GB/T14173-2008
水利水电工程钢闸门制造、安装及验收规范
Specificationformanufacture,installationandacceptanceofsteelgateinhydraulicandhydroelectricengineering
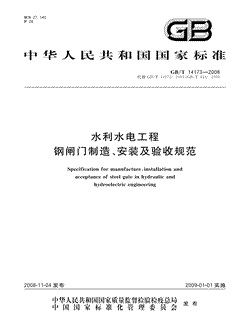
- 中国标准分类号(CCS)P26
- 国际标准分类号(ICS)27.140
- 实施日期2009-01-01
- 文件格式PDF
- 文本页数46页
- 文件大小1.44M
以图片形式预览水利水电工程钢闸门制造、安装及验收规范
水利水电工程钢闸门制造、安装及验收规范
国家标准 GB/14173一2008 代替GB/T14173一 -1993,GB/T814一1989 水利水电工程 钢闸门制造、安装及验收规范 Specifieationformanufaeture,installationand acceptanceofsteelgateinhydraulicand hydroeleetrieenghneering 2008-11-04发布 2009-01-01实施 国家质量监督检验检疫总局 发布 国家标准化管蹬委员会国家标准
GB/T14173一2008 目 次 前言 范围 规范性引用文件 -般规定 技术资料 材料 基准点和测量工具 标志、包装及运输 3 焊接 焊接工艺规程及焊接工艺评定 焊工资格 焊接的基本规定 焊缝检验 焊缝缺欠返工 焊后消除应力处理 *+ 螺栓连接 螺孔制备 螺栓制备 螺栓紧固 防腐蚀 防腐蚀的基本规定 表面预处理 表面防护 6. 表面防腐蚀的检测 闸门制造 零件和单个构件制造 铸钢件和锻件 3 7.3 埋件制造 5 平面闸门门体制造 弧形闸门门体制造 23 人字闸门门体制造 22 闸门安装 8 22 埋件安装 8 20 平面闸门门体安装 2s 弧形闸门门体安装 8 30 人字闸门门体安装 32 闸门试验 32 拦污栅制造和安装
GB/T14173一2008 32 9.1拦污栅制造 32 9.2拦污栅安装 33 验收 l0 0.1总则 33 0.2闸门制造验收 33 0.3闸门安装验收 3 35 附录A资料性附录各种工艺评定方法的应用说明 35 A.1应用说明 35 A?焊拨工艺评定试验 A.基于媒接经验的工艺评定 35 35 A.4基于预生产焊接试验的工艺评定 36 附录B规范性附录高强度螺栓抗滑移系数和紧固力矩检测 36 B.1高强度螺栓摩擦面抗滑移系数检测规定 36 B.2高强度螺栓紧固力矩检测规定 37 附录C资料性附录支承滑道常用材料 37 增强(填充)四氟板材 C.2钢背铜塑复合材料 37 自润滑铜合金支承材料 37 工程塑料合金材料 38 附录D(资料性附录)橡胶水封的物理力学性能 39 图!组合焊缝的焊脚 图2止水板与主轨轨面的相互关系 14 15 图3止水板与反轨工作面的相互关系 图4护角与主轨(反轨)的相互关系 15 图5支臂示意图 2 图 6 铲座钢梁的倾斜 28 图7底枢装置 30 图 顶枢装置 8 3 表1焊缝外观质量要求 表?焊缝无损检测比例 焊后热处理时的保温时间 3 表 表!螺栓与螺栓孔的做限偏差 表》螺栓的选用 丧 零件的极限偏差 表7,零件形位公差 1o 表 构件尺寸极限偏差和形位公差 8 l 表 13 9 锻件的检验项目 13 表10具有止水要求的埋件公差 14 表ll没有止水要求的埋件公差 14 表12平面链轮闸门主轨凹槽和承压面公差 15 表13平面闸门门叶的公差或极限偏差
GB/T14173一2008 1 表14滑道支承夹槽底面与门叶表面的间隙 18 表15滚轮或滑道支承组装的公差或极限偏差 19 表16弧形闸门门叶的公差或极限偏差 21 表17形状公差 21 表18支臂开口处弦长极限偏差 22 表19弧形闸门组装的公差或极限偏差 2: 表20 25 21 表 2 表22 表 21 23弧形闸门埋件安装的公差或极限偏差 表24弧形闸门较座安装公差或极限偏差 26 表 25 32 表 26 32 表27活动式拦污棚埋件安装的极限偏差 33 表 A.l 评定方法 35 表B.1高强度螺栓规定的紧固力及紧固力矩表 36 37 表C.1 增强C填充)四氧材料的物理力学性能 表c.2钢背铜塑复合材料的物理力学性能 37 表 自润滑铜合金力学性能 C.3 38 表c.4工程塑料合金材料的物理力学性能 38 表D.1橡胶水封的物理力学性能 39 业
GB/T14173一2008 前 言 本标准代替GB/T14173一1993《平面钢闸门技术条件》和GB/T814一1989《弧形闸门通用技术 条件》,并参考合并编人了SL37一1991《偏心钞弧形闸门技术条件》,SL/T57一1993(《平面链轮闸门技 术条件》及DL50182004《水电水利工程钢闸门制造安装及验收规范》相关内容
本标准与原标准相比主要有如下变化 适用范围扩展应用到所有水利水电工程及其他工程钢闸门的制造、安装及验收; -增加了钢板表面质量及其表面缺欠的修正要求; 要求焊接工艺评定按GB/T19866及GB/T19868.4、GB/T19869.1的规定进行; 对于使用新材料、水头大于等于80m或结构复杂的闸门,提出宜增加无损检测检查比例的 要求; -增加了媒缝表面无损检测验收等级的规定; 增加了当机加工后需要保持尺寸公差时应采取消除应力处理的要求; 增加了当结构尺寸有稳定要求时宜采用整体消除应力热处理或振动时效处理而不宜采用局部 热处理的规定; 对组合想缝的质量标准进行了修改 对铸钢件和锻件进行了质量等级分类 增加了一、二类铸钢件表面无损检测检查的要求; 规定了锻件的制造和验收技术要求应符合JB/T6397或JB/T6396的要求; 增加了一类锻件的主轨表面无损检测检查的要求; 规定充压式、压紧式水封弧形闸门门叶面板加工后,面板板厚局部允许偏差应不小于图样 尺寸; 增加有关工程塑料合金材料的要求
本标准附录B为规范性附录,附录A、附录C,附录D为资料性附录
本标准由水利部提出
本标准由水利部综合事业局负责归口
本标准起草单位;水利部水工金属结构质量检验测试中心、二滩水电开发有限责任公司、江河机电 装备工程有限公司
本标准主要起草人:张亚军、铁汉、毋新房、王兆成、张小阳、王安、梅燕、郭云峰、李义茂、李文明、 熊剑鸣、朱国纲、盂庆奎、何配排、李世刚、王翠萍、胡木生
本标准由水利部水工金属结构质量检验测试中心负责解释
本标准所代替标准的历次版本发布情况为 -GB/T814一1989 -GB/T141731993
GB/T14173一2008 水利水电工程 钢闸门制造、安装及验收规范 范围 本标准规定了水利水电工程钢闸门(包括拦污栅,下同)制造、安装及验收的技术要求 本标准适用于水利水电工程和其他工程钢闸门的制造、安装及验收
规范性引用文件 下列文件中的条款通过本标准的引用而成为本标准的条款
凡是注日期的引用文件,其随后所有 的修改单(不包括勘误的内容)或修订版均不适用于本标准,然而,鼓励根据本标准达成协议的各方研究 是否可使用这些文件的最新版本
凡是不注日期的引用文件,其最新版本适用于本标准
GB/T228金属材料室温拉伸试验方法 GB/T229金属材料夏比摆锤冲击试验方法 GB/T232金属材料弯曲试验方法 GB/T699优质碳素结构钢 GB/T700碳索结构钢 GB/T983不锈钢焊条 GB/T985气、手工电弧焊及气体保护焊焊缝坡口的基本形式与尺寸 GB/T986埋狐焊焊缝坡口的基本形式和尺寸 GB/T1184一1999形状和位置公差未注公差值 GB/T1231钢结构用高强度大六角头螺栓、大六角螺母、垫圈技术条件 GB/T1591低合金高强度结构钢 1998极限与配合基础 第2部分;公差、偏差和配合的基本规定 .2 GB/T1800. 极限与配合公差带和配合的选择 GB 1801 1999 厚钢板超声波检验方法 GB 2970 钢及钢产品力学性能试验取样位置及试样制备 GB 2975 GB/T3077 合金结构钢 GB/T3098. 紧固件机械性能螺栓、螺钉和螺柱 GB/T3098. 紧固件机械性能螺母粗牙螺纹 紧固件机械性能不锈钢螺栓、螺钉和螺柱 GB/T3098.15紧固件机械性能不锈钢螺母 GB/T3323金属熔化焊焊接接头射线照相 GB/T3398(所有部分)塑料硬度测定 GB/T4237 不锈钢热轧钢板和钢带 GB/T4842 敏 GB/T5117 碳钢焊条 G;B/T5118低合金钢焊条 GB/T5216保证淬透性结构钢 GB/T5293 埋弧焊用碳钢焊丝和焊剂
GB/T14173一2008 GB/T5616无损检测应用导则 GB/T5680高锰钢铸件 GB/T6402钢锻件超声检测方法 GB/T6414 铸件尺寸公差与机械加工余量 GB/T6654 压力容器用钢板 GB/T7233铸钢件超声探伤及质量评级方法 7659焊接结构用碳素钢铸件 GB/T8110 气体保护电弧焊用碳钢、低合金钢焊丝 8165不锈钢复合钢板和钢带 GB/T8923 1988涂装前钢材表面锈蚀等级和除锈等级 9443 铸钢件渗透检测 9444 铸钢件磁粉检测 人员资格鉴定与认证 GB 9445 无损检测 GB" 11345 制焊缝手工超声波探伤方法和探衡结果分级 一般工用祷造谈制件 GB 1352 GB 12470埋弧焊用低合金钢焊丝和焊剂 GB 13819 铜合金铸件 -般工程与结构用低合金铸钢件 14408 GB GB 14977热轧钢板表面质量的一般要求 GB 16253 承压钢铸件 埋弧焊用不锈钢焊丝和焊剂 GB 17854 焊接工艺规程及评定的一般原则 GB 19866 电弧焊焊接工艺规程 GB 19867. 基于焊接经验的工艺评定 GB/T19868. 2 GB /T 基于预生产焊接试验的工艺评定 19868. 钢、镍及镍合金的焊接工艺评定试验 GB/T19869. HG/T2537焊接用二氧化碳气体 JB/T4730. 承压设备无损检测第4部分;磁粉检测 JB/T4730.5承压设备无损检测第5部分;渗透检测 JB/T5926振动时效效果评定方法 JB/T6061无损检测焊缝磁粉检测及验收等级 JB/T6062无损检测焊缝渗透检测及验收等级 JB/T6396大型合金结构钢锻件技术条件 JB/T6397大型碳素结构钢锻件技术条件 JG82钢结构高强度螺栓连接的设计施工及验收规程 SL35水工金属结构焊工考核规则 SL36水工金属结构焊接通用技术条件 SL105水工金属结构防腐蚀规范 -般规定 3.1技术资料 3.1.1闸门及埋件制造前,应具备下列资料 设计图样,施工图样和技术文件,设计图样包括闸门及埋件总图,施工图样包括闸门及埋件装 a
GB/T14173一2008 配图及零件图
D) 主要钢材、焊材及防腐蚀材料质量证书
c 标准件和非标准协作件质量证书
3.1.2闸门及埋件安装前应具备下列资料 a)设计图样,施工图样和技术文件
D 闸门出厂合格证
c)闸门制造验收资料和出厂检验资料
d)闸门制造竣工图或能反映闸门出厂时实际结构尺寸的图样
发货清单、到货验收文件及装配编号图
e' n 安装用控制点位置图
3.1.3闸门及埋件制造与安装应按图样和有关技术文件进行,如有修改应有设计修改通知书 3.2材料 闸门使用的钢材应符合图样规定,其性能应分别符合 GB/T699、GB/T700、GB/T1591、 标号不请或 GB/T3077、,GB/T4237,GB/T6654,GB/T8165等标准的规定,并应具有出厂质量证书
对材质有疑问时应予复验,复验符合有关标准后方可使用
钢板性能试验取样位置及试样制备应符合GB/T2975的规定,试验方法应符合GB/T228 3.2.2 GB/T229、GB/T232的规定
钢板表面质量及其表面缺欠的修正应符合GB/T14977的规定
钢板如需超声波检测,则应按 2970标准执行,超声波检测的位置、比例及合格标准由供需双方确定
焊接材料(焊条、焊丝、焊剂、保护气体)应具有出厂质量证书
标号不清或对材质有疑问时应予 3 复验复验合格方可使用
焊条的化学成分、力学性能和扩散氢含量等各项指标应符合GB/T5117 GB/T5118或GB/T983等标准的规定;埋弧媒用媒丝和煤剂应符合GB/T5293.,GB/T12470或 (GB/T17854等标准的规定;气体保护焊用焊丝应符合GB/T8110等标准的规定;气体保护电弧炽用二 氧化碳气体应符合HG/T2537优等品的规定;氨气应符合GB/T4842的规定
3.3基准点和测量工具 3.3.1闸门出厂检验,制造验收和安装验收所用的量具和仪器,应经计量检定机构检定合格并在有效 期内,主要量具和仪器的精度应达到下述规定 a)钢卷尺精度应不低于一级; b 经纬仪的精度应不低于D
级 水准仪的精度应不低于DS级 c 全站仪的测角精度应不低于1",测距精度应不低于1mm十2×D×10-
mm,D为测量距离、 d 单位mm
3.3.2对于闸门制造,安装过程中所用的量具和仪器,使用单位应自行定期检定或送计量检定机构检 定,并提供修正值,在使用时根据修正值进行数据修正
3 .3.3用于测量高程和安装轴线的基准点及安装用的控制点均应准确、牢固、明显和便于使用
3.4标志、包装及运输 33 .4.1闸门应有标志,标志内容应包括 -制造厂名; -产品名称; 生产许可证标志及编号; -产品型号或主要技术参数; 制造日期 闸门重心位置及总重量
GB/T14173一2008 3.4.2闸门门叶应分节编号,加工面应有可靠保护;埋件可成捆包装并用钢架拴紧;附件应成套装箱
3.4.3闸门起吊时应防止构件损坏或变形;装车时应摆放平稳、位置适中,加固可靠;超长、超宽件运输 应悬挂危险警示牌,注意保护道路、桥梁,通信、电力等设施安全 焊接 焊接工艺规程及焊接工艺评定 闸门在制造与安装前,施焊单位应根据结构特点及其质量要求制定焊接工艺规程
电弧焊焊接 工艺规程的主要内容和具体格式见GB/T19867.1
4.1.2未经评定过的焊接工艺规程应按GB/T19866的规定进行焊接工艺评定
有关各种焊接工艺 评定方法的应用说明参见附录A
、二类焊缝应通过焊接工艺评定试验进行焊接工艺的评定,进行评定试验的方法按照 GB/T19869.1的规定进行
三类焊缝的工艺评定可参照以前的焊接经验来进行工艺评定,但应有文件证实其以前曾焊制了 满足要求并相同的接头和材料种类
评定方法按GB/T19868.2的规定进行
尺寸,拘束度、热传导效应等)对焊缝性能影响较大,采用标准 4.1.5当实际焊接接头的某些条件(如: 试件无法有效地验证焊接工艺规程的正确性时,应使用预生产焊接试验进行评定
评定的方法按照 GB/T19868.4的规定进行
4.1.
焊接工艺评定报告应包括所有变量(主要变量和非主要变量)以及相关标准规定的评定范围 4.1.7施焊单位应以工艺评定报告为依据,形成用于生产的媒接工艺规程 4.2焊工资格 4.2.1从事水利水电工程闸门一,二类焊缝焊接的焊工应持有按照sL35考试合格,由水利水电行业 主管部门签发的水工金属结构煤工考试合格证书
从事其他行业工程闸门一,二类焊缝焊接的煤工应 符合国家或相应行业有关焊工资质的规定
4.2.2焊工焊接的钢材种类,焊接材料、焊接方法和焊接位置等均应与焊工本人考试合格的项目相符
4. 3 焊接的基本规定 4. 3.1焊缝按其重要性分为三类,合同文件及图样另有规定者,按合同文件及图样的规定
-类焊缝 a 闸门主梁、边梁、臂柱的腹板及翼缘板的对接缝
1) 2 闸门及拦污栅吊耳板、拉杆的对接焊缝
3 闸门主梁腹板与边梁腹板连接的组合焊缝(对接焊缝与角焊缝)或角焊缝;主梁翼缘板与 边梁翼缘板连接的对接焊缝
4)转向吊杆的组合焊缝或角焊缝
D 人字闸门端柱隔板与主梁腹板及端板的组合焊缝
b 二类焊缝 1 闸门面板的对接焊缝
拦污栅主梁和边梁的腹板及翼缘板的对接焊缝
2 3) 闸门主梁、边梁、支臂的翼缘板与腹板的组合焊缝或角焊缝
闸门吊耳板与门叶的组合焊缝或角焊缝
4 5 主梁、边梁与门叶面板相连接的组合焊缝或角焊缝
6 支臂与连接板的组合焊缝或角焊缝
三类焊缝: 不属于一,二类焊缝的其他焊缝都为三类焊缝,设计有特殊要求者按设计要求 4.3.2水利水电工程闸门的焊接应符合SL36的有关规定;其他行业工程闸门的焊接应符合国家或相
GB/T14173一2008 应行业焊接规程的有关规定
4.3.3闸门上的焊缝除图样上有特殊标示外,均为接头全长连续的焊缝
4.4焊缝检验 4.4.1所有焊缝均应进行外观检查,外观质量应符合表1的规定
表1焊缝外观质量要求 单位为毫米 允许缺欠尺寸 目 序号 项 类焊缝 二类焊缝 三三类焊缝 裂纹 不允许 炽瘤 不允许 飞溅 清除干净 电弧擦伤 不允许 不加垫板单面焊允许 <0.1谷且<2每1001 mm 值0
5且1.5,每 未焊透 不允许 焊缝长度内缺欠总长度 100mm焊缝长度内缺 25 欠总长度<25 表面夹渣 不允许 深0.2,长<0.5且一20 咬边 深<0.5 深<1.5 每米范围内允许3个每米范围内允许5个 表面气孔 不允许 .0气孔,且间距>20nmm.5气孔,且间距>20mm 媒条电弧媒 在焊缝任意300mm长度内<3 媒缝边缘 气体保护焊 直线度 在媒缝任意300mm长度内< 埋弧炸 10 未炽满 不允许 焊条电弧焊 平焊03. 焊缝 气体保护焊 立焊、横焊、仰焊04 11 余高 03 埋弧 对接 媒缝 焊条电弧焊 盖过每侧坡口宽度2~4,且平滑过渡 气体保护娜 焊缝 12 宽度 开坡口时盖过每侧坡口宽度2~7,且平滑过渡; 埋弧 不开坡口时盖过每侧坡口宽度414,且平滑过渡 s0.3十0.05且<1, 0.3十0.05且2,每 角烬缝厚度不足 13 不允许 每100mm焊缝长度内100mm焊缝长度内缺欠总 (按焊缝计算厚度) 缺欠总长度<25 长度<25 角 焊条电弧焊 焊 -3.K12.04 K<12;0~ 气体保护焊 14 缝 炽脚 K 埋弧 <12;04,K>12:05 媒脚不对称 5 差值<1+0.1K 注l; 板厚,K焊脚 注2:在角焊缝检测时,凹形角焊缝以检测角焊缝厚度不足为主,凸形角焊缝以检测角焊缝焊脚为主
GB/T14173一2008 4.4.2无损检测人员应按照GB/T9445的要求进行培训和资格鉴定合格,取得全国通用资格证书并 通过相关行业部门的资格认可
各级无损检测人员应按照GB/T5616的原则和程序开展与其资格证 书准许项目相同的检测工作,质量评定和检测报告审核应由2级及2级以上的无损检测人员担任
4.4.3焊缝内部质量检测可选用射线或超声波检测,焊缝表面检测可选用渗透检测或磁粉检测
当无 损检测人员应用其中一种检测方法,不能对所发现的缺欠进行定性和定量时,应采用其他无损检测方法 进行复查
4.4.4同一焊缝部位或同一焊接缺欠,使用两种及两种以上的无损检测方法进行检测时,按各自标准 分别评定合格时为合格
4.4.5焊缝无损检测长度占全长的百分比应不少于表2规定,合同、图样或设计文件另有规定时,按合 同、图样和设计文件的规定执行
表2焊缝无损检测比例 射线检测/% 超声波检测/% 板厚/mm 钢种 -类 二类 -类 二类 10 38 15 50 30 碳素钢 10 50 38 20 100 10 30 <32 20 50 低合金钢 10 50 >32 25 100 局部无损检测部位应包括全部丁字焊缝及每个煤工所焊焊缝的一部分
4.4.6 使用新材料、水头大于或等于80m或结构复杂的闸门,宜增加无损检测检查比例,增加的比例 4.4.7 按合同文件或图样的规定
4.4.8焊缝局部无损检测发现存在裂纹,未熔合或不允许的未焊透等危害性缺欠时,应对该条焊缝进 行全部检测
如发现存在其他不符合质量要求的缺欠,应在其延伸方向或可疑部位作补充检测,补充检 测的长度应大于等于200mm,经补充检测仍发现存在不符合质量要求的缺欠,应对该整条焊缝进行全 部检测
4.4.9射线检测按GB/T3323进行,射线透照技术等级为B级,一类焊缝不低于I级合格,二类焊缝" 不低于级合格
超声波检测按GB/T11345进行,检验等级为B级,一类焊缝I级为合格,二类焊缝 不低于I级为合格
焊缝表面无损检测按JB/T6061或JB/T6062进行,验收等级为2级
4.4.10对有延迟裂纹倾向的钢材,无损检测应在焊接完成24h后进行
4.4.11T形接头的对接和角接的组合焊缝,合同文件和图样上无特殊规定时,一类焊缝的组合焊缝应 为完全焊透焊缝,翼板上的焊脚应大于1/4腹板板厚,见图la),b);合同文件和图样未明确规定时,二 类焊缝的组合焊缝可为部分焊透焊缝,未焊透深度不应大于腹板板厚的25%,且不大于4nmm,双面坡 口时其翼板方向焊脚应大于6mm,见图le),单面坡口时其翼板方向焊脚应大于8mm,见图1d
d K 烬脚; 板厚
图1组合焊缝的焊脚
GB/T14173一2008 4.4.12翼板厚度大于或等于36mm时,一、二类焊缝中的角焊缝,应进行焊缝表面无损检测,检测比 例宜不小于10%
4.5焊缝缺欠返工 焊缝发现有超标缺欠时,应进行返工
返工的要求应符合SL36及国家有关焊接标准的规定
4.6焊后消除应力处理 4.6.1闸门、埋件的合同文件及图样有要求时,应进行消除应力处理
4.6.2有稳定结构尺寸要求的部件,宜采取整体消除应力热处理或振动时效处理,不宜采用局部热 处理 4.6.3消除应力热处理的温度应按合同文件及图样的规定,如无规定时,经淬火十回火处理的钢,热处 C 理加热温度应低于母材供货状态的回火温度50C且不大于590C,其他钢的加热温度为600 650 4.6. 消除应力热处理应符合以下要求: 焊件人炉时,炉内温度应低于300C
b 炉温升至300C后,加热速度不应超过(220×免C/h,且小于等于220C/h
式中o为 最大板厚,单位为毫米(mm). 炉温达到热处理温度后,应根据板厚进行保温,保温时间不应少于表3的规定
对有稳定结构 尺寸要求的部件进行消应处理时,保温时间应根据最厚部件的厚度确定
保温期间,各部温差 不得超过50C 表3焊后热处理时的保温时间 板厚/mm 保温时间/h 0.25 >650 0.04× 50 >50 2+0.25× 25 1C/h,且小于等于260C/h
式中 4.6.5在300C以上进行冷却时,冷却速度不应超过(260X om为最大板厚,单位为毫米(mm)
炉温降至300C以下后,可在静止的空气中冷却 4.6.6有再热裂纹倾向的低合金钢焊接接头和高强钢焊件,不宜采用焊后热处理,宜采用振动时效法 进行消除应力处理
4.6.7热处理后,应提供热处理曲线及消除应力的效果及硬度测定记录
4.6.8振动时效法进行消除应力处理后,应按JB/T5926的规定进行消除应力效果的评价,并提供消 除应力的效果报告
螺栓连接 螺孔制备 螺栓孔应配钻,或用钻模钻孔,螺栓孔应具有GB/"T1800.2一1998中ITI4级精度要求 为防止构件钻孔时出现位移应先将最远处孔制作销钉孔,销钉孔数量应不低于全部孔数的 0%,且不少于2个
打人销钉后再钻制其他螺孔
销钉直径与孔径应符合GB/T1801-1999中H7) 6的配合要求 5.1.3构件配钻后,螺栓与螺栓孔的极限偏差应符合表4的规定
GB/T14173一2008 表4螺栓与螺栓孔的极限偏差 单位为毫米 公称直径及极限偏差 号 名 序 称 27 公称直径 12 20 22 24 30 16 螺栓 士0.52 极限偏差 士0.43 士0.84 直径 13,5 17.5 22 24 26 30 33 螺栓孔 +0.43 +0.52 +0.84 极限偏差 中心线倾斜度 应不大于板厚的3%,且单层板不得大于2.0,多层板叠组合不得大于3.0 5.1.4使用高强度螺栓连接的构件表面,应保证抗滑移系数值达到有关标准要求
闸门制作和安装单 位应按附录B的规定分别进行高强度螺栓连接摩擦面的抗滑移系数试验和复验
抗滑移系数试验用 的试件应由制造厂加工,试件与所代表的钢结构构件应为同一材质、同批制作、采用同一摩擦面处理工 艺和具有相同的表面状态,并应用同批同一性能等级的高强度螺栓连接副在同一环境条件下存放
现 场处理的构件摩擦面应单独进行摩擦面抗滑移系数试验,其结果应符合设计要求
螺栓制备 5.2 普通螺栓与高强度螺栓根据连接件工作特性、布置条件按不同强度等级选用.并应符合表5的 规定,其螺母及垫圈按相应的强度级别组合选用
普通螺栓、螺母应符合GB/T3098.1,GB/T3098.2 的要求,不锈钢螺栓、螺母应符合GB/T3098.6,GB/T3098.15的要求
螺栓、螺母和垫圈都应妥善保 管,防止锈蚀和丝扣损伤
表5螺栓的选用 螺栓的强度级别 螺母的强度级别 螺栓与螺母按强度级别组合 级别 MPa 推荐材料牌号 级别 MPa 推荐材料牌号 螺母 螺栓 4.6 15、,Q235 400 400 10Q215 !.6、4.8 0,Q215 4.8 5.6 25、35 500 500 10,Q215 5.6,5,8 5,8 15.Q235 35 6,8 600 600 15.Q235 6.8 35 8.8 800 35、45、40B 800 8H 8.8S 20MnTiB,35VB 10 *10.9 l000 1000 35,45、15MnVB 10H 10.9S 注;“关”"为高强度螺栓
5.2.2高强度大六角螺栓应符合GB/T1231的规定,高强度连接副应注明规格,分箱保管,使用前严" 禁任意开箱
5.2.3高强度大六角螺栓连接副在施工前按出厂批号复验扭矩系数,试验方法与结果应符合GB/T 1231的规定
5.3螺栓紧固 5.3.1钢结构连接用的普通螺栓的最终合适紧度宜为螺栓拧断力矩的50%60%,并应使所有螺栓 拧紧力矩保持均匀
5 3.2高强度螺栓连接副的施拧顺序和初拧复拧扭矩应符合设计要求和JGJ82的规定
5 3. 初拧力矩宜为终拧施工力矩值的50%,终拧到规定力矩
拧紧螺栓应从中部开始对称向两端 3 进行 不同等级的高强度螺栓规定的施工预紧力、施工扭矩及检查扭矩的计算公式可参照第B.2章
GB/T14173一2008 5.3.5检验所用的扭矩扳手应在使用前进行标定,其扭矩精度误差应不大于3%,并在使用过程中定 期复验 5.3.6经检验合格的高强度连接副,应按设计要求涂漆防锈,并在连接处缝隙及时用腻子封闭
防腐蚀 6.1防腐蚀的基本规定 6. .1.1防腐蚀操作工应具有行业主管部门颁发的防腐蚀操作工资质证书并在有效期内,所从事的工作 应与本人考试合格的项目相符
6. 1 .2 防腐蚀施工的质检人员应具有行业主管部门颁发的防腐蚀质检人员资质证书并在有效期内
6.1.3防腐蚀施工前,施工单位应编写防腐蚀工艺规程
6. 1.4防腐蚀材料应具有出厂质量证明
标号不清或对材质有疑问时应予复验,复验符合有关标准后 方可使用
6.2表面预处理 6.2.1表面预处理应符合SL105或国家有关标准的规定
闹门表面预处理后,基体金属表面请洁度不应低于GBT823- -1988中规定的S2一级,表面 粗糙度值及质量评定应符合SL105或国家有关标准的规定
6 闸门埋件露出混凝土的钢表面预处理要求同闸门表面,埋人混凝土部分表面处理清洁度不应低 GB/T8923一1988中规定的Sal级
6 表面防护 6 3.1表面涂料保护,金属热喷涂保护及牺牲阳极保护应符合SL105或国家有关标准的规定
设计图样和有关技术文件无特殊要求时,闸门埋件露出混凝土的钢表面防护要求同闸门表面
6 埋人混凝土部分防护要求应符合SL105或国家有关标准的规定
表面防腐蚀的检测 6. 6 4.1在防腐蚀施工过程中,应对每道工序进行检测并做好检测记录,在前道工序合格后方可进行下 道工序 4.2表面预处理及表面防护的质量检测应按SL105或国家有关标准的规定
6 闸门制造 7.1零件和单个构件制造 制定零件和单个构件的制造工艺时,应预留焊接收缩量、机械加工部位的切削余量
7.1.2用钢板或型钢下料而成的零件,其未注公差尺寸的应符合表6规定
表6零件的极限偏差 单位为毫米 极限偏差 极限偏差 基本尺寸 基本尺寸 切割 刨)边缘 切割 刨)边缘 S1000 士2 士0.5 >20003150 士2.5 士1.5 >l0002000 士l 士2 士2.5 >3150 士3 切割钢板或型钢,其切断口表面形位公差及表面粗糙度要求 钢板或型钢切断面为待焊边缘时,切断面应无对缝质量有不利影响的缺欠;断面粗糙度 Ra<50 0Am;长度方向的直线度公差应不大于边棱长度的0.5/1000,且不大于1.5” ;厚度 mm; ;24mnm 方向的垂直度公差:当板厚<24mm 若局 n时,不大于0.5mm; 时,不大于1" 1mm
部存在少量较深的割痕时,可采用电焊方法进行焊补,但焊补应遵守本标准有关焊接的规定,
GB/T14173一2008 焊补后应磨平
b)钢板或型钢切断面为非焊接边缘时,切断面应光滑、整齐、无毛刺;长度方向的直线度公差应 不大于表6中尺寸公差的一半;厚度方向的垂直度公差应不大于厚度的1/10,且不大于 2mm
7.1.4焊缝坡口的基本形式和尺寸应符合GB/T985和GB/T986的有关规定
7.1.5钢板零件的边棱之间平行度和垂直度公差为表6相应尺寸公差的一半
7.1.6零件经矫正后,钢板的平面度、型钢的直线度、角钢肢的垂直度、工字钢和槽钢翼缘的垂直度和 扭曲应符合表7的规定 表7零件形位公差 单位为毫米 序号 称 心 公 差 简 在lm范围内 0>4;t<2 钢板、扁钢的局部平面度" 0>4~12;/1.5 1000 12;1! 角钢、工字钢、槽钢的直线度 长度的1/1000但不大于5 A100 角钢肢的垂直度A 芯 工字钢、槽钢翼缘的垂直度A 忙 么l00 <2000 "1.5 角钢、工字钢、槽钢扭曲
" 0.75 0.5 H 000" >2000 10
GB/T14173一2008 7.1.7单个构件的尺寸极限偏差和形位公差应符合表8的规定
表8构件尺寸极限偏差和形位公差 单位为毫米 号 名 称 图 序 简 极限偏差或公差 构件宽度b 构件高度h 士2 腹板间距e a150,且不大于2 上 翼缘板对腹板的垂直度a T 立" a<0.003b,且不大于2 腹板对翼缘板的中心位置 工 不大于2 的偏移e 000 腹板的局部平面度 每米范围内不大于" A 长度不大于3m的构件,应不 扭曲 大于1,每增加1m,递增0.5, 目 最大不大于2 构件长度的1/1500,且不大 正面(受力面)弯曲度 构件长度的1/1000,且不大 侧面弯曲度 于6 7.1.8零件和单个构件变形,可以采用机械方法或局部火焰加热方法矫正
若采用局部火焰加热矫 正,应控制加热区的温度不超过650c(呈暗红色). 铸钢件和锻件 7.2.1铸钢件和锻件根据零件的受力情况、重要性程度及工作条件分为4类,合同文件及图样另有规 定者,按合同文件及图样的规定
-类铸钢件和锻件 门叶面积×水头>1000m的平面闸门的主轮、主轮轴、吊耳轴、节间连接轴、铸锻件 1l
GB/T14173一2008 主轨; 门叶面积×水头>l000m的弧形闸门的支钞、支钞轴; 人字闸门的顶、底枢零件及支枕垫块
b 二类铸钢件和锻件: -门叶面积×水头<1000m'的平面闸门的主轮、主轮轴、节间连接轴、铸锻件主轨; 门叶面积×水头<1000m的弧形闸门的支铃、支钞轴
三类铸钢件和锻件 平面滑动闸门的主滑块及滑块座
四类铸钢件和锻件 除以上3类之外的铸钢件及锻件
7.2.2除本标准另有规定外,铸钢件的化学成分和力学性能等技术要求,试验方法和检验规则应分别 符合GB/T11352或GB/Tl4408的规定;焊接结构用铸锅的牌号及其铸件的技术条件应符合GB/T 7659的规定;承受压力铸钢的牌号及其铸件的技术条件应符合GB/T16253的规定;承受冲击负荷下 耐磨损尚锯钢的牌号及其铸件的技术条件应符合 GB/T5680的规定
7.2.3 铸钢件应按批提供出厂质量合格证书,内容包括;订货合同号铸件名称及设计图号.铸钢牌号 熔炼炉号,批g 、热处理类型、各项检验结果及标准编号
凡同- a 牌号、同一炉次浇注及同炉热处理者为一批
b) 质量合格证书中应包括化学成分和力学性能试验的实测数据
力学性能应提供R,R.(R2),A、乙的实测数据
设计有要求时提供硬度的实测数据
对于 c) 低温、冲击工作条件下的铸钢件还应提供冲击功(夏比V型缺口试验Akv)的数据,冲击试验 的试验温度应按设计规定
7.2.4铸钢件的尺寸和机械加工余量的数值、确定方法及检验评定规则应符合GB/T6414的规定
7.2.5铸钢件的表面质量 a)铸钢件表面应清理干净,修整飞边与毛刺,去除补贴、粘砂、氧化铁皮及内腔残余物
b) 浇冒口的残根应清除干净、平整
e铸钢件表面不应有裂纹、冷隔和缩松等缺欠,加工面上允许存在机械加工余量范围内的表面 缺欠
7.2.6 二类铸钢件应按GB/T7233进行超声波检测,一类铸钢件的主要受力部位质量等级应符合 2级标准,其余部位质量等级应符合3级标准;二类铸钢件的主要受力部位应符合3级标准,其余部位 质量等级应符合4级标准
二类铸钢件应作100%外观目视检查,其主要受力部位的加工面应按 GB/T9443或GB/T9444进行表面无损检测,一类铸钢件检查比例不低于50%,二类铸钢件检查比例 不低于20%,不得有裂纹
同一批的主轨可对该批30%的主轨进行抽查,其他部位对有疑问处应进行 检查
当检查发现有裂纹缺欠时,应进行100%检查
7.2.7铸钢件有超标缺欠时,可用焊接方法进行修补,合同或图样另有规定时按其规定执行
7.2.8铸钢件焊补前应将缺欠全部清除干净,露出致密金属表面,坡口面应修整圆滑,不得有尖角存 在;对于裂纹类缺欠,在清除裂纹前为防止裂纹扩展,应开止裂孔,并采用磁粉检测或渗透检测方法对焊 补区坡口进行检验,以证实缺欠被全部清除
7.2.9铸钢件焊补前应进行预热,焊补后应进行消除应力热处理
7.2.10焊补应遵照本标准有关焊接的规定
7.2.11当焊补坡口深度超过壁厚的20%或25mm或坡口面积大于65cnm时,被认为是重大焊补
重大焊补应征得设计同意和监理批准;重大焊补应有焊补技术记录,及时、正确、真实地记录焊补过程的 实际情况
7.2.12铸钢件在最终性能热处理之后不得再进行焊补 12
GB/T14173一2008 7.2.13锻件用的钢棒、钢锭或钢坯应是镇静钢,其制造和验收技术要求应符合JB/T6397或 JB/T6396的要求
要求保证淬透性的锻件的牌号、技术要求、试验方法及检验规则应符合GB/T5216 的要求
7.2.14锻件用钢应具有出厂合格证书,合格证书应包括化学成分及力学性能试验的实测数据
每批 锻件应由同一图样锻成,也可由不同图样锻造但形状和尺寸相近的锻件组批
各类锻件的试验要求见 表9 表9锻件的检验项目 试验项目及检验数量 锻件 组批条件 拉伸(R、R或 级别 冲击(AKV 化学成分 硬度 R.2、A、2 每 -炉号 100% 100% 00% 逐件检验 每批抽2% 每批抽2%, 每一炉号 100% 同钢号,同热处理炉次 但不少于2件 但不少于2件 炉号 100% 同钢号,同热处理炉次 每批抽2%,但 四 每 -炉号 同钢号、同热处理炉次 不少于2件 注1;按百分比计算检验数量后,不足1件的余数应算为l件
注2: 二类锻件的硬度值不作为验收的依据
7.2.15锻件表面不应有裂纹、缩孔、折叠、夹层及锻伤等缺欠
需机械加工的表面若有缺欠,其深度不 应超过单边机械加工余量的50%
二类锻件应按照GB/T6402进行超声波检测类锻件的质量等级应符合2级标准,二类锻件 的质量等级应符合3级标准
一类锻件应按JB/T4730.4或JB/T4730.5进行表面无损检测检查,主 要受力部位检查比例不低于50%,其他部位对有疑问处进行检查
不允许任何裂纹和白点,紧固件和 轴类零件不允许任何横向缺陷显示,其他部件和材料川级合格
当检查发现有超标缺欠时,应进行 100%检查
7.2.16有白点的缺欠应予报废,且与该锻件同一熔炉号、同炉热处理的锻件均应逐个进行检查
7.2.17焊补应遵照本标准有关焊接的规定
7.3埋件制造 7.3.1除本标准另有规定者外,预埋在各类闸室中的钢结构件,包括底槛、主轨,副轨,反轨,止水座板、 门楣,侧轮导板、侧轨、钞座钢梁和具有止水要求的胸墙及钢衬护制造的允许公差应符合表10的规定
表10具有止水要求的埋件公差 单位为毫米 差 项 目 序号 构件表面未经加工 构件表面经过加工 1/! 工作面直线度 构件长度的1 500 且不大于3 构件长度的1 /2000 且不大于1 侧面直线度 构件长度的1/1000且不大于4 构件长度的1/1000且不大于2 工作面局部平面度 每米范围内不大于1,且不超过2处每米范围内不大于0,5,且不超过2处 长度不大于3m的构件,不应大于1! 扭曲 每增加1m,递增0.5,且最大不大于2 注l:工作面直线度,沿工作面正向对应支承梁腹板中心测量
注2:侧面直线度,沿工作面侧向对应隔板或筋板处测量
注3;扭曲系指构件两对角线中间交叉点处不吻合值
13
GB/T14173一2008 7.3.2没有止水要求的胸墙和钢衬护制造的允许公差应符合表11的规定
表11没有止水要求的埋件公差 单位为毫米 序号 项 目 差 公 工作面直线度 构件长度的1/1500且不大于3 侧面直线度 构件长度的1/1500且不大于4 工作面局部平面度 每米范围内不大于3 长度不大于3m,不应大于2,每增加lm,递增0.5,且不大于3 扭曲 注l:工作面直线度,沿工作面正向对应支承梁腹板中心测量
注2侧面直线度,沿工作而侧向对应隔板或筋板处测量
注3:扭曲系指构件两对角线中间交叉点处不吻合值
7.3.3平面链轮闸门主轨承压凹槽及承压板加工按GB/1800,2一1998应不低于IT8级精度要求, 凹槽底面的直线度应符合表12的规定
当设计要求对主轨承压板进行表面热处理时,热处理工艺应保证表面硬度及硬度分布满足要求
承压板装配在主轨上之后,接头的错位应不大于0.! ,主轨承压面的直线度允许公差应符合 lmm, 表12的规定
表12平面链轮闸门主轨凹槽和承压面公差 单位为毫米 差 主轨长度 主轨凹槽底面 主轨承压面 S1000 0.15 0.20 >10002500 0.20 0.30 0.25 25004000 0.40 >40006300 30 50 0
0. >630010000 0.40 0.60 7.3.4采用充压式、压紧式水封的弧形闸门,埋件的止水座基面的曲率半径极限偏差为士2mm,其偏 差方向应与门叶面板外弧的曲率偏差方向一致;其他型式弧形闸门侧止水座板和侧轮导板的中心线曲 率半径极限偏差为士3mm
7.3.5底槛和门楣的长度极限偏差为一4mm~0mm,如底槛不是嵌于其他构件之间,则极限偏差为 士4mm,胸墙的宽度极限偏差为一4mm~0mm,对角线相对差应不大于4mm. 7.3.6焊接主轨的不锈方钢、止水板与主轨面板组装时应压合,局部间隙应不大于0.5mm,且每段长 度不超过100 mm, 1,累计长度不超过全长的15%
铸钢主轨支承面(《踏面)宽度尺寸极限偏差为士3 7.3.7 mm
7.3.8 当止水板在主轨上时,任一横断面的止水面与主轨轨面的距离c的极限偏差为士0.5mm,止水 板中心至轨面中心的距离a的极限偏差为士2mm,止水板与主轨轨面的相互关系见图2 主轨; -止水板
图2止水板与主轨轨面的相互关系 14
GB/T14173一2008 7.3.g当止水板在反轨上时,任一横断面的止水板与反轨工作面的距离c的极限偏差为士2mm,止水 板中心至反轨工作面中心的距离a的极限偏差为士3mm,止水板与反轨工作面的相互关系见图3. -反轨工作面 -止水板
图3止水板与反轨工作面的相互关系 7.3.10护角如兼作侧轨,其与主轨轨面(或反轨工作面)中心距离a的极限偏差为士3mm,其与主轨 轨面(或反轨工作面)的垂直度公差应不大于1mm(见图4)
主轨; 反轨; 护角
图4护角与主轨反轨)的相互关系 支钦的钦链和铃座平面的平面度公差、钦链轴孔和钦座轴孔的同轴度公差应符合 7.3.11 -1999中B级精度要求,其表面粗糙度R<25m;钦链与支臂的连接螺孔宜采用模板套钻
GB/Tl184 7.3.12分节制造的埋件,应在制造厂进行预组装,组装可以立拼,也可以卧拼,但不应以外力强制 组装
组装时,相邻构件组合处的错位允差为 7.3.13 a经过机加工的工作面应不大于0.5mm b) 未经机加工的应不大于2mm
e)链轮门主轨承压面应不大于0.1 mm
7.3.14预组装检验合格后,应在埋件的工作面和止水面显著标记中心线,应在节间组合面两侧 150mm处标定检查线,必要时应设置定位装置,并按本标准有关规定进行编号和包装
平面闸门门体制造 除本标准另有规定者外,平面闸门门叶制造、组装的公差或极限偏差应符合表13的规定 表13平面闸门门叶的公差或极限偏差 单位为毫米 序号 项 门叶尺寸 公差或极限偏差 注 s1000 士3 门叶厚度b >10003000 士4 >3000 士s 5000 士5 士8 5000l0000 门叶外形高度H 士10 >10000~15000 门叶外形宽度B >1500020000 士12 >20000 士15 15
GB/T14173一2008 表13(续 单位为毫米 项 注 序号 门叶尺寸 公差或极限偏差 5000 >500010000 门叶宽度B和高度H >10000~15000 10 的对应边之差 >1500020000 >20000 5000 >500010000 门叶尺寸取门高或 >10000~15000 对角线相对差1D-D 门宽中尺寸较大者 >1500020000 20000 s10000 扭曲 l0000 B/1500,且不大于6 通过各横梁中心线 门叶横向直线度 (凸向背水面时为3)测量 通过两边梁中心线 门叶竖向直线度f H/1500,且不大于4 测量 <10000 士3 >1000015000 士4 两边梁中心距 士5 >15000一20000 士6 >20000 l0000 >l0000~15000 两边梁平行度|1'一 >l500020000 >20000 10 纵向隔板错位 面板与梁组合面的励 1 部间隙 面板厚度 每米范围内不大于: 5 10 12 面板局部平面度 >1016 >16 13 门叶底缘直线度 14 门叶底缘倾斜值2C 两边梁底缘平面或承 15 2 压板)平面度 止水座面平面度 16 1" 节间止水板平面度 止水座板至支承座面 18 士1 的距离 侧止水螺孔中心至门 19 士1.5 叶中心距离 16
GB/T14173一2008 表13(续 单位为毫米 项 目 注 序号 门叶尺寸 公差或极限偏差 顶止水螺孔中心至门 20 士3 叶底缘距离 21 土2 底水封座板高度 自动挂钩定位孔或 22 士2 销)至门叶中心距离 简图 7.4.2滚轮和轴套应按图样要求的配合公差加工
在图样未明确规定时,轴套内孔直径偏差应符合 GB/T1801一1999规定的H8级精度要求,其圆柱度公差为尺寸公差的1/2,滚轮踏面圆跳动宜不低于 GB/T1184一1999中9级精度要求
滚轮组装好后,应转动灵活,无卡滞现象
7.4.3滑道支承常用材料 -填充四氟乙烯板材、钢基铜塑复合材料、自润滑铜合金,工程塑料合金的 物理力学性能与技术要求参见附录C
7.4.4滑道支承夹槽底面与门叶表面的间隙应符合表14的规定
表14滑道支承夹槽底面与门叶表面的间隙 单位为毫米 极限偏差 序号 间隙性质 接触表面未经加工 接触表面经过加工 贯穿间默 4应不大于1,每段长度不 4应不大于0.3,每段长度 超过200,累计长度不大于滑不超过l00,累计长度不大于 道全长的20% 滑道全长的15% 局部间除 40,5,b1/10,累计长度 么0.3,b1/10,累计长度 不大于滑道全长的50% 不大于滑道全长的25% 17
GB/T14173一2008 7.4.5平面闸门的滚轮或滑道支承组装时,应以止水座面为基准面进行调整
组装的公差或极限偏差 应符合表15的规定
表15滚轮或滑道支承组装的公差或极限偏差 单位为毫米 序号 项目 特征尺寸 公差或极限偏差 备注 跨度<1000o 滚轮或滑道支承所组平面 测量时应在每段滑道 的平面度 两端各测一点 跨度 10000 <0.5 滑道长度<50o 滑道支承与止水座基准面 平行度 滑道长度>500 <1 相邻滑道衔接端的高低差 <1 滚轮或支承滑道的工作面 士1.5 与止水座面的距离极限偏差 同 -横断面上 反向支承滑块或滚轮的工 作面与止水座面的距离极限 士2 偏差 滚轮对任何平面的倾斜度 2/1000 同侧滚轮或滑道的中心线 土2 与闸门中心线的极限偏差 哎 跨 滚轮 滑道 滚轮或滑道支承跨度的极 士2 士2 5000 限偏差 >500010000 士3 士2 >10000 士4 土2 跨距 <5000 平面链轮闸门承载走道跨 士1 >500010000 士2 度极限偏差 >10000 士3 4.6闸门吊耳距门叶中心线极限偏差为士1.5mmm
闸门吊耳孔在闸门高度、厚度方向中心线与图 7. 样给定基准面的极限偏差为士2mm,且相对差不大于2mm 7.4.7吊耳、吊杆的轴孔倾斜度应不大于1/1000
7.4.8平面闸门出厂前应进行整体预组装(包括主支承装置、反向支承装置、侧向支承装置及充水装 置),预组装应在自由状态下进行
如节间焊接连接的,则节间允许用连接板连接,但不得强制组合 平面链轮闸门门叶焊接完成之后,为了保证门叶整体形状和几何尺寸的稳定,宜进行消除应力 7.4.9 处理
当设计图样要求对门叶进行机加工时,应满足下列要求 相应平面之间距离极限偏差为士0.5mm a 门叶两侧与承载走道相接触的表面平面度应不大于0.3mm. b 平行平面的平行度应不大于0.3mm. c) d)各机械加工面的表面粗糙度R,<25m. e 加工后的梁系翼缘板厚应符合设计要求,局部极限偏差- 一2mm
平面链轮闸门的主要零部件(滚轮、承载走道、非承载走道)的制造应满足下列要求 7.4.10 主要零部件尺寸公差可参照GB/T 1800.2一1998中按IT6IT8级选用,表面粗糙度 R, <3.2m. 18
GB/T14173一2008 b 当设计要求对承载走道进行表面热处理时,热处理工艺应保证表面硬度和硬度分布满足 要求 7.4.11平面链轮闸门链条组装好后,应活动灵活,无卡滞现象
门叶水平放置时,每个链轮与承载走 道面应接触良好,接触长度不应小于链轮长度的80%,局部间隙应小于0.1mm
门叶处在工作位置 时,应检查链轮与下部端走道之间的距离(下驰度)并满足设计的要求
7.4.12平面链轮闸门反轮、侧轮及止水橡皮的组装应以承载走道上的链轮所确定的平面和中心为基 准进行调整与检查
7.4.13预组装后,平面闸门组合处的错位应不大于2 1,但平面链轮闸门组合处的错位应不大于 mm mm
mm作 7.4.14检查合格后,应明显标记门叶中心线、边柱中心线及对角线测控点,在组合处两侧150 供安装控制的检查线,设置可靠的定位装置并进行编号和标志
7.5弧形闸门门体制造 7.5.1除本标准另有规定者外,弧形闸门门叶制造、组装的允许公差与极限偏差应符合表16的规定
表16弧形闸门门叶的公差或极限偏差 单位为毫米 公差或极限偏差 序号 项 目 门叶尺寸 注 潜孔式 露顶式 s1000 士3 士3 门叶厚度b >10003000 士! 士4 >3000 士5 士5 5000 士5 士5 门叶外形高度H和外形 >500010000 土8 土8 宽度B >l000015000 士1o 士10 >15000 士12 士12 5000 在主梁与支臂组合 对角线相差|一D 5000l0000 处测量 >l0000 <5000 在主梁与支臂组合 >5000l0000 处测量 >10000 拼曲 5000 >500010000 在门叶四角测量 >10000 二5000 通过各主、次横梁或 门叶横向直线度 5000l0000 横向隔板的中心线 >l0000 测量 通过各主、次纵梁或 门叶纵向弧度与样板的 纵向隔板的中心线,用 间隙 弦长3m的样板测量 士3 两主梁中心距 士3 两主梁平行度|'-L l9
GB/T14173一2008 表16(续 单位为毫米 公差或极限偏差 项 目 备 注 序号 门叶尺寸 潜孔式 露顶式 纵向隔板错位 面板与梁组合面的局部 10 间隙 每米范围不大于 板厚心: >6~10 1 面板与样尺的间阶 >1016 16 12 门叶底缘直线度 2C 门叶底缘倾斜值 13 14 侧止水座面平面度 15 顶止水座面平面度 侧止水座面至门叶中心 16 士1,5 士1.5 距离 侧止水螺孔中心至门叶 1 士1.5 士1.5 中心距离 顶止水螺孔中心至门叶 18 底缘距离 简图 注:当门叶宽度、两边梁中心距及其直线度与侧止水有关时,其偏差值应符合图样规定
7.5.2采用充压式、压紧式水封弧形闸门门叶面板加工后的外弧的曲率半径极限偏差为士2mm,其偏 差方向应与埋件的止水座基面的曲率半径偏差方向一致;门叶面板加工后的板厚应不小于图样尺寸,其 表面粗糙度R,<254m,形状公差应符合表17的规定 20
GB/T14173一2008 表17形状公差 单位为毫米 目 序号 项 特征尺寸 公差 1000 0,5 >1000~1600 0.8 >1600一2500 门叶横向直线度 >25004000 1.2 >40006300 >630010000 <630 0. 25 >6301000 0.3 各组合面的平面度 >10001600 0.4 >16002500 0.5 7.5.3弧形闸门吊耳的位置及吊耳孔中心线的极限偏差应符合7.4.6的规定 7.5.4支臂见图5)制造与组装的极限偏差应符合下列规定 臂柱; 连接板
图5支臂示意图 a 臂柱下料时,应留出焊接收缩和调整的余量,在弧形闸门整体组装时再修正,以使其长度最后 能满足铵链轴孔中心至面板外缘曲率半径的要求
b)臂柱作为单个构件制造的极限偏差应符合表8的规定
支臂开口处弦长L的极限偏差应符合表18的规定
c 表18支臂开口处弦长极限偏差 单位为毫米 序号 支腿开口处弦长L. 极限偏差 S4000 士2 >40006000 士3 >6000 士4 D 直支臂的侧面扭曲应不大于2 反向弧形闸门支臂两侧对水平面的垂直度应不大于支腿 mm, 开口处弦长L/1000.
斜支臂组装应以臂柱中心线夹角平分线为基准线,臂柱腹板应与门叶主梁腹板形成水平连接 支臂连接板应与基准线垂直上、下臂柱腹板在垂直于基准线的剖面的扭角应用样板检查,样 板间隙应不大于2mm,臂柱补强板应根据计算扭角大小预折成形,不得强制装配
狐形闸门出厂前,应进行立体组装检查,其公差或极限偏差除符合本章中的有关规定外,并应符 7.5.5 合表19的要求
21
GB/T14173一2008 表19弧形闸门组装的公差或极限偏差 单位为毫米 目 注 序号 项 公差或极限偏差 两个钦链轴孔的同轴度公差 <1/1000 每个钦链轴孔的倾斜度 士1 钦链中心至门叶中心距离L 臂柱中心与较链中心的不吻合值 <2 臂柱腹板中心与主梁腹板中心的不吻合值4 二4 支臂中心至门叶中心距离La 士1.5 在支臂开口处测量 支臂与主梁组合处的中心至支臂与钦链组合处 的中心对角线相对差D一D 在上、下两支臂夹角平分线的垂直剖面上,上、下 支臂侧面的位置度公差C一 -L l 露顶式弧形闸门 士?7 潜孔式弧形闸门 土3 钦链轴孔中心至 其偏差方向应与埋 面板外缘的半径R 采用充压式、压紧式水封 士2 件的止水座基面的曲 弧形闸门 率半径偏差方向一致 露顶式弧形闸门 5 铵链轴孔中心 至 潜孔式弧形闸门 2 面板外缘的半径R 10 采用充压式,压紧式水封 两侧相对差 弧形闸门 组合处错位 11 应有75%以上的面积 连接螺栓紧固后,用 支臂两端连接板与门叶、较链组合面之接触面, 12 紧贴,且边缘最大间欧不 0.3 nmm塞尺检查其塞 臂柱间两连接板的接触面 人面积应小于25% 应大于0.8mm H- 人 简图 -l削面 22
GB/T14173一2008 7.5.6组装检查合格后,应明显标记门叶中心线,对角线测控点,在组合处两侧150mm作供安装控制 的检查线设置可靠的定位装置,并进行编号和标志
7.6人字闸门门体制造 7.6.1人字闸门门叶制造、组装的公差或极限偏差,应符合表20的规定
表20人字闸门门叶的公差或极限偏差 单位为毫米 序号 门叶尺寸 公差或极限偏旅 项 目 备 注 s1000 士3 门叶厚度b >l0003000 >3000 土5 5000 土8 >5000~10000 土12 门叶外形高度H 二 l0000~15000 王 >1500020000 士20 >20000 5000 土2 门叶外形半宽B/2 >500010000 10000 s5000 >500010000 按门高或门宽尺寸 对角线相对差|D一D >10000l5000 较大者选取 >1500020000 >2000o 5000 2.5 门轴柱、斜接柱正面直线度 >500010000 >l0000 门轴柱,斜接柱侧面直线度 通过各横梁中心线 门叶横向直线度 B/1500,且不大于4 测量 通过左、右两侧两根 门叶竖向直线度h H/1500,且不大于6 纵向隔板中心线测量 s5000 2.5 >5000l0000 顶、底主梁的长度相对差 10000 门叶底面的平面度 10 1r 止水座面平面度 12 面板与梁组合面的局部间隙 面板板厚 每米范围内 10 13 面板局部不平度 >1016 >16 14 门叶底缘倾斜值2C