GB/T41154-2021
金属材料多轴疲劳试验轴向-扭转应变控制热机械疲劳试验方法
Metallicmaterials—Multiaxialfatiguetesting—Axial-torsionalstrain-controlledthermo-mechanicalfatiguetestingmethod
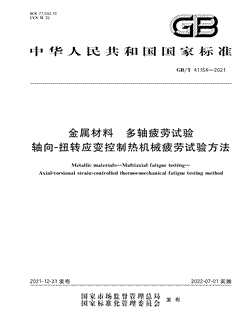
- 中国标准分类号(CCS)H22
- 国际标准分类号(ICS)77.040.10
- 实施日期2022-07-01
- 文件格式PDF
- 文本页数20页
- 文件大小1.64M
以图片形式预览金属材料多轴疲劳试验轴向-扭转应变控制热机械疲劳试验方法
金属材料多轴疲劳试验轴向-扭转应变控制热机械疲劳试验方法
国家标准 GB/T41154一2021 金属材料多轴疲劳试验 轴向-扭转应变控制热机械疲劳试验方法 Metealiematerals一Nutiasialtatiguetesting一 Axial-torsionalstrain-eontrolledtherm0>meehanicalfatiguetestingmethod 2021-12-31发布 2022-07-01实施 国家市场监督管理总局 发布 国家标涯花管理委员会国家标准
GB/41154一2021 目 次 前言 范围 2 规范性引用文件 术语和定义 符号和说明 试验装置 试样 试验程序 8 试验结果 试验报告 附录A资料性) 材料常数测定 l6 参考文献
GB/41154一2021 前 言 本文件按照GB/T1.1一2020<标准化工作导则第1部分;标准化文件的结构和起草规则》的规定 起草
请注意本文件的某些内容可能涉及专利
本文件的发布机构不承担识别专利的责任
本文件由钢铁工业协会提出 本文件由全国钢标准化技术委员会(SAC/TC183)归口
本文件起草单位:北京工业大学、冶金工业信息标准研究院、中航工业沈阳飞机设计研究所、航 发北京航空材料研究院、航发商用航空发动机有限公司、中机试验装备股份有限公司深圳万测试 验设备有限公司、上海海洋高端装备功能型平台有限公司
本文件主要起草人;尚德广、李道航、童莉、李芳代.左林玄,曲林锋、刘建中陈勃、张成成、杨秀光 黄星、周路海、孙鹏、汪宏斌、侯慧宁
GB/41154一2021 金属材料多轴疲劳试验 轴向-扭转应变控制热机械疲劳试验方法 范围 本文件规定了轴向-扭转应变控制下金属材料多轴热机械疲劳试验的试验装置,试样,试验程序,试 验结果和试验报告
本文件适用于金属薄壁管试样在恒定轴向机械应变循环,恒定剪切应变循环和恒定温度循环条件 下,对应任意恒定的循环应变比、恒定的轴向机械应变-剪切应变相位差和恒定的轴向机械应变-温度相 位差的试验
注1循环周次通常考虑低周疲劳的范略,即疲劳寿命N<10 注2,试验的温度一般不超过1200c
规范性引用文件 下列文件中的内容通过文中的规范性引用而构成本文件必不可少的条款
其中,注日期的引用文 件,仅该日期对应的版本适用于本文件;不注日期的引用文件,其最新版本(包括所有的修改单)适用于 本文件
GB/T228.1金属材料拉伸试验第1部分;室温试验方法 GB/T228.2金属材料拉伸试验第2部分;高温试验方法 GB/T6394金属平均晶粒度测定方法 GB/T7314金属材料室温压缩试验方法 GB/T10623金属材料力学性能试验术语 GB/T12443金属材料扭矩控制疲劳试验方法 GB/T16825.1静力单轴试验机的检验第1部分拉力和(或)压力试验机测力系统的检验与 校准 GB/T25917.1单轴疲劳试验系统第1部分;动态力校准 GB/T33812金属材料疲劳试验应变控制热机械疲劳试验方法 GB/T40410金属材料多轴疲劳试验轴向-扭转应变挖制方法 JJF1637廉金属热电偶校准规范 JJG141工作用贵金属热电偶 扭转试验机 JJG269 JG556轴向加力疲劳试验机 JJG617数字温度指示调节仪 JG762引伸计 术语和定义 GB/T10623GB/T33812和GB/T40410界定的以及下列术语和定义适用于本文件
GB/T41154一2021 3.1 轴向-扭转热机械疲劳axial-torsionaltherm-meehaniealfatigue:AT-TMr 同时存在轴向机械应变循环,剪切应变循环和温度循环的疲劳行为
3.2 轴向应力axialstress 按室温下原始横截面积计算的轴向方向上的应力分量
注:圆管试样的轴向应力与轴向力的关系见公式(1) 4F R(,- 3.3 轴向应变axialstrain 引伸计标距长度的变化量AL
与引伸计标距长度L,的比值
注:用公式(2)计算
=Al/L 3.4 轴向热应变axialthermalstrain" E 由于温度变化产生的自由膨胀所对应的轴向应变(3.3) 3.5 轴向机械应变axialmeehaniealstrain 独立于温度,并与试样上施的轴向力有关的轴向应变(3.3)
3.6 轴向总应变axialtotalstrain Eo 轴向机械应变(3.5)和轴向热应变(3.4)的代数和
注用公式(3)计算 e=E十E 3 3.7 同相位inphase 在相同频率下,轴向机械应变循环与温度循环相位差为0`的相位关系,或轴向机械应变循环与勇 切应变循环相位差为0"的相位关系
3.8 非同相位 ofphase out 在相同频率下,轴向机械应变循环与温度循环相位差不为0°的相位关系,或轴向机械应变循环与 奠切应变循环相位差不为0"的相位关系
符号和说明 表1中的符号适用于本文件
GB/41154一2021 表1符号说明和单位 符号 说明 单位 d. 试样夹持端外径 mm 试样标距段内径 d mm 试样标距段外径 mm 弹性模量 MPa 轴向力,载荷 N MP 剪切模量 试样全长 mmm Lo 试样夹持端长度 mmm 夹持淄和过渡段总长度 LGr mm L 引伸计标距长度 mm L 引伸计标距长度的变化量 mmm L 试样中间平直段的长度 mmm M Nmm 扭矩 周,cyele N 失效循环数 2N 失效反复数 反复数 循环数 周,eydle 过渡弧段半径 mm Ra 表面粗糙度 mm 温度 试样引伸计标距段的壁厚 mn 剪切应变 mmm/mm, 轴向应变 mm/mmm, 轴向机械应变 mm,% mm 轴向热应变 E, mm/mmm, " 轴向热应变范围 Ael mm/mm, 轴向总应变 mm/mm,% MPa 轴向应力 剪切应力 MPa 注:本文件使用上述符号时所带下脚标含义如下 机械(mechanical).o tot 总(total),th -热(thermal),m 外(outside), 内inside).
GB/T41154一2021 5 试验装置 5.1试验机 5.1.1 -般要求 5.1.1.1试验应在平稳起动且力和扭矩过零时无反向间隙的轴向-扭转试验机上进行
试验机应能按 照指定的波形控制轴向应变和剪切应变,可以是液压、电子或机械加载的
5.1.1.2横梁处于工作位且加载链准确对中(平行和同心)时,载荷机架应有较高的侧向刚度
5.1.1.3整个加载链(包括轴向力传感器,扭矩传感器、拉杆/夹具和试样)应有较高的侧向刚度以减小 试样的弯曲
5.1.2轴向力、扭矩测量系统 5.1.2.1 轴向力传感器应适合于试验过程中施加的轴向力,扭矩传感器应适合于试验过程中施加的 扭矩
5.1.2.2轴向力传感器、扭矩传感器应能够进行温度补偿,且温度每变化1C,零点漂移或温度敏感度 的变化应不超过传感器满量程的0.002%
5.1.3试样夹持装置 5.1.3.1夹持装置在试验过程中传递循环轴向力值和扭矩值给试样时应没有反向间隙,其几何特性应 能确保同轴度满足5.1.4的要求
注最好的设计方案是尽量将机械连接数降到最小
51.32火持装置应确保一系则后皱试样同轴度的重复性
5.1.3.3夹持装置的材料应选择在整个试验条件范围都能够正常工作的材料 5.1.4加载链的同轴度 对试验机架(包括夹具)应使用一个试样进行同轴度校正,该试样的几何形状宜尽可能与试验中带 轴向-扭转引伸计的试样相似
允许的最大试验机弯曲应变不大于零载时50微轴向应变或所加轴向机 械应变的5%,二者取较大者
上述校正应于每12个月或者有下列情形时进行 aa 作为新机服役检测的一部分 b试样的事故性破坏之后,除非能说明同轴度不受影响;s c 对加载链做了任何调整
5.2应变测量系统 5.2.1应使用轴向-扭转引伸计测量试样的轴向应变和剪切应变
5.2.2轴向-扭转引伸计应适合于长试验周期下测量动态应变量,并且有最小的漂移、滑动或仪器的滞 后
应直接测量试样标距长度的轴向变形量和扭转变形量
5.2.3轴向-扭转引伸计的传感器应防止由于热波动引起的漂移 5.2.4鉴于轴向-扭转热机械疲劳试验温度的瞬时特性,宜对轴向-扭转引伸计实行主动冷却,保证试验 过程中轴向-扭转引伸计的传感器部分保持恒温
5.2.5接触式轴向-扭转引伸计的动态设计应保证在与其接触的试样区域发生侧向或角度移动时,轴 向-扭转引伸计接触点或刀口处不发生滑动
5.2.6轴向-扭转引伸计的接触压力和操作时的力不应损伤试样表面,并不应与轴向-扭转引伸计接触
GB/41154一2021 或刀口部位引起裂纹的萌生
5.3加热系统 5.3.1加热系统应能提供系列轴向-扭转热机械疲劳试验的最大加热和冷却速率
5.3.2为了减小直接感应加热系统产生的试样径向温度梯度,宜选择频率足够低的加热装置(一般在 几百千赫兹范围或更低)
这将有助于减小加热过程中的趋肤效应
5.3.3试验过程中应使用热电偶,高温计、红外测温装置或其他温度测量装置测量试样温度
5.3.4对于热电偶,应保证其与试样的直接接触,并且不会在触点处发生失效
注,常用的附着方法是在标距外点焊或捆绑和压套的方法将热电偶固定在试样表面上 5.3.5如果用光学高温计测量标距部分的温度,应采取措施标定出试验持续过程中试样热辐射可能的 变化
可行的方法包括双色高温计和试样表面预氧化处理
5.4试验监控仪器 5.4.1宜采用能进行数字采集和处理轴向力、扭矩、轴向变形、扭转变形温度和循环数据的自动化系 统
数据点的采样频率应能确保迟滞回线尤其是反转区域的正确表征
不同的数据采集方法将会影响 每一回线所需的数据点数
一般每一回线需要200点
5.4.2也可选择其他能够测量相同数据的模拟系统,但应包括 两个X-Y-Y记录仪,一个用于记录轴向力、轴向变形和温度的迟滞回线,另一个用于记录扭 矩、扭转变形和温度的迟滞回线 个连续记录仪,用于记录几个与时间相关的参数轴向力、轴向变形、扭矩、扭转变形和温度; 每一信号的峰值检测装置; -循环计数器等
5.4.3记录仪可用能以照片或模拟形式重现记录信号的存储装置取代
这些装置记录信号的速率应 大于记录仪的最大转动速率,并且允许暂存的记录随后以较慢的速率回放
5.5检查和校准 5.5.1试验机和其控制及测量系统应定期进行检查
特别是以下每一个传感器和其相关的电器应作 为一个单元校准: -轴向力测量系统应按照GB/T16825.1和GB/T25917.1或JJG556进行校准,其准确度应为 1级或优于1级; -扭矩测量系统应满足GB/T1243要求并按照JG2进行校准,其准确度应为1级或优于 1级; 温度测量系统应按照JJG617进行校准; 热电偶应按照JG141或JJF1637进行校准; 引伸计应按照JG762进行校准,其准确度应为1级或优于1级
5.5.2每系列试验之前应检查轴向-扭转引伸计的原始标距,应利用分流电阻或其他合适的方法对轴向 力传感器、扭矩传感器和轴向-扭转引伸计进行确认,并且对热电偶或高温计确认
试样 6.1 -般要求 本文件以圆形截面的薄壁管为试样进行试验
为了避免循环载荷下的不稳定性,试样标距段的壁 厚应满足平均直径与壁厚的比值大于或等于10:1的薄壁管准则
对于多晶体材料,应保证壁厚部分
GB/T41154一2021 至少存在10个晶粒来保持各向同性
注,试样平均直径d
=(d,十d,)/2. 6.2材料要求 应预测试样的拉伸和压缩性能
设计试样时,应按GB/T228.1.GB/T228.2和GB/T7314测定 拉伸和压缩性能
如需要测定材料的平均晶粒尺寸,应按GB/T6394进行测定
推荐试样形状如图1所示
试样设计时,应保证同心度,避免附加弯曲应力
注图中标引符号及其说明见表2
图1薄壁管试样 6.3尺寸要求 试样的具体尺寸要求见表2
表2薄壁管试样的尺寸要求 名称 单位 尺寸要求 试样引伸计标距段的壁厚( mm 0.5d dl 试样标距段外径 dl mm 14t士3t 试样标距段内径(d mm 0.85dl士0.04dl 试样夹持端的外径(de mm 1.6d
士0.4d
45" 倒角(C 过渡狐段半径( R mmm 3.2d
士0.4ddl 试样全长 mm 8.5dl士l.5d 试样夹持端长度 mm 2dl.十0.3dl LG 爽持端和过渡段总长度(Lr mm 3.5d 试样中间平直段的长度L l.5dl
十0.5d mm 引伸计标距长度 mnm 0.9d
士0.3ddl d
和d的同心度 mnm 士0.0151 试样引伸计标距段的壁厚()的典型取值范围 mmm 2.0十0.5 6.4附加说明 6.4.1非多晶体材料(如单晶材料和定向凝固材料)管状试样的壁厚应确保充分包含该材料的典型微 观结构
6.4.2通常在包含扭转的循环载荷下,疲劳寿命与管状试样的内外径之比(d/d.)有关
因此,应注意 比较材料相同但具有明显不同内外径比值试样的疲劳寿命
承受轴向-扭转热机械疲劳载荷时,在内外
GB/41154一2021 径比值的标准取值范围内试样疲劳寿命的差别不应过大
6.5试样制备 6.5.1概述 试样加工可能会在试样表面引人残余应力从而影响试验结果
残余应力可能来源于加工过程中的 热梯度、材料变形相关的应力或显微结构的变化
高温试验时残余应力影响较小,因为残余应力在开始 的热循环中已部分或全部释放
然而还是要在加工最终阶段通过适当的方法减小其影响,尤其是在最 终的抛光阶段
对于较硬材料,首选以下磨削方法而不是刀具加工(车或)
试样内表面应研磨并抛 光,以防止疲劳裂纹在试样内表面萌生 研磨;在离最终尺寸还差0.1mm时,以每道工序不超过0.005mm的磨削量研磨 抛光;对于最终的0.025mm,用逐级降低粒度的砂纸对试样进行抛光;最后的抛光方向宜平行 于试样的轴向
试样中间平直段的内表面与外表面应从一端到另一端一次性加工成型
应在最终精加工完成后对 试样的尺寸进行检查,采用的检查方法应不改变试样的表面状态
6.5.2材料显微组织的改变 材料显微组织的改变可能与机加工引起的温升和变形有关
温升和变形可能造成试样发生相变或 更常见的表面再结晶,直接的后果是被测材料原始状态的改变使试验结果无效
因此应采取措施避兔 此类情况的发生
6.5.3污染物去除 某些元素或化合物的出现会破坏材料的力学性能
典型的例子是氯元素对钢材或钛合金的影响 因此,应避免使用含这类元素或化合物的产品(切削冷却液等)
保存试样之前宜去除试样表面的油污 并清洗干净
6.6取样和标记 6.6.1半成品或构件试验材料的取样操作可能对试验结果产生重要的影响,因此取样时需要充分了解 具体的状况
6.6.2如适用,试验报告应附有一张取样图,并应清楚地标明以下内容 各个试样的位置; 半成品的加工方向特征(例如轧制、挤压方向等); 各个试样的标记
6.6.3试样在整个准备过程都应有唯一性标识
标识可以采用任何可靠的方法标记在试样上,只要标 识在加工过程中不会消失和不影响试验结果
试验前标识应分别标记在试样两端
试样的表面状态 6.7 6.7.1试样的表面状态会对试验结果产生影响,这种影响通常与以下一个或几个因素有关 试样的表面粗糙度; 存在残余应力; -材料显微组织的变化 污染物的介人 6.7.2试样的表面状态通常用表面粗糙度或同等意义的参量表征(如,十点的粗糙度或不平度的最大
GB/T41154一2021 高度)
表面粗糙度对试验结果的影响在很大程度上与试验条件有关,试样的表面腐蚀或非弹性变形会 降低其影响
6.7.3任何试验条件下试样平行段内外表面粗糙度(Ra)宜小于0,2pm
注使用磨粒流工艺对内表面进行抛光,能够达到建议的内表面粗糙度
6.7.4另一个不包含在表面粗糙度中的重要参量是存在于局部的加工划痕
加工的最后工序应去除 所有环向的划痕
在磨削之后宜对试样进行纵向抛光
在低倍(约20倍)下检查试样应没有环向的 划痕
6.7.5如果在试样表面粗加工完成后再进行热处理,应在热处理后对试样表面进行抛光
如果不能抛 光,则热处理应在真空环境或惰性气体保护条件下进行,以避免试样的氧化
同时宜去除热处理引起的 应力
6.7.6热处理应不改变被测材料的显微结构特征
热处理及机加工的详情应在试验报告中注明
6.8存放和处置 6.8.1试样制备完成后应妥善存放以避免任何损害(接触刮伤或氧化等)
宜采用单独的盒子或带封 头的管保存试样
在一些特定情况下,有必要将试样存放在真空瓶或者放有硅胶的干燥器中 6.8.2应减少对试样的拿取操作,以避免损伤
6.8.3对试样进行标记时应特别小心
宜在试样的两端标记试样,以便试样断裂后每段试样都可以被 识别
试验程序 7.1实验室环境 轴向-扭转热机械疲劳试验结果的准确性与采用的试验方法及环境有关
试验应在以下合适的环 境下进行 恒定的环境温度; 最小的大气污染(如灰尘化学燕气等). 没有能够影响试验机控制和数据采集的外部电信号, 最小的外部机械振动
7.2试样安装 试样应以最小外力夹紧,注意在安装接触式轴向-扭转引伸计时,不应划伤管状试样标距段内外 表面
7.3温度控制 7.3.1温度循环在整个试验过程中应保持稳定
注:在整个试验过程中保持稳定的温度循环的重要性见参考文献[2]
7.3.2在零载荷条件下温度循环的任一给定温度点(T),轴向热应变(e由)的滞后不应大于相应的轴向 热应变范围(Ae铺)的5%
7.3.3整个试验期间,控温装置例如热电偶在循环内任何给定时刻显示的温度与预设值的偏离不应 超过士5C或者稳定温度(即已建立温度的动态平衡)范围值的土1%,取较大者
7.3.4整个试验期间,非控温传感器在循环内任何给定时刻显示的温度不应超过稳定温度值的士3c
7.4温度梯度 7.4.1试验开始加载之前,轴向、径向、环向的温度梯度应在零载荷热循环条件下测量并优化
标距段
GB/41154一2021 热循环的温度梯度应当与轴向-扭转热机械疲劳试验循环的相同
7.4.2试样标距段在循环期间任何给定时刻允许的轴向最大显示温度梯度应为2%AT或10C的较 大者
其中,AT是动态条件下测得的温度循环范围[以摄氏度(C)表示]
注,目前没有标准方法用于温度测量装置的动态标定
因此,为了应用,与非静态条件下要求相关的所有温度都是 在静态下标定的
7.4.3宜检查和限制轴向标距段内试样厚度方向的温度梯度(即径向梯度)
这种梯度在使用高的温 度变化速率时特别受关注
管状试样径向温度梯度可通过同一轴向位置内外表面附着的热电偶测量 得到
7.4.4在循环过程中也可用光学高温计测量表面温度梯度
7.5轴向机械应变和剪切应变控制 7.5.1轴向机械应变和剪切应变的循环波形应在整个试验过程中保持恒定 e,在循环的任一时刻不应偏离轴向机械应变范围要求值的2%
轴向 7.5.2轴向机械应变e= 机械应变范围的要求值根据总应变和补偿热应变之间的差得到
轴向机械应变和温度都应在整个试验 期间保持循环稳定,在整个试验过程中都应保持同步,不应有累积误差
7.5.3剪切应变在循环的任一时刻不应偏离剪切应变范围要求值的2%
注:剪切应变理论上不受温度变化的影响,在试验过程中不需要考虑扭向热应变补偿,见参考文献[3]、[1
7.6轴向热应变补偿 7.6.1一般要求 为了得到需要的轴向机械应变,应在试验中主动补偿由于温度产生的轴向热应变
7.6.2补偿方法 7.6.2.1概述 有几种方法可以用来补偿产生的轴向热应变
这些方法取决于特定的试验装置和控制软硬件
然 而最主要的目的是在循环内给定点提供足够精确的轴向热应变补偿,并由此准确地控制轴向机械应变
7.6.2.2和7.6.2.3中给出了常用的两个方法
7.6.2.2方法1 试验开始前通过记录(在零负荷下)轴向热应变的自由膨胀作为试样温度的函数补偿轴向热应变
这里的温度循环应与随后的轴向-扭转热机械疲劳试验的温度循环相同
这些补偿可以拟合成适当的 代数方程或函数段(典型的一个升温部分的函数、一个降温部分的函数),其中温度是独立变量
这些函 数关系之后用于计算轴向-扭转热机械疲劳试验即时的补偿应变
补偿关系可以用公式(4)表示
=e.()十e(T) Etot=! 式中: T !时刻的温度
7.6.2.3方法2 试验开始前通过记录在零负荷下轴向热应变的自由膨胀作为循环时间的函数补偿轴向热应变
这 里的温度循环与随后的轴向扭转热机械疲劳试验的温度循环相同
这些记录值在循环期间相应的时 间被调用
补偿关系式如公式(5). 5 e=e()el( 注;式中ea()不是常数
GB/T41154一2021 7.6.3轴向热应变补偿检查 7.6.3.1 方法2没有提供轴向机械应变的闭环控制,如果试样温度与期望值不一致,可能会导致明显的 过应变
通常不能十分精确地得到自由轴向热应变范围,将其分成等时间的或与温度相关的增量,在后 续补偿计算就利用该恒定增量值
这种方法不能解释正常的非线性膨胀(a),也不能解释试验过程中 的温度滞后
方法1在试验过程中出现温度问题时,会减小对试样的损伤
7.6.3.2轴向热应变补偿的精度应在轴向-扭转热机械疲劳试验开始之前检查,检查的方法是以轴向机 械应变控制模式使试样在零轴向机械应变下承受温度循环
这里应用轴向热应变补偿方法对温度产生 的轴向热应变进行主动补偿
7.6.3.3循环过程中,产生的最大可接受的轴向应力应由试验的峰值轴向机械应变及相应弹性模量计 算,两个温度下发生的最大和最小轴向应力见公式(6)和公式(7) d,=2%emm×E(丁在Em时 dm=2%em.m×E(T在eam时 式中 -可接受的最大轴向应力,单位为兆帕(MPa); G 最大轴向机械应变,单位为毫米每毫米(mm/mm). emx"" 可接受的最小轴向应力,单位为兆帕(MPa); omin 最小轴向机械应变,单位为毫米每毫米(mm/mm)
Emin. 7.6.3.4可接受应力应不大于(o一d)/2
7.6.3.5零轴向机械应变下测量的温度循环产生的轴向应力绝对值不应超过上面确定的可接受轴向应 力范围,确保在正式试验过程中控制的轴向机械应变范围精度在2%轴向机械应变范围之内
7.7轴向机械应变和剪切应变、轴向机械应变和温度的相位差 7.7.1整个试验过程,轴向机械应变和剪切应变的相差在循环期间的任意时刻漂移不应超过期望相 位"
7.7.2轴向机械应变和温度如果用共同的时钟控制(推荐采用)时,轴向机械应变和温度的相位通常不 成为问题
7.7.3用于评估轴向机械应变和温度相位差的温度值应是热循环过程的响应值(反馈值),而不应是指 令值 7.7.4当轴向机械应变和温度使用各自独立的时钟控制时,用以下的方法评估轴向机械应变和温度之 间的相位 用于评估轴向机械应变和温度的相位差的轴向机械应变由循环期间的瞬时总应变减去补偿的 轴向热应变计算得到,如公式(8) 8 整个试验过程,轴向机械应变和温度的相位差在循环期间的任意时刻漂移不应超过期望相 位5"
7.7.5试验过程中要特别注意温度相位的响应变化
宜通过测量同一时刻的轴向机械应变和温度测 定相位漂移,并与起始循环比较得到相位漂移量
应当在整个试验过程检测相位的漂移
7.7.6典型的加载波形有以下四种 轴向机械应变循环和剪切应变循环同相位,轴向机械应变循环与温度循环同相位(MIPTIP) 见图2; 轴向机械应变循环和剪切应变循环同相位,轴向机械应变循环与温度循环180'非同相位 MIPToP),见图3 -轴向机械应变循环和剪切应变循环90”非同相位,轴向机械应变循环与温度循环同相位 10
GB/41154一2021 MOPTIP),见图4; 轴向机械应变循环和剪切应变循环90'"非同相位,轴向机械应变循环与温度循环180"非同相 位(MOPTOP),见图5
加载波形也可为其他相位关系
标引序号说明: -轴向机械应变; -剪切应变; -温度
图2MIPP加载波形图 标引序号说明 -轴向机械应变; -剪切应变; 温度
图3MIPIoP加载波形图 11
GB:/T41154一2021 /s 标引序号说明 -轴向机械应变; 剪切应变; -温度
图4MoPTP加载波形图 标引序号说明 -轴向机械应变; -剪切应变; 温度 图5MoPIoP加载波形图 7.8指令波形 轴向机械应变,剪切应变和温度的波形在试验过程中应一直重复且保持不变
在一项试验或试验 12
GB/41154一2021 计划中经常希望采用相同的循环周期,这样在试验过程中轴向机械应变(剪切应变)范围的变化将导致 轴向机械应变(剪切应变)速率的变化
同一系列试验轴向机械应变(剪切应变)的速率变化不宜超过 5倍
7.9试验开始 7.9.1弹性模量和剪切模量测量 应至少检查室温和循环最高温度下的拉伸和压缩模量值、剪切模量值(见附录A),确保轴向-扭转 引伸计没有滑动并处于良好的工作状态
这样确定的模量值不应超过已知模量值的5%,如果模量值 超过已知模量值的10%,不应继续进行试验
7.9.2热膨胀测量 应测量和记录整个轴向-扭转热机械疲劳循环温度范围的热膨胀
在与轴向-扭转热机械疲劳试验 相同的热循环条件下,应在控制载荷为零的状态下测量达到动态温度平衡时每根试样的热膨胀 7.9.3轴向机械应变和剪切应变开始加载 轴向机械应变和剪切应变应逐渐接近它的最小绝对值,当达到循环中所对应的温度时,立即开始加 载给定相位的轴向-扭转热机械疲劳循环
对于总应变幅较大的试验,为了防止过冲,可经过几个循环 后逐渐将轴向机械应变和剪切应变增加到试验所需的应变幅
对于呈现不连续屈服现象的材料可逐级 增加应变幅
7.10试验监控 应监控整个试验过程的试样温度、轴向总应变和剪切应变等控制变量
轴向机械应变和剪切应变 应按7.5的要求进行控制,试验温度条件应按7.3的要求控制
7.11失效判据 7.11.1当试样在标距以内分离或断裂成两半时,则认为试样失效
应记录所有失效位置
7.11.2当试验轴向力(扭矩)下降到稳定峰值轴向力(扭矩)的某一规定值常在5%一50%之间)认为 试样失效
试样表面的复型技术可用于判定试样的失效
这种方法需要在预定的循环间隔中断疲劳试验 7.11.3 见7.13),做试样表面的复型,例如使用醋酸纤维膜
随后检查用膜连接起来的表面裂纹,当观察到的 最大裂纹扩展到规定的长度(一般在0.1lmm~1lmm 之间)时,判定为失效
7.12试验的终止 7.12.1当满足选定的试验结束条件时终止试验
为了减小试样和裂纹表面的腐蚀和氧化,以便试验 后的检查,只要试验终止,应立即停止加热
如果失效判据不是试样断开,应确保终止试验期间不过载
7.12.2宜对失效试样进行后续的金相和断口分析
由此确认各种失效机理,并有助于了解判废试验 结果的非正常现象
7.13试验中断 如果试验中断,试验重新开始时应保证没有明显温度、轴向力或轴向机械应变,扭矩或剪切应变的 过冲
下面给出一个试验中断后重新启动的例子
示例;在中断应变控制的轴向扭转热机械疲劳试验之前,记录最后3个循环的最大和最小轴向力,扭矩
试验中断 13
GB/T41154一2021 之后,将试样冷却到室温之前记录几个自由的热循环(在零载荷控制下)并注明最大最小应变值
轴向热应变范围不应 改变,但由于标距的改变可能会漂移
卸除轴向扭转引伸计之前记录室温应变值,并标记轴向-扭转引伸计在试样上的 位置
试样复形和仔细地重新安装试样之后,轴向-扭转引伸计安装在相应标记的位置,手工调节到轴向-扭转引伸计卸 除之前相同的应变值
然后重新开始热循环,轴向热应变与先前记录的切断机械应变后的应变值一致
调整轴向-扭转 引伸计直到与轴向热应变符合
重新启动时的轴向力值,扭矩值与中断试验之前的相一致
可用轴向-扭转引伸计小量 微调帮助达到先前的轴向力值、扭矩值
试验结果 8 8.1初始数据 可根据附录A测量试样弹性模量、剪切模量与温度的函数关系
试样的轴向热应变和温度的关系 可用图表的形式来表达
8.2记录数据的处理 至少应绘制典型的轴向应力、轴向机械应变,剪切应力,剪切应变、温度与时间的关系图,轴向机械 应变与轴向应力、温度的关系图.以及剪切应变与剪切应力、温度的关系图
8.3寿命的确定 对同一系列试验应采用相同失效判据进行规定
8.4试验结果的表达 8.4.1单个试验结果的表达 单个试验结果的表达应包括轴向应力、,轴向总应变反馈、,剪切应力,剪切应变反馈、温度和轴向热应 变与时间的关系图,以及典型循环的迟滞回线,轴向机械应变对轴向应力和温度的关系图,剪切应变对 剪切应力和温度的关系图
还应包括开始直到失效的每一个记录的循环的最大与最小轴向应力,剪切 应力,轴向总应变反馈,剪切应变反馈和温度
8.4.2系列试验结果的表达 系列试验结果的表达取决于试验研究目的,通常包括寿命[寿命分数(n/N]与最大轴向应力、最 小轴向应力、最大剪切应力,最小剪切应力、非弹性轴向机械应变范围和非弹性剪切应变范围的关系图
另外还应包括每组材料弹性模量、剪切模量与温度的关系图,每根试样轴向热应变与温度的关系图
表3列出系列试验报告的典型数据
3 表 系列试验的典型数据 图线 记录的典型循环 报告的典型循环 对数方案 N=1,半寿命循环 轴向应力与时间 N=l,2,3,6,l0,20,30,60,l00 对数方案 轴向机械应变与时间 N=l,半寿命循环 N=l,2.3,6.l0.20.30,60.l00 对数方案 剪切应力与时间 N=1,半寿命循环 N=1,2,3,6,10,20,30,60,100 14
GB/41154一2021 表3系列试验的典型数据续》 记录的典型循环 报告的典型循环 图线 对数方案 剪切应变与时间 N=1,半寿命循环 N=1,2,3,6,l0,20,30,60,100 对数方案 N=l,半寿命循环 温度与时间 N=1,2.3,6.10.20.30,60.,100 轴向应力与轴向机械应变 对数方案 N= =1,半寿命循环 迟滞回线 N=1,2,3,6,10,2030,60,100 剪切应力与剪切应变 对数方案 N=1,半寿命循环 N=1,2,3,6,l0,20,30,60,100 迟滞回线 最小最大轴向应力,轴向应力范围 对数方案 最小最大剪切应力,剪切应力范围 所有循环 N=1,2,3,6,10,20,30,60,100 峰值温度与循环数的关系 试验报告 试验报告应包括以下内容 本文件编号; a b 材料牌号和规范编号、生产厂家、炉批号、材料规格、热处理制度; 材料微观结构和沿着长度方向以及薄壁管厚度方向的晶粒尺寸、化学成分和常规力学性能等 c 如适用); d)试样的形状、尺寸、表面状态等; 试验设备的基本信息; e f 轴向热应变补偿技术和结果,例如方法1或方法2,见7.6.2 试验控制变量;试验温度,频率,应变速率,应力比或应变比,载荷或应变最大,最小值和波形 g 轴向、扭向应变波形之间的相位角 h 试验过程中不符合本文件的任何情况 试验结果;轴向应力、轴向机械应变、剪切应力,剪切应变以及温度随时间变化关系;典型循环 的迟滞回线;轴向机械应变与轴向应力关系,剪切应变与剪切应力关系;试样失效的确定方法; 导致试样失效的主裂纹方向;与引伸计和试样的接触点有关联的裂纹以及所有超出规定界限 外的控制变量差值
15
GB:/T41154一2021 附 录 A 资料性) 材料常数测定 弹性模量(E)和勇切模量(G)可用如下的方法测定
在温度稳定条件下,用循环拉伸和压缩载荷控制的三角波(或正弦波),测量每个温度的弹性模 量(E)
在温度稳定条件下,用循环扭矩载荷控制的三角波(或正弦波),测量每个温度的剪切模量 G)
施加的轴向力值或扭矩值不超过最高温度下材料屈服等效应力的20%,应力循环的频率不小 于0.1Hz
每个温度的模量至少通过5个循环确定
需要的测量数与试验温度范围和试验温度下应力(或应变)范围的大小有关
宜测量温度循环 中最小、平均和最大温度的模量,或以不使模量变化超过5%的温度间隔测量模量,取其中效 果较优者
16
GB/41154一2021 参 考文献 [1]GB/Z40387金属材料多轴疲劳试验设计准则 ttermomechanicealFatigue BehaviorofMaterials [[2]ASTMSTP1428,Th [[3]C.E.Bakis,M.G.Castelli,J.R.Elis.Thermo-mechanm ncealoadinimpurer torsion:testcontrol AdvancesinMultiaxialFat ,ASTMSTPl191,eds.D.L.McDowell anddeformationbehavior,in tigue, J.R.EllisASTMInternational,Philadelphia,1993,pp.223-243 ang,C.C.Zhang,.X.D.Liu,F.D.li,Z.G.L.Thermomechaniealfatiguedamage [4]D.H.Li,D,G,Shan behaviorforNi-based eralloyunderaxial-torsional loadng. .MaterialsScience&. A719 Eanginre super eering 201861-71
金属材料多轴疲劳试验轴向-扭转应变控制热机械疲劳试验方法GB/T41154-2021解析
随着工程结构的复杂化和高速发展,对于金属材料的耐久性和可靠性提出了更高要求。而多轴疲劳试验是评估金属材料疲劳强度和设计寿命的重要手段之一。
针对多轴疲劳试验中扭转应变控制的问题,GB/T41154-2021标准提出了一种热机械疲劳试验方法。该方法通过控制温度、应变率和载荷模式等参数,使试件在实际使用条件下的循环载荷作用下,产生类似于实际工况下的应力状态。
该标准中规定了试验设备、试样制备、试验方式等多个方面的要求。其中试样的制备是保证试验精度和可靠性的关键环节之一,GB/T41154-2021标准中对于不同材料类型的试样制备方法进行了详细说明。
通过采用这一标准,可以更加准确地评估金属材料在多轴载荷下的疲劳强度和寿命,为工程设计提供重要参考依据。