GB/T26610.2-2014
承压设备系统基于风险的检验实施导则第2部分:基于风险的检验策略
Guidelineforimplementationofrisk-basedinspectionofpressureequipmentsystem―Part2:Risk-basedinspectionplan
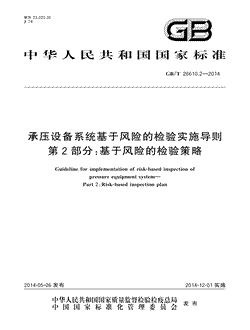
- 中国标准分类号(CCS)J74
- 国际标准分类号(ICS)23.020.30
- 实施日期2014-12-01
- 文件格式PDF
- 文本页数15页
- 文件大小406.66KB
以图片形式预览承压设备系统基于风险的检验实施导则第2部分:基于风险的检验策略
承压设备系统基于风险的检验实施导则第2部分:基于风险的检验策略
国家标准 GB/T26610.2一2014 承压设备系统基于风险的检验实施导则 第2部分;基于风险的检验策略 Guidelineforimplementationofrisk-basedlinspeetioof pressureequipmentsystem- Part2:Risk-basedlinspeetionplan 2014-05-06发布 2014-12-01实施 国家质量监督检监检疫总局 发布 国家标准花管理委员会国家标准
GB/T26610.2一2014 前 言 GB/T26610(《承压设备系统基于风险的检验实施导则》分为5个部分 -第1部分:基本要求和实施程序; 第2部分基于风险的检验策略; 第3部分;风险的定性分析方法 第4部分;失效可能性定量分析方法 第5部分;失效后果定量分析方法 本部分为GB/T26610的第2部分
本部分按照GB/T1.1-2009给出的规则起草
本部分由全国锅炉压力容器标准化技术委员会(SAc/Tc262)提出并归口
本部分起草单位;特种设备检测研究院、国家质量监督检验检疫总局特种设备安全监察局、合 工股份有果公司.石油天然气股份有限公司.石油化工股份有 肥通用机械研究院、石油化工 限公司燕山分公司、石油天然气股份有限公司独山子石化分公司,中海石油化学股份有限公司、中 海壳牌石油化工有限公司、中石油石家庄炼化分公司、上海特种设备监督检验技术研究院、广东省特种 设备检测院、南京锅炉压力容器检验研究院、江苏省特种设备安全监督检验研究院无锡分院
本部分主要起草人;贾国栋、王辉、李志峰、邵珊珊,李军,关卫和,胡明东、何承厚、陈轩、戴澄、 杨瑞平、罗传武、杨瑞增、昌胜杰,罗晓明,郑炯,姜海一,业成、费宏伟、徐鹏,王笑梅
GB/T26610.2一2014 承压设备系统基于风险的检验实施导则 第2部分:基于风险的检验策略 范围 GB/T26610的本部分规定了承压设备系统基于风险的检验策略(包括检验时间、检验类型、检验 方法和检验有效性等)的制定方法
本部分适用于GB/T26610.1所指的承压设备系统
规范性引用文件 下列文件对于本文件的应用是必不可少的
凡是注日期的引用文件,仅注日期的版本适用于本文 件
凡是不注日期的引用文件,其最新版本(包括所有的修改单)适用于本文件
GB/T26610.1承压设备系统基于风险的检验实施导则第1部分;基本要求和实施程序 GB/T26610.3承压设备系统基于风险的检验实施导则第3部分;风险的定性分析方法 GB/T26610.4一2014承压设备系统基于风险的检验实施导则第4部分;失效可能性定量分析 方法 GB/T26610.52014承压设备系统基于风险的检验实施导则第5部分;失效后果定量分析 方法 术语和定义 GB/T26610.1界定的以及下列术语和定义适用于本文件 3.1 检验有效性inspectioneffectiveness 对检验效果的定性分级评价,从高度有效到无效分为5个等级 3.2 腐蚀回路corrosioncircuit 个系统中,具有相同材料类别相似操作条件和相同损伤模式的一组设备回路 在 3.3 置信度 confidence -组子样(即观测值),对表征母体的参数进行估计的统计可信程度
根据来自母体的一 总则 基本原则 4.1 检验策略的制定应以控制设备的风险可接受为目标,重点关注潜在损伤模式、损伤速率以及失效 模式
GB/T26610.2一2014 4.2人员及单位要求 检验策略的制定人员应具有足够的工艺流程、材料、腐蚀,检验等知识背景和实践经验,并经过风险 评估专业培训合格
检验策略的制定单位(风险评估单位)应建立相应的质量控制程序
4.3通用流程 4.3.1风险分析计算 采用本部分制定检验策略前,应分别按照GB/T26610.4和GB/T26610.5的规定对承压设备进行 失效可能性和失效后果等级的定量分析计算,按照GB/T26610.1的规定确定承压设备的风险
风险 的定性分析可用于定量分析前设备的筛选分析,按GB/T26610.3的规定进行
4.3.2确定风险可接受水平 风险可接受水平由使用单位根据自身实际情况确定,但应满足GB/T26610.1的规定,同时应考虑 政府关于人员安全的基本要求和使用单位的社会责任
4.3.3制定检验策略 根据设备的风险和风险可接受水平,按照本部分的要求制定检验策略
4.3.4安全阀及换热管束检验策略 安全阀的检验策略见附录A,换热管束的检验策略见附录B. 4.4主要内容 检验策略一般包括以下内容: 检验时间(或基于检验时间确定的检验范围) a b)检验类型 检验方法和检验有效性
检验时间 检验时间点一般分为评估时间点,本次停机检修时间点和预计的下次停机检修时间点
检验时间 的确定应以在预计的下次停机检修时间点,设备的风险位于可接受水平之下为目标 如果在本次停机检修时间点之前,设备的风险已达到或超过风险可接受水平,应立即实施 检验; b)如果在预计的下次停机检修时间点之前,设备的风险已达到或超过风险可接受水平,应在本 次停机检修时间点实施检验
设备检验时间的确定按照以上原则进行,也可以参照附录C确定
若同一设备的不同部件检验时 间不同,则根据最近检验时间点确定设备整体的检验时间 检验类型及选择原则 6.1检验类型 6.1.1容器的检验类型:
GB/T26610.2一2014 a停机内部检验; b) 停机外部检验 c)在线检验 6.1.2管道的检验类型: 停机外部检验 a b 在线检验 6.2检验类型的选择原则 容器检验类型的选择原则 6.2.1 a)首次检验:具备条件时应进行停机内部检验,否则进行停机外部检验或在线检验
b)非首次检验;具备条件时优先选择停机内部检验,否则进行停机外部检验或在线检验
6.2.2管道检验类型的选择原则 具备条件时优先选择停机外部检验,否则进行在线检验
6.3在线检验的选用原则 如果不具备停机检验的条件,且在线检测方法的有效性能够达到检验策略提出的有效性级别要求 可以选用在线检验
检验方法和检验有效性 7.1检验方法 龈据设备潜在的损伤模式及其严重程度确定检验方法和比例
检验部位应选择损伤模式发生 7.1.1 可能性最高的区域
如果实施在线检验,选择检验方法时还应考虑从设备外部检测内部缺陷的能力和 温度等操作条件对检验有效性的影响
7.1.2首次检验时,检验内容不仅包括使用环境下可能发生的损伤检验,还应补充对制造、安装质量的 检验抽查
7.1.3若设备的风险以失效后果为主导,还应当考虑其他的风险控制措施
7.2检验有效性 7.2.1检验有效性分级 7.2.1.1确定检验有效性应考虑下列因素: a)检验类型, b)设备或部件的结构类型; 损伤模式及失效模式; c 损伤速率或敏感性 dD 检测方法和频次 受检区域的可检程度
fD 7.2.1.2检验有效性分为5个级别,见表1
GB/T26610.2一2014 表1检验有效性分级 检验有效性级别 描 述 高度有效 某种检验方法准确识别某种损伤实际状态的置信度为80%100% 某种检验方法准确识别某种损伤实际状态的置信度为60%一80% 中高度有效 中度有效 某种检验方法准确识别某种损伤实际状态的置信度为40%一60% 某种检验方法准确识别某种损伤实际状态的置信度为20%一40% 低度有效 无效 某种检验方法准确识别某种损伤实际状态的置信度小于20% 7.2.2检验有效性的选取原则 对于高风险的设备,应采用中高度有效及以上级别的检验方法;对于中风险和中高风险的设备,应 采用中度有效及以上级别的检验方法;对于低风险的设备可以采用低度有效及以上级别的检验方法
各种检测方法对应的检验有效性级别见表2和表3 表2停机检测方法及有效性 失 效 形 式 检测方法 尺寸变化 氢鼓池 减满 表面裂级 近表面裂纹微裂纹/微孔金相组织变化 目视检测 1,2,3 2,3 1,2,3 1,23 纵波超声检测 l,2,3 l2 横波超声检测 1,2,3 x 2,3 3X TOFD 2,3 2,3 2,3 3,× 1,2 射线成像检测 1,2,3 3,× X 荧光磁粉 1,2 3,× X 渗 透 1,2.3 × 针对活性 针对活性 声发射 3.× 裂纹)2,3 裂纹)2,3 × 涡流 1.2 1.2 3.X l,2 漏磁 1.2 X 3,X × X 尺寸测量 l,2,3 1,2 相 x 金 2,3 2,3 2,3 1,2 超声导波 1,2,3 注,1为高度有效:2为中高度有效;3为中度有效;×为低度有效或无效
GB/T26610.2一2014 表3在线检测方法及有效性 效 形 失 式 检测方法 减薄 表面裂纹 近表面裂纹微裂纹/微孔金相组织变化 尺寸变化 氧鼓泡 脉冲涡流测厚 1,2,3 X 高温纵波超声检测 123 1,2 高温横波超声检测 3,X × X X 2,3 1,2,3 X 高温磁粉 1,2 × 针对活性 (针对活性 在线声发射监测 3,× 裂纹)2,3 裂纹)2,3 超声导波 1,2.3 注1为高度有效;2为中高度有效;3为中度有效;×为低度有效或无效 检验策略的实施 8.1使用单位应当根据检验策略,制定检验计划
检验机构应当根据检验策略和检验计划,结合现场 条件,制定具体的检验方案并实施检验
8.2检验机构在检验过程中应详细记录检验结果,并由风险评估单位将检验结果与风险评估结果进行 对比验证 8.3对于评估中由于某一种损伤模式导致的失效可能性大于或等于4的设备,若在检验实施过程中该 损伤模式得到验证,则应扩大同一腐蚀回路中设备的检验比例
在预计的下次停机检修时间点前,风险评估单位应根据本次检验和风险评估的对比验证结果、年 8.4 度检查的结果,以及腐蚀检查和监测结果,更新评估数据,进行再评估
GB/T26610.2一2014 附 录A 规范性附录 安全阀检验策略 A.1符号 与第种超压悄况相关的安全闵开启失效后果,元 Cr 安全阀泄漏失效后果,元; C" 某一种超压情况 超压情况次数 ndc 与第种超压情况相关的安全阀开启失效造成的设备超压泄漏可能性,失效次数/年; P P -安全阀泄漏可能性,失效次数/年; risk" 第种超压情况下安全阀开启失效风险,元/年; risk" 所有超压情况下安全阀开启失效的总风险,元/年; Hlsk" -安全阀泄漏风险,元/年; riskl 安全阀总风险,元/年
A.2基于风险的校验时间 A.2.1安全阀风险计算 A.2.1.1安全阀开启失效风险的计算: 某 一种超压情况下安全阀开启失效的风险按式(A.1)计算: (A.1 risk=PxC b)所有超压情况下安全阀开启失效的总风险按式(A.2)计算 Pxc- (A..2 riskrd= 式中,尸"按GB/T26G10.4一2014附录K计算,C按GB/T20610.5一2014附录A计算 A.2.1.2安全阀泄漏风险按式(A.3)计算 risk=P×c" (A.3 式中,P按GB/T26610.4一2014附录K计算,C按GB/T26610.5一2014附录B计算 A.2.1.3安全阀风险按式(A.4)计算: (A.4 risked=riskr"十risk" A.2.2最长校验时间 安全阀经过校验重新投人使用后,其最长校验时间为风险达到设定的可接受水平所对应的时间
校验时间的调整 在校验过程中发现诸如裂纹、腐蚀等问题,检验人员可视其严重程度,以及对安全阀功能的影响程 度适当缩短其校验时间,若存在的问题严重影响安全阀正常运行,且难以修复的,则应向使用单位提出
GB/T26610.2一2014 更换建议,详见表A.1
表A.1校验时间调整表 序号 校验发现的问题 处理方式 轻度 不影响校验时间 缩短校验时间 中度 密封面磨掀 重度 缩短校验时间 重度且无法修复 更换 阀盖,调节螺杆腐蚀粘连无法修复 更换 阀体内部腐蚀 视其严重程度缩短校验时间或更换 阀座、阀芯损坏严重 更换 密封压力达不到试验要求 更换 调节圈锈死 更换 阀座裂纹 更换 调节螺母锈死 更换 阀瓣裂纹 更换 更换 10 弹簧断裂 出口堵死,无法清除 更换 1 阀体不接触介质部位裂纹 视其严重程度缩短校验时间或更换 12
GB/T26610.2一2014 附 录 B 规范性附录 换热管束检验策略 B.1符号 webull形状参数; -weibul特征寿命参数,年 C" 管束失效后果,元 C
基于管束计划更换周期下的管束失效后果,元; 管束更换费用,元 cost bndle 管束泄漏导致的环境影响费用,元; costom -管束检验费用,元; costnp -管束检维修费用,包括抽出管束和准备好检验或更换的费用,元 cOst lmins -管束计划更换周期内,管束更换的费用,元/年; cOsttr 停车对管束进行维修或更换导致的生产损失,元 cOst 管束计划更换周期内,管束更换计划的总费用,元/年 costtr) 计划停机检修管束所需要的时间,天; D.dl ERL 管束预期剩余服役年限,年 EsL 管束预期服役年限,年; ESL 管束计划更换周期内,管束失效的平均服役年限,年; ESL 管束计划更换周期内,管束没有失效的平均服役年限,年; EIR; 在本次停机检修时间和预计的下次停机检修时间和之间预期风险增量,元/年; r(r 关于r的方程; LEF -管束预期服役年限的延寿因子 MTTF 平均无故障工作时间,年; N 换热器管束历次更换数量; PBL 基于检验修正的管束预期服役年限,年; P 管束失效概率,次/年; P 基于使用单位风险可接受水平得到的最大可接受失效概率,次/年; 换热器历次失效的管束数量; -管束故障导致的产能下降百分比,% raterd ROR 收益率 RWT 失效指数,定义为剩余壁厚的分数; risk" -管束失效风险,元/年; risk 在管束计划更换周期内,管束失效风险,元/年; tr riskim 风险可接受水平,元/年; ,mm/年 管束的减薄速率, tnte 时间,年; 管束的服役时间,年; lde -管束调整后的服役时间,年 tada的
GB/T26610.2一2014 管束计划更换周期,年; tr -换热器中第i个管束的服役时间,年; lur, 换热管实测平均壁厚,mm: t 换热管制造平均壁厚,mm:; t" -管束计划更换周期优化的时间步长,天 -装置每天的生产利润,元/天
unitprod B.2最大可接受失效概率 换热管束最大可接受失效概率是换热管失效后果、使用单位设定的风险可接受水平的函数,其关系 见式(B.1): riskn (B.1 P: Cule B.3检验时间 在换热管束风险达到使用单位设定的风险可接受水平risk的日期前应对其实施检验,选择的检 验有效性应保证换热管束运行至下次停机检修时间点时,其风险不超过可接受水平
B.3.1检验时间的初始值 检验时间的初始值按式(B.2)计算 !=刀(一ln[1一Pt] B.2 其中: 取P=尸.;9取默认值3;按式(B.3)和式(B.4)计算,结果取小值 利用平均无故障工作时间计算,见式(B.3) a MTTF B.3 r'1+ 利用特定的管束历史情况计算,见式(B.4) b 生 B.4) B.3.2首检情况下的检验时间 -般取式(B.2)中检验时间初始值的一半
B.3.3有检验历史情况下的检验时间 B.3.3.1对于主导损伤模式为均匀腐蚀的管束,根据管束壁厚测量结果预估将来的失效日期,其计算 程序如下 a 换热管束的壁厚减薄速率可以根据其制造平均壁厚和上次检验实测平均壁厚按式(B.5)进行 计算: -'e二 B.5 tra ldur b)根据剩余壁厚分数确定失效时间点,按式(B.6计算基于检验修正的管束预期服役年 限PBL l: RWT lots PBL= B.6 lrt0
GB/T26610.2一2014 剩余壁厚分数RwT,默认值为0.75,也可以自行赋值
B.3.3.2若无法获取壁厚减薄速率计算所需要的换热管壁厚数据,或者损伤模式不仅仅是均匀腐蚀, 则根据自上次检验以来管束预期剩余服役年限ERL,计算基于检验修正的管束预期服役年限PBL (B.7 PBL=/i十ERL B.3.3.3若根据式(B.6)或式(B.7)确定了基于检验修正的管束预期服役年限,则通过增加基于检验修 正的管束预期服役年限作为另外的失效点,按式(B.8)可以确定管束修正的weibull特征寿命参数 -义 B.8 刀d B.3.3.4将)m代替式(B.2)中的7则可计算出有检验历史情况下的检验时间
B.3.4管束延寿措施的影响 换热管束检验之后的延寿方法以及管束预期服役年限延寿因子LEF见表B.1,根据式(B.9)以及 LEF值计算调整后的服役时间tadij tadi=(I-LEF)ia (B.9 式(B.9)中,实际的管束服役时间1可以根据其最初安装日期以及实施延寿处理时的检验日期计 算,见式(B.1o):
=实施延寿处理的检验日期一最初安装日期 (B.10) tlu 调整后的安装日期可以根据实施延寿处理的检验日期减去调整后的服役时间tad计算见 式(B.l1); 调整后的安装日期=实施延寿处理的检验日期一tad (B.ll 表B.1管束延寿方法 延寿方法 管束预期服役年限延寿因子LEE 堵管 0.10 管束旋转18o" 0.50 更换部分管子 0.50 更换全部管子 0.75 更换备用管束 1.00 B.4经济成本分析确定换热管束检验或更换策略 B.4.1在本次停机检修时间点,换热管束不实施检验或者不更换,直至预计的下次停机检修时间点所 造成的预期风险增量EIR可以根据式(B.12)进行计算 (B.12 EIR- -踪份 式中: 本次停机检修时间点; t" 预计的下次停机检修时间点
B.4.2根据式(B.12)计算实施检验或者更换的费用与不采取措施造成的风险增量进行比较,若检验或
GB/T26610.2一2014 者更换的成本低于预计的风险增量,则应进行检验或更换,判断条件如下: B.13 costap十costam.1RoR)
GB/T26610.2一2014 c 附 录 资料性附录 推荐的检验范围 C.1容器的检验范围见表c.1 表C.1容器的检验范围 检 围 验范 本次停机检修时间点的风险等级 -般保守程度 较高保守程度 高风险 100% 100% >60% >75% 中高风险 中风险 >40% >50% 低风险 >20% >25% C.2管道的检验范围见表C.2
表C.2管道的检验范围 围 验 范 本次停机检修时间点的风险等级 -般保守程度 较高保守程度 高风险 100% 100% 中高风险 50% 60% 中风险 30% 40% 低风险 >10% >20% c.3按照表c.1和表c.2给出的范围实施的检验,包括本次停机检修时间点实施的停机检验和其他时 间的在线检验
首次检验时,建议按照较高保守程度确定检验范围
C.4 C.5确定检验范围时,应保证覆盖所有腐蚀回路,并优先抽检满足以下条件的设备 a)失效可能性大于或等于3的 b 材质劣化和环境开裂敏感性较高的; e)有衬里的 d)超过设计寿命的
C.6对于在本次停机检修时间点前为高风险的设备,应在停机前采取在线检验或监测等措施降低 风险
C.7对于在预计的下次停机检修时间点前为高风险的设备,在本次停机检修时间点到下次停机检修时 间点之间,应采取在线检验等措施降低风险
13
承压设备系统基于风险的检验实施导则第2部分:基于风险的检验策略GB/T26610.2-2014
承压设备是现代工业生产中广泛应用的一种装备,包括锅炉、压力容器、管道等。由于其特殊的工作环境和作用,安全性至关重要。为了保障承压设备的正常运行,国家标准化管理委员会制定了《承压设备系统基于风险的检验实施导则》标准,并包括了多个部分。其中,第2部分《基于风险的检验策略GB/T26610.2-2014》主要针对承压设备的风险评估和检验策略进行了规定和要求。
该标准强调了基于风险的检验策略在检验实施中的应用,主要包括风险评估、检验计划制定和检验方法选择等内容。其中,风险评估是基于承压设备的关键参数和工作环境对各类风险进行综合评估,以确定检验的重点和难点;检验计划制定则需要根据风险评估结果确定具体的检验内容和频率;检验方法选择则需要根据承压设备的特点和检验需求,选择适合的检验方法。
该标准还规定了承压设备的检验周期和检验记录的管理要求。其中,检验周期需要根据设备的使用年限、检验结果和风险评估等因素进行确定;检验记录则需要详细记录检验的过程、结果及处理措施,以便于后期跟踪分析和改进。
通过基于风险的检验策略,可以有效避免传统检验方式带来的盲目性和浪费性,同时提高承压设备的安全性能和可靠性,保证其正常运行,促进了工业生产的良性发展。