GB/T37775-2019
大型钢质自由锻件通用技术规范
Heavysteelopendieforgings—Generaltechnicalspecification
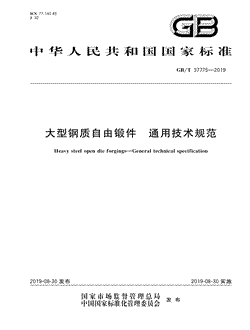
- 中国标准分类号(CCS)J32
- 国际标准分类号(ICS)77.140.85
- 实施日期2019-08-30
- 文件格式PDF
- 文本页数22页
- 文件大小1.40M
以图片形式预览大型钢质自由锻件通用技术规范
大型钢质自由锻件通用技术规范
国家标准 GB/T37775一2019 大型钢质自由锻件通用技术规范 Heaysteelopendieforgings一Generalteechniealspecifieaton 2019-08-30发布 2019-08-30实施 国家市场监督管理总局 发布 国家标准化管理委员会国家标准
GB/37775一2019 目 次 前言 范围 规范性引用文件 2 术语和定义 3 订货要求 制造工艺 5.1冶炼和浇注 5.2锻造 5.3热处理 5.4缺陷清除和补煤 6 技术要求 6.1化学成分 6.2力学性能 6.3硬度均匀性 6.4金相组织 6.5残余应力 6.6无损检测 6.7尺寸检查 检验规则和试验方法 化学成分分析 力学性能试验 7.2 硬度检验 7.3 7.4 10 金相检验 7.8 残余应力测定 7.6 无损检测 7. 复试 7.8 重新热处理 ll 验收和质量证明书 8 1 ll1 8.1验收 8.2质量证明书 12 标志和包装 9.1标志 12 12 9.2包装 13 附录A资料性附录特殊产品的技术和车间评定 16 附录B规范性附录锻造比
GB/T37775一2019 附录C资料性附录大型钢质自由锻件常用的材料标准 图1T×T/4取样示意图 图21×2取样示意图 图3实心轴类锻件取样示意图 图4筒形锻件取样示意图 图5饼形锻件取样示意图(外圆加大) 饼形锻件取样示意图高度增高 图7环形锻件取样示意图(外圆加大 环形锻件取样示意图(高度增高 相对于锻件的主变形方向时取样位置图 图10相对于锻件的产品几何形状时取样位置图 表1成品化学成分允许偏差 表2锻件的试料和试样数量 I
GB/37775一2019 前 言 本标准按照GB/T1.1一2009给出的规则起草
本标准由机械工业联合会提出
本标准由全国大型铸锻件标准化技术委员会(SAC/TC506)归口
本标准起草单位:二重德阳)重型装备有限公司、第一重型机械股份公司、上海电气上重铸锻 有限公司太原重工股份有限公司
本标准主要起草人:蒋新亮、冯敬,董涛,郭义、张智峰、翟小铁、陈杰、曹华、罗玉立、蔡静、于海涛、 王晓芳、牛玉温
GB/37775一2019 大型钢质自由锻件通用技术规范 范围 本标准规定了大型钢质自由锻件的订货要求,制造工艺、技术要求、检验规则和试验方法、验收和质 量证明书及标志和包装
本标准适用于压机和锻锤自由锻造的结构钢、不锈钢、模具钢、耐热钢等大型锻件的订货、制造与 检验
规范性引用文件 下列文件对于本文件的应用是必不可少的
凡是迷日期的引用文件,仅注日期的版本适用于本文 件
凡是不注日期的引用文件,其最新版本(包括所有的修改单)适用于本文件
GB/T222钢的成品化学成分允许偏差 GB/T223所有部分钢铁及合金化学分析方法 GB/T228.1金属材料拉伸试验第1部分:室温试验方法 GB/T228.2金属材料拉伸试验第2部分;高温试验方法 GB/T229金属材料夏比摆锤冲击试验方法 GB 231. 金属材料布氏硬度试验第1部分;试验方法 GB 6394金属平均晶粒度测定方法 GB/T10561钢中非金属夹杂物含量的测定标准评级图显微检验法 GB/T13298金属显微组织检验方法 GB/T13299钢的显微组织评定方法 GB/T20066钢和铁化学成分测定用试样的取样和制样方法 JB/T8467锻钢件超声检测 NB/T47008一2010承压设备用碳素钢和合金钢锻件 术语和定义 NB/T47008一2010界定的以及下列术语和定义适用于本文件
为了便于使用,以下重复列出了 NB/T47008一2010中的某些术语和定义 3.1 大型钢质自由锻件heavysteel lopendieforging 经10MN以上的自由锻压机、50kN以上的自由锻锤锻造而成的钢质锻件 3.2 轴类锻件shaftforging 截面为圆形,轴向长度L大于其直径D的实心锻件
3.3 筒形锻件shellforging 轴向长度L大于其外径D的轴对称空心锻件
GB/T37775一2019 [NB/T47008一2010,定义3.1] 3.4 环形锻件rnetortme 轴向长度L小于或等于其外径D的轴对称空心锻件
[NB/T47008一2010,定义3.2] 3.5 饼形锻件diskforging 轴向长度L小于或等于其外径D的轴对称实心锻件
3.6 条形锻件barforging 截面为矩形,长度L均大于其两边长的锻件
注改写NB/T47008一2010,定义3.6 3.7 合锻件combinedforging 将两个或两个以上的锻件组合,放在一个锻件中,按一个锻件锻造生产
3.8 主要截面manseeton 确定力学性能的截面
3.9 等效截面equivalentseetiom 与主要截面具有同样力学性能、近似相等的截面
订货要求 4.1采购方应在订货合同中写明执行的标准和技术条件、锻件名称材料牌号、订货图样、订货数量,交 货状态、检验项目及其他附加要求
4.2若锻件由制造方转至分供方后,分供方应具有相应的生产条件和资质或得到采购方的认可
4.3对于特殊产品,为验证制造方是否具备制造合格产品的能力,可参考附录A的要求进行评定,采 购方应在订货合同中写明 若订货合同或标准中规定,制造方应在制造开始前编写制造大纲,并提交采购方认可
在采购方 4.4 批准之后,未经采购方许可,不得进行修改
若在生产过程中出现不符合制造大纲的偏差,应向采购方 提交偏差申请并记录
制造大纲内容可参考A.3.5
制造工艺 5 5.1冶炼和浇 锻件用钢应采用经电炉或转炉加钢包精炼炉冶治炼的镇静钢,或采用电渣重熔等能够保证钢锭质量 的其他冶炼方法
5.2锻造 5.2.1钢锭的冒口和水口应有足够的切除量,以确保成品锻件无缩孔和严重的成分偏析
5.2.2锻件应在有足够压力的锻压设备上锻造成形,对钢锭的原始缺陷进行改善,如凝固缺陷焊合,夹 杂打碎等,以保证锻件内部质量
GB/37775一2019 5.2.3用钢锭锻造时,未经徵粗的锻件的总拔长锻造比应不小于3.0;经过徵粗的锻件,单次连续拔长 锻造比应不小于2.0,总拔长锻造比应不小于2.5
用锻材或轧材锻造时,拔长总锻造比应不小于1.3
大截面法兰部位的拔长锻造比可适当减小,但不得小于1.7
若使用电渣锭,适当减小锻造比
锻件的 总锻造比按附录B规定的方法进行计算
5.2.4锻件的形状和尺寸应符合锻件图样和工艺文件的要求
锻造工艺应考虑锻造的均匀性并防止 混晶
锻后热处理应考虑去除氢的不良影响和为最终热处理做组织准备
5.2.5当制造方需要时,可以采用组合锻造的方法
5.3热处理 5.3.1锻件应按照材料标准的要求进行热处理
在保温过程中,炉温应处于规定温度士15笔的范围 内
必要时应在锻件表面放置外接热电偶
在综合考虑工件壁厚,形状结构尺寸等因素的情况下,外 接热电偶应放置在锻件预计最高温度处和最低温度处
5.3.2 若需要规定最低回火温度,呆购方应在订货合同中写明 5.3.3性能热处理后,若锻件需校形,热校形的预热温度应低于回火温度40C一60笔
校形后,应在 笔的温度下进行去应力处理
低于最终回火温度30C50 5.3.4对于有残余应力要求的锻件,应采用受控和缓慢冷却的方法进行冷却.以保证残余应力值低于 规定要求
5.4缺陷清除和补焊 5.4.1对于尺寸超出公差范围的局部缺陷,在得到采购方认可后,可以进行修磨清除,修磨边缘应平滑 过渡,但清理深度不应超过加工余量的75%
修磨清除后,应按材料标准规定在修磨部位进行磁粉检 测或渗透检测,以确认缺陷已清除
5.4.2若发现锻件缺陷无法通过加工清除.未经采购方同意,制造方不应进行补焊
在得到采购方同 意后方可进行补焊
补焊前,应进行合适的无损检测,以证明缺陷已被完全清除
若采购方要求,制造 方应提交接工艺规程(wPs),焊接工艺评定报告(PQR)、焊接人员资质
5.4.3补焊后应提供补焊检查记录,记录内容应包括补焊区硬度、补焊区的相对位置及大小、焊后热处 理等内容,并具有可追溯性
技术要求 6.1化学成分 6.1.1熔炼分析 制造方应对每炉(每包)钢液进行熔炼分析,分析结果应符合材料标准的规定
多炉合浇时允许单 包钢液成分超出材料标准的规定,采用加权平均计算法进行计算,其权重平均分析结果应符合材料标准 的规定
大型钢质自由锻件常用的材料标准参见附录C
6.1.2成品分析 当采购方有要求时,制造方应对锻件进行成品分析
成品分析结果应符合材料标准的规定,但允许 有表1规定的偏差,表1中未规定的元素偏差应符合GB/T222的规定
GB/T37775一2019 表1成品化学成分允许偏差 横截面面积/em 规定化学成分上 650 1300 2600 5200 <650 >10400 元素 限值/% 1300 -2600 -5200 -l0400 超过规定值上限或下限的允许偏差值/% <0.30 士0.01 士0.03 士0.03 士0.04 士0.05 士0.05 >0.30~0,.55 士0,02 士0,04 士0,04 士0.05 士0.06 士0,06 s0.37 士0.05 士0.03 士0.02 士0,04 士0.04 士0.06 Si >0.371.40 士0.04 士0.06 士0.06 士0.07 士0.07 士0.09 s1.00 士0.03 士0.04 士0.05 士0.06 士0,07 士0.08 Mn >1.001.90 土0.04 士0.06 士0.07 士0.08 士0.09 土0.08 <0.025 0.005 +0.005 +0.007 十0,007 十0.010 十0.010 <0.025 +0.005 +0.005 +0.005 十0,005 +0.006 +0.006 0.90 士0,03 士0,04 士0,04 士0.05 士0.05 士0.06 >0.902.1o 0.05 0.07 0.08 士0.07 士0.006 士006 士 士 士6 >2.102.70 士0.1o 士0.10 士0.12 士0.14 士0.15 士0.16 <1.00 士0.03 士0.03 士0.03 士0.03 士0.03 士0.03 N >1.002.00 士0.05 士0.05 士0.05 士0.05 土0.05 士0,05 >2.004.50 士0.07 士0.07 士0.07 士0.07 土0.07 士0.07 0.30 士0,01 士0.02 士0.02 士0.02 士0.03 士0,03 Mo >0,30~0.,60 士0,02 士0,03 士0,03 士0.03 士0.04 士0,04 0.03 士0.05 0.06 士0.07 士008 士004 0.600.80 士 士 Nb s0.045 士0.02 士0.02 士0.02 士0.02 士0.03 士0.03 T <0.10 十0.02 +0.02 十0.03 十0.03 十0.04 十0.04 s1.00 士0.04 士0.05 士0.05 士0.06 士0.06 士0.07 w 士0.08 士0.09 士0.10 >l.001.20 士0.12 士0.12 士0.14 A >0.701.10 士0.05 士0.05 士0.05 士0.07 士0.07 士0.09 <0.10 十0,01 +0.01 +0.01 +0.01 +0.01 +0.01 0.10一0.30 士0.03 士0.,03 士0.,03 士0.03 士0.03 士0.03 6.2力学性能 锻件的力学性能应符合材料标准的规定
6.3硬度均匀性 锻件只要求按硬度验收时,同一锻件的硬度偏差不超过30HBw,同一批次锻件的硬度相对差不超 过40HBw
GB/37775一2019 6.4金相组织 锻件的平均晶粒度和非金属夹杂物应符合材料标准的规定
6.5残余应力 锻件的残余应力应符合材料标准的规定 6.6无损检测 一般要求 6.6.1 在制造的各阶段,应注意检查锻件表面,以避免锻件表面无肉眼可见的裂纹、夹层、折叠、夹渣、严重 的偏析等有害缺陷
6.6.2超声检测 当订货合同有超声检测要求时,采购方应写明超声检测的检测方法、检测部位、检测范围,以及验收 标准
6.6.3其他无损检测 若采购方要求,经供需双方协商确定,应在订货合同写明其他无损检测如磁粉检测、渗透检测等 的相关要求
6.7尺寸检查 在热处理后交货前,按照订货图样的要求进行尺寸检查,并记录主要尺寸;所得的尺寸应在订货图 样规定的公差范围内
检验规则和试验方法 7.1化学成分分析 7.1.1取样方法和分析方法 7.1.1.1化学成分分析用试样的取样方法应按GB/T20066规定的方法进行
7.1.1.2化学成分分析方法应按GB/T223规定的方法或经采购方认可的能保证分析质量的其他方法 进行
7.1.2熔炼分析 每炉(每包)钢液应在浇注前取样测定钢液的化学成分 7.1.2.1 7.1.2.2对于电渣重熔钢锭,若使用同一炉号电极进行重熔,则重熔钢锭的化学成分分析可视为熔炼分 析;若使用不同炉号电极依次重熔,应在水口、冒口两端取样进行化学成分分析,必要时可增加取样部位 和数量,每个部位试样的分析结果均应符合材料标准的规定
7.1.2.3若分析及试样不符合分析要求,无法判定钢液是否符合材料标准规定或不足以确定钢液的化 学成分,制造方可在钢锭或钢坯表面附近合适部位取替代试样以确定钢液的化学成分
7.1.3成品分析 制造方可在锻件上取样分析
取样规定如下:
GB/T37775一2019 优先在锻件力学性能试样上取样进行分析; a D)实心锻件及饼形锻件可在锻件延长部位1/2半径处到外圆之间的任意一点取样进行分析; c 空心锻件或环形锻件可在锻件内外表面之间取样进行分析
7.2力学性能试验 7.2.1试验方法 7.2.1.1室温拉伸试验按GB/T228.1规定的方法进行,高温拉伸试验按GB/T228.2规定的方法 进行
7.2.1.2冲击试验按GB/T229规定的方法进行
7.2.2取样数量 应在最终热处理状态的锻件上切取足够的试料,以保证有足够的试样用于相关试验和可能的复试
若在订货合同、材料标准或技术协议中未做规定,锻件的取样数量按表2的规定
表2锻件的试料和试样数量 热处理时的长度(不含试料延长部分)/ /mm 热处理时的单重/kg 3000 >3000 组批规则 试料的数量 试样的取样组数 同一熔炼号、同时 每批次取1件 500 两端各1组(共2组) 1组 热处理和相似尺寸 >5004500 100% 1组 两端各1组(共2组 >4500 100% -端2组 两端各1组(共2组 在一端取2组试样时,按同一侧面间隔180°;在两端各取1组试样时,按间隔180"的对角位置
7.2.3取样位置 7.2.3.1承压锻件 承压锻件的试料优先取自锻件的本体或本体的延长部分
若采购方在订货图样、专用技术协议中 或经供需双方协商规定了取样方法,则应优先按照订货图样、专用技术协议或双方商定的要求进行取 样
若无特殊规定,试料从锻件上取下后,不应进行任何会影响力学性能的处理
试料的取样位置规定 如下 截取试料时应保证试样的纵轴到任何表面的距离至少为T/4,且试样长度的中线到任何第二 a 表面的距离至少为T(T为锻件取样部位最大热处理厚度)
若使用热缓冲环(块)作为试料. 热缓冲环(块)应通过不完全焊透焊缝完全密封缓冲表面
同时,热缓冲环(块)的高度和宽度 应大于或等于T,长度应至少超过试料区长度两侧各一个T,且试样表面离开缓冲表面的距离 应大于或等于13mm
热缓冲环(块)应是可焊的碳钢或低合金钢
取样示意图见图1
GB/37775一2019 试样位置 锻件最终尺寸 热处理形状 图1r×r/4取样示意图 对于特厚的锻件,订货图样应注明承受主载荷的成品表面
截取试料时应保证试样的纵轴离 b 锻件最近的热处理表面的距离至少等于所注明的承受主载荷的成品表面到最近的热处理表 面的最大距离(t),且试样长度的中线到其他热处理表面至少为此距离的两倍
在任何情况 下,试样的纵轴到锻件任何热处理表面的距离应不小于19mm,试样长度的中线到任何第二 表面的距离应不小于38mm
取样示意图见图2
试样位置 锻件最终尺寸 2r 热处理形状 图21×2取样示意图 c 代表同一炉号和同一热处理批次的锻件试样,可在同熔炼炉号单独锻造的检验样坯上截取
单独生产的检验样坯与所代表的产品锻件应有基本相近的锻造比并经受基本相同的加工过 程,具有与所代表的产品锻件相同的名义厚度,并与所代表的产品锻件进行同一类型的热加 工,同炉并同时进行热处理
7.2.3.2非承压锻件 非承压锻件的试料优先取自锻件主要截面(或等效截面)的本体延长部分;若采购方在订货图样、专 用技术协议中或经供需双方协商规定了取样方法,则应优先按照订货图样、专用技术协议或双方商定的 要求进行取样
如无特殊规定,试料从锻钢件上取下后,不应进行任何会影响力学性能的处理
试料的 取样位置规定如下: 实心轴类锻件的试样应取自距表面1/3半径处,条形锻件的试样应取自沿对角线顶点到中心 a 的1/3处
取样示意图见图3
GB/T37775一2019 D主赞被面 D效截面 说明:要求D~D
图3实心轴类锻件取样示意图 b)筒形锻件的试样应取自1/2壁厚处,取样示意图见图4
T/" 图4筒形锻件取样示意图 饼形锻件,当在外径加大部分取样时,试样应取自加大部分至少1/3高度处;当在延长部位取 样时,试样应取自距外缘1/3半径处或至少距边缘20mm处
取样示意图见图5、图6
H/3 图5饼形锻件取样示意图(外圆加大) R/3或距离外圆>20mm 图6饼形锻件取样示意图(高度增高
GB/37775一2019 d)环形锻件,当在外径加大部位取样时,试样应取自加大部分至少1/3高度处;当在延长部位取 样时,试样应取自至少1/3壁厚处
取样示意图见图7,图8
睐 图7环形锻件取样示意图(外圆加大 T/3 图8环形锻件取样示意图高度增高 若采购方同意,锻件的力学性能试样也可从同熔炼炉号单独锻造的检验样坯上截取,检验样坯 与所代表的锻件应有相近的锻造比、检验样坯的热处理有效厚度大于或等于产品锻件的有效 厚度,并与所代表的产品锻件进行同一类型的热加工,同炉并同时进行热处理
7.2.4取样方向 7.2.4.1一般规定 试样取样方向应为锻件的主加工方向
若无法满足规定的取样方向要求,经由供需双方商定,也可 取其他方向的试样
7.2.4.2试样相对于锻件的主变形方向 当试样相对于锻件的主变形方向时,取样位置如下(见图9) 纵向试样;试样的长轴平行于锻件主变形方向;冲击试样的缺口轴线垂直于纵向和横向形成的 平面
横向试样;试样的长轴垂直于锻件主变形方向;冲击试样的缺口轴线垂直于纵向和横向形成的 平面
法向试样;试样的长轴垂直于锻什纵向和横向形成的平面;冲击试样的缺口轴线平行于主变形 方向
7.2.4.3试样相对于锻件的产品几何形状 当试样相对于锻件的产品几何形状时,取样位置如下(见图10) -轴向试样:试样的长轴平行于锻件旋转对称轴;冲击试样的缺口轴线垂直于圆周
GB/T37775一2019 -切向试样;试样的长轴与锻件圆周相切;冲击试样的缺口轴线垂直于圆周
径向试样;试样的长轴垂直于锻件圆周;冲击试样的缺口轴线平行于圆周
主变形方向(切向 口 C 纵向(切向) 法向(径向) 横向(轴向) 图9相对于锻件的主变形方向时取样位置图 o 横向(切向) 法向(径向) 纵向(轴向) 主变形方 向(轴向 图10相对于锻件的产品几何形状时取样位置图 7.3硬度检验 7.3.1检验方法 硬度检验按GB/T231.1规定的方法进行
7.3.2检验位置 重量小于或等于10o0k的饼形锻件和环形锻件,应至少在接近锻件12半径的上下端面上 7.3.2.1 进行一次硬度检验,上下端面相隔180';重量小于或等于1000kg的长轴锻件,应至少在其轴线上均匀 进行三次硬度检验
重量大于1000kg的饼形锻件,环形锻件,应至少在接近锻件1/2半径处和每个端面上相隔 7.3.2.2 180"处进行两次硬度检验,两个端面相隔90;重量大于1000k的轴类锻件,应至少在其轴线的两条素 线上各均匀进行三次硬度检验,两条素线相隔180°
7.4金相检验 7.4.1显微组织的检验方法按GB/T13298的规定,评定方法按GB/T13299的规定 平均晶粒度的测定方法按GB/T6394的规定
7.4.2 7.4.3非金属夹杂物的评定方法按GB/T10561的规定
10
GB/37775一2019 7.5残余应力测定 锻件残余应力的检测位置由供需双方商定,测定方法宜参照JB/T8888规定的方法进行,其他测定 方法由供需双方商定
7.6无损检测 超声检测方法按JB/T8467的规定
7.7复试 7.7.1拉伸试验 7.7.1.1由于试验机故障或试样的制备不正确而使试验结果不能满足规定的要求时,则应重新取试进 行试验
7.7.1.2拉伸试验中某一试验结果不合格,可在原试样相邻部位取双倍试样进行复试,双倍试样的复试 结果应全部满足规定要求
7.7.1.3力学性能试验如因试样有裂纹和白点原因不合格者,不得复试
7.7.2冲击试验 7.7.2.1V型缺口冲击试验 若一组冲击试样的试验结果不合格,可在原试样相邻部位再取一组三个试样复试,前后两组试样的 算术平均值不应低于规定要求,且单个值低于规定值的个数不应多于两个只能有一个单个值低于规定 值的70%
7.7.2.2U型缺口冲击试验 若某一试验结果不合格,可在原试样相邻部位取双倍试样进行复试,两个试样的复试结果均不应低 于规定要求
7.8重新热处理 如果锻件的任何一项或几项力学性能试验结果未达到规定时,允许对锻件进行重新热处理
重新 热处理的情况应记录在热处理报告中
重新热处理后的锻件应按原规定重新进行取样试验,重新热处 理的次数不得超过两次
除非另行规定,因力学性能试验结果不合格而进行的任何热处理均应记人重 新热处理次数,回火次数不限
验收和质量证明书 8.1验收 采购方有权选择锻件的某些试验项目进行验收,在验收检验中或以后的加工或检验中,发现锻件不 符合本标准、产品材料标准和订货合同中规定的技术要求时,采购方应及时通知制造方,双方协商解决 8.2质量证明书 交货时,制造方应向采购方提供质量证明书,质量证明书应至少包括以下内容; 合同号; a b)执行标准编号和材料牌号; 11
GB/T37775一2019 冶炼方法、熔炼炉号和锻件标识号; c d 热处理报告(若需要的话,包括重新热处理); e 化学分析报告(熔炼分析和成品分析); 力学性能试验报告; 金相检验报告 8 h 无损检测报告; 尺寸检查报告 其他要求的检验结果 j 标志和包装 9.1标志 9.1.1制造方应按订货合同规定的标识方法和标志进行标识,以保证锻件的可追溯性
9.1.2 若采剔方未规定标识方法,制造方应在每个缎什相当于锻绽水口猫打上合同号,熔炼炉号.银件 卡号,图样编号,制造方标识,并用白漆圈上 标识位置和标识方法不应对锻件的最终使用产生不利影响
9.1.3 9.2包装 9.2.1锻件的清洁,包装和运输应按订货合同的规定进行
供方应对锻件的表面进行适当保护以防止 运输和保管过程中出现损坏或锈蚀
9.2.2不锈钢锻件在制造和运输过程中,应避免接触到可能对材料性能和完整性产生不利影响的物 质,如;硫、铅、锌、铜,汞、铝、镐、锡、锄、呻、锯、卤素以及其他低熔点金属和其合金及化合物
此外,由于 含氯材料老化产生的酸性氯化物是潜在的危险,应合理选用胶带,标识材料等,以避免与其接触
9.2.3在加工,储存、,装卸、包装及运输过程中,应避免不锈钢与碳钢材料直接接触
9.2.4在焊接或热处理等热加工前,应清除干净可能与锻件表面发生反应或物质交换的异物
12
GB/37775一2019 附录 A (资料性附录) 特殊产品的技术和车间评定 A.1目的 本附录的目的是确定锻件制造车间的生产能力和锻件制造程序的适用性,以保证锻件适合于预期 的使用要求,同时,还可以保证本标准规定的验收试验和验收准则是具有代表性的
若制造方拥有经认 可的某类锻件产品的生产资格证书,则可以视为制造商通过该类锻件产品的技术和车间评定
A.2概述 制造方按规定的制造程序生产锻件前,应进行下述评定 按A.3的规定进行锻件的技术评定; 按A.4的规定进行车间评定
A.3锻件的技术评定 A.3.1适用范围 本技术评定适用于按规定制造大纲生产的锻件的检验和验证,以证明锻件制造工艺的合理性及使 用条件的适用性
评定过程中可确定锻件各项性能,特别是特殊要求和可检测性
A.3.2评定报告 采购前,应提交锻件的技术评定报告,报告中应包括A.3规定的所有要素或参数
锻件制造方应 编制评定报告,至少包括以下内容 -制造大纲; 各项试验和检验的结果
对已按制造大纲生产出类似锻件的有经验的制造方,检验力学性能等的试验大纲可适当地减少相 关内容.并用以前的存档资料进行补充
A.3.3评定的有效性 若锻件制造方改变任何一个可能影响评定的要素或参数,则应对这一改变可能产生的结果做出 评价
根据评价结果,对于锻件的技术评定是否有效可以得出以下某一结论: 评定继续有效; -补充检验后,评定继续有效 重新评定
A.3.4材料 采购方和制造方应以设计准则为基础考虑材料牌号,设计准则应包括尺寸规格,加工制造工艺和使 13
GB/T37775一2019 用条件
A.3.5制造大纲 锻件制造方应在制造大纲中写明可能直接影响锻件质量的主要参数
制造大纲应按制造流程顺序列出冶炼、锻造、机械加工、热处理、取试、无损检测等的工艺流程
制造大纲中应包括以下内容 -钢液的冶炼方式; 钢锭的重量和类型, 钢锭冒口,水口切除量; 锻件在钢锭中的位置; 锻造毛坯图(标明总锻造比); 热处理外形图,力学性能试料在图中位置,试样在试料上的位置; 性能热处理条件
A.3.6锻件性能的检验 制造方应按制造大纲规定对锻件进行各项试验和检验,以验证锻件的内部质量,评定锻件的化学成 分和力学性能,保证验收试验具有代表性,并保证无损检测的方法适合锻件的形状和制造工艺产生的各 类缺陷
A.3.7验收试验 评定报告中的各项数据应能够确定制造大纲中的验收试验可用来证明锻件质量,并已考虑到验收 准则对后序正式产品制造中的可能产生的偶然性 A.4车间评定 A.4.1适用范围 本车间评定适用于证明制造方有足够的能力制造出合格的产品
A.4.2评定报告 锻件制造方应在供货前提供制造锻件车间的评定报告
车间评定报告应包括设备、人员和编制、制 造经验等内容
A.4.3评定的有效性 若制造方改变或调整可能影响锻件技术评定的车间评定要素中任何一个要素,制造方应对改变和 调整可能带来的影响进行评价
根据评价结果,对于制造方的车间评价报告是否继续有效可以得出以下某一结论 继续有效或扩大适用范围 补充检验后,评定继续有效或扩大适用范围 重新评定
A.4.4设备 制造车间应具备满足制造要求的设备
制造方应提供下列设备的说明: 14
GB/37775一2019 冶炼和压力加工用的主要设备; 热处理设备; 力学性能检验和无损检测设备; 化学分析和金相检验的主要设备 若制造方没有所需的检验设备,应在车间评定报告中写明负责试验和检验的企业从事相关试验和 检验所具备的设备情况,并提供设备使用的相关资料
A.4.5人员 制造方从事制造的所有相关人员应具有相应的技能和资格
A.4.6制造经验 A.4.6.1制造 每种冶炼工艺和锻件的加工过程应提供以下资料 按材料牌号给出能生产的锻件重量; 锻件的外形和允许的尺寸(重量、厚度、长度等) 新产品的主要用户和主要用途; 通常使用的技术规范类型(规范、标准、规则等》
制造方制造的产品锻件(必要时经过评定),应尽可能同主要产品及同类型产品(牌号,尺寸,成形方 法)类似
A.4.6.2研发能力 制造方应提供以下可能影响供货的现有的和预期将进行的研发工作 研发能力简介; 材料的研究与开发情况
15
GB/T37775一2019 录 附 B 规范性附录) 锻造比 B.1定义 B.1.1锻造方向 锻件各部位在锻造过程中产生最大延伸的方向
注:锻件是纵向锻造还是横向锻造,取决于锻造方向是平行于钢锭的轴线还是垂直于钢锭的轴线
锻造方向平行 于钢锭的轴线为纵向锻造,锻造方向垂直于钢锭的轴线为横向锻造
锻造比代表锻件的各个部位锻造前与锻 造后在平行于锻造方向上测得的金属件长度之比
B.1.2拔长比 钢锭或坯料在拔长前的截面积与拔长后的截面积之比
B.1.3徵粗比 钢锭或坯料在锻造后的截面积与锻造前的截面积之比
B.1.4芯棒锻造比 锻件在芯棒锻造前的截面积与锻造后的截面积之比
B.1.5挤压比 锻件在挤压后的长度与挤压前长度之比
B.2 总锻造比 B.2.1锻件的纵向总锻造比等于每次连续锻造纵向锻造比的乘积
B.2.2锻件的横向总锻造比等于每次连续锻造横向锻造比的乘积
B.2.3总锻造比等于纵向锻造比与横向锻造比的乘积
B.3锄粗或压扁制品的总锻造比 B3.1压扁锻造比的定义:用平行于钢锭轴线的负荷对钢锭进行徵粗或压扁的锻造比等于锻件锻粗、 压扁后的横截面积和之前的横截面积之比,或锻粗、压扁前的厚度与之后的厚度之比
B.3.2锁粗或压扁锻件产品的总锻造比等于锻件皈粗或压扁的锻造比与徵粗或压扁前纵向锻造比的 平方根的乘积
16
GB/37775一2019 附录 C 资料性附录 大型钢质自由锻件常用的材料标准 本附录给出了大型钢质自由锻件常用的材料标准
对特定产品,还可能涉及所列材料标准之外的 其他标准
GB/T33083大型碳素结构钢锻件技术条件 GB/T33084大型合金结构钢锻件技术条件 GB/T33522渗碳轴承钢锻件技术条件 JB/T126525Mw200Mw汽轮机转子体和主轴锻件技术条件 JB/T126625Mw200Mw汽轮机轮盘及叶轮锻件技术条件 B/T1267 0Mw~200Mw汽轮发电机转子锻件技术条件 JB 1268汽轮发电机Mnl8Cr5系无磁性护环锻件技术条件 JB/T1269 汽轮发电机磁性环锻件技术条件 JB 1270 水轮机、水轮发电机大轴锻件技术条件 JB/T1271 交、直流电机轴锻件技术条件 JB/T3733大型锻造合金钢热轧工作辐技术条件 JB/T4120 大型锻造合金钢支承轭技术条件 JB/T6395大型齿轮、齿圈锻件技术条件 JB/T6398 大型不锈、耐酸、耐热钢锻件技术条件 大型轧锯锻件用钢技术条件 JB/T6401 JB/T7022工业汽轮机转子体锻件技术条件 JB/T7023水轮发电机镜板锻件技术条件 JB/T702525Mw以下汽轮机转子体和主轴锻件技术条件 以下汽轮发电机转子锻件技术条件 JB/T7026 50MW 00Mw以上汽轮机转子体锻件技术条件 JB/T7027 以下汽轮机轮盘及叶轮锻件技术条件 JB/T702825 JB/T7030汽轮发电机Mnl8Cr18N无磁性护环锻件技术条件 JB/T7032大型全纤维曲轴锻件技术条件 JB/T870550Mw以下汽轮发电机无中心孔转子锻件技术条件 JB/T870650Mw~200Mw汽轮发电机无中心孔转子锻件技术条件 JB/8707 300Mw以上汽轮机无中心孔转子锻件技术条件 JB/T8708300Mw一600Mw汽轮发电机无中心孔转子锻件技术条件 JB/T10265水轮发电机上下圆盘锻件技术条件 JB/T1066325Mw及25Mw以下汽轮机无中心孔转子和主轴锻件技术条件 JB/T1066425Mw200Mw汽轮机无中心孔转子和主轴锻件技术条件 JB/T110171000Mw及以上火电机组发电机转子锻件技术条件 JB/T11019超临界及超超临界机组汽轮机用高中压转子锻件技术条件 JB/T11020超临界及超超临界机组汽轮机用超纯净钢低压转子锻件技术条件 JB/T11021大型高铬锻钢支承辐技术条件 B/T11024大型核电机组汽轮机用焊接转子锻件技术条件 JB/T1l026大型核电机组四极汽轮发电机转子锻件技术条件
GB/T37775一2019 JB/T11028汽轮发电机集电环锻件技术条件 JB/T11030汽轮机高低压复合转子锻件技术条件 JB/T11032燃气轮机压气机轮盘不锈钢锻件技术条件 JB/T11033燃气轮机压气机轮盘合金钢锻件技术条件 JB/T12136 瓦楞辗筒体锻件 JB/T12137风力发电机组主轴锻件技术条件 JB/T12138风塔法兰大型环锻件技术条件 JB/T12139大型核电机组汽轮机整锻低压转子锻件技术条件 JB/T13378大型锻造合金钢铝轧机工作技术条件