GB17578-2013采
客车上部结构强度要求及试验方法
Requirementsandtestmethodsofstrengthforthesuperstructureofbus
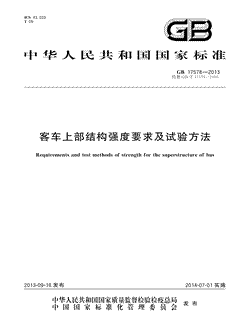
- 中国标准分类号(CCS)T09
- 国际标准分类号(ICS)43.020
- 实施日期2014-07-01
- 文件格式PDF
- 文本页数44页
- 文件大小948.13KB
以图片形式预览客车上部结构强度要求及试验方法
客车上部结构强度要求及试验方法
国家标准 GB17578一2013 代替GB/T175781998 客车上部结构强度要求及试验方法 Requirementsandtesmethodsofstrengthforthesuperstruetureofbs 2013-09-18发布 2014-07-01实施 国家质量监督检验检疫总局 发布 国家标准化管理委员会国家标准
GB17578一2013 目 次 前言 范围 规范性引用文件 术语和定义 技术要求及试验方法 同一型式的判定 标准实施的过渡期要求 附录A(资料性附录)本标准章条编号与ECER66章条编号对照 本标准与ECER66技术性差异及其原因 附录B资料性附录 附录c规范性附录基本试验方法整车侧翻试验 附录D(规范性附录)型式核准试验需要的技术文件 附录E规范性附录等效试验方法一车身截段侧翻试验 附录F(规范性附录等效试验方法二车身截段准静态负荷试验 附录G规范性附录等效试验方法三根据测试部件进行准静态计算 26 附录H(规范性附录)等效试验方法四计算机模拟整车侧翻试验 31 附录1规范性附录)车辆质心的测量 33 附录J(规范性附录)关于上部结构的结构基本说明 36 参考文献 4G
GB17578一2013 前 言 本标准中4.1和4.2为强制性的,其余为推荐性的 本标准按照GB/T1.1一2009给出的规则起草
本标准代替GB/T17578一1998(客车上部结构强度的规定》
本标准与GB/T17578一1998相比,主要变化如下 标准的属性由推荐性改为强制性 标准名称由“客车上部结构强度的规定”改为“客车上部结构强度要求及试验方法” 标准的范围改变(1998版第1章;本版第1章); 增加和修改了术语和定义(1998版第3章;本版第3章); 增加了侧翻试验的加载质量,原来的试验质量为整车整备质量,现在修改为空载质量或者总有 效质量(1998版5.1.l;本版4.3.1) 增加了车身截段侧翻试验、车身截段准静态负荷试验,根据测试部件进行准静态计算和计算机 模拟整车侧翻试验等四种等效试验方法(见4.4及附录E一附录H); 增加了对较接客车测试方式的规定(见4.5); 增加了侧翻试验方向的规定(见4.6) 增加了同一型式的判定原则(见第5章) 修改了整车侧翻试验,作为基本试验方达(1998版第5章,本版附录C); 增加了侧翻试验台应该有足够的刚度和充分可控的转速,以保证举起车轴的同步性见 C1.1); -增加了侧翻平台起始水平面与撞击面之间高度差800 mm的误差见C.1.2); 增加了车轮挡板详细尺寸的说明[见c.1.4a)] -修改了翻转轴巾心线距离撞击平面侧壁的水平距离,由0" nmm一200mm改为不大于100 mm [[1998版5.2.2b);本版C.1.3a]; 增加了装有约束装置的座椅上的配重说明[见c.2.le]; 增加了试验时车辆悬架系统应锁止的规定[见C.2.2b]; -增加了针对钞接客车的试验说明见C.2.3); 增加了对高速摄像机位置的规定见C.3.4); 增加了侧翻试验的文件说明见C.4); -增加了型式核准试验需要的技术文件(见附录D); -增加了车辆质心的测量(见附录1); -增加了关于上部结构的结构基本说明(见附录J 本标准使用重新起草法,参照联合国欧洲经济委员会2006年2月22日颁布的第66号法规“关于 大客车上部结构强度认证的统一技术规定”o1版(EECER66Uniform technicalprescriptionsconcerning the uehicleswith 2rdltothe their approaloflargeasenger re)及其修 o" regar" strengll superstrclur 订单、勘误单的技术内容编制
本标准在附录A中列出了本标准章条编号与ECER66章条编号的对照一览表
附录B中给出了 与ECER66的技术性差异及其原因的一览表,以供参考
为便于使用,本标准还对ECER66做了以下编辑性修改 “本法规”一词改为“本标准”; a m
GB17578一2013 b 增加我国标准的前言
本标准由工业和信息化部提出
本标准由全国汽车标准化技术委员会(SAC/TC1l4)归口
本标准负责起草单位;公路车辆机械有限公司、厦门金龙联合汽车工业有限公司
本标准参加起草单位;交通运输部公路科学研究院、郑州宇通客车股份有限公司、湖南大学、国家客 车质量监督检验中心、国家汽车质量监督检验中心襄樊,东风商用车技术中心、国家机动车质量监督 检验中心(重庆,金龙联合汽车工业(苏州)有限公司、丹东黄海汽车有限责任公司、北汽福田汽车股份 有限公司北京新能源客车分公司、南京依维柯汽车有限公司、金华青年汽车制造有限公司、安徽安凯汽 车股份有限公司、西安西沃客车有限公司、汽车工程研究院股份有限公司
本标准主要起草人孙鹰、赵东旭,裴志造、段勇、聂玉明、刘建农、董晓坤、张维刚、王欣,汪祖国、 刘学琼,阮廷勇,赵伟、郭迎春,赵天红,邓玉林、李冬梅、,赵理想、陈彦夫,吴建华,吴长风,张晨罡,谢庆喜 犹海祷.W桃员.张红权.王万玉
本标准所代替标准的历次版本发布情况为 GB/T175781998
GB17578一2013 客车上部结构强度要求及试验方法 范围 本标准规定了客车上部结构强度的技术要求和试验方法
本标准适用于M类和M类中的B级、I级、级客车和专用校车,M类和M类中的其他客车可参 照执行
规范性引用文件 下列文件对于本文件的应用是必不可少的
凡是注日期的引用文件,仅注日期的版本适用于本文件
凡是不注日期的引用文件,其最新版本(包括所有的修改单)适用于本文件
GB11551乘用车正面碰撞的乘员保护 术语和定义 下列术语和定义适用于本文件
3.1 车型系列gropofvehicletpes 根据本标准满足或优于最差状态试验要求的现有的或将来推出的一组车型
3.2 最差状态worstcase 一个车型系列中,最不可能满足本标准有关上部结构强度要求的车型,确定最差状态的三个参数为 在 结构强度、基准能量和生存空间
3.3 -deck1 双层客车 double bus 至少有一部分乘客空间布置为上下两层,并且上层不设站立乘客空间的车辆
3.4 乘客区 paSSemgercOmpartment 供乘客使用的空间,不包括如酒吧、厨房或洗手间等固定设施所占有的空间
注,改写(GB/T47802000,定义3.22
3.5 乘员约束装置ocupantrestraint 可将乘客、驾驶员或车组人员固定在其座位上,并在翻车事故中通过限制佩戴者的身体移动减轻其伤 害程度的装置
3.6 垂直纵向中心面vertieallongitinalcentralplane VLCP 穿过前轴轮距中点和后轴轮距中点的垂直平面
GB17578一2013 3.7 生存空间rsidualspaee 侧翻试验过程中,乘客区、,驾驶区和分隔舱中为乘客、驾驶员和车组人员提供生存可能的剩余空间
3.8 空载质量umladenkerbhms M 车辆在可运行状态下未载运乘客、货物,但包括驾驶员(及随身行李)75kg的质量、燃料箱容量的90% 燃料的质量、工具、备用车轮、润滑剂冷却液(如果需要)的车辆质量,即整车整备质量加驾驶员75kg的 质量
3.9 约束乘员总质量 totalrestrictedoccupantmss M. 就坐于装有约束装置的座位上的乘客和车组人员的质量总和
3.10 车辆总有效质量totalefrectievehidemus M 车辆空载质量(M)与约束乘员总质量M.)的一部分的总和(见附录C). 3.11 基准能量refereneeener E 准备试验的车辆的势能,通过测量或计算翻滚过程开始时的临界状态下,车辆质心相对于撞击平面的 高度来获得
3.12 整车侧翻试验roloertesomacopletevehiele 对一辆完整的、与准备验证车型大小一致的车辆进行的、用以测试其上部结构强度的侧向滚翻试验
3.13 侧翻试验台tiltingbeneh 由侧翻平台和与之形成高度落差的混凝土撞击平面组成的装置用于对整车或车身截段进行侧翻 试验
3.14 侧翻平台tiltingplatfom 能绕水平轴线旋转以使整车或车身截段侧翻的刚性平台
3.15 车身bodywork 可运行状态下的车辆整体结构,包括构成乘客区、驾驶区,行李舱以及机械装置和部件空间的所有结 构部件 16 上部结构sperstretwre 车身的承载部分,包括增加车身强度和能量吸收能力的、在侧翻试验中保护生存空间的那些相连接的 部件和零件
GB17578一2013 3.17 隔间by 上部结构的一个结构单元,其在垂直于车辆垂直纵向中心面的两个平面之间形成一个封闭环
隔间包括车辆每侧的一个车窗(或车门)立柱以及侧围部件、一部分车顶结构和一部分地板和地板下结构
3.18 车身截段bolysection 代表用于试验的上部结构的一部分的结构单位,车身截段至少包括由代表性连接件(侧围车顶和地 板下结构等)连接的两个隔间
3.19 车身截段原型owtgimlbmltyxctiun 由两个或两个以上隔间构成的车身截段
各隔间形状、,位置关系与其在实车状态相同
隔间之间的 所有连接件也与其在实车上的状态相同
3.20 模拟车身截段artinicialbodysection 由两个或两个以上的隔间构成一个车身截段,但它们与实际车辆上的彼此间位置不同,距离也不同
这些隔间之间的连接件无需与实际车身结构上的完全相同,但在结构功能上应相当
3.21 刚性零部件rigidpart 在侧翻试验中无明显变形和吸收能量的结构性部件或零件
3.22 塑性区域plaste Z0ne Pz 车辆上部结构中一个特定的几何限定区域,动态冲击力会在该区域造成: 大面积的集中塑性变形; 原来的形状(横截面、长度或其他几何形状)严重变形 由于局部皱曲,造成稳定性下降 由于变形使动能被吸收 3.23 塑性铵链plastichinge PH 在杆状部件(单管、窗立柱等)上形成的一个简化的塑性区域
3.24 上边梁canrail 侧窗上方车身的纵向结构部件,包括与车顶结构相连的弯曲过渡部分,在侧翻试验中,上边梁(对于双 层客车,指上层的上边梁)最先与地面接触
3.25 腰梁 waistrail 侧窗下方车身的纵向结构部件,在侧翻试验中,腰梁(对于双层客车,指上层的腰梁)是在车辆横截面 部分开始变形后第二个接触到地面的部分
注:改写GB/T47802000,定义5,67
GB17578一2013 技术要求及试验方法 总体要求 4.1.1车辆的上部结构应具有足够的强度,以确保在整车侧翻试验过程中和侧翻后生存空间没有受到 侵人 1.2测试时,生存空间之外的车辆其他部件(如立柱、拉手、行李架、,灭火器等,不包括生存空间内的结 4 构部件)在测试过程中不得侵人生存空间,也不应发生结构件完全断开的现象
4.1.3生存空间内的部件(如座椅、垂直把手、隔间,小厨房和卫生间等)不应有导致乘员伤害的可能,并 且不应突出至变形结构的轮外
变形结构的轮廓线应在每个相邻的窗和/或门立柱间按顺序进行确定 两个变形的立柱之间的轮廓线,理论上应是一个连续的平面,由立柱内部各轮廓点连接的直线确定,这些 点在侧翻试验前距地板平面处于同一高度(见图1)
立柱1 立柱2 图1变形结构轮廓线的技术参数 4.2生存空间 车辆生存空间的外廓通过在车厢内建立一个垂直横截面进行确定,其边缘如图2a)和图2b)所示,将 此垂直横截面按如下方法移动穿过整个车长[见图2] S点位于外侧每个朝前或朝后的座椅(或假定的座椅位置)靠背前表面,距乘客脚下地板500m mm (不考虑发动机舱等引起的地板高度局部变化),距侧围内表面1501 对于侧向座椅,这些尺 mm
寸在座椅中心平面测量
如果车辆的左右两侧因地板布置而不对称,则S点的高度也不同;两侧生存空间的高度差应在 车辆纵向垂直中心平面内体现[见图2b]
生存空间的最后端是最后排外侧座位的S点向后200mm处的垂直平面;如果车辆后围内表面 距s点小于200mm,则取车辆后围内表面作为生存空间最后端
生存空间的最前端也是垂直平面,在车辆最前排座位(不论是乘客、车组人员或是驾驶员座位)最 大限度向前调整后,位于其点前方0. mm
GB17578一2013 如果车辆最前排和/或最后排的两侧座位不在同一横向平面上,则每侧生存空间的长度可能 不同
生存空间在乘客,车组人员和驾驶员区域内是连续的,将图2a)和图2b)所示的垂直横截面沿车 辆两侧各S点形成的直线由生存空间前端面移至后端面所形成的扫描区来确定
通过最前排 座位S点之前以及最后排座位S点之后的直线是水平的
为满足产品设计上的需要,允许试验时根据规划的车型系列中的最差状态车型,确定一个比给定 座位布置所需空间更大的生存空间
右侧 左侧 250 生存空间 员 座椅下面地板 横截面 横截面2 生存空间 S 座椅下面地板 朝内侧的双人座椅 驾驶员座椅 纵截面 图2座位客车生存空间示意图 4.3作为基本试验方法的整车侧翻试验 4.3.1将整车放置在一个可倾斜的侧翻平台上(见图3),将悬架锁止,再慢慢地倾斜到一个不稳定的平衡 位置
未安装乘员约束装置的车型,按空载质量进行测试;装有乘员约束装置的车型,按车辆总有效质量 进行测试
4.3.2侧翻试验从车辆不稳定位置开始,角速度初速度为0,围绕车轮-侧翻平台平面接触点作为翻转轴 翻转,此时的车辆特征用基准能量E表示(见附录D和图3).
GB17578一2013 单位为毫米 CG 口口口 口O口 Lc e麻谷 K平起始位置 翻转 撞击平面 图3试验过程中车辆质心位置变化及其轨迹示意图 4.3.3车辆从侧翻平台翻滚撞击在800mm落差的水平、干燥平整的混凝土撞击平面上
4.3.4作为基本试验方法采用整车进行的侧翻试验,其详细规定见附录C
4.4等效试验方法 4.4.1采用等效试验方法的基本原则是该方法应能代表附录C所规定的基本侧翻试验
如果选定的等 效试验方法不能将车辆的一些特殊特征或结构(如车顶安装空调、腰梁高度变动、车顶高度变动等)考虑在 内,应对整车进行附录C规定的侧翻试验 4.4 在满足4.4.1的前提下,可以采用下列任何一种等效的试验方法来代替整车侧翻试验: a)按照附录E,采用可代表整车的车身截段进行侧翻试验
b)按照附录F,进行车身截段准静态负荷试验 按照附录G,以部件测试结果为基础进行准静态计算
c d按照附录H,通过动态计算,用计算机模拟整车的基本侧翻试验
4.5对铵接客车进行的试验 铃接客车的每个刚性段应符合4.1的规定
车辆每个相连的刚性段可以单独进行测试,或联接进行 测试,见附录C中C.2.3和附录I中I.2.6g)的规定
4.6侧翻试验的方向 进行侧翻试验时,应朝向车辆生存空间相对更危险的一侧,由检测机构以制造商的建议为基础进行确 定,并至少考虑到以下因素: 质心的横向偏心距及它在车辆不稳定开始位置时对基准能量的影响,见附录D. a b)生存空间不对称,见4.2
车辆两侧不同的、不对称的结构特点以及隔间和内厢(如衣柜、卫生间、小厨房等)的支撑,支撑 c 较少的一侧应选为侧翻试验的方向
如不能明确判定薄弱结构侧时,优先考虑向右侧侧翻
GB17578一2013 4.7对B级客车的替代要求 对于B级客车,应满足4.1一4.4及4.6的要求,或通过试验或其他适当的方法证明车辆结构足以承 受施加在车顶上,其值相当于该车最大设计总质量的均布静载荷
同一型式的判定 5.1以已经通过试验的车型为基础车型,对其他车型进行同一型式判定时,应基于以下最差状态下的三 重原则 a)结构强度:与基础车型相比,上部结构没有改变或新的结构强度更好 基准能量;基准能量与基础车型的相同或者更小 b c 生存空间;生存空间的每一处轮廓线都在基础车型生存空间之内. 如果5.1中的三方面都符合,则可以判定为同一型式;如果都不符合,则需要重新试验;如果有1条或 5.2 2条符合,则需要进一步分析确认(比如试验、计算、结构分析等)
标准实施的过渡期要求 4.3.1及附录c附录H中关于按总有效质量进行加载的规定,自本标准实施之日起12个月后实施
GB17578一2013 附 录 A 资料性附录 本标准章条编号与CER66章条编号对照 表Al给出了本标准章条编号与BER6章条编号的对照 表A.1本标准章条编号与CER66章条编号对照 本标准章条编号 对应的ECER66章条编号 3,1,3,3,3.4 .14.6 5.15.6 6.1 5. 6.2 5.2 6.3 6.46.5 711 附件1 附件2 附录A 附录B 附录 附件5 附录D 3.2 附录E 附件6 E.1一E.3 附件6中1 E.3.1 附件6中3.1 附件6中3.1.1~3.1.5 E.3.1a)一E.3,1e) E.3.1 E.3.lg" E.3.2~E.3.5 附件6中3.2~ 3.5 E.3.5a一E.3.5b) 附件6中3.5.13.5.2 E.3.5e E.3.5d 附件6中3.5.3 E.4一E.6 附件6中4一6
GB17578一2013 表A.1(续》 本标准章条编号 对应的BCER66章条编号 附录F 附件7 F.1F.5 附件7中1 5 F.6 附件7中附录1 附录G 附件8 G.1G.4 附件8中1一4 G.5 附件8中附录1 附录H 附件g H.1 附件9 中1 H.2a)~H.2e) 附件9中2.1 2.3 H.2d H.2e H3 附件9中3 H.4 附件9中4 附件9中5 H.5 附录1 附件3 附录J 附件4
GB17578一2013 附 录 B 资料性附录 本标准与CER66技术性差异及其原因 表B1翁出了本标准与EcERe6的技术性差异及其原因 表B.1本标准与CER66的技术性差异及其原因 本标准的 技术性差异 原 因 章条编号 比BCER66的适用范围扩大;增加了对专用对专用校车,乘客数不大于16人的B级客车以及乘客数大 校车,乘客数不大于16人的B级客车以及乘于16人的B级、级和川级客车中的双层客车产品提高安全 客数大于16人的B级,I级和级客车中的性能要求 双层客车的强制要求 别除了BER中"2.了车型""2.8饺接车我国标准中已有对应的术语和定义.并且所定义的内容基本 辆”“2.9乘客区”,“2.10驾驶室” 相同,所以本标准不重复定义 将CER66中“2.15乘员总质量”改为“约束以免“Totaloccupantmas”被误解为“全体乘员”质量的总 乘员总质量" 合,这样表达更确切和便于理解 删除了ECER66中“2.17单个乘员质量” 采用GB/T12428及专用校车标准规定的乘员质量 将ECER66"车辆其他部件如立柱、拉手、行为了增加厂家对灭火器安装牢固的关注度,在侧翻试验中, 李架等)在测试过程中不得侵人生存空间”的曾有灭火器掉下来侵人到生存空间,严重影响到乘客安全 4.1.2 规定中增加灭火器也不准侵人生存空间的 规定 将CER66中“生存空间内的部件(如垂直把原因:在倾翻试验中,有一些座椅安装不牢固,掉下来侵人到 手、隔间、小厨房和卫生间等)不应突出至变生存空间,严重影响到乘客安全
为了增加厂家对座椅安装 形结构的轮廓外
”的规定中增加座椅也不应牢固的关注度,建议在括号中增加座椅
4.1.3 最后改为“生存空间内的部件(如座椅,垂直把手、隔间,小厨 突出至变形结构的轮廓外 房和卫生间等)不应有导致乘员伤害的可能,并且不应突出 至变形结构的轮廓外
4.7 增加对B级客车的替代要求 与现行强制性国家标准相协调 将CER66中车轮挡板的宽度由20mm改国内现有条件车轮挡板采用钢材,如果采用20mm厚度的 为不小于20, 钢板,无论是媒接或在其两端拉,其钢版强度不足,易出现试 mmm C.1.4 验安全事故 XCER6的2.17规定每个乘员质量68ke" 与我国客车乘员质量的规定相统 C.2.1.e 本标准采用GB/T12428及专用校车标准中 等处 规定的乘员质量 比BCER6附件6的3.1增加了准备试验的使车身截段的选取总原则更为明确和清晰 E.3.1 车身截段的“几何特性、翻转轴和质心位置应 是该整车有代表性的”规定 比CER66附件6的3.l.5增加了“顶盖高对局部特殊性进一步说明,更有利于标准的具体操作与实施 E.3.ley 度变化、 10o
GB17578一2013 表B.1(续》 本标准的 技术性差异 原 因 章条编号 比BCER66附件6的3.1增加了“应至少具对如何在车辆上选取车身截段做出了更明确的规定,便于标 有两个车身截段:一个在整车的纵向方向的准的具体操作和实施 E.3.1 质心前部,一个在整车的纵向方向的质心 后部
" BCER66附件6的3.1增加了“为了评价对如何在车辆上选取车身截段做出了更明确的规定,便于标 车辆的最差状态标准,车身截段应至少需要准的具体操作和实施 E.3.lg 包含结构强度最弱的隔间、质量最重的隔间 录 和生存空间最苛刻的隔间 CER66附件6的3.5. 2增加了",并且质对等质量配载物体进行了更为详细的说明,主要也是为了使 比 量分布应同试验车辆上的相符
主要的质量标准更为明确和清晰 包括;发动机,变速箱,悬挂系统、车桥,油箱 E.3.5b) 等底盘部件的质量和玻璃、空调、座椅、行李 架和地板等车身部件的质量
比CER66附件6的3.5增加了“等质量配对等质量配载物体的强度和刚度进行了更为详细的说明,主 载物体应具有足够的强度和刚度,能够避免要也是为了使标准更为明确和清晰 任何在倾斜和侧翻过程中会改变车身截段运 E.3,5e 动方向的变形,即它们在倾斜和侧翻过程中 无相对移动,质量分布和质心位置无重大 改变 将加载作用的“刚性梁”改为“刚性平板",并修改后才能完全模拟地面,且与原文中的附件8基于部件的 将原文中仅对“刚性梁”的长度要求扩展为对准静态计算方法中的要求一致 F.3.2a “刚性平板"的尺寸要求(包括了宽度 增加了“当需要通过多个车身截断的质心垂原文没有该限定条件,相应条款内容在全文用途不明 F.6.d) 直位移确定整车的质心垂直位移时"的内容 别除了BER66附件9的1.1中“,分析软件进行了简化
原因是目前采用的软件都是通用的商用软件 的精确鉴定,至少应包括其生产者、商业名其精度在其商业化时已做过鉴定,并已为相关领域广泛应用 H.la 称、使用版本及开发人的详细联系方式” 比ECER66附件9的1.2增加了“并说明输因为输人数据有可能是厂家通过实验测得的,也可能是通过 H.1b 人数据的来源
" 材料手册获得 比CER6附件9的么.1增加了“选取用于对如何在车辆上选取结构部位以及如何进行模型验证做出 测试的部位主要是车身骨架的两侧接头部了更明确的规定,便于标准的具体操作和实施 ,包括媒接,娜接、螺栓连接等接头
试验 位, 方法是截取接头部位,对其施加静态或动态 H.2a 载荷,使构件发生弯折或断裂等破坏,测试 头部位的变形或破坏模式,数学模型采用同 样的工况进行比较,验证部件模型的有效性 或模型中的假设
GB17578一2013 表B.1(续》 本标准的 技术性差异 原 因 章条编号 在EER66附件9中2.3后继续增加了本条增加本条有利于统一有限单元尺寸标准 关于上部结构有限元网格尺寸客车有限元 H.2d 模型中,推荐的上部结构网格尺寸不大于 20mm. 在BCER66附件9中2.3后继续增加了本条增加本条有利于统一有限单元质量标准 关于有限单元质量标准 “推荐有限单元网格质量标准为 翘曲度(Warpage)15”; 22) 长宽比(AspeetRatio)<5 H.2e' )0- 四边形内角(AngleQud) 3 l135 4三角形内角(AngleTia):25"120°; 5》雅各比(Jacobian)>0.6; 三角形单元数目不超过总单元数目 6 的5%
删除了CER66附件9中3条的“计算设备”因为下文条款中并未提到对计算设备有何要求,所以这几个 H.3 字是多余的 在ECER66附件9中3.2原文后增加了“在明确了侧翻仿真中的初始侧倾角速度以及往哪一侧倾翻的 不稳定平衡位置时,赋予车辆最大侧倾角速确定原则 度5/s进行倾翻,倾翻方向应朝向汽车相对 于生存空间更危险的一侧,至少考虑到以下 因素; H.3.2 质心的横向离心力及它对车辆在不稳定 平衡位置时的基准能量的影响 生存空间不对称的情况:汽车两侧不同 的、不对称的结构特点,以及隔间和内厢 如衣柜,卫生间,小厨房等)的支撑,支 撑较少的一侧应选作侧翻的方向
将BCER66附件9中3.7改为“地面接触点更改后使摩擦系数的确定方法更加明确符合仿真计算应趋 的摩擦系数应由物理测试得出,计算所采用于保守的原则,同时便于实际操作实施 H.3.7 的摩擦系数应当大于或等于实际测量得到的 摩擦系数
” 删除了ECER66附件9中5.1.4的“m",本条将“每毫秒"改为了“毫秒",因为“每毫秒”意味着每一毫 即由“每毫秒"改为"毫秒" 秒都要进行输出,而“毫秒"可以根据具体情况如2毫秒输出 H.5.ld -次,或者5毫秒输出一次
另外,输出值可以用图的形式 或者表格的形式进行表达,所以将“表格"改为“图表" 删除了ECER66附件9中5.l.6的“以适当修改后的结果分析中包含了仿真变形,原条款中只提到了变 方式呈现的满足4.1. .1和A.1.2规定的绘图形曲级 H.5.l或数据”改为"按4.l.1和4.l.2规定方法进 行仿真结果分析",同时增加了“可以是包含 生存空间在内的结构仿真变形” 12
GB17578一2013 表B.1(续》 本标准的 技术性差异 原 因 章条编号 H.5.2 删除了BCER66附件9中5.2的“建议" 去掉“建议"意味着应这样做 将ECE66附件9中5.3的“根据”改成了此处“如果”比“根据”更贴近实际含义
按原文(Atthe H.5.3 rquestof),也可翻译成“如果” "如果" 将ECER66附件3中“每个轴距以及每一车对试验样车的轴距、轮距的测量是试验最基本的检测项目, 轴上的轮距应根据制造商的图纸确定”改为使用测量值进行计算和提供报告数据,可以更规范地提供试 1.1.1 应对试验样车进行测量" 验数据 将CER66的(见BCER21附件5座椅R点与我国标准相协调,方便标准的使用 I.2.1、 的定义)改为按GB11551一2003的附件C C.2.le 中R点的定义 13
GB17578一2013 C 附 录 规范性附录 基本试验方法整车侧翻试验 c.1侧翻试验台 c.1.1侧翻平台应具有足够的刚度并且其转速可以控制,以保证举起车轴的同步性,当被测客车的车轴 举起时,前、后轴处平台的翻转角度差小于1" c.1.2撞击平面(见图c.1)与侧翻平台上表面的高度差为800*mm
c.1.3侧翻平台相对于撞击平面,应按下列要求布置(见图c.1). 翻转轴与撞击平面侧壁的水平距离不大于100mm a b)翻转轴与侧翻平台上表面的距离不大于100 mm
单位为毫米 最宽车轴的车轮 车轮挡板 >20 车轮挡板 R10 侧翻 >500 翻转轴 ! <100 撞击平面 图c.1侧翻试验台 C.1.4车轮挡板应置于车轮靠近翻转轴一侧的轮胎处,防止车辆倾斜时产生滑移
车轮挡板(见图C.1 的主要特征为 车轮挡板的尺寸: 高度:不大于被挡车轮轮剌最低点距台面高度的2/3; 厚度;不小于20 mm; 边缘半径:l0 mm; 长度:不小于500" mm; b)最宽车轴处的车轮挡板距翻转轴中心的水平距离不大于100 mm; e其他车轴处的车轮挡板应进行调整,以使车辆的垂直纵向中心面(VICP)平行于翻转轴
C.1.5侧翻平台应防止车辆沿其纵轴移动
C.1.6撞击平面应为水平,均匀、干燥,光滑的混凝土或其他坚硬材料构成的平面
14
GB17578一2013 C.2测试车辆的准备 准备测试的车辆无需是全部完工的"可运行”"状态
总体上讲,如果上部结构的基木特性和功能不受 C.2.1 影响,未全部完工状态所做的任何改变都可接受
测试车辆在下列方面应与其全部完工车辆相同 a)质心的位置、车辆总质量(空载质量或装有约束装置的车辆总有效质量),以及质量的分布及 位置
b)所有有助于上部结构强度的部件应安装在其原始的位置(见附录J
对上部结构强度没有帮助或太昂贵的部件(如传动系统、仪表板、司机座椅、厨房设备、卫生间 设备等),可由质量和安装方法相同的其他部件进行替代
这些“其他部件”对上部结构的强度 不能有强化作用
燃料、电池酸液及其他易燃、易爆或易腐蚀材料可由其他材料替代,但应达到C.2.la)规定的 条件
在每个装有乘员约束装置的座椅上加载,加载质量为 -每个乘员质量的50%; 将其质心置于GB11551中定义的座椅R点上方100mm和前方100mm的位置 -固定牢靠,使其测试时不会脱落
对于成人座椅,也可采用如下加载方式, 个质量为65k的仿成人人体配重物,由安全带约束,该配重物应允许安全带定向和 定位; 根据图c.2放置其质心并确定尺寸 单位为毫米 630 2A9 2 C.G 100 90" 250 注;胸宽~315mm一322mm;腰宽~290mm一310mm;臀宽~325mm一342mm
总质量为65kg 图c.2仿成人人体配重物 C.2.2测试车辆应按下列要求准备: 轮胎应按制造商指定的压力充气
a b车辆悬架系统应锁止,即车桥,弹簧和悬架系统的部件相对车身应该是固定的
地板高度取 决于车辆是空载还是总有效质量的负载状态
车辆的每个车门和可打开的车窗应关闭但不锁止
15
GB17578一2013 C.2.3较接客车的刚性段可单独测试,也可以联接测试
C.2.3.1如联接测试较接客车,车辆各刚性段间的互相固定应确保 a)在侧翻过程中不会相对移动; b) 质量分布和质心位置无明显改变; e上部结构的强度及刚度无明显改变
c.2.3.2如单独测试钦接客车车身段,单轴车身段应连接到一个支架上,并在侧翻平台从水平位置到 倾翻临界点的旋转过程中保持车身段-支架与侧翻平台的同步翻转
该支架应满足下列要求 a)应以一种方式固定在车身段上,该方式对上部结构既不具有强化作用,也不增加额外的负载; 不应产生任何变形导致改变车辆翻倒方向; b 其质量应同名义上在该刚性段进行试验但并未放置上的那些钦接零部件(如转盘及其地板、手 C 把、橡胶密封帘等)的质量相等; d)其质心应与c.2.3.2e)中所列的那些部件的共同质心的高度相同; e 应有一个翻转轴平行于车辆多轴车身段的纵向轴线,并穿过该车身段的轮胎接地点
试验程序、试验过程 c.3.1侧翻试验是一个有明显阶段性的高速、动态过程,应考虑在侧翻试验中使用必要的仪器设备
C.3.2客车在没有摇晃和不受其他外力影响的情况下侧倾直至翻倒
侧翻平台的角速度不得超过 5"/s(0.087rad/s). C.3.3 为了观察车辆内部,可用高速摄影,视频,可变形模板、电感触传感器或其他适当的方法来确定 其生存空间是否符合4.1的要求,在生存空间中的任何位置加以验证,如乘客所在的任何位置,驾驶员 和车组人员分隔舱等,其准确位置由检测机构自行确定
其中至少应在乘客舱前部和后部这两个位置 予以验证
对侧翻及车身变形过程进行外部观测及记录,包括下列内容 C.3.4 两台高速照相机 车辆前、后各一台,分别置于距离车辆前围和后围足够远的位置,以生成 a 可测量图像,避免在阴影处的广角变形,见图c.3
单位为毫米 200 图C.3外部照相机的建议视野 质心的位置及上部结构的轮廓线(见图c.4)由条带标出,以保证对图像的正确测量 b 16
GB17578一2013 参考点 质心位置及车辆轮廓线的建议标记 c.4侧翻试验的文件 c.4.1制造商应提供详细的测试车辆说明,包括 a)列出工作状态下完工车辆与测试车辆之间的差别; b)当结构零件、部件由其他部件或同等质量物体代替时,对每一方案的等效代替均应加以验证 有关质量,质量分布和安装) 测试车辆质心位置的明确说明,该位置基于在车辆准备试验时测量,或综合测量在完工车辆 上进行),并以质量代人法进行计算
C.4.2测试报告应包括所有数据(图片、记录、图纸、测量值等),并加以说明: a)测试是根据本附录进行的 b是否符合C.4.Ib)和C.4.le)的要求; e)对内部观测的单独评估; d)用于鉴别车型、测试车辆、测试本身以及对其评价的测试责任人员所需的全部数据及资料
C.4.3建议在测试报告中说明车辆在静止状态下相对撞击平面的质心位置
17
GB17578一2013 附 录 D 规范性附录 型式核准试验需要的技术文件 D.1车型或车型系列的主要鉴定数据和参数 D.1.1车型总体平面布置图纸,包括车身和内部布置及主要尺寸,装有乘员约束装置的座位应明确标 明,它们在车内的位置应标有准确的尺寸
D.1.2车辆空载质量以及相应的轴荷
D.1.3空载车辆质心的准确位置及其测量报告,应采用附录I中说明的测量和计算方法确定车辆的质 心位置
D.1.4总有效车辆质量及相应的轴荷
D.1.5总有效质量车辆质心的准确位置及其测量报告,应采用附录1中说明的测量和计算方法确定车 辆的质心位置
D.2用于评价车型系列中最差情况所需的全部数据和资料 D.2.1基准能量值(ER),它是车辆质量(M),重力加速度(g)和侧翻试验开始时车辆位于不稳定平衡 时的质心高度(h)(见图3)的乘积
(D.1 ER=M×g×h=M×[o.8十/;B王 式中: M一 空载质量M如无乘员约束装置),或总有效质量M如装有乘员约束装置单位为千克 kg): M. M十kMm,此处k=0.5,M是约束乘员总质量,单位为千克(kg); 所选定质量值(M)下的车辆的质心高度,单位为米(m) ho 从车辆质心到纵向垂直中心平面的垂直距离,单位为米(m); B -侧翻试验中转动轴到车辆纵向垂直中心平面的垂直距离,单位为米(m); 重力加速度,单位为米每二次方秒(m/、); g 车辆在开始不稳定状态时,质心到撞击平面水平面高度,单位为米(n m w D.2.2附录」要求的车型或车型系列的上部结构的图纸和详细说明
D.2.3根据4.2的要求,每个准备试验验证的车型所需的生存空间的详细图纸
D.3其他数据和资料 附录C,附录E、附录F、附录G和附录H中详细说明的,按照所选试验方法要求的更为详细的文 件、参数和数据等
D.4铵接客车的数据和资料 对于钦接客车,车型每一段的资料都应单独提供,D.1.1中提及的与整车相关的资料除外
18
GB17578一2013 附 录 E 规范性附录 等效试验方法 车身截段侧翻试验 E.1附加数据及资料 如选择该试验方法,除附录D要求的数据,资料及图纸外,应向检测机构提供下列资料: a)准备试验的车身截段的图纸 b)在车身截段侧翻试验顺利完成后,按J.4的要求,对质量分布的有效性的证明 c 准备试验的车身截段的测量质量,以及它们的质心位置同未安装乘员约束装置的空载质量的 车辆质心相同或同装有乘员约束装置的车辆总有效质量的质心相同的证明需提供测量报 告. E.2侧翻台 侧翻台应符合C.1的要求
E.3车身截段的准备 E.3.1准备试验的车身截段的数量、几何特性、翻转轴和质心位置应是该整车有代表性的,具体由下 列规定确定 所有属上部结构一部分的不同隔间构造应至少在一个车身截段内试验 a b) 每一车身截段至少应有两个隔间 e)在模拟车身截段中任何一个隔间与另一个隔间的质量比不得大于2 d 整个车辆的生存空间均应在车身截段中充分体现,包括车身构造中形成的任何特殊结合 如具有局部特殊性,如顶盖的高度变化、空调安装、燃气罐、行李架等,应在车身截段中充分体 现出整个上部结构; 应至少具有两个车身截段;一个在整车的纵向方向的质心前部,一个在整车的纵向方向的质心 后部; 为了评价车辆的最差状态标准,车身截段应至少需要包含结构强度最弱的隔间质量最重的 隔间和生存空间最苛刻的隔间
E.3.2车身截段的隔间,在外形、几何尺寸、材料及连接上,应同其在上部结构中代表的结构完全 -致
E.3.3隔间之间的连接结构应代表制造商对上部结构的说明(见J.3)并考虑下列规定 a)对于直接从实际车辆设计图上截取的车身截段原型,其基本的及附加的连接结构[见J.3a)7 应同车辆上部结构中的一致 b)在采用模拟车身截段时,连接结构在强度、刚度及特性方面应同车辆上部结构中的等效 对于在变形时可能侵占生存空间,但不属于上部结构部分的那些刚性元件,应安装在车身截 段中; d)根据特殊隔间的属性及在该隔间中的分布,连接结构的质量应含在质量分布中 E.3.4车身截段应配备人工支架,以便在侧翻台上提供与整车相同的质心位置及翻转轴
该支架应 19
GB17578一2013 符合下列要求 应以一种对车身截段中的吸能部件既不具有强化作用也不增加额外附加载荷的方式; a b 应具有足够的强度和刚度,能够阻止任何在倾斜和侧翻过程中会改变车身截段运动方向的 变形; 支架的质量应含在车身截段的质量分布及质心位置中
c E.3.5车身截段中的质量分布应根据下列事项布置: 在检查附录」的J.4.2a)和J.4.2b)中两个等式的有效性时,应考虑整个车身截段(隔间、连接 a 结构、附加结构部件、支撑 b)任何附加在隔间上的等质量配载物体[见J.4.2b)和图J.4]应以一种不起强化作用、不增加额 外附加载荷或限制变形的方式固定在车身截段上,并且质量分布应同试验车辆上的相符
主 要的质量包括:发动机、变速箱、悬挂系统、车桥、油箱等底盘部件的质量和玻璃、空调、座椅、 行李架和地板等车身部件的质量
等质量配载物体应具有足够的强度和刚度,能够避免任何在倾斜和侧翻过程中会改变车身截 段运动方向的变形,即它们在倾斜和侧翻过程中无相对移动,质量分布和质心位置无重大 改变
在乘员约束装置作为车型的一部分时,乘员质量应按附录」和附录c中的说明进行考虑
E.4试验程序 试验程序应与c.3的整车试验程序相同
E.5试验评估 E.5.1如所有车身截段通过侧翻试验且符合附录」中的公式(J.3)和公式J.4),则该车型应通过 试验
E.5.2如有一个车身截段未通过侧翻试验,则该车型不能通过试验
E.5.3如一个车身截段通过了侧翻试验,构成该车身截段的每个隔间应视为通过了侧翻试验,试验结 果可在今后的型式核准中引用,但应证明在后续试验的上部结构中它们的质量比例保持不变 E.5.4如一个车身截段未通过侧翻试验,即使生存空间仅在一个隔间中被侵占,该车身上的所有隔间 也应视为未通过侧翻试验
E.6车身截段侧翻试验的文件 试验报告应包含所需的全部数据,以证明 a)试验的车身截段的构造(尺寸、材质、质量、质心位置及制造方法); b试验是按本附录的要求进行的 是否符合4.1的要求; c d)对车身截段及其隔间的单独评估; 车型、其上部结构,试验的车身截段,试验本身,试验责任人员及其评估的一致性
2o0
GB17578一2013 附 录 ! 规范性附录 等效试验方法二车身截段准静态负荷试验 F.1需要提供的数据及资料 该试验方法将车身截段用做试验单元,每一单元至少由待评估车辆上的两个隔间组成,并同典型的 结构件连接在一起
如选择该试验方法,除附录D要求的数据及图纸外,还应向检测机构提供下列 资料 拟测试的车身截段的图纸; a b需由上部结构单独隔间吸收的能量值,以及需由拟测试车身截段吸收的能量值,见F.4.2
F.2车身截段的准备 F.2.1当设计和生产测试用的车身截段时,应符合E.3.l~E.3.3的要求
F.2.2车身截段内应装备显示生存空间轮廓的装置,该装置应位于可能产生预期变形并导致生存空 间侵人的立柱或其他结构部件处
F.3试验程序 F.3.1每个拟测试的车身截段均应通过一个刚性的底座结构牢固、安全地固定在试验台上,并且: a)固定点周围不得产生局部塑性变形 b)固定的位置与方法不得影响预期的塑性区域及绞链的形成及工作
F.3.2负荷应按下列规定施加在车身截段上 负荷应通过一个刚性平板均匀地分布于上边梁上,刚性平板的尺寸应能模拟在侧翻试验中接 a 触的地面,并能适应上边梁的几何形状
施加负荷的方向(见图F.1)应同车辆的纵向垂直中心平面成a角,可由式(F.1)求得 b 800 a=90°一arcsin --**- F.1 H 式中: 在完整车辆停放的水平面上测得的车辆上边梁高度,单位为毫米(mm)
H 21
GB17578一2013 隔间( 隔间(I 车身截段质心 G CP CP cG 图F.1作用于车身截段上的负荷 负荷应在车身截段的质心处作用于刚性平板,车身截段的质心位置由隔间及连接它们的结构 部件的质量导出
采用图F.1中的符号,车身截段的质心位置可由式(F.2)确定: m/×l F.2 lcG= 7m 式中: 车身截段中的隔间数量; 第隔间的质量,单位为千克(kg); mn 选择的取距点(图F.1中隔间(1)的中心平面至第隔间质心间的距离,单位为毫米 mm; 从相同的取矩点至车身截段质心间的距离,单位为毫米(mm) lcG 负荷应逐渐加大,以不连续的时间间隔对相应的变形加以测量,直到剩余空间被车身截段的 d) 某一部件侵人时为止,此时的变形记为最终变形(d.,
r.3.3应绘制负荷-变形曲线,相应测量要求 采样频率应能保证生成一条连续的曲线(见图F.2); a b)负荷及变形值应同步测量; e)承受负荷的上边梁的变形应在负荷作用的平面内沿作用力方向上测量; 负荷及变形的测量精度均要求不低于士1%
d F.4试验结果的评估 车身截段实际吸收的能量(E)由曲线下方的面积表示(见图F.2)
F.4.1 22
GB17578一2013 测定曲线 E 变形 推导曲线 变形d 图F.2由测量的负荷-变形曲线推导出的车身截段吸收的能量 F.4.2需要车身截段吸收的最小能量(Emm)应由式(F.3)确定 上部结构吸收的全部能量(ET)为 a F.3 E=0.75×M×g×Ah 式中: 空载质量M.如无乘员约束装置),或总有效质量M.如装有乘员约束装置),单位为千克 M一 kg); 重力加速度,单位为米每二次方秒(m/s); g -侧翻试验中车辆质心的垂直移动量,单位为米(m);按F.6确定
h b)按总质量在上部结构各隔间的分配比例计算各隔间吸收的能量
m F.4 E=E× M 式中 E -第i隔间所吸收的能量,单位焦J) -第i隔间的质量,单位为千克(kg);按J.4.1确定
mn 需由车身截段吸收的最小能量(E)为车身截段包括的隔间的能量总和 c En= F.5 习 F.4.3如满足下面条件,则车身截段通过了负荷试验 E >E 在这种情况下,组成车身截段的所有隔间均视为通过了准静态负荷试验,其他车型如采用与该车身 23
GB17578一2013 截段相同的隔间,这些试验结果可直接引用,但需提供各隔间在其他车型的上部结构中不承载更大质量 的证明
F.4.4如出现下列情况,则车身截段未通过负荷试验 EE 在这种情况下,即使生存空间仅在一个隔间内发生侵占,组成车身截段的所有隔间均视为未通过负 荷试验
F.4.5如要求的车身截段全部通过了负荷试验,则该车型上部结构强度符合本标准规定
F.5车身截段准静态负荷试验的文件 试验报告应包含E.6要求的内容
.6侧翻过程中车辆质心垂直位移的确定 侧翻试验的质心垂直位移()可按下列所述的绘图法确定: 当车辆随侧翻试验台的倾斜角度正好处于车辆发生侧翻的临界位置时,采用车辆横截面的比 例图确定此时质心(位置1)相对于撞击平面的初始高度(h)(见图F.3); 假定车辆横截面围车轮挡板的上边缘旋转(图F.3点A),将车辆横截面图旋转至其上边梁刚 好触及撞击平面位置(图F.4),以确定此时质心(位置2)相对于撞击平面的高度(h,). O 图F.3车辆质心的初始高度 24
GB17578一2013 VLCp 图F.4车辆质心垂直位移的确定 质心的垂直位移量)由式(F.6)确定 F.6) 4h=h一h 当需要通过多个车身截段的质心垂直位移确定整车的质心垂直位移时,如果每个车体截段具 D 有不同的质心垂直位移(h),则每个车体截段的质心垂直位移量h,)均应分别确定,整车 质心的垂直位移量h)由式(F.7)确定: = F.7 n 式中 -第i车身截段的质心垂直位移,单位为毫米(mm); 被测试的车身截段的数量
25
GB17578一2013 附录G 规范性附录) 等效试验方法三根据测试部件进行准静态计算 G.1附加的数据及资料 G.1.1如制造商选择该试验方式,除附录D要求的数据及图纸外,还应向检测机构提供下列附加 资料
G.1.2塑性区域(PZ)及塑性钞链(PH)在上部结构中的位置; 所有单独的塑性区域及塑性钦链应按其几何尺寸的确定位置在上部结构的图纸中单独标明 a 见图G.1); b)塑性区域及塑性钦链之间的结构部件在计算中可作为刚性或弹性件处理,它们的长度应按其 在车辆上的实际尺寸确定
G.1.3塑性区域及塑性较链的技术参数; a)塑性区域及塑性钞链所在的结构部件的横截面几何尺寸; b 作用于每一塑性区域及塑性铵链上的负荷的类型及方向; 按G.5中说明的每一塑性区域及塑性蛟链的负荷-变形曲线,可采用塑性区域及塑性铵链的静 态或动态特征进行计算,但在同一计算中不得混合使用静态和动态特征
PH
R PHH PH 图G..1隔间上塑性铵链的几何参数 G.1.4需由上部结构吸收的总能量(E)应采用式(G.2)进行计算
G.1.5计算中采用的运算法则和电脑程序的简要技术说明
26
客车上部结构强度要求及试验方法GB17578-2013
客车是人们日常生活中不可或缺的交通工具之一,其安全性和舒适性一直备受关注。而客车上部结构强度的要求和试验方法则直接关系到乘客的安全,因此十分重要。
根据GB17578-2013标准,客车上部结构应满足以下强度要求:
- 客车上部结构应满足正常使用条件下的静态载荷,即空载、额定荷载、满载状态下的悬架位移量、车身侧倾角等条件下,车辆承受的最大侧向加速度不应超过0.8g。
- 客车上部结构在发生碰撞时,应能有效地吸收和分散冲击力,保护乘客免受伤害。
- 客车上部结构应具有防腐蚀、防燃、隔音等特性,以确保乘客的舒适和安全。
同时,根据该标准,对客车上部结构的试验方法也有明确规定:
- 静载试验:按照额定荷载或者满载条件下进行,测试车辆所承受的最大侧向加速度是否符合标准要求。
- 碰撞试验:采用正面、侧面碰撞试验来检测车身抗碰撞能力,并通过脱离试验来检测底盘与上部结构之间连接的可靠性。
- 环境试验:模拟不同环境条件下的作用,如高温、低温、潮湿、震动等,以验证车身结构的耐久性。
综上所述,客车上部结构强度的要求及试验方法是确保乘客安全的重要因素之一,相关规定应严格遵守,以提高客车的安全性和舒适性。
客车上部结构强度要求及试验方法的相关资料
- 客车用燃料电池发电系统测试方法GB/T28183-2011
- 如何使用GB/T28370-2012标准检测长途客车内空气质量
- 客车上部结构强度要求及试验方法GB17578-2013
- 客车用安全标志和信息符号GB30678-2014
- 了解载货汽车和客车轮辋规格系列GB/T31961-2015
- 客车上部结构强度要求及试验方法GB17578-2013
- 专用校车学生座椅系统及其车辆固定件的强度GB24406-2012
- 客车上部结构强度要求及试验方法GB17578-2013
- 三轮汽车和低速货车座椅系统强度要求及试验方法GB/T19126-2015
- 农林拖拉机和机械安全带第2部分:固定装置强度要求GB/T33641.2-2017
- 大型游艇甲板起重机和登船梯强度要求GB/T35354-2017
- 折叠翻靠床安全要求和试验方法第2部分:试验方法GB/T26172.2-2010
- 液压管接头试验方法GB/T26143-2010
- GB/T24218.3-2010断裂强力和断裂伸长率的测定(条样法)
- GB/T24218.14-2010包覆材料返湿量的测定
- 纺织品非织造布试验方法第13部分:液体多次穿透时间的测定GB/T24218.13-2010