
4.2.3通风、照明等其他环境条件应符合GB/T29070中的规定
GB/T38535一2020 5 检测系统 5.1概述 工业CT检测系统由射线源、探测器系统、机械运动控制系统、计算机系统等组成
5.2系统性能要求 5.2.1技术要求 工业CT检测系统的空间分辨率应优于2.0lp/mm(10%调制度下),密度分辨率应优于0.5%
实 际缺陷检测能力、检测范围等性能应满足具体检测的要求
5.2.2功能要求 5.2.2.1工业CT检测系统应配备相关的图像处理软件,具有图像重建、尺寸测量、面积测量、CT密度 测量等功能
5.2.2.2工业CT检测系统的探测器为线阵探测器时,切片厚度应在使用范围内可调,以满足不同的检 测需要
5.3系统核查 工业cT系统的密度分辨率、空间分辨率等主要性能指标和机械控制系统的上升、下降、旋转等运 动控制性能应进行定期核查
密度分辨率和空间分辨率,宜采用GB/T29069进行测试
对比试样 6 对比试样的材料、结构尺寸及射线衰减特性应与被检件相同或相近
常见缺陷对比试样的制作可 参见附录A
检测程序 7.1被检件准备 目视检查被检件,表面应无影响工业cT检测的异物,若有应予以标注,并做好记录
7.2检测系统准备 按操作规程进行开机前的安全检查、射线机预热及训机、机械运动控制回零、射线源与探测器对齐、 探测器的本底校正和增益校正等
7.3工艺参数的选择 7.3.1射线控制 7.3.1.1 根据被检件的材料密度、结构、尺寸、最大穿透厚度等因素选择合适的射线能量,射线能量应保 证穿透被检件的最大穿透厚度
被检测部位最大穿透厚度可通过图1的箭头所示方向进行测量或 计算
7.3.1.2被检件的射线能量选择应综合考虑信噪比、对比度等因素,推荐选用X射线穿透率为10%
GB/38535一2020 20%时的射线能量
附录B给出了玻璃纤维/环氧树脂和碳纤维/环氧树脂在X射线穿透率为10% 20%时对应的透照电压
材料种类有变化时,应根据实际情况选用 圆环形 b)圆形 正方形 长方形 d 最大穿透厚度的确定 7.3.1.3在检测条件允许的情况下,宜选用较高的管电流
注,选用较高的管电流,可以提高射线源强度,提高投影图像的信嗓比,从而缩短扫描时间,提高扫描效率 7.3.1.4在射线能量和射线强度允许情况下,宜选择较小的射线源焦点尺寸
注;选用较小的焦点尺寸,可以提高图像清晰度和空间分辨率,利于细小缺陷的检出
7.3.1.5将滤波片放置在射线源一测,可减少X射线能谱中的低能成分,降低射束硬化的影响
7.3.2扫描位置的确定 扫描时,被检件扫描成像位置的计算公式见式(1). SDD sOD一 M 式中 SOD -射线源焦点至被检件中心的距离,单位为毫米(mm); SDD -射线源焦点至探测器之间的距离,单位为毫米(mm); M 几何放大倍数
几何放大倍数宜选择工业CT检测系统的最佳放大倍数,其计算见式(2) 1+(份 Mep 式中: M 最佳放大倍数; -探测器单元尺寸,单位为毫米(n mm; -射线源焦点尺寸,单位为毫米(n mm 当检测系统无法使用最佳放大倍数时,M应选择在保证机械安全及其他工艺参数允许条件下M 的最接近值 7.3.3扫描方式的选择 层析CT宜采用线阵探测器二代(TR)或三代OR)扫描方式;三维CT扫描宜采用面阵探测器
TR扫描方式适合于被检件几何尺寸较大,射线扇形束不应包含整个被检件的情形;OR扫描方式适合 于射线扇形束包含整个被检件的情形
7.3.4扫描参数的确定 7.3.4.1线阵探测器每圈采集投影数应不小于1800,面阵探测器每圈采集投影数应不小于36o. 7.3.4.2在检测条件允许情况下,宜选择较长的积分时间;较大的采集图像合并数和较高的图像采集 帧频
GB/T38535一2020 7.3.5切片的选择 7.3.5.1切片位置应根据被检件图纸或者检测要求,采用DR图像定位或直接测量确定
切片数量应 满足检测要求
7.3.5.2根据检测要求,选择合适的切片厚度
对于线阵探测器系统,切片厚度通过调节后准直器来设 置;对于面阵探测器系统,切片厚度由探测器探元纵向排列密度和软件设置确定
7.4工艺卡的编制 检测前,应编制工业CT检测工艺卡,工艺卡中一般应包括以下内容:工艺卡编号、被检件名称、纤 维种类、树脂种类,成型工艺、检测序号、检测标准、设备型号、检测工艺参数、切片厚度、检测示意图等
7.5扫描检测 按选择的检测工艺参数对对比试样进行检测,确认检测工艺参数
7.5.1 7.5.2将被检件放置在CT扫描系统转台中心,保证被检件的待检部位处于射线束中心区域且始终在 探测器的有效成像区域
进行被检件扫描,获取满足要求的CT图像
7.5.3 7.6图像重建和处理 7.6.1图像重建 7.6.1.1图像重建范围应大于被检件成像部位的最大断面,被检件图像应占整幅cT图像的2/3左右 CT图像不应具有影响结果评判的伪影
7.6.1.2重建矩阵大小应满足缺陷检测要求,最小缺陷特征至少由2×2个像素显示 7.6.2图像处理 7.6.2.1根据需要,选取灰度,放大、二维或三维等图像显示方式
7.6.2.2通过对比度、亮度调整方式等得到便于观察分析的图像
结果评定 8 8.1缺陷类型 8.1.1根据图像的形状、像素值,灰度值、尺寸等对缺陷进行分析判断,采用缺陷cT密度比值进行缺陷 类型的识别
8.1.2缺陷CT密度比值的计算见式(3)
A二B ×100% X= 式中 缺陷CT密度比值: -非缺陷区域CT密度5次测量的平均值; B -缺陷区域CT密度5次测量的平均值
8.1.3部分纤维增强树脂基复合材料缺陷类型和缺陷CT密度比值范围参见附录C
部分纤维增强树 脂基复合材料内部缺陷工业CT图参见附录D.
GB/38535一2020 8.2缺陷尺寸及位置 调整CT图像对比度,利用图像分析处理软件,对缺陷尺寸及位置进行测量并记录 记录与报告 g.1记录 记录至少应包括如下内容: 记录编号; a b 委托单位; 被检件:名称、纤维类型、树脂类型、成型工艺、数量等; c 检测设备;名称,型号等 d 检测工艺参数:射线源参数、扫描位置、切片厚度、切片位置、扫描方式、重建矩阵等 本标准编号及检测方法; g 检测示意图; h检测数据及结果; 检测人员; 检测日期等
i 9.2报告 报告内容至少应包括如下内容 报告编号 aa b) 委托单位; 被检件;名称、纤维类型、树脂类型、数量等; c 检测日期 d 本标准编号及检测方法; e 检测工艺参数:射线源参数、扫描位置、切片厚度、切片位置等; 检测结果 g 检测人员、审核人员及批准人员等
h)
GB/T38535一2020 附 录 A 资料性附录) 对比试样的制作 气孔对比试样 A.1 气孔对比试样的材料应与被检件射线吸收特性相同或相近,基本结构见图A.1
A.1.1 A.1.2气孔对比试样直径D与被检件最大穿透厚度尺寸应一致,对比试样高度H为10 mm A.1.3气孔缺陷直径d分别为0.20mm,0.40mm,0.60mm.,0.80mm、,1.0nmm 单位为毫米 1/4业 说明 -气孔对比试样直径; D 气孔缺陷直径
图A.1气孔对比试样结构图 A.2夹杂对比试样 A.2.1夹杂对比试样材料应与被检件射线吸收特性相同或相近,基本结构见图A.2 A.2.2夹杂对比试样直径D与被检件最大穿透厚度尺寸应一致,对比试样高度H为10 mm
A.2.3夹杂直径d分别为0.20nmm,0.40mm,0.60mm、0.80mm,1.0mm A.2.4夹杂缺陷材质应根据检测需求确定
GB/38535一2020 单位为毫米 /40 说明: 夹杂对比试样直径 夹杂缺陷直径
图A.2夹杂对比试样结构图 A.3分层对比试样 A.3.1分层对比试样的材料应与被检件射线吸收特性相同或相近,基本结构见图A.3
A.3.2分层对比试样外径为D、内径为D.,高度为H,具体尺寸可根据实际需要进行设计
mmmm0,60mmm
A.3.3分层缺陷材质为聚四氟乙烯膜或聚酯膜,薄膜厚度为0.10n 单位为毫米 说明 H 分层对比试样高度; 分层对比试样外径; D D. 分层对比试样内径" w 分层缺陷宽度 图A.3分层对比试样结构图
GB/T38535一2020 A.4裂纹对比试样 A.4.1裂纹对比试样的材料应与被检件射线吸收特性相同或相近,基本结构示意见图A.4
A.4.2裂纹对比试样上半部分为两个半圆柱形,直径D与被检件最大穿透厚度尺寸应一致,裂纹宽度 nmm0.401 为0.10 mm,高度H根据实际需要进行设计
A.4.3裂纹对比试样下半部分为正方体,其边长L根据实际需要进行设计
单位为毫米 说明: H -裂纹对比试样高度 裂纹对比试样半圆柱直径; D 正方体边长 裂纹缺陷宽度 图A.4裂纹对比试样结构图
GB/38535一2020 附录 B 资料性附录 穿透曲线 穿透率定义 B.1 射线穿透率为射线穿透过物体后,探测器接收到的射线光子数与射线源发射出的光子数之比 B.2穿透曲线定义 被检件(材料厚度等)与工艺参数(电压、电流等)之间关系的曲线
B.3制作步骤 B.3.1确定被检件合适的射线穿透率
固定阶梯试样的扫描位置、射线源焦点等参数,改变电压、电流,在探测器相应范围内,对其进行 B.3.2 X射线透照,得到相同穿透率下不同厚度的透照电压
B.3.3根据试验数据绘制透照电压和穿透厚度的关系曲线
B.4穿透曲线 碳纤维/环氧复合材料穿透率为10%20%时的X射线穿透曲线见图B.1,玻璃纤维/环氧复合材 料穿透率为10%一20%时的x射线穿透曲线见图B.2
400 350 300 250 200 150 100 50 20 3o 5o s 70 说明 所度.m 穿透率10%; -穿透率15%; -穿透率20%
探测器为NTB640线阵探测器;碳纤维/环氧树脂质量分数35%
图B.1碳纤维/环氧x射线穿透曲线
GB/T38535?2020 400 350 300 250 200 150 100 50 10 20 40 50 60 70 30 /mm ?: -?10% ?15% -?20% ??NTB640?;?/?35% ?B.2?/X?? 0
GB/38535一2020 附录 C 资料性附录 缺陷类型与缺陷CI密度比值范围 碳纤维/环氧、碳纤维/酚醛,玻璃纤维/环氧、高硅氧/酚醛等纤维增强树脂基复合材料常见缺陷类 型的缺陷cT密度比值范围见表C.1
表c.1缺陷类型 缺陷类型 缺陷CT密度比值 分层 5%30% >30% 气孔 高密度夹杂 注上述纤维增强树脂基复合材料的树脂质量分数为20%一50% 11
GB/T38535?2020 ? D ??) ???CT??CT?? D.1?D.1????????CT? ?????? ?????? b ? ??????? ?????? ?D.1????????CT? 12
GB/T38535一2020 气孔 分层 碳纤维增强复合材料分层缺陷图 高硅氧增强复合材料气孔缺陷图 图D.1续 D.2缺陷CT密度比值 图D,1中缺陷对应的cT密度比值见表D.1
表D.1缺陷CT密度比值列表 序号 缺陷类型 缺陷c值比值 对应的CT图像 气孔 46.1% 图D.1a 夹杂 -87.6% 图D.1b) 分层 8.6% 图D.1lc) 夹杂 176.1% 图D,ld 45.5% 气孔 图D.l e 25.9% 图D,.1 分层 13
纤维增强树脂基复合材料工业计算机层析成像(CT)检测方法GB/T38535-2020
纤维增强树脂基复合材料是由树脂和纤维增强材料组成的一种高性能材料。这种材料具有轻质、高强度、耐腐蚀等特点,在航空、汽车、建筑等领域有着广泛的应用。
传统的纤维增强树脂基复合材料检测方法主要依靠人工检验或者单一非破坏性检测方法,如超声波检测、X射线检测等。然而,这些方法都存在缺陷,如人工检验缺乏标准化、重复性差,单一非破坏性检测方法无法全面评估材料的内部结构。
因此,计算机层析成像(CT)技术作为一种新兴的无损检测技术,被广泛应用于纤维增强树脂基复合材料的检测中。CT技术通过对样品进行多角度的X射线扫描,再通过计算机重建出样品的三维图像,从而实现对样品的全面检测。
GB/T38535-2020是我国针对纤维增强树脂基复合材料使用CT技术进行检测的标准。该标准规定了CT图像质量要求、检测方法和结果判定等内容,保证了检测结果的准确性和可靠性。
在具体的纤维增强树脂基复合材料检测中,CT技术可以进行以下方面的检测:
- 样品的尺寸和形状
- 孔隙率和孔径分布
- 裂纹和缺陷
- 纤维方向和分布
通过对这些方面的检测,可以全面地评估纤维增强树脂基复合材料的性能和质量。同时,CT技术还具有高可重复性、高精度、高效率等优点,大大提高了检测效率。
总之,计算机层析成像(CT)技术在纤维增强树脂基复合材料的检测中具有不可替代的作用。GB/T38535-2020标准的出台,更是为该领域的发展提供了坚实的保障。