GB/T30582-2014
基于风险的埋地钢质管道外损伤检验与评价
Risk-Based-Inspectionandassessmentmethodologyofexternaldamageforburiedsteelpipelines
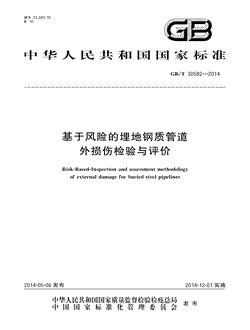
- 中国标准分类号(CCS)E16
- 国际标准分类号(ICS)23.040.10
- 实施日期2014-12-01
- 文件格式PDF
- 文本页数55页
- 文件大小1.06M
以图片形式预览基于风险的埋地钢质管道外损伤检验与评价
基于风险的埋地钢质管道外损伤检验与评价
国家标准 GB/T30582一2014 基于风险的埋地钢质管道 外损伤检验与评价 tmethodology Risk-Baset-lnspettonand aSsesSment ofexternaldamageforburiedsteelpipelines 2014-05-06发布 2014-12-01实施 国家质量监督检验检疫总局 发布 国家标准化管理委员会国家标准
GB/I30582一2014 目 次 前言 范围 规范性引用文件 术语和定义 总则 数据收集 基于风险的外损伤检验 埋地钢质管道合于使用评价 外损伤综合评价 20 附录A(规范性附录)管道外损伤检验方法及检验比例 22 附录B(规范性附录)材料性能测试方法 2s 附录c规范性附录)体积型缺陷管道剩余强度评价 37 附录D(规范性附录)含凹陷管道的剩余强度评估 4G 附录E规范性附录不良条件下埋地钢质管道安全评定 附录F(规范性附录埋地钢质管道外腐蚀剩余寿命预测 56
GB/T30582一2014 前 言 本标准按照GB/T1.1一2009给出的规则起草
本标准由全国锅炉压力容器标准化技术委员会(SAC/TC262)提出并归口
本标准起草单位:特种设备检测研究院、国家质量监督检验检疫总局特种设备安全监察局、中 国石油大学(北京,北京科技大学、北京工业大学、石油化工股份有限公司镇海炼化分公司、上海质 量技术监督局、石油西南油气田安全环保与技术监督研究院、深圳市燃气集团有限公司、石油 天然气集团公司长庆油田分公司、石油天然气股份有限公司大庆油田特种设备检验中心、石油 化工股份有限公司油品销售事业部、上海市特种设备监督检验技术研究院、石油化工股份有限公司 上海高桥石化分公司
本标准主要起草人;何仁祥、陶雪荣杨永,黄解、孟涛、杨绪运、周德敏、刘长征、修长征、孙亮、 王笑梅、帅健,马彬,刘智勇,周方勤、秦林、高健、王新华、徐成裕,王善江,陈秋雄、安跃红.陈运文,李佩、 臧国军、王兴龙、李曙华、吴亚滨、单洪翔、卜文平、顾雪东、蔡建平、杨惠谷
m
GB/I30582一2014 基于风险的埋地钢质管道 外损伤检验与评价 范围 本标准规定了基于风险的埋地钢质管道外损伤的检验与评价内容,给出了检验与评价方法
本标准适用于长输管道、集输管道、公用管道、工业管道和动力管道中的埋地钢质管道外损伤的检 验与评价,其他的埋地钢质管道可参照本标准执行
规范性引用文件 下列文件对于本文件的应用是必不可少的
凡是注日期的引用文件,仅注日期的版本适用于本文 件
凡是不注日期的引用文件,其最新版本(包括所有的修改单)适用于本文件 GB/T223(适用部分)钢铁及合金化学分析方法 金属材料拉伸试验第1部分;室温试验方法 GB/T228.l1 GB/T229 金属材料夏比摆锤冲击试验方法 化学试剂过硫酸铵 GB/T655 金属和合金的腐蚀不锈钢晶间腐蚀试验方法 GB/T4334.l 金属材料维氏硬度试验第1部分;试验方法 T GB 4340.1 金属在硫化氢环境中抗特殊形式环境开裂实验室试验 GB 4157 GB/T8650管线钢和压力容器钢抗气致开裂评定方法 石油天然气工业管线输送系统用钢管 GB/T971l GB/T9854化学试剂二水合草酸(草酸) GB/T192852014埋地钢质管道腐蚀防护工程检验 GB/T26610.1承压设备系统基于风险的检验实施导则第1部分;基本要求和实施程序 GB/T27512埋地钢质管道风险评估方法 GB/T50251输气管道工程设计规范 JB/T4730(适用部分)承压设备无损检测 SY/T4109石油天然气钢质管道无损检测 SY/T6476输送钢管落锤撕裂试验方法 TSGD7003压力管道定期检验规则 长输(油气)管道 公用管道 TsGD7004压力管道定期检验规则 国质检锅(2003)108号在用工业管道定期检验规程(试行 术语和定义 下列术语和定义适用于本文件
外损伤 externaldamage 由外腐蚀、外力破坏(包括机械破坏不良地质条件和不良地面条件等)危害造成的埋地钢质管道结
GB/T30582一2014 构不完整性 3.2 合于使用评价fitnessforserieeassessmenmt 对含有缺陷或损伤的管道进行的一种评价,以确定在预期的工作条件下是否可以继续安全运行
3.3 剩余强度 remainingstrength 含缺陷管道的剩余承载能力
3.4 凹陷dent 凹陷为管壁受外部挤压或碰撞产生径向位移而形成的局部塌陷,是由于管壁永久塑性变形而使管 道横截面发生的形状改变
3.5 划伤scratches 外部物体接触导致管道表面金属损失
3.6 不良条件unfaverableconditiom 不良地质条件和不良地面条件
不良地质条件包括采空沉陷、冻土、滑坡和断层等;不良地面条件 包括场地占压和洪水等
3.7 剩余寿命remaininglite 在预期工作条件下,损伤缺陷尺寸扩展到临界尺寸所需的时间
总则 4.1本标准规定的检验与评价是按照TsG7003、TsGD7004和国质检锅(2003)108号规定开展的针 对埋地钢质管道外损伤的全面检验、合于使用评价与综合评价
4.2本标准通过基于风险的检验,识别已经发生,正在发生或预测可能发生的外损伤,并进行合于使用 评价及综合评价,对危及管道安全的缺陷与问题提出处理意见
4.3基于风险的埋地钢质管道外损伤检验与评价关键要素及流程见图1
GB/T30582一2014 确定检验与评价范围 数据收集/更新(第5章 潜在危险辨识(6.2.1) 风险评估(6.2.2) 检验策略制定(6.2.3 检验方案制定(6.2.4 外损伤检验6.3) 合于使用评价第7章 外损伤综合评价8.21 问题处理(8.3) 图1基于风险的外损伤检验评价流程图 4.4开展检验与评价的单位和人员应在认可的资格范围内从事检验与评价工作,并对检验与评价结论 的真实性、准确性和有效性负责
注:真实性表示结论、报告以事实为基础,不作假证;准确性表示结论,报告所涉及的检测数据符合相关要求;有效 性表示检验机构的资质,检验人员的资格符合要求,所使用的仪器设备在检定校准有效期内,检验依据合法,报 告审批程序符合要求
4.5基于风险的埋地钢质管道外损伤检验与评价除执行本标准外,应符合现行有关国家标准的规定
5 数据收集 5.1检验与评价需要的数据 5.1.1在进行检验与评价前应对各类相关数据进行全面收集、整合、对比及分析
5.1.2开展外损伤检验与评价应收集以下典型数据: 管道类型; a b)材质 检测,维修和更换记录; c d)输送介质; 运行条件; e f 安全与监测系统;
GB/T30582一2014 g损伤模式、速率和严重程度; h 沿线人员密度; 腐蚀防护系统 停产损失 5.1.3应采用一致的原则进行数据收集,收集的数据应真实有效
5.1.4在数据收集过程中,当现有数据不完整时,应根据缺少数据的重要程度,通过实施现场检测进行 数据收集
5.2 数据来源 5.2.1设计、制造、安装与竣工资料,其中包括 设计文件(包括计算书,施工图,说明书等),设计变更 a 管道元件制造质量证明文件、监督检验报告; b 管道安装竣工验收资料、管道安装监督检验报告、工程质量检验和评定报告; c) 采用的法规和标准 d e)腐蚀防护系统; 水工保护 f 泄漏检测与监控系统; g h)紧急泄压与泄放系统
5.2.2检测与评价报告,其中包括 a)时间与周期 b) 类型和数量" e)维修与更新 d 结论 5.2.3工艺文件,其中包括 a)介质成分分析(含腐蚀成分); b) 数据采集系统 e)运行规范 d 应急预案 e)运行日志与工艺记录; f 管理变更记录
5.2.4失效数据文件,其中包括: a)泄漏数据 b 腐蚀数据 e)外力破坏数据 d) 地质灾害数据
5.2.5管道事故调查资料
5.2.6现有的完整性管理系统或地理信息系统
5.3数据更新 管道经过检验与评价后,管道使用单位应对管道数据进行完善和更新,并补充到管道数据库中
GB/T30582一2014 基于风险的外损伤检验 6.1基于风险的外损伤检验流程 基于风险的埋地钢质管道外损伤检验流程如图2所示 带在 检验 检验 检验 风险 检验 方案 危险 策略 结论 评估 实随 辨识 制定 制定 环境腐蚀性检测 不开 开找 挖检 直接 窝蚀 检验 外防腐层检测 验 防护 系统 检验 阴极保护系统检测 机 焊 排流系统效果检渊 机械 破坏位置确认 破坏 检验 不良条 件下管 管道危险位置确认 道检验 图2基于风险的外损伤检验流程图 6.2基于风险的外损伤检验步骤 潜在危险辨识 6.2.1 检验人员应在数据收集分析基础上,辨识危害管道结构完整性的潜在危险
潜在危险可分为以下几种 a)固有危险,如制造与安装、改造、维修施工过程中产生的缺陷 运行过程中与时间有关的危险,如内腐蚀,外腐蚀,应力腐蚀; b e)运行过程中与时间无关的危险,如第三方破坏,误操作,外力机械破坏及不良地质条件等; 其他危害管道安全的潜在危险
d) 检验人员应通过辨识所有危害管道结构完整性的潜在危险以确认能否应用本标准,否则应采取其 他检验与评价方法
6.2.2风险评估 6.2.2.1风险评估包括风险预评估和风险再评估
风险预评估是检验机构对资料审查分析完成后,全 面检验开展前,按照有关安全技术规范及其相应标准进行的风险评估
风险再评估是使用单位对管道
GB/T30582一2014 采取相应的修复或采取降压措施,并且经评价机构确认后,评价机构重新对风险预评估结果进行的 修正
6.2.2.2风险评估人员应充分了解每种管道风险评估方法的优缺点,并应在相应的资质范围内开展评 估工作 6.2.2.3应遵守GB/T26610.1的基本原则和要求,并按照GB/T27512进行风险评估 6.2.2.4风险评估应按照GB/T27512进行风险区段划分
6.2.2.5风险评估人员应根据管道实际情况,以修正模型开展外损伤为主要潜在危险的风险评估
在 基本模型的架构下调整相关因素的评分权重,或增加所评估管道特有的风险因素,或在基本模型中剔除 不影响所评管道各区段风险排序的风险因素
6.2.3检验策略制定 6.2.3.1检验策略的制定应遵守国家相关法律,法规、规章和安全技术规范
检验策略应由检验人员依据风险评估报告制定,并征询使用单位意见
6.2.3.2 6.2.3.3制定检验策略的人员应具有足够的材料.电化学腐蚀、外腐蚀检测及合于使用评价等知识背景 和实践经验,单位应建立制定基于风险的检验策略质量控制程序
6.2.3.4基于风险的检验策略一般包括以下内容 管道的潜在失效模式 a b)设定的风险可接受水平; 管道检验前的风险水平; c) 实施检验后预期可达到的风险水平 d 检验的时间 检验的管道区段 f g检验针对的潜在危险; 检验的范围 h 检验的方法、仪器及比例
6.2.3.5管道风险可接受水平可使用失效可能性、,失效后果或风险级别来表述,根据管道使用单位的实 际情况,由用户与检验策略制定人员协商确定,但应满足法律、法规、规章和安全技术规范的有关规定
宜以风险级别来描述风险可接受水平
6.2.3.6检验区段划分时应综合考虑以下因素 a)风险评估的区段,检验区段长度不应小于风险评估区段长度; 检验方法及检测工具的差异; D 检验实施的经济性
c 6.2.4检验方案制定 6.2.4.1检验人员应依据风险预评估结果和基于风险的检验策略内容,按照相关法规标准制定检验 方案
6.2.4.2检验方案应至少包括以下内容要求: a安全注意事项; b检验人员; c 检验设备 d)检验方法; 检验项目: e f检验比例
GB/T30582一2014 检验记录格式; g h 检验报告格式; 管道使用单位配合项目
6.2.4.3检验人员应于检验前就检验方案征询管道使用单位意见
6.2.5检验实施与结论 检验机构与人员应根据外损伤检验方案开展检验工作,外损伤检验包括不开挖检验和开挖直接检 验,并根据检验情况给出单项检验结论
6.3基于风险的外损伤检验过程 6.3.1 检验时间 6.3.1.1新建管道投用后3年内一般应进行首次基于风险的检验 6.3.1.2其他管道检验时间的确定以管道风险是否达到风险可接受水平来调整原定检验周期
6.3.1.3属于下列情况之一的管道,当只能进行外损伤检验时,应当立即进行外损伤检验与评价 a)运行工况发生显著改变从而导致运行风险提高的; b)输送介质种类发生重大变化,改变为更危险介质的 e停用超过1年后再启用的; d年度检查结论要求进行外损伤检验的; 所在地发生地震、滑坡、泥石流等重大地质灾害的 6.3.2外损伤不开挖检验 -般要求 6.3.2.1 6.3.2.1.1埋地钢质管道外损伤不开挖检验包括腐蚀防护系统检验、机械破坏检验和不良条件下管道 检验
6.3.2.1.2I、级公路、高速公路、铁路和大中型水域穿越管段、检验人员认为重要的管段,可采用行 业认可的其他方法进行检验
6.3.2.2腐蚀防护系统检验 6.3.2.2.1腐蚀防护系统检验的内容包括环境腐蚀性检测,外防腐层检测、阴极保护系统检测和排流系 统效果检测
6.3.2.2.2确定腐蚀防护系统检验比例时应考虑不同类别,不同风险等级管道的差异
6.3.2.2.3环境腐蚀性检测包括土壤腐蚀性检测和杂散电流检测: 土壤腐蚀性检测采用抽样检测,必要时可根据腐蚀活性增加土壤腐蚀抽样检测点
检测方法 见 GB/T19285一2014的附录A,检测比例见本标准附录A中A.l; b杂散电流检测包括直流杂散电流检测和交流杂散电流检测
应对日常巡检、年度检查或外损 伤检验过程中发现的杂散电流干扰区域进行检测
检测方法及评价准则见GB/T19285
6.3.2.2.4外防腐层检测包括外防腐层整体状况和局部破损点的不开挖检测 外防腐层整体状况不开挖检测可采用直流电流衰减法和交流电流衰减法,并利用外防腐层电 a 阻率,电流衰减率等指标进行评价,检测评价方法见GB/T19285一2014的附录I: b外防腐层破损点不开挖检测可采用交流电位梯度法和直流电位梯度法,并利用破损点密度指 标进行评价,检测方法见GB/T19285一2014的附录D 外防腐层不开挖检测项目及比例见A.1
GB/T30582一2014 6.3.2.2.5阴极保护系统检测应包括阴极保护效果检测和阴极保护设施状况检测
检测对象包括外加 电流阴极保护系统和牺牲阳极阴极保护系统,检测评价方法见GB/T19285 针对外加电流阴极保护系统,当管道风险等级为高或较高等级时,应进行100%密间隔断电电 位检测;当管道风险等级为中或低风险等级时,应在电位测试桩处进行管地电位检测;发现异 常时,应对该处前后管段进行100%密间隔断电电位检测 b)针对牺牲阳极阴极保护系统,外加电流与牺牲阳极联合保护系统,当管道风险等级为高或较高 等级时,应进行 100%密间隔电位检测;当管道风险等级为中或低风险等级时,应在电位测试 桩处进行管地电位检测;发现异常时,应对该处前后管段进行密间隔电位检测; 检测管道无阴极保护电位测试桩时,应开挖进行管地电位检测,开挖间隔不宜大于1km; d阴极保护设施检测时,针对外加电流阴极保护系统,可对恒电位仪、辅助阳极床、绝缘装置及电 连接装置等设施性能状况进行检测;针对牺牲阳极阴极保护系统,可对电位测试桩、牺牲阳极 等设施性能状况进行检测 6.3.2.2.6排流系统检测应包括排流效果检测和排流设施检测
检测对象包括直流排流和交流排流系 统,检测内容测评价方法见GB/T19285 排流效果检测通过排流点电位检测、杂散电流干扰段阴极保护效果检测,交流接地体安全距离 H 检测等方法检测排流效果
交流接地体安全距离的测量范围应包括已知交流接地体安全距离 的复核和未知交流接地体的调查与测量 b应对包括排流器,排流线,接地床,电绝缘装置等设施性能状况检测
6.3.2.3机械破坏检验 通过数据收集、日常巡查,并结合现场地物地貌分析、管道附属设施完好情况统计及第三方活动情 况调查等,确定管段是否存在机械破坏;再对管道走向,埋深和防腐层状况进行不开挖检测,确定机械破 坏的准确位置
6.3.2.4不良条件下管道检验 对管道走向、位置、埋深等进行不开挖检测,确定是否存在不良条件造成的管道本体凹陷、变形、漂 管等潜在危险 a)采空沉陷区管道不开挖检验项目有;管道途经地区地下资源开采活动资料收集,地表沉降情况 调查,管道的走向、位置、埋深检测和高程测量; 冻土区管道不开挖检验项目有;历史冻土深度调查,管道的走向、位置和埋深检测; b 滑坡区管道不开挖检验项目有;管道途经地区地质资料调查,管道的走向、位置和埋深检测,坐 标与高程测量
计算管道中心线位移量; 断层区管道不开挖检验项目有:管道途经地区地质断层状况调查,管道的走向、位置和埋深 检测; 占压不开挖检验项目有;地面建构筑物情况调查,管道的走向、位置,埋深和防腐层状况、阴极 保护效果检测 洪水区不开挖检验项目有;河床、河岸的稳定性和洪水季节性资料调查,管道的走向、位置和埋 深检测
6.3.3外损伤开挖直接检验 6.3.3.1一般要求 埋地钢质管道外损伤开挖直接检验包括外腐蚀直接检测、机械破坏直接检测、,不良条件下直 6.3.3.1.1 接检测及焊缝无损检测,所选择的检测项目应满足合于使用评价的需要 6.3.3.1.2开挖点的选取应当结合数据收集中的错边、咬边严重的焊接接头以及碰口与连头焊口,使用
GB/I30582一2014 中发生过泄漏,第三方破坏的位置,并重点选择风险评估中属于较高风险及高风险等级管段
6.3.3.2外腐直接检测 6.3.3.2.1外腐蚀直接检测包括土壤腐蚀性检测、外防腐层直接检测、管地电位检测和管体腐蚀检测
6.3.3.2.2外腐蚀开挖点数量确定原则见表1
每条管道应至少开挖一处
表1埋地钢质管道外腐蚀开挖点数量确定原则 单位为处每千米 腐蚀防护系统质量等级 管道类别 长输气管道.GB1-级和GB1-l级高压燃气管 不开挖 1.01.2 1.82.0 0.1 道,联合站至长输首站集输气管道 长输油管道、联合站至长输首站集输油管道,集 0.60.8 1.21.5 不开挖 0.l 输站至联合站集输管管道 GB1-川级次高压燃气管道.GB1-级次高压燃气 0.05 0.60.8 1.21.5 0.l 管道 GB1-V级和GB1V级中压燃气管道.G2级热 不开挖 0.05 0.3 0.60.8 力管道 GC1级工业管道 0.5 1.01.2 GC2级工业管道、GD1级动,GD2级动力管道 0.05 0.1 0.60.8 1.21.5 GC3级工业管道 不开挖 0.05 0.3 0.60.8 0.,05 1.2~1.5 单井站至集输站集输管道 0.1 0.60.8 注,当有机械破坏和不良条件管体检验需要的开挖点时,开挖数量可纳人本表所需比例 6.3.3.2.3土壤腐蚀性检测 土壤腐蚀性检测包括土壤质地、土壤电阻率,氧化还原电位,管地电位、土壤pH值、土壤的含水率、 土壤含盐量、土壤C含量等参数的测试,检测方法依据GB/T192852014的附录A 6.3.3.2.4外防腐层直接检测 包括外观检查、漏点检测、防腐层厚度检测和粘结力检测,检测评价方法见GB/T19285一2014的 附录C,并应遵守以下要求 应对开挖探坑中露出的防腐层全部进行检测 b) 进行防腐层厚度检测时,应检测管道截面12个时钟位置的厚度
6.3.3.2.5管地电位检测 应在开挖处使用饱和硫酸铜参比电极检测近参比管地电位 管体外腐蚀检测 6.3.3.2.6 管体外腐蚀检测项目包括 a)外观检查;应检测外腐蚀的位置、腐蚀程度,形貌等; b腐蚀产物分析;如存在腐蚀产物,应检测腐蚀产物分布(均匀、非均匀厚度,颜色、结构(分层 状,粉状或多孔),紧实度(松散、紧实,坚硬)
腐蚀产物分析可采用现场初步鉴定方达,现场初 步鉴定方法见A.2; 外腐蚀尺寸检测;包括腐蚀深度和腐蚀面积检测,并检测腐蚀缺陷在管道轴向与环向上的投影 长度,对于腐蚀严重缺陷或位于风险等级为高或较高等级区段的腐蚀缺陷,应采用危险厚度截 面法检测腐蚀缺陷尺寸,检测方法见A.3
管道风险等级为中或低风险等级的腐蚀缺陷,可采 用危险厚度截面法检测腐蚀缺陷尺寸 内腐蚀尺寸检测;应采用外壁漏磁、超声扫描成像或超声测厚等技术判断管道是否存在内腐 蚀,检测要求见外腐蚀尺寸检测;
GB/30582一2014 选取未腐蚀区域进行管道壁厚的检测,应检测管道截面12个时钟位置的厚度
6.3.3.3机械破坏直接检测 对存在机械破坏的管段进行开挖检测,包括外观检查、尺寸检测、管体损伤无损检测等项目 外观检查:应检测机械破坏的位置、损伤类型、损伤程度、形貌等 a b)尺寸检测;应检测损伤的深度和面积,检测方法与外腐蚀检测相同
对于沟槽状缺陷应检测根 部曲率半径 管体缺陷无损检测;应对凹陷的边缘和沟槽状缺陷进行磁粉检测,并对凹陷底部进行射线检 测
具体检测方法见A.4
6.3.3.4不良条件下直接检测 对不良条件下存在损伤的管段进行开挖检测,包括管道偏移量检测和损伤检测等项目 a)管道偏移量检测;采用坐标测量等方法检测管段最大偏移量; b 损伤检测;应对不良条件下管道表面损伤进行检测,检测方法同6.3.3.3
6.3.3.5焊接缺陷无损检测 6.3.3.5.1焊接缺陷无损检测按照JB/T4730或sY4109执行,一般采用射线或者超声方法,也可采用 国家质检总局认可的其他无损检测方法
6.3.3.5.2焊接缺陷无损检测应与探坑检测、露管段检测相结合
开挖检测部位的焊接接头应100%无 损检测
必要时还应对以下焊接接头进行无损检测 a)制造、安装中返修过的焊接接头和安装时固定口的焊接接头; b错边、咬边超标的焊接接头; 泵、压缩机、调压站、分水器、阀室进出口第一道焊接接头或相近的媒接接头; d)穿跨越部位、出土与人土端附近的焊接接头; 表面检测发现裂纹的焊接接头 e 硬度检验和厚度测试中发现异常的接接头; 们 检验人员和使用单位认为需要抽查的其他焊接接头
g 埋地钢质管道合于使用评价 7.1一般要求 7.1.1外损伤检验完成后,应及时开展埋地钢质管道合于使用评价(以下简称合于使用评价)工作
合 于使用评价包括材料适用性评价、剩余强度评估、不良条件下管道安全评定和剩余寿命预测
7.1.2根据外损伤检验管道类别、检验结论确定需开展的合于使用评价项目 7.1.3评价机构必须制定合于使用评价方案(包括安全措施和应急预案),征询使用单位的意见,并由 评价机构授权的技术负责人审批
合于使用评价人员必须严格按照批准后的合于使用评价方案进行评 价工作
评价过程中根据实际情况需作调整时,必须经过评价机构授权的技术负责人审查批准,并征求 使用单位意见
7.1.4评价工作结束后,评价人员应出具合于使用评价报告
7.2材料适用性评价 7.2.1一般要求 7.2.1.1对材质不明,以及有可能发生HS等应力腐蚀,或者使用年限已经超过15年并且发生过与应 力腐蚀焊接缺陷有关的修理改造的管道,应当进行管道材料适用性评价
10o
GB/T30582一2014 7.2.1.2材料适用性评价应在材料性能试验的基础上,开展化学成分、金相组织、力学性能、特殊服役条 件评价等工作
7.2.1.3输送石油天然气介质的管道材料适用性评价见7.2.2与7.2.3,输送其他介质的管道材料适用 性评价参照相关标准
7.2.2测试种类与数量 根据材料适用性评价项目开展材料测试,测试种类与数量见表2,测试方法见附录B
材料性能测 试应由具有国家实验室相应资质的单位进行
表2测试种类与数量 钢管类型 测试种类 取样位置 埋弧焊管 试样数量 无缝钢管 电阻焊管 直缝 螺旋缝 化学成分分析 管体 管体 金相分析 媒缝 管体 拉伸测试 焊缝 环焊缝 管体 夏比V型缺口冲击韧性 媒缝 测试 环媒缝 热影响区 落锤撕裂测试 管体 管体 夏比V型缺口低温冲击 焊缝 环媒缝 韧性测试 热影响区 硬度测试 见图B, HIC测试 管体 焊缝 SCC测试 管体 晶间腐蚀测试 焊缝" 环焊缝" 热影响区 注:对于不宜取样的管段可采用微损伤试样进行力学性能测试,测试方法可参考相关文献
未经压平
若管道壁温0,可不进行夏比V型缺口低温冲击韧性测试
若管道运行环境中无硫化物存在,可不进行Hlc租scC测试
本项测试仅针对奥氏体不锈钢
7.2.3材料适用性评价要求 7.2.3.1化学成分要求 各钢级的化学成分应达到表3一表5对应要求,表3表5中没有对应的钢级或者供货商原始标准 高于表3表5的,应达到供货商提供的原始标准要求;二者都不能满足的,应达到实际使用要求
表 11
GB/T30582一2014 中的碳当量CEw或CEp应根据待测材料成分按式(1)或式(2)进行计算 Cr十Mo十V Cu十N Mn CEIrw S Mn十Cu十Cr N Mo CEpm 十5B 30 20 60 15 表3化学成分要求(壁厚<25.Omm的PsL1级钢管 元索含量质量分数% 钢级 Mn Ni T 最大" 最大 最小 最大 最大 最大 最大 最大 I175(A25 0,21 0,60 0.030 0.030 0.80 0.030 L175(A25P) 0,21 0,045 0.080o I210(A 0.22 0.90 0.030 0.030 L245B 0.28 1.20 0.030 0.030 0.030 L.290(X42) 0,.28 1.30 0.030 无 缝 1.40 0.030 L320(X46 0,28 0,030 L360(X52 0.28 1.40 0.030 0.030 管 390(X56 0.030 0.28" l.40 0.030 0.030 IL415(X60) 0,28" 1,40 0.030 0.030 I450(X65 0.28" 1.40 0.030 L485X70 0.030 1.40 0.28" 0.030 L555(X80 0.005 0.1 0.025 0,09 1.85 0,022 0.06 I175(A25 0,21 0,60 0.030 0.030 I175(A25P 0,21 0,60 0,045 0.080 0.030 I210(A 0.22 0.90 0.030 0.030 L245B 0.030 0,26 1.20 0.030 L.290(X42) 0,.26 1.30 0.030 0.030 0.030 0,26 1.40 L320(X46 0,030 L360(X52 1.40 0.030 0.26 0.030 390(X56 1.40 0.030 0.26 0,030 L415(X60) 0,26" 1.40 0.030 0.030 450(X65 0.030 0.26" 1.45 0.030 485(X70 0,26 1.65 0.030 0.030 L555(X80 0.09 0.005 0.1 0.025 1.85 0,022 0.06 最大铜(Cu)含量为0.50%;最大镍(Ni)含量为0.50%,最大铬(Cr)含量为0.50%,最大钼Mo)含量为0.15%
对于L360/X52及以下俐级,不得随意加人cu.cr.Ni
碳(c)含量比规定最大碳含量减少0.01%,则允许钰(Mn)含量比规定最大的钮(Mn)含量高0.05%,但进行如 下限制对于l245/B<钢级
GB/T30582一2014 表5化学成分要求壁厚<25.0mm的SL2级钢管(酸性服役条件) 最大元素含量质量分数)/% 碳当量"/9%(最大) 钢级 S T Mn" I NBb 其他d CEnw CEp L245NS(NS 0.14 0.40 1.35 0.0200,.003" 0.04 0.36 0,19 L290NS(X42NS0.14 0.40 1.35 0.0200.003 0.05 0,05 0.04 0.36 0,19" 1.32oNs(X46Ns 0.07 0.05 0.14 0.40 1.40 0.0200.003" 0.04 0.38 0,20° L36oNs(X52Ns)o.16 0.45 1.65 0.0200.003" o.1o 0.05 0.04 0,43 0,.22 无 L245QSBQS 0.14 0.40 1.35 0.0200.003 0.04 0.04 0.04 0.34 0.19 和 L.290Qs(X42QS)0,14 0.40 1.35 0.,0200,003" 0.04 0.04 0.04 0,34 0.19 L320N(X46QS 0.15 0.45 1.40 0.0200,.003" 0.05 0.05 0.04 0.36 0.2o' 接 0.45 0,.20 L360QS(X52QS)0.16 1.65 0.0200.003 0.07 0,05 0.04 0.39 管 I390Qs(X56QS)0.160.45 1.650.0200.0030.07 0.050.04 0.40 0.21" E-I-k l415QS(X60QS 0.16 0.45 1.65 0.0200.003 0.08 0.05 0.04 0.41 0,22" 星,i,k L450Qs(X65QS0.16 1.65 0.05 0.22 0.45 0.0200.003” 0.09 0.06 0.42 星i,k 485QS(X70QS)0.16 0.45 1.65 0.0200.003" 0.09 0.05 0.06 0,42 0.22 L.245Ms(BMS 0.10 0.40 1.25 0.0200.002 0.04 0.04 0.04 0.19 L.290MS(X42MS)0.10 0.40 1.25 0.0200.002" 0.04 0.04 0.04 0.19 L320MS(X46MS0.10 0.45 1.35 0.0200.002” 0.05 0.05 0.04 0.20 焊 L360MS(X52MS)0,10 0.45 1.45 0.0200.002 0.05 0,06 0.04 0.20 接 钢 L390MSX56MS 0,10 0.45 1.45 0.0200.002 0.06 0,08 0,04 0,21 管 L415Ms(X6oMS)o.10 0.45 1.45 0.0200.002 0.08 0.08 0.06 0.21 i L450MS(X65Ms)o.10 0.45 1.60 0.0200.002 0.1o 0.08 0.06 0.22 Ri IL485MS(X70MS)0.10 0.45 1.60 0.0200.002 0.10 0.08 0.06 0.22 依据产品分析结果,碳含量大于0.12%使用CEnw,碳含量小于或等于0.12%使用CEm Ren" 碳含量比规定的最大碳含量每减少0.01%,允许含量比规定最大含量高0.05%,最大增加0.20%
Al<0.060%;N<0.012%;AI/N>2(不适合钛镇静钢或钛处理钢);Cu<0.35%如果协议,Cu<0.10%); Ni<0.30%;Cr<0.30%;Mo<0.15%;B0.0005%
在焊管有意增加钙(Ca)含量的情况下,除另有协议外,如果S>0.0015%,则Ca/S>1.5
对于无缝钢管和焊接 钢管钙(Ca)含量应<0.006%
无缝钢管的最大硫(S)含量可增加至0.008%,而且如果协议焊管可增至0,006%
对于硫(S)含量水平较高的 焊管,可协议确定较低的Ca/S. 除另有协议外,(Nb)含量和饥(V)含量之和应s0.,06%
锯(Nb)含量、饥(V)含量和钛(Ti)含量之和应<0.15%
对于无缝钢管,表列值可增加0.03%
如果协议,钼(Mo)含量应<0.35% 如果协议,铬(Cr)含量应0.45%
如果协议,铬(Cr)含量应<0,45%且镍(Ni)含量应<0,50%
14
GB/T30582一2014 7.2.3.2金相组织要求 应对管道的母材和焊缝进行显微组织和夹杂物金相分析,试样应未出现明显的由硫化氢等导致的 环境开裂 7.2.3.3力学性能要求 7.2.3.3.1抗拉强度和屈服强度要求 抗拉强度和屈服强度应符合表6对应的钢级代号要求,表6中没有对应钢级代号的或者供货商原 始标准高于表6的,以原始标准为依据
达不到原始要求的,按照表6对应的抗拉强度和屈服强度标准 钢级进行分析
其他钢质管道材料拉伸性能可参照相关标准 表6管道拉伸性能要求 钢级 最小屈服强度/MPa 最小抗拉强度/MPa 最小伸长率A/% Q235 235 375 Q345 345 490 27 L175 175 315 25 210 335 l.210(A 1.245(B) 245 415 21 21 L290(X42 290 415 20 L320(X46 320 435 L360(X52 360 460 19 L390(X56) 490 18 390 415 17 L415(X60 520 450 17 l450(X65 535 l6 L485(X70 485 570 L555(X80 555 625 15 7.2.3.3.2断裂韧性要求 断裂韧性性能应满足表7的要求
若管道所用钢材的钢级不在表7范围之内,则应按照实测的最 低屈服强度和抗拉强度对应表6中钢级,当屈服强度和抗拉强度位于两个钢级之间时,应取较高的钢级 以确定其冲击韧性的要求
应根据夏比V型缺口冲击性能断裂韧性测试结果制定相应的韧脆转变 曲线 15
GB/T30582一2014 表7埋地管道夏比V型缺口冲击性能与落锤撕裂性能要求 落锤撕裂测试 最小冲击功/门J 剪切面积/% 钢级 钢管外径D/mm 钢管外径D/mm 508 508762 762914 91412191219142214222134 5082134 L175 27(20 27(20 40(30 40(30 40(30 40(30 40(30 40(30 L.210(A 27(20 27(20) 40(30 40(30) I245(B 27(20 27(20 40(30 40(30 40(30 40(30 L.290(X421 27(20 27(20) 40(30) 40(30 4030) 4030) L320(X46 40(30) 27(20 27(20) 40(30 4030) 030 L360(X52 27(20 27(20) 40(30) 40(307 4030) 40(30 >85 L.390(X56 27(20) 27(20) 40(30 40(30 40(30 40(30 L415X60 2720 27(20 40(30 40(30 40(30 40(30 27(20 40(30 54(40 5440) L450(X65) 27(20 40(30 L485(X70 40(30) 40(30) 40(30 40(30 54(40 68(50) L555(X80 40(30 40(30) 40(30 40(30 54(40 68(50) 注:括号内为单个试样要求的最小值
对于螺旋焊缝、环焊缝和热影响区等特殊区域试样,其夏比V型缺口冲击性能可降低要求
在与 母材相同测试温度条件下,3个试样的最小冲击功平均值为40J,单个试样的最小冲击功平均值为 30 " 7.2.3.3.3硬度要求 对于运行环境中含H,s的管线俐,硬度不得超过250HV10
7.2.3.4特殊服役条件性能要求 7.2.3.4.1抗氢致开裂HIC)性能要求 母材与焊缝的氢致开裂(HIC)测试结果应满足表8要求
表8抗氢致开裂测试性能要求 钢级 裂纹敏感性比率/CSR 裂纹长度比率/CLR 裂纹厚度比率/C'TR Q235 Q345 L175 二2 15 5 L.210(A 二2 <15 5 L.245(B) 二2 15 5 L.290(X42 二2 15 5 L.320(X46 5 L360(X52 2 15 5 L390(X56) 5 L415(X60 二2 15 5 L450(X65) 二2 15 二5 L485(X70) 二2 15 5 L555(X80) <10 S3 16
GB/T30582一2014 7.2.3.4.2抗硫化氢应力腐蚀开裂(SSC)性能要求 硫化氢应力腐蚀开裂(SsC)测试应用10倍以上放大镜或长焦距显微镜观察,沿钢管壁厚方向的试 样表面上没有深度超过0.1mm的裂纹
7.2.3.4.3抗晶间腐蚀性能要求 不锈钢管道须取样进行10%的草酸浸泡测试,其腐蚀特征应满足表9的要求
表9不允许存在的晶间腐蚀形貌特征 名称 试样类别 组织特征 阶梯组织 压力加工试样 晶界无腐蚀沟,晶粒呈台阶状 混合组织 压力加工试样 晶界有腐蚀沟,但没有一个晶粒被腐蚀沟包围 沟状组织 压力加工试样 晶界有腐蚀沟,个别或全部晶粒被腐蚀沟包围 铸造试样和焊缝区 游离铁素体组织 品界无腐蚀沟,铁素体被显现 包括焊缝和热影响区 铸造试样和焊缝区 连续沟状组织 媒缝晶界沟状组织很深,并形成连续沟状组织 包括焊缝和热影响区 压力加工试样、铸造试样和焊缝区 凹坑组织! 浅凹坑多,深凹坑少的组织 包括焊缝和热影响区 压力加工试样、铸造试样和焊缝区 凹坑组织l 浅凹坑少,深凹坑多的组织 包括媒缝和热影响区 7.3剩余强度评估 7.3.1适用范围 剩余强度评估适用于含体积型缺陷和凹陷的在役埋地钢质管道的评估
7.3.2数据收集 除按第5章的规定进行数据收集外,还应收集以下数据: a)缺陷的类型、尺寸和位置; b结构和煤缝的几何形状和尺寸; 材料的化学成分、力学和断裂韧度性能数据 e) 承受载荷
d 7.3.3体积型缺陷剩余强度评估 7.3.3.1 般要求 体积型缺陷剩余强度评估含单一体积型缺陷或含相互作用体积型缺陷的埋地钢质管道,应同时满 足以下条件" 体积型缺陷由腐蚀、.缺陷打磨或机械拭伤形成, a b材料韧性良好,并且未出现材料性能劣化及劣化趋向; 缺陷深度在管道壁厚的20%80%之间; c 17
GB/30582一2014 d)缺陷处及其附近区域无其他表面缺陷或埋藏缺陷 无明显塑性变形与应力集中; e f不承受疲劳载荷、动态冲击载荷
7.3.3.2单一体积型缺陷管道剩余强度评估 当管段只含一个独立的缺胎时,采用单一体积型缺陷管道剩余强度评钻方法
该方法分为 7.3.3.2.1 彼此独立的3个等级,根据获得数据的完整性及管道使用单位的要求选择一级、二级或三级
-级评估见c.1.1
7.3.3.2.2 7.3.3.2.3二级评估见c.1.2 三级评价采用有限元分析方法,依据管道材料属性选用下列相应失效准则 7.3.3.2.4 a)弹性极限准则;缺陷处的Mises等效应力不超过管材的屈服强度; b)塑性极限状态失效准则缺陷处的Mises等效应力不超过管材的抗拉强度 e)塑性失效准则;缺陷处的Mises等效应力不超过管材的后屈服点
7.3.3.3相互作用体积缺陷管道剩余强度评估 当管段分布有多个缺陷时(见图3),如缺陷之间的相对位置满足下列任一条件,则作为单一体积缺 陷处理,否则,应按相互作用体积缺陷评估,见C.2 相邻缺陷之间的环向角乡满足式(3 3 中>36067D b 相邻缺陷之间的纵向间距、满足式(4) s>2.0D 式中: 管道壁厚,单位为毫米(mm); 管道外径,单位为毫米(mm)
轴向 缺陷 缺陷2 图3管道上缺陷位置与尺寸 7.3.4含凹陷管道的剩余强度评估 7.3.4.1适用于受外部硬物挤压或碰撞而产生无划伤和含划伤凹陷的埋地钢质管道的剩余强度评估 方法
18
GB/T30582一2014 应同时满足以下条件: a)含径向变形不大于管道外径6%的凹陷 b材料韧性良好,并且未出现材料性能劣化及劣化趋向 缺陷处及其附近区域无其他表面缺陷或埋藏缺陷; c D 无明显塑性变形与应力集中; 管道焊缝及热影响区影响范围之外的体积型缺陷 e 不承受疲劳载荷、动态冲击载荷
当焊缝处存在凹陷时,应采取修复措施
7.3.4.2无划伤四陷评估可采用基于应变准则和基于凹陷深度准则
宜优先采用基于凹陷深度准则; 当管道凹陷尺寸数据充足时,宜采用基于应变准则 基于凹陷深度准则 管道凹陷深度不应超过管道外径的6%
当凹陷深度超过外径的6%时应采取修复措施,否则 应采取定期监测措施
b)基于应变准则 管道凹陷处的应变不应超过0.06,见D.1
含划伤凹陷管道的剩余强度评估见D.2
7.3.4.3 不良条件下埋地钢质管道安全评定 7.4 不良条件下埋地钢质管道安全评定是对评定对象的状况调查(历史、工况、环境等),缺陷检测,缺陷 成因分析、失效模式判断、材料检验(性能、损伤与退化等、应力分析、必要的实验与计算,并根据本标准 的规定对评定对象的安全性进行综合分析和评价
针对不良条件下埋地钢质管道极限状态的安全评定判据见附录E
7.5剩余寿命预测 7.5.1 -般要求 7.5.1.1当应用本标准的规定确定管道的检验周期时,应遵守特种设备安全技术规范TsGD7003、 TsGD7004的规定,并不超过预测的剩余寿命的一半
腐蚀寿命预测可以选用TsGDr003,TsGD7004中的计算方法或本标准中的预测方法
7.5.1.2 使用 本标准中的方法时,当检验区段开挖点数量小于16处时,宜选用均匀腐蚀剩余寿命预测方法或局部腐 蚀剩余寿命预测方法,计算每处抽检管段的剩余寿命,其中的最小值确定为管道的腐蚀剩余寿命;当检 验区段开挖点数量大于或等于16处时,宜选用极值统计法进行剩余寿命预测
7.5.2均匀腐蚀剩余寿命预测 7.5.2.1直管段均匀腐蚀剩余寿命预测 直管段均匀腐蚀剩余寿命采用壁厚法进行预测,壁厚法是基于未来服役条件、实测壁厚、金属损失 区域尺寸,预期腐蚀速率以及裂纹扩展速率估计计算需要的最小壁厚
预测过程见F.1
7.5.2.2弯头、三通均匀腐蚀剩余寿命预测 弯头、三通等管道元件均匀腐蚀剩余寿命采用最大允许工作压力(MAwP)方法进行预测,见F.2. 19
GB/T30582一2014 7.5.3局部腐蚀剩余寿命预测 7.5.3.1直管段局部腐蚀剩余寿命预测 直管段局部腐蚀剩余寿命采用壁厚法进行预测,直管段局部腐蚀与均匀腐蚀剩余寿命计算不同之 处在于剩余壁厚比R的取值不同,详见F.1
7.5.3.2弯头,三通局部腐蚀剩余寿命预测 弯头、三通等管道元件局部腐蚀剩余寿命采用MAwP方法进行预测,见F.2
7.5.4极值统计腐蚀剩余寿命预测 检验区段开挖点数量大于或等于16处时宜使用本方法,如果管道壁厚减薄达到最小要求壁厚,即 认为管道剩余寿命为0,计算过程见F.3
外损伤综合评价 8.1 -般要求 8.1.1外损伤检验与合于使用评价完成后,应对埋地钢质管道区段进行外损伤综合评价,为制定管道 外损伤问题的处理提供依据
8.1.2在外损伤检验评价报告中应明确许用参数、下次检验日期
当有管道外损伤问题时应明确处理 措施
8.1.3问题处理措施实施后,应对管道的数据资料进行更新,并由合于使用评价机构对管道进行风险 再评估,其结果纳人管道使用登记工作中
8.2外损伤综合评价 8.2.1外损伤综合评价结果分为以下4个等级 1级管道安全质量符合有关法规和标准要求,满足设计条件下在6年的检验周期内能安全 使用; 2级;管道安全质量符合有关法规和标准要求,但腐蚀防护系统或管道本体存在某些不符合有 关规范和标准的问题或缺陷,经合于使用评价,结论为满足设计条件下在3年6年的检验周 期内能安全使用; 3级;管道安全质量符合有关法规和标准要求,但腐蚀防护系统或管道本体存在某些不符合有 关规范和标准的问题或缺陷,经合于使用评价,结论为满足设计条件下在1年3年检验周期 内在限定的条件下安全使用; 4级;管道系统外损伤缺陷严重,不能满足设计要求,管道不能安全运行,使用单位应立即采取 重大维修措施
8.2.2腐蚀防护系统评价等级依据GB/T19285划分
8.2.3管道本体评价等级依据管体本身的损伤情况评价,分级规则如下 经合于使用评价能安全使用6年以上(含6年)的,管道本体评价等级为1级 a b)经合于使用评价6年内能安全使用的,管道本体评价等级为2级 经合于使用评价3年内能安全使用的,管道本体评价等级为3级 c d存在无法通过安全评定的外损伤缺陷,管道本体评价等级为4级 8.2.4管道外损伤综合评价等级依据腐蚀防护系统评价、管道本体评价等级进行评级,见表10
2o0
GB/T30582一2014 表10管道外损伤综合评价等级 管道外损伤综合评价等级 管道本体评价等级 腐蚀防护系统 评价等级 8.3外损伤检验评价报告要求及问题处理措施 8.3.1外损伤检验评价报告要求 8.3.1.1报告内容应至少包括以下内容: a)项目概况 b) 数据收集;应简要说明数据来源,并特别注明有怀疑或矛盾的数据 e)潜在危险辨识;说明辨识的依据,明确目标管道是否存在外损伤危险,辨识过程中确认的其他 非外损伤危险也应在报告体现 d)风险评估;包括所依据的评价标准、主要的原始信息及详细评估结论 外损伤检验;包含检验的管道区段、检验的时间、检验时的环境条件、使用的技术方法与设备
e 相关单项检验的结论; f 合于使用评价;包括评价的初始条件,评价过程涉及的所有单项评价参数及单项评价结论; g综合评价:包括评价的过程参数; h)结论建议:许用参数、下次检验日期;当有缺陷要求进行处理时,应明确缺陷进行修复或者采取 降压运行的措施
8.3.1.2检验与评价工作结束后,检验机构一般应在30个工作日内出具报告,交付使用单位存人压力 管道技术档案
8.3.1.3检验评价结论报告应当有编制审核,批准三级人员签字,批准人员为检验机构的主要负责人 或者授权的技术负责人
8.3.1.4风险再评估报告宜在问题处理措施完成后单独出具,并作为检验评价报告的附件
8.3.2问题处理措施 8.3.2.1使用单位应对检验评价发现的问题进行处理
8.3.2.2问题处理措施包括对管道的维修维护及管理工作
8.3.2.3管道本体的维修,可使用传统的加套简等方法、不动火的复合材料补强等技术
宜优先使用不 动火的复合材料补强技术 21
GB/T30582一2014 附录A 规范性附录 管道外损伤检验方法及检验比例 A.1腐蚀防护系统检验项目和检验比例 A.1.1土壤腐蚀性检测项目包括土壤质地、土壤电阻率、管地电位、氧化还原电位、土壤pH值、土壤含 水率、土壤含盐量、土壤CI含量等参数的测试,根据管段的风险等级,按表A.1选择检测项目及检测 比例 表A.1土壤腐蚀性检测项目和检测比例 土壤腐蚀性检测项目 管道类型 风险等级 土壤 土壤cr 土壤 管地氧化还原土壤 土壤 土壤 p 质地 电阻率 电位 电位 含水率 含盐量 含量 高风险 全部 全部 全部 全部 全部 全部 全部 全部 50% 50% 50% 50% 50% 较高风险 全部 全部 全部 输气管道 中风险 全部 全部 全部 20% 20% 20% 20% 20% 低风险 全部 全部 全部 高风险 全部 全部 全部 全部 全部 全部 全部 全部 较高风险 全部 全部 全部 50% 50% 50% 50% 50% GA级输油管道 中风险 全部 全部 全部 低风险 50% 50% 50% 高风险 全部 全部 全部 全部 全部 全部 全部 全部 较高风险 全部 全部 全部 20% 20% 20% 20% 20% GA2级输油管道 中风险 全部 全部 全部 低风险 20% 20% 20% 全部 高风险 全部 全部 全部 全部 全部 全部 全部 20% 20% 20% 20% 20% 全部 联合站至长输首站较高风险 全部 全部 集输油气管道 中风险 全部 全部 全部 低风险 全部 全部 全部 高风险 全部 全部 全部 全部 全部 全部 全部 全部 集输站至联合站 较高风险 全部 全部 全部 20% 20% 20% 20% 20% 集输油气管道 中风险 全部 全部 全部 低风险 50% 50% 50% 全部 全部 全部 全部 全部 全部 全部 全部 高风险 单井站至集输站 较高风险 全部 全部 全部 中风险 全部 集输油气管道 全部 全部 低风险 20% 20% 20% 高风险 全部 全部 全部 全部 全部 全部 全部 全部 GB1-I级.,GB1-级较高风险 全部 全部 50% 50% 全部 50% 50% 50% 燃气管道 中风险 全部 全部 全部 20% 20% 20% 20% 20% 低风险 全部 全部 全部 心
GB/T30582一2014 表A.1(续 土壤腐蚀性检测项目 管道类型 风险等级 土壤 土壤 管地氧化还原土壤 土壤 土壤土壤cr 质地 电阻率 电位 电位 pH值 含水率 含盐量 含量 高风险 全部 全部 全部 全部 全部 全部 全部 全部 较高风险 全部 全部 全部 50% 50% 50% 50% 50% GB1-级燃气管道 中风险 全部 全部 全部 低风险 50% 50% 50% 全部 全部 全部 全部 高风险 全部 全部 全部 全部 全部 全部 全部 20% 20% 20% 20% 20% GB-级.GB1-V级、较高风险 GB1-W级燃气管道 中风险 50% 50% 50% 低风险 20% 20% 20% 高风险 全部 全部 全部 全部 全部 全部 全部 全部 较高风险 全部 全部 全部 20% 20% 20% 20% 20% G2级热力管道 中风险 50% 50% 50% 低风险 20% 20% 20% 高风险 全部 全部 全部 全部 全部 全部 全部 全部 较高风险 全部 全部 全部 50% 50% 50% 50% 50% GC1级工业管道 中风险 全部 全部 全部 20% 20% 20% 20% 20% 低风险 全部 全部 全部 高风险 全部 全部 全部 全部 全部 全部 全部 全部 较高风险 全部 全部 全部 20% 20% 20% 20% 20% GC2级工业管道 全部 全部 中风险 全部 低风险 50% 50% 50% 高风险 全部 全部 全部 50% 50% 50% 50% 50% 较高风险 全部 全部 全部 GC3级工业管道 中风险 全部 全部 全部 低风险 高风险 全部 全部 全部 全部 全部 全部 全部 全部 较高风险 全部 全部 20% 20% 全部 20% 20% 20% GD1级动力管道 中风险 全部 全部 全部 低风险 50% 50% 50% 高风险 全部 全部 全部 50% 50% 50% 50% 50% 较高风险 全部 全部 全部 20% 20% 20% 20% 20% GD2级动力管道 全部 全部 中风险 全部 低风险 注1:全部指所有开挖检测点进行土壤腐蚀性检测,表中百分数是指应在开挖检测点进行土壤腐蚀性检测的百 分数
注2:当存在腐蚀活性时,应增加土壤腐蚀性检测
23
GB/T30582一2014 A.1.2外防腐层不开挖检测包括整体状况和破损点不开挖检测,按表A.2选择检测项目及检测比例
表A.2外防腐层检测项目和检测比例 整体状况不开挖检测 破损点不开挖检测 管道类型 风险等级 交流电流衰减法 交流电位梯度法直流电位梯度法 100% 30% 100% 高风险 较高风险 100% 00% 输气管道 中风险 100% 100% 低风险 50% 100% 高风险 100% 100% 30% 较高风险 1o0% 100% GAl级输油管道 00% 中风险 0% 20% 100% 低风险 高风险 100% 100% 30% 较高风险 100% 100% GA2级输油管道 中风险 100% 100% 低风险 20% 100% 高风险 100% 100% 30% 较高风险 00% 100% 联合站至长输首站 集输油气管道 50% 100% 中风险 00% 20% 低风险 高风险 100% 100% 30% 较高风险 100% 100% 集输站至联合站 集输油气管道 中风险 50% 100% 低风险 0% 100% 100% 高风险 100% 30% 100% 100% 较高风险 单井站至集输站 集输油气管道 中风险 20% 100% 低风险 100% 高风险 100% 100% 30% 较高风险 100% 100% I级.GB1-】级 GB1- 燃气管道 中风险 1o0% 100% 低风险 0% 0% 100% 100% 30% 高风险 较高风险 100% 100% GB-级燃气管道 中风险 50% 100% 低风险 50% 100% 2
GB/T30582一2014 表A.2(续 整体状况不开挖检测 破损点不开挖检测 管道类型 风险等级 交流电流衰减法 交流电位梯度法直流电位梯度法 100% 100% 30% 高风险 较高风险 100% 100% GB1-级、GB1-V级、 GB1-W级燃气管道 中风险 50% 100% 低风险 20% 100% 高风险 100% 100% 30% 较高风险 100% 100% GB2级热力管道 中风险 0% 00% 20% 100% 低风险 高风险 100% 00% 30% 较高风险 100% 100% Gc1级工业管道 中风险 100% 100% 低风险 50% 100% 高风险 100% 100% 30% 较高风险 100% 00% GC2级工业管道 50% 100% 中风险 20% 100% 低风险 高风险 100% 100% 30% 100% 较高风险 100% Gc3级工业管道 中风险 20% 100% 低风险 100% 30% 高风险 00% 00% 100% 100% 较高风险 GD1级动力管道 50% 100% 中风险 低风险 20% 100% 高风险 100% 100% 30% 较高风险 100% 100% GD2级动力管道 中风险 20% 100% 低风险 1006 当两种检测方法结果存在差异时应开挖验证
A.2腐蚀产物现场辨识 可根据产物颜色按表A.3的方法进行辨识
25
GB/T30582一2014 表A.3现场腐蚀产物颜色与成分 产物颜色 主要成分 黑 FeO 红棕至黑 Fe.O Fe,O 红棕 黑棕 FeS Fe(OH. 绿或白 灰 FeCO. A.3外腐蚀缺陷尺寸检测 A.3.1外腐蚀形貌宏观检查 清除腐蚀产物后,应进行外腐蚀宏观检查
A.3.2外腐蚀深度和腐蚀面积的测量 A.3.2.1探针法 采用带尾针游标卡尺、千分表或专用探针,清除腐蚀区域表面异物后,测量坑边缘到最深底部的 深度 A.3.2.2超声波法 采用超声波测厚仪测量管壁厚度
当管壁厚度变化均匀时,可直接进行厚度测量;当管壁厚度变化 不均匀时,应先用超声波测厚仪连续扫查,确定管壁最薄处的面积区域,然后再进行测量,或者采用超声 波C扫技术,进行管道壁厚分布测量
A.3.2.3危险厚度截面法(ICP) 当管体存在大面积腐蚀坑时,除上述测量外,还需采用危险厚度截面法(TCP)确定腐蚀坑的尺寸, 步骤如下: 将腐蚀区域划分为管道轴向、环向交叉的若干个方格,见图A1,推荐的截面间距计算见式(A.l); (A.1 =maxt0.l8:万,12.7) Ls 式中: Ls 推荐的检测截面间距,单位为毫米(mm); 管道内轻.单位为毫米(mm) 基于设计压力计算的最小要求壁厚,单位为毫米(mm) 测量每个交叉点的坑深或壁厚,作好记录
b 26
GB/T30582一2014 金属 损尖 外曲面 M3 C2 金属损失区 MlM2M3 内曲面 图A.1腐烛区域危险厚度截面网格划分 A.3.3相邻外腐蚀的尺寸确定 A.3.3.1当两个相邻腐蚀之间未腐蚀区域最小尺寸小于25mm时,应视为同一腐蚀,即轴向腐蚀长度 为两个腐蚀长度与未腐蚀区域长度之和
A.3.3.2当两个相邻腐蚀之间未腐蚀区域最小尺寸小于6倍壁厚(6t)时,应视为同一腐蚀计算其环向 投影的长度
A.3.3.3在不考虑腐蚀的轴向、环向投影长度时,按图A.2的步骤确认相邻腐蚀的尺寸
管壁 步骤l;画出一个长方形,它完全包围了减薄区
测 步骤2围着减薄区画出第二个长方形,其尺寸为第一个长 量在此长方形中的最大的轴向范围s英寸或毫米 方形的2倍(2s×2e)
及环向范围c(英寸或毫米)
这两个尺寸在评价中 将用于确定减薄区的面积
图A.2相邻腐蚀区域尺寸的确定方法 27
基于风险的埋地钢质管道外损伤检验与评价GB/T30582-2014解读
随着城市化进程的不断发展,埋地钢质管道在城市供水、供气、供热等领域中得到广泛应用。然而,由于长期使用和外部环境的影响,埋地钢质管道存在外损伤的风险,这可能会给城市带来极大的安全隐患。为此,国家制定了一系列的标准和规范,其中就包括了GB/T30582-2014《基于风险的埋地钢质管道外损伤检验与评价》。
该标准是在总结并借鉴国内外先进经验的基础上,结合我国国情、行业特点和技术现状而编制的,旨在对埋地钢质管道的外损伤进行有效控制,保障城市供水、供气、供热等基础设施的安全稳定运行。
标准内容及解读
标准主要涵盖了埋地钢质管道外损伤检验和评价的基本原则、组织与职责、风险识别与评估、检验方法、评价指标和应急管理等方面的内容。其中,重点介绍了基于风险的埋地钢质管道外损伤检验和评价方法。
标准明确提出,埋地钢质管道的外损伤检验和评价必须基于风险,即根据管道受损情况、使用年限、工作环境等因素,全面评估管道的安全风险程度,并采取相应的检验和评价措施。标准还规定了具体的检验方法和评价指标,如壁厚测量、金相分析、裂纹检测等。
标准的实施意义
GB/T30582-2014《基于风险的埋地钢质管道外损伤检验与评价》的实施,对于保障城市基础设施的安全运行、降低事故发生率、提高供水、供气、供热等领域的服务质量具有重要意义。同时,该标准的实施也可以帮助企业提高风险管理和应急处理的能力,提升企业的核心竞争力。
总之,埋地钢质管道是城市供水、供气、供热等领域中不可或缺的基础设施之一,其安全稳定运行对于城市的正常生产和居民生活至关重要。因此,大力推广GB/T30582-2014《基于风险的埋地钢质管道外损伤检验与评价》的相关内容,对于促进城市基础设施的可持续发展、加强城市安全管理具有十分重要的意义。