GB/T37681-2019
大型铸钢件通用技术规范
Heavysteelcastings—Generaltechnicalspecification
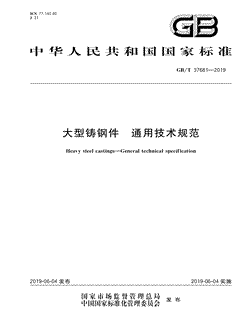
- 中国标准分类号(CCS)J31
- 国际标准分类号(ICS)77.140.80
- 实施日期2019-06-04
- 文件格式PDF
- 文本页数13页
- 文件大小1.01M
以图片形式预览大型铸钢件通用技术规范
大型铸钢件通用技术规范
国家标准 GB/T37681一2019 大型铸钢件通用技术规范 Hleavysteeleastings一Generaltechniealspecifieatonm 2019-06-04发布 2019-06-04实施 国家市场监督管理总局 发布 币国国家标准化管理委员会国家标准
GB/37681一2019 前 言 本标准按照GB/T1.1一2009给出的规则起草
本标准由机械工业联合会提出
本标准由全国大型铸锻件标准化技术委员会(SAC/TC506)归口
本标准起草单位:二重德阳)重型装备有限公司、第一重型机械股份公司、中信重工机械股份 有限公司、沈阳铸锻工业有限公司、太原重型机械集团有限公司
本标准主要起草人:刘显有、李骏骋、肖章玉、谢军虎、张亚才、徐恩献、杨树文、卫心宏、徐文金、 林平,李彬许诺、马宏、刘洪生
GB/37681一2019 大型铸钢件通用技术规范 范围 本标准规定了大型铸钢件(以下简称为“铸件”)的订货要求、制造工艺、技术要求、检验规则和试验 方法、验收和发货等
本标准适用于采用砂型或导热性与砂型相当的铸型铸造的大型铸钢件
规范性引用文件 下列文件对于本文件的应用是必不可少的
凡是注日期的引用文件,仅注日期的版本适用于本文 件
凡是不注日期的引用文件,其最新版本(包括所有的修改单)适用于本文件 GB/T222钢的成品化学成分允许偏差 GB/T223(所有部分钢铁及合金化学分析方法 GB/T228.1金属材料拉伸试验第1部分;室温试验方法 GB/T228.2金属材料拉伸试验第2部分;高温试验方法 GB 229 金属材料夏比摆锤冲击试验方法 GB 231. 金属材料布民硬度试验第1部分;试验方法 GB 232金属材料弯曲试验方法 GB 2039 金属材料单轴拉伸蠕变试验方法 3375 GB 1994接术语 GB 4334金属和合金的腐蚀不锈钢晶间腐蚀试验方法 GB 4336碳素钢和中低合金钢多元素含量的测定火花放电原子发射光谱法常规法 GB T 5611 2017铸造术语 GB 5677铸钢件射线照相检测 GB T 5678铸造合金光谱分析取样方法 GB 6394金属平均晶粒度测定方法 GB 6414一2017铸件尺寸公差、几何公差与机械加工余量 GB 6477 2008金属切削机床术语 GB 7233.1铸钢件超声检测第1部分:一般用途铸钢件 GB 7233.2铸钢件超声检测第2部分;高承压铸钢件 T GB 9443铸钢件渗透检测 GB 9444铸钢件磁粉检测 GB 9452热处理炉有效加热区测定方法 GB/T1l170不锈钢多元素含量的测定火花放电原子发射光谱法常规法 GB/T11261钢铁氧含量的测定脉冲加热惰气熔融-红外线吸收法 GB/T11351一2017铸件重量公差 GB/T113522009 -般工程用铸造碳钢件 GB/T13298金属显微组织检验方法 GB/T13299钢的显微组织评定方法
GB/T37681一2019 GB/T15056铸造表面粗糙度评定方法 GB/T17505一2016钢及钢产品交货一般技术要求 GB/20066钢和铁化学成分测定用试样的取样和制样方法 GB/T20123钢铁总碳硫含量的测定高频感应炉燃烧后红外吸收法(常规方法 GB/T20124钢铁氮含量的测定惰性气体熔融热导法(常规方法 GB/T20125低合金钢多元素含量的测定电感合等离子体原子发射光谱法 GB/T30824燃气热处理炉温度均匀性测试方法 TB/T2451铸钢中非金属夹杂物金相检验 术语和定义 GB/T561l一2017,GB/T3375一1994,GB/T6477一2008,GB/T17505一2016界定的以及下列术语和 定义适用于本文件
为了便于使用,以下重复列出了GB/T5611一2017.GB/T3375一1994,GB/T6477 2008,GB/T17505一2016中的一些术语和定义
3.1 大型铸钢件heaysteeleasting 通常,重量在3t以上或重量小于3t、但空间体积达到1m以上的铸钢件
3.2 铸造缺陷eastdefeet 在铸造过程产生的缺陷,一般主要是指铸件内部的孔洞、裂纹,夹杂物等缺陷
3.3 主要缺陷majordefect 重大缺陷 为补焊准备的坡口的深度超过25mm或超过所在截面厚度的40%以两者较小者为准)的缺陷
3.4 单铸试块separatedtetbarofcasttns 在单独制成的试块铸型中浇注的试块
单铸试块必须用与浇注铸件同炉或同包的金属液浇注
用 于加工成试样供检验化学成分、金相组织和力学性能等
[GB/T561l2017,定义3.1.21] 3.5 附铸试块testlug;castonsample 附在铸件上,切除以后不损坏铸件本体的试块
注:附铸试块加工成试样后用于检验铸件的化学成分、金相组织,力学性能等
[GB/T5611一2017,定义3.1.22] 3.6 铸造缺陷补焊坡口wedinggrooeforcastdefect 为便于补焊较深的铸造缺陷而成型的具有一定几何形状并带有一定斜度的型面
一般可采用机械 加工、碳弧气刨、砂轮等工具成型
3.7 熔炼meltins 通过加热使金属由固态转变为液态,然后进行成分调节和精炼,使其纯净度、温度和成分达到要求 的过程和操作
[GB/T5611一2017,定义3.5.1
GB/37681一2019 3.8 补贴pad 为增加冒口的补缩效果,沿冒口补缩距离,向着冒口方向铸件断面逐渐增厚的多余金属
[GB/T5611一2017,定义5.2.26] 3.9 精整dresingandinishins 通过采用补焊、碳弧气刨、砂轮打磨、喷丸(砂)等方式,使铸件表面质量或形状尺寸满足标准要求的 过程和操作
注改写GB/T5611一2017,定义8.3.7
3.10 碳当量 carbonequivalent 把钢中合金元素的含量按其作用折算成碳的相当含量,等于各种合金元素含量的折算碳量与实际 的总碳量之和
可作为评定钢材补焊性的一种参考指标
除另有规定,一般按照国际补焊学会推荐的 碳当量公式进行计算
CE=C十Mn/6十(Cr十V十Mo)/5十(Cu十Ni/15 式中: C、Mn、Cr、Mo、V、Ni、Cu -钢中该元素的质量分数,以%表示
注:改写GB/T3375一1994,定义2.124
3.11 粗加工roughing 以切除大部分加工余量为主要目的的加工
[GB/T6477一2008,定义2.6.8] 3.12 试验单元tesumit 根据产品标准或合同的要求,以在抽样产品上所进行的试验为依据,一次接收或拒收产品的件数或 吨数
[GB/T17505一2016,定义3.6们 3.13 抽样产品sampleprduet 检验,试验时,从试验单元中抽取的部分产品
[[GB/T175052016,定义3.7] 订货要求和文件 4.1在订货合同或订货协议中应注明铸件名称、图号、执行的标准、材料牌号,技术要求、检验项目,交 货状态和供货数量等信息
4.2需方应明确规定铸件的交货状态,提供经供需双方认可的订货图样和技术条件
4.3当需方提出执行的标准(技术规范)以外的特殊要求或补充要求时,应经供需双方商定
5 制造工艺 5.1熔炼 铸件用钢应采用感应炉或电弧炉熔炼,根据需要可进行炉外精炼,或其他经供需双方确认的满足要
GB/T37681一2019 求的熔炼方法
5.2铸造 除另有规定外,铸造工艺方法由供方自行确定包括铸造工艺方案,试块方案,造型,浇注等毛坯制 造过程的所有操作). 5.3切割 除另有规定外,一般在铸件性能热处理前可利用气体火焰、等离子,碳弧气刨等的热能切割去除(以 下简称为“热切割”)工件上多余的部分(如冒口、浇口、补贴等),以及对产品附铸试块切口
5.4热处理 5.4.1工艺制定及相关要求 除另有规定外,供方可根据产品要求制定合适的热处理工艺和进行热处理
5.4.2热处理设备的检验要求和炉温均匀性要求 热处理所使用的热处理炉及其配套设备应经测试和校检合格,测试和校检应按照cB/T9!52或 GB/T30824的规定进行
5.5补焊 5.5.1补焊前的技术准备 缺陷的消除 5.5.1.1 除另有规定外,根据铸件铸造缺陷情况,可采用铲挖、磨削、碳弧气刨、气割或机械加工等方法清除 缺陷
5.5.1.2坡口制备 根据缺陷大小、位置选择合适的铸造缺陷补焊坡口形式
对于采用碳弧气刨清理缺陷,碳弧气刨后 应打磨清除增碳层
坡口面应修至平整圆滑,并满足补焊操作的要求,不应存在尖角
5.5.1.3坡口焊前的无损检测 在补焊前,应采用磁粉检测或渗透检测对凹坑和坡口表面进行检测
应经无损检测证实无缺陷后 才能进行补焊
5.5.1.4焊前的预热 对于要求补焊的铸件,如有需要,焊前应进行预热,预热温度应符合焊接工艺规程要求
5.5.2补悍要求 5.5.2.1焊工的资格要求 焊工应取得符合要求的资格证书
5.5.2.2补悍工艺的审批确认 当需方有要求时,主要缺陷的补焊应报需方认可,并提供相应的焊接工艺规程(WPS)及工艺评定
GB/37681一2019 记录(PQR) 缺陷补焊前应详细记录补区的位置及坡口尺寸,形成完善可追溯的补焊区记录报告
5.5.2.3补焊过程的控制要求 铸件缺陷的补焊应在铸件奥氏体化热处理后进行
补焊应严格按照wPs文件要求进行,并对补 焊过程中的电流、电压参数、补焊时间、,缺陷编号、预热温度、层间温度、焊工信息等进行详细记录
补焊 过程中,若检查发现裂纹,未熔合、未焊透等影响质量的缺陷时,应及时采取措施清除缺陷,在确认缺陷 已被清除后,才能继续补煤
5.5.3焊后热处理及检验 5.5.3.1焊后热处理 原则上当铸件补焊完成后补焊区应进行去应力退火(特殊材料或特殊要求的产品除外). 焊后去应力退火温度应低于性能热处理时的回火温度,特殊情况,如果焊后去应力退火温度高于性 能热处理时的回火温度,性能试块应随炉去应力退火,并重新进行力学性能检测;去应力退火保温时间 应根据缺陷补焊深度及产品壁厚共同决定,推荐按照每100mm保温2h4h,最低保温时间为3h. 5.5.3.2焊后的检验 补焊部位按产品技术要求进行无损检测和表面硬度检验,除另有规定外,应按该补焊区所在部位铸 件本体的无损检测要求进行检验
在图样或订货协议中要求对补焊部位进行硬度检验时,还应在去应 力退火后进行表面硬度检验
5.6机械加工 5.6.1机械加工余量 除另有规定外,加工余量的选取由制造厂自行确定或按照GB/T6414一2017的规定选取,但应保 证机械加工后铸件成品的尺寸符合图样或协议要求
5.6.2机械加工后去应力退火 铸件在粗加工后如需进行去应力退火,退火温度应低于性能热处理时的回火温度,并保证随炉去应 力退火的性能试块的性能满足标准的要求
如果粗加工后还需进行补,且随后进行焊后去应力退火, 则可以省略粗加工后去应力退火工序
技术要求 6.1化学成分 6.1.1化学成分通用要求 铸件的化学成分应符合执行的标准、图样或协议的规定
大型铸钢件常用材料标准参见附录A
6.1.2残余元素 当需方无要求时,残余元素不作为验收依据;有要求时,应符合执行的标准、图样或协议的规定 6.1.3特殊当量值 当需方有要求时,可进行相关特殊当量碳当量、镍当量、铬当量等)计算,但需方应提供相应的计算
GB/T37681一2019 公式
当未提供相应的计算公式时,其中的碳当量计算公式按3.10执行
6.1.4成品化学成分允许偏差 当需方有要求时,应进行成品化学成分分析
除另有规定外,成品化学成分允许偏差应符合 GB/T222的规定 6.2力学性能 当需方有要求时,铸件的力学性能应符合执行的标准或协议的规定
6.3金相组织 当金相组织作为验收条件时,需方应规定各项检验的取样位置和验收等级
金相检验用试样应在力学性能用试块中制取,金相试样的制取应距试块毛坯表面不少于6mm;若 需方要求检验本体金相,其检验位置由供需双方商定
6.4无损检测 铸件在精整过程及机械加工后应进行无损检测,但由于铸件的形状,结构对内部质量保证有较大影 响,因此无损检测的方法、区域、验收等级等要求应根据产品设计或使用要求,由供需双方商定 6.5外观、形状、尺寸公差和重量公差 6.5.1外观质量要求 铸件上的粘砂,夹砂,分边、毛刺、氧化皮应清理干净
铸件的表面粗糙度应符合图样或订货协议的 要求
铸件表面不应存在影响使用的缺陷,如有缺陷可进行补焊修复
6.5.2尺寸公差 铸件尺寸公差应符合图样或订货协议的规定,如图样或订货协议中无规定,铸件尺寸公差应符合 GB/T64142017中的DCTG13至DCTG15级的规定
6.5.3重量公差 订货时供需双方可商定铸件的重量公差,若需方无要求时,重量公差应符合GB/T113512017中 的MT13级至MT15级规定
6.6特殊试验要求 当需方有要求时,可提出特殊试验如金相、高温拉伸、高温短时持久、低温冲击、弯曲试验、 FATT晶间腐蚀等)要求
试块方案 6.7 铸件应附带铸出附铸试块
除另有规定外,附铸试块的位置、数量和尺寸由供方确定
若由于工艺 或产品结构等原因无法放置附铸试块时,征得需方同意后,亦可采用单铸试块
单铸试块的形状和尺寸 应按GB/T11352一2009中图1中I、I、的规定执行
6.8试块的切割 当检验试块为附铸试块时,除另有规定外,允许附铸试块在热处理前进行切割开口,但不应完全从
GB/37681一2019 30mm 本体切断,应留10mm 的量与本体相连
热处理完成后,可采用火焰切割、锤击等方式使附铸 试块与本体分离
检验规则和试验方法 7.1试块检验要求 7.1.1试块热处理 对于切离本体的附铸试块,应随工件同炉执行所有热处理工序
单铸试块应与同炉浇注的铸件同 炉热处理后才能作为该批次铸件的检验试块
7.1.2试块数量不足时的处理 当检验试块数量不足时,经供需双方商定,可在铸件本体合适位置用机械加工方式取样用于检验, 但由于铸件本体与试块间存在差异,因此其取样位置、验收指标值等应由供需双方另行商定
7.1.3性能试验的时机 一般情况下以铸件性能热处理后的性能作为验收依据,当用户要求验收最终热处理后的性能,应在 订货要求中进行规定
7.1.4检验批 7.1.4.1当铸件的重量(净重)小于3t时,按照双同原则(同炉冶炼、同炉热处理)进行一组理化检验
7.1.4.2当铸件的重量(净重)大于或等于3t时,每件产品均应进行一组理化检验
7.1.5试样的加工 试样采用机械加工的方法从试块取下,至铸造表面最小距离为6mm,至用热切割表面的最小距离 为30mm
7.2无效试验的规定 试验结果不符合规定时,若存在以下的情况时,试验无效
试验无效时,可从相同试料上或靠近不 合格试块的相邻位置的试料上,重新取单倍样并重做试验,将重新试验的数据作为试验结果
试样加工不当(试样存在刀痕、未倒角等); a b) 试样安装不当或试验机的动作不当; c 试样上存在缺陷(断裂位置明显存在夹渣、气孔、缩松等铸造缺陷) d)拉伸试验中,在标点外的位置断裂
7.3化学成分分析 7.3.1取样和制样规定 化学成分分析取样和制样应按GB:/T20066或GB/T5678的规定执行
7.3.2熔炼分析 铸件化学成分熔炼分析用试样应在浇注过程中或出钢前从钢包中取样,每包取1个试样
如果单 个铸件采用多钢包合浇,则应对每一钢包取样并进行熔炼分析和记录
多包合浇的铸件,其化学成分用 加权平均分析法计算
GB/T37681一2019 7.3.3成品分析 如果需要成品分析,应在试块或在铸件本体上离铸造表面6mm以下部位取样进行成品分析
对 于检验批(炉)次,可随机在该试验单元中选取一个铸件的成品分析代表此批(炉)次所有铸件
7.3.4分析方法 化学成分分析按GB/T4336,GB/T11170,GB/T11261,GB/T20123,GB/T20124,GB/T20125、 GB/T223的规定执行
仲裁分析按GB/Tl1261,GB/T20123,GB/T20124,GB/T223(GB/T223.79 除外)的规定执行
7.4力学性能 7.4.1拉伸试验 室温拉伸试验按GB/T228.1的规定执行,试样尺寸应符合GB/T228.1的规定
7.4.2冲击试验 冲击试验按GB/T229中的规定执行
一组试验为3个冲击试样,3个冲击试样的试验结果的算术 平均值应符合规定,其中只允许有1个试样的试验结果低于规定值,但不应低于规定值的70%
7.4.3硬度检验 7.4.3.1 -般情况下,硬度不作为材料性能合格与否的验收依据
当硬度作为验收条件时,除另有规定 外,硬度要求均指检验试块的硬度,硬度检验应按批或件进行
mm6mm 7.4.3.2当在订货文件中要求验收铸件本体硬度时,产品硬度应在铸件的铸造表面下方3m 处测试
位置及数量无要求时,供方应至少选择2个具有代表性的位置进行测试
测试位置的表面粗 糙度Ra应<3.2m,若硬度测试工具对铸件测试表面有规定的,应达到相应的规定
7.4.3.3布氏硬度试验按GB/T231.1的规定执行
7.4.3.4除另有规定外,同一试样或本体同一区域的硬度应测量3个硬度值,3个硬度值的平均值应符 合规定 7.5无损检测 7.5.1渗透检测 铸件表面可进行渗透检测,以检测表面缺陷
渗透检测按GB/T9443的规定执行
7.5.2磁粉检测 铸件可采用磁粉检测,以检测铸件表面或近表层缺陷
磁粉检测按GB/T9444的规定执行
7.5.3超声检测 铸件内部缺陷可采用超声检测
超声检测按GB/T7233.1或GB/T7233.2的规定进行
7.5.4射线检测 铸件内部缺陷也可采用射线检测
射线检测按GB/T5677的规定执行
GB/37681一2019 7.6表面质量,形状、尺寸和重量检查 7.6.1表面质量检查 铸件表面进行目视检查,表面粗糙度评定按GB/T15056的规定执行
7.6.2形状、尺寸检查 铸件的尺寸和几何形状检验应使用量具、样板、机床划线或三维检测仪器检查
7.6.3重量检查 采用过磅方式进行重量检查,若对重量无特殊要求,可用尺寸检查代替重量检查
7.7特殊试验 特殊试验由需方规定试验方法和试验参数
推荐采用的特殊试验方法标准如下 高温拉伸试验按GB/T228.2的规定执行; a b 高温持久试验按GB/T2039的规定执行 FATT试验按GB/T229的规定执行; c d 晶间腐蚀试验按GB/T4334的规定执行; 显微组织检验方法按GB/T13298的规定,评定方法按G;B/T13299的规定 平均晶粒度测定方法按GB/T6394的规定 非金属夹杂物评定方法按TB/T2451的规定; g h)弯曲试验按GB/T232的规定执行,对于试验结果的判定准则(试验后试样外表面显示的缺陷 是否为裂纹),应由供需双方事先商定
7.8复试 7.8.1当力学性能试验结果不符合要求时,供方可进行复试
7.8.2拉伸试验不合格时,可在靠近不合格试块的相邻位置的试块上取试样进行双倍复试,如2个试 验结果均符合需方的规定,则该批量的拉伸性能为合格,否则供方可按7.9的规定处理
7.8.3冲击试验不合格时,可在靠近不合格试块的相邻位置的试块上取试样进行双倍复试,如果复试 的6个冲击试样的试验结果的算术平均值达到需方规定的平均值,且其中只允许有2个试样的试验结 果低于规定的平均值,但每个不应低于规定的70%,否则供方可按7.9的规定处理
7.8.4硬度不合格时,可在靠近不合格试块的相邻位置的试块上取试样进行双倍复试
复试结果的算 术平均值应符合需方的规定,则该批的硬度为合格,否则供方可按7.9的规定处理
7.8.5特殊试验不合格时,可进行一次复试,复试规则由供需双方商定
7.8.6当复试不合格对象为抽检样品时,且抽检样品所代表的试验单元由非双同(同熔炼,同热处理) 炉次,批量同种铸件组成时,可在所在单元剩余的产品中重新取样进行检验,取样位置及数量由供需双 方商定,如重新取样的试验结果均符合需方的规定,则该单元剩余的产品的性能为合格,否则供方可按 7.9的规定处理
第一次抽检不合格的样品需按7.9的规定处理
7.9重新热处理 当复试结果仍不符合规定时,可将铸件和试块重新进行热处理,未经需方同意,重新热处理不应超 过2次回火次数不限)
重新热处理后应按7.4一7.8的规定重新进行检测,检测内容及试样数量与原
GB/T37681一2019 规定相同
8 验收与交货 8.1验收 供方按订货文件要求对每一检验批的铸件进行检验,符合要求后交货
8.2标识 铸件应有供方标识、订货合同号,熔炼炉号,生产批号、铸件识别号等标识内容
8.3质量证明书 交货时,供方应向需方提供质量证明书
质量证明书应包括下列内容 a 订货合同号; b图号; 铸件名称 c 重量 d 产品执行标准编号和材料牌号 铸件识别号或熔炼炉号; 化学成分分析试验报告和力学性能试验报告等; g 热处理状态、热处理报告、热处理炉批号; h 主要缺陷及补焊记录(包括位置与尺寸草图); 合同和订货协议中有要求的其他检验报告
j 8.4涂装、包装 8.4.1当向需方交货时,铸件应清理干净,没有锈溃
只有订货文件有要求时,才使用表面涂漆或类似 的方法进行涂装防护处理
8.4.2供方应根据订货文件的要求进行包装,当订货文件没要求时.应根据运输条件要求进行包装
8.5售后申诉内容 8.5.1铸件在交货后,若发现因供方的责任造成产品质量问题无法使用,需方有权拒收,供方自行处理 拒收的产品
8.5.2铸件在交货后,产品铸件仍然存在超过规定的缺陷等质量问题,则供方应负产品不满足规定部 分的责任,并承担相关的修复工作及费用
8.5.3铸件在交货后,需方在后续加工中发现(或应当发现)铸件缺陷后因没有及时通知供方处理而继 续加工,从而造成供方无法修复或增大修复成本的,需方应承担相应的责任
8.5.4铸件在交货后,若存在需要由需方复检的项目如力学性能、尺寸等),需方应及时将所需复检项 目验收合格后再进行推序(加工,装配等)
若铸件在推序后才发现铸件需复检项目不合格的,从而导致 铸件无法进行修复的,供方不应承担相应的责任
10
GB/37681一2019 附 录 A 资料性附录 大型铸钢件常用材料标准 本附录给出了大型铸钢件常用材料标准清单
对特定产品,还可能涉及所列标准之外的其他标准
GB/T7659焊接结构用铸钢件 GB/T11352一般工程用铸造碳钢件 JB/T3735铸钢混流式转轮 JB/T6402大型低合金钢铸件技术条件 JB/T6403大型耐热钢铸件技术条件 JB/T6404大型高钢铸件技术条件 JB/T6405大型不锈钢铸件技术条件 JB/T7024300Mw以上汽轮机缸体铸钢件技术条件 JB/T7031 大型磨机类端盖铸钢件技术条件 JB/T7349水轮机不锈钢叶片铸件 JB/T8709大型轧钢机机架铸钢件技术条件 10264混流式水轮机补焊转轮上冠、下环铸件 JB/T11018超临界及超超临界机组汽轮机用Crl0型不锈钢铸件技术条件 JB/T11022大型高铬铸钢热轧工作儡技术条件 JB/T11025大型核电机组汽轮机用铸钢件技术条件 JB/T11027电渣熔铸大型水轮机铸件技术条件 JB/T11837大型曲轴电渣钢熔铸件技术条件
大型铸钢件通用技术规范GB/T37681-2019详解
随着工业制造技术的不断发展,大型铸钢件在各种重要设备和机器中得到广泛应用。为了规范大型铸钢件的生产和使用,国家发布了《大型铸钢件通用技术规范GB/T37681-2019》标准。
一、标准内容
《大型铸钢件通用技术规范GB/T37681-2019》标准共分为八个章节,分别是:范围、规范性引用文件、术语和定义、技术要求、试验、检验、包装、标志、运输和贮存。
其中,“技术要求”是该标准的核心部分,主要包括以下内容:
- 材料要求:规定了大型铸钢件所采用的材料种类、化学成分、力学性能和物理性能指标等。
- 制造要求:规定了大型铸钢件的制造工艺、加工方法、表面质量和尺寸精度等。
- 试验要求:规定了大型铸钢件的检测方法、检验标准和检验结果评定标准等。
二、对大型铸钢件制造行业的影响
《大型铸钢件通用技术规范GB/T37681-2019》标准的实施,将直接影响到大型铸钢件制造行业的生产和使用。具体来说,将从以下几个方面对大型铸钢件制造行业进行改进:
- 提高产品质量:标准对大型铸钢件的材料要求、制造要求和试验要求等都有所规定,将有助于提高大型铸钢件的产品质量。
- 优化生产流程:标准明确了大型铸钢件的制造工艺、加工方法和表面质量等方面的要求,将有助于优化生产流程,提高生产效率。
- 提高企业竞争力:标准对大型铸钢件的质量要求更加严格,企业在生产过程中必须按照标准规定进行制造和检测,这将有助于提高企业的竞争力。
三、总结
《大型铸钢件通用技术规范GB/T37681-2019》标准的出台,对规范大型铸钢件的生产和使用具有重要的意义。大型铸钢件制造企业应当积极响应国家政策,加强产品质量管理,优化生产流程,提高企业竞争力,为中国制造业的现代化建设做出自己的贡献。