GB/T33594-2017
电动汽车充电用电缆
Chargingcablesforelectricvehicles
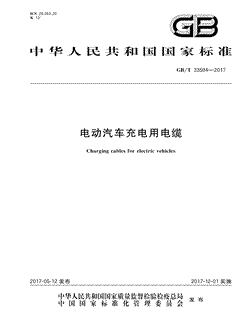
- 中国标准分类号(CCS)K13
- 国际标准分类号(ICS)29.060.20
- 实施日期2017-12-01
- 文件格式PDF
- 文本页数39页
- 文件大小2.59M
以图片形式预览电动汽车充电用电缆
电动汽车充电用电缆
国家标准 GB/T33594一2017 电动汽车充电用电缆 Charging cablesfo”electricvehicles 2017-05-12发布 2017-12-01实施 国家质量监督检验检疫总局 发布 国家标准化管理委员会国家标准
GB/33594一2017 前 言 本标准按照GB/T1.1一2009给出的规则起草
本标准由电器工业协会提出
本标准由全国电线电缆标准化技术委员会(SAC/TC213)归口
本标准起草单位:上海电缆研究所、上海国缆检测中心有限公司、质量认证中心,无锡鑫宏业特 塑线缆有限公司、广东奥美格传导科技股份有限公司、衡阳恒飞电缆有限责任公司、中天科技装备电缆 有限公司、无锡市明珠电缆有限公司、中利科技集团股份有限公司、金杯电工股份有限公司、金龙羽集团 股份有限公司深圳市沃尔核材股份有限公司、江苏亨通电力电缆有限公司、广州南洋电缆有限公司、远 东电缆有限公司,浙江万马股份有限公司、江苏上上电缆集团有限公司、常州船用电缆有限责任公司、扬 州亚光电缆有限公司、德凯质量认证(上海)有限公司、广东产品质量监督检验研究院、湖南长高高压开 关集团股份公司
本标准主要起草人李娜、,朱永华,曲文波,肖继东、杨娟娟,谢志国,关丽丽、关勇、刘瑶勋,王福珊 徐鹏飞、于金花、孙建宇、杨志强、陆枝才、张强、管新元、王志辉、汪传斌、刘焕新、祝军、高骏、贾云鹏、 洪健、刘伟海、卢圣杆、王灿
GB/33594一2017 电动汽车充电用电缆 范围 本标准规定了电动汽车充电用电缆的使用特性、表示方法、技术要求、标志、试验方法和要求、检验 规则以及电缆的包装,运输和贮存
本标准适用于电动汽车传导充电连接装置用额定电压交流450/750V及以下、直流1.0kV及以下 充电用电缆(可包括信号或控制线芯). 规范性引用文件 下列文件对于本文件的引用是必不可少的
凡是注日期的引用文件,仅注日期的版本适用于本文 件
凡是不注日期的引用文件,其最新版本(包括所有的修改单)适用于本文件
GB/T16902010硫化橡胶或热塑性橡胶耐液体试验方法 GB/T2423.3一2006环境试验第2部分;试验方法试验Cab;恒定湿热试验 GB/T2900.10电工术语电缆 GB/T2951.l1一2008电缆和光缆绝缘和护套材料通用试验方法第11部分;通用试验方法 厚度和外形尺寸测量机械性能试验 GB/T2951.12一2008电缆和光缆绝缘和护套材料通用试验方法第12部分;通用试验方法 热老化试验方法 GB/T2951.13一2008电缆和光缆绝缘和护套材料通用试验方法第13部分:通用试验方法 密度测定方法吸水试验收缩试验 GB/T2951.14一2008电缆和光缆绝缘和护套材料通用试验方法第14部分:通用试验方法 低温试验 GB/T2951.21一2008电缆和光缆绝缘和护套材料通用试验方法第21部分弹性体混合料专 用试验方法耐臭氧试验-热延伸试验-浸矿物油试验 GB/T2951.31一2008电缆和光缆绝缘和护套材料通用试验方法第31部分聚氯乙烯混合料 专用试验方法高温压力试验-抗开裂试验 GB/T3048.4一2007电线电缆电性能试验方法第4部分导体直流电阻试验 GB/T3048.5一2007电线电缆电性能试验方法第5部分:绝缘电阻试验 GB/T3048.8一2007电线电缆电性能试验方法第8部分;交流电压试验 3048.92007电线电缆电性能试验方法第9部分:绝缘线芯火花试验 T GB 3048.14一2007电线电缆电性能试验方法第14部分;直流电压试验 GB 3956一2008电缆的导体 GB/T4909.22009裸电线试验方法第2部分:尺寸测量 GB/T5013.2一2008额定电压450/750V及以下橡皮绝缘电缆第2部分:试验方法 GB/T16422.2一2014塑料实验室光源暴露试验方法第2部分怎弧灯 GB/T17650.1一1998取自电缆或光缆的材料燃烧时释出气体的试验方法第1部分;卤酸气体 总量的测定 GB/T17650.2一1998取自电缆或光缆的材料燃烧时释出气体的试验方法第2部分:用测量
GB/T33594一2017 pH值和电导率来测定气体的酸度 GB/T17737.1一2000射频电缆第1部分;总规范总则,定义,要求和试验方法 GB/T18380.12一2008电缆和光缆在火焰条件下的燃烧试验第12部分单根绝缘电线电缆火 焰垂直蔓延试验1kw预混合型火焰试验方法 GB29518一2013柴油发动机氮氧化物还原剂尿素水溶液(AUS32) JB/T8137(所有部分电线电缆交货盘 JB/T10696.6一2007电线电缆机械和理化性能试验方法第6部分:挤出外套刮磨试验 ISO48;2010硫化型或热塑型橡胶硬度测定(硬度在10IRHD和100IRHD之间)(Rubber, vulceanizedorthermoplastic一Determinationofhardness(hardnessbetween10IRHDand100IRHD) IEC60684-2:2011绝缘软套管第2部分:试验方法(Flexibleinsulationsleeving一 -Paurt2: test Methodsof 术语和定义 GB/T2900.10界定的以及下列术语和定义适用于本文件
3. 标称值nominalvalue 指定的量值并经常用于表格之中
注在本标准中,通常标称值引伸出的量值在考虑规定公差下通过测量进行检验
3.2 中间值medianvalue 将试验得到的若干数值以递增(或递减)的次序依次排列时,若数值的数目是奇数,中间的那个值即 是;若数值的数目是偶数,中间两个数值的平均值即是
3.3 额定电压ratedvolage 电缆设计使用和进行电性能试验用的基准电压
注在交流系统中,额定电压用U/U表示
U,表示任一主绝缘导体与“地"金属屏蔽,金属套或周围介质)之间的 电压有效值;U为多芯电缆或单芯电缆系统中任意两相导体之间的电压有效值
电缆的额定电压至少等于使 用电缆系统的标称电压,这个条件对U和U值都适用
在直流系统中,额定电压用U
表示,U,表示导体与屏 蔽之间的电压有效值
系统工作电压不大于系统标称电压的1.1倍
3.4 例行试验routinetests R 由制造方在成品电缆的所有制造长度上进行的试验,以检验所有电缆是否符合规定要求
3.5 抽样试验sampletests 由制造方按规定的频度在成品电缆试样上、或在取自成品电缆的某些部件上进行的试验,以检验电 缆是否符合规定要求
3.6 型式试验typetests 按一般商业原则对本标准所包含的一种类型电缆在供货前所进行的试验,以证明电缆具有能满足
GB/33594一2017 预期使用条件的良好性能
注,该试验的特点是除非电缆材料,设计或制造工艺的改变可能改变电缆的特性,否则试验做过以后不需要重做
电动汽车eleetrievehieles 包括纯电动汽车和混合动力(电动)汽车
纯电动汽车为由电动机驱动的汽车,电动机的驱动电能来源于车载可充电蓄电池或其他能量储存 装置;混合动力(电动)汽车为能够至少从下述两类车载储存能量中获得动力的汽车;可消耗燃料和可再 充电能/能量储存装置
3.8 充电charging 将交流或直流供电网(电源)调整为标准的电压/电流为电动汽车动力电池提供电能,也可额外地为 车载电气设备供电
使用特性 4.1额定电压 交流:U/U为450/750V及以下
直流:U
为1.0kV及以下
4.2温度范围 使用环境温度范围为一40C一十50C,使用时应根据环境需要选择适合的电缆
绝缘和护套(内护层)材料的导体最高连续工作温度和使用环境最低温度见表1
表1材料适用温度 温度 绝缘材料代号 护套材料代号 导体最高连续工作温度 使用环境最低温度 S,F 70 -25 -40 S90 S90、U、F 90 U、F 90 -40 EY U,Y] 十90 -40 代号型号和产品表示方法 5 5.1代号 5.1.1产品代号 电动汽车 EV AC(可省略) 交流充电用 DC 直流充电用
GB/T33594一2017 5.1.2导体结构 省略) 第5种铜导体 R 第6种铜导体 5.1.3绝缘材料代号 连续工作温度70C热塑性弹性体(TPE S90 连续工作温度90热塑性弹性体(TPE 连续工作温度90C的乙丙橡胶或类似的合成橡胶 EY 硬乙丙橡胶或类似的无卤合成材料 5.1.4护套(内护层)材料代号 连续工作温度70C热塑性弹性体(TPE S90 连续工作温度90C热塑性弹性体(TPE 热固性弹性体合成材料 聚氨酯弹性体材料 无卤交联聚烯胫或类似材料 Y 5.1.5结构特性代号 铜丝编织总屏蔽 P) 信号或控制线芯铜丝编织屏蔽 P2 信号或控制线芯铝塑复合带绕包十铜丝编织复合屏蔽 5.2型号 5.2.1电缆型号的组成和排列顺序见图1
护套 总屏敞(若有 内护层(若有 绝缘 导体 图1型号组成和排列顺序 5.2.2常用电缆型号及名称见表2.
GB/33594一2017 表2型号名称 常用电缆型号 称 SS 热塑性弹性体绝缘热塑性弹性体护套电动汽车充电用电缆 ssPs 热塑性弹性体绝缘饷丝编织屏蔽热塑性弹性体内护层和护套电动汽车充电用电缆 SF 热塑性弹性体绝缘热固性弹性体护套电动汽车充电用电缆 SSPF 热塑性弹性体绝缘铜丝编织屏蔽热塑性弹性体内护层热固性弹性体护套电动汽车充电用电缆 S90S90 热塑性弹性体绝缘热塑性弹性体护套电动汽车充电用电缆 S90S90PS90 只屏蔽热塑性弹性体内护层和护套电动汽车充电用电缆 热塑性弹性体绝缘铜丝编织 S90F 热塑性弹性体绝缘热固性弹性体护套电动汽车充电用电缆 S90S90PF s90U 热塑性弹性体绝缘聚氨酯弹性体护套电动汽车充电用电缆 S90S90PU 热塑性弹性体绝缘铜丝编织屏蔽热塑性弹性体内护层聚氨酯弹性体护套电动汽车充电用电缆 S90UPU 热塑性弹性体绝缘铜丝编织屏蔽聚氨酯弹性体内护层和护套电动汽车充电用电缆 EU 乙丙橡胶或类似合成橡胶绝缘聚氨酯弹性体护套电动汽车充电用电缆 EUPU 乙丙橡胶或类似合成橡胶绝缘铜丝编织屎蔽聚氨酯弹性体内护层和护套电动汽车充电用电缆 EF 乙丙橡胶或类似合成橡胶绝缘热固性弹性体护套电动汽车充电用电缆 EFPF 乙丙橡胶或类似合成橡胶绝缘铜丝编织屏蔽热固性弹性体内护层和护套电动汽车充电用电缆 EYu 硬乙丙橡胶或类似合成材料绝缘聚氨酯弹性体护套电动汽车充电用电缆 EYUPU 硬乙丙橡胶或类似合成材料绝缘铜丝编织屏蔽聚氨酯弹性体内护层和护套电动汽车充电用电缆 EYY] 硬乙丙橡胶或类似合成材料绝缘交联聚烯泾护套电动汽车充电用电缆 硬乙丙橡胶或类似合成材料绝缘铜丝编织屏蔽交联聚烯焰内护层和护套电动汽车充电用电缆 EYYJPY] 电缆导体为第6种导体时,在型号的左侧标示“R" 5.3产品表示方法 产品表示方法见图2 信号或控制线芯允许多个组合单元
示例1热塑性弹性体绝缘铜丝编织屏蔽聚氨酯弹性体内护层和护套电动汽车交流充电用电缆,导体为第6种导 体,额定电压为450/750V,主绝缘线芯3芯,标称截面积2.5mm,一对0.5mm信号或控制线芯,信号或控制线芯绞对 外有铜丝编织屏蔽层,表示为 VRsoUPU450750V3x2.5(2x0.5)(P)cGBT33594一2017 示例2;热塑性弹性体绝缘聚氨酯弹性体护套电动汽车直流充电用电缆,导体为第6种导体,额定电压为1.0kV,主 绝缘线芯2芯,标称截面积35mm,接地线芯1芯,标称截而积25mm',辅助电源线芯2芯,标称截面积4mm,两对 1.5mm'信号或控制线芯,其中一对1.5mm信号或控制线芯绞对外有塑复合带绕包十铜丝编织复合屏蔽层,表 示为 EVDC-RS90U1.0kV2×35+1×25+2×4+2×1.5+(2×1.5)(P2GB/T33594一2017
GB/T33594一2017 本标准编号 信号或控制线芯结构特 性若有 信号或控制线芯数×标称 截面积 辅助电源线芯数×标称截 面积 接地线芯数×标称截面积 主绝缘电源线芯数×标 称截面积 额定电压 电缆型号 产品代号 图2产品表示方法 技术要求 6 6.1导体 导体应是符合GB/T39562008中的第5种或第6种镀金属层或不镀金属层退火铜导体
信号 或控制线芯导体允许采用适当材料加强
导体标称截面积见表3. 表3导体标称截面积 标称截面积 电缆类型 线芯类型 mm 1.0~70 主绝缘线芯 交流充电用电缆 信号或控制线芯 0.5~1.5 主绝缘线芯 0~240 6120 接地线芯 直流充电用电缆 辅助电源线芯 4,6 信号或控制线芯 0.75~2.5 6.2 隔离层 允许在导体外包覆一层合适材料制成隔离层
GB/33594一2017 6.3绝缘(包括主绝缘线芯,接地线芯,辅助电源线芯) 6.3.1结构 绝缘应紧密挤包在导体或隔离层外,并应能够被剥除而不破坏绝缘、导体或镀锡层(若有)
6.3.2材料 绝缘应采用表1中所列的一种挤包成型的绝缘材料混合物
绝缘机械物理性能应符合表13的规定
6.3.3厚度 绝缘标称厚度见表4,任何隔离层的厚度应不包括在绝缘厚度中
绝缘厚度测量值的平均值应不小于规定的标称厚度,其最小测量值应不小于规定标称值的90%一 0.1mm
表4绝缘标称厚度 绝缘标称厚度 绝缘标称厚度 导体标称截面积 导体标称截面积 mm mm mm mm” S,S90,E EY S、S90,E EY 1.0 35 0,8 0." 1.2 0.9 1.5 0.8 0." 50 1.4 1.0 70 2.5 0,8 0." 1.4 1. l.0 0." 95 l.6 1.l 1.0 0." 120 1.6 1.2 10 l.0 0." 150 l.8 1." 16 1.0 0." 185 2.,0 1.6 25 1,2 0.9 240 2.2 1.7 6.3.4火花试验 绝缘线芯应按GB/T3048.92007的规定经受表5规定的工频火花试验作为中间检查
表5火花试验电压 绝缘标称厚度 试验电压 绝缘标称厚度 试验电压 kV kV mm mm 15 0.50 2.02.5 20 1.01.5 10 25 6.4信号或控制线芯 6.4.1结构 允许有一根或多根信号或控制线芯
GB/T33594一2017 若有屏蔽,信号或控制线芯的屏蔽可采用两种方式;裸铜线或镀锡铜线编织屏蔽;或铝塑复合带绕 包屏蔽加裸铜线或镀锡铜线编织复合屏蔽
编织用裸铜线或镀锡铜线的标称直径应不小于0.10mm 只用裸铜线或镀锡铜线编织屏蔽时,编织密度应不小于80%
采用铝塑复合带绕包屏蔽加裸铜线或镀 锡铜线编织复合屏蔽时,铜线或镀锡铜线的编织密度应不小于60%,铝塑复合带的绕包搭盖率应不小 于15%
编织密度的计算方法见6.7规定
复合屏蔽时,铝塑复合带的金属面应与编织层接触
屏蔽外允许挤包或绕包内衬层
6.4.2绝缘材料 信号或控制线芯的绝缘材料应与主绝缘线芯材料一致
6.4.3厚度 信号或控制线芯的绝缘标称厚度为0.5mm,测量值的平均值应不小于标称值,最小测量值应不小 于标称值的90%一0.1nmm 6.44火花试验 绝缘线芯应按6.3.4的要求进行火花试验 6.5缆芯和填充物 6.5.1结构 所有绝缘线芯(可包括信号或控制线芯)应绞合在一起
信号或控制线芯可绞合为一个单元与其他 线芯绞合,但不应位于缆芯的中心位置
允许在绞合绝缘线芯时使用填充物
6.5.2填充物材料 用于填充物的材料应适合电缆的运行温度并与电缆的绝缘和护套材料相容
若为无卤电缆,填充 物应符合表13中卤素含量评估的要求
6.6内护层 6.6.1结构 若有总屏蔽,缆芯外应有挤包内护层 挤包内护层应包覆在缆芯外并使电缆圆整,挤包内护层不应粘连绝缘线芯 挤包内护层前允许用合适的带子扎紧
6.6.2材料 在工作温度下,内护层材料应适合电缆的运行温度并与电缆的绝缘、护套材料相容
内护层的机械物理性能应符合表l4的要求(耐矿物油、耐酸碱性、耐水解性、抗撕试验除外)
6.6.3厚度 内护层的标称厚度为0.6mm,内护层厚度测量值的平均值应不小于标称值
GB/33594一2017 6.7总屏蔽(若有 屏蔽应采用裸铜线或镀锡铜线编织在内护层上
编织用裸铜线或镀锡铜线的标称直径见表6. 编织屏蔽铜线每锭在1001 mm 长度上应不超过1个接头,屏蔽层应均匀,编织层的编织密度应不小 于80%
编织密度按式()计算
P=2p一力×100 式中 编织层编织密度,以百分比(%)表示 单向覆盖系数,见式(2)
"D mndl 11 式中: 单向覆盖系数 m 编织机同一方向的锭数; -每锭的编织线根数 -编织铜线的直径,单位为毫米( d mm; D -编织层的节圆直径,单位为毫米(m mm -编织节距,单位为毫米(mm) 表6编织用裸铜线或镀锡铜线标称直径 标称直径 编织前电缆直径D mm nmm 10 0.15 10
GB/33594一2017 表8交流充电用电缆护套厚度和电缆外径(EY绝缘 电缆平均外径参考值 护套标称厚度 mm 主绝缘芯数 mmm 无总屏蔽电缆 总屏蔽电缆 标称截面积 总屏蔽电缆 无总屏蔽电缆 U护套 其他材料 U护套 其他材料 mm U 其他 其他 下限上限下限上限下限上限下限上限 护套材料护套材料 1.8 9.3 12.0 13.7 10.6 13.7 12.0 15,4 1.7 3×1.0 10.6 l.0 1.l 3×1.5 1.0 1.7 1.1 1.9 9.7" 12.5 1l.0 14.2 1.0 14.2 12.6 6.1 3×2.5 1. 1.8 1.l 1.9 10,.6 13.7 12.0 15.4 11.8 15.1 13.3 17.0 13.1 19.0 1.3 22 11.6 14.9 16.813.317.o14.9 1.9 3×4 1 3×6 1.2 2.9 16.4 14.4 18.4 14.4 18.4 20.5 2.0 2.2 16.1 1. a 2 3×10 l4." 8.7" 16,4 20,.9 l6.2 20.6 18. 23.0 1. 2.5 1.5 17.0 25.9 s 2.6 21.6 18.9 24.0 18.5 23.5 20.4 3x5 1. 3.0 20.6 26.2 22.7" 28.8 22.2 31.0 2.8 1.8 28.124.5 X5 a 2a 1.9 32.4 3.3 23.8 30.1 26.1 33.0 25,6 28.1 35.5 2.2 2. 3×0 3.6 3.7 37.3 27.9 35.3 30.638.629.6 32. 0.9 2. 3×70 32.4 40.9 35.5 34.3 43.2 37.5 47.3 4.0 4.2 2.5 44.8 4×1.0 9,9 12.7 1l.2 14.4 1l.2 14.4 12.8 16.3 1.? 1.9 1. 1.1 19 4X1.5 .8 15.4l1.8 17.0 10,6 13.7 12.0 15,1 13.3 8 I. 2. 11.5 14.8 13.0 16.7 13.2 16.9 14.8 18.8 4x2.5 1. 20 . 4x4 2.2 1.2 12.9 6.4 14.4 18.4 14.4 18.4 16. 20.5 x6 2.2 2.s3 1.3 1.4 17.6 14.3 18.2 16,0 20,4 15.8 20,2 22.3 4X10 1. D 2.516.320.8 23.217.822.719.825.1 15 18,2 2 xI16 9.0 24.1 21. 26.8 20.5 28.7 1.6 2.8 26.022.6 又s 9 2a0 3.3 23.4 29.6 25,7 32.5 25.2 31.9 27." 35.0 20 22 4x35 3.626. 28. 31. 33.4 29.1 36,7 35.9 39.2 2.3 没.9 30.9 39.0 34.0 42.8 32.9 41.5 36.o 45.4 4×0 2.5 4 4. 2.8 4×70 2.6 4.6 36.l 45.5 39.5 49.8 38.l 48.0 41.6 52.3 2.0 12.215.612.215.613.7 17.5 1.2 13.9 1.8 5×1.0 1. 10,.8 14.6 12.9 16.6 13.1 16.8 5X1.5 1.9 11.4 14.7 18.7 1 1 20 22 5×2.5 l. 1. 12.7 16.2 14.2 18.1 14.2 18,1 15.9 20.3 .S 22 1. 3 20.315.720.017.522.2 l4.2 18.l 15,9 5×6 15.7 20.0 17.5 22.2 17.3 22.0 19.2 24.4 2.3 2.5 1!. 1. 26 .6 5×10 1.6 2. 18.3 23.3 20.2 25.7 19.7 25.0 21.8 27.6 2.9 1.7 1.8 5×16 3.0 21. 26.8 23.4 29.6 22.6 28.7 24.9 31.6 5×25 2.0 3.4 2. 26.2 28.235.630.9 3.6 33.l 28,9 36.5 39.0 5×35 3.9 29,4 37.1 32.2" 40.7 31.2 39.4 34.3 43.2 3.7 25 aa 2.5 5×50 4.2 2.6 4.4 34.3 43.2 37.5 47.3 36.1 45.5 39.5 49.8 5X70 2.9 4.8 3,.0 5,0 40,2 50.6 43.9 55,2 42.2 53,2 46. 58.0 1
GB/T33594一2017 表9直流充电用电缆护套厚度和电缆外径(s,s90和E绝缘) 电缆平均外径参考值 护套标称厚度 mm 主绝缘芯数 mmm 无总屏蔽电缆 总屏蔽电缆 标称截面积 无总屏蔽电缆 总屏蔽电缆 U护套 其他材料 U护套 其他材料 mm U 其他 其他 下限 上限 下限 上限 下限 上限 下限 上限 护套 材料 护套 材料 2×10 1. 2.3 2.4 15.3 19.6 17.1 21." 16.7 21.2 18.6 23.6 1.4 2×16 1.5 2.5 1.6 2.7 17.8 22.7 19.8 25.l 19,4 24.6 21.5 27.2 2×25 1.8 3.0 1.9 3.2 22.2 28.1 24.5 31.0 24.0 30.4 26.5 33.5 2.0 7.6 2×35 3.3 2. 3.525.231.927.735.027.134.229.7 22 2x50 3,7 2.3 3,9 29.6 37.3 32.4 40,9 31.4 39.6 34.5 43.4 4.2 2.6 33.9 42.7 46.8 35.9 45.2 39. 49.6 2 x70 2.5 37.1 4,4 2×95 2.8 4.6 2.9 4.8 38.4 48.4 41.8 52.7 40,4 50.9 44.1 55.4 2×120 3.0 5.0 3.l 5.2 42.3 53.3 46.2 58. 44.3 55.8 48. 60.8 2×150 3.3 5.5 3.4 5.7 47.4 59,6 51.6 64.9 49,0 61.7 53.5 67.2 2×185 3.6 6.0 3.7 6,2 52.3 65.8 56.9 71.5 53.9 67.8 58.7 73.8 59.5 64.7 81.2 2×240 6.8 4.1 6.9 74.8 60.9 76.6 66.3 83.3 4.l 表10直流充电用电缆护套厚度和电缆外径(EY绝缘) 电缆平均外径参考值 护套标称厚度 mm 主绝缘芯数 mm 无总屏蔽电缆 总屏敞电缆 标称截面积 U护套 其他材料 U护套 其他材料 无总屏蔽电缆总屏蔽电缆 nmm" U 其他 其他 下限上限下限上限下限上限下限上限 护套材料护套材料 2×10 1.3 2.1 1.4 2.3 13.9 17.8 15.4 19,7 15,4 19.7 17.2 21.8 2×16 1.4 2.4 1.6 2,6 16.4 20,9 18.3 233 18.1 23.0 20,1 25.4 20.7 2×25 1. 2.8 22.828.9 26.4 3.4 1.9 3.2 26.3 23,9 30.3 2×35 1.9 3. 2.0 3.3 23.8 30.l 26.l 33.0 25.6 32.3 28.1 35.5 3,6 2.2 3.7 27.9 35.3 30.6 38.6 29.5 37.3 32. 40.9 2×50 2.2 2×70 2.4 4.0 2.5 4.2 32.4 40.9 35.5 44.8 34.2 43.1 37.5 47.2 2X95 4.4 2.8 4.6 36.0 45.4 39. 49.7 38,2 48.1 41.7 52.4 2.6 2×120 2.9 4.8 3.0 5,0 40.5 51,0 44.1 55.6 42.5 53.5 46,4 58.3 2×150 3,2 5,4 3.3 5,5 45.6 57.4 49.8 62,6 47.2 59.4 51.4 64.7 2×185 63.5 54.9 52.1 3.5 5.8 50.5 65.556., 1.3 3.6 69.0 6.0 2×240 3.9 6.5 4.0 6.7 57.1 71.8 62.1 78.0 58.7 73.8 63.9 80.3 12
GB/33594一2017 电缆标志 7.1 -般要求 电缆应有制造厂名、产品代号、电缆型号规格和额定电压的连续标志
厂名标志可以是制造厂名称 或商标
电缆型号见5.2
标志可以用油墨印字或采用压印凸字在护套上
7.2标志连续性 护套表面一个完整标志的末端和下一个完整标志的始端之间的距离应不超过550mm
7.3清晰度和耐擦性 所有标志应字迹清楚
印刷标志应耐擦
应通过以下试验检查是否满足要求:用浸过水的脱脂棉或棉布,轻轻擦拭10次, 然后目力检查,电缆表面印字应基本不变
绝缘线芯识别 8.1 -般要求 电缆主绝缘线芯应采用颜色识别,并应符合8.2规定
电缆的辅助电源线芯,信号或控制线芯及其他扩展线芯可采用颜色识别或数字识别,并应符合8.2 和8.3规定 8.2颜色色谱 8.2.1 -般要求 电缆绝缘线芯应采用着色绝缘或其他适合的方法进行识别 除用绿/黄组合颜色识别的线芯外,电缆的每根绝缘线芯应只用一种颜色
绿色和黄色不能作为独 立的颜色使用
8.2.2颜色色谱 电缆主绝缘线芯着色优先选用的色谱如下 两芯电缆;蓝色、棕色 三芯电缆;绿/黄色、蓝色、棕色; 四芯电缆绿/黄色、蓝色、棕色、灰色 五芯电缆;绿/黄色、蓝色、棕色、黑色、灰色
各种颜色应清楚可识别、持久
对于采用颜色识别的辅助电源线芯、信号或控制线芯及其他扩展线芯等的着色不作要求,但其颜色 应可清晰识别,并与主绝缘线芯颜色不同
8.2.3绿/黄色组合 绿/黄色组合的线芯颜色分布应符合下列要求;对于每一段长15mm的绝缘线芯,其中一种颜色应 至少覆盖绝缘线芯表面的30%,且不大于70%,而另一种颜色则覆盖绝缘线芯的其余部分
13
GB/T33594一2017 注:关于使用绿/黄组合色的情况说明;当按上述规定使用绿/黄组合色时,表示专门用作识别连接接地或类似保护 用途的绝缘线芯
8.3数字识别 8.3.1 般要求 电缆的辅助电源线芯、信号或控制线芯及其他扩展线芯可采用数字识别
线芯的绝缘应是同一种颜色,并按数序排列,但绿/黄色线芯(若有)除外 数字编号应从数字1开始
数字应用阿拉伯数字印在绝缘线芯的外表面上
数字颜色相同并与绝缘颜色有明显反差,数字应 字迹清晰
8.3.2数字的优先排列方法 数字标志应沿着绝缘线芯以相等的间隔重复出现,相邻两个完整的数字标志应彼此颠倒
当标志是由一个数字组成时,则破折号应放置在数字的下面
当标志是由两个数字组成时,则一个 数字排在另一个数字的下面,同时在底下的数字下面放破折号
相邻两个完整的数字标志之间的距离 d应不超过50mm 标志的排列如图3所示
图3数字标志的排列 8.3.3耐擦性 数字标志应耐擦,应按7.3规定的检查方法检查是否符合要求
例行试验 9.1导体直流电阻试验 成品电缆应在保持适当温度的试验室内至少存放12h后再进行导体直流电阻试验
导体直流电阻试验应按GB/T3048.4一2007的要求进行
电阻测量值应按GB/T39562008规定的公式和系数校正到20C下1km长度的数值 每一根导体20C时的导体直流电阻应不超过GB/T3956-2008规定的相应的最大值
9.2电压试验 电压试验应在环境温度下进行,交流充电用电缆应按GB/T3048.8-2007的要求进行,直流充电 用电缆应按GB/T3048.14一2007的要求进行
电压试验按下列要求进行: 交流充电用电缆;依次在每一主绝缘导体对其余导体和编织屏蔽(若有)之间施加交流电压 3.5kV,时间为15min;依次在每一信号或控制线芯导体与其余导体以及编织屏蔽(若有)之 14
GB/33594一2017 间施加交流电压1.5kV,时间15min;电缆绝缘均应无击穿 直流充电用电缆;依次在每一绝缘导体(包括接地线芯导体,辅助线芯导体等)对其余导体和编 织屏蔽(若有)之间施加直流电压8.4kV,时间15min;依次在每一信号或控制线芯导体与其 余导体以及其编织屏蔽(若有)之间施加电压3.6kV,时间15nmin;电缆绝缘均应无击穿
9.3火花试验 绝缘线芯应按6.3.4和6.4.4进行火花试验
10抽样试验 0.1抽样频度 10.1.1导体检查和尺寸检查 导体检查和尺寸检查应在每批同一型号和规格电缆中的一根制造长度的电缆上进行,但应限制不 超过合同数量的10%
0.1.2其他试验项目 应按商定的质量控制协议,在制造长度电缆上取样进行试验
若无协议,对于总长度大于2km的 电缆可按表11进行
表11 抽样试验样品数量 电缆长度 样品数(最少) km 10 >10 <20 20 s30 余类推 余类推 10.2复试 如果任一试样没有通过10.3一10.》规定的任一项试验,应从同一批中再取两个附加试样就不合格 项目重新试验
如果两个附加试样都合格,则认为样品所取批次的电缆符合本标准的要求
如果附加 试样中有一个试样不合格,则认为抽取该试样的这批电缆不符合本标准的要求
0.3导体检查 应采用目力检查和可行的测量方法检验导体结构是否符合GB/T3956一2008的要求
10.4绝缘厚度的测量 选取的每根电缆去除可能受到损伤的部分后,从端头取一段代表取样的电缆
按照GB/T2951.11一2008中8.1的规定测量每根线芯的绝缘厚度
测量结果应符合6.3.3和6.4.3的要求
15
GB/T33594一2017 0.5护套厚度的测量内护层和护套》 选取的每根电缆去除可能受到损伤的部分后,从端头取一段代表取样的电缆 按照GB/T2951.11一2008中8.2的规定进行测量
测量结果应符合6.6.3和6.8.2的要求
0.6屏蔽层结构的测量 在选取的试样上用合适的测量工具测量6.7规定的参数,并计算屏蔽层的编织密度,测量结果应符 合6.7和6.4.1的要求
0.7外径的测量 电缆外径的测量应按GB/T2951.l1一2008中8.3的规定进行
测量结果应符合6.9的要求
0.8绝缘及护套(内护层)热延伸试验(适用时) 绝缘及护套(内护层)的热延伸试验的取样和试验步骤应按GB/T2951.21一2008中第9章的规定 进行,试验条件和试验结果应符合表13和表14的规定
10.9电缆的单根阻燃试验 电缆的单根阻燃试验要求和方法应符合GB/T18380.122008的规定 1 型式试验 11.1电缆的结构尺寸 电缆结构尺寸检查应按10.3~10.7的规定进行,检查结果应符合6.1一6.9的要求
11.2电缆的电气性能 11.2.1导体直流电阻试验 导体直流电阻试验应按GB/T3048.4一2007的要求进行
每一根导体20C时的导体直流电阻应不超过GB/T3956-2008规定的相应最大值
11.2.2成品电缆耐压试验 交流充电用电缆应按GB/T3048.8一2007规定的方法进行试验,直流充电用电缆应按GB/T3048.14 2007规定的方法进行试验,试验条件和结果应符合表12的规定 11.2.3绝缘线芯耐压试验 试验在5m长的试样上进行,剥去电缆护套和任何其他包覆层或填充物而不应损伤绝缘线芯
将绝缘线芯按表12的要求浸于水中,电压施加在导体和水之间
试验电压和施压时间应按表12 的要求进行,试验结果应符合表12的规定
11.2.4长期直流耐压试验 试验在5m长的试样上进行,剥去电缆护套和任何其他包覆层或填充而不应损伤绝缘线芯
16
GB/33594一2017 将绝缘线芯浸人含氯化钠30g/儿L的恒温水槽中,试样两端应露出水面约250mm
水浴温度、在 水溶液和试样导体之间施加的电压值以及施加电压时间应按表12的要求进行
施加电压正极接浸人 水溶液中的铜电极,负极接试样导体
试验结果应符合表12的规定
11.2.5绝缘电阻常数K 应按GB/T3048.5- -007规定的方法测量电缆绝缘线芯的绝缘电阻,在试验前绝缘线芯试样应浸 在20C或导体最高运行温度下的水中至少2h,直流测试电压应为(80500V,测试时间应不少于 min且不超过5min
测量在导体与水之间进行
绝缘电阻常数K,由所测得的绝缘电阻值按式(3)计算
LxRx10" K,=" lg(D/d 式中: K 绝缘电阻常数,单位为兆欧公里(Mnkm). 电缆长度,单位为厘米(em) R -测得的绝缘电阻,单位为欧姆(Q); D 绝缘外径,单位为毫米(mm). -绝缘内径,单位为毫米(mmm)
从式(3)中计算出的数值应不小于表12的规定值
11.2.6护套表面电阻 截取三段成品电缆试样,每段试样长度约为250mm
用工业酒精清洁电缆护套表面,每个试样上用直径为0.2 2mm~0.6mm的细铜丝螺旋缠绕两个电 极,两电极之间距离为(100士2)mm,缠绕完成后再次彻底清洁两电极间的电缆护套表面
将制好电极的试样放置在温度为(20士2)、湿度为(65士5)%的试验箱中24h
从试验箱中取出试样,立刻在两电极间施加100V500V的直流电压,lmin后测量电阻值
测 量结果按式(4)计算
Rs=R×a/100 式中: 表面电阻,单位为欧姆(Q) Rs R -测得的电阻值,单位为欧姆Q); -电缆试样的周长,单位为毫米mm. 测量三个试样的表面电阻,以计算结果中间值作为该电缆的护套表面电阻,护套表面电阻值应符合 表12的规定
1.2.7信号或控制线芯屏蔽层表面转移阻抗 信号或控制线芯屏蔽层表面转移阻抗试验应按GB/T17737.1一2000中12.2.4.1规定的试验方法 进行,试验结果应符合表12的规定
17
GB/T33594一2017 表12电气性能试验要求 要 求 序号 试验项目 单位 交流充电电缆 直流充电电缆 成品电缆耐压试验 1.1 试验条件 试样长度 m 0 10 施加电压时间 S min 15 施加电压 见9.2 见9.2 1.2 试验结果 不击穿 不击穿 绝缘线芯耐压试验 2.1 试验条件 -试样长度 m 浸水最少时间 h C 水温(偏差士5 20 20 -施加电压时间 min -试验电压 2.5(AC 6(C 主绝缘(辅助/接地)线芯 kV .D 信号或控制线芯 kV l.5(AC 试验结果 2.2 不击穿 不击穿 长期直流耐压试验 3.l 试验条件 -试样长度 m o 85 85 -试验温度(偏差士2C -浸水时间 h 240 240 施加电压(DC) 600 600 3,2 试验结果 不击穿,试验后绝缘不击穿,试验后绝缘 表面无损伤 表面无损伤 绝缘电阻常数K S90 绝缘材料代号 EY 试验结果 -20C偏差士1),最小 Mnkm 36.7 3670 3670 3670 MQkmm 0.037 3.67 3.67 3.67 正常运行时导体最高温度(偏差士2C),最小 护套表面电阻,最小 Q l0° 10?" 信号或控制线芯屏蔽层表面转移阻抗 mn/m 250 250 试验频率30MHz),最大 1.3绝缘机械物理性能 绝缘机械物理性能应符合表13的规定 18
GB/33594一2017 表13绝缘机械物理性能 要 求 序号 试验项目 试验方法 单位 S90 E FY 原始性能 GB/T2951.ll一2008 抗张强度,最小 N/mm 10,0 10,0 5.,0 8.0 1. 断裂伸长率,最小 % 250 300 200 200 1. GB/T2951.12一2008 空气烘箱老化后性能 2.1 处理条件 100 135 135 135 温度(偏差士2c) 168 168 168 168 持续时间 抗张强度 2.2 老化后数值,最小 N/mm 10,0 10,0 5.,0 % 变化率",最大 士25 士25 士30 士30 2.3 断裂伸长率 250 300 老化后数值,最小 % 士25 士25 士30 变化率",最大 士30 GB/T2951.122008 空气弹老化后性能 处理条件 3.1 温度偏差士2C) 127 处理时间 h 40 抗张强度 3.2 % 变化率",最大 士30 3.3 断裂伸长率 % 变化率",最大 十30 热延伸试验 GB/T2951.21一2008 4.1处理条件 温度偏差士3) 250 250 15 负荷时间 min 15 机械应力 N/enm 20 20 4.2 试验结果 负荷下伸长率,最大 100 100 冷却后永久伸长率,最大 25 25 高温压力 GB/T2951.312008 5.1 处理条件 温度(偏差土2C 8o0 90 处理时间 见GB/T2951.31 2008中8,1.5 5.2 试验结果 % 50 50 -压痕深度,最大中间值 收缩试验 GB/T2951.132008 6.1 处理条件 -标志间长度 200 200 200 200 mmm 丫 -温度(偏差士3 100 130 130 130 持续时间 6.2 试验结果 允许收缩率,最大 19
GB/T33594一2017 表13(续 要 求 序号 试验项目 试验方法 单位 S90 E EY 低温卷绕试验 GB/T2951.l4一2008 试样外径D<12.5mm时 7.1 处理条件 -25 温度(偏差士2C) -40 -40 40 见GB/T2951.14一2008中 -施加低温时间 8,1,4和8,l.5 7.2试验结果 不开裂 低温拉伸试验临 GB/T2951.14一2008 试样外径D>12.5mm时) 8.1 处理条件 -25 -40 温度(偏差士2C -40 -40 施加低温时间 见GB/T2951.14一2008中 8.3.4和8.3.5 8.2 试验结果 % 30 30 30 30 -断裂伸长率,最小 GB/T2951.212008 耐臭氧试验 处理条件 9.1 温度(偏差士2C C 25 25 处理时间 h 24 24 0,025~o,025 % -臭氧浓度(体积比 0.030 0.030 不开裂 9.2 试验结果 10 硬度测定" 附录A 试验结果 -硬度值,最小 80 IRHD l 卤素含量评估 试验结果 % -卤酸气体含量(以HCl表示),最大GB/T17650.1一1998 0.5 GB/T17650.21998 pH值,最小 4.3 电导率,最大 GB/T17650.2 0 -l998 4S/mm 叙含量,最大 0. IEC60684-2;2011 老化后中间值与老化前中间值之差除以老化前中间值,以百分数表示
试验不能用挤出绝缘线芯进行时,可采用材料压片进行测试
11.4护套(内护层)机械物理性能 有总屏蔽结构电缆内护层的机械物理性能应符合表14的规定(耐矿物油、耐酸碱性、耐水解性、抗 撕试验除外. 20
GB/33594一2017 护套机械物理性能应符合表14的规定
表14护套机械物理性能 要求 序号 试验项目 试验方法 单位 S90 原始性能 GB/T2951.l12008 抗张强度,最小 10.0 10.0 10.0 20.0 10.0 1.l1 N/mm 1.2 % 250 300 300 300 150 -断裂伸长率,最小 空气烘箱老化后性能 GB/T2951.122008 2.1 处理条件 135 100 110 130 温度《偏差士2C) 100 持续时间 h 168 168 168 168 168 2.2抗张强度 老化后数值,最小 N/mm' 10,010,0 % 士25 士25 士30 士30 士30 -变化率",最大 2.3断裂伸长率 老化后数值,最小 250 300 250 300 士25 变化率",最大 士25 士40 士30 士30 耐矿物油试验(IRM902 3.1 处理条件 c 温度(偏差土2C) 100 100 100 h 24 168 168 处理时间 3.2抗张强度 -变化率",最大 士40 士40 士40 断裂伸长率 3.3 浸油后数值,最小 300 -变化率",最大 士40 士30 士40 热延伸试验 GB/T2951.21一2008 处理条件 4.1 温度(偏差土3C C 250 200 负荷时间 min 15 15 20 -机械应力 20 N/em 4.2 试验结果 负荷下伸长率,最大 % 175 100 % 冷却后永久伸长率,最大 15 25 GB/T2951.312008 高温压力试验 5.1 处理条件 80 温度(偏差士2C 90 100 h 见GB/T 处理时间 见GB/门T 2951.31 2951.31 2008中8,2.5 -2008 中8.2.5 试验结果 50 50 50 压痕深度,最大中间值
GB/T33594一2017 表14(续 要求 序号 试验项目 试验方法 单位 S90 热冲击试验 GB/T2951.31一2008 处理条件 6.l C 150 150 150 -温度(偏差士2 处理时间 h 6.2 试验结果 不开裂 不开裂 GB/T2951.132008 热收缩试验 7.1 处理条件 温度(偏差土2 8o 80 80 80 80 加热持续时间 h -加热周期 7.2 试验结果 允许收缩率,最大 低温卷绕试验 GB/T2951.l42008 试样外径D<12.5mm时 8.1 处理条件 -温度偏差士2C 25 一40 一40 一40 -40 -施加低温时间 见GB/T2951.14一2008中8.2.3 8.2 试验结果 不开裂 GB/T2951.142008 低温拉伸试验 试样外径D>12.5mm时 9.1 处理条件 " 温度(偏差士2c 25 40 40 40 40 见GB/T2951.142008 -施加低温时间 中8.4.4和8.4.5 试验结果 9.2 % 断裂伸长率,最小 30 30 30 30 30 GB/T2951.212008 1o耐臭氧试验 10.1处理条件 -温度(偏差土2 25 25 25 24 处理时间 h 24 24 % -臭氧浓度(体积比) I0.025一0.025一0.025- 0.0300.0300.030 10.2试验结果 不开裂 耐酸,碱性(分开测试) l1 GB/T2951.21一2008 1.1处理条件 -酸;标准草酸(0.5mol/L)或醋 酸溶液(1mol/L 碱;标准氢氧化钠溶液(1mol/L 22
GB/33594一2017 表14(续》 要求 单位 序号 试验项目 试验方法 S90 YJ C 23 温度偏差士2C) 23 23 23 23 处理时间 h 168 168 168 168 168 1.2抗张强度 -变化率,最大 % 士30 士30 士30 士30 士30 11.3断裂伸长率 -试验后数值,最小 100 100 100 100 100 GB/T2951.212008 12 耐水解性 12.1处理条件 -水:蒸僧水或去离子水 c 70 70 温度(偏差土2C 80 80 80 h -处理时间 168 168 168 168 168 12.2抗张强度 变化率",最大 士30 士30 士30 士30 士30 2.3断裂伸长率 试验后数值,最小 250 300 变化率",最大 士30 士30 士30 士30 士30 抗撕试验 附录B 13 试验结果 20 40 抗撕强度,最小 N/mm 20 10 10 附录c 14 皂化试验 200 试验结果,最大(以KOH计) tmg/g 15 卤素含量评估!" 试验结果 卤酸气体含量(以HC表示),GB/T17650.1l一1998 0.5 0.5 最大 GB/T17650.21998 pH值,最小 4.3 4.3 -电导率,最大 GB/T17650.2一1998 4S/mm 35 10 氟含量,最大 EC60684-2;2011 0. 0. 变化率;老化后中间值与老化前中间值之差除以老化前中间值,以百分数表示
当绝缘材料没有岗素含量评估要求时,U护套不作此要求
11.5成品电缆特殊试验 11.5.1相容性试验 本试验适用于所有类型的电缆
按GB/T2951.12一2008中8.1.4的规定从成品电缆截取样品,并在符合表15中规定温度的空气 烘箱中处理168h
在相容性老化试验后的电缆试样上按GB/T2951.11一2008中第9章进行机械性能试验,试验结 果应符合表15的要求
23
GB/T33594一2017 表15相容性试验要求 绝缘 护套(内护层) 单位 S90 E,EY s,S90 U,YJ 烘箱温度偏差士2 80 100 100 % 抗张强度变化率,最大 士25 士30 士30 士25 士25 士30 % 士25 士25 士25 断裂伸长率变化率,最大 士30 士30 士40 11.5.2耐化学液体试验 各取一段成品电缆进行本试验,每段电缆长度应不小于600mm,在室温下浸人表16中规定的液 体中浸泡1h,取出后在室温下放置22h,再进行弯曲试验
弯曲试验用试棒直径最大为5D(D为处理前电缆外径),试样180"弯曲后电缆表面应无肉眼可见 裂纹
表16试验用化学液体 序 液体名称 润滑油(重载柴油及汽油引擎用)(15W40) 无汽油(GB/T1690一2010中液体C 尿素溶液(32.5%)(GB29518一2013) 矿物油(IRM902) (90%IRM903十10%对二甲苯 柴油(9 防冻液(乙二醇与水1:】混合 清洁液,例如P3-soleleanAK 11.5.3人工气候老化试验 从被试电缆上截取足够长的电缆,取出绝缘线芯制取护套试样(试片),有机械损伤的护套不应作为 试验用试样
nm400nm 试验设备应符合GB/T16422.22014的规定
饭弧灯在波长3001 的辐照强度应不 小于43w/m士15%
试样暴露时间为720h,即360个120 min的循环,每个循环的要求如下 无喷水时间为(102土0.5)min,有饭弧灯照射,黑板温度为(63士3C,相对湿度(50士10)%; 喷水时间(18士0.5)min,无缸弧灯照射,黑板温度为(50士3)C,相对湿度不控制
完成规定的循环次数后,将试样放置于环境温度下16h,检查试样光照面,应无目力可见的裂纹
将试样按GB/T2951.1l一2008中第9章进行机械性能试验,人工气候老化试验后抗张强度变化 率应不超过士30%,断裂伸长率变化率应不超过士30%
11.5.4低温冲击试验 成品电缆低温冲击试验的试验温度按表1列出的使用环境最低温度进行,试验步骤和方法按 GB/2951.14一2008中8.5进行,但落锤重量、中间铁块重量和落锤落下高度应符合表17的要求
24
GB/33594一2017 试验后用正常视力或校正视力而不用放大镜检查电缆绝缘外表面和护套内外表面,3个试样均不 应有裂纹
低温冲击试验参数 表17 电缆直径D 中间铁块重量 落锤重量 落下高度 mmm mm D<15 1000 200 100 15
GB/33594一2017 90" 90 说明 -电缆的弯曲半径; 中心点; 电缆试样; -固定导板; 外力F 循环(每边90"为一个循环) 图5摇摆试验示意图 表18摇摆试验参数 电缆外径D 外力F 弯曲半径R N mm mm D<35 50 80 75 12o 35 50 200 50
电动汽车充电用电缆GB/T33594-2017
随着电动汽车的不断普及,越来越多的人开始选择购买电动汽车。而电动汽车充电用电缆则是电动汽车必备的充电设备之一。GB/T33594-2017标准规定了电动汽车充电用电缆的技术要求和测试方法,以保障电动汽车充电用电缆的安全可靠性。
一、技术要求
1. 外观:电动汽车充电用电缆应具有良好的外观质量,表面不能有明显的裂纹、气泡、污渍等缺陷。
2. 机械性能:电动汽车充电用电缆应具有良好的机械性能,耐磨、抗拉伸、抗扭曲等性能要求均达到标准规定。
3. 电气性能:电动汽车充电用电缆在额定电压下,其绝缘电阻、介质损耗因数、直流电阻和交流电阻等性能指标应均符合标准规定。
4. 耐久性:电动汽车充电用电缆应具有较强的耐久性,经过多次弯曲和拉伸后,其性能指标也应符合标准规定。
二、测试方法
1. 外观检验:采用目视检查法对电动汽车充电用电缆进行外观检验。
2. 机械性能:采用拉伸试验、弯曲试验、扭转试验等方法对电动汽车充电用电缆的机械性能进行测试。
3. 电气性能:采用高压耐受性试验、绝缘电阻测试、电阻测试等方法对电动汽车充电用电缆的电气性能进行测试。
4. 耐久性:采用弯曲试验、拉伸试验等方法对电动汽车充电用电缆的耐久性进行测试。
三、使用注意事项
1. 在使用电动汽车充电用电缆时,应仔细查看其外观是否完好无损,避免因破损导致安全隐患。
2. 在拔插电动汽车充电用电缆时,应先断开电源,避免因误操作导致电击事故发生。
3. 选择合适的电动汽车充电桩和电动汽车充电用电缆,以保障充电过程的安全可靠性。
四、结论
GB/T33594-2017标准规定了电动汽车充电用电缆的技术要求和测试方法,保障了其安全可靠性。在使用电动汽车充电用电缆时,应注意外观是否完好无损,拔插电动汽车充电用电缆时先断开电源,并选择合适的充电桩和电动汽车充电用电缆。通过遵守相关使用注意事项,可以更好地保障电动汽车充电用电缆在使用过程中的安全性和稳定性。