GB/T33630-2017
海上风力发电机组防腐规范
Offshorewindturbinegeneratorsystems—Specificationforcorrosionprotection
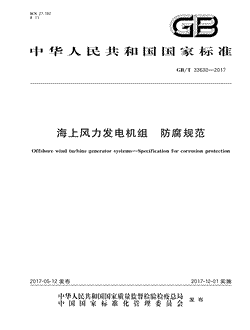
- 中国标准分类号(CCS)F11
- 国际标准分类号(ICS)27.180
- 实施日期2017-12-01
- 文件格式PDF
- 文本页数23页
- 文件大小1.99M
以图片形式预览海上风力发电机组防腐规范
海上风力发电机组防腐规范
国家标准 GB/T33630一2017 海上风力发电机组防腐规范 ortshorewtmdturbinegeneratorsystes一speeifieationtorcwrosionproteetionm 2017-05-12发布 2017-12-01实施 国家质量监督检验检疫总局 发布 国家标准化管理委员会国家标准
GB/33630一2017 前 言 本标准按照GB/T1.1一2009给出的规则起草
本标准由机械工业联合会提出
本标准由全国风力机械标准化技术委员会(SAC/TC50)归口
本标准起草单位:中船重工(重庆)海装风电设备有限公司、农业机械化科学研究院呼和浩特分 院、电建集团华东勘测设计研究院有限公司、华北电力大学,新疆金风科技股份有限公司、中船重工 第七二五研究所、华锐风电科技(集团)股份有限公司、国电联合动力技术有限公司、湘电风能有限公司、 东方电气风电有限公司
本标准主要起草人陶友传、唐永春、王建平、王叶、侯承宇、张万军、黄金余、李顺建、张海亚 汤文兵,欧阳海黎,赵生校、姜贞强、颜加明、田德、武占海,张东亚、张乐显、徐初琪、张芹 周祖田、 刘作辉、杨建峰、罗衡强、宗多
GB/33630一2017 海上风力发电机组防腐规范 范围 本标准规定了海上风力发电机组腐蚀环境控制及主要结构件,部件(设备)防腐蚀常用方法和相关 技术要求
本标准适用于水平轴海上风力发电机组(以下简称“机组”)及部件的防腐蚀设计,施工、验收及运行 维护
本标准不适用于海上风力发电机组塔架以下结构和基础
规范性引用文件 下列文件对于本文件的应用是必不可少的
凡是注日期的引用文件,仅注日期的版本适用于本文 件
凡是不注日期的引用文件,其最新版本(包括所有的修改单)适用于本文件
GB/T470锌锭 GB/T1732漆膜耐冲击测定法 GB/T1733漆膜耐水性测定法 GB/T1740漆膜耐湿热测定法 GB/T1768色漆和清漆耐磨性的测定旋转橡胶砂轮法 GB/T1771 色漆和清漆耐中性盐雾性能的测定 GB/T1865色漆和清漆人工气候老化和人工辐射暴露滤过的缸弧辐射 GB/T2423.4电工电子产品环境试验第2部分;试验方法试验Db;交变湿热(12h十12h循 环 GB/T2423.16电工电子产品环境试验第2部分;试验方法试验」及导则:长霉 GB/T2423.18环境试验第2部分:试验方法试验Kb盐雾,交变(氯化钠溶液 GB/T2694一2010输电线路铁塔制造技术条件 GB/T4208外壳防护等级(IP代码 GB/T5210色漆和清漆拉开法附着力试验 GB/T5267.4紧固件表面处理耐腐蚀不锈钢钝化处理 GB/T6742色渎和清漆弯曲试验圆柱轴 GB/T8923.1涂覆涂料前钢材表面处理表面清洁度的目视评定第1部分;未涂覆过的钢材 表面和全面清除原有涂层后的钢材表面的锈蚀等级和处理等级 GB/T8923.3涂覆涂料前钢材表面处理表面清洁度的目视评定第3部分;焊缝、边缘和其他 区域的表面缺陷的处理等级 GB/T9258.3涂附磨具用磨料粒度分析第3部分;微粉P240~P2500粒度组成的测定 GB/T9274色漆和清漆耐液体介质的测定 GB/T9278涂料试样状态调节和试验的温湿度 GB/T97932012热喷涂金属和其他无机覆盖层锌,铝及其合金 GB/T10125 人造气氛腐蚀试验盐雾试验 GB/T12608热喷涂火焰和电弧喷涂用线材、棒材和芯材分类和供货技术条件
GB/T33630一2017 GB/T13288.2涂覆涂料前钢材表面处理喷射清理后的钢材表面粗糙度特性第2部分;磨料 喷射清理后钢材表面粗糙度等级的测定方法比较样块法 GB/T13452.2色漆和清漆漆膜厚度的测定 GB/T13912金属覆盖层钢铁制件热浸镀锌层技术要求及试验方法 GB/T16545金属和合金的腐蚀腐蚀试样上腐蚀产物的清除 GB/T17850.1涂覆涂料前钢材表面处理喷射清理用非金属磨料的技术要求导则和分类 GB/T18570.3涂覆涂料前钢材表面处理表面清洁度的评定试验第3部分;涂覆涂料前钢材 表面的灰尘评定(压敏粘带法 GB/T18570.6涂覆涂料前钢材表面处理表面清洁度的评定试验第6部分;可溶性杂质的取 样Bresle法 GB/T18570.9涂覆涂料前钢材表面处理表面清洁度的评定试验第9部分:水溶性盐的现场 电导率测定法 GB/T18684锌铬涂层技术条件 GB/T18838.1涂覆涂料前钢材表面处理喷射清理用金属磨料的技术要求导则和分类 GB/T18839.2涂覆涂料前钢材表面处理表面处理方法磨料喷射清理 GB/T18839.3涂覆涂料前钢材表面处理表面处理方法手工和动力工具清理 GB/T19355钢铁结构耐腐蚀保护锌和铝覆盖层指南 GB/T23987色漆和清漆涂层的人工气候老化曝露曝露于荧光紫外线和水 GB/T26110锌铝涂层技术条件 色漆和清漆防护涂料体系对钢结构的防腐蚀保护第1部分;总则 GB/T30790.1 GB/T30790.2 色漆和清漆防护涂料体系对钢结构的防腐蚀保护第2部分;环境分类 G;B/T30790.4色渎和清漆防护涂料体系对钢结构的防腐蚀保护第4部分:表面类型和表面 处理 GB/T30790.5色漆和清漆防护涂料体系对钢结构的防腐蚀保护第5部分;防护涂料体系 色漆和清漆海上及有关结构的防腐涂料体系的性能要求(Paintsandvarnishes ISO20340 Performancerequirementsforprotectivepaintsystemsforofshoreandrelatedstructures 3 术语和定义 GB/T30790.1.GB/T30790.2,GB/T30790.4,GB/T30790.5界定的以及下列术语和定义适用于 本文件
3.1 腐蚀环境corosionenvironment 含有一种或多种腐蚀介质的环境
3.2 腐蚀环境控制corrosionenvironmentcontrol 对腐蚀速率起关键作用的环境因素(腐蚀介质含量、温度、相对湿度、日照及降水等)进行控制,以降 低环境的腐蚀性
3.3 迷宫密封labyrinthsel 在转轴周围设若干个依次排列的环形密封齿,齿与齿之间形成一系列截流间隙与膨胀空间,被密封 介质在通过曲折迷宫的间隙时产生节流效应而达到阻漏
GB/33630一2017 3.4 微正压密封meropositivepressuresenl 将外部空气处理后充人到一个相对密闭的罩壳内,使壳内空气压力略高于外部大气压力,阻止外部 大气侵人到壳内
总则 4.1腐蚀环境 4.1.1机组主要结构(塔架及以上结构,部件处于海洋大气区,按GB/T30790.2的规定,根据低碳钢 在大气环境中的年腐蚀速率,将其所处腐蚀环境分为舱外区、舱内区、干洁区,见表1
4.1.2干洁区内部件应按不低于C3腐蚀性等级进行防腐蚀保护 4.1.3在炎热、潮湿的沿海区域,质量或厚度损失有可能超过C5-M等级的范围,因此为这些区域使用 的结构选择涂料防护体系时应采取特别的预防措施
表1海上风力发电机组腐蚀环境区域划分 环境条件 区域名称低碳俐腐蚀速率" 特征 示例 腐蚀性等级 g/nma 不受自然气候,海洋大气和海水的影响,彻采用腐蚀环境控制措 二400 C3 干清区 施的机舱内部 湿时间和腐蚀介质含量均处于较低水平 与海洋大气相通,不受阳光、雨,雪,露等污采用罩壳保护的轮毅 >400且<65o 舱内区 染物的直接侵蚀,潮湿时间或腐蚀介质含量内部、机舱内部、塔架 至少有一个处于较高水平 内部 暴露在海祥大气环境中,受阳光、雨、雪、露 舱外区 >650且1500 C5-M 等污染物的直接侵蚀,温度、湿度变化大,潮机舱外部、塔架外部 湿时间和腐蚀介质含量均处于很高水平 经过第一年暴露后的单位面积质量损失值,按附录A进行低碳钢标准试样的制作及腐蚀速率的测定
4.2总体防腐蚀措施 4.2.1防腐蚀系统的设计使用年限应考虑到机组的设计使用年限,不宜小于25年
4.2.2机组总体结构应采用密封设计,塔架、机舱、轮毂及发电机(直驱型机组)内部宜采用腐蚀环境控 制措施保持干洁空气环境
其总体防腐蚀措施如下 塔架宜采用密闭筒式结构,安装时法兰连接面宜采用涂密封胶等措施进行密封处理
塔架门 应采用密封设计,门内侧宜设置隔离间减少门开/闭过程中外部空气的侵人
机舱和轮毂宜采用耐蚀材料制作的罩壳并设计成一个尽可能密闭的空间
b 直驱机组独立安装在机舱和轮毂间的发电机外壳宜采用耐蚀材料,机体及散热系统采用密封 设计
4.2.3机组主要结构及部件按所处区域腐蚀性等级进行防腐蚀保护,可采用但不限于涂料保护、热喷 涂金属保护,热浸镀锌保护,以及金属涂层与涂料涂层联合保护等防腐蚀措施
GB/T33630一2017 4.2.4结构,部件设计应采取以下措施 根据所处腐蚀环境区域合理选用耐蚀材料和涂覆保护; a 用管型构件代替其他形状的构件,结构形式力求简单 b 在可能积水和留存湿气的空间开设排水孔和排气孔,不留死角; c d 尽量减少配合面和搭接面,焊接构件采用连续焊缝并进行密封涂覆,不留缝隙 形状和尺寸改变时采用圆弧过渡,棱角、边缘采用圆角设计,避免应力腐蚀和提高镀涂的工 艺性 同一结构中尽量选用同一种金属材料,防止电偶腐蚀
fD) 5 腐蚀环境控制 5.1措施 腐蚀环境控制可采用但不限于迷宫密封加温湿度控制装置、微正压密封加除湿除盐过滤装置的措 施进行防腐蚀保护 5.2要求 5.2.1采用腐蚀环境控制后的区域应进行腐蚀速率测定,并按表1进行区域划分
5.2.2为达到干洁区腐蚀环境要求,宜按表2规定的腐蚀环境控制参数进行控制
表2腐蚀环境控制主要参数 盐雾沉降量 相对湿度 温度 微正压力 mg/m'd Pa 0.8 65 不小于50 50 密封区域内部空气压力与外部空气流场压力差该参数仅适用于采用微正压密封防腐蚀系统) 电气设备的防护 6 6.1措施 6.1.1柜体宜采用焊接的型材框架结构及薄形钢板材料,内外表面宜采用环氧类粉末涂料进行防腐蚀 保护,粉末厚度应不小于100m.
6.1.2柜体采用密封设计,舱外区及舱内区电气设备需外部空气进行冷却时,应对冷却空气进行去腐 蚀介质处理
6.2要求 6.2.1按照GB/T4208定义的防护等级,设备外壳防护等级要求见表3
6.2.2设备设计应满足“防盐雾、防潮湿、防霉菌”三防要求,应按表4规定的项目进行环境试验(不限 于),试验前、后按相应设备规范对试样进行目视检查、绝缘电阻及性能检测
6.2.3设备柜体内宜装设加热除湿装置或放置适量的吸湿防霉剂,相对湿度应控制在65%以下
GB/33630一2017 表3电气设备外壳防护等级 区域 干洁区 舱内区 舱外区 外壳防护等级 IP54 IP65 IP43 安装于舱外区的设备本身不能达到防护要求时,应采用其他措施或改善安装场所条件来确保本表要求
表4电气设备环境试验要求 严酷等级 试验项目 试验标准 干洁区 舱外区 舱内区 GB/T2423.18 盐雾试验 严酷等级2 严酷等级1 高温40C,循环次数2高温40C,循环次数6 湿热试验 GB/T2423.4 高温40,循环次数12 霉菌试验 GB/T2423.16 方法1-严酷等级128d方法1-严酷等级128d方法1-严酷等级128dl 钢制结构件及部件的防护 7.1措施 7.1.1结构形状简单、易于喷涂处理的部件表面宜采用涂层保护;结构形状复杂、不易进行喷涂处理的 部件表面宜采用镀层保护;不易维护,防腐性要求高的部件表面宜采用金属涂层和涂料涂层联合保护 各部件防腐蚀措施如下: 塔架外壁(包括塔架法兰盘的外壁、塔架门板的内外表面及隔离间塔架内壁)可采用涂料涂层 a 保护,或热喷锌和涂料涂层联合保护 塔架外部钢结构平台、梯子、围栏等可采用热浸镀锌和涂料涂层联合保护; b 塔架法兰连接面可采用热喷锌金属涂层保护; c 塔架内壁(包括塔架法兰盘的内壁)可采用涂料涂层保护; d 机架、轮毂可采用涂料保护或热喷锌和涂料涂层联合保护; 塔架、机舱、轮毂内部的支架,电缆桥架,钢结构梯子,扶栏以及其他结构和形状比较复杂的钢 构件可采用热浸镀锌保护 运输和吊装期间需临时防腐蚀的部件可采用喷涂环氧富锌底漆进行保护,干膜厚度应不大于 g 50丛m; h)加工及安装过程中需短期防腐蚀的部件可采用涂抹防锈油脂进行保护,涂抹防锈油脂后不易 清除并影响其功能的部件(如刹车盘)应采用其他合适的保护措施
7.1.2紧固件的选用应考虑连接重要性、易更换性及腐蚀环境,其防腐蚀要求如下 a 高强度连接螺栓(包含螺母、垫片)可选用碳钢或合金钢制作,其表面可按GB/T18684规定的 4级锌铬涂层或GB/T26110规定的5级锌铝涂层进行处理,或采用耐蚀性、耐磨性更优的金 属渗层技术进行表面处理; 强度要求不高的连接螺栓(包含螺母、垫片)宜选用奥氏体A!或A5组别不锈钢制作,其表面 按GB/T5267.4的规定进行钝化处理 按GB/T10125的规定进行中性盐雾试验,出现红锈的时间应大于1200h
GB/T33630一2017 7.2表面处理 7.2.1处理流程 在喷涂或镀覆前,应按预处理、除污、除锈、除尘和表面水溶性盐浓度测定的次序对基材表面进行 处理
7.2.2预处理 按GB/T18839.3规定的手工或动力工具清理方法进行预处理,要求如下 用刮刀或砂轮机去除焊接飞溅物,焊缝应打磨光滑; a 表面层叠、裂缝,夹杂物等需打磨处理,必要时在不影明部件机械性能的前提下可补焊 b c 锐边和切割边缘打磨成曲率半径大于2mm的圆角 d 基材各类表面缺陷的处理等级应达到GB/T8923.3规定的P级
7.2.3除污 表面污物(焊剂、油、脂、盐等)应采用专用清洁剂进行低压喷洗或软刷刷洗,并用洁净淡水冲洗掉所 有残余物
也可采用火焰处理或碱液清洗,碱液清洗要用淡水冲洗至中性
小面积污物可采用专用溶 剂擦洗
7.2.4除锈 按GB/T18839.2规定的磨料喷射清理方法进行除锈,不便于喷射清理的部位可采用GB:/T18839.3 规定的手工或动力工具清理方法进行除锈,要求如下 a 除锈应在空气相对湿度不高于85%、基材表面温度至少高于露点3C的环境条件下进行; b)根据表面粗糙度及清洁度要求,选择合适粒度的磨料
金属磨料应符合GB/T18838.1的要 求,非金属磨料应符合GB/T17850.1的要求; 除锈后按GB/T8923.1的规定评定处理等级,基材表面处理等级应满足表5要求(技术文件另 有规定除外); 除锈后按GB/T13288.2的规定评定表面粗糙度,基材表面粗糙度应达到“中”级,待热浸镀锌 d 的表面可不做评定
7.2.5除尘 使用真空吸尘器或无油、无水的压缩空气对基材表面进行除尘处理,表面灰尘数量等级和灰尘尺寸 等级应不超过GB/T18570.3规定的2级
表5基材表面处理等级要求 待涂(镀)覆类型 清理等级 热喷涂金属 Sa3级 喷涂无机富锌底漆 Sa2~Sa3级 喷涂环氧富锌底漆 Sa2%级 st3级 手工或动力工具清理 热浸镀锌 不做评定
GB/33630一2017 7.2.6水溶性盐浓度测试 基材表面水溶性盐浓度的测定按GB/T18570.6规定的方法进行取样,按GB/T18570.9规定的方 法进行电导率测定
其水溶性氧化物含量应不大于50mg/m,超标时应采用洁净的高压淡水冲洗
7.3涂料保护 7.3.1涂层配套 7.3.1.1按GB/T30790.1的规定,防护涂层体系耐久性设定为高;按GB/T30790.5的规定,推荐防护 涂层配套方案见表6
7.3.1.2涂层间应具有相同或相近的热膨胀系数、良好的匹配性及附着力
7.3.1.3防护涂层体系应满足表7中规定的性能要求(不限于)
表6钢制件防护涂层推荐配套方案 额定干膜厚度 主要作用 m 涂层 涂料类型 保护基材,为后续涂料提供附着基础 C4 C3 C5-M 环氧富锋 保护基材,为后续涂料提供附着基础 60 60 60 底漆 200 120 中间漆 环氧类 增加涂层厚度,减少腐蚀介质渗透 40 面漆 聚氨酯类 60 60 提高耐候性,抵御紫外线、雨水的侵蚀 60 总干膜厚度 320 240 160 富锌底漆不挥发组分中锌粉颜料的质量分数应不低于80%
表7钢制件防护涂层体系性能要求 序号 试验项目 试验时间 性能指标 试验标准 >5MPa GB/T521o 附着力 不起泡、不剥落、不生锈、不开裂 ISO20340 循环老化试验 C5-M:4200h 划痕腐蚀蔓延;2mm划线M<3,0.05mm 划线M<" 不起泡、不剥落、不生锈、,不开裂、不粉化 耐人工加速老化试验 C4:1000h 变色:2级,失光:2级 GB/T1865 循环 A C3:1000h 附着力'>5MP% C5-M;4000h 不起泡、不剥落、不生锈、不开裂 耐盐雾试验 C4:2500h GB/T1771 附着力'>5MPa C3:1200h C5-M;720h 耐盐水试验 不起泡、不剥落、不生锈、不开裂 C4;480h GB/T9274 浸泡法,5%NaCD 变色1级,失光1级 C3;320h 试验后涂层粉化满足供需双方协议要求
试验完成后,试板在GB/T9278规定的标准条件下放置24h,再按GB/T5210进行附着力测试
GB/T33630一2017 7.3.2涂装要求 7.3.2.1 涂装环境 施工场所无风砂和灰尘,涂装作业应在空气流通,光线明亮、清洁干净的厂房内进行
如无特殊要 求,下列情况之一不应进行涂装作业 施工现场环境温度低于5或高于40C; a 施工现场空气相对湿度高于85%; b 基材表面温度低于周围空气的露点以上3C; c 表面处理过的结构或机械部件已重新锈蚀或沾污 d 基材表面潮湿或者有可能溅湿
e 7.3.2.2涂料配制 涂料应充分搅拌均匀后方可施工,宜采用电动或气动搅排装置,如无特殊要求,配制要求如下: 检查涂料品种、型号,规格、贮存期限应符合设计文件的规定; a b) 涂料一般不宜稀释,特殊情况下可舔加稀释剂,稀释剂添加量应符合产品说明书的规定 使用双组分或多组分涂料,应先将各组分分别搅拌均匀后,再严格按比例混合并搅拌均匀; c d 混合好的涂料按照产品说明书规定的时间进行熟化,并在规定的时间内使用
7.3.2.3涂装施工 采用高压无气喷涂,小面积或形状复杂构件可采用刷涂和辐涂
按相关工艺进行涂装,施工过程应 满足如下要求 表面处理完成后4h内应喷涂底漆,当所处环境的相对湿度小于60%时可以适当延长,但最长 a 不超过12h
如果基材表面有可见返锈现象、变湿或被污染,应重新进行表面处理
每道涂层涂装的间隔时间应符合涂料产品使用说明书要求,超过最大重涂间隔时间时需进行 b 拉毛处理后再涂装
涂装作业中应按GB/T13452.2规定的方法检测每一道涂层的湿膜厚度和干膜厚度
c 涂装作业中应对法兰连接面、防雷接地耳板、螺柱、螺孔等采取有效的保护措施,涂装完成后去 d 除残余油漆,螺纹孔进行过丝处理
7.3.3涂层检验与质量控制 7.3.3.1涂层体系的型式检验包括表7中的全部项目,涂料供应商应提供国家认可检测机构出具的涂 层性能检测报告,必要时可进行复检
7.3.3.2过程检验按表8规定执行,出货品质检验按表9规定执行
表8钢结构防护涂层过程检验 序号 测试项目 测试方法 测试频率或范围 验收准则 GB/T8923.1 A级或B级 基材锈蚀等级 1o0%表面检查 基材表面缺陷 GB/T8923.3 100%表面检查 按7.2.2执行 除锈环境条件 使用温、湿度仪进行检测 每工班测量次数应不少于3次 按7.2.4执行 除锈清洁度 (GB/T8923.1 100%表面检查 按7.2.4执行 基材粗糙度 GB/T13288.2 每10m表面检测1次,不足10m'检测1次按7.2.4执行
GB/33630一2017 表8(续 序号 测试项目 验收准则 测试方法 测试频率或范围 除尘清洁度 GB/T18570.3 局部检查 按7.2.5执行 除盐清洁度 GB/T18570.9 局部测试 按7.2.6执行 涂装环境条件 使用温、湿度仪进行检测每工班检测次数应不少于3次 按7.3.2.1执行 每道涂层 GB/T13452.2 技术文件规定 湿膜厚度 l0 每道涂层 技术文件规定 GB/T13452.2 干膜厚度 表9钢结构防护涂层出货品质检验 序号 测试项目 测试方法 要求 表面平滑,色泽均一,无漏涂、针孔、起泡、裂纹、脱落、返锈等缺陷,允许 外观 目视检查 有轻微橘皮和局部轻微流挂;涂层颜色,光泽度满足设计文件要求 所有测点的干膜厚度应不低于额定干膜厚度的90% 低于额定干膜厚度但不低于额定干膜厚度的90%测点应不超过总测点 总干膜厚度 GB/T13452.2 的10% 所有测点的干膜厚度应不大于规定的最大干膜厚度,最大干膜厚度不应 大于额定干膜厚度的3倍 附着力" GB/T5210 >5MPa 采用与制件同类型材料的试板进行检测,试板随制件一起进行涂装,必要时可在制件表面直接进行附着力 检测
7.3.4涂层修补 运输,安装后涂层破损处应按下面要求进行修补 采用原涂料并按原工艺进行修补,条件不具备时可选用适合现场条件的涂料体系进行修补,所 a 选涂料体系性能应满足表7要求,且与原体系具有良好的相容性 修补前要对漆膜损伤进行评估.然后做出修补计划,修补从损坏的最底涂层开始 b 如中间漆和面漆损伤,应对损伤涂层做表面拉毛处理,然后涂装相应中间漆、面漆; 如底漆损伤,应重新对金属基体进行表面处理,损伤部位周边完好的涂层也应打磨到St3级, d 然后涂装相应底渎、中间漆、面漆 大面积修补宜采用无气喷涂,小面积修补可采用多次刷涂,干膜厚度应不低于涂层设计值
7.4热喷涂金属保护 7.4.1涂层配套 7.4.1.1 按GB/T12608的规定选用热喷涂金属,推荐选用标记为Zn99.99、AI99.5,AIMg5或ZnAI15 的实心线材,线材直径宜为2.0mm或3.0nmm.
7.4.1.2按GB/T9793一2012的规定,推荐热喷涂金属覆盖层最小局部厚度见表10
GB/T33630一2017 表10热喷涂金属覆盖层最小局部厚度 最小局部厚度 涂层类型 Am C5-M C4 C3 150 Zn99.99 150 100 AI99.5 150 200 200 AIMg5 250 200 150 ZnAl15 150 150 100 7.4.2涂装要求 7.4.2.1涂装环境 施工场所无风砂和灰尘,涂装作业应在空气流通,光线明亮、清洁干净的厂房内进行
下列情况之 ,不应进行涂装作业: 施工现场环境温度低于0C a b 施工现场空气相对湿度高于85%; 基材表面温度低于周围空气的露点以上3C; c d 表面处理过的结构或机械部件已重新锈蚀或沾污 e 基材表面潮湿或者有可能溅湿
7.4.2.2涂装施工 热喷涂锌及锌合金可采用火焰喷涂或电弧喷涂,热喷涂铝及铝合金宜采用电弧喷涂
按相应工艺 进行涂装,施工过程中应满足如下要求 a)表面处理完成后4h内应进行热喷涂; b)两层或两层以上涂层应采用相互垂直、交叉的方法进行喷涂,单层厚度应不超过100"r m; c 热喷涂金属后应及时进行封闭,最长不应超过4h
7.4.3涂层检验与质量控制 过程检测按表8中1~7项的规定执行,涂装环境条件的检验按7.4.2.1的规定执行,出货品质检验 按表11的规定执行
表11热喷涂金属涂层质量检验 序号 测试项目 要求 测试方法 表面均匀一致,无气泡、无斑点、无附着不牢固的金属熔融颗粒及影响涂 外观 目视检查 层使用寿命的缺陷 厚度 GB/T9793 满足表10和设计文件提出的最小局部厚度要求 按GB/T9793一2012附录A供需双方协议选择试验方法,试验结果满足 附着力 GB/T9793 设计文件要求 10
GB/33630一2017 7.4.4涂层修补 运输、安装后涂层破损处应按下面要求进行修补 采用原涂料并按原工艺进行修补,条件不满足时热喷涂锌和锌合金涂层可用富锌底漆修补,热 a 喷涂铝和铝合金涂层可用铝粉底漆修补; b)选用中间漆和面漆对修补处进行加强,所选涂料体系应适合现场条件,且与金属涂层具有良好 的相容性
7.5热浸镀锌保护 7.5.1镀层配套 按GB/T470的规定选用Zn99.99或Zn99.995锌锭,熔融锌液中杂质总含量(铁,锡除外)应不 7.5.1.1 超过总质量的1.5%
7.5.1.2按GB/T19355的规定,推荐热浸镀锌层厚度见表12
7.5.1.3需要较厚镀层时,供需双方应探讨热浸镀技术上的可能性并注明相关技术条件
表12推荐热浸镀锌层厚度 单面镀层平均厚度(最小值 镀层类型 4m C5-M C4 C3 镀锌 200" 100' 55 该厚度按耐久性大于25年确定
该值大于GB/T13912规定的一般镀锌层厚度,在未与热浸镀锌方讨论以及未镀出满意的热浸镀锌样品之前, 不规定这类覆盖层 制件钢的厚度>l.5mm 7.5.2镀覆要求 7.5.2.1 镀覆准备 热浸镀锌施工前,需对制件进行处理,满足下述要求才可进行施工 制件基体表面已处理,无锈蚀、无污垢、无缺陷 a 制件封闭空腔,应按工艺要求设置导流孔和排气孔 b 制件尺寸和重量不超过镀锌池的承受能力; c 制件有合适悬挂点 d 有防止飞溅的锌液烫伤人体的保护措施
e 7.5.2.2镀覆施工 按脱脂,清洗、酸洗、清洗、助镀、烘干,镀覆,冷却及钝化或磷化、修整的工艺流程进行镀覆,要求 如下 脱脂、,酸洗均应采用槽内浸泡化学试剂的方式进行
a b 清洗应采用压力不小于0.4MPa的淡水进行冲洗
1
GB/T33630一2017 助镀应避免漏镀,浸润时间应不小于1min,厚壁件可延长至3min. c d 烘干应避免助镀剂膜被烘焦或发蓝色,否则应重新进行脱脂、酸洗和助镀
e 镀覆应按设计文件要求控制锌液温度和镀锌时间
从锌液中取出的镀锌件除去余锌后再浸人水中冷却,冷却水温度控制在20C50C
冷却 水可加钝化剂实现冷却钝化一步法,对于复杂的大型结构件和薄型工件,为避免水冷却产生较 大变形,可采用空气自然冷却
如后续需涂装涂料,冷却后无需钝化而直接进行磷化处理
制件镀锌完工后,宜对导流孔和排气孔进行封堵,当采用金属焊接封堵时,对焊接及周边影响 区域,按热喷涂锌工艺进行涂锌修补
h 制件交付前应以不损伤镀层的完整性为原则,对锐角、锌瘤等缺陷用专用工具进行修整
7.5.3镀层检验与质量控制 过程检测按表8中1一7项的规定执行,镀覆前检查按7.5.2.1的规定执行,出货品质检验按表13 的规定执行
表13热浸镀锌镀层质量检验 序号 测试项目 测试方法 要求 每个漏镀面的面积应不超过10cm=,漏镀面总面积应不超过镀件总表面积的 镀覆率 测量统计 0.5% 表面平滑、色泽均匀,无滴瘤、无锌刺、无起皮、无漏镀、无残余的溶剂渣、无锌瘤 外观 目视检查 和锌灰
只要镀层厚度大于规定值,镀件表面允许存在发暗或浅灰色的色彩不 均匀区城 GB/T13912 厚度 满足表12和设计文件抛出的平均厚度(最小值)要求 通常不需检测,如需检测按GB/T2694一2010规定的落锤法进行试验,试验后 附着力 GB/T2694 镀锌层不凸起、不剥离,则认为合格 7.5.4镀层修补 漏镀面及运输、安装后镀层破损处应按下面要求进行修补 采用热喷涂锌、涂敷富锌涂料或融敷锌合金等方法进行修补,再选用中间漆和面漆对修补处进 a 行加强 b)修补前应去除漏镀面或破损处的氧化皮和其他污物; 所选涂料体系应适合现场条件,且与金属涂层具有良好的相容性
7.6复合涂层保护 7.6.1涂层配套 7.6.1.1推荐热喷涂锌和涂料涂层配套方案见表14,推荐热浸镀锌和涂料涂层配套方案见表15
7.6.1.2复合涂层体系的性能应不低于表7的要求(不限于) 12
GB/33630一2017 表14热喷涂锌和涂料涂层推荐配套方案 额定干膜厚度 涂层 涂料类型 主要作用 Am c5-M C4 100 100 保护基材,为后续涂料提供附着基础 金属涂层 热喷涂锌 封闭漆 环氧封闭漆 20 20 减少金属涂层固有空隙,提高其使用寿命 中间漆 环类 200 120 增加涂层厚度,减少腐蚀介质渗透 60 60 面漆 聚氨酯类 提高耐候性,抵御紫外线、雨水的侵蚀 总干膜厚度 38O0 300 表15热浸镀锌和涂料涂层推荐配套方案 额定干膜厚度 4m 涂层 涂料类型 主要作用 C5-M C4 C3 50 50 金属涂层 热浸镀锌 保护基材,为后续涂料提供附着基础 50 底漆 环氧锋黄 提高金属涂层与后续涂层间的附着力 40 40 40 中间漆 环气类 200 120 增加涂层厚度,减少腐蚀介质渗透 40 60 面漆 聚氨酯类 60 60 提高耐候性,抵御紫外线、雨水的侵蚀 总干膜厚度 350 270 190 7.6.2涂装要求 按7.4.2或7.5.2的规定进行金属涂层施工,按GB/T30790.4的要求对金属涂层表面进行处理,再 按7.3.2的规定进行涂料涂层施工
7.6.3涂层检验与质量控制 金属涂层的检测按7.4.3或7.5.3的规定执行,涂料涂层的检测按7.3.3的规定执行
7.6.4涂层修补 金属涂层的修补按7.4.4或7.5.4的规定执行,涂料涂层的修补按7.3.4的规定执行
复合材料部件的防护 8.1叶片的防护 8.1.1涂层配套 8.1.1.1推荐防护涂层配套方案见表16
8.1.1.2防护涂层体系应满足表17规定的性能要求(不限于)
13
GB/T33630一2017 表16叶片防护涂层推荐配套方案 最低干膜厚度 涂层 涂料类型 主要作用 m 封闭打磨过的腻子表面,增加防护涂层厚度,延长防护 底漆 聚脉类、聚氨酯类 120 寿命 聚脉类、改性聚氨酯类、 保护被涂表面免受高速运转磨蚀及紫外线、雨水、潮气、 80 面漆 改性氟碳类 盐雾等的侵蚀 总干膜厚度 200 表17叶片防护涂层体系性能要求 序号 测试项目 性能指标 测试标准 附着力" >5MPa GB/T5210 23士2)C轴径3mm 不开裂、不剥落 弯曲试验 GB/T6742 圆柱轴) -40士2)轴径32mm" 不开裂,不剥落 不起泡、不剥落、不变色、不失光 指定要求" 高低温交变湿热(1000h 附着力‘>5MPa 不起泡、不剥落、不开裂、不粉化 耐人工加速老化 变色:2级,失光;2级 GB/T23987 UVB313,方法A,2000h 附着力>5MP% 不起泡、不剥落、不开裂 耐湿热(1000 变色:2级 GB/T1740 附着力>5MPa 不起泡、不剥落、不开裂 GB/T1771 耐盐雾(3000h) 附着力‘>5MPa 不起泡、不剥落、不开裂 耐水性(甲法,240 GB/T1733 变色:1级,失光:1级 耐油性(浸泡法,液压油,4 不起泡 GB/T9274 耐酸性(浸袍法,5%HSO,240h 变色:1级 耐碱性浸泡法,5%NaOH,240h 10 耐磨性(1000g/500r,CS-10 平均质量损耗30mg GB/T1768 12 GB/T1732 耐冲击(重锤高度50cm 不开裂、不剥落、无皱纱 采用不低于6mm厚玻璃钢试板进行检测
高低温交变晶热测试条件;5C持续2h;2h之内降到-40C;-0C持续6h;2h之内升到5C;5C持续 2h,2h之内升到[60,98%湿度];[60C,98%湿度]持续6h,2h之内降到5c
按上述过程循环,直至达 到规定时间
试验完成后试板在GB/T9278规定的标准条件下放置24h,再按GB/T5210进行附着力测试
14
GB/33630一2017 8.1.2表面处理 8.1.2.1涂装前应对叶片基材进行彻底的清洁处理处理后的表面应洁净,无脱模剂、油污、油脂等 污物
8.1.2.2基材干燥后对表面进行打磨,直至逆光观察时表面呈现无光/哑光状态,并清洁打磨留下的 粉尘 8.1.2.3采用大缝腻子对叶片进行修型,填充被涂表面凹陷,干膜厚度应不超过1.5mm;采用针孔腻子 封闭表面针孔砂眼,填充被涂表面、大缝腻子表面针孔砂眼,干膜厚度应不超过200m;腻子与涂料体 系应具有良好的相容性
8.1.2.4腻子干燥后,采用基材处理工艺对腻子表面进行打磨和除尘
砂纸粒度、可打磨时间、腻子施 工均应满足涂料供应商提供的工艺要求
8.1.2.5对基材表面进行除静电处理 8.1.3涂装要求 涂装施工按7.3.2的规定执行
8.1.4涂层检验与质量控制 8.1.4.1涂层体系的型式检验包括表17规定的全部项目,涂料供应商应提供国家认可检测机构出具的 涂层性能检测报告,必要时可进行复检
8.1.4.2表面处理及涂装施工过程应满足8.1.2、8.1.3的规定,如不满足应立即停止施工,处理至合格 后才可继续
出货品质检验按表18的规定执行
表18叶片涂料涂层质量检验 序号 测试项目 测试方法 测试频率或范围 要求 表面平滑、色泽均匀,无露底、无剥落、无起泡、无裂纹、无 涂层外观 目视检查 100%表面检查 针孔,防雷接闪器表而无异物覆盖
允许有不影响涂层防 护性能的轻微刷痕、流挂和少量杂质 所有测点的干膜厚度应不低于额定干膜厚度的90% 低于额定干膜厚度但不低于额定干膜厚度的90%测点应 干膜厚度”GB/T13452.2 每一批次 不超过总测点的10% 所有测点的干膜厚度应不大于规定的最大干膜厚度,最大 干膜厚度不应大于额定干膜厚度的3倍 附着力>5MP 附着力" GB/T5210 每一批次 干膜厚度与湿膜厚度的对应关系经实际验证及工艺评审后,可通过检测湿膜厚度代替干膜厚度的检测
采用叶片同类型材料试板进行检测,试板随叶片一起进行涂装,必要时可在叶片表面直接进行附着力检测
8.1.5涂层修补 运输、安装后涂层破损处应采用原涂料并按原工艺进行修补
条件不具备时可选用适合现场条件 的涂层体系进行修补,所选涂层体系性能应满足表17的要求,且与原体系具有良好的相容性
15
GB/T33630一2017 8.2机舱罩和导流罩的防护 8.2.1涂层配套 宜采用胶衣涂层体系,推荐体系见表19,腔衣涂层体系应满足表20规定的性能要求(不限于) 表19机舱罩、导流罩胶衣涂层体系 额定干膜厚度 涂层 涂料类型 主要作用 mm 底面合 聚酯胶衣 400 保护机舱罩和导流罩免受磨蚀及紫外线、雨水、潮气、盐雾等的侵蚀 表20机舱罩、导流罩胶衣涂层体系的性能要求 序号 测试项目 性能指标 测试标准 >5NMP% 附着力 GB/T5210 GB/T10125 耐盐雾(Nss,3000h) 不起泡,不剥落,不开裂,不变色,附着力">5MPa 不起泡、不剥落、不开裂、不粉化、不变色 耐人工加速老化 失光;2级 GB/T23987 UVB313,方法A,2000h 附着力">5MPa 不起泡,不剥落,不开裂,变色;2级 耐湿热(1000h) GB/T1740 附着力">5MPa 耐磨性(1000g/500r,CS-10 平均质量损耗30mg GB/T1768 耐冲击重锤高度30nm) GB/T1732 不开裂、不剥落、无皱纹 试验完成后试板在GB/T9278规定的标准条件下放置24h,再按GB/T5210进行附着力测试 8.2.2表面处理 8.2.2.1 涂装前对模具表面进行打磨,砂纸磨料粒度应满足GB/T9258.3的规定
8.2.2.2打磨后再对模具表面进行抛光和清理,表面应光滑洁净,无油脂、水分和粉尘等异物
8.2.2.3清理后对模具表面进行封孔处理并涂抹脱模剂
8.2.3涂装要求 8.2.3.1涂装环境 施工场所无风砂和灰尘,涂装作业应在空气流通、光线明亮、清洁干净的厂房内进行
并满足下述 条件才可进行涂装作业: 施工现场环境温度在5C40C,环境温度低于15C时需要对胶衣和模具表面加热,并根据 a 环境温度调节固化剂用量 b 施工现场空气的相对湿度低于80%; 模具表面温度比胶衣温度高2C3C
c 16
GB/33630一2017 8.2.3.2涂装施工 采用高压无气喷涂,当喷枪不能保持合理位置(如深槽等)时可采用刷子涂刷,其要求如下 涂装前检查胶衣品种、型号,规格.耽存期限应符合设计文件的规定 b 胶衣用稀释剂、固化剂及色浆的类型和用量应遵循产品使用说明书要求 在原桶内充分搅拌胶衣,尽量采用不产生漩涡的机械搅拌机,并控制速度以免混人气泡 c 喷枪应匀速平移,开始时喷嘴由外移向模具,停止时从模具的边缘移向外面;喷嘴类型,喷射压 d 力和喷射距离按产品说明书要求确定 采取2遍3遍喷涂,喷涂间隔应符合产品使用说明书要求; e 涂装作业中应按GB/T13452.2规定的方法检测每一道涂层的湿膜厚度; f g 胶衣基本固化后充分固化前,即可进行后续的糊制或铺层操作
8.2.4涂层检验与质量控制 8.2.4.1胶衣涂层体系的型式检验包括表20中的全部项目,涂料供应商应提供国家认可检测机构出具 的涂层性能检测报告,必要时可进行复检
8.2.4.2表面处理及涂装施工过程应满足8.2.2,8.2.3的规定,如不满足应立即停止施工,处理至合格 后才可继续,出货品质检验按表21的规定执行
机舱罩、导流罩涂料涂层质量检验 表21 序号 测试项目 测试方法 测试频率或范围 验收准则 表面平滑、色泽均匀,无露底、无剥落、无起泡、无 外观 目视检查 100%表面检查 裂纹、无针孔,允许有不影响胶衣防护性能的轻 微刷痕、流挂和少量杂质 所有测点的干膜厚度应不低于额定干膜厚度 190% 的! 低于额定干膜厚度但不低于额定干膜厚度的 干膜厚度" GB/T13452.2 每一批次 90%测点应不超过总测点的10% 所有测点的干膜厚度应不大于规定的最大干膜 厚度,最大干膜厚度不应大于额定干膜厚度的 3僧 GB/T5210 附着力" -批次 附着力>5MPa 每 干膜厚度与湿膜厚度的对应关系经实际验证及工艺评审后,可通过检测湿膜厚度代替干膜厚度的检测
采用与实际使用材料同类试板进行检测,试板随部件一起进行涂装,必要时可在部件表面直接进行附着力 检测 8.2.5涂层修补 运输、安装后涂层破损处应采用原胶衣并按原工艺进行修补
条件不具备时可选用适合现场条件 的涂层体系进行修补,修补用涂层体系性能应满足表20中的规定,且与原体系具有良好的相容性
17
GB/T33630一2017 9 维护与检查 9.1海上风力发电机组的腐蚀状况及防腐蚀效果应定期进行巡视检查和定期检测
9.2巡视检查周期宜为一年,内容主要包括涂层老化破坏状况及结构腐蚀状况
g.3定期检测周期一般为5年,根据巡视检查结果可适当缩短检测周期
检测应查明结构腐蚀程度、 评价腐蚀防护系统效果,预估腐蚀防护系统使用年限,提出处理措施和意见
g.4机组吊装前应提供机组干洁区环境腐蚀性型式检测报告
机组运行第一年抽取风场机组总数量 的5%(不少于1台)按附录A对干洁区腐蚀速率进行检测,以评估腐蚀环境控制效果,如检测结果未满 足表1要求,提出处理措施和意见
g.5检测用仪器、设备、量具应经计量认证并在检定有效期内
9.6检查、检测结果及维护应详细记录并妥善保存以备核查
18
GB/33630一2017 附 录 A 规范性附录 腐蚀速率检测 A.1检测方法 将碳素结构钢试样暴露在被测大气环境中持续一年,检测试样暴露前后的质量变化,按式(A.1)计 算出试样在被测大气环境中的腐蚀速率
m (A.1 reor" At 式中 腐蚀速率,单位为克每平方米年[g/ma)]; reorr 质量损失,单位为克g); m 表面面积,单位为平方米(m'); A 暴露时间,单位为年(a)
A.2试样制备 试样制备如下: 试样为碳素结构钢(Cu:0.03%一0.10%,P;<0.07%)矩形平板,最佳尺寸为100mmm×150mm. a 应不小于50mm×100mm,厚度1mm2mm; 下料时试样单边应预留一定尺寸,以便最终通过机加工将下料工序的影响区切除,加工完成后 b 应对试样进行校平; 试样表面不允许喷砂或抛丸处理 根据被测环境空间合理选择试样数量,一般为奇数且不小于3; d 制备一件对比试样,储存在无腐蚀的环境中
e A.3试样前处理 暴露试验前应对试样进行表面处理,并测量尺寸和质量,其过程如下: 对试样表面进行除油脂、除锈以及氧化皮等,按GB/T16545规定去除试样表面腐蚀产物 a b 对试样进行标识及质量、尺寸测量,质量精确到0.1mg,尺寸精确到0.1mm; 表面处理后的试样操作时应穿戴清洁手套,并将试样保存在干燥、清洁的环境内,严禁机械划 c 伤或腐蚀 A.4试样安装 前处理完成后应尽快将试样安装到试验现场,其方法如下 试样安装时操作人员应当穿戴清洁手套,并保证安装过程试样表面不被油脂等污染,严禁机械 a 划伤或腐蚀等; b 夹持装置与试样接触位置应当选用陶瓷、尼龙或聚酰胺等材料,夹持装置应固定牢固,避免试 19
GB/T33630一2017 样发生掉落等 c 根据被测环境空间合理选择试样安装位置,准确反映被测大气环境的腐蚀状态 d 建立试样安装档案便于试验数据记录
A.5试验记录 试样暴露期间应每三个月对试样进行检查并记录试样表面状态变化情况等,其记录如下 试样安装时及后期的定期巡检,应对试样正反面进行拍照和记录,并检查试样及其夹持情况 a b)记录时应包含腐蚀产物的颜色、结构,均匀性,以及它们的附着性与剥离倾向
A.6试样后处理 暴露试验结束后应按如下方法及时将试样取回实验室进行后处理,其方法如下 取回过程中应当对试样妥善保存,严禁试样遭受机械划伤或腐蚀; a 按GB/T16545去除试样表面腐蚀产物并称重重复几次直到质量趋于稳定,质量精确到 b 0.1mg; 按式(A.l)计算出试样在被测大气环境中的腐蚀速率 A.7 试验报告 试验报告应包含以下内容 试验场描述; a 试样材质、表面状态、质量、尺寸以及数量; b 试样初始性能及安放位置 c 试样暴露、取出和评价日期; d 试样暴露过程检查记录表及试验前、中、后的照片 e 试样失重检测记录表,及年腐蚀速率平均值; fD) 试样测量用仪器名称、类型、特性、检定有效期 日 h)试验结论
20
海上风力发电机组防腐规范GB/T33630-2017解读
随着全球对可再生能源的需求不断增加,海上风力发电作为一种新兴的清洁能源,受到越来越多的关注。然而,由于海洋环境的特殊性,海上风力发电机组的防腐工作尤为重要。因此,《海上风力发电机组防腐规范GB/T33630-2017》标准的推出对于确保海上风力发电机组长期稳定运行至关重要。
该标准主要针对海上风力发电机组各部件进行规范,旨在提高海上风力发电机组的抗腐蚀性能,保证其长期、安全运行。标准中规定了海上风力发电机组各部件的涂层施工质量、涂层材料的选择、涂层施工要求、涂层检测方法以及防腐材料的储存等内容。
其中,海上风力发电机组各部件的涂层是保证其抗腐蚀性能的重要组成部分。标准中规定了涂层施工的质量控制要求和检测方法,以确保其符合标准要求。此外,标准还对涂层材料和防腐材料的选择、储存等方面进行了详细的规定。
如今,海上风力发电作为一种新兴的清洁能源,正在快速发展。但是,海洋环境的特殊性也给海上风力发电机组的防腐工作带来了很大的挑战。因此,我们必须认真贯彻执行《海上风力发电机组防腐规范GB/T33630-2017》标准,加强防腐工作,提高海上风力发电机组的抗腐蚀性能,推动全球可再生能源事业的健康发展。