GB/T38528-2020
轿车轮胎耐撞击性能评价
Evaluatingimpactresistanceforpassengercartyres
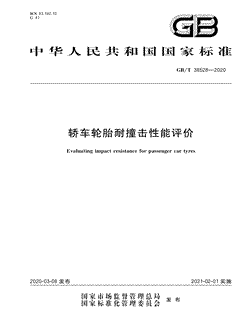
- 中国标准分类号(CCS)G41
- 国际标准分类号(ICS)83.160.10
- 实施日期2021-02-01
- 文件格式PDF
- 文本页数11页
- 文件大小1.31M
以图片形式预览轿车轮胎耐撞击性能评价
轿车轮胎耐撞击性能评价
国家标准 GB/T38528一2020 轿车轮胎耐撞击性能评价 Evalatingimpactresistaneeftorp8ssengerearyres 2020-03-06发布 2021-02-01实施 国家市场监督管理总局 发布 国家标涯花管理委员会国家标准
GB/38528一2020 前 言 本标准按照GB/T1.1一2009给出的规则起草
本标准由石油和化学工业联合会提出
本标准由全国轮胎轮绸标准化技术委员会(SAC/TC19)归口
本标准起草单位:汕头市浩大轮胎测试装备有限公司、中策橡胶集团有限公司山东玲珑轮胎股份 有限公司山东丰源轮胎制造股份有限公司北京橡胶工业研究设计院有限公司、万力轮胎股份有限公 司、安徽佳通乘用子午线轮胎有限公司、浦林成山(山东)轮胎有限公司、赛轮集团股份有限公司、三角轮 胎股份有限公司、青岛森麟麟轮胎股份有限公司、四川轮胎橡胶(集团)股份有限公司、山东宏盛橡胶科 技有限公司、双星集团有限责任公司、双钱轮胎集团有限公司、天津市万达轮胎集团有限公司、厦门正新 橡胶工业有限公司,山东泰山轮胎有限公司,米其林()投资有限公司、韩泰轮胎有限公司、住友橡胶 )有限公司、普利司通()投资有限公司、大陆马牌轮胎()有限公司,大连固特异轮胎有限 公司,优科豪马橡胶有限公司、上汽通用五菱汽车股份有限公司,南京依维柯汽车有限公司,、国家市场监 督管理总局缺陷广品管理中心 本标准主要起草人;陈迅、曾少丽,吕剑、陈少梅、潘超、王克先、牟守勇、韩贞花、葛风雷,刘昌波 侯晓情、张昨,秦龙、董继学、肖圣龙、徐伟、曹峰、于振江、陈建明、王洪训、陆奕,梁斌、黄晓青、朱诚 马忠、尹庆叶、王镇潇、韦宝倡,朱晓,徐丽红,郑基、王项肖凌云
GB/38528一2020 轿车轮胎耐撞击性能评价 范围 本标准规定了摆锤法轿车轮胎耐撞击性能评价要求、试验方法、判定规则和试验报告
本标准适用于新的30系列至65系列充气无内胎轿车轮胎,不适用于缺气保用轮胎和仅供临时使 用的备用轮胎
规范性引用文件 下列文件对于本文件的应用是必不可少的
凡是注日期的引用文件,仅注日期的版本适用于本文 件
凡是不注日期的引用文件,其最新版本(包括所有的修改单)适用于本文件
GB/T2978轿车轮胎规格、尺寸、气压与负荷 GB/T3487乘用车轮绸规格系列 GB/T6326轮胎术语及其定义 GB/T8170数值修约规则与极限数值的表示和判定 GB/T30195汽车轮胎耐撞击性能试验方法 HG/T2177轮胎外观质量 术语和定义 GB/T6326和GB/T30195界定的以及下列术语和定义适用于本文件
3. 撞击锤角度striker angle 撞击锤中心平面和撞击锤前端曲面的交线与车轮中心平面的夹角,如图1a)所示
3.2 外倾角eamberangle;cA 撞击锤角度在通过车轮旋转轴的水平面上的投影,如图1b)所示
3.3 侧偏角slpangle;SA 撞击锤角度在通过车轮旋转轴的铅垂面上的投影,如图1e)所示
GB/T38528一2020 靠 e b) 2 撞击锤角度 外倾角 侧偏角 说明 轮胎; 撞击锤
撞击锤角度、侧偏角和外倾角 3.4 撞击能量impactenergy E 撞击锤从撞击高度或撞击角度落下撞击轮胎瞬间时的动能
3.5 鼓包impaetbulge 轮胎受到撞击导致轮胎胎侧异常起鼓的现象
3.6 漏气airleakage 轮胎受到撞击导致轮胎气压明显持续下降的现象
3.7 鼓包高度impactbulgeheight H 轮胎受到撞击后鼓起的高度
3.8 轮胎耐撞击因子robustnessfactor 轮胎耐撞击性能的评价指标
3.9 鼓包破坏能impactbulgeenery E 撞击锤撞击轮胎引起轮胎鼓包或漏气时的撞击能量
3.10 machinedsteelrim 钢制轮辗 通过机加工制作,仅用于室内试验,且轮廓曲线符合GB/T3487规定的钢质材料轮轭
GB/38528一2020 评价要求 4.1试验轮胎的耐撞击因子应不小于表1的规定 表1充气无内胎轿车轮胎耐撞击因子 单位为牛平方米 轮胎名义高宽比 65,60,55系列 50系列 45,40系列 35,30系列 轮胎耐撞击因子() 80 50 30 65 4.2将表1规定的轮胎耐撞击因子()代人式(1),计算得出试验轮胎应通过的最小鼓包破坏能 Emm),并按GB/T8170的规定修约到个位整数
2.5 200 Emi=f×LIX l厅 D 式中: 最小轮胎鼓包破坏能,单位为焦( E min" 轮胎耐撞击因子,单位为牛平方米(Nm)
LI 轮胎负荷指数,无量纲
标准型轮胎采用标准型轮胎的负荷指数;增强型轮胎采用与该 规格对应的标准型轮胎的负荷指数;只有增强型没有标准型的轮胎,负荷指数由增强型 轮胎的负荷指数减4 常量,C=80mm
轮胎名义断面高度,单位为毫米(mm),按照式(2)进行计算,并修约到毫米整数
H 轮胎外直径,单位为毫米(mm),按照式(3)进行计算,并修约到毫米整数 D H=S.×A,六100 2 式中 s 名义断面宽度,单位为毫米(mn m; 名义高宽比
A D=D,十2H 式中 轮绸名义直径,单位为毫米(mm); D. H 轮胎断面高度,单位为毫米(mm). 5 试验方法 5.1设备和仪器 5.1.1撞击试验设备 撞击试验设备的撞击锤、撞击锤支架、撞击锤组合件应符合附录A的规定,其他应符合GB/T30195 的规定
5.1.2鼓包测量仪 鼓包测量仪由百分表和支架组成,具体参见附录B
5.1.3充气压力表/气压传感器 手持充气压力表气压传感器,精度为士5kPa
GB/T38528一2020 5.1.4图像记录设备 试验中出现的鼓包或漏气现象应采用彩色、清晰、可存储的图像记录设备进行记录
5.2试验条件及试验准备 5.2.1试验轮胎在硫化后应放置24h以上,其外观质量应符合HG/T2177的要求
5.2.2试验环境温度为20C30C 5.2.3试验轮绸应为轿车轮胎耐撞击性能试验专用钢制轮惘,其规格型号应与GB/T2978中规定的测 量轮一致;装配柔性轮惘的车辆所使用的轮胎应使用与车辆要求一致的柔性轮进行试验,并在试验 报告中加以说明
5.2.4将试验轮胎安装在5.2.3规定的试验轮辖上,充人200kPa气压
安装轮胎时,可使用润滑剂
5.2.5充气后的轮胎轮惘组合体应在试验环境温度下放置3h以上
5.2.6沿轮胎圆周方向确定5个大致等间距分布的试验点,并逐一做标记、编序号
5.2.7轮胎耐撞击性能试验机的撞击锤角度固定在外倾角6,侧偏角0',偏差为士0.5°
5.3试验程序 5.3.1将放置后的试验轮胎气压重新调整到5.2.4规定的气压,偏差应不超过士2kPa
如果放置后的 试验轮胎气压有不正常的损失,应观察试验轮胎和轮惘状况,重新准备试验轮胎 5.3.2将校正气压后的试验轮胎轮酮组合体按GB/T30195的规定安装在试验装置上,并将轮绸进行 锁定,使其在周向上不能转动,按标记序号逐点进行试验
.使轮胎旋转中心与撞击锤顶部处于同一水平线上,沿水平方向横 5.3.3将摆杆调整到自由悬挂状态, 向调整轮胎位置,使轮胎胎肩触及撞击锤中部
摆杆因轮胎触及撞击锤产生的摆杆角位移应不超过 0.1! 5.3.4提升撞击锤使其撞击能量等于4.2规定的最小鼓包破坏能,然后锁定摆杆
5.3.5使撞击锤从锁定位置自由下落,撞击试验轮胎
撞击锤反弹时,由锁定装置锁定摆杆,防止二次 撞击
再将轮胎后退,撞击锤缓缓下落到自由悬垂状态
5.3.6每个试验点撞击后3min使用5.1.2规定的鼓包测量仪对该撞击点附近进行检查,并记录检查 结果;用5.1.3规定的充气压力表/气压传感器测量轮胎气压并记录结果;用5.1.4规定的图像记录设备 对撞击部位出现的鼓包或裂口等受损情况进行记录
5.3.7轮胎如出现漏气或3min内气压损失超过5.2.4规定气压的5%,应检查轮胎和轮铜
如明显可 见因轮剌受损而引起的漏气 如明显可见因轮胎受损开裂而引起的漏气, 应终止试验,并用5.l.4规定的图像记录设备对漏气的裂口位置进行记录
若轮胎受损和轮轭受损均 不明显,则宜在撞击点做标记后卸下试验轮胎轮绸组合体,检查轮胎;若轮胎检查出受损,应终止试验 用5.1.4规定的图像记录设备记录受损位置;若轮胎未检查出受损,重新装配(允许更换轮绸)后按5.2.4 规定的气压充气,充气后15min,重新检查轮胎是否开裂,测量气压和鼓包高度
5.3.8每次进人下一个试验点进行撞击前,应将试验轮胎气压重新调整到5.2.4规定的气压(偏差应不 超过士2kPa),同时检查撞击锤的紧固螺栓是否松动
5.3.9如果每个撞击点的鼓包高度均小于1 应静置30min,再次检查鼓包高度
mm, 试验过程中如轮铜因撞击受损,应更换轮饷重新装配轮胎,按5.2.4的规定的气压充气,充气后 5.3.10 15min,重新检查轮胎是否开裂、测量气压和鼓包高度
6 判定规则 被测试轮胎按5.3.1~5.3.10要求完成试验后,未出现下列情况之一的,判定为“通过”,否则判定为
GB/38528一2020 “未通过” a 任意一个撞击点因轮胎受损出现漏气或3min内气压损失超过5.2.4规定气压的5%; b 任意一个撞击点,试验过程或试验结束后外观检查存在明显可见的脱层、崩花、接头裂开、龟裂 或帘布层露出的; 任意一个撞击点,试验过程中轮绸因撞击受损出现漏气,按5.3.10规定更换轮绸后充气过程 中轮胎持续漏气,或充气后15min检查气压损失超过5.2.4规定气压的5%或出现裂口或鼓 包大于或等于1mm的 d 任意一个撞击点出现鼓包高度大于或等于1mm的; 每个撞击点的鼓包高度均小于1 mm, ,但按5.3.9规定静置30min后,任何一个出现鼓包高度 大于或等于lmm的
试验报告 试验报告宜包括以下内容 试验轮胎制造商名称、商标、规格、生产编号; a 试验轮胎负荷指数负荷能力、速度符号、材料结构等 b 试验轮圜规格; c d 实验室环境温度; 试验标准编号、试验日期 e 试验气压 耐撞击试验轮胎各试验点的鼓包高度(含0mm),耐撞击因子和撞击能量 g 轮胎各试验点撞击后的气压,出现外观异常、,鼓包、漏气时的照片; h 试验过程的其他意外情况 评价结果
GB/T38528?2020 ? A 淶??) ????? ???A.1 A.1 λ? 406 203 C0.CD 150 G228 6 22 39 ? ip 50 30 ?? ?:;īQT500 L?派,?>40HRc ?A.1??
GB/38528一2020 A.2撞击锤支架尺寸见图A.2
单位为毫米 0 M6 9平 63.5O 127 62 R25 2-M18 RG 目 zI R30 断面4一4 注,材料;45或等效
图A.2撞击锤支架尺寸 A.3撞击锤组合体见图A.3. 剂面4一4 固定螺栓 撞击锤组合体 图A.3
GB/T38528一2020 附 录 B 资料性附录) 鼓包测量仪 B.1组成 鼓包测量仪包括百分表(一级)和支架,示意图见图B.1
百分表 8 支架 测爪 百分表探头 图B.1鼓包测量仪 B.2校正 使用鼓包测量仪前在撞击位置做好标识,将其探测头与标识位置对齐并校正(图B.2),探头和测爪 垂直于轮胎表面
图B.2鼓包测量仪的校正
GB/38528一2020 B.3鼓包测量 轮胎受撞击后,目视发现有或不确定有鼓包的,使用鼓包测量仪对鼓包位置进行检查,见图B.3
图B.3鼓包测量 B,4量程及尺寸要求 百分表量程:l0.00 mm
测爪间距离见图B.4
单位为毫米 110 100 68 图B.4鼓包测量仪量程及尺寸
轿车轮胎耐撞击性能评价GB/T38528-2020
轿车轮胎是汽车中最为重要的组成部分之一,而其耐撞击性能的好坏直接关系到行车安全。因此,制定一套科学、严谨的轮胎耐撞击性能评价标准对于保障行车安全至关重要。我国最新发布的轿车轮胎耐撞击性能评价标准为GB/T38528-2020,本文将针对该标准进行详细介绍。
一、 标准概述
GB/T38528-2020《轿车轮胎耐撞击性能评价》标准是我国最新发布的对于轿车轮胎耐撞击性能评价的标准,该标准适用于轿车用气囊轮胎和非气囊轮胎。标准主要涵盖以下内容:
- 术语和定义
- 试验设备
- 试验方法
- 试验程序
- 试验结果的判定与报告
二、 试验方法
标准中规定了三种不同的试验方法,分别是单点撞击试验、多点撞击试验以及路面撞击试验。其中,单点撞击试验主要用于对轮胎冲击耐受性进行评价;多点撞击试验则可以模拟轮胎在日常使用中遇到的各种情况下的耐撞击性能;而路面撞击试验则可以更加真实地模拟轮胎在行驶过程中遇到的情况。
具体来说,单点撞击试验是将钢球从一定高度自由落下,撞击轮胎上的一个点;多点撞击试验则是将钢球同时自由落下,撞击轮胎上的多个点;而路面撞击试验则是将轮胎安装在车辆上,在特定速度下,通过撞击机构施加冲击力,模拟轮胎在路面上行驶时的受力情况。
三、 试验结果的判定
标准中规定了轮胎经过试验后的判定标准。在单点撞击试验和多点撞击试验中,通过检测轮胎表面是否有破损、裂纹等现象来进行判定;而在路面撞击试验中,则需要通过检测轮胎内部是否出现异常情况、轮胎是否可以正常使用等指标来进行判定。
四、 结论
GB/T38528-2020《轿车轮胎耐撞击性能评价》标准作为我国最新制定的轿车轮胎耐撞击性能评价标准,对于保障行车安全具有十分重要的意义。标准制定了严格的试验方法和判定标准,确保了轮胎的耐撞击性能得到了科学、全面的评价。同时,该标准的实施也将促进我国轮胎制造行业的发展,提升其产品质量和技术水平。
总之,GB/T38528-2020《轿车轮胎耐撞击性能评价》标准是我国目前最为权威的对于轿车轮胎耐撞击性能评价的标准,对于保障行车安全、促进轮胎制造业的可持续发展具有重要作用。